Введение
Развитие технологии и оборудования сварочных процессов идет в настоящее время достаточно быстрыми темпами. Это вызвано все более возрастающей потребностью создания качественных неразъемных соединений как из однородных, так и разнородных материалов.
Сварка – технологический процесс получения неразъемных соединений материалов посредством установления межатомных связей между свариваемыми частями при их местном или общем нагреве, или пластическом деформировании, или совместном действием того и другого.
Сварка – экономически выгодный, высокопроизводительный и в значительной степени механизированный технологический процесс, широко применяемый практически во всех отраслях машиностроения.
Физическая сущность процесса сварки заключается в образовании прочных связей между атомами или молекулами на соединяемых поверхностях заготовок. Для образования соединений необходимо выполнение следующих условий: освобождение свариваемых поверхностей от загрязнений, оксидов и адсорбированных на них инородных атомов; энергетическая активация поверхностных атомов, облегчающая их взаимодействие друг с другом; сближение свариваемых поверхностей на расстояния, сопоставимые с межатомным расстоянием в свариваемых заготовках.
Указанные условия реализуются различными способами сварки путем энергетического воздействия на материал в зоне сварки. Энергия вводится в виде теплоты, упругопластической деформации, электронного, ионного, электромагнитного и других видов воздействия. В результате поверхностные атомы металлов и кристаллических неметаллических материалов образуют общие для соединяемых заготовок кристаллические решетки, а на поверхности пластмасс происходит объединение частей молекулярных цепей.
В зависимости от формы энергии, используемой для образования сварного соединения, все виды сварки разделяют на три класса: термический, термомеханический и механический.
К термическому классу относят виды сварки, осуществляемые плавлением с использованием тепловой энергии (дуговая, плазменная, электрошлаковая, электроннолучевая, лазерная, газовая и др.).
К термомеханическому классу относят виды сварки, осуществляемые с использованием тепловой энергии и давления (контактная, диффузионная и др.).
К механическому классу относят виды сварки, осуществляемые с использованием механической энергии и давления (ультразвуковая, взрывом, трением, холодная и др.).
1.
Выбор материала для изготовления изделия
Условия работы лопаток и требования к материалу
Для изготовления диафрагменной лопатки предоставлена высокохромистая жаропрочная сталь мартенситно-ферритного класса 12Х13 (ГОСТ 18968–73). Подбор данной стали осуществлен из условий эксплуатации изделия. Лопатки являются наиболее нагруженными деталями паровых турбин. Лопатки паровых турбин подразделяются на направляющие (диафрагменные), закрепленные в статоре и рабочие – на роторе. На диафрагменные лопатки в основном действуют только аэродинамические силы, которые являются не стационарными, а переменными. Воздействующая среда, которая направляется диафрагменными лопатками, достигает температуры 400 0
С. При этом имеет место неравномерный нагрев лопаток. Из-за взаимного воздействия приложенных сил материал лопатки испытывает меняющиеся по значению, но всегда высокие напряжения, что приводит к возникновению вибрации усталости материала.
Поверхности лопаток подвержены химическому воздействию среды. Химическая агрессивность водяного пара на материал лопаток особенно сильно проявляется с повышением начальной температуры, что приводит к постепенному разрушению материала, вызванного его эрозией. Поверхности лопаток (как на роторе, так и в диафрагме) последних ступеней паровых турбин при этом разъедаются со стороны входной кромки частицами воды влажного пара. Поэтому для лопаток применяют высококачественные материалы. От таких материалов требуют прочности при высокой температуре, высокой пластичности, сопротивления ползучести, коррозионной стойкости, высокой усталостной прочности, высокого декремента затухания.
Классификация сталей по структурному признаку
Номенклатура марок сталей, применяемых в настоящее время в различных отраслях промышленности для изготовления сварных конструкций, исключительно широка, а все возможные сочетания из их разнородных соединений практически трудно перечислить. Поэтому для упрощения задачи классификации и выбора наиболее распространенные (преимущественно стандартизованные) марки сталей, разделены исходя из структурного состояния на три основных класса:
1. – перлитные (углеродистые и низколегированные);
2. – ферритные и ферритно-мартенситные (высокохромистые);
3. – аустенитные и ферритно-аустенитные (хромоникелевые).
Каждый класс разделен, в свою очередь, на группы, в которую включены стали с относительно близкими свойствами, свариваемостью и служебными характеристиками.
Разделение высоколегированных сталей на группы (кислотостойкие, жаростойкие, жаропрочные) произведено в соответствии с их основными служебными свойствами и в некоторой степени условно, так как кислотостойкие стали одновременно являются жаростойкими до определенных температур, а жаростойкие являются также коррозионостойкими в определенных средах и т.д.
Для определения структурного класса сталей часто пользуются диаграммой Я.М. Потака и Е.А. Сагалевича, которая позволяет полуколичественно определять фазовый состав сталей. Наиболее существенным отличием этой диаграммы является то, что по осям координат откладываются хромовые эквиваленты ферритообразования (абцисса) и мартенситообразования (ордината), причем последний рассчитывается по степени влияния всех легирующих элементов на температуру начала мартенситного превращения.
Обоснование выбора материала
Теоретически, для изготовления диафрагменной лопатки, при условии выполнения всех вышеперечисленных требований, возможно применение и других материалов. Например, высокохромистые стали того же класса, что и сталь 12Х13, но с другим химическим составом: 08Х13, 20Х13, 15Х11МФ, 15Х12ВМФ и др.; аустенитные стали с высоким содержанием никеля и марганца: ХН35ВТ, 09Х14Н19В2БР1 и др.; титановые сплавы. При выборе материала, для изготовления любой конструкции, обеспечивающего ее технологичность, необходимо учитывать экономический и технологический факторы. Учитывая экономический фактор данной задачи, сталь 12Х13 является одной из самых дешевых в своем классе высокохромистых сталей, т. к. чем выше степень легирования, тем выше цена стали и степень ее распространенности в промышленности. В химический состав других классов и сплавов входят никель и титан соответственно, которые являются стратегическими материалами, что обеспечивает им более высокую цену. Поэтому для обоснования выбора высокохромистой стали 12Х13 по технологическому фактору, рассмотрим еще несколько сталей из этого же класса. Возьмем стали обладающие одинаковым набором элементов в своем составе: 08Х13 и 20Х13. Химический состав (ГОСТ 5632–72) высокохромистых коррозионно-стойких сталей приведены в таблице 1. Механические свойства – таблица 2.
Таблица 1.
Марка стали |
Класс |
Содержание элементов
(остальное Fе), %
|
С |
Сr |
08Х13 |
Ферритный |
< 0,08 |
12–14 |
12Х13 |
Ферритно – мартенситный |
0,09–0,15 |
12–14 |
20Х13 |
Мартенситный |
0,16–0,25 |
12–14 |
Таблица 2.
