Машиностроение - одна из ведущих отраслей народного хозяйства. Задачей машиностроения является создание совершенных конструкций машин и передовой технологии ее изготовления. Объем продукции должен увеличиваться за счет автоматизации и механизации производства. Основное направление в развитии технического процесса - это создание принципиально новых технологических процессов производства и замена существующих процессов более точными и экономичными. Главное внимание уделяется вопросам сокращения сроков подготовки и повышению качества продукции машиностроения, в значительной степени качество и технико-экономические показатели выпускаемой продукции зависят от подготовки производства, важной составной частью которой является проектирование технологических процессов.
Внедряемые технологические процессы должны обеспечивать высокое качество, точность и низкую себестоимость выпускаемой продукции. Эти показатели обеспечиваются обоснованным применением высокопроизводительного оборудования и технологической оснастки, а также средствами механизации и автоматизации.
В разрабатываемом проекте решается задача получения детали минимальными затратами при использовании высокопроизводительного оборудования и технологической оснастки, также рационального метода получения заготовки.
Целью данного курсового проекта является систематизация, расширение и закрепление теоретических знаний студентов, обучение правильно и самостоятельно решать инженерные и исследовательские задачи, возникающие при проектировании технологических процессов изготовления изделий машиностроения и средств технологического оснащения, а также подготовить студентов к выполнению выпускной квалификационной работы.
В соответствии с поставленной целью в процессе курсового проектирования выделяют следующие задачи:
- развитие и закрепление навыков ведения самостоятельной творческой инженерной работы;
- овладение методикой проектирования технологических процессов механико-сборочного производства;
- приобретения опыта анализа существующих и конструирования современных видов технологической оснастки;
- овладение технико-экономическим анализом принимаемых решений;
- развития навыков самостоятельной защиты принимаемых технических решений.
Анализ исходной информации
Служебное назначение и техническая характеристика узла и деталей
Корпус входит в состав гидрозамка погрузчика. Гидрозамок предназначен для закрытия движения потока рабочей жидкости в рабочий орган погрузчика, что позволяет рабочему органу находится в заданном положении без потребления мощности гидромотора.
Давление рабочей жидкости передаётся через магистральный трубопровод. Давление нагнетается насосной станцией. Трубопроводы подводятся в гнёзда бобышек корпуса, Н, Ш, Сл, У.
При подаче рабочей жидкости в гнездо У поршень смещается влево и двигает штоком подпружиненый шарик. В гнздо Н подаётся рабочая жидкость от источника давления, рабочая жидкость при отжатии шарика попадает в гнездо Ш, далее к рабочему органу. Через гнездо Сл выводится рабочая жидкость поступающая из линии У для предотвращения излишнего отжатия шарика и удаления жидкости поступившей из линии У после перекрытия линии У. Также после прекращения поступления давление рабочей жидкости в линию У, шарик передвигается вправо и закрывает путь истечения жидкости из рабочего органа.
Корпус изготавливается из стали 40Х ГОСТ 4543-71. Химический состав данной стали, приведен в таблице.
Таблица 1
Химический состав, % |
С |
Si |
Mn |
Cr |
0,36…0,44 |
0,17…0,37 |
0,50…0,80 |
0,80…1,10 |
При обработке вала выполняется 5 оригинальных операций. Таким образом, деталь ПЭ1.001 А удовлетворяет всем требованиям курсового проекта.
Принимаем среднесерийный тип производства. В соответствии с этим по [17, табл. 3] найдя трудоёмкость сборки определим среднемесячный выпуск изделий. Трудоёмкость сборки находим избазовог технологического процесса: T = 2,4час
Таким образом среднемесячный выпуск изделий:
Nизд
= 81 - 800 шт
Принимаем:
Nизд
= 800 шт
Определим количество обрабатываемых в год деталей.

где i - количество рассматриваемых деталей в сборке
шт
По [17, табл. 4], исходя из массы детали и годовой программы выпуска, уточняем тип производства.
Масса детали: m = 0,81 кг
Таким образом, тип производства при изготовлении 9600 деталей в год- среднесерийное.
Полученные значения сведены в таблицы 2 и 3.
Годовая программа выпуска изделий
Таблица 2
Наименование изделия |
Характеристика, модель |
Число изделий на программу |
Масса, т |
изделия |
на годовую программу |
Корпус |
ПЭ1.001 А |
9600 |
0,0081 |
7,776 |
Подетальная годовая производственная программа
Таблица 3
№ перехода |
№ чертежа |
Наименование детали |
Марка материала |
Число деталей на изделие |
Процент на запасные части |
Число деталей |
Масса, т |
на основную программу |
на запасные части |
всего |
детали |
На программу с запасными частями |
Корпус |
Сталь 40Х ГОСТ 4543-71 |
1 |
10 |
9600 |
960 |
10560 |
0,0081 |
8,5536 |
В этой части курсового проекта тип производства определён приближённо, используя [17, табл. 3]. В дальнейшем после разработки технологических процессов сборки и изготовления детали серийность производства будет уточняться. Уточнение производится по коэффициенту закрепления операций в соответствии с ГОСТ 14.004-83.
Коэффициент закрепления операций находится как:

где FД
- действительный фонд рабочего времени работы оборудования, час;
N - годовая программа, шт;
tШТ-К.ср
- среднее штучно-калькуляционное время выполнения операции, мин.
Для серийного определяется размер партии запуска:
, шт
где N - годовая программа, шт;
а - период запуска в днях, по рекомендациям [17, с. 11] принимаем а = 12;
F - число рабочих дней в году, для 2003-го года F = 250.
шт.
Анализ действующих технологических процессов
Базовый технологический процесс имеет структуру, представленную в таблице 4.
Базовый технологический процесс изготовления вала
Таблица 4
Операция |
Наименование
операции
|
Оборудование, приспособления, режущий и измерительный инструмент |
Тшт
,
н/ч
|
Во всех операциях: |
Контроль первой детали мастером
Контроль ОТК
Очки 0 ГОСТ12.4.013-85
|
005 |
Фрезерная |
6Т13Ф20-1;
ИОТ №6-89
|
0,5
(2,713)
|
010
|
Слесарная
|
Верстак;
ИОТ №410-98
|
0,8
(3)
|
015 |
Токарная |
1КМ62;
ИОТ №4-91
|
3,28
(5,428)
|
020 |
Токарная |
1К62;
ИОТ №4-91
|
0,81
(5)
|
025 |
Сверлильная |
2А554
ИОТ №5-99
|
1,20´4
(8)
|
030 |
Сверлильная |
2А544
ИОТ №5-99
|
0,30 |
035 |
Слесарная |
Верстак
ИОТ №410
|
040 |
Контроль |
Плита;
ИОТ №238-88,356
|
0,32
(2,52)
|
Специальная оснастка |
Зенкер черн. 027-871, Шаблон 4+0,4
106-6757
Развёртка черн. 037-717
Развёрткам чист. 037-718, Шаблон 32,4+0,16
103-740
Зенкер 7Н12 022-1806
Притир R0.2...0.4 093-845, Калибр на собираемость 150-2629
|
1. В качестве заготовки в базовом технологическом процессе используется штамповка в открытом штампе. Способ получения заготовки рационален для существующего производства.
2. При токарной обработке на операциях 015, 020, 025 и сверлильной обработке на операциях 030 и 035 применяются универсальные станки, что недопустимо при разработке курсового проекта, их необходимо заменить более производительным оборудованием.
3. Недостатком в конструкции корпуса с точки зрения технологичности является выполнение отверстия в бобышках.
4. Широко применяется универсальные инструмент, оснастка и приспособления, их замена специализированным повысит производительность и снизит затраты на производство.
5. Скругление острых кромок во внутренних отверстиях производится ручным способом, что увеличивает время изготовления и процент брака.
6. Базовый технологический процесс сборки расчленён на отдельные узловые сборки, что является технологичным. Стоит отметить отсутствие механизации процесса сборки. Положительным фактором является то, что не требуется механическая обработка после сборки.
7. Сборочный чертёж выполнен согласно соответствуеющим стандартам.
8. На рабочем чертеже корпуса выполнена одна проекция, шесть местных видов. Этого достаточно для однозначного определения конструкции детали. Обозначение шероховатостей, полей допусков, отклонений формы, и расположения поверхностей соответствуют требованиям оформления конструкторской документации.
Базовый технологический процесс сборки
Таблица 5
Технические требования |
1. Рабочая жидкость масло М-10В2
ГОСТ 8581, М-8А ГОСТ 10541 или М-10В2
ГОСТ 8581. Класс чистоты рабочей жидкости не ниже 16 по ГОСТ 17216.
2. Сборку резьбовых соединений и монтаж резиновых колец производить со смазкой рабочей жидкостью.
|
Требования безопасности |
При выполнении работ по данному ТП соблюдать правила безопвсности согласно ИОТ №120, 410, 47А, СТП 406-07256-88, 238А. |
Операция |
Наименование
операции
|
Оборудование и приспособления |
005 |
Комплектование:
1.Подорать детали согласно спецификпции чертежа.
2.Подобрать технологическую оснастку согласно ведомости оснастки.
3.Получить вспомогательные материалы.
4.Контроль мастером первого комплекта.
5.Контроль БТК
|
Тара цеховая, стеллаж цеховой. |
010
|
Подготовка ИОТ №120, 410, 238А
1.Промыть детали в уайт-спирите и продуть сжатым воздухом от цеховой пневмосети, пропущенным через пыле-влагоотделитель.
2.Контроль БТК наличия клейм, отсутствия дефектов и загрязнений.
3.Контроль БТК перехода 2.
|
Сетка цеховая, тара цеховая, стеллаж цеховой.
Ёмкость цеховая, кисть КФ-25, рукав цеховой очки защитные О ГОСТ 12.4.03
|
015 |
Сборка ПЭ1.47.000 А СБ ИОТ №410, 238А
1.Установить последовательно на детали п.4 (ПЭ1.47.004А), п.5 (ПЭ1.47.005 или ПЭ1.47.005-01 для исп. 02) резиновые кольца п.16 (021-25-25-2-2 или 021-025-25-2-2-ТIII-3-100 для исп. 02), п.18 (026-032-36-2-2 или 026-032-36-2-2-ТIII-3-100 для исп. 02), п.17 (024-030-36-2-2 или 024-030-36-2-2- ТIII-3-100 для исп. 02) согласно чертежу.
2.*Установить золотник п.4 в сборе, на подставку, установить в лунку золотника шарик п.19 (13,494-100) или п.20 (14.000-100) и пристукнутьл до образования фаски Б шириной не более 0,3 мм.
3.Закрепить корпус п.1 (ПЭ1.47.001А) в тисках, отв. М30х1,5 вверх, завести в корпус золотник п.4, в сборе и проверить перемещение от руки золтника в отв. Æ25Н8 корпуса без заеданий.
4.Установить в сборку последовательно детали п.19 или 20, п.10 (ПЭ1.47.011), п.5, в сборе, согласно чертежу.
5.Перекернить корпус в тисках установив отв. М27х1,5-7Н вверх.
6.Установить в корпус шарик п.21 (19,844-100) или п.22 (19,447-100) и пристукнуть до образования фаски А шириной не более 0,3 мм. Демонтировать шарик
7.Установить последовательно в сборку детали п.21 или 22 п.9 (ПЭ1.47.009 А), п.2, в сборе, согласно чертежу.
8.Прекрепить сборку в тисках под маркирование.
9.Маркировать сборку для исполнений -01, 02.
10.Контроль БТК.
|
Верстак слесарный 503-47, стеллаж цеховой, тиски слесарные 7827-0262 ГОСТ 4045
Кисть КФ-25, ёмкость цеховая, оправка 30 СТП 406-2525-80, оправка 27 СТП 406-2525-80, пластина профильная пластиковая цеховая.
Выколотка 16 СТП406-2558-82, молоток 7850-0116, Лупа ЛП-4*-7* ГОСТ 25706, Штангенциркуль 125, подставка цинковая.
Выколотка 16 СТП406-2558-82, штырь Æ12 цеховой, кисть КФ-25, ёмкость цеховая.
Кисть КФ-25, ёмкость цеховая, ключ 7811-043.
Выколотка 16 СТП406-2558-82, молоток 7850-0116, Лупа ЛП-4*-7* ГОСТ 25706, Штангенциркуль 125.
Кисть КФ-25, ёмкость цеховая, клбюч 7811-0043.
Комплект клейм 5 СТП 406-2520-79, комплект клейм 5 СТП 406-2521-79, молоток 7850-0116.
|
Технологический процесс сборки изделия
Сборка состоит из минимально достаточных деталей для обеспечения работы изделия. Собираемость деталей, в общем, не представляет трудностей. Однако все же существуют затруднения при образовании фасок, для соприкосновения шариков. Но этот процесс можно автоматизировать, точно выбрав силу удара по шарику.
В конструкции изделия допущен целый ряд решений, которые усложняют его производство в условиях серийного производства.
Цилиндрические бобышки расположены диаметрально противоположно, притом конструкция корпуса делает невозможным делать его сборным.
Составляем схему сборки изделия, используя рекомендации [14, с. 304…306]. При этом стремимся разбивать технологический процесс на большее количество узловых сборок. При составлении схемы учитываем удобство соединения изделий.
Таблица 6
№ перехода |
Содержание работы |
Факторы, влияющие на продолжительность сборки |
№ карты и позиция |
Оперативное время, мин |
1 |
Установить последовательно на дет. поз.4 и поз.5 резиновые кольца поз.16 и поз.18 согласно чертежу |
Длина продвижения- 3мм, установка в канавку, наружный диаметр кольца-2,5мм.
Длина продвижения- 18мм, установка в канавку, наружный диаметр кольца-3,6мм.
|
Карта 45, поз. 1а
|
0,030
|
2 |
установить золотник в сборе в гнездо, сформировать фаску Б 0,3ММ |
Длина продвижения-20мм, масса детали-до 0,25кг, посадка скользящая
|
Карта 40, поз. 1к |
0,043 |
3 |
Закрепить корпус в пневмотисках, отв М30х1,5 вверх, установить золотник поз.4в сборе кольц0 |
Длина передвижения 22,5мм, масса детали до 0,25кг
|
Карта81, поз. 2
Карта 45, поз.1в
|
0,02
0,045
|
4 |
Установить в сборку последовательно дет. поз.19 или 20, поз.10, поз.5 в сборе согласно чертежу |
Диаметры 13,494 ли 14,000.Длина продвижения - L = 18мм |
Карта 40, поз. 1к |
2*0,043 |
5 |
Установить в корпус шарик поз.21, или 22 образование фаски 0,3мм, Демонтировать шарик |
Диаметр шарика 19,844 мм или 19,447мм |
Карта40, поз. 1в |
2*0,043 |
6 |
Установить последовательно в сборку детали поз.21 или 22, поз.9, поз.2, в сборе согласно чертежу |
Диаметр шарика 19,844 мм или 19,447мм |
Карта40, поз. 1в |
3*0,043 |
7 |
Маркировать сборку |
Ударное клеймо с подбором, высота знаков-5мм, число знаков-12 |
Карта 26, поз. 3к |
0,48 |
8 |
КоНтроль БТК |
Масса изделия 1,33кг |
Карта 26, поз. 3к |
0,27 |
Суммарное время - 1,189 мин |
Время на организационно-техническое обслуживание рабочего места:
- подналадка механизированного инструмента и приспособлений в процессе работы
- смена инструмента
- инструктаж рабочего мастером
|
Место работы - сборочный стол |
Карта 1, поз. 2 |
4%
|
Время на отдых и личные надобности |
Карта 4 |
4%+2%
|
Поправочный коэффициент к оперативному времени в зависимости от типа производства |
Тип производства - среднесерийное |
Карта 5 |
1,0 |
Поправочный коэффициент к оперативному времени в зависимости от условий выполнения работы |
Положение сборки - сбоку |
Карта 8, поз. 1 |
1,0 |
Норма времени на сборочной операции для среднесерийного производства определяется по формуле:
,
где
Топ - оперативное время, мин;
Тобс - время на организационно-техническое обслуживание рабочего места, %;
Тотд - время на отдых и личные потребности, %;
К - коэффициент, учитывающий тип производства;
Кз - коэффициент, учитывающий условия сборки.
Для общей сборки гидрозамка норма времени:
=1,308 мин.
Найдем расчетное количество сборочных стендов
, шт.
=0,06 шт.
Округляем в большую сторону СР
=1. Коэффициент загрузки стенда будет равен 0,06.
Технологический процесс изготовления детали
Материал детали позволяет применять высокопроизводительные методы обработки.
Наличие радиусов закругления повышает стойкость инструмента. Целесообразная простановка размеров от оси детали до торцев бобышек, что облегчет наладку станка и сокращает трудоемкость обработки. Введение постоянных технологических баз позволяет повысить точность и сократить трудоемкость обработки ступенчатых соосных поверхностей.
Точность размеров, формы и относительного расположения поверхностей, а также их шероховатость соответствуют требованиям, предъявленным к детали. Эта точность достигается небольшим количеством последовательных операций с применением в основном стандартного инструмента и универсального оборудования.
Нетехнологичным элементом в конструкции корпуса является расположение отверстий перпендикулярно осями друг другу и выполненые в противоположном друг другу направлении, в остальном, деталь можно считать технологичной.
Выбор заготовок и методов их изготовления
При выборе вида заготовки и методов её изготовления рассматриваются два альтернативных варианта. В первом случае заготовкой является штампованная поковка в открытых штампах на кривошипном горячештамповочном прессе, во втором случае - поковка, получаемая на молоте с подкладными штампами.
Для последующих расчётов необходимо знать массу детали. Масса детали по чертежу , кг.
Используя рекомендации [4, с. 134…168] в качестве двух альтернативных вариантов заготовок принимаем горячую объёмную штамповку в открытых (заводской вариант) и закрытых штампах. Проектируем заготовку и рассчитываем технологическую себестоимость детали для обоих случаев.
Штамповка в открытых штампах
По заводскому варианту масса заготовки для штамповки 2,3 кг., масса штамповки 1,9 кг.
Штамповка в закрытых штампах (безоблойная)
Материал - Сталь 40Х ГОСТ 4543-71.
Оборудование - КГШП с выталкивателем.
Нагрев заготовок - индукционный.
Масса детали -0,81 кг.
Заготовку проектируем по ГОСТ 7505-89.
Группа стали, сложность поковки и масса - М2
По [2, П.1] принимаем степень точности Т2.
Степень сложности определяем в следующей последовательности:

