Министерство образования и науки Российской Федерации
Федеральное агентство по образованию
Государственное образовательное учреждение
высшего профессионального образования
«Комсомольский-на-Амуре» государственный технический университет»
Факультет ИКП МТО
Кафедра МиТЛП
ПОЯСНИТЕЛЬНАЯ ЗАПИСКА
К курсовому проекту
по ОТП ОМД
Технология электроконтактного нагрева заготовок
Содержание
Цели и задачикурсового проекта
Введение
1. Характеристика нагревательных установок
2. Характеристика материала заготовок
3. Потери энергии
4. Особенности расчёта и проектирования
5. Основные технико-экономические показатели электроконтактного способа нагрева
Заключение
Список использованной литературы
Введение
Физическая сущность электроконтактного способа нагрева заключается в том, что масса металла (деталь, заготовка или жидкая масса) нагревается за счет тепловой энергии электрического тока, протекающего по нему и преодолевающего электрическое сопротивление, оказываемое этим металлом, вследствие чего в последнем выделяется тепловая энергия, которая количественно определяется по закону Джоуля-Ленца.
Говоря о тепловой энергии, выделяемой в нагреваемом металле по указанному закону, следует иметь в виду, что в магнитных металлах происходит выделение некоторого количества тепловой энергии еще и за счет гистерезиса. Но так как это количество энергии незначительно по сравнению с тепловой энергией электрического тока, то им обычно пренебрегают.
Термин, «электроконтактный нагрев» является условным, так как он полностью не отражает ни физической, ни технологической сущности явления. Электроконтактным он назван потому, что к нагреваемому телу (детали, заготовке или массе) электрический пи подводится с помощью токоподводящих зажимных контактов. На рисунке 1, а приведена принципиальная электрическая схема, иллюстрирующая в самом общем виде принцип электроконтактного способа нагрева. Как видно из этой схемы, непременными элементами всякого электроконтактного устройства являются: токоподводящие контакты, с помощью которых ток подводится к нагреваемой заготовке; источник тока; токоподводящие провода или шины, соединяющие полюса источника тока с зажимными токоподводящими контактами, и зажимное устройство.
Существуют различные устройства и электрические схемы элктроконтактного способа нагрева, отличающиеся друг от друга конструктивным исполнением механической и электрической частей и технологическим назначением, все они могут быть сведены к принципиальным схемам, показанным на рисунке 1.
Для нагрева заготовки может быть использован постоянный и переменный электрический ток. Применение же постоянного тока при электроконтактном нагреве металлов практически затруднительно и экономически невыгодно из-за отсутствия источников (генераторов) большой силы тока и низкого напряжения, которые необходимы для нагрева металлических заготовок или деталей с малым электрическим сопротивлением, как это имеет место при
электроконтактном нагреве. Целесообразнее применение переменного тока, так как его способность к трансформации позволяет довольно просто получать требуемые напряжения на нагреваемых металлических телах (от долей до многих десятков вольт при токах от нескольких сот до многих десятков тысяч ампер). С этой целью существующие в настоящее время электроконтактные нагревательные установки снабжаются силовыми понизительными трансформаторами (рисунок 1, б).
Схема, показанная на рисунке 1, б, отличается от схемы на рисунке 1, а наличием силового трансформатора.
При использовании переменного тока приходится считаться с явлением скинн-эффекта, вызывающим неравномерность распределения температуры по поперечному сечению тел сравнительно больших линейных размеров, а также появление индуктивного электрического сопротивления. Следует отметить, что, несмотря на указанныенедостатки, электроконтактный способ имеет целый ряд преимуществ перед другими способами нагрева. Электроконтактный способ нагрева характеризуется равномерным выделением тепловой энергии в требуемом количестве за единицу времени непосредственно в каждом элементарном объеме нагреваемого тела, если не считать незначительной и технологически допустимой неравномерности распределения ее по сечению (вследствие скинн-эффекта), а также довольно высокой производительностью нагревательных установок, при высоком к. п. д.
При рассмотрении приведенных схем электроконтактных установок следует иметь в виду, что подвод тока к нагреваемым заготовкам обычно осуществляется с двух сторон для разгрузки контактов и улучшения распределения температуры по длине нагреваемой зоны; ток может подводиться и с одной стороны в каждом месте контактирования.
С точки зрения принципа нагрева количество точек (или мест) контактирования, т. е. точек подвода тока к нагреваемой заготовке, не имеет существенного значения, однако на практике это очень важно, так как токовая нагрузка токоподводящего контакта является одним из основных физических факторов, от которого зависят не только технологические, но и технико-экономические показатели всякой электроконтактной нагревательной установки.
При большой скорости нагрева и токе во вторичной цепи двусторонний подвод тока к каждому месту нагреваемой заготовки часто является решающим условием нормальной работы нагревательной установки. Об этом обстоятельстве не следует забывать, хотя оно и не имеет непосредственного отношения к физической сущности способа, а также к теоретическим зависимостям, существующим между отдельными физическими факторами, характеристиками и технико-экономическими показателями электронагре- вательного оборудования для электроконтактного способа нагрева.
1.
Характеристика нагревательных установок
Основные теоретические закономерности электроконтактного способа нагрева в самом общем виде известны из физики и теоретических основ электротехники. Однако при разработке и эксплуатации электроконтактных нагревательных устройств необходимо глубокое знание основных теоретических положений и математических зависимостей, на которых базируется этот способ и которые используются при разработке конструкций нагревательных устройств и технологических операций, осуществляемых на них.
Мощность электроконтактной нагревательной установки определяется из условия равенства тепловой энергии, необходимой для нагрева данной массы металла до заданной температуры, тепловой энергии электрического тока, а также энергии магнитного поля, обусловленной индуктивным сопротивлением элементов силовой цепи установки и самой нагреваемой заготовки.
Полная мощность всякого электроконтактного устройства может быть выражена формулой (1)
Где С - теплоемкость в дж/(кг•град);
G2
- масса нагреваемого металла в кг; t2
- конечная температура нагрева данной массы металла в o
С; t1
— начальная температура металла o
С;
ή0
— коэффициент, учитывающий общие потери энергии и носящий название общего к. п. д. электронагревательной установки или устройства;
τ— время нагрева в сек;
cos ф1
— коэффициент мощности.
О порядке и особенностях определения каждой составляющей, входящей в формулу (1), и о зависимости их от различных факторов будет сказано ниже. Следует иметь в виду, что из всех членов формулы (1) от конструкции нагревательной установки не зависят: теплоемкость С, масса нагреваемого металла G2
и температуры t1
и tx
2
; другие члены зависят от конструкции отдельных деталей, узлов и установки в целом, от геометрических параметров, физических свойств нагреваемой детали, а также от технологических требований, предъявляемых к процессу нагрева и к качеству нагреваемого металла.
Полная мощность установки, определяемая по формуле (1), является средней за период нагрева, так как теплоемкость С, к. п. д. ή0
и коэффициент мощности cos ф1
изменяются в зависимости от температуры; это обусловливается нестабильностью теплоемкости и удельного электрического сопротивления материала нагреваемой детали.
Как правило, с этим сталкиваются в начале нагрева, когда стальная деталь холодная, а мощность, потребляемая электроконтактной установкой, при прочих равных условиях, значительно меньше, чем в конце и когда деталь нагреется до температуры выше 800—900° С (если влияние скинн-эффекта несущественно). Но это справедливо только для магнитных материалов.
Разница значений между начальной и конечной мощностями зависит от марки материала, поперечных размеров нагреваемой детали и скорости нагрева.
При рассмотрении и использовании формулы (1) указанное обстоятельство следует учитывать при разработке конструкций и электрических схем нагревательных установок. При этом необходимо стремиться к тому, чтобы разница между начальной и конечной мощностями была бы минимальной, так как колебания значений последних в процессе нагрева оказывают отрицательное воздействие на работу энергетического оборудования и другого оборудования цеха и токоподводящих контактов.
Насколько существенно может изменяться мощность, потребляемая из сети электроконтактной установкой в процессе нагрева, в зависимости от поперечного размера нагреваемой детали или заготовки и времени нагрева, видно из рисунка 2.
Для заготовок диаметром 60 мм мощность в процессе нагрева изменяется в 1,3—1,4 раза, увеличиваясь к концу нагрева, а для заготовок диаметром 48 мм мощность изменяется сравнительно незначительно. Это объясняется более заметным влиянием скинн-эффекта, сказывающимся на соотношении активного и реактивного сопротивлений нагреваемых заготовок в начальный и коночный периоды нагрева в зависимости от поперечных размеров сечений. Для заготовок диаметром 60 мм это соотношение изменяется с ростом температуры более резко, чем для заготовок меньшего диаметра.
При нагреве продолжительностью 125 сек отношение начальной и конечной мощностей составляет 1,2, при нагреве продолжительностью 80 сек оно достигает 1,3—1,4.
Еще большая разница между начальной и конечной мощностями наблюдается при использовании заготовок, которые обладают большей магнитной проницаемостью, а электрические вторичные цепи и трансформатор имеют малое индуктивное сопротивление,
Рисунок 2.1 - График
т. е. в тех случаях, когда нагрузка имеет преимущественно активное сопротивление, а влияние скинн-эффекта сказывается более резко.
Электрический ток в нагреваемой детали. Для нагрева конкретной детали до требуемой температуры необходимо по ней пропустить электрический ток определенной величины в продолжение заданного промежутка времени, т. е. необходимо нагреть деталь с вполне определенной скоростью.
Величина потребного тока может быть найдена из выражения:
(2)
где r2
— активное электрическое сопротивление нагреваемой заготовки в ом;
I3
— электрический ток в а;
ήт
— тепловой к. п. д.
Величину тока в зависимости от геометрических параметров нагреваемой детали и физических факторов можно выразить формулой:
(3)
где /2
— электрический ток в нагреваемой детали в а;
S2
— площадь поперечного сечения детали в см'2
;
ς2
— удельное электрическое сопротивление в ом-см;
ζ, — плотность материала нагреваемой детали в г/см3
.
Величина тока, полученная по формуле (3), является средней, поскольку значения теплоемкости, удельного электрического сопротивления и теплового к. п. д. усредненные, так как практически для каждого данного момента определить их не возможно из-за сложной зависимости этих величин от температуры и времени, отсчитываемых от момента включения тока.
Выражение под корнем в формуле (3) не зависит от геометрических параметров нагреваемой детали. Следовательно, потребный электрический ток не зависит от длины заготовок. На первый взгляд это кажется не совсем понятным, но все становится ясным, если представить себе, что мощность, потребная для нагрева данной детали, зависит не только от тока, но и от напряжения, которое пропорционально длине детали, а энергия, выделяемая в элементарном объеме тела, зависит от плотности тока и удельного электрического сопротивления.
При одних и тех же поперечных размерах заготовок потребный электрический ток тем больше, чем больше скорость нагрева (меньше время, τ), и, наоборот, он обратно пропорционален корню квадратному из времени нагрева и удельного электрического сопротивления материала заготовки. При этом следует иметь в виду, что при выводе формулы (3) влиянием явления скинн-эффекта пренебрегают; в холодном же состоянии заготовки скинн-эффект имеет вполне определенное значение и потому в большинстве случаев его необходимо учитывать. При горячем режиме под которым понимается период нагрева заготовок до температуры выше точки Кюри, по формуле (3) можно с достаточной точностью определить потребный ток. В данном случае речь идет о токе, потребном для нагрева данной массы металла до заданной температуры; значение его является величиной усредненной, так как такие переменные факторы, как теплоемкость и удельное сопротивление, являются усредненными величинами.
Если в формулу (3) подставить истинные значения этих переменных, соответствующие какому-то моменту времени от начала нагрева (включения тока), то можно будет получить ток, сответствующий данному моменту времени.
Изменение тока в первичной цепи в процессе нагрева заготовок одинакового диаметра с различным временем нагрева на однопозиционной электроконтактной установке видно из рисунка 2.2.
Из рисунка 2.2 следует, во-первых, что ток и мощность довольно существенно изменяются в процессе нагрева; причем в начале нагрева ток имеет наибольшее значение, а к концу нагрева меньшее; во-вторых, чем меньше продолжительность нагрева, т. е. чем больше скорость, тем больше разница между указанными значениями токов; в-третьих, чем меньше поперечное сечение нагреваемой заготовки, тем больше между токами эта разница при прочиходинаковых условиях. Это объясняется различной степенью влияния скинн-эффекта.
Рисунок 2.2
Но наиболее резкое влияние на ток и мощность оказывает зависимость удельного электрического сопротивления от температуры (для заготовок малого диаметра), возрастающей в процессе нагрева от температуры окружающего воздуха до температуры, установленной в соответствии с технологическими требованиями.
Разница между начальным и конечным значениями тока зависит также от конструкции электрической вторичной цепи установки и отдельных ее элементов, а также от конструкции трансформатора. Поэтому характер зависимости тока от времени нагрева для различных установок в принципе сохраняется (ток падает с течением времени), но количественные соотношения между начальными и конечными значениями его могут изменяться значительно.
Напряжение на нагреваемой заготовке. Для нагрева конкретной заготовки с заданной скоростью к ней должно быть подведено определенное напряжение, зависимость которого от различных геометрических параметров заготовки и других физических факторов выражается формулой
(4)
где сг
— постоянный коэффициент, равный 0,032;
l2
—: длина нагреваемой детали между токоподводящими контактами в см.
Из формулы (4) следует, что напряжение на нагреваемой заготовке пропорционально длине и не зависит от ее поперечного сечения, кроме того, оно возрастает к концу нагрева (подтверждается данными из практики).
