РЕДУКТОР ЗУБЧАТЫЙ ПРЯМОЗУБЫЙ
Оглавление
1 Задание на курсовой проект
2 ВЫБОР ЭЛЕКТРОДВИГАТЕЛЯ
3 КИНЕМАТИЧЕСКИЙ РАСЧЕТ ПЕРЕДАЧИ
4 ПРОЕКТНЫЙ РАСЧЕТ РЕДУКТОРА
4.1 Структурная схема редуктора.
4.2 Расчет зубчатых колес редуктора
4.3 Проверочный расчет спроектированной передачи
4.4 Расчет диаметров валов редуктора.
4.5 Конструктивные размеры корпуса редуктора
4.6 Выбор подшипников и расчет их на долговечность.
4.7 Проверка прочности шлицевых и шпоночных соединений
4.8 Проверка опасных сечений быстроходного вала
4.9 Проверка опасных сечений тихоходного вала
5 Расчет муфты (определение диаметра срезаемого штифта)
6 Выбор сорта масла.
7 ДОПУСКИ И ПОСАДКИ
8 СПИСОК ИСПОЛЬЗОВАННЫХ ИСТОЧНИКОВ
1 Задание на курсовой проект
    1 2 3 4 5
1-электродввигатель
2-упругая втулочно-пальцевая муфта
3-передача
4-комбинированая муфта
5-исполнительный механизм
Задание: для приведенной выше схемы выполнить проект передачи, входящей в него.
Исходные данные:
1.1 Номер варианта……………………………….…….29
Номер схемы……………………………….….……...1
Вид колес………………….……………...прямозубый
Мощность на ведущем валу……………….….2,2 кВт
Частота вращения ведущего вала……..1425 об/мин
ведомого вала ………360 об/мин
Вид нагрузки………….………………….реверсивная
Смазка зацепления………………………….картерная
Срок службы …………………………...…24000 часов
Характер нагружения…..……вибрационная нагрузка
Учитывая исходные данные, по табл. П1 [1, стр. 390] выбираем двигатель асинхронной серии 4А ( по ГОСТ 19523-81) , мощности P = 2,2кВт , n1
= 1425 об/мин. Условные обозначения 90L4/95 .По табл. П2 [1, стр. 391] определяем диаметр выходного вала для выбранного электродвигателя dэ = 24 мм
Передаточное число привода находится по формуле
U12
=n1
/n2
=1425/360 = 4 (3.1)
n1
- частота вращения на ведущем валу, (об./мин.)
n2
- частота вращения на ведомом валу, (об./мин.)
n1
= 1425 об/мин
n2
=360 об/мин
Замечание: передаточное число до стандартного значения не доопределяется
Крутящий момент на валу находится по следующей формуле
Т=9,55Ч106
ЧРh/n , (3.2)
где :
Р - мощность электродвигателя, (кВт)
h-КПД
n -частота вращения вaлa, (об/мин)
КПД привода принемаем за единицу h=1
Определяем крутящий момент на ведущем валу
T1
= 9,55Ч106
Ч2,2/1425 = 14735,65 НЧмм
Рассчитываем крутящий момент на ведомом валу
T2
= T1
ЧU12
=14735,65 Ч 4 = 58942,6 НЧмм
Принимаем согласно рекомендациям табл. 2,6 - 2,8 [З] марку материалов и их термообработку. Выписываем механические характеристики из табл. 2.8 [3].
