Орловский Государственный Технический Университет
Ерошенко Александр Викторович
Получение биметаллических заготовок центробежным способом
Специальность 05.16.04 Литейное производство
Диссертация на соискание магистра технических наук
Научный руководитель
доцент, кандидат технических наук
Маркова Н.Н
Орел, 2009г.
СОДЕРЖАНИЕ
ВВЕДЕНИЕ
ГЛАВА I. СОСТОЯНИЕ ВОПРОСА
1.1 Современные требования, предъявляемые к качеству мелющих валков
1.1.1 Общие требования к валкам различного назначения пищевой отрасли
1.1.2 Условия эксплуатации и технические характеристики мелющих валков
1.2 Анализ и тенденции развития перспективных процессов производства биметаллических мелющих валков
1.3. Основные направления дальнейшего совершенствования технологических процессов производства биметаллических мелющих валков
1.4 Влияние химического состава чугуна на качество рабочего слоя валков
Выводы, цель и задачи настоящей работы
ГЛАВА II. МЕТОДИКА ИССЛЕДОВАНИЯ
2.1. Объект исследования и общие методические положения работы
2.2. Методы исследования структуры и физико-механических свойств металла отливок
Выводы
ГЛАВА III. ИССЛЕДОВАНИЕОСОБЕННОСТЕЙ ФОРМИРОВАНИЯ БИМЕТАЛЛИЧЕСКИХ ЗАГОТОВОК ВАЛКОВ В ПОЛЕ ДЕЙСТВИЯ ЦЕНТРОБЕЖНЫХ СИЛ
3.1 Исследование особенностей процесса затвердевания отливки в массивной изложнице
3.2 Определение кинетики затвердевания рабочего слоя валков
3.3 Влияние скорости затвердевания на свойства металла рабочего слоя валков
Выводы
ГЛАВА IV. ИССЛЕДОВАНИЕ И РАЗРАБОТКА ТЕХНОЛОГИИ ИЗГОТОВЛЕНИЯ БИМЕТАЛЛИЧЕСКИХ МЕЛЮЩИХ ВАЛКОВ
4.1. Исследование и выбор оптимальных параметров формы для отливки мелющих валков
4.2 Оптимизация состава и способа нанесения теплоизоляционного покрытия на внутреннюю поверхность изложницы
4.3 Совершенствование конструкции заливочного устройства для отливки валков
4.4 Технологический регламент вращения формы
4.5 Термовременные параметры режима заливки двух разнородных металлов в форму
4.6 Исследование и выбор состава чугуна мелющих валков рабочего слоя
4.7 Экспериментально-производственная отработка технологии отливки биметаллических валков методом центробежного литья
Выводы
ГЛАВА V. ПРОМЫШЛЕННОЕ ВНЕДРЕНИЕ ТЕХНОЛОГИИ ИЗГОТОВЛЕНИЯ БИМЕТАЛЛИЧЕСКИХ МЕЛЮЩИХ ВАЛКОВ
5.1 Внедрение разработанного технологического процесса производства мелющих валков в промышленных условиях
Выводы
ОБЩИЕ ВЫВОДЫ
Список использованных источников
Приложение
ВВЕДЕНИЕ
Задачей современного машиностроения является повышение надежности и долговечности оборудования, в том числе работающего в условиях повышенных удельных нагрузок и интенсивного износа рабочих элементов.
Подавляющее количество оборудования для пищевого машиностроения связано с переработкой продуктов аграрно-продовольственного комплекса страны, таких как пшеница, рожь, солод, кофе, какао-бобы, сахар, соль и др.
Основная нагрузка по их переработке ложится на рабочие органы размольных агрегатов - мелющие валки, от качества которых зависит производительность, энергоемкость и стабильность работы всего технологического оборудования, а также сортность выпускаемой продукции.
Преждевременный выход из строя мелющих валков приводит к остановке всего перерабатывающего оборудования, работающего в синхронном режиме, и отнимает до 25% полезного времени в связи с перевалкой валков.
Общие потери от преждевременного износа мелющих валков в пищевой отрасли страны, включающей 350 крупных мукомольных комбинатов, около 300 крупных кондитерских предприятий и несколько сотен более мелких, составляют сотни миллионов рублей в год.
Сложность технологии изготовления биметаллических заготовок мелющих валков состоит в необходимости достижения высокой твердости поверхностного рабочего слоя при наличии «мягкой» сердцевины с достаточно высокой пластичностью металла, что приводит к затруднениям при изготовлении цельной заготовки, которая должна обладать дифференцированными свойствами по сечению.
Традиционная технология изготовления заготовок мелющих валков методом «промывки» в стационарный кокиль, отличающаяся низкой эффективностью процесса, хотя и позволяет получать дифференцированную структуру по сечению отливки, однако не обеспечивает равномерной твердости и одинаковой глубины отбеленного слоя по длине и окружности валков, что является одной из основных причин их низкой эксплуатационной стойкости.
Продолжительность работы мукомольных валков отечественного производства, полученных стационарным способом, крайне низка и оценивается в 3,5...4,0 месяца до первой переточки рифлей при работе на драных системах грубого помола, в то время как валки зарубежного производства в аналогичных условиях работают в 2,0.. .2,5 раза дольше.
Наиболее эффективным способом изготовления мелющих валков с дифференцированной структурой является центробежное литье с последовательной заливкой во вращающуюся форму металлов рабочего и внутреннего слоев, что позволяет не только обеспечить их высокие эксплуатационные характеристики, но и в максимальной степени механизировать процесс их изготовления.
Однако, несмотря на ряд выполненных работ с участием специалистов ряда организаций, эксплуатационная стойкость мелющих валков, изготовленных способом центробежного литья, все еще не соответствует растущим требованиям пищевого машиностроения.
В основном это связано с отсутствием стабильной технологии применяемого способа центробежного литья, что ведет к повышенному браку по расслоению, трещинам, спаям, появлению бугристости на поверхности отливок, и связанной с этим «пятнистости», т.е. неравномерной твердости на поверхности отливки, что во многом объясняется недостаточной изученностью процесса формирования разнородных составов чугуна в поле действия центробежных сил.
В связи с этим проблема изготовления надежных и долговечных в эксплуатации, то есть конкурентоспособных мелющих валков для пищевого машиностроения, является актуальной.
Цель и задачи работы.
Целью работы является исследование особенностей технологического процесса получения заготовок мелющих валков для пищевого машиностроения методом центробежного литья с последующим внедрением полученных результатов в промышленности.
Для достижения поставленной цели решались следующие задачи:
- исследование особенностей процессов заполнения и распределения жидкого металла в форме с учетом действия центробежных сил и определение их влияния на качество отливок;
- изучение кинетики и скорости затвердевания рабочего слоя валков и их влияния на структуру и свойствами металла, а также взаимосвязь их температурно-временными условиями заливки двух разнородных составов чугуна;
- разработка технологического регламента центробежного литья бочек мелющих валков по основным его параметрам: скорость и температура заливки металла, способ и режим ввода металла во вращающуюся форму, частота вращения формы, состав и способ нанесения теплоизоляционного покрытия в изложницу, интервал времени между заливками двух металлов и др.
На
учная новизна раб
оты:
- научно обосновано использование массивной изложницы с рабочей поверхностью, облицованной самотвердеющим покрытием, толщина стенки которой соизмерима с толщиной стенки отливки, что позволило существенно повысить ее теплоаккумулирующую способность, снизить температурный перепад по отношению к отливке и повысить изотропность свойств рабочего слоя валка;
- разработан технологический регламент заливки рабочего и внутреннего слоев металла валков, обеспечивающий прочное сваривание двух разнородных металлов;
- экспериментально обосновано, что частота вращения формы должна определяться с учетом толщины заливаемого слоя металла, а не наружного диаметра отливки;
- выявлена определяющая роль термического сопротивления облицованного покрытия, которая при толщине слоя 2,0 мм позволяет обеспечить требуемую твердость и глубину отбела рабочего слоя валка; показано, что использование заливочного устройства с боковой подачей жидкого чугуна по ходу вращения формы сокращает на 20...25% период его вовлечения во вращение до частоты вращения формы, что позволяет обеспечивать получение плотной и однородной структуры рабочего слоя.
Практическая ценн
ос
ть и реализация раб
оты:
разработан и внедрен на ООО «Орловский литейный завод имени Медведева» технологический регламент производства высококачественных биметаллических валков для пищевого машиностроения методом центробежного литья
Личный
вклад
Автор принимал непосредственное участие в качестве технолога-литейщика ООО «Орловский литейный завод имени Медведева» под руководством специалистов ОрелГТУ и профессора д.т.н. Мирзояна на литейно-металлургической базе ФГУП «ЦНИИТМАШ» в постановке задачи работы, проведении лабораторных экспериментов и опробовании полученных результатов в промышленных условиях.
Автор непосредственно участвовал при анализе и обобщении результатов теоретических, экспериментальных и расчетных данных.
При его участии отлиты биметаллические заготовки мельничных валков на ООО «Орловский литейный завод имени Медведева»
Глава
I
. СОСТОЯНИЕ ВОПРОСА
1.1 Современные требования, пре
дъявляемые к качеству мелющих валков
1.1.1 Общие требования к заготовкам валков различного назначения пищевой промышленности
Широкое распространение в пищевой промышленности получило оборудование для переработки различных продуктов и, в частности, их размола в валковых мельницах [1, 2, 3].
Размолу подвергаются такие широко применяемые продукты как пшеница, рожь, какао-бобы, солод, кофе, сахар, соль и др.
Процесс измельчения продуктов на предприятиях пищевой отрасли является одним из основных, так как в значительной мере влияет на выход и качество готовой продукции.
Главным рабочим инструментом мельниц, в которых происходит размол, являются мелющие валки, от качества которых зависит стабильная работа и производительность всего комплекса перерабатывающего оборудования, а также качество выпускаемой продукции.
Мелющие валки работают в сложных условиях, испытывая большие динамические нагрузки и воздействие механических факторов изнашивания.
Преждевременный выход из строя мелющих валков связан не только с остановкой группы мельниц, но и всего производственного цикла, что приводит к значительным временным и экономическим потерям [5, 6].
В связи с этим вопросу эксплуатационной стойкости мелющих валков придается первостепенное значение.
Исходя из специфических условий эксплуатации мелющих валков их стойкость во многом обусловлена дифференцированным характером структуры и свойств металла по сечению отливки, то есть наличием поверхностного отбеленного слоя толщиной 0,020...0,025 м с достаточно высокими значениями твердости (62...72 HSD), равномерно распределенными по длине и сечению бочки валка, и «мягкой» сердцевины с твердостью 180...230 НВ [11, 30].
Применение легированных хромом и никелем чугунов для формирования рабочего слоя мелющих валков /30/ приводит к необходимости в четкой дифференциации макроструктурных зон в сечении бочки валка, так как при достаточной протяженности отбеленного (рабочего) слоя, но наличии хрупкого структурно-свободного цементита в сердцевине валка запрессовка стальных полуосей с торцев бочки сопровождается появлением трещин. Наряду с наличием дифференцированной структуры бочка валка должна обладать 100% сплошностью, то есть прочным свариванием металла рабочего слоя и сердцевины, а также отсутствием дефектов в теле отливки.
Традиционная технология изготовления мелющих валков методом «промывки» в стационарный кокиль, отличающаяся низкой эффективностью процесса, не обеспечивает оптимального соотношения структурных зон по сечению бочки валка, а также равномерного распределения значений твердости и глубины отбеленного слоя по длине и окружности валков, что является одной из основных причин их низкой эксплуатационной стойкости, которая оценивается на уровне 40... 50% от стойкости валков современного производства.
Поэтому существующая практика использования мельничных валков предусматривает их закупку за рубежом.
Использование прогрессивного способа центробежного литья с современной технологией изготовления мелющих валков позволяет решить проблему повышения их стойкости, а также отказаться от закупки дорогостоящей (в 2,0...2,5 раза по отношению к отечественной) импортной продукции.
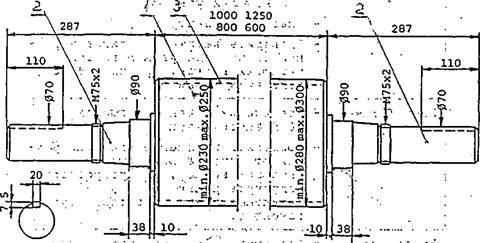
1 - чугунная бочка, 2 - стальные полуоси, 3 - рабочий слой из легированного чугуна
Рисунок 1.1 - Схема конструкции мелющего валка для пищевой промышленности
Общие признаки, характеризующие мелющие валки, используемые в мукомольной, шоколадной, кофейной, пивоваренной и других отраслях пищевого машиностроения (рис. 1.1), сводятся к следующему:
- рабочим органом мелющих валков является биметаллическая чугунная бочка (1), а в качестве опорных элементов применяются стальные полуоси (2) запрессованные с двух торцев бочки;
- наружный (рабочий) слой бочки валков (3) изготавливают из отбеленного легированного чугуна, а внутренний слой - из серого чугуна;
- толщина наружного слоя валков составляет 0,02...0,025 м, а внутреннего слоя 0,06...0,08 м;
- твердость наружного слоя металла составляет 62...72 HSD;
- твердость внутреннего слоя металла составляет 180.. .230 НВ;
- наружный слой бочки большинства валков подвергается нарезке рифлей для эффективного измельчения пищевых продуктов;
- размеры бочек наиболее распространенных мелющих валков составляют по диаметру 0,25...0,30 м, а по длине 0,6... 1,25 м.
Учитывая общность основных технических характеристик, используемых для большинства применяемых пищевых валков, целесообразно объединить их с точки зрения технологического исполнения в единую группу сменных изделий, используемых в пищевом машиностроении.
Годовая потребность мелющих валков для пищевой промышленности Российской Федерации составляет около 20900 шт. [2, 5, 8] (таблица 1.1).
Таблица 1.1 - Годовая потребность в мелющих валках для пищевой промышленности РФ
Тип валков |
Диаметр и
длина бочки, м
|
Годовая потребность |
масса |
количество |
T |
%
|
шт. |
%
|
Мукомольные (для крупных предприятий) |
0,25x1,0 |
5000 |
70,0 |
15000 |
72,0 |
Мукомольные (для мини-производств) |
0,25x0,30 |
1000 |
13,7 |
4000 |
19,0 |
Шоколадные (размол какао-бобов) |
0,4x1,2 |
300 |
4,0 |
400 |
1,8 |
Пивоваренные (размол солода) |
0,4x1,0 |
800 |
11,0 |
1000 |
4,8 |
Кофейные (размол зерен кофе) |
0,25x0,30 |
100 |
1,3 |
500 |
2,4 |
Всего: |
7200 |
100 |
20900 |
100 |
Анализ табличных данных свидетельствует о том, что около 84% по массе и 90,0% по количеству мелющих валков в пищевой промышленности составляют мукомольные валки для крупных и мелких предприятий.
Учитывая однотипность технических характеристик мелющих валков, применяемых в пищевом машиностроении, целесообразно в дальнейшем рассматривать особенности их использования и технологические приемы изготовления на примере наиболее распространенных валков, применяемых в мукомольной отрасли.
1.1.2 Условия эксплуатации и технические характеристики
мелющих валков
Размол зерна пшеницы и ржи осуществляются на мельницах отечественного производства: А1-БЗН, ЗМ2 и БВ2 [9, 10, 11]. На мельницах типа А1-БЗН используются валки с внутренней полостью в бочке.
В количественном отношении такие мельницы составляют 60...65%, остальная доля 35...40% приходится на мельницы типа ЗМ2 и БВ2, в которых применяются валки с бочкой сплошного сечения массой в 1,5 раза превышающей массу валков мельниц типа А1-БЗН.
Наряду с этим используются мельницы зарубежного производства.
Принципиальной разницы в процессе размола зерна между ними нет. В мельницах зарубежного производства применяются в основном валки с полой бочкой[12, 14, 17].
Размольное отделение современного мукомольного завода производительностью 500 т/сутки обычно разделено на две секции, в каждой из которых установлено по 16 валковых мельниц вместе с другим специальным оборудованием [3,19].
На рисунке 1.2 представлена конструктивная схема мельницы для размола зерна типа А1-БЗН [1]. Мельница разделена сплошной перегородкой на две половины (секции), каждая из которых работает самостоятельно.
