АННОТАЦИЯ
В настоящем дипломном проекте разработана установка для переработки отходов слюдопластового производства на «Слюдяной фабрике» в Колпино.
Актуальность темы обусловлена необходимостью решения проблемы утилизации отходов производства, которой должно уделяться особое внимание, так как использование техногенных минеральных ресурсов является важной составной частью государственной политики ресурсосбережения и охраны окружающей среды. Настоящая разработка позволяет практически полностью использовать отходы, имеющие 3-4 класс опасности. В настоящее время отходы размещаются на территории предприятия, а затем вывозятся и захораниваются, что приносит немалые убытки предприятию. Внедрение же разработанной установки позволит не только снизить отрицательное воздействие на экологию, но и получить экономический эффект. Годовая прибыль от реализации продукта переработки - слюды флогопит мокрого помола 315 составит около 2 млн. руб. в год, и это не считая экономии на вывозе и утилизации отходов другими предприятиями. Срок окупаемости установки - 2 года.
Главными техническими решениями, принятыми в данной работе являются использование для помола шаровой барабанной мельницы с разгрузкой через решетку, классификация при помощи гидроциклона, отжим слюдяной пульпы в осадительной горизонтальной шнековой центрифуге и окончательное удаление влаги в сушилке кипящего слоя.
При помощи технологических расчетов выявлены основные конструктивные размеры оборудования и его потребное количество. Конструктивные расчеты выполнены для сушилки кипящего слоя. Рассчитана толщина стенки корпуса аппарата, толщина газораспределительной решетки, произведен расчет укреплений отверстий, фланцевого соединения и др.
В качестве объекта автоматизации выбрана спроектированная сушилка кипящего слоя. Нормальная работа сушилок КС возможна только при определенной высоте кипящего слоя, с целью поддержания заданного значения этого параметра стабилизируется гидродинамическое сопротивление слоя, т. е. перепад давлений до и после решетки, воздействием на вариатор электродвигателя питателя сухого материала.
Сушилка кипящего слоя является наиболее опасным аппаратом установки для переработки отходов. Поэтому она выбрана в качестве основного объекта анализа с точки зрения безопасности. Универсальное оборудование эксплуатируется в соответствии с технической документацией завода-изготовителя и паспортом промышленной безопасности объекта.
В данной пояснительной записке содержатся 33 рисунка и 18 таблиц, общий объем - 114 страниц. К пояснительной записке прилагаются 9 чертежей.
СОДЕРЖАНИЕ
1. ВВЕДЕНИЕ
2. ТЕХНИКО-ЭКОНОМИЧЕСКОЕ ОБОСНОВАНИЕ
2.1 Производство слюдопластовых электроизоляционных материалов
2.2 Образование отходов при производстве слюдопластовой бумаги
2.3 Продукт переработки отходов - молотая слюда флогопит
2.4 Измельчение
2.5 Классификация
2.6 Центрифугирование
2.7 Сушка
2.8 Транспортирование материала
2.9 Технические решения
3. ТЕХНОЛОГИЧЕСКИЕ РАСЧЕТЫ
3.1 Расчет барабанной мельницы
3.2 Расчет классификатора
3.3 Подбор насосов
3.4 Расчет центрифуги
3.5 Расчет сушилки с кипящим слоем
3.5.1 Материальный и тепловой баланс процесса горения
3.5.2 Тепловой и материальный баланс процесса сушки
3.5.3 Тепловой конструктивный расчет
3.6 Подбор циклона
3.7 Подбор фильтра
3.8 Расчет топочного устройства
3.9 Подбор газодувки
3.10 Подбор питателей
4. КОНСТРУКТИВНЫЕ РАСЧЕТЫ
4.1 Расчет сушилки кипящего слоя
4.1.1 Выбор материала аппарата
4.1.2 Расчет толщины обечайки
4.1.3 Расчет толщины газораспределительной решетки
4.1.4 Расчет штуцеров и подбор фланцев
4.1.5 Расчет фланцевого соединения
4.1.6 Расчет укрепления отверстий
4.1.7 Расчет тепловой изоляции
4.1.8 Расчет опор аппарата
5. СИСТЕМА АВТОМАТИЗАЦИИ
6. БЕЗОПАСНОСТЬ ОБЪЕКТОВ
6.1 Производственная безопасность
6.2 Экологическая безопасность
6.3 Возможные неполадки и аварийные ситуации, способы их устранения
7. РАСЧЕТ ЭКОНОМИЧЕСКОЙ ЭФФЕКТИВНОСТИ
8. СПИСОК ИСПОЛЬЗОВАННОЙ ЛИТЕРАТУРЫ
1. ВВЕДЕНИЕ
Актуальность темы дипломной работы обусловлена необходимостью решения проблемы утилизации отходов производства, которой должно уделяться особое внимание, так как использование техногенных минеральных ресурсов является важной составной частью государственной политики ресурсосбережения и охраны окружающей среды. Ежегодно на территории России накапливается 3,5 млрд. т техногенных отходов, но уровень их использования продолжает оставаться крайне низким. Необходимо постоянно улучшать качество и количество используемых минерально-сырьевых ресурсов на всех стадиях от добычи полезных ископаемых и переработки сырья до выпуска и использования конечной продукции. В силу вышесказанного, появляется объективная необходимость в разработке максимально возможной безотходной технологии, позволяющей наиболее полно использовать отходы производства.
Сегодня проблема утилизации отходов горнодобывающего и горноперерабатывающего производств чрезвычайно актуальна в силу различных причин. С одной стороны, происходит истощение разрабатываемых месторождений, а дальнейшая их разработка требует крупных капитальных вложений. В такой ситуации возможно вовлечение в переработку так называемых техногенных образований. С другой стороны, особый интерес представляет переработка текущих отходов производства, позволяющая наиболее рационально извлечь из них ценные компоненты, снижая количество вновь поступающих отходов. Основная масса добываемых и перерабатываемых сегодня слюд идет на производство электроизоляционных материалов, среди которых следует выделить слюдяную бумагу, слюдопластоленту, слюдопласт, микалекс, миканит. Производство любого вида продукции из слюды сопровождается наличием определенного количества технологических отходов (от 10 до 40%).
На «Слюдяной фабрике» наибольшее количество отходов образуется при производстве слюдопластовой бумаги из слюды флогопит. Среди видов отходов следует выделить нерасщепленную слюду, слюду в оборотной воде, укрупненные частицы - «хвосты» и «мику» в отходящей воде. Отходам слюды присвоен 4 класс опасности, степень вредного воздействия на окружающую природную среду - низкая. Критерием отнесения к данному классу является нарушение экологической системы с периодом самовосстановления не менее 3-х лет. Слюда флогопит мелкодисперсная имеет 3 класс опасности, для которого период восстановления - не менее 10 лет после снижения вредного воздействия от существующего источника. Вовлечение этих отходов в переработку позволит решить проблему их утилизации и снизить себестоимость основной продукции - слюдопластовой бумаги.
Существующие сейчас на «Слюдяной фабрике» способы утилизации отходов слюдяного производства имеют огромное количество недостатков. Для складирования требуются все большие и большие территории, отходы проникают в почву, нарушая обменные процессы в природной среде. Дальнейшее захоронение отходов опять же требует новых территорий. Подземные свалки не заметны на первый взгляд, но на поверхности земли над ними почва отравлена и разрыхлена, она не пригодна, ни для строительства, ни для земледелия, ни для выпаса скота. Таким образом, единственным, относительно экологически чистым, способом борьбы с промышленными отходами, на сегодняшний день, является переработка отходов.
Отходы, получаемые в процессе производства слюдопластовой бумаги и слюдопласта, по своим характеристикам близки к природным компонентам, поэтому могут быть вторично вовлечены в производство. Продукт переработки отходов производства слюдопластовой бумаги - молотая слюда флогопит пользуется спросом на рынке и находит применение в различных отраслях промышленности. Отходы слюдяной пульпы образуются в результате сброса из системы расщепления находятся в отстойниках в водной среде. Это обстоятельство определяет способ помола, которым производится порошок слюды флогопит. Слюда мокрого помола используется, в основном, в качестве наполнителя для производства «перламутровых» красок для автомобильной промышленности и в качестве добавок во всевозможные лаки и шпаклевки, что придает им влагоустойчивость, морозоустойчивость и стойкость против коррозии. Уникальные светоотражающие и светопреломляющие свойства слюды мокрого помола обусловили ее применение в производстве художественных обоев и в косметической промышленности в качестве наполнителя при производстве средств макияжа (тени, пудра, помада с эффектом блеска и т.д.). Также молотую слюду флогопит используют для производства резины и в качестве наполнителя в пластмассу.
Таким образом, разработка установки для переработки отходов слюдопластового производства актуальна не только из-за необходимости снижения отрицательного воздействия на окружающую среду, но и по экономическим соображениям.
К сожалению, на сегодняшний день нельзя говорить о достаточной степени изученности проблемы по использованию отходов слюдяного производства. Проведенный анализ литературы показал, что в настоящее время уделяется недостаточное внимание вопросам утилизации отходов слюдяного производства как в форме техногенных образований, так и текущим производственным отходам. Но все же стоит отметить, что кое-какие исследования и разработки в этой области ведутся.
В 2008 году при Иркутском государственном техническом университете Перфильевой Ю. В. была разработана технология извлечения слюды из отходов горно-обогатительных и слюдоперерабатывающих предприятий.
«Нижнеудинская слюдинитовая фабрика» являлась базой эксперимента. Производственные отходы этой фабрики были использованы в качестве исходного компонента для производства модифицированного микалекса. Отходы фабрики можно разделить на две группы - отходы слюдяного производства (включают 5 видов) и отходы слюдокерамического сырья (включают два вида). Обе группы отходов были использованы в производстве микалекса. После грохочения в процессе производства слюдопластовой бумаги на базе скрапа флогопита Ковдорского месторождения образуются отходы. Подрешетный продукт является отходом и представляет собой грубые чешуйки различной формы и разных размеров. Из этих отходов были изготовлены пластины модифицированного микалекса. Технология изготовления модифицированного микалекса из отходов осталась та же, что и при изготовлении микалекса из слюды мусковит.
Кроме того были проведены исследования процесса измельчения отходов с целью получения сырья оптимальной структуры и плотности. Была проведена проверка уравнения кинетики измельчения отходов в шаровой мельнице и молотковой дробилке экспериментальным и графическим методом, обосновано применение технологии флотации для получения дополнительного источника сырья при производстве модифицированного микалекса.
Также решением проблемы по переработке отходов слюды занимаются в Горном институте Кольского научного центра Российской академии наук. В 2000 году сотрудники института обратились к проблеме переработки мусковитовых руд отвалов рудника Риколатва. Были обследованы все отвалы, выделены промышленно значимые, подсчитаны запасы и отобраны технологические пробы. По данным опробований отвалов, проведенных технологических исследований, впервые в России были утверждены запасы забалансовых мусковитовых руд на примере рудника Риколатва с учетом всей слюды, находящейся в отвалах. Эта слюда может быть использована для производства молотых слюд, а крупный мусковит (до 20 мм) для производства слюдобумаг. Учитывая состояние мусковитовых рудников, эти отвалы могут стать основным сырьем для производства концентратов различной крупности и молотых слюд на основе мусковита.
Перечисленные выше факторы в пользу актуальности проблемы переработки отходов слюды и ее недостаточная изученность определили тему дипломной работы. Целью настоящей работы является разработка установки, позволяющей использовать отходы слюдопластового производства для производства молотой слюды флогопит.
Работа имеет практическую значимость, так как разработанная установка может быть использована для переработки отходов на «Слюдяной фабрике» в городе Колпино.
2. ТЕХНИКО-ЭКОНОМИЧЕСКОЕ ОБОСНОВАНИЕ
2.1 Производство слюдопластовых электроизоляционных материалов
Темой настоящей дипломной работы является переработка отходов слюды. В коммерческом отношении термином "слюда" обозначают мусковит и маложелезистый флогопит. К листовой слюде относят светлые прозрачные разновидности, которые расщепляются на пластины разной толщины, пригодные для штамповки изделий нужных форм. Благодаря высоким электроизоляционным свойствам слюды используются в радиоэлектронике, электромашиностроении, электротермии. С самого начала использования слюды специалисты стремились заменить редкую и чрезвычайно ценную крупнолистовую слюду более мелкой. Мелкочешуйчатая слюда под торговым названием "скрап" идет на изготовление теплоизоляционных материалов в теплоэнергетике и стройиндустрии и служит сорбентом в сельском хозяйстве.
Продуктами слюдопластового производства являются следующие теплоизоляционные материалы: слюдопластовая бумага, слюдопласт, слюдопластовая лента, изделия из слюдопластов (трубки и втулки). Последним направлением использования мелкой слюды как заменителя крупнолистовой слюды является изготовление различных слюдопластовых бумаг. Их производство интенсивно растет во всем мире. В слюдопластовой бумаге чешуйки скреплены между собой молекулярными силами без помощи склеивающих веществ. Он изготовляется посредством расщепления отходов или мелких (не пригодных для ручной щипки) кристаллов слюды на чешуйки и соединения их в листы без применения смолы.
В зависимости от назначения листы слюдопластовой бумаги в дальнейшем подвергают пропитке (лакировке) с термообработкой и прессованием. Склеивающие вещества служат для заполнения пор в материале и склеивания листов слюдопластовой бумаги между собой. Слюдопласты обладают достаточно высокой механической прочностью при повышенной температуре, позволяющей изготовлять из них различные фасонные изделия. Эти свойства слюдопласта являются следствием того, что в данном производстве слюда не подвергается химической деструкции и не загрязняется химикатами, как это происходит при получении слюдинитовых бумаг; элементарные частицы имеют в основном толщину от 0,5 до 2 мкм, а по площади намного превосходят свою толщину, что обеспечивает хорошее прилегание частиц друг к другу и дальнейшее их сцепление за счет сил молекулярного притяжения.
Как говорилось раньше, наиболее отходным видом слюдопластового производства является производство слюдопластовой бумаги. Поэтому целью настоящей работы является разработка установки, позволяющей перерабатывать отходы и получать при этом не менее полезный и востребованный в промышленности продукт - молотую слюду флогопит.
2.2 Образование отходов при производстве слюдопластовой бумаги
На «Слюдяной фабрике» в Колпино производят слюдяную бумагу из слюды флогопит марок ИФ-14, ИФ-12 ТУ 21-25-41-78. Сырьем для слюдобумаги является слюда-сырец флогопит Ковдорского месторождения марок СФК-25, СФК-10, СФК-4, СФК-4-10 (ТУ 21-25-223-79). Эта слюда представляет собой пластинчатые кристаллы произвольной формы, ограниченные по площади и толщине. В таблице 2.2.1 приведены технические требования к сырью для производства слюдобумаги.
Таблица 2.2.1 Технические требования к слюде флогопит для производства слюдопластовой бумаги
Продукт
|
Площадь кристалла, мм2
∙102
|
Толщина кристалла, мм
|
СФК-25
|
от 25 до 35
|
не более 20
|
СФК-10
|
то 10 до 25
|
не более 20
|
СФК-4
|
от 4 до 25
|
от 0,05 до 2
|
СФК-4-10
|
от 4 до 35
|
не более 20
|
Технологический процесс производства состоит из следующих этапов:
1. участок первичной обработки слюды (термирование, расколка, очистка);
2. участок производства слюдяной массы;
3. участок отлива слюдобумаги.
1. Участок первичной обработки слюды.
Термист насыпает из ящика слюду в приемный бункер, откуда она подается транспортером (2) на грохот (3) и далее в конвейерную электропечь (4). Грохот служит для очистки слюды от песка и пыли. В процессе подачи сырья в термопечь обеспечивается очистка его от щепок и мусора вручную. Загрузка слюды регулируется скоростью движения подающего транспортера. При термировании слюды удаляется вода, что приводит к уменьшению связей между плоскостями совершенной спайности. Продолжительность термирования слюды - не менее 15 минут.
Из печи термированная слюда поступает в ударную машину (8), где происходит расщепление кристаллов на слои. Расщепленные пластинки слюды проскакивают в щель между броней и лопастями, подаются на пневмосепарацию и далее на сито-бурат (14). Толщина кристаллов регулируется величиной зазора между лопастями ротора и лопастями брони.
Вентилятор (5) подает слюду в циклон (11), где она оседает и поступает в трубопровод, в котором происходит пневмосепарация, плохо расщепленные кристаллы возвращаются в ударную машину, а кристаллы толщиной менее 2 мм поступают в следующий циклон и далее на сито бурат. Пневмосепарация регулируется шибером перед вентилятором (13). Воздух, который расходуется на пневмотранспорт и пневмосепарацию, очищается от слюдяной пыли в скруббере (7) и выбрасывается в атмосферу.
Сито-бурат (14) представляет собой вращающийся барабан, покрытый сеткой с размером ячеек 3*4 мм. Слюда поступает внутрь барабана, где проходит сортировка ее по площади. Мелкая фракция (класс «-5») проходит сквозь ячейки барабана и поступает в бумажные мешки (15). Деловая слюда (класс «+5») поступает в делитель объемов (16). Содержание мелочи в деловой слюде не превышает 1%.
2. Участок производства слюдяной массы
После сито-бурат деловая фракция поступает в делитель объемов слюды, где происходит разделение общей массы на четыре примерно равных потока, каждый поток слюды по пневмотранспорту подается в осадитель (17). Из осадителя слюда подается в моечные машины непрерывного действия (19). В моечной машине происходит удаление с поверхности слюды загрязнений. Слюда непрерывно через загрузочный лоток поступает во вращающийся перфорированный барабан, погруженный в бак с водой и с помощью ребер лопастей перемещается к выходу, где посредством ковшей выгружается из барабана в лоток и по лотку подается на вибролоток (20) и далее на многовалковый прокатный станок (21).
Прокатные станки служат для расщепления кристаллов слюды по плоскостям совершенной спайности и частичного измельчения по площади за счет вдавливания последней рифлеными валиками в резиновую ленту. В процессе прокатки кристаллы слюды смачиваются водой. В конце транспортирующей ленты прокатанные кристаллы смачиваются водой в течку, соединенную с приемной воронкой дезинтегратора (22).
Мокрые, прокатанные кристаллы слюды через загрузочную трубу попадают в расщепляющую камеру дезинтегратора. Расщепление слюды происходит под действием струи воды, входящей в камеру через сопловое отверстие под давлением. Расщепленные чешуйки слюды поднимаются в классифицирующую часть дезинтегратора и под действием восходящего потока подпиточной воды поднимаются наверх и через переливную трубу транспортируются в сгуститель (25). Нерасщепленные чешуйки слюды снова опускаются в расщепляющую камеру.
В сгустителе происходит повышение концентрации пульпы за счет осаждения слюдяных частиц. Подача пульпы в сгуститель осуществляется через центральный приемник, оборудованный гасителем в виде сеточного рукава. Сгущенная пульпа подается в классификатор непрерывным потоком в нижней части конуса по трубопроводу, называющемуся «гусиной шейкой». Осветленная вода от сгустителей поступает в бак оборотных вод.
В гидравлическом классификаторе (26) происходит выделение из слюдяной пульпы грубых частиц - «хвостов», которые не могут подняться вверх, вследствие малой скорости восходящего потока. Частицы эти опускаются вниз классификатора, откуда через «гусиную шейку» непрерывно сливаются в канализацию. Верхний класс слюдяной пульпы поступает через слив в сгуститель-накопитель (28). Сгуститель-накопитель представляет собой емкость, оборудованную барботирующим устройством периодического действия. При достижении заданного количества пульпы автоматически включается в работу пневматический затвор, герметизирующий накопитель. Затем открывается кран и через отверстия в барботирующее устройство подается сжатый воздух, необходимый для взрыхления слюдяной массы перед ее поднятием наверх в промежуточную емкость (29). После взрыхления кран перекрывается, а барботирующее устройство продолжает работать. В результате того воздух собирается в верхней части накопителя и выдавливает пульпу в промежуточную емкость, в которой производится накапливание слюдяной массы перед загрузкой мешального бассейна. Мешальный бассейн заполняется водой, затем из промежуточной емкости выгружается пульпа, перемешивается и перекачивается в рабочий бассейн.
3. Участок отлива слюдобумаги
Отлив слюдобумаги производится на слюдопластоделательной машине К-1425. Слюдяная пульпа из рабочего бассейна (32) по лотку поступает в напускное устройство машины, где она равномерно распределяется по ширине и через переливной барьер, поступает в ригельную зону (зону осаждения). В ригельной зоне частицы слюды оседают на непрерывно движущуюся по наклонному формовочному столу сетку, образую слой слюдопластовой бумаги. Этот слой удерживается на сетке при выходе из воды благодаря вакууму в отсасывающих ящиках формовочного стола. Далее сетка со слюдобумагой перемещается по вакуум-блоку, где слюдобумага подвергается вакуумированию. В зоне вакуума воздух над блоком нагревается трубчатыми электронагревателями, что способствует лучшему испарению воды. Затем полотно слюдобумаги поступает в сушильную часть, которая разделена на 4 зоны сушки. Сушка производится горячим воздухом, нагретым электрокалориферами. Намотка слюдобумаги производится на накате осевого типа. Слюдобумага после прохождения сушильной части поступает на натяжную станцию, состоящую из параллельно укрепленных на поворотной вилке валов и неподвижно укрепленного вала. Рулоны слюдобумаги, снятые с машины, взвешиваются и проверяются контролером на соответствие требованиям ТУ.
Как видно из таблицы 2.1.1, отходы, подлежащие переработке, находятся в отстойнике в водной среде. Эти отходы представляют собой пульпу - смесь воды и пластинок слюды, размером до 30-40 мм. Массовая влажность отходов, находящихся в отстойнике и поступающих на дальнейшую переработку, равна примерно 50-60%, т.е. на 2 тонны слюдяной пульпы, поступающей в отстойник в сутки от основного производства слюдопластовой бумаги, приходится примерно 1 т воды и 1 т слюды. Остальные отходы реализуются другими предприятиями, например, слюда мелкой фракции (класс «-5»). На свалку вывозится только мелкая загрязненная слюда класс «-4», дальнейшее применение которой пока что невозможно на данном предприятии. Отходы производства можно переработать в пористый наполнитель для бетона, например. Но так как в данном производстве слюдопластовой бумаги слюда не подвергается химической деструкции и не загрязняется химикатами, из отходов можно получить более качественный продукт - слюду мокрого помола по ГОСТ 19571-74, 19572-74, 19573-74, ТУ 5725-011-13187253-97, применяемую в качестве добавок в лаки, краски, шпаклевки, жидкие обои, в качестве наполнителя в пластмассу, для производства резины и др.
Таблица 2.1.1 Отходы производства, их использование
Наименование отходов
|
% отходов
|
Местообразование отходов
|
Использование отходов
|
Мелкая загрязненная слюда (класс «-4»)
|
3
|
Грохот
|
Вывоз на свалку
|
Слюда крупная толщиной более 2 мм
|
2
|
Пневмосепарация
|
Подача в термопечь
|
Слюда мелкой фракции (класс «-5»)
|
12
|
Сито-бурат
|
Реализация другими предприятиями
|
Слюда (класс «-5») в оборотной воде
|
8
|
Моечная машина
|
В отстойник
|
Нерасщепленная слюда
|
4
|
Дезинтегратор
|
В отстойник
|
Слюда в оборотной воде
|
9-11
|
Сгуститель-осадитель, сгуститель-накопитель
|
Подается с оборотной водой в дезинтеграторы, моечные машины
|
Укрупненные частицы слюды (хвосты)
|
8
|
Классификатор
|
В отстойник
|
«Мика» в отходящей воде
|
13-14
|
Слюдопласто-делательная машина
|
В отстойник
|
Кромка, обрывы слюдобумаги
|
5-6
|
Накат
|
Барботер отходов, затем промежуточная емкость
|
2.3 Продукт переработки отходов - молотая слюда флогопит
Как говорилось раньше, слюдопластовая бумага производится из флогопита, поэтому продуктом переработки отходов является молотая слюда флогопит по ГОСТ 19571-74, 19572-74, 19573-74 - порошок с размером частиц до 315 мкм. Слюда флогопит является представителем группы слюд алюмосиликатов щелочных и щелочноземельных металлов. Для слюды характерна высокая электрическая и механическая прочность, термическая и химическая стойкость, гибкость, упругость, прозрачность. В таблице 2.2.1 представлен химический состав слюды флогопит.
Таблица 2.2.1 Химический состав флогопита (%):
SiO2
|
37-41
|
Al2
O3
|
12-14
|
Fe2
O
|
6,5-7
|
MgO
|
24-26
|
K2
O
|
9-11
|
TiO2
|
0,8-2
|
Na2
O
|
0,4-0,7
|
Физические свойства слюды флогопит:
· удельная теплоемкость: 0,87∙10-3
Дж/кг∙К;
· твердость: 2 3 (по шкале Мооса);
· плотность: 2670 2730 кг/м3
;
· удельное объемное сопротивление: (1,7 6,8)∙1012
Ом∙мм;
· пробивное напряжение: 4,2 4,6 кВ при частоте 50 ГЦ;
· термостойкость: линейное увеличение толщины 29 169 % при нагревании до 750 градусов Цельсия;
· тангенс угла диэлектрических потерь: 0,0034 0,0147 при частоте 50 кГц.
Технические требования к порошку слюды флогопит 315:
· массовая доля остатка на сетке № 2 - отсутствует;
· массовая доля остатка на сетке № 0315 - не более 6,0 %;
· массовая доля остатка на сетке № 0125 - не более 50,0 %;
· массовая доля частиц, проходящих через сетку № 0063 -
не более 55,0 %;
· массовая доля пустой породы - не более 5 %;
· массовая доля влаги - не более 3,0 %;
· массовая доля Si2
O- не более 40,0 %;
· массовая доля FeO3
- не более 7,5 %;
· массовая доля Al2
O3
- не более 15,0 %;
· массовая доля MgO - не менее 20,0 %;
· массовая доля (K2
O и Na2
O) - не менее 8,0 %;
· массовая доля SO3
- не более 0,1 %;
· массовая доля P2
O5
- не более 0,1 %;
· насыпная масса - не более 0,5 г/см3
.
Данные качественные показатели вырабатываемой продукции определяют технологию производства, а с учетом заданной производительности, равной 1 тонне порошка в сутки, и основные конструктивные параметры оборудования. Из слюдяной пульпы со средним размером частиц, равным 20 мм и влажностью 50 процентов необходимо получить продукт - порошок с размером частиц до 315 мкм и влажностью не более 3%. На рисунке 2.3.1 изображена схема материального баланса производства молотой слюды флогопит с размером частиц до 315 мкм. Отходы от производства слюдопластовой бумаги подлежат измельчению и сушке с предварительным отжимом в центрифуге. Таким образом, целью настоящей дипломной работы является разработка установки, позволяющей осуществить технологический процесс по переработке отходов, образующихся при производстве слюдопластовой бумаги, в материал с заданными качествами.
влажная слюда - 2 т/сут
влажность - 50 %
размер частиц - 20 мм
влажная слюда - 2 т/сут
влажность - 50 %
размер частиц - 315 мкм
влажная слюда - 1,43 т/сут
влажность - 30 %
размер частиц - 315 мм
слюда - 1 т/сут
влажность - 1 %
размер частиц - 315 мм
МОЛОТАЯ СЛЮДА ФЛОГОПИТ 315 мкм
|
|
Рисунок 2.3.1. Материальный баланс производства молотой слюды
2.4 Измельчение
Измельчением называют процесс разрушения кусков твердого материала при критических внутренних напряжениях, создаваемых в результате какого-либо нагружения и превышающих соответствующий предел прочности. Напряжения в материале могут создаваться механическим нагружением, температурными воздействиями, ультразвуковыми колебаниями и др. Наибольшее применение в современном производстве имеют механические способы измельчения. Измельчение делят на дробление и помол, а машины, применяемые для этих целей, называются дробилками и мельницами. В зависимости от размеров частиц продукта (конечного размера частиц dк
) различают следующие виды измельчения: дробление крупное (dк
= 100 350 мм), среднее (dк
= 40 100 мм), мелкое (dк
= 5 40 мм), помол грубый (dк
= =0,1 5 мм), средий (dк
= 0,05 0,1 мм), тонкий (dк
= 0,001 0,05 мм), сверхтонкий (dк
< 0,001 мм).
Основной характеристикой процесса измельчения является степень измельчения, которая определяется соотношением средневзвешенных размеров частиц материала до (dн
) и после (dк
) измельчения:
i = dн
/dк
,
i = 20/0,315 65.
Степень измельчения отражает технологию и определяет параметры измельчителей. Таким образом, необходимо подобрать аппарат, способный обеспечить степень измельчения, равную 65. Степень измельчения, достигаемая на одной машине, для большинства видов дробильного оборудования не превышает 5 50. Поэтому для обеспечения больших степеней измельчения необходимо применить несколько стадий дробления. В то же время следует отметить, что увеличение стадий измельчения приводит к переизмельчению материала и увеличению эксплуатационных затрат. Поэтому процесс измельчения следует осуществлять, исходя из условия обеспечения минимального числа стадий дробления. Кроме того, необходимо учесть, что измельчаемый материал представляет собой пульпу, т.е. аппарат должен обеспечивать мокрое измельчение.
Рассмотрим возможность применения различных видов используемого в промышленности оборудования для проведения мокрого измельчения с i = 65.
Щековые и конусные дробилки применяют для крупного и среднего дробления различных материалов во многих отраслях народного хозяйства. По технологическому назначению их делят на дробилки: крупного дробления, обеспечивающие степень измельчения i = 5 8; среднего и мелкого дробления (степень измельчения i = 20 50). Вышеперечисленные аппараты не могут обеспечить требуемую степень измельчения в одну стадию.
Валковые дробилки применяют для среднего и мелкого дробления материалов высокой и средней прочности, а также для измельчения пластичных и хрупких материалов. Процесс измельчения осуществляется непрерывно при затягивании кусков материала в суживающееся пространство между параллельно расположенными и вращающимися навстречу друг другу валками. Валковые дробилки также не способны обеспечить требуемую степень измельчения.
Выше были рассмотрены дробилки, разрушающие материал сжатием, рассмотрим дробилки ударного действия. В измельчителях ударного действия измельчение материала осуществляется под действием ударных нагрузок, которые могут возникать при взаимном столкновении частиц измельчаемого материала, столкновении частиц материала с неподвижной поверхностью, столкновении материала и движущихся рабочих органов машин. К дробилкам ударного действия относятся роторные и молотковые дробилки, а также пальцевые измельчители. Дробилки ударного действия применяют для измельчения малоабразивных материалов средней и низкой прочности (известняков, мела, гипса, калийных руд и др.). Они обеспечивают степень измельчения i = 15 20, и лишь в отдельных случаях до i = 50.
Таким образом, осуществить необходимый технологический процесс способны лишь аппараты для помола. Среди них можно выделить барабанные, вибрационные и струйные мельницы. При проектировании схем измельчения любых материалов необходимо соблюдать принцип «не измельчать ничего лишнего», поскольку переизмельчение приводит к излишнему расходу энергии, снижению производительности и росту износа дробилок и мельниц. Поэтому нецелесообразно применять в данном производстве молотой слюды вибрационную и бисерную мельницы, которые способны произвести помол слюды до 5 мкм.
Наиболее оптимальным является использование барабанной мельницы. Она способна обеспечить степень измельчения до 100. Достоинствами барабанных мельниц являются простота конструкции и удобство в эксплуатации. Кроме того, существуют конструкции барабанных мельниц мокрого помола.
Схема процесса измельчения материала в барабанной мельнице показана на рисунке 2.4.1. При вращении полого барабана смесь измельчаемого материала и мелющих тел (шаров или стержней) сначала движется по круговой траектории вместе с барабаном, а затем, отрываясь от стенок, падает по параболической траектории. Часть смеси, расположенная ближе к оси вращения, скатывается вниз по слоям смеси. Измельчение материала происходит в результате истирания при относительном движении мелющих тел и частиц материала, а также вследствие удара.
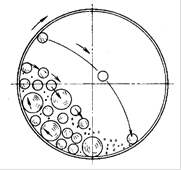
Рисунок 2.4.1. Схема рабочего процесса в барабанной шаровой мельнице
Режим движения мелющих тел в барабане, от которого зависит эффективность помола, определяется его угловой скоростью ω. При небольшой угловой скорости загрузка (мелющие тела и измельчаемый материал) циркулирует в нижней части барабана (рисунок 2.4.2), поднимаясь по концентрическим круговым траекториям на некоторую высоту и затем скатываясь параллельными слоями вниз. Такой режим работы называют каскадным.

