Министерство сельского хозяйства РФ
Федеральное государственное образовательное учреждение
высшего профессионального образования
Алтайский государственный аграрный университет
Институт техники и агроинженерных исследований
Кафедра технологии конструкционных материалов и ремонта машин
Курсовая работа по метрологии, стандартизации и сертификации.
ОПРЕДЕЛЕНИЕ ПАРАМЕТРОВ ОСНОВНЫХ ТИПОВЫХ СОЕДИНЕНИЙ
Содержание
Введение
Нормативные ссылки
1. Допуски и посадки гладких сопряжений
2. Допуски и посадки резьбовых сопряжений
3. Допуски и посадки подшипников качения
4. Допуски и посадки шпоночных соединений
5. Допуски и посадки шлицевых соединений
6. Расчёт размерной цепи
Список используемой литературы
Введение
Для повышения технического уровня и качества продукции, роста производительности труда, экономии трудовых и материальных ресурсов необходимо во всех отраслях народного хозяйства развивать и совершенствовать системы стандартизации на основе внедрения достижений науки, техники и практического опыта.
Необходимо усилить действенное и активное влияние стандартов на выпуск продукции, соответствующей по своим технико-экономическим показателям высшему мировому уровню.
Сегодня, когда для производства одной машины необходима кооперация между сотнями предприятий различных отраслей промышленности, вопросы качества продукции невозможно решить без расширения работ по совершенствованию системы взаимозаменяемости, метрологического обеспечения, улучшения методов и средств контроля продукции.
Цель – выработка у будущих инженеров знаний и практических навыков использования и соблюдения требований комплексных систем общетехнических стандартов, выполнения точных расчётов и метрологического обеспечения при изготовлении, эксплуатации и ремонте сельскохозяйственной техники.
1. Допуски и посадки гладких сопряжений
Диаметр сопряжения 6 мм
Сопряжение 1: ø6
H
9/
d
9
Сопряжение 2: ø6
S
7/
h
6
1.1 Расчёт сопряжения 1:
H
9/
d
9
1.1.1 Посадка выполнена в системе отверстия. Посадка с зазором.
Отверстие ø6
H
9
[1]:
EI
= 0 мкм;
ES
=
EI
+
T
;
(1)
где ES
(
es
)
– верхнее отклонение отверстия (вала), мкм;
EI
(
ei
)
– нижнее отклонение отверстия (вала), мкм;
Т
– допуск, мкм;
ES
=
0+30 = +30 мкм
Вал ø6
d
9
[1]:
es
= -30 мкм;
ei
=
es
–
Т
;
(2)
e
i
= -30–30 = -60 мкм
1.1.2 Находим предельные размеры отверстия и вала
D
нб
= D+ES
(3)
D
нм
= D+EI.
(4)
где D
(
d
)
– номинальный диаметр отверстия, мм;
D
нб
(
D
нм
)
– наибольший(наименьший) диаметр отверстия, мм.
D
нб
= 6+0,03 = 6,03 мм;
D
нм
= 6+0 = 6 мм.
d
нб =
d
+
es
(5)
d
нм =
d
+
ei
(6)
где d
нб
(
d
нм
)
– наибольший(наименьший) диаметр вала, мм;
d
– номинальный диаметр вала, мм;
d
нб
= 6+(-0,03)=5,97 мм;
d
нм
= 6+(-0,06) = 5,94 мм.
1.1.3 Определяем величину допусков каждой детали и величину допуска посадки
TD
= ES-EI
(7)
Td = es – ei
(8)
где TD
(Td
)
– допуск отверстия (вала), мкм;
TD
= 30–0 = 30 мкм;
Td
=-30 – (-60) = 30 мкм.
T
∆ =
TD
+
Td
(9)
где T
∆
– допуск посадки, мкм;
T
∆
= 30+30 = 60 мкм.
1.1.4 Вычисляем величину наибольших зазоров и натягов
S
нб =
ES
-
ei
(10)
где S
нб
(S
нм)
– наибольший (наименьший) зазор, мкм;
S
нб
= 30 – (-60) = 90 мкм.
