В
ведение
В настоящее время в нашей стране сложилась такая ситуация, что развитие промышленности является самой приоритетной из всех поставленных задач. Для того, чтобы Россия заняла прочное место среди ведущих мировых держав, в ней должна существовать развитая сфера промышленного производства, которая должна основываться не только на восстановлении основанных в советский период заводов, но и на новых, более современно оборудованных, предприятиях.
Одним из важнейших шагов на пути к экономическому процветанию является подготовка специалистов, которые имели бы не строго ограниченные рамками своей профессии знания, а могли комплексно оценить выполняемую ими работу и ее результат. Такими специалистами являются инженеры-экономисты, разбирающиеся не только во всех тонкостях экономических аспектов функционирования предприятия, но и в сущности производственного процесса, который и обуславливает это функционирование.
Целью данного дипломного проекта является ознакомление непосредственно с процессом производства, а также оценка и сравнение его эффективности не только с экономической, но и с технологической точек зрения.
Производство изделия, его сущность и методы оказывают наиболее весомое влияние на технологические, эксплуатационные, эргономические, эстетические и, конечно, функциональные характеристики этой продукции, а, следовательно, на его себестоимость, от которой в прямой зависимости находятся цена изделия, спрос на него со стороны пользователей, объемы продаж, прибыль от реализации, а, следовательно, все экономические показатели, которые и определяют финансовую устойчивость предприятия, его рентабельность, долю рынка и т.д. Таким образом, то, как изготовляется продукция, оказывает влияние на весь жизненный цикл товара.
Сегодня, когда конкурентный рынок вынуждает производителей переходить к наиболее качественным и дешевым продуктам, особенно важно оценить все аспекты производства, распространения и потребления изделия еще на стадии его разработки, чтобы избежать неэффективного использования ресурсов предприятия. Это помогает также в совершенствовании технологических процессов, которые разрабатываются часто не только исходя из потребностей рынка в изготовлении новый продукции, но и принимая во внимание стремление производителей к более дешевому и быстрому способу получения уже существующей продукции, что сокращает производственный цикл, уменьшает величину связанных в производстве оборотных средств, а, следовательно, стимулирует рост инвестиций в новые проекты.
Итак, проектирование технологического процесса является важнейшим этапом производства продукции, который влияет на весь жизненный цикл товара и способен стать определяющим при принятии решения о производстве того или иного продукта.
1. Разработка технологического процесса
1.1 Служебное назначение и техническая характеристика изделия и детали
Деталь «Крышка ТМ966 Сб2120-5СБ» (рис. 1) является одной из сборочных единиц гидравлической установки для ЗРК «Печора-2М». Характерными особенностями детали является то, что она представляет собой буксу (переднюю крышку) гидроцилиндра. По наружной резьбе М210х3 и торцу 8 сопрягается с цилиндром 5П73-75. По внутренней поверхности через бронзовую втулку со штоком 5П73-72. На торце детали имеются резьбовые отверстия М6, для крепления крышки манжеты.
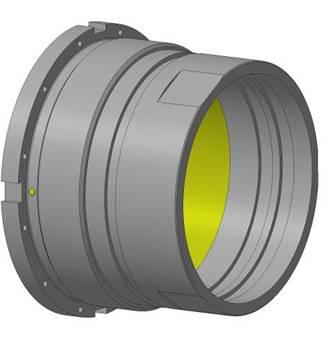
Рис. 1. Общий вид детали ТМ966. Сб2120-5СБ
В качестве материала для изготовления заготовки «Корпус» применяется сплав стали 30ХГСА ГОСТ 4543-71. Применяется для изготовления валов, осей, зубчатых колес, фланцев и др. Это улучшаемые детали, работающие при температуре до 200ºС, ответственные сварные конструкции, работающие при знакопеременных нагрузках, крепежные детали, работающие при низких температурах.
Таблица 1. Химический состав в % материала 30ХГСА
Si |
S |
Cu |
Mn |
CR |
P |
C |
Ni |
0,9…1,2 |
0,025 |
0,3 |
0,8…1,1 |
0,8…1,1 |
0,025 |
0,28…0,34 |
0,30 |
Механические свойства
Предел прочности при растяжении МПа
Относительное удлинение после разрыва 7% (стабилизирующий отпуск 220°)
Плотность, 7б85 кг/см3
Твердость по Бринеллю, HB=487
Шероховатость: для поверхностей детали высота неровностей профиля от
Rа = 0,8 мкм до Rа=6,3 мкм.
Степень точности: наименьший квалитет 7.
В качестве материала для изготовления заготовки «Втулка» применяется безоловянная бронза БрАЖН 10-4-4 ГОСТ 1280-90.
Таблица 2. Химический состав в % материала БрАЖН 10-4-4
Fe |
Si |
Mn |
Ni |
P |
Al |
Cu |
Pb |
Zn |
Sn |
Примесей |
3.5 - 5.5 |
До 0.1 |
до 0.3 |
3.5 - 5.5 |
до 0.01 |
9.5 - 11 |
77 - 83.5 |
до 0.02 |
до 0.3 |
до 0.1 |
всего 0.6 |
1.2 Постановка задачи на проектирование
Совершенствование качества продукции невозможно без чёткой работы всей производственной цепочки от маркетинговых условий до реализации продукции потребителю, от изучения дефектов, возникающих у потребителя в процессе эксплуатации, до внесения коррективов и в технологический процесс, устраняющий эти дефекты.
Изготовления детали осуществляется на основании анализа конструкции и технологичности изделия и его деталей, а также годовой программы выпуска.
С целью обеспечения повышенной надежности работы детали, организации высокопроизводительного процесса обработки её поверхностей необходимо решить следующие задачи:
1. на основе критического анализа существующего технологического процесса разработать более эффективный процесс изготовления детали;
2. предусмотреть возможность широкого использования высокопроизводительного оборудования, режущего инструмента и технологической оснастки;
3. разработать проект токарно-фрезерного с ЧПУ участка по изготовлению деталей;
4. наметить мероприятия по охране окружающей среды и безопасности жизнедеятельности работников цеха и по увеличению ресурса деталей;
5. определить технико-экономические показатели работы участка.
Проектируемый технологический процесс должен иметь более высокие показатели по сравнению с базовым процессом.
1.3 Анализ технологичности конструкции детали
Рабочие чертежи обрабатываемых деталей ТМ966.2120-35 и ТМ966.2120-36 содержат все необходимые сведения, дают полное представление о деталях, т.е. все проекции, разрезы, сечения чётко и однозначно объясняют их конфигурацию и возможные способы получения заготовок.
Показаны размеры с необходимыми отклонениями, требуемая шероховатость обрабатываемых поверхностей, допускаемые отклонения от правильных геометрических форм, а также относительного расположения поверхностей.
При анализе чертежа ТМ966.2120-35 выявили следующее:
Основными конструкторскими базами
являются: наружная цилиндрическая поверхность №3 D200 и торец №8. Поверхность №3 выполнена по 9 квалитету точности, с допуском на размер 0,115 мм, с шероховатостью 2.5 мкм.
Вспомогательными конструкторскими базами
являются:
— внутренняя цилиндрическая поверхность №14 D190. Отверстия №14 выполняется с допуском на размер 0,072 мм и шероховатостью 2,5 мкм. На последующих операциях в отверстие №14 запрессовывается бронзовая втулка – это способствует снижению износа штока;
— канавка №4 D193, выполняется по 8 квалитету точности, с допуском на размер 0,072 и шероховатостью 2,5 мкм;
— торец №10 выполняется с радиального биения 0,08 мм относительно базы Е (поверхность №3);
— торец канавки №15 выполняется с допуском на размер 0,74 мм, с допуском радиального биения 0,1 мм относительно базы Ж (поверхность №14);
Вышеперечисленные основные и вспомогательные базы связаны между собой допусками:
— допуск радиального биения поверхности №14 относительно базы Е (поверхность №3) 0,3 мм;
— допуск радиального биения торца №8 относительно Е 0,1 мм;
— допуск радиального биения наружной поверхности резьбы №5 относительно базы Е 0,1 мм;
— допуск радиального биения диаметра канавки №4 относительно базы Е 0,08 мм;
Сложность изготовления детали «Корпус» обусловлена высокими требованиями к соосности под уплотнения (канавка №4) и опорно-направляющую втулку (поверхность №14) относительно посадочного места в цилиндр (поверхность №3).Из всех поверхностей детали «Корпус» наименее технологичной является канавка №4. Причин низкой технологичности несколько: высокие требования к шероховатости посадочного места уплотнения 2,5 мкм, к соосности диаметра канавки относительно базы Е 0,08 мм, выполнение размера D193 мм по 8 квалитету точности.
Перед началом разработки технологического процесса необходимо оформить технологический чертёж детали, изображающий деталь без размеров, с присвоением номера каждой поверхности подлежащей обработке.

Рис. 2. Технологический чертеж детали «Корпус»

Рис. 3. Технологический чертеж детали «Втулка»
1.4 Выбор и обоснование типа производства
Тип производства согласно ГОСТ 3.1108–74 характеризуется коэффициентом закрепления операции за одним рабочим местом или единицей оборудования:
,
где N – число различных операций, выполняемых в течении календарного времени; Pm – число рабочих, на которых выполняются данные операции.
Типы производства характеризуются следующими значениями коэффициентов закрепления операций:
Тип производства |
Кз.о |
Массовое |
1 |
Серийное: |
крупносерийное |
Свыше 1 до 10 |
среднесерийное |
Свыше 10 до 20 |
мелкосерийное |
Свыше 20 до 40 |
Единичное |
Свыше 40 |
Тип производства характеризуется коэффициентом закрепления операций, который показывает число различных операций, закрепленных в среднем по цеху (участку) за каждым рабочим местом в течение месяца.
Для расчета коэффициента закрепления операций составим таблицу №3. В первую графу запишем все операции базового техпроцесса, во вторую нормы времени.
Определим и запишем в третью графу таблицы расчетное количество mp для каждой операции:
,
где N – годовой объем выпуска деталей, шт;
tшт – штучное время, мин.;
Fд – действительный годовой фонд времени, ч (действительный годовой фонд времени при двухсменной работе Fд = 3876 ч = 232560 мин)
hз.н. – нормативный коэффициент загрузки оборудования (0,75…0,85).
m10=180*4,28/60/3876/0,75=0,010
m20=180*7,8/60/3876/0,75=0,016
m30=180*24,9/60/3876/0,75=0,026
m40=180*4,5/60/3876/0,75=0,012
m80=180*4,32/60/3876/0,75=0,013
m90=180*40,11/60/3876/0,75=0,052
m100=180*18,7/60/3876/0,75=0,019
m110=180*5,6/60/3876/0,75=0,012
m120=180*6,1/60/3876/0,75=0,014
m130=180*20/60/3876/0,75=0,028
Принятое число рабочих мест P (четвертая графа) устанавливаем, округляя значение mp (третья графа) до ближайшего большего целого числа.
Далее для каждой операции вычисляем значения фактического коэффициента нагрузки.
.
Количество операций (последняя графа), выполняемых на рабочем месте, определяется по формуле:
,










Коэффициент закрепления операций рассчитывается по формуле:

Таблица 3. Расчет коэффициента закрепления операций
№ |
Наименование операции |
Модель станка |
Тшт, мин |
mр |
P |
з.н. |
10 |
Заготовительная |
Hercules |
10,1 |
0,010 |
1 |
0,010 |
54,00 |
20 |
Токарно-винторезная |
1М63 |
15,3 |
0,016 |
1 |
0,016 |
47,50 |
30 |
Токарно-винторезная |
1М63 |
24,9 |
0,026 |
1 |
0,026 |
29,19 |
40 |
Токарно-винторезная |
1М63 |
11,6 |
0,012 |
1 |
0,012 |
47,65 |
80 |
Токарно-винторезная |
1М63 |
12,3 |
0,013 |
1 |
0,013 |
51,09 |
90 |
Токарная с ЧПУ |
16К30 NC 210 |
50,11 |
0,052 |
1 |
0,052 |
14,50 |
100 |
Токарная с ЧПУ |
16К30 NC 210 |
18,7 |
0,019 |
1 |
0,019 |
28,86 |
110 |
Вертикально-фрезерная |
6Р12 |
11,2 |
0,012 |
1 |
0,012 |
59,89 |
120 |
Вертикально-фрезерная |
6Р12 |
13,4 |
0,014 |
1 |
0,014 |
39,24 |
130 |
Радиально-сверлильная |
2Н55 |
27,5 |
0,028 |
1 |
0,028 |
26,43 |
Итого |
– |
– |
– |
10,00 |
– |
398,35 |
SP = 10, S = 398,35.
.
Коэффициент закрепления операций технологического равен 39,83, следовательно, производство корпуса будет мелкосерийным.
1.5 Выбор вида и способа получения заготовки. Технико-экономическое обоснование
1. Определение размеров заготовки из круглого проката.