Рисунок 2.4.2. Схема для расчета параметров шаровой барабанной мельницы
При большей скорости центробежная сила инерции Ри
превысит составляющую G∙cosα силы тяжести G шара, и последний не будет отрываться от стенки барабана даже в верхней точке C, т.е.
m∙ω2
∙R > m∙g,(2.4.1)
где m - масса шара, кг.
Откуда критическая угловая скорость вращения барабана будет равна:
ωк
= , (2.4.2)
где R - радиус внутренней поверхности барабана, м.
Большей эффективностью помола характеризуется водопадный режим движения шаров. Он реализуется при частоте вращения барабана меньше критической. При этом шары поднимаются, например, в точку А (рисунок 2.4.2), а затем, отрываясь от стенок, свободно падают по параболическим траекториям. Измельчение материала происходит под воздействием удара, а также, частично, раздавливания и истирания.
Для определения условия отрыва и свободного полета шара массой m рассматриваем его как материальную точку, на которую действуют лишь массовые силы. Отрыв шара в точке А от стенки барабана происходит при условии m∙g∙cosα ≥ Pи
. Следовательно, условие отрыва и свободного падения, которое можно получить из соотношения m∙g∙cosα ≥ m∙ω2
R, имеет вид:
ω ≤ . (2.4.3)
Опыт эксплуатации барабанных мельниц показал, что наиболее рациональным является избирательное измельчение материала, когда крупные частицы измельчаются ударом, а мелкие - истиранием. Следовательно, режим работы мельниц должен обеспечивать чередование ударного режима с истиранием. На практике это реализуется за счет использования для футеровки элементов, обеспечивающих переменный коэффициент сцепления мелющих тел со стенками барабана. [4]
Основными критериями при выборе той или иной конструкции барабанной мельницы являются производительность, природа измельчаемого материала и вид помола - сухой или мокрый. В меньшей степени влияние на выбор оказывает тонина помола.
Шаровые мельницы по виду разгрузки измельчаемого материала делятся на два вида: мельницы с принудительной разгрузкой через решетку и мельницы с центральной разгрузкой через цапфу. Мельницы с разгрузкой через решетку предназначены для получения сравнительно крупного продукта, а мельницы с центральной разгрузкой - более мелкого продукта.
Так как помол, производимый при переработке отходов является грубым (dк
= = 0,1 5 мм), то наиболее рационально использовать мельницу с разгрузкой через решетку. Решетку перед разгрузочной цапфой ставят для увеличения производительности шаровой мельницы за счет понижения уровня разгрузки и регулирования степени измельчения при значительных коэффициентах заполнения барабана. Так же решетка служит для удержания в рабочем пространстве барабана шаров и недостаточно размолотого материала. Достаточно измельченный продукт проходит через отверстия решетки, поднимается ее ребрами (лифтерами) и выгружается через разгрузочную цапфу. Разгрузочная решетка мельницы, конструкция которой приведена на рисунке 2.4.3, обычно характеризуется «живым сечением», т. е. суммарной площадью всех отверстий.

Рисунок 2.4.3. Разгрузочная решетка шаровой мельницы: 1 - центральная футеровка; 2 - клинья крепления решетки
В отношении выбора «живого сечения» решеток в литературе не имеется твердых указаний. Так, например, многие специалисты рекомендуют общее «живое сечение» решеток выбирать в 10 раз большим поперечного сечения разгрузочной цапфы. Диаметр цапф мельниц обычно не является параметром ГОСТа, поэтому определение «живого сечения» решеток, как функции нерегламентируемого параметра, следует считать неудачным. Канд. техн. наук Е. Н. Болталов «живое сечение» решетки рекомендует выражать как функцию от диаметра мельницы или от площади поперечного сечения барабана. «Живое сечение» решеток современных мельниц, выпускаемых отечественными и зарубежными заводами, составляет 20 30% площади поперечного сечения барабана. Профиль сечения щелей решеток в большинстве случаев выполняется сопловидной формы с углом расширения в сторону разгрузочной цапфы. Расположение щелей в плоскости решетки определенным образом влияет на производительность мельницы. Экспериментально доказано, что мельницы, оборудованные решетками с щелями, расположенными по хордам, имеют большую производительность по мелким классам и вновь образованной поверхности измельчаемого продукта.
С учетом установки решетки задаемся отношением диаметра к длине барабана мельницы. Правильный выбор длины барабана по отношению к ее диаметру оказывает большое влияние на получение максимальной производительности и на оптимальный расход энергии, т. е. на решающие технико-экономические показатели измельчительного агрегата в целом. Для современных мельниц с разгрузкой через решетку это отношение равно 0,75 1,6. Принимаем это отношение, равным 1.
Применение шаров в качестве мелющих тел обусловлено тем, что стержни способны обеспечить тонину помола лишь до 0,5 мм, что неприемлемо для настоящих требований к степени измельчения слюды.
Загрузочные устройства шаровых мельниц в принципе состоят из двух элементов - питателя той или иной конструкции и загрузочного патрубка цапфы, служащего одновременно ее футеровкой. Оба эти элемента предназначены для транспортирования продукта с уровня загрузки в полость барабана мельницы. Конструкцию и размеры загрузочных устройств выбирают такими, чтобы обеспечить поступление необходимого количества продукта в барабан мельницы и тем самым обеспечивать необходимую скорость загрузки. Скорость загрузки определяется количеством материала, пропускаемого через мельницу в единицу времени. При работе мельницы в открытом цикле она равна производительности по исходному материалу. При работе в открытом цикле количество материала увеличенной крупности, выдаваемого мельницей, возрастает с увеличением скорости загрузки. Низкая скорость загрузки приводит к переизмельчению материала и, следовательно, к понижению производительности и эффективности измельчения по определенному классу. Таким образом, при неудачном выборе параметров питателя или загрузочного патрубка цапфы, может быть снижена производительнсть мельницы. Одним из основных требований, которому должны удовлетворять питатели любой конструкции, является его высокая транспортирующая сила, способная преодолеть все сопротивления движению загружаемого материала. Эти сопротивления движению материала слагаются из сопротивлений движению в спиральном проходе и загрузочном патрубке цапфы, обусловленных трением и зависанием материала, а также из сопротивлений, обусловленных давлением пульпы из внутренней полости барабана мельницы.
Барабанный питатель, конструкция которого приведена на рисунке 2.4.4, представляет собой литую из чугуна или сварную из стали цилиндро-коническую камеру, открытую с обоих концов. Отверстие 2 служит для загрузки и отверстие 3 - для разгрузки материала. Питатель крепится болтами к загрузочной цапфе мельницы. Большее распространение барабанные питатели получили для загрузки на уровне оси мельниц при питании последних крупным сухим исходным материалом. При применении этих питателей отпадает необходимость в устройстве специальной загрузочной коробки, необходимой, например, при применении улиткового питателя.

Рисунок 2.4.4. Барабанный питатель: 1 - крышка питателя; 2 - загрузочное отверстие; 3 - разгрузочное отверстие; 4 - полость
Данный тип питателей трудноприменим в условиях мокрого помола, поэтому рассмотрим другие конструкции. Улитковый питатель, конструкция которого представлена на рисунке 2.4.5, представляет собой конструкцию из одного, двух или трех спиральных черпаков.

Рисунок 2.4.5. Улитковый питатель: 1 - корпус питателя; 2 - сменный козырек
Обычно питатель делается сварным из листовой стали. Питатель имеет отверстие для выпуска зачерпнутого материала. На конце каждого черпака крепится сменный козырек из марганцовистой стали или легированного чугуна. Максимальный радиус улиткового питателя выбирается в зависимости от скорости вращения мельницы. Для предотвращения разбрасывания материала в загрузочной коробке скорость черпания не должна превышать 85% критической скорости, вычисленной по отношению к козырьку улитки. Предпочтительнее делать питатели симметричными, так как при одночерпаковых питателях, из-за неуравновешенности вращающихся частей мельницы иногда появляется неравномерный износ зубьев венцовой шестерни привода мельницы. Мельницы с улитковыми питателями применяют в тех случаях, когда необходимо производить загрузку материала с более низкого уровня, например, при работе с классификатором. Улитковый питатель снабжен загрузочной коробкой. Между стенками и днищем загрузочной коробки и улиткой должны быть предусмотрены зазоры, по размеру несколько большие, чем максимальный размер куска руды или догружаемого шара. Комбинированный питатель, конструкция которого приведена на рисунке 2.4.6, представляет собой конструкцию, объединяющую достоинства барабанных и улитковых питателей.

Рисунок 2.4.6. Комбинированный питатель: 1 - корпус питателя; 2 - спиральный черпак; 3 - козырек; 4 - крышка
При использовании барабанного питателя крупнокусковой материал попадает в мельницу, минуя загрузочную коробку. Черпаки при этом служат как элеваторы. Конструкция комбинированного питателя наиболее предпочтительна для производства молотой слюды из отходов, так как с одной стороны улитковый питатель позволяет осуществить мокрый помол, а с другой - может служить для загрузки в мельницу крупных кусков материала. [1]
Барабан мельницы изготовлен из углеродистой стали, и если его не защитить изнутри прочной облицовкой, то при измельчении абразивных материалов он быстро износится, и мельница выйдет из строя. Кроме того футеровка обеспечивает лучший подъем мелющих тел при вращении барабана. По назначению футеровки обычно делят на две основные группы - футеровки для мельниц, работающих на крупном загружаемом материале и футеровки для мельниц тонкого измельчения. Конечно, такое деление сугубо условное. Футеровки барабанов в цилиндрической части шаровых мельниц, работающих на крупном исходном материале, имеют ребра или волны. Футеровки мельниц тонкого измельчения имеют мелкие ребра или выполняются гладкими. Совсем гладкая футеровка применяется при дроблении сравнительно мягких пород или мелкого питания, когда не требуется создавать высокое давление дробящей среды, но зато требуется получить максимальное истирающее действие. В данном технологическом процессе наиболее целесообразно использовать футеровку с небольшой высотой волн, так как помол слюды - грубый, но ближе к среднему помолу, чем к мелкому дроблению. Футеровка, конструкция которой приведена на рисунке 2.4.3, пригодна больше для очень грубого помола, чем для описанного выше. На рисунке 2.4.7 изображена волнистая футеровка с распорными клиньями. Кроме того, данная футеровка барабанных мельниц является самой распространенной и выпускается отечественными заводами.

Рисунок 2.4.7. Волнистая футеровка с распорными клиньями
Крепление к барабану ступенчатых и волнистых футеровочных плит шаровых мельниц осуществляется чаще при помощи болтов с фасонными головкам. Для посадки фасонных головок болтов в тело плиты последние имеют отверстия овальной формы, идущие на конус в направлении к барабану. На рисунке 2.4.8 изображен болт для крепления футеровочных плит к барабану.

Рисунок 2.4.8. Болт для крепления футеровочных плит к барабану: 1 - упругая шайба; 2 - уплотняющая шайба; 3- корпус барабана
Также футеровочные плиты устанавливают и на торцевых частях барабана. У мельниц с решеткой роль футеровки торцевой части барабана на разгрузочном конце выполняет сама решетка, снабженная центральной футеровкой. Футеровку загрузочной и разгрузочной крышек чаще выполняют гладкой, состоящей из отдельных секторов. Футеровки загрузочной и разгрузочной цапф делают в виде вставных втулок разной конструкции. Загрузочный патрубок выполняют из чугуна в виде конуса, расширяющегося в сторону барабана. Футеровку разгрузочной цапфы выполняют в виде чугунной воронки с гладкой внутренней поверхностью.
На рисунке 2.4.9 приведена примерная конструкция барабанной мельницы мокрого помола, которую предполагается использовать при производстве молотой слюды. Для поддержания в барабане определенного уровня пульпы и вывода измельченного материала из зоны измельчения перед торцовой крышкой 15 устанавливают диафрагму. Она состоит из круглой решетки 9 с ребрами 10. Форма ребер соответствует наклону торцовой крышки. Пространство между решеткой и крышкой делится ребрами на секторы. Со стороны барабана против отверстий на решетку укладывают колосники 8 и закрепляют их с помощью кольца 11 и болтов 12. Этими же болтами притягивают к торцовой крышке и диафрагму.
Пульпа через колосники и отверстия в решетке попадает в нижние секторы между диафрагмой и крышкой. При вращении барабана секторы поднимаются вверх, а находящаяся в них пульпа стекает в выводную цапфу и удаляется из измельчителя.
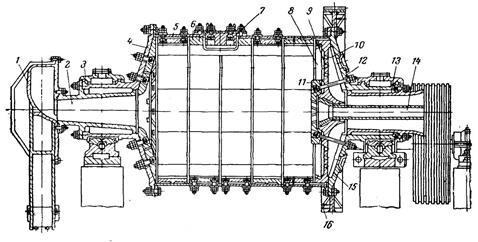
Рисунок 2.4.9. Разрез барабанной мельницы мокрого помола: 1 - улитковый питатель; 2 - загрузочный вкладыш; 3 - подшипник; 4 -передняя крышка с цапфой; 5 - барабан; 6 - броневые плиты; 7 - люк; 8 - колосники; 9 - решетка диафрагмы; 10 - ребра решетки; 11- кольцо; 12 - болты; 13 - выводной вкладыш; 14 - центральная труба; 15 - задняя крышка; 16 - венцовая шестерня
Уровень пульпы в барабане, из которого она начинает переливаться в секторы, регулируется закрытием или открытием отверстий в решетке. Если в решетке открыты все отверстия, то в секторы попадает пульпа из самых нижних слоев материала в барабане. Если же в решетке все отверстия закрыты, то пульпа может выходить только через центральное отверстие в диафрагме и трубу 14. Следовательно, в этом случае уровень пульпы должен подниматься выше нижней точки центрального отверстия. Открытие и закрытие отверстий в решетке, а также очистку этих отверстий и колосников производят через люки, предусмотренные в крышке. Колосники устанавливают на решетке так, что во время вращения барабана они могут перемещаться в радикальном направлении и таким образом самоочищаться. Загрузку шаров в мельницу и их выгрузку производят через люки 7.
Исходный материал вместе с определенным объемом жидкости поступает в специальный приемный короб, устанавливаемый под улитковым питателем. Днище короба имеет цилиндрическую форму с радиусом цилиндра, несколько большим радиуса вращения крайней точки черпака питателя. При вращении барабана вместе с ним вращается и питатель, захватывая черпаком пульпу из короба. Зачерпнутая питателем пульпа по улитке проходит через загрузочный вкладыш 2 в зону измельчения, а измельченный материал также в виде пульпы, пройдя разгрузочную диафрагму и выводной вкладыш 13, выходит из мельницы. Мельницы этого типа работают в замкнутом цикле с гидравлическими классификаторами. [2]
2.5 Классификация
Измельчение слюды осуществляется в замкнутом цикле, т.е. материал неоднократно проходит через барабанную мельницу. Измельченный материал из мельницы поступает в классификатор, где из продукта выделяются частицы материала размерами больше допустимого предела, которые возвращаются в ту же мельницу. Частицы размером 315 мкм и меньше удаляются в слив и далее поступают в центрифугу, а частицы с размером больше 315 мкм возвращаются обратно на доизмельчение в мельницу.
Аппаратами для гидравлической классификации являются спиральные классификаторы и гидроциклоны. Первые применяются преимущественно в первой из двух или трех стадий измельчения при небольшой и средней производительности измельчительных переделов. Гидроциклоны могут устанавливаться как в первой, так и во второй стадиях измельчения, а также при доизмельчении продуктов. Гидроциклоны, используемые в качестве классификаторов, обеспечивают то же качество разделения, что и механические классификаторы, но имеют большую производительность. Достоинства гидроциклонов: высокая производительность, отсутствие движущихся частей, компактность, простота и легкость обслуживания, относительно небольшая стоимость. Выбираем в качестве классификатора гидроциклон.
Выбор типоразмеров классифицирующих аппаратов определяется принятой схемой измельчения и производительностью. При выборе гидроциклонов так же необходимо учитывать следующее:
· гидроциклоны большего диаметра надежнее в эксплуатации, чем гидроциклоны малого диаметра. Гидроциклоны диаметром 710 мм и более рекомендуются для классификации материала по граничной крупности 100 150 мкм;
· давление «Р0
» пульпы на входе в гидроциклон при работе последнего в открытом цикле должно быть не менее 0,04 МПа, а для гидроциклонов, работающих в замкнутом цикле - не менее 0,08 МПа. [14]
Исходная пульпа подается в гидроциклон под давлением через питающую насадку 2, установленную тангенциально непосредственно под крышкой аппарата. Пески разгружаются через песковую насадку 3, а слив - через сливной патрубок 4, расположенный в центре крышки и соединенный со сливной трубой 5 непосредственно или через сливную коробку 6 (рисунок 2.5.2).