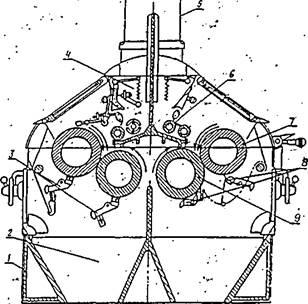
1 - станина, 2 - бункер, 3 - щетки, 4 - механизм питания, 5 - приемная труба, 6 - питающие валики, 7 - быстро вращающийся валок, 8 - ножи для очистки, 9 - медленно вращающийся валок
Рисунок 1.2 - Мельница типа А1-БЗН для размола зерна
Как видно из приведенной схемы, мельница состоит из следующих основных узлов: 1 - станина, 2 - бункер, 3 - щетки, 4 — механизм питания, 5 - приемная труба, 6 - питающий валик, 7 - быстро вращающийся валок, 8 — ножи для очистки, 9 - медленно вращающийся валок.
Мукомольные валки в количестве 4 штук установлены парами в двух секциях мельницы и работают автономно. При этом линия, соединяющая их оси вращения, образует угол 30° с горизонталью.
Уменьшение этого угла способствует улучшению питания валков зерном, а также повышению коэффициента заполнения площади измельчения.
Зерно пшеницы или ржи по приемной трубе - 5 поступает на питающие валики — 6, посредством которых равномерно распределяется по всей длине расположенных ниже мелющих валков 7 и 9. Регулировка величины рабочего зазора между мелющими валками осуществляется путем перемещения нижнего валка, закрепленного в подвижных буксах.
Верхний валок вращается с более высокой скоростью, чем нижний, что обеспечивает интенсивное измельчение продуктов.
Отличительной особенностью мельниц подобного типа является использование полых по конструкции бочек валков. При этом внутренняя полость бочки быстро вращающегося валка охлаждается водой, что оказывает положительное влияние на свойства измельчаемой продукции.
Мельницы типа ЗМ2 и БВ2 по своей технологической схеме мало отличаются от соответствующих характеристик мельниц типа А1-БЗН.
Мелющий валок для мельниц А1-БЗН имеет следующие характеристики: внешний диаметр бочки валка - 1 составляет 0,25 м, длина бочки составляет 1 м, масса 2646 Н, диаметр внутренней полости бочки - 0,158 м /3/ (рис. 1.4).
По торцам бочки запрессованы цапфы - 2, диаметр запрессованной части 0,16 м, шейка цапфы имеет три части: переходную цилиндрическую диаметром 0,1 м, опорную, состоящую из цилиндрической и конической частей (0,075...0,080 м), и концевую цилиндрическую 0,065 м. На конусной части - 3 цапфы установлены подшипники - 4, а концевая цилиндрическая служит для насадки приводного шкива или шестерни - 5 межвалыдовой передачи (13 -малая шестерня).
Мелющий валок охлаждается водой, которая поступает через трубку - 6 и заполняет внутреннюю полость.
При нормальной работе системы охлаждения температура быстро вращающегося валка не должна превышать 60°С. По данным испытаний температура поверхности валка не превышает 36°С, а самого продукта после измельчения не более 25°С /3/.
Мелющие валки со сплошным сечением бочки, предназначенные для мельниц ЗМ2 и БВ2, имеют размеры по внешнему диаметру 0,25 м и по длине 1, 0,8 и 0,6 м, соответственно массой 3822, 3116и2411Н.
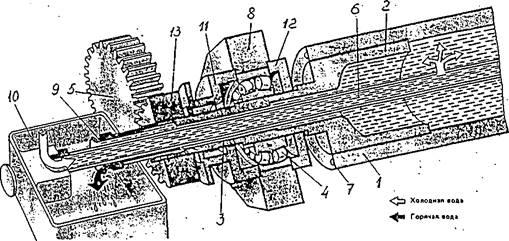
1 - корпус, 2 - цапфа, 3 - конус цапфы, 4 - подшипник, 5 - шестерня, 6 - труба, 7 - полость для балансировки, 8 - корпус подшипника, 9 - втулка, 10 - камера, 11, 12 - крышки подшипника, 13 - малая шестерня
Рисунок 1.3 - Мелющий валок А1-БЗН с системой охлаждения
Анализ технических характеристик мелющих валков с полой и сплошной бочками позволяет сделать вывод о предпочтительном использовании валков с полой бочкой по следующим причинам:
- уменьшается на 50% расход металла на изготовление заготовок валков и снижается масса готовых валков на 33% по сравнению с массой полого валка;
- снижается тепловое расширение при нагревании валков в результате охлаждения водой внутренней полости бочки и стабилизируется размер зазора, т.е. повышается качество размола;
- уменьшается расход электроэнергии при эксплуатации;
- увеличивается контактная поверхность полости бочки с запрессованной частью цапфы и в связи с этим снижаются радиальные внутренние напряжения примерно на 40%, а также усилия при запрессовке цапф примерно в 3 раза [1];
- улучшаются качественные показатели измельченной продукции в результате охлаждения внутренней полости бочки. Представленные преимущества использования мелющих валков с полой бочкой позволяют ставить вопрос о необходимости изменения конструкции валков для мельниц типа ЗМ2 и БВ2 со сплошной на полую бочку.
Однако традиционный способ их изготовления методом стационарного литья сдерживает такой прогрессивный путь наиболее эффективного изготовления валков, т.к. сопряжен со значительными трудностями технологического исполнения.
В то же время, несмотря на открывающиеся возможности при использовании центробежного метода для получения валков с полой бочкой, в настоящее время отсутствуют разработанные рекомендации по его использованию для реализации этой важной для мукомольной отрасли задачи.
1.2 Анализ и тенд
енции развития
перспективных процессов производства биметаллических мелющих валков
Противоречивость требований к служебным свойствам биметаллических чугунных валков состоит в необходимости образования твердого поверхностного слоя для противодействия абразивному износу и сравнительно «мягкого» внутреннего слоя для возможности расточки и запрессовки стальных полуосей, что в значительной степени усложняет технологическую задачу получения биметаллических литых изделий.
Для реализации этой задачи были разработаны способы стационарной заливки валков «промывкой» [21 ...24] и «полупромывкой» [25...29].
По методу «промывки» в форму (рис. 1.4) заливается металл до уровня отверстия в прибыльной части валка. После образования на бочке слоя твердого металла необходимой толщины осуществляется заливка другого металла в форму. Незатвердевший легированный металл вытесняется из формы серым чугуном для образования сердцевины валка.
Промывное отверстие закрывается и форма заполняется серым чугуном до верхней кромки прибыли [21, 22].
Метод «полупромывки» применяется для получения валков из высокопрочного чугуна. При этом способе после затвердевания рабочего слоя валка (из чугуна, имеющего 0,4...0,5% кремния и обработанного магнием) в форму заливается чугун с повышенным содержанием кремния (7... 10%), что препятствует образованию отбела /21, 23, 25/, с тем, чтобы после смешения двух металлов получить состав чугуна с содержанием кремния 2,0...2,3%.
Указанные способы получения биметаллических валков имеют существенные недостатки: большой расход жидкого металла, особенно легированного, нестабильность процесса, трудность получения равномерного отбела по длине и сечению бочки валка, значительная длительность технологического цикла.
Несмотря на сложность и трудоемкость изготовления мелющих валков стационарными способами и низкое качество получаемых валков они продолжают находить применение в современной практике.
Так, все мукомольные валки типа ЗМ со сплошной конструкцией бочки, составляющие 35-40% объема всего производства, изготавливают только стационарным способом.
Многие валки с пустотелой бочкой для мельниц типа А1-БЗН изготавливают также стационарным способом с использованием центрального стержня в форме.
На рис. 1.5 представлена схема заливки полого мелющего валка в кокиль с центральным стержнем.
Стержни для формирования внутренней полости валка изготавливаются из смеси кварцевого песка с метилакриловой смолой, отверждаемой углекислым газом.
Материалом отливок является нелегированный серый чугун, отбеленный рабочий слой составляет по глубине 0,010. ..0,015 м.
Использование стационарного способа изготовления бочек мукомольных валков связано как с большими издержками в процессе их производства (низкий выход годного 40-50%, большой расход формовочных материалов, высокая трудоемкость процесса), так и низкими качественными характеристиками: неравномерность твердости по длине и сечению бочки валка, а также неравномерность толщины рабочего слоя, что в значительной степени снижает их эксплуатационную стойкость (3,5...4,0 месяца до первой переточки рифлей) [30].
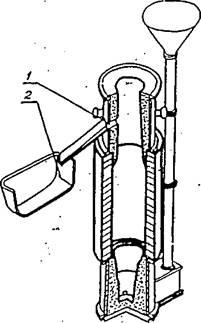
Рисунок 1.4 – Стационарная кокильно-песчаная форма для отливки валков методом «промывки» 1 — отверстие в прибыльной части валка, 2 - приемное устройство для слива чугуна
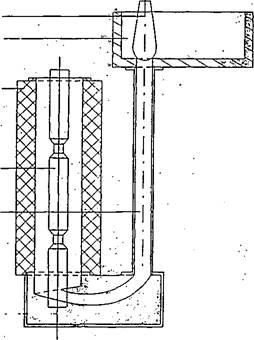
Рисунок 1.5 - Схема стационарной заливки полого мельничного валка
1 - стопор, 2 - заливочная чаша, 3 - кокиль, 4 - стержень, 5 — литниковый канал
Практика производства биметаллических валков показывает, что перечисленные недостатки, характерные для стационарного литья, устраняются при использовании центробежного способа изготовления валков [26, 31.. .35].
О преимуществах способа центробежного литья, по сравнению со стационарным, упоминалось в ряде отечественных и зарубежных публикаций, в которых подчеркивалось удачное решение проблемы качества отливок и экономии металла [3 6... 3 8].
Анализ литературных данных показывает, что в мировой практике разработаны и применяются различные способы центробежного литья биметаллических валков:
1. Заливка рабочего слоя и сердцевины металла валка на машинах с вертикальной осью вращения [32, ].
2. Отливка двухслойных валков на машинах с наклонной осью вращения [30,32,41].
3. Заливка рабочего слоя в форму с горизонтальной осью вращения с последующим заполнением сердцевины в вертикальном положении [47].
4. Заливка рабочего слоя на машинах с горизонтальной осью вращения [45, 46].
Каждый из указанных способов имеет свои преимущества и недостатки. Так, например, первый из них характеризуется сложностью конструкции, а также неравномерной толщиной рабочего слоя по длине бочки валка.
Второй способ (с наклонной осью вращения формы) также отличается определенной сложностью конструкции машин, требует ее заглубления и также не обеспечивает равномерной толщины рабочего слоя бочки валка.
Этот способ не нашел широкого применения.
Третий способ получения биметаллических валков имеет две разновидности.
Одна из них заключается в наличии поворотного устройства изложницы, с помощью которого форма после заливки металла рабочего слоя при горизонтальной оси вращения и его кристаллизации устанавливается в вертикальное положение, а затем производится заливка металла сердцевины.
Этот способ приемлем для небольших по массе валков, у которых интервал между заливкой рабочего слоя и сердцевины ограничен по времени, однако его применение из-за сложности конструкции машины тоже ограничено.
Второй разновидностью этого способа является заливка металла сердцевины валка в форму, расположенную в вертикальном положении вне зоны расположения машины (кессон), после кристаллизации рабочего слоя при горизонтальной оси вращения.
Указанный способ нашел применение в ряде стран для производства преимущественно крупных валков, при изготовлении которых интервал между окончанием кристаллизации рабочего слоя и заливкой металла сердцевины достаточно велик [47, ].
Четвертый способ отличается простотой конструкции центробежной машины, не требует заглубления и обеспечивает равномерную толщину рабочего слоя бочки валка.
Учитывая, что при изготовлении валков для пищевой промышленности полуоси не отливаются, а запрессовываются, то изготовление полой бочки наиболее целесообразно производить на центробежных машинах с горизонтальной осью вращения путем последовательной заливки поверхностного рабочего слоя, а затем и внутреннего.
Использование этого способа для получения биметаллических валков отмечается в работах [30, 32, 34] (рис. 1.6).
Он нашел применение в металлургическом производстве ряда зарубежных стран (США, Япония, Германия, Франция) для изготовления двухслойных валков применительно к мелкосортным, проволочным и трубопрокатным станам.
Отмечается ряд преимуществ центробежного литья двухслойных валков по сравнению со стационарным способом их изготовления, например:
- структурная однородность рабочего слоя по глубине и длине бочки;
- равномерная твердость металла рабочего слоя по сечению и длине бочки;
- более плотная структура;
- экономичное и гибкое производство.
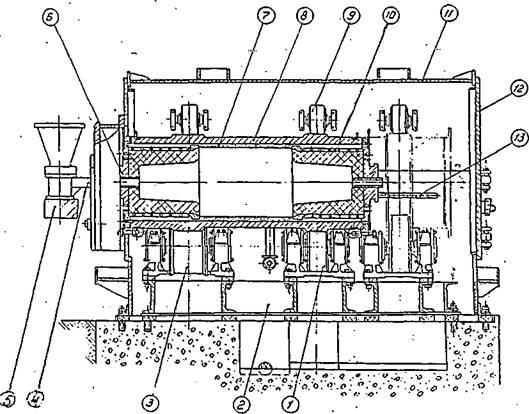
1 - ролик, 2 - станина, 3 - ролик приводной, 4 - траверса, 5 - заливочное устройство, б - крышка изложницы, 7 - теплоизоляционное покрытие, 8 - изложница, 9 - ролик нажимной, 10 - стакан, 11 - кожух, 12 - крышка задняя, 13 - система охлаждения
Рисунок 1.6 - Центробежная машина для отливки прокатных валков
Однако сведения о технологических особенностях изготовления мелющих валков центробежным способом являются недостаточно полными [30] и чаще всего носят рекламный характер .
Поэтому исходной ступенью настоящей работы являлась та база научных и практических разработок в области производства центробежнолитых биметаллических чугунных изделий, которая была близка по техническим характеристикам (геометрии, материалам, физико-механическим свойствам) к мелющим валкам пищевой промышленности.
Ближе всего к такого рода разработкам относятся исследования в области изготовления центробежнолитых биметаллических сортопрокатных валков диаметром бочки 0,25...0,46 м и длиной 1,0... 1,5 м [32, 34].
1.3 Осн
овные направления дальнейшего совершенствования технологических процессов производства биметаллических мелющих валков
Технологический процесс получения заготовок разрабатывается с учетом особенностей процесса их формирования в литейной форме и должен обеспечивать необходимые служебные свойства изделия.
Существенную роль в формировании служебных свойств играет литейная форма, ее теплоизоляционное покрытие, обеспечивающие определенный теплоотвод, скорость затвердевания металла и, как следствие, характер его структуры и физико-механические свойства.
Теплоизоляционные покрытия, используемые на внутренней поверхности изложницы, влияют также на чистоту поверхности бочки валка, предопределяя трудоемкость дальнейших операций при механической обработке заготовок.
Сокращение трудозатрат на указанные операции приобретает особую актуальность в связи со сложностью механической обработки высокотвердых материалов, к которым относится рабочий слой мелющих валков, с уровнем твердости 65...72 HSD и с требованием высокого качества поверхности бочки валка.
Решение указанной проблемы в значительной степени зависит от качества применяемых теплоизоляционных покрытий.
При изготовлении заготовок из различных сплавов способом центробежного литья широкое распространение получили сыпучие теплоизоляционные покрытия на основе кварцевого песка [30...36].
В работе [30] в качестве литейной формы для получения мукомольных валков рассматривается тонкостенная стальная изложница, толщиной стенки 0,035...0,040 м, покрытая изнутри сыпучим теплоизоляционным слоем и интенсивно охлаждаемая водой спрейерным способом.
В качестве сыпучего теплоизоляционного покрытия используется сухой кварцевый песок, марок 1К0315, 1К02С, толщиной слоя 0,003...0,005 м и слой противопригарного материала (цирконовая мука или маршалит зернистостью 0,020...0,005 мм) толщиной 0,001...0,0015 м [32]. Такое покрытие вводят во вращающуюся изложницу с помощью пескосыпа, представляющего собой трубу с продольным пазом, равным длине бочки валка.
Пескосып, заполненный песком, медленно поворачивают против направления вращения изложницы, высыпая песок, который, под действием центробежных сил, распределяется по внутренней поверхности изложницы. Затем на поверхность песка таким же способом наносят слой цирконовой муки.
Несмотря на наличие слоя противопригарного покрытия из цирконовой муки на поверхности отливки иногда наблюдается пригар (рис. 1.7), а также волнистость, из-за появления неровностей на поверхности теплоизоляционного покрытия (рис. 1.8).
Наряду с этим при использовании сыпучего покрытия на внутренней поверхности изложницы в зоне падения струи металла часто происходит вымывание песчинок и проникновение металла внутрь покрытия, что вызывает появление дополнительного пригара кольцевой формы.
Такая поверхность валка с трудом поддается механической обработке твердосплавным инструментом и это приводит к необходимости увеличения припуска на механическую обработку.