Марка стали |
Механические свойства |
Число твердости по Бринеллю НВ, МПа |
Предел текучести s0,2
, МПа |
Предел текучести sв
, Мпа |
Относительное удлинение d5,
% |
Относительное сужение j, % |
Уд. вязкость aн
при 200
С, Н м/см2
|
Не менее |
08Х13 |
412 |
588,6 |
20 |
60 |
98,1 |
1834–2129 |
12Х13 |
539–686,7 |
637,7 |
18 |
45 |
58,9 |
1933–2502 |
20Х13 |
568,5–716 |
755,4 |
15 |
50 |
58,9 |
2226–2639 |
Исходя из этих данных, охарактеризуем каждую сталь в отдельности, а затем сделаем вывод. Для каждой из этих сталей свойственны одни и те же дефекты, вызванные воздействием сварочного процесса, но проявляются они в разной степени. Главными среди них являются склонность к охрупчиванию и к образованию холодных трещин (для 08Х13 – ХТ нет).
В случаях, когда металл шва и околошовной зоны в процессе охлаждения претерпевает фазовые и структурные превращения, связанные с изменением его удельного объема и значительным ухудшением пластических свойств, трещины могут возникать в области низких температур – ниже 200˚С. Подобные явления имеют место при сварке закаливающихся сталей. Такие трещины называются холодными. Они могут быть поперечными (в шве, чаще в околошовной зоне), а также располагаться параллельно границе сплавления (отколы). Процесс образования холодных трещин определяется двумя факторами:
1) величиной и характером напряжений и деформаций, возникающих вследствие неравномерного нагрева, фазовых и структурных превращений в металле;
2) свойствами (главным образом пластичностью) металла в температурном интервале образования холодных трещин.
Насыщение металла сварного соединения водородом способствует образованию трещин, так как отрицательно влияет как на первый, так и на второй фактор.
Появление холодных трещин связывают с фазовыми и структурными превращениями, продуктами которых являются структуры с низкими пластическими свойствами (в нашем случае мартенсит).
По сравнению с другими структурными составляющими, мартенсит характеризуется высокой твердостью (НВ 500–600), весьма малой пластичностью и повышенным удельным объемом. В связи с этим структурные превращения аустенит – мартенсит связаны с наиболее значительным увеличением объема.
Обеспечить стойкость металла шва и, в особенности, околошовной зоны к образованию трещин – основная проблема свариваемости сталей мартенситного и мартенситно – ферритного классов. В этом случае для металла шва и околошовной зоны характерно наличие укрупненных зерен низкоуглеродистого высокохромистого феррита (микротвердость 152–164 кГ/мм2)
и легированного мартенсита (микротвердость 429–458 кГ/мм2)
.
Легированный мартенсит более пластичен, чем углеродистый, и называется игольчатым мартенситом. Но присутствие в структуре металла последнего все же увеличивает общую твердость и хрупкость шва, а также околошовной зоны, заметно снижая ударную вязкость. Поэтому здесь возможно появление холодных трещин.
Чтобы уменьшить возможность появления холодных трещин при сварке закаливающихся сталей, стремятся предупредить образование хрупкой закаленной зоны вблизи шва. Для этого выбирают режимы сварки с большой погонной энергией, при которой скорость охлаждения шва и околошовной зоны уменьшается. В тех же целях применяют подогрев изделия (до температуры 250˚С и выше в зависимости от содержания углерода и хрома в стали), замедленное охлаждение изделия после сварки и д. р.
После сварки обязательна термообработка изделия – высокий отпуск 650˚ – 700˚С. В результате отпуска несколько уменьшается прочность металла, а его твердость и ударная вязкость достигает исходных величин.
Сталь 08Х13
используется для деталей и инструментов, подвергающихся воздействию слабоагрессивных сред: воды, атмосферы, разбавленных растворов кислот и солей т.д., работающих при температурах до 4000
С.
Данная сталь обладает ферритной структурой, а следовательно, не имеет превращения g«a и не упрочняется термической обработкой. Главный недостаток этой стали – резкое охрупчивание после нагрева выше 1000–11000
С. Это объясняется наличием большого количества свободного d-феррита, содержание которого зависит от количества С и Сr. Это затрудняет сварку ферритных сталей, так как для частичного уменьшения хрупкости сварные соединения должны подвергаться отжигу при 750–8000
С, а перед ней – предварительному подогреву до 150 – 2500
С. По завершении отжига требуется ускоренное охлаждение, чтобы не допустить охрупчивание. Сталь данной структуры после высокотемпературного нагрева подвержена МКК.
Сталь 20Х13
используется для деталей и инструментов, подвергающихся воздействию слабоагрессивных сред: воды, атмосферы, разбавленных растворов кислот и солей т.д., работающих при температурах до 4500
С. Структура отожженных сталей представляет собой легированный феррит с частицами карбида хрома. Отожженные стали имеют удовлетворительную стойкость против коррозии, но их прочность невысока – 500Мпа. Прочность увеличивается после закалки и отпуска. Закалку проводят с 1050–11000
С для растворения карбида хрома. Изделия после закалки подвергают либо низкому (200–4000
С), либо высокому (600–7000
С) отпуску. Максимальное сопротивление коррозии стали имеют после низкого отпуска, пониженное, но тем не менее достаточно высокое – после высокого отпуска. Шлифование и полирование поверхности дополнительно повышает стойкость изделий. Отпуск при 400–6000
С резко снижает сопротивление коррозии и поэтому не применяется.
Мартенситные стали после отжига удовлетворительно обрабатываются резанием, горячая обработка и сварка этих сталей затруднены из-за образования мартенсита. Мартенсит увеличивает склонность этой стали к образованию холодных трещин при сварке. Это объясняется высокой степенью тетрагональности кристаллической решетки мартенсита. При снижении содержания мартенсита вязкость увеличивается, однако, при этом образуется свободный d-феррит, который придает сталям повышенную хрупкость. При сварке мартенситных сталей холодные трещины могут наблюдаться в процессе непрерывного охлаждения при температуре ниже Мн
, а также в процессе выдержки при нормальной температуре.
Сталь 12Х13
, как видно из табличных данных, занимает промежуточное положение по свойствам между 08Х13 и 20Х13, т. к. обладает промежуточной ферритно-мартенситной структурой (содержание феррита не менее 10%).
2.
Свариваемость стали 12Х13
Из-за своего промежуточного положения, сталь 12Х13 обладает лучшей свариваемость среди всех трех сталей. Это объясняется умеренным содержанием d-феррита. Количество d-феррита увеличивается с увеличением в стали % Сr и уменьшением % С. Формирование значительного количества d-феррита в структуре ОШЗ резко уменьшает склонность сварного соединения к образованию холодных трещин, но увеличивает хрупкость. Количество d-феррита зависит от уровня температуры нагрева. В участках ОШЗ, нагреваемых до температур близких к Тсолидуса
, количество d-феррита может быть подавляющим. Такая структура характерна для участка ЗТВ примыкающего к линии сплавления. Ширина этого участка мало зависит от температуры подогрева, но возрастает с увеличением qп
– погонной энергии, которая зависит от выбранных режимов и способа сварки.
