Введение
Целью данного курсового проекта является расчет параметров структуры транзистора и определение технологических режимов ее изготовления.
По заданным параметрам структуры транзистора выбирается технологический маршрут изготовления. Определяются технологические режимы эпитаксиального наращивания, имплантации, длительность и температура диффузии, рассчитываются профили распределения примеси.
В курсовом проекте рассматривается задача синтеза структуры транзистора с использованием расчетных соотношений и параметров материалов, применяемых в его производстве.
Экономический расчет проекта не проводился.
Новизны в работе нет, так как проектирование проводилось по материалам учебной литературы.
Реферат
Пояснительная записка содержит 17 рисунков, 1 таблицу, приложение. При написании проекта использовался 1 источник.
Перечень ключевых слов: транзистор, диффузия, имплантация, легирующая примесь, p-n-переход, удельное сопротивление, напряжение лавинного пробоя, профиль распределения, температура, коэффициент диффузии, кремний, технологический режим.
Объект разработки: структура кремниевого эпитаксиально-планарного n-p-n транзистора.
Цель работы: расчет параметров структуры транзистора и определение технологических режимов ее изготовления.
Метод разработки: аналитический расчет.
Полученные результаты: xjСС
= 8,49 мкм, hЭС
6 мкм, ЭС
= 0,4 Ом*
см, xjРД
= 7,062 мкм, xjКБ
= 3 мкм, xjЭБ
= 2,3 мкм, cc = 3 мкм.
Степень внедрения: не внедрено.
Рекомендации по внедрению: нет.
Эффективность: не рассчитывалась.
Основные конструктивные и технико-эксплутационные характеристики: VКБ
= 120 В, Wа
= 0,8 мкм, материал подложки – ЭКДБ-10, ЭС
= 0,4 Ом*
см.
Область применения: расчет кремниевых эпитаксиально-планарных транзисторов.
Содержание
Введение
1. Определение режимов имплантации и термической диффузии
2. Имплантированных ионов сурьмы для создания в подложке скрытого слоя
3. Определение удельного сопротивления эпитаксиального слоя
4. Определение толщины эпитаксиального слоя
5. Определение режимов эпитаксии
6. Определение режимов разделительной диффузии
7. Определение режимов базовой диффузии
8. Определение режимов эмиттерной диффузии
9. Проверка величины размывания скрытого слоя в процессе последующих диффузий
10. Последовательность процессов при производстве ИМС
Заключение
Список использованных источников
1. Определение режимов имплантации и термической диффузии имплантированных ионов сурьмы для создания в подложке скрытого слоя
Определяем параметры скрытого слоя (СС). Поскольку параметры СС в задании на курсовой проект не указаны, то мы воспользуемся стандартными технологическими режимами, используемыми в изготовлении ИМС. Скрытый слой формируется путем имплантации ионов сурьмы с последующей термической диффузией имплантированных ионов.
Стандартный режим имплантации следующий:
Ф = 500 мкКл/см2
– доза облучения;
Е = 50 кэВ – энергия имплантированных ионов.
Термическая диффузия имплантированных ионов сурьмы Sb+
проводится по режимам:
ТСС
= 1220 0
С;
tСС
= 12 ч.
Распределение атомов сурьмы после диффузии определяется следующим выражением:
, (1.1)
где Q – количество ионов примеси на единицу поверхности, см-2
; x – глубина, соответствующая данной концентрации, см; D – коэффициент диффузии примеси, см2
/c; t – длительность диффузии, с.
Выразим дозу в количестве частиц, внедренных на единицу поверхности:
Q = 6,25*
1012
*
Ф. (1.2)
В нашем случае Q = 6,25*
1012
*
