ПЛАН
1. Выбор емкости (садки) конвертера и определение количества конвертеров.
1.1 Общие замечания.
1.2 Определение емкости и количества конвертеров.
2. Выбор типа и определение количества необходимого оборудования и основных характеристик отделений цеха.
2.1 Подача жидкого чугуна.
2.1.1 Выбор емкости и определение количества миксеров.
2.1.2 Планировка и основные размеры миксерного отделения.
2.1.3 Оборудование миксерного отделения.
2.2 Шихтовый двор.
2.2.1 Выбор типа и основных размеров шихтового двора.
2.2.2 Выбор типа и определение количества основного оборудования шихтового двора.
2.2.3 Емкость и габаритные размеры скрапных ям и бункеров для сыпучих материалов.
2.2.4 Замечания к расчету.
2.3 Количество кранов на шихтовом дворе.
3. Главное здание цеха.
3.1 Планировка и определение основных размеров пролетов главного здания цеха.
3.2 Выбор типа и определение количества основного оборудования пролетов главного здания цеха.
3.2.1 Конвертерный пролет.
3.2.2 Газоочистка.
3.2.3 Загрузочный пролет.
3.2.4 Ковшевой пролет.
3.2.5 Разливочные пролеты при разливке стали в изложницы.
3.2.6 Шлаковый пролет.
1 ВЫБОР ЕМКОСТИ (САДКИ) КОНВЕРТЕРА И
ОПРЕДЕЛЕНИЕ КОЛИЧЕСТВА КОНВЕРТЕРОВ
1.1 ОБЩИЕ ЗАМЕЧАНИЯ
1) Выбор емкости (садки) и количества конвертеров для цехов разной производительности определяется рядом факторов, наиболее важными из которых являются: принятый способ разливки (в изложницы или на MHЛЗ), вес отливаемых слитков, условия передачи слитков в прокатные цехи, тип процесса, принятая схема работы конвертеров и др.
Решающее влияние не выбор емкости (садки) конвертера (скрап + жидкий чугун) оказывает заданная производительность цеха и принятый способ разливки стали.
2) С увеличением емкости (садки) улучшаются технико-экономические показатели работы конвертеров: повышается производительность, снижается удельный расход огнеупоров и себестоимость стали. Кроме того, с увеличением емкости конвертера уменьшаются удельные тепловые потери, что позволяет повысить долю лома в металлошихте. Поэтому при прочих равных условиях следует отдавать предпочтение установке конвертеров большой емкости, но с учетов обеспечения равномерности работы конвертерного и прокатного цехов и использования оборудования при остановке конвертера на ремонт.
3) Для цехов относительно небольшой производительности установка одного-двух больших агрегатов, обеспечивающих выполнение всей программы цеха, как правило не рекомендуется, т.к. это приводит к недогрузке оборудования и осложнениям в работе смежных цехов и отделений при остановке конвертера на ремонт.
4) Емкость (садку) выбираемых в проекте конвертеров необходимо увязывать также с емкостью существующих сталеразливочных ковшей и особенно с грузоподъемностью имеющихся заливочных и разливочных кранов. Кроме того, годовая производительность выбранного конвертера должна быть примерно кратной заданной годовой производительности цеха с тем, чтобы фактическая суммарная производительность установленных конвертеров в проектируемом цехе была отличной к данной. Следовательно для каждой заданной производительности цеха и других указанных выше условий необходимо выбирать наиболее рациональную емкость конвертеров и их количество.
5) Емкость действующих и строящихся в настоящее время конвертеров колеблется в очень широких пределах (от 10 до 400 т). Наиболее широкое распространение на современных металлургических заводах получили конвертеры емкостью 100-350 т.
6) Исходя из вышеизложенного, в дипломных и курсовых проектах, в зависимости от заданной производительности цеха, а также принятого способа разливки стала (разливка в изложницы или на МНЛЗ) и варианта (схемы) работы конвертеров в цехе, можно принимать номинальные емкости конвертеров в следующих пределах:
а) 130 - 150 и 250 - 350 т - при разливке в слитки и на МНЛЗ;
б) 350 - 400 т - только при разливке на МНЛЗ.
7) При выборе емкости (садки) конвертера для заданной производительности цеха ориентировочно можно исходить из следующих данных (см.табл.I):
Производительность цеха млн. тонн в год
|
Рекомендуемые номинальные емкости конвертеров, т
|
от 2 до 4
от 3 до 6
от 5 до 8
от 6 и более
|
130 - 150
25О - 300
300 – 350
350 - 400
|
8) Для дипломных работ и курсовых проектов можно рекомендовать следующие схемы (варианты) работы конвертеров (см. табл.2):
Табл.2
Варианты работы
Конвертеров
|
Количество конвертеров в цехе |
Количество непрерывно работающих конвертеров |
Количество
конвертеров
находящихся в
ремонте или
ожидании
|
1 |
2 |
I |
I |
2 |
3 |
2 |
I |
3 |
4 |
3 |
I |
1.2 ОПРЕДЕЛЕНИЕ ЕМКОСТИ И
Kоличества
конвертеров
Исходя из вышеизложенного, в проектируемом цехе производительностью 5.2 млн.т годных слитков в год принимаем конвертеры номинальной емкостью (садкой) 260т, работающие по второму варианту (схеме).
Количество непрерывно работающих конвертеров в цехе, обеспечивающих заданную производительность, определяется из зависимости:

где
- расчетное количество одновременно работающих конвертеров в цехе;
Тц
- годовая производительность цеха, т годных слитков;
- годовая производительность одного работающего конвертера, т годных слитков.
Производительность одного работающего конвертера можно определить по формуле :