Так как во всех сталях содержание Сr остается постоянным, то объем d-феррита зависит от % С. Пониженное содержание С в стали 08Х13 способствует резкому увеличению содержания d-феррита, а следовательно и высокому охрупчиванию. А высокое содержание % С в стали 20Х13 способствует увеличению склонности к холодным трещинам, но с низким охрупчиванием. В стали же 12Х13 эти два негативных момента находятся на удовлетворительном уровне. К этому можно добавить, что меньшее содержание С, по сравнению со талью 20Х13, сопровождается увеличением количества феррита и образованием более пластичного мартенсита, а по сравнению со сталью 08Х13, не требуется предварительный нагрев. Для уменьшения количества закалочных структур и увеличения выделения карбидов после сварки рекомендуется проводить высокий отпуск при Т=650–7000
С.
Особенности термической обработки сварных соединений из сталей феррито-мартенситного класса
Термическая обработка сварных соединений из высокохромистых сталей производится с целью:
1) снятие остаточных сварочных напряжений при необходимости сохранения точных размеров изделий;
2) обеспечения стойкости против межкристаллической коррозии при эксплуатации в агрессивных средах;
3) повышение жаропрочности и стойкости против локальных разрушений при эксплуатации в условиях высоких температур.
4) обеспечение уменьшения количества закалочных структур и увеличения выделения карбидов.
Учитывая высокую склонность к закалке нержавеющих феррито-мартенситных сталей, содержащих углерода 0,1% и более, после сварке необходим высокий отпуск в интервале температур от 650 до 7000
С ºС.
3.
Выбор способа сварки и его основные параметры
Параметры выбора способа сварки
При выборе способа сварки для изготовления сварной конструкции на предприятии необходимо руководствоваться следующими условиями:
– экономическая целесообразность,
– технологичность,
– наличие необходимого оборудования,
– наличие квалифицированных кадров,
– экологичность и безопасность.
Под технологичностью способа понимается возможность создавать сварное соединение, удовлетворяющего требованиям к нему, на современном оборудовании, удобном в эксплуатации и обслуживании и наиболее эффективном в экономическом отношении. Технологичность способа понятие относительное и зависит от производственных условий.
Исходя из условий, существующих на предприятии, где изготавливается диафрагменная лопатка, наиболее приемлемым является способ электронно-лучевой сварки.
Общая характеристика электронно-лучевой сварки (ЭЛС)
Электронно-лучевое воздействие на металлы, приводящее к их нагреву, плавлению и испарению, как технологическое направление в области их обработки интенсивно применяется в последнее время. Сущность процесса электронно-лучевого воздействия состоит в том, что кинетическая энергия сформированного в вакууме тем или иным способом электронного пучка (импульсного или непрерывного) превращается в тепловую в зоне обработки. Так как диапазоны мощности и концентрации энергии в луче велики, то практически возможно получение всех видов термического воздействия на материалы: нагрев до заданных температур, плавления и испарения с очень высокими скоростями.
Электронно-лучевая технология развивается в основном в трех направлениях: плавки и испарения в вакууме, сварки и прецизионной обработки.
Для сварки металлов создано оборудование трех классов: низко-, средне-, и высоковольтное, охватывающее диапазон ускоряющих напряжений 20–150 кВ. мощность установок составляет 1–120 кВт и более при максимальной концентрации энергии 105
-106
Вт/см2
. Электронно-лучевые установки мощностью до 30 кВт позволяют решить большинство сварочных проблем.
Электронно – лучевое воздействие в диапазоне плотностей энергии 105
-106
Вт/см2
характеризуется феноменом «кинжального», или глубокого проплавления с соотношением глубины шва к его ширине 10:1 и более. При этом электронный луч фокусируется на площади диаметром менее 0,001 см, что позволяет получить большую удельную мощность. При использовании обычных сварочных источников теплоты (дуги, газового пламени) металл нагревают и плавят за счет распространения теплоты от поверхности в глубину, при этом форма зоны расплавления в сечении приближается к полукругу F2
. при сварке электронным лучом теплота выделяется непосредственно в самом металле F1,
причем наиболее интенсивно на некоторой глубине под его поверхностью. (рис. 1).
    1,5 мм
F2
F1
15
  0,5
Рис. 1. Кинжальное проплавление при ЭЛС; F2
и F1
– сечения швов при дуговой электроннолучевой сварке
Незначительная ширина зоны теплового воздействия дает возможность резко уменьшить деформацию заготовок. Кроме того, за счет вакуума обеспечиваются зеркальная поверхность соединения и дегазация расплавленного металла. При этом минимальная толщина свариваемых заготовок составляет 0,02 мм, максимальная – до 100 мм.
Электронный луч представляет собой сжатый поток электронов, перемещающийся с большой скоростью от катода к аноду в сильном электрическом поле. При соударении электронного потока с твердым телом более 99% кинетической энергии электронов переходит в тепловую, расходуемую на нагрев этого тела. Температура в месте соударения может достигать 5000–6000 о
С. Электронный луч образуется за счет эмиссии электронов с нагретого в вакууме 133*(10-4
-10-5
) Па катода 1 и с помощью электростатических и электромагнитных линз 4 фокусируется на поверхности свариваемых материалов (рис. 2).
   1
    2
  3
   4
    5
        6
Рис. 2. Схема установки для ЭЛС
В установках для электронно-лучевой сварки электроны эмитируются на катоде 1 электронной пушки; формируются в пучок электродом 2, расположенным непосредственно за катодом; ускоряются под действием разницы потенциалов между катодом и анодом 3, составляющей 20–150 кВ и выше, затем фокусируются в виде луча и направляются специальной отклоняющей магнитной системы 5 на обрабатываемое изделие 6. На формирующий электрод 2 подается отрицательный или нулевой по отношению к катоду потенциал. Фокусировкой достигается высокая удельная мощность (до 5*105
кВт/м2
и выше). Ток электронного луча невелик (от нескольких миллиампер до единиц ампер). При перемещении заготовки под неподвижным лучом образуется сварной шов. Иногда при сварке перемещают сам луч вдоль неподвижных кромок с помощью отклоняющих систем. Отклоняющие системы используют также и для колебаний электронного луча поперек и вдоль шва, что позволяет сваривать с присадочным металлом и регулировать тепловое воздействие на металл.
Достоинства электронно-лучевой сварки (ЭЛС)
Электронный луч успешно применяется в машиностроении для сварки изделий из высоколегированных сталей, в частности из высокохромистых коррозионно-стойких сталей (12Х13). Это объясняется рядом достоинств ЭЛС при сварке этих сталей:
1. Минимальная деформация свариваемого изделия, т. к. поток электронов внедряется в свариваемое изделие на всю глубину проплавления, что обеспечивает получение минимальной металлоемкости сварочной ванны. Это обеспечивается возможностью концентрации большой мощности в электронном луче и управления ею в широких пределах в сочетании с высоким вакуумом в рабочем объеме.
2. Высокие физико-химические характеристики сварного соединения непосредственно после сварки позволяют исключить последующую механическую обработку.
3. Относительно высокая погонная энергия при сильной степени ее концентрации, т.е. энергия, вводимая в участок сварного соединения за определенный промежуток времени. При этом достигается высокая скорость кристаллизации металла сварного шва и минимальное термическое воздействие сварочного нагрева на основной металл в ОШЗ (локальность сварочного нагрева).