Из формулы видно, что характер зависимости напряжения на нагреваемой заготовке от времени нагрева тот же, что и для силы тока, т. е. величина напряжения обратно пропорциональна корню квадратному из продолжительности нагрева, отсюда следует обратно пропорциональная зависимость между потребной мощностью и временем нагрева.
На рисунке 2.3 приведена графическая зависимость напряжения на нагреваемой заготовке от времени нагрева.
Из рисунка 2.3 видно, насколько быстро возрастает напряжение при τ = 70-80 сек и ниже; это подтверждается и формулой (4), в которую, кроме времени нагрева τ, входит тепловой к. п. д. ήt
, находящийся в сравнительно сложной зависимости от τ.

Рисунок 2.3 - График Рисунок 1.5 - График
Прямая пропорциональность между напряжением на нагреваемой заготовке и длиной последней является важным свойством злектроконтактного способа нагрева; оно свидетельствует о возможности увеличения производительности электроконтактного нагревательного устройства за счет увеличения длины нагреваемой заготовки и повышения напряжения без увеличения тока [это подтверждается также формулой (3)].
Следует различать напряжение на заготовке в данный момент времени и напряжение, потребное для нагрева заготовки до требуемой температуры. В то время как первое определяется значениями С, qи ήt
, соответствующими данному моменту времени, второе определяется средними их значениями за период нагрева.
Влияние геометрических параметров нагреваемой заготовки на напряжение в процессе нагрева показано на рисунке 2.4; на кривых нанесены экспериментальные данные испытания однопозиционной установки для обособленного нагрева, выполненной по схеме, приведенной на рисунке 1, б.
Из формулы (4) и кривых на рисунке 2.4 видно, что, во-первых, напряжение на заготовке к концу нагрева возрастает; во-вторых, оно тем больше возрастает по сравнению с начальным, чем больше сопротивление нагреваемой детали. При этом необходимо учитывать, что так как напряжение зависит от тока, а последний в электроконтактной установке определяется полным сопротивлением (импедансом) всей электрической цепи и напряжением на выводах вторичной обмотки трансформатора, то изменение напряжения на детали в действительных условиях, которым соответствуют кривые рисунок 2.4, меньше, чем это следует из теоретической формулы (4), не учитывающей этого обстоятельства.
Так как колебания напряжения на детали на зажимах силового трансформатора, нежелательны, то с этой точки зрения может показаться, что при конструировании электроконтактных установок целесообразно увеличивать реактивное сопротивление цепи. Однако это не так, потому что последнее обусловливает наличие реактивной мощности со всеми связанными с ней более нежелательными последствиями, чем изменение напряжения.
Скорость нагрева металлов при любом способе имеет существенное значение, так как оно определяет производительность нагревательного оборудования и от него в значительной степени зависят не только электротехнические данные, но и конструкция оборудования.
Выделение тепловой энергии при электроконтактном нагреве почти по всей площади поперечного сечения нагреваемой детали позволяет получать большие скорости нагрева. Но, как и при любом другом технологическом процессе, скорость, с которой осуществляется электроконтактный нагрев, по различным причинам имеет определенные пределы.
Такими причинами являются: 1) допустимый температурный перепад между центральной и периферийной зонами поперечного сечения нагреваемой детали; 2) допустимая неравномерность нагрева детали по длине — перегрев или недогрев ее вблизи контактов или под контактами; 3) скорость протекания фазовых превращений и образование наиболее желательной для последующей обработки металла давлением структуры кристаллической решетки и размеров зерна или микроструктуры.
Неравномерное распределение температуры по поперечному сечению нагреваемой детали объясняется наличием явления скинн-эффекта, хотя и слабо выраженного при температурах выше точки Кюри и при нагреваемых заготовках с поперечными размерами больше 40—50 мм, но оказывающего некоторое влияние на неравномерное распределение температуры по сечению. При температурах нагреваемых заготовок ниже точки Кюри явление скинн-эффекта выражено довольно резко в остальных заготовках даже малого диаметра, так как в этом случае глубина проникновения тока, т. е. толщина поверхностного слоя, в котором выделяется тепловая энергия, во много раз меньше, чем при температурах выше точки Кюри.
Степень неравномерности нагрева зависит не только от температуры, но и от химического состава, электромагнитных свойств детали и от ее поперечных размеров; для деталей одного и того же типоразмера она зависит только от температуры и интенсивности или скорости нагрева.
Обработка металлов давлением осуществляется при температурах, значительно более высоких, чем температура точки Кюри (760—780° С), когда сталь теряет свои магнитные свойства, вследствие чего глубина проникновения тока значительно возрастает, а степень неравномерности нагрева (распределения температуры по сечению) существенно снижается. Температурный перепад между центральной и периферийной зонами поперечного сечения нагреваемой заготовки сказывается на времени нагрева в том, что при неравномерном распределении температуры по сечению в толще металла возникают термические напряжения, служащие причиной появления трещин при обработке заготовки давлением и остывании или местных перенапряжений, которые, в свою очередь, могут явиться причиной последующего брака или преждевременного выхода из строя детали.
Как известно, появление опасных термических напряжений зависит не только от величины температурного перепада (разницы температур в поперечных сечениях двух соседних зон), но и от температурного градиента в переходной области между этими зонами.
Основательных и сколько-нибудь надежных исследований в этом направлении применительно к электроконтактнсму нагреву пока еще не проведено (были только сделаны грубые замеры температуры периферийной и центральной зон заготовок диаметром 60—70 мм), и опубликованных в литературе работ по этому вопросу то же нет.
Обычно принято считать, что температурный перепад между центральной и периферийной зонами не должен превышать 100° С (такой перепад принимается при индукционном нагреве). Так как технологические операции, следующие за нагревом, не зависят от способа нагрева, то указанный температурный перепад можно принять и для электроконтактного нагрева.
В результате исследований, проведенных в НИИТВЧ получена зависимость скорости индукционного нагрева от диаметра нагреваемых заготовок и различных частот при сохранении температурного перепада, равного 100° С, между центральной зоной и поверхностью.
Пользуясь этими экспериментальными кривыми, можно выразить время нагрева в функции отношения диаметра заготовок к глубине проникновения; можно предположить, что при одинаковом значении этого отношения время нагрева будет примерно одно и то же для заготовок с различными поперечными сечениями.
Рисунок 2.5 - График
Обычно принимается, что эта зависимость сохраняется для всех случаев, когда глубина проникновения тока при температурах выше точки Кюри больше радиуса цилиндрической заготовки или больше половины поперечного сечения прямоугольной детали или заготовки, независимо от частоты. В этом случае время нагрева заготовок можно определить из формулы:
τ = d2
2
(5)
Так как глубина проникновения тока или толщина поверхностной зоны, по которой течет ток в стальной заготовке при температуре выше точки Кюри, составляет 70— 75 мм (для всех конструкционных, поделочных и для большинства специальных легированных сталей), то указанная зависимость (5) остается справедливой для всех заготовок диаметром 10—125 мм, которые могут быть подвергнуты нагреву электроконтактным способом. Время нагрева, определяемое из выражения (5), будет минимально допустимым для заготовок соответствующего диаметра при сохранении в них перепада температур между поверхностной и центральной зонами не более 100° С и температуре нагрева до 1100—1200° С. На рисунке 6 приведена зависимость времени электроконтактного нагрева от диаметра заготовок. Кривая 1 соответствует условию, определяемому формулой (5), кривая 2 отражает данные, рекомендуемые работниками Горьковского автозавода на основе первоначального опыта эксплуатации электроконтактных установок.
При сопоставлении кривых, показанных на рисунке 2.5, можно сделать следующие выводы:
1.Время нагрева, соответствующее зависимости, выраженной формулой (5), значительно меньше полученного по формуле (6).
Последнее соответствует температурному перепаду между центральной и поверхностной зонами поперечного сечения заготовки, равному менее 100° С, что подтверждается экспериментальными данными, отражающими изменение температуры центральной и поверхностной зон в процессе нагрева заготовки диаметром 70 мм с различной интенсивностью.
2.При определении времени электроконтактного нагрева, если его не ограничивает недопустимая неравномерность нагрева по длине, следует пользоваться кривой 1 на рисунке 2.5, соответствующей максимальной производительности нагревательной установки и допустимой степени равномерности распределения температуры по сечению заготовки.
Однако следует иметь в виду, что температурный перепад между указанными зонами изменяется в процессе нагрева. В начальный период нагрева температурный перепад больше допустимого, к концу же нагрева он становится меньше допустимого.
Перегрев, а часто и недогрев заготовок вблизи или под контактами недопустим технологически; перегрев вызывает оплавление заготовок или контактов и приварку их т. е, в конечном счете приводит к браку заготовок или выводу из строя контактов. Недогрев же вообще недопустим при нагреве заготовок под штамповку. Поэтому наиболее ответственной и еще полностью неразрешенной задачей является подводка тока к нагреваемым деталям при электроконтактном способе нагрева.
Рисунок 2.6-Зависимость температурного перепада между поверхностной и центральной зонами заготовки диаметром 70 мм
от времени
нагрева
Причина этих трудностей заключается в сложности физических явлений, происходящих в точках контактирования токоподводящего контакта с поверхностью нагреваемой детали. В месте соприкосновения имеется так называемое контактное сопротивление, величина которого зависит от многих и разнообразных по своей природе факторов. В переходном слое выделяется сравнительно большая тепловая энергия, отводимая от места контактирования за счет теплопроводности в ближайшие слои металла детали и контакта. В результате эти слои детали нагреваются быстрее всей остальной массы, так как в них помимо тепловой энергии электрического тока, выделяемой непосредственно в каждом элементарном объеме, прибавляется еще и указанная дополнительная энергия.
Так как активное сопротивление металла зависит от температуры и возрастает с ростом последней и так как тепловая энергия электрического тока пропорциональна сопротивлению, то слои и зоны заготовки, расположенные вблизи мест контактирования и доведенные с начала нагрева до больших по сравнению с остальной частью нагреваемой зоны заготовки температур, будут интенсивно нагреваться. Это приведет к перегреву их в процессе нагрева.
С другой стороны, элементарные участки нагреваемой детали, находящиеся под контактами, через которые протекает не весь ток, а только часть его и от которых тепло отводится контактом, будут иметь пониженную температуру по сравнению с температурой остальной части детали.
тепень неравномерности нагрева зависит от еще большего числа факторов, чем величина переходного сопротивления, являющегося основной, но не единственной причиной, оказывающей влияние на неравномерность распределения температуры по длине нагреваемой детали. Сложность заключается еще и в том, что и холодном состоянии, т. е. в начале нагрева, переходное контактное сопротивление и электрический ток особенно велики, а потому в месте контактирования выделяется в этот момент относительно большая тепловая энергия, вызывающая с самого начала интенсивный рост температуры в зонах поперечного сечения детали, прилегающих к токоподводящему контакту со стороны нагреваемой зоны этой детали.
В самом общем виде функциональную зависимость температурного перепада между перегретой зоной у контакта и остальной частью нагреваемой детали можно представить выражением:
∆t1,2
= φ(rп
, I2 ,
ψв
,d2
, ψm
, t2
),(6)
где rп
= φ (рк
Sк
ψф
) — сопротивление переходного контакта;
/2
— сила тока, протекающего во вторичной цепи;
ψв
— функция, учитывающая интенсивность охлаждения контакта;
ψm
— функция, учитывающая свойства материала и состояние
поверхности детали и контакта;
tз
— температура нагрева перегреваемой зоны детали;
рк
— давление на контакт;
SK
— площадь контактирования;
ψф
— функция, учитывающая форму контакта.
Выражение (6) наглядно показывает, насколько сложно выявить и установить, хотя бы приближенно, зависимость степени неравномерности нагрева от различных физических и технологических факторов, геометрических параметров и эксплуатационных условий.
Ниже приведены предельно допустимые скорости нагрева цилиндрических заготовок, установленные при эксплуатации электроконтактных заготовок и полученные при экспериментах.
Диаметр нагреваемой
детали в мм……………10.. 20..30..40..50..60..70
Время нагрева в сек……6..,15..40..60..80..100..120
При таких скоростях не наблюдается перегрева или оплавления нагреваемых заготовок или приварки их к токоподводящим контактам.
Другими словами, перегрева заготовок не наблюдается при перепаде температур, не превышающем 100° С, и при применении призматических медных радиальных зажимных контактов (давление на них 10 000—30 000 н) с осевыми размерами 50—60 мм.
Для сопоставления данных о времени нагрева, представленных выше, с расчетными, полученными по формуле (5), построена кривая 3 (рисунок 2.5). Из рисунка 2.5 видно, что практически применяемое время нагрева значительно больше расчетного.
Увеличение контактного давления, тщательная зачистка поверхности заготовок в местах контактирования, применение специальной формы контактов, устройства для охлаждения способствуют снижению продолжительности нагрева.
Однако все это связано с трудностями конструктивного и эксплуатационного характера, а поэтому в большинстве случаев используют практически применяемое время нагрева:
1. Наибольшую температуру имеет зона шириной 20—25 мм, отстоящая от торца заготовки на расстоянии 4—6 мм.
2.Положение этой зоны в процессе нагрева меняется — в начале нагрева она занимает место у самого торца (перегрет сам торец), а затем при повышении температуры зона постепенно перемещается в сторону от торца. При температуре 600—800° С температура на конце детали длиной 4—6 мм становится не только ниже температуры рядом расположенной зоны перегрева длиной 20—25 мм, но и ниже всей остальной (средней) части заготовки.
3.Степень неравномерности распределения температуры тем больше, чем больше ток.
Зависимость температурного перепада от тока количественно может быть выражена так: при изменении тока в 1,5 раза температурный перепад между зоной, перегрева и средней частью возрастает примерно в 1,5 раза, т.. е. можно сделать вывод о том, что изменение температурного перепада пропорционально току.