S
нм =
EI
-
es
(11)
S
нм
= 0 – (-30) = 30 мкм.
1.1.5 Находим чистоту обработки сопрягаемых поверхностей [1]:
R
a
D
= 0,05*
TD
(12)
где R
a
D
(
Rad
)
– шероховатость отверстия (вала);
R
a
D
= 0,05*30 = 1,5 мкм.
Принимаем R
a
D
=1,25 мкм.
Rad
= 0,05*
Td
(13)
Rad
= 0,05*30 = 1,5 мкм.
Принимаем Rad
= 1,25 мкм
1.1.6 Устанавливаем предельную величину погрешности формы [1]:
Т/0/
= 0,3*Т
D
(14)
Т/0/
= 0,3*Т
d
(15)
где Т/0/
- допуск цилиндричности, мкм.
Отверстие ø6
H
9
:
Т/0/
=
0,3*30=9 мкм.
Принимаем Т/0/ =
6 мкм.
Вал ø6
d
9:
Т/0/
=
0,3*30=9 мкм.
Принимаем Т/0/ =
6 мкм.
1.1.7 Строим схему расположения полей допусков сопряжения в масштабе 1 мкм – 1 мм. (рис. 1)

Рисунок 1. Схема расположения полей допусков сопряжения Æ6
H
9/
d
9
1.1.8 Вычерчиваем эскиз сопряжения и деталей в отдельности с обозначением посадок, отклонений, чистоты обработки поверхностей (черт 1)
1.2 Расчёт сопряжения ø6
S
7/
h
6:
1.2.1 Посадка выполнена в системе вала. Посадка с натягом
Отверстие ø6
S
7
ES
= -15 мкм
EI
=
ES
–
T
;
(16)
По формуле (16):
EI
=
-15–12=-27 мкм
Вал ø6
h
6:
es
= 0 мкм
Находим нижнее отклонение вала по формуле (2):
e
i
=
0–8 = -8 мкм.
1.2.2 По формулам (3), (4), (5) и(6) находим предельные размеры отверстия и вала:
D
нб =
6+(-0,015) = 5.985 мм;
D
нм = 6
+(-0,027) = 5,973 мм;
d
нб =
6+0 = 6 мм;
d
нм =
6+(-0,008) = 5.992 мм.
1.2.3 По формулам (7), (8) и(9) определяем величину допусков каждой детали и величину допуска посадки
T
D
=
-15 – (-27) = 12 мкм;
Td
=
0 – (-8) = 8 мкм;
T
∆ = 12
+8= 20 мкм.
1.2.4 Вычисляем величину наибольших зазоров
и натягов
Вычисляем величину наибольшего натяга, мкм:
N
нб =
es
–
EI
;
(17)
где N
нб
–
наибольший натяг мкм,
N
нб
= 0 – (-27) =27 мкм.
Вычисляем величину наименьшего натяга, мкм:
N
нм =
ei
–
ES
;
(18)
где N
нм –
наименьший натяг мкм,
N
нм =
-8 – (-15) = 7 мкм
1.2.5 По формулам (12) и (13) находим чистоту обработки сопрягаемых поверхностей [1]:
Ra
D
=
0,05*12 = 0,6 мкм;
Rad
=
0,05*8 = 0,4 мкм.
Принимаем Rad
= 0,4
; Ra
D
= 0,5 мкм
.
1.2.6 По формулам (14), (15) устанавливаем предельную величину погрешности формы [1]:
Отверстие ø6
S
7
:
Т/0/
=
0,3*12=3,6 мкм.
Принимаем Т/0/ =
2,5 мкм
Вал ø6
h
6:
Т/0/
=
0,3*8=2,4 мкм.
Принимаем Т/0/ =
1,6 мкм
1.2.7 Строим схему расположения полей допусков данного сопряжения в масштабе 1 мкм-1 мм (рис 2.).