-минимальная масса простой фигуры, в которую вписывается деталь.
-ориентировочная масса заготовки
-коэффициэнт учитывающий форму и вид детали [2,ст31,п.2.3,тб20]

Коэффициэнт сложности=
Учитывая коэффициэнт сложности принимаем степень сложности С2 [2,ст30]
Исходный индекс - 7.
Конфигурация поверхности разъёма штампа - плоская.
Заготовку выполняем в виде вала с тремя цилиндрическими бобышками, оси бобышек перпендикулярены <<валу>>. Две с одной стороны одна с другой стороны. Назначаем в местах сопряжения бобышек с <<валом>> радиусы скругления 10 мм с целью облегчения заполнения штампа металлом и уменьшения напряжения в металле. В качестве баз выбираем осевую линию <<вала>> и его торец (ближайший к бобышке).
Находим основные припуски на размеры поковки.
Находим основные припуски на размеры поковки по [2,ст10,тб13]:
2´1,0-длина 140 мм с чистотой поверхн. Rа12,5;
2´0,9- длина 40 мм с чистотой поверхн. 12,5;
Находим дополнительные припуски.
Смещение по поверхности разъёма штампов - Т = 0,1 мм [2.ст14,тб4].
Допуск величины смещения поверхности разъёма: Т = 0,3 мм [2,ст20,тб9].
Радиусы закруглений:
При глубине полости ручья до 25мм -2мм.
В местах сопряжения диаметров 38мм и 30мм принимаем -10мм.
Величина остаточного заусенца = 0,4мм,
Допуски на радиусы:
R2
R5
Рассчитываем размеры поковки, округляя их до 0,1 мм, и назначаем допуски.
140+2×(1,0+0,1+0,3) = 142,8; принимаем 
40+2(0,9+0,1+0,3) = 42,6; принимаем 
Штамповочные уклоны -5 град.
Допуски на штамповочные уклоны -0,25 от номинальной величины.
Массу поковки определяем объёмным прочерчиванием:
кг

Выбор варианта производства заготовок
Выбор варианта производства заготовок производим по технологической себестоимости заготовок:
, руб
где - масса заготовки штамповки при открытой штамповке, кг;
GД
- масса детали, кг;
КИМ
- коэффициент использования материала с учётом заусенца при открытой штамповке;
КИМ1
- коэффициент использования материала без учёта заусенца при закрытой штамповке;
СЗАГ
- удельная стоимость материала заготовки, руб/кг;
СС
- средняя по машиностроению стоимость срезания одного килограмма стружки при механической обработке, руб/кг.
СЗАГ
= 315 руб/кг в ценах 1991 г. [2], СЗАГ
= 10,5 руб/кг, отсюда коэффициэнт инфляции равен 33,(333)
В ценах 1991 г средняя по машиностроению стоимость срезания одного килограмма стружки при механической обработке составляет 0,495 руб/кг, с учётом инфляции получаем:
СС
= 14,5 руб/кг
При открытой штамповке:
руб/шт
При закрытой штамповке:
руб/шт
Экономический эффект:
Эт
=(39,96-34,06)×9600 = 56640 руб/год
В качестве заготовки выбираем штампованную поковку, получаемую в закрытых штампах на КГШП.
Выбор баз
005. Токарная с ЧПУ
Базирование осуществляется по двум цилиндрической поверхности в самоцентрирующемся двухкулачковом патроне, на кулачки установлены призмы, и по плоскости торца в упор.
Так как размер 141,4 (143,06 -с учётом штамповочных уклонов) получается при настройке станка, то погрешность базирования в данном случае равна нулю – εб
= 0.
Погрешность базирования для остальных размеров – εб
= ±0.5, что не превышает допуск на эти размеры.
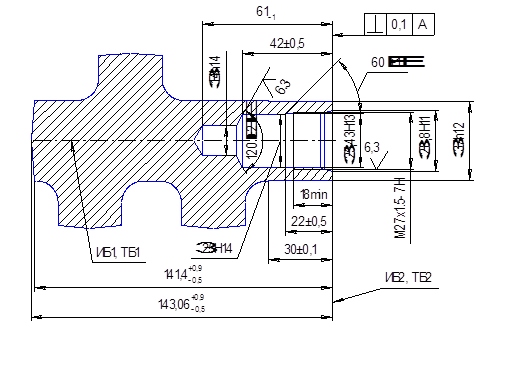
Рис.1. Токарная с ЧПУ
Базирование осуществляется при помощи трёхкулачкового самоцентрирующего патрона
Так как размер 140,4±0,5 получается при настройке станка, то погрешность базирования в данном случае равна нулю – εб
= 0.
Погрешность базирования для остальных размеров – εб
= ±0.5, что не превышает допуск на эти размеры.
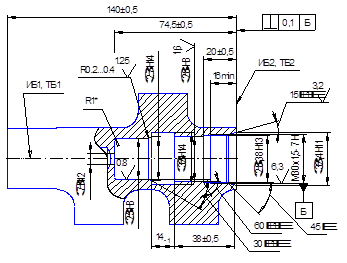
Рис.2 Фрезерно-сверлильная
Базирование корпуса осуществляется по цилиндрической и конической поверхностям в трёх кулачковом патроне и вращающемся центре для обработки полых деталей.
Погрешность базирования для размеров измеряемых вдоль осей обрабатываемых отверстий – εб
=0.
Погрешность базирования для размеров определяющих расположение осей отверстий относительно торца корпуса – εб
= ±0.5, что не превышает допуск на эти размеры.