При этом имеют место случаи попадания сдвинутых песчинок и частиц цирконовой муки на границу раздела двух слоев металла [30].
В работе [34] проведено исследование температурного поля заготовки валка диаметром 0,25 м и длиной 1,5 м с рабочим слоем из хромоникелевого чугуна, полученной в тонкостенной изложнице с сыпучим покрытием.
На рис. 1.9 представлено изменение температуры металла рабочего слоя на глубине 0,01 м [34].
Как видно из представленного рисунка в зоне падения струи металла на расстоянии 0,5 м от заливочного края изложницы наблюдается повышение температуры металла по сравнению с температурой соседнего участка отливки.
Эта разница температур в отливке не исчезает в течение всего периода затвердевания рабочего слоя валка.
При этом указывается, что при заливке второго металла эта зона падения струи металла с повышенной температурой дополнительно нагревается, что приводит к нежелательному изменению структуры и твердости металла рабочего слоя, а также размыву струей металла рабочего слоя [34].
При этом высказывается предложение производить заливку второго металла с противоположной стороны по отношению к первой, что намного усложняет технологический процесс изготовления валков.
Сыпучее теплоизоляционное покрытие, наряду с приведенными недостатками, имеет ряд преимуществ, которые выражаются в доступности и дешевизне покрытия в виде кварцевого песка, а также простоту ввода в изложницу и его распределения на внутренней поверхности под действием центробежных сил.
В течение ряда десятилетий метод использования сыпучего теплоизоляционного покрытия на внутренней поверхности изложницы при центробежном литье был широко распространен на ряде предприятий и сыграл свою положительную роль [31].
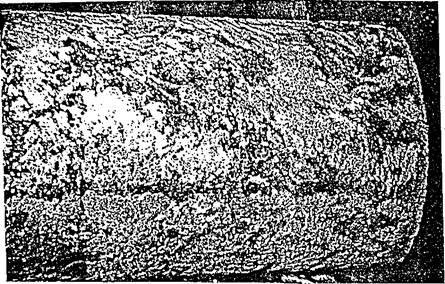
Рисунок 1.7 - Пригар на поверхности мелющих валков с использованием сыпучей футеровки

Рисунок 1.8 -Неровности и бугристость на поверхности мельничных валков с использованием сыпучей футеровки

Рисунок 1.9 -Повышение температуры рабочего слоя в месте падения струи металла в форму
Однако, в связи с развитием машиностроения и широкого применения ряда изделий со специальными свойствами, например прокатных валков, валков для пищевой промышленности, труб для машиностроения и др., где необходима строгая равномерность структурных составляющих и физико-механических свойств по длине и сечению изделия, а также чистота их поверхности с низкими припусками на механообработку, сыпучие покрытия должны были уступить свое место отверждаемым покрытиям, удовлетворяющим всем вышеперечисленным требованиям.
Поэтому в настоящей работе вопросу использования отверждаемого теплоизоляционного покрытия уделяется особое внимание.
Появление дефектов в отливке в зоне падения струи металла в форму способствует также распространенный способ заливки металла в направлении оси вращения изложницы.
Исследования гидродинамического состояния жидкого потока во вращающейся форме свидетельствуют о том, что при заливке жидкости в осевом направлении во вращающуюся форму происходит гидравлический удар («прыжок»).
Поэтому участок формы в месте падения струи металла является наиболее опасным с точки зрения разбрызгивания струи и захвата пузырьков воздуха в поток металла.
В работе [35] показано, что при осевом истечении струи металла из заливочного устройства размывание сыпучей теплоизоляции во вращающейся форме можно избежать при соответствующем угле наклона струи по отношению к форме и величине гравитационного коэффициента К > 20.
Однако с увеличением массы заготовок, когда используется более толстый слой сыпучего покрытия 0,004...0,006 м и повышенная скорость заливки металла энергия удара струи металла возрастает и частицы песчаного слоя вымываются более интенсивно, образуя кольцевой слой пригара.
Поэтому изменение способа заливки металла во вращающуюся форму для смягчения воздействия струи на теплоизоляцию является одним из этапов исследования настоящей работы.
Наряду с этим возникает проблема использования тонкостенных водоохлаждаемых изложниц с толщиной стенки 35...40 мм, которые используются при изготовлении биметаллических валков способом центробежного литья.
Такая изложница, интенсивно охлаждаемая водой, работает в режиме передатчика тепла от отливки в окружающую среду и испытывает значительные термоциклические нагрузки в различные периоды технологического процесса, что приводит к снижению ее эксплуатационной стойкости. Кроме этого, в процессе формирования биметаллических заготовок, близких по размерам и составу металла к мельничным валкам, возникают значительные напряжения в отливках из-за высокого перепада температур (400...500°С) между водоохлаждаемой тонкостенной изложницей и отливкой [34], что приводит к появлению трещин в рабочем и внутреннем слоях валка.
В связи с этим возникает задача, связанная с применением толстостенных изложниц, толщина стенки которых (0,12...0,15 м) сопоставима с толщиной стенки отливки. Такая изложница выполняет уже роль аккумулятора тепла, выделяемого отливкой и может не охлаждаться водой.
Одним из распространенных дефектов при литье биметаллических чугунных валков является несваривание металла на границе двух сплавов [34, 36] и, как правило, причиной появления такого дефекта служит отсутствие четких представлений о кинетике затвердевания металла рабочего слоя валка, и невозможность расчета и назначения оптимального температурно-временного режима процесса заливки двух металлов.
При чрезмерно большом интервале между окончанием затвердевания рабочего слоя и началом заливки второго металла, когда рабочий слой полностью затвердел и успел охладиться ниже определенной температуры, наблюдается несваривание слоев.
А при коротком интервале, когда рабочий слой еще не затвердел, при заливке второго металла происходит смешивание двух слоев с проникновением карбидообразующих элементов в сердцевину валка, в связи с чем появляются трудности при расточке отверстия бочки при запрессовке полуосей.
В приведенных работах [34, 36] на основе результатов определения продолжительности затвердевания металла рабочего слоя валка даются рекомендации по улучшению свариваемости рабочего слоя и сердцевины прокатных валков, полученных в тонкостенной водоохлаждаемой изложнице, покрытой изнутри сыпучим теплоизоляционным материалом.
Для обеспечения сваривания двух слоев металла (рабочего слоя из хромоникелевого чугуна и сердцевины из серого) необходимо обеспечить температуру в зоне сваривания равную 1050...1100°С, т.е. на 100...150°С ниже температуры затвердевания легированного чугуна.
При этом необходимо использование флюса для предотвращения образования на внутренней поверхности рабочего слоя пленки окислов, затрудняющей сваривание двух слоев металла.
С этой целью предлагается флюс следующего состава /34/:
силикат натрия (mNa2
0 • nSiCb) 25%
окись кальция (СаО) 35%
фтористый кальций (CaF2
) 25%
бура (Na2
B4
07
) 15%
Температура плавления флюса составляет 820°С.
Способы ввода флюса в изложницу, как правило, состоят в его засыпке на струю заливаемого металла при подаче в заливочную чашу [34] или в конце процесса заливки после выхода струи металла из заливочного желоба .
Указанные способы отличаются необходимостью дополнительного использования конструктивных элементов для ввода флюса и отсутствием их надежности, что способствует загрязнению металла неметаллическими включениями.
Особенностью производства двухслойных мельничных валков является значительная (в 1,8...2,1) разница в диаметрах внешнего и внутреннего поверхностного рабочего и внутреннего слоев, поэтому очень важна рекомендация по определению частоты вращения формы.
В большинстве случаев авторы для определения частоты вращения формы, имеют ввиду тонкостенные отливки (трубы, втулки, гильзы) с отношением внешнего и внутреннего диаметров в пределах 1,10... 1,15, как, например, в формуле Константинова Л.С [34]:
(1.1)
где n - частота вращения формы, мин-1
;
р - плотность сплава, г/см3
;
r - внутренний радиус отливки, см;
5520 – опытный числовой коэффициент.
Формула (1.1) выведена из предположения, что на свободной поверхности отливки коэффициент гравитации для чугунных заготовок составляет 47.
При изготовлении тонкостенных отливок эта формула дает положительные результаты, но при литье толстостенных заготовок какими являются мелющие валки, ее использование приводит к заниженным значениям гравитационного коэффициента на внутренней поверхности отливки и, как следствие, появлению структурной неоднородности.
Применительно к литью толстостенных заготовок в большей мере подходит расчетная формула Цветненко К.У. для определения частоты вращения стальных заготовок [45].
Однако при изготовлении биметаллических заготовок и эти рекомендации для определения скорости вращения формы не подходят, т.к. не учитывают условий заполнения двух металлов, их вовлечения в круговое движение и продольное перемещение в форме, т.е. особенностей гидродинамического состояния потока, а также тепловых условий, которые, в конечном счете, определяют свойства отливки.
Анализ технологического процесса изготовления двухслойных биметаллических заготовок центробежным способом показывает, что для получения мелющих валков с однородной плотной структурой рабочего слоя, высоким по качеству свариванием двух разнородных металлов рабочего слоя и сердцевины с высокой отбеливаемостью рабочего слоя необходимо решение ряда задач, позволяющих обеспечить:
- равномерный теплоотвод от отливки в окружающую среду;
- прочное сваривание двух металлов;
- плавный и быстрый ввод металла во вращающуюся форму;
- замена сыпучего покрытия на отверждаемое;
- усовершенствование ряда элементов конструкции центробежной машины, способствующих эффективному использованию процесса отливки валков.
1.4 Влияние химическог
о состава чугуна на качество рабочего слоя валков
Основным требованием к качеству мукомольных валков, как показали условия их эксплуатации, является высокая износостойкость рабочего слоя, которая во многом обусловлена высокими показателями твердости.
Однако в связи с тем, что на рабочей поверхности мукомольных валков нарезают рифли, к металлу предъявляются требования достаточной вязкости для предотвращения выкрашивания рифлей при эксплуатации валков.
Вместе с тем, как показывают результаты изучения эксплуатации мелющих валков, рифленая поверхность, применяемая на первичных драных системах помола, испытывает повышенные на 20...30% нагрузки по сравнению с валками, имеющими микрошероховатую поверхность, которые используются на конечных стадиях размола.
Поэтому физико-механические свойства рабочего слоя и структура металла, определяемые во многом его химическим составом, должны быть различны, в соответствии с разными служебными требованиями.
Несмотря на это обстоятельство практика производства мелющих валков показывает, что валки, изготавливаемые по одному, устоявшемуся химическому составу, эксплуатируются как на первичном помоле, на драных системах, так и на конечной стадии помола - на размольных системах.
Существующие нормативные документы по изготовлению мукомольных валков регламентируют один состав материала вне зависимости от использования валков в той или иной системе помола, что намного снижает их эксплуатационную стойкость.
Так, например, ГОСТ 2789-59 регламентирует химический состав рабочего слоя валков для нелегированного (белого) и легированного чугунов вне зависимости от особенностей их эксплуатации (таблица 1.2).
Таблица 1.2 - Химический состав рабочего слоя валков
Тип рабочего слоя |
Содержание элементов, мае. % |
углерод |
кремний |
марганец |
фосфор |
сера |
хром |
никель |
Нелегированный |
3,2-3,7 |
0,4-0,7 |
0,2-0,8 |
<0,5 |
<0,14 |
<0,25 |
<0,25 |
Легированный |
3,4-3,7 |
0,4-0,8 |
0,2-0,8 |
<0,5 |
<0,14 |
<0,35 |
0,5-0,8 |
Нелегированный чугун в качестве рабочего слоя валка используется преимущественно при стационарном литье валков.
Образование белого чугуна связано с высокой скоростью затвердевания его поверхностных слоев, соприкасающихся (через слой краски) с массивной металлической изложницей и образованием перлитно-цементитной структуры.
По мере снижения скорости затвердевания металла в центральных зонах отливки углерод выделяется в виде графита, при этом, чем дальше от наружной поверхности, тем его больше.
Использование белого чугуна в качестве отбеленного слоя на поверхности бочки валка оказалось малоэффективным при их эксплуатации.
Так мукомольные валки, отливаемые в стационарные формы /30/ с глубиной отбеленного слоя до 0,01 м, после одной-двух переточек настолько теряли износостойкость из-за нарастания количества графитовых включений по глубине слоя, что дальнейшее их использование становилось нецелесообразным.
При этом износостойкость валков оказалось весьма низкой и составляла около 50 суток до первой переточки рифлей на драной линии[30].
Поэтому дальнейшие работы были сосредоточены на использовании валков с рабочим слоем из легированного чугуна, что позволило повысить их стойкость до 4 месяцев, хотя и этот срок считается неудовлетворительным, так как не вписывается в годичный период межремонтных работ, установленный на крупных мелькомбинатах.
Дальнейшее совершенствование конструкции мукомольного оборудования и ввод в эксплуатацию в конце прошлого столетия новых конструкций валков, работающих с повышенными удельными нагрузками, потребовал значительного увеличения их износостойкости, а, следовательно, и совершенствования состава материала рабочего слоя валков.
Химический состав легированного чугуна для рабочего слоя валков был несколько скорректирован по сравнению с действующими нормативами по ГОСТ 2789-59/87/(табл. 1.3).
Таблица 1.3 — Химический состав легированного чугуна для рабочего слоя валков
Номер
технических
условий
|
Содержание элементов,. % |
С |
Si |
Мп |
Р |
S |
Сг |
Ni |
ТУ 14-2-241-79 МЧМ СССР |
3,4-3,7 |
0,4-1,0 |
0,3-0,8 |
<0,5 |
<0,16 |
<0,4 |
0,5-1,0 |
Твердость металла такого рабочего слоя из легированного чугуна, имеющего состав, приведенный в таблице 1.3, должна соответствовать 62...72 HSD на расстоянии 0,01 м от поверхности бочки валка, однако это условие на практике часто нарушается.
Наличие хрома и никеля в легированном чугуне обусловлено, наряду с получением заданной твердости, необходимостью повышения прочности и вязкости металла рабочего слоя валков, на поверхности которых нарезаются рифли.
Хром, являясь карбидообразующим элементом, увеличивает глубину отбеленного слоя и повышает его твердость.
В работах [21, 24] показано, что хром способствует увеличению переходной зоны валков, что может сказаться на появлении карбидов в сердцевине бочки валков и затруднении процесса расточки отверстий с торцевых ее поверхностей для запрессовки полуосей.
Никель способствует измельчению перлита, созданию более равномерной структуры чугуна и устранению микропористости отливок в отбеленном слое, легируя феррит и измельчая включения графита, и таким образом способствует повышению их прочности и вязкости [36].
Вместе с тем никель является графитизирующим элементом, поэтому повышение его содержания, по данным работы [21], способствует уменьшению чистоты металла в рабочем слое валка.
Таким образом, легирование чугуна рабочего слоя мелющих валков хромом и никелем обеспечивает получение необходимой твердости, снижает преждевременный выход из строя по причине выкрашивания рифлей, а с другой стороны обеспечивает получение чистого по графиту отбеленного слоя и короткой переходной зоны.
В связи с вышеизложенным совершенствование химического состава материалов валков является актуальной задачей и повышение качества материала рабочего слоя должно осуществляться с учетом особенностей их эксплуатации.
Выв
оды, цель и задачи настоящей работы
- Проанализированы возросшие за последние годы требования, предъявляемые к качеству мелющих валков для пищевой промышленности в области материалов, их физико-механических свойств и конструктивных параметров в зависимости от условий их эксплуатации на современном оборудовании, работающем с высокими удельными нагрузками.
- Установлено, что использование традиционного метода изготовления мелющих валков «промывкой» в условиях стационарного литья не удовлетворяет возросшим требованиям пищевого машиностроения по качественным и экономическим характеристикам.
- Определено перспективное направление в производстве биметаллических мелющих валков способом центробежного литья с горизонтальной осью вращения путем последовательной заливки металла рабочего слоя и сердцевины, позволяющее гарантировать их эксплуатационные свойства на уровне лучших мировых показателей.
- Выявлены проблемные вопросы по унификации конструктивных элементов центробежнолитых мелющих валков, в частности возможности перехода на серийное изготовление валков с полой бочкой для мельниц отечественного производства.
Из представленных выводов вытекают цель и задачи настоящей работы.
Глава П. МЕТОДИКА ИССЛЕДОВАНИЯ
2.1 Объект иссле
дования и общие методические положения работы
В соответствии с поставленной в работе целью объектом исследования являлись наиболее распространенные в пищевом машиностроении мукомольные валки с диаметром бочки 0,26 м и длиной 1 м.