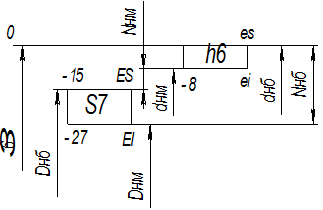
Рисунок 2. Схема расположения полей допусков сопряжения Æ6
S
7/
h
6
1.2.8 Вычерчиваем эскиз сопряжения и деталей в отдельности с обозначением посадок, отклонений, чистоты обработки поверхностей (черт 2)
1.3 Выбираем средства измерения
1.3.1 По формулам (7), (8) определяем допуски деталей, мкм [1]
Отверстие ø6
H
9
TD
= 30–0 = 30 мкм.
Вал ø6
d
9
Td
=-30 – (-60) = 30 мкм.
Отверстие ø6
S
7
T
D
=
-15 – (-27) = 12 мкм
Вал ø6
h
6
Td
=
0 – (-8) = 8 мкм
1.3.2 Выбираем допустимую погрешность измерения, мкм:
Отверстие ø6
H
9 ∆изм =
7; Вал ø6
d
9 ∆изм =
7; Отверстие ø6
S
7 ∆изм =
3,5;Вал ø6
h
6 ∆изм =
2,5.
1.3.3 Определяем средние размеры деталей
d
ср(
D
ср
) = (
d
нб(
D
нб
)+
d
нм(
D
нм
))/2
(19)
Отверстие ø6
H
9
D
ср=
(6,03+6)/2=6,015 мм
Вал ø6
d
9
d
ср=
(5,97+5,94)/2=5,955 мм
Отверстие ø6
S
7
D
ср=
(5,985+5,973)/2=5,979 мм
Вал ø6
h
6
d
ср=
(6+5,992)/2=5,996 мм
1.3.4 Для валов выбираем микрометр рычажный
с ценой деления 0,002 мм предел измерения (0–25) ∆
lim
=
4 мкм. Для отверстий выбираем нутромер индикаторный с ценой деления головки 0,001 мм, в границах шкалы в 0,1 мм: ∆
lim
=
3,5 мкм
1.3.5 Рассчитываем величину относительной погрешности
A
мет(
σ
)=(σ/
T
)*100
(20)
где σ – среднее квадратическое отклонение погрешности измерения.
σ =∆изм/
2 (21)
Отверстие ø6
H
9
A
мет(
σ
)=((7/2)/30)*100=12
Так закон распределения размеров деталей в партии неизвестен, принимаем средние значения. Устанавливаем, что процент деталей, неправильно принятых (брак в годных) m=3,92%; неверно забракованных (годные в браке) n=5,6%; величина выхода размеров неправильно принятых деталей за границы поля допуска C/T=0,17.
Вал ø6
d
9
A
мет(
σ
)=((7/2)/30)*100=12
m=3,92%; n=5,6%; C/T=0,17.
Отверстие ø6
S
7
A
мет(
σ
)=((3,5/2)/12)*100=14,6
m=4,74%; n=7,32%; C/T=0,23.
Вал ø6
h
6
A
мет(
σ
)=((2,5/2)/8)*100=15,6
m=5,07%; n=7,82%; C/T=0,24.
1.3.6 Рассчитываем размер блока концевых мер для настройки средства измерения
Прибор будем настраивать по размеру d
ср(
D
ср
).
Отверстие ø6
H
9
l
1
=1,005; l
2
=1,01; l
3
=4;
Вал ø6
d
9
l
1
=1,005; l
2
=1,45; l
3
=3,5;
Отверстие ø6
S
7
l
1
=1,079; l
2
=1,9; l
3
=3;
Вал ø6
h
6
l
1
=1,996; l
2
=4.
1.3.7 Определяем требуемый класс точности мер
[Δ
i
]=0,75*∆изм/√К
(22)
где Δ
i
– допустимая погрешность i‑й составляющей дополнительной погрешности;
К – число составляющих причин, образующих дополнительную погрешность (К=9).
Отверстие ø6
H
9
[Δ
i
]=
0,75*7/√9=1,75 мкм
Вал ø6
d
9
[Δ
i
]=
0,75*7/√9=1,75 мкм
Отверстие ø6
S
7
[Δ
i
]=
0,75*3,5/√9=0,88 мкм
Вал ø6
h
6
[Δ
i
]=
0,75*2,5/√9=0,62 мкм
Устанавливаем класс концевых мер по условию:
Δ
i
ф
≤ [Δ
i
]
(23)
где Δ
i
ф
–
фактическая погрешность блока плиток.