Рис.3
Таблица 7
Операция |
Наименование и содержание операции |
Оборудование |
005 |
Токарная с ЧПУ
А- Установить и снять деталь
- Подрезать торец Æ38мм в размер 143,06 ; точить поверхн. Æ37-0,25
, l=30±0,1
- Центровать отв. Æ9*мм, глубиной 4,5±1,5мм
- Cверлить отв. Æ14Н14, l=61-1 мм, сверлить конус 120
0
±20
; сверлить отв.Æ25Н14, l=42±0,5; сверлить конус600
±10
; сверлить отв. Æ25,43Н13, l=22±0,5. Одновременно.
- Точить конус под углом 450
; точить фаску Æ32,4Н11 с улом 150
±10
.
- Нарезать резьбу М27х1,5-7Н, в размер l=18min
|
Токарный полуавтомат с ЧПУ СТП -220 АП |
010 |
Токарная с ЧПУ
А- Установить и снять деталь
- Подрезать торец Æ38 в размер 140±0,5
- Центровать отв. Æ9*мм, глубиной 4,5±1,5мм
- Сверлить отв. Æ18Н13, l=70±0,5мм
- Рассверлить отв. Æ22Н12, l=70±0,5мм; рассверлить отв. Æ25Н12, l=50±0,5мм; рассверлить отв. Æ28,38Н12, l=20±0,5мм. Одновременно
- Зенкеровать отв. Æ24Н10, l=23,5±0,5мм; зенкеровать конус Æ27Н14, под углом 300
±10
, зенкеровать отв. Æ27,2Н10, l=20±0,5мм. Одновременно.
- Расточить отв. Æ32,4Н14, l=14-1
- Точить фаску Æ32,4Н11, с углом 150
±10
, точить конус под углом 450
.
- Сверлить отв. Æ7Н12, l=2,5±0,5мм
- Развернуть отв. Æ24,6Н9, l=23,5±0,5мм, развернуть отв. Æ27,6Н9, l=34±0,5мм. Одновременно.
- Развернуть отв. Æ25Н8, l=23,5±0,5мм, развернуть отв. Æ28Н8, l=20±0,5мм. Одновременно.
- Точить торец Æ23мм в размер l=74,5±0,5мм, точить радиус R1max.
- Нарезать резьбу М30х1,5-7Н, в размер l=16min
|
Токарный полуавтомат с ЧПУ СТП -220 АП |
015 |
Вертикально-фрезерная с ЧПУ
А- Установить и снять деталь
Позиция I
-Фрезеровать поверхн. Æ30мм в размер 40±0,5.
-Центровать отв. Æ9*мм, глубиной 4,5±1,5мм.
-Сверлить отв. Æ12Н14, l=24мм, сверлить конус Æ17,9мм с углом 1200
*; сверлить отв. Æ17,9Н14, l=20±0,5мм. Одновременно.
-Зенковать конус под углом 450
; зенковать фаску Æ21,8Н11, l=3+0,4
, под углом 150
±10
. Одновременно.
-Фрезеровать резьбу М20х1,5-7Н, в размер l=15,5min
Б- Повернуть деталь
Позиция II
Выполнение переходов выполненых в позиции I
Позиция III
-Фрезеровать поверхн. Æ30мм в размер 40±0,5.
-Центровать отв. Æ9*мм, глубиной 4,5±1,5мм.
-Сверлить отв. Æ17,9Н14, l=26±0,5мм.
-Зенковать конус под углом 450
; зенковать фаску Æ21,8Н11, l=3+0,4
, под углом 150
±10
. Одновременно.
-Фрезеровать резьбу М20х1,5-7Н, в размер l=15,5min
|
Вертикально-фрезерный станок ГФ-2171 С5 |
020 |
Слесарная
-Снять заусенцы и притупить острые кромки в соответствии счертежом и СТП предприятия, протереть.
-Маркировать обозначение детали на бирке.
|
Участок слесарный |
025
|
Контроль
-Проверить размеры и требования по чертежу и ТП.
-Оформить прёмку деталей.
|
Контрольная плита |
Выбор средств технологического оснащения
Оборудование
005, 010. Токарная с ЧПУ. Модель СТП220АП.
Наибольший диаметр изделия, устанавливаемого над станиной - 400 мм.
Наибольший диаметр обрабатываемого изделия:
- над станиной - 250 мм;
- над суппортом - 220 мм.
Наибольшая длина обрабатываемого изделия:
- наружное точение - 350 мм;
- растачивание - 170 мм.
Наибольший рабочий ход суппорта:
- в продольном направлении - 430 мм;
- в поперечном направлении - 200 мм.
Бесступенчатое регулирование частоты вращения шпинделя.
Пределы частот вращения шпинделя - 11…2800 об/мин.
Наибольший крутящий момент на шпинделе - 150 кгс´м.
Пределы рабочих подач суппорта - 0…4000 мм/мин.
Максимальный шаг нарезаемой резьбы - 20 мм.
Класс точности нарезаемой резьбы - 6H, 6g.
Количество инструментов, устанавливаемых в револьверную головку - 12.
Габаритные размеры:
- длина - 4570 мм;
Мощность электропривода главного движения - 22 кВт.
015. Вертикально-фрезерный станок. Модель ГФ 2171С5
- Интерполятор 2С42-65
- Размеры рабочей поверхности стола (длина´ширина), мм 1600´400
- Наибольшее перемещение стола, мм продольное Х, 1000попнрнчное Y, 400
вертикальное Z250
- Наибольшее перемещение ползуна, ммкоордината Z 260
- Расстояние от торца шпинделя до рабочей поверхности
стола, мм 250…500
Расстояние от оси шпинделя
- До вертикальных направляющих станины, мм 500
- Колличество Т-образных пазов, шт 3
- Расстояние между Т-образными пазами, мм 100
- Ширина Т-образных пазов, ммцентрального18Н8
крайних18Н12
- Размер конуса шпинделя с конусностью 7/2450
- Наибольшая масса обрабатываемой детали и приспособления
устанавливаемых на столе станка, кг, не более400
- Предельные размеры обрабатываемых
поверхностей (длина´ширина´высота), мм 250´850´380
- Ёмкость магазина инструментов, шт12
- Время смены инструментов, с не более20
- Максимальный диаметр инструмента, ммторцевой фрезы 125
концевой фрезы 40
сверла30
- Максимальный вес инструмента, кг не более15
- Вылет инструмента от торца шпинделя, мм не более250
- Колличество частот вращения шпинделя18
- Пределы частот вращения шпинделя, об/мин40-2000
- S: 40, 50, 63, 80, 100, 125, 160, 200, 250, 315, 400, 500, 630, 800, 1000, 1250,1600, 2000
- Пределы подач стола, ползуна,, мм/мин3-6000
- Скорость быстрого перемещения стола по координатам
X, Y, и ползуна по координате Z, мм/мин6000
- Мощность электродвигателя главного движения, кВт7,5
- Наибольший крутящий момент на шпинделе, кН·м0,615
- Допустимое усилие подачи, Н
координата X, Y15690
координата Z9806
- Тип устройства ЧПУ - контурно-позиционный
- Колличество управляемых координат3
- Колличество одновременно управляемых координат
при линейной интерполяции3
при круговой интерполяции2
- Масса - 4700 кг.
Приспособления и инструменты
005. Токарная с ЧПУ
Резец 002-3862 - Т5К10 ГОСТ 18884-73
Сверло центровочное- Сверло 10 СТП 406-1234-76.
Сверло комбинированное трёхступенчатое специальное.
Резец расточной j=930
К.01.4983.000-06 ТУ2-035-1040-86
Резец резьбовой j=600
с треугольной пластиной К.01.4957.000-00 ТУ2-035-1040-86
Патрон специальный;
Шаблон 5+0,4
106-6757, шаблон Æ32,4+0,4
103-740.
Калибр на собираемость150-2629
Штанген нутромер 101-984
ШЦ-250-0,1 ГОСТ 166-80
Очки О ГОСТ 12.4.013-85
Тара 505-190
010. Токарная с ЧПУ
Резец 002-3862 - Т5К10 ГОСТ 18884-73
Сверло центровочное- Сверло 10 СТП 406-1234-76.
Сверло Æ18 ГОСТ 10903-77.
Сверло комбинированное трёхступенчатое специальное.
Зенкер комбинированный двухступенчатый.
Резец канавочный 5мм К.01.4963.000-00 ТУ2-035-1040-86.
Резец расточной j=930
К.01.4983.000-06 ТУ2-035-1040-86.
Резец расточной S 20S-XTFPR/L 11, пластина 1103.
Развёртка комбинированная специальная 037-717.
Развёртка комбинированная специальная 037-718.
Резец резьбовой SANDVIKCTGPR-1212-11, пластиной TPUN.
Патрон 7108-0023 ГОСТ 12595-72;
Шаблон 4+0,4
106-6757, шаблон Æ32,4+0,4
103-740.
Калибр на собираемость250-2629
Штанген нутромер 101-984
ШЦ-250-0,1 ГОСТ 166-80
Очки О ГОСТ 12.4.013-85
Тара 505-190
015. Фрезерная с ЧПУ.
Фреза 2214-0192 Т5К10 ГОСТ 22085-76 (торцовая насадная с механическим креплением круглых твёрдосплавных пластин).
Сверло центровочное- Сверло 10 СТП 406-1234-76.
Сверло комбинированное трёхступенчатое специальное.
Зенковка 023-806
Гребенчатая резьбовая фреза 2672-0577-7Н ГОСТ 1336-77
Шаблон 3+0,4
106-6737, шаблон Æ21,8Н11103-720.
Специальное приспособление с базированием корпуса в трёхкулачковом патроне жёстком заднем центре.
Калибр на собираемость 350-2629
Штанген нутромер 101-984
Очки О ГОСТ 12.4.013-85
Тара 505-190
Кран-укосина - 0,5 т
Расчёт припусков
Расчёт припусков производим аналитическим методом.
Расчёт припусков на механическую обработку поверхности Æ28Н8
Выбираем следующие технологические переходы:
- сверление чернвое
- рассверливание
- зенкерование
- развёртывание черновое
- развёртывание чистовое
Штамповка
Шероховатость поверхности - Rz = 160 мкм
Глубина дефектного слоя - h = 200 мкм
Суммарные отклонения формы и расположения поверхностей - ΔΣ
= мкм
Где - Dåк
=Dк
×lк
Где - Dк
=0,20 мкм/мм[14]
lк
= 38 мм
Dåк
=0,20×38=8 мкм
Dy
=0,25×T=0,25×840=210 мкм
ΔΣ
= =213 мкм
Сверление предварительное
Выполняем по 13-му квалитету.
Шероховатость поверхности - Rz = 32 мкм
Глубина дефектного слоя - h = 40 мкм
Суммарные отклонения формы и расположения поверхностей - ΔΣ
= мкм
Где - Dу
=0,7 мкм -увод сверла на 1 мм длины отверстия[14, с. 190, тб28]
Где - С0
=25 мкм[14, с. 190, тб28]
ΔΣ
= =27 мкм
Рассверливание
Выполняем в соответствии с таблицами точности [14] по 12-му квалитету.
Шероховатость поверхности - Rz = 32 мкм
Глубина дефектного слоя - h = 40 мкм
Суммарные отклонения формы и расположения поверхностей - ΔΣ
= мкм
Где - Dу
=0,7 мкм - увод сверла на 1 мм длины отверстия[14, с. 190, тб28]
Где - С0
=25 мкм[14, с. 190, тб28]
ΔΣ
= =27 мкм
Зенкерование черновое
Выполняем в соответствии с таблицами точности [14] по 10-му квалитету.
Шероховатость поверхности - Rz = 40 мкм
Глубина дефектного слоя - h = 40 мкм
Развёртывание черновное
Выполняем в соответствии с таблицами точности [14] по 9-му квалитету.
Шероховатость поверхности - Rz = 40 мкм
Глубина дефектного слоя - h = 50 мкм
Развёртывание чистовое
Выполняем в соответствии с таблицами точности [14] по 8-му квалитету.
Шероховатость поверхности - Rz = 2,5 мкм
Глубина дефектного слоя - h = 20 мкм
Результаты приведены в таблице 8.
Таблица 8
Технологический переход обработки поверхности |
Элементы припуска, мкм |
Расчётный размер, мм |
Допуск TD, мм |
Предельные размеры, мм |
Предельные значения припусков, мкм |
min |
max |
2Zmin
|
2Zmax
|
Rz |
h |
ΔΣ
|
ε |
Заготовка |
160 |
200 |
213 |
- |
28,945 |
0,84 |
28,94 |
31,07 |
- |
- |
Сверление IT13 |
32 |
40 |
27 |
0 |
28,658 |
0,33 |
28,66 |
30,23 |
287 |
797 |
РассверливаниIT12 |
32 |
40 |
27 |
0 |
28,46 |
0,21 |
28,46 |
29,9 |
198 |
318 |
Зенкерование предварительное IT10 |
2,5 |
20 |
0 |
0 |
28,3 |
0,084 |
28,3 |
29,69 |
160 |
286 |
Развёртывание черновое IT9 |
0,63 |
5 |
0 |
0 |
28,12 |
0,052 |
28,12 |
28,85 |
180 |
212 |
Развёртывание чистовое IT9 |
0,32 |
0 |
0 |
0 |
28 |
0,033 |
28 |
28,33 |
120 |
139 |
Общие припуски 2ZО
min
= 945 мкм, 2ZО
max
= 1752 мкм
Проверка расчёта припусков:

мкм
мкм
005. Токарная с ЧПУ
Переход I: Подрезать торец Æ38мм в размер 143,06 ; точить поверхн. Æ37-0,25
, l=30±0,1
Расчёт режимов производим аналитическим методом.
Пластина Т5К10, φ = φ1
=450
.
1. Глубина резания t=1,4мм.
2. Подачу выбираем по [14, с. 268, табл. 14].
S = 0,66 мм/об, r=0,8мм.
3. Скорость резания
, м/мин,
где
T=60 мин - период стойкости материала пластины;
CV
, x, y, m - коэффициент и показатели степени;
CV
=350; x=0,15; y=0,35; m=0,2 [29,табл.17, c.269];

[29,с.261, табл.17];
Кг
=0,95, nv
=0.9 [29,с.262, табл.2];

[29,с.263, табл.5]; [29,с.271, табл.18];
KV
=1,0186×0,8×0,87×0,94=0,6614;
112,23 м/мин.
145,222 м/мин -подольное точение
4. Частота вращения шпинделя
941 об/мин
1218 об/мин -родольное точение
5. Силу резания найдем по формуле [29, с. 271]:
, Н,
где
CP
, x, y, n - коэффициент и показатели степени,
CP
=300, x=1, y=0,75, n=-0.15 [14,табл 2,ст273]
КP
=Кмр
×Кjр
×Кgр
×Кlр
×Кrр
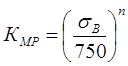
n=0,75
Кjр
=1,0; Кgр
=1,1; Кlр
=1,0; Кrр
=0,93
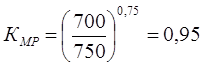
КP
=0,95×1,0×1,1×0,93=0,971
, Н
6. Мощность резания определяем по формуле [29, с. 271]:
, кВт,
кВт
7. Проверка на достаточность привода станка:
,
где
Nшп
- мощность привода станка;
Nшп
=Nст
×h, Nст
=22 кВт, h=0,8 - КПД привода;
Nшп
=22×0,8=17,6 кВт.
0,384<17,6 кВт.
Условие выполняется.
8. Основное время.
, мин,
где
i=1 - число проходов.
l1
=38 мм
L1
=l1
+lвр
+lпер
=38+5=43 мм,
L2
=30 мм
L2
=l2
+lвр
+lпер
=30+5=35 мм,
мин
Переход II:Центровать отв. Æ9мм, l=4,5мм
Сверло центровочное Р6М5, 2φ=900
.
1. Скорость резания
[14, с. 278, табл. 28];
где Т=25 – стойкость сверла, мин [14, с. 279, табл. 30];
CV
, m, x, y– определяются по [14, с. 278, табл. 28];
CV
= 7,0
m = 0,2
y = 0,7
q = 0,4
S=0,15мм/об[14, с. 277, табл. 25];

К1
V
=1.0[14, с. 263, табл. 6];
КИ
V
=1.0[14, с. 280, табл. 30];
KV
=1.01086×1,0×1,0=1,01086
=33,7775 м/мин
2. Частота вращения шпинделя
1195 об/мин
3. Крутящий момент по формуле [14, с. 277]:
, Н×м,
где
СМ
, q, x, y - коэффициент и показатели степени,
СМ
=0,0345, q=2,0, x=-, y=0,8 [14, табл. 32, с. 281];
КР
= [14, табл. 9, с. 264];
Н×м.
4. Осевую силу определяем по формуле [14, с. 281, табл. 32]:
, Н,
где
СР
, x, y, q - коэффициент и показатели степени,
СР
=68, x=-, y=0,7, q=1,0 [14, табл. 32, с. 281];
КР
= [14, табл. 9, с. 264];
Н,
5. Мощность резания определяем по формуле [29, с. 280]:
, кВт,
кВт.
6. Проверка на достаточность привода станка:
,
где
Nшп
- мощность привода станка;
Nшп
=Nст
×h, Nст
=7,5 кВт, h=0,8 - КПД привода;
Nшп
=22×0,8=17,6 кВт.
0,76<17,6.
Условие выполняется.
7. Основное время
ТО
= ,
l=4,5 мм, lпер
=5 мм, i=1.
ТО
= =0,053 мин.
Переход III: Сверлить отв. Æ14Н14, l=61-1 мм, сверлить конус 120
0
±20
; сверлить отв.Æ25Н14, l=42±0,5; сверлить конус600
±10
; сверлить отв. Æ25,43Н13, l=22±0,5. Одновременно.
Сверление (расчёт мощности, силы резания по наибольшему диаметру)
1. Скорость резания
[14, с. 276];
где Т=50 – стойкость сверла, мин [14, с. 279, табл. 30];
CV
, m, x, y– определяются по [14, с. 278, табл. 28];
CV
= 9,8
m = 0,2
y = 0,5
q = 0,4
S=0,33мм/об[14, с. 277, табл. 25];

К1
V
=1.0[14, с. 263, табл. 6];
КИ
V
=1.0[14, с. 280, табл. 30];
KV
=1.01086×1,0×1,0=1,01086
=35,531 м/мин
2. Частота вращения шпинделя
450об/мин
3. Крутящий момент по формуле [14, с. 277]:
, Н×м,
где
СМ
, q, x, y - коэффициент и показатели степени,
СМ
=0,0345, q=2,0, x=-, y=0,8 [14, табл. 32, с. 281];
КР
= [14, табл. 9, с. 264];
Н×м.
4. Осевую силу определяем по формуле [14, с. 281, табл. 32]:
, Н,
где
СР
, x, y - коэффициент и показатели степени,
СР
=68, x=-, y=0,7, q=1.0 [14, табл. 32, с. 281];
КР
= [14, табл. 9, с. 264];
Н,
5. Мощность резания определяем по формуле [29, с. 280]:
, кВт,
кВт.
6. Проверка на достаточность привода станка:
,
где
Nрез общ
=4,29+0,153=4,443 кВт
Nшп
- мощность привода станка;
Nшп
=Nст
×h, Nст
=7,5 кВт, h=0,8 - КПД привода;
Nшп
=22×0,8=17,6 кВт.
3,167<17,6.
Условие выполняется.
7. Основное время
ТО
= ,
Разбиваем рабочий ход на три прохода по 20, 40, 61 мм
l=121 мм, lвр
=5 мм, i=1.
ТО
= =0,85 мин
Переход IV: Сверлить отв. Æ7Н12, l=2,5±0,5мм
1. Скорость резания
[14, с. 276];
где Т=25 – стойкость сверла, мин [14, с. 279, табл. 30];
CV
, m, x, y– определяются по [14, с. 278, табл. 28];
CV
= 7,0
m = 0,2
y = 0,7
q = 0,4
S=0,11мм/об[14, с. 277, табл. 25];

К1
V
=1.0[14, с. 263, табл. 6];
КИ
V
=1.0[14, с. 280, табл. 30];
KV
=1.01086×1,0×1,0=1,01086
=37,95 м/мин
2. Частота вращения шпинделя
1726 об/мин
3. Крутящий момент по формуле [14, с. 277]:
, Н×м,
где
СМ
, q, x, y - коэффициент и показатели степени,
СМ
=0,0345, q=2,0, x=-, y=0,8 [14, табл. 32, с. 281];
Н×м.
4. Осевую силу определяем по формуле [14, с. 281, табл. 32]:
, Н,
где
СР
, x, y, q - коэффициент и показатели степени,
СР
=68, x=-, y=0,7, q=1.0 [14, табл. 32, с. 281];
КР
= [14, табл. 9, с. 264];
Н,
5. Мощность резания определяем по формуле [29, с. 280]:
, кВт,
кВт.
6. Проверка на достаточность привода станка:
,
где
Nшп
- мощность привода станка;
Nшп
=Nст
×h, Nст
=22 кВт, h=0,8 - КПД привода;
Nшп
=22×0,8=17,6 кВт.
0,52<17,6.
Условие выполняется.
7. Основное время
ТО
= ,
l=2,5 мм, lвр
=2,5 мм, i=1.
ТО
= =0,026 мин
Переход V: Точить конус под углом 450
; точить фаску Æ32,4Н11 с улом 150
±10
. Расчёт режимов производим аналитическим методом.
Пластина Т15К6, φ = 930
, φ1
=300
.
1. Глубина резания t=2,01мм.
2. Подачу выбираем по [14, с. 268, табл. 14].
S = 0,25×0,45=0,1125 мм/об, r=0,4мм.
3. Скорость резания
, м/мин,
где
CV
=420; x=0,15; y=0,2; m=0,2 [29,табл.17, c.269];

[29,с.263, табл.5]; [29,с.271, табл.18];
KV
=1,0186×1,0×0,87×0,91×0,94=0,75228;
194,217 м/мин.
4. Частота вращения шпинделя
1909 об/мин
5. Силу резания найдем по формуле [29, с. 271]:
, Н,
где
CP
, x, y, n - коэффициент и показатели степени,
CP
=300, x=1, y=0,75, n=-0.15 [14,табл 2,ст273]
КP
=Кмр
×Кjр
×Кgр
×Кlр
×Кrр
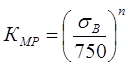
n=0,75
Кjр
=1,0; Кgр
=1,1; Кlр
=1,0; Кrр
=0,93
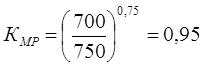
КP
=0,95×1,0×1,1×0,93=0,971
, Н
6. Мощность резания определяем по формуле [29, с. 271]:
, кВт,
кВт
7. Проверка на достаточность привода станка:
,
где
Nшп
- мощность привода станка;
Nшп
=Nст
×h, Nст
=22 кВт, h=0,8 - КПД привода;
Nшп
=22×0,8=17,6 кВт.
2,92<17,6 кВт.
Условие выполняется.
8. Основное время.
, мин,
где
i=1 - число проходов.
l=6 мм
L=l+lвр
+lпер
=6+5=11 мм,
мин
Переход VI: Нарезать резьбу М27х1,5-7Н, в размер l=18min
1. Скорость резания
[14, с. 295];
где: CV
, m, x, y – определяются по [14, с. 296, табл. 49];
KV
- общий поправочный коэффициент на скорость резания.
Т = 70 мин
CV
= 332
m = 0,2
x = 0,23
y = 0,3
[14, с. 297];
КТГ
=1,0[14, с. 298, тб50];

м/мин
2. Частота вращения шпинделя
1446 об/мин
3. . Силу резания найдем по формуле [29, с. 297]:
, Н
где
CP
, x, y, n - коэффициент и показатели степени,
CP
=148, y=1,7, n=0.71 [14,табл 2,ст273]
КP
=Кмр
×Кjр
×Кgр
×Кlр
×Кrр
Кjр
=0,94; Кgр
=1,1; Кlр
=1,0; Кrр
=0,87
КP
=0,95×0,94×1,1×1,0=0,9823
811,66, Н
4. Мощность резания определяем по формуле [29, с. 271]:
, кВт,
кВт
5. Проверка на достаточность привода станка:
,
где
Nшп
- мощность привода станка;
Nшп
=Nст
×h, Nст
=22 кВт, h=0,8 - КПД привода;
Nшп
=22×0,8=17,6 кВт.
1,626<17,6 кВт.
Условие выполняется.
6. Основное время.
, мин,
где
i=1 - число проходов.
l=18 мм
lвр
+lпер
=5мм
L=l+lвр
+lпер
=18+5=23 мм,
мин
Основное время операции
Т0общ
=0,114+0,053+0,85+0,023+0,026+0,066=1,132 мин
010 Токарная с ЧПУ
Переход I: Подрезать торец Æ38 в размер 140±0,5
Расчёт режимов производим аналитическим методом.
Пластина Т5К10, φ = φ1
=450
.
1. Глубина резания t=1,4мм.
2. Подачу выбираем по [14, с. 268, табл. 14].
S = 0,66 мм/об, r=0,8мм.
3. Скорость резания
, м/мин,
где
T=60 мин - период стойкости материала пластины;
CV
, x, y, m - коэффициент и показатели степени;
CV
=350; x=0,15; y=0,35; m=0,2 [29,табл.17, c.269];