4.Наибольшее значение температурного перепада наблюдается в концевой зоне. Отставание роста температуры на конце заготовки от двух других зон объясняется отводом тепла от торца детали контактом, охлаждаемым водой.
5.Наибольшее значение температурного перепада наблюдается при температуре 700—1000° С.
Еще одним условием, лимитирующим скорость нагрева заготовок или производительность нагревательных устройств, является продолжительность протекания структурных и фазовых превращений. Приведенные выше скорости нагрева соответствующих типоразмеров заготовок значительно меньше тех, которые необходимы для указанных превращений, 'поэтому последнее условие при электроконтактном нагреве во внимание не принимается.
До сих пор речь шла о зависимости температурного перепада между зонами заготовки, расположенными близко от токоподводящего контакта, от различных факторов, но не о ширине зоны. Последняя существенно зависит от физических свойств материала заготовок, от формы поперечного сечения, а главным образом от теплопроводности и соотношения между площадью поперечного сечения и его периметром. Чем больше теплопроводность и указанное соотношение, тем больше ширина зоны перегрева. Это особенно необходимо иметь в виду в тех случаях, когда продолжительность нагрева очень мала, т. е. скорость нагрева большая, а длина нагреваемых заготовок небольшая, а перегрев широких зон заготовок у контактов недопустим. Но такого рода случаи не являются общими, хотя и нередко встречаются на практике. Вообще при контактном нагреве под гибку и штамповку целесообразнее использовать стали с большим коэффициентом теплопроводности, так как в этом случае при относительно большой ширине ион с различными температурами абсолютное значение температурного перепада будет относительно меньшим, при прочих равных условиях.
Эксперименты и практика эксплуатации электроконтактных установок показали, что при времени нагрева, близком к данным, приведенным выше, получается вполне удовлетворительная равномерность нагрева, с точки зрения требований, предъявляемых к равномерности нагрева заготовок подлине при радиальных и торцовых контактах.
2. Характеристика материала заготовок
Нагреву для последующей обработки давлением подвергаются преимущественно стальные заготовки, поэтому ниже рассматриваются характеристики и приводятся данные, относящиеся главным образом к стали.
Для электроконтактного нагрева существенное значение имеют следующие характеристики материала нагреваемых заготовок: теплоемкость, теплопроводность, магнитная проницаемость и удельное электрическое сопротивление.
Все они в большей или меньшей степени оказывают влияние на режим нагрева, его технологические особенности и на технико-экономические показатели работы электроконтактной установки. Поэтому знание закономерностей, свойственных каждой из этих характеристик, и технологических особенностей режима нагрева необходимо для рационального и эффективного применения данного способа нагрева в каждом конкретном случае.
Теплоемкость материала является фактором, определяющим "количество тепловой энергии, которую необходимо сообщить нагреваемой части заготовки для нагрева ее до заданной температуры.
Теплоемкость большинства материалов, в том числе и стали, зависит от температуры нагрева, поэтому теплосодержание массы материала нагреваемой детали или заготовки, необходимое для повышения температуры до заданного значения, зависит от этого значения.
На рисунке 3.1 приведена зависимость теплоемкости и теплопроводности сталей от температуры . Из фигуры видно, что теплоемкость до температуры 450—500" С изменяется незначительно, при 500—800о
С она изменяется резко, затем снова незначительно, а при температуре свыше 1000° С она остается почти постоянной (даже несколько падает).
Рисунок 3.1 - График
При расчете характеристик электроконтактных нагревательных установок удобно пользоваться средней теплоемкостью для заданных температур нагрева, по которой и определяется теплосодержание, потребное для нагрева данной массы металла до соответствующей температуры.
Теплопроводность материала нагреваемой детали и контакта играет довольно большую роль при электроконтактном нагреве и оказывает влияние на следующие технологические показатели: на скорость выравнивания температуры по поперечному сечению нагреваемой детали и по длине, а следовательно, и на производительность установки; на возможность оплавления заготовки под контактами и сварки детали с контактом, а это, в свою очередь, сказывается на конструкции контактов и допустимом токе.
Скорость выравнивания температуры тем быстрее, чем больше теплопроводность материала. Поэтому детали, обладающие большим коэффициентом теплопроводности, в меньшей степени склонны к неравномерному распределению температуры по длине, так как тепловая энергия, выделяемая в переходном контактном сопротивлении, отводится быстрее и в больший объем детали, следовательно, температура этой, хотя и более широкой, зоны будет относительно ниже.
Выравнивание температуры по сечению детали облегчается в большей степени, чем выше теплопроводность, так как при этом тепловая энергия, сконцентрированная в начальный период нагрева в сравнительно узком поверхностном слое детали, интенсивней отводится в центральную зону, что приводит к уменьшению температурного перепада между поверхностной и центральной зонами и выравниванию температуры по длине.
Следовательно, величина температурного перепада по сечению становится меньше в тем большей степени, чем больше теплопроводность.
Изучение характера и степени влияния теплопроводности осложняется еще и тем, что коэффициент теплопроводности, как и теплоемкость, изменяется в процессе нагрева в зависимости от температуры.
Важную, а иногда и решающую роль теплопроводность материала играет при торцовом нагреве (деталь зажимается с торцов) и при электроконтактной высадке металлов. В этих случаях режим нагрева, скорость протекания процесса высадки, а следовательно, и производительность, качество нагрева и набора металла или высадка изделия зависят от теплопроводности материала обрабатываемой детали.
Не менее важное значение имеет теплопроводность токоподводящего зажимного торцового контакта, так как от того, насколько интенсивно тепло отводится от нагреваемой детали с торца в толщу контакта, зависит перегрев или недогрев конца детали, а также оплавление и сварка контактирующих участков детали и контакта.
О роли теплопроводности при торцовом нагреве можно сказать следующее:
1.Если теплопроводность материала контакта и детали мала, то неизбежен перегрев конца детали.
2.Если теплопроводность материала детали мала, а контакта велика, то конец детали будет недогрет, а зона детали, находящаяся на небольшом расстоянии от торца, будет перегрета.
3.Существуют оптимальные значения коэффициентов теплопроводности материала детали и контакта, при которых условия нагрева будут наиболее благоприятными.
Магнитная проницаемость. Так как при электроконтактном нагреве используется переменный ток промышленной частоты ( 50 периодов), то, как уже указывалось, в нагреваемых телах в и большей или меньшей степени наблюдается явление скинн-эффекта, влияние которого зависит не только от геометрических размеров поперечного сечения тела и его удельного электрического сопротивления, но и от магнитной проницаемости. Последняя оказывает существенное влияние на следующие характеристики нагреваемой детали и нагревательной установки: на электрическое (активное и реактивное) сопротивление детали, а следовательно, и на технико-экономические показатели электроконтактной установки; на степень неравномерности распределения температуры по сечению нагреваемой детали, а следовательно, и на скорость нагрева; па энергетические характеристики режима нагрева (тока, мощности и напряжения), изменяющиеся в процессе нагрева в зависимости от изменения магнитной проницаемости.
Такое влияние магнитной проницаемости объясняется тем, что толщина поверхностного слоя детали, в котором концентрируется ток, тем меньше, чем больше проницаемость.
Как известно, сущность явления скинн-эффекта заключается и том, что электрический ток распределяется неравномерно по поперечному сечению нагреваемой детали, концентрируясь в периферийном слое определенной толщины.
Чем больше магнитная проницаемость, тем меньше глубина слоя концентрации тока и тем более резко выражена неравномерность распределения тока в этом слое.
Дли упрощения расчетов неравномерное распределение переменного тока заменяется условно током постоянного значения, равным току на поверхности детали, распределенному в поверхностном слое определенной толщины, и носящим название глубины проникновения тока. Последняя определяется из условия одинаковой тепловой эффективности неравномерно распределенного тока с равномерно распределенным на глубину проникновения и равного по величине значению тока на поверхности.
Исходя из этого условия глубину проникновения δ (в см) можно определить из формулы:
(7)
Где ς - удельное электрическое сопротивление в ом-см;
f — частота тока в гц;
μ— магнитная проницаемость материала детали.
Из формулы следует, что глубина проникновения обратно пропорциональна корню квадратному из магнитной проницаемости. Следовательно, значение величины μ для данного материала в известной степени определяет значение указанных выше характеристик. Однако вопрос осложняется тем, что μнаходится в своеобразной зависимости от температуры и тока. Поэтому изменение соответствующих характеристик детали и нагревательной установки в процессе нагрева определяется преимущественно характером зависимости магнитной проницаемости от температуры и в меньшей степени от тока.
До температуры точки Кюри, различной для различных материалов, магнитная проницаемость почти не изменяется или изменяется очень незначительно. При переходе через точку Кюри магнитная проницаемость независимо от дальнейшего повышения температуры быстро падает до постоянной величины.
Исходя из этого можно сделать вывод, что и указанные выше характеристики, зависящие от магнитной проницаемости, претерпевают аналогичные изменения, когда деталь достигнет температур, близких к температуре точки Кюри. Однако это не так — изменение характеристик происходит плавно во всем диапазоне температур нагрева.
Изложенное может быть объяснено следующим образом:
1. Явление скинн-эффекта при использовании тока промышленной частоты сравнительно слабо выражено.
2. На изменение тока и мощности, кроме магнитной проницаемости, влияют и другие факторы, в частности, удельное электрическое сопротивление, возрастающее с ростом температуры.
Зависимость магнитной проницаемости от тока (напряженности магнитного поля) показана на рисунке 3.2
Из кривой видно, что при определенном значении тока или напряженности магнитного поля магнитная проницаемость достигаетмаксимума, после которого она сравнительно быстро падает до примерно постоянного значения, мало изменяющегося с дальнейшим повышением тока.
Рисунок 3.2 - Зависимость магнитной проницаемости от напряженности магнитного поля
При электроконтактном нагреве магнитная проницаемость лежит, как правило, далеко справа от максимума кривой на рисунке 3.2. Поэтому изменение проницаемости от тока при электроконтактном нагреве не учитывают, считая ее постоянной для соответствующего интервала температур.
При электроконтактном нагреве магнитная проницаемость лежит, как правило, далеко справа от максимума кривой на рисуке 3.2. Поэтому изменение проницаемости от тока при электроконтактном нагреве не учитывают, считая ее постоянной для соответствующего интервала температур.
Магнитная проницаемость влияет на количество энергии, выделяемой в стали вследствие перемагничивания (так называемые потери гистерезиса), и считается в электрических машинах и трансформаторах явлением отрицательным.
При электронагреве эта энергия — явление положительное, так как она возникает в массе нагреваемой заготовки.
Энергия, выделяемая в заготовке вследствие гистерезиса, может быть вычислена по формуле Штейметца [7]:
Pг
= kB1.6
m
fv(8)
Где k— коэффициент Штейметца, 0.6…..0.75 зависящий от свойства материала нагреваемой детали, значения которого для различных материалов приведены ниже; Вт
— максимальная индукция в гс;
f—-частота перемагничивания в гц;
V— объем материала, подвергающегося нагреву, в см3
Если подставить в формулу Штейметца значения коэффициента k, максимальной магнитной индукции Вт
и выразить энергию в вт, то применительно к сталям, нагреваемым для обработки давлением, получим величины в долях ватта на единицу объема, что по отношению к энергии, необходимой для повышения температуры материала (единицы объема)
на 1 °С, не превышает нескольких процентов даже в начальной стадии нагрева, когда температура нагреваемой детали низкая. При температурах, близких и выше точки магнитного превращения (точка Кюри), когда материал теряет магнитные свойства, потери на гистерезис практически будут отсутствовать. Поэтому при электроконтактном нагреве до температуры 1000—1200° С тепловую энергию гистерезиса не учитывают.
Но в тех случаях, когда нагревают до 200—400° С и когда магнитная проницаемость велика, а температура нагрева регулируется достаточно точно, энергию гистерезиса, выделяющуюся в нагреваемой детали, необходимо учитывать.
Удельное электрическое сопротивление материала нагреваемой детали является одним из основных физических факторов, от которого непосредственно или косвенно зависят электротехнические характеристики режима нагрева и технико-экономические показатели электроконтактной нагревательной установки.
От него прежде всего зависит величина тока и напряжения на нагреваемой детали. Электрическое сопротивление изменяется в зависимости от температуры, этим вызывается изменение соответствующих характеристик и показателей.
Аналитически значение удельного электрического сопротивления для данной температуры определяется по формуле:
(9)
где ςt
— удельное электрическое сопротивление заготовки при
температуре t2
;
ς 0
— удельное электрическое сопротивление при t1
~ 20° С; α — температурный коэффициент сопротивления для соответствующего материала нагреваемой заготовки. При электроконтактном нагреве зависимость удельного электрического сопротивления от температуры сказывается на технологическом режиме нагрева.
3.
Потери энергии
Экономическая эффективность любого способа нагрева и оборудования зависит от потерь энергии при нагреве данной конкретной детали или заготовки.
При электронагреве различают два вида потерь: тепловые и электрические. Первые обусловливаются наличием трех видов или процессов теплообмена между телами с различной температурой: излучения, теплопроводности и конвекции.
В частности, при электроконтактном нагреве тепловые потери могут быть следствием указанных трех видов теплообмена.
Обычно трудно провести четкое разграничение между процессами, так как они могут проявляться одновременно, но в разной степени. Поэтому тот процесс, который будет преобладать над другим, является основным и определяющим процессом теплообмена.
Рассмотрим каждый вид тепловых потерь применительно к электроконтактному нагреву.
