Министерство образования и науки Российской Федерации
Федеральное агентство по образованию
Государственное образовательное учреждение высшего профессионального образования
Магнитогорский государственный технический университет
им. Г.И. Носова
Кафедра металлургии черных металлов
Реферат
Тема: "Устройство и назначение агрегата внепечной обработки стали типа печь-ковш"
Магнитогорск 2009
Содержание
Введение
1. Устройство агрегата печь-ковш
2. Технологические операции, производимые на агрегате печь-ковш
3. Технико-экономические показатели использования установки
Заключение
Список литературы
Введение
Переход на непрерывную разливку, с одной стороны, и непрерывное повышение требований к качеству стали, с другой, привели к необходимости создания специальной установки доводки стали. Ставший обычным и обязательным вариант установки предусматривает возможность завершения процесса раскисления – легирования стали в более благоприятных условиях, чем в сталеплавильном агрегате во время выпуска плавки, и регулирование температуры металла путем его охлаждения. Для этого установка оборудуется средствами: продувки металла аргоном; ввода в металл раскисляющих и легирующих присадок, включая в виде обычной проволоки (алюминий) и порошковой проволоки (ЩЗМ, РЗМ) с помощью трайб-аппарата.
Однако такой вариант установки ковшевой доводки стали требует очень высокого перегрева металла к концу окислительного рафинирования его в сталеплавильном агрегате, что отрицательно сказывается на стойкости футеровки агрегата и ковша, а также на газонасыщенности металла. Поэтому появилась необходимость обеспечить нагрев металла в ковше, используя электрическую энергию. Были опробованы индукционный, дуговой и плазменно-дуговой варианты нагрева. Наиболее приемлемым вариантом оказался электродуговой нагрев.
Установка доводки стали в ковше с нагревом металла появилась более 40 лет назад и получила название печь-ковш.
В данной работе будут рассмотрены устройство и назначение агрегата внепечной обработки стали типа печь-ковш.
1. Устройство агрегата печь-ковш
Типичная конструкция установки LF (печь-ковш) показана на рисунке 1. В ковше наводится рафинировочный шлак, и в него сверху опускают электроды системы электродугового нагрева таким образом, чтобы обеспечить достаточную эффективную теплопередачу и одновременно защитить огнеупоры ковша от дуги. При этом остаточные оксиды железа в шлаке восстанавливаются графитовыми электродами. В результате получают "ультрачистую" сталь с низким содержанием серы.
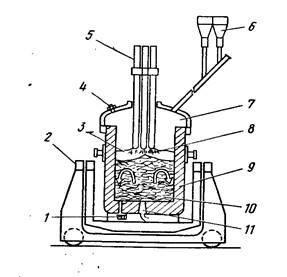
1 - шиберный затвор; 2 - тележка; 3 -основной шлак; 4 - смотровое окно; 5- электроды; 6 - бункеры для хранения легирующих добавок; 7 - инертная атмосфера внутри печи; 8 - нагрев погруженной дугой; 9 - жидкая сталь; 10 - перемешивание инертным газом; 11 - пористая пробка
Рисунок 1 – Схема установки типа печь-ковш
На рисунке 2 показан вариант установки типа печь-ковш, предусматривающий возможность перемешивания металла аргоном под слоем синтетического шлака, вдувание порошкообразных реагентов и подогрев расплава одновременно.
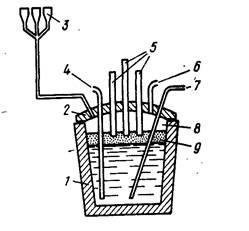
1 - ковш; 2 - крышка-свод; 3 -бункера для ферросплавов и флюсов; 4 - фурма для подачи в металл аргона или азота; 5 - электроды; 6 - подача аргона; 7 - фурма для вдувания порошка силикокальция в струе аргона; 8 - безокислительная атмосфера; 9 -шлак (CaO-SiO2
-Al2
O3
)
Рисунок 2 – Схема установки АР (Arc-Process)
Примером комбинированного процесса с обработкой металла вакуумом, продувкой аргоном и синтетическими шлаковыми смесями может служить VAD -процесс. Схема установки представлена на рисунке 3.

1 - электроды; 2 - бункер с вакуумным затвором для ввода добавок; 3 - пористая пробка для подачи инертного газа
Рисунок 3 – Схема VAD-пpoцecca
Агрегат состоит из камеры, установленной на самодвижущейся тележке, и вакуумного трубопровода в стационарном своде (а не в корпусе камеры). Технология проведения операции следующая: 1) помещение ковша в VAD-камеру и продувка аргоном в течение 3 мин (без вакуума); 2) отбор пробы металла на химический анализ и перемещение камеры с ковшом на участок скачивания шлака (содержащего FeOи Р2
О5
); перемещение камеры с ковшом к VAD-устройству, накрывание сводом и вакуумирование с подогревом (или без подогрева); подогрев осуществляется при помощи электродов, опускаемых через свод; 3) одновременно с вакуумированием наводится присадкой CaO, CaF2
и алюминия новый шлак и продолжается продувка аргоном; 4) после 20-25 мин такой обработки под вакуумом производится корректировка химического состава и температуры (электроподогревом); 5) после получения требуемых результатов вакуумирование прекращается, и камера с ковшом транспортируется на разливочную площадку.