Рисунок 2.5.2. Гидроциклон: 1 - цилиндроконический сосуд; 2 - питающая насадка; 3 - песковая насадка; 4 - сливной патрубок; 5 - сливная труба; 6 - сливная коробка
Возникающая при вращении пульпы благодаря тангенциальной подаче питания центробежная сила выводит частицы из потока к наружной стенке циклона. Поскольку скорость радиальной миграции частиц пропорциональна плотности частиц и их диаметру в квадрате, то более крупные и более тяжелые частицы успевают выйти из ядра потока, а мелкие, в основной своей массе, остаются в ядре потока. В результате крупная фракция частиц выгружается через песковую насадку, а слив - через сливной патрубок и сливную трубу.
2.6 Центрифугирование
После процессов измельчения и классификации слюдяная пульпа подлежит центрифугированию - разделению в поле центробежных сил. Слюда имеет слишком высокую влажность, поэтому перед подачей в сушилку необходимо произвести отжим и снизить влажность процентов до 30. Процесс центрифугирования проводится в аппаратах, называемых центрифугами. По принципу разделения различают осадительные О, фильтрующие Ф, комбинированные К центрифуги и разделяющие сепараторы Р; по конструктивному признаку - горизонтальные Г, вертикальные В, подвесные с верхним приводом П, маятниковые М; по способу выгрузки осадка - ручная через борт Б, ручная через днище Д, саморазгружающаяся-гравитационная С, ножевая Н, шнековая Ш, вибрационная В. Выбор типа промышленной центрифуги, если неизвестен ее аналог, работающий в промышленности на том же продукте, производится на основе анализа технологических требований, предъявляемых к процессу разделения, свойств суспензии и осадка, мощности производства. В основу такого анализа положен опыт промышленной эксплуатации центрифуг.
Влияние свойств суспензии на выбор типа центрифуги показано в таблице 2.6.1.
Таблица 2.6.1 Влияние свойств суспензии и осадка на выбор типа центрифуги
Тип центрифуги
|
Концентрация суспензии х, %
|
Минимальный размер частиц σ, мкм
|
Скорость осаждения, ω0
∙103
, мм/с
|
∆ρ, кг/м3
|
Осадок зернистый, рыхлый
|
Осадок уплотняющийся мажущий
|
Осадок тексотропный
|
Хорошая растворимость твердой фазы
|
Плохая растворимость твердой фазы
|
Нерастворимая твердая фаза
|
ОМД
ОГШ
ОГН
|
5-30
1-50
5-30
|
1
5
1
|
2-50
>10
2-50
|
>50
>200
>50
|

+

|
+
|
+


|
+
|
+
|
+
|
ФМД
|
>5
|
10
|
Не регламентируется
|
+
|
+
|
+
|
ФМД
ФПД
|

|
ФМН
ФГН
|
10-40
|
30
|

|
спец.
|
спец.
|
ФГШ
ФВШ
ФГП
|
15-50
15-50
20-50
|
150
|
+
|
Как видно из таблицы 2.6.1, пульпу с концентрацией 50% способны разделять следующие центрифуги: ОГШ, ФГШ, ФВШ, ФГП. Но последние три модели центрифуг не подходят для данного технологического процесса. Минимальный размер частиц, которые способны отделить эти центрифуги, равен 150 мкм, что недопустимо, так как большая часть измельченной слюды имеет еще меньший размер и прямиком отправится в слив. ОГШ напротив способна разделять частицы до 5 мкм. И по всем остальным критериям, приведенным в таблице 2.6.1, центрифуга ОГШ подходит, поэтому выбираем ее для процесса отжима слюдяной пульпы.
В таблице 2.6.2 приведены основные факторы, влияющие на выбор размера центрифуги. [13]
Таблица 2.6.2 Влияние заданной производительности на выбор типоразмера центрифуги
Производительность
|
Индекс центрифуги
|
по суспензии, м3/ч
|
по осадку, т/ч
|
1-5
|
0,15-0,5
|
ОМД-80; ОГШ-35; ФГН-63; ФГН-90; ФМД-80; ФМБ-80; ФМБ-120;
ФМД-120; ФПН-100; ФПД-120
|
5-15
|
0,5-3,0
|
ОГШ-35; ОГШ-50; ОГН-180;
ФГН-90; ОГН-90; ФГН-125;
ФВШ-35; ½ ФГП-40; ½ ФГП-63
|
15-25
|
3-6
|
ОГШ-5; 20ГН-220; ФГШ-35;
ФГШ-40; ФГН-180; ½ ФГП-80
|
>25
|
>6
|
ОГШ-63; ОГШ-80; ФГН-200;
½ ФГП-120
|
Как уже говорилось выше, при производстве слюдопластовой бумаги образуется 2 тонны слюдяной пульпы в сутки, с учетом того, что ее влажность составляет 50%, а центрифугирование проводится до влажности 30%, производительность по осадку будет равна 1,43 т/сут. В сутки установка по переработке отходов работает 7 часов, поэтому часовая производительность равна 0,2. Слюда флогопит является среднеабразивным материалом - это также следует учитывать, центрифуга ОГШ допускает абразивные свойства твердой фазы. Таким образом, предварительно выбираем одну из центрифуг ОГШ с небольшой производительностью - ОГШ-35.
На рисунке 2.6.1 приведена конструктивная схема осадительной горизонтальной шнековой центрифуги непрерывного действия.

Рисунок 2.6.1. Осадительная горизонтальная шнековая центрифуга непрерывного действия: 1 - защитное устройство редуктора; 2 - окна выгрузки осадка; 3 - кожух; 4 - питающая труба; 5 - сливные окна; 6, 11 - опоры центрифуги; 7 - штуцер отвода фугата; 8 - шнек; 9 - ротор; 10 - штуцер выгрузки осадка; 12 - планетарный редуктор
Общим конструктивным признаком центрифуг типа ОГШ (НОГШ) является горизонтальное расположение оси неперфорированного конического или цилиндроконического ротора с соосно-расположенным внутри пего шнеком. Ротор и шнек вращаются в одном направлении, но с различными скоростями, так что образующийся осадок перемещается шнеком вдоль ротора. Ротор расположен на двух опорах и приводится во вращение от электродвигателя через клиноременную передачу. Шнек приводится во вращение от ротора центрифуги через планетарный редуктор. Ротор закрыт кожухом, имеющим внизу штуцер для отвода осадка и фугата.
Суспензия подается по питающей трубе во внутреннюю полость шнека, откуда через окна обечайки шнека поступает в ротор. Под действием центробежной силы происходит ее разделение, и на стенках ротора осаждаются частицы твердой фазы. Осадок транспортируется шнеком к выгрузочным окнам, расположенным в узкой части ротора. Осветленная жидкость течет в противоположную сторону к сливным окнам, переливается через сливной порог и выбрасывается из ротора в кожух. Диаметр сливного порога можно регулировать с помощью сменных заслонок или поворотных шайб. Скорость вращения изменяется путем смены приводных шкивов.
Центрифуга обычно снабжена защитным устройством, которое отключает ее при перегрузке, одновременно включая световой или звуковой сигнал. В некоторых случаях центрифуги комплектуют трубой для подачи промывных жидкостей, однако поскольку промывка осадка в центрифугах рассматриваемого типа малоэффективна, ее заменяют обычно репульпацией выгружаемого осадка.
Технологический режим в центрифугах ОГШ регулируют, изменяя скорость подачи суспензии, скорость вращения ротора, диаметр сливного порога. Степень осветления фугата можно повысить, уменьшив диаметр сливного порога (увеличив длину зоны осаждения) и увеличив скорость вращения ротора; степень просушки (степень влажности) осадка - увеличив диаметр сливного порога (увеличив длину зоны сушки) и скорость вращения ротора. [10]
2.7 Сушка
Одной из основных стадий технологического процесса по переработке отходов слюды является сушка. Процесс осуществляется в сушилке с кипящим слоем. Эти аппараты широко распространены в химической и смежных отраслях промышленности, поскольку в аппаратах такого типа можно высушивать зернистые, пастообразные и жидкие материалы. В сушилках с кипящим слоем обычно сушат продукты с размерами зерен от 0,1 до 5,0 мм. Процесс протекает с большой скоростью, съем влаги с 1 м2
газораспределительной решетки в зависимости от размера частиц материала и температурного режима сушки составляет 500-3000 кг/(м2
∙ч). В установках со взвешенным слоем можно одновременно проводить несколько процессов, например сушку и обжиг, сушку и гранулирование, сушку и измельчение. Эти аппараты отличаются высокой надежностью, сокращением времени сушки за счет усиленного перемешивания материала в сушильной камере. Сушилки кипящего слоя просты как в конструктивном исполнении, так и в эксплуатации, обладают высокими эксплуатационными показателями, легко поддаются автоматизации. Корпус сушилок кипящего слоя неподвижен, что значительно упрощает требования к монтажу и эксплуатации. Эффективность сушки в кипящем слое, в значительной мере, зависит от правильного определения конструктивных и технологических параметров сушилки, правильного выбора аппаратурного оформления. Как правило, параметры сушилок кипящего слоя определяются для сушки конкретного материала и учитывают начальную и конечную влажность материала, его физико-механические свойства, требования к температурному режиму, минимизации или максимизации уноса мелких фракций и другие требования, предъявляемые к материалу и процессу сушки. [6]
Кипящим слой (КС) является, в принципе, одним из видов взвешенного слоя. Взвешенный слой образуется в бинарных гетерогенных системах газ -твердое, газ - жидкость, жидкость - твердое и жидкость - жидкость (несмешивающиеся жидкости) при пропускании с определенными скоростями потока менее плотной фазы (газа или жидкости) снизу вверх через слой более плотной фазы (дернистого материала или жидкости). Взвешенный слой получают и в трехфазных системах, например, при пропускании газа через суспензию мелких зерен в жидкости.
Во всех системах взвешенный слой характеризуется тем, что вес тяжелой фазы (сила тяжести) уравновешивается трением газа о зерна или пленку жидкости (в сочетании с архимедовой силой). Тяжелая фаза не лежит на опоре, а подвешена в потоке легкой. Зерна твердого материала или пленки и капли жидкости плавают в потоке легкой фазы, пульсируют, совершают вихревые движения, но не покидают пределов слоя при значительном увеличении линейной скорости легкой фазы вследствие одновременного увеличения порозности, т. е. доли легкой фазы в слое. Взвешенный слой неоднороден, он пронизан пузырями или струями легкой фазы.
Взвешенный слой в системе газ - твердое в зависимости от характера взвешивания (псевдоожижения) зерен и соответствующих конструкций аппаратов подразделяют на ряд видов, имеющих соответственные наименования, в том числе: кипящий (КС), фонтанирующий и т. д.
КС образуется в аппаратах, представляющих собой камеру или колонну круглого либо прямоугольного сечения, разделенную одной или несколькими ситчатыми либо колпачковыми решетками и снабженную приспособлениями (например, штуцерами) для ввода и вывода реагирующих фаз. При очень малых линейных скоростях непрерывного потока газа зернистый слой лежит на решетке. По мере возрастания скорости увеличивается сила трения газа о зерна и давление зерен на решетку уменьшается. При первой критической скорости (называемой скоростью взвешивания или скоростью псевдоожижения) вес слоя зерен уравновешивается силой трения газа в совокупности с архимедовой подъемной силой, зерна взвешиваются в потоке газа и не оказывают давления на решетку. Ввиду незначительности архимедовой силы можно приближенно считать, что сила тяжести равна силе трения газа о зерна. Следовательно, и перепад давления в слое равен его весу, отнесенному к единице поперечного сечения решетки. Решетка служит в основном для распределения потока газа по сечению аппарата и в слое зерен. Решетка также ограничивает пульсации зерен.
В дальнейшем при увеличении скорости газа количество газовых пузырей в слое и их размеры увеличиваются настолько, что суммарная порозность КС возрастает пропорционально скорости газа. При этом высота слоя увеличивается, а гидравлическое сопротивление остается неизменным во всем диапазоне скоростей газа, соответствующих существованию КС. По виду слой сходен с кипящей жидкостью; в нем возникают пузыри газа, которые увеличиваются при подъеме и выталкивают фонтанчики зерен при выходе из слоя. При значительных скоростях газа пузырьковый режим кипения переходит в агрегатный (пакетный). Газовые пустоты в виде крупных пузырей и струй уже составляют большую часть объема слоя, становятся непрерывной фазой, в которой плавают, совершают вихревые движения агрегаты зерен с порозностью, близкой к порозности неподвижного слоя. В слое большого сечения отмечается наличие зон с преимущественно восходящим и нисходящим потоком частиц.
При значительном увеличении фиктивной скорости газа, рассчитанной на полное сечение аппарата, КС разрушается и зерна уносятся из аппарата. Отношение скорости уноса твердых частиц к скорости взвешивания их может составлять для мелких зерен до 50, а для крупных (2 - 4 мм) - около 15.
Важным свойством взвешенного слоя является его текучесть, подобная текучести жидкости. Так, применение КС катализатора при крекинге обеспечивает циркуляцию катализатора между контактным аппаратом и регенератором. Вследствие текучести КС его называют также ожиженным или псевдоожиженным. Циркуляционное движение зерен и газа внутри слоя дало ему еще одно название - вихревой слой.
Значительное перемешивание зернистого материала наряду с положительным эффектом выравнивания температуры одновременно приводит к неодинаковому времени пребывания частиц в объеме КС при непрерывной их подаче и выгрузке из аппарата, следствием чего является различная степень обработки отдельных порций выгружаемого из аппарата материала. Это существенно для процессов, в которых желательна равномерная степень обработки дисперсного материала, или в тех случаях, когда излишнее время экспозиции частиц приводит к нежелательным эффектам, например к термическому разложению пересушенного и перегретого материала, переукрупнению кристаллов и т. п.
Истирание части твердого материала вызывает унос его в виде пыли, обусловливает необходимость очистной аппаратуры, габариты которой обычно превышают размеры собственно КС, приводит к потерям ценных веществ и загрязнению ими продукции, получаемой из газовой фазы. В КС истираются также конструктивные элементы аппаратов.
Для равномерного распределения газа по сечению слоя необходимы решетки с малым свободным сечением (1,5 - 2,0 %), что вызывает рост гидравлического сопротивления в многополочных аппаратах и увеличивает вероятность забивания отверстий решетки.
Отдельные недостатки аппаратов КС уменьшаются или снимаются путем применения других видов взвешенного слоя, прежде всего фонтанирующего. Аппарат фонтанирующего слоя представляет собой усеченный конус. Газ проходит в основном в центральной зоне, составляющей лишь около 10% объема всего слоя. Зерна увлекаются струей газа и выбрасываются фонтаном, а расширенную часть аппарата, где теряют скорость, а затем сравнительно медленно опускаются вниз в периферийной зоне. Пройдя до нижней узкой части аппарата зерна вновь подхватываются струей газа и поднимаются вверх. В аппаратах фонтанирующего слоя можно не устанавливать распределительную решетку, так как скорость газа в нижней узкой части конуса выше скорости начала взвешивания. Это дает возможность использовать аппараты фонтанирующего слоя для особо высокотемпературных процессов и при переработке агрессивных сред, т. е. в тех случаях, когда неприменимы металлические решетки. Фонтанирующий слой позволяет обрабатывать полидисперсные материалы с меньшим уносом, чем в аппаратах КС, однако он имеет и специфические недостатки, прежде всего малую долю активной зоны. Конусные аппараты имеют малую мощность, и поэтому аппарат большой производительности конструируют из длинных коробов с днищем треугольного сечения, в нижней части которого расположены щелевые отверстия для входа газа.
Имеются и другие виды фонтанирующего слоя, в том числе с тангенциальным вводом газа в аппарат с днищем корытообразного типа. Газ полается в днище снизу тангенциально с таким расчетом, чтобы движение зернистого материала происходило вращательно; по одной стороне аппарата - восходящим потоком, а по другой - нисходящим.
Виброкипящий слой получают в аппаратах КС с вибрирующими поверхностями в слое. Благодаря вибрации усиливается перемешивание материала и уменьшаются размеры пузырей.
Применяются также аппараты с закрученными потоками различного типа, в том числе вихревые. [8]
Наиболее простыми по конструкции являются аппараты кипящего слоя постоянного или несколько расширяющегося по высоте сечения. Они нашли широкое применение в промышленности. Недостатки кипящего слоя в таких аппаратах:
· невозможность повышения скорости сверх значения, соответствующего верхней границе существования кипящего слоя;
· трудность обработки полидисперсных систем;
· недостаточно интенсивный гидродинамический режим вблизи решетки, что приводит к ее заплавлению в высокотемпературных процессах при обработке полидисперсных и термолабильных материалов и в процессах с вводом в слой жидкой фазы.
Указанные недостатки ограничивают возможности повышении производительности этих аппаратов, и в ряде отраслей в упомянутых выше случаях применяют аппараты расширяющегося по высоте сечения (коническо-цилиндрические), работающие в режиме фонтанирования.
Преимущества таких аппаратов следующие:
· закономерное изменение скорости снизу вверх позволяет одновременно обрабатывать твердые частицы различных размеров и в режимах различной интенсивности;
· достаточно высокие скорости в нижней части аппарата позволяют, особенно при значительных углах раствора конуса, обрабатывать вещества, длительный контакт которых с решеткой недопустим, комкающиеся и слипающиеся вещества, а также вводить в слой жидкости и пасты.
Так как в данном технологическом процессе по переработке слюдопластовых отходов производится сушка молотой слюды, которая характеризуется полидисперсностью, то применение цилиндрического аппарата неуместно ввиду большого уноса частиц. Поэтому аппарат над решеткой выполняем коническим с углом при вершине 20°. Таким образом, кипящий слой будет слегка фонтанировать, тем самым снижая скорость витания частиц и их унос.
На рисунке 2.7.1 приведена типовая конструкция сушильной установки кипящего слоя с цилиндрической сушилкой.

Рисунок 2.7.1. Схема сушильной установки с цилиндрической сушилкой: 1 - бункер; 2 - питатель; 3 - сушильная камера; 4 - топка; 5 - патрубок для выгрузки продукта; 6 - циклон; 7 - бункер циклона; 8 – фильтр
Влажный материал из бункера 1 шнековым (или другой конструкции) питателем 2 непрерывно подается в сушильную камеру 3 в слой «кипящего» материала. Топочные газы из топки 4 смешиваются с воздухом в смесительной камере и затем подаются с помощью турбогазодувки или вентилятора под опорную решетку. Разгрузка высушенного продукта производится через патрубок 5, расположенный непосредственно над решеткой, со стороны, противоположной загрузке. Отработанные запыленные газы направляются и циклон 6 с бункером 7, где выделяется основная часть унесенного газами сухого материала; окончательная очистка газов происходит в рукавном фильтре 8. [6]
Топочные газы в смеси с атмосферным воздухом широко используют при сушке различных материалов, в том числе и органических продуктов. Многие материалы, например песок, глину, топливо, неорганические соли и т. д., высушивают при довольно высоких температурах - от 300 до 800 С
С и выше. Для этой цели можно использовать топочные газы, разбавляя их до нужной температуры атмосферным воздухом. Преимущества сушки топочными газами: возможность получения высоких температур; простота топочных устройств; возможность непосредственного применения отработанных газов котельных установок, печей и других агрегатов. Топочные газы получают при сжигании газообразного, жидкого (мазут, нефть) или твердого (уголь, торф) топлива в топках и смешивают их в специальных камерах (камерах смешения) с атмосферным воздухом для получения смеси определенной температуры.
Топочные (дымовые) газы состоят из кислорода, азота, окиси и двуокиси углерода, сернистого газа и водяных паров. Состав топочных газов зависит от количества воздуха, подводимого в топку для сжигания топлива (первичный воздух) и подмешиваемого к продуктам сгорания для понижения их температуры до заданной (вторичный воздух). Природный газ производит меньше СО2
на единицу энергии, чем другие виды ископаемых топлив. Поэтому подогрев сушильного агента производится за счет сгорания именно газа, а не, к примеру, мазута. Выбросы в атмосферу при сжигании ископаемого топлива зависят не только от вида топлива, но от того, насколько эффективно оно используется. Газообразное топливо обычно сжигается легче и эффективнее, чем уголь или нефть. Утилизация сбросной теплоты от отходящих газов в случае природного газа осуществляется также проще, так как топочный газ не загрязнен твердыми частицами или агрессивными соединениями серы. Благодаря химическому составу, простоте и эффективности использования природный газ может внести существенный вклад в снижение выбросов диоксида углерода путем замены им ископаемых видов топлив.
Во избежание пережога слюды для каждого вида отходов устанавливается определенная температура отжига; для слюды мусковит 400 - 500° С, для флогопита 400 - 600° С. Поэтому сушку лучше производить при температуре 300 - 400° С.
На рисунке 2.7.2 показана топка для сжигания газа с использованием эжекционной горелки внутреннего смешения. Отличительной особенностью такой топки является зазор между камерой горения и кожухом, куда тангенциально подается вторичный воздух. Воздух охлаждает наружную стенку камеры горения и затем смешивается с продуктами сгорания. При воздушном охлаждении камера может быть футерована в один кирпич, сжигание топлива можно вести при высоких температурах. Так как температура теплоносителя, используемого для сушки, обычно не превышает 700 - 800 °С, в топочных устройствах имеется специальная камера, топочные газы разбавляются воздухом до нужной температуры. Топка может работать как под давлением, так и при разрежении. Тепловое напряжение достигает 1,75∙106
Вт/м3
, т. е. 1,5∙106
ккал/(м3
∙ч), и зависит от температуры в камере горения и давления.
Основное требование, предъявляемое к топочным устройствам, - обеспечение полного сгорания топлива. Особенно это относится к устройствам, работающим на жидком топливе (об использовании твердого топлива здесь не говорится, поскольку в последнее время его редко применяют в сушильных установках на химических производствах). Таким образом, топливные форсунки должны обеспечивать тонкое диспергирование мазута, чтобы не происходило проскока крупных капель в сушилку и порчи продукта. В сушилке со взвешенным слоем это может привести к сгоранию капель мазута на газораспределительной решетке и забиванию отверстий. Несгоревшее топливо, осевшее на стенках газоходов и в циклонах, может стать причиной пожаров.
Если топка еще горячая, при пуске установки нужно следить за тем, чтобы мазут был подогрет, а конденсат (когда распыление топлива производится паром) спущен из линии подогрева мазута, так как холодный мазут и конденсат, попав на свод топки, вызовут его растрескивание. Смешение продуктов сгорания с воздухом должно быть полным. Для этого в камере смешения необходимо устанавливать пороги или завихрители.
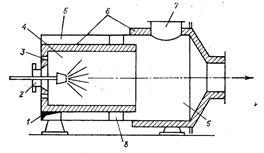
Рисунок 2.7.2. Топка с охлаждением наружной стенки камеры горения: 1 - окно для ввода вторичного воздуха; 2 - гнездо для установки горелки: 3 - смотровое отверстие; 4 - камера горения; 5 - камера смешения: 6 - футеровки; 7 - взрывной клапан; 8 - опора.
Пылеотделители используют для отделения пыли от потока уходящего теплоносителя с целью более полного выделения продукта, а так же для предотвращения загрязнения окружающей среды. Методы выделения твердых частиц из газового потока разделяют на сухие и мокрые. При сухой очистке используют пылеосадительные камеры, циклоны и рукавные фильтры. Для мокрой очистки применяют мокрые скрубберы и пенные газопромыватели.
Пылеосадительные камеры в химической промышленности используют редко ввиду их низкой эффективности. Интенсивное и эффективное выделение твердых частиц из запыленного газа достигается под действием центробежной силы в циклонах, конструкция которых представлена на рисунке 2.7.3. Запыленный газ поступает в верхнюю цилиндрическую часть 1 циклона по газоходу прямоугольного сечения 2. Сверху циклон закрыт крышкой 3, на которой помещен цилиндрический патрубок 4. Нижняя коническая часть циклона заканчивается выгрузочным отверстием. Попадающий в циклон запыленный газ приобретает вращательное движение, частицы пыли под действием центробежной силы отбрасываются к периферии и сползают по стенкам вниз, а обеспыленный газ выводится сверху. На практике все циклоны снабжаются бункером (на схеме не показан), и разгрузка пыли производится из бункера, что уменьшает вторичный унос, т. е. вынос пыли потоком уходящего из циклона воздуха.

Рисунок 2.7.3. Схема действия циклона: 1 - цилиндрическая часть; 2 - патрубок для входа газа; 3 - крышка; 4 - патрубок для выхода газа; 5 - коническая часть.
Степень очистки газов в циклонах составляет 70 - 95% и зависит от свойств пыли. Чем крупнее и тяжелее частицы, тем лучше они улавливаются. Концентрация пыли в газе влияет на степень очистки не очень существенно. Следует иметь в виду, что с увеличением скорости газа в циклоне величина центробежной силы растет, но одновременно увеличивается гидравлическое сопротивление аппарата.
При необходимости обеспечения высокой производительности иногда устанавливают групповые или батарейные циклоны, так как делать один циклон большого диаметра нецелесообразно: с увеличением радиуса циклона будет уменьшаться величина центробежной силы и ухудшаться очистка (поэтому не рекомендуется ставить циклоны диаметром более 800 мм). Можно использовать батареи по два, четыре, шесть, восемь циклонов, работающих параллельно. При очистке газов от очень тонких пылей, имеющих низкую плотность (т. е. когда масса частицы очень мала), для увеличения центробежной силы необходимо уменьшить радиус циклона (скорость газа увеличивать не следует). В этом случае устанавливают батареи, состоящие из нескольких десятков, а иногда и сотен циклонов диаметром 150 - 200 мм. Запыленный газ вводится в кольцевой зазор, образуемый корпусом каждого циклона и выходным патрубком, а для закручивания потока внутренняя труба снабжается винтовой вставкой. Степень очистки в батарейных циклонах ниже, а гидравлическое сопротивление выше, чем в одиночных циклонах.
Для нормальной работы циклона необходимо своевременно удалять пыль из буккера, так как при большом уровне пыли она будет частично захватываться потоком газа и степень очистки снизится. Степень очистки резко уменьшается при наличии неплотностей в циклоне, поскольку засасываемый снаружи воздух движется навстречу ссыпающейся пыли и часть ее выбрасывается в выхлопную трубу. Вследствие этого обязательна проверка герметичности циклонов, как при приемке смонтированной установки, так и периодически при ее эксплуатации. Газоходы от сушилок до циклонов могут забиваться пылью (особенно колена и горизонтальные участки), поэтому их необходимо монтировать с наименьшим количеством поворотов и без горизонтальных участков, снабжать специальными люками для чистки. В некоторых случаях для предотвращения быстрого зарастания стенок циклона улавливаемым материалом аппарат снабжают водяной рубашкой, причем температура воды должна быть на несколько градусов выше точки росы.
В данном технологическом процессе достаточно установить для очистки газа два циклона или один циклон и рукавный фильтр. Второй вариант более предпочтителен, так как позволяет практически полностью очистить газ от частиц слюды.
Рукавные фильтры, предназначенные для отделения пыли от уходящих из сушилки газов, обычно ставят после циклонов, однако при сравнительно небольшой запыленности (если основное количество сухого материала выгружается из сушилки) они могут быть единственными пылеочистными устройствами в установке, так как при правильном выборе ткани степень очистки превышает 99 %. Внутри кожуха 3 фильтра (рисунок 2.7.4) вертикально расположены сшитые из ткани рукава (мешки) 4 длиной до 3,6 м и диаметром около 200 мм. Снизу рукава открыты и закреплены на трубной доске, замыкающей нижнюю камеру 2. Сверху рукава закрыты и подвешены на крючках к раме 6 со штангой, выходящей из кожуха. Запыленный газ поступает в аппарат по газоходу 7 в нижнюю камеру, движется вверх по рукавам и через поры ткани выходит в пространство между рукавами и кожухом, а затем удаляется по верхнему газоходу 5. Осевшая внутри рукавов пыль периодически удаляется из них при встряхивании с помощью кулачкового механизма, соединенного с верхней штангой. Одновременно со встряхиванием рукава продуваются воздухом, который специальным небольшим вентилятором подается в направлении, противоположном направлению движения обеспыленного газа. Во время продувки кожух фильтра автоматически отключается от газохода 5. Ссыпавшаяся в коническую часть кожуха пыль удаляется через выгрузочное отверстие 8 шнеком. Обычно фильтр состоит из нескольких камер, одна из которых отключена на очистку, тогда как в остальных идет фильтрование. Переключение происходит автоматически.
Рисунок 2.7.4. Рукавный фильтр: 1 - днище; 2 - нижняя камера; 3 - кожух; 4 - рукав: 5, 7 - газоходы; 6 - рама; 8 - выгрузочное отверстие
При сушке необходимо дозировать, а часто и диспергировать материал, подаваемый в сушилку. В некоторых случаях питатель должен служить одновременно затвором между сушильной камерой и окружающим пространством.
На рисунке 2.7.5 показан лопастной питатель-затвор, применяемый для загрузки и выгрузки материала из сушилок, выгрузки пыли из циклона и т. д.
Рис 2.7.5. Лопастный затвор: 1 - сальник; 2 - ротор; 3 - корпус: 4 - вал
Газораспределительные решетки являются одним из основных элементов сушилок, работающих с кипящим (псевдоожиженным) слоем материала. Они выполняют функцию поддерживающей конструкции для кипящего слоя и способствуют равномерному распределению теплоносителя по сечению сушилки. Решетка должна удовлетворять следующим требованиям: I) обеспечивать равномерное газораспределение; 2) провал материала в подрешеточное пространство должен быть минимальным; 3) быть простой в изготовлении и надежной в работе (легкая очистка, ремонт); 4) гидравлическое сопротивление не должно превышать 1,5 - 2,0 кПа. Решетки распределительного типа, изображенные на рисунке 2.7.6, могут быть плоскими, вогнутыми, выпуклыми; направление струй из колпачков и барботеров - различными.