Потери излучением с поверхности нагреваемой заготовки составляют существенную долю тепловых потерь при электроконтактном нагреве.
Как уже указывалось такого вида потери зависят от температуры нагрева, типоразмера нагреваемой заготовки и состояния ее поверхности.
Зная удельные потери, нетрудно вычислить мощность потерь излучением со всей поверхности нагреваемой заготовки для соответствующей температуры
P3
=5,7e0
(T2
4
- T1
4
)10-12
вт/см2
, (10)
где е0
— коэффициент излучения поверхности в вт/(см2
-град)4
;
Т1
и Т2
—абсолютнаятемпература (исходная и конечная) поверхности заготовки.
Приближенно полную энергию потерь вследствие излучения с нагреваемой заготовки за период нагрева можно вычислить исходя из следующего допущения: удельная мощность излучения в среднем равна 12 вт/см2
, это соответствует примерно температуре 1100—1200 ° С при коэффициенте излучения поверхности, равном 0,8.
Такое допущение заранее предопределяет некоторое завышение потерь излучением по сравнению с расчетными, которые могут быть получены для каждого конкретного случая аналитическим путем, если воспользоваться зависимостью роста температуры от времени нагрева. Следует учитывать, что потери такого рода при принятой в настоящее время продолжительности нагрева малы, а при температуре 700—750° С они еще меньше (продолжительность нагрева до этих температур всегда больше половины общего времени нагрева). Поэтому при принятых допущениях и значении средней удельной мощности, соответствующей температуре 1100—1200° С, в процессе нагрева можно учесть с достаточной для практики точностью все потери излучением с нагреваемых заготовок различных типоразмеров. В тех случаях, когда интенсивность нагрева мала (продолжительность нагрева большая), т. е. когда время повышения температуры от 800—900 до 1100—1200° С больше половины всей продолжительности нагрева, удельные потери излучения и общие потери следует рассчитывать с учетом зависимости температуры от времени в процессе нагрева.
Общие потери излучения цилиндрической детали найдем из формулы:
(11)
Где τ — время нагрева в сек;'
l2
— длина нагреваемой зоны детали в см;
рэ
— удельная мощность излучения в впг/см2
;
d2
— диаметр детали в см.
Потери конвекцией. Тепловые потери с нагреваемой детали вследствие конвекции составляют значительно меньшую часть от общих тепловых потерь по сравнению с потерями излучением.
Мощность потерь конвекцией с цилиндрической детали можно определить по формуле
(12)
где F2
— поверхность детали в см2
.
При подсчете потерь, вызванных конвекцией, необходимо иметь н пиду, что они зависят не только от температуры тела, но и от температуры воздуха, от направления и турбулентности потока, от формы и ориентации тела в пространстве и т. д.
В электроконтактных установках, как правило, нагреваемые детали или заготовки расположены горизонтально, имеют простую форму (цилиндрическую или прямоугольную), охлаждение воздухом естественное, так как на установках и вблизи них нет воздушных вентиляторов или других устройств, создающих принудительное
Рисунок 4.1 - Схема расположения контактов относительно заготовки и направлений отвода тепла от нее теплопроводностью
а
— контакты радиальные; б — контакты торцовые; 1 — заготовки;
2
— контакты; 3 — перемычки; 4 — трансформатор.
охлаждение. Поэтому при электроконтактном нагреве влиянием перечисленных выше факторов можно пренебречь.
Потери теплопроводностью. При электроконтактном нагреве заготовок потери вследствие теплопроводности представляют собой довольно значительную величину, но обычно их не учитывают, так как считают, что они небольшие по сравнению с потерями вследствие излучения и магнитными потерями.
Особенность механизма теплообмена вследствие теплопроводности заключается в том, что тепловая энергия отводится от зоны детали, находящейся между зажимными контактами, в массу контактов и в ненагреваемые концы детали.
На рисунке 4.1 приведены простейшие схемы расположения зажимных контактов относительно заготовок и указаны направления отвода тепловой энергии от нагреваемой части заготовки.
Наибольшее количество тепла отводится через зажимные токоподводящие контакты, изготовляемые обычно из меди и охлаждаемые водой, наименьшее количество — в нагреваемые (холодные) концы детали при радиальных контактах; при использовании торцовых зажимных контактов отвод тепла происходит только через контакты.
Интенсивность отвода тепла зависит от разности температур между двумя соприкасающимися телами или зонами одной детали. В данном случае такими телами являются контакты и участки нагреваемой детали, соприкасающиеся между собой, а при наличии холодных концов — нагретые участки заготовки между контактами, контакты и зона холодного конца у контакта.
Поэтому в зависимости от температуры контакта, находящегося в непосредственной близости от заготовки, отвод тепла контактом от заготовки будет меньшим или большим.
Для уменьшения этого вида потери энергии было бы целесообразно поддерживать на контактах как можно более высокую температуру; однако это нельзя осуществить по следующим соображениям:
а)из-за возможности местных перегревов в точках контактирования вследствие выделения тепла в контактном сопротивлении;
б)из-за окисления поверхности контакта и образования не проводящей пленки на нем.
Образование пленки окисления приводит к увеличению переходного контактного сопротивления, а следовательно, к росту потерь энергии в нем; к местному перегреву, к росту температурного перепада между заготовкой и контактом, т. е. приводит к результатам, противоположным тем, которые достигаются при холодном контакте.
Учитывая это обстоятельство, в электроконтактных установках предусматривают режимы работы с холодными контактами, изготовляемыми из меди и охлаждаемыми водой.
Неохлаждаемые контакты, как правило, быстро выходят из строя, способствуют местному перегреву деталей у контактов, выплеску металла, а в конечном счете — некачественному нагреву.
При электроконтактном нагреве отвод тепла контактами от заготовки нежелателен с экономической точки зрения, так как это приводит к снижению к. п. д., недогреву конца детали под контактами или вблизи последних; в то же время он способствует выравниванию температуры по длине (на участке вблизи контакта), повышению срока службы контактов, улучшению условий эксплуатации.
К сожалению, все эти вопросы еще недостаточно исследованы, а потому о них можно говорить только в самой общей форме.
Электрические потери. Другой составной частью потерь энергии при электроконтактном нагреве являются электрические потери.
В зависимости от типа электронагревательной установки, конструкции контактов, типоразмера нагреваемой детали и режима нагрева электрические потери либо примерно равны, либо больше или меньше тепловых потерь.
Электрические потери наблюдаются в следующих элементах электроконтактной установки:
1. В медных элементах вторичной цепи — в токоподводящих шинах, контактных колодках, зажимных контактах, переходных контактных сопротивлениях этих элементов.
2. В обмотках силового трансформатора.
3. В трансформаторном железе.
4. В металлических деталях конструкции установки. Характерной для электрических потерь является зависимость
этих потерь от квадрата силы тока, электрических и магнитных
свойств материала.
Рассмотрим хотя бы приближенно вопрос о каждом из перечисленных видов потерь.
Потери в медных элементах вторичной цепи. Вторичная электрическая цепь электроконтактной установки состоит из вторичной обмотки силового трансформатора, токоподводящих шин, подконтактных колодок и токоподводящих зажимных контактов.
Мощность потерь в медных элементах можно выразить формулой:
(13)
где /2
— сила тока во вторичной цепи в а;
Σri
—сумма сопротивлений шин, подконтактных колодок, переходных контактов и т. д.
Вычисление этих сопротивлений обычно производится по известным формулам и не представляет особого труда, если не считать контактных сопротивлений болтовых соединений и сопротивлений других элементов цепи переменному току с учетом явления скинн-эффекта.
Для уменьшения электрических потерь, как видно из формулы (13), нужно прежде всего стремиться к уменьшению тока, а при постоянном значении последнего — к уменьшению электрического сопротивления токоподводящих элементов, вторичной цепи установки, т. е. к увеличению, в разумных пределах, поперечного сечения и к уменьшению длины их в направлении тока.
Так как на практике могут встретиться самые разнообразные случаи, когда по конструктивным соображениям нельзя уменьшить до определенных пределов длину шин и других элементов и увеличить их сечение, то при этом следует руководствоваться следующим общим правилом: сечение, длина шин и других элементов должны быть такими, чтобы общая величина сопротивления их составляла не более 4—5% от величины сопротивления нагреваемой детали при температуре последней более 800—900° С.
Сопротивление меди в подконтактных колодках и контактах в худшем случае близко к сопротивлению шин, а в лучшем случае значительно меньше его, а потому им обычно пренебрегают.
Контактное сопротивление болтовых соединений имеет особое значение при электроконтактном нагреве, потому что оно не только соизмеримо с общим сопротивлением остальных элементов вторичной цепи, но часто значительно его превышает. Если в электроконтактной установке, только что вступившей в эксплуатацию, контактное сопротивление проводников, стягиваемых болтами, мало, то после некоторого периода эксплуатации оно становится во много раз больше первоначального и больше сопротивления всех элементов вторичной цепи.
Контактное сопротивление контактов более чем в 2 раза превышает сопротивление меди.
Это позволяет сделать важный для практики вывод: экономическую эффективность электроконтактной установки нельзя повысить за счет увеличения сечения меди свыше определенного предела или несущественного сокращения длины элементов цепи.
Целесообразнее в этом случае идти по линии уменьшения тока и контактного сопротивления. Последнее подтверждается тем, что электрические потери пропорциональны квадрату силы тока и сопротивлению, а контактное сопротивление является основным фактором.
Потери в активных материалах трансформаторов. Активными элементами силового трансформатора считаются обмотки и трансформаторное железо.
Потери в обмотках зависят от сопротивления последних и тока и носят название электрических потерь.
Кроме этих потерь, в трансформаторе имеются еще и электромагнитные потери в трансформаторном железе, зависящие от марки и веса железа.
В том случае, когда трансформатор используется при постоянной настройке на заданную нагрузку без перенастройки на различное число витков первичной обмотки, т. е. когда индукция в железе остается постоянной, то потери в трансформаторном железе также будут постоянными. Так как в производственной практике, как правило, сталкиваются с такими случаями, то можно считать потери в железе постоянными, не зависящими от типа нагреваемых заготовок и режимов нагрева.
Конструкция обмоток, сечение провода и марка железа выбираются обычно исходя из того, чтобы потери энергии в них не превышали 5—6% от общей мощности трансформатора.
Потери в металлических деталях каркаса. Электрические потери в металлических деталях конструкции нагревательной установки возникают вследствие наличия магнитного потока рассеяния элементов, обтекаемых электрическим током.
Потери такого рода очень трудно поддаются учету. В лучшем случае их можно учесть теоретически весьма приближенно, так как такие расчеты сопряжены с большими трудностями из-за неопределенности магнитных характеристик (магнитной проницаемости) материала. В практике электроконтактного нагрева эти потери не принимают во внимание (не рассчитывают) и относят их к тепловым.
Но, как показали эксперименты и опыт эксплуатации электроконтактных установок, потери в стальных деталях конструкции часто составляют основную часть не только электрических, но и тепловых потерь.
Чем отличаются тепловые потери от электрических и расчетные данные от экспериментальных, видно из табл. 4.1, в ней приведены данные для однопозиционной электроконтактной установки мощностью- 150 ква, при нагреве заготовок диаметром 45 мм.
Данные, приведенные табл. 6, позволяют сделать следующие выводы:
Таблица 4.1 -
Значения потерь различного вида в электроконтактной установке в квт
Потери |
ЭЭлектрическиееререрчрские |
Тепловые |
Изучением |
Теплопроводностью и конвекцией |
Общие |
Расчетные ...... Экспериментальные… |
1,4 2,6 |
0,8
-
|
1,3
-
|
2,1 3,6 |
1. Электрические потери, полученные расчетным путем по сопротивлению элементов вторичной цепи и путем замеров, тока и сопротивления примерно в 2 раза меньше действительных, полученных по показаниям прибора (ваттметра). Несоответствие этих данных вызывается токами Фуко и явлением скинн-эффекта в толстых шинах, подконтактных колодках и других медных элементах цепи.
2.Действительные тепловые потери примерно в 1,5 раза больше расчетных, что указывает на наличие неучтенных потерь за счет вихревых токов, индуктированных в металлических деталях, вследствие магнитных потоков рассеяния в них.
3.Потери вследствие теплопроводности и конвекции несколько больше потерь излучения. Основную часть составляют потери вследствие теплопроводности зажимных токоподводящих контактов
Они приблизительно в 3—5 раз больше потерь конвекции.
Это говорит о том, насколько важен правильный выбор размеров контактов, их конструкции и системы охлаждения.
4.Наличие относительно больших потерь в металлических деталях нагревательной установки указывает на необходимость избегать размещения стальных и вообще каких-либо металлических деталей вблизи токоведущих элементов силовой цепи.
Тепловую энергию вихревых токов, возбуждаемых в металлических деталях, находящихся в магнитных полях рассеяния цилиндрических проводников стоком, приближенно можно записать в следующем виде:
(14)
Где /2
- ток в проводе в а;
dn
диаметр провода в см;
lпр
длина детали в см;
h – расстояние металлической детали от оси провода в см;
ς - удельное электрическое сопротивление детали в ом-см;
μ— магнитная проницаемость материала детали.
Формула (14) справедлива для цилиндрического проводника, поперечные размеры которого малы по сравнению с расстоянием до металлической детали.
Так как шины в электроконтактных установках в большинстве случаев прямоугольного сечения с конечными размерами, соизмеримыми с расстоянием до металлических деталей, то для этого случая можно рекомендовать несколько другую формулу:
(15)
Из формул (14) и (15) видно, что потери энергии в стальных деталях, находящихся в магнитном поле рассеяния токов, прямо пропорциональны квадрату тока, ширине детали и обратно пропорциональны квадрату расстояния от проводника до детали.
