Содержание
1. Выбор электродвигателя. 3
1.1 Общий коэффициент полезного действия. 3
1.2 Мощность электродвигателя(предварительная) 3
1.3 Частота вращения. 4
1.4 Найдем передаточные числа ступеней. 4
2. Определение мощности, частоты вращения и крутящего момента валов редуктора. 5
2.1 Определим мощности. 5
2.2 Определим частоту вращения. 5
2.3 Определим крутящие моменты.. 6
3. Проектный и проверочный расчет зубчатых передач. 7
3.1 Тихоходная ступень. 7
3.2 Быстроходная ступень. 13
4. Предварительный расчёт валов редуктора. 20
5. Конструктивные размеры корпуса редуктора. 22
6. Крышки подшипников. 23
6.1. Крышка на быстроходный вал. 23
6.2. Крышка на тихоходный вал. 23
6.3 Крышка на промежуточный вал. 24
6.4 Выбор посадок для внутреннего кольца подшипника. 24
7. Смазывание зубчатой передачи. 25
8. Выбор муфт. 26
9. Расчет подшипников. 27
9.1 Реакции в горизонтальной плоскости. 27
9.2 Реакции в вертикальной плоскости. 28
9.3 Реакции от консольной силы.. 28
9.4 Полная реакция в опорах. 29
10. Проверочный расчет вала. 31
10.1 Проверочный расчёт вала на усталостную прочность. 31
10.2 Проверочный расчёт вала по перегрузкам.. 33
10.3. Проверочный расчёт вала на жёсткость. 34
11. Расчет шпоночного соединения. 35
Список используемой литературы.. 36

Где:
-к. п. д. привода;
-к. п. д. муфты;
-к. п. д. цилиндрической зубчатой передачи
кВт
где Р΄эл – предварительная мощность э/д, [кВт] ;
Рвых – мощность на выходе, [кВт] ;
кВт
где Ft = 1700 Н – окружная сила;
v = 0,9 м/с – скорость ленты;
Из таблицы определяем тип и параметры электродвигателя:
Тип 100LB6;
частота вращения ;
мощность электродвигателя
Частота вращения вала электродвигателя равна частоте вращения вала быстроходной ступени редуктора
Частота вращения вала тихоходной ступени 
Общее передаточное число 
Примем передаточное число тихоходной ступени Uт=4
Передаточное число быстроходной ступени
кВт;
;
;
;
где – мощность на валах, – коэффициенты полезного действия упругой муфты и цилиндрической передачи соответственно.
;
;
;

где – частоты вращения на валах редуктора, – передаточное число быстроходной и тихоходной ступеней редуктора соответственно.
;
;
;

где – крутящие моменты на валах.
Получившиеся результаты расчётов занесём в таблицу 1.
Таблица 1.
Вал
|
Частота вращения
n, об/мин
|
Мощность
P, Вт
|
Крутящий момент 
|
1
|
950
|
2156
|
21,67
|
2
|
184,11
|
1962
|
101,77
|
3
|
46,03
|
1903
|
394,82
|
4
|
46,03
|
1865
|
386,94
|
Материал колеса – сталь 40X(термообработка-улучшение).
Материал шестерни – сталь 40ХН(термообработка-закалка ТВЧ).
По таблице 3.1 имеем:
для шестерни: ;
для колеса: МПа
Отметим что шестерня входит в зацепление 3 раза, колесо 1 раз.
где – твёрдость рабочей поверхности зубьев, – предел текучести материала.
Определим коэффициенты приведения на контактную выносливость и на изгибную выносливость по таблице 4.1, учитывая режим работы №III: ; .
Определим число циклов перемены напряжений на контактную и изгибную выносливость соответственно по графику 4: , , .
Ресурс передачи, т.е. суммарное время работы, задано в расчёте, и имеет следующее значение: .
Определим суммарное число циклов перемены напряжений для шестерни и колеса соответственно: , , где:
– частота вращения шестерни; и – число вхождений в зацепление зубьев шестерни или колеса соответственно за один его оборот.
Рассчитаем эквивалентное число циклов перемены напряжений для расчёта на контактную выносливость:  , где:
– коэффициенты приведения на контактную выносливость; – суммарное число циклов перемены напряжений для шестерни или колеса.
Найдём эквивалентное число циклов перемены напряжений для расчёта на изгибную выносливость: принимаем NFE1= 4∙106,
, где
– коэффициенты приведения на изгибную выносливость; – суммарное число циклов перемены напряжений для шестерни или колеса.
Определим предельные допускаемые напряжения при действии пиковых нагрузок:
при расчете на контактную выносливость