Рисунок 2.7.6. Газораспределительные решетки: а - перфорированная; б - колпачковая; в - барботажная подача газа
В сушильных установках используют обычно вентиляторы типа ВВД. Центробежные вентиляторы высокого давления серии ВВД (номера 8; 9 и 11) предназначены для перемещения воздуха и газов (при температуре до 100 °С), не содержащих липких и длинноволокнистых веществ. Содержание пыли в среде не должно превышать 150 мг/м3
. Вал вентилятора ВВД-11 приводится во вращение от электродвигателя при помощи эластичной муфты, а вал вентиляторов ВВД-8 и ВВД-9 - при помощи ременной передачи и эластичной муфты. Эти вентиляторы создают давление до 10 кПа (1000 мм вод. ст.) и имеют производительность до 20000 м3
/ч (в зависимости от номера).
В сушильной установке надо следить за тем, чтобы заданное количество газов (по регламенту) проходило через сушилку, поэтому не должно быть неплотностей в системе и гидравлическое сопротивление всех аппаратов не должно превышать норму.
Сушилки кипящего слоя принадлежат к наименее металлоемким, наиболее простым, а, следовательно, дешевым аппаратам и отличаются от остальных сушилок высокой эффективностью процесса. Несомненно, на рентабельности сушилок кипящего слои сказывается значительная стоимость изготовления решетки, а также необходимость периодической ее чистки. Поскольку расход тепла в газовых сушилках колеблется в небольших пределах и тем меньше, чем меньше удельный расход газов (так как при этом уменьшаются потери тепла с отработанными газами), то в однокамерных сушилках кипящего слон при удельном расходе сушильного агента 5 - 20 кг/кг влаги расход тепла меньше, чем в барабанных сушилках. Только расход энергии на дутье иногда превышает эту же статью расхода в сушилках других типов.
Как уже было отмечено, экономичность сушилки тем выше, чем меньше удельный расход газов. Поэтому особенно выгодны однокамерные сушилки, и, по возможности, именно эти аппараты и следует применять. Более сложные и дорогие многокамерные аппараты возможно рекомендовать лишь в тех случаях, когда это оправдано, т. е. при необходимости снижения температуры теплоносителя по зонам, для получения равномерно высушенного продукта и т. д.
Поскольку во всех газовых сушилках применяются более или менее однотипные пылеулавливающие аппараты и установки для получения теплоносителя, то увеличение расхода энергии в сушилках кипящего слоя происходит только из-за гидравлического сопротивления слоя. [7]
2.8 Транспортирование материала
При выборе типа, конструкции и исполнения транспортирующих аппаратов необходимо учитывать следующие факторы:
1) состояние транспортируемого материала, его физические и химические
свойства (крупность кусков, хрупкость, коррозионные свойства, возможное измельчение при перемещении, склонность материала к слипанию и слеживанию, плотность, угол естественного откоса, размеры);
2) производительность машины;
3) длину и траекторию перемещения, размеры и форму помещений;
4) технологический прогресс, перспективы развития предприятия;
5) технику безопасности;
6) хранение материалов и способы загрузки и разгрузки транспортных устройств;
7) климатические условия (для установок, работающих на открытых площадках);
8) экономические показатели.
Из отстойника отходы слюдопластового производства перемещаются в приемный короб барабанной мельницы при помощи винтового конвейера.
К преимуществам винтовых конвейеров относятся компактность, герметичность, простота конструкции и эксплуатации, удобство промежуточной разгрузки, а также возможность транспортирования мокрых и тестообразных материалов (при специальной форме винта). Конструкция винтового конвейера позволяет совмещать операцию транспортирования материалов с некоторыми технологическими процессами (охлаждение, увлажнение, сушка, смешивание). Эти достоинства определяют применение данного аппарата в установке по переработке отходов слюдопластового производства. Конвейер находится в наклонном положении, поэтому слюда будет частично не только измельчаться при перемещении, но и обезвоживаться. Конструкция винтового транспортера представлена на рисунке 2.8.1.
Винтовой конвейер состоит из неподвижного желоба 4 полукруглой формы, внутри которого расположен рабочий орган - винт 5, вращающийся в подшипниках 3. Винт вращается при помощи привода 8, состоящего из электродвигателя и редуктора. Транспортируемый материал загружается через загрузочное отверстие 2. Материал под действием винта поступательно движется по желобу. При этом вращение материала вместе с винтом исключено, так как этому препятствует сила тяжести частиц материала. Разгрузка винтового конвейера может производиться в любом месте по его длине через патрубок 6 с задвижкой 7. Желоб сверху обычно закрывается крышкой 1. Винтовые конвейеры хорошо зарекомендовали себя при транспортировании пылящих (кальцинированная порошкообразная сода, апатитовый концентрат, фосфоритная мука, колчеданный огарок), остро пахнущих и горячих выделяющих газы и пары материалов. Их используют также для транспортирования вязких и тестообразных (мокрая глина и т.д.) материалов.

Рисунок 2.8.1. Горизонтальный винтовой конвейер: 1 - крышка; 2 - загрузочное отверстие; 3 - подшипник; 4 - неподвижный желоб; 5 - винт; 6 - патрубок; 7 - задвижка; 8 – привод
Винтовые конвейеры незаменимы в небольших помещениях, когда необходимо транспортировать малое количество материала на короткие расстояния. Поэтому винтовой транспортер также используется и для перемещения отжатой в центрифуге слюды в бункер сушилки кипящего слоя.
Применяются винтовые конвейеры с винтом следующих размеров: диаметр 100 600 мм, длина до 30 40 м, а в отдельных случаях до 50 60 м. Производительность винтовых конвейеров составляет в среднем 20 40 м3
/ч, но при больших размерах винта может доходить до 100 м3
/ч и более. Винтовые конвейеры выполняют горизонтальными или пологонаклонными (устанавливают под углом до 20° к горизонту) и вертикальными (для перемещения порошкообразных удобрений, поташа, крахмала, соли и др.). В конструкции вертикального конвейера предусматривается подача материала от горизонтальных винтовых конвейеров, которые создают подпор материала.
Для транспортирования высушенного порошка слюды из сушилки кипящего слоя в фасовочно-упаковочный аппарат лучше использовать ленточный транспортер, чем винтовой. Порошок будет быстрее остывать на открытой ленте, чем в закрытом желобе. Лента должна быть в таком случае жаропрочной.
Ленточный конвейер является широко распространенным типом транспортирующих устройств непрерывного действия с тяговым органом. Основной рабочий орган ленточного конвейера - гибкая замкнутая лента, на которой транспортируется груз. В ленточных конвейерах в качестве тягового элемента применяются резинотканевые (ГОСТ 20-85, ГОСТ 23831-79), резинотросовые (ТУ 38-105841-75) и стальные (ТУ-14-1-525-73) ленты. Область применения ленточных конвейеров достаточно широка: механизация, загрузка и разгрузка складов сырья, подача сырья из склада в цех, перемещение грузов от одного аппарата к другому, транспортирование готового продукта из цеха в склад и т.д.
К достоинствам ленточных конвейеров следует отнести высокую производительность (до 1000 м3
/ч и более), широкий диапазон скоростей и
размеров (ширины ленты), непрерывность и равномерность перемещения грузов, пригодность для транспортирования на большие расстояния, простоту устройства и эксплуатации, небольшие энергозатраты и пригодность для перемещения как мелкозернистого сыпучего материала, так и крупнокускового, а также штучных и тарных грузов. В качестве недостатков ленточных конвейеров можно отметить непригодность обычной текстильной ленты для транспортирования горячих спекающихся материалов, возможность химического и механического разрушения, пыление при перемещении порошкообразных материалов и сравнительно малые допускаемые углы наклона конвейера к горизонту. [4]
2.9 Технические решения
При производстве слюдопласта, в частности слюдопластовой бумаги, на Слюдяной фабрике в г. Колпино образуется более 500 м3
отходов в год. Они представляют собой нерасщепленные пластинки и чешуйки слюды со средним размером 20 мм. Отходы находятся в отстойнике в водной среде и имеют 3-4 класс опасности. Складирование, вывоз и утилизация отходов не только наносят вред окружающей среде, но и являются экономически нецелесообразными. В настоящей работе принято решение о переработке этих отходов. Получаемый порошок слюды флогопит ГОСТ 19571-74, 19572-74, 19573-74 имеет влажность не более 3 % и размер частиц до 315 мкм. Данные качественные показатели вырабатываемой продукции определяют технологию производства, а с учетом заданной производительности, равной 1 тонне порошка в сутки, и основные конструктивные параметры оборудования. Таким образом, отходы подлежат помолу до необходимой тонины и сушке с предварительным центрифугированием. Итак, в данном дипломном проекте на тему «Установка для переработки отходов слюдопластового производства» приняты следующие технические решения:
· Отходы транспортируются из отстойника в мельницу при помощи наклонного шнекового транспортера, частично измельчаясь и обезвоживаясь;
· В качестве измельчителя используется шаровая барабанная мельница мокрого помола с волнистой футеровкой и улитковым питателем, периодически захватывающим слюду из приемного короба и направляющим материал в барабан;
· Мельница работает в замкнутом цикле с гидравлическим классификатором. Гидроциклон отправляет деловую фракцию на дальнейшую переработку, а недомол - обратно в барабанную мельницу;
· Для перекачки пульпы используются песковые или дисковые насосы, позволяющие перемещать материал с относительно высокой плотностью и содержанием твердого;
· Слюдяная пульпа подлежит отжиму в осадительной горизонтальной шнековой центрифуге до влажности 30%;
· Осадок шнековым транспортером направляется в сушилку кипящего слоя, которая может работать в непрерывном, периодическом и полунепрерывном режиме, сушка производится топочными газами с температурой 330 °С до влажности 1 %;
· Для снижения уноса частиц слюды корпус сушилки выполняется расширяющимся;
· Уносимые из сушильной камеры частицы улавливаются газоочистной системой, состоящей из циклона и рукавного фильтра;
· Высушенная слюда транспортируется ленточным конвейером к фасовочно-упаковочному аппарату, где порошок фасуют в полипропиленовые мешки массой по 30 кг и запаивают;
Установка разработана для переработки отходов слюдопластовой бумаги, но может быть также использована для переработки и других отходов слюдяного производства. Наиболее крупные отходы могут поступать в барабанную мельницу через барабанный питатель, конструкция которого скомбинирована с улитковым питателем. Также возможно проведение измельчения в две стадии с использованием, например, роторной дробилки;
При переработке слюдопластовых отходов, содержащих в себе примеси, в сушилке кипящего слоя возможно проведение обжига. Наличие в этих отходах лака, смолы, бумаги и других примесей не дает возможности вторичного использования такой слюды без предварительной очистки. Одним из наиболее рациональных способов извлечения слюды из отходов является способ выжигания. Под воздействием высокой температуры сгорают органические примеси и образующиеся при этом углеродистые соединения уносятся потоком воздуха. Регенерированная слюда после обжига подвергается очистке на сортировочных машинах и может найти применение в производстве коллекторного миканита.
3. ТЕХНОЛОГИЧЕСКИЕ РАСЧЕТЫ
3.1 Расчет барабанной мельницы
Технологический расчет шаровой мельницы для мокрого помола слюды заключается в определении диаметра и длины барабана и параметров его загрузки. Для определения диаметра барабана воспользуемся формулой расчета производительности мельницы. Производительность шаровых мельниц зависит от многих факторов, учесть которые теоретически обоснованной формулой сложно, поэтому практически ее рассчитывают по эмпирическим приближенным формулам, учитывающим лишь некоторые основные факторы.
В химической и горно-металлургической промышленностях принята эмпирическая формула
Q = k∙V∙D0,6
,(3.1.1)
где k - опытный коэффициент, учитывающий влияние размеров шаров, шаровую загрузку, плотность пульпы при мокром помоле, природу измельчаемого материала, крупность питания и готового продукта, циркуляционную нагрузку, схему измельчения и др.;
V - объем барабана, м3
;
D - внутренний диаметр барабана, м.
Коэффициент k определяем по формуле:
k = (2,3∙10-3
8∙10-3
)∙(dн
/dк
), (3.1.2)
где dн
- средний диаметр частиц материала до измельчения, равный 20 мм;
dк
- средний диаметр частиц материала после измельчения, равный 0,3 мм.
k = 5∙10-3
∙(20/0,3) = 0,33.(3.1.3)
Тогда, принимая отношение диаметра барабана к его длине, равным 1/1 (т.е. L = D), получим:
Q = k∙V∙D0,6
= 0,33∙0,785∙D3
∙D0,6
=(3.1.4)
= 0,33∙0,785∙D3,6
= 0,26∙D3,6
,
где V = π∙R2
∙L = π∙(D/2)2
∙D = π∙(D2
/4)∙D = (3.1.5)
= 0,785∙D2
∙D = 0,785∙D3
.
Откуда
D = (Q/0,26)1/3,6
,(3.1.6)
где Q - производительность, равная 0,286 т/ч.
D = (0,286/0,26)1/3,6
= 1,02 м.(3.1.7)
Тогда длина барабана равна L = D = 1,02 м.(3.1.8)
В результате выполненных расчетов принимаем к установке однокамерную барабанную мельницу для мокрого измельчения типа 4-ШМ-2. Ее технические характеристики приведены в таблице 3.1.
Таблица 3.1 Технические характеристики барабанной мельницы мокрого помола 4-ШМ-2
Диаметр барабана, мм
|
1200
|
Длина барабана, мм
|
1200
|
Частота вращения барабана, об/мин
|
35
|
Мощность двигателя, кВт
|
26
|
Определим параметры шаровой загрузки мельницы.
Размер шаров, загружаемых в барабан, зависит от размеров частиц измельчаемого материала и готового продукта, и может быть определен по следующему эмпирическому соотношению (формула В.А. Олевского):
dш
= 4,8(lgdк
)dн
0,5
,(3.1.9)
где dн
- размер частиц материала до измельчения, равный 20 мм;
dк
- размер частиц материала после измельчения, 315 мкм.
dш
= 4,8(lg315)∙200,5
= 53,6 мм.(3.1.10)
Шаровая загрузка барабанных мельниц составляет приблизительно 30 % от объема барабана, т.е. коэффициент заполнения барабана мелющими телами равен φ = 0,3. Коэффициент заполнения рассчитываем по формуле:
φ = Mш
/(ρн
∙V),(3.1.11)
где Mш
- масса шаров;
ρн
- насыпная плотность шаров, равная 3800 кг/м3
;
V - объем барабана мельницы.
По этой формуле определим массу шаровой загрузки:
Mш
= φ∙ ρн
∙V,(3.1.12)
Mш
= 0,3∙3800∙0,785∙1,22
= 1546 кг.(3.1.13)
Масса одного стального шара диаметром dш
= 53,6 мм:
mш
= ∙π∙rш
3
∙ρ,(3.1.14)
где rш
- радиус шара;
ρ = 7800 кг/м3
– плотность стали.
mш
= ∙3,14∙(26,8∙10-3
)3
∙7800 = 0,63 кг.(3.1.15)
Число шаров в загрузке:
z = Mш
/mш
, (3.1.16)
z = 1546/0,63 = 2454.(3.1.17)
Определим массу загрузки, состоящую из массы Mш
мелющих тел и массы измельчаемого материала, которую принимаем равной 14 % массы мелющих тел. Следовательно,
mз
= 1,14∙Mш
,(3.1.18)
mз
= 1,14⋅1546 = 1,762 т. (3.1.19)
Масса измельчаемого материала, находящегося в мельнице:
mи
= 0,14∙Mш
,(3.1.20)
mи
= 0,14∙1546 = 216 кг.(3.1.21)
В результате выполненных расчетов барабанная мельница мокрого измельчения 4-ШМ-2 имеет следующие параметры загрузки:
диаметр шаров dш
= 53,6 мм;
масса шаровой загрузки Mш
= 1546 кг;
число шаров в загрузке z = 2454;
масса влажной слюды, находящейся в мельнице mн
= 216 кг. [3]
3.2 Расчет классификатора
Необходимо подобрать гидроциклон для поверочной классификации измельченной слюды. В начале технологического расчета точно устанавливаем требования, которые предъявляются к гидроциклону в данной операции и исходные условия их работы. В гидроциклон поступает на классификацию пульпа, состоящая из измельченной слюды и воды. Влажность слюды равна 50%, производительность установки - 2 тонны пульпы в сутки. С учетом того, что установка работает 7 часов в сутки питание гидроциклона:
твердого - 0,143 т/ч;
жидкого - 0,143 т/ч;
добавляемая вода - 0 т/ч;
номинальная крупность слива - 315 мкм.
Объем пульпы для классификации в гидроциклоне составляет:
Vп
= Vж
+ Vтв
= W2
+ (Q2
/δт
),(3.2.1)
где δТ
- плотность твердого в пульпе, плотность флогопита, равная 2,7 т/м3
.
Vп
= 0,143 + (0,143/2,7) = 0,196 м3
/ч. (3.2.2)
На одну секцию измельчения в шаровой барабанной мельнице объем пульпы в питании составит:
Vсекц
= Vп
/N, (3.2.3)
где N - количество секций измельчения, равное 1 (так как измельчение проводится в один этап).
Vсекц
= 0,196/1 = 0,196 м3
/ч. (3.2.4)
Гидроциклон подбираем по граничной крупности слива, которая составляет:
dг
= dн
/1,75,(3.2.5)
где dн
- номинальная крупность слива, равная 315 мкм.
dг
= 315/1,75 = 180 мкм.(3.2.6)
По таблице 3.2.1 такая граничная крупность обеспечивается гидроциклоном с D = 500 мм, технические характеристики которого приведены в таблице 3.2.2.
Таблица 3.2.1 Данные для выбора гидроциклонов
D, мм
|
150
|
250
|
360
|
500
|
710
|
1000
|
1400
|
dг
, мкм
|
20–50
|
30–100
|
40–150
|
50–200
|
60–250
|
70–280
|
80–300
|
Таблица 3.2.2 Технические характеристики ГЦ 500К
Диаметр цилиндрической части, мм
|
500
|
Угол конуса, град
|
20
|
Диаметр сливного отверстия, мм
|
150
|
Диаметр пескового отверстия, мм
|
48, 75, 96, 150
|
Производительность по питанию при давлении 0,1 МПа, м³/час
|
180
|
Длина, мм
|
825
|
Ширина, мм
|
875
|
Высота, мм
|
2210
|
Давление P0
пульпы на входе в гидроциклон при работе в замкнутом цикле должно быть не менее 0,08 МПа.
Объемная производительность гидроциклона для P0
= 0,1 МПа составит:
V = 3∙Kα
∙KD
∙dп
∙dс
∙P0
0,5
,(3.2.7)
где KD
- поправка на диаметр гидроциклона, равная 1,1;
dп
- эквивалентный диаметр питающего отверстия, равный 130 мм;
dс
- диаметр сливного отверстия, 150 мм;
P0
- рабочее давление пульпы на входе в гидроциклон, равное 0,1 МПа;
Kα
- поправка на угол конусности для α = 20°, равная 1.
V = 3∙1∙1∙13∙15∙0,10,5
= 185 м3
/ч.(3.2.8)
Необходимое количество гидроциклонов на одну секцию составит:
N = Vсекц
/V = 0,17/185 1.(3.2.9)
Следовательно, принимаем к установке 1 гидроциклон, обеспечивающий граничную крупность слива, равную 180 мкм.
Принимаем предварительно к установке песковую насадку с диаметром отверстия, равным 48 мм. Граничная крупность слива для песковой насадки Δ = 48 мм составляет:
dг
= 1,5∙((D∙dC
∙TП
)/(Δ∙KD
∙P0
0.5
∙(δТ
- 1)))0,5
,(3.2.10)
где δт
- плотность твердого в пульпе, плотность слюды флогопит, равная 2,7 т/м3
;
Tп
- содержание твердого в питании гидроциклона, равное 50 %.
dг
= 1,5 ((50∙15∙50)/(4,8∙1,1∙0,10.5
∙(2,7 - 1)))0,5
= 172,4 мкм, (3.2.11)
что меньше 180 мкм.
Нагрузка по пескам Qп
выбранного гидроциклона составляет 208,7 т/ч. Удельная нагрузка тогда составит:
q = (Qп
∙4) / (N∙π∙Δ2
),(3.2.12)
q = (208,7∙4) / (1∙3,14∙4,82
) = 0,00115 т/(м2
∙ч).(3.2.13)
Удельная песковая нагрузка по твердому должна находиться в пределах 0.5 2.5 т/ч на 0,0001 м2
площади песковой насадки.
Площадь насадки:
Sп
= π∙R2
= 3,14∙2,4∙2,4 = 0,001808 м2
.(3.2.14)
Тогда допустимая песковая нагрузка:
qд
= (0,5 2,2) Sп
,(3.2.15)
qд
= 0,000904 0,00398 т/(м2
∙ч).(3.2.16)
Так как qд
min
< q < qд
m
ах
, окончательно принимаем песковую насадку с Δ = 48 мм. [14]
3.3 Подбор насосов
Подача пульпы в гидроциклон осуществляется песковым насосами. Выбор насоса производится по заданной объемной производительности (м3
/ч), содержанию твердого в пульпе и необходимому манометрическому напору.
Производительность насоса по воде определяется по формуле:
Vн2
о = Vп
∙(1 + Тп
),(3.3.1)
где Vн2
о - объемная производительность насоса по воде, м3
/ч;
Vп
- объемная производительность насоса по пульпе, равная 0,196 м3
/ч (3.2.2);
ТП
- содержание твердого в пульпе, равное 50%.
Vн2
о = 0,196∙(1 + 0,5) = 0,3 м3
/ч.(3.3.2)
К установке принимаем песковой насос с наименьшей возможной производительность, но обеспечивающий достаточный напор для гидроциклона ГЦ 500К. В таблице 3.3.1 приведены технические характеристики насоса П-12.5/12.5. Такой же насос установлен для перекачки пульпы в центрифугу. [14]
Таблица 3.3.1 Технические характеристики П-12.5/12.5
Подача по воде, м3
/ч
|
Напор, МПа
|
Мощность двигателя, кВт
|
Масса, т
|
Длина, м
|
Ширина, м
|
Высота, м
|
12,5
|
0,125
|
2,2
|
0,05
|
0,840
|
0,360
|
0,365
|
3.4 Расчет центрифуги
Исходя из заданной производительности по твердому осадку Dт
= 143 кг/ч, предварительно принимаем к установке универсальная центрифуга ОГШ-35.
Ее технические характеристики приведены в таблице 3.4.1.
Таблица 3.4.1 Технические характеристики ОГШ-35
Диаметр барабана, мм
|
350
|
Отношение длины барабана к диаметру
|
1,8
|
Максимальная частота вращения ротора, 1/с
|
67
|
Фактор разделения
|
3140
|
Расчетная производительность по твердой фазе, кг/ч
|
500
|
Необходимая крупность разделения δк
= 0,005 мм.
Для нахождения скорости осаждения частицы размером δк
= 0,005 мм рассчитываем критерий Архимеда:
Ar = [δк
3
(ρт
- ρж
) ρж
g]/μ2
,(3.4.1)
где ρт
- плотность слюды, равная 2700 кг/м3
;
ρж
- плотность воды, равная 1000 кг/м3
;
μ - вязкость воды, равная 0,9∙10-3
Па∙с.
Ar = [0,0053
∙10-9
∙(2700 - 1000)∙1000∙9,81]/(0,9∙10-3
) = 2,32∙10-6
.(3.4.2)
Режим осаждения ламинарный Ar < 3,6, поэтому скорость осаждения рассчитана по формуле Стокса:
ω0
= δк
2
(ρт
- ρж
)∙g/(18∙μ),(3.4.3)
ω0
= 0,005 2
∙10-6
∙(2700 - 1000)∙9,81/(18∙0,9∙10-3
) = 0,257∙10-4
м/с. (3.4.4)
Средний диаметр потока жидкости в барабане:
Dср
= (Dв
+ Dб
)/2,(3.4.5)
где Dв
- внутренний диаметр барабана центрифуги, равный 350 мм;
Dб
- диаметр слива жидкости, равный 260 мм.
Dср
= (350 + 260)/2 = 305 мм = 0,305 м.(3.4.6)
Фактор разделения, соответствующий среднему диаметру, определяется по зависимости:
Frср
= (ω2
∙ Dср
)/(2g) = (2π2
n2
Dср
)/g, (3.4.7)
где n - частота вращения ротора центрифуги, равная 66 1/с.
Frср
= (2∙3,142
∙662
∙0,305)/9,81 = 2710.(3.4.8)
Производительность центрифуги по подаваемой суспензии рассчитываем по уравнению:
Vc = π∙Dср
∙ℓ∙ω0
∙Frср
∙ɳэ
,(3.4.9)
где ℓ - длина пути осаждения, равная 0,375 м; ɳэ
- коэффициент эффективности разделения, равный 0,2 для центрифуг непрерывного действия.
Vc
= 3,14∙0,305∙0,375∙0,257∙10-4
∙2710∙0,2 =(3.4.10)
= 0,005 м3
/с = 18 м3
/ч.
Плотность суспензии была определена по формуле:
ρс
= (ρт
∙ρж
)/(ρт
- (ρт
- ρж
)∙xm
),(3.4.11)
где xm
- массовая концентрация твердой фазы, равная 50%.
ρс
= (2700∙1000)/(2700 - (2700 - 1000)∙0,5) = 1495 кг/м3
. (3.4.12)
Производительность центрифуги по твердому осадку при Vc
= 18 м3
/ч была определена по формуле:
Gт
= Vc
∙ρс
∙xm
,(3.4.13)
Gт
= 18∙1495∙0,5 = 13131 кг/ч.(3.4.14)
Полученное значение производительности по осадку
Gт
= 13131 кг/ч > Gт
max
= 500 кг/ч.(3.4.15)
В этом случае рабочую производительность по осадку принимаем:
Gтр
= 0,5∙Gт
max
= 0,5∙500 = 250 кг/ч. (3.4.16)
Тогда максимальная производительность по суспензии:
Vc
= Gтр
/(ρс
∙xm
),(3.4.17)
Vc
= 250/(1495∙0,5) = 0,343 м3
/ч.(3.4.18)
Требуемое количество центрифуг:
z = Vтр
/Vc
, (3.4.19)
где Vтр
- требуемая производительность по суспензии, равная 0,196 м3
/ч (3.2.2).
z = 0,196/0,343 = 0,6. (3.4.20)
Таким образом, для установки принимаем одну центрифугу ОГШ-35. [13]
3.5 Расчет сушилки с кипящим слоем
3.5.1 Материальный и тепловой баланс процесса горения
В сушильной установке с кипящим слоем подогрев сушильного агента осуществляется за счет сжигания газообразного топлива с высоким избытком воздуха в топке. При этом требуемая температура сушильного агента обеспечивается за счет дополнительного смешения продуктов сгорания и воздуха перед сушильной камерой.
Целью расчета является определение состава сушильного агента (смеси продуктов сгорания и воздуха), влагосодержания и энтальпии. Исходными данными являются элементарный состав топлива и температура газов перед сушилкой. Основой для расчета являются уравнения материального и теплового баланса процесса горения, учитывающие изменения теплоемкости газов в зависимости от температуры.
Требуемые для расчета параметры воздуха - энтальпия h0
и влагосодержание x0
определяем по h-x диаграмме влажного воздуха: h0
= 38 кДж/кг; x0
= 9∙10-3
кг/кг.
Сжигание газообразного топлива
В качестве теплоносителя используем топочный газ, образующийся при горении газообразного топлива. В таблице 3.5.1.1.1 представлен состав используемого природного газа.
Таблица 3.5.1.1.1 Состав топлива
Компонент газа
|
CH4
|
C2
H6
|
C3
H8
|
C4
H10
|
CO2
|
N2
|
Объемное содержание данного компонента yi
, %
|
98,7
|
0,35
|
0,12
|
0,06
|
0,1
|
0,67
|
Теоретически необходимое количество воздуха для сжигания 1 м3
газа:
V0
= 0,0476 [yH2
/2 + yCO/2 + yH2
S + (3.5.1.1.1)
+ ∑(m+n/4)yCm
Hn
- yO2
],
где yi
- объемное содержание данного компонента, %.
Так как используемый газ не содержит в себе H2
, O2
и H2
S, то в соответствии с уравнением (1) имеем:
V0
= 0,0476 [(1+4/4)98,7 + (2+6/4)0,35 + (3.5.1.1.2)
+ (3+8/4)0,12 + (4+10/4)0,06] = 9,5 м3
/м3
.
Находим объем дымовых газов. Теоретический объем азота:
V0
N2
= 0,79V0
+ 0,01yN2
,(3.5.1.1.3)
V0
N2
= 0,79∙9,5 + 0,01∙0,67 = 7,5 м3
/м3
. (3.5.1.1.4)
Объем трехатомных газов:
VRO2
= 0,01∙(yCO2
+ yCO + yH2
S +∑myCm
Hn
), (3.5.1.1.5)
VRO2
= 0,01[(1∙98,7 + 2∙0,35 + 3∙0,12 +(3.5.1.1.6)
+ 4∙0,06 + 0,1)] = 1,0 м3
/м3
.
Теоретический объем водяных паров:
V0
H2
O = 0,01(yH2
S+∑(n/2)yCm
Hn
) + 1,61V0
∙x0
, (3.5.1.1.7)
где V0
- теоретически необходимое количество воздуха для сжигания 1 м3
газа, равное 9,5 м3
/м3
,
x0
- влагосодержание воздуха, равное 9∙10-3
кг/кг.
V0
H2
O = 0,01(2∙98,7 + 3∙0,35 + 4∙0,12 + 5∙0,06) +(3.5.1.1.8)
+ 1,61∙9,5∙9∙10-3
= 2,13 м3
/м3
.
Низшая теплота сгорания газового топлива определяется на 1м3
газа при нормальных условиях через теплоты сгорания составляющих его компонентов:
Qc
н
= 358,2∙yCH4
+ 637,5∙yC2
H5
+ 912,5∙yC3
H8
+ (3.5.1.1.9)
+ 711,7∙yC4
H10
+ 126,4∙yCO,
Qc
н
= 358,2∙98,7 + 637,5∙0,35 + 912,5 ∙0,12 +(3.5.1.1.10)
+ 711,7∙0,06 + 126,4∙0,1 = 35742,31 кДж/м3
.
Определение избытка воздуха и параметров смеси
Коэффициент избытка воздуха α определяется из уравнения теплового баланса, записанного для условий адиабатного сжигания:
Qφ
в
+ Qc
н
= hг
,(3.5.1.2.1)
Qc
н
+ α∙ V0
∙cв
∙t0
= hг
0
+ (α-1)∙h0
в
,(3.5.1.2.2)
где cв
- теплоемкость воздуха, кДж/м3
К,
h0
в
- энтальпия теоретически необходимого количества воздуха при температуре t = t1
, °С.
Здесь энтальпия газов hг
0
при α = 1 и температуре газов t = t1
определяется выражением:
hг
0
= VRO2
∙ сRO
2
∙ t1
+ V0
H2
O∙ cH
2
O
∙ t1
+(3.5.1.2.3)
+ V0
N2
∙ cN
2
∙ t1,
кДж/м3
.
При расчете необходимо учитывать зависимость теплоемкости от температуры для газовых компонентов в следующем виде:
Теплоемкость сухих трехатомных газов
сRO
2
= 1,6 + 0,00088∙ t1
,(3.5.1.2.4)
где t1
- температура теплоносителя на входе в сушилку, равная 330°С,
сRO
2
= 1,6 + 0, 00088∙330 = 1,89 кДж/м3
К.(3.5.1.2.5)
Теплоемкость азота
cN
2
= 1,29 + 0,000202∙ t1
,(3.5.1.2.6)
cN
2
= 1,29 + 0,000202∙ 330 = 1,36 кДж/м3
К. (3.5.1.2.7)
Теплоемкость водяных паров
cH
2
O
= 1,49+0,00016∙ t1
,(3.5.1.2.8)
cH
2
O
= 1,49+0,00016∙ 330 = 1,54 кДж/м3
К.(3.5.1.2.9)
Теплоемкость воздуха
cв
= 1, 319 + 0, 000078∙ t1
,(3.5.1.2.10)
cв
= 1, 319 + 0, 000078∙ 330 = 1, 34 кДж/м3
К.(3.5.1.2.11)
Энтальпия теоретически необходимого количества воздуха при температуре t = t1
, °С:
h0
в
= V0
∙ cв
∙ t1
,(3.5.1.2.12)
h0
в
= 9,5∙1,34∙330 = 4200 кДж/м3
.(3.5.1.2.13)
Таким образом, уравнение (3.5.1.2.3) принимает вид:
hг
0
= 1,0∙1,89∙330 + 2, 13∙1,54∙330 + (3.5.1.2.14)
+ 7,5∙1,36∙330 = 5072 кДж/м3
.
Физическая теплота воздуха:
Qφв
= α∙V0
∙ cв
∙t0
,(3.5.1.2.15)
где V0
- теоретически необходимое количество воздуха для сжигания 1 м3
газа, равное 9,5 м3
/м3
(3.5.1.1.2).
Qφв
= α∙9,5∙1,34∙20 = 255∙α кДж/м3
.(3.5.1.2.16)
Определяем избыток воздуха из уравнения (3.5.1.2.2):
α = (Qc
н
- hг
0
+ h0
в
)/(h0
в
- V0
∙ cв
∙t0
),(3.5.1.2.17)
где Qc
н
- низшая теплота сгорания газового топлива определяется на 1м3
газа при нормальных условиях, равная 35742,31 кДж/м3
(3.5.1.1.10).
α = (35742,31 - 5072 + 4200)/(4200 - 255) = 8,84. (3.5.1.2.18)
Тогда действительный объем водяных паров при избытке воздуха будет равен:
VH2
O = V0
H2
O + 1, 61(α - 1) V0
∙x0
,(3.5.1.2.19)
где x0
- влагосодержание определяемое по h-x диаграмме влажного воздуха, равное 9∙10-3
кг/кг.
VH2
O = 2, 13 + 1, 61(8,84 - 1)*(3.5.1.2.20)
*9,5∙9∙10-3
= 3,2 м3
/м3
.
Объем сухих дымовых газов:
Vс.г. = VRO2
+ V0
N2
+(α - 1) V0
,(3.5.1.2.21)
где VRO2
- объем трехатомных газов, м3
/м3
; V0
N2
- теоретический объем азота, м3
/м3
.
Vс.г. = 1,0 + 7,5 + (8,84 - 1)∙ 9,5 = 82,98 м3
/м3
. (3.5.1.2.22)
Найдем плотность отдельных компонентов при данном давлении (Р = 101, 325 кПа) и температуре из уравнения состояния идеального газа:
ρi
= (P∙μi
)/[R∙( t1
+ 273)],(3.5.1.2.23)
где μi
- молярная масса компонентов газа.
Плотность воздуха:
ρв
= (P∙μв
)/[R∙( t1
+ 273)],(3.5.1.2.24)
ρв
= (101325∙28,8)/[8314∙(330 + 273)] = 0, 582 кг/м3
. (3.5.1.2.25)
Плотность азота:
ρ N
2
= (P∙μ N
2
)/[R∙( t1
+ 273)],(3.5.1.2.26)
ρ N
2
= (101325∙28)/[8314∙(330 + 273)] = 0, 566 кг/м3
. (3.5.1.2.27)
Плотность сухих трехатомных газов:
ρ RO
2
= (P∙μ RO
2
)/[R∙( t1
+ 273)],(3.5.1.2.28)
ρ RO
2
= (101325∙44)/[8314∙(330 + 273)] = 0, 889 кг/м3
. (3.5.1.2.29)
Плотность сухих дымовых газов:
ρ с.г. = (∑ρi
∙Vi)/Vс.г.,(3.5.1.2.30)
ρ с.г. = [(0, 889∙1,0) + (0, 566∙7,5) + (3.5.1.2.31)
+ (0, 582∙(8, 84 - 1)∙ 9,5)]/82, 98 = 0, 584 кг/м3
.
Плотность водяных паров:
ρ H2
O = (P∙μ H2
O)/[R∙( t1
+ 273)], (3.5.1.2.32)
ρ H2
O = (101325∙18)/[8314∙(330 + 273)] = 0, 364 кг/м3
. (3.5.1.2.33)
Влагосодержание теплоносителя на входе в сушильную камеру при заданной температуре t1
определяем из выражения:
x1
= (VH2
O/Vс.г.)∙( ρ H2
O/ρ с.г.),(3.5.1.2.34)
где VH2
O - действительный объем водяных паров при избытке воздуха, равный 3,2 м3
/м3
,
Vс.г. - объем сухих дымовых газов, равный 82,98 м3
/м3
(3.5.1.2.22).
x1
= (3,2 / 82, 98)∙( 0, 364 / 0, 584) = 0, 024 кг/кг. (3.5.1.2.35)
По h-x диаграмме влажного воздуха (рисунок 3.5.1.2.1) при известных температуре t1
, равной 330°, и влагосодержании x1
, равному 0, 024, определяем энтальпию газов перед сушильной установкой: h1
= 400 кДж/кг.