Учитывая, что технические требования к мелющим валкам, используемым в пищевой промышленности, по основным параметрам — твердости металла рабочего слоя, его структуре, толщине рабочего слоя, составу металла рабочего слоя и сердцевины, а также размерам практически совпадают, допустимо распространить полученные результаты, касающиеся технологии изготовления бочек мукомольных валков.
Изготовление мукомольного валка, также как и всех других мелющих валков, состоит из ряда последовательных операций, которые заключаются в следующем [3, 39]:
- отливка двухслойной бочки валка;
- первичная механическая обработка бочки с внешней и внутренней поверхности и вырезка кольцевого темплета для определения качества металла у противоположного от начала заливки торца;
- механическая обработка бочки с расточкой торцевой поверхности под запрессовку полуосей;
- запрессовка полуосей;
- механическая обработка полуосей и шлифовка бочки;
- балансировка валка;
- нанесение микрошероховатости на поверхности бочки валка.
Отливку бочки валков осуществляли в условиях литейного цеха ООО «Орловский литейный завод имени Медведева». Чугун для отливки валков получали соответственно из индукционных тигельных печей емкостью ИCT-0.4.
Из печей чугун выпускали в ковш и передавали в заливочное отделение участка центробежного литья.
Для отливки валков использовали центробежные машины конструкции ЦНИИТМАШ (рис. 2.1).
Заливку осуществляли с помощью заливочного устройства, которое состоит из чаши и литниковой воронки, укрепленных на поворотном кронштейне.
Рабочий слой необходимого состава заливали во вращающуюся форму, строго контролируя его массу для получения необходимой толщины слоя.
Контроль массы заливаемого металла осуществлялся с помощью тензометрических весов марки KGW 5 с точностью показаний ±0,1%.
Первичная механическая обработка бочки валка и отрезка темплета для исследования качества металла производилась на токарном станке.
Толщина вырезанного темплета составляла 0,01 м, а расстояние от торца бочки до вырезаемого места 0,05 м.
Механическая обработка бочки и расточка отверстий под запрессовку цапф осуществлялась на токарных и расточных станках.
Для валков типа А1-БЗН диаметр отверстия под расточку составляет 0,16 м, а глубина 0,2 м с обеспечением необходимой точности размеров с допусками под прессовую посадку для последующей запрессовки цапф.
Запрессовка цапф осуществлялась в холодном состоянии на прессе (модель П6736 объединения «Прессмаш»).
В качестве материала полуосей использовалась сталь марки 45 (ГОСТ 1050-88) или сталь марки 40Х (ГОСТ 4543-71) с твердостью после термообработки HRC = 31.. .36.
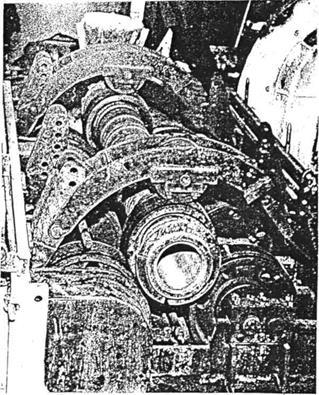
Рисунок 2.1 - Опытная центробежная машина на литейно-металлургической базе ЦНИИТМАШ
2.2 Мет
оды исследования структуры и физико-механических свойств металла отливок
Металлографические исследования проводили на образцах, взятых из темплета, вырезанного в поперечном направлении бочки валка на расстоянии 50 мм от ее торца.
Анализ микроструктуры рабочего слоя и сердцевины валка производили, применяя оптическую и электронную микроскопию на установках МИМ-8 и «Тесла», с помощью которых определяли количество и распределение структурных составляющих, а также дисперсность продуктов распада аустенита.
Дисперсность перлита оценивали по ГОСТ 3443-87.
Твердость металла рабочего слоя и сердцевины валка определяли на образцах, взятых из темплета, вырезанного в поперечном сечении бочки валка.
Твердость чугуна определялась через каждые 5 мм от внешней поверхности мелющего валка.
Твердость определяли на приборе Бринеля при нагрузке 29400 Н путем вдавливания шарика диаметром 0,01 м (ГОСТ 9013-59), а затем представляли по переводным таблицам (Приложение 1) в значениях HSD.
Наряду с этим использовали электронный переносной твердомер ТЭМП-2 на базе микропроцессора конструкции ФГУП «ЦНИИТМАШ» для оценки твердости металла мелющих валков [36].
Для качественной оценки прочности сваривания рабочего слоя металла и металла сердцевины мелющих валков было использовано приспособление, разработанное в ЦНИИТМАШ (рис. 2.2) [34,36].
В корпус установки (1) помещается вырезанный из биметаллического валка темплет (3), который усилием пуансона (2) продавливается.
По характеру излома темплета можно судить о качестве сваривания двух металлов.

Рисунок 2.2 - Схема устройства для оценки прочности, сваривания двух слоев металла
1 - корпус, 2 - пуансон, 3 - темплет, вырезанный из бочки двухслойного валка
Литейные свойства хромоникелевого чугуна для рабочего слоя валков определялись на специальных приборах и пробах.
Линейная усадка для рабочего слоя определялась на приборе конструкции ЦНИИТМАШ, позволяющем регистрировать процесс усадки с изменением температуры. Запись полученных характеристик производилась на электронном потенциометре ЭПП-04.
Жидкотекучесть хромоникелевого чугуна для рабочего слоя валков определялась с помощью специальной пробы [38].
Выплавку чугуна производили в индукционных печах с использованием стандартных отечественных шихтовых материалов.
Графитизирующее модифицирование осуществляли с применением ферросилиция (FeSi 75%).
Замеры температуры перед выпуском из печи и перед заливкой в центробежную машину осуществляли платино-платинородиевыми термопарами.
Содержание элементов в чугуне определяли рентгеноспектральным, спектральным и химическим методами.
Выв
оды по главе 2
- Разработаны расчетные и экспериментальные методы определения интенсивности охлаждения и продолжительности затвердевания рабочего слоя мелющих валков в условиях поля центробежных сил.
- Использованы методы определения прочности сваривания двух металлов - рабочего слоя и сердцевины, позволяющие давать надежную оценку состояния металла в граничной области их соединения.
Использованы различные, в том числе современные методы термографического анализа металла рабочего слоя валка, определения химического состава, структуры металла и др., позволяющие оценить влияние технологических параметров на однородность структуры, глубину рабочего слоя, механические и эксплуатационные свойства валков.
Глава
III
. ИССЛЕДОВАНИЕ ОСОБЕННОСТЕЙ ФОРМИРОВАНИЯ БИМЕТАЛЛИЧЕСКИХ ЗАГОТОВОК ВАЛКОВ В ПОЛЕ ДЕЙСТВИЯ ЦЕНТРОБЕЖНЫХ СИЛ
3.1 Иссле
дование особенностей процесса затвердевания отливки в массивной изложнице
Значительная часть свойств отливки формируется в процессе затвердевания металла, т.е. перехода его из жидкого состояния в твердое.
На процесс затвердевания отливки оказывают влияние множество факторов, таких как свойства металла и формы, зазор между ними, режим течения металла, интенсивность охлаждения и др.
Учет этих факторов настолько затрудняет общее решение процесса затвердевания, что большинство авторов прибегает к ряду упрощений, например, выделению частных условий литья, когда пренебрегают второстепенными факторами, оставляя решающие из них [43, 45].
В нашем случае наиболее общими признаками классификации литья являются относительные геометрические характеристики системы «отливка-зазор-форма» (рис. 3.1).
Их выбор обусловлен особенностями аккумулирующей способности отдельных элементов этой системы.
Аккумулирующая способность предопределяет то количество теплоты, которую приобретает тело (или потеряет) при изменении его температуры и зависит от массы тела и его теплоемкости.
В работе [43] предлагается при оценке свойств отдельных элементов системы заменить точное значение аккумулирующей способности отливки, зазора и формы их массой, объемом или другими геометрическими характеристиками.
В качестве определяющего размера выделим толщину цилиндрической отливки (рис. 3.2):
Xx
=
R
-
r
(3.1)
где R- наружный радиус отливки, м;
r- внутренний радиус отливки, м.

Рисунок 3.1 - Схема распределения температур в системе «отливка-форма»
Толщину зазоров обозначим:
Хпок
. и Хгаз
где Хпок
. - толщина покрытия, м;
Хгаз. - толщина газовой прослойки. Толщина стенки изложницы Х2:
где Rвнешн.изл. - внешний радиус изложницы, м; rвнугр.изл. - внутренний радиус изложницы, м.
В нашем случае используется массивный кокиль (Х2 = 0,14 м, масса 11613 н), аккумулирующая способность которого соизмерима с аккумулирующей способностью отливки.
При этом часть выделившегося тепла при затвердевании отливки будет аккумулирована изложницей, а часть потеряна в окружающую среду.
При рассмотрении данной задачи вносится допущение о пренебрежении количеством теплоты, аккумулированной зазором между отливкой и формой, ввиду ее небольшой величины, при обязательном учете аккумулирующей способности изложницы и потерями тепла в окружающую среду.
Особенность теплового взаимодействия системы «отливка-форма» с учетом превалирующего значения аккумулирующей способности отливки и изложницы заключается в том, что окружающей средой в данном случае для отливки является зазор, т.е. отливка отдает тепло в зазор, как в окружающую среду, а форма прогревается теплом от зазора, играющего роль окружающей среды.
В этом случае процесс затвердевания отливки и прогрева изложницы можно рассматривать как два независимых процесса.
Связь между температурными полями отливки и изложницы в этом случае может осуществляться через среднюю калориметрическую температуру системы tk (рис. 3.3).
Значение средней калориметрической температуры (tK
) определяется из уравнения теплового баланса, в котором приравнивается количество теплоты, потерянной отливкой при ее охлаждении от температуры заливки (tjM
.) до температуры tk и количеством теплоты, приобретенной изложницей при ее нагреве от начальной температуры до температуры tk
[43]:
где G1 - масса отливки, н; G2 —
масса изложницы, н;
C1 - удельная теплоемкость металла отливки, Дж/кг-°С;
С2 - удельная теплоемкость металла изложницы, Дж/кг-°С
В реальных условиях литья внешняя поверхность изложницы охлаждается водой (или воздухом), теряя с наружной поверхности количество тепла Q0
Kp
..
Потери тепла изложницей в окружающую среду Q0
Kp
. можно определить из уравнения теплового баланса:
где d3
- коэффициент теплоотдачи в окружающую среду;
t
2 -
температура внешней поверхности изложницы;
tокр. - температура среды, окружающей изложницу;
С- МИН
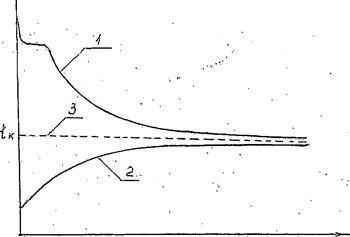
Рисунок 3.2 - Кривые охлаждения отливки - 1 и массивной изложницы - 2, 3 - средняя калориметрическая температура системы F2 - площадь наружной поверхности изложницы, м
Указанная температура используется для оценки затвердевания отливки и прогрева формы.
Для полной оценки теплового состояния отливки и изложницы необходимо знание коэффициента теплоотдачи в зазоре, который находится с учетом термического сопротивления зазора между отливкой и изложницей.
Удельный тепловой поток через зазор составит:
Вт/м2
(3.13)
Это выражение можно представить в преобразованном виде:
Вт/м2
(3.14)
Вт/м2
(3.15)
где - коэффициент теплоотдачи через зазор, Вт/м -°С;
- условный коэффициент теплоотдачи на внешней поверхности отливки, Вт/м2
-°С;
- условный коэффициент теплоотдачи на внутренней поверхности изложницы, Вт/(м2
-°С).
Значение коэффициента равно /43/:
Представленное выше выражение (3.12) по определению средней калоритмической температуры позволяет оценить тепловое состояние толстостенной отливки, какой в нашем случае является бочка мелющего валка, затвердевание которой осуществляется в массивной изложнице, аккумулирующая способность которой является превалирующей по сравнению с теплоотдачей в окружающую среду.
Указанная способность позволяет с большой достоверностью оценить тепловое состояние отливки с учетом особенностей теплообмена в зазоре между отливкой и изложницей или термического сопротивления зазора, а также коэффициентов теплоотдачи на внешней и внутренней поверхности изложницы.
С учетом полученных зависимостей представляется возможным приступить к определению продолжительности и кинетики затвердевания рабочего слоя бочки мелющих валков.
3.2 Опре
деление кинетики затвердевания рабочего слоя валков
Оценка продолжительности и скорости затвердевания рабочего слоя валков в массивной изложнице необходима для определения временного интервала между окончанием затвердевания рабочего слоя металла и началом заливки металла внутреннего слоя валка, а также ее влияния на физико-механические свойства металла.
Для расчета продолжительности затвердевания бочки валка в поле действия центробежных сил примем следующие значения геометрических и теплофизических параметров [38...40].
Размеры и масса:
di - внешний диаметр заготовки 0,26 м
dj - внутренний диаметр рабочего слоя 0,18 м
di - внутренний диаметр заготовки 0,08 м
L - длина заготовки 1,2 м
Gj - масса металла рабочего слоя 2391 н
Gj - масса металла заготовки 4214 н
Fj - поверхность охлаждения 1,1 м2
D2
- внешний диаметр изложницы 0,504 м
D2
- внутренний диаметр изложницы 0,264 м
G2
- масса изложницы 11613 н
ХП
ок - толщина теплоизоляционного покрытия 0,002 м
Термофизические коэффициенты:
Yi - удельный вес чугуна (жидкого) 68600 н/м
С - удельная теплоемкость жидкого чугуна 837,4 Дж/кг-°С
Ci - удельная теплоемкость материала отливки 753,6 Дж/кг«°С
С2
- удельная теплоемкость материала изложницы 481,5 Дж/кг-°С
X
- коэффициент теплопроводности отливки 37,21 Вт/м«°С
Xпок. - коэффициент теплопроводности покрытия 0,7234 Вт/м-°С
р - удельная теплота кристаллизации 267929 Дж/кг.
Температуры:
Lикв. - температура ликвидус 1270°С
W-
температура солидус 113 0°С
t2
- начальная температура изложницы 180°С
W ~ температура заливки чугуна 1350°С
Рабочий слой мелющего валка из хромоникелевого чугуна с химическим составом:
С = 3,2...3,4%, Si = 0,35...0,45%, Мп = 0,5...0,6%, S < 0,10%, Р < 0,15%, Сг = 0,3...0,4%, Ni = 0,6...0,8%.
Внутренняя поверхность изложницы покрывается теплоизоляционной смесью, состоящей из кварцевого песка марки КО 16 в количестве 95% и связующей смолы СФП-011Л в количестве 5%.
Продолжительность затвердевания рабочего слоя бочки валка (т) состоит из трех периодов:
т = т1
+т2
+т3
сек. (3.20)
где m1 - период заливки металла, сек;
m2 - период отвода теплоты перегрева, сек; mз - период затвердевания металла, сек.
Первая стадия формирования определяется продолжительностью течения металла, которая из практических данных соответствует времени m1 = 0,15 сек.
Во второй стадии, благодаря естественной конвекции, температура металла по сечению жидкого металла выравнивается при незначительной интенсивности охлаждения.
В этом случае величиной газового зазора можно пренебречь.
Продолжительность отвода теплоты перегрева х2
определяется по формуле [43]:
после подстановки исходных данных получим:
2391-837,4(1350-1270)
9,8-1,1-361,7(1350-407)
При этом интенсивность охлаждения отливки составляет:
Третья стадия охлаждения отливки (затвердевание) характеризуется образованием газовой прослойки между нею и формой.
Толщина газового зазора определяется из выражения /43/:
где ат
-
коэффициент линейного расширения твердого металла 1/°С;
tкр-температура кристаллизации, °С.
Примем для чугуна значение ат
=
10 • 4 • 10"* 1/°С.
Температура tKp
определится из выражения:
Величина tK
определяется по формуле (3.12) при Q0
Kp
= О
Произведем оценку влияния внешнего охлаждения Q0
Icp
изложницы на величину tK
=3,14x0,504x1,2 = 1,9м2
где - коэффициент теплоотдачи на внешней поверхности изложницы, вращающейся в воздушной среде, Вт/(м • °С)
Значение В = 2,4 при температуре стенки изложницы 180°С определяем из графика [25]
W = окружная скорость - 16 м/сек
Таким образом, эффект от внешнего охлаждения массивной изложницы практически ничтожен (0,4%), вследствие малой интенсивности теплообмена на ее наружной поверхности.
После подстановки найденных значений в формулу (3.22) получим: Хгаз
=10,4-10-6
(1200-552)-0,13 = 0,0008м.