Применительно к стали 12Х13 необходимо отметить то, что последний пункт имеет к ней особое значение. Количество d-феррита в этой стали зависит от уровня температуры нагрева. В участках ОШЗ, нагреваемых до температур близких к Тсолидуса
, количество d-феррита может быть подавляющим. Такая структура характерна для участка ЗТВ примыкающего к линии сплавления. Ширина этого участка мало зависит от температуры подогрева, но возрастает с увеличением qп
– погонной энергии, которая при ЭЛС велика, но в то же время одновременно уменьшается склонность стали к холодным трещинам.
Основные параметры электронного луча в непрерывном и импульсном режимах
Параметрами электронного луча, измеряемыми в процессе обработки, являются:
- ток луча I
,
- ускоряющее напряжение U
,
- ток фокусирующей системы Iф
,
- рабочее расстояние (расстояние от центра фокусирующей системы до поверхности свариваемой детали) l
,
- скорость перемещения электронного луча V,
- угол сходимости луча a.
Кроме основных параметров, существуют другие количественные показатели ЭЛС:
1. Мощность электронного луча
(Вт) q= IU.
2. При заданном рабочем расстоянии l
,
токе фокусировки Iф
и мощности сварки можно определить диаметр электронного луча d
и, следовательно, удельную мощность q
2
(Вт/см2
), которая является одним из определяющих параметров процесса:
q2
= IU/pd2
/4.
3. Погонная энергия (кал/см)
Q = 0,24IU/V
не является определяющим параметром, так как при электронно-лучевой обработке в зависимости от величины удельной мощности q2
, при одинаковой погонной энергии можно получить различную конфигурацию зоны обработки.
При воздействии в импульсном режиме средняя мощность (Вт)
qи
= IUf
t
,
где I
– величина тока в импульсе, А; f
– частота следования импульсов, Гц; t – длительность импульса, с.
4. Скорость обработки в импульсном режиме (см/с)
V = B (1-k)/(t-tп
) = B (1-k) f
,
где tп
– время паузы между импульсами, с; k – коэффициент перекрытия точек (обычно k = 0,5 – 0,9); В-диаметр зоны обработки (точки).
5. Шаг точек (см) S = V(t+tп
), скорость обработки
V= S/(t+tп
),
6. Параметром, характеризующим соотношения длительности импульса и времени паузы в импульсном режиме, является скважность цикла
G= t/(t+tп
),
7. Наиболее существенным и одновременно наиболее трудноопределяемым параметром электронного луча является его диаметр. При заданных плотностях тока эмиссии с катода, температуре катода и сферической аберрации линзовой системы пучок электронов с максимальным током может быть сфокусирован в пятно минимального диаметра.
d = S0
(I/U)3/8
,
где S0
– постоянная электронно-оптической системы, вычисляемая эмпирически.
8. Разряжение (мм. рт. ст., Па).
9. Частота автоколебаний: f»Vсв
/d.
4. Исследование влияния основных параметров сварки на форму шва и качество сварного соединения
Влияние тока электронного луча на глубину проплавления металла
С целью определения зависимости величины сварочного тока от толщины соединяемых деталей была проведена серия экспериментов. Сварку выполняли с помощью электронно-лучевой установки «Луч-4» на образцах из нержавеющей стали. Полученные зависимости при разных скоростях сварки и при общих остальных параметрах (U = 30 кВ, l
= 100 мм, Iф = 100мА).
Из представленных графиков можно сделать вывод, что при увеличении тока электронного луча, глубина проплавления тоже увеличивается.
Влияние удельной мощности электронного луча на геометрию зоны проплавления
В связи с тем, что энергетический баланс процесса электронно-лучевой сварки близок к аналогичному балансу при дуговой сварке, связь параметров электронного луча с характеристиками зоны проплавления можно дать в виде уравнения для секундного объема плавления металла:
0,24 IUhи
hт
= rVFпр
Sм
, (1)
где Fпр
–
площадь проплавления,см2
; Sм
= (сТпл
+ Lпл
) – теплосодержание жидкого металла при температуре плавления, кал/г.
Из этого уравнения следует, что чем выше погонная энергия Q = 0,24 IU/V, тем больше площадь проплавления. Это действительно справедливо для процесса дуговой сварки, который в большинстве случаев осуществляется при q2
<q2
*
. Для электронно-лучевой сварки экспериментально установлено, что обобщенный параметр – погонная энергия Q не является определяющим при количественной оценке процесса. При постоянной погонной энергии можно получить глубину проплавления и 15 и 2 мм. Этот факт следует считать естественным, так как образование кинжального проплавления при электронно-лучевой сварке определяется не только количеством введенной энергии, но, и ее плотностью.
Эффективность процесса проплавления металла электронным лучом определяется величиной теплового КПД hпр
= hи
hт
, где hи
– эффективный; hт
– термический КПД. Величина эффективного КПД hи
при воздействии луча с образованием канала в веществе практически приближается к единице. При оценке эффективности процесса проплавления существенную роль играет величина термического КПД.
Для использования в инженерных расчетах в уравнениях (1) должна быть учтена удельная мощность электронного луча q2.
С этой целью произведены эксперименты по электронно-лучевой сварке с постоянной погонной энергией, но разной степенью фокусировки (разной удельной мощностью). Сварку выполняли с помощью электронно-лучевой установки ЭЛУ-9Б с электронной пушкой ЭП-60/10М на образцах из нержавеющей стали размером 500 х 80 х 20 мм.
В первой серии опытов образцами служили две пластины толщиной 10 мм каждая, сварку выполняли встык с зазором. Во второй серии в качестве образцов использовали пластины толщиной 20 мм.
В процессе сварки через каждые 60 мм длины шва изменяли фокусировку электронного луча на 4 мА в диапазоне токов фокусировки от 76 до 100 мА. Таким образом, концентрация мощности при постоянной погонной энергии в процессе наложения сварного шва постепенно увеличивалась, а после достижения максимума уменьшалась. Рабочее расстояние сохранялось постоянным h
= 90 мм (см. табл. 3).
Анализ макрошлифов и очертаний зон проплавления показал, что при постоянном значении погонной энергии можно в широком диапазоне изменять геометрию проплавления с помощью только одного параметра режима сварки – степени фокусировки электронного луча. При этом очертание зоны проплавления изменялось от полукруглого до кинжального, а при больших отрицательных значениях степени фокусировки переходило в «клыкообразное». Опыт показал также, что максимуму глубины проплавления соответствует минимальная ширина шва. Зависимость глубины проплавления Н
от степени фокусировки электронного луча DIф
приведена на рис. 5. Под степенью фокусировки DIф
понимают алгебраическую разность токов магнитной линзы при сварке и фокусировке на малом токе луча (2–4 мА): DIф
= ±(Iф
– I0
) – За нулевую точку отсчета принят ток фокусировки Iф
= 88 мА.
Характер кривой Н= f
(DIф
) (рис. 4) Н, свидетельствует, что степень фоку – мм сиповки, соответствующая максимальному проплавлению на данном режиме, зависит от тока луча: с уменьшением тока луча до величины, обеспечивающей максимальное проплавление, DIф
стремится к нулю.