500 = 3,125*
1015
см-2
.
С помощью рис. 9.5, а [1] определим коэффициент диффузии сурьмы в кремнии при температуре ТСС
= 1220 0
С. Заданной температуре соответствует коэффициент D = 4,5*
10-13
см2
/c.
Глубина залегания p-n-перехода CC–подложка описывается выражением:
, (1.3)
где N0
– величина концентрации примеси на поверхности легированного слоя, т.е. при x = 0; NП
– концентрация примеси в исходной подложке.
Концентрация примеси N0
определяется на основе соотношения:
(1.4)
В нашем случае
см-3
.
В стандартной конструкции микросхем используются кремниевые подложки с удельным сопротивлением = 10 Ом*
см. По графику зависимости концентрации примеси от удельного сопротивления рис. 6.4 [1] находим, что удельному сопротивлению = 10 Ом*
см соответствует концентрация примеси: NП
= 1,2*
1015
см-3
.
С учетом полученных результатов глубину залегания p-n-перехода определяем по формуле (1.3):
8,49*
10-4
см = 8,49 мкм.
2. Определение удельного сопротивления эпитаксиального слоя
Величина удельного сопротивления эпитаксиального слоя (ЭС) определяется с учетом заданного значения пробивного напряжения VКБ
.
Известно [1], что величина пробивного напряжения плоского резкого p-n-перехода определяется следующим соотношением:
, (2.1)
где NЭС
– концентрация примеси в ЭС, в котором формируется p-n-переход коллектор–база.
Для планарного p-n-перехода справедливо следующее выражение [1]:
, (2.2)
где Uпр.плоск.
– пробивное напряжение плоского p-n-перехода; n = 1 для цилиндрического и n = 2 для сферического p-n-перехода.
, (2.3)
где r – радиус кривизны p-n-перехода, равный глубине залегания этого p-n-перехода; W0
– ширина области объемного заряда (ООЗ) резкого p-n-перехода при напряжении пробоя плоского p-n-перехода:
. (2.4)
Проведем расчет для случая сферического p-n-перехода, т.е. n = 2.
Зададим значение глубины залегания p-n-перехода xjК-Б
= 3 мкм, тогда r = xjК-Б
=3 мкм.
Зададим приблизительное значение NЭС
. Для этого воспользуемся графиком зависимости напряжения лавинного пробоя p-n-перехода с различной геометрией переходов рис. 9.3 [1]: NЭС
(15 В) = 5*
1016
см-3
.
Используя полученное из графика значение NЭС
, рассчитаем пробивное напряжение плоского p-n-перехода. Согласно формуле (2.1):
= 17,944 В.
Определяем величину W0
в соответствии с (2.4):
= 6,826*
10-5
см = 0,6826 мкм.
Находим
.
По формуле (2.2) определяем точное значение пробивного напряжения p-n-перехода коллектор–база при NЭС
= 5*
1016
см-3
:
Uпр.план.
= 17,944*
{[(2+1+4,395) *
4,3952
]1/3
-4,395} = 14,937 В.
Сравниваем полученное нами точное значение пробивного напряжения (14,937 В), с заданным в задании на курсовой проект значением пробивного напряжением коллектор–база (15 В). Отмечаем, что разница не превышает 10%. Поэтому оставляем выбранное нами значение концентрации эпитаксиального слоя NЭС
= 5*
1016
см-3
. С помощью рис. 6.4 [1] найдем удельное сопротивление ЭС ЭС
= 0,4 Ом*
см.
3. Определение толщины эпитаксиального слоя
Толщина ЭС определяется исходя из соотношения:
hЭСmin
= xjК-Б
+W0
+сс, (3.1)
где xjК-Б
– глубина залегания p-n-перехода коллектор–база; W0
– ширина ООЗ p-n-перехода при рабочем напряжении (напряжении пробоя); сс – величина расплывания СС в ЭС, отсчитываемая от границы раздела подложка–ЭС. Зададим глубину залегания xjК-Б
= 3 мкм и величину расплывания сс = 3 мкм.
Определим ширину ООЗ p-n-перехода по формуле (2.4)
6,241*
10-5
см = 0,624 мкм.
Согласно (3.1) толщина ЭС hЭС
будет равна:

4. Определение режимов эпитаксии
Температура эпитаксии обычно равна 11501200 0
С. Зададим температуру эпитаксии ТЭ
=1150 0
С.
Скорость наращивания ЭС соответствует диапазону vЭН
= 0,10,3 мкм/мин. Выбираем vЭН
= 0,2 мкм/мин.
Следовательно, длительность эпитаксиального наращивания:

5. Определение режимов разделительной диффузии
Разделительные дорожки (РД) формируются путем диффузии бора В+
с поверхности ЭС вглубь до смыкания с подложкой. При этом глубина залегания РД должна быть меньше ЭС на 1 мкм, т.е.
xjРD
= hЭС
+ 1 мкм. (5.1)
В нашем случае, согласно выражению (5.1) xjРD
= 7,062 мкм.
Глубина разделительной диффузии описывается следующим выражением:
, (5.2)
где D2
t2
– параметры второй стадии разделительной диффузии; N0
– концентрация на поверхности диффузионного разделительного слоя; NП
= NЭС
– концентрация примеси в ЭС.
В формуле (5.2) должно выполняться соотношение: N0
103
NП
. (5.3)
Положим, что N0
= 103
NП
= 103
NЭС
= 5*
1019
см-3
. Из выражения (5.2) определяем D2
t2
:
.
Задаем температуру второй стадии диффузии: Т2
=1220 0
С. Определим D2
. Пользуясь рис. 9.5, а [1] находим, что для Т2
= 1220 0
С коэффициент диффузии бора D2
(1220) = 3,5*
10-12
см2
/c.
Рассчитываем значение t2
:

Определяем параметры первой стадии разделительной диффузии. Распределение примеси после второй стадии диффузии описывает выражение:
, (5.4)
где Q – количество примеси, введенное в полупроводник на первой стадии диффузии. Оно определяется через параметры первой стадии диффузии выражением:
, (5.5)
где N01
– величина предельной растворимости. Определяется по графику (рис.9.5, а) [1].
Подставим выражение (5.5) в (5.4), и выразим N0
:
, (5.6)
где N0
, согласно (5.3), принимаем равным N0
= 103
NЭС
= 5*
1019
см-3
.
Из (5.6) выражаем D1
t1
:
. (5.7)
Зададим температуру первой стадии диффузии: Т1
=1150 0
С. По графику зависимости рис. 9.5, а [1] находим: D1
(1150 0
C) = 7*
10-13
см2
/c.
С помощью рис. 5.2 [1] находим предельную растворимость бора в кремнии N01
(T1
) = N01
(1150 0
C) = 5,4*
1020
см-3
.
Определяем t1
из выражения (5.7):

В результате получаем следующее распределение примеси в разделительных дорожках:
.
6. Определение режимов базовой диффузии
Формирование базовой области проведем методом имплантации ионов бора В с последующей термической диффузией имплантированных ионов.
Выбираем дозу имплантированных ионов бора Ф = 10 мкКл/см2
и энергию имплантированных ионов ЕИ
= 20 кэВ. Профиль распределения примеси после термической диффузии имплантированных ионов описывается следующим выражением:
, (6.1)
глубина залегания p-n-перехода коллектор-база:
, (6.2)
где [см-3
]; NП
= NЭС
[см-3
]. Согласно соотношению (5.3) положим, что N0Б
= 5*
1019
см-3
.
Температуру базовой диффузии выбираем равной 1150 0
С. При этом D(1150 0
C) = 7*
10-13
см2
/c.
Определяем время базовой диффузии из выражения (6.2):

Определяем параметры ионной имплантации:
см-2
,
С помощью формулы (1.2) найдем дозу облучения
мкКл/см2
.
Профиль распределения примеси в базовом слое описывается следующим выражением:
.
7. Определение режимов эмиттерной диффузии
Эмиттерные области формируются путем диффузии фосфора P. Глубина перехода эмиттер–база определяется на основании следующих значений:
1) выбранного нами значения глубины залегания xjКБ
= 3 мкм,
2) заданного в задании значения ширины активной базы Wa
= 0,7 мкм.
Глубина залегания p-n-перехода эмиттер–база определяется выражением:
, (7.1)
где xjЭБ
= xjКБ
- Wa
= 2,3 мкм.
Определяем параметры второй стадии эмиттерной диффузии. Согласно соотношению (5.3) положим, что N0Э
= 5*
1019
см-3
. Зададим температуру второй стадии диффузии Т2
= 1100 0
С. Определяем D2
(T2
) = 1,7*
10-13
см2
/с.
С помощью выражения (7.1) определяем длительность второй стадии t2
:

Определяем параметры первой стадии диффузии.
Находим

Принимаем N0Э
= 103
NП
= 8,59*
1020
см-3
.
Известно, что
. (7.2)
Из (7.2) выразим:

Также известно, что . Отсюда находим
. (7.3)
Задаем температуру первой стадии диффузии Т1
= 1100 0
С. При заданной температуре по графикам зависимостей рис. 9.5. и рис. 5.2. [1] определяем
значения коэффициента диффузии и предельной растворимости для фосфора P. Соответственно D1
= 1,7*
10-13
см2
/с и N01
= 2*
1021
см-3
.
Из выражения (7.3) найдем длительность первой стадии диффузии t1
:

Выражение описывающее профиль распределения фосфора Р в эмиттере имеет следующий вид:
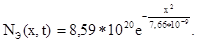
8. Проверка величины размывания скрытого слоя в процессе последующих диффузий
Фактическая глубина диффузии примеси из скрытого слоя в эпитаксиальный слой определяется следующим выражением:
(8.1)
где - сумма произведений всех значений коэффициента диффузии сурьмы при температурах: эпитаксии, разделительной, базовой и эмиттерной диффузии (см. табл. 8.1), и времени; N0
– поверхностная концентрация в скрытом слое; NП
– концентрация примеси в ЭС; i – индекс, соответствующий процессу термической обработки структур, начиная с эпитаксиального наращивания.
Концентрация N0
определяется по следующей формуле:
, (8.2)
где Q - количество ионов сурьмы Sb+
имплантированных в подложку; Dcc
tcc
- произведение коэффициента диффузии сурьмы и времени, соответствующее формированию СС.
Табл. 8.1
Зависимость коэффициента диффузии сурьмы в кремнии от температуры
Т, 0
C |
1100 |
1150 |
1220 |
D, см2
/c |
3,8*
10-14
|
9,8*
10-14
|
4,5*
10-13
|
Рассчитаем величину расплывания скрытого слоя. Для рассчитанных нами технологических режимов величина
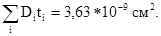
С помощью выражения (8.2) найдем поверхностную концентрацию в СС:
.
По формуле (8.1) найдем

Так как полученное нами значение cc < 3 мкм, значит оставляем толщину эпитаксиального слоя без изменений.
9. Последовательность процессов при производстве ИМС
1) Составление партии пластин. Количество пластин в партии 15 – 20 штук. Используются пластины марки ЭКДБ–10 диаметром 100 мм.
Исходный вид структуры
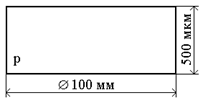
Рис. 9.1.
2) Химическая обработка пластин.
3) Термическое окисление Si.
Пластина после термического окисления
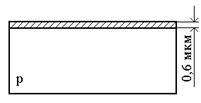
Рис. 9.2.
4) Фотолитография по окислу кремния.
Вид структуры после фотолитографии

Рис. 9.3.
5) Имплантация ионов сурьмы. Она выполняется по режимам: Ф = 500 мкКл/см2
; Е = 50 кэВ.
Имплантация ионов Sb+
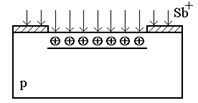
Рис. 9.4.
6) Термическая диффузия имплантированных ионов сурьмы Sb+
. Проводится при температуре Т = 1220 0
С и времени t = 12 ч.
Структура после термической диффузии

Рис. 9.5.
7) Травление окисла и химическая обработка пластины.
Травления окисла
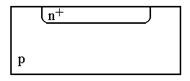
Рис. 9.6.
8) Наращивание эпитаксиального слоя.
ТЭ
= 1150 0
С, tЭ
= 30,312 мин. Толщина ЭС hЭС
6мкм. Удельное сопротивление ЭС
= 0,4 Ом*
см.
Структура после эпитаксиального наращивания
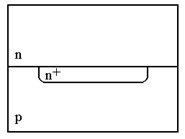
Рис. 9.7.
9) Химическая обработка.
10) Термическое окисление.
11) Фотолитография по окислу Si под разделительные дорожки.
Фотолитография под РД
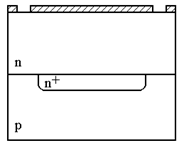
Рис. 9.8.
12) Химическая обработка.
13) Термическая диффузия бора В для создания разделительных дорожек.
1 стадия: Т1
= 1150 0
С и t1
= 9,08 мин; 2 стадия: Т2
= 1220 0
С и t2
= 1,43 ч.
Термическая диффузия бора в РД

Рис. 9.9.
14) Фотолитография по окислу кремния для создания базовых областей.
Фотолитография под базовые области
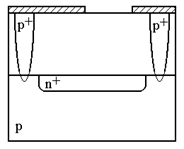
Рис. 9.10.
15) Химическая обработка.
16) Имплантация ионов бора В проводится по следующим режимам:
Е = 50 кэВ, Ф = 242 мкКл/см2
.
17) Термическая диффузия имплантированных ионов бора В. Проводится при температуре Т = 1150 0
С и t = 77,55 мин.
Диффузия бора в область базы
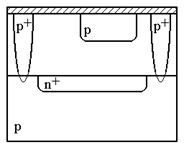
Рис. 9.11.
18) Фотолитография по окислу под эмиттер.
Фотолитография под эмиттер