Материал детали :
шестерня сталь 45
колесо сталь 45
Вид термообработки:
шестерня улучшение
колесо улучшение
Твердость:
шестерня HB 300
колесо HB 240
Базовое число циклов перемены напряжений при расчете на контактную выносливость:
шестерня NHO1
=1,7Ч107
колесо NHO2
=1,3Ч107
Базовое число циклов перемены напряжений при расчете на изгибную выносливость:
шестерня Nfo1
=4Ч106
колесо Nfo2
=4Ч106
Допускаемое контактное напряжение при базовом числе циклов:
шестерня sHO1=
580 н/мм2
колесо sHO2
=514 н/мм2
Допускаемое напряжение изгиба в зубьях при базовом числе циклов:
шестерня sfo1
=294 н/мм2
колесо sfo2
=256 н/мм2
По рекомендациям табл. 2,9 [3] для прямозубых передач определяем допускаемые напряжения:
а) Допускаемое контактное напряжение
[sH
] = sHO
ЧКн (4.2.1)
sHO
- допускаемое контактное напряжение при базовом числе циклов (см. п. 3.2)
Кн- коэффициент долговечности принимаем = 1
Nнo- базовое число циклов перемены напряжений при расчете на контактную выносливость
NHe-эквивалентное число циклов, определяется по формуле
Nнe = Nfe = 60ЧhЧn (4.2.2)
Подставим в формулы численные значения данных
Шестерня
Nнe1
= Nfе =60Ч24Ч103
Ч1425 = 2052000000
(4.2.3)
КHL1
= 1
[sH1
] = sHO1
ЧКH1
=580Чl = 580 н/ мм2
Колесо
NHE
= NFE
= 60Ч24Ч103
Ч360 = 518400000
(4.2.4)
КHL2
= 1
[sH2
] = sHO2
Ч Кн2
=514 Ч l = 514 н/ мм2
б) Допускаемое напряжение при изгибе
[sF
] = sFO
ЧKF
(3.3.4)
sFO
- допускаемое напряжение изгиба в зубьях при базовом числе циклов (см. п. 3.2)
KF
- коэффициент долговечности, принимается = 1
NFO
- базовое число циклов перемены напряжений при расчете на изгибную выносливость
NFE
- эквивалентное число циклов определено выше по формуле (4.2.2)
Подставим в формулы численные значения данных
Шестерня
NFE1
= NHE1
= 2052000000
(4.2.5)
KFL1
= 1
[sF1
] =
sFO1
ЧKFL1
= 294Ч1 = 294 н/мм
2
Колесо
NFE2
= NHE2
= 518400000
(4.2.6)
KFL2
= 1
[sF2
] = sFO2
ЧKFL2
= 256Ч1 = 256 н/мм2
Расчетное допускаемое
контактное
напр
яжение для пер
едачи
[sH
] = min([sH1
],[sH2
]) (4.2.7)
[sH1
] -допускаемое контактное напряжение для шестерни
(см. выше)
[sH2
]-
допускаемое контактное напряжение для колеса (см. выше)
Численный расчет допустимого контактного напряжения:
[бн] =
[sH2
]=514 н/мм2
а) Межосевое расстояние
Ориентировочное значение межосевого расстояния аw
, согласно рекомендациям табл. 2.9 [3] определяется следующей формулой
(4.2.8)
КA
- коэффициент, учитывающий механические свойства материалов колес (см. ниже)
U12
- передаточное число (см. п. 3)
Т1
- крутящий момент на ведущем валу (см, п. 3)
Кнв - коэффициент, учитывающий распределение нагрузки по ширине венца (см. ниже)
yBA
-коэффициент относительной ширины колеса (см. ниже)
[sH
] - расчетное допускаемое контактное напряжение для передачи (см. п. 4.2.2)
Замечание: в скобках знак "+" - соответствует колесам внешнего зацепления, "-'' колесам внутреннего зацепления, в данном задании рассматривается случай внешнего зацепления зубчатых колес, поэтому формуле (4.2.8) соответствует знак «+».
Зададимся недостающими коэффициентами:
Коэффициент относительной ширины колес yBA
, определяем согласно рекомендациям табл. 2,24 [3] для прямозубых передач: yBA
= 0,2-0,6 выбераем 0,4
Коэффициент yBD
вычисляем по формуле
yBD
= yBA
Ч(1+U12
)/2 (4.2.9)
yBD
= 0,4Ч(1+4)/2 = 1
Коэффициент, учитывающий механические свойства материала колес
КA
- определяем из таблицы 2.10 [3]
Вид колес цилиндрический прямозубый
Материал шестерни и колеса сталь 45
Коэффициенты Кa
= 49,5 (н/мм2
)
ZM
= 274 (н/мм2
)
КHB
- определяем из таблицы 2.11 [3]
Твердость <350 НВ
Расположение шестерни - несимметрично относительно опор
КH
b
=1,07 – коэффициент учитывающий расположение нагрузки по ширине венца
KF
b
= 1,15
Произведем ориентировочный расчет межосевого расстояния
(4.2.10)
Округляем значение Aw до ближайшего значения из ряда R 40 (см. табл. 2.5 [3]):
Aw = 100 мм
б) Значение модуля
Определяем значение модуля m = mn
из соотношения
m =
(0,01 - 0,03) Ч Aw (4.2.11)
Рассчитываем
m =
0,02Ч100 мм
Значения модуля лежат в диапазоне от 1,0 мм до 3,0 мм. Выбираемые в соответствии со стандартом, одно из значений таблицы 2.22 [З]
mn
= 2,0 мм
в) Ширина венца колеса и шестерни
Определяем рабочую ширину венца колеса:
b2
= yBA
ЧAw (4.2.12)
Рассчитываем
b2
= yBA
ЧAw = 0,4Ч100 = 40 мм
Выбираем рабочую ширину венца колеса из ряд предпочтительных линейных размеров
b2
= 40 мм
Рабочая ширина шестерни определяется соотношением
b1
= b2
+ (2 - 5) = 40+5 = 45 мм (4.2.13)
В соответствии со стандартами числовых значений таблицы 2.5 [З], выбираем из полученного диапазона следующее значение для рабочей ширины шестерни
b1
= 45 мм
г) Число зубьев шестерни и колеса
Aw = mn
Ч(Z1
+Z2
) / (2Чcos(b)) (4.2.14)
ZS
= Z1
+Z2
= 2Aw .