(24)
Отверстие ø6
H
9
Проверяем меры третьего класса их погрешности, мкм: Δ
1
=0,8; Δ
2
=0,8; Δ
3
=0,8
Так как 1,38 ≤ 1,75; то для настройки выбранного средства измерения используем набор мер третьего класса.
Вал ø6
d
9
Проверяем меры третьего класса их погрешности, мкм: Δ
1
=0,8; Δ
2
=0,8; Δ
3
=0,8

Так как 1,38 ≤ 1,75; то для настройки выбранного средства измерения используем набор мер третьего класса.
Отверстие ø6
S
7
Проверяем меры третьего класса их погрешности, мкм: Δ
1
=0,8; Δ
2
=0,8; Δ
3
=0,8

Так как 1,38≥0,88; то проверяем меры второго класса их погрешности, мкм: Δ
1
=0,35; Δ
2
=0,35; Δ
3
=0,35

Так как 0,61 ≤ 0,88; то для настройки выбранного средства измерения используем набор мер второго класса.
Вал ø6
h
6
Проверяем меры третьего класса их погрешности, мкм: Δ
1
=0,8; Δ
2
=0,8

Так как 1,13≥0,62; то проверяем меры второго класса их погрешности, мкм: Δ
1
=0,35; Δ
2
=0,35.

Так как 0,49 ≤ 0,62; то для настройки выбранного средства измерения используем набор мер второго класса.
2. Допуски и посадки резьбовых сопряжений
2.1 Расшифровываем условное обозначение резьбового соединения
M
20–6
H
/6
h
: резьба метрическая с крупным шагом Р
=2,5 мм, угол профиля 60º
, с наружным диаметром d(D)=20
мм; выполнена в комбинированной системе, посадка с зазором. Гайка
M
20–6
H
:
точность исполнения наружного диаметра не установлена; среднего диаметра – нормирована полем допуска 6
H
;
внутреннего – степенью точности 6.
Болт
M
20–6
h
: точность изготовления внутреннего диаметра не регламентирована; среднего диаметра – задана полем допуска 6
h
; наружного – степенью точности 6
. [3]
2.2 Выписываем отклонения диаметров резьбового профиля гайки и болта (ГОСТ 25347 – 82), (таб. 1). [1]
Таблица 1. Параметры резьбового профиля, мкм
Наименование |
Отклонение |
Допуск |
детали |
диаметра |
основное |
второе |
Гайка |
Наружный, D
|
Е
I
=
0
|
He стандартизированы
|
Средний, D
2
|
Е
I
2
=
0
|
E
S
2
=+
224
|
TD2
=
224
|
Внутренний,D
1
|
E
I
1
=
0
|
E
S
1
=+
450
|
TD1
=
450
|
Болт |
Наружный,d
|
es =
0
|
ei=-
335
|
Td
=
335
|
Средний,d
2
|
es2
=
0
|
ei2
=-
170
|
Td2
=
170
|
Внутренний,
d
1
|
es1
=
0
|
He стандартизированы
|
2.3 Строим схему расположения полей допусков параметров резьбового профиля в масштабе: 1: 100 (рис 3)
2.4 Выполняем чертежи деталей и соединения (черт. 3)
2.5 Подбираем средство измерения болта [1]
2.5.1 Определяем допуск детали
T =
170 мкм.
2.5.2 Выбираем допустимую погрешность измерения
D
изм
=
30 мкм.
2.5.3 Выбираем средство измерения – резьбовой калибр, или резьбовой шаблон [4]
Резьбовой шаблон представляют собой собранные в наборы резьбовые пластинки с зубьями стандартных метрических профилей резьбы с шагами от 0,4 до 6 мм [4].
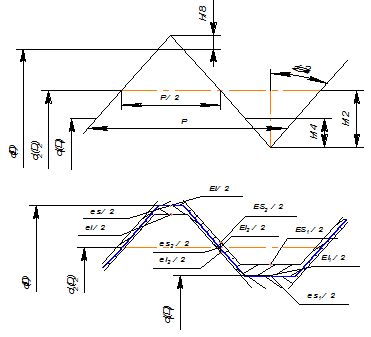
Рисунок 3. Схема расположения полей допусков параметров резьбового профиля
3. Допуски и посадки подшипников качения
Подшипник номер 32206
, нагружение внутреннего кольца колебательное.