Таблица 3. Характеристика экспериментальных очертаний зон проплавления
Параметр |
Условный индекс шва |
1 |
2 |
3 |
4 |
5 |
6 |
7 |
Ток фокусировки Iф,
мА. |
76 |
80 |
84 |
88 |
92 |
96 |
100 |
Степень фокусировки DIф
, мА. |
-12 |
-8 |
-4 |
0 |
+4 |
+8 |
+12 |
Коэффициент формы шва,
Кф
= Н/В.
|
2,11 |
4 |
2,45 |
1,46 |
1,0 |
0,72 |
0,56 |
Экспер-ная ширина зоны проплавления, мм |
24 |
22 |
21 |
20,6 |
32 |
47 |
59 |
Опыт |
Ток фокусировки, мА |
72 |
76 |
80 |
84 |
88 |
92 |
96 |
100 |
№1 |
       |
       |
      |
      |
      |
      |
      |
      |
Влияние изменения рабочего расстояния пушка-деталь на геометрию зоны проплавления
Заглубление в материал фокуса электронного луча может существенно увеличить глубину отверстия. Аналогичный эффект наблюдается и при электронно-лучевой сварке с кинжальным проплавлением.
С целью определения влияния заглубления фокального пятна на геометрию зоны проплавления при экспериментах на электронно-лучевой установке ЭЛУ-9Б с электронной пушкой ЭП-60/10М на образцах из нержавеющей стали размером 500 х 80 х 20 мм сварку осуществляли с переменной рабочей дистанцией Н.
После сварки четырех швов, полученных при одинаковой погонной энергии на различных рабочих дистанциях пушки и при постоянной степени фокусировки во всех случаях DIф
= 0, оказалось, что площади проплавления являются эквивалентными. Такой факт имеет большое практическое значение, так как позволяет сохранять неизменную форму проплавления на различных рабочих дистанциях электронной пушки, находящихся в расчетных (паспортных) пределах для данной электронно-оптической системы.
Влияние ускоряющего напряжения на геометрические характеристики проплавления
Экспериментальные данные (рис. 5.) показывают, что ускоряющее напряжение существенно влияет на глубину проплавления: с увеличением ускоряющего напряжения при прочих равных условиях глубина проплавления увеличивается.
Связано это с уменьшением рассеяния электронов пучка на атомах пара при повышении ускоряющего напряжения. Действительно, например, при U = 30 кВ коэффициент поглощения a = 2,4*106
/U2
= 2,67*103
см2
/г, а при U = 100 кВ a = 2,4*102
см2
/г, т.е. уменьшается более чем на порядок. Таким образом, повышение ускоряющего напряжения обеспечивает большую кинетическую энергию электронов и увеличивает пробег электронов в парах металла.
 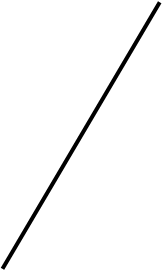       Н, мм
2
3
24
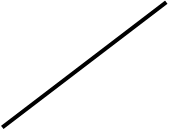   16
1
8
0 30 60 90 110 I, мА
Рис. 5. Зависимость глубины проплавления от тока луча у нержавеющей стали при V = 0,3 см/с: 1 – U = 30кВ, 2 – U = 60кВ, 3 – U = 100кВ
Эксперименты проводились на ЭЛУ при давлении в рабочей камере 5*10-5
– 1*10-4 мм рт. ст.
Аналогичным образом подтвердилась зависимость глубины проплавления от мощности сварки, в которой происходит одновременное увеличение обоих параметров.
При постоянной общей и удельной мощности и радиусе электронного луча rе
была получена экспериментальная зависимость глубины проплавления от скорости сварки и ускоряющего напряжения (см. рис. 6).
      Н, мм
60
 3
40
2
30
1
10
0 0,3 0,6 0,9 Vсв
, см/с
Рис. 6. Зависимость глубины проплавления от скорости сварки и ускоряющего напряжения: 1 – U = 30 кВ, 2 – U = 63 кВ, 3 – U = 100 кВ.
Все вышеперечисленные экспериментальные зависимости сохраняют свою суть при их теоретическом исследовании. На основании этих закономерностей можно написать зависимость глубины проплавления и ускоряющего напряжения:
Н @ . (см. рис. 7).
h/h (30 кВ), отн. ед.
2,0
1,6
1,4
1,0
             20 40 60 80 Uуск
, кВ
Рис. 7. Теоретическая зависимость глубины проплавления от ускоряющего напряжения при постоянных общей мощности и удельной мощности.
Исследование второстепенных параметров ЭЛС
Влияние параметров электронного луча на его диаметр
Экспериментально доказано, что с увеличением расстояния до объекта обработки диаметр электронного луча возрастает линейно. Это можно проследить по осциллограмме, представленной на рис. 8.
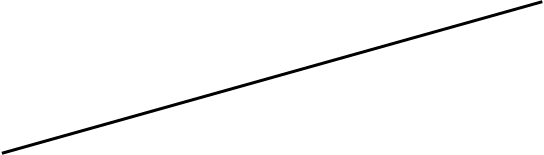 180
0,4
 140
0,2
100
0
-0,1 0,1
|
Iф
=f
(l
)
|
4
3
|
2
1
|
Рис. 8. Изменение диаметра луча d, тока фокусировки Iф
электронно – лучевой установки типа Луч-4 в зависимости от расстояния l
от объекта обработки для случая U = 30 кВ = const; 1-I = 35; 2–60; 3–80; 4–100 mA.
Пользуясь уравнением прямой, можно написать выражение для диаметра луча: d
=
d
0
+
kl
.
Коэффициенты d
0
иk
в этом уравнении можно определить, построив соответствующие зависимости d
0
= f
(I
), k
= f
(I
).
Зависимость диаметра луча от тока см. на рис. 9.
       мА
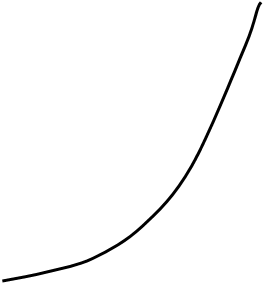 120
100
80
60
40
20
Рис. 9. Зависимость диаметра луча от тока при постоянном ускоряющем напряжении U = 30 кВ (для работы в режиме сварки)
Экспериментальная проверка по глубине проплавления некоторых металлов при воздействии электронного луча, формируемого электронно-оптической системой типа Луч-4 на разных расстояниях l
при одних и тех же параметрах луча, показывает, что глубина проплавления аналогично диаметру уменьшается с увеличением расстояния до объекта сварки.
Установлено, что распределение плотности тока по радиусу луча является Гауссовым:
j = jm
exp(-r2
/re
),
где r – текущее значение радиуса луча; re
– радиус луча на уровне jm
/e (нормальный радиус); jm
– максимальное значение плотности тока.
Глубина пробега электронов в твердом теле
Максимальную глубину пробега электронов d в твердом теле при ЭЛС чаще всего определяют по формуле Шонланда
d = 2,35*10-12
U2
/r.
Где U – ускоряющее напряжение, В; r – плотность, г/см3
; d – глубина проникновения, см.