Образование газового зазора толщиной 0,0008 м соответствует температуре металла, равной 552°С. В процессе охлаждения отливки величина газового слоя изменяется от нуля до найденного значения 0,0008 м. Поэтому средняя за процесс величина газового слоя может быть приближенно принята равной 0,0004 м.
Учитывая, что в поле действия центробежных сил усадка отливки затруднена [50], примем в расчетах (при = 100) величину газовой прослойки равной 50% от расчетной, т.е. Х^. = 0,0002 м.
Значение составляет 0,058 Вт/(м2
°С).
Величина Bi = 0,174 соответствует средней интенсивности теплообмена, поэтому продолжительность затвердевания отливки в нашем случае можно определить с помощью разности критериев Фурье [43]:
где — толщина затвердевающей зоны по сечению отливки, м;
- толщина жидкой зоны, м;
а
= коэффициент температуропроводности, {а
= 10,6 • Ю-6 м2
/сек ) /43/. Принимая значения = 1 при полном затвердевании отливки и 0 при отсутствии жидкой фазы, получим:
Таким образом величина т3
= 255 + 44 = 299 сек, а с учетом продолжительности заливки (г = 15 сек) общая продолжительность затвердевания рабочего слоя бочки валка составит 314 сек (5,23 мин).
Наряду с расчетным методом оценки продолжительности затвердевания рабочего слоя валков в работе использовали экспериментальный метод путем погружения жидкого свинца во вращающуюся форму с затвердевающим металлом.
Опыты проводили на центробежной машине конструкции ЦНИИТМАШ на отливках с внешним диаметром 0,26 м и внутренним 0,12 м.
Заливка металла рабочего слоя валка производилась при частоте вращения формы, соответствующей гравитационному коэффициенту = 100.
Температура заливки составляла 1350°С, продолжительность заливки металла ~ 15 сек. Толщина теплоизоляционного покрытия составляла 0,001, 0,002 и 0,003 м.
Свинец нагревали до 600...650°С и путем его ввода во вращающуюся форму заливали в кристаллизующийся металл в три приема через определенный интервал времени.
Масса заливаемого свинца составляла за один прием 1 кг.
После охлаждения отливки и ее извлечения из формы ее разбивали на копре и на изломах производили замеры расстояния полосок свинца от внешней поверхности.
На рис. 3.9 показано, что свинец, введенный через 1,3; 2,5 и 3,8 мин в процессе затвердевания отливки с теплоизоляционным покрытием толщиной 0,002 м четко фиксирует границы затвердевания металла на расстоянии 0,015, 0,026 и 0,034 м от внешней ее поверхности.
Аналогичным образом проведены опыты по определению продолжительности затвердевания рабочего слоя валка с использованием теплоизоляционного слоя толщиной 0,001 и 0,0035 м.
Результаты экспериментальных данных, полученных при использовании ввода свинца во вращающуюся форму для оценки кинетики затвердевания рабочего слоя валка при различной толщине теплоизоляционного слоя приведены в табл. 3.4 и на рис. ЗЛО.
На рис. 3.10 также обозначены расчетные данные по продолжительности затвердевания рабочего слоя отливки.
Анализ полученных результатов свидетельствует о близкой сходимости расчетных и экспериментальных данных, что позволяет с высокой степенью надежности пользоваться расчетными методами для определения временных параметров интервала между заливками двух металлов.

Рисунок 3.9 -Поперечный излом стенки отливки с прослойками свинца после его ввода через 1,3; 2,5 и-3,8 мин.
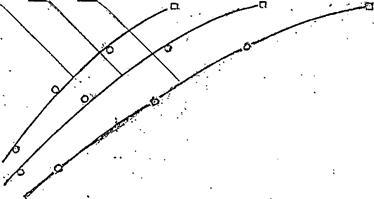
Рисунок 3.10 – Кинетика затвердевания рабочего слоя валка при различной толщине теплоизоляционного покрытия
Таблица 3.4 - Влияние толщины слоя покрытия на скорость затвердевания рабочего слоя валка
Толщина слоя теплоизоляционного покрытия,
м
|
Граница
кристаллизации
от внешней поверхности
отливки,м
|
Продолжи-тельность
нарастания твердой корки металла, мин
|
Линейная
скорость
затвердевания,
мм/мин
|
Средняя
скорость
затвердевания,
мм/мин
|
0,001 |
0,018 0,026 0,034 0,040 |
1,3 2,0 2,8 3,8 |
13,8 13,0 12,0 10,5 |
10,52 |
0,002 |
0,015 0,026 0,034 0,040 |
1,3 2,5 3,8 5,2 |
11,5 10,4 9,0 7,7 |
7,65 |
0,0035 |
0,015 0,025 0,033 0,040 |
2,0 3,5 5,0 6,8 |
7,5 7,2 6,6
6,9 |
5,88 |
Таким образом с помощью расчетного метода определена и экспериментально подтверждена кинетика и общая продолжительность затвердевания рабочего слоя валка, а также зависимость теплообменных процессов в системе «отливка - зазор - изложница» от толщины и свойств теплоизоляционного слоя на внутренней поверхности изложницы.
Выбранный интервал толщины теплоизоляционного покрытия 0,001...0,0035 м является наиболее характерным для отливки бочки пищевых валков, а полученные при этом закономерности позволяют в дальнейшем устанавливать взаимосвязи между кинетикой затвердевания и свойствами металла для последующего определения технологических параметров литья.
3.3 Влияние ск
орости затвердевания на свойства металла рабочего слоя валков
Влияние скорости затвердевания на качество чугунных отливок является одним из решающих факторов технологического процесса.
Для рабочего слоя валка наиболее характерным является изменение его структуры и твердости под влиянием различной скорости затвердевания металла, которая для массивных изложниц в основном зависит от толщины слоя покрытия.
Исследования проводились на трех отливках, полученных при одинаковых температурах заливки металла с толщиной слоя покрытия 0,001, 0,002 и 0,0035 м.
Влияние толщины покрытия и скорости затвердевания отливки на твердость металла, глубину отбеленного слоя и его структурные характеристики представлены в таблице 3.5 и на рис. 3.11. Твердость и характеристики микроструктуры определялись на расстоянии 0,005 м от поверхности отливки.
Величина средней скорости по расчетным и экспериментальным данным составляет 10,52, 7,65 и 5,88 мм/мин соответственно толщине слоя теплоизоляционного покрытия 0,001, 0,002 и 0,0035 м.
Таблица 3.5 — Влияние скорости затвердевания на твердость и структуру металла
№ плавок |
Толщина слоя покрытия, м |
Средняя скорость затвердевания,
мм/мин
|
Глубина
отбеленного
слоя, м
|
Твердость, HSD |
Характеристика микроструктуры |
1050 |
0,001 |
10,52 |
0,030 |
73,71,74 |
В/бейнит, н/бейнит,
троостит,
цементит 47%,
зерно мелкое
|
1063 |
0,002 |
7,65 |
0,025 |
70,68,69 |
В/бейнит, н/бейнит,
троостит,
цементит 40%,
зерно мелкое
|
1071 |
0,0035 |
5,88 |
0,012 |
64, 62,63 |
В/бейнит, троостит, цементит 20%, зерно крупное |
Анализ полученных результатов свидетельствует о том, что с понижением скорости затвердевания падает твердость рабочего слоя, уменьшается глубина отбеленного слоя и ухудшаются характеристики микроструктуры металла.
С повышением средней скорости затвердевания металла рабочего слоя валка величина твердости, при толщине слоя в 0,002 м, принимает значения, удовлетворяющие техническим условиям (68...71 HSD).
При значениях средней скорости, соответствующей толщине слоя 0,001 м, твердость металла приближается к верхним значениям технических условий, а при толщине слоя 0,0035 м - к нижним, поэтому наиболее приемлемой в плане стабильного получения нужной твердости является толщина слоя 0,002 м.
При уменьшении скорости затвердевания структура металлической матрицы заметно грубеет. Включения цементита и перлита становятся крупнее. При этом общее количество цементита уменьшается: так, если при толщине покрытия 0,001 и 0,002 м, количество свободного цементита составляет 47 и 40% соответственно, то при толщине слоя покрытия 0,0035 м - 20%.
Для удовлетворения необходимой твердости и глубины отбеленного слоя рабочего слоя валка наиболее приемлемой является скорость затвердевания, соответствующая толщине слоя покрытия 0,002 м.
Выводы по 3 главе
1. Установлено, что течение жидкого металла во вращающейся форме имеет турбулентный характер, а параметры потока зависят от частоты вращения формы и линейной скорости нарастания толщины его слоя.
2. Показано, что на структуру отливки влияет продолжительность приобретения металлом частоты вращения равной частоте вращения формы.
3. Чем продолжительнее этот процесс, тем грубее микро- и макроструктура чугуна, тем больше вероятность образования дефектов на стыке металла рабочего слоя и сердцевины валка.
3. Показано, что для удержания в круговом вращении большого по толщине слоя жидкости требуются более высокие скорости вращения, а с увеличением гравитационного коэффициента до значений 100...110 на внутренней поверхности рабочего слоя толщиной 0,026...0,050 м продолжительность выравнивания угловых скоростей жидкости и формы минимизируется.
4. Установлено, что при боковой заливке жидкости выравнивание угловых скоростей потока с толщиной слоя 0,026...0,050 м и формы сокращается на 20...25% по сравнению с продольной заливкой.
5. Экспериментально и расчетным методом определена скорость затвердевания рабочего слоя мелющих валков из хромоникелевого чугуна в условиях теплоотвода через массивную изложницу, полностью аккумулирующую тепло отливки.
6. Показано влияние толщины теплоизоляционного покрытия на внутренней поверхности изложницы и скорости затвердевания металла на его твердость, глубину отбеленного слоя и структурные характеристики чугуна.
Глава
IV
. ИССЛЕДОВАНИЕ И РАЗРАБОТКА ТЕХНОЛОГИИ ИЗГОТОВЛЕНИЯ ЗАГОТОВОК МЕЛЮЩИХ БИМЕТАЛЛИЧЕ
СКИХ ВАЛКОВ
4.1 Иссле
дование и выбор параметров формы для отливки мелющих валков
Вращающаяся форма, в которой происходит заливка и распределение металла, его затвердевание и формирование основных свойств заготовки, является определяющим звеном технологического процесса получения двухслойных заготовок.
Форма состоит из изложницы с крышками и теплоизоляционного покрытия на ее внутренней поверхности и функционально связана с заливочным устройством, предопределяющим расходные и термовременные характеристики вводимого в нее расплава.
От состояния каждого из элементов формы, их теплофизических и геометрических характеристик зависит характер распределения металла, интенсивность его охлаждения и, в конечном счете, основные свойства изделия.
Поэтому выбору материала и геометрических размеров формы в работе придается первостепенное значение.
В отличие от применяемых для производства трубных заготовок тонкостенных изложниц с интенсивно охлаждаемой внешней поверхностью, при отливке валков широко используются толстостенные изложницы, соизмеримые по массе и размерам стенок с ее бочкой [21.. .25].
Как показано в главе 3 теплообмен между отливкой и массивной изложницей принципиально отличается от теплообмена при тонкостенной изложнице, играющей роль передатчика тепла от отливки в окружающую среду, а при массивной изложнице она играет роль аккумулятора выделяемого отливкой тепла.
Поэтому с учетом соизмеримости толщины стенки мелющих валков в пределах 0,09...0,11 м с толщиной стенки изложниц для последних она составляет 0,10...0,13 м.
Длина изложницы увеличивается по сравнению с длиной бочки валка на 20% в связи с необходимостью вырезки темплета толщиной ~ 0,015 м в поперечном сечении бочки для определения твердости и структуры металла, а также удаления дефектного металла со структурой торцевого эффекта.
Таким образом, длина изложниц составляет 1,2 /, где / - длина бочки валка.
В качестве материала изложниц рекомендуется сталь марки 35Л, подвергнутая термообработке по режиму гомогенизирующего отжига /31/:
- нагрев до 880...900°С со скоростью 50...60°С/ч, выдержка при этой температуре (5 мин на 1 мм сечения);
- охлаждение с печью до 200°С;
- охлаждение на воздухе.
Эксплуатационная стойкость стальных изложниц достигает 260...290 наливов.
4.2 Оптимизация состава и способа нанесения теплоизоляционного покрытия на внутреннюю поверхность изложницы
Использование широко применяемого на практике метода покрытия внутренней поверхности изложницы сыпучими теплоизоляционными покрытиями в виде кварцевого песка [17, 18, 45], наряду с преимуществами -простота ввода во вращающуюся форму и его распределения в ней, имеет ряд существенных недостатков, основным из которых является наличие пригара на поверхности отливки, засорение песком материала отливок и появление неровностей на их поверхности, что отрицательно сказывается на качествo заготовок.
Поэтому в работе рассмотрена возможность использования в качестве теплоизоляционного покрытия тех же сыпучих материалов (кварцевый песок), но со связующими добавками, например пульвербакелита, представляющего собой смесь размолотой новолачной смолы с уротропином, которая при нагреве превращается в резольную быстротвердеющую смолу.
Необходимая для спекания пульвербакелита температура изложницы составляет 200...220°С и обеспечивается за счет тепла ранее отлитой заготовки валка, а для начальной плавки за счет подогрева изложницы в термопечи.
Для определения необходимой толщины отвердевающего покрытия на внутренней поверхности изложницы исходили из условий, обеспечивающих получение отливок необходимой твердости и структуры, а также без литейных дефектов типа трещин, спаев и неслитин.
Для выполнения указанных условий одним из основных требований к покрытию является обеспечение возможности распределения во время заливки металла во вращающейся форме без существенных тепловых потерь, т.е. покрытие должно обладать таким термическим сопротивлением, при котором продолжительность отвода теплоты перегрева была бы больше, чем продолжительность заливки металла рабочего слоя валка.
Продолжительность заливки металла рабочего слоя валка диаметром бочки 0,25x1,0 м массой 2391 н составляет 15 сек, что соответствует скорости заливки 160н/сек.
Продолжительность отвода теплоты перегрева в зависимости от термического сопротивления покрытия, а, следовательно, и толщины ее слоя определяли по формуле (3.21), представленной в главе 3.
Исходные данные для расчета составляли:
d = 2391 н, Ci = 837,4 дж/(кг-°С), U = 1350°С, tmK
= 1270°С, F, = 1,1 м2
,
tK
= 407°C.
Величину коэффициента теплоотдачи определяли применительно к различным толщинам покрытия:
X, = 0,001 м, Х2
= 0,002 м, Х3
= 0,003 м и Х4 = 0,004 м.
Соответственно коэффициент теплоотдачи для разных покрытий составляет:
После подстановки полученных данных в формулу (3.21) расчетное время отвода теплоты перегрева металла составит:
Xi = 22 сек, Тг = 44 сек, т3
= 66
сек, Т4 = 88 сек.
Представленные на графике данные (рис. 4.1) свидетельствуют о том, что толщина теплоизоляционного слоя должна находиться в пределах 0,0015...0,0025 м для гарантированного предотвращения от дефектов на поверхности отливки.
При меньших значениях толщины покрытия менее 0,0015 м продолжительность теплоотвода невелика и металл в процессе течения может затвердеть, образуя спаи.
Наряду с этим повышается твердость металла свыше значений 72 HSD, что приводит к скалыванию рифлей при их нарезке.
При значении толщины покрытия свыше 0,0025 м продолжительность отвода теплоты перегрева существенно возрастает и ухудшаются качественные характеристики металла бочек валка, при этом твердость рабочего слоя снижается ниже уровня технических требований (< 62 HSD). Поэтому выбор толщины слоя покрытия 0,002 м (среднее из крайних значений) представляется оптимальным.
Способ нанесения теплоизоляционного слоя на внутреннюю поверхность вращающейся формы, наряду с составом и толщиной теплоизоляционного покрытия, также предопределяет качество литья.
От способа ввода покрытия в изложницу зависит наличие неровностей на поверхности покрытия, а, следовательно, и на поверхности отливки, что ведет к неравномерному теплоотводу от отливки в окружающую среду, появлению неравномерной твердости, а также к повышению припуска на механическую обработку поверхности отливки.
Исследования, проведенные в настоящей работе, по определению качества поверхности теплоизоляционного материала на внутренней поверхности изложницы, заключались в изучении следующих параметров засыпки:
- частота вращения изложницы;
- направление засыпки по отношению к направлению вращения формы;
- длительность вращения формы с покрытием;
- длительность проворачивания пескосыпа с покрытием.
Опыты проводились с использованием вращающейся изложницы с горизонтальной осью вращения диаметром 0,28 м.
Нанесение теплоизоляционного покрытия на внутреннюю поверхность вращающейся изложницы осуществляли с помощью цилиндрического пескосыпа с прорезью по образующей для высыпания смеси.