где 8760 - количество часов в году;
tпл
- общая продолжительность плавки, час.;
К - количество простоев конвертера, % от календарного времени;
m - коэффициент выхода годных слитков из металлозавалки;
- номинальная садка конвертера (скрап + чугун), т.
Примечание: в предварительном расчете производительности конвертера принимается низший предел выбранной номинальной емкости (садки.) конвертера.
1) Продолжительность плавки (tпл
) складывается из продолжительности продувки и вспомогательных операций (завалка лома, заливка чугуна, взятие проб, замер температуры металла, ожидание анализа, спуск шлака, слив металла в ковш, разделка и заделка сталевыпускного отверстия и т.д.):
а) продолжительность продувки плавки зависит главным образом от интенсивности подачи кислорода (2,5-6 м3
/т*мин) и составляет обычно 10-20 мин независимо от массы садки конвертера (чем больше интенсивность подачи кислорода, тем меньше продолжительность продувки плавки);
б) продолжительность вспомогательных операций (особенно завалки лома, заливки чугуна, слива металла вковш) определяется емкостью (садкой) конвертера и мощностью оборудования, а такие технологией и организацией процесса плавки и при работе на обычных передельных чугунах на рядовые марки стали всовременных конвертерных цехах обычно составляет 15-25 мин. (при прочих равных условиях чем больше емкость конвертера, тем больше в среднем продолжительность вспомогательных операций).
Следовательно, общая продолжительность плавки (tпл
) в зависимости от интенсивности продувки, емкости (садки) конвертера и др., условий обычно колеблется в пределах 25-45 мин. (чаще 30-40 мин,).
В примерном расчете при интенсивности продувки 4-5 м3
/т.мин., использовании мощного оборудования и т.д., принимаем общую продолжительность плавки (tпл
) для конвертера номинальной емкостью (садкой) 260 т равной 45 мин. или
tпл
= 45 : 60 = 0,75 часа.
2) Количество простоев, работающего конвертера (Kp
) определяется продолжительностью капитальных ремонтов цеха (обычно 1,0-2,0% календарного времени) и продолжительностью текущих (горячих) простоев, связанных с ремонтом и сменой фурм, кессонов и т.д. (обычно 2,0-3,0%- календарного времени).
В примерном расчете принято:
а) простои на капитальных ремонтах - 1,4%
б) текущие (горячие) простои - 2,4%
т.е. Кр = 1,4 + 2,4 = 3,8% календарного времени.
3) Выход годных слитков (m) определяется выходом годной стали из металлической завалки (берется из расчета материального баланса плавки) и выходом годных слитков из жидкой стали, т.е. коэффициентом выхода годных слитков из металлической садки конвертера, представляющим собой произведение коэффициента выхода жидкой стали из металлозавалки на коэффициент выхода годных слитков из жидкой стали.
Выход годных слитков изжидкой стали зависит главный образомот принятого способа разливки и веса отливаемых слитков и в среднем составляет:
а) при сифонной разливке в мелкие слитки (до 7 т) - 0,96;
б) при сифонной разливке в крупные слитки (более 7 т) - 0,97 — 0,98;
в) при разливке сверху в крупные слитки - 0,98 - 0,99;
г) при разливке на МНЛЗ - 0,96 - 0,98.
В примерном расчете, при разливке стали сверху в крупные слитки ( >7 т) и на мнлз принимаем коэффициент выхода жидкой стали равный 0,98. Коэффициент выхода жидкой стали из металлозавалки принимается по данным расчета материального и теплового балансов плавки. В настоящем примерном расчете этот коэффициент принят равным 0,91 или 91% от массы садки конвертера. Тогда коэффициент выхода годных слитков из металлозавалки в нашем случае составит:
M = 0,91 • 0,98 = 0.89 (или 89,18% от массы садки конвертера).
Подставляя известные величины в формулу, получим годовую производительность одного непрерывно работавшего конвертера номинальной емкостью (садкой) 160 т

для обеспечения заданной годовой производительности цеха 5.2 млн.тонн потребуется непрерывно работавших конвертеров номинальной емкостью 260 т

Принимая, что общая продолжительность плавки (tпл
) при этом изменяется незначительно, уточнение фактической садки конвертера производим из следующей зависимости:

где - фактическая (уточненная) садна конвертера, т.
- предварительно принятая (расчетная) садка конвертера, т;
- расчетное количество непрерывно работающих конвертеров
номинальной емкостью (садкой) 260 т;
- фактическое (приятое) количество непрерывно работающих
конвертеров.
Для обеспечения заданий производительности цеха при двух непрерывно работающих конвертерах примерно той же общей продолжительности плавки (tпл
=0,75 часа) фактическая садка конвертера (скрап + чугун) должна быть:

(что находится в пределах выбранной номинальной емкости конвертеров ). Если, например, металлошихта состоит из 24% лома и 76% жидкого чугуна, на плавку потребуется:
а) лома = 259,47 • 0,24 = 62,2729 т;
0) жидкого чугуна = 259,47 • 0,76 = 197,1976 т.
Таким образом, для обеспечения заданной производительности в проектируемом цехе должно быть установлено три конвертера садкой 260 т, из которых два конвертера непрерывно находятся в работе, а один в ремонте (или в ожидании).
При коэффициенте выхода жидкой стали из металлозавалки, равном 0,910, масса плавки по жидкой стали для конвертера садкой 260 т составит:
Мж
= • 0,910 = 260 · 0,910 = 236,1181т
При коэффициенте выхода годных слитков из жидкой стали, равном
0,98 масса плавки по годным слиткам составит:
Мсл
= Мж
· 0,98 = 236,1181 · 0,98 = 231,3958 т
При той же общей продолжительности плавки (tпл
=0,75 часа) годовая производительность одного непрерывно работавшего конвертера садкой 260 т составит ( ):

В связи с тем, что текущие простои (ремонт и смена фурм, кессонов и т.д.) в действительных условиях работы могут быть не ежесуточно, максимальное количество плавок всутки по цеху составит:
плавки
где
2 - количество одновременно работающих конвертеров;
0,75- принятая в расчете (проекте) общая продолжительность плавки, час;
24 - количество часов б сутки.
Тогда максимально возможная суточная производительность цеха по годным слиткам (А) составит:

2 Выбор типа и определение количества
необходимого оборудования и основных
характеристик отделений цеха
2.1 Подача жидкого чугуна
В настоящее время существует две схемы подачи жидкого чугуна из доменного цеха к конвертерам:
а) с использованием миксеров как промежуточной емкости;
б) с использованием ковшей миксерного типа.
2.1.1 Выбор емкости и определение количества
миксеров
В современных конвертерных цехах взависимости от производительности в настоящее время используются типовые миксеры емкостью 1300 и 2500 т;
При выборе емкости миксера необходимо стремиться к установке возможно меньшего количества миксеров в цехе. Однако, для бесперебойного снабжения конвертеров жидким чугуном количество установленных миксеров в цехе должно быть не менее двух (но не более трех в одном миксерном отделении).
Суммарная потребная емкость миксеров ( ) может быть определена по следующей формуле:

где
А = 9967,818 - суточная производительность проектируемого цеха в годных слитках, т;
tч
= 7,0 - принятое в проекте среднее время пребывания чугуна в миксере, необходимые для усреднения его состава и температуры, час.(обычно колеблется в пределах 6-9 часов, но не менее 6 часов);
h = 0,73 - коэффициент заполнения миксера (зависит от степени неравномерности заливки чугуна в миксер и выдачи его из миксера и колеблется обычно в пределах 0,65-0,77;
1,01 – коэффициент, учитывающий потери чугуна в миксере;
24 - количество часов в сутках;
Кч
- расход чугуна на тонну годных слитков, т/т.