3.1 Расшифровываем условное обозначение
0032206
подшипника качения. Порядок счета цифр и значение мест в условном обозначении по ГОСТ 3189 – 75 справа налево
3.1.1 ПоГОСТ 3189 – 75 устанавливаем тип и конструктивную разновидность подшипника: 32206 – роликовый радиальный с короткими цилиндрическими роликами, без бортов на внутреннем кольце. Изготовлен по ГОСТ 8338 – 75.
3.1.2 Окончательно устанавливаем значение цифр в условном обозначении (номере) подшипника качения (ГОСТ 3189 – 89)
«6»
и «0»
(первое и второе места) – обозначение посадочного размера внутреннего кольца –
– d = 30 мм
;
«2»
(третье место) – серия подшипника по диаметру – легкая серия диаметров – 2;
«2»
(четвертое место) – тип подшипника – роликовый радиальный с короткими цилиндрическими роликами;
«3»
и «0»
(пятое и шестое место) – конструктивные особенности – без бортов на внутреннем кольце;
«0»
(седьмое место) – дополнительная маркировка, класс точности подшипника – 0
3.2 Определяем номинальные размеры подшипника: [2]
Внутренний диаметр d
= 30 мм
;
Наружный диаметр D
= 72 мм
;
Ширина подшипника B
= 19 мм
;
Радиус закругления кромок r
= 2 мм
.
3.3 Выбираем посадки сопряжений с учетом нагружения кольца по ГОСТ 3325–85 (нагружение колебательное):
вал – внутреннее кольцо: L
0/
js
6
.
корпус – наружное кольцо: JS
7/
l
0
.
3.4. Выписываем предельные отклонения колец подшипника и посадочных мест вала и корпуса: [1]
Вал d
30
js
6
:
es
= +6,5
мкм;
ei
= -6,5
мкм.
Корпус D
72
JS
7
:
ES
= +15
мкм;
EI
= -15
мкм.
Внутреннее кольцо ∆
dmp
:
ES
= 0
мкм;
EI
= -10
мкм.
Наружное кольцо ∆
Dmp
:
es
= 0 мкм;
ei
= -13
мкм.
3.5 Строим схему расположения полей допусков деталей сопряжения «кольцо подшипника – деталь» в масштабе 1 мкм – 1 мм (рис. 4).
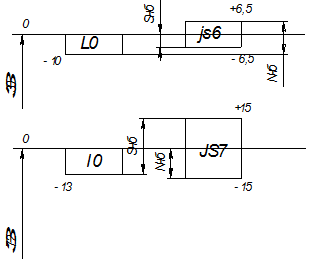
Рисунок 4. Схема расположения полей допусков деталей сопряжения «кольцо подшипника – деталь».
3.6 По формулам (8) и (17) вычисляем значения предельных зазоров – натягов в сопряжениях
Внутреннее кольцо – вал: ø30
L
0/
js
6
S
нб
= 0 – (-6,5) = 6,5 мкм;
N
нб
= 6,5 – (-10) = 16,5 мкм.
Наружное кольцо – корпус: ø72
JS
7/
l
0
S
нб
= 15 – (-13) = 28
мкм;
N
нб
= 0 – (-15) = 15
мкм.
3.7 Подбираем величину шероховатости посадочных поверхностей, устанавливаем допускаемые отклонения круглости и цилиндричности посадочных поверхностей и биение заплечников. [1]
Вал ø30
js
6
:
Шероховатость – 1,25 мкм;
Опорные торцы заплечиков – Ra
=
2,5 мкм
Допуск круглости – 3,5 мкм;
Допуск профиля продольного сечения – 3,5 мкм;
Допуск торцевого биения – 21 мкм.