Рис. 4 Деталь «Корпус»
МЦХ
Корпус
Площадь S = 228316.726 мм2
Объем V = 982603.684 мм3
Материал Сталь 30ХГСА ГОСТ 4543-71
Плотность Ro = 0.00785 г/мм3
Масса M = 7713.439 г
МД=7,713 кг, NT=180 шт/г, тип производства мелкосерийное.
Размеры труб-заготовок для последующей механической обработки выбираем, исходя из размеров готового изделия, в соответствии с приложением ГОСТ 23270-89. Расчетный размер округляем до ближайшего стандартного в соответствии с табл. 1 ГОСТ 23270-89.
Выбираем трубу с наружным диаметром 245 мм, с толщиной стенки 45 мм, из стали 30ХГСА:
Труба 245 ´ 45 – 30ХГСА ГОСТ 23270-89
Предельные отклонения по наружному диаметру, толщине стенки и
отклонения по длине труб - по ГОСТ 8732-78 «Трубы стальные бесшовные горячедеформированые» табл. №1 и №2. Точность проката назначаем В – обычной точности, так как производство мелкосерийное.
Ø245±1,25% мм
45±12,5% мм
Кривизна любого участка трубы на 1 м длины не должна превышать 1,5 мм – для труб с толщиной стенки до 20 мм; 2,0 мм – для труб с толщиной стенки свыше 20 до 30 мм; 4,0 мм для труб с толщиной стенки свыше 30 мм.
Затем определяем длину заготовки. По таблице П1.3 Приложения 1 назначаем двусторонний припуск на обработку обоих торцов детали. Тогда длина заготовки Lз составит: Lз = Lд +2Z0=154+10=164 мм.
Предельные отклонения на длину заготовки зависят от способа резки проката на штучные заготовки и определяются по таблице П3.1.

Рис. 5 Заготовка
При разрезке на дисковых, ленточных и ножовочных механических пилах Предельные отклонения равны ±1,5 мм.
МЦХ
Заготовка
Площадь S = 262637.151 мм2
Объем V = 4636990.842 мм3
Материал Сталь 30ХГСА ГОСТ 4543-71
Плотность Ro = 0.00785 г/мм3
Масса M = 36400.378 г
2. Определение диапазона торговых длин проката.
В соответствии с ГОСТ 2327-89 торговая длина трубы выбирается в интервале 1,5-11,5 метров. При расчете некратности необходимо стремиться к минимальным величинам.
Для каждого значения торговой длины проката, следует определить величину некратности Lнк по формулам (1.11) и (1.12) и в дальнейших расчетах использовать ту торговую длину, для которой величина некратности будет наименьшей.
Некратность в зависимости от принятой длины проката:
Lнк = Lпр – Lто – Lзаж –n ∙ ( Lз + Lр ),
где:
Lпр –торговая длина проката из сортамента, мм;
n - целое число заготовок, изготавливаемых из принятой торговой длины проката, шт;
Lз – длина заготовки, мм;
Lр – ширина реза, мм.
Число заготовок, изготавливаемых из принятой длины проката:

Где Lзаж – минимальная длина опорного (зажимного) конца проката.
Lто = (0,3…0,5) ∙ Dз=0,3*164=50 мм.
Lзаж=80 мм.
Lз=164 мм.
Lр=7 мм.











LНК1500 = 1500–50–80–8·(164+7) = 2 мм
LНК2500 = 2500–50–80–13·(164+7) = 147 мм
LНК3500 = 3500–50–80–19·(164+7) = 121 мм
LНК4500 = 4500–50–80–25·(164+7) = 95 мм
LНК5500 = 5500–50–80–31·(164+7) = 69 мм
LНК6500 = 6500–50–80–37·(164+7) = 43 мм
LНК7500 = 7500–50–80–43·(164+7) = 17 мм
LНК8500 = 8500–50–80–48·(164+7) = 162 мм
LНК9500 = 9500–50–80–54·(164+7) = 136 мм
LНК10500 = 10500–50–80–60·(164+7) = 110 мм
LНК11500 = 11500–50–80–66·(164+7) = 84 мм
Окончательно выбираем ту торговую длину, для которой потери на некратность наименьшие т.е. Lпр=1500 мм.
3. Определение общей потери металла.
Общие потери материала Побщ на деталь, изготавливаемую из проката, состоят из потерь на некратность торговой длины проката длине заготовки Пнк, торцовой обрезки Пто, потерь на зажим Пзаж опорных концов и потерь на отрезку Потр в виде стружки при разрезании:
Поб = Пнк + Пто + Пзаж + Потр,

где Lнк – величина некратности длины заготовки торговой длине проката Lпр, мм.

Потери на торцовую обрезку проката, %

где Lто – длина торцового обрезка, мм.

Потери на зажим опорного конца проката при выбранной длине зажима, %:


Потери на отрезку заготовки при выбранной по таблице П1.1.2 Приложения 1 ширине реза, %:

Поб =0,13+3,3+5,3+0,46=9,19%
КИМ= 7,713 /= 36,4 =0,21
4. Определение стоимости См материала заготовки.
Затраты на материал заготовки См определяются по массе проката, расходуемой на изготовление детали и массе возвращаемой в виде отходов стружки:


5. Определение tмаш и tшт.к.
Штучно-калькуляционное время приближенно определяется в виде:
tшт.к.= tмаш∙ φк,
где tмаш – машинное время при разрезании заготовки, мин; φк - коэффициент, равный 1,84 для условий единичного и мелкосерийного производства и 1,51 – для массового производства.
tшт.к.= tмаш∙ φк,
tмаш = 0,011*Dз=0,011*245=2,695 мин.
tшт.к.= tмаш∙ φк=2,695*1,84=4,96 мин.
6. Определение стоимости заготовки, стоимость ее механической обработки и стоимость детали.
Технологическая себестоимость i-ой заготовительной операции:

где Спзi – приведенные затраты на i-ой заготовительной операции, руб/час; tшт.к.i – штучно-калькуляционное время выполнения i-ой заготовительной операции, мин.
По данным базового предприятия приведенные затраты за один час работы заготовительного оборудования при правке и резке прутков составляют 25 руб/час

Сд = Сз + Смех=2,07+1533,523=1535,593 руб
1.6 Назначение и обоснование технологических баз, схем базирования и установки заготовки
Достижение конструкторских требований к детали в процессе их изготовления обеспечивается технологией обработки, в которой особая роль принадлежит установке заготовок в рабочие поверхности приспособлений. Определенное положение относительно режущих инструментов и станка придается заготовке в процессе базирования, когда образуются её геометрические связи с элементами приспособления. Чтобы эти связи не нарушились при механической обработке, заготовку закрепляют, создавая силовое замыкание связей. В процессе установки решаются две различные задачи: базирование и закрепление заготовок.
При разработке технологического процесса механической обработки детали основополагающим принципом, обеспечивающим требуемую точность изготовления, считается обеспечение принципа единства конструкторских, технологических и измерительных баз.
Особое значение вопросы базирования приобретают при обработке заготовок в условиях мелкосерийного производства с использованием настроенного на размер оборудования, для стабильности выполнения размеров при механической обработке.
Разработка схем базирования делится на два основных этапа:
1. Выбор черновых технологических баз;
2. Назначение чистовых технологических баз.
Назначение черновых технологических баз
При назначении черновых технологических баз учитываем те условия, при которых обеспечивается заданная точность при минимуме припусков на обработку. Для базирования на первой операции используется наружная поверхность стальной трубы, диаметр которой Ç245 мм. Эта поверхность удовлетворяет требованиям для черновых баз:
- достаточные размеры для закрепления;
- на поверхностях отсутствуют дефекты;
- используются только на первых переходах.
- наиболее ответственные поверхности при прокате.
Схема базирования представлена на рис. 4
Назначение чистовых технологических баз
Назначение чистовых технологических баз является многовариантной задачей. Оптимальный вариант можно отыскать только на основе анализа решений технологических размерных цепей. При этом должны соблюдаться принципы соответствия конструкторских и технологических баз (по мере возможности).

Рис. 6. Схемы базирования и установки на черновых операциях
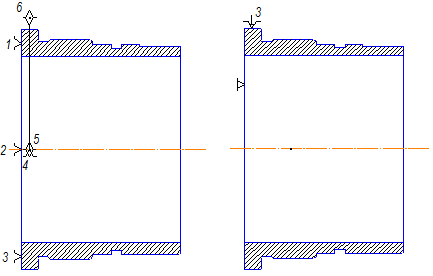

Рис. 7. Схемы базирования и установки на чистовых операциях
1.7 Выбор методов обработки отдельных поверхностей с альтернативными вариантами
Оптимальный способ обработки поверхностей детали означает, что удалось отыскать технологический переход. Таким образом, это является началом поиска структуры технологической операции, а затем и всего технологического процесса.
Применим таблично–расчётный метод выбора способа обработки более точных поверхностей, основанный на определении уточнения.
Уточнение – это отношение допусков заготовки Тзаг на каждую поверхность к соответственным допускам детали Тдет, проставленным на чертеже детали:
,
такое уточнение называется общим.
1. Найдём число операций для обработки поверхности (4): . Для данной поверхности общее уточнение равно:

Необходимо обеспечить условие:
eобщ.расч. = e1*e2*e3*…*en ≥ eобщ
Методом подбора определяем количество технологических переходов на обработку данной поверхности. Получаем 3 – черновое точение, получистовое и чистовое.
1. Находим уточнение после чернового точения
Ra = 6,3
2. Находим уточнение после получистого точения
Ra = 3,2
3. Находим уточнение после чистого точения
Ra = 2,5
Общее уточнение после трёхкратной обработки:
eобщ.расч. = e1*e2*e3*…*en = 16,25 ≥ eобщ = 15,97
Условие выполнено, следовательно, другие методы обработки данной поверхности не нужны.
II. Найдём число операций для обработки поверхности (3): . Для данной поверхности общее уточнение равно:

Необходимо обеспечить условие:
eобщ.расч. = e1*e2*e3*…*en ≥ eобщ
Методом подбора определяем количество технологических переходов на обработку данной поверхности. Получаем 3 – черновое точение, получистовое и чистовое.
1. Находим уточнение после чернового точения
Ra = 6,3
2. Находим уточнение после получистого точения
Ra = 3,2
3. Находим уточнение после чистого точения
Ra = 2,5
Общее уточнение после трёхкратной обработки:
eобщ.расч. = e1*e2*e3*…*en = 10 ≥ eобщ = 10
Условие выполнено, следовательно, другие методы обработки данной поверхности не нужны.
На остальные поверхности с невысокими технологическими требованиями для выбора способов обработки воспользуемся табличным методом.
После определения методов обработки каждой поверхности детали заполним таблицу 4.
Таблица 4. Методы обработки поверхностей детали
Номер |
Метод обработки |
Квалитет точности |
Допуск обработки, мкм |
Шероховатость поверхности, мкм |
1 |
Черн. Точение П-чист. Точение |
14 12 |
1000 500 |
6,3 3,2 |
2 |
Черн. Фрезерование П-чист. Фрезерование Чист. Фрезерование |
12 10 9 |
300 140 55 |
6,3 3,2 1,6 |
3 |
Черн. Точение П-чист. Точение Чист. Точение |
12 10 9 |
460 185 115 |
6,3 3,2 2,5 |
4 |
Черн. Точение П-чист. Точение Чист. Точение |
12 10 8 |
460 185 72 |
6,3 3,2 2,5 |
5 |
Черн. Точение П-чист. Точение Чист. Точение |
12 10 8 |
460 185 72 |
6,3 3,2 2,5 |
6 |
Нарезание резьбы |
8 |
72 |
3,2 |
7 |
Черн. Точение П-чист. Точение |
14 12 |
1000 500 |
6,3 3,2 |
8 |
Черн. Точение П-чист. Точение |
14 12 |
1000 500 |
6,3 3,2 |
9 |
Черн. Точение П-чист. Точение |
14 12 |
1000 500 |
6,3 3,2 |
10 |
Черн. Точение П-чист. Точение |
14 12 |
1000 500 |
6,3 3,2 |
11 |
Черн. Точение П-чист. Точение |
14 12 |
1000 500 |
6,3 3,2 |
12 |
Черн. Точение П-чист. Точение |
14 12 |
1000 500 |
6,3 3,2 |
13 |
Черн. Точение П-чист. Точение |
14 12 |
1000 500 |
6,3 3,2 |
14 |
Черн. Точение П-чист. Точение |
14 12 |
1000 500 |
6,3 3,2 |
15 |
Черн. Точение П-чист. Точение |
14 12 |
1000 500 |
6,3 3,2 |
16 |
Черн. Точение П-чист. Точение |
14 12 |
1000 500 |
6,3 3,2 |
17 |
Черн. Фрезерование П-чист. Фрезерование Чист. Фрезерование |
12 10 9 |
300 140 55 |
6,3 3,2 1,6 |
18 |
Черн. Фрезерование П-чист. Фрезерование Чист. Фрезерование |
12 10 9 |
300 140 55 |
6,3 3,2 1,6 |
19 |
Черн. Фрезерование П-чист. Фрезерование |
12 10 |
300 140 |
6,3 3,2 |
20 |
Черн. Фрезерование П-чист. Фрезерование |
12 10 |
300 140 |
6,3 3,2 |
21 |
Черн. Фрезерование П-чист. Фрезерование |
12 10 |
300 140 |
6,3 3,2 |
22 |
Черн. Фрезерование П-чист. Фрезерование |
12 10 |
300 140 |
6,3 3,2 |
23 |
Сверление |
7 |
12 |
3,2 |
24 |
Зенкование |
7 |
12 |
3,2 |
25 |
Нарезание резьбы |
7 |
12 |
3,2 |
1.8 Формирование структуры вариантов технологического процесса
Для формирования структуры технологического процесса необходимо сначала наметить структуру технологических операций. Для этого компонуем одинаковые методы обработки однообразных поверхностей:
- Ф для поверхностей 2,17,18,19, 20, 21, 22;
- Cв для поверхностей 23, 24, 25;
- Т для поверхностей 1, 3, 4, 5, 6, 7, 8, 9, 10, 11, 12, 13, 14,15, 16;
Выше приняты следующие обозначения: Ф – фрезерование, Св – сверление, Т – точение.
После чего, оцениваем возможность объединения методов обработки для реализации их на металлорежущем оборудовании.
Процесс механической обработки должен проходить в следующей последовательности:
1. Обработка поверхностей, образующих установочные базы для всех последующих операций.
2. Черновая обработка основных поверхностей детали.
3. Чистовая обработка основных поверхностей детали.
4. Черновая и чистовая обработка второстепенных поверхностей.
5. Термическая обработка, если она предусмотрена чертежом и техническими требованиями.
6. Выполнение второстепенных операций, связанных с термообработкой.
7. Выполнение отделочных операций основных поверхностей.
8. Выполнение доводочных операций основных поверхностей.
При формировании операций в условиях действующего завода необходимо учитывать возможности имеющегося оборудования, перспективы его модернизации, замены или пополнения новым.
Таблица 5. Исходные данные сравниваемых вариантов
Базовый вариант |
Предлагаемый вариант |
Содержание технологических процессов |
010 Заготовительная |
010 Заготовительная |
Станок |
Hercules |
Станок |
Hercules |
Приспособление |
Приспособление |
020 Токарно-винторезная |
020 Токарно-винторезная |
Станок |
1м63 |
Станок |
1м63 |
Приспособление |
3-х кулачковый патрон |
Приспособление |
3-х кулачковый патрон |
030 Токарно-винторезная |
030 Токарно-винторезная |
Станок |
1м63 |
Станок |
1м63 |
Приспособление |
3-х кулачковый патрон |
Приспособление |
3-х кулачковый патрон |
040 Токарно-винторезная |
070 Токарная с ЧПУ |
Станок |
1м63 |
Станок |
Monforts RNC 700 |
Приспособление |
3-х кулачковый патрон |
Приспособление |
3-х кулачковый патрон |
080 Токарно-винторезная |
080 Токарная с ЧПУ |
Станок |
1м63 |
Станок |
Monforts RNC 700 |
Приспособление |
3-х кулачковый патрон |
Приспособление |
3-х кулачковый патрон |
090 Токарная с ЧПУ |
Станок |
16К30 NC 210 |
Приспособление |
3-х кулачковый патрон |
100 Токарная с ЧПУ |
Станок |
16К30 NC 210 |
Приспособление |
3-х кулачковый патрон |
110 Вертикально-фрезерная |
Станок |
6Р12 |
Приспособление |
УДГ |
120 Вертикально-фрезерная |
Станок |
6Р12 |
Приспособление |
УДГ |
130 Радиально-сверлильная |
Станок |
2Н55 |
Приспособление |
Тиски с призм. губками |
Штучное время |
оп. 10 |
10,1 |
оп. 10 |
10,1 |
оп. 20 |
15,3 |
оп. 20 |
15,3 |
оп. 30 |
24,9 |
оп. 30 |
24,9 |
оп. 40 |
11,6 |
оп. 70 |
40,1 |
оп. 80 |
12,3 |
оп. 80 |
38,22 |
оп. 90 |
50,1 |
оп. 100 |
18,7 |
оп. 110 |
11,2 |
оп. 120 |
13,4 |
оп. 130 |
27,5 |
Итого: (мин) |
195,1 |
Итого: (мин) |
128,6 |
Построение операций с разработкой схем обработки
010 Заготовительная
1. Резать трубу на заготовки по типовому техпроцессу цеха №1
020 Токарно-винторезная
1. Точить поверхность 1
2. Точить поверхность 9
3. Расточить поверхность 16
4. Притупить острые кромки
030 Токарно-винторезная
1. Точить поверхность 10
2. Точить поверхность 9
3. Притупить острые кромки
040 Слесарная
1. Вырезать бирку из листа в размер 50х30 мм
2. Маркировать черт. номер детали на бирке
3. Прикрепить бирку к детали
050 Контрольная
1. Проверить марку материала
2. Проверить деталь на отсутствие мех. повреждений и коррозии
3. Проверить шероховатость
4. Проверить размеры
060 Термическая
1. Произвести термообработку
070 Токарная с ЧПУ
1. Точить поверхности 1, 3, 5, 7, 8 (черн.)
2. Точить поверхности 1, 3, 5, 7, 8 (чист.)
3. Нарезать резьбу 6
4. Точить канавку 4
5. Точить поверхность 16 (черн.)
6. Точить поверхность 16 (чист.)
7. Фрезеровать поверхность 2
8. Фрезеровать поверхность 17
9. Фрезеровать поверхность 18
10. Снять заусенцы по контуру
080 Токарная с ЧПУ
1. Точить поверхности 9, 10
2. Точить поверхности 11, 12, 13, 14 (черн.)
3. Точить поверхности 11, 12, 13, 14, 15 (чист.)
4. Сверлить 12 отв. – 23
5. Цековать 12 отв. – 24
6. Нарезать резьбу в 12 отв. – 25
7. Фрезеровать поверхность 19
8. Фрезеровать поверхность 20
9. Фрезеровать поверхность 21
10.Фрезеровать поверхность 22
11.Снять заусенцы по контуру
090 Контрольная
1. Произвести магнитный контроль
100 Слесарная
1. Зачистить дефектные места после магнитного контроля
110 Контрольная
1. Проверить деталь на отсутствие мех. повреждений и коррозии
2. Проверить шероховатость
3. Проверить размеры
4. Клеймить деталь на бирке
120 Прессовая
1. Получить втулку ТМ966.2120-36
2. Запрессовать втулку до упора
130 Радиально-сверлильная
1. Сверлить отверстие 26
2. Зенкеровать отверстие 26
3. Развернуть отверстие 26
4. Сверлить отверстие 27
5. Зенкеровать отверстие 27
6. Развернуть отверстие 27
140 Промывочная
150 Штифтование
1. Получить штифты ТМ966.2120-37 – 2шт.
2. Запрессовать штифты
160 Токарная с ЧПУ
1. Точить поверхности 11, 12, 16 (черн.)
2. Точить поверхности 11, 12, 16 (чист.)
3. Точить канавки 28, 29
170 Промывочная
180 Контрольная
190 Покрытие
200 Промасливание
210 Контрольная
1.9 Выбор оборудования и средств технологического оснащения (приспособлений, инструмента, контрольно-измерительных средств)
Для выполнения токарных операций с ЧПУ применяем станок Monforts RNC 700. Станки модельного ряда RNC фирмы Monforts высокопроизводительные токарные станки с ЧПУ.
Наличие бесступенчатых приводов и современной техники управления позволяет экономично обрабатывать единичные детали и мелкие серии. Возможность задания элементов контура открывает новые дополнительные возможности токарной обработки:
1. Визуализация значения подачи и числа оборотов
2. Обработка фасок и радиусов без фасонных инструментов
3. Обработка сферических поверхностей без специальных приспособлений.
4. Обработка конических поверхностей без смещения верхнего суппорта
5. Точение резьбы с любым шагом в многопроходном цикле
6. Циклы черновой обработки
7. Циклы обработки канавок и сверления
8. Компенсация радиуса инструмента
9. Графическое представление контура детали
10. Запоминание с последующей отработкой отдельных перемещений и циклов
11. Графическое представление перемещений, сделанных в процессе «обучения»
Станок имеет высокую жесткость конструкции, что необходимо при выполнении черновых операций.

Рис. 8. Токарный станок с ЧПУ MonfortsRNC 700
Таблица 6. Технические данные станка Monforts RNC 700
Рабочая зона |
Макс. диаметр обработки над станиной |
720 мм |
Макс. диаметр обработки над суппортом |
550 мм |
Макс. длина обрабатываемой детали |
1500 мм |
Ход револьверной головки по оси X |
430 мм |
Ход револьверной головки по оси Z |
1600 мм |
Шпиндельная бабка |
Диаметр шпинделя в переднем подшипнике |
150 мм |
Посадочное место под патрон по DIN 55026 |
A11 |
Диаметр отверстия в шпинделе |
85 мм |
Главный привод |
Главный привод переменного тока (100 %/40 % ED) с прямой передачей: |
37/46 кВт |
Частота вращения |
6-4000 мин-1 |
Макс. крутящий момент |
2121/2636 Н•м |
Приводы подачи |
Скорость холостого хода оси X |
12 м/мин |
Скорость холостого хода оси Z |
12 м/мин |
Усилие подачи оси X |
13,6 кН |
Усилие подачи оси Z |
13,6 кН |
Охлаждение |
Емкость бака |
420 л |
Насос |
40 л/мин, 3 бар |
Для закрепления обрабатываемой детали, используется гидравлический трехкулачковые патрон.
Выбор режущего инструмента определяется методами обработки, свойствами обрабатываемого материала, требуемой точности обработки и качество обрабатываемой поверхности. Правильный выбор режущей части инструмента имеет большое значение для производства труда и снижение себестоимости обработки. В серийном типе производства в основном применяется стандартный режущий инструмент и реже специальный.
Таблица 7. Выбор оборудования и режущего инструмента
№ |
Наименование операции |
Оборудование |
Режущий инструмент |
010 |
Заготовительная |
Пилоотрезной станок «HERCULES». |
Ленточная пила |
020 |
Токарно-винторезная |
Токарно-винторезный станок 1М63 |
Расточной резец 616/1715/ Т15К6 Подрезной резец 2102/0055/Т15К6 |
030 |
Токарно-винторезная |
Токарно-винторезный станок 1М63 |
Подрезной резец 2102/0055/Т15К6 |
040 |
Слесарная |
Верстак слесарный Н2.007 |
Пневмошлифмашинка ГОСТ 12633 – 90, шлиф. ГЦ25х32х6 головка ГОСТ2447 – 82, напильник ГОСТ 1465 – 80 |
050 |
Контрольная |
Стол контролера |
060 |
Термическая |
Печь |
070 |
Токарная с ЧПУ |
Токарный станок с ЧПУ MONFORTS – RNC 700 Пульт: Sinumerik 840D |
Весь инструмент фирмы KennaMetall 1. Резец расточной черновой Чертежный номер державки: D40MTTB530 Тип пластины: CNMG 120412 MN KC9125 2. Резец подрезной чистовой Чертежный номер державки: MVJNL3225P16 Тип пластины: VNMG 160404 MN KC9110
3. Резец подрезной черновой Чертежный номер державки: PDJNL 32325 P15 Тип пластины: DNMG 150612 MN KC9125 4. Резец резьбовой Чертежный номер державки: A2532LSER 16 Тип пластины (SANDVIK): ICTR 3300F 5. Резец канавочный Чертежный номер державки: A4SML2525M0520 Тип пластины: A4G0500M05P04GMP 6. Резец расточной чистовой Чертежный номер державки: D40MTTB530 Тип пластины: DNMG 150612 MN KC9125 7. Фреза концевая Чертежный номер державки: FBAV2500ADL45 Диаметр фрезы: 25мм
|
080 |
Токарная с ЧПУ |
Токарный станок с ЧПУ MONFORTS – RNC 700 Пульт: Sinumerik 840D |
Весь инструмент фирмы KennaMetall 1. Резец расточной черновой Чертежный номер державки: D40MTTB530 Тип пластины: CNMG 120412 MN KC91253. 2. Резец подрезной черновой Чертежный номер державки: PDJNL 32325 P15 Тип пластины: DNMG 150612 MN KC9125 3. Резец расточной чистовой Чертежный номер державки: D40MTTB530 Тип пластины: DNMG 150612 MN KC9125 |
090 |
Контрольная |
Установка УМДЭ-1000 |
100 |
Слесарная |
Верстак слесарный Н2.007 |
Пневмошлифмашинка ГОСТ 12633 – 90, шлиф. ГЦ25х32х6 головка ГОСТ2447 – 82, напильник ГОСТ 1465 – 80 |
110 |
Контрольная |
Стол контролера |
120 |
Прессовая |
Верстак слесарный Н2.007 |
Молоток ГОСТ 2310-77 |
130 |
Радиально-сверлильная |
2Н55 |
Сверло 2301-3001 Ф5 ГОСТ 10903-77 Зенкер2320-2531 Ф5,8 ГОСТ 21543-76 Развертка 2363-1127 Ф6 ГОСТ 16086-70 |
140 |
Промывочная |
По инструкции 26-02-82 |
150 |
Штифтование |
Верстак слесарный Н2.007 |
Молоток ГОСТ 2310-77 |
160 |
Токарная с ЧПУ |
Токарный станок с ЧПУ MONFORTS – RNC 700 Пульт: Sinumerik 840D |
1. Резец расточной черновой Чертежный номер державки: D40MTTB530
Тип пластины: CNMG 120412 MN KC9125
2. Резец расточной чистовой Чертежный номер державки: D40MTTB530 Тип пластины: DNMG 150612 MN KC9125
3. Резец канавочный
Чертежный номер державки: A4OTA4EMLO416M Тип пластины: A4GD4D5MO4UO4GMN KC 9110
|
170 |
Промывочная |
По инструкции 26-02-82 |
180 |
Контрольная |
Стол контролера |
190 |
Покрытие |
По технологии цеха №10 |
200 |
Промасливание |
По технологии цеха №10 |
210 |
Контрольная |
Стол контролера |
1.10 Выбор и расчет припусков и операционных размеров
Величина припуска влияет на себестоимость изготовления детали. При увеличенном припуске повышаются затраты труда, расход материала и другие производственные расходы, а при уменьшенном приходится повышать точность заготовки, что также увеличивает стоимость изготовления детали.
Для определения припуска на обработку и предотвращения перерасхода материала применяют аналитический метод для каждого конкретного случая с учётом всех требований выполнения заготовок и промежуточных операций.
Аналитический метод определения припусков базируется на анализе производственных погрешностей, возникающих при конкретных условиях обработки заготовки.
Произведем определение припусков аналитическим методом на пов.26, при этом, учитывая многоинструментальную наладку на каждой из операций в маршруте.
Порядок расчета припусков на обработку и предельных размеров по технологическим переходам
1. Пользуясь рабочим чертежом детали и картой технологического процесса механической обработки, записываем в расчетную карту обрабатываемые поверхности заготовки и технологические переходы обработки в порядке последовательности их выполнения.
2. Записываем значения Rz, h, Δ, δ и ε.
3. Определяем минимальные припуски на обработку по всем технологическим переходам.
2zimin = 2*(Rz+h)
4. Запишем для конечного перехода в графу «Расчетный размер» наибольший предельный размер детали по чертежу.
5. Для перехода, предшествующего конечному, определим расчетный размер вычитанием из наибольшего предельного размера по чертежу расчетного припуска
Zmin.dр.чист. = dр.тонк – Zmin тонк
6. Последовательно определим расчетные размеры для каждого предшествующего перехода вычитанием из расчетного размера расчетного припуска Zmin следующего за ним смежного перехода.
7. Запишем наибольшие предельные размеры по всем технологическим переходам, округляя их уменьшением расчетных размеров; округление производим до того же знака десятичной дроби, с каким дан допуск на размер для каждого перехода.
8. Определим наименьшие предельные размеры путем вычитания допуска из округленного наибольшего предельного размера.
9. Запишем предельные значения припусков Zmax, как разность наименьших предельных размеров и Zmin, как разность наибольших предельных размеров выполняемого и предшествующего переходов.
Zmax = dmin тонк – dmin чист
Zmin = dmax тонк – dmax чист
10. Общие припуски
ZOmax = Сумма промежуточных припусков
ZOmin = Сумма промежуточных припусков
11. Проверка 
Таблица №8. Расчет припусков и предельных размеров
Технологические переходы обработки поверхности №3 D200 |
Элементы припуска |
Расчетный припуск 2Zmin, мкм |
Расчетный размер dр, мм |
Допуск, δ |
Пред. размеры мм |
Пред. значения припусков мм |
Rz |
h |
Δ |
ε |
dmin |
dmax |
2zmin |
2zmax |
Прокат |
150 |
250 |
- |
- |
- |
198,85 |
- |
- |
- |
- |
- |
Черновое точение |
40 |
50 |
- |
- |
800 |
199,65 |
400 |
198,82 |
199,22 |
- |
- |
Получистовое точение |
20 |
40 |
- |
- |
180 |
199,83 |
250 |
199,47 |
199,72 |
0,5 |
0,65 |
Чистовое точение |
10 |
30 |
- |
- |
120 |
199,95 |
115 |
199,835 |
199,95 |
0,23 |
0,365 |
Проверка:
0,400-0,115=(0,5+0,365)-(0,5+0,23)
0,285=1,015-0,73
0,285=0,285
1.11 Выбор и расчёт режимов резания
Рассчитанные или выбранные режимы резания при выполнении технологической операции должны обеспечивать требуемую точность обработки при максимальной производительности труда и минимальной себестоимости.
При выборе режимов обработки необходимо придерживаться определённого порядка, т. е. при назначении и расчёте режима обработки учитывают тип и размеры режущего инструмента, материал его режущей части, материал и состояние заготовки, тип оборудования и его состояние. Следует помнить, что элементы режимов обработки находятся во взаимной функциональной зависимости, устанавливаемой эмпирическими формулами.
При расчёте режимов резания сначала устанавливают глубину резания в миллиметрах. Глубину резания назначают по возможности наибольшую, в зависимости от требуемой степени точности, шероховатости обрабатываемой поверхности и технических требований на изготовление детали. После установления глубины резания устанавливается подача станка. Подачу назначают максимально возможную с учётом погрешности обработки жёсткости технологической системы, мощности привода станка, степени точности и качества обрабатываемой поверхности по нормативным таблицам. Величину подачи согласовывают с паспортными данными станка. От правильно выбранной подачи во многом зависят точность и качество обработки, и производительность труда. Для черновых технологических операций назначают максимально допустимую подачу.
Операция 070 Токарная с ЧПУ
Переход 1 Черновое точение пов-ей 1, 3, 5, 7, 8
Токарный подрезной резец |
Пластина |
DNMG 150612 MN KC9125 |