Подставляя известные величины в формулу, получим необходимую суммарную емкость миксеров в проектируемом цехе:

При емкости миксера Qм
= 2500 т, количество миксеров в цехе будет равно:
миксера
Принимаем два миксера емкостью 1300 т и один миксер емкостью 2500 т, тогда среднее фактическое время пребывания жидкого чугуна в миксере составит:
часа.
2.1.2 ПЛАНИРОВКА И ОСНОВНЫЕ РАЗМЕРЫ микСЕРНОГО
ОТДЕЛЕНИЯ
Миксеры устанавливаются в отдельно стоящем здании, и перемещение чугуновозных ковшей от миксера к конвертерам осуществляется при помощи чугуновозных тележек тепловозами или электровозами по железнодорожным путям, для ковшей емкостью до 140 т применяется нормальная колея, для ковшей большей емкости - широкая колея (до 4,5 м).
Расположение и планировка миксерного отделения зависят главным образом от типа цеха, емкости миксеров и принятой схемы подачи чугуна к конвертерам. В конвертерных цехах средней и большой производительности может применяться «высокое расположение» миксеров, при котором пути подачи чугуна к конвертерам располагаются не уровне рабочей площадки загрузочного пролета конвертерного отделения цеха. Для удешевления строительства конвертерных цехов Укргипромез рекомендует подавать чугун в загрузочное отделение на уровне заводского пола, что позволяет снизить высоту миксерного здания на 8-I2 м. Миксерное отделение обычно располагается в торце главного здания цеха и соединяется с ним эстакадой. Ковши с чугуном после взвешивания на ж.д. весах, расположенных под сливным носком миксера, подаются к конвертерам (в загрузочный пролет) по специальному пути, проходящему по рабочей площадке загрузочного пролета или на уровне пола.
Расстояние между миксерным и главным зданиями - обычно составляет 36-60 м.
С целью удешевления строительства конвертерного цеха миксерное отделение может непосредственно примыкать (блокироваться) к загрузочному (или конвертерному) пролету для обеспечения бесперебойной подачи жидкого чугуна к конвертерам при установке миксеров большой емкости рекомендуется ступенчатое расположение их в миксерном отделении с наличием самостоятельного (своего) пути подачи чугуна от каждого миксера. Пo этой же причине в одном миксерном отделении должно устанавливаться не более трех миксеров (с двумя путями подачи чугуна), В этом случае два миксера из трех ставятся в одну линию.
Подача чугуна из доменного цеха к миксерам и огнеупоров для ремонта ковшей и миксеров, а также уборка мусора и шлака, удаляемого из миксеров, осуществляется по ж.д. путям. Нормальной колеи, уложенным на уровне заводского пола.
Основные габаритные размеры здания миксерного отделения (ширина, длина и высота) определяются размерами и количеством миксеров и их расположением, габаритами чугуновозных ковшей и ж.д. путей, а также высотой рабочей площадки (эстакады).
Высота миксерного здания зависит от емкости и размеров миксера и высоты рабочей площадки. Ширина миксерного здания (по осям колонн) – A6 при емкости миксеров 1300т составляет 30 м, при емкости миксеров 2500 т и ступенчатом их расположении - 36 м.
Длина миксерного здания – B5 зависит главным образом от размеров и количества установленных миксеров и обычно составляет; 48-96 м.
2.1.3 ОБОРУДОВАНИЕ МИКСернОГООТДеЛЕния
Миксерные отделения современных цехов имеет следующее основное оборудование:
1) мостовые заливочные краны;
2) чугуновозные и шлаковозные тележки с ковшами (чащами);
3) стенды для шлаковых ковшей (чаш);
4) весы ж.д. типа для взвешивания чугуна;
5) электровозы или тепловозы для подачи чугуна к конвертерам. Грузоподъемность весов зависит от емкости чугуновозных ковшей. Количество весов в отделении соответствует количеству миксеров.
Количество чугуновозных ковшей (тележек) в составе обычно составляет 2-4, б зависимости от емкости ковшей ипринятой схемы подачи чугуна к конвертерам.
Емкость чугуновозных ковшей для подачи чугуна из доменного
цеха в миксерное отделение в современных сталеплавильных цехах
обычно составляет100 или 140 т, при грузоподъемности заливочных
кранов соответственно 125 - 30 и I80 – 50 т.
В примерном расчете проектируемого цеха с миксерами емкостью 1300 т и 2500 т принято, что подача жидкого чугуна из доменного цеха в миксерное отделение осуществляется в ковшах емкостью 140 т. Заливка чугуна в миксеры производится заливочными кранами грузоподъемностью 180 - 50 т.
Количество заливочных кранов в миксерном отделении (при коэффициенте их загрузки, равной 0,8) можно определить по следующей формуле:

где - суммарная задолженность крана на одну тонну чугуна, сливаемого в миксер, мин;
А1
= 9,96 - суточная производительность цеха в годных слитках, тыс.т;
Кч
= 0,85 - коэффициент расхода чугуна на тонну годных слитков, т/т.
Суммарная задолженность крана на заливке одной тонны чугуна в миксер ( ) зависит от продолжительности заливки одного ковша чугуна в миксер, емкости чугуновозного ковша и степени (коэффициента) его заполнения, а также задолженности крана на вспомогательных работах (обычно 15% от основных работ) и может быть определена по следующей Формуле;