Оценка состояния поверхности покрытия при различной частоте вращения изложницы приведена в табл. 4.1.
Анализ экспериментальных данных, представленных в табл. 4.1, показывает, что с повышением частоты вращения изложницы волнистость на поверхности покрытия уменьшается вследствие того, что длительность сдвига частиц при взаимодействии с поверхностью изложницы сокращается и при частоте вращения 700 об/мин и выше поверхность покрытия становится ровной.
Таблица 4.1 — Состояние поверхности покрытия при различной частоте вращения изложницы
Частота вращения, об/мин |
Гравитационный коэффициент |
Толщина слоя, м |
Состояние поверхности |
500 |
39 |
0,002 |
Волнистость (высота 0,001 м) |
600 |
56 |
0,002 |
Мелкие волны |
700 |
76 |
0,002 |
Ровная поверхность |
800 |
100 |
0,002 |
Ровная поверхность |
Направление засыпки по отношению к вращению формы (по ходу или против) также влияет на волнистость поверхности покрытия.
При засыпке песчаного покрытия против хода вращения изложницы, как показали опыты, волнистость увеличивается.
Длительность вращения изложницы с песчаным покрытием толщиной 0,002 м в течение 10, 20 и 30 мин не оказала влияния на состояние поверхности покрытия.
С увеличением длительности проворачивания пескосыпа с покрытием в течение 2, 5, 8 и 10 сек поверхность покрытия становится ровной при времени засыпки 8 сек и более.
Таким образом поверхность теплоизоляционного покрытия становится ровной при соблюдении следующих параметров засыпки:
- частота вращения формы > 700 об/мин;
- направление вращения пескосыпа - по ходу вращения изложницы;
- длительность проворачивания пескосыпа - > 8 сек.
Количество засыпок теплоизоляционного покрытия (к), производимого из пескосыпа на внутреннюю поверхность вращаемой изложницы, рассчитывали исходя из равенства объема покрытия необходимой толщины слоя (8) в изложнице и объема покрытия, подаваемого из пескосыпа с заданным диаметром (рис. 4.2):
Для практического удобства использования полученной формулы приравняем значение R
+
r
&
D
(D - внутренний диаметр изложницы), тогда выражение 4.2 примет вид:

1 - изложница, 2— теплоизоляционное покрытие, 3 - пескосып
Рисунок 4.2 - Схема засыпки теплоизоляционного покрытия на внутреннюю поверхность изложницы
4.3 Совершенств
ование конструкции заливочного устройства для отливки валков
Заливочное устройство для отливки валков выполняет важную функцию при формировании основных свойств заготовки и, прежде всего, обусловливает скорость заливки металла, температурный режим заливки и характер ввода металла в форму.
При изготовлении полых отливок значительное распространение получила конструкция заливочного устройства с коротким желобом и продольным сливом металла.
Исследования, проведенные в настоящей работе по распределению жидкости во вращающейся форме, показали, что применение подобных устройств сопряжено с рядом недостатков, вызывающих ухудшение качества отливки из-за разбрызгивания металла в месте падения струи. По этой причине происходит усиление окисления металла, местный разогрев формы и вызываемое этим явлением неравномерное охлаждение рабочего слоя валка и как следствие появление неоднородной структуры и различной твердости рабочего слоя на поверхности («пятнистость»).
Наряду с этим продольный слив металла во вращающуюся форму способствует замедлению перемещения металла вдоль формы из-за гашения скорости потока в месте падения струи.
Для исключения этих недостатков в работе предложен боковой слив металла через продольное отверстие в канале заливочной воронки по направлению вращения формы, что способствует плавному вовлечению металла во вращение без разбрызгивания.
Сравнительное исследование металла рабочего слоя валка при различных способах ввода металла во вращающуюся форму показали, что в случае боковой подачи металла твердость рабочего слоя по длине бочки мелющего валка остается практически постоянной в отличие от прямого ввода, при котором в зоне падения металла твердость снижается (табл. 4.2 и рис. 4.3).
Твердость определялась на расстоянии 5 мм от поверхности бочки валка.
Таблица 4.2 — Величина твердости металла рабочего слоя по длине бочки мелющих валков 0 0,25x1,2 м при разных способах ввода металла в форму
Способ ввода металла |
Твердость металла по длине бочки валка, HSD,
на расстоянии от заливочного
конца, м
|
0,2 |
0,4 |
0,6 |
0,8 |
1,0 |
Продольный |
68 69 68 |
65 65 65 |
64 65 64 |
68 67 68 |
68 67 68 |
Боковой |
69 70 69 |
69 69 68 |
68 70 69 |
68 69 70 |
68 68 70 |
Как видно из приведенных в таблице данных при использовании заливочного устройства с продольной подачей металла наблюдается снижение твердости металла рабочего слоя валка на 3...6 ед. HSD в зоне падения струи металла на расстоянии 0,4...0,6 м от заливочного конца, в то время как при боковом сливе металла изменение твердости незначительно.
Отмеченная особенность распределения твердости металла по длине бочки валка полностью соответствует характеру распределения температур по длине валка [30].
Таким образом, применение заливочного устройства с боковой подачей металла при заливке рабочего слоя валка наряду со спокойным сливом металла способствует стабилизации твердости металла рабочего слоя и, в конечном счете, повышению эксплуатационной стойкости мелющих валков.
4.4 Техн
ологический регламент вращения формы
Частота вращения формы является важным параметром технологического процесса, во многом предопределяющим свойства отливки.
При заниженной частоте вращения формы в отливках появляется рыхлота, «слоистость», структура становится неоднородной [34,40].
При повышенной частоте вращения формы возникают трещины, усиливается пригар на поверхности отливок, а также усиливается ликвация элементов по удельным весам и др. [45, 47].
Представленный в главе 1 анализ существующих формул для определения частоты вращения формы [44...47] показывает, что стремление к их универсальности не дает положительных результатов, так как многообразие технологических факторов, свойств материалов отливок и их размеров усложняет их применение.
В настоящем разделе для определения частоты вращения формы исходили из экспериментальных данных гидродинамического состояния жидкости во вращающейся форме, учитывающих процесс вовлечения слоя жидкости во вращение.
Опыты свидетельствуют о том (глава 3), что наиболее благоприятные условия формирования заготовок возникают в случае быстрого вовлечения металла до скорости вращения формы, что достигается при достаточно высоких значениях гравитационного коэффициента (К = 100... 110).
При указанных значениях гравитационного коэффициента структура металла становится более однородной, что благоприятно сказывается на его физико-механических свойствах.
В соответствии с этими данными определим частоту вращения формы (п) для рабочего слоя валка толщиной 0,04 м, для вовлечения которого с минимальным временем до скорости вращения формы требуется утяжеление (К) в 100 раз (рис. 3.4)
где г - внутренний радиус отливки, м.
Для формирования рабочего слоя заготовки бочки мукомольного валка, имеющего г = 0,09 м, частота вращения формы в соответствии с формулой (4.5) составит 1000 об/мин.
При заливке внутреннего слоя заготовки бочки валка с величиной г = 0,065 м частота вращения формы составляет п = 1176 об/мин.
Как показано в работе /103/ увеличение частоты вращения формы при заливке второго слоя металла способствует улучшению свариваемости двух разнородных металлов.
По окончании процесса затвердевания второго слоя металла частота вращения формы с целью снижения уровня вибрации и улучшения условий работы машины снижается до 800 и 400 об/мин.
4.5 Термовременны
е параметры режима заливки двух разнородных металлов в форму
При изготовлении биметаллических заготовок значительная роль отводится таким факторам как:
- температура заливки первого и второго металлов;
- продолжительность перерыва между заливками двух металлов;
- скорость заливки каждого из двух металлов;
- частота вращения формы при заливке двух металлов.
Нахождение зависимости между указанными параметрами для отливок определенной конфигурации позволяет определить пути получения высококачественных заготовок с прочным свариванием двух слоев металла.
В литературе приводятся примеры получения биметаллических чугунных заготовок, основанные на технологии, при которой заливка второго металла осуществляется на полностью затвердевший первый металл /30, 34/.
При этом рекомендуется производить заливку второго металла в момент понижения температуры внутренней поверхности первого металла на 120... 150°С ниже температуры его затвердевания [34].
Такая технология предусматривает использование флюса на внутренней поверхности первого металла, для защиты его от окисления, которое может стать причиной несваривания двух металлов.
Известно, что вводимый в полость формы флюс, наряду с положительным воздействием на жидкий металл, может явиться причиной его загрязнения неметаллическими включениями [33].
Учитывая сложности, связанные с применением флюса, в настоящей работе исследовали возможность заливки второго металла на поверхность еще не полностью затвердевшего первого слоя с возможностью их частичного перемешивания с созданием переходного слоя без применения флюса.
С этой целью после заливки из ковша металла рабочего слоя во вращающуюся форму и перерыва, соответствующего продолжительности перемещения границы затвердевания рабочего слоя до ее внутренней поверхности, производится заливка из того же ковша остатка жидкого металла, промодифицированного ФС-75, который, взаимодействуя с незатвердевшей твердожидкой фазой, образует прочную переходную зону.
Указанный режим порционной заливки двух металлов для формирования биметаллических заготовок требует строгого учета временных особенностей затвердевания чугуна во вращающейся форме, которые отражены в главе 3.
С учетом этих особенностей составлен совмещенный с режимом вращения формы график заливки двух металлов во вращающуюся форму применительно к наиболее распространенным мукомольным валкам с размерами бочки 0 0,25x1,0 м (рис. 4.4).
Основные операции процесса заливки металла в форму состоят в следующем:
- заливка рабочего слоя со скоростью 200 н/сек при температуре 1350°С±10°С;
- выдержка металла в форме в течение 5,2 мин., в течение которой граница рабочего слоя перемещается к ее внутренней поверхности (рис. 3.9);
- заливка второго металла в форму после модифицирования в ковше ФС-75 при температуре 1340°С± 10°С;
- выдержка металла в форме до полной ее остановки. Разработанный режим порционной заливки металла во вращающуюся форму обладает рядом технико-экономических преимуществ по сравнению с традиционным способом получения подобных биметаллических заготовок [30, 33,34]:
- упраздняется необходимость в работе второго металлургического агрегата по выплавке металла внутреннего слоя валка, так как его приготовление осуществляется путем модифицирования ФС-75 в ковше;
- устраняется необходимость в вводе флюса на поверхность рабочего слоя, залитого в форму;
- улучшаются экологические и технико-экономические показатели процесса за счет высвобождения трудозатрат, сокращения расхода материалов и электроэнергии на операции плавки второго металла, а также приготовления и хранения флюса.
4.6 Иссле
дование и выбор состава рабочего слоя мелющих валков
Особенности эксплуатации мелющих валков, рассмотренные в 1 главе, показали, что материал их рабочего слоя в процессе переработки зернопродуктов испытывает высокие нагрузки в сложных условиях абразивного износа, поэтому выбор необходимого состава чугуна является одним из основных факторов эффективности размольного процесса.
Выбор материала рабочего слоя бочки мелющих валков предусматривает оптимизацию их составов с учетом специфических условий их эксплуатации.
Анализ работы мелющих валков показывает, что из-за принципиального различия их функций при первичном дроблении (драные системы) и вторичном помоле (размольные системы) состав материала рабочего слоя должен различаться, вопреки существующей практике с использованием однотипного состава, что приводит к их повышенному износу.
Поэтому одним из требований к составу рабочего слоя мелющих валков является избирательный подход в зависимости от условий их эксплуатации.
В связи с определяющим влиянием твердости металла на служебные свойства валков выбор состава их материалов производили в основном с учетом этого фактора.
При этом учитывалась также необходимость создания однородной мелкодисперсной структуры отбеленного слоя бочки валка глубиной 0,020...0,025 м от его поверхности.
При первичном дроблении на валках с нарезанными рифлями в щелевой зоне между ними продукты переработки испытывают деформации сдвига-среза, а поверхностный слой валков значительные нагрузки, способствующие интенсивному износу материала валка.
Поэтому рабочий слой рифленых валков должен обладать сравнительно высокой твердостью, но при этом ее верхний предел не должен превышать значений 72 HSD, выше которых возникают трудности с нарезкой рифлей.
Нижний предел твердости рифленых валков должен гарантировать отсутствие графитовых включений в отбеленном слое с уровнем 66
HSD.
Таким образом оптимальная твердость рабочего слоя рифленых валков должна быть в пределах 66...72 HSD.
Анализ традиционно используемых составов рабочего слоя мелющих валков свидетельствует о широких пределах применения основных и легирующих элементов сплава [24]:
С = 3,0...3,8%, Si = 0,2...1,2%, Мп = 0,4...1,2%, Сг = 0,4...1,0%, Ni = 0,3...2,5%, Р < 0,4%, S < 0,2%.
Повышенное содержание углерода в рабочем слое валков с рифленой поверхностью в количестве 3,6...3,8% способствует увеличению твердости металла, а также понижению его вязкости и охрупчиванию материала, что ведет к выкрашиванию рифлей [30].
Понижение содержания углерода способствует проявлению в большей мере положительного эффекта при небольших добавках легирующих элементов .
Поэтому, наряду с понижением содержания углерода до значений 3,2...3,4%, необходимо принимать меры к увеличению вязкости материала рабочего слоя валка, чему способствует ввод никеля в количестве 0,7...0,9%.
Несмотря на то, что повышение содержания никеля ведет к образованию более дисперсной структуры и улучшению вязкости металла, что положительно сказывается на работоспособности рифленых валков, сочетание его с хромом, карбидообразующим элементом, свыше 1,0% каждого в отдельности, ухудшает отбеливаемость рабочего слоя [21], поэтому содержание хрома в пределах 0,3.. .0,5% может считаться рациональным.
Уровень содержания кремния в чугуне предпочтительнее удерживать в пределах 0,4...0,6%, так как при большем его количестве твердость металла рабочего слоя заметно снижается [30].
Для повышения дисперсности структуры металла вводили 0,1 ...0,3% Мо.
Таким образом, рекомендованный состав для рабочего слоя валков с рифленой поверхностью представляет в %:
С = 3,2...3,4; Si = 0,4...0,6; Мп = 0,4...0,6; Сг = 0,3...0,5; Ni = 0,7...0,9, S < 0,02; Р < 0,2; Мо = 0,1...0,3.
Выбор материала рабочего слоя мелющих валков с микрошероховатой поверхностью, работающих в размольных системах, производили с учетом специфических особенностей процесса их эксплуатации.
Изнашивание поверхности этих валков происходит под воздействием усилий, которые возникают при размоле продуктов, испытывающих деформации сдвиг-сжатие, т.е. при меньших нагрузках на валок по сравнению с драными системами помола.
Поэтому уровень предела твердости рабочего слоя этих валков ниже, чем в валках, используемых в драных системах, и составляет 62...65 HSD.
Наряду с указанными характеристиками твердости чугуна, решающее значение в процессе эксплуатации этих валков приобретает самовосстанавливаемость микрошероховатой поверхности рабочего слоя при ее изнашивании.
Отсутствие этого качества приводит к образованию полированной поверхности рабочего слоя валков, что сводит к нулю их способность к дальнейшему истиранию продуктов размола и они начинают работать в холостом режиме.
Для повышения самовосстанавливаемости микрошероховатой поверхности валков использовали специфическую способность фосфора к образованию легкоплавкой фосфидной эвтектики в виде сетки по границам зерен.
Чрезмерное повышение содержания фосфора (более 0,7%) ведет к охрупчиванию чугуна, поэтому рекомендуемый уровень составляет 0,5...0,7%.
Содержание углерода при требуемой твердости может быть снижено до 3,1... 3,3 л).
Некоторое повышение содержания кремния по сравнению с нарезными валками до 0,6...0,8% способствует образованию фосфидной эвтектики более компактной формы.
Содержание никеля по сравнению с валками, имеющими рифленую поверхность, может быть понижено до 0,5...0,7% в связи с отсутствием необходимости увеличения вязкости чугуна для нарезки рифлей.
Таким образом, рекомендуемый состав рабочего слоя валка с
микрошероховатой поверхностью представляет в %:
С = 3,1...3,3; Si = 0,6...0,8; Мп = 0,4...0,6; Сг = 0,3...0,4; Ni = 0,5...0,7; S < 0,02; Р = 0,5...0,7; Мо = 0,1...0,3.
В процессе всего цикла эксплуатации валков с рабочим слоем, содержащим включения фосфидной эвтектики, износ поверхности определяется различной способностью твердой и хрупкой (фосфидная эвтектика) и вязкой (металлическая основа) составляющих структуры чугуна к изнашиванию, в результате чего появляются выступы и впадины в виде микрошероховатости на поверхности бочки валка.