|
Державка |
PDJNL 32325 P15 |
Инструментальный блок |
B5 11/6032/25 |
tmax=3 мм
Vc =160 м/мин
fn=0,3 мм/об
D=200 мм об/мин
Тм = 18,2 мин.
Переход 2 Чистовое точение пов-ей 1, 3, 5, 7, 8
Токарный подрезной резец |
Пластина |
VNMG 160404 MN KC9110 |

|
Державка |
MVJNL3225P16 |
Инструментальный блок |
B5 11/6032/25 |
tmax=0,5 мм
Vc =160 м/мин
fn=0,3 мм/об
D1=200 мм; об/мин.
Тм =3,75 мин.
Переход 3 Нарезание резьбы 6
Токарный резьбовой резец |
Пластина |
ICTR 3300F (Sandvik) |

|
Державка |
A2532LSER 16 |
Инструментальный блок |
B5 11/6032/25 |
tmax=0,25 мм
Vc =95 м/мин
fn=3 мм/об.
D=210 мм; об/мин
Тм = 1,8 мин
Переход 4 Точение канавки 4
Токарный канавочный резец |
Пластина |
A4G0500M05P04GMP |

|
Державка |
A4SML2525M0520 |
Инструментальный блок |
B5 11/6032/25 |
tmax=5 мм
Vc =65 м/мин
fn=0,05 мм/об.
D1=203 мм; об/мин.
Тм =4,7 мин.
Переход 5 Черновое точение поверхности 16
Токарный расточной резец |
Пластина |
CNMG 120412 MN KC9125 |

|
Державка |
D40MTTB530 |
Инструментальный блок |
EWS-Sonder |
tmax=2 мм
Vc =160 м/мин
fn=0,3 мм/об.
D1=178 мм; об/мин.
Тм = 2,9 мин.
Переход 6 Чистовое точение поверхности 16
Токарный расточной резец |
Пластина |
DNMG 150612 MN KC9125 |

|
Державка |
D40MTTB530 |
Инструментальный блок |
EWS-Sonder |
tmax=0,5 мм
Vc =170 м/мин
fn=0,2 мм/об.
D1=180мм; об/мин.
Тм = 1,83 мин.
Переходы 7, 8, 9 Фрезерование поверхностей 2, 17, 18
Фреза |
Инструмент |
F8AV2500ADL45 KC637M |
Инструментальный блок |
80.6040 5482 |
Частота вращения шпинделя: ,
где Vc – скорость резания, Vc =87 м/мин;
D – диаметр фрезы, D=25 мм.
об/мин.
Подача: ,
где fz – подача на зуб фрезы, fz=0,03;
z – число зубьев фрезы, z=8.
мм/мин.
Тм =6,09 мин.
Переход 10 Снятие заусенцев по контуру
Металлическая щетка |
Инструмент |
OSBORN PRO |
Инструментальный блок |
80.6040 5482 |
fn=0,5 мм/об
n=1500 об/мин
Тм =1,5 мин
Операция 080 Токарная с ЧПУ
Переход 1 Точение поверхностей 9, 10
Токарный подрезной резец |
Пластина |
DNMG 150612 MN KC9125 |

|
Державка |
PDJNL 32325 P15 |
Инструментальный блок |
B5 11/6032/25 |
tmax=0,5 мм
Vc =160 м/мин
fn=0,2 мм/об
D1=230 мм; об/мин.
Тм =1,05 мин.
Переход 2 Черновое точение пов-ей 11, 12, 13, 14, 15
Токарный расточной резец |
Пластина |
CNMG 120412 MN KC9125 |

|
Державка |
D40MTTB530 |
Инструментальный блок |
EWS-Sonder |
tmax=2 мм
Vc =160 м/мин
fn=0,3 мм/об.
D1=190 мм; об/мин.
Тм = 4,05 мин.
Переход 3 Чистовое точение пов-ей 11, 12, 13, 14, 15
Токарный расточной резец |
Пластина |
DNMG 150612 MN KC9125 |

|
Державка |
D40MTTB530 |
Инструментальный блок |
EWS-Sonder |
tmax=0,5 мм
Vc =160 м/мин
fn=0,15 мм/об
D1=190 мм; об/мин.
Тм = 2,2 мин.
Переход 4 Сверление 12 отв. - 23
Сверло |
Инструмент |
SD-203A-14.07-37-14R1-M |
Инструментальный блок |
80.6040 5485 |
tmax=5 мм
Vc =28 м/мин
fn=0,3 мм/об
D1=5 мм; об/мин.
Тм = 6,6 мин
Переход 5 Цекование 12 отв. - 24
Цековка |
Инструмент |
SD200-C45-8R1 |
Инструментальный блок |
80.6040 5485 |
tmax=1 мм
Vc =25 м/мин
fn=0,3 мм/об
D1=6 мм; об/мин.
Тм = 3,6 мин
Переход 6 Нарезание резьбы 12 отв. - 25
Метчик |
Инструмент |
OO315-8.000 M6 |
Инструментальный блок |
80.6040 5485 |
tmax=0,5 мм
Vc =5 м/мин
fn=1 мм/об
D1=6 мм; об/мин.
Тм = 5,4 мин
Переходы 7, 8, 9, 10 Фрезерование поверхностей 19, 20, 21, 22
Фреза |
Инструмент |
F8AV1600ADL45 KC637M |
Инструментальный блок |
80.6040 5482 |
Частота вращения шпинделя: ,
где Vc – скорость резания, Vc =60 м/мин;
D – диаметр фрезы, D=15 мм.
об/мин.
Подача: ,
где fz – подача на зуб фрезы, fz=0,03;
z – число зубьев фрезы, z=8.
мм/мин.
Тм =13,6 мин.
Переход 11 Снятие заусенцев по контуру
Металлическая щетка |
Инструмент |
OSBORN PRO |
Инструментальный блок |
80.6040 5482 |
fn = 0,75 мм/об
n = 1200 об/мин
t =1 мм
Тм =1,7 мин
1.12 Расчёт норм времени
При нормировании в мелкосерийном производстве штучно-калькуляционное время определяется по формуле
Т шт-к = Т шт + Т п-з / n,
где штучное время Т шт находим из выражения
Т шт = Т о+ Т в+ Т об+ Т от
где Т п-з – подготовительно-заключительное время; n – число заготовок в операционной партии; Т в – вспомогательное время, Т об – время обслуживания рабочего места в % от оперативного Т о; Т от – время на отдых и личные надобности.
Операция 070 Токарная с ЧПУ
Общее время операции
Топ = 40,1 мин
Вспомогательное время
Т в= 8,02 мин
Время обслуживания рабочего места в % от оперативного То
Т об = Т о Ä 14%/100% = 5,614 мин
Время на отдых и личные надобности
Т об = Т о Ä 10%/100% = 4,01мин
Т шт = 40,1+8,02+5,614+4,01 =57,75 мин
Определяем состав подготовительно-заключительного времени:
· Получение задания у мастера – 5 мин.
Штучно-калькуляционное время на операцию будет равно:
Т шт-к = 57,75 + 5/100 = 57,8 мин.
Операция 080 Токарная с ЧПУ
Общее время операции
Топ = 38,2 мин
Вспомогательное время
Т в= 7,64 мин
Время обслуживания рабочего места в % от оперативного То
Т об = Т о Ä 14%/100% = 5,35 мин
Время на отдых и личные надобности
Т об = Т о Ä 10%/100% = 3,82мин
Т шт = 38,2+7,64+5,35+3,82 =55 мин
Определяем состав подготовительно-заключительного времени:
· Получение задания у мастера – 5 мин.
Штучно-калькуляционное время на операцию будет равно:
Т шт-к = 55 + 5/100 = 55,058 мин.
1.13 Технико-экономический анализ вариантов технологических операций по себестоимости
Таблица 9. Содержание базового технологического процесса
№ |
Наименование операции |
Оборудование |
Нормы времени, мин. |
Разряд
рабочего
|
Часовая тариф. ставка, руб. |
Расценка, руб. |
Тмаш |
Твсп |
Тшт |
020 |
Токарно-винторезная |
1М63 |
12,2 |
3,1 |
15,3 |
3 |
45 |
11,5 |
030 |
Токарно-винторезная |
1М63 |
19,9 |
5,0 |
24,9 |
3 |
45 |
18,7 |
040 |
Токарно-винторезная |
1М63 |
9,3 |
2,3 |
11,6 |
3 |
45 |
8,7 |
080 |
Токарно-винторезная |
1М63 |
9,8 |
2,5 |
12,3 |
3 |
45 |
9,2 |
090 |
Токарная ЧПУ |
16К30 NC 210 |
40,1 |
10,0 |
50,1 |
4 |
66,81 |
55,8 |
100 |
Токарная ЧПУ |
16К30 NC 210 |
15,0 |
3,7 |
18,7 |
4 |
66,81 |
20,8 |
110 |
Вертикально-фрезерная |
6Р12 |
9,0 |
2,2 |
11,2 |
4 |
51 |
9,5 |
120 |
Вертикально-фрезерная |
6Р12 |
10,7 |
2,7 |
13,4 |
4 |
51 |
11,4 |
130 |
Радиально-сверлильная |
2Н55 |
22,0 |
5,5 |
27,5 |
4 |
51 |
23,4 |
И Т О Г О |
148 |
37 |
185 |
169 |
Таблица 10. Содержание предлагаемого технологического процесса
№ |
Наименование операции |
Оборудование |
Нормы времени, мин. |
Разряд рабочего |
Часовая тариф. ставка, руб. |
Расценка, руб. |
Тмаш |
Твсп |
Тшт |
20 |
Токарно-винторезная |
1М63 |
15,3 |
3,06 |
18,3 |
3 |
45 |
13,77 |
30 |
Токарно-винторезная |
1М63 |
24,9 |
4,98 |
29,8 |
3 |
45 |
22,41 |
70 |
Токарная ЧПУ |
Monforts RNC 700 |
40,1 |
8,02 |
48,1 |
4 |
65 |
52,13 |
80 |
Токарная ЧПУ |
Monforts RNC 700 |
38,2 |
7,64 |
45,8 |
4 |
65 |
49,66 |
И Т О Г О |
118 |
23,7 |
94,8 |
137,97 |
1.
Определение стоимости затрат на материал одной детали:
Зм = (Gз ∙ Цз) – (Gотх ∙ Цотх), руб
где Gз – масса заготовки, Gз=36,4 кг;
Gотх - масса отходов, кг Gотх=28,7;
Цз= 44,1 руб/кг - цена 1 кг заготовки;
Цотх=2,5 руб. - цена1 кг отходов;
Зм= (36,4*44,1 ) – (28,7*2,5) =1605,24-71,75=1533 руб.
2.
Определим заработную плату, приходящуюся в расчете на одну деталь. В данном случае она складывается из трех составляющих:
Зо –основной фонд заработной платы,
Зд –добавочный фонд заработной платы,
Зсоц. отчисления в фонд социального страхования.
Зпр= Зо + Зд + Зсоц.,
Основной фонд заработной платы при базовом технологическом процессе [табл.9]:
З0б = 169 руб.
Основной фонд заработной платы при предлагаемом технологическом процессе [табл.10]:
З0п = 137,97 руб.
Добавочный фонд заработной платы рассчитывается по формуле:

где, a=15% величин добавочной заработной платы.
Откуда:


Определим величину отчислении в социальный фонд, их величина составляет 26 %:



Таким образом, заработная плата основных рабочих, приходящаяся на одну деталь, равна:
Зпр.б = 169 + 25,4 + 50,5 = 244,9 руб.
Зпр.п = 137,97 + 20,7 + 41,25 = 199,92 руб.
3.
Амортизационные отчисления на оборудование и дорогостоящую оснастку с длительным сроком службы

где Кпервi – первоначальная стоимость оборудования (оснастки) на i-той операции, руб;
Наi – годовая норма амортизационных отчислений на оборудование (оснастку) на i-той операции, %;
tOC – основное (машинное) время на i-той операции, мин;
FД – действительный (эффективный) фонд времени работы оборудования (оснастки), ч.
Таблица 11. Амортизационные отчисления на оборудование для базового ТП
№ |
Стоимость станка, руб |
Тмаш, мин |
Нai, % |
FД, час |
Аотч, руб |
20 |
250000 |
12,2 |
5 |
4015 |
0,63 |
30 |
250000 |
19,9 |
0,13 |
40 |
250000 |
9,3 |
0,48 |
80 |
250000 |
9,8 |
0,51 |
90 |
300000 |
40,1 |
1,55 |
100 |
300000 |
15 |
0,77 |
110 |
270000 |
9 |
0,50 |
120 |
270000 |
10,7 |
0,60 |
130 |
200000 |
22 |
0,49 |
АотчБАЗ = 0,63+0,13+0,48+0,51+1,55+0,77+0,5+0,6+0,49=5,66 руб.
Таблица 12. Амортизационные отчисления на оборудование для предлагаемого ТП
№ |
Стоимость станка, руб |
Тмаш, мин |
Нai, % |
FД, час |
Аотч, руб |
20 |
250000 |
15,3 |
5 |
4015 |
0,79 |
30 |
250000 |
24,9 |
1,29 |
70 |
1500000 |
40,1 |
12,48 |
80 |
1500000 |
38,2 |
11,89 |
АотчПРЕД =0,79+1,29+12,48+11,89 =26,46 руб.
4.
Затраты на инструмент.
Расчет зависит от типа инструмента (режущий, мерительный, вспомогательный и т.п.). Для режущего инструмента:

где ЦИНij – цена j-ого вида i-той операции, руб/шт.;
tMij – основное время работы j-ого инструмента на i-той операции, мин;
tстij – период стойкости j-ого инструмента, мин;
nПj – число переточек j-ого инструмента до полного износа.
Таблица 13. Затраты на инструмент в базовом ТП
№ |
Стоимость инструмента, руб. |
Время работы инструмента, мин |
Период стойкости, мин |
Число переточек |
Затраты на инструмент, руб. |
20 |
200 |
12,2 |
40 |
3 |
15,25 |
30 |
200 |
2,5 |
40 |
3 |
3,13 |
100 |
2,1 |
40 |
3 |
1,31 |
250 |
15,3 |
40 |
3 |
23,91 |
40 |
200 |
9,3 |
40 |
3 |
11,63 |
80 |
200 |
9,8 |
40 |
3 |
12,25 |
90 |
500 |
24,86 |
40 |
4 |
62,15 |
600 |
6,54 |
40 |
4 |
19,62 |
500 |
8,7 |
40 |
4 |
21,75 |
100 |
500 |
2,7 |
35 |
4 |
7,71 |
850 |
12,3 |
35 |
4 |
59,74 |
110 |
150 |
9 |
35 |
2 |
12,86 |
120 |
150 |
10,7 |
35 |
2 |
15,29 |
130 |
100 |
11,8 |
45 |
2 |
8,74 |
100 |
3,3 |
45 |
2 |
2,44 |
150 |
6,9 |
45 |
2 |
7,67 |
ИТОГО |
285,44 |
Таблица 14. Затраты на инструмент в предлагаемом ТП
№ |
Стоимость инструмента, руб. |
Время работы инструмента, мин |
Период стойкости, мин |
Число переточек |
Затраты на инструмент, руб. |
20 |
200 |
7,4 |
80 |
3 |
4,63 |
200 |
4,8 |
80 |
3 |
3,00 |
30 |
200 |
19,9 |
80 |
3 |
12,44 |
70 |
1200 |
9,2 |
80 |
4 |
27,60 |
1200 |
2,2 |
80 |
4 |
6,60 |
1200 |
5,1 |
80 |
4 |
15,30 |
1200 |
8,2 |
80 |
4 |
24,60 |
2000 |
2,7 |
80 |
4 |
13,50 |
2000 |
1,5 |
80 |
4 |
7,50 |
1500 |
3,1 |
80 |
4 |
11,63 |
80 |
1200 |
1,5 |
80 |
4 |
4,50 |
2000 |
3,3 |
80 |
4 |
16,50 |
2000 |
1,8 |
80 |
4 |
9,00 |
1000 |
6,1 |
80 |
4 |
15,25 |
300 |
2,4 |
80 |
4 |
1,80 |
550 |
3 |
80 |
4 |
4,13 |
1500 |
12,4 |
80 |
4 |
46,50 |
ИТОГО |
224,46 |
5.
Затраты на технологическую электроэнергию



6.
Затраты на обслуживание и ремонт оборудования



7.
Прочие общезаводские расходы



СТБАЗ = 1533+244,9+5,66+285,44+19,83+82,2+594,88=2765,91 руб.
СТПРЕД =1533+199,92+26,46+224,46+12,67+51,22+404,45=2452,18 руб.
Из выполненного расчета экономических параметров видно, что предлагаемый технологический процесс является экономически более эффективным.
2. Разработка и конструирование средств технологического оснащения
2.1 Описание приспособления
Деталь на токарных ЧПУ операциях наружной цилиндрической поверхностью устанавливается и зажимается в трехкулачковый патрон фирмы SMW-AUTOBLOCK.

Рис. 9 Патрон фирмы SMW-Autoblock
2.2 Определение сил резания
Силу резания Р принято раскладывать на составляющие направленные по осям координат станка Pz, Py, Px. При наружном продольном и поперечном точении, растачивание и отрезании эти составляющие вычисляются по следующей формуле
Px, y, z = 10*Cp*tx *sy *νn *Kp
где t, s, ν – глубина резания в мм, подача мм/об, скорость резания м/мин.
Постоянную Cp и показатели степени x, y и n выписываем из таблицы №22 книги «Справочник технолога - машиностроителя» том 2.
Поправочный коэффициент Кр представляет собой произведения ряда коэффициентов
Кр = Кмр Кφр Кγр Кλр Кrр
Значения этих коэффициентов находим так же в «Справочнике технолога - машиностроителя».
В нашем случае значение нужных нам величин равны:
t = 2 мм
s = 0,3 об/мин
ν = 160 м/мин
Кр = Кмр Кφр Кγр Кλр Кrр = 0,85*0,94*1,1*0,93=0,81
Для силы Pz:
Сp = 300
x = 1
y = 0.75
n = -0.15
Для силы Px:
Сp = 339
x = 1
y = 0.5
n = -0.15
Находим численное значение составляющих сил резания:
Pz = 10*Cp*tx *sy *νn *Kp
Pz = 10* 300*21*0,30,75*160(-0,15)*0.81= 920.15 Н.
P x = 10*Cp*tx *sy *νn *Kp
Px = 10*339*21*0,30,5*160(-0,15)*0.81 = 1404.94 Н.
2.3 Силовой расчет приспособления
Определение силы зажима в патроне(1 способ)
Составляем схему взаимодействия сил резания и сил зажима на деталь установленную в патроне.

Рис. 10 Схема для расчета сил зажима заготовки
Рассмотрим действие двух сил Pxи Pz на обрабатываемую деталь, зажатую в трехкулачковом патроне станка; сила резания Pz создает момент
Мрез = Pz * r1
который стремится повернуть обрабатываемую деталь вокруг ее оси, а сила Px – переместить деталь вдоль её оси.
Суммарная сила зажима обрабатываемой детали тремя кулачками патрона
Wсум *f*r = K*Mрез =К*Pz*r1,
откуда
Wсум = К*Мрез/(f*r) = K*Pz*r1/(f*r),
где:
К=1.4-2.6 – коэффициент запаса
Мрез – момент от силы резания Pz
f – коэффициент трения между поверхностями детали и кулачков
r – радиус обрабатываемой части детали
r1 – радиус обработанной части детали
Тогда сила зажима деталей одним кулачком патрона
W = Wсум/z
где z – число кулачков патрона, z=3.
Находим численное значение силы зажима:
Wсум = K*Pz*r1/(f*r)
Wсум = 2*920,15*226/(0.06*230)= 30133
Величину Wсум проверяют на возможность продольного сдвига обрабатываемой детали силой Рх по формуле:
Wсум*f ≥K*Px
откуда
Wсум ≥K*Px/f
Проверим:
30133≥2*1404/0,06
30133≥46800
Так как так расчетная сила зажима оказалась меньше силы продолного сдвига силы Рх, окончательно выбираем суммарную силу зажима равную 46800 Н или силу в 15600 Н на один кулачек.
Определение силы зажима в патроне(2 способ)

Рис. 11 Схема для расчета сил зажима заготовки



Сумма моментов на плоскость торца детали относительно центра равна:

Отсюда сила зажима равна:

где: Pz – составляющая силы резания
Px – составляющая силы резания
D1 – обрабатываемый диаметр детали
D2 – обработанный диаметр детали
D3 – диаметр на который приложена сила реакции опоры
f – коэффициент трения
Pz = 920.15 Н, Px = 1404.94 Н, D1 = 228, D2 = 230, D3 = 200, f = 0,06

Суммарная сила зажима равна:


2.4 Расчет приспособления на точность
Определяем необходимую точность приспособления для размера
Æ206H14 (-0,115).
Погрешность базирования: εб = 0,01 мм
Погрешность закрепления: εз = 0 т.к. сила зажима действует перпендикулярно выдерживаемому размеру.
Погрешность установки фактическая:
εб = εб + εз = 0 + 0,01 = 0,01 мм
Суммарная погрешность обработки:
εс = εу + К ∙ ώ т.с. = 0,01 + 0,7 ∙ 0,07 = 0,059 ≈ 0,06 мм
Расчёт допустимой установки погрешности:
__________ ____________
[εу] = √Т2 - К2 ∙ ώ2тс = √0,12 + 0,72 ∙ 0,072 = 0,09 мм
εтс = 70 мкм, допуск полного радиального биения по ОНВ ГОСТ24642-81
0,01 ≤ 0,09
если εу ≤ [εу], то предлагаемая схема считается допустимой
Расчет суммарной погрешности:
___________ ______________
εпр = Т- √ εу 2 + К2 ∙ ώ2тс = 0,1- √0,01 2 + 0,72 ∙ 0,072 =0,1 - 0,043 = 0,057 ≈ 0,06 мм
Расчёт погрешности собранного приспособления:
Тс = εпрΣ - (εупс + εизн + εпер) = 0,06 - (0 + 0 + 0) = 0,06 мм
εупс = 0, погрешность установки приспособления
εизн = 0, т.к. установка заготовки производится без зазоров
εпер = 0, т.к. отсутствуют направляющие элементы режущего инструмента
Собранное приспособление удовлетворяет всем требования технического задания.
3. Удаление заусенцев металлической щеткой
При фрезеровании трех лысок на наружном диаметре 200 (База Е), на операции «070 Токарная с ЧПУ» образуются заусенцы по контуру лыски. Наличие заусенцев предполагает наличие слесарной операции, после токарной операции, для их удаления. В базовом технологическом процессе так и было. В предлагаемом технологическом процессе слесарная операция заменяется технологическим переходом в операции 070. Заусенцы предлагается убирать вращающейся металлической щеткой, по контуры лыски, траектория щетки будет задана программой. Металлическую щётку подбираем по онлайн каталогу фирмы «Osborn».
3.1 Выбор щётки по каталогу
Одним из всемирно признанных производителей технических и бытовых щёток является немецкая фирма OSBORNINTERNATIONAL. Отличительной особенностью этой фирмы является не только то, что она на своих заводах выпускает огромный ассортимент инструмента (более 80 тысяч наименований), но, что особенно важно для российских потребителей, предлагает и технологии их применения.
Обычно до недавнего времени щётки, как правило, относились до к вспомогательному, как бы «второстепенному», инструменту, который использовали традиционно для снятия окалин, удаления старых покрытий.
Все щётки обладают максимальной безопасностью и надёжностью в эксплуатации, экономичны, характеризуются высокой стойкостью.
Фирма OSBORN INTERNATIONAL предлагает поставку щёток с соответствие с тремя каталогами:
- OSBORNPRO – щетки повышенной стойкости для профессионального применения на крупных промышленных предприятиях.
- OSBORNTOP – топовая серия для выполнения особо ответственных задач. Для эксплуатации в самых тяжелых условиях.
- OSBORNECO – экономный вариант щеток для частных мастерских и мелких предприятий.
Для нашего вида работ, выбираем оптимальный каталог – OSBORN PRO. В разделе «Щётки для высокооборотных машин» выбираем специальные концевые щётки точечной формы.