Корпус ø72
JS
7
:
Шероховатость – 1,25 мкм;
Опорные торцы заплечиков – Ra
=
2,5 мкм
Допуск круглости – 7,5 мкм;
Допуск профиля продольного сечения – 7,5 мкм;
Допуск торцевого биения – 46 мкм.
3.8 Вычерчиваем эскизы узла в сборе, вала и корпуса с обозначением посадок, предельных отклонений, чистоты обработки и отклонений геометрической формы в соответствии с ЕСКД (черт. 4).
3.9 Охарактеризовываем вид нагружения колец подшипника: [1]
Колебательное нагружение – поверхность беговой дорожки кольца воспринимает равнодействующею двух сил, действующих на подшипник качения, постоянной по направлению и вращающейся.
4 Допуски и посадки шпоночных соединений
В соединении Æ
66
использована призматическая шпонка. Применяется в индивидуальном производстве.
4.1 Принимаем шпонку с размерами
: ширина b=
20 мм; высота h=
18 мм;
длина l
=
70 мм. Условное обозначение шпонки: Шпонка
20
´
18
´
70
ГОСТ 8788–68
4.2 Устанавливаем поля допусков деталей шпоночного соединения на элемент «
b
» [4] (таб. 2)
Таблица 2. Рекомендуемые поля допусков в сопряжении «шпонка-паз детали» по «b».
Вид сопряжения |
Поле допуска |
Ширина шпонки |
Ширина паза вала |
Ширина
паза втулки
|
Плотное
(индивидуальное производство)
|
h9
|
P
9
|
P9
|
4.3 Выписываем размеры остальных элементов шпоночного соединения (табл. 3)
4.4 Строим схему расположения полей допусков элементов шпоночного соединения по «
b
» в масштабе: в 1 мм – 2 мкм (Рисунок 5).
.
Рисунок 5. Схема расположения полей допусков элементов шпоночного соединения по «b»
4.5 Выполняем чертежи деталей шпоночного соединения (черт 5)
4.6 Подбираем средство измерения паза вала [1].
4.6.1 Определяем допуск детали
T
=100 мкм
4.6.2 Выбираем допустимую погрешность измерения
D
изм
=
25 мкм
4.6.3 Определяем размеры детали
b
нб
=
b
+es,
(25)
где b
нб
-наибольшая ширина паза вала, мм;
b
– ширина паза вала, мм;
b
нб
=20+(-0,022)=19,978 мм.
b
нм
=
b
+e
i
,
(26)
где b
нм
– наименьшая ширина паза вала, мм;
b
нм
=20+(-0,074)=19,926 мм.
b
ср
=(
b
нб
+
b
нм
)/2,
(27)
где b
ср
- средняя ширина паза вала, мм;
b
ср
=(19,978+19,926)/2=19,952 мм.
4.6.4 Выбираем нутромер индикаторный с ценой деления головки 0.001 мм настройка по концевым мерам 1-го класса с боковиками: D
lim=
3.5 мкм.
4.7 Подбираем средство измерения паза втулки.
4.7.1 Определяем допуск детали: T=
100 мкм.
4.7.2 Выбираем допустимую погрешность измерения:
D
изм
=
25 мкм
4.7.3 Определяем размеры детали по формулам (25), (26), (27):
b
нб
=20+(-0,022)= 19,978 мм;
b
нм
=20+(-0.074)= 19,926 мм;.
b
ср
=(19,978+19,926)/2=19,952 мм.
4.7.4 Выбираем нутромер индикаторный
с ценой деления 0.001 мм настройка по концевым мерам 1=го класса [1]: D
lim=
3.5 мкм.