Для обеспечения более равномерного и компактного распределения фосфидной эвтектики в чугуне, а также повышения дисперсности его структуры рекомендуется ввод молибдена в количестве 0,1...
0,3%.
4.7 Эксперим
ентально-производственная отработка технологии отливки биметаллических валков методом центробежного литья
Для оценки качества мелющих валков, полученных по рекомендованной технологии, были отлиты три экспериментальных заготовки размером 0,26x1,2 м на установке центробежного литья с горизонтальной осью вращения.
Изучение макро- и микроструктуры, характер распределения твердости по сечению и длине отливки и показателей прочности сваривания двух слоев металла проводили на темплетах, вырезанных в трех поперечных сечениях заготовки, расположенных на расстоянии 0,25 м от ее торцев и по середине (рис. 4.5).
Механические свойства металла на растяжение, изгиб и износ определялись на образцах, вырезанных из рабочего слоя валка (рис. 4.6).
Твердость металла определяли через каждые 5 мм от поверхности заготовки бочки валка диаметром 0,25 м.
Химический состав металла рабочего слоя валков (плавочный) приведен в табл. 4.3.
Таблица 4.3 - Плавочный химический состав рабочего слоя валков
Способ
отливки
валка
|
Номер валка и плавки |
Химический состав, масс. % |
С |
Si |
Мп |
Р |
S |
Сг |
Ni |
Mo |
Центробежный |
1 2839 |
3,20 |
0,40 |
0,49 |
0,15 |
0,04 |
0,30 |
0,80 |
0,03 |
2 2847 |
3,10 |
0,53 |
0,36 |
0,15 |
0,05 |
0,33 |
0,77 |
0,03 |
3 2858 |
3,02 |
0,47 |
0,31 |
0,10 |
0,08 |
0,31 |
0,75 |
0,02 |
Исследование твердости центробежного и стационарного валков определяли по длине и глубине их рабочего слоя (табл. 4.4).

Рисунок 4.5 - Вид заготовок мукомольных валков с вырезанными темплетами
Анализ распределения значений твердости металла рабочего слоя свидетельствует о ее постоянстве от внешней поверхности бочки валка с последующим спадом (рис. 4.7).
Таблица 4.4 - Твердость металла рабочего слоя центробежнолитых заготовок
Способ
изготовления
бочки валка
|
Твердость (HSD) по глубине |
рабочего слоя, мм |
5 |
10 |
15 |
20 |
25 |
30 |
35 |
Центробежный |
70 |
70 |
70 |
70 |
69 |
54 |
44 |
68 |
68 |
68 |
68 |
67 |
50 |
42 |
61
|
67 |
67 |
61
|
66
|
46 |
38 |
При этом в центробежнолитой бочке постоянное значение твердости по глубине рабочего слоя сохраняется на расстоянии 0,025 м.
Это принципиальное отличие в распределении значений твердости в металле рабочего слоя свидетельствует о потенциальных возможностях увеличения долговечности центробежнолитых мелющих валков за счет повышения количества переточек в процессе эксплуатации.
Значения твердости по длине бочки свидетельствуют о минимальной разнице в 1...2 единицы HSD в центробежнолитой бочке. Твердость металла рабочего слоя мелющих валков определяется количеством и характером распределения карбидной фазы и структуры металлической матрицы.
Исследование количества и характера распределения цементита по сечению мелющего валка показало (рис. 4.8), что его количество в рабочем слое центробежного валка составляет 45%.
Внутренняя зона стационарного валка содержит около 10% карбидной фазы, а центробежного 1...2%, что создает благоприятные условия при расточке торцевых отверстий под посадку полуосей.
Электронно-микроскопические исследования позволили определить ряд особенностей в строении карбидной фазы в зоне чистого отбела, например, выявить сравнительно тонкую и плотную ее структуру в металле центробежной отливки и более грубую в металле стационарной отливки (рис. 4.9).
..
Рисунок 4.7 - Распределение твердости по сечению рабочего слоя валка о - центробежнолитые; Д – стационарнолитые

0,0/ 0,02 0,05 . 0,04, 0,05 0(
06 00
Расстояние от внешней поверхности
о - центробежнолитые; Л - стационарнолитые
Рисунок 4.8 - Распределение карбидной фазы по сечению валков
Исследования показали, что характер изменений структуры мелющих валков по их сечению соответствует особенностям распределения твердости материала рабочего и внутреннего слоя по протяженности и их уровню, который обеспечивается определенным содержанием карбидной составляющей (более 40%) в рабочем слое, дальнейшим его снижением в переходной зоне и сведением его до минимума во внутренней зоне.
Излом образца на рис. 4.10, полученный на поперечном темплете, свидетельствует о глубине отбела бочки центробежнолитого валка, который составляет 0,025 м и соответствует показателям твердости по сечению валка. Отбел на изломе характеризуется как чистый, включения графита практически отсутствуют (рис. 4.11, а, б).
Первые графитные включения в рабочей зоне валков появляются только на границе переходной (рис. 4.11, в) и внутренней зон (рис. 4.11, г). Макроструктура отливки бочки центробежнолитого валка приведена на рис. 4.12.
Снимок характеризует плотное строение металла без дефектов литейного происхождения, а также хорошую свариваемость рабочего и внутреннего слоев.
Микроструктура металла по сечению мелющих валков центробежнолитого и стационарнолитого валков представлена соответственно на рис. 4.13 и 4.14.
Отличительной особенностью этих структур является их видоизменение по сечению на протяжении трех зон:
- внешней с чистым отбелом и перлито-цементитной структурой (а) протяженностью 0,025...0,030 м (центробежнолитой) и протяженностью 0,008...0,012 м (стационарнолитой);
- переходной с перлито-цементито-графитной структурой (б) протяженностью 0,01...0,015 м (центробежнолитой) и 0,02...0,025 м (стационарнолитой);
- внутренней с перлито-графитной структурой (в).
Протяженность каждой из этих зон в сечении отливки валка является важной качественной характеристикой его служебных свойств. Установлено, что величина зоны чистого отбела определяет износостойкость валка, а переходная зона - сопротивление поломкам /21/.
В соответствии с критерием качества валков (Ак
) соотношение представленных зон имеет следующий вид /21/:
где А - глубина зоны чистого отбела, м; Б - глубина переходной зоны, м.
Центробежнолитые мелющие валки характеризуются величиной Ак
= 0,66...0,71, что является показателем их высоких служебных свойств по сравнению со стационарнолитыми (Ак
= 0,28...0,32) /119/, у которых они более чем в два раза ниже.
Наряду с изучением твердости и структуры металла образцы из исследуемых валков были подвергнуты механическим испытаниям.
Металл рабочего слоя мелющего валка подвергали испытанию на растяжение и изгиб, а также испытывали на износ.
На статическое растяжение подвергались исследованию стандартные цилиндрические образцы. Образцы вырезались из центральной части рабочего слоя валка.
Образцы на ударный изгиб (размером 10x10x60 мм) вырезались из средней зоны рабочего слоя валка. Результаты исследований механических испытаний образцов на изгиб и растяжение (среднее из трех значений) приведены в таблице 4.5.
Анализ полученных результатов исследования в таблице 4.5 показывает, что уровень механических свойств металла центробежнолитых валков на 20...25% выше уровня аналогичных свойств стационарнолитых валков.
Прочность сваривания двух разнородных металлов изучали на кольцевых темплетах толщиной 0,01 м, вырезанных из бочки валка в поперечном сечении, с помощью установки, представленной на рис. 2.4.
Таблица 4.5 - Показатели механических свойств мелющих валков
Способ
изготовления
валка
|
Вид
механических испытаний
|
Механические свойства на различном расстоянии от заливочной зоны валка, м |
0,2 |
0,6 |
1,0 |
Центробежно-литой |
Прочность на
разрыв ств
,
МПа
|
220 |
210 |
208 |
Сопротивление
при изгибе,
Стизг., МПа
|
400 |
390 |
387 |
Стационарно-литой |
Прочность на
разрыв ст
МПа
|
190 |
170 |
175 |
Сопротивление
при изгибе,
Стизг., МПа
|
315 |
290 |
300 |
Исследования проводили на прессе с усилием 3-104
Н до полного разрушения образцов с последующим изучением характера их разрушения.
Результаты исследований показывают, что изломы темплетов центробежнолитых валков проходят по металлу внутренней зоны отливки, не затрагивая граничной зоны двух слоев отливки, что свидетельствует о высокой степени их сваривания.
Выводы по главе 4
Установлено, что объемная подача металла должна обеспечивать продвижение жидкого слоя быстрее, чем осуществляется от него отвод тепла перегрева. Для валков диаметром бочки 0,25...0,35 м и длиной до 1,2 м подача металла при заливке должна составлять не менее 200 н/сек. Установлены термовременные параметры режима заливки в форму рабочего слоя и сердцевины валка (температуры заливки и перерыв между заливками), обеспечивающие их прочное сваривание в поле действия центробежных сил.
Показано, что использование на внутренней поверхности изложницы самотвердеющего теплоизоляционного покрытия с пульвербакелитовой смолой взамен сыпучего позволяет исключить на отливках появление поверхностных дефектов.
Установлено, что рекомендуемый слой теплоизоляционного покрытия толщиной 0,002 м и предлагаемый режим ввода покрытия во вращающуюся форму обеспечивает необходимую скорость затвердевания и равномерную толщину слоя по длине окружности формы, а также требуемую твердость и структуру металла. Установлено, что заливочное устройство с боковым сливом чугуна по ходу вращения формы сокращает период вовлечения слоя металла до скорости ее вращения на 20...25% и предотвращает смыв теплоизоляционного покрытия по сравнению с продольной заливкой металла.
Установлено, что при заливке второго металла в период достижения на внутренней поверхности рабочего слоя средней температуры интервала ликвидус-солидус, можно обеспечить прочное сваривание разнородных сплавов, тем самым, устраняя необходимость использования флюсов и второго металлургического агрегата для заливки внутреннего слоя.
Установлен режим вращения формы, позволяющий осуществить ввод металла при повышенном значении гравитационного коэффициента на внутренней поверхности отливки, позволяющий обеспечить условия для повышения физико-механических свойств заготовки валка, вследствие ускоренного выравнивания угловых скоростей металла и изложницы.
Показано, что рекомендованный химический состав рабочего слоя мелющих валков, учитывающий условия эксплуатации, соответствует специфическим условиям размольного процесса и способствует повышению их стойкости.
Выявлены существенные преимущества в физико-механических свойствах центробежнолитых валков (структура, твердость, распределение карбидной фазы, прочность на разрыв и изгиб, износ металла) по сравнению со стационарнолитыми валками, вследствие более плотного и дисперсного строения металлической структуры, которая достигается в условиях кристаллизации металла в поле действия центробежных сил.
4.4 Техн
ологический регламент вращения формы
Частота вращения формы является важным параметром технологического процесса, во многом предопределяющим свойства отливки.
При заниженной частоте вращения формы в отливках появляется рыхлота, «слоистость», структура становится неоднородной [34,40].
При повышенной частоте вращения формы возникают трещины, усиливается пригар на поверхности отливок, а также усиливается ликвация элементов по удельным весам и др. [45, 47].
Представленный в главе 1 анализ существующих формул для определения частоты вращения формы [44...47] показывает, что стремление к их универсальности не дает положительных результатов, так как многообразие технологических факторов, свойств материалов отливок и их размеров усложняет их применение.
В настоящем разделе для определения частоты вращения формы исходили из экспериментальных данных гидродинамического состояния жидкости во вращающейся форме, учитывающих процесс вовлечения слоя жидкости во вращение.
Опыты свидетельствуют о том (глава 3), что наиболее благоприятные условия формирования заготовок возникают в случае быстрого вовлечения металла до скорости вращения формы, что достигается при достаточно высоких значениях гравитационного коэффициента (К = 100... 110).
При указанных значениях гравитационного коэффициента структура металла становится более однородной, что благоприятно сказывается на его физико-механических свойствах.
В соответствии с этими данными определим частоту вращения формы (п) для рабочего слоя валка толщиной 0,04 м, для вовлечения которого с минимальным временем до скорости вращения формы требуется утяжеление (К) в 100 раз (рис. 3.4)
g
900-
g
v
J
откуда
n
=-
j
=
r
об/мин (4.5)
где г - внутренний радиус отливки, м.
Для формирования рабочего слоя заготовки бочки мукомольного валка, имеющего г = 0,09 м, частота вращения формы в соответствии с формулой (4.5) составит 1000 об/мин.
При заливке внутреннего слоя заготовки бочки валка с величиной г = 0,065 м частота вращения формы составляет п = 1176 об/мин.
Как показано в работе /103/ увеличение частоты вращения формы при заливке второго слоя металла способствует улучшению свариваемости двух разнородных металлов.
По окончании процесса затвердевания второго слоя металла частота вращения формы с целью снижения уровня вибрации и улучшения условий работы машины снижается до 800 и 400 об/мин.
Глава
V
. ПРОМЫШЛЕННОЕ ВНЕДРЕНИЕ ТЕХНОЛОГИИ ИЗГОТОВЛЕНИЯ БИМЕТАЛЛИЧЕСКИХ МЕЛЮЩИХ ВАЛКОВ
5.1 Вне
дрение разработанного технологического процесса производства мелющих валков в промышленных условиях
Промышленное внедрение технологии получения мелющих валков для пищевой отрасли (мукомольной, кондитерской, пивоваренной) осуществлялось в литейном цехе ООО «Орловский литейный завод им. Медведева».
Производство мелющих валков включает следующие технологические операции:
- плавка металла для получения двухслойной бочки валка;
- отливка двухслойных заготовок бочек валков на центробежной машине;
- механическая обработка бочек валка;
- механическая и термическая обработка полуосей;
- запрессовка полуосей с торцев бочки;
- окончательная механообработка валка;
- балансировка валка;
- нарезка рифлей или нанесение микрошероховатости на поверхности валков.
5.1.1 Плавка металла для получения двухслойной бочки валка
Плавка металла поверхностного рабочего слоя валка производится в индукционной тигельной печи промышленной частоты ИCT-0.4 предназначенной для получения жидкого литейного чугуна, как серого, так и легированного.
Печь обеспечивает интенсивное перемешивание металла с получением однородного химического состава и низкого угара элементов.
В качестве шихтовых материалов применяются:
- чушковый чугун по ГОСТ 805-80 марок Ш, П2, ПЛ1, ПЛ2;
- стальной лом, соответствующий ГОСТ 2787-86 марок 1А и 2А;
- лом (бой) валков из легированного чугуна;
- отходы и лом серого чугуна;
- ферросплавы и лигатуры для легирования и модифицирования чугуна: ферросилиций ФС75 ГОСТ 1415-93, ферромарганец ФМн 70-78 ГОСТ 4755-79, феррофосфор ФФ 14-18 по ТУ 14-5-72-80, феррохром ФХ 650-800А ГОСТ 4557-79, никель металлический Н-3, Н-4 ГОСТ 849-70.
При плавлении металлошихты в печи происходит угар и потери элементов, входящих в ее состав. Угар основных элементов в печи с кислой футеровкой в % от массы элемента в шихте составляет:
Углерод Кремний Марганец Хром
3-5 10-15 8-10 до 10
Общий угар при плавке чугуна в печи ИCT-0.4 не превышает 5-10% от массы шихты.
Все загружаемые в печь материалы должны быть сухими.
Загрузка печи проводится так, чтобы тигель был плотно заполнен шихтой, что позволяет сократить длительность плавки, обеспечить меньшую окисляемость металла, уменьшить износ тигля и потери электроэнергии.
После полного расплавления шихты при температуре металла в печи 1400°С производится отбор пробы на химанализ и производится доводка состава металла добавлением необходимого количества стали и ферросплавов.
Через 25...30 мин после присадки стали и ферросплавов производится отбор второй пробы на химанализ.
После получения результатов второго химического анализа производится корректировка состава присадкой ферросплавов в печь.
Химический состав базового металла на выпуске из печи должен соответствовать:
С = 3,2...3,4%, Si = 0,60...0,70%, Mn = 0,40...0,70%, P = 0,5...0,6%, S < 0,10%, Cr = 0,40...0,60%, Ni = 0,80...1,0%, Mo = 0,1...0,3%.
При температуре 1470°С ± 10°С производится отливка технологической пробы.
Технологическая проба должна быть полностью светлой без графитовых включений.
После подготовки металла согласно заданного химического состава производится его выпуск в подготовленный ковш необходимой емкости.
5.1.2 Отливка двухслойных заготовок бочек валков на центробежной машине
Основным агрегатом для получения двухслойных бочек мелющего валка является центробежная машина с горизонтальной осью вращения формы, позволяющая отливать валки с бочкой диаметром до 0,5 м и длиной до 2,0 м.