Рис. 12 Специальные концевые щётки
Таблица №15. Основные типоразмеры щёток
Размер (мм) |
Тип |
Максимальное число оборотов |
Стандартная упаковка |
D |
T |
K |
L |
об/мин |
шт. |
8,9 |
29 |
9,5 |
57 |
122F |
12000 |
12 |
9,5 |
29 |
11 |
55 |
123F |
12000 |
12 |
10 |
27 |
8 |
158 |
121F/L |
12000 |
6 |
12 |
29 |
13 |
60 |
124F |
12000 |
12 |
12 |
55 |
12 |
55 |
302 |
12000 |
6 |
20 |
25 |
22 |
47 |
102F |
12000 |
6 |
20 |
70 |
22 |
51 |
303 |
12000 |
6 |
28 |
25 |
29 |
47 |
103F |
12000 |
6 |
По каталогу выбираем щетку с диаметром щётки 10 мм.

Рис. 13 Основные размеры выбранной щётки
3.2 Выбор режимов резания по каталогу
Сначала определим оптимальное позиционирование щётки по отношению к обрабатываемой детали. Прижимное усилие наряду с другими параметрами регулируется глубиной погружения обрабатываемой детали в рабочий материал щётки. В качестве рекомендации действует трёхкратность к используемому ворсу, к примеру, 1 мм глубины при диаметре ворса 0,35 мм.
Использую таблицу рекомендаций по выбору числа оборотов и подачи в каталоге, подберем режимы резания:
Таблица №16. Таблица линейных скоростей
Таблица линейных скоростей. |
Об/мин |
Диаметр щетки в мм. |
10 |
800 |
- |
900 |
- |
1150 |
- |
1200 |
0,75 |
1400 |
0,8 |
1500 |
0,9 |
1800 |
1 |
2000 |
1,1 |
2500 |
1,2 |
2800 |
1,3 |
3000 |
1,4 |
n = 1200 об/мин
f = 0,75 мм/об
t = 1мм

Рис. 14 3D Модель выбранной щётки
3.3 Предписание по монтажу
- Недопустимо превышение числа оборотов, указанных на щётке. Убедитесь, что машина не имеет большего числа оборотов.
- Длина приводного вала должна обеспечивать прочное соединение зажимной гайки с валом.
- Щётки с хвостовиком могут беспроблемно зажиматься в патрон дрели.
- Щётки с резьбой имеют поверхность под ключ, что обеспечивает беспроблемный монтаж/демонтаж.
3.4 Общие указания по технике безопасности
Во время обработки поверхности мы настоятельно рекомендуем ношение защитной одежды и очков в целях предотвращения травм посторонними предметами таких, как загрязнения, ржавчина, заусенцы и т.д. Также в непосредственной близости рабочего места не должны находиться лица без защитной одежды.
Принимайте во внимание в целях личной безопасности и безопасности окружающих рекомендованные рабочие и максимальные обороты для изделий ОСБОРНа и руководство по эксплуатации приводной машины.
4. Стандартизация и управление качеством продукции
Стандартизация – важное средство для повышения качества продукции и повышения производительности.
Стандартизация устанавливает и применяет правила, с целью упорядочения деятельности в определенной области на пользу и при участии всех заинтересованных сторон, в частности, для достижения всеобщей оптимальной экономичности, при соблюдении условий эксплуатации и требовании безопасности. Стандартизация устанавливает обязательные требования для обеспечения качества продукции; повышения производительности труда; экономичного использования материалов; энергии и безопасности. К методам стандартизации относится унификация – это метод, направленный на приведение объектов одинакового функционального назначения к единообразию и рациональному сокращению числа этих объектов и их составных частей.
Стандарты предприятий разрабатывают на создаваемые и применяемые только на данном предприятии процессы, требования, детали и узлы к изготовляемым изделиям.
4.1. Основные принципы системы качества (СК), применяющиеся на ОАО «АвиаАгрегат»
При рассмотрении системы качества ОАО «АвиаАгрегат» был определён следующий состав функций: политика и планирование качества, организация работ по качеству, контроль качества, информация о качестве, разработка мероприятий, внедрение мероприятий в производственный процесс.
Организация работ по качеству включает в себя следующие этапы:
Во-первых, - это разработка системы качества, т.е. - определение структур, входящих систему качества, их функций и методов работ.
СК создается и внедряется как средство, обеспечивающее проведение определенной политики и достижение поставленных целей в области качества.
СК должна охватывать все 4 стадии жизненного цикла продукции: исследование и разработка; изготовление; обращение и реализация; эксплуатация. Жизненный цикл продукции («петля качества») разделен на более мелкие этапы (см. рис. 13).

Рис. 15 «Петля качества» при производстве корпуса
Обеспечение качества продукции – совокупность планируемых и систематически проводимых мероприятий, создающих необходимые условия для выполнения каждого этапа петли качества. Планируемые мероприятия определяются целевыми научно-техническими программами повышения качества конкретной продукции, которые содержат требования к материалам, сырью, оборудованию, комплектующим изделиям, метрологическим средствам, производственному персоналу и т.д.
К систематически производимым мероприятиям относятся работы, которые выполняются предприятием постоянно или с определенной периодичностью (работы по изучению рынка, постоянному обучению персонала).
Особое место среди этих мероприятий занимают те, которые связаны с предупреждением различных отклонений. В соответствии с идеологией стандартов ИСО серии 9000 СК должна функционировать таким образом, чтобы обеспечить уверенность в том, что проблемы предупреждаются, а не выявляются после возникновения (принудительная замена технологической оснастки и инструмента, ППР, обеспечение необходимой документацией всех рабочих мест и своевременное изъятие устаревшей документации).
Управление качеством – методы и деятельность оперативного характера (управление процессами, выявление различного рода несоответствий в продукции, производстве и их устранении).
Пример (рис. 10) - статистическое регулирование техпроцесса с помощью контрольных карт предупреждает появление дефектов или отклонений и является предпочтительным перед методом, связанным с управлением качеством по уже случившимся отклонениям.

Рис. 16 Схема «замкнутого управленческого цикла»
Меры по выявлению и устранению отклонений и их причин известны как замкнутый управленческий цикл, который включает контроль, учет, анализ (оценку), принятие и реализацию решения.
Управление качеством должно предусматриваться как необходимый принцип по отношению ко всем элементам системы качества на всех этапах петли.
Улучшение качества – постоянная деятельность, направленная на повышение технического уровня продукции, качества ее изготовления, совершенствование элементов производства и системы качества. Улучшение качества связано с решением задачи получения результатов, лучших по отношению к первоначально установленным нормам.
Идеология постоянного улучшения качества прямо связана и вытекает из тенденции повышения конкурентоспособности такой продукции, которая обладает высоким уровнем качества при более низкой цене. В связи с этим целью постоянного улучшения качества является либо улучшение параметров продукции, либо повышение стабильности качества изготовления, либо снижение издержек.
Характерной организационной формой работ по улучшению качества являются группы качества, рационализаторская деятельность, создание временных творческих коллективов.

Рис. 17 Иллюстрация снижения потерь за счет улучшения качества
П 0 - начальные потери; Т о - размах средних арифметических базовых значений (математического ожидания) показателя надёжности; Т 1 – то же самое в предлагаемом варианте.
Материалы, комплектующие детали и узлы, закупленные предприятием, становятся частью выпускаемой им продукции, за качество которой изготовитель несет ответственность.
После разработки следует этап внедрения системы качества, в течение которого проводятся внутренние проверки системы и, как правило, - ее доработка по результатам проверок.
Завершающим этапом можно считать сертификацию системы качества на соответствие стандартам ИСО 9000. Получение такого сертификата от авторитетного, независимого органа существенно укрепляет позиции предприятия на рынках сбыта, т.к. дает заказчикам дополнительную уверенность в возможности предприятия стабильно обеспечивать требуемый уровень качества.
При организации работ по качеству крайне важно обратить внимание на то, чтобы на всех этапах производственного процесса было предусмотрено все необходимое для обеспечения качества продукции: хорошие материалы, современное оборудование инструмент и средства измерений, хорошо обученный дисциплинированный персонал и необходимая документация.
На авиационных предприятиях применяются следующие виды контроля качества:
- контроль проектирования
- входной контроль материалов и комплектующих изделий;
- контроль за состоянием технологического оборудования;
- операционный контроль при изготовлении;
- авторский надзор за изготовлением;
- активный контроль приборами, встроенными в технологическое оборудование;
- приемочный контроль готовой продукции;
- контроль монтажа и надзор за эксплуатацией на объектах;
- выборочный контроль;
- сплошной контроль.
Из нормативных документов, регламентирующих метрологическую деятельность, а первую очередь следует упомянуть закон РФ о единстве измерений и международный стандарт ИСО 10012-1:1992 о подтверждении метрологической пригодности измерительного оборудования.
Оценку качества готовой продукции на предприятии ОАО «АвиаАгрегат» проводят в следующей последовательности:
1. Выбор показателя качества оцениваемой продукции.
2. Оценка показателя качества.
3. Сравнение с базовыми значениями.
При обработке детали «Корпус ТМ966.2120-35» к параметрам качества относят следующие параметры: точность размеров; формы и расположение обрабатываемых поверхностей детали; твердость; шероховатость поверхности; структура материала.
Надежность и долговечность работы корпуса в значительной степени зависит от точности размеров, а также структурного состояния материала и шероховатости поверхностей.
Мероприятия по обеспечению качества продукции Корпус на предприятии ОАО «АвиаАгрегат»:
- входной контроль качества заготовок;
- статистический контроль качества действующих технологических процессов;
- активный контроль выполняемых размеров на отдельных операциях;
- аттестация выпускаемой продукции.
На этапе поставок прутков на предприятие необходимо обеспечить мероприятия связанные с контролем и выявлением недоброкачественной продукции поставщиков. Для этого необходимо и достаточно реализовать контроль поверхности заготовок, контроль предельных отклонений размеров заготовок, контроль твёрдости материала заготовок, которые должны удовлетворять требованиям предусмотренным ОСТ 1.90073-72, ОСТ 1.41187-78.
Важным моментом эффективности обработки корпуса является применение средств активного контроля.
Задача средств активного контроля (САК) состоит в выдаче информации о размере обрабатываемой или только что обработанной детали. Информация в определенной форме используется оператором или автоматически для управления станков с целью получения требуемого размера. Результаты измерения размера детали активно воздействуют на получение требуемого размера и предупреждают брак.
Средства активного контроля помогают не только увеличить производительность труда и точность обработки деталей, на и не вводить дополнительное оборудование и производственные площади.
Экономическая эффективность от повышения производительности за счет САК определяется сокращением времени, затрачиваемого на пробные изменения и вспомогательные действия, связанные с измерениями.
Твёрдость детали проверяется с точностью до 10 ед. НВ.
Шероховатость базовых поверхностей проверяют на двойном микроскопе МИС – 11 с точностью измерения 4,5…10 Rа.
Контроль геометрических параметров обработанных поверхностей осуществляется мерительными инструментами, указанными в операционном контроле.
В предлагаемом процессе также в качестве средства контроля режущей кромки инструмента предполагается использовать специальную измерительную руку Renishaw HPPA (Рис.16).
Данная рука представляет собой специальный кронштейн, который подводится непосредственно к режущей кромке инструмента и контролирует его с высокой точностью. Данная рука позволяет наладить процесс обработки в автоматическом режиме и устранить брак возникающий по причине поломки инструмента, точность измерения инструмента δ=0,005 мм.

Рис. 18 Общий вид руки
Наладка инструмента проводится для следующих типов инструмента:
-наладка неподвижных резцов, отрезного инструмента и т. п. в направлениях X и Z.
-наладка вращающегося инструмента (приводного инструмента типа сверл, метчиков и пазовых фрез) по длине и/или диаметру в направлениях X и Z (Рис.4.5).
Также осуществляется определение поломки инструмента:
-быстрая проверка режущего инструмента на предмет поломки (изменения размеров) после окончания обработки.