Таблица 3. Размерная характеристика элементов деталей шпоночного соединения, мкм
Параметры элементов шпоночного соединения |
Шпонка |
Паз вала |
Паз втулки |
b |
h |
l |
b |
t1
|
l |
b |
D+t2
|
l |
Размер, мм |
20 |
18 |
70 |
20 |
11 |
70 |
20 |
 |
– |
Поле допуска |
h9 |
h11 |
h14 |
P9
|
– |
H15 |
P9 |
– |
– |
Условное обозначение |
20h9
|
18h11
|
70h14 |
20P9
|
 |
70H15 |
20P9 |
 |
– |
Отклонение, мкм |
верхнее |
0 |
0 |
0 |
-22 |
+200 |
1200 |
-22 |
+200 |
– |
нижнее |
-52 |
-110 |
-740 |
-74 |
0 |
0 |
-74 |
0 |
– |
Допуск на изготовление, мкм |
52 |
110 |
740 |
52 |
200 |
1200 |
52 |
200 |
– |
Высота неровностей, Ra
, мкм |
2,5 |
5 |
– |
2,5 |
10 |
– |
2,5 |
10 |
– |
Допуск прямолинейности, Т_
»
0.6∙
Tb
, мкм |
30 |
– |
– |
– |
– |
– |
– |
– |
– |
Допуск плоскостности, Т
»
0.6∙
Tb
, мкм |
30 |
– |
– |
– |
– |
– |
– |
– |
– |
Допуск параллельности, Т//
»
0.6∙
Tb
, мкм |
30 |
– |
– |
30 |
– |
– |
30 |
– |
– |
Допуск симметричности, Т÷
»
4∙
Tb
, мкм |
– |
– |
– |
200 |
– |
– |
200 |
– |
– |
5. Допуски и посадки шлицевых соединений
Шлицевое соединение d
‑8
´
62
H
7/
h
6
´
68
´
12
D
9/
d
9
5.1 Расшифровываем условное обозначение шлицевого соединения: шлицевое соединение легкой серии прямобочного профиля, центрировано по внутреннему диаметру (по
d
).
5.2 Номинальные размеры и посадка элементов профиля (ГОСТ 1139–80), [3])
– центрирующий (внутренний) диаметр d– Æ
62
H
7/
h
6;
– ширина зуба – 12
D
9/
d
9;
– нецентрирующий (наружный) диаметр Æ
68.
5.3 Осуществляем размерную характеристику элементов шлицевого профиля [4] (табл. 4).
Таблица 4. Размерная характеристика элементов деталей шлицевого профиля, мкм
Параметры элементов шлицевого соединения |
Втулка |
Вал |
D |
d |
b |
D |
d |
b |
Номинальный размер, мм |
6
8
|
62
|
1
2
|
6
8
|
62
|
1
2
|
Поле допуска |
-
|
H7
|
D9
|
-
|
h6
|
d9
|
Условное обозначение |
Æ
68
|
Æ
62H7
|
Æ
12D9
|
Æ
68
|
Æ
62h6
|
Æ
12d9
|
Отклонение, мкм |
верхнее |
-
|
+30
|
+93
|
-
|
0
|
-50
|
нижнее |
-
|
0
|
+50
|
-
|
-19
|
-93
|
Допуск на изготовление, мкм |
-
|
30
|
43
|
-
|
19
|
43
|
Высота неровностей Ra, мкм |
-
|
1
,25
|
2
|
-
|
0,
8
|
2
|
Допуск параллельности, мкм |
-
|
-
|
2
|
-
|
-
|
2
|
5.4 Строим схемы расположения полей допусков шлицевого соединения масштаб 1 мм – 2 мкм (ри
c
.6)
5.5 Выполняем чертежи деталей шлицевого профиля и соединения (черт. 6)
Принимаем шлицевой вал исполнения А.
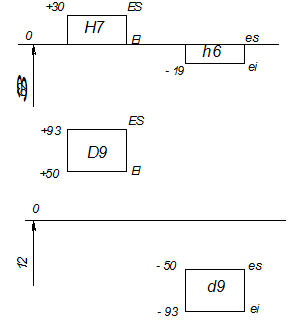
Рисунок 6. Расположение полей допусков шлицевого соединения
6. Расчёт размерной цепи
Е∑
=1
6.1 По заданному замыкающему звену составим размерную цепь и проверим правильность её составления
   Е5 Е6
   Е4 Е3 Е2 Е1 Е∆
Рисунок 7. Схема размерной цепи
Уменьшающие звенья:
Е1
=14 мм – ширина подшипника,
Е 2
=14 мм – ширина подшипника,
Е 3
=18 мм – длина втулки без реборды,
Е 4
=4 мм – толщина реборды втулки.