[29,с.261, табл.17];
Кг
=0,95, nv
=0.9 [29,с.262, табл.2];

[29,с.263, табл.5]; [29,с.271, табл.18];
KV
=1,0186×0,8×0,87×0,94=0,6614;
112,23 м/мин.
4. Частота вращения шпинделя
941 об/мин
5. Силу резания найдем по формуле [29, с. 271]:
, Н,
где
CP
, x, y, n - коэффициент и показатели степени,
CP
=300, x=1, y=0,75, n=-0.15 [14,табл 2,ст273]
КP
=Кмр
×Кjр
×Кgр
×Кlр
×Кrр
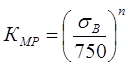
n=0,75
Кjр
=1,0; Кgр
=1,1; Кlр
=1,0; Кrр
=0,93
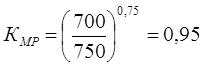
КP
=0,95×1,0×1,1×0,93=0,971
, Н
6. Мощность резания определяем по формуле [29, с. 271]:
, кВт,
кВт
7. Проверка на достаточность привода станка:
,
где
Nшп
- мощность привода станка;
Nшп
=Nст
×h, Nст
=22 кВт, h=0,8 - КПД привода;
Nшп
=22×0,8=17,6 кВт.
0,384<17,6 кВт.
Условие выполняется.
8. Основное время.
, мин,
где
i=1 - число проходов.
l=38 мм
L=l+lвр
+lпер
=38+5=43 мм,
мин
Переход II 010 операции аналогичен переходу II 005 операци
Переход III: Сверлить отв. Æ18Н13, l=70±0,5мм
1. Скорость резания
[14, с. 276];
где Т=45 – стойкость сверла, мин [14, с. 279, табл. 30];
CV
, m, x, y– определяются по [14, с. 278, табл. 28];
CV
= 9,8
m = 0,2
y = 0,5
q = 0,4
S=0,33мм/об[14, с. 277, табл. 25];

К1
V
=1.0[14, с. 263, табл. 6];
КИ
V
=1.0[14, с. 280, табл. 30];
KV
=1.01086×1,0×1,0=1,01086
=36,29 м/мин
2. Частота вращения шпинделя
642 об/мин
3. Крутящий момент по формуле [14, с. 277]:
, Н×м,
где
СМ
, q, x, y - коэффициент и показатели степени,
СМ
=0,0345, q=2,0, x=-, y=0,8 [14, табл. 32, с. 281];
КР
= [14, табл. 9, с. 264];
Н×м.
4. Осевую силу определяем по формуле [14, с. 281, табл. 32]:
, Н,
где
СР
, x, y, q - коэффициент и показатели степени,
СР
=68, x=-, y=0,7, q=1.0 [14, табл. 32, с. 281];
КР
= [14, табл. 9, с. 264];
Н,
5. Мощность резания определяем по формуле [29, с. 280]:
, кВт,
кВт.
6. Проверка на достаточность привода станка:
,
где
Nшп
- мощность привода станка;
Nшп
=Nст
×h, Nст
=22 кВт, h=0,8 - КПД привода;
Nшп
=22×0,8=17,6 кВт.
3,06<17,6.
Условие выполняется.
7. Основное время
ТО
= ,
Разбиваем переход на три прохода, 25, 50, 70
l=145 мм, lвр
=5 мм, i=1.
ТО
= =0,708 мин
Переход IV: Рассверлить отв. Æ22Н12, l=70±0,5мм; рассверлить отв. Æ25Н12, l=50±0,5мм; рассверлить отв. Æ28,43Н12, l=20±0,5мм. Одновременно
Сверление (расчёт мощности, силы резания по наибольшему диаметру)
1. Скорость резания
[14, с. 276];
где Т=50 – стойкость сверла, мин [14, с. 279, табл. 30];
CV
, m, x, y– определяются по [14, с. 279, табл. 29];
CV
= 16,2
m = 0,2
y = 0,5
q = 0,4
х=0,2
S=0,33мм/об[14, с. 277, табл. 25];

К1
V
=1.0[14, с. 263, табл. 6];
КИ
V
=1.0[14, с. 280, табл. 30];
KV
=1.01086×1,0×1,0=1,01086
=44,63 м/мин
2. Частота вращения шпинделя
500 об/мин
3. Крутящий момент по формуле [14, с. 277]:
, Н×м,
где
СМ
, q, x, y - коэффициент и показатели степени,
СМ
=0,09, q=1,0, x=0,9, y=0,8 [14, табл. 32, с. 281];
КР
= [14, табл. 9, с. 264];
Н×м.
4. Осевую силу определяем по формуле [14, с. 281, табл. 32]:
, Н,
где
СР
, x, y, q, х - коэффициент и показатели степени,
СР
=67, x=1,2, y=0,65, q=- [14, табл. 32, с. 281];
Н,
5. Мощность резания определяем по формуле [29, с. 280]:
, кВт,
кВт.
6. Проверка на достаточность привода станка:
,
где
Nшп
- мощность привода станка;
Nшп
=Nст
×h, Nст
=22 кВт, h=0,8 - КПД привода;
Nшп
=22×0,8=17,6 кВт.
2,4<17,6.
Условие выполняется.
7. Основное время
ТО
= ,
Разбиваем переход на три прохода, 25, 50, 70мм
l=145 мм, lвр
=5 мм, i=1.
ТО
= =0,91 мин
Переход V: Зенкеровать отв. Æ24Н10, l=23,5±0,5мм; зенкеровать конус Æ27Н14, под углом 300
±10
, зенкеровать отв. Æ27,2Н10, l=34±0,5мм. Одновременно.
1. Скорость резания
[14, с. 276];
где Т=50 – стойкость зенкера, мин [14, с. 279, табл. 30];
CV
, m, x, y– определяются по [14, с. 278, табл. 28];
CV
= 16,3
m = 0,2
y = 0,5
х=0,2
q = 0,3
S=0,8мм/об[14, с. 277, табл. 25];

К1
V
=1.0[14, с. 263, табл. 31];
КИ
V
=1.0[14, с. 280, табл. 6];
KV
=1.01086×1,0×1,0=1,01086
=16,724 м/мин
2. Частота вращения шпинделя
197 об/мин
3. Крутящий момент по формуле [14, с. 277]:
, Н×м,
где
СМ
, q, x, y - коэффициент и показатели степени,
СМ
=0,09, q=1,0, x=0,9, y=0,8 [14, табл. 32, с. 281];
Н×м.
4. Осевую силу определяем по формуле [14, с. 281, табл. 32]:
, Н,
где
СР
, x, y - коэффициент и показатели степени,
СР
=67, x=1.2, y=0,65 [14, табл. 32, с. 281];
КР
= [14, табл. 9, с. 264];
Н,
5. Мощность резания определяем по формуле [29, с. 280]:
, кВт,
кВт.
6. Проверка на достаточность привода станка:
,
где
Nшп
- мощность привода станка;
Nшп
=Nст
×h, Nст
=22 кВт, h=0,8 - КПД привода;
Nшп
=22×0,8=17,6 кВт.
1,62<17,6.
Условие выполняется.
7. Основное время
ТО
= ,
Разбиваем переход на три прохода, 25, 50, 73,5мм
l=148,5 мм, lвр
=5 мм, i=1.
ТО
= =0,974 мин
Переход VI: Расточить отв. Æ32,4Н14, l=14-1
.
Пластина Т5К10, φ = 900
, φ1
=00
.
Прорезание канавки шириной 5мм, глубиной 1,98мм
1. Подачу выбираем по [14, с. 268, табл. 14].
S = 0,47 мм/об, r=0,4мм.
2. Скорость резания
, м/мин, [14, с.268]
где
CV
=47; y=0,8; m=0,2 [14,табл.17, c.269];

[14,с.263, табл.5]; [14,с.271, табл.18];
KV
=1,0186×1,0×0,87×0,7×0,94=0,58;
21,94 м/мин.
3. Частота вращения шпинделя
215 об/мин
4. Силу резания найдем по формуле [29, с. 271]:
, Н,
где
CP
, x, y, n - коэффициент и показатели степени,
CP
=408, x=0,72, y=0,8, n=0 [14,табл 2,ст273]
КP
=Кмр
×Кjр
×Кgр
×Кlр
×Кrр
Кjр
=0,89; Кgр
=1,1; Кlр
=1,0; Кrр
=0,87
КP
=0,95×0,89×1,1×0,87=0,7356
, Н
5. Мощность резания определяем по формуле [29, с. 271]:
, кВт,
кВт
6. Проверка на достаточность привода станка:
,
где
Nшп
- мощность привода станка;
Nшп
=Nст
×h, Nст
=22 кВт, h=0,8 - КПД привода;
Nшп
=22×0,8=17,6 кВт.
0,222<17,6 кВт.
Условие выполняется.
Точение канавки
7. Скорость резания
, м/мин, [14, с.268]
где
CV
=350; x=0,15; y=0,35; m=0,2 [14,табл.17, c.269];

[14,с.263, табл.5]; [14,с.271, табл.18];
KV
=1,0186×1,0×0,87×0,7×0,94=0,58;
147,8 м/мин.
8. Частота вращения шпинделя
1452 об/мин
9. Силу резания найдем по формуле [29, с. 271]:
, Н,
где
CP
, x, y, n - коэффициент и показатели степени,
CP
=300, x=1,0, y=0,75, n=-0,15 [14,табл 2,ст273]
КP
=Кмр
×Кjр
×Кgр
×Кlр
×Кrр
Кjр
=0,89; Кgр
=1,1; Кlр
=1,0; Кrр
=0,87
КP
=0,95×0,89×1,1×0,87=0,7356
, Н
10. Мощность резания определяем по формуле [29, с. 271]:
, кВт,
кВт
11. Проверка на достаточность привода станка:
,
где
Nшп
- мощность привода станка;
Nшп
=Nст
×h, Nст
=22 кВт, h=0,8 - КПД привода;
Nшп
=22×0,8=17,6 кВт.
2,83<17,6 кВт.
Условие выполняется.
12. Основное время.
, мин,
где
i=1 - число проходов.
L1
=l1
+lвр
=1,98+2=3,98 мм,
L1
=l2
=9 мм
0,053 мин
Переход VII аналогичен переходу IV 005 операции с отличием по длине рабочего хода, поэтому считаем машинное время:
Основное время.
, мин,
где
i=1 - число проходов.
l=5 мм
L=l+lвр
+lпер
=5+5=10 мм,
мин
Переход VIII: Развернуть отв. Æ24,6Н9, l=23,5±0,5мм, развернуть отв. Æ27,6Н9, l=20±0,5мм. Одновременно.
1. Скорость резания
[14, с. 276];
где Т=80 – стойкость развёртки, мин [14, с. 280, табл. 30];
CV
, m, x, y– определяются по [14, с. 278, табл. 28];
CV
= 10,5
m = 0,4
y = 0,65
х=0,2
q = 0,3
S=1,2 мм/об[14, с. 278, табл. 27];

К1
V
=1.0[14, с. 263, табл. 31];
КИ
V
=1.0[14, с. 280, табл. 6];
KV
=1.01086×1,0×1,0=1,01086
=5,624 м/мин
2. Частота вращения шпинделя
64 об/мин
3. Крутящий момент по формуле [14, с. 277]:
, Н×м,
где
СР
, x, y - коэффициент и показатели степени,
СР
=200, x=1.0, y=0,75 [14, табл. 32, с. 281];
=31,9 Н×м
4. Мощность резания определяем по формуле [29, с. 280]:
, кВт,
кВт.
5. Проверка на достаточность привода станка:
,
где
Nшп
- мощность привода станка;
Nшп
=Nст
×h, Nст
=22 кВт, h=0,8 - КПД привода;
Nшп
=22×0,8=17,6 кВт.
0,21<17,6.
Условие выполняется.
6. Основное время
ТО
= ,
l=51,5 мм, lвр
=2 мм, i=1.
ТО
= =0,7 мин
Переход IX: Развернуть отв. Æ25Н8, l=23,5±0,5мм, развернуть отв. Æ28Н8, l=20±0,5мм. Одновременно
1. Скорость резания
[14, с. 276];
где Т=80 – стойкость развёртки, мин [14, с. 280, табл. 30];
CV
, m, x, y– определяются по [14, с. 278, табл. 28];
CV
= 10,5
m = 0,4
y = 0,65
х=0,2
q = 0,3
S=0,96 мм/об[14, с. 278, табл. 27];