при расчете на изгибную выносливость

Определим допускаемые напряжения для расчёта на контактную выносливость: 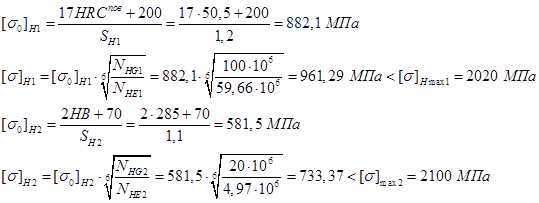
Определим допускаемые напряжения для расчета на изгибную выносливость:
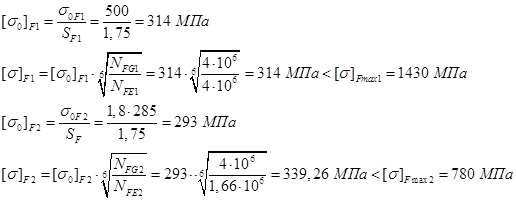
Так как HBср1-HBср2=505-285=220>70 и HBср2=285<350, то расчетное допускаемое напряжение:

Принимаем меньшее значение [σ] H=762,6 МПа
Определим коэффициенты нагрузки на контактную и изгибную выносливость по формулам:
и ,
где и – коэффициенты концентрации нагрузки по ширине венца; и – коэффициенты динамической нагрузки (учитывают внутреннюю динамику передачи).
Определим относительную ширину венца:
,
где =4
-для косозубых передач и принимаем 
По таблице 5.2. и 5.3, схемы 7 расположения зубчатых колёс относительно опор и варианта соотношения термических обработок находим , 
Значения определяются по табл.5.6 по известной окружной скорости:
<15, где
=nэд=1410 мин-1– частота вращения быстроходного вала,
=58 – крутящий момент на валу,
=4 – передаточное число данной ступени редуктора, коэффициент определяется по табл.5.4 в зависимости от вида передачи.
Для 8-й степени точности изготовления передачи получим, что
и .
Находим значения коэффициентов нагрузки:


Определим предварительное значение межосевого расстояния:

где ψа = 0,35 – коэффициент ширины передачи.
=4 – передаточное число редуктора;
= 762,6 МПа – допускаемое контактное напряжение;
=1,055 – коэффициент, учитывающий распределение нагрузки между зубьями, определяем по Рис.6.2;
=394,82 Н м– крутящий момент на валу колеса;
По стандартному ряду принимаем а = 100 мм
Определяем рабочую ширину колеса:
.
Ширина шестерни: .
Вычислим модуль передачи по формуле:
,
где =339,26 МПа – изгибное напряжение на колесе; , . Тогда . Из стандартного ряда значений по ГОСТ 9563–60 выбираем значение .
Минимально возможный угол наклона зубьев для косозубой передачи
.
Рассчитываем предварительное суммарное число зубьев: . Округлив это число в меньшую сторону, получаем .
Определяем действительное значение угла и сравниваем его с минимальным значением:
, .
Найдём число зубьев шестерни и колеса , учитывая что минимальное число зубьев для косозубой цилиндрической передачи: .
Итак получим: ; .
Найдём фактическое передаточное число тихоходной ступени: . Таким образом фактическое передаточное число совпадает с заданным.
Проверим зубья колёс на изгибную выносливость. Для колеса получим:
где – коэффициент нагрузки при расчёте на изгибную выносливость;
– коэффициент, учитывающий распределение нагрузки между зубьями, выбираем по табл.6.4;
– коэффициент, учитывающий форму зуба, находится по табл.6.2;
– коэффициент, учитывающий наклон зуба.
Сравниваем полученное значение напряжения с допускаемым напряжением при расчёте на изгиб зубьев колеса: .
Определим диаметры делительных окружностей шестерни и колеса соответственно.
, ,
где – модуль косозубых колёс;
– угол наклона зуба;
Проверка: , откуда 40+160=2·100, т.е. 200=200 – верно.
Определим диаметры окружностей вершин зубьев и впадин зубьев . ;
;
;
.
Определим силы, действующие на валы косозубых колёс.
Окружная сила:
,
Радиальная сила: ,
где – угол зацепления; – угол наклона зуба.
Осевая сила: .
Отметим, что поскольку редуктор трехпоточный, то момент на быстроходном валу ТБ=Т2/3=101,77/3=33,923(в данном случае Т2-монент на быстроходной ступени)
Материал колеса – сталь 40X(термообработка-улучшение).
Материал шестерни – сталь 40ХН(термообработка-закалка ТВЧ).
По таблице 3.1 имеем:
для шестерни: ;
для колеса: МПа
Отметим что колесо входит в зацепление 3 раза, шестерня 1 раз.
где – твёрдость рабочей поверхности зубьев, – предел текучести материала.
Определим коэффициенты приведения на контактную выносливость и на изгибную выносливость по таблице 4.1, учитывая режим работы №III: ; .
Определим число циклов перемены напряжений на контактную и изгибную выносливость соответственно по графику 4: , , .
Ресурс передачи, т.е. суммарное время работы, задано в расчёте, и имеет следующее значение: .
Определим суммарное число циклов перемены напряжений для шестерни и колеса соответственно: , , где:
– частота вращения шестерни; и – число вхождений в зацепление зубьев шестерни или колеса соответственно за один его оборот.
Рассчитаем эквивалентное число циклов перемены напряжений для расчёта на контактную выносливость:  , где:
– коэффициенты приведения на контактную выносливость; – суммарное число циклов перемены напряжений для шестерни или колеса.
Принимаем NHE1=NHG1=100·106, NHE2=NHG2=20·106.
Найдём эквивалентное число циклов перемены напряжений для расчёта на изгибную выносливость: принимаем NFE1= 4∙106, принимаем NFE1= 4∙106,
где – коэффициенты приведения на изгибную выносливость; – суммарное число циклов перемены напряжений для шестерни или колеса.
Определим предельные допускаемые напряжения при действии пиковых нагрузок:
при расчете на контактную выносливость

при расчете на изгибную выносливость

Определим допускаемые напряжения для расчёта на контактную выносливость: 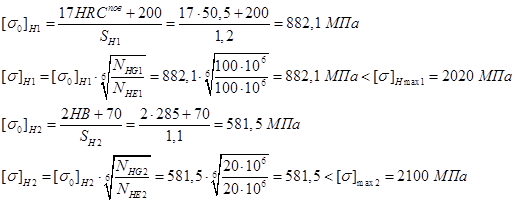
Определим допускаемые напряжения для расчета на изгибную выносливость:

Так как HBср1-HBср2=505-285=220>70 и HBср2=285<350, то расчетное допускаемое напряжение:

Принимаем меньшее значение [σ] H=658,62 МПа
Поскольку редуктор соосный, то дальнеший расчет имеет свои особенности.
Определим коэффициенты нагрузки на контактную и изгибную выносливость по формулам:
и ,
где и – коэффициенты концентрации нагрузки по ширине венца; и – коэффициенты динамической нагрузки (учитывают внутреннюю динамику передачи).
Зададимся значением 
Определим относительную ширину венца:
,
где =5,16.
При расчете принимается
По таблицам определяем
<15, где
=nэд=184,11 мин-1– частота вращения быстроходного вала,
=33,923 – крутящий момент на валу,
=5,16 – передаточное число данной ступени редуктора, коэффициент определяется по табл.5.4 в зависимости от вида передачи.
Для 8-й степени точности изготовления передачи получим, что
и .
 