Помимо установок LF с дуговым подогревом разработаны установки с использованием методов индукционного нагрева (и перемешивания). Были попытки использовать в процессе внепечной обработки и такой традиционный способ нагрева, как топливные горелки.
Все современные установки снабжены системой АСУ ТП.
2. Технологические операции, производимые на агрегате печь-ковш
Разработанная и освоенная технология внепечной обработки в агрегатах типа печь-ковш позволяет производить весь спектр металлургических операций в ковшах различной вместимости:
- скачивание шлака с помощью специальной машины,
- электродуговой подогрев металла трехфазным переменным током со скоростью нагрева до 5 град/мин,
- вакуумирование металла при остаточном давлении до 0,5 ГПа и продувку кислородом в вакууме,
- перемешивание металла в ковше с помощью электромагнитного индуктора и продувку аргоном через дно ковша,
- введение добавок с помощью специальной системы.
Возможность нагрева металла в ковше позволяет: снизить перегрев металла в сталеплавильном агрегате; провести раскисление – легирование с повышенным расходом материалов; обеспечить глубокую десульфурацию металла путем наводки высокоосновного восстановительного шлака. Кроме этого, на такой установке высокоэффективно используется продувка металла аргоном. Эта продувка обеспечивает не только дегазацию металла, но и перемешивание его, благодаря чему ускоряется расплавление присаживаемых в ковш ферросплавов и гомогенизация расплава по химическому составу и температуре, существенно улучшается взаимодействие металла и шлака, т.е. десульфурация металла.
Разработаны метод и устройство контроля окисленности шлака, позволяющие экспрессно определять и регулировать содержание окислов железа непосредственно в шлаковой ванне, определять количество вводимых в шлак раскислителей с учетом особенностей каждой плавки. Разработанная технология обеспечивает возможность получения высококачественного металла, и в т.ч. сверхчистой хромистой стали для современных роторов газовых турбин, которые должны надежно работать при температурах от -40°С при пуске до 500°С в рабочем режиме и обладать высокой стойкостью против термического старения.
Повышению эффективности использования установки способствуют многие усовершенствования конструкции, особенно в части электронагрева, в том числе обслуживание двух стендов одним трансформатором и одним комплектом электродов с поворотными электрододержателями (двухпозиционная установка). В части регулирования химического состава металла предусмотрены: продувка металла аргоном через два пористых блока в дне ковша и через погружную фурму; подача в ковш всех материалов, необходимых для наведения шлака, раскисления – легирования и науглероживания металла.
Наиболее важные положения технологии доводки стали на установке печь-ковш сводятся к следующему.
Доводка металла на установке начинается с продувки его в течение 1-2 минуты, после чего производится измерение температуры и окисленности металла. С учетом содержания кислорода в металле вводят в него с помощью трайб-аппарата расчетное количество алюминиевой катанки (проволоки), чтобы осуществить предварительное раскисление металла. После этого приступают к наводке восстановительного шлака, присаживая известь и плавиковый шпат порциями не более 150 кг (общий расход до 10 кг/т). После получения жидкого шлака его раскисляют алюминием, расходуя 0,2-0,3 кг на тонну металла. Наводка шлака продолжается примерно 5 минут.
По окончании наводки шлака через 3 минуты продувки отбирают пробы металла и шлака, измеряют температуру. После получения результатов химического анализа металла производят основную корректировку его химического состава присадкой необходимого количества раскисляющих и легирующих присадок из расчета получения среднего содержания элементов. Затем металл перемешивают не менее 5 минут. После этого снова отбирают пробу металла, по результату ее анализа, если надо, осуществляют дополнительную корректировку химического состава и температуры стали. Высокоактивные элементы в виде порошковой проволоки вводят только после окончания последнего цикла нагрева металла.
3. Технико-экономические показатели использования установки
Использование данного агрегата для внепечной обработки стали позволяет достичь таких технико-экономических показателей:
- повышение производительности - 20-30%;
- сокращение расхода легирующих и раскислителей - 5-25 кг/т;
- сокращение расхода электродов - 5-6 кг/т;
- сокращение расхода электроэнергии - 5-10%;
- сокращение брака - 50-70%.
Агрегат позволяет существенно улучшить экологическую обстановку и повысить социальную привлекательность работы в сталеплавильных цехах.
Заключение
По существу современные установки печь-ковш позволяют успешно провести доводку стали, используя все элементы ковшевой доводки. Это дает основание считать их самой совершенной техникой, применяемой в настоящее время для ковшевой доводки стали.
Список литературы
1) Кудрин В.А. Внепечная обработка стали и чугуна. М.: МИСиС, 1992. 256 с.
2) Бигеев А.М., Бигеев В.А. Металлургия стали. Магнитогорск: МГТУ, 2000. 544 с.
3) Кудрин В.А. Металлургия стали. М.: Металлургия,1989. 560 с.
|