Увеличивающие звенья:
Е 5
=22 мм – длина втулки,
Е 6
=29 мм – проточка под подшипники.
Е∆
=∑Еув
-∑Еум
(20)
где ∑Еув
– сумма увеличивающих звеньев.
∑Еум
– сумма уменьшающих звеньев.
Е∆
= (22+29) – (18+14+14+4)=1 мм.
Вывод: расчетная цепь составлена верно.
6.2 Определяем метод решения размерной цепи – метод неполной взаимозаменяемости
6.3 Сведения о размерной цепи заносим в таблицу 5
6.4 Уточняем начальные условия
: применяем закон нормального распределения размеров звеньев цепи, коэффициент относительного рассеяния размеров λ=1/9;
риск (принятый процент брака по замыкающему звену) Р=0,27%;
коэффициент риска tΔ
=3.
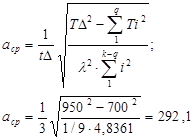
6.5 Рассчитываем среднее число единиц допуска аср
:
Таблица 5. Сведения о звеньях размерной цепи
Звено увеличивающее →
Уменьшающее ←
|
Начальный размер, мм |
Параметры звена, мкм |
Исполни
тельный размер, мм
|
Ед.
допуска, i
|
отклонение |
Допуск,
Т∆
|
Верхнее
ES(es)
|
Нижнее
EI(ei)
|
Среднее
E0
(e0
)
|
Замыкаю
щее
|
Е∆
|
1 |
- |
+400 |
-450 |
-25 |
950 |
 |
Стандарт
ные
|
Е1←
Е2←
Е3←
|
14
14
18
|
-
-
-
|
0
0
+250
|
-100
-100
-250
|
-125
-50
0
|
100
100
500
|
14-0,1
14-0,1

|
Ремонтиру
емые
|
Е4←
Е5→
Е6→
|
4
22
29
|
0,83
1,44
1,44
|
0
+840
-265
|
-480
0
-1105
|
-240
+420
-685
|
480
840
840
|
4-0,048
22+0,084

|
6.6 Принимаем ближайшее стандартное меньшее число единиц допуска
ac
т
≤ аср
.
По ac
т
устанавливаем квалитет JT
13
.
6.7 Выбираем корректирующее звено
Е6
, размеры которого изменять просто. Выписываем допуски размеров остальных ремонтируемых звеньев цепи по ГОСТ 25346–89, назначаем отклонения. Для увеличивающих ES
=+
T
,
EI
=0
; для уменьшающих es
=0,
ei
=-
T
. Определяем среднее отклонение составляющих звеньев, исключая корректирующее:
ЕΔ
=Е0Δ
=(
ESΔ
+
EIΔ
)/2 (22)
Е0Δ
=(400–450)/2= -25 мкм
6.8 Находим среднее отклонение корректирующего звена
Е06
Е06
=Е0Δ
-
(23)
Е06
= -25 – (420)+(-240)= -685 мкм.
6.9 Находим отклонения звеньев
Верхнее отклонение:
ES
6
= Е06
+
T
6
/2
(24)
ES
6
= -685+840/2= -265 мкм,
Нижнее отклонение:
EI
6
= Е06
-
T
6
/2
(25)
EI
6
= -685–840/2= -1105 мкм.
6.10 Проверяем правильность расчета параметров звеньев
Е0Δ
= ;
(26)
;
(27)
,
Так как зависимости соблюдаются, значит расчеты верны.
Список используемой литературы
1. Ожгибинцев Б.С. Практический курс стандартизации, метрологии и сертификации. Барнаул: Издательство АГАУ, 2004. 237 с.
2. В.Н. Нарышкина и Р.В. Коросташевский Подшипники качения: Справочник каталог. – М.: Машиностроение, 1984.-280 с.,
3. Анурьев В.И. Справочник конструктора – машиностроителя. В 3-х т. Т. 2. – 5-е изд., перераб. и доп. – М.: Машиностроение, 1978. 559 с.
4. Серый И.С. Взаимозаменяемость, стандартизация и технические измерения. 2-е изд., перераб. и доп. – М.: Агропромиздат, 1987. 367 с.
|