В формулы не входят толщина детали, так как предполагается, что она значительно больше глубины проникновения тока в сталь.
Коэффициент полезного действия. Коэффициент полезного действия любой электроконтактной нагревательной установки является основным техническим показателем, характеризующим эффективность и целесообразность ее применения.
К. п. д. всякого нагревательного устройства зависит от конструкции последнего, от способа нагрева и от геометрических размеров нагреваемых деталей.
Чтобы вывести формулу для определения общего к. п. д. любого нагревательного устройства, необходимо записать выражение баланса энергии, справедливое для любого момента нагрева той или иной детали (речь идет об общей мощности, потребляемой электронагревательной установкой из сети):
(16)
где Рп
— полезная мощность, затрачиваемая на нагрев детали
до заданной температуры;
Р1
— мощность, теряемая в силовом трансформаторе;
Рц
— мощность, теряемая в элементах вторичной электрической цепи;
Р3
— мощность тепловых потерь вследствие излучения, конвекции и теплопроводности;
Р4
— мощность потерь в металлических деталях вследствие наличия магнитных потоков рассеяния проводников с током.
Тогда общий к. п. д. нагревательного устройства может быть найден из формулы:
(17)
Если в эту формулу подставить значение отдельных видов потерь, то получим зависимость к. п. д. от конкретных параметров детали и нагревательной установки (геометрических размеров детали и шин и их свойства).
Для практического использования формулы ее целесообразно представить в виде
ή о
= ήтр
ήэ
ήt
(18)
где ήтр
— коэффициент полезного действия трансформатора;
ήэ
— коэффициент, учитывающий электрические потери в
элементах вторичной цепи;
ήt
— коэффициент, учитывающий тепловые потери, в том числе и потери в металлических массах, и носящий название теплового к. п. д.
Обычно в литературе по электронагреву к. п. д. трансформатора и вторичных элементов цепи ήэ
объединяются одним коэффициентом, называемым электрическим к. п. д. установки. Но в данном случае будет удобнее пользоваться двумя коэффициентами — для учета потерь в трансформаторе и в элементах вторичной цепи.
К. п. д. силового трансформатора электроконтактных установок учитывает потери энергии в обмотках и в трансформаторном железе, а также в металлических крепежных деталях.
Поскольку токи и электрическое сопротивление в обмотках, а также индукция в трансформаторном железе и вес его известны, то определение потерь в них не представляет особых затруднений.
Общее выражение для к. п. д. трансформатора будет иметь следующий вид:
(19)
где I1
— ток в первичной обмотке трансформатора;
rт
— активное сопротивление обмоток, проведенное к "первичной обмотке;
∆р — потери в трансформаторном железе магнитопровода;
Рн
— номинальная мощность трансформатора в кет.
Из формулы видно, что для уменьшения потерь в трансформаторе необходимо стремиться к уменьшению сопротивления в обмотках и к уменьшению тока (если это возможно по условиям сохранения требуемой производительности).
Электрический к. п. д. ήэ
вторичной цепи учитывает потери энергии в токоподводящих шинах, контактных колодках, контактах и других элементах вторичной цепи нагревательной установки.
Выражение для электрического к. п. д. в самой общей форме имеет следующий вид:
(20)
где rМ.д
— электрическое сопротивление меди элементов вторичной силовой цепи;
r2
— омическое сопротивление нагреваемой детали.
Так как сопротивление детали зависит от температуры, то и электрический к. п. д. зависит также от последней. Ввиду того, что на одной и той же электроконтактной установке нагревается обычно несколько различных типоразмеров заготовок, сопротивление которых зависит от геометрических параметров нагреваемых зон заготовок, то целесообразно выразить сопротивление r2
через геометрические параметры и удельные сопротивления материала этих зон, тогда формула для электрического к. п. д. будет
(21)
где s2
— поперечное сечение нагреваемой детали;
ς2
— удельное электрическое сопротивление материала детали;
l2
— длина нагреваемой зоны.
Из формул (20) и (21) следует, что для получения наибольшего к. п. д. необходимо: а) уменьшить в разумных пределах сопротивление элементов вторичной цепи; б) максимально увеличить отношение длины нагреваемой зоны к сечению.
При учете явления скинн-эффекта толщина шин, подконтактных колодок и других элементов должна быть не более 30— 35 мм, а ширина их по конструктивным соображениям не более150 мм.
Если минимальная длина шины будет не менее 500 мм, то оптимальное сопротивление токоподводящих шин должно быть равным около (0,5-0,6) • 10- 5
ом. При учете контактных сопротивлений контактов, сопротивления колодок и других элементов вторичной цепи фактическое сопротивление ее, как показывают эксперименты, равно (0,15 - 0,20) • 10-4
ом.
На рисунке 4.2кривая 3 представляет собой зависимость ήэ
от отношения l2
/s2
при среднем значении удельного сопротивления большинства стальных деталей ς2
= 0,6-10- 6
ом-м, при температуре 20—1100 ° С и указанных выше значениях сопротивления вторичной цепи. Из рассмотрения кривой следует, что электрический к. п. д. начинает быстро падать при l2
/s2
менее 1,0—1,5. При больших значениях l2
/s2
к. п. д. достигает максимальной величины и затем изменяется очень мало. Это обстоятельство, характеризующее установки электроконтактного нагрева, необходимо иметь в виду при их проектировании и эксплуатации, особенно в тех случаях, когда l2
/s2
< 1, например в электровысадочных установках.
Тепловой к. п. д. учитывает тепловые потери вследствие тепловых процессов теплообмена, потерь на токи Фуко и гистерезис в стальных деталях каркаса и зажимных головках нагревательной установки, находящихся в магнитных полях проводников с током.
Тепловой к. п. д. в общем виде может быть найден из формул, определяющих перечисленные три вида тепловых потерь, и исходя из значения теоретического минимума энергии, потребной для нагрева данной детали до соответствующей температуры.
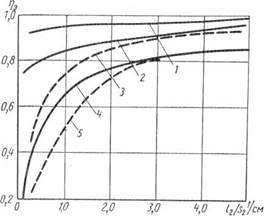
Рисунок 4.2 - Зависимость к. п. д. электроконтактной установки ς2
от отношения длины к сечению нагреваемой детали
1- ή
t
для
l
2
= 1000 мм; 2- ή
t
для
l
2
= 100 мм; 3 — ή э
для ς2
=0,6; 4- ή
t
= 0,94ή
t
ή э
для
l
2
= 100 мм; 5- ή
t
эксплуатационный коэффициент
Если предположить, что в нагреваемую деталь передаются теоретически потребное количество энергии и тепловые потери, то для теплового к. п. д. цилиндрической детали можно написать следующую приближенную формулу:
(22)
где τ — время нагрева в сек;
d2
и l2
—диаметр и длина нагреваемой зоны детали в см. Эта формула соответствует следующим условиям:
1. Удельная интенсивность излучения с нагретой детали равна 12 вт/см2
в продолжение всего периода нагрева, т. е. потери этого вида взяты с явным превышением с тем, чтобы ими восполнить потери, не поддающиеся непосредственному учету.
2. Осевая длина зажимного токоподводящего контакта равна диаметру нагреваемой детали, а ширина площадки контактирования l К
— 0,5 смпо всей длине контакта.
3. Для подвода тока, а следовательно, и для отвода тепла используется четыре контакта.
4. Потери конвекции определяются по формуле (12).

Рисунок 4.3 - График
Если скорость нагрева определяется из формулы (5), то тепловой к. п. д. можно выразить либо через параметры детали, либо через длину детали и время нагрева:
(23)
На рисунке 4.2и 4.3 приведены кривые зависимости теплового к. п. д.
ήt
от отношения /2
/s2
, диаметра d2
и времени нагрева τ для двух значений длин нагреваемых зон детали (/2
=100 и 1000 мм).
Большее значение теплового к. п. д. для заготовок большой длины объясняется относительно меньшими потерями теплопроводности через токоподводящие контакты, приходящимися на единицу длины детали; при этом энергия, вводимая в деталь, пропорциональна ее длине. Поэтому хотя потери конвекции и излучения и пропорциональны длине детали, они в данном случае не сказываются на величине к. п. д.
Общий к. п. д. В связи с тем, что все три коэффициента формулы (21) определены, общий к. п. д. электроконтактного устройства может быть выражен кривой 4 (на рисунке 4.2) в зависимости от отношения длины заготовки к сечению при среднем значении к. п. д. силового трансформатора ήтр
= 0,94.
Для сопоставления расчетно-теоретической кривой общего к. п. д. с экспериментальной на той же фигуре приведена кривая 5, выражающая значения общего к. п. д. одной из однопозиционных электроконтактных установок.
Из рассмотрения кривых видно, что действительный к. п. д. нагревательной установки в функции отношения l 2
/s2
в основном соответствует расчетно-теоретическому, отличаясь от него только при малых значениях l 2
/s2
(от 2,2 до 1,2).
При теоретических расчетах электротехнических характеристик нагревательных установок целесообразнее пользоваться расчетно-теоретической кривой 4 общего к. п. д., а не экспериментальной 5, справедливой для определенной конкретной установки. Экспериментальные данные можно было бы обобщить для любого случая электроконтактного нагрева, если бы они отвечали условию изменения напряжения на заготовке в соответствии с потребной мощностью, вычисляемой по теоретической формуле.
Но так как в действительности такое изменение напряжения осуществить очень трудно, то и получить обобщенную зависимость общего к. п. д. от отношения l2
/s2
почти невозможно, поэтому наиболее приемлемой является расчетно-теоретическая зависимость.
Коэффициент мощности
Для всякой электронагревательной установки коэффициент мощности, (после коэффициента полезного действия) является наиболее важным технико-экономическим показателем.
В связи с тем, что электроконтактные установки в большинстве своем имеют большую мощность и преимущественно активную нагрузку при сравнительно высоком коэффициенте мощности, применение компенсирующих конденсаторов для увеличения коэффициента мощности, как правило, нерационально. Тем не менее повышение его весьма желательно, поэтому при разработке электроконтактных установок необходимо использовать все имеющиеся в распоряжении проектанта и конструктора средства, чтобы получить оптимальный для данных конкретных условий коэффициент мощности.
Коэффициент мощности электроконтактных установок зависит от типа и конструкции обмоток трансформатора, их взаимного размещения, от конструкции магнитопровода, а также от индуктивного и активного сопротивления вторичной цепи установки и геометрических параметров нагреваемой детали.
Теоретически учесть перечисленные факторы чрезвычайно сложно и можно только очень приближенно. Поэтому целесообразнее коэффициент мощности выразить с помощью экспериментальных и эксплуатационных данных. Изменение коэффициента мощности в процессе Рисунок 4.4 – График нагрева аналогично изменению сопротивления детали, напряжения на ней и т. Д.
На рисунке 4.4 приведены кривые изменения коэффициента мощности первичной цепи однопозиционной нагревательной установки в процессе нагрева деталей различных типоразмеров.
Из рассмотрения кривых на рисунке 4.4 можно сделать следующие выводы:
1. Коэффициент мощности медленно возрастает с повышением температуры нагрева детали.
2. Коэффициент мощности изменяется тем быстрее, чем меньше диаметр нагреваемой детали. Это объясняется тем, что у заготовок малого диаметра относительное влияние активного сопротивления значительно больше, чем у заготовок большего диаметра.
Рисунок 4.5 – График
На рисунке 4.5 приведена зависимость коэффициента мощности от отношения длины к площади сечения детали; коэффициент мощности тем больше, чем больше указанное отношение.
В данном случае речь идет о коэффициенте мощности всей установки, включая и силовой трансформатор, определяемом по формуле:
. (24)
где rт
— активное сопротивление силовой цепи установки, приведенное к сопротивлению первичной обмотки силового трансформатора, включая нагрузку;
rm
— приведенный импеданс указанной цепи.
Поскольку электрическая цепь установки состоит из трех составных частей: силового трансформатора, вторичной цепи и нагреваемой детали (нагрузки), то и косинусы соответственно этому будут определены по формуле (24) для каждой составной части. В формулу должны быть подставлены значения сопротивлений соответствующей цепи или элемента.
Если электрические сопротивления, входящие в формулу для определения коэффициента мощности, выразить через параметры, определяющие указанные сопротивления, то можно убедиться, что последний находится в наибольшей зависимости от геометри-ческих размеров нагреваемой зоны детали, от числа витков первичной обмотки и индукции в сердечнике магнитопровода трансформатора.
Рисунок 4.6 – График
На рисунке 4.6 дана зависимость коэффициента мощности и характеристик холостого хода трансформатора (250 ква) от числа витков первичной обмотки при нагреве заготовок одинакового типоразмера.
Эксперименты производились при 36, 33, 30, 27 и 24 витках в первичной обмотке и при напряжении на ней, равном 185—210 в.
Изменение коэффициента мощности обусловливалось использованием различного числа витков, а значит, и различной индукцией в железе трансформатора; изменение последней примерно на 40% вызывает уменьшение коэффициента мощности на 5—7%. Такое снижение коэффициента мощности следует признать значительным и избегать его; правда на практике это не всегда удается, но об этом надо помнить, особенно при использовании мощных трансформаторов.
4. Особенности расчета и проектирования
Следует иметь в виду, что, говоря о приведенных ниже специфических особенностях, с которыми приходится сталкиваться при расчете и проектировании электроконтактных установок, нельзя их все рассмотреть в данной книге из-за многообразия технологических разновидностей и конструктивных типов нагревательных устройств. Поэтому целесообразно остановиться только на основных и наиболее важных общих особенностях, справедливых для всех установок независимо от их технологического назначения и конструкции.