Рис. 9.12.
19) Химическая обработка.
20) Диффузия фосфора P в область эмиттера.
1 стадия: Т1
= 1100 0
С и t1
= 5125,96 с; 2 стадия: Т2
= 1100 0
С и t2
= 11261,85 с.
Диффузия фосфора
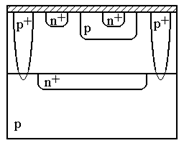
Рис. 9.13.
21) Фотолитография под контактные окна.
Фотолитография под контактные окна
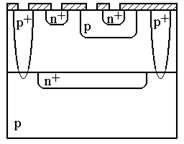
Рис. 9.14.
22) Контроль электрических параметров элементов. Измерения проводятся при помощи зарядовой установки и ПИХЛ22.
23) Химическая обработка.
24) Напыление алюминия.
Напыление алюминия
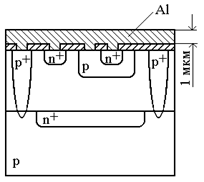
Рис. 9.15.
25) Фотолитография по алюминию.
Структура эпитаксиального n-p-n-транзистора
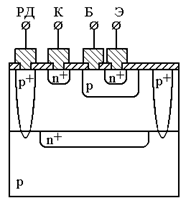
Рис. 9.16.
26) Вплавление алюминия.
ТВПЛ
< ТЭВТ
Al-Si
= 570 0
С.
ТВПЛ
= 565 0
С, t = 3 мин
Заключение
В данном курсовом проекте при заданном напряжении коллектор-база VКБ
= 15 В, ширине активной базы Wа
= 0,7 мкм рассчитаны параметры структуры транзистора и определены технологические режимы ее изготовления.
Скрытый слой глубиной xjСС
=8,49 мкм формируется по стандартным режимам имплантации (Е=50 кэВ, Ф=500 мкКл/см2
) и последующей термической диффузии ионов сурьмы (ТСС
=1220 0
С, tCC
=12 ч). Эпитаксиальный слой толщиной hЭС
6 мкм и удельным сопротивлением ЭС
=0,4 Ом*
см наращивается на кремниевую пластину ЭКДБ-10. Параметры эпитаксии: температура ТЭ
=1150 0
С, скорость наращивания vЭН
= 0,2 мкм/мин, длительность эпитаксиального наращивания tЭ
=38 мин.
Разделительные дорожки формируются путем диффузии бора с поверхности ЭС вглубь до смыкания с подложкой (глубина залегания xjРD
= 7,062 мкм). Разделительная диффузия проводится в два этапа: Т1
=1150 0
С и t1
=9,08 мин, Т2
=1220 0
С и t2
=1,43 ч. Формирование базовой области проводим методом имплантации ионов бора (Е=50 кэВ, Ф=809 мкКл/см2
) с последующей термической диффузией имплантированных ионов (Т=1150 0
С и t=77,55 мин). Эмиттерные области формируются путем последовательной диффузии фосфора Р (Т1
=1100 0
С и t1
=5125,96 с, Т2
=1100 0
С и t2
=11261,85 с). Величина размывания скрытого слоя в эпитаксиальный слой в процессе термообработки КЭСС равна cc = 0,36 мкм.
Областью применения результатов данного проектирования может являться расчет кремниевых эпитаксиально-планарных транзисторов.
Список использованных источников
1. Курносов А.И., Юдин В.В. Технология производства полупроводниковых приборов и интегральных микросхем. Учеб. пособие для вузов по спец. «Полупроводники и диэлектрики» и «Полупроводниковые приборы». – 3-е изд., перераб. и доп. – М.: Высш. шк., 1986. – 386 с., ил.
Приложение 1
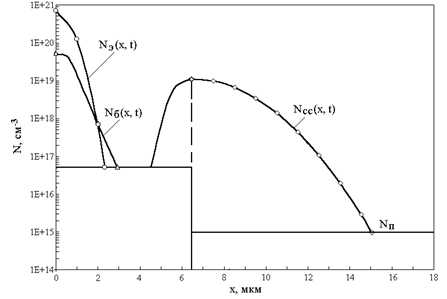
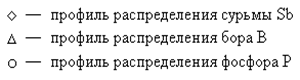
|