Процесс отливки заготовок бочек мелющих валков на центробежной машине включает ряд подготовительных операций, от тщательности которых зависит качество будущего изделия.
Основными из этих операций являются следующие:
- сборка формы и заливочного устройства;
- заливка металла в установку центробежного литья. 5.1.2.1. Сборка формы и заливочного устройства
Сборка формы заключается в монтаже изложницы с двух ее торцев крышками. Изложница очищается металлической щеткой от остатков теплоизоляции и устанавливается на сборочную плиту, с предварительно очищенными посадочными местами, на которые устанавливается крышка.
Крышка закрепляется к изложнице клиньями.
После установки крышек изложница укладывается в контейнер для сушки и подогрева до 220.. .230°С
Подогретая изложница устанавливается на центробежную машину, после чего в нее вводится теплоизоляционная смесь при вращении с помощью специального устройства - пескосыпа.
Облицовочная смесь равномерно распределяется в процессе засыпки во вращающейся форме, обеспечивая толщину слоя, равную 0,002 м.
Для облицовки изложницы используется песчано-смоляная смесь (песок, смешанный со смолой) в следующей пропорции:
- 95% кварцевого песка марки КО 16;
- 5% связующей смолы сверх 100% типа СФП-011Л по ТУ 6-05-1370-90. Песчано-смоляная смесь наносится на внутреннюю поверхность
изложницы по ходу ее вращения при медленном повороте пескосыпа на 180°С и при частоте вращения формы 700 об/мин.
Продолжительность отверждения слоя смеси составляет 4 мин.
Заливочное устройство футеруется стандартными шамотными изделиями.
Концевая сифонная труба сбоку имеет прорезь длиной 200 мм и шириной 40 мм для обеспечения боковой заливки металла по ходу вращения формы.
Собранная воронка с подставкой окрашивается графитовой краской, сушится переносной горелкой, после чего заливочное устройство устанавливается на центробежную машину.
5.1.2.3 Заливка металла в установку центробежного литья
Температура металла перед выпуском из печи составляет 1480...1500°С
Выпуск металла осуществляется в подогретый до температуры 400°С поворотный ковш емкостью 1,0 т.
Перед заливкой металла берется проба на отбел. Величина отбела на пробе должна составлять 0,010...0,015 м.
Ковш с металлом с помощью крана подается к центробежной машине, счищается шлак с зеркала металла и при температуре 1350±10°С заливается через литниковую воронку в центробежную машину (рис. 5.1).
Продолжительность заливки металла рабочего слоя толщиной 0,04 м составляет 15 сек.
После выдержки продолжительностью 3 мин заливается второй слой металла из оставшегося в ковше чугуна, предварительно промодифицированного FeSi 75% из расчета получения содержания Si =1,5...1,7%.
Скорость заливки металла во вращающуюся форму составляет 160 н/сек.
После окончания процесса формирования бочки валка в форме производится поэтапное снижение частоты вращения изложницы с целью уменьшения вибрации машины до 800 об/мин, а затем до 400 об/мин через соответственно 13 и 14 мин с последующей остановкой вращения формы через 15 мин от начала заливки металла.
После перемещения защитного кожуха в нерабочее положение изложница извлекается из машины и устанавливается на стенд для окончательного остывания отливки.
При достижении на поверхности изложницы температуры Ю0...120°С производится разборка формы и извлечение отливки.
5.1.3 Разборка изложницы
Разборка изложницы производится при следующей последовательности операций:
- выбиваются клинья и снимаются обе крышки;
- изложница чалкой приподнимается над уровнем пола и отливка извлекается из изложницы;
- изложница укладывается на стенд для последующей сборки.
В соответствии с разработанной технологической документацией продолжительность изготовления одной заготовки бочки мелющего валка на центробежной машине составляет ~ 30 мин, включая продолжительность операции по установке формы на машину, перемещению защитного кожуха, нанесению теплоизоляционного покрытия, заливке металла, его кристаллизации во вращающейся форме, остановки формы, снятию крышки кожуха и извлечению заготовки из машины.
5.1.4 Механическая обработка бочек валка
После отливки бочка валка подвергается механической обработке для снятия припусков на внешней и торцевой поверхностях, вырезки темплета для оценки твердости и структуры металла, а также для расточки отверстий под запрессовку полуосей.
5.1.5 Механическая и термическая обработка полуосей
Заготовки полуосей изготавливают из стали 40Х по ГОСТ 4543-71, которые подвергаются термической обработке (закалка в масле при 840...860°С, отпуск при 560...570°С) для обеспечения твердости HRC 31...36.
Механическая обработка заготовки производится в соответствии с чертежом детали.
Запрессовка полуосей с торцев бочки
Полуоси запрессовываются в торцевые отверстия бочки в холодном состоянии на специальном прессе модели П6736 Одесского объединения «Прессмаш».
5.1.6 Окончательная механообработка валка
Окончательная механическая обработка мелющего валка состоит в шлифовке поверхности рабочего слоя бочки и посадочных поверхностей для установки в подшипниках согласно требованиям чертежа.
5.1.7 Балансировка валка
Балансировка валка осуществляется на специальном стенде, осуществляющим динамическую балансировку при скорости 7,67 сек".
Допускаемый дисбаланс у каждой из сторон бочки валка составляет 500 г-см.
5.1.8 Нарезка рифлей на поверхность рабочего слоя валков
Нарезка рифлей на поверхности бочки мелющего валка производится на специальном рифленарезном станке типа ТТ-43.
Микрошероховатость на рабочей поверхности мелющих валков, полученных по разработанной технологии, образуется в процессе их эксплуатации путем самовосстановления, благодаря рекомендованному химическому составу металла с повышенным содержанием фосфора (Р = 0,5...0,7%).
В этом случае валок для размольной системы помещается в мельницу без предварительной обработки в дробеструйной камере и в процессе помола приобретает микрошероховатую поверхность (рис. 5.3).
Такая технология позволяет сократить расходы на специальное оборудование для нанесения микрошероховатости на поверхность бочки валка и дополнительные трудозатраты.
Выво
ды по
V
главе
1. Показано, что по предложенному технологическому процессу получения мелющих валков, внедренному на ООО «Литейном заводе им. Медведева» прокатных валков.
2. Показано, что на основании результатов, полученных в настоящей работе, спроектирована и изготовлена новая конструкция центробежной машины для получения биметаллических валков, которая эксплуатируется в настоящее время в промышленных условиях
ОБЩИЕ ВЫВОДЫ
В процессе разработки технологии получения биметаллических заготовок валков для пищевого машиностроения, выявлены следующие особенности их производства, оказавшие решающую роль в повышении надежности и долговечности литых изделий с дифференцированной структурой:
1. Установлено, что применение массивной изложницы с облицованным покрытием, соизмеримой с толщиной стенки отливки (~ 130 мм) взамен тонкостенной (~ 40 мм), позволило существенно повысить ее аккумулирующую способность, снизить температурный перепад по отношению к отливке, повысить изотропность свойств рабочего слоя валка, полностью исключив появление дефектов в виде трещин.
2. Показано, что при заливке второго металла в период достижения на внутренней поверхности рабочего слоя средней температуры интервала ликвидус-солидус, можно обеспечить прочное сваривание металлов без употребления специального флюса.
3. Установлено, что при пульвербакелитовом покрытии толщиной 2,0 мм средняя скорость затвердевания металла рабочего слоя составляет 8 мм/мин и создаются условия для получения требуемой твердости и глубины отбела.
4. Выявлено, что при частоте вращения формы, которая соответствует значению гравитационного коэффициента К = 100 на внутренней поверхности заливаемого слоя металла, создаются условия для повышения физико-механических свойств заготовки вследствие ускоренного выравнивания угловых скоростей металла и изложницы.
5. Установлено, что применение заливочного устройства с боковой подачей жидкого чугуна по ходу вращения формы, сокращающей на 20...25% период вовлечения во вращение слоя металла до частоты вращения формы по сравнению с продольной заливкой, обеспечивает получение отливок с более однородной структурой и предотвращает появление окисных пленок в металле, спаев и других дефектов.
СПИСОК ИСПОЛЬЗУЕМОЙ ЛИТЕРАТУРЫ
1. Бутковский В.А., Мерко А.И., Мельников Е.М. Технология зерноперерабатывающих производств. - М.: Колос, 1999. - 472 с.
2. Косов И.П. Состояние и перспективы развития мукомольно-крупяной промышленности России. - В сб.: Машиностроители – предприятиям хлебопродуктов. - М.: ИГШ, 2001. - с. 10... 14.
3. Бутковский В.А., Птушкина Г.Е. Технологическое оборудование мукомольного производства. - М.: ГП Журнал «Хлебопродукты», 1999. -208 с.
4. Зотьев А.И., Аронов А.Г., Петрухин И.П. Современные средства размола зерна. - М.: Колос, 1982. - 140 с.
5. Юкиш А.Е. Предприятиям хлебопродуктов - современное оборудование. - В сб.: Машиностроители — предприятиям отрасли хлебопродуктов. -М.: МПА, 2002. - с. 7...8.
6. Демский А.Б., Птушкина Г.Е., Борискин М.А. Комплектное оборудование мукомольных заводов. - М.: Агропромиздат, 1985. - 137 с.
7. Птушкина Г.Е., Товбин Л.И. Высокопроизводительное оборудование мукомольных заводов. - М.: ВО «Агропромиздат», 1987. - 190 с.
8. Соколов А.Я., Журавлев В.Д., Душин В.Н. и др. Технологическое оборудование предприятий по хранению и переработке зерна. - М.: Колос, 1984.-220 с.
9. Птушкин А.Т., Новицкий O.A. Автоматизация производственных процессов в отрасли хранения и переработки зерна.- М.: ВО «Агропромиздат», 1987. - 272
10. Бутковский В. А., Мельников Е.М. Технология мукомольного, крупяного и комбикормового производства. М.: ВО «Агропромиздат», 1989. - 199 с.
11. Кулак В.Г., Максимчук Б.М., Чакар А.П. Мукомольные заводы на комплектном оборудовании. - М.: Колос, 1984. — 95 с.
12. Будагьянц М.А., Карский В.Е. Литые прокатные валки. — М.: Металлургиздат, 1983.- 175 с.
13. Гималетдинов Р.Х. Производство прокатных валков из высококачественных чугунов. - М.: Полтекс, 2000. - 329
14. Стрижов Г.С, Карсский В.Е., Дорощенко П.П. и др. Центробежная отливка прокатных валков. - Литейное производство, № 4, 1969. —Филиппов А.С Разработка центробежного способа производства чугунных прокатных валков.
15. Гималетдинов Р.Х. Центробежная отливка крупнотоннажных прокатных валков. - Литейное производство, № 6,2000. - 37 с.
16. Мирзоян Г.С Исследование и разработка теоретических основ формирования и технологии производства крупногабаритных
17. Будагьянц Н.А. Исследование технологических параметров центробежной отливки валков. М.: Сталь, 1982. - С. 25...26.
18. Белай Г.Е., Белокопытов Г.М. Центробежное литье двухслойных валков. - Литейное производство, 1979. - С 33...34.
19. Рабинович Б.В. Введение в литейную гидравлику. - М.: Машиностроение, 1966.-423 с.
20. Лойцянский Л.Г. Механика жидкости и газа. - М.: Наука, 1970. - 904 с.
21. Цветненко К.У. Применение моделирования и метода подобия в центробежном литье. - Литейное производство, 1962, № 7. - 45 с.
22. Вейник В.И. Теория затвердевания отливки. - М.: Машгиз, 1962. -433
23. Глаголев В.А. Геометрические методы количественного анализа агрегатов под микроскопом. - Львов: Наука, 1960. - 264 с.
24. Гусятинская Н.С Современное состояние метрологического обеспечения измерений твердости металлов методом упругого отскока бойка (по Шору). - М.: ВНИИКИ, 1980. - 40 с.
25. Щербинский В.Г., Артемьев С.А., Самедов Я.Ю. Новые средства ультразвуковой дефектоскопии металлопродукции и оборудования. — Металлург, № 10, 2002. - С. 44...47.
26. Машиностроение. Энциклопедия, под ред. Фролова К.В. Том 11-12. -М.: «Машиностроение», 2001. - 784 с.
27. Баландин Г.Ф. Основы теории формирования отливки. 4.1. - М.: «Машиностроение», 1979.-325 с.
28. Куманин И.Б. Литейные свойства сплавов. - Литейное производство, 1980,№2.-С3...6.
29. Беляков А.И., Петров Л.А., Жуков А.А. и др. Интеллектуальная система термографического анализа контроля качества литейных сплавов. -Литейное производство, № 10, 1999. - С. 28...29.
30. Беляков А.И., Петров Л.А., Долбенко Е.Т. и др. Термографический анализ валкового чугуна. - Труды пятого съезда литейщиков России. М.,21...25мая,2001.-С397...400.
31. Мирзоян А.Г. Формирование двухслойных мелющих валков в поле центробежных сил. Изобретатели - машиностроению, 2005, № 6. — с. 30...31.
32. Левин М.М., Каменев А.Ф. Ускоренное охлаждение крупногабаритных центробежнолитых заготовок. - В книге: Тепловые процессы в отливках и формах.-М.: Наука, 1972.-С. 135... 138.
33. Технические условия «Валки мукомольные» ТУ 14-2-241-76, МЧМ СССР, 1979.-5 с.
34. Специальные способы литья. Справочник под общ. ред. Ефимова В.А. — М.: Машиностроение, 1991.-436 с.
35. Руденко А.Б., Серебро B.C. Литье в облицованный кокиль. - М.: Машиностроение, 1987. - 184 с.
36. Справочник по чугунному литью. Под редакцией Гиршовича Н.Г. - Л.: Машиностроение, 1978. - 758 с.
37. Мирзоян А.Г. Влияние скорости затвердевания на качество центробежнолитых мелющих валков. - Литейное производство, 2005, №8.-9с.
38. Цветненко К.У. Расчет скорости вращения формы при центробежной отливке трубных заготовок. - Литейное производство, 1970, № 4. -С. 41...42.
39. Гималетдинов Р.Х., Мирзоян А.Г. Центробежное литье биметаллических бочек мукомольных валков. - Литейное производство, 2003, № 11.-С 34...36.
40. Семенов П.В., Тиняков В.Г., Мирзоян А.Г. Производство двухслойных заготовок. Изобретатели - машиностроению, 1997, № 1. - С. 21.. .22.
41. Александров Н.Н., Иванов Е.В., Куликов В.И., Смирнов И.В. Центробежная отливка двухслойных бандажей валков среднеходных размольных мельниц. -В кн.: Повышение эффективности производства и качества чугунных и стальных отливок. - Л.: ЛДНТП, 1982. -С 44...46.
42. Александров Н.Н., Смирнов И.В. Прогрессивная технология производства отливок бандажей углеразмольных мельниц для теплоэнергетики. - В кн.: Энерго- и ресурсосберегающие технологические процессы в литейном производстве. - Красноярск, 1986.-С 40...42.
43. Александров Н.Н., Слепнев Г.М. Исследование влияния технологических параметров литья на качество центробежнолитых биметаллических заготовок. - В кн.: Теория и практика получения биметаллических и многослойных отливок и заготовок. - Киев: Науковадумка, 1978.-С 107
44. Гималетдинов Р.Х., Копьев А.В., Мирзоян А.Г. и др. Разработка технологии получения двухслойных мукомольных валков. - Сб. науч. тр. «Литейное производство сегодня и завтра», вып. 3. - СП., 2000. -125 с.
45. Казанцев А.Г., Мирзоян А.Г. Методы оптимизации рабочего профиля валков вальцовочных машин. - Изобретатели - машиностроению, 1999
46. Гималетдинов Р.Х., Копьев А.В., Мирзоян А.Г. Двухслойные вальцы для мукомольной промышленности. - Труды пятого съезда литейщиков России. - М., 2001. - С 103... 106.
47. Гималетдинов Р.Х., Павлов СП., Капустина Л.С, Мирзоян А.Г. Центробежное литье биметаллических бочек мукомольных валков. -Литейное производство, 2003, № 4. - С. 34...36.
48. Гималетдинов Р.Х., Капустина Л.С, Мирзоян А.Г. Особенности производства мельничных валков для пищевой промышленности. -Технология металлов, 2004, с. 10. - С 46...47.
49. Белай Г.Е., Белокопытов Г.М. Влияние частоты вращения формы на кристаллизацию рабочего слоя центробежнолитых валков. -Металлургическая и горнорудная промышленность, 1982, № 1. -С 33...35.
50. Миляев В.Н., Поручиков Ю.П. Выбор гравитационного коэффициента при центробежном литье. - Литейное производство, 1974, № 4. -С 41...42.
|