При проектировании и расчете электроконтактных установок необходимо учитывать следующее:
1. Зависимость технологических и электротехнических характеристик режима нагрева от температуры нагреваемой детали или заготовки, т. е. непостоянство характеристик во времени (в процессе нагрева).
2. Неравномерное распределение температуры по длине и при больших диаметрах (более 50 мм) по сечению нагреваемой заготовки и во времени.
3. Зависимость тепловых явлений, происходящих под кон тактами, от контактного давления и состояния поверхности нагреваемой детали, а в связи с этим использование тока и мощности нагревательной установки большой величины.
Учесть эту технологическую особенность можно только на основе опытных данных эксплуатации электроконтактных установок.
4. Расчетные электротехнические данные в большинстве случаев являются "сугубо приближенными, поэтому требуют после дующего уточнения.
5. Принимать во внимание, что нагрев деталей и целых узлов происходит за счет энергии излучения с нагреваемых заготовок
и вихревых токов Фуко, возбуждаемых в металлических деталях магнитными потоками рассеяния.
Это обстоятельство, как и предыдущее, не поддается теоретическому расчету и может быть учтено при разработке конструкции нагревательной установки. При этом следует помнить, что металлические массы, особенно стальные, необходимо располагать как можно дальше от токоподводящих элементов и от нагреваемой детали.
6. Максимально возможную универсальность нагревательной установки, так как важна не только техническая эффективность применения данного типа нагревательной установки, но и возможность использования ее для разнообразных типоразмеров заготовок. При этом во много раз возрастает техническое совершенство, технико-экономическая эффективность, рентабельность, а следовательно, и народнохозяйственная значимость нагревательной установки.
Исходные данные для расчета и проектирования
Расчет и проектирование электроконтактной установки производится на основании определенного технологического задания, в котором должны содержаться перечисленные ниже исходные технологические, технические и эксплуатационные данные.
1. Марка материала и типоразмеры заготовок.
2. Темп выдачи нагретых заготовок или производительность нагревательной установки с учетом времени, потребного на загрузочно-разгрузочные, транспортные и другие операции.
3. Технологическая разновидность электроконтактного нагрева и назначение электроконтактной установки.
4. Температура нагрева, точность регулирования и допустимые пределы неравномерности распределения ее по длине и сечению нагреваемой заготовки.
5. Напряжение для питания установки, т. е. напряжение сети, к которой она подсоединяется.
6. Технические данные о заводской пневмосистеме и водопроводе, если в электроконтактной установке предусмотрен пневматический привод зажимных головок и водоохлаждение элементовсиловой цепи проточной водой.
7. Специальные требования, касающиеся механизации и авто матизации загрузки и выгрузки заготовок, или условия встройки установки в автоматические линии или привязки ее к другому оборудованию.
Особое внимание следует обратить на технологический принцип электроконтактного нагрева. Он должен быть подробно указан в задании, в противном случае при проектировании прежде всего должен быть решен вопрос о технологически-конструктивном типе нагревательной установки, дающем наилучшие технико-экономические показатели.
Иногда вместо производительности или скорости нагрева в задании указывается мощность установки и по ней требуется определить время нагрева деталей заданного типоразмера. В этом случае необходимо исследовать вопрос, подойдет ли вычисленное по заданной мощности время нагрева (по условиям равномерности распределения температуры по длине и сечению детали, а также по токовой нагрузке на контакты). Если этому или одному из этих условий время нагрева не удовлетворяет, то заданная мощность должна быть уменьшена.
Механизация загрузки и выгрузки заготовок и автоматизация работы нагревательной установки являются очень важными вопросами не только с эксплуатационной точки зрения, но и с точки зрения конструкции установки, которая при этом усложняется. Поэтому, прежде чем приступить к разработке проекта, нужно обосновать необходимость и целесообразность механизации и автоматизации загрузки и выгрузки заготовок, учитывая все ее преимущества и отрицательные стороны.
Определениепроизводительности электроконтактной установки
Производительность электроконтактной установки задается или устанавливается исходя из местных специфических условий каждого отдельного предприятия.
Она указывается в соответствующем технологическом задании. При разработке проекта остается определить скорость нагрева с учетом времени, необходимого для разгрузочно-загрузочных, транспортных и других операций.
Если расчетное время не отличается от полученного графическим путем, то заданную производительность можно считать приемлемой, в противном случае необходимо выяснить обоснованность заданной производительности и принять меры к устранению осложнений, которые могут возникнуть при нагреве.
Но если время нагрева или производительность должны быть определены при проектировании, то первое находят по указанному графику с учетом типоразмера заготовки; затем, прибавив к этой величине дополнительное время, затрачиваемое на другие операции и равное 15—25% от, времени нагрева (зависит от величины последнего), по формуле (25) определяют производительность электроконтактной установки:
П = (3,6 К.' G2
)/τ т/ч, (25)
где G2
— масса нагреваемой части заготовки в кг;
К.' — коэффициент, учитывающий дополнительное время, за трачиваемое на другие операции, связанные с нагревом;
τ — время нагрева в сек.
Темп выдачи нагретых заготовок или время одного Цикла работы установки определяется по формуле:
(26)
Выбор технологического варианта и типа электроконтактной установки
Выбор технологического варианта электроконтактного нагрева и соответственно выбор конструктивного типа нагревательной установки является одним из основных вопросов, который должен быть решен, как правило, перед проектированием конкретной установки определенной технологически-конструктивной группы.
В большинстве случаев технологический принцип или вариант нагрева определяет тип нагревательной установки, конструкцию и предопределяет принадлежность ее к соответствующей технологически-конструктивной группе. Но разнообразие конструктивных типов электроконтактных
установок данной группы
Рисунок 5.1 - График
приводит к необходимости выбирать установки с оптимальными данными, обеспечивающими наилучшие технико-экономические показатели: к. п. д., коэффициент мощности, стоимость нагрева, производительность и др.
Бывает, что, несмотря на меньшую массу металла, подлежащего нагреву, двухзональная установка оказывается менее рентабельной и эффективной, чем однозональная, на которой будет нагреваться заготовка по всей длине, включая и участок между зонами.
Вопрос о выборе конструкций установки должен быть решен в каждом отдельном случае применительно к конкретным условиям.
Покажем это на конкретном примере. Предположим, что по технологическим соображениям требуется нагреть заготовку в двух местах для гибки (рисунок 5.1). Участок заготовки /2
= 200 мм между нагреваемыми зонами можно не нагревать, так как это не требуется по условиям гибки.
Если остановить выбор на однозональной установке, т. е. нагревать заготовку по всей длине, включая и участок между зонами, то отношение длины к площади сечения /2
/s2
будет равно 2,4, а при двухзональном варианте установки — 1,6.
По графикам на рисунке 5.2 и 5.3 находим к. п. д. и коэффициент мощности для указанных значений /2
/s2
применительно к однозональнои и двухзональной установкам. Для первой ή= 0,67 и cosf1
= 0,65, а для второй ή= 0,46 и cosf 2
= 0,64.
Если принять полезную энергию для нагрева двух зон заготовки на двухзональной установке W2
, то расход энергии из сети будет:
(27)
Для однозональной установки потребный минимум энергии возрастет в 1,5 раза по сравнению с двухзональной установкой, поэтому энергия, потребляемая из сети однозональнои установкой, будет равна:
Wс1
=1,5 W2
/(ή1
cosf 2
) (28)
Расход активной и реактивной энергии, потребляемой из сети этими установками, практически одинаковый, несмотря на то, что на однозональнои установке нагревается большая масса металла; поэтому, учитывая сложность конструкции двухзональной установки и неудобство ее эксплуатации, целесообразно в подобных случаях применять однозональную установку.
Подобные примеры еще чаще встречаются при проектировании установок других технологически-конструктивных групп многозонального нагрева.
При проектировании установок сталкиваются с двумя основными вопросами: выбором технологического варианта нагрева и выбором конструктивного типа нагревательной установки данной технологически-конструктивной группы.
Определение коэффициента полезного действия
Для определения к. п. д. наиболее целесообразно расчеты производить в следующей последовательности:
1. Определить отношение длины к площади поперечного сечения нагреваемой детали.
2. По кривой 4 на рисунке 4.2 в соответствии со значениями отношений /2
/s2
определить предварительное оптимальное значение к. п. д., по которому найти другие характеристики или технические данные проектируемой установки с учетом того, что используемый в расчетах к. п. д. является оптимальным (если конкретный тип установки не выбран, а речь идет вообще о контактном нагреве).
3. Определить эксплуатационный к. п. д. в соответствии с расчетным отношением /2
/s2
в случае, если выбран конкретный тип одно- или двухзональной установок, конструкция которых
аналогична разработанным в НЙИТракторосельхозмаше, и если геометрические размеры нагреваемых зон соответствуют размерам, приведенным на рисунке 5.2. Эти значения к. п. д. следует рассматривать как минимальные, так как они соответствуют эксплуатационным данным одно- и двухзональных нагревательных установок.
4. Для установок других типов расчет к. п. д. производится по данным, соответствующим конкретной технологически-конструктивной группе установок. При отсутствии последних можно воспользоваться кривыми на рисунках 4.2 или 5.2.
Если ни один из перечисленных вариантов определения к. п. д. не может быть использован и требуется произвести подробные расчеты к. п.д. цепи установки и тепловой к. п. д., то следует воспользоваться формулами и рекомендациями, изложенными применительно к данным конкретным условиям.
Рисунок 5.2 - График
Однако следует иметь в виду, что для таких расчетов необходимо иметь конструктивные размеры всех элементов силовой цепи установки, а следовательно, почти полностью спроектированную установку. Для ориентировочных расчетов или оценки тех или иных характеристик или показателей, необходимых при проектировании, следует воспользоваться предварительными расчетно-эмпирическими кривыми (рисунок 4.2) и экспериментальными кривыми для соответствующей группы установок.
Определение коэффициента мощности
Следующим после к. п. д. техническим показателем электроконтактной установки является коэффициент мощности, который определяется в такой последовательности:
1. Находят отношение длины к сечению заготовки или заготовок (если в техническом задании речь идет о нескольких типоразмерах, нагреваемых на данной установке).
В соответствии с этим отношением по кривой рисунка 4.5 определяют коэффициент мощности, который следует считать оптимальным независимо от типа электроконтактной установки.
В том случае, когда выбран тип одно- или двухзональной установок обособленного нагрева, значения коэффициента мощности следует определять по кривым на рисунке 5.3, показывающим зависимость коэффициента мощности указанных электроконтактных установок НИИ Тракторосельхозмаша от отношения /2
/s2
для различных типоразмеров заготовок. При этом значения коэффициента являются минимальными и наиболее правильными.

Рисунок 5.3 - Зависимость коэффициента мощности
cos
f
1
электроконтактных установок обособленного нагрева от отношения
/2
/
s
2
.
1 —
для двухпозиционной установки при поочередном _нагреве заготовок
d
= 70 мм; 2 — то же при одновременном нагреве заготовок
d
= 60 мм 3 — для однозональной однопозиционной установки ЭУ-150,
U
= 180-360 мм; 4 — для двухпозиционной установки при поочередном нагреве заготовок длиной
l
2
= 850 мм; 5 — то же при одновременном нагреве заготовок длиной
l
2
= 850 мм', 6 — для однопозиционной двухзональной установки ЭУ-150 при нагреве заготовки с общей длиной нагреваемых зон
l
2
= 550-=-750 мм.
4. Для других типов установок коэффициент мощности следует брать по данным, соответствующим конкретной технологически- конструктивной группе.
5. После определения действительных конструктивных размеров элементов силовой цепи и конструкции установки можно произвести теоретический расчет коэффициента мощности по формуле (24), подставив в нее соответствующие значения общих со противлений установки, приведенных к сопротивлению первичной обмотки силового трансформатора. К теоретическому расчету следует прибегать только в том случае, если нельзя воспользоваться экспериментальными или эксплуатационными данными, приведенными выше. Такой расчет будет сугубо ориентировочным из-за целого ряда допущений, к которым при этом приходиться прибегать.
Расчет мощности нагревательной установки
После определения к. п. д. и коэффициента мощности можно перейти к расчету мощности нагревательной установки. При этом различают:
а)активную и реактивную мощности, потребляемые из сети нагревательной установкой;
б)активную и реактивную мощности, подводимые к нагреваемой детали.
Активная мощность определяется по формуле: (29)
.
Полная мощность, подводимая к нагреваемой детали, определяется по формуле: (30)
Где cosf2
коэффициент мощности нажимных контактах нагреваемой детали,
Определяемый по формуле: (31)
где r2
— активное сопротивление заготовки переменному току; z2
— полное сопротивление заготовки.
Поскольку активное сопротивление заготовки зависит от температуры, то и мощность изменяется в процессе нагрева.
Если в формулы (29), (30) и (31) подставить средние значения всех факторов, изменяющихся в процессе нагрева от температуры, то значения мощностей также будут средними.
Активная мощность, потребляемая из сети нагревательной установкой, определяется по формуле:
Pa
=( CG2
(t2
-t1
))/ή0
τ квт (32)
где ή0
— общий к. п.д.
Полная мощность', потребляемая из сети, определяется по формуле:
(33)
Значения к. п. д. и коэффициента мощности определяются по указанной выше методике.
Из сопоставления формул (30)—(33) видно, что активная и реактивная полные мощности, подводимые к заготовке, могут отличаться от таких же мощностей, потребляемых из сети, в зависимости от значения- теплового и общего к. п. д. и значения коэффициентов мощности нагрузки и установки. Разница в потребляемой мощности видна из кривых на рисунках 5.4 и 5.5; из фигур также видна зависимость коэффициентов мощности нагрузки и установки от диаметра детали и отношения длины к диаметру.