Рисунок 3.5.1.2.1. Нахождение энтальпии по h-x диаграмме влажного воздуха
3.5.2 Тепловой и материальный баланс процесса сушки
При известной производительности по сухому продукту G2
, равной 143 кг/ч, и конечной влажности по сухому продукту U2
, равной 1 %, количество испаренной влаги определяют как:
W = G2
∙[(U1
-U2
)/(100-U1
)],(3.5.2.1)
где U1
- начальная влажность слюды, влажность после процесса центрифугирования, равная 30 %.
W = (143/3600)∙[(30 - 1)/(100-30)] =(3.5.2.2)
= 0,0164 кг/с.
Расход исходного материала:
G1
= G2
+ W,(3.5.2.3)
G1
= (143/3600) + 0, 0164 = 0,056 кг/с. (3.5.2.4)
Конечное влагосодержание для теоретической установки находим по h-x диаграмме влажного воздуха (рисунок 3.5.2.1). Необходимо построить процесс сушки. Построение производится по расчетным параметрам наружного воздуха φ0
и t0
, состояния сушильного агента перед камерой x1
и t1
и его температуры на выходе из сушильной установки t2
.
Точка 0 на рисунке 3 соответствует состоянию воздуха, поступающего в топку. Условно процесс в топке и камере смешения изображается прямой 0-1. Точка 1 определяется по температуре t1
и рассчитанному влагосодержанию х1
. От точки 1 проводим линию h = const до изотермы t2
и определяем конечное влагосодержание х'2
для идеальной (без теплопотерь) сушильной установки. х'2
= 0, 115 кг/кг .
Расход теплоносителя на испарение 1 кг влаги в теоретической сушилке:
ℓ1
= 1 / (х'2
- х1
),(3.5.2.5)
ℓ1
= 1 / (0, 115 - 0, 024) = 10, 99 кг/кг влаги.(3.5.2.6)
Расход теплоты на испарение 1 кг влаги в теоретической сушилке:
q1
= ℓ1
(h1
– h0
),(3.5.2.7)
где h1
- энтальпия газов перед сушильной установкой, равная 400 кДж/кг, h0
- начальная энтальпия воздуха, равная 38 кДж/кг.
q1
= 10, 99 (400 - 38) = 3978 кДж/кг влаги.(3.5.2.8)

Рисунок 3.5.2.1. Нахождение х'2
и x2
по h-x диаграмме влажного воздуха
Количество теплоты, необходимое для испарения 1 кг влаги и подогрева продукта от начальной до конечной температуры qм
с учетом теплопотерь в окружающую среду q5
определяется из уравнения теплового баланса:
q = ℓ1
(h1
– h0
) + q5
+ qм
– t0
∙CH2
O, кДж/кг влаги, (3.5.2.9)
где ℓ1
(h1
– h0
) - расход теплоты для теоретической сушилки;
qм
- расход теплоты на нагрев материала;
q5
- потери теплоты в окружающую среду;
t0
∙CH2
O - физическая теплота влаги, вводимая с материалом, подлежащим сушке.
Тогда отклонение процесса в реальной сушильной установке от идеальной может быть определено:
∆ = t0
∙CH2
O - q5
- qм
, кДж/кг влаги. (3.5.2.10)
Потери теплоты в окружающую среду:
q5
= 0,1 q1
, (3.5.2.11)
q5
= 0,1∙3978 = 398 кДж/кг.(3.5.2.12)
Потери теплоты на нагрев материала:
qм
= (G2
∙сс
/W)∙( t2
- tс
), (3.5.2.13)
где cс
- теплоемкость сухой слюды, равная 0, 88 кДж/кг,
tс
- начальная температура слюды, равная 20°С;
qм
= ((143/3600)∙ 0,88 / 0,0164)∙(100 - 20) = (3.5.2.14)
= 170 кДж/кг.
Тогда отклонение процесса от теоретического по (3.5.2.10):
∆ = (1,49+0,00016∙20)∙20 - 398 - 170 = (3.5.2.15)
= 538 кДж/кг.
Переходим к построению реального процесса сушки (рисунок 3.5.2.1). Для этого из точки 2 на рисунке 3.5.2.1 откладываем отрезок вниз, равный ∆/ℓ1
= 49 кДж/кг (точка 3). Из полученной точки проводится прямая 1-3. Конечная точка действительного процесса определяется пересечением данной политропы с изотермой t2
. Далее определяем энтальпию газов на выходе из сушильной установки и истинное значение влагосодержания x2
: x2
= 0,095 кг/кг.
Расход теплоносителя на испарение 1 кг влаги в реальной сушильной установке:
ℓ = /(х2
- х1
),(3.5.2.16)
где х1
- влагосодержание теплоносителя на входе в сушильную камеру при заданной температуре t1
= 330° С, равное 0, 024 кг/кг.
ℓ= 1/(0,095 - 0,024) = 14,08 кг/кг влаги.(3.5.2.17)
Массовый расход свежего теплоносителя:
L = ℓ∙W,(3.5.2.18)
L = 14,08∙0,0164 = 0,23 кг/с.(3.5.2.19)
Тогда расход теплоты на сушку:
Q = L(h1
– h0
), (3.5.2.20)
Q = 0,23∙(400 - 38) = 83,3 кВт.(3.5.2.21)
Расход топлива при сушке дымовыми газами с учетом потерь теплоты в камере сгорания:
В = Q / Qc
н
∙1, 05 ,(3.5.2.22)
B = (83,3 / 35742,31)∙1,05 = 8,64 м3
/ч. (3.5.2.23)
3.5.3 Тепловой конструктивный расчет
Тепловой конструктивный расчет проводится для определения основных габаритных размеров аппарата.
Поскольку теплообмен между газом и частицами в кипящем слое заканчивается на высоте равной двум-трем диаметрам частиц слюды, то расчет скорости псевдоожижения проводим при температуре, равной температуре кипящего слоя. При этом средняя плотность газов в слое:
ρг
= ρс.г. ((t1
+ 273)/(t2
+ 273)),(3.5.3.1)
ρг
= 0,584 ((330 + 273)/(100 + 273)) = 0,944 кг/м3
. (3.5.3.2)
Находим по таблице 3.5.3.1 кинематический коэффициент вязкости газа: υг
= 23,9∙10-6
м2
/с.
Таблица 3.5.3.1 Зависимость кинематического коэффициента вязкости газа от его температуры при давлении, близком к атмосферному
tг
, °C
|
100
|
120
|
140
|
160
|
180
|
200
|
250
|
300
|
350
|
υг
∙10-6
, м2
/с
|
23,9
|
26,2
|
28,7
|
31,0
|
33,5
|
36,0
|
42,8
|
49,9
|
57,3
|
Определим критерий Архимеда для частицы:
Ar = [(g∙d3
)/υг
2
] ∙ [(ρс
- ρг
)/ρг
] , (3.5.3.3)
где d - средний размер частиц слоя, равный 0,3 мм;
ρс
- плотность слюды флогопит, равная 2700 кг/м3
.
Ar = [(9,81∙0,33
∙10-9
)/2,392
∙ 10-10
]*[(2700 - 0,944)/0,944] = 1326.(3.5.3.4)
Определяем критерий Рейнольдса, соответствующий началу ожижения слоя:
Reкр
= (Ar∙ε0
4,75
)/(18 + 0,61∙(Ar∙ε0
4,75
)0,5
), (3.5.3.5)
где ε0
- порозность насыпного слоя, равная 0,6.
Reкр
= (1326∙0,64,75
)/(18 + 0,61∙(1326∙0,64,75
)0,5
) = 4,76. (3.5.3.6)
Тогда скорость ожижения равна:
ωкр
= Reкр
∙( υг
/d), (3.5.3.7)
ωкр
= 4,76∙(23,9 ∙ 10-6
/0,3∙10-3
) = 0,37 м/с. (3.5.3.8)
Принимаем значение порозности в рабочих условиях ε = 0,8.
Определяем критерий Рейнольдса в рабочих условиях:
Reр
= (1326∙0,84,75
)/(18 + 0,61∙(1326∙0,84,75
)0,5
) = 14,76. (3.5.3.9)
Рабочая скорость подачи газа:
ωр
= Reр
∙( υг
/d), (3.5.3.10)
ωр
= 14,76(23,9 ∙ 10-6
/0,3∙10-3
) = 1,17 м/с. (3.5.3.11)
Число псевдоожижения в рабочих условиях:
Wр
= ωр
/ωкр
, (3.5.3.12)
Wр
= 1,17/0,37 = 3,16. (3.5.3.13)
Среднее влагосодержание газа:
xг
= (x1
+ x2
)/2, (3.5.3.14)
где x1
- влагосодержание теплоносителя на входе в сушильную камеру при заданной температуре t1
= 330° С, равное 0, 024 кг/кг;
x2
- истинное значение влагосодержания, равное 0,095 кг/кг.
xг
= (0, 024 + 0,095)/2 = 0,06 кг/кг. (3.5.3.15)
Определим площадь газораспределительной решетки:
S = (L∙(1 + xг
))/( ρг
∙ ωр
), (3.5.3.16)
где L - массовый расход свежего теплоносителя, равный 0, 23 кг/с
S = (0, 23∙(1 + 0,06))/(0,944∙1,17) = 0,22 м2
.(3.5.3.17)
Из условия устойчивого псевдоожижения принимаем высоту насыпного слоя H0
= 0,3 м. Тогда масса сухого продукта, находящегося на решетке:
Gс
= ρс
∙(1-ε0
)∙S∙ H0
,(3.5.3.18)
Gс
= 2700∙(1 - 0,6)∙0,22∙0,3 = 71,3 кг.(3.5.3.19)
Тогда время пребывания частиц в кипящем слое, необходимое для полного протекания процесса сушки:
τ = Gс
/G2
,(3.5.3.20)
где G2
- производительность по сухому продукту, равная 143 кг/ч.
τ = 71,3/(143/3600) = 1795 с. (3.5.3.21)
Определяем высоту кипящего слоя в рабочих условиях:
H = H0
∙((1 - ε0
)/(1 - ε)),(3.5.3.22)
H = 0,3∙((1 – 0,6)/(1 – 0,7)) = 0,4 м.(3.5.3.23)
Тогда высота сепарационной зоны аппарата:
Hсеп
= 4∙Н,(3.5.3.24)
Hсеп
= 4∙0,4 = 1,6 м.(3.5.3.25)
Определяем конструктивную высоту аппарата от газораспределительной решетки до газохода:
Hа
= Hсеп
+ Н,(3.5.3.26)
Hа
= 1,6 + 0,4 = 2 м.(3.5.3.27)
Диаметр аппарата:
D1
= ((4∙S)/π)0,5
, (3.5.3.28)
D1
= ((4∙0,22)/3,14)0,5
= 0,53 м.(3.5.3.29)
Газораспределительная решетка является наиболее ответственным узлом аппарата, от ее работы зависит качество псевдоожижения и, следовательно, интенсивность сушки. На рисунке 3.5.3.1 представлена конструкция наиболее распространенного типа колпачковой газораспределительной решетки для сушилок с кипящим слоем.