Рис. 19 Наладка инструмента
4.3 Применение методов статистического регулирования ТП изготовления детали «Корпус ТМ966.2120-35» и статистического приемочного контроля
Применение статистического регулирования технологического процесса изготовления детали «Корпус ТМ966.2120-35» представляет собой корректировку параметров процесса по результатам выборочного контроля параметров продукции, осуществляемого для технологического обеспечения заданного уровня качества. Статистическое регулирование технологического процесса осуществляется с помощью контрольных карт, на которых отмечают значения определенной статистики, полученной по результатам выборочного контроля. Такими статистиками являются среднее арифметическое , медиана , среднее квадратическое отклонение S, размах R, доля дефектных единиц продукции Р и др. На контрольной карте отмечают границы регулирования, ограничивающие область допустимых значений статистики. Выход точки за границы регулирования (или появление ее на самой границе) служит сигналом о разладке технологического процесса. Контрольная карта позволяет не только обнаруживать разладку процесса, но и помогает выявлять причины возникновения разладки. Кроме того, контрольная карта служит документом, который может быть использован для принятия обоснованных решений по улучшению качества продукции. На основании анализа результатов контрольной карты может быть принято, например, решение о пересмотре допуска на контролируемый параметр, либо это может послужить достаточным основанием для замены или модернизации оборудования. Контрольные карты используются в виде графиков, полученных в ходе технологического процесса. Графики отражают динамику процесса. Применяют различные контрольные карты: медиан, р-карты (дефектной продукции), pn-карты, с-карты.
По способу отбора изделий, подвергаемых контролю качества, различают сплошной (стопроцентный) и выборочный контроль. Для сокращения затрат на контроль в крупносерийном производстве больших партий изделий (генеральной совокупности) контролю подвергают только часть партии - выборку. Выборка производиться случайным образом. Если уровень качества изделий в выборке соответствует установленным требованиям, то считают, что всю партию можно принять как годную. В противном случае партия бракуется.
Статистический приемочный контроль качества продукции - это выборочный контроль качества продукции, основанный на применении методов математической статистики для проверки соответствия качества продукции установленным требованиям.
В отличие от статистического регулирования технологических процессов, где по результатам контроля выборки принимается решение о состоянии процесса (налажен или разлажен), при статистическом приемочном контроле по результатам контроля выборки принимается решение - принять или отклонить партию продукции. Поэтому статистический приемочный контроль применяется при входном контроле материалов, сырья и комплектующих изделий, контроле закупок, при операционном контроле, при контроле готовой продукции. Статистический приемочный контроль может осуществляться по количественному, качественному и альтернативному признакам. Статистический приемочный контроль может быть одноступенчатым, двухступенчатым, многоступенчатым и последовательным. При одноступенчатом контроле решение о контролируемой партии продукции принимается на основании проверки только одной выборки или пробы. Это наиболее простой вид контроля. При двухступенчатом контроле решение о контролируемой партии продукции принимается по результатам проверки не более двух выборок или проб, причем отбор второй выборки или пробы зависит от результатов контроля первой выборки или пробы. То есть, первоначально для проверки отбирается небольшое число образцов, и если дефектов при их проверке окажется много, партия отклоняется, если мало - принимается. Когда число обнаруженных дефектов оказывается недостаточно убедительным, проверяются образцы второй выборки и соответствующее решение принимается по сумме результатов обеих проверок.
Преимущество двухступенчатого контроля заключается в том, что в среднем он требует при прочих одинаковых условиях на 20-30% меньше изделий для проверки, чем при одноступенчатом контроле. Однако, двухступенчатый контроль требует более высокой квалификации контролеров и организационно более сложен. При многоступенчатом и последовательном контроле решение о контролируемой партии продукции принимается по результатам проверки ряда последовательных выборок, причем при многоступенчатом контроле максимальное число выборок ограничено, а при последовательном - нет. В обоих случаях отбор последующей выборки или пробы зависит от результатов проверки предыдущей выборки или пробы. При последовательном контроле в среднем требуется при прочих равных условиях минимальное количество изделий для проверки. Следует отметить, что среднее число проверяемых изделий с ростом числа ступеней убывает, однако, организационные трудности внедрения многоступенчатого контроля, как правило, не компенсируются экономией от сокращения среднего числа проверяемых изделий. По этой причине многоступенчатый контроль в практике применяется редко. Последовательный контроль получил распространение в практике ресурсных испытаний на надежность, где по условиям их проведения очень важно сокращение объема выборок
4.4 Нормативная документация, использованная при выполнении данного раздела пояснительной записки
1. ИСО 8402-94. Управление качеством и обеспечение качества. Словарь.
2. ИСО 9001:2000 Международная система управления качеством.
3. ГОСТ 24297 - 87 Входной контроль. Основные положения.
4. ГОСТ Р ИСО 9002 - 96. Системы качества. Модель обеспечения качества при производстве, монтаже и обслуживании.
5. Р50 - 601 - 40 - 93. Входной контроль. Основные положения.
6. P50-601-27-92. Формирование, реализация и актуализация политики предприятия в области качества
7. РД 50-605 -86. Приемочный статистический контроль.
8. ГОСТ 15467-79 Качество продукции
9. ГОСТ 2.116-84 ЕСКД Карта технического уровня и качества продукции.
10. ГОСТ 14318-83 ЕСТПП Правила разработки процессов контроля.
11. ГОСТ 27401-83 Надежность в технике.
12. ГОСТ 24297-80 ЕСКД Входной контроль качества продукции.
Основные положения.
13. ГОСТ 22.732-77 Методы оценки уровня качества промышленной продукции.
14. ГОСТ 14.318-77 ЕСТПП Виды процессов контроля.
15. ГОСТ 94297-80 СПКП Входной контроль качества продукции.
16. Основные положения.
17. ГОСТ 22851-77 Выбор номенклатуры показателей качества пром. продукции.
18. ГОСТ 14.318-83 ЕСТПП Виды процессов контроля.
19. ГОСТ 24.002-83 Надежность в технике. Термины и определения.
20. ГОСТ 27.307-83 Надежность в технике. Прогнозирование надежности изделий.
5. Охрана окружающей среды
Отходы производства и потребления (остатки сырья, материалов, полуфабрикатов, иных изделий или продуктов), образовавшихся в процессе производства и потребления подразделяются:
По классам опасности |
По видам |
По видам опасности |
По способам удаления отходов |
чрезвычайно опасные |
бытовые |
пожаро - и взрывоопасные |
захоронение |
высокоопасные |
пищевые |
горючие |
переработка |
умеренно опасные |
биологические |
радиоактивные |
хранение |
малоопасные |
химические |
химические реакционно-способные |
практически неопасные |
коррозионно-активные |
опасные по степени воздействия на человека |
Технологические операции обработки детали «Корпус ТМ966.2120-35», можно подразделить на следующие виды:
Операции механической обработки:
· токарные;
· фрезерные;
· сверлильные;
Вспомогательные операции:
· контрольные;
· моечные;
· термическая закалка.
При выполнении операций механической обработки
используются токарные станки, станки с ЧПУ, многофункциональные токарные обрабатывающие центры. Применяются инструменты: токарные резцы, сверла, фрезы, метчики.
Вспомогательные операции
выполняются вручную на специальном оборудовании.
В процессе изготовления детали типа «Корпус» возникают следующие отходы:
· стружка;
· СОЖ.
А также возникают следующие вторичные отходы:
· отработанное масло;
· опилки;
· ветошь;
· отработанный инструмент (сверла, развертки, зенкера, фрезы и т.д.).
Стружка
При обработке заготовки точением или фрезерованием образуется стружка. Остается решить вопрос об удалении стружки от станка и рабочей зоны. Данный станок фирмы «MONFORTS» имеет наклонную станину, обеспечивающую свободный сход стружки и удобный доступ к обрабатываемой заготовке.
Стружка падает на скребковый конвейер, расположенный под станком и удаляется в специальный контейнер. При заполнении контейнера производится его замена.
Обработку твердых отходов целесообразно проводить в местах образования отходов, что сокращает затраты на погрузочно — разгрузочные работы, снижает безвозвратные потери при их перевозке и транспортировке и высвобождает транспортные средства.
Эффективность использования лома и отходов металлов зависит от их качества. Загрязнение и засорение отходов приводит к большим потерям при переработке, поэтому сбор, хранение и сдача их регламентируются специальными стандартами. Основные операции первичной обработки металлоотходов - сортировка, разделка и механическая обработка. Согласно дополнительного соглашения №681 завод ОАО «Авиаагрегат » утилизирует лом черных металлов на завод ОАО «Самаравтормет».
СОЖ
Современные СОЖ представляют собой сложные многокомпонентные композиции, отвечающие комплексу требований к их технологическим и сопутствующим свойствам. Но в процессе многократного использования при механической обработке металлов СОЖ теряют свои технологические свойства, и возникает необходимость в её замене и последующей утилизации.
Наиболее часто используемый метод с предварительной очисткой от механических примесей является реагентный метод разложения отработанных эмульсий. Его основным достоинством является простота реализации технологического процесса, доступное оборудование и материалы.
На ряде крупных российских предприятий действуют технологические системы утилизации СОЖ с применением реагентов-коагулянтов, флокулянтов, минеральных кислот и щелочей.
Однако остаточные концентрации загрязняющих веществ в водной фазе после разложения СОЖ достаточно велики, в десятки раз превышая установленный предельно допустимый сброс (ПДС.
Для комплексной утилизации СОЖ используют гидрофобизированные порошки (ГФП) на основе природных сорбентов. Установлена возможность и эффективность их применения, как для разрушения отработанной эмульсии, так и для очистки водной и масляной фаз. Сорбционный метод разрушения эмульсий обладает рядом преимуществ по сравнению с реагентным методом.
Вторичные отходы
Часть этих отходов (отработанное масло; ветошь; СОЖ, загрязненная маслом и стружкой, опилки) являются пожароопасными. Поэтому они хранятся в специальных пожаробезопасных емкостях, с огнеупорными стенками.
Площадки для сбора и временного хранения отходов покрыты неразрушимым и непроницаемым для токсичных веществ материалом; освещены; обеспечены первичными средствами пожаротушения и подъездами для погрузочно-разгрузочных работ. Передача отходов сторонним организациям для их дальнейшего захоронения, переработки, использования, обезвреживания осуществляется только при наличии у них разрешающих документов на осуществление данного вида деятельности. Для всех подразделений предприятия, проектным управлением разрабатываются проекты нормативов образующихся отходов и лимиты на их размещение, на основании которых главным управлением природных ресурсов по Самарской области ежегодно выдаются лимиты на размещение, передачу и переработку отходов. Основным документом в сфере обращения с отходами является государственный статистический отчет по форме 2-ТП (отходы) «Сведения об образовании, использовании, обезвреживании, транспортировке и размещении отходов производства и потребления», который предъявляется в природоохранительные органы.
Использованные ветошь, опилки и тканевые фильтры для механической очистки СОЖ сжигают на отходоперерабатывающих предприятиях.
Отработанное масло
Один литр отработанного масла делает непригодными для питья до 1000000 (миллиона) литров грунтовой воды.
Регенерация отработанных масел – один из самых экологически выходных способов утилизации.
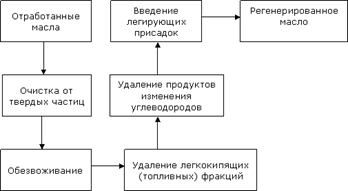
На первой стадии используется грубое удаление воды и механических примесей путем осаждения при повышенной температуре в сырьевом парке, имеющем в своем составе 36 емкостей от 60 до 120 кубометров. Удаление продуктов окисления отработанных присадок и других примесей осуществляется в процессе коагуляции. При этом, в зависимости от химической структуры регенерируемых масел, используются различные коагулянты или их композиции, определенные лабораторными и опытно-промышленными испытаниями: сначала проводятся пилотные лабораторные обработки образцов, после чего подбирается оптимальный коагулянт.
Окончательная доочистка масляных фракций осуществляется на фильтровальном блоке с использованием высокоэффективного природного минерального адсорбента, который является экологически чистым продуктом.
Режущий инструмент
В настоящее время для производства режущих инструментов широко используются твердые сплавы. Они состоят из карбидов вольфрама, титана, тантала, сцементированных небольшим количеством кобальта. Карбиды вольфрама, титана и тантала обладают высокой твердостью, износостойкостью. Скорости резания инструментами, оснащенными твердыми сплавами, в 3-4 раза превосходят скорости резания инструментами из быстрорежущей стали. Недостатком твердых сплавов, по сравнению с быстрорежущей сталью, является их повышенная хрупкость, которая возрастает с уменьшением содержания кобальта в сплаве. И, следовательно, возникает вопрос утилизации таких сплавов. Переработка лома и отходов позволяет вернуть металл в кругооборот. Твердосплавные пластинки режущих инструментов, накапливаются и сдаются, как вторсырьё производителю инструмента. Неисправные державки, подлежащие ремонту, восстанавливаются во вспомогательном цехе завода. Не подлежащие ремонту инструменты сдаются на металлолом.
6. Охрана труда
6.1 Классификация опасных и вредных производственных факторов при изготовлении детали «Корпус»
БЖД — система знаний, направленных на обеспечение безопасности в производственной и непроизводственной среде с учетом влияния человека на среду обитания. Наука о безопасности жизнедеятельности исследует мир опасностей, действующих в среде обитания человека, разрабатывает системы и методы защиты человека от опасностей. В современном понимании безопасность жизнедеятельности изучает опасности производственной, бытовой и городской среды, как в условиях повседневной жизни, так и при возникновении чрезвычайных ситуаций техногенного и природного происхождения.
Целью
БЖД является достижение безаварийных ситуаций, предупреждение травматизма, сохранение здоровья человека, повышение работоспособности и качества труда.
Технологический процесс изготовления корпуса включает в себя следующие операции:
Наименование операции |
Оборудование |
Инструмент |
Приспособление |
Отрезная |
Hercules |
Пила ленточная |
Призматические тиски |
Токарно-винторезная |
1М63 |
Токарные резцы |
3-х кулачковый патрон |
Токарная с ЧПУ |
Monforts RNC 700 |
Токарные резцы, фреза, свела, метчик |
3-х кулачковый патрон |
Слесарная |
Верстак слесарный Н2.007 |
Надфиль, ПШМ ИП2020 |
–– |
Контрольная |
Стол контролёра |
–– |
–– |
Согласно [__], опасные и вредные производственные факторы подразделяются по природе действия на следующие группы: физические, химические, биологические, психофизиологические.
При выполнении технологического процесса изготовления корпуса на работников действуют следующие опасные и вредные технологические факторы:
- физические
- открыто движущиеся, вращающиеся, выступающие части оборудования (станков, приспособлений, инструментов и т.д.);
- повышенный уровень шума и вибрации на рабочем месте;
- отходящая из зоны резания стружка всех видов;
- тепловые факторы (горячие предметы обрабатываемых деталей);
- острые кромки, заусенцы и шероховатость на поверхностях заготовок, инструментов и оборудования;
- недостаток естественного света;
- избыточная влажность при испарение СОЖ.
- химические
- пары и газы от смазывающе-охлаждающей жидкости (СОЖ); по характеру воздействия – раздражающие, проникают в организм человека через кожный покров и слизистые оболочки;
- психофизиологические
- физические перегрузки;
- нервно-психические перегрузки.
Вышеперечисленные опасные и вредные производственные факторы могут стать причинами профзаболеваний и несчастных случаев.
6.2 Разработка мероприятий по устранению опасных и вредных производственных факторов
Рассмотрим более подробно каждую из операций технологического процесса, связанные с ней ОВПФ и мероприятия по устранению данных ОВПФ.
Отрезная операция
выполняется ленточной пилой. При работе за пилой рабочий должен строго соблюдать инструкцию по технике безопасности №180, во избежание травмирования или несчастного случая. Т.к. данный тип оборудования является универсальным, то он имеет весьма низкий уровень автоматизации процессов, поэтому автоматические средства защиты здесь не предусмотрены. Обеспечить безопасность при обработке, призваны оградительные щитки и ограждения.
Токарно-винторезная операция
выполняется на одношпиндельном токарном станке 1М63, с использованием охлаждающей жидкости Велс 1М. В качестве инструмента используются 4-х и 3-х угольные пластины с держателями. Станки токарной группы составляют около 30% всего парка металлорежущих станков. При работе на токарных станках наиболее часто отмечаются случаи ранения рук, ног станочника ленточной сливной стружкой, образующейся при обработке вязких материалов. Наиболее эффективным средством предупреждения порезов ленточной стружкой является изменение ее формы в процессе резания путем завивания в винтовую спираль или дробления на отдельные элементы. Это осуществляется приданием передней поверхности резца криволинейной формы, а также устройством на передней поверхности резца постоянных или регулируемых порогов. Принцип дробления ленточной стружки состоит в следующем: стружка, скользящая по поверхности резца, попадая в канавку, повторяет ее форму (обтекает профиль канавки) и, отклоняемая канавкой, завивается в кольцо. Если кольцо не встречает какого-нибудь препятствия свободному движению, то стружка завивается в непрерывную спираль. При упоре завитка стружки в препятствие (деталь, резец и др.) она дробится на отдельные элементы.
Наиболее рационально для работы на универсальных станках использовать сборные резцы, оснащенные многогранными неперетачиваемыми пластинками с мелкоразмерными канавками, формируемыми при прессовании пластинок.
Следует иметь в виду, что при использовании средств дробления стружки в процессе резания элементы, разлетаясь на значительное расстояние, представляют собой определенную опасность для травмирования глаз. Поэтому использование средств защиты (защитные экраны, очки) являются обязательным и необходимым.
Токарные с ЧПУ операции
выполняются на станке MonfortsRNC 700. На данной операции производится обработка основных формообразующих поверхностей детали. Не смотря на то, что рабочая зона станка закрывается герметично дверью, и всё управление ведется с дистанционного пульта, расположенного на отдельной стойке, при работе на станках с ЧПУ следует соблюдать дополнительные меры безопасности в сравнении с универсальным оборудованием. Это связано со спецификой данного оборудования. Станки, работая в полуавтоматическом режиме, выполняют программу. Необходимо следить за тем режимом, в котором в данный момент находится оборудование во избежание старта работы станка в процессе наладки станка, что может повлечь за собой травмирование оператора или привести к несчастному случаю. Таким образом, к пульту станка допускается только заранее подготовленные операторы. На пульте управления станка расположены кнопки отключения питания механизмов станка, останова программы, сброса программы. Кнопка отключения питания продублирована на корпусе станка на противоположной стороне от пульта.
При наладке станка на работу необходимо уделять отдельное внимание правильному и надежному закреплению инструмента и детали в патроне станка. Зажим на станке осуществляется при помощи патрона с пневматическом приводом. Устройство данного механизма подобно обычному патрону, с той лишь разницей, что привод кулачков патрона приводится в движение рычажной системой штока. Контроль зажимного усилия производится при помощи пневмодатчика, который контролирует рабочее давлении в рабочей полости пневмоцилиндра и поддерживает его в первоначальном виде для обеспечения силы зажима патрона.
При организации работы на токарном станке MonfortsRNC 700 к средствам защиты можно отнести автоматическую дверь станка, которая закрывается и тем самым ограничивает рабочую зону станка. В двери предусмотрено смотровое окошко, для контроля над процессом резания.
Стружка в процессе обработки выводится специальным конвейером, который складирует ее специальный приемник. Для хранения инструмента и специальной оснастки на участке предусмотрены специальные стеллажи и ячейки.
Поскольку данные станки с ЧПУ являются сложными машинами с большим количеством дополнительных узлов и агрегатов, то при начале работы со станком необходимо проверить все параметры работы станка, а именно: давление масла, давление воздуха, температуру подшипников шпинделя, параметры стойки с ЧПУ.