Экспериментально и теоретически установлено, что максимум энерговыделения по глубине пробега находится под поверхностью. На рис. 10 представлена экспериментальная зависимость изменения глубины проникновения электронов в железо от ускоряющего напряжения.
d, м
        10-4
8
6
4
3
2
10-5
8
6
4
3
10-6
8
6
4
3
10-7
0 20 40 60 80 100 120 U, кВ
Рис. 10. Изменение глубины проникновения электронов в железо в зависимости от ускоряющего напряжения U
Таким образом, с увеличением ускоряющего напряжения (а следовательно, и глубины проникновения электронов) максимум температуры перемещается в глубь металла. Поэтому теоретически возможна ситуация, когда поверхность материала не успевает нагреться, хотя на глубине (в максимуме энерговыделения) достигается температура кипения.
На характер распределения температурного поля в зоне электронно-лучевого нагрева существенное влияние оказывает отношение диаметра луча к глубине пробега электронов. Установлено, что, например, обработка материала (плавление и выброс) эффективна только при условии d>2d, т.е. использование очень тонких пучков электронов затруднено.
Разряжение
Одним из параметров ЭЛС является степень разряжения (мм. рт. ст., Па). В большей степени этот параметр зависит от характеристик, обеспечиваемых в ЭЛУ.
ЭЛС осуществляют чаще всего вертикальным либо горизонтальным лучом в вакуумных камерах, размеры которых зависят от габаритов свариваемых изделий. Объем камер современных установок составляет от 0,1 (и менее) до сотен кубических метров. Камера с находящейся на ней (или в ней) электронной пушкой, формирующей электронный луч, может откачиваться как до высокого (» 10-3
Па), так и до низкого (» 1 – 10 Па) вакуума, но с отдельной откачкой объема электронной пушки до 10-3
Па.
Даже в низком вакууме » 1 Па содержание кислорода в 17 раз, а азота в 10 раз меньше, чем в особо чистом аргоне, поэтому при ЭЛС защита расплавленного металла очень эффективна. В вакууме электронный луч сохраняет свою удельную мощность, т. к. в нем не происходит рассеяние электронов вследствие отсутствия атомов и молекул атмосферы.
Частота автоколебаний
Для ЭЛС характерно, что при постоянном во времени потоке энергии возникают колебания физических параметров, характеризующих систему луч – вещество, а именно: потока пара, интенсивности светового излучения, эмиссии электронов и т.п. из зоны воздействия луча. Существует критическое значение потока энергии для возбуждения колебаний: если q2
> q*
2
,
то колебания возникают, если q2
< q*
2
, не возникают. Здесь q2
*
= Sкип
rd/hн
t*
, где Sкип
= r(сТкип
+ Lкип
) – теплосодержание кипящего металла, Дж/см3
; rd – массовая толщина слоя, г/см2
, hн
– эффективный КПД электронно-лучевого нагрева поверхности, t*
– характерное время, зависящее от теплофизических свойств металла.
При нагреве вещества постоянным во времени потоком энергии, который больше некоторого критического значения, отмечают существенные особенности в характере изменения температуры поверхности: она не стремится к постоянному значению, но колеблется относительно некоторого среднего значения. Эта закономерность обусловлена возникновением автоколебаний температуры и плотности пара в процессе нагрева.
Регистрация характеристик автоколебаний дает новые возможности для построения систем контроля и регулирования процесса ЭЛС.
В процессе ЭЛС луч надвигается на зону металла перед передней стенкой канала и проплавляет ее на глубину Н за время t, т.е. периодически с частотой f»Vсв
/d углубляется в металл (периодическое «строгание» передней стенки).
Таким образом, при формировании сварного шва наблюдаются два основных типа периодических процессов: периодическое испарение по мере углубления электронного луча в металл (с частотами порядка единиц и десятков килогерц) и колебания жидкого металла в сварочной ванне за счет периодического «строгания» передней стенки (с частотами порядка единиц и сотен герц). В литературе также отмечены плазменные колебания (с частотами порядка 106
Гц). Зависимость амплитуды колебаний от частоты для всех трех типов колебаний при ЭЛС показана на рисунке 11.
  А
жидкость
пар
плазма
101
103
105
107
f, Гц
Рис. 11. Зависимость амплитуды от частоты автоколебаний для различных процессов в канале при ЭЛС.
Специфические дефекты сварных швов при ЭЛС
Критическое изменение некоторых параметров при ЭЛС с несквозным проплавлением может привести к появлению дефектов в сварном соединении. Такими дефектами в основном являются: не заполненные металлом полости размером до 5 – 10 мм и длиной до 20 – 30 мм и периодическое несплавление корня шва.
Это объясняется тем, что давление пара в канале прямо пропорционально удельной мощности луча, а при одной удельной мощности можно получить разную глубину проплавления, т. к. чем меньше скорость, тем больше глубина проплавления. При правильном подборе удельной мощности, мощности и скорости сварки давление пара в канале отвечает условию
Р > (РG
+ Рs
) = rgH + s/r,
где Р – давление пара в канале; РG
– давление, обусловленное весом жидкого металла; Рs
– давление, обусловленное поверхностным натяжением жидкого металла.
В некоторых случаях, на выходе из канала это условие может не соблюдаться, т.е. возможно захлопывание канала жидким металлом и образование полости (рис. 12).
а б в
Рис. 12. Схема поведения канала при ЭЛС.
а – канал свободен от жидкости; б – отражение волны жидкого металла от хвостовой части ванны; в-захлопывание канала
Еще одним часто встречающимся специфическим дефектом при ЭЛС является отклонение канала проплавления от линии стыка вследствие отклонения луча магнитным полем при сварке сталей с остаточной намагниченностью. Для ликвидации этого дефекта прибегают к предварительному размагничиванию свариваемого изделия.
5. Выбор параметров режима сварки для изготовления изделия
Основные параметры ЭЛУ «Луч-4»
Для правильного подбора параметров режима сварки необходимо основываться на следующих условиях:
- – требуемые геометрические характеристики шва,
- – требуемое качество (прочностное и химическое) шва,
- – технологические возможности ЭЛУ.
Последний пункт является важным критерием для подбора параметров сварки, т. к. они должны входить в предел возможностей данной установки.
Рассмотрим основные параметры ЭЛС типа «Луч-4» в (табл. 5).
Табл. 5. Основные параметры ЭЛС типа «Луч-4».
№ п\п |
Наименование параметра |
Норма |
1. |
Максимальные размеры свариваемого изделия, мм.
Диаметр
Длина
|
900
840
|
2. |
Вакуум, мм рт. ст. |
5*10-5
|
3. |
Ускоряющее напряжение электронного луча, кВ. |
30
|
4. |
Ток электронного луча, мА. |
450 |
5. |
Ход электронно лучевой пушки, мм. Вдоль камеры
Поперек камеры
|
575
840
|
6. |
Давление охлаждающей воды,/см2
. |
2–3 |
7. |
Потребляемая электрическая мощность, кВт. |
8
|
8. |
Режим работы. |
Полуавтоматический |
9. |
Наблюдение за сваркой. |
Через иллюминатор |
10. |
Обслуживающий персонал, чел. |
2 |
Исходя из этих норм можно подбирать параметры, обеспечивающие выполнение первых двух пунктов условий (см. выше).