К1
V
=1.0[14, с. 263, табл. 31];
КИ
V
=1.0[14, с. 280, табл. 6];
KV
=1.01086×1,0×1,0=1,01086
=6,2 м/мин
2. Частота вращения шпинделя
70 об/мин
3. Крутящий момент по формуле [14, с. 277]:
, Н×м,
где
СР
, x, y - коэффициент и показатели степени,
СР
=200, x=1.0, y=0,75 [14, табл. 32, с. 281];
=20,22 Н×м
4. Мощность резания определяем по формуле [29, с. 280]:
, кВт,
кВт.
5. Проверка на достаточность привода станка:
,
где
Nшп
- мощность привода станка;
Nшп
=Nст
×h, Nст
=22 кВт, h=0,8 - КПД привода;
Nшп
=22×0,8=17,6 кВт.
0,145<17,6.
Условие выполняется.
6. Основное время
ТО
= ,
l=51,5 мм, lвр
=2 мм, i=1.
ТО
= =0,8 мин
Переход X: Точить торец Æ23мм в размер l=74,5±0,5мм, трочить радиус R1max. Одновременно
Пластина Т15К6, φ = 900
, φ1
=50
.
1. Ширина резания t=1,0мм.
2. Подачу выбираем по [14, с. 268, табл. 14].
S = 0,66 мм/об, r=1,0мм.
3. Скорость резания
, м/мин,
где
T=60 мин - период стойкости материала пластины;
CV
, x, y, m - коэффициент и показатели степени;
CV
=350; x=0,15; y=0,35; m=0,2 [29,табл.17, c.269];

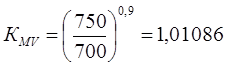
[29,с.263, табл.5]; [29,с.271, табл.18];
KV
=1,0186×1,0×1,0×0,7×1,0=0,707602;
113,824 м/мин.
4. Частота вращения шпинделя
1449 об/мин
5. Силу резания найдем по формуле [29, с. 271]:
, Н,
где
CP
, x, y, n - коэффициент и показатели степени,
CP
=300, x=1, y=0,75, n=-0.15 [14,табл 2,ст273]
КP
=Кмр
×Кjр
×Кgр
×Кlр
×Кrр
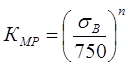
n=0,75
Кjр
=1,0; Кgр
=1,1; Кlр
=1,0; Кrр
=0,93
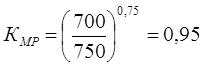
КP
=0,95×1,0×1,1×0,93=0,971
, Н
6. Мощность резания определяем по формуле [29, с. 271]:
, кВт,
кВт
7. Проверка на достаточность привода станка:
,
где
Nшп
- мощность привода станка;
Nшп
=Nст
×h, Nст
=22 кВт, h=0,8 - КПД привода;
Nшп
=22×0,8=17,6 кВт.
3,9<17,6 кВт.
Условие выполняется.
8. Основное время.
, мин,
где
i=1 - число проходов.
l=10 мм
L=l+lвр
+lпер
=10+5=43 мм,
мин
Переход XI: Нарезать резьбу М30х1,5-7Н, в размер l=16min
1. Скорость резания
[14, с. 295];
где: CV
, m, x, y – определяются по [14, с. 296, табл. 49];
KV
- общий поправочный коэффициент на скорость резания.
Т = 70 мин
CV
= 332
m = 0,2
x = 0,23
y = 0,3
[14, с. 297];
КТГ
=1,0[14, с. 298, тб50];

м/мин
2. Частота вращения шпинделя
1301 об/мин
3. Силу резания найдем по формуле [29, с. 297]:
, Н
где
CP
, x, y, n - коэффициент и показатели степени,
CP
=148, y=1,7, n=0.71 [14,табл 2,ст273]
КP
=Кмр
×Кjр
×Кgр
×Кlр
×Кrр
Кjр
=0,94; Кgр
=1,1; Кlр
=1,0; Кrр
=0,87
КP
=0,95×0,94×1,1×1,0=0,9823
811,66, Н
4. Мощность резания определяем по формуле [29, с. 271]:
, кВт,
кВт
5. Проверка на достаточность привода станка:
,
где
Nшп
- мощность привода станка;
Nшп
=Nст
×h, Nст
=22 кВт, h=0,8 - КПД привода;
Nшп
=22×0,8=17,6 кВт.
1,626<17,6 кВт.
Условие выполняется.
6. Основное время.
, мин,
где
i=6 - число проходов.
l=18 мм
lвр
+lпер
=5мм
L=l+lвр
+lпер
=16+5=21 мм,
мин
Основное время операции
Т0общ
=0,07+0,053+0,708+0,91+0,974+0,053+0,021+0,7+0,8+0,16+0,065=4,514 мин
015. Фрезерно-сверлильная с ЧПУ. Станок ГФ-2171С5
Позиция I
Переход I: Фрезеровать поверхн. Æ30мм в размер 40±0,5.
1. Скорость резания
, м/мин
где: CV
, m, x, y – определяются по [14, с. 296, табл. 49];
KV
- общий поправочный коэффициент на скорость резания.
Т = 120 мин [14, с. 290, табл. 40]
CV
= 332
m = 0,2
x = 0,1
y = 0,4
q=0,2
p=0
=0,15[14, с. 283, табл. 34]
t=4 мм- с учётом штамповочных уклонов


[14, ст263, тб5]
[14, ст263, тб6]

м/мин
2. Частота вращения фрезы:
, об/мин
где V - скорость резания, м/мин;
D - диаметр фрезы, мм.
об/мин
В соответствии с паспортом станка принимаем частоту вращения:
nст
= 400 об/мин
3. Определяем фактическую скорость резания:
, м/мин
м/мин
4. Находим минутную подачу:
, мм/мин
мм/мин
Так как регулирование подачи бесступенчатое, то оставляем минутную подачу без изменений.
5. Сила резания
, Н
где КМР
- поправочный коэффициент;
CР
, n, x, y, q, w - определяются по таблицам [14].
СР
= 825
n = 0,75
x = 1,0
y = 0,75
q = 1,3
w = 0,2
6. Сила резания:
Н
7. Мощность резания
, кВт
кВт
8. Проверка по мощности:
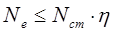
где Nст
= 7,5 кВт - мощность привода фрезерной головки;
h = 0,8 - КПД привода.

Условие выполняется
9. Расчёт основного времени
, мин
где L - длина рабочего хода, мм;
S - минутная подача, мм/мин.
L = l + l1
+ lдоп
, мм
где l = 30 мм длина торца, мм;
l1
+ lдоп
– длина врезания и перебега, мм.
Для симметричной установки фрезы по [11, прил. 4]:
l1
+ lдоп
= 15 мм
L = 30 +15 = 40 мм
мин
Переход II: Центровать отв. Æ9*мм, глубиной 4,5±1,5мм.
Сверло центровочное Р6М5, 2φ=900
.
1. Скорость резания
[14, с. 278, табл. 28];
где Т=25 – стойкость сверла, мин [14, с. 279, табл. 30];
CV
, m, x, y– определяются по [14, с. 278, табл. 28];
CV
= 7,0
m = 0,2
y = 0,7
q = 0,4
S=0,15мм/об[14, с. 277, табл. 25];

К1
V
=1.0[14, с. 263, табл. 6];
КИ
V
=1.0[14, с. 280, табл. 30];
KV
=1.01086×1,0×1,0=1,01086
=33,7775 м/мин
2. Частота вращения шпинделя
1195 об/мин,
принимаем 1000 об/мин по паспорту станка
3. Фактическая скорость резания
м/мин
4. Крутящий момент по формуле [14, с. 277]:
, Н×м,
где
СМ
, q, x, y - коэффициент и показатели степени,
СМ
=0,0345, q=2,0, x=-, y=0,8 [14, табл. 32, с. 281];
КР
= [14, табл. 9, с. 264];
Н×м.
5. Осевую силу определяем по формуле [14, с. 281, табл. 32]:
, Н,
где
СР
, x, y, q - коэффициент и показатели степени,
СР
=68, x=-, y=0,7, q=1,0 [14, табл. 32, с. 281];
КР
= [14, табл. 9, с. 264];
Н,
6. Мощность резания определяем по формуле [29, с. 280]:
, кВт,
кВт.
7. Проверка на достаточность привода станка:
,
где
Nшп
- мощность привода станка;
Nшп
=Nст
×h, Nст
=7,5 кВт, h=0,8 - КПД привода;
Nшп
=7,5×0,8=6,0 кВт.
0,635<6,0.
Условие выполняется.
8. Основное время
ТО
= ,
l=4,5 мм, lпер
=5 мм, i=1.
ТО
= =0,064 мин.
Переход III: Сверлить отв. Æ12Н14, l=24мм, сверлить конус Æ17,9мм с углом 1200
*; сверлить отв. Æ17,9Н14, l=20±0,5мм. Одновременно.
1. Скорость резания
[14, с. 276];
где Т=45 – стойкость сверла, мин [14, с. 279, табл. 30];
CV
, m, x, y– определяются по [14, с. 278, табл. 28];
CV
= 9,8
m = 0,2
y = 0,5
q = 0,4
S=0,33мм/об[14, с. 277, табл. 25];

К1
V
=1.0[14, с. 263, табл. 6];
КИ
V
=1.0[14, с. 280, табл. 30];
KV
=1.01086×1,0×1,0=1,01086
=36,29 м/мин
2. Частота вращения шпинделя
630 об/мин
3. Крутящий момент по формуле [14, с. 277]:
, Н×м,
где
СМ
, q, x, y - коэффициент и показатели степени,
СМ
=0,0345, q=2,0, x=-, y=0,8 [14, табл. 32, с. 281];
КР
= [14, табл. 9, с. 264];
Н×м.
4. Осевую силу определяем по формуле [14, с. 281, табл. 32]:
, Н,
где
СР
, x, y, q - коэффициент и показатели степени,
СР
=68, x=-, y=0,7, q=1.0 [14, табл. 32, с. 281];
КР
= [14, табл. 9, с. 264];
Н,
5. Мощность резания определяем по формуле [29, с. 280]:
, кВт,
кВт.
6. Проверка на достаточность привода станка:
,
где
Nшп
- мощность привода станка;
Nшп
=Nст
×h, Nст
=22 кВт, h=0,8 - КПД привода;
Nшп
=22×0,8=17,6 кВт.
3,0<17,6.
Условие выполняется.
7. Основное время
ТО
= ,
l=33 мм, lвр
=5 мм, i=1.
ТО
= =0,183 мин
Переход IV: Зенковать конус под углом 450
; зенковать фаску Æ21,8Н11, l=3+0,4
, под углом 150
±10
. Одновременно
3. Скорость резания
[14, с. 276];
где Т=80 – стойкость зенковки, мин [14, с. 280, табл. 30];
CV
, m, x, y– определяются по [14, с. 278, табл. 28];
CV
= 10,5
m = 0,4
y = 0,65
х=0,2
q = 0,3
S=0,8 мм/об[14, с. 278, табл. 27];