гдз tз
- продолжительность операции заливки в миксер одного ковша чугуна, мин.(по данным практики, в зависимости от емкости ковша и других конкретных условий работы в отделении, может быть принята в пределах 14-18 мин);
вк
- коэффициент заполнения ковша (обычно составляет 0,8 – 0,9);
Принимая для условий проектируемого цеха среднюю продолжительность операции заливки одного ковша чугуна в миксер (при емкости ковша 140т) равной 16 мин.( tз
= 16 мин.),средний коэффициент заполнения ковша вк
= 0.85, получим следующую суммарную задолженность заливочного крана на I т чугуна.
Подставляя известные величины формулу, получим необходимое количество заливочных кранов е миксерном отделении проектируемого цеха:
= 0,87 • 14,809 • 0,85 • 0,154 = 1,697 крана.
С учетом резервных приникаем три заливочных крана грузоподъемностью 360+100/16т каждый.
Примечание: По данным практики в миксерных отделениях современных сталеплавильных цехов устанавливается не менее одного заливочного, крана на каждый миксер.
Для обеспечения заливки чугуна в конвертер в один прием, особенно при увеличений массы плавки, емкость чугуновозных ковшей для подачи чугуна из миксерного отделения к конвертерам должна быть на 20-30% больше номинальной емкости конвертера и приближаться к емкости сталеразливочного ковша. В соответствии с этим грузоподъемность заливочных кранов должна быть равной грузоподъемности разливочных кранов (выбирается по ГОСТ 6909-61)
В примерном расчете для конвертеров с фактической садкой 260 т для подачи чугуна к конвертерам приняты чугуновозные ковши емкостью 140т.
2.2 Шихтовый двор
2.2.
I
ВЫБОР ТИПА И ОСНОВНЫХ РАЗМЕРОВ ШИХТОВОГО
ДВОРА
Шихтовый двор современного конвертерного цеха, как правило, состоит из двух отделений, расположенных в одной или двух самостоятельных зданиях (или пролетах):
1) отделение шихтовых магнитных материалов (скрапное отделение);
2) отделение шихтовых сыпучих материалов (или общезаводской склад сыпучих материалов).
В скрапном отделении шихтового двора хранятся в основном металлический лом, а в некоторых случаях и раскислители. Для складирования этих материалов в отделении имеются соответствующие площадки или ямы. Суммарный объем ям для хранения скрапа определяется суточной производительностью цеха, расходом скрапа на одну тонну стали, числом суток запаса и насыпной массой скрапа.
Расположение и оборудование скрапного отделения зависит от производительности цеха и принятого способа подачи скрапа к конвертерам и их загрузки.
В цехах сравнительно небольшой производительности применяется продольное расположение шихтового двора. В этом случае шихтовый двор (скрапное отделение) обычно располагается в одной линии к загрузочным пролетам главного здания цеха и подача скрапа к конвертером осуществляется по эстакаде на отметке рабочей площадки по пути, проходящей вдоль фронта конвертеров.
В цехах большой производительности наиболее рациональным следует считать параллельное расположение скрапного отделения с подачей скрапа по поперечным путям с загрузкой его в конвертеры совками с помощью кранов загрузочного пролета и использованием для продольного перемещения совков со скрапом специальных загрузочных кранов. Наиболее удобный является применение полупортальных кранов, позволяющих осуществлять загрузку металлолома независимо от работы заливочных кpaнoв. Для загрузки всего скрапа в конвертер обычно достаточно двух совков, которые одновременно захватываются двумя подъемами крана. Объем совковбудет зависеть от емкости конвертера, доли скрапа в металлошихте и его плотности.
Ширина здания скрапного отделения определяйся количеством и расположением ж.д. путей в нем, принятой шириной скрапных ям и в современных цехах отечественных заводов обычно составляет 24-36 м по осям колонн здания. Высота здания зависит от габаритов подвижного состава, а также кранового оборудования, расположения путей транспортировки совков со скрапом и обычно составляет 9-14 м от уровня пола цеха до головки подкрановых рельсов. Длина здания скрапного отделения определяется прежде всего длиной скрапных ям (полученных расчетом), а также суммарной толщиной разделительных стенок и длиной торцевых участков отделения, не занятых ямами. Шаг колонн здания обычно составляет 12 м. При выносе газоочисток за пределы главного здания скрапное отделение может состоять из двух участков, расположенных по одной оси.
В отделении сыпучих материалов хранятся известь, плавиковый шпат, железная руда, агломерат, боксит и др. сыпучие материалы. Для предотвращения попадания влаги все сыпучие материалы рекомендуется хранить б закрытых помещениях с ямными бункерами с последующей перегрузкой этих материалов в приемные воронки конвейеров грейферными кранами.
Подача сыпучих материалов к конвертером производится системой ленточных конвейеров и питателей, расположенных в изолированном от цеха участке конвертерного пролета, во избежание распространения по цеху пыли, выделяющейся при перегрузке сыпучих материалов, особенно извести, галерея, в которой располагается конвейер подачи сыпучих материалов, примыкает к торцу конвертерного пролета. Комплекс механизмов для подачи сыпучих материалов к конвертерам и загрузки их в конвертеры обычно состоит из следующих основных узлов:
1) подачи сыпучих в расходные буккеры;
2) подачи сыпучих из расходных бункеров в промежуточный бункер;
3) подачи сыпучих из промежуточного бункера в конвертер.
Расположение отделения сыпучих шихтовых материалов относительно главного здания цеха и его размеры выбираются по конструктивным соображениям, исходя изтерриториальных возможностей.
2.2.3 ЕМКОСТЬ И ГАБАРИТНЫЕ РАЗМЕРЫ СКРАПНЫХ ЯМ И
БУНКЕРОВ ДЛЯ СЫПУЧИХ МАТЕРИАЛОВ
Емкость скрапных ям и бункеров для сыпучих материалов определяется, исходя из суточного расхода этих материалов и принятых норм их запаса.
а) Расход материалов на плавку (Рпл
) - равен pасходному коэффициентусоответствующего материала на тонну годных слитков (Рк) умноженному на массу плавки в годных слитках, т.е.:
Рпл
= Рк
´ Мсл

Рк
- расходный коэффициент соответствующего материала на тонну годных слитков, т/т;
а - расход соответствующего материала на 100 кг металлической завалки, кг.
б) Суточный расход материалов по цеху _(Рсут) - равен расходу соответствующих материалов на одну плавку (Рпл) умноженному на
максимальное количество плавок в цехе в сутки ( ), т.е.:

в) Количество материалов на шихтовом дворе (Ршд) – равно максимальному суточному расходу соответствующих материалов в цехе умноженному на количество суток запаса этих материалов, принятых в данном цехе, т.е.:

где - принятое б цехе количество суток запаса соответствующих материалов.
Пример расчета расходных коэффициентов соответствующих шихтовых материалов на тонну годных слитков, а также расхода этих материалов на одну плавку, по цеху в сутки иколичества материалов на шихтовом дворе с учетом принятых норм запаса б проектируемом цехе приведен в табл.
Пример расчета необходимой полезной и полной (фактической) емкости бункеров для сыпучих материалов и ям для магнитных материалов и их габаритных размеров приведен в табл.
2.2.4 Замечания к расчету
1) Необходимая полезная емкость бункеров для сыпучих материалов и ям для магнитных материалов равна массе (весу) соответствующего материала деленной на его насыпную массу.
2) Полная (фактическая) емкость бункеров для сыпучих материалов и ям для магнитных материалов равна их полезной емкости деленной на коэффициент заполнения.
3) Для определения полной (фактической) емкости бункеров и ям коэффициент заполнения их для сыпучих материалов принимается равный 0,8 и для магнитных материалов 1,2.
4) Для обеспечения поточного расходования извести (с целью устранения ее залеживания и порчи) вбункерах устраивается разделительная стенка внизу. Поэтому фактический коэффициент заполнения бункеров известью будет меньше, чем другими сыпучими материалами, хранящимися в бункерах без разделительных стенок. В примерном расчете он принят равным 0,5.
5) Коэффициент заполнения бункеров ферросплавами также принимается несколько меньше, чем металлическим ломом. В примерном расчете (проекте) он принят равным 1,0.
6) Глубина бункеров для сыпучих материалов обычно составляет 6-7 м, включая нижний «мертвый» слой материала толщиной О,5-0,75 м, предназначенный для удобства работы грейфера и защиты подошвы бункера от ударов грейферов. Для удобства работы магнитных кранов глубина ям для магнитных материалов обычно принимается равной 2-3 м. Толщина разделительных стенок между бункерами должна быть не менее 0,7 м.
7) Ширина бункеров и ям определяется в основном шириной здания шихтового двора (шихтовых отделений), зависящей в свою очередь, от длины пролета моста магнитных и грейферных кранов, необходимости размещения определенного количества ж.д., путей для шихтовых составов (тележек), прибывающих вагонов и другого оборудования, а также шириной проходов в соответствии с правилами техники безопасности и другими условиями и может колебаться в довольно широких пределах (от 12 до 18 м и более).
8) Длина бункеров и ям определяется расчетом, исходя из необходимой полной (фактической) емкости бункеров для данного материала и принятых в расчете его глубины и ширины, но с учетом возможности нормальной работы грейфера.
Примечание: Для возможности нормальной работы грейфера минимальная длина бункера для любого сыпучего материала должна быть - примерно на 0,8-1,0 м больше размера грейфера внизу при максимальном его раскрытии (равном 3 м для грейфера емкостью 1,75 м3
и 3,3 м - для грейфера емкостью 2,5 м3
) независимо от того, какой она получилась по расчету.
В примерном расчете принято:
а) общая глубина бункеров для сыпучих материалов равной 6,5 м (в том числе «мертвый» слой 0,5 м), ширина бункеров - 14,0 м;
б) глубина ям для металлического лома и ферросплавов - 2,7 м, ширина ям - 17,0 м.
Расчетная длина бункеров и ям в свету равна полной емкости бункера (ямы), деленной на площадь его поперечного сечения, т.е. на произведение ширины бункера (ямы) на полезную глубину (без «мертвого» слоя).
Пример расчета длины в свету ям для металлического лома и ферросплавов и бункеров для сыпучих материалов приведен в табл.
Запасы сырых материалов в цехе.
№
п\п
|
Наименование материалов |
Расход на 100кг м\з |
Расходный коэффициент |
Расход на одну плавку |
Макс сут расход материал |
Всего материал на шихт дворе |
Примечание |
Рек нор-мы запас в сутках |
Принятые в проэкт норм зап |
Кол-во материал на ш.дв. |
1 |
Мет\лом |
24 |
0.269 |
62.26 |
3984.57 |
От 6 до 10 |
7 |
27892,01 |
2 |
Известь |
7.35 |
0.082 |
19.06 |
1220,276 |
До 2 |
2 |
2440,551 |
3 |
Боксит |
0.6 |
0.006 |
1.55 |
99.614 |
До 15 |
15 |
1494,215 |
4 |
Плав шпат |
0.65 |
0.007 |
1.68 |
107.91 |
До 25 |
20 |
2158,31 |
5 |
FeMn |
0.26 |
0.003 |
0.67 |
43.16 |
20-30 |
22 |
949,6566 |
6 |
FeSi 45%
|
0.48 |
0.005 |
1.24 |
79.69 |
20-30 |
22 |
1753,212 |
Емкости и габаритные размеры бункеров и ям для шихтовых отделений.
Отдел ш\дв |
Наимен матер |
Кол-во мат на ш\дв |
Насыпн масса матер |
Необх пол пл б и ям |
Габаритные размеры бункеров и ям |
Коэфф запол |
Пол ем бун и ям |
Принят глубин |
Принят ширина |
Расчет дл в св |
Констр дл в св |
Общая дл в св |
Скрап отдел |
М\л |
27892,01 |
2,5 |
11156,8 |
1,2 |
9297,337 |
2,7 |
17 |
202,5564 |
202,5564 |
226,8149 |
FeMn |
949,6566 |
3 |
316,5522 |
1 |
316,5522 |
2,7 |
17 |
6,896562 |
6,896562 |
FeSi45%
|
1753,212 |
2,2 |
796,9146 |
1 |
796,9146 |
2,7 |
17 |
17,36197 |
17,36197 |
Отдел сыпуч матер |
Извест |
2440,551 |
0,8 |
3050,689 |
0,5 |
6101,378 |
6,5 |
14 |
72,63545 |
72,63545 |
106,3518 |
Боксит |
1494,215 |
1,5 |
996,1433 |
0,8 |
1245,179 |
6,5 |
14 |
14,82356 |
14,82356 |
Пл шп |
2158,31 |
1,7 |
1269,594 |
0,8 |
1586,993 |
6,5 |
14 |
18,89277 |
18,89277 |
2.3 Количество кранов на шихтовом дворе
На шихтовых дворах с раздельным хранением сыпучих и магнитных материалов, состоящих из двух самостоятельных отделений (или пролетов), в отделении магнитных материалов (в скрапном устанавливается только магнитные, а в отделении сыпучих материалов только грейферные краны. Грузоподъемность шихтовых кранов 10 и 15т с емкостью грейфера соответственно 1,75 и 2,5 м3
в диаметром магнита 1,15 и 1,65 м.
примечание: в цехах с большегрузными конвертерами могут применяться магнитные краны большей грузоподъемности (до 30 т).
Выбор грузоподъемности кранов шихтового двора определяется в основном производительностью цеха, емкостью сталеплавильных агрегатов (конвертеров) и выбранной емкостью совков.
Для конвертерных цехов производительностью до 4 млн.т годных слитков в год в основном применяются шихтовые краны грузоподъемностью 10 т, для цехов с годовой производительностью более 4 млн.т грузоподъемностью 15 т и более.
Краны шихтового двора используются для выполнения основных (разгрузка скрапа и др. материалов из ж.д. платформ, погрузка материалов в мульды, совки и бункера и т.д.; и вспомогательных (очистка путей, перестановка оборудования в т.д.) операций.
При необходимости перестановки груженных совков со скрапом, краны шихтового двора оборудуются подъемами со специальными, захватами. Кроме того, для разворота длинных совков на платформах могут также устанавливаться краны с поворотными тележками.
Общая занятость шихтовых кранов не тонну годных слитков зависит от расхода шихтовых материалов на тонну слитков (от соотношения чугуна и лома в шихте), качества сырых материалов, скоростных характеристик кранов и т.д.»
Постоянное количество кранов на шихтовом дворе (Пкр.ш) можно определить по следующей формуле:

где К - коэффициент расхода кранового времени на выполнение вспомогательных операций (принимается равным 1,15);
А - суточная производительность цеха в годных слитках, t;
в - коэффициент загрузки кранов (принимается равным 0,8);
1440 - число минут в сутках;
- сумма затрат кранового времени на одну тонну слитков, мин.
Сумма затрат кранового времени не тонну слитков ( ) определяется, исходя из затрат кранового времени на переработку одной тонны шихтовых материалов и расходных коэффициентов соответствующих шихтовых материалов на тонну слитков.
Средняя продолжительность крановых операций, отнесенных к одной тонне шихтовых материалов (мин/т), для кранов грузоподъемностью 10 и 15 т (диаметр электромагнитов соответственно- 1,15 и 1,65 м; емкость грейферов - 1,75 и 2.5 м3
) приведена в таблице
№ п\п
|
Наименование операций
|
Продолжительность мин/т
|
Примечание |
 |
 |
1 |
2 |
3 |
4 |
5 |
1 |
Разгруз скрап из ж.д. платформ |
1,7 |
0,9 |
Магнитные краны |
2. |
Разгрузка ферросплавов
|
1,5-1,7 |
0,75-0,9 |
---//--- |
1 |
2 |
3 |
4 |
5 |
3. |
Погрузка скрапа (в мульды или совки)
|
1,9 |
1,0 |
---//--- |
4. |
погрузка ферросплавов (в мульды или бадьи)
|
1,7-1,9 |
0,85-1,0 |
---//--- |
5. |
догрузка железной руды |
0,6 |
0,40 |
Грейферные краны |
6. |
нагрузка извести (в бункера) |
1,9 |
1,40 |
---//--- |
7. |
погрузка боксита (в бункера) |
1,0 |
0,7 |
---//--- |
8. |
погрузка плавикового шпата
|
0,9 |
0,6 |
---//--- |
Расчет суммарных затрат кранового времени на тонну слитков для примерного расчета приведен в таблице.
Наименование шихтовых материалов
|
Расходный коэффициент, т/т
|
продолжитель-ность опера-ций мин/т
|
мин/т
|
Примечание |
магнитные краны |
Грейферные краны |
Металлолом |
0.269 |
1.9 |
0.511 |
0 |
Разгрузка и погрузка |
FeMn |
0.002 |
1.6 |
0.004 |
0 |
FeSi(45%) |
0.005 |
1.9 |
0.010 |
0 |
Известь |
0.082 |
1.4 |
0 |
0.115 |
Погрузка |
Боксит |
0.006 |
0.7 |
0 |
0.004 |
Плавиковшпат |
0.007 |
0.6 |
0 |
0.004 |
Итого |
- |
- |
0.526 |
0.124 |
- |
Подставляя известные величины в формулу, получим:
а) количество магнитных шихтовых кранов в скрапном отделении

принимаем в примерном расчете 8 магнитных кранов грузоподъемностью 15т.
б) количество грейферных кранов в отделении сыпучих материалов