Подбор основных параметров ЭЛС для ЭЛУ «Луч-4»
Необходимые параметры для проведения процесса сварки:
1. Ускоряющее напряжение U
.
2. Скорость перемещения электронного луча V.
3. Ток луча I
.
4. Рабочее расстояние (расстояние от центра фокусирующей системы до поверхности свариваемой детали) l.
5. Ток фокусирующей системы Iф
.
Выбор ускоряющего напряжения
Экспериментальные данные (рис. 6,7.) показывают, что ускоряющее напряжение существенно влияет на глубину проплавления: с увеличением ускоряющего напряжения при прочих равных условиях глубина проплавления увеличивается. Это увеличение происходит пропорционально по квадратичному закону.
Для выбора ускоряющего напряжения для сварки диафрагменной лопатки необходимо знать требуемую глубину проплавления, которая данном соединении составляет 12 – 13 мм. При этом необходимо учитывать, что сварка будет производиться на установке «Луч-4», обладающей определенными рамками по выбору данного параметра режима.
Основываясь на этих данных и используя графическую зависимость глубины проплавления от ускоряющего напряжения при постоянных общей мощности и удельной мощности выбираем Uуск = 30 кВ.
Выбор скорости перемещения электронного луча
Для определения скорости перемещения электронного луча воспользуемся экспериментальной зависимостью глубины проплавления от скорости сварки и ускоряющего напряжения (см. рис. 6).
Из предыдущего пункта известно, что ускоряющее напряжение равно 30 кВ. Следовательно, можно определить скорость сварки (рис. 13).
Н, мм      
30
  10
0 0,3 0,6 0,9 Vсв
, см/с
Рис. 13. Зависимость глубины проплавления от скорости сварки и ускоряющего напряжения U = 30 кВ.
Таким образом, принимаем Vсв = 0,3 см/с или равным 20 см/мин.
Выбор тока луча
В исследовательской части работы приведена зависимость величины сварочного тока от толщины соединяемых деталей из стали 12Х13 при трех разных скоростях сварки: 1 – V = 10 см/мин, 2 – V = 20 см/мин, 3 – V = 30 см/мин (рис. 3). В нашем случае, для сварки диафрагменной лопатки, используется V = 20 см/мин (рис. 14). Другие параметры сварки при этом остаются постоянными (ток фокусировки – Iф, ускоряющее напряжение – Uуск, и рабочая длина).
По результатам выбора принимаем Iсв = 100 А. Возможности установки «Луч – 4» позволяют получить такой ток, что не противоречит
3-ему условию по подбору параметров.
Увеличить вероятность правильного выбора сварочного тока можно путем использования еще одной зависимости (см. рис. 5). Как и предыдущая, она показывает зависимость величины сварочного тока от толщины соединяемых деталей из нержавеющей стали, но при постоянном значении напряжения и скорости сварки (рис. 15).
Все эти зависимости справедливы при давлении в рабочей камере 5*10-5 мм рт. ст. Следует помнить, что степень разряжения влияет на рассеяние луча, а значит и на геометрические характеристики шва.
Таким образом, подтвердилась зависимость глубины проплавления от мощности сварки, в которой происходит одновременное увеличение обоих параметров.
Выбор рабочего расстояния
Рабочее расстояние – расстояние от центра фокусирующей системы до поверхности свариваемой детали или просто – расстояние пушка – деталь.
Заглубление в материал фокуса электронного луча может существенно увеличить глубину отверстия. Аналогичный эффект наблюдается и при электронно-лучевой сварке с кинжальным проплавлением, а при сварке диафрагменной лопатки оно таким и является.
При одинаковой погонной энергии на различных рабочих дистанциях пушки и при постоянной степени фокусировки DIф
= 0 площади проплавления являются эквивалентными. Таким образом сохраняется неизменность формы проплавления на различных рабочих дистанциях электронной пушки, находящихся в расчетных (паспортных) пределах для данной электронно-оптической системы.
Принимаем рабочее расстояние от пушки до изделия равным 100 мм.
Выбор
тока фокусирующей системы Iф
Для нахождения численного значения тока фокусирующей системы Iф,
рассмотрим графическую зависимость на рис. 16.
Iф
, мА
0 25 50 75 100 125 150 l
, мм
Рис. 16. Изменение тока фокусировки Iф
электроннолучевой установки типа Луч-4 в зависимости от расстояния l
от объекта обработки для случая U = 30 кВ = const;
Зная рабочее расстояния, можно найти ток фокусировки. Т.о. Iф
= 100 мА.
Итоги выбора параметров
В результате подбора основных параметров получены следующие численные значения:
Uуск = 30 кВ,
Iсв = 100 мА,
Iф
= 100 мА,
L
= 100 мм,
Vсв = 20 см/мин,
Частота колебаний – 300 Гц.
Перед внедрением их в производство (перед занесением в маршрутную карту) следует провести сварку образцов – свидетелей с соответствующими испытаниями. После этого возможна их корректировка, целью которой должно быть улучшение качества сварного соединения.
6. Характеристика источника питания установки аргонодуговой сварки
Выпрямитель универсальный для сварки неплавящимся электродом модели ВСВУ-400 предназначен для питания установок автоматической, полуавтоматической и ручной электродуговой сварки обычной и сжатой, непрерывной и импульсной (пульсирующей) дугой, жаропрочных, нержавеющих сталей и титановых сплавов в аргоне.
Основные параметры
.
1. Номинальный сварочный ток при ПВ = 60% и длительности цикла 60 мин, Iном = 400 А.
2. Диапазон регулирования Iсв при непрерывной сварке, ток импульсный – при импульсной сварке, Iсв = 5+10% – 400+10%.
3. Диапазон регулирования Iдежурного, Iдеж = 5+10% – 100+10%.
4. Напряжение холостого хода, Uх.х.= не более 100 В.
5. Номинальное рабочее напряжение, Uном= 30 В.
6. Потребляемая мощность, Р – не более 21 кВА.
7. Номинальное напряжение трехфазной питающей сети частотой 50 Гц, Uном= 380+10%.
8. ВАХ источника питания – падающая.
7. Технологический процесс. Изделие – лопатка диафрагменная
0000 Заготовительная.
Доставить на сварочный участок поковки.
0005 Подготовительная.
Места сварки и околошовную зону на расстоянии 20 мм протереть бязью, смоченной в спирте (ацетоне) и отжатой.
0010 Контрольная.
Визуальный технический контроль качества обезжиривания.
0015 Сборочно-сварочная.
Установить в сборочное приспособление лопатку (поз. 1) и прижать вставку (поз. 2) к лопатке эксцентриковым зажимом. Зазор между вставкой и лопаткой не более 0,2 мм. Вставка смещена относительно лопатки на расстояние 10 мм по узкой стороне (см. чертеж).
Использовать источник питания – выпрямитель ВСВУ-400, редуктор АР-40, горелку РГА-400, ротаметр РС-3. Прихватить детали поз. 1 и поз. 2 в местах стыка ручной аргоно – дуговой сваркой: длина прихваток – L=10 мм, количество прихваток – 6 шт. Прихватки выполнять от центра к краям. Iсв=70 А, Uсв=8–12 В, Св – 08Г2С Æ2 мм, прямая полярность, расход газа Q=6–8 л/мин.