К1
V
=1.0[14, с. 263, табл. 31];
КИ
V
=1.0[14, с. 280, табл. 6];
KV
=1.01086×1,0×1,0=1,01086
=4,7 м/мин
4. Частота вращения шпинделя
68 об/мин,
принимаем 63 об/мин по паспорту станка
3. Фактическая скорость резания
об/мин
4. Крутящий момент по формуле [14, с. 277]:
, Н×м,
где
СР
, x, y - коэффициент и показатели степени,
СР
=200, x=1.0, y=0,75 [14, табл. 32, с. 281];
=60,48 Н×м
5. Мощность резания определяем по формуле [29, с. 280]:
, кВт,
кВт.
6. Проверка на достаточность привода станка:
,
где
Nшп
- мощность привода станка;
Nшп
=Nст
×h, Nст
=22 кВт, h=0,8 - КПД привода;
Nшп
=7,5×0,8=6 кВт.
0,39<6.
Условие выполняется.
7. Основное время
ТО
= ,
l=4 мм, lвр
=5 мм, i=1.
ТО
= мин
Переход V: Фрезеровать резьбу М20х1,5-7Н, в размер l=15,5min
Нарезание резьбы производим гребёнчатой фрезой 2672-0577 8g ГОСТ 1336- 77. Расчёт режимов резания ведём аналитическим методом.
1. Подачу на один зуб фрезы выбираем по [14, с. 295, табл. 48].
SZ
= 0,04…0,05 мм, принимаем SZ
= 0,05 мм
2. Расчёт скорости резания
Скорость резания определяется по формуле:
, м/мин,
где
Т - стойкость фрезы, мин;
S = 1,5- шаг резьбы;
KV
- коэффициент, учитывающий реальные условия резания;
CV
, m, x, y - коэффициент и показатели степени, определяются по [14, с. 296, табл. 49].
По рекомендациям [14] стойкость принимаем равной:
Т = 70 мин
КV
=КMV
КИ
V
КТ
V
По [14, с. 298, табл. 50]:
КMV
=0,9;
КИ
V
1,0;
КТ
V
=1,0;
КV
=0,8×1,0×1,0=0,9.
CV
=198;
m=0,50;
x=0,4;
y=0,3.
=146,2 м/мин.
3. Частота вращения фрезы:
, об/мин, где
Dф
= 10 мм - диаметр фрезы.
=4656 об/мин,
В соответствии с паспортом станка и его кинематикой:
nст
= 250 б/мин
4. Фактическая скорость резания:
, м/мин.
=7,85 м/мин.
5. Расчёт основного времени
Основное время определяется по формуле:
, мин, где
l = 15,5 мм - длина нарезаемой резьбы,
l1
- величина врезания и перебега (определяется по [12, прил. 4]), мм;
z = 1 - число заходов резьбы;
К = 1 - число заходов фрезы.
l1
= 0,5Dотв
, мм
Dотв
=21,8мм[18,ст225,тб3.113]
l1
= 10,9 мм.
=0,022 мин
Обработка на позиции II по всем параметрам аналогична позиции I.
Обработка на позиции III по всем параметрам аналогична позиции I, с отличием по продолжительности операции на переходе III, подлине рабочего хода инструмента.
Основное время
ТО
= ,
l=35,2 мм, lвр
=5 мм, i=1.
ТО
= =0,1931 мин
020 Слесарная
025 Контроль
Норма времени:
, мин
где ТШТ-К
- штучно-калькуляционное время выполнения работ на станках, мин;
ТШТ
- норма штучного времени, мин;
ТП-З
- норма подготовительно-заключительного времени, мин.
, мин
где ТО
- основное время на обработку одной детали, мин;
ТВ
- вспомогательное время, мин;
КtВ
- поправочный коэффициент вспомогательного времени;
АОБС
- время на обслуживание рабочего места, %;
АОТД
- время на отдых и личные надобности, %.
, мин
где ТВУ
- время на установку и снятие детали, мин;
ТВ.ПЕР
- время, связанное с переходом, мин;
ТВ.ИЗМ
- время на измерение, мин.
, мин
где ТП-З1
- время на организационную подготовку, мин;
ТП-З2
- время на наладку станка, мин;
ТП-З.ОБР
- нормы времени на пробную обработку, мин.
Результаты нормирования времени приведены в таблице 13. Карты помеченные символом * - взяты по [10], остальные по [9].
Таблица 13
№ п/п |
Наименование операции и содержание работы |
Карта, позиция |
Время, мин и коэффициенты |
1 |
2 |
3 |
4 |
005 |
Токарная с ЧПУ
1. Основное время
- Подрезать торец Æ38мм в размер 143,06 ; точить поверхн. Æ37-0,25
, l=30±0,1
- Центровать отв. Æ9*мм, глубиной 4,5±1,5мм
- Cверлить отв. Æ14Н14, l=61-1 мм, сверлить конус 120
0
±20
; сверлить отв.Æ25Н14, l=42±0,5; сверлить конус600
±10
; сверлить отв. Æ25,43Н13, l=22±0,5. Одновременно.
- Точить конус под углом 450
; точить фаску Æ32,4Н11 с улом 150
±10
.
- Нарезать резьбу М27х1,5-7Н, в размер l=18minВспомогательное время:
2. Время на установку и снятие изделия
Время связанное с переходом
Время на измерение:
- контроль длины отверстий
- 143,06 ;,
- фаски
- контроль отверстий
Коэффициент на вспомогательное время
Время на смену инструмента
Суммарное вспомогательное время
2. Время на обслуживание рабочего места
3. Время перерывов на отдых и личные надобности
4. Подготовительно-заключительное время на партию
- на наладку станка, инструмента и приспособлений
- на дополнительные приёмы
- на получение инструмента и приспособлений до начала и сдачу их после окончания обработки
Штучное время
Суммарное подготовительно-заключительное время
Штучно-калькуляционное время
|
Карта 17, поз. 2
Карта 86, поз. I
Карта 87, поз. 164 и карта 88
Карта 87,
поз. 16 и
карта 88
Карта 87, поз. 9
Карта 87, поз. 9
Карта 1
Карта 86, поз. I
Карта 89
Карта 86, поз. I
|
1,132
0,85
0,75
0,18
0,04
0,04х4
0,2
0,91
0,6
2,78
3,5% от оперативного
4% от оперативного
10,0
1,5
5,0
3,938
16,5
3,978
|
010
|
Токарная копировальая
1. Основное время
- Подрезать торец Æ38 в размер 140±0,5
- Центровать отв. Æ9*мм, глубиной 4,5±1,5мм
- Сверлить отв. Æ18Н13, l=70±0,5мм
- Рассверлить отв. Æ22Н12, l=70±0,5мм; рассверлить отв. Æ25Н12, l=50±0,5мм; рассверлить отв. Æ28,38Н12, l=20±0,5мм. Одновременно
- Зенкеровать отв. Æ24Н10, l=23,5±0,5мм; зенкеровать конус Æ27Н14, под углом 300
±10
, зенкеровать отв. Æ27,2Н10, l=20±0,5мм. Одновременно.
- Расточить отв. Æ32,4Н14, l=14-1
- Точить фаску Æ32,4Н11, с углом 150
±10
, точить конус под углом 450
.
- Сверлить отв. Æ7Н12, l=2,5±0,5мм
- Развернуть отв. Æ24,6Н9, l=23,5±0,5мм, развернуть отв. Æ27,6Н9, l=20±0,5мм. Одновременно.
- Развернуть отв. Æ25Н8, l=23,5±0,5мм, развернуть отв. Æ28Н8, l=20±0,5мм. Одновременно.
- Точить торец Æ23мм в размер l=74,5±0,5мм, точить радиус R1max.
Нарезать резьбу М30х1,5-7Н, в размер l=16min
2. Время на установку и снятие изделия
Время связанное с переходом
Время на измерение:
- контроль длины отверстий
- -Æ140±0,5,
- фаски
- контроль отверстий
Коэффициент на вспомогательное время
Время на смену инструмента
Суммарное вспомогательное время
5. Время на обслуживание рабочего места
6. Время перерывов на отдых и личные надобности
7. Подготовительно-заключительное время на партию
- на наладку станка, инструмента и приспособлений
- на дополнительные приёмы
- на получение инструмента и приспособлений до начала и сдачу их после окончания обработки
Штучное время
Суммарное подготовительно-заключительное время
Штучно-калькуляционное время
|
Карта 17, поз. 2
Карта 86, поз. I
Карта 87, поз. 164 и карта 88
Карта 87, поз. 16 и
карта 88
Карта 87, поз. 9
Карта 87, поз. 9
Карта 1
Карта 86, поз. I
Карта 89
Карта 86, поз. I
|
4,514
0,85
0,75
0,36
0,04
0,04х4
0,4
0,91
0,6
2,78
3,5% от оперативного
4% от оперативного
10,0
1,5
10,0
14,062
21,5
14,108
|
015 |
Фрезерная с ЧПУ
Позиция I
-Фрезеровать поверхн. Æ30мм в размер 40±0,5.
-Центровать отв. Æ9*мм, глубиной 4,5±1,5мм.
-Сверлить отв. Æ12Н14, l=24мм, сверлить конус Æ17,9мм с углом 1200
*; сверлить отв. Æ17,9Н14, l=20±0,5мм. Одновременно.
-Зенковать конус под углом 450
; зенковать фаску Æ21,8Н11, l=3+0,4
, под углом 150
±10
. Одновременно.
-Нарезать резьбу М20х1,5-7Н, в размер l=15,5min
Б- Повернуть деталь
Позиция II
Выполнение переходов выполненых в позиции I
Позиция III
-Фрезеровать поверхн. Æ30мм в размер 40±0,5.
-Центровать отв. Æ9*мм, глубиной 4,5±1,5мм.
-Сверлить отв. Æ17,9Н14, l=26±0,5мм.
-Зенковать конус под углом 450
; зенковать фаску Æ21,8Н11, l=3+0,4
, под углом 150
±10
. Одновременно.
-Нарезать резьбу М20х1,5-7Н, в размер l=15,5min
2. Время на установку и снятие изделия
Время связанное с переходом
Время на измерение:
- контроль длины отверстий
- 40±0,5;,
- фаски
- контроль отверстий
Коэффициент на вспомогательное время
Время на смену инструмента
Суммарное вспомогательное время
8. Время на обслуживание рабочего места
9. Время перерывов на отдых и личные надобности
10. Подготовительно-заключительное время на партию
- на наладку станка, инструмента и приспособлений
- на дополнительные приёмы
- на получение инструмента и приспособлений до начала и сдачу их после окончания обработки
Штучное время
Суммарное подготовительно-заключительное время
Штучно-калькуляционное время
|
Карта 17, поз. 2
Карта 86, поз. I
Карта 87, поз. 164 и карта 88
Карта 87,
поз. 16 и
карта 88
Карта 87, поз. 9
Карта 87, поз. 9
Карта 1
Карта 86, поз. I
Карта 89
Карта 86, поз. I
|
1,908
0,85
0,75
0,18
0,04
0,04х4
0,2
0,91
5,0
7,18
3,5% от оперативного
4% от оперативного
10,0
1,5
5,0
9,075
16,5
9,107
|
020 |
Слесарная
- включить пневматическую машину
- зачистить кромки отверстия
- выключить пневматическую машину
Время на организационно-техническое обслуживание:
- регулировка механизированного инструмента
- инструктаж рабочего мастером
Время на отдых и личные надобности
Штучно-калькуляционное
|
Карта
63,поз
4а
Карта 1,
Поз.2
Карта 4
|
2´0,072
4%
6%
0,079
4%
0,259576
|
025 |
Контроль
по операциям
005
010
015
Всего
|
0,58
0,96
0,58
2,12
|
Расчёт потребного количества оборудования и коэффициентов его загрузки
, шт
где tшт-к
- норма штучно-калькуляционного времени на операцию, мин;
N - годовая программа выпуска, шт;
Fд
- действительный фонд рабочего времени, час.
Полученное значение округляем в большую сторону до ближайшего целого числа. Расчёт вёдём по методике для групповой технологии, принимаем
Fд
= часа
Коэффициент загрузки оборудования:

где СП
- принятое количество станков на операции, шт.
Все полученные данные сведены в таблицу.
Таблица 14
Операция |
ТШТ-К
, мин |
СР
|
СП
|
КЗ
|
005 Токарная с ЧПУ |
3,978 |
1,6 |
2 |
0,8 |
010 Токарная с ЧПУ |
14,108 |
5,6544 |
7 |
0,81 |
015 Фрезерно-сверлильная |
9,107 |
3,663 |
4 |
0,916 |
Средний коэффициент загрузки оборудования:

где n - количество операции в технологическом процессе

На рис. 14 представленна столбчатая диаграмма коэффициентов загрузки оборудования.
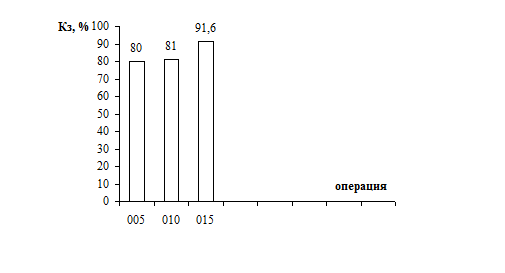
График загрузки оборудования
Производим проверку правильности выбранного ТП, путём определения КСЕР
КСЕР
=
Где t- такт выпуска, мин
tШТ-К
-средне калькуляционное время на одну операцию
мин
2,0937 мин
КСЕР
= = =11,94
-что соответствует среднесерийному производству
Конструкторская часть
Обоснование и описание конструкции
Установка детали в приспособление для сверления обеспечивает закрепление определенного положения детали относительно режущего инструмента, позволяет вести обработку отверстий с достаточно высокой точностью и с малыми затратами времени. Применение приспособления позволяет вести обработку при более высоких режимах резания, значительно сокращает время, вспомогательное.
Данное приспособление оснащено делительным устройством. Приспособление устанавливается на стол станка в Т-образные пазы с помощью болтов. Обрабатываемая деталь устанавливается в трёхкулачковый патрон и жесткий задний центр. С помощью делительного диска происходит деление. После закрепления и выверки заготовки ручка приспособления прижимается винтом к диску, приспособление готово для деления на 1800
. Стопорение поисходит силой трения развиваемой винтом в корпусе приспособления о шпиндель.
Приспособление может быть легко переналажено на другие детали заменой делительного диска и патрона на другие установочные элементы.
При расчёте приспособления на точность необходимо определить погрешность установки заготовки в приспособлении, которая определяется как
,
При установке деталей в упор в торец погрешность базирования по длине равна нулю. Погрешность закрепления также равна нулю, так как вектор силы закрепления перпендикулярен размерной цепи для отверстия.
Погрешность установки заготовки в приспособлении равна
=0 мкм.
Спроектированное приспособление удовлетворяет точности обработки детали на данной операции.
Силовой расчет и выбор параметров приспособления
Возникающая окружная сила резания сдвинуть деталь в осевом направлении отверстия, а при дальнейшем фрезеровании деталь может проворачиваться вокруг оси отверстияи одновременно отжиматся вниз.
Сила зажима без учета подачи определяется по формуле из схемы ;
[15, с.380]

Рис.
Где- y=300
- угол при вершине центра
j1
=j2
=30
- угол трения
l=80 мм- растояние от середины центрового гнезда досередины пиноли
ап
=50 мм- длина пиноли
Ph
=0,4Pz
=0,4×903,74=361,5 H
PV
=0,95Pz
=0,95×903,74=859 H
= =932 H
К- коэффициэнт запаса учитывающий нестабильность силовых воздействий на заготовку
К=К0
×К1
×К2
×К3
×К4
×К5
[15, с.382]
К0
=1,5- гарантированный коэффициэнт запаса[15, с.382]
К1
=1,2- учёт случайных сил резания из-за случайных неровностей на обрабатываемой поверхн. заготовки[15, с.382]
К2
=1,4- коэффициэнт учитывающий увеличение сил резания вследствии затупления[15, с.383, тб2]
К3
=1,2- учёт величения сил резания при прерывистом резании[15, с.383]
К4
=1,3- коэффициэнт характеризующий постоянство
сил развиваемых зажимным механизьмом[15, с.383]
К5
=1,2[15, с.383]
К=1,5×1,2×1,4×1,2×1,3×1,2=4,72
=2025 Н
Данная нагрузка эквивалентна прочности болта с внутренним диаметром болта 5,286 мм - соответствует примерно М8, что намного меньше резьбы применяемой для перемещения пиноли заднего центра (примерно М30).
Экономическая часть
Расчёт производим в ценах 1975-го года.
Условие эффективного применения приспособления:

где ЭП
- годовая экономия без учёта годовых затрат на приспособление, руб;
Р - годовые затраты на приспособление, руб.
, руб
где Тшт - штучное время на операции при обработке детали в универсальном приспособлении, мин;
ТштП
- штучное время на операции при использовании спроектированного приспособления, мин;
СЧ.З.
- часовые затраты по эксплуатации рабочего места, коп/ч;
N - годовая программа выпуска, шт.
В соответствии с нормативами вспомогательного времени [9; карта 1; карта 12, поз. 8; карта 17, поз. 2]:
мин
, коп/ч
где - практические скорректированные часовые затраты на базовом рабочем месте, для условий двухсменного крупносерийного производства =36,3коп/ч;
kМ
- машино-коэффициент, показывающий во сколько раз затраты, связанные с работой данного станка, больше, чем аналогичные расходы у базового станка, в соответствии [12, прил. II, с175]kМ
= 1,8
коп/ч
руб
, руб
где SПР
- стоимость приспособления, руб;
А - коэффициент амортизации;
В = 0,2 - коэффициент, учитывающий ремонт и хранение приспособления.
В соответствии с [2, табл. 63] стоимость, приспособления, включающего 20-25 наименований деталей составляет 125…145 руб, принимаем:
SПР
= 145 руб
Назначаем срок амортизации - 2 года, тогда коэффициент амортизации:
А = 0,5
руб
Экономический эффект от применения специального приспособления:
, руб
руб
В нынешних ценах:
руб
Оценка экономической эффективности технологического процесса [23]
Оценка экономической эффективности разработанного технологического процесса производим по приведенным затратам. Экономию на приведенных затратах определяем по формуле:
DС п. н.
= С п. н.1
- С п. н.2
,
где С п. н. 1
и С п. н. 2
- приведенные затраты, обусловленные производством годового объема продукции по базовому (1) и новому (2) вариантам, руб./год.
Приведенные затраты на операцию определяются:
×20,
где С п. н. н.
- приведенные затраты, приходящиеся на 1 час работы металлорежущего оборудования, коп.;
-поправочный коэффициент на инфляцию;
Базовый Т.П.:
005: С п. н. н
= 6,6× =36,74 руб.
015: С п. н. н
= 24,6× =68,47 руб.
020: С п. н. н
= 49× =136,38руб.
025: С п. н. н
= 18× =83,2 руб.
030: С п. н. н
= 30× =138,67 руб.
S С п. н. н
=36,74+68,47+136,38+83,2+138,67=463,46 руб.
Новый Т.П.:
005: С п. н. н
= 3,978× =9,30(44) руб.
010: С п. н. н
= 14,108× =33,17 руб.
015: С п. н. н
= 9,107× =50,7 руб.
S С п. н. н
=9,30(44)+33,17+50,7=93,18 руб.
DС п. н.
= С п. н.1
- С п. н.2
=468,46-93,18=370,28 руб.
На партию:
SDС п. н
=9600×370,28=3554688 руб.
С учётом изменения способа получения заготовки экономический эффект равен:
SDС=SDС п. н
+ЭТ
=3554688+56640=3611328 руб/партия.
Квалиметрическая оценка проекта
В ходе данной курсовой работе был проделан большой объём работы, которая включала в себя аналитические расчёты, выполнение чертежей, подготовка и выбор альтернативных вариантов, изучение литературы и стандартов.
Аналитические расчёты велись при определении режимов резания, производственной программы выпуска изделий, определении припусков, расчёте потребного количества станков, силовом и точностном расчёте приспособления, экономической оценке приспособления и технологического проекта. При выполнении курсового проекта технологичность изделия была повышена. Более рационально построен маршрут обработки изделия для условий среднесерийного производства: исключены некоторые операции (создание чистовой базы под установку в токарный патрон), ряд операций объединены в одну. Применено более производительное оборудование.
В проекте рассматривались два альтернативных варианта изготовления заготовки: штамповка в открытых штампах на КГШП (заводской вариант) и безоблойная штамповка на КГШП. При сопоставимой технологичесой себестоимости обоих вариантов, безоблойная штамповка даёт меньшую себестоимость, что привело к выбору второго варианта получения заготовки. Необходимо отметить, что при одинаковом способе получения заготовок в данном проекте и базовом технологическом процессе, припуски под механическую обработку разработанном технологическом процессе получились меньше, что связано с широким применением в проекте аналитического метода назначения припусков.
Разработанное приспособление удовлетворяет требованиям прочности и точности, а также даёт по сравнению с универсальным приспособлением годовую экономию в размере 69553,33 руб/год. В результате разработки технологического процесса и расчёта его экономической эффективности, экономический эффект составил 3611328 руб/партия.
Недостатком разработанного технологического процесса можно считать неравномерную загрузку оборудования. Но это можно устранить при использовании эффективной системы управления планирования путём дозагрузки оборудования другими изделиями, применение относительно дорогово режущего инструмента.
Литература
1. Ансеров М.А., Гущин В.Ф. Приспособления для сверлильных станков. Конструкции и наладки. - Л.: Машгиз, 1950 - 300 с.
2. Горбацевич А.Ф., Шкред В.А. Курсовое проектирование по технологии машиностроения: Учебное пособие для машиностроительных специальностей ВУЗов. - Минск: Высшая школа, 1983. - 256 с.
3. Добрыднев И. С. Курсовое проектирование по предмету «Технология машиностроения»: Учебн. пособие для техникумов по специальности «Обработка металлов резанием». - М.: Машиностроение, 1985. - 184 с.
4. Маликов Ф.П. Патроны для металлорежущих инструментов. Справочник. -* М. Машгиз, 1963. - 104 с.
5. Металлорежущий инструмент. Каталог-справочник. Часть 1. Резцы и фрезы. - М.: Машиностроение, 1976. - 448 с.
6. Металлорежущий инструмент. Каталог-справочник. Часть 3. Резьбообрабатывающий, трубо- и муфтообрабатывающий и зуборезный инструмент. - М.: НИИМАШ, 1971. - 476 с.
7. Мягков В.Д, Палей М.А., Романов А.Б.. Допуски и посадки: Справочник. В 2-х ч. Ч. 1. - Л.: Машиностроение, 1982. - 543 с.
8. Мягков В.Д., Палей М.А., Романов А.Б.. Допуски и посадки: Справочник. В 2-х ч. Ч. 2. - Л.: Машиностроение, 1978. - 545 с.
9. Общемашиностроительные нормативы времени вспомогательного на обслуживание рабочего места и подготовительно-заключительное для технического нормирования станочных работ. Серийное производство. - М.: Машиностроение, 1974. - 422 с.
10. Общемашиностроительные нормативы времени и режимов резания для нормирования работ, выполняемых на универсальных и многоцелевых станках с ЧПУ. Часть 1. Нормативы времени. - М.: Экономика, 1990. - 208 с.
11. Общемашиностроительные нормативы режимов резания для технического нормирования работ на металлорежущих станках. В 3-х частях. Часть 1. Токарные, сверлильные станки. - М.: Машиностроение, 1974. - 416 с.
12. Общемашиностроительные нормативы режимов резания для технического нормирования работ на металлорежущих станках. В 3-х частях. Часть 2. Зуборезные, горизонтально-расточные, резьбонакатные и отрезные станки. - М.: Машиностроение, 1974. - 200 с.
13. Справочник технолога-машиностроителя. В 2-х т. Т. 1 / Под ред. А.Г.Косиловой и Р.К.Мещерякова. - М.: Машиностроение, 1986. - 656 с.
14. Справочник технолога-машиностроителя. В 2-х т. Т. 2 / Под ред. А.Г.Косиловой и Р.К.Мещерякова. - М.: Машиностроение, 1985. - 596 с.
15. Станочные приспособления: Справочник в 2-х томах. Т. 1 / под общ ред. Б.Н.Вардашкина. - М.: Машиностроение, 1984. - 592 с.
16. Станочные приспособления: Справочник в 2-х томах. Т. 2 / под общ ред. Б.Н.Вардашкина. - М.: Машиностроение, 1984. - 656 с.
17. Технология машиностроения: Методические указания по выполнению курсового проекта для студентов специальности 120100 «Технология машиностроения» дневной и вечерней формы обучения. - Юрга: ИПЛ ЮФ ТПУ, 1999. - 39 с.
18. Балабанов А.Н. Краткий справочник технолога - машиностроителя.-М.: Издательство стандартов, 1992.-464 с.
19. Расчеты экономической эффективности новой техники: Справочник./ Под. общ. ред. К.М. Великанова - 2-ое изд. перераб. и доп. - Л.: Машиностроение. Ленингр. отделение, 1990. - 448 с.
|