Следует иметь в виду, что определяемые по указанным формулам мощности являются средними за период нагрева.
Рисунок 5.4 – График Рисунок 5.5 - График
Для каждого данного момента времени они будут различны и соответствовать значениям сопротивлений заготовок и токов в них при температуре, относящейся к этому моменту времени. При проектировании целесообразно производить расчет мощности для начала и конца нагрева с тем, чтобы оценить, насколько значительны колебания мощности в процессе нагрева, а для этого необходимо знать сопротивления заготовки и всей цепи, а также температуру детали для соответствующего момента времени.
Расчет сопротивления нагреваемой детали
Активное и реактивное сопротивления' детали являются одними из основных и определяющих электротехнических характеристик (тока, напряжения, мощности и др.) режима нагрева и технических показателей электроконтактной нагревательной установки.
Определение электрического сопротивления деталей при электроконтактном нагреве осложняется наличием скинн-эффекта и зависимостью удельного сопротивления и магнитной проницаемости материалов от температуры.
Сопротивление детали переменному току находится в более сложной зависимости от геометрических параметров детали и магнитных свойств. Это объясняется своеобразной зависимостью магнитной проницаемости от температуры.
Активное сопротивление цилиндрической заготовки переменному току можно определить по формуле:
r2
/r0
=0.5ε0
(j0
(ε0
)/j1
(ε)) (34)
где r2
— активное сопротивление детали переменному току;
r 0
— то же постоянному току;
|
Здесь μ — магнитная проницаемость материала; μ0
= 4π-10-9
гн/см;
R2
— радиус цилиндрической заготовки в см;
ς2
— удельное электрическое сопротивление в ом-см;
j0
— функция Бесселя первого рода нулевого' порядка;
j1
— функция Бесселя первого рода первого порядка.
Зависимость активного сопротивления от отношения радиуса детали к глубине проникновения R2
/δ2
приведена на рисунке 5.6 (кривая 1)
Из рисунка 5.6 видно, что для R2
/δ2
от 0 до 1 активное сопротивление детали переменному току не отличается от сопротивления постоянному току, а для R2
/δ2
>1 оно отличается от последнего тем больше, чем больше значение R2
/δ2
.
На рисунке 5.6 приведены экспериментальные и расчетные кривые активных сопротивлений заготовок диаметром 12 и 35 мм в функции температуры по отношению к сопротивлению при 20° С.
Из рассмотрения кривых можно сделать следующие выводы:
1. С возрастанием температуры от 20 до 1000° С активное сопротивление заготовок диаметром 12 и 35 мм возрастает соответственно примерно в 2 и 4,5 раза, в то время как сопротивление их постоянному току в том же интервале температур возрастает в 9—10 раз. Это свидетельствует о существенном влиянии скинн-эффекта на сопротивление детали, находящейся при температуре ниже точки Кюри.
2. Степень возрастания сопротивления с температурой у заготовок диаметром 12 и 35 мм также подтверждает влияние скинн-эффекта.
В то время как сопротивление заготовки диаметром 35 мм, у которой скинн-эффект более резко выражен (отношение R2
/δ2
большое), возрастает всего в 2 раза, у заготовки диаметром 12 мм (R2
/δ2
меньше) оно возрастает уже в 4,5 раза.
Сопротивления указанных заготовок, вычисленные по формуле (34) с учетом изменения электрического сопротивления и магнитной проницаемости от температуры (μ = 200 при t= 200-760° С и μ = 1 при t = 760° С), несколько больше экспериментальных. Это, провидимому, объясняется тем, что абсолютное значение магнитной проницаемости и характер зависимости ее от температуры взяты отличными от расчетных.
 
Рисунок 5.6 – График Рисунок 5.7 - График
Следовательно, скинн-эффект при низких температурах существенно сказывается на активном сопротивлении.
Необходимо также считаться и с реактивным сопротивлением детали.
Реактивное сопротивление определяетсяпо формуле, аналогичной формуле (34).
Если графически выразить зависимость реактивного сопротивления от отношения R2
/δ2
, то получится кривая 2, изображенная на рисунке 5.6.
Модуль общего сопротивления нагреваемой детали определяется по известной формуле: (35)
При равенстве активного и реактивного сопротивлений полное сопротивление детали равно:
r2
= 1,4r2
= 1,41Х2
.
Приведенные выше формулы и графики справедливы для цилиндрических деталей. В общем случае для любого сечения, например для сечения прямоугольной формы, можно воспользоваться формулами, рекомендуемыми проф. Л. Р. Нейманом.
Активное сопротивление детали:
. (36)
Реактивное сопротивление:
. (37)
Полное сопротивление:
(38)
где l2
— длина нагреваемой детали в см;
и2
— периметр поперечного сечения детали в см;
μ — магнитная проницаемость материала;
ς2
—удельное электрическое сопротивление в .ом-см;
f— частота тока.
Из всех переменных, входящих в формулы (36)—(38), неизвестной является магнитная проницаемость. Так как она определяется неоднозначно в зависимости от напряжения магнитного поля (тока) и гистерезиса, а последние зависят еще и от температуры, то найти ее весьма затруднительно.
Поэтому для расчета сопротивления заготовок, находящихся в холодном состоянии, следует брать определенное значение магнитной проницаемости для данной стали и считать ее постоянной до температуры 750—780 °С, а свыше этой температуры — равной единице.
Определение напряжения на нагреваемой детали
Напряжение на нагреваемой детали необходимо знать для определения вторичного напряжения силового трансформатора, так как без этого нельзя рассчитать число витков обмоток последнего.
Напряжение, потребное на заготовке для нагрева ее до заданной температуры, определяется по формуле: (39)
где z2
— определяется по формуле (38);
P2
— определяется по формуле (29);
r2
— определяется по формуле (36).
В случае, когда скинн-эффектом можно пренебречь (при температуре нагрева выше точки Кюри для заготовок диаметром до 70 мм), формулу (39) можно выразить через параметры детали и теплоемкость:
. (40)
В которой постоянный коэффициент зависит от удельного веса материала нагреваемой детали. Для стали его можно принять равным 6.
Следовательно, напряжение на детали, не зависит от ее поперечного сечения, а зависит только от ее длины (пропорционально длине).
Другим фактором, от которого зависит напряжение на детали, является время нагрева τ.
После определения теплового к. п. д. ήt
для выбранного типа нагревательной установки по кривой 2 на рисунке 4.2 и зная среднюю теплоемкость, а также среднее удельное электрическое сопротивление, можно по формуле (40) найти напряжение, потребное для данной заготовки.
Рассчитанное по этим формулам напряжение будет достаточно точным и обеспечивающим требуемый режим электроконтактных установок обособленного нагрева. Для установок других технологически-конструктивных групп, таких как установки для набора металла или установки, в которых совмещается набор металла с высадкой, расчет напряжения на заготовке должен производиться с учетом особенностей нагрева на этих установках.
Расчет тока, потребного для нагрева детали
Для нагрева данной конкретной детали или заготовки с установленной скоростью необходимо пропустить через нее вполне определенный электрический ток.
Потребный ток определяется по формуле: (41)
Так как и2
и z2
известны из формул (40) и (41), то вычислить потребный ток нетрудно.
Для вычисления тока в начальный, конечный периоды нагрева или в любой другой момент времени в формулу (41) необходимо подставить соответствующее этому моменту значение полного сопротивления z2
; если влиянием скинн-эффекта можно пренебречь, то активное сопротивление r2
можно вычислить по известной формуле с учетом возможного повышения температуры.
После определения конструктивных размеров элементов силовой цепи и всей.установки рассчитывают по ним более точно значения сопротивления r2
и z2
, а по формуле (41) находят величину тока.
Расчет сечения токоподводящих шин
Площадь сечения шин вторичной силовой цепи электроконтактной установки определяется с учетом следующих условий:
1. Длина шины выбирается (насколько это возможно по конструктивным соображениям) минимальной.
2. Толщина шины не должна превышать 30—35 мм, так как увеличение толщины из-за наличия скинн-эффекта вызывает излишний расход материала.
Масса материала оказывает влияние на тепловые характеристики: чем она больше, тем больше требуется тепловой энергии для повышения ее температуры на 1° С. Поэтому при одних и тех же потерях в шинах повышение температуры тем меньше, чем больше масса шины. Но это продолжается только до установления стационарного состояния.
3. Одна из шин в большинстве случаев должна быть гибкой, если она крепится к подвижной зажимной головке. Поэтому такая шина должна набираться из медной полосовой фольги.
4. Так как электрические токи в шинах вторичной цепи нагревательных установок довольно велики, то при обычных допустимых плотностях тока сечения шин будут слишком большие. Поэтому все жесткие шины следует охлаждать водой и предусматривать плотности, которые в 2—2,5 раза больше плотностей, допускаемых для шин с естественным охлаждением воздухом.
5. Для гибких шин, не охлаждаемых водой, при расчете площади поперечного сечения рекомендуется принимать удельную плотность тока 3—2,5 а/мм2
.
6. Расчетным током служит ток, определяемый по формуле:
I2
P
= I2
√kn
.в
,(42)
где I2
— ток, определяемый по формуле (41), при подстановке в нее средних значений напряжения на заготовке u2
и полного сопротивления последней z2
;
kn
.в
— показатель повторно-кратковременного режима, определяемый как отношение времени нагрева к общему времени цикла работы установки с учетом времени, которое затрачивается на загрузочно-разгрузочные, транспортные, машинные и другие операции и паузы между ними.
Показатель kn
.в
выраженный в процентах, обычно называется коэффициентом повторного включения.
При проектировании установок большой мощности с малым вторичным напряжением ширина шин Может получиться настолько большой, что по конструктивным условиям гибкую шину вообще нельзя или очень трудно выполнить. В случае, если необходимо иметь гибкую шину, то придется идти на некоторое увеличение ее сечения или на применение воздушного искусственного охлаждения. Жесткие шины охлаждаются водой и используются при применении токов большой плотности.
Необходимо при этом иметь в виду, что увеличения плотности тока в 2—2,5 раза и больше в шинах не следует опасаться, так как потери и к. п. д. в электроконтактных установках определяются в основном сопротивлением переходных контактов и других элементов цепи.
5. Основные технико-экономические показатели электроконтактного способа нагрева
Основными технико-экономическими показателями всякого способа нагрева являются: 1) скорость нагрева; 2) к. п. д. нагревательных устройств; 3) стоимость нагрева; 4) качество металла после нагрева; 5) стоимость штампов и 6) коэффициент мощности для электронагревательных установок.
Скорость нагрева. Вопрос о скорости электроконтактного нагрева был довольно подробно рассмотрен в гл. I, здесь достаточно будет сослаться на то, что последующие расчеты и данные, касающиеся установления зависимости технико-экономических показателей электроконтактного способа от параметров нагреваемых заготовок, справедливы для условия, когда время нагрева определяется по формуле:
τ = d2
2
cek,(42)
где d2
— диаметр заготовки в см.
Продолжительность электроконтактного нагрева, определяемая по формуле (42), является примерно средней между применяемой в настоящее время на практике и той, которая может быть использована для заготовок диаметром 20—100 мм при перепаде температур по длине и сечению, равном 100 °С.
К. п. д. электроконтактной установки зависит прежде всего от технологической группы и конструктивного типа последней и от геометрических параметров нагреваемой заготовки.
Сопоставление показателей при электроконтактном нагреве с показателями при других способах нагрева можно сделать только при условии, если речь идет об установках обособленного нагрева технологической группы I, установки же других технологических групп не являются нагревательными устройствами в том смысле, в каком обычно говорят об индукционных или о пламенных печах.
Общий к. п. д. можно определить из формулы
где к. п. д. трансформатора ήтр
не зависит от геометрических размеров заготовок и равен ~0,94.
С помощью формул (21) и (22) и (42) можно вычислить общий к. п. д. электроконтактного нагрева для заготовок различных типоразмеров.
На рисунке 6.1 приведены кривые зависимости общего к. п. д. установок электроконтактного нагрева от диаметра нагреваемых заготовок. Если при электроконтактном нагреве соблюдается условие l2
/d2
> 1, то общий к. п. д. практически не зависит от диаметра заготовок при соблюдении условия формулы (42).
Стоимость электроконтактного нагрева. При электроконтактном способе нагрева на установках технологической группы Iрасходы на нагрев 1 т металла складываются из одних и тех же статей, что и при других способах: стоимости энергоносителя (электроэнергии), затрачиваемой на нагрев 1 т металла, амортизационных расходов, стоимости обслуживания, стоимости воды и воздуха, расходуемых при нагреве 1 т.
Стоимость электроэнергии при электроконтактном нагреве определяется из формулы:
Сэ
= (Wmin
/ ήо
)Сэ1
,.(43)
где Wmin
— теоретический минимум энергии, необходимой для нагрева 1 т металла до соответствующей температуры (1100 0
С), в квт-ч/т;
ήо
— общий к. п. д. нагревательного устройства;
С э1
— стоимость 1 квт-ч электроэнергии.
Рисунок 6.1 - Зависимость общего к. п. д. установок для электроконтактного нагрева от диаметра заготовок:
1 —
l
2
/
d
2
2
= 1; 2 —
l
2
= 1000 мм; 3 —
l
2
= 100 мм.
Если использовать к. п. д., выраженный кривыми на рисунке 6.1, то получим кривые 1, 2, 3 на рисунке 6.2, показывающие зависимость стоимости электроэнергии, расходуемой на 1 т металла заготовок длиной 200 и 1000 мм, от различных условий.