Рисунок 3.5.3.1. Конструкция наиболее распространенного типа колпачковой газораспределительной решетки
Размеры d1
, H1
, H2
принимаются конструктивно ( d1
= 30 50 мм, H2
= 20 50 мм, H1
= 50 100 мм). Шаг s1
между колпачками выбирается в пределах от 150 до 250 мм. Число отверстий в колпачках n0
- от 4 до 16. Диаметр центрального отверстия колпачка d2
должен быть таким, чтобы скорость движения газа в нем составляла ωг
= 25 30 м/с.
Принимаем общее число колпачков N = 9 при шаге s1
= 150 и число отверстий в каждом колпачке n0
= 16, ωг
= 25 м/с.
Тогда при скорости истечения ωист
45 м/с диаметр отверстия:
d0
= ((4∙L)/(π∙ ρс.г.
∙ ωист
∙N∙ n0
))0,5
, (3.5.3.30)
где ρс.г.
- плотность сухих дымовых газов, равная 0, 584 кг/м3
.
d0
= ((4∙0,23)/(3,14∙0,584∙45∙9∙16)) 0,5
= 0,0088 м. (3.5.3.31)
Диаметр центрального отверстия колпачка:
d2
= ((4∙L)/(π∙ ρс.г.
∙ ωг
∙N))0,5
,(3.5.3.32)
d2
= ((4∙0,23)/(3,14∙0,584∙25∙9)) 0,5
= 0,047 м. (3.5.3.33)
Отношение площадей отверстий:
n = ωг
/ωист
, (3.5.3.34)
n = 25/45 = 0,56. (3.5.3.35)
Живое сечение решетки:
φ = ωр
/ωист
, (3.5.3.36)
φ = 1,17/45 = 0,026.(3.5.3.37)
Коэффициент гидродинамического сопротивления вычисляем по формуле:
ζ= 1,55∙φ0,07
∙(2,9∙n2
∙(d0
/ d2
)4
+ 2,5)* (ωист
∙d0
/ υг
)-0,07
, (3.5.3.38)
ζ= 1,55∙0,020,07
∙(2,9∙0,422
∙(0,0088 / 0,047)4
+ 2,5)* (3.5.3.39)
*(45∙0,0088 / 23,9∙10-6
)-0,07
= 1,5.
Зная значение этого коэффициента, можем вычислить аэродинамическое сопротивление решетки:
Рр
= ζ∙( ρс.г.
∙ ωист
2
/2), (3.5.3.40)
Рр
= 1,5∙(0,584∙452
/2) = 887 Па.(3.5.3.41)
Аэродинамическое сопротивление кипящего слоя:
Рк.с.
= Н∙ρс
∙g(1 - ε), (3.5.3.42)
где ρс
- плотность слюды флогопит, равная 2700 кг/м3
;
ε - порозность в рабочих условиях, равная 0,8.
Рк.с.
= 0,4∙2700∙9,81∙(1 - 0,7) = 3178 Па. (3.5.3.43)
Живое сечение решетки не должно превышать (в долях единицы) 0,05. Аэродинамическое сопротивление решетки должно составлять около 30% от сопротивления слоя. При несоответствии полученных параметров (φ и Рр
) данным требованиям необходимо задаться другой скоростью истечении ωист
либо изменить конструктивные характеристики и повторить расчет.
Поскольку соотношение Рк.с.
/Рр
= 3,5, расчет газораспределительной решетки считаем законченным. [5], [6], [7] После проведенных расчетов необходимо определить, какой формы будет сушильная камера, для этого проверим условие уноса мелких частиц из аппарата. Принимает размер мелкой частицы равным 0,1 мм. Тогда Критерий Архимеда для частиц с минимальным диаметром:
Ar = [(g∙dmin
3
)/υг
2
] ∙ [(ρс
- ρг
)/ρг
],(3.5.3.44)
где dmin
- размер мелких частиц слоя, равный 0,1 мм; ρс
- плотность слюды флогопит, равная 2700 кг/м3
; ρг
- средняя плотность газов в слое, равная 0,944 кг/м3
; υг
- кинематический коэффициент вязкости газа, равный 23,9∙10-6
м2
/с.
Ar = [(9,81∙0,13
∙10-9
)/2,392
∙ 10-10
]*[(2700 - 0,944)/0,944] = 49,2. (3.5.3.45)
Определяем критерий Рейнольдса, соответствующий началу ожижения слоя:
Re= Ar/(18 + 0,61∙(Ar0,5
)), (3.5.3.46)
Re= 49,2/(18 + 0,61∙(49,20,5
)) = 2,21. (3.5.3.47)
Тогда скорость витания частиц равна:
ωв
= Re∙( υг
/ dmin
), (3.5.3.48)
ωкр
= 2,21∙(23,9 ∙ 10-6
/0,1∙10-3
) = 0,53 м/с. (3.5.3.49)
Полученное значение скорости витания частиц меньше, чем рабочая скорость подачи газа по (3.5.3.11). Поэтому для снижения уноса частиц корпус сушильной камеры выполняем расширяющимся над газораспределительной решеткой. [8]
В результате выполненного расчета сушилка с кипящим слоем расширяющегося по высоте сечения имеет следующие характеристики:
диаметр аппарата D1
= 0,53 м;
высота сепарационной зоны аппарата Hсеп
= 1,6 м;
высота аппарата от газораспределительной решетки до газохода Hа
= 2 м;
высота кипящего слоя H = 0,4 м.
3.6 Подбор циклона
Циклон для улавливания уноса выбираем по объемному расходу газов на выходе из установки.
Объемный расход газа:
V2
= (L∙(1 + x2
)/ρг
),(3.6.1)
где x2
- истинное значение влагосодержания, равное 0,095 кг/кг, найденное по h-x диаграмме влажного воздуха в пункте 3.5.2;
ρг
- средняя плотность газов в слое, равная 0,944 кг/м3
(3.5.3.2).
V2
= (0, 23∙(1 + 0,095)/0,944) = 0,27 м3
/с. (3.6.2)
Задаваясь скоростью газа на полное сечение цилиндрической камеры циклона ωц
= 4 м/с, получаем ориентировочный диаметр циклона:
Dц
= ((4/π)∙( V2
/ωц
))0,5
,(3.6.3)
Dц
= ((4/3,14)∙( 0,27/4))0,5
= 0,24 м.(3.6.4)
Выбираем к установке 1 циклон ЦН-15-250, технические характеристики которого представлены в таблице 3.6.1.
Таблица 3.6.1 Технические характеристики ЦН-15-250
Производительность по воздуху, м3
/ч
|
828 954
|
Диаметр, мм
|
250
|
Высота, мм
|
1140
|
Масса, кг
|
79
|
3.7 Подбор фильтра
Подбор рукавного фильтра осуществляем по поверхности фильтрации Fф
.
Учитывая неагрессивность газов, принимаем фильтровальную ткань (лавсан с начесом), допускающую максимальную температуру газа около 130°. Примем температуру газа на входе в фильтр (после смешения с подсасываемым воздухом) tсм
= 70 °С.
Расход подсасываемого воздуха, обеспечивающего снижение температуры газа от tг
=100 до 70 °С:
Vп.в.
= V2
∙(ρг
∙(tг
- tсм
)/ρв
∙(tсм
- tв
)), (3.7.1)
где V2
- объемный расход газа, равный 0,27 м3
/с по (3.6.2);
ρг
- плотность газа, равная 0,944 кг/м³;
ρв
- плотность воздуха при нормальном атмосферном давлении и температуре 20 °С, равная 1,2 кг/м³;
tв
- температура воздуха, равная 20°С.
Vп.в.
= 0,27(0,944(100 - 70)/1,2(70 - 20)) = 0,127 м3
/с. (3.7.2)
Расход воздуха, подаваемого на продувку, примем:
Vпр
= 0,2∙V2
, (3.7.3)
Vпр
= 0,2∙0,27 = 0,054 м3
/с. (3.7.4)
Тогда площадь поверхности фильтрации при скорости газа в фильтре ωг
= 0,2 м/с:
Fф
= (V2
+ Vпр
+ Vп.в.
)/0,2, (3.7.5)
Fф
= (0,27 + 0,054 + 0,127)/0,2 = 2,3 м3
. (3.7.6)
Принимаем к установке 1 фильтр марки ФРКИ-8, его технические характеристики представлены в таблице 3.7.1.
Таблица 3.7.1 Технические характеристики ФРКИ-8
Производительность по воздуху, м3
/ч
|
800
|
Площадь фильтрации, м2
|
8
|
Диаметр фильтра, мм
|
1000
|
Высота фильтра без бункера, мм
|
4178
|
Высота фильтра с бункером, мм
|
4780
|
3.8 Расчет топочного устройства
Диаметр топочного устройства выбираем таким, чтобы скорость движения теплоносителя на свободное сечение топки не превышала 5 м/с. Объем топочной камеры определяют по величине допустимых тепловых напряжений объема топочного пространства qv
= 0,6 МВт/м3
.
Тогда объем топки:
Vт = Q/qv
, (3.8.1)
где Q - расход теплоты на сушку, равный 83,3 кВт по (3.5.2.21).
Vт = 83,3∙10-3
/0,6 = 0,139 м3
. (3.8.2)
При соотношении длины топки ℓт к ее диаметру Dт, равной примерно 2, получаем:
Dт = , (3.8.3)
Dт = = 0,45 м.(3.8.4)
ℓт = 2∙Dт,(3.8.5)
ℓт = 2∙0,45 = 0,9 м. (3.8.6)
Принимаем к установке топку с диаметром, равным 0,5 м, и длинной 1 м.[6]
3.9 Подбор газодувки
Вентиляционное оборудование подбираем, исходя из значения суммарного аэродинамического сопротивления сушилки с газоочистной аппаратурой (циклон и рукавный фильтр) и производительности по сушильному агенту.
Суммарное аэродинамическое сопротивление:
Р = Рр
+ Рк.с.
+ Рц
+ Рр.ф.
, (3.9.1)
где Рр - аэродинамическое сопротивление решетки, равное 887 Па по (3.5.3.32);
Рк.с. - аэродинамическое сопротивление кипящего слоя 3178 Па по (3.5.3.32);
Рц - аэродинамическое сопротивление циклона, равное 500 Па;
Рр.ф. - аэродинамическое сопротивление рукавного фильтра, равное 1000 Па.
Р = 887 + 3178 + 1000 + 500 = 5565 Па.(3.9.2)
Объемный расход газа равен 0,27 м3
/с.
Выбираем вентилятор высокого давления ТВ-25-1,1, технические характеристики которого приведены в таблице 3.9.1.
Таблица 3.9.1 Технические характеристики ТВ-25-1,1
Производительность,
м3
/с
|
Напор,
Па
|
Частота вращения,с-1
|
Электродвигатель
|
тип
|
NН
, кВт
|
ɳдв
|
0,833
|
10000
|
48,3
|
АО2-71-2
|
22
|
0,88
|
3.10 Подбор питателей
Часовая объемная производительность сушильной установки:
Q = G/rн
= 143/500 = 0,286 м3
/час, (3.10.1)
где rн
= 500 кг/м3
- насыпная плотность слюды.
По объемной производительности выбираем к установке для загрузки сушилки винтовой питатель типа Ш3-15, его технические характеристики приведены в таблице 3.10.1.
Таблица 3.10.1 Технические характеристики Ш3-15
Производительность, м3
/час
|
0,1 5
|
Диаметр шнека, мм
|
150
|
Мощность привода, кВт
|
0,75 2,2
|
Крупность материала, мм
|
до 0,5
|
Для разгрузки сушилки выбираем шлюзовой питатель типа ПШ1-250, его технические характеристики приведены в таблице 3.10.2.
Таблица 3.10.2 Технические характеристики ПШ1-250
Производительность, м3
/час
|
0,18 1,65
|
Частота вращения ротора, об/мин
|
от 2,5 5
|
Мощность привода, кВт
|
0,55
|
Частота вращения двигателя синхронная, об/мин
|
1000
|
4. КОНСТРУКТИВНЫЕ РАСЧЕТЫ
4.1 Расчет сушилки кипящего слоя
4.1.1 Выбор материала аппарата
Среда, в которой работает аппарат, не является агрессивной, поэтому нет потребности в материале, обладающим повышенной стойкостью в химически активных средах. С другой стороны необходимо подобрать материал, который был бы жаростоек, т.к. сушилка работает в условиях повышенной температуры до 350 °С. Наиболее целесообразно выполнить аппарат из качественной углеродистой конструкционной стали 20К или низколегированной конструкционной стали для сварных конструкций 16ГС. Сталь 20К характеризуется хорошим сочетанием механических и механо-технологических свойств. Назначение - обечайки, днища, крышки, плоские фланцы и другие детали аппаратов, работающих при температуре от - 40 °С до 450 °С. Свариваемость - без ограничений, способы сварки: АДС под флюсом с газовой защитой, РДС, ЭШС. Сталь неустойчива во многих агрессивных средах, однако в некоторых средах она показывает удовлетворительную устойчивость. Назначение стали 16ГС аналогично назначению 20К. Из стали 16ГС изготовливают элементы сварных конструкции, работающие при температуре от - 70 °С до 475 °С. Сваривается без ограничений, также как и 20К неустойчива во многих агрессивных средах. Допускаемые напряжения при 350 °С для проката из стали 16ГС выше, чем из стали 20К, соответственно 140 МПа против 106 МПа. Следовательно применение стали 16ГС сделает аппарат более легким, а значит и более дешевым, так как разница в цене этих сталей незначительна. Таким образом, для изготовления корпуса сушилки с кипящим слоем используем низколегированную конструкционную сталь для сварных конструкций 16ГС.
4.1.2 Расчет толщины обечайки
Толщину стенки цилиндрической части сушилки определяем согласно нормам и методам расчета по ГОСТ 14249-89 «Сосуды и аппараты. Нормы и методы расчета на прочность».
Толщина цилиндрической обечайки рассчитывается по формуле:
s sp
+ c,(4.1.2.1)
где sp
- расчетная толщина стенки;
с - суммарная прибавка к расчетной толщине стенки.
Расчетная толщина стенки - это минимальное значение толщины стенки, которое должно остаться у оболочки на исходе расчетного срока службы, чтобы обеспечить ей эксплуатационную прочность с максимально возросшим в её материале значением напряжения, равном допускаемому напряжению в потенциально опасном месте (сечении). С учетом этого расчетная толщина стенки цилиндрической обечайки определяется по формуле:
sp
= (р∙D)/(2∙[σ]∙φ-p),(4.1.2.2)
где р - расчетное давление;
Аппарат работает под небольшим избыточным давлением, обусловленным работой вентилятора высокого давления. С учетом суммарного аэродинамического сопротивления имеем:
p = pатм
+ pизб
= 0,1 + (0,01-0,005565) = 0,105 МПа;
D - диаметр цилиндрической части аппарата, равный 0,53 м по (3.5.3.29);
[σ] - допускаемое напряжение для проката из стали 16ГС при температуре 350 °С, равное 140∙106
Па, согласно ГОСТ 14249-89;
φ - коэффициент прочности стыкового сварного шва, выполняемого вручную с одной стороны, равный 0,9 по ГОСТ 14249-89.
sp
= (105
∙0,53)/(2∙140∙106
∙0,9-10,55
) =(4.1.2.3)
= 0,0002 м = 0,2 мм.
Суммарная прибавка к расчетной толщине стенки:
с = с1
+ с2
+с3
, (4.1.2.4)
где с1
- прибавка для компенсации коррозийно-эрозийного износа стенки проката в рассматриваемом сечении;
с2
- прибавка для компенсации минусового допуска по толщине стенки проката, используемого для изготовления аппарата, равная 1 мм.
с3
- прибавка для компенсации технологического утонения стенки проката в рассматриваем сечении при изготовлении из него рассчитываемого элемента, равная нулю для цилиндрической обечайки.
Прибавку с1
определяем по формуле:
с1
= П∙τ, (4.1.2.5)
где П - интенсивность (скорость) корозийно-эрозийного износа стенки, равная 0,1 мм/год; τ - расчетный срок службы, равный 30 годам.
Тогда с1
= 0,1∙30 = 3 мм. (4.1.2.6)
Таким образом, суммарная прибавка к расчетной толщине стенки:
с = 3 + 1 + 0 = 4 мм.(4.1.2.7)
Тогда толщина стенки (исполнительное значение):
s 0,2 + 4 = 5 мм.(4.1.2.8)
Принимаем исполнительную толщину стенки, равной 5 мм.
Исполнительную толщину стенки конической обечайки находим по формуле аналогичной (4.1.2.1):
sp
= (р∙D)/((2∙[σ]∙φ-p)∙cosα), (4.1.2.9)
sp
= (10,55
∙0,53)/((2∙140∙106
∙0,9-10,55
)∙cos10°) = (4.1.2.10)
= 0,0002 м = 0,2 мм.
С учетом прибавок, толщина будет равна так же 5 мм. Принимаем толщину обечайки во всех сечениях равной 5 мм.
Снизу аппарат закрыт плоским круглым неотбортованным днищем по ГОСТ 12622-78, приваренным непосредственно к обечайке, а сверху - коническим отбортованным с углом при вершине 120° по ГОСТ 12623-67.
4.1.3 Расчет толщины газораспределительной решетки
Рассчитаем толщину газораспределительной решетки. Номинальная расчетная толщина плоской цельной круглой решетки s' (м), опирающейся по окружности на какое-либо опорное устройство и не имеющей дополнительных опор в виде ребер, балок и т.д., определяется по формуле:
s' = 0,45∙Dр
∙(p/σи
∙φ0
)0,5
*, (4.1.3.1)
где Dр
- диаметр решетки;
σи
- допускаемое напряжение на изгиб для материала решетки, стали 16ГС;
p - давление на решетку от силы тяжести слоя материала и массы собственно тарелки с учетом дополнительных нагрузок;
φ0
- коэффициент ослабления решетки отверстиями.
φ0
= (t - d)/t, (4.1.3.2)
где t - расстояние между центрами отверстий в тарелке, равное 0,15 м;
d - диаметр отверстий, равный 0,047 м по (3.5.3.33),
φ0
= (0,15 - 0,047)/0,15 = 0,69. (4.1.3.3)
* Получена из формулы (1) табл. 26 с введением в знаменатель подкоренного выражения коэффициента φ.
Диаметр решетки принимают на 1 3% больше наружного диаметра цилиндрической обечайки:
Dр
= 1,02∙ Dн
, (4.1.3.4)
где Dн
- наружный диаметр обечайки, равный сумме внутреннего диаметра и толщины стенки, Dн
= D + 2∙s = 0,53 + 2∙0,005 = 0,54 м; (4.1.3.5)
D - диаметр аппарата, равный 0,53 м по (3.5.3.29);
s - толщина стенки цилиндрической обечайки, равная 0,005 м по (4.1.2.8).
Dр
= 1,02∙ 0,54 = 0,55 м. (4.1.3.6)
Обычно считается, что для сталей предел выносливости при изгибе составляет, грубо говоря, половину от предела прочности:
σи
(0,4 0,5) σвр,
(4.1.3.7)
где σвр
- предел прочности для стали 16ГС при температуре 350 °С, равный 140 МПа.
Так как сталь низколегированная, то выбираем нижнюю границу:
σи
= 0,4∙140 = 56 МПа. (4.1.3.8)
Находим значение давления на газораспределительную решетку. По (3.5.3.19) масса сухой слюды, находящейся на решетке равна 71,3 кг. С учетом находящейся на решетке влаги и веса самой решетки масса будет равна более 100 кг, но так как материал частично в определенный момент времени находится во взвешенном состоянии, принимаем расчетную массу равной 100 кг. Тогда вес равен 981 Н, а давление на единицу площади газораспределительной решетки:
р = Р/Sр
, (4.1.3.9)
где Sр
- площадь решетки, равная 2πr2
, равная 1,7 м2
;
р = 981/1,7 = 577 Н/м2
= 0,000577 МН/м2
.(4.1.3.10)
Таким образом (4.1.3.1) принимает вид:
s' = 0,45∙0,55∙(0,000577/56∙0,69)0,5
= 0,001 м.(4.1.3.11)
С учетом прибавок на компенсацию коррозийного износа, минусового допуска, влияния абразивных свойств слюды принимаем толщину газораспределительной решетки равной 5 мм. [18]
4.1.4 Расчет штуцеров и подбор фланцев
Диаметр штуцеров для входа и выхода теплоносителя рассчитываем по формуле:
d = (G/(0,785∙ρ∙ω))0,5
,(4.1.4.1)
где G - массовый расход теплоносителя, равный 0,23 кг/с по (3.5.2.19);
ρ - плотность теплоносителя, равная на входе и выходе в сушилку 0,584 и 0,944 кг/м3
соответственно по (3.5.1.2.31) и (3.5.3.2);
ω - скорость движения теплоносителя в штуцере, принятая равной 25 м/с.
Диаметр входного штуцера:
d1
= (0,23/(0,785∙0,584∙25))0,5
= 0,14 м.(4.1.4.2)
Диаметр выходного штуцера:
d2
= (0,23/(0,785∙0,944∙25))0,5
= 0,11 м.(4.1.4.3)
Рассчитываем диаметры штуцеров для подачи влажной слюды в аппарат со скорость 0,01 м/с:
d3
= (0,056/(0,785∙2700∙0,01))0,5
= 0,05 м,(4.1.4.4)
здесь 0,056 кг/с - расход влажного материала по (3.5.2.4).
Диаметр штуцера для вывода сухой слюды из аппарата принимаем равным также 0,05 м.
Все штуцеры снабжаются фланцами. Для разъемного соединения цилиндрической части аппарата в месте установки газораспределительной решетки используем плоские приварные фланцы с Dвн
= 530 мм, по ГОСТ 12820-80, их конструкция приведены на рисунке 4.1.3.1.

Рисунок 4.1.3.1. Плоский приварной фланец
Для штуцеров для подачи теплоносителя, вывода теплоносителя из аппарата, для подачи и вывода слюды используем свободные фланцы на приварном кольце по ГОСТ 12822-80. Конструкция свободного фланца приведена на рисунке 4.1.3.2. Такой фланец отличается от остальных видов удобством монтажа, так как к трубе приваривается только кольцо, а сам фланец остается свободным, что обеспечивает легкую стыковку болтовых отверстий свободного фланца с болтовыми отверстиями фланца арматуры или оборудования без поворота трубы.

Рисунок 4.1.3.2. Свободный фланец на приварном кольце
4.1.5 Расчет фланцевого соединения
Рассчитываем фланцевое соединение крышки и корпуса сушилки кипящего слоя. Выбираем плоские приварные фланцы или приварные встык и гладкую уплотнительную поверхность или поверхность типа «шип-паз». Их конструкции приведены на рисунках 4.1.5.1 и 4.1.5.2 соответственно.