принимаем в примерном расчете 3 грейферных крана грузоподъемностью 15т.
3 ГЛАВНОЕ ЗДАНИЕ ЦЕХА
3.1 ПЛАНИРОВКА И ОПРЕДЕЛЕНИЕ ОСНОВНЫХ РАЗМЕРОВ
ПРОЛЕТОВ ГЛАВНОГО ЗДАНИЯ ЦЕХА
Планировка главного здания конвертерного цеха, зависит главным образом от его производительности и выбранного способа разливки стали (в изложницы или на МНЛЗ). В цехах с конвертерами 100-250 т при разливке стали слитки, разливочные пролеты находятся в главном здании цеха.
В этом случае главное здание цеха состоит из пяти параллельно расположенных пролетов: конвертерного, загрузочного, ковшевого и двух разливочных. Все пролеты размещены под одной крышей и впоперечном направлении соединены между собой путями нормальной или широкой колеи, проложенными по полу цеха и предназначенными для перемещения шлаковозов и сталевозных тележек. В некоторых случаях в состав главного здания могут входить скрапной и шлаковый пролеты. Вцехах с конвертерами садкой 100-150 т подготовка ковшей может осуществляться в одном из разливочных пролетов. В этом случае отдельного пролета для ремонта ковшей не делается.
В цехах с конвертерами 100-250 т при разливке на МНЛЗ и вцехах с конвертерами более 250 т при любом способе разливши разливочные пролеты выносятся в отдельное здание, соединенное с главным зданием передаточным пролетом. В этом случае в состав главного здания входят загрузочный, конвертерный, скрапной, ковшевой и шлаковый пролеты, a такжеможет входить пролет бункеров расхода сыпучих материалов.
Для лучшего наблюдения за работой конвертеров может быть сделан отдельный пролет (шириной 6-9 м) для размещений пультов управления. Взаимное расположение пролетов определяется конструктивными особенностями цеха и расположением газоочистки, пролет подготовки ковшей обычно располагается ближайшим к разливочным пролетам.
Размеры пролетов зданий при строительстве сталеплавильных цехов определяются, исходя из условий размещения необходимого оборудования, сооружений и ж.д. путей с соблюдением требуемых правилами техники безопасности проходов между ними. Для унификации типоразмеров элементов зданий рекомендуется компоновать здания изпролетов кратных по ширине 6 м (12,18,24,30 и 36 м в зависимости от емкости установленных агрегатов). Основной шаг колонн по длине здания равен 12 м, в местах расположения конвертеров 24, 36 и 48 м. В настоящее время в целях удешевления строительства здания рекомендуется не более 36 м.
3.2 ВЫБОР ТИПА И 0ПРЕДЕЛЕНИЕ КОЛИЧЕСТВА
ОСНОВНОГО ОБОРУДОВАНИЯ ПРОЛЕТОВ ГЛАВНОГО
ЗДАНИЯ ЦЕХА
3.2.1
Конвертерный пролет
В конвертерной пролете размещены конвертера, буккера для приема, хранения и завалки в конвертера сыпучих материалов и устройства для удаления конвертерных газов.
Для хранения текущего запаса сыпучих шихтовых материалов каждый конвертер имеет 4-8 расходных бункеров. Емкости бункеров должны обеспечивать необходимый запас соответствующих материалов на 15-40 часов работы конвертера.
Комплекс подачи и завалки сыпучих материалов в конвертера состоит из трех узлов:
а) узел подачи сыпучих материалов в расходные бункера;
б) узел подачи сыпучих материалов из расходных бункеров в промежуточный бункер;
в) узел подачи сыпучих из промежуточного бункера в конвертер.
В цехах с крупнотоннажными конвертерами бункера запаса сыпучих устанавливаются в отдельном пролете шириной 12м.
В одной из торцов конвертерного пролета устанавливаются промежуточные бункера для ферросплавов. Длина участка ферросплавов 60-108м. Загрузка ферросплавов в бункера осуществляется с помощью многорельсовой тележки или мостового крана. Передача ферросплавов к конвертерам в большинстве цехов осуществляется автопогрузчиками.
С другой стороны конвертерного пролета делается участок для хранения оборудования и огнеупоров длиной 36-72 м.
Обслуживание конвертеров и агрегатов связанных с их работой, производится с рабочих площадок, расположенных на различных отметках от уровня пола цеха.
Главная рабочая площадка, на которой производятся основные работы по обслуживанию конвертеров, являетсяпродолжением площадки загрузочного пролета.
3.2.2 Газоочистка
В цехах с конвертерами емкостью до 200 т газоочистка делается, с дожиганием СО. При конвертерах емкостью более 200 т - экономичнее газоочистка без дожигания СО.
В цехах с малыми конвертерами (до 150 т) газоочистка располагается в конвертерном пролете. В цехах с крупнотоннажными конвертерами в целях удешевления строительства зданий делается выносная газоочистка которая либо примыкает к конвертерному пролету, либо устанавливается у торца главного здания.
3.2.3 Загрузочный пролет
Основное назначений загрузочного пролета - прием и завалка в конвертер чугуна и скрапа, а также прием и хранение ферросплавов и огнеупоров. Для обеспечения быстрой завалки и устранения простоев конвертеров транспортировка и загрузка каждого вида материалов в конвертер производится отдельными механизмами и машинами. При размещении газоочистки в конвертерном пролете загрузочный пролет располагается с внешней стороны главного здания цеха. При выносной газоочистке с целью сокращения длины газоотводящего тракта загрузочный пролет располагается внутри главного здания. Ширина загрузочного пролета вцехах с конвертерами до 200 т - 18-24 м, более 200 т - 30м. Длина загрузочного пролета обычно равна длине конвертерного пролета.
При емкости конвертеров до 150 т и расположении шихтового двора в направлении загрузочного пролета подача лотков с ломом производится по железнодорожному пути нормальной колеи, подача чугуна осуществляется по двум путям нормальной колеи. При расположении шихтового пролета параллельно конвертерному подача лома производится по поперечным путям, и в загрузочном пролете делаются только два пути для подачи чугуна.
Если пути подачи миксерных ковшей проходят между конвертерами и скрапным пролетами, пути для подачи скрапа располагается на уровне рабочей площадки.
При емкости конвертеров 250 т и более подача ковшей с чугуном осуществляется по путям широкой колеи (3,0-4,5 м). Соосно с этими путями могут прокладываться пути нормальной колеи для подачи в пролет железнодорожных вагонов.
Для подачи огнеупоров и ферросплавов на полу цеха (пролета) укладывается тупиковый ж.д. путь.
Завалка лома и заливка жидкого чугуна в конвертер производятся установленными в пролете специальными завалочными и заливочными кранами, грузоподъемность которых определяется емкостью совков и чугуновозных ковшей.
В примерном расчете для обеспечения заливки чугуна в один прием при увеличении массы плавки приняты чугуновозные ковши емкостью 280 т, а грузоподъемность заливочных кранов 360+100/16т. Количество заливочных кранов в загрузочном пролете принимается из расчета один кран на один непрерывно работающей конвертер и, кроне того, один кран в резерве на случай их ремонта.
Для завалки лома в конвертер чаще всего используются полупортальные загрузочные устройства, имеющие по два подъема для возможности завалки двух лотков лома. Грузоподъемность одного подъема для конвертеров емкостью до 150 т - 50 т, емкостью до 300 т – 90 т и емкостью свыше 300 т - 130 т. В пролете ставится по одному устройству на каждый непрерывно работающий конвертер, но не менее двух.
3.2.4 Ковшевой пролет
Основное назначение, ковшевого пролета - смена футеровки сталеразливочных и чугуновозных ковшей, а также наборка и сушка стопоров (в специальных помещениях).
Перемещение ковшей внутри пролета производится мостовыми кранами. В пролете имеются ямы для одновременного ремонта двух ковшей в каждой, помещения для наборки стопоров или шиберных затворов, стенды для сушки ковшей и установки стопоров в ковши, стенды для ломки футеровки ковшей. В пролете имеется тупиковый ж.д. путь, предназначенный для подвоза огнеупоров и вывоза мусора. Для постановки стопоров и вспомогательных работ ставятся два консольных крана грузоподъемностью 5 т. Ширина ковшевого пролета 18-24 м. Если в нем производится ремонт промежуточных ковшей, ширина его увеличивается до 30м.
3.2.5 Разливочные пролеты при разливке стали в
изложницы
В цехах с конвертерами емкостью до 250 т разливочные пролеты располагаются в главном здании цеха. Число их обычно равно двум.
В цехах с большегрузными конвертерами разливочные пролеты выносятся в самостоятельное здание. Количество пролетов при этом определяется объемом разливаемой стали. Через разливочные пролеты убирается мусор и шлак, остающиеся в ковшах после разливки стали.
В каждом пролете уложены сквозные и тупиковые железнодорожные пути, предназначенные для разливки стали и уборки мусора и шлака.
К основному оборудованию разливочных пролетов относятся разливочные краны, сталеразливочные ковши и шлаковые чаши, изложницы и тележки, разливочные площадки. К вспомогательному - стенды для разнесения сталеразливочных ковшей, шлаковых чаш и т.д.
При подготовке ковшей в разливочных пролетах в них устанавливаются консольные краны грузоподъемностью 5 т, предназначенные для постановки стопоров в ковши и вспомогательных работ - по одному крану в пролете.
Основные характеристики оборудования и его количество определяются производительностью проектируемого цеха, емкостью установленных в цехе агрегатов (конвертеров), принятым способом разливки и др. условиями.
Ширина разливочных пролетов для цехов с конвертерами до 200 т 18 м, в цехах с большегрузными конвертерами 24 м.
I) грузоподъемность разливочных кранов определяется максимально возможным весом металла и шлака в сталеразливочном ковше и весом самого ковша.
В примерном расчете для цеха с конвертерами емкостью 260,5 т грузоподъемность разливочных кранов, как и заливочных, принята равной 360+100/16т.
2) Необходимое количество_разливочных__кранов_ в цехе, (без учета резервных), зависит от занятости их на операциях по разливке стали и на вспомогательных работах (смене шлаковых чаш, уборка мусора и т.д.), т.е. от задолженности крана на тонну слитков (через два стопора) и суточной производительности цеха.
С учетом коэффициента неравномерности выпуска плавок, равным 1,3, необходимое количество разливочных кранов можно определить по следующей формуле:

где - общая задолженность крана на разливке и работах, мин/т слитков.
В зависимости от массы плавки (емкости ковша), принятой в цехе скорости и других условий разливки, а также занятости разливочных кранов на вспомогательных операциях, общую задолженность разливочного крана на тонну годных слитков ( ), исходя из практических денных, можно принимать равной 0,25-0,40 мин.
В примерном расчете при разливке стали сверху в крупные слитки (массой 150 т) с повышенной скоростью наполнения одновременно двух слитков (через два стопора), принимаем =0,32 мин/т. Тогда необходимое количество разливочных кранов в цехе составят:
Пкр.р = 1,13 • 14,809 • 0,32 = 5,35 крана.
Принимаем 6 разливочных кранов грузоподъемностью 500+100/16 т.
3) Емкость сталеразливочного ковша выбирается исходя из максимально возможной массы плавки по жидкому металлу и некоторого количества шлака для прикрытия металла (толщиной 150 - 250 мм).
В проектируемом цеxe для конвертеров емкостью 260 т (при средней массе плавки по жидкой стали Мж
=236,39 т) приняты сталеразливочные ковши емкостью 175 т.
4) Количество сталеразливочных ковшей находящихся в обороте определяем по формуле

При стойкости футеровки ковша 11 плавок (обычно 6-15 плавок) в ремонте за сутки побывает:
64 : 11 = 5,82 ковша, что составляет, от количества находящихся в работе ковшей. При продолжительности ремонта одного ковша 8 часов одновременно будет находиться в ремонте