Находим значения коэффициентов нагрузки:


Межосевое расстояние a=100 мм.
Определим коэффициент ширины быстроходной ступени :

Принимаем 
Определяем рабочую ширину колеса:
.
Ширина шестерни: .
Вычислим модуль передачи по формуле:
,
где =293 МПа – изгибное напряжение на колесе; , . Тогда . Из стандартного ряда значений по ГОСТ 9563–60 подходит значение , но из конструктивный соображений (во избежание неприемлемых чисел зубьев), принимаем .
Минимально возможный угол наклона зубьев для косозубой передачи
.
Рассчитываем предварительное суммарное число зубьев: . Округлив это число в меньшую сторону, получаем .
Определяем действительное значение угла и сравниваем его с минимальным значением:
, .
Найдём число зубьев шестерни и колеса , учитывая что минимальное число зубьев для косозубой цилиндрической передачи: .
Итак получим: , принимаем z1=21;
Получим .
Найдём фактическое передаточное число быстроходной ступени: . Таким образом погрешность составляет 2%, что меньше предельно допустимого значения 4%, т.е. подходит.
Проверим зубья колёс на изгибную выносливость. Для колеса получим:
где – коэффициент нагрузки при расчёте на изгибную выносливость;
– коэффициент, учитывающий распределение нагрузки между зубьями, выбираем по табл.6.4;
– коэффициент, учитывающий форму зуба, находится по табл.6.2;
– коэффициент, учитывающий наклон зуба.
Сравниваем полученное значение напряжения с допускаемым напряжением при расчёте на изгиб зубьев колеса: .
Определим диаметры делительных окружностей шестерни и колеса соответственно.
, ,
где – модуль косозубых колёс;
– угол наклона зуба;
Проверка: , откуда 33,071+166,929=2·100, т.е. 200=200 – верно.
Определим диаметры окружностей вершин зубьев и впадин зубьев . ;
;
;
.
Определим силы, действующие на валы косозубых колёс.
Окружная сила:
,
Радиальная сила: ,
где – угол зацепления; – угол наклона зуба.
Осевая сила: .
Расчет валов производится по ранее найденным значениям крутящего момента:
Для быстроходного вала определим диаметр посадочной поверхности:
мм; Принимаем d=21 мм.
Из таблицы определяем: , откуда получим посадочный диаметр под подшипник, а также диаметр буртика, ограничивающего подшипник:
мм, 
Для быстроходного вала определим диаметр посадочной поверхности:
мм; Принимаем d=42 мм.
Из таблицы определяем: , откуда получим посадочный диаметр под подшипник, а также диаметр буртика, ограничивающего подшипник:
мм, 
Для промежуточного вала определим:
; Принимаем dK=34/35 (размер посадочных мест под подшипники).
Из таблицы определяем: , откуда получим посадочный диаметр под подшипник, а также диаметр буртика, ограничивающего подшипник:
мм, 
Диаметр буртика, ограничивающего колесо:
мм.
В данном случае целесообразно нарезать зубья шестерен непосредственно на валах ввиду незначительной разницы диаметров колеса и вала.
Рассчитаем ступицы для валов. Расчет заключается в определении диаметра и длины ступицы.
Для быстроходного вала:
мм; мм.
Для тихоходного вала:
мм; мм.
Для промежуточного вала:
мм; мм.
Толщина стенок корпуса редуктора.
мм принимаем =7мм
Толщина фланцев корпуса мм
Ширина фланца корпуса 
Определим расстояние между зубчатыми колёсами и боковыми стенками редуктора.
мм, где L-сумма межосевого расстояния и половины диаметров вершин зубчатых колёс.
Минимальное расстояние между зубчатыми колёсами, дном и крышкой предполагается равным и равно 41,6мм.
Корпус редуктора имеет две боковые и одну верхнюю крышки.
Боковые крышки крепятся к корпусу винтами с потайной головкой, диаметры которых определяются по формуле: мм. Принимаем диаметр винтов равный 8мм (М8). Количество винтов принимаем 10 на каждую крышку.
Крышки подшипников изготовляют из чугуна марки СЧ-15. Определяющим при конструировании крышки является диаметр отверстия в крышке под подшипник, и все остальные параметры принимают по таблице после определения этого параметра.
По таблице определим параметры для крышки быстроходного вала:
мм, мм, мм, .
Креплении крышки к корпусу осуществляется винтами с потайной головкой.
Толщина фланца при креплении крышки винтами
мм.
Толщина центрирующего пояска мм.
Диаметр фланца крышки определяем по формуле мм.
Расстояния от поверхности отверстия под подшипник до оси крепёжного болта принимается приблизительно равным диаметру винта:
мм.
Определим параметры для крышки тихоходного вала по таблице:
мм, мм, мм.
Толщина фланца при креплении крышки винтами:
мм.
Толщина центрирующего пояска мм.
Диаметр фланца крышки определяем по формуле:
мм.
Расстояние от поверхности отверстия под подшипник до оси крепежного болта:
мм.
Конструктивные размеры крышек промежуточного вала принимаются равными размерам крышки быстроходного вала. Отличительной чертой является отсутствие сквозного отверстия под выход вала, а также отсутствие дополнительного места под манжету.
Поле допуска внутреннего кольца подшипника, выбирается по ГОСТ 520-71. Так как в редукторе внутренние кольца подшипников всех валов вращаются, а наружные стоят на месте, то имеет место местное нагружение, следовательно подшипник монтируют с зазором, что позволяет уменьшить износ внутренних дорожек.
Для внутреннего кольца подшипника быстроходного вала принимаем размер . Для внешнего кольца подшипника быстроходного вала, который монтируется в корпус редуктора, принимаем размер: .
Для внутреннего кольца подшипника тихоходного вала принимаем размер . Для внешнего кольца подшипника тихоходного вала, который монтируется в корпус редуктора, принимаем размер: .
Для внутреннего кольца подшипника промежуточного вала принимаем размер . Для внешнего кольца подшипника промежуточного вала, который монтируется в корпус редуктора, возьмём размер: .
Для смазывания передач широко применяют картерную систему. В корпус редуктора заливают масло так, чтобы венцы колес были в него погружены. Колеса при вращении увлекают масло, разбрызгивая его внутри корпуса. Масло попадает на внутренние стенки корпуса, откуда стекает в нижнюю его часть. Внутри корпуса образуется взвесь частиц масла в воздухе, которая покрывает поверхность расположенных внутри корпуса деталей.
Принцип назначения сорта масла следующий: чем выше окружная скорость колеса, тем меньше должна быть вязкость масла и чем выше контактные давления в зацеплении, тем большей вязкостью должно обладать масло. Поэтому требуемую вязкость масла определяют в зависимости от контактного напряжения и окружной скорости колес.
Контактные напряжения:

Частота вращения промежуточного вала .
Круговая частота и окружная скорость.

По таблице 11.2 [2 c.173] выбирается марка масла И-Г-А-32.
И – индустриальное
Г – для гидравлических систем
А – масло без присадок
32 – класс кинематической вязкости
В соосных редукторах при расположении валов в горизонтальной плоскости в масло погружают колеса быстроходной и тихоходной ступеней.
Для передачи крутящего момента от вала электродвигателя к быстроходному валу и предотвращения перекоса вала выбираем упругую втулочно-пальцевую муфту, крутящий момент которой передается пальцами и упругими втулками. Ее размеры стандартизированы и зависят от величины крутящего момента и диаметра вала.
Используя ранее рассчитанные диаметр выходного вала редуктора и величину крутящего момента на нем, выбираем для передачи крутящего момента от выходного вала редуктора на приводной вал зубчатую муфту. Ее размеры стандартизованы по ГОСТ 5006-55.
Рассчитаем подшипники на тихоходном валу, для этого определим силы нагружающие подшипник.
Силы действующие в зацеплении: 
=1645Н
=376Н
Т=394.8Нм
Определим радиальную нагрузку на вал от втулочно-пальцевой муфты
Н
Где l-расстояние от зубчатого сочленения до торца муфты

Так как нагрузка приложена точно к середине вала то и значит 






Консольная нагрузка:

Реакции опор от консольной нагрузки 

В расчете принимаем наихудший вариант действия консольной силы 

Предварительный выбор подшипника
– диаметр внутреннего кольца,
– диаметр наружного кольца,
– динамическая грузоподъёмность,
– статическая грузоподъёмность.
– предельная частота вращения при пластичной смазке.
Линия симметрии шестерни совпадает с линией симметрии относительно которой установлен подшипник, а значит суммарную реакцию опоры на один подшипник можно найти как:
- Это реакция от сил действующих на один подшипник.
Эквивалентная нагрузка в этом случае вычисляется как:
Н
=1 так как вращается внутреннее кольцо
- коэффициент безопасности. -температурный коэффициент.
<e следовательно Х=1 Y=0
Базовую долговечность работы подшипника определяют по формуле:
; где n-число оборотов вала в минуту,
, где -динамическая грузоподъёмность, а - эквивалентная нагрузка приведённая выше.
Итак . Степень три выбираем для шарикового подшипника. Тогда часов. А требуемый ресурс 10000 часов, значит можно сделать вывод, что подшипники подходят.
Необходимые данные: Н; Н
Определим реакции опор в вертикальной плоскости.
1. , , . Отсюда находим, что .
2. , , . Получаем, что .
Определим реакции опор в горизонтальной плоскости:
3. , , , получаем, что .
4. , , , отсюда .
Эпюры моментов от сил будут иметь вид:


Суммарный изгибающий момент:

Нормальные напряжения изменяется по симметричному циклу, а касательные по пульсирующему. Для симметричного цикла амплитуду нормальных напряжений можно найти по формуле:
, где М – изгибающий момент, W – момент сопротивления изгибу для данного опасного сечения равен:

Для определения касательных напряжений воспользуемся формулой:
; где Т - крутящий момент, а - момент сопротивления кручению, учётом того, что в опасном сечение вал внутри со шлицами а снаружи гладкий вал, получим:

Амплитуда нормальных напряжений изгиба: МПа. Среднее напряжение 
Амплитуда и среднее напряжение цикла касательных напряжений в опасном сечении:
МПа.
Коэффициент запаса прочности по нормальным и касательным напряжениям:
; 
Где МПа - предел выносливости гладкого образца при симметричном цикле. МПа. - придел выносливости при симметричном цикле кручения.
и -коэффициент влияния абсолютных размеров поперечного сечения тела при изгибе и кручении; - коэффициент влияния шероховатости тела.
Коэффициенты чувствительности к асимметрии цикла примем равными: .
Коэффициент влияния поверхностного упрочнения, для закалки в ТВЧ: 
По таблицам приложения выбираем: . После выбора всех коэффициентов и определения напряжений получим:
; 
Общий коэффициент усталостной прочности: .
Допустимое значение для S=1.5 .2.5 Можно сделать вывод, что запас прочности вала значительно превышает допустимое значение прочности.
Проверим статическую прочность при перегрузках, определим её по формуле: , При напряжения могут увеличиваться в 2.2 раза и составят:
МПа
МПа
МПа
Эквивалентное напряжение в опасном сечении:
МПа. Условие прочности выполняется.
Из условий работы зубчатого зацепления получаем наибольшее напряжение
под колесом. Поскольку из конструктивных соображений был принят диаметр вала больше расчетного, то расчет на жесткость проводить нецелесообразно.
При передачи с вала крутящего момента возникают напряжения сечения σсм, а в продольном сечении шпонки напряжение среза τ.
У стандартных шпонок размеры b и h подобранны так, что нагрузку соединения ограничивают не напряжение среза, а напряжение смятия. Поэтому расчет шпонок проведем на напряжение смятия.
Рассчитаем шпоночное соединение наиболее нагруженного вала редуктора – тихоходного вала, где установлена шпонка 10х8х40 ГОСТ 23360-78.
σсм=Ft/h*lp≤ [σсм], где
Ft=2T/db
[σсм] =0.5στ=0.5*320=160 МПа.
Тогда σсм=4T/db*h*lp≤ [σсм], где
σсм - расчетное напряжение смятия
Т – крутящий момент
db - диаметр вала
lp – рабочая длина шпонки
h – высота шпонки
[σсм] – допускаемое напряжение смятия
στ – предел текучести материала
σсм=4*395000/35*8*40=121 МПа < [σсм] =160 МПа
Условия несмятия шпонки выполняются, следовательно шпонка выбрана правильно.
1. М.: М.Н. Иванов. Детали машин. М.: "Машиностроение", 1991.
2. П.Ф. Дунаев, О.П. Леликов – Конструирование узлов и деталей машин. "Высшая школа", 1985.
3. В.И. Анурьев – Справочник коструктора-машиностроителя, т.1. М.: "Машиностроение", 1980.
4. В.И. Анурьев – Справочник коструктора-машиностроителя, т.2. М.: "Машиностроение", 1980.
5. В.И. Анурьев – Справочник коструктора-машиностроителя, т.3. М.: "Машиностроение", 1980.
|