Рисунок 4.1.5.1. Конструкция плоского приварного фланца. Расчетная схема

Рисунок 4.1.5.2. Уплотнительная поверхность типа «шип-паз»: 1 - фланцы; 2 - болт; 3 - прокладка
Определение конструктивных размеров фланца
Исходными данными для расчета являются внутренний диаметр аппарата D = 920 мм, толщина стенки обечайки s = 5 мм, температура обрабатываемой среды t = 300 °С. Прибавку к расчетной толщине стенки принимаем равной 1 мм. Материал корпуса и крышки - сталь 16ГС, коэффициент прочности сварных швов φ = 0,9, давление в аппарате 0,1 МПа.
Толщину втулки фланца принимаем s0
= 7 мм, что удовлетворяет условию s0
> s (7 мм > 5 мм). Высота втулки тогда будет равна:
hв
> 0,5(D∙(s0
- c))0,5
, (4.1.5.1.1)
hв
= 0,5(920∙(7 - 1))0,5
= 37,15 мм. (4.1.5.1.2)
Принимаем hв
= 50 мм.
Диаметр болтовой окружности:
Dб
= D + 2∙(2∙s0
+dб
+ u), (4.1.5.1.3)
где dб
- наружный диаметр болта при D = 920 мм, рр
= 0,105 МПа, равный 20 мм;
u - нормативный зазор, равный 4 мм.
Dб
= 920 + 2∙(2∙7 + 20 + 4) = 996 мм = 0,996 м.(4.1.5.1.4)
Наружный диаметр фланца:
Dн
= Dб
+ a,(4.1.5.1.5)
где а - конструктивная добавка, равная 40 мм для шестигранных гаек при dб
= 20 мм, тогда
Dн
= 996 + 40 = 1036 мм.(4.1.5.1.6)
Наружный диаметр прокладки:
Dн.п.
= Dб
- е,(4.1.5.1.7)
где е - нормативный параметр, равный 30 мм для плоских прокладок, тогда
Dн.п.
= 996 - 30 = 966 мм.(4.1.5.1.8)
Средний диаметр прокладки:
Dс.п.
= Dн.п.
- b,(4.1.5.1.9)
где b - ширина прокладки, принятая равной 12 мм, тогда
Dс.п.
= 966 - 12 = 954 мм = 0,954 м. (4.1.5.1.10)
Количество болтов, необходимых для обеспечения герметичности соединения:
nб
> π∙Dб
/tш
, (4.1.5.1.11)
где tш
- шаг размещения болтов М20 на болтовой окружности при 0,1 МПа,
tш
= 4,5∙ dб
= 4,5∙ 20 = 90 мм, тогда(4.1.5.1.12)
nб
= 3,14∙996/90 = 35 шт. (4.1.5.1.13)
Принимаем nб
= 36, кратное четырем.
Высота (толщина) фланца:
hф
> λф
∙(D∙sэк
)0,5
,(4.1.5.1.14)
где λф
- коэффициент, равный 0,3 для плоских приварных фланцев при 0,1 МПа,
sэк
= s0
= 7 мм, так как для плоских приварных фланцев β1
= s1
/s0
= 1.
hф
= 0,3∙(920∙7)0,5
= 24,1 мм. (4.1.5.1.15)
Принимаем hф
= 24 мм.
Расчетная длина болта:
ℓб
= ℓб.о.
+ 0,28∙dб
, (4.1.5.1.16)
где ℓб.о.
- расстояние между опорными поверхностями головки болта и гайки при толщине прокладки hп
= 2 мм,
ℓб.о.
= 2∙(hф
- hп
) = 2∙(24 + 2) = 52 мм. (4.1.5.1.17)
ℓб
= 52 + 0,28∙20 = 57,6 мм = 0, 058 м.(4.1.5.1.18)
Расчет нагрузок, действующих на фланец
Равнодействующая внутреннего давления:
Fд
= рр
∙π∙D2
с.п.
/4, (4.1.5.2.1)
Fд
= 0,105∙3,14∙0,9542
/4 = 0,07 МН.(4.1.5.2.2)
Реакция прокладки:
Rп
= π∙Dс.п.
∙b0
∙kпр
∙рр
,(4.1.5.2.3)
где b0
– эффективная ширина прокладки, равная b = 12 мм = 0,012 м, так как b 15 мм;
kпр
– коэффициент для паронита толщиной более 1 мм, равный 2,5.
Rп
= 3,14∙0,954∙0,012∙2,5∙0,105 = 0,009 МН. (4.1.5.2.4)
Усилие, возникающее от температурных деформаций рассчитываем по формуле:
Ft
= (yб
∙nб
∙fб
∙Eб
∙(αф
∙tф
- αб
∙tб
))/(4.1.5.2.5)
/(yп
+ yб
+ 0,5yф
∙(Dб
- Dс.п.
)2
),
где αф
- коэффициент линейного расширения материала фланца (16ГС), равный 14,7∙10-6
1/°С;
αб
- коэффициент линейного расширения материала ботов (35Х), равный 13,3∙10-6
1/°С;
tф
- расчетная температура неизолированных фланцев, равная 0,96∙t= 0,96∙300 = 288 °С;
tб
- расчетная температура болтов, равная 0,95∙t = 0,95∙300 = 285 °С;
Eб
- модуль продольной упругости для болтов из стали 35Х, равный 1,9∙105
МПа;
fб
- расчетная площадь поперечного сечения болта, равная 2,35∙10-4
м2
для болтов с диаметром dб
= 20 мм;
nб
- количество болтов, равное 36;
yп
, yб
, yф
- податливости, соответственно болтов, прокладки, фланцев.
Вычисляем значение податливости болтов по формуле:
yб
= ℓб
/(Eб
∙fб
∙nб
),(4.1.5.2.6)
где ℓб
- расчетная длина болта равная 0,058 м по (4.1.4.1.18).
yб
= 0,058/(1,9∙105
∙2,35∙10-4
∙36) =(4.1.5.2.7)
= 36∙10-6
м/МН.
Податливость прокладки из паронита равна:
yп
= hп
/(Eп
∙π∙Dс.п.
∙b),(4.1.5.2.8)
где Еп
- модуль упругости прокладки из паронита, равный 2000 МПа;
hп
- толщина прокладки, равная 2 мм;
b - ширина прокладки, равная 12 мм.
yп
= 2∙10-3
/(2000∙3,14∙0,954∙12∙10-3
) =(4.1.5.2.9)
= 27,8∙10-6
м/МН.
Податливость фланца:
yф
= [1 - ν∙(1 + 0,9∙λ'ф
)]∙ψ2
/(h3
ф
∙Е),(4.1.5.2.10)
где ν, λ'ф
- безразмерные параметры;
ψ1
, ψ2
- коэффициенты, определяемые по формулам;
Е - модуль упругости фланца, равный 1,8∙105
МПа для стали 16ГС.
ψ1
= 1,28∙lg(Dн
/D) =(4.1.5.2.11)
= 1,28∙lg(1,036/0,92) = 0,07;
ψ2
= (Dн
+ D)/( Dн
- D) =(4.1.5.2.12)
= (1,036 + 0,92)/( 1,036 - 0,92) = 16,9;
λ'ф
= hф
/( D∙sэк
)0,5
=(4.1.5.2.13)
= 0,024/(0,92∙7∙10-3
)0,5
= 0,002;
ν = 1/(1 + 0,9∙λ'ф
∙(1 + ψ1
∙h2
ф
/sэк
2
)) =(4.1.5.2.14)
= 1/(1 + 0,9∙0,002∙(1 + 0,07∙0,0242
/0,0072
)) = 0,99.
Таким образом,
yф
= [1 - 0,99∙(1 + 0,9∙0,002)]∙16,9/ (4.1.5.2.15)
/(0,0243
∙1,8∙105
) = 68∙10-3
1/(МН∙м).
Тогда (4.1.5.2.5) принимает вид
Ft
= (36∙10-6
∙36∙2,35∙10-4
∙1,9∙105
∙(14,7∙10-6
∙288 - (4.1.5.2.16)
- 13,3∙10-6
∙285))/(27,8∙10-6
+ 36∙10-6
+ 0,5∙68∙10-3
∙(0,996 – 0,954)2
) = 0,17 МН.
Коэффициент жесткости фланцевого соединения:
kж
= (yб
+ 0,5∙yф
∙(Dб
- D - sэк
)∙(Dб
- Dс.п.
))/ (4.1.5.2.17)
/(yп
+ yб
+0,5∙yф
∙(Dб
- Dс.п.
)2
),
kж
= (36∙10-6
+ 0,5∙68∙10-3
∙(0,996 - 0,92 - 7∙10-3
)* (4.1.5.2.18)
*(0,996 - 0,954))/(27,8∙10-6
+ 36∙10-6
+
+ 0,5∙68∙10-3
∙(0,996 - 0,954)2
) = 2,24
Болтовая нагрузка в условиях монтажа:
kж
∙Fд
+ Rп
= 2,24∙0,07 + 0,009 = 0,166 МН (4.1.5.2.19)
Fб1
= max
0,5∙π∙Dс.п.
∙b0
∙pпр
= 0,5∙3,14∙0,954∙12∙10-3
∙20 = 0,36 МН,
где pпр
- минимальное давление обжатия прокладки из паронита, равное 20 МПа.
Болтовая нагрузка в условиях монтажа равна большему из рассчитанных значений, следовательно, Fб1
= 0,36 МН.
Болтовая нагрузка в рабочих условиях:
Fб2
= Fб1
+ (1 - kж
) ∙Fд
+ Ft
,(4.1.5.2.20)
Fб2
= 0,36 + (1 - 2,24)∙0,07 + 0,17 = 0,44 МН.(4.1.5.2.21)
Приведенный изгибающий момент вычисляем из условия:
0,5∙(Dб
- Dс.п.
)∙Fб1
= 0,5∙(0,996 - 0,954)∙0,36 = 0,0076 МН∙м
0,5∙((Dб
-Dс.п.
)∙Fб2
+ (Dс.п.
- D - sэк
)∙Fд
)∙[σ]20
/[σ] = (4.1.54.2.2)
= 0,5∙((0,996 - 0,954)∙0,44 + (0,954 - 0,92 -
- 0,007)∙0,07)∙170/134 = 0,0129 МН∙м,
где [σ]20
= 170 МПа, [σ] = 134 МПа - соответственно для материала фланца при 20 °С и расчетной температуре t = 300 °С. [19]
Проверка прочности и герметичности соединения
Условия прочности болтов при монтаже фланцевого соединения и в его рабочем состоянии выполняются так как:
Fб1
/(nб
∙fб
) < [σ]б.20
, (4.1.5.3.1)
0,36/(36∙2,35∙10-4
) = 43 МПа < 230 МПа; (4.1.5.3.2)
Fб2
/(nб
∙fб
) < [σ]б.
,(4.1.5.3.3)
0,44/(36∙2,35∙10-4
) = 52 МПа < 220 МПа; (4.1.5.3.4)
Условие прочности выполняется с запасом, поэтому можно уменьшить количество болтов до 12.
Условие прочности прокладки выполняется:
Fб
max
/(π∙Dс.п.
∙b) < [pпр
], (4.1.5.3.5)
где [pпр
] = 130 МПа для прокладки из паронита;
Fб
max
= max {Fб1
; Fб2
} = Fб2
;
0,44/(3,14∙0,954∙0,012) = 12,2 < 130 МПа.(4.1.5.3.6)
Максимальное напряжение в сечении, ограниченном размером s0
:
σ0
= fф
∙σ1
= fф
∙Тф
∙М0
∙ν/(D*
(s1
- c)2
).(4.1.4.3.7)
У плоского приварного фланца втулка цилиндрическая, fф
= 1, так как s1
/ s0
= 1, D*
= D = 0,92 м, так как D > 20∙s0
(0,92 м > 20∙0,007 = 0,14 м).
Безразмерный параметр:
Tф
= (Dн
2
∙(1 + 8,55∙lg(Dн
/D)) - D2
)/ (4.1.5.3.8)
/((1,05∙D2
+ 1,945∙Dн
2
)∙(Dн
/D - 1)),
Tф
= (1,1362
∙(1 + 8,55∙lg(1,136/0,92)) - 0,922
)/ (4.1.5.3.9)
/((1,05∙0,922
+ 1,945∙1,1362
)∙(1,136/0,92 - 1)) = 0,78.
Таким образом, (4.1.5.3.7) принимает вид
σ0
= 1∙0,78∙0,0129∙0,99/(0,92∙(0,007 - - 0,001)2
) = 301 МПа. (4.1.5.3.10)
Находим напряжения во втулке от внутреннего давления. Тангенциальное
σt
= pр
∙D/(2∙(s0
- c)), (4.1.5.3.11)
σt
= 0,105∙0,92/(2∙(0,007 – 0,001)) = 7,7 МПа; (4.1.5.3.12)
σm
= pр
∙D/(2∙(s0
- c)), (4.1.5.3.13)
σm
= 0,105∙0,92/(2∙(0,007 – 0,001)) = 3,85 МПа.(4.1.5.3.14)
Проверяем условие прочности для сечения, ограниченном размером s0
= 7 мм.
((σ0
+ σm
)2
+ σt
2
- (σ0
+ σm
)∙σt
)0,5
< φ[σ]0
,(4.1.5.3.15)
((301 + 3,85)2
+ 7,72
- (301 + 3,85)∙ 7,7)0,5
< φ[σ]0
, (4.1.5.3.16)
301 МПа < 0,9∙540 = 486 МПа,(4.1.5.3.17)
где [σ]0
= 0,003∙Е = 0,003∙1,8∙105
= 486 МПа;
φ - коэффициент прочности сварных швов, равный 0,9.
Окружное напряжение в кольце фланца находим по формуле:
σк
= М0
∙(1 - ν∙(1 + 0,9∙λ'ф
))∙ψ2
/(D∙h2
ф
),(4.1.5.3.18)
σк
= 0,0129∙(1 - 0,99∙(1 + 0,9∙0,002))*(4.1.5.3.19)
*16,9/(0,92∙0,0242
) = 4,1 МПа.
Условие герметичности фланцевого соединения:
θ = (σк
/Е)∙(D/hф
) < [θ],(4.1.5.3.20)
где θ - угол поворота фланца;
[θ] - допускаемый угол поворота плоского фланца, равный 0,013 рад.
θ = (4,1/1,8∙105
)∙(0,92/0,024) = (4.1.5.3.21)
= 0,001 < [θ] = 0,013 рад.
Таким образом, условие герметичности выполняется, следовательно, расчет фланцевого соединения считаем законченным. [19]
4.1.6 Расчет укрепления отверстий
Корпус аппарата снабжен необходимым количеством штуцеров для подключения его к технологической линии. Отверстия не только уменьшают несущую площадь материала корпуса, механически ослабляя конструкцию, но и вызывают высокую концентрацию напряжений вблизи края отверстия.
Необходимо снизить повышенные напряжения в области отверстий до допускаемых значений за счет компенсации ослабления, вызванного наличием выреза.
Сначала проверим выполнение условия укрепления одиночных отверстий.
Наибольший диаметр одиночного отверстия, не требующего укрепления:
d0
= 2{[(s - c)/sp
- 0,8] - c},(4.1.6.1)
где s - исполнительная толщина обечайки, равная 5 мм по (4.1.2.8);
sp
- расчетная толщина стенки, равная 0,2 мм по (4.1.2.3);
c - суммарная прибавка к расчетной толщине, равная 4 мм (4.1.2.7);
D - диаметр аппарата, равный 0,53 м по (3.5.3.29).
Таким образом,
d0
= 2{[(5 - 4)/0,2 - 0,8] -(4.1.6.2)
- 4∙10-3
} = 0,185 м = 185 мм
Диаметры вырезов в корпусе под штуцеры
d1
= 0,14 м по (4.1.4.2)
d2
= 0,11 м по (4.1.4.3)
d3
= 0,05 м по (4.1.4.4) меньше d0
, следовательно их можно не укреплять. [19]
4.1.7 Расчет тепловой изоляции
В качестве материала тепловой изоляции выберем совелит - наиболее распространенный асбесто-магнезиальный материал (85% магнезии + 15% асбеста).
Сырьем для производства совелита служат доломит и асбест. Совелит применяют для тепловой изоляции, материал способен выдерживать температурную нагрузку до +500 °С. Коэффициент теплопроводности совелита λи
= 0,08 Вт/м∙К.
Принимаем температуру наружной поверхности стенки tст
= 50 °С, температуру окружающей среды tв
= 20 °С, тогда толщина слоя изоляции:
δи
= [λи
∙(tб
- tст
)]/[αв
∙(tст
- tв
)], (4.1.7.1)
где αв
- коэффициент теплоотдачи от внешней поверхности изоляции в окружающую среду;
tб
– температура стенки аппарата без изоляции, равная 300 °С.
aв
= 8,4 + 0,06∙(tст
- tв
) = (4.1.7.2)
= 8,4+0,06∙(50 - 20) = 10,2 Вт/м2
×К.
Таким образом, формула (4.1.6.1) принимает вид:
dи
= [0,08∙(300 - 50)]/[10,2∙(50 - 20)] = 0,06 м. (4.1.7.3)
Принимаем толщину слоя тепловой изоляции равной 60 мм. При такой толщине изоляция будет весить примерно 400 кг.
4.1.8 Расчет опор аппарата
В качестве опор выбираем опорные лапы подвесных аппаратов. Находим массу аппарата.
Масса цилиндрической обечайки:
Go
= 0,785∙(Dн
2
– D2
)∙Н∙rст
, (4.1.8.1)
где Dн
- наружный диаметр обечайки, равный сумме внутреннего диаметра и толщины стенки, 0,53 + 0,005 + 0,005 = 0,54 м;
D - диаметр аппарата, равный 0,53 м по (3.5.3.29);
Нц
- высота цилиндрической части аппарата, равная 2 м;
rст
- плотность стали, равная 7800 кг/м3
.
Go
= 0,785∙(0,542
– 0,532
)∙2∙7800 = 131 кг. (4.1.8.2)
Масса плоского днища:
Gпд
= 0,785∙D2
∙s∙rст
, (4.1.8.3)
где s - толщина днища, равная 5 мм.
Gпд
= 0,785∙0,532
∙0,005∙2700 = 3 кг.(4.1.8.4)
Масса конической крышки с диаметром DH
= 920 мм равна 35,9 кг по ГОСТ 12620-78.
Масса конической обечайки с углом при вершине 20° и высотой 1,1 м равна 100 кг.
Принимаем массу вспомогательного оборудования (загрузочное и разгрузочное устройства, фланцы, штуцера, газораспределительная решетка) 30% от массы основных частей аппарата, тогда полная масса аппарата:
Ga
= 1,3∙(Go
+ Gк
+Gпд
+ Gкд
), (4.1.8.5)
Ga
= 1,3∙(131 + 100 + 3 + 35,9) = 351 кг. (4.1.8.6)
Тогда вес аппарата с учетом веса теплоизоляции будет равен 7367 Н.
Принимаем, что аппарат установлен на четырех опорах, тогда нагрузка приходящаяся на одну опору:
Роп
= 7367/4 = 1842 Н.(4.1.8.7)
Принимаем опоры по ГОСТ 26296-84 с допускаемой нагрузкой 0,0063 МН.
5. СИСТЕМА АВТОМАТИЗАЦИИ
Установка для переработки отходов слюдопластового производства может быть полностью автоматизирована. В данной части дипломной работы подробно рассмотрена автоматизация сушилки кипящего слоя и вспомогательного оборудования.
При автоматизации сушки в кипящем слое основным показателем процесса является температура в слое, и только в случае крупных установок, когда температура по высоте слоя меняется, лучше в качестве такого показателя брать температуру сушильного агента не выходе, которая соответствует средней температуре материала в слое. Регулирующие воздействия при стабилизации температур могут осуществляться изменением расхода влажного материала или сушильного агента, а также изменением температуры последнего. Более предпочтителен первый вариант, так как изменение параметров сушильного агента можно производить только в определенном, довольно узком диапазоне (температуры - ввиду терморазложения материала, расхода - вследствие повышенного уноса частиц с сушильным агентом). Первый способ предполагает наличие между сушилкой и предыдущим технологическим процессом промежуточного бункера с определенным запасом материала. Для предотвращения сводообразования и зависания материала в бункере предусматривают автоматические устройства, которые осуществляют встряхивание через определенные промежутки времени.
Нормальная работа сушилок КС возможна только при определенной высоте кипящего слоя, с целью поддержания заданного значения этого параметра стабилизируется гидродинамическое сопротивление слоя, т. е. перепад давлений до и после решетки, воздействием на вариатор электродвигателя питателя сухого материала. Можно регулировать перепад давлений и изменением расхода сушильного агента, однако при этом температура в кипящем слое будет сильно колебаться.
Кроме этих регуляторов предусматриваются стандартные узлы регулирования разрежения, начальной температуры сушильного агента, его расхода, соотношения расходов топлива и первичного воздуха.
При сушке, выпаривании, обжиге и других процессах в качестве теплоносителя часто используют топочные газы, получаемые в толках и результате сжигания топлива. В зависимости от требований, предъявляемых к топочному газу, в промышленности используют топки разных конструкций. Наиболее простой является топка с инжекционными горелками, её схема приведена на рисунке 5.1(а). Расход топлива в этом случае изменяется в зависимости от температуры (или какого-либо другого параметра) того процесса, в котором используют полученные топочные газы. Соотношение расходов топлива и воздуха, подсасываемого из атмосферы, поддерживается постоянным за счет изменения инжекционной способности горелки при изменении расхода топлива. Температуру топочных газов сразу после топки регулируют изменением расхода вторичного воздуха.
При использовании горелок с принудительной подачей первичного воздуха (схема приведена на рисунке 5.1(б)) возникает необходимость в регуляторе соотношения топливо - первичный воздух.
В отдельных случаях разбавляющий воздух подается одновременно в охлаждающую рубашку топки и в смесительную камеру. Расход вторичного воздуха при такой технологии изменяется в зависимости от температуры во внутренней футеровке топки или температуры в топке вблизи футеровки, а расход третичного воздуха - от температуры после смесительной камеры.
В данном случае используем горелку с принудительной подачей первичного воздуха.

Рисунок 5.1. Схемы регулирования топок: а - с инжекторной горелкой; б - с принудительной подачей первичного воздуха; 1 - топка; 2 - смесительная камера; 3 - технологический аппарат (сушилка КС); 4 - инжекторная горелка
С учетом всего раньше сказанного на рисунке 5.2 приведена схема регулирования процесса в сушилках с кипящим слоем.

Рисунок 5.2. Схема регулирования процесса в сушилках с кипящим слоем: 1 - сушилка; 2 - кипящий слой; 3 - решетка; 4 - топка; 5 - промежуточный бункер; 6 - питатели; 7 - вариаторы; 8 - электродвигатели; 9 - циклон.
В установке по переработке отходов слюдопластовой бумаги предусмотрено помимо циклона использование рукавного фильтра. Рукавные фильтры устанавливают, как правило, для полной очистки газа от твердых веществ, являющихся ценным продуктом. Поэтому показателем эффективности процесса будем считать концентрацию твердого вещества в газе на выходе из фильтра, а целью управления - поддержание его на заданном (минимально возможном для данных условий) значении. В рукавные фильтры поступают возмущения по каналу сжатого воздуха, подаваемого в сопла для регенерации. Регулируют перепад давления ∆Р в камерах загрязненного и очищенного газа, который наиболее полно отражает ход процесса:
∆Р = ∆Рt
+ G∙µ∙W/(k∙ρ∙g),
где ∆Рt
- перепад давления, обусловленный фильтрующей тканью и неудаленными частицами пыли;
G - масса пыли, осевшей ив единице площади фильтра за определенный промежуток времени;
µ - вязкость газ;
W - скорость газа;
k - проницаемость слоя пыли на ткани;
ρ - плотность пыли.
Из уравнения следует, что регулировать перепад ∆Р можно лишь изменением массы пыли G, так как остальные параметры обусловлены ходом предыдущего технологического процесса. Регулирование осуществляется следующим образом. При достижении максимального перепада позиционный регулятор выдает сигнал па электромагнитные клапаны, установленные на магистрали сжатого воздуха. Клапаны открываются, импульсы сжатого воздуха через сопла поступают в рукава и деформируют ткань, сбивая при этом пыль. Регенерации ткани происходит до достижения минимального перепада давления.
Качественная регенерация фильтрующей ткани рукавов будет осуществляться только при определенном значении давления сжатого воздуха, подаваемого на продувку. Для стабилизации этого давления устанавливают регулятор.
Контролю и сигнализации подлежат следующие параметры: температура загрязненного газа (фильтровальная ткань рассчитана только на определенные температуры), давление сжатого воздуха, перепад давления. При критических значениях давления сжатого воздуха и перепада давления (превышение критического значения перепада приводит к разрыву ткани) срабатывает устройство защиты, отключающее рабочий фильтр и включающее резервный. Контролю подлежит расход газового потока. На рисунке 5.3 представлена типовая схема автоматизации процесса фильтрования газовых систем.

Рисунок 5.3. Схема автоматизации рукавного фильтра: 1 - корпус фильтра; 2 - рукава; 3 - сопла импульсной продувка; 4 – шнек
Высушенный материал перемещается к фасовочно-упаковочному аппарату при помощи ленточного транспортера. Показателем эффективности этого процесса является расход транспортируемого материала, а целью управления будем считать поддержание заданного значения расхода. В связи с тем, что все возмущения на входе в объект (изменение гранулометрического состава материала, его влажности и насыпной массы, проскальзывание ленты транспортера и т.д.) устранить невозможно, расход материала следует принять в качестве величины и регулировать его корректировкой работы дозировочных устройств. Контролю подлежит расход перемещаемого материала и количество потребляемой приводом электроэнергии. При резком возрастании тока электродвигателя транспортера, например в случае залипания ленты, должны сработать устройства сигнализации и защиты. Последние отключают электродвигатель. В связи с возможностью засорения отдельных участков транспортной системы посторонними включениями (комками, налипшим материалом) и опасности выхода из строя отдельных элементов транспортера контролируется и сигнализируется также наличие потока материала с помощью специального датчика. На рисунке 5.4 приведена типовая схема автоматизации процесса перемещения сыпучих материалов.