Рис. 20 Общий вид станка Monforts RNC 700
Чтобы устранить возникновение термического ОПФ в технологическом процессе предлагается в качестве смазочно-охлаждающей жидкости использовать пятипроцентный раствор «Велс-1» (ТУ 0258-017-00148843-2002), представляющий собой сбалансированную смесь минерального масла, эмульгаторов, ингибиторов коррозии, которые при смешении с водой образуют мелкодисперсную эмульсию, которая применяется во всех металлообрабатывающих станках.
Для устранения опасных и вредных производственных факторов на основных технологических операциях необходимо применять следующие меры безопасности:
- Оградительные устройства: кожухи, экраны (прозрачные и непрозрачные), коробки для вращающихся частей станка.
- Обеспечение надежного закрепления обрабатываемой детали и инструмента.
- Механизация транспортных и подъемно-транспортных средств и операций в цехе, применение электрокаров, конвейеров, тельферов и т.д.
- Герметизация и изоляция процессов с выделением газов, паров, пыли.
- Применение эффективных систем вентиляции рабочих мест.
Обеспечение всех рабочих специальной одеждой и средствами защиты от вредных воздействий.
Общецеховые мероприятия по устранению ОПФ и ВПФ на участке следующие:
- требуемое состояние воздуха в цехе обеспечивается приточно-вытяжной вентиляцией;
- для поддержания заданной температуры 20°С применяется система водяного отопления;
- при освещении производственного помещения используется совмещенное освещение, при котором естественное боковое освещение дополняется комбинированным искусственным освещением;
- защита тела рабочего обеспечивается применением средств индивидуальной защиты
- регулярность проведение инструктажей и бесед по технике безопасности с обслуживающим персоналом при использовании наглядной агитации, не реже чем 1 раз в 3 месяца.
6.3 Электробезопасность
< Помещение участка по электробезопасности относится к первой группе – без повышенной опасности (сухое, хорошо отапливаемое, помещение с токонепроводящими полами, с температурой 18—20°, с влажностью 40—50%).
Электропитание оборудования цеха обеспечивается от трехфазной трёхпроводной с изолированной нейтралью сети, трансформатором напряжением 220/380В с частотой 50 Гц, с заземлением.
Снижение вероятности поражения при коротком замыкании на металлические части станков, последние обеспечены заземлением к общему контуру заземления цеха. Также следует отметить, что в качестве электроустановок для местного освещения зоны обработки применены слаботочные электроустановки напряжением 12 / 24 В. Оснащение каждого рабочего места деревянной подставкой или резиновым ковриком также защищает от поражения электрическим током.
Основные причины несчастных случаев от воздействия электрического тока следующие:
- случайное прикосновение к токоведущим частям, находящимся под напряжением в результате: ошибочных действий при проведении работ; неисправности защитных средств, с которыми пострадавший касался токоведущих частей и др.
- появление напряжения на металлических конструктивных частях электрооборудования в результате: повреждения изоляции токоведущих частей; замыкание фазы на землю; падение провода (находящегося под напряжением) на конструктивные части электрооборудования и др.
- появление напряжения на отключенных токоведущих частях в результате: ошибочного включения отключенной установки; замыкания между отключенными и находящимися под напряжением токоведущими частями; разряда молнии в электроустановку и др.
- возникновения напряжения шага на участке земли, где находится человек, в результате: замыкания фазы на землю; выноса потенциала протяженным токопроводящим предметом (трубопроводом, железнодорожными рельсами); неисправностей в устройстве защитного заземления и др.
Основными мерами защиты от поражения электрическим током являются:
- обеспечение, по мере возможности, конструктивных характеристик станка недоступности к токоведущим частям, находящихся под напряжением;
- применение двойной изоляции, состоящей из рабочей и дополнительной части для проводки на открытых местах;
- оснащение каждого рабочего места деревянной подставкой или резиновым ковриком от поражения электрическим током;
- для снижения вероятности поражения при коротком замыкании станки должны быть обеспечены заземлением, подсоединенным к общему контуру общецехового заземления;
- применение слаботочных электроустановок для освещения;
- своевременные оповещения при ремонтных работах с помощью специальных предупреждающих табличек;
- проверкой, не реже одного раза в месяц контура общего заземления;
- обучением и проверкой знаний электробезопасности обслуживающего персонала.
6.4 Пожарная безопасность
Пожарная безопасность обеспечена мерами пожарной профилактики и активной пожарной защиты. Понятие пожарной профилактики включает комплекс мероприятий, необходимых для предупреждения возникновения пожара или уменьшения его последствий. Под активной пожарной защитой понимаются меры, обеспечивающие успешную борьбу с возникающими пожарами или взрывоопасной ситуацией.
Производство связано с технологическими процессами с использованием твердых негорючих веществ и материалов в холодном состоянии (механическая обработка металлов), поэтому производство можно охарактеризовать как не пожароопасное и отнести к категории «Д».
Максимально допустимое расстояние до выхода должно составлять – 50 метров. Широкие проходы (6 метров) и проезды обеспечивают возможность быстрой эвакуации из цеха в случае пожара.
По степени огнестойкости данный цех относится ко II степени, так как его конструкции выполнены из несгораемого материала – каркасного железобетона.
Анализируя возникновение пожаров на машиностроительных предприятиях, можно выделить причины неэлектрического и электрического характера.
К причинам неэлектрического характера относятся:
- неисправность, неправильное устройство и эксплуатация отопительных систем;
- неисправность производственного оборудования и нарушение технологического процесса;
- неосторожное и халатное обращение с огнём;
- неправильное устройство и неисправность вентиляционной системы.
К причинам электрического характера относятся:
- короткие замыкания;
- неисправность или перегрузка электрооборудования и электросетей;
- искрение и электрические дуги;
- большие переходные сопротивления в местах соединений, ответвлений, в контактах электромашин и аппаратов, приводящие к локальному перегреву.
Мероприятия для предупреждения пожарных ситуаций.
- планирование мероприятий по защите персонала от Ч.С.;
- обучение персонала;
- изучение методов и средств пожаротушения;
- обследование противопожарного состояния цехов;
- схемы эвакуации на участке;
- памятки о том, что нужно делать в случае пожара
- планировка помещений.
Для предотвращения пожаров и возгораний по всему периметру участка расположены огнетушители. Для оповещения о пожаре, на участке расположен громкоговоритель для массового оповещения рабочих о пожаре.
Средства пожаротушения:
- огнетушители ОУ – 140; ОП – 100(3).
- пожарные гидранты;
- системы автоматического пожаротушения.
6.5 Заключение
Внедрение инновационного технологического процесса позволило уменьшить травматизм и аварийные ситуации; повысило работоспособность и качество труда. Благодаря замене универсального оборудование на современные обрабатывающие центра Monforts RNC 700, удалось снизить многие ОВПФ. Порезы рук рабочих стали практически не возможными благодаря герметично закрывающейся двери, и не доступности зоны резания. Местное освещение зоны обработки, значительно лучше, чем на устаревшем оборудование. Применение мощных насосов для подачи эмульсии в зону резания позволяет снизить термический фактор (нагрева заготовки). В случае возникновения аварийной ситуации (например, вырыв заготовки из патрона) рабочий будет защищен стальной дверью и восьмислойным обзорным стеклом.
Применение токарного обрабатывающего центра оправдано, как с технологической точки зрения, так и с точки зрения охраны труда.
Заключение
В выполненной работе рассмотрен в сравнении с базовым альтернативный вариант технологического процесса изготовления детали «Крышка ТМ966.Сб2120–5СБ». Разработка велась с учетом того, что деталь представляет собой нежесткую конструкцию. В отличие от базового варианта, где токарная обработка построена, исходя из имеющегося в производстве оборудования, и поэтому излишне дифференцирована, предлагаемый вариант предусматривает использования токарных станков с ЧПУ, что позволяет повысить производительность обработки и точность геометрических параметров.
Сокращение числа операций привело к уменьшению трудоемкости изготовления детали и одновременно – себестоимости ее изготовления.
|