0020 Маркирование.
Маркирование ударом (по ТТ чертежа).
Использовать набор клейм, молоток слесарный.
0025 Контрольная.
Технический контроль сборки под ЭЛС. Использовать набор щупов №2, измерительную линейку. Проверить зазор между деталью поз. 1 и поз. 2; в профильной полости зазор более 0,1 мм не допускается, зазор в стыке не более 0,2 мм.
Проверить неплоскостность вставки, допустимая неплоскостность 0,2 мм.
Внимание!
Собранная партия лопаток не должна пролеживать до сварки более 3-х дней. В процессе сварки лопатки должны быть укрыты полиэтиленовой пленкой или бумагой.
0030 Подготовительная.
Произвести замеры силового магнитного поля лопатки, собранной под ЭЛС. Прибор FSM – 1.
Произвести размагничивание лопатки перед ЭЛС. Допустимая намагниченность составляет 1–2 А/см. Использовать стенд для размагничивания 0861 – 5467.
Поместить 7 лопаток в приспособление, предварительно удалив прижимную планку.
0035 Сварочная.
Электронно-лучевая сварка на ЭЛУ «Луч – 4». Заварить лопатку электронно-лучевой сваркой с параметрами:
Iсв=100 мА,
Iф =100 мА,
Vсв=20 см/мин,
Uуск=30 кВ,
Частота колебаний 300 Гц,
Lраб=100 мм.
Сварку начинать с широкой части торца. Одновременная загрузка в камеру – 7 лопаток (см. приспособление). На концах вставок допускается непровар 5 мм, образованный резким уменьшением сварочного тока. Выполнение разглаживающего прохода не допускается.
0040 Термическая.
Отпуск. Снятие сварочных напряжений.
   Т, 0
С 700
 t, с
Использовать электрическую печь KS-1300.
0045 Слесарная.
Зачистить усиление сварного шва после ЭЛС. Использовать шлифовальную машинку ИП 2009-п1, металлическую щетку. Выступание сварного шва над поверхностью планки не допускается.
0050 Правка.
Использовать гидропресс.
1. Вырезать прокладки 40х30 мм, d=1,5 мм, Ст10 (для 4-х лопаток) 3 штуки.
Установить лопатки на вставку п. 2. Замерить неплоскостность.
2. Установить с подгонкой по месту под лопатку прокладки. Произвести рихтовку лопатки для получения неплоскостности вставки до 0,7 мм согласно чертежу. Рихтовать каждую лопатку 3 раза.
3. После рихтовки 4-х лопаток повторно вырезать прокладки и произвести рихтовку.
0055 Контрольная.
Технический контроль геометрических размеров изделия. Набор щупов №2.
Установить лопатку на разметочную плиту. Положить на нее мерительную линейку. Проверить неплоскостность. Допустимая неплоскостность не более 0,7 мм.
0060 Подготовительная.
Подготовить поверхность подреза для сварки. Использовать пневмо – мех. щетку и машину шлиф ИП 2009-п1. Зачистить дефектную поверхность до чистого металла: Lшва=0,3 м, глубина 1 мм или отдельные поры в кол-ве 6 штук длиной 2,5 мм.
Обезжирить поверхность, обработав ее бязью, смоченной в спирте (ацетоне) и отжатой.
0065 Сварочная.
Подварить оставшиеся подрезы после ЭЛС. Использовать источник питания – выпрямитель ВСВУ-400, редуктор АР-40, горелку РГА-400, ротаметр РС-3. Осуществлять ручной сваркой неплавящимся электродом в среде аргона. Iсв=100 А, Uсв=10–14 В, Св – 04Х19Н11М3 Æ2 мм, прямая полярность, расход газа Q=6–8 л/мин. При сварке не допускать перегрева металла.
0070 Слесарная.
Зачистить усиление сварного шва после ручной сварки неплавящимся электродом в среде аргона. Использовать шлифовальную машинку ИП 2009-п1, металлическую щетку. Выступание сварного шва над поверхностью лопатки не допускается.
0075 Контрольная.
1. Внешний осмотр – 100%.
2. Ультразвуковая дефектоскопия – 100%.
Для ультразвукового контроля использовать дефектоскопы УД-2 или ДУК-13ИМ.
Заключение
Для изготовления диафрагменной лопатки паровой турбины выбрана высокохромистая жаропрочная сталь мартенситно-ферритного класса сталь 12Х13. Данный материал обеспечивает высокую технологичность изделия, по сравнению с другими материалами. Выбор производился с учетом экономических и технологических (химическая и механическая характеристики) факторов оценки. Учитывая экономический фактор данной задачи, сталь 12Х13 является одной из самых дешевых в своем классе высокохромистых сталей, т. к. чем выше степень легирования, тем выше цена стали и степень ее распространенности в промышленности.
Для сварки диафрагменной лопатки из стали 12Х13 был выбран способ с использованием электронного луча. Это объясняется рядом достоинств ЭЛС при сварке этих сталей:
1. Минимальная деформация свариваемого изделия, т. к. поток электронов внедряется в свариваемое изделие на всю глубину проплавления, что обеспечивает получение минимальной металлоемкости сварочной ванны.
2. Высокие физико-химические характеристики сварного соединения непосредственно после сварки позволяют исключить последующую механическую обработку.
3. Относительно высокая погонная энергия при сильной степени ее концентрации, т.е. энергия, вводимая в участок сварного соединения за определенный промежуток времени. При этом достигается высокая скорость кристаллизации металла сварного шва и минимальное термическое воздействие сварочного нагрева на основной металл в ОШЗ (локальность сварочного нагрева).
Все эти положительные стороны ЭЛС с сочетанием правильно подобранных параметров режима сварки помогают достичь наилучшего качества сварного соединения.
Выбор параметров режима ЭЛС производился на основе детального теоретического и экспериментального анализа каждого из них. Выявление закономерностей влияния некоторых из параметров на геометрические характеристики сварного соединения помогло максимально исключить возможность появления в нем дефектов.
Литература
1. Волченко В.Н. Справочник. Сварка и свариваемые материалы, т. 2. – М.: МГТУ им. Н.Э. Баумана, 1998.
2. Арзамасов В.И., Мухин Г.Г. и др. Материаловедение. – М.: МГТУ им. Н.Э. Баумана, 2001.
3. Рыкалин Н.Н., Углов А.А., Зуев И.В. Справочник. Электроннолучевая обработка материалов. – М.: Машиностроение, 1981.
4. Акулов А.И., Бельчук Г.А. Технология и оборудование сварки плавлением. – М.: Машиностроение, 1977.
5. Башенко В.В. Электронно-лучевые установки. – М.: Машиностроение, 1972.
6. Шиллер З., Гайзиг У., Панцер З. Электроннолучевая технология. – М.: Энергия, 1980.
7. Лившиц Л.С. Металловедение. – М.: Машиностроение, 1979.
8. Степанов В.В. Справочник сварщика. – М.: Машиностроение, 1982.
9. Журавлев В.Н., Николаева О.И. Справочник. Машиностроительные стали. – М.: Машиностроение, 1992.
|