Рисунок 5.4. Типовая схема автоматизации процесса перемещения сыпучих материалов: бункер, 2 – дозатор; 3 – вариатор; 4- ленточный транспортер
В таблице 5.1 представлена спецификация на технические средства автоматизации. [20]
Таблица 5.1 Спецификация на технические средства автоматизации
Обозн.
|
Наименование и техническая
характеристика оборудования
|
Тип, марка оборудования
|
Завод-изготовитель
|
Ед-ца изм.
|
Кол.
|
Индикация, регистрация и регулирование температуры с помощью пневматического регулятора (TIRС, пневматика)
|
TE
|
Термоэлектрический термометр тип ТХА, гр. ХА, пределы измерения от –50 °С до 900 °С, материал корпуса Ст0Х20Н14С2
|
ТХА-0515
|
ОАО «АПЗ», Россия, г.Арзамас
|
шт.
|
1
|
TT
(E/E)
|
Преобразователь термоЭДС в стандартный токовый сигнал 0…5 мА, гр. ХА
|
Ш-72
|
АОЗТ «ТД» «Тизприбор», г. Москва
|
шт.
|
1
|
TT
(E/P)
|
электропневмопреобразователь, входной сигнал 0…5 мА, выходной – стандартный пневматический 0,02…0,1 МПа
|
ЭПП-63
|
АОЗТ «ТД» «Тизприбор», г. Москва
|
шт.
|
1
|
TIRK
|
пневматический вторичный прибор на 3 параметра со станцией управления
|
ПВ 10.1Э
|
ОАО «Челябинский завод Техприбор»
|
шт.
|
1
|
TC
|
Пневматический ПИ-регулятор
|
ПР 3.31
|
АОЗТ «ТД» «Тизприбор», г. Москва
|
шт.
|
1
|
Индикация, регистрация и регулирование давления (PIRC, пневматика)
|
РT
|
Пневматический первичный преобразователь давления, предел измерения 0… 1,6 МПа, выходной сигнал 0,02…0,1 МПа
|
МС-П-2
|
ОАО «АПЗ», Россия, г.Арзамас
|
шт.
|
1
|
РIRK
|
пневматический вторичный прибор на 3 параметра со станцией управления
|
ПВ 10.1Э
|
ОАО «Техприбор», г.Рязань
|
шт.
|
1
|
РC
|
Пневматический ПИ-регулятор
|
ПР 3.31
|
Концерн «Метран», г. Челябинск
|
шт.
|
1
|
Регулирующий клапан для неагрессивных сред, корпус из чугуна, предельная температура Т = 300 °С, давление Ру
= 1,6 МПа, условный диаметр Dу
= 100 мм,
|
25нч32нж
|
АОЗТ «ТД» «Тизприбор», г. Москва
|
шт.
|
1
|
Индикация и регистрация давления (PIR, эл.)
|
РТ
|
Первичный преобразователь давления со стандартным токовым выходом 0…5 мА
|
МС-Э
|
Концерн «Метран», г. Челябинск
|
шт.
|
1
|
РIR
|
Миллиамперметр показывающий регистрирующий на 2 параметра
|
А-542
|
ОАО «Челябинский завод Техприбор»
|
шт.
|
1
|
Индикация, регистрация, регулирование и сигнализация
давления (PIRCA, пневматика).
|
РT
|
Пневматический первичный преобразователь давления, предел измерения 0… 1,6 МПа, выходной сигнал 0,02…0,1 МПа
|
МС-П-2
|
Концерн «Метран», г. Челябинск
|
шт.
|
1
|
РIRK
|
пневматический вторичный прибор на 3 параметра со станцией управления
|
ПВ 10.1Э
|
ОАО «Техприбор», г.Рязань
|
шт.
|
1
|
РC
|
Пневматический ПИ-регулятор
|
ПР 3.31
|
Концерн «Метран», г. Челябинск
|
шт.
|
1
|
Регулирующий клапан для неагрессивных сред, корпус из чугуна, предельная температура Т = 300 °С, давление Ру
= 1,6 МПа, условный диаметр Dу
= 100 мм,
|
25нч32нж
|
ОАО «Техприбор», г.Рязань
|
шт.
|
1
|
РА
|
Электроконтактный манометр с сигнальной лампой
|
ЭКМ-1
|
Концерн «Метран», г. Челябинск
|
шт.
|
1
|
Лампа сигнальная
|
Л-1
|
шт.
|
1
|
Контроль и сигнализация температуры (TIRA)
|
TE
|
Преобразователь термоэлектрический хромель-копелевый. HCX-XK(L). Диапазон измерения -40…600°С. Монтажная длина 400 мм.
|
ТХК-0192
|
ОАО «Челябинский завод Техприбор»
|
шт.
|
1
|
TIRA
|
Прибор аналоговый, регистрирующий с дисковой диаграммой и устройством сигнализации. Шкала 0-300 °С.
|
ДИСК-250
|
ОАО «Челябинский завод Техприбор»
|
шт.
|
1
|
Контроль расхода сырья (FIR)
|
FE
|
Диафрагма камерная Dy=150 мм, Py=4 МПа, Dраст=82,60 мм.
|
ДСК-4-150
|
ОАО «Техприбор», г.Рязань
|
шт.
|
1
|
FT
|
Преобразователь измерительный разности давлений, предельный номинальный перепад давления 40 КПа, выходной сигнал 0,02…0,1 МПа.
|
ДПП-2-11
|
ОАО «Техприбор», г.Рязань
|
шт.
|
1
|
FIR
|
Прибор контроля пневматический регистрирующий. Шкала 0-100% неравномерная
|
ПКР.1
|
ОАО «Саранский приборостроительный завод»
|
шт.
|
1
|
6. БЕЗОПАСНОСТЬ ОБЪЕКТОВ
Производство молотый слюды флогопит из отходов является сопутствующим при производстве слюдопластовой бумаги. Разрабатываемая установка располагается в том же цеху что и основное производство. Поэтому в рабочем помещении уже обеспечены необходимые метеорологические параметры воздуха, организованы соответствующие системы вентиляции и отопления. Безопасность труда обеспечивается правильно организованным естественным и искусственным освещением. Предусмотрены санитарно-бытовые помещения и устройства.
Барабанная мельница мокрого помола, центрифуга, насосы, вентиляторы, газоочистное, пылеулавливающее оборудование, а также транспортные средства относятся к универсальному оборудованию общего назначения или заводскому. Оно применяется без каких-либо изменений в различных химических производствах. Универсальное оборудование эксплуатируется в соответствии с технической документацией завода-изготовителя и паспортом промышленной безопасности объекта.
В настоящей работе был спроектирован колонный аппарат - сушилка кипящего слоя. Сушилки с кипящим слоем являются одним из прогрессивных типов аппаратов для сушки. Процесс в кипящем слое позволяет значительно увеличить поверхность контакта между частицами материала и сушильным агентом, интенсифицировать испарение влаги из материала и сократить продолжительность сушки. Сушилка кипящего слоя является наиболее опасным аппаратом установки для переработки отходов. Поэтому она выбрана в качестве основного объекта анализа с точки зрения безопасности.
6.1 Производственная безопасность
На этапе проектирования были приняты некоторые решения для обеспечения безопасности дальнейшей эксплуатации сушильной установки. В том числе:
1. Произведен расчет тепловой изоляции (пункт 4.1.7), обеспечивающий соблюдение требуемых теплозащитных характеристик. В качестве материала изоляции выбран совелит - наиболее распространенный асбесто-магнезиальный материал (85% магнезии + 15% асбеста). Толщина его слоя для снижения температуры корпуса сушилки с 300 °С до 50 °С составляет 60 мм. Паропровод, сушильные тракты и циклон, который находится в месте прохода обслуживающего персонала, также имеют тепловую изоляцию;
2. Среда внутри сушильного аппарата имеет повышенную температуру, сушилка снабжена необходимым числом штуцеров и фланцевых соединений. Во избежание прорыва горячего газа необходимо обеспечение герметичности. В пункте 4.1.4.3 произведена проверка условий прочности и герметичности соединения конической части корпуса с крышкой аппарата.
3. Сушилка кипящего слоя является аппаратом колонного типа, у которого высота в несколько раз больше диаметра, поэтому он должен быть надежно закреплен во время эксплуатации. В пункте 4.1.6 был произведен расчет массы аппарата и принято решение о креплении его при помощи опорных лап подвесных аппаратов к сварной конструкции, которая в свою очередь крепится к полу при помощи фундаментных болтов.
4. Для снижения количества выбросов в атмосферу и запыленности рабочего помещения сушилка снабжена необходимыми газоочистными аппаратами - циклоном и рукавным фильтром;
5. Во избежание образования пробки и прорыва горячих газов сушильные тракты не имеют участков, мешков и тупиков, где может отлагаться пыль. Угол наклона газоходов к горизонту должен составлять не менее 45°. Скорость теплоносителя на входе в сушилку больше 20 м/с, поэтому принято решение о применении горизонтального газохода;
6. Так как сушильная установка является вновь проектируемым аппаратом, вместимость бункера сырой слюды должна быть не менее часовой производительности сушилки, поэтому бункер спроектирован из расчета на 185 кг материала, подлежащего сушке;
7. Питатель для загрузки влажной слюды имеет устройство для плавного регулирования его производительности, чтобы избежать чрезмерной или недостаточной подачи материала в сушилку, что может привести к спеканию слюды и аварийной ситуации;
8. Температура газов перед дымососом не должна превышать 120 °С, данное условие обеспечивается необходим объемом подсасываемого воздуха;
9. В период пуска и остановки сушилки должен дистанционно подаваться защитный пар над и под газораспределительной решеткой, для чего над решеткой предусмотрен дополнительный штуцер.
Правила безопасности при эксплуатации сушилки с кипящим слоем включают в себя следующие требования:
1. Работники, обслуживающие газовую сушильную установку, должны следить за:
· исправностью механизмов, оборудования и предохранительных клапанов;
· давлением пара в подводящем трубопроводе;
· герметизацией всех трактов сушилки, не допуская увеличения присосов воздуха выше нормированной величины;
· устанавливать строгий контроль за местами возможных отложений частиц слюды;
2. Запрещаются пуск и работа сушильной установки при:
· отсутствии или неисправности КИП, сигнализации и блокировок;
· неисправности оборудования, укрытий и систем промышленной вентиляции;
· отсутствии защитного пара или инертного газа;
· наличии очага горения в сушильном тракте;
· забивке отводов и неисправности предохранительных клапанов;
· забивке отверстий газораспределительной решетки;
· повышении температуры газов перед дымососом более предела;
· достижении нижней величины температуры газов на входе в сушилку;
3. Перед пуском сушильной установки обслуживающий персонал обязан проверить наличие и исправность:
· КИП, сигнализации;
· устройств подачи защитного пара (инертного газа) в сушильный тракт;
· оборудования предохранительных клапанов;
· ограждений и защитных устройств.
· температуру в контролируемых точках сушильного тракта;
На основании настоящих требований составляется рабочая инструкция по безопасной эксплуатации сушильной установки, которая проходит экспертизу промышленной безопасности в специализированных организациях и утверждается техническим руководителем. По результатам режимных испытаний инструкция корректируется, и в соответствии с этим срок ее действия продлевается на два года.
6.2 Экологическая безопасность
В сушильной установке с кипящим слоем подогрев сушильного агента осуществляется за счет сжигания газообразного топлива с высоким избытком воздуха в топке. При этом требуемая температура сушильного агента обеспечивается за счет дополнительного смешения продуктов сгорания и воздуха перед сушильной камерой. В качестве топлива используется природный газ.
Продукты горения природного газа отрицательно влияют на экологию.
Источники диоксида углерода могут быть с достаточной уверенностью выражены количественно. Одним из наиболее значительных источников роста концентрации СО2
в атмосфере является сгорание ископаемого топлива. Природный газ производит меньше СО2
на единицу энергии, чем другие виды ископаемых топлив. Поэтому подогрев сушильного агента производится за счет сгорания именно газа, а не, к примеру, мазута.
Кроме того использование природного газа вместо других видов ископаемых топлив является экономически привлекательным и может внести важный вклад в выполнение обязательств, принятых отдельными странами в соответствии с РКИК. Это топливо, которое оказывает минимальное воздействие на окружающую среду по сравнению с другими видами ископаемых топлив. Переход с ископаемых углей на природный газ при сохранении того же соотношения эффективности преобразования энергии топлива в электроэнергию сократил бы выбросы на 40%. Природный газ генерирует меньше СО2
при том же количестве вырабатываемой энергии, чем уголь или нефть, поскольку он содержит больше водорода по отношению к углероду, чем другие виды топлива.
Выбросы в атмосферу при сжигании ископаемого топлива зависят не только от вида топлива, но от того, насколько эффективно оно используется. Газообразное топливо обычно сжигается легче и эффективнее, чем уголь или нефть. Утилизация сбросной теплоты от отходящих газов в случае природного газа осуществляется также проще, так как топочный газ не загрязнен твердыми частицами или агрессивными соединениями серы. Благодаря химическому составу, простоте и эффективности использования природный газ может внести существенный вклад в снижение выбросов диоксида углерода путем замены им ископаемых видов топлив.
В целом установка для переработки отходов производства слюдопластовой бумаги положительно влияет на состояние экологии. Отходам слюды присвоен 4 класс опасности, степень вредного воздействия на окружающую природную среду - низкая. Критерием отнесения к данному классу является нарушение экологической системы с периодом самовосстановления не менее 3-х лет. Слюда флогопит мелкодисперсная имеет 3 класс опасности, для которого период восстановления - не менее 10 лет после снижения вредного воздействия от существующего источника. Существующие сейчас на «Слюдяной фабрике» способы утилизации отходов слюдяного производства имеют огромное количество недостатков. Для складирования требуются все большие и большие территории, отходы проникают в почву, нарушая обменные процессы в природной среде. Дальнейшее захоронение отходов опять же требует новых территорий. Подземные свалки не заметны на первый взгляд, но на поверхности земли над ними почва отравлена и разрыхлена, она не пригодна, ни для строительства, ни для земледелия, ни для выпаса скота. Таким образом, единственным, относительно экологически чистым, способом борьбы с промышленными отходами, на сегодняшний день, является переработка отходов. Вовлечение отходов в переработку позволяет решить проблему их утилизации и снизить себестоимость основной продукции - слюдопластовой бумаги.
6.3 Возможные неполадки и аварийные ситуации, способы их устранения
Как уже говорилось раньше, спроектированная установка находится в одном цеху с установкой для производства слюдопластовой бумаги. Технологические процессы осуществляются в соответствии с режимными картами и рабочими инструкциями по безопасной эксплуатации, разработанными на основании требований по безопасной эксплуатации. Режимные карты и рабочие инструкции утверждены техническим руководителем организации, прошли экспертизу промышленной
безопасности в специализированных организациях. Поэтому уже определены и утверждены определенные меры безопасности в случае аварийных ситуаций.
В случае аварийной ситуации на этапе сушки предусмотрена автоматическая остановка работы сушильной установки. Вынужденная (автоматическая) остановка должна производиться в случаях:
· остановки механизмов топочного устройства;
· нарушения параметров топочного режима - обрыва факела, снижения давления топлива и воздуха перед горелкой (форсункой);
· остановки механизмов дымососа, загрузочного устройства сушилки, циклона, рукавного фильтра, конвейера для высушенной слюды;
· забивки циклона, рукавного фильтра;
· прорыва наружу сушильного агента и резкое падение температуры внутри аппарата.
Вынужденная остановка с участием оператора должна производиться в случае неисправности предохранительных клапанов.
При аварийных ситуациях срабатывают блокировки на автоматическую остановку, после чего одновременно открывается клапан растопочной трубы, закрывается направляющий аппарат дымососа с последующим отключением электродвигателя дымососа, подается защитный пар под и над газораспределительной решеткой, останавливается узел загрузки.
Оператор должен уменьшить теплопроизводительность топки посредством ограничений подачи первичного, вторичного воздуха и топлива и наблюдать за выходом слюды из сушилки, циклона, аппарата сухого пылеулавливания, затем остановить разгрузочные устройства, конвейер высушенной слюды, пылеулавливающую систему.
В зависимости от продолжительности остановки необходимо перевести топку в горячий резерв (ограниченная теплопроизводительность топки) или в холодный резерв, при котором отключаются вентиляторы и прекращается подача топлива, на подшипники дымососов и охлаждающие панели топки прекращается подача воды.
После чего обязательно проведение мероприятий по осмотру сушильного тракта, устранению причин, которые привели к вынужденной остановке, восстановлению диафрагм предохранительных клапанов.
7. РАСЧЕТ ЭКОНОМИЧЕСКОЙ ЭФФЕКТИВНОСТИ
Молотая слюда флогопит производится из слюдопластовых отходов. Ее производство является сопутствующим при основном производстве слюдопластовой бумаги. Образующиеся отходы подлежат измельчению, центрифугированию и сушке. Проектируемая установка для переработки отходов находится в одном цеху с основным производством. Главной задачей при разработке установки по переработке отходов слюдопластового производства является не столько экономическая выгода, сколько экологический эффект, получаемый от вторичного использования сырья, имеющего 3-4 класс опасности.
1) Расчет инвестиций в оборудование
Величина необходимых инвестиций в оборудование Ik определяется исходя из расчетно-балансовой стоимости (К), включающей цену оборудования и затраты на его доставку и монтаж. Расчетно-балансовая стоимость i-й единицы оборудования:
Кi
= Pi
∙k (руб.),(7.1)
где Рi
- цена аппарата или отдельного модуля i-го типа;
k - коэффициент перехода к расчетно-балансовой стоимости,
для техники, не требующей специального монтажа и настройки, k = 1,07,
для техники, требующей дополнительного монтажа и настройки, k = 1,12.
Для барабанной мельницы, центрифуги, сушилки и фасовочно-упаковочного аппарата k = 1,12; для остального оборудования k = 1,07.
Таким образом,
Kбар.мельн.
= 600 000∙1,12 = 672 000 руб.; (7.2)
Kцен.
= 800 000∙1,12 = 896 000 руб.; (7.3)
Kсуш.
= 250 000∙1,12 = 280 000 руб.; (7.4)
Kупак.
= 500 000∙1,12 = 560 000 руб.; (7.5)
Kшн.тр.
= 80 000∙1,07 = 85 600 руб.; (7.6)
Kнас.
= 25 000∙1,07 = 26 750 руб.; (7.7)
Kгидр.
= 15 000∙1,07 = 16 050 руб.; (7.8)
Kцикл.
= 20 000∙1,07 = 21 400 руб.; (7.9)
Kрук.ф.
= 200 000∙1,07 = 214 000 руб.;(7.10)
Kлент.тр.
= 100 000∙1,07 = 107 000 руб.;(7.11)
Kшл.затв.
= 100 000∙1,07 = 107 000 руб.(7.12)
Инвестиции в оборудование:
Ik =N∙Ki
(руб.),(7.13)
где N - потребное количество техники.
В производстве используется 2 шнековых транспортера и 2 насоса. Так как установка состоит из нескольких различных типов оборудования, то инвестиции рассчитываем по формуле:
Ik= (руб.),(7.14)
где М - количество типов машин (оборудования);
Ni
- необходимое количество машин (оборудования) данного (i-го) типа.
Ik = 672 000 + 896 000 + 560 000 + 280 000 +(7.15)
+ 85 600∙2 + 26 750∙2 + 16 050 + 21 400 +
+ 214 000 + 107 000 + 107 000 = 3 098 150 руб.
С учетом дополнительных расходов на трубопроводы, промежуточные баки, бункеры и др. принимаем величину инвестиций раной 3 200 000 руб.
2) Расчет эксплуатационных затрат
Определяем величину затрат на электроэнергию:
Зэн
= ,(7.16)
где М - количество типов техники (аппаратов);
Ni
- количество техники (аппаратов) i-го типа;
Pi
- совокупная мощность электродвигателей аппарата i-го типа;
Fpi
- реальный фонд рабочего времени в год на один аппарат i-го типа;
Цэн
- текущая цена за 1Квт∙ч, равная 2 руб.
Наибольшее количество энергии потребляют барабанная мельница, вентилятор высокого давления и фасавочно-упаковочный аппарат. Эти аппараты работают непрерывно 7 часов в сутки. Шнековые транспортеры, насосы, центрифуга работают дискретно (меньше 7 часов), но они потребляют небольшое количество энергии, поэтому для простоты расчетов будем считать их работу непрерывной.
Зэн
= (26∙7 + 2∙(1,1∙7) + 2∙(2,2∙7) + 1,8∙7 +(7.17)
+1,1∙7 + 22∙7 + 15∙7 + 4∙7)∙2∙250 = 267 750 руб./год.
Сушка слюды производится топочными газами, образующимися при сгорании природного газа. Затраты на топливо:
Зт
= ,(7.18)
где М - количество типов техники (аппаратов), равное 1;
Ni
- количество техники (аппаратов) i-го типа, равное 1;
Тi
- нормативное (расчетное) потребление топлива за ед. времени (за час) аппаратом i-го типа, сушилкой кипящего слоя, равное 8,64 м3
;
Fpi
- реальный фонд рабочего времени в год на один аппарат i-го типа, равный 1750 ч.;
Цi
- цена за ед. топлива для аппарата i-го типа, равная 3 руб 30 коп за 1 м3
газа.
Зт
= 1∙1∙8,64∙1750∙3,3 = 49 896 руб./год. (7.19)
Стоимость смазочных и обтирочных материалов для аппаратов, входящих в состав установки для переработки отходов слюдопластового производства незначительна. Тогда годовые затраты на топливо и электроэнергию:
С2
= Зэн
+ Зт
= 267 750 + 49 896 = (7.20)
= 317 646 руб./год.
Принимаем С2
= 320 000 руб./год с учетом дополнительных расходов.
С1
- затраты на сырье, используемое в процессе производства в год, считаем, что С1
= 0 руб./год, так отходы - бесплатное сырье, ранее вывозимое на свалку.
Издержки на основную заработную плату производственным рабочим (С3
):
Годовой фонд оплаты труда = (руб./год), (7.21)
где N - количество специальностей;
Ti
- годовой фонд рабочего времени для одного рабочего i-й специальности (ч);
Mi
- количество рабочих i-й специальности;
Pi
- тарифная ставка рабочего i-й специальности (руб./ч).
Установку обслуживает один человек, он работает 5 дней в неделю по 8 часов. Его заработную плату принимаем равной 20 000 руб./мес., тогда годовой фонд оплаты труда (С3
) составляет 240 000 руб.
Издержки на дополнительную заработную плату в год:
С4
= 7,5% от С3
;(7.22)
С4
= 0,075∙240 000 = 18 000 руб./год. (7.23)
Отчисления на социальные нужды (С5
):
Отчисления во внебюджетные фонды составляют 26% от фонда оплаты труда (ФОТ).
С5
= 26% от (С3
+ С4
);(7.24)
С5
= 0,26∙(240 000 + 18 000) = 67 080 руб./год. (7.25)
Отчисления на амортизацию:
С6
= (руб.), (7.26)
где N - количество типов оборудования;
Iki
- инвестиции в i-й тип оборудования (руб.);
На
i
- норма амортизации i-го типа оборудования (%);
На
i
= 100% / Тi
,
Тi
- нормативный срок службы оборудования i-го вида (лет).
Средний срок службы используемой аппаратуры составляет 10 лет, тогда
С6
= (1/10)∙3 200 000 = 320 000 руб./год. (7.27)
Отчисления в ремонтный фонд:
С7
= 3% от инвестиций;
С7
= 0,03∙3 200 000 = 96 000 руб./год.(7.28)
Таким образом, суммарные расходы:
С = С1
+ С2
+ … + С7
= 320 000 + 0 +(7.29)
+ 240 000 + 18 000 + 67 080 + 320 000 + 96 000 =
= 1 061 080 руб./год.
С учетом прочих возможных расходов С8
принимаем общую сумму расходов равной 1 100 000 руб./год.
3) Определение стоимости товарной продукции
Отпускная цена
Ротп
= Суд
+ Нпр
(руб. за ед. товара), (7.30)
где Ротп
- отпускная цена;
Суд
- удельная себестоимость;
Нпр
- норма прибыли (% от Суд
), задается исходя из анализа текущих рыночных цен на аналогичную продукцию.
Цена реализации:
Рреал
= Ротп
с учетом НДС;(7.31)
Рреал
= (Ротп
∙100%) / (100% - НДС) (руб. за ед. товара).
Анализируя текущие рыночные цены на молотую слюду, принимаем отпускную цену на продукцию равной 15 000 руб. за тонну. Тогда цена реализации равна:
Рреал
= (15 000∙100%) / (100% - 18%) = 18 300 руб./т. (7.32)
4) Определение валовой выручки
ВВ = Рреал
∙V (руб./год),(7.33)
где V - объем товарной продукции, равный 250 т молотой слюды в год.
ВВ = 18 300∙250 = 4 575 000 руб./год.(7.34)
5) Расчет налоговых отчислений
Налог на добавленную стоимость:
НДС = 18% от ВВ (руб.);(7.35)
НДС = 0,18∙ 4 575 000 = 823 500 руб.(7.36)
Налог на пользователей автомобильных дорог:
НПАД = 1% от (ВВ - НДС) (руб.);(7.37)
НПАД = 0,01∙(4 575 000 - 823 500) =(7.38)
= 37 515 руб.
Налог на имущество:
НИ = 2% от Ik (руб.);(7.39)
НИ = 0,02∙3 200 000 = 64 000 руб.(7.40)
6) Расчет чистой прибыли
Расчет прибыли:
П = ВВ - С - НДС - НПАД - НИ (руб.), (7.41)
где С - полная себестоимость производства продукции.
П = 4 575 000 - 1 100 000 - 823 500 -(7.42)
- 37 515 - 64 000 = 2 549 985 руб./год.
Налог на прибыль:
НП = 24% от прибыли (руб.);(7.43)
НП = 0,24∙2 549 985 = 611 997 руб.(7.44)
Чистая прибыль:
ЧП = П - НП (руб.);(7.45)
ЧП = 2 549 985 - 611 997 = 1 937 988 руб./год.(7.46)
7) Расчет срока окупаемости
Ток
= Ikå
/
ЧП (лет), (7.47)
где Ikå
- инвестиции в проект,
так как проект представляет собой организацию нового производства «с нуля», то
Ikå
= Ik + C = 3 200 000 + 1 100 000 = (7.48)
= 4 300 000 руб.
Ток
= 4 300 000 / 1 937 988 2 года. (7.49)
Из произведенных расчетов видно, что проектируемая установка не только позволяет перерабатывать отходы с целью уменьшения отрицательного влияния на окружающую среду, но и дает прибыль равную 2 млн. рублей в год и окупается за 2 года, что говорит о несомненной целесообразности внедрения данного проекта.
8 СПИСОК ИСПОЛЬЗОВАННОЙ ЛИТЕРАТУРЫ
1. Сиденко, П.М. Измельчение в химической промышленности / П. М. Сиденко. - М.: Химия, 1977. - 368 с.
2. Крюков, Д.К. Футеровки шаровых мельниц / Д.К. Крюков. - М.: Машиностроение, 1965. - 184 с.
3. Борщев, В.Я. Оборудование для переработки сыпучих материалов/ В.Я. Борщев, Ю.И. Гусев, М.А. Промтов, А.С. Тимонин. - М.: Машиностроение - 1, 2006. - 208 с.
4. Борщев, В. Я. Оборудование для измельчения материалов: дробилки и мельницы / В. Я. Борщев. - Тамбов: ТГТУ, 2004. - 75с.
5. Лебедев, П.Д. Расчет и проектирование сушильных установок / П. Д. Лебедев. - Л.: Государственное энергетическое издательство, 1963. - 320 с.
6. Мухленов, П.И. Расчеты аппаратов кипящего слоя / П. И. Мухленов, Б. С. Сажин, В.Ф. Фролов. - Ленинград: Химия, 1986. - 352 с.
7. Рашковская, Н.Б. Сушка в химической промышленности / Н. Б. Рашковская. - Л.: Химия, 1977. - 80 с.
8. Романков, П.Г. Сушка во взвешенном слое: теория, конструкции, расчет / П. Г. Романков, Н. Б. Рашковская. - Л.: Химия, 1968. - 360 с.
9. Лукьяненко В. М. Промышленные центрифуги / В. М. Лукьяненко, А. В. Таранец. - М.: Химия, 1974. - 378 с.
10. Соколов В. И. Современные промышленные центрифуги / В. И. Соколов. - М.: Машиностроение, 1967. - 525 с.
11. Ветошкин А. Г. Процессы и аппараты защиты гидросферы / А. Г. Ветошкин. - Пенза: ИПГУ, 2004. - 188 с.
12. Чернобыльский И. И. Машины и аппараты химических производств / И. И. Чернобыльский. - М.: Машиностроение, 1975. - 465 с.
13. Соколов В. Н. Машины и аппараты химических производств: примеры и задачи / В. Н. Соколов. - Л.: Машиностроение, 1982. - 384 с.
14. Сажин Ю. Г. Расчеты рудоподготовки обогатительных фабрик / Ю. Г. Сажин. - Алматы: КазНТУ, 2000. - 179 с.
15. Тимонин А.С. Основы расчета и конструирования химико-технологического и природоохранного оборудования: Справочник: В 3 т. Т.2. / А. С. Тимонин - Калуга: Изд-во Н.Бочкаревой, 2002. - 1025 с.
16. Иоффе И. Л. Проектирование процессов и аппаратов химической технологии / И. Л. Иоффе. - Л.: Химия, 1991. - 352 с.
17. Кольман - Иванов Э. Э. Расчет и конструирование машин химических производств / Э. Э. Кольман - Иванов, Ю. Н. Гусев, И. Н. Карасев, Ю. И. Макаров, М. П. Макевнин, Н. И. Рассказов. - М.: Машиностроение, 1985. - 408 с.
18. Лащинский А. А. Основы конструирования и расчета химической аппаратуры / А. А. Лащинский, А. Р. Толчинский. - Л.: Машиностроение, 1970. - 752 с.
19. Михалев М. Ф. Расчет и конструирование машин и аппаратов химических производств / М. Ф. Михалев. - Л.: Машиностроение, 1984. - 301 с.
20. Голубятников В. А. Автоматизация производственных процессов в химической промышленности / В.А. Голубятников, Шувалов В. В. - М. Химия, 1985. - 352 с.
|