Из этих кривых видно, что при соблюдении условия l2
/ d2
2
= 1 стоимость электроэнергии не превышает 3,5 руб/т независимо от диаметра заготовок.
Амортизационные расходы на оборудование электронагревательных устройств складываются из амортизационных отчислений от общей стоимости оборудования и от стоимости его капитального ремонта в год.
Электроконтактные установки изготовляют мелкими сериями не специализированными организациями, поэтому стоимость их, несмотря на простоту конструкции, сравнительно велика.
Амортизационные расходы при электроконтактном нагреве определяют из формулы:
. (44)
Где Сн
— стоимость электроконтактной установки в руб.; а3
— процент амортизационных отчислений; Ср — стоимость годового ремонта электроконтактной установки в руб.;
а0
— число часов работы установки в год;
Рн
— номинальная мощность установки в кет;
cos φ — коэффициент мощности установки.
Рисунок 6.2 - Зависимость стоимости электроэнергии и воды при нагреве от диаметра заготовок:
1 —
l
2
/
d
2
2
= 1; 2 —
l
2
= 200 мм; 3 —
l
2
= 1000 мм стоимость электроэнергии; 4 —
l
2
/
d
2
2
=1; 5 —
l
2
=
200 мм
; 6
— 10
= 1000 мм, стоимость воды
Данные на рисунке 6.2 справедливы только при следующих значениях членов в формуле (44) и постоянном коэффициенте, равном 0,5: а3
= 10% , Сн
= 7500руб., Wmin
= 192 квт-ч, Рн
= 250ква, Ср
= 1000 руб., а0
= 4200 ч, cos φ = 0,8. Из этой формулы следует, что амортизационные расходы на 1 т нагреваемого металла при электроконтактном нагреве не больше 1 руб., если l2
/ d2
2
= 1. Стоимость электроэнергии в 5 раз больше амортизационных расходов.
Стоимость обслуживания электроконтактных установок. При определении стоимости обслуживания принимается, что один нагревальщик обслуживает двенагревательные установки мощностью 250 ква каждая. Тогда можно принять, что средняя часовая заработная плата рабочего с учетом отчислений на специальное страхование составит 0,615 руб/ч.
С учетом производительности нагревательной установки, коэфициента мощности и общего к. п. д. расходы на обслуживание могут быть определены из формулы:
. (45)
где Сч
= 0,615 руб/ч — часовая заработная плата нагревальщика;
Кц
— коэффициент, учитывающий долю расхода на общецеховой персонал.
Ориентировочно можно принять Кц
— 1,1 (10% от заработной платы нагревальщика). Стоимость обслуживания может быть найдена по формуле для расчета стоимости амортизационных расходов.
Стоимость воды, расходуемой на охлаждение электроконтактных установок. Электроконтактные нагревательные установки потребляют большое количество электрической энергии; в токоведущих элементах, охлаждаемых водой, наблюдаются значительные тепловые потери. Поэтому для охлаждения этих элементов требуется соответствующее количество воды, которое зависит от тепловых потерь.
Так как тепловые потери учитываются электрическим к. п. д., то потребное количество воды и стоимость ее на 1 т металла можно определить в зависимости от к. п. д. установки, а следовательно, и от геометрических размеров заготовки. Стоимость воды, отнесенную к 1 т металла, можно вычислить по формуле:
(46)
Где - Wmin
теоретический минимум энергии, необходимый для нагрева 1 т металла до температуры 1200 0
С в квт-ч;
∆t — разность температур воды на входе и выходе из охладительной системы установки.
Постоянный коэффициент в формуле соответствует условию, когда
∆t = 25° С и с4
= 0,6 коп/м3
воды.
Пользуясь кривыми, приведенными на рисунке 6.1 для к. п. д. ήо
, и значениями электрического к. п. д., получим стоимость воды, отнесенную к 1 т металла, в зависимости от диаметра нагреваемых заготовок (кривые 4—6 на рисунке 6.2).
Из формулы (46) и кривых на рисунке 6.2 видно, что стоимость воды, отнесенная к 1 т металла, не превышает 0,3 руб. при l2
/ d2
2
= 1.
Следовательно, все основные статьи расходов, связанные с нагревом металла, учтены.
В отдельных случаях приходится учитывать стоимость штампов, но так как в настоящее время нет даже сколько-нибудь надежныхданных, касающихся стойкости штампов при различных способах нагрева, основаны на эксплуатации электроконтактных установок Горьковского автозавода с радиальными зажимными контактами, непригодных для нагрева заготовок под объемную штамповку, то здесь принимается, что износ штампов будет одинаковый при всех способах нагрева.
Общая стоимость нагрева. Из указанных выше статей расходов складывается общая стоимость нагрева 1 т металла электроконтактным способом:
Рисунок 6.3 - Зависимость общей стоимости нагрева электроконтактным способом от диаметра заготовок
1 —
l
2
/
d
2
2
= 1; 2 —
l
2
= 1000 мм; 3 —
l
2
= 200 мм
На рисунке 6.3 приведены кривые, показывающие зависимость стоимости нагрева 1 т металла от диаметра нагреваемых заготовок.
Сопоставление технико-экономических показателей двух способов нагрева
Приведенные выше экспериментально-расчетные данные двух электрических способов сквозного нагрева металлов и рассмотрение условий, которым они соответствуют, позволяют сопоставить основные и наиболее важные их технико-экономические показатели.
Скорость нагрева. Зависимость времени (продолжительности)
нагрева заготовок от их диаметра для указанных двух способов нагрева приведена на рисунке 6.4.
Рисунок 6.4
-
Зависимость времени нагрева заготовок различными способами от диаметра последних: 1 — электроконтактный; 2 — индукционный.
Скорость индукционного нагрева соответствует оптимальной частоте и температурному перепаду между центральной и периферийными зонами, равному не более ∆t = 100° С (экспериментальные кривые на рисунке 6).
Значения скоростей электроконтактного способа нагрева соответствуют эксплуатационным значениям скоростей действующих установок (кривая 3 на рисунке 8).
Коэффициент полезного действия. Для сопоставления к. п. д. двух этих способов нагрева на рисунке 6.5 приведена зависимость общих расчетно-эмпирических к. п. д. от диаметра нагреваемыхзаготовок.
Так как к. п. д. электроконтактных установок находится в зависимости от длины заготовок при одном и том же диаметре, то на фигуре приведены кривые для l2
= 100 мм и l2
= 1000 мм и для оптимального условия, соответствующего отношениюl2
/ d2
2
>= 1.
Из фигуры видно, что, начиная со значения отношения l2
/ d2
2
= 1,0, к. п. д. электроконтактных установок примерно в 1,5— 2 раза больше к. п. д. индукционных установок.
К. п. д. индукционных установок при оптимальной частоте и постоянном зазоре между катушкой индуктора и заготовкой (25 мм) имеет наибольшее значение и равен 0,42—0,44 , для заготовок диаметром 30—100 мм; при изменении диаметра заготовок в ту или иную сторону к. п. д. уменьшается до 0,25—0,3.
Стоимость нагрева 1 т металла. При сопоставлении стоимости нагрева 1 т металла для рассматриваемых способов нагрева необходимо иметь в виду, что она зависит от геометрических параметров нагреваемых заготовок и нагревательного устройства.
На рисунке 6.6 приведена зависимость стоимости нагрева 1 т металла от диаметра нагреваемых заготовок для рассматриваемых способов нагрева.
Рисунок 6.5 - Зависимость общего к. п. д. для различных способов нагрева от диаметра заготовок:
1 — для индукционного; 2 —
l
2
/
d
2
2
= 1; 3 —
l
2
= 100 мм;
4 —
l
2
= 1000 мм для электроконтактного способа нагрева.
Приведенные данные позволяют сделать следующие выводы:
1.Из двух электрических способов сквозного нагрева заготовок с поперечными сечениями до 100 мм и длиной более 150 мм электроконтактный способ является экономичнее индукционного.
2.При l2
/ s2
>= 1 электроконтактный нагрев в 1,5—2,0 раза дешевле индукционного.
3.Стоимость нагрева 1 т металла индукционным способом наибольшая для заготовок малого диаметра, наименьшая для заготовок среднего диаметра (40—75 мм).
4.К. п. д. этих способов нагрева, а следовательно, и стоимость нагрева 1 т металла зависят от геометрических параметров нагреваемых заготовок.
Для получения наибольшего значения к. п. д. и большей производительности нагревательного устройства при индукционном способе необходимо иметь оптимальную частоту тока, при этом следует соблюдать условие l2
/ δ2
> 5/6, а при электроконтактном способе — условие l2
/s2
> 1 при прочих равных условиях.
5. При индукционном способе нагрева существенное значение имеет эксплуатационный к. п. д. индукционного устройства, включая генератор, питающий нагревательный индуктор или несколько индукторов; работа их вхолостую или с неполной нагрузкой значительно снижает к. п. д.
При электроконтактном способе нагрева понятие эксплуатационного к. п. д. теряет свой обычный смысл, так как электроконтактные установки не работают вхолостую, при выключении нагрева трансформатор отключается от сети и энергия из сети не потребляется.
Рисунок 6.6 - Зависимость стоимости нагрева 1 т металла различными способами от диаметра заготовок:
1 — для индукционного способа нагрева; 2 —
l
2
/
d
2
2
= 1; 3 —
l
2
= 100 мм; 4 —
l
2
= 1000 мм для электроконтактного нагрева
Приведенные технико-экономические показатели позволяют сделать вывод о том, что электроконтактный способ является технически наиболее совершенным, экономически более эффективным и рентабельным; конструкция нагревательных установок наиболее проста и удобна в эксплуатации по сравнению с индукционными и печными установками.
Однако это ни в какой степени не снижает ценности индукционного способа при применении его в тех областях, в которых индукционный принцип передачи энергии в нагреваемую массу металла является единственно целесообразным — при нагреве коротких мерных заготовок диаметром более 50 мм под объемную штамповку, при нагреве для поверхностной закалки, сквозном нагреве заготовок с большим поперечным сечением (более 100 мм) и для других технологических операций.
Весьма существенное значение имело бы сопоставление технико-экономических показателей электрических способов нагрева с печным, но сделать это в общем виде, подобно произведенному выше, для рассмотренных способов крайне затруднительно, поэтому практически производится сопоставление для каждого конкретного случая отдельно.
Заключение
Приведенные технико-экономические показатели позволяют сделать вывод о том, что электроконтактный способ является технически наиболее совершенным, экономически более эффективным и рентабельным; конструкция нагревательных установок наиболее проста и удобна в эксплуатации по сравнению с индукционными и печными установками.
Современное развитие машиностроения связано все с большим применением труднообрабатываемых материалов, деталей сложной конфигурации, большая часть из которых имеет низкую производительность при механической обработке. Одним из перспективных направлений новых технологий, позволяющих значительно увеличить производительность обработки, а также стойкость инструментов является электроконтактная обработка, сущностью которой является создание искусственного источника тепла в зоне обработки от ввода технологического тока, что, в свою очередь, ведет к увеличению производительности обработки в несколько раз. Следует также иметь в виду, что электроконтактная обработка не только позволяет получать поверхности высокой точности и низкой шероховатости, но и при необходимости упрочнять поверхностный слой детали. Для получения же аналогичного качества поверхности при лезвийной обработке требовалась дополнительная термическая обработка поверхностей.
Одним из наиболее эффективных способов термической интенсификации рассматриваемого процесса является нагрев деформируемого профиля, позволяющий повысить пластические свойства материала заготовки. На Комсомольском-на-Амуре авиационном производственном объединении освоен процесс гибки профилей с растяжением на станке ПГР-7 с применением электроконтактного нагрева заготовки, позволяющий существенно повысить точность изготовления деталей из высокопрочных материалов.
Установка работает так: заготовку устанавливают в изолированные от корпуса зажимные патроны, к которым с помощью специальных шин от силовых трансформаторов типа ТКП 150/2 подводится электрический ток, после чего производится электроконтактный нагрев профиля до необходимой температуры. Затем заготовка подвергается предварительному растяжению и обтяжке по пуансону до заданных размеров. После окончания изгиба выключают нагрев и прикладывают к концам заготовки калибрующее усилие. При этом профиль находится на оправке до полного остывания. Благодаря тому, что профиль изолирован от корпуса с одной стороны асбестовой тканью, а с другой - асбоцементной прокладкой, которые обладают низкой теплопроводностью, удается осуществить обтяжку в нагретом состоянии, что практически полностью устраняет пружинение и повышает точность. Корректировка оснастки и промежуточный отжиг в печах при этом не требуется.
Таким образом, разработанный и внедренный в производство технологический процесс и оснастка для его реализации позволяют повысить точность изготовления гнутых из профилей деталей без корректировки формообразующей оснастки и повысить производительность за счет исключения ручных доводочных операций, что особенно важно для высокопрочных материалов.
Список использованной литературы
1. Романов Д.И. Электроконтактный нагрев металлов 2-е изд., перераб. и доп. - М. Машиностроение, 1981г. – 166 с.
2. Алиферов А.И., Лупи С. Электроконтактный нагрев. – Новосибирск: Изд-во НГТУ, 2004г. – 224 с.
3. Хасин Г.А., Дианов А.И., Попов Т.П. - М.: Металлургия, 1984г. - 284с.
4. Болотов А.В., Шепель Г.Л., Электро- технологические установки.- М. Машиностроение, 1980г. – 160 с.
5. Мостовяк И.В. Цепи уравновешивания режимов трёхфазных систем с установками электроконтактного нагрева. - Киев. ИЭД, 1988г. - 266с.
6. Болотин И.Б., Эйдель Л.З. Измерения в переходных режимах короткого замыкания. - Л.: Энергия, 1981г. -192с.
|