Следовательно, для ремонта ковшей в ковшевом отделении должно быть не менее трех одноместных ремонтных ям. С учетом на непредвиденные задержки принимаем, что 10% рабочего парка ковшей находится в резерве, или
22 ´ 0,1 = 2,2 = 3 ковша.
Таким образом, общее количество сталеразливочных ковшей в проектируемом цехе составит:
22 + 2 + 3 = 27 ковшей.
5) количество изложниц на плавку равно массе плавки по годным слиткам деленной нa массу одного слитка, т.е:
пизл
= Мсл
: 12 = 231,39 : 12 = 19,28 = 20 изложниц.
Принимаем с запасом 22 изложницы.
6) количество тележек на плавку равно количеству изложниц на плавку деленному на количество изложниц, устанавливаемых на тележке. Последнее, в свою очередь зависит от грузоподъемности тележки и мессы слитка вместе с изложницей.
Для установки изложниц под разливку применяются три типа сталеразливочных тележек:
а) Двухосные - грузоподъемностью 60т. Длина тележки по осям сцепок 4780 мм;
б) Четырехосные - грузоподъемностью 120 и 160 т, длина тележек по осям сцепок 5840 и 6240 мм;
в) Шестиосные - грузоподъемностью 200-240 т, длина по осям сцепок 7940 мм.
Полезная нагрузка (грузоподъемность) тележки складывается из массы слитков, изложниц и поддона. Следовательно, количество изложниц на тележке зависит от принятой грузоподъемности тележки, развеса отливаемого слитка и соответствующей ему массы изложницы.
В примерном расчете принята масса изложницы с прибыльной надставкой равней 14 т, тогда масса слитка с изложницей составят:
12,0 + 14,0 = 26,0 т.
При грузоподъемности тележки 160 т (6240 мм) и учете массы поддона это позволит установить шесть изложниц на тележке (с общей массой 26,0 • 6 = 156 т). Тогда количество тележек с изложницами на одну плавку составит:
= 22 : 6 = 3,66 = 4 тележки с общей длиной разливочного состава = 4 • 6,24 = 24,96м.
7) Количество находящихся в обращении разливочных составов в цехе определяется расчетным графиком в зависимости от продолжительности оборота составов, связанной с продолжительностью выдержки слитков в изложницах, способом разливки стали, условиями охлаждения изложниц и скоростью подготовки разливочных составов, а также с транспортными условиями.
При воздушном охлаждении изложниц для ориентировочного расчета необходимого количества одновременно находящихся в обращении разливочных составов в цехе можно принимать следующие продолжительности оборота составов, вчасах:
Разливка сверху |
Разливка сифоном |
Составы со сквозными изложницами |
7 – 9 |
9 – 11 |
Составы с изложницами с дном |
11 – 13 |
14 – 17 |
В примерном расчете, при разливке сверху в сквозные изложницы, принята продолжительность оборота одного состава 8 часов. Тогда количество находящихся б обращении разливочных составов в цехе (Псост
), должно быть равно
из 4 тележек.
8) Количество _разливочных площадок в цехе определяется, временем задолженности площадки на разливке одной плавки, которое складывается из продолжительности разливки и выдержки разливочного состава у разливочной площадки до и после разливки (ожидание разливки, отстой и смена составов), количеством разливок (плавок) б сутки и степенью использования разливочных площадок.
Необходимое количество разливочных площадок в цехе (в разливочных пролетах) может быть определено по следующей формуле:
одинарных площадок.
Принимаем 8 одинарных разливочных площадок. Ширина разливочной площадки обычно составляет 3 – 3,5м.
9) Определение длины разливочного пролета.
При расположении разливочного пролета в главной звании длина разливочного пролета складывается из длин разливочных площадок (В9
) определяется расчетом), длины промежуточного заезда (В7
=36 м), длин начала закругления ж.д. путей {B6
=6 м) и длин торцевых участков (B10
=6 м).
Во внешнем разливочном пролете при наличии промежуточного заезда разливочные площадки делаются сдвоенными. Во внутреннем разливочной пролете разливочные площадки могут быть как одинарные, так и сдвоенные, или одинарные со ступенчатым их расположением и односторонним заездом к каждой ступени.
При расположении разливочных пролетов в отдельно стоящем здании заезды б разливочные пролеты делаются только торцевые. Подъезд к разливочной площадке с дальнего пути осуществляется по криволинейному пути внутри пролета. Длина разливочного пролета в этом случае складывается из длин разливочных площадок (В9
), расстояний между сталевозными путями (B1
), габаритных участков (В11
= 6-10 м), длин закруглений(В12
=18-24м) и торцевых участков (B10
= 6-12 м), т.е.:

Внешний разливочный пролет может также делаться с промежуточным заездом.
Ширина разливочных пролетов в цехах с конвертерами емкостью до 200 т 18 м, в цехах с большегрузными конвертерами 24м.
Длина разливочной площадки должна быть не меньше максимальной длины разливочного состава. Кроме того, каждая разливочная площадка должна иметь резервную длину не менее, чем на одну тележку.
При сдвоенных разливочных площадках должен быть пролет между составами равный 6-12м. Длина разливочной площадки должна быть кратной 6 м.
В примерном расчете, для цеха с конвертерами 166 т, принято размещение разливочных пролетов в отдельно стоящем здании. В каждом пролете принято по четыре одинарных разливочных площадки. Следовательно, для разливки всей стали в изложницы в нашем случае необходимо три разливочных пролета.
Длина одной одинарной заливочной площадки для состава из пяти тележек и одной резервной тележки должна быть равна:
Lр.пл.
= В9
= (4 + 1) ´ 6,24 = 31,2 м
Принимаем в примерном расчете В1
= 36м, В11
= 6м, В10
= 6м, В12
= 18м,тогда длина разливочного пролета будет равна:

С учетом кратности 12м принимаем фактическую длину разливочного пролета = 216м. За счет избытка проектной длины разливочного пролета над расчетной соответственно увеличивается длина разливочных площадок.
3.2.6 Шлаковый пролет
В цехах с конвертерами емкостью 200 т иногда специальных шлаковых пролетов не делается. В этом случае шлаковозы из-под конвертеров направляются прямо на шлаковый двор. При движении шлаковозов по специальным путям широкой колеи делается специальный шлаковый пролет для перестановки шлаковозных ковшей на специальные составы. Ширина шлакового пролета 12-18м.
В шлаковый пролет делаются торцевые ж.д. заезды. Пролет оборудуется двумя кранами грузоподъемностью 100/20-120/30т, в зависимости от емкости шлаковых чаш. Шлаковый пролет размещается в главном здании, исходя из конструктивной компоновки цеха.
 
 
 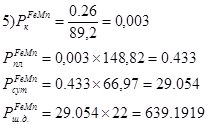
|