cosb / mn
Замечание: для цилиндрической прямозубой передачи b принимаем за 0о
Вычислим ZS
(сумарное число зубьев)
ZS
= AwЧ2Чcos(b)/mn
= 100Ч2Ч1 / 2 = 100 (4.2.15)
Определим Z1
и Z2
из соотношения U12
=Z2
/Z1
cos(b)=0
Z2
= U12
Ч Z1
=>U12
= Z2
/Z1
= 80/20 = 4
Zl
= 20 - число зубьев шестерни
Z2
= 80 - число зубьев колеса
д) Делительные диаметры колеса и шестерни
Определяем делительные диаметры шестерни и колеса по формулам: [1, стр. 37]
d1
= Z1
Чmn
/cos(b) (4.2.16)
d2
= Z2
Чmn
/cos(b) (4.2.17)
d1
= 20Ч2/1 = 40 мм
d2
= 80Ч2/1 = 160 мм
Осуществим проверку правильности полученных результатов
Aw = (d1
+d2
)/2 (4.2.18)
Aw = (40+160)/2 = 100 мм
Точность произведенных вычислений не превысила допустимую , данные, полученные в ходе расчета являются верными.
Основные параметры цилиндрических зубчатых передач, выполненных без смещения
Диаметр вершин зубьев
шестерни dA1
=d1
+2Чmn
=40+2Ч2 = 44мм (4.2.19)
колеса dA2=d2+2Чmn
=160+2Ч2 = 164 мм (4.2.20)
Диаметр впадин зубьев
шестерни dF1=d1 –2,5Чmn
=40-2,5Ч2 = 35 мм (4.2.21)
колеса :dF2=d2 –2,5Чmn
=160-2,5Ч2 = 155 мм (4.2.22)
е)Степень точности передачи
определяем окружную скорость колес по формуле
V = pЧdl
Чnl
/60Ч103
(4.2.23)
V = 3,14Ч37,14Ч1425/60Ч103
= 2,985 м/с
Согласно табл. 2.21 [З] выбираем требуемую точности передачи
степень точности передачи Ст-9
а) Расчет на контактную выносливость
Выполним проверочный расчет спроектированной передачи: sH
Ј [sH
], согласно рекомендациям табл. 2.9 [З]
Для цилиндрических передач
(н/мм2
) (4.3.1)
ZH
-коэффициент, учитывающий форму сопряженных поверхностей зубьев (см.ниже)
ZM
-вспомогательный коэффициент, учитывающий механические свойства материалов колес (см. п. 4)
ZE
- коэффициент, учитывающий суммарную длину контактных линий (см.ниже)
WHT
- удельная расчетная окружная сила (см.ниже)
U12
- передаточное число (см. п, 3)
dl
- делительный диаметр шестерни (см, п, 4)
Зададимся недостающими коэффициентами:
Коэффициент ZH
определим из таблицы 2.15 [3], угол наклона линии зуба b=0o
ZH
= 1,76
Коэффициент Ze определим из таблицы 2.17 [3]
ZE
= 0,90
Коэффициент ZМ
определим из таблицы 2.9 [3]
ZМ
=274
1.Коэффициент торцового перекрытия
Ea
= [1,88 - 3,2 Ч(1/Z1
± 1/Z2
)] cos(b)= [1,88 - 3,2 Ч(1/20+1/80)]/1 = 1,68 (4.3.2)
2.Коэффициент осевого перекрытия
Eв
= b2
Чsin(b)/(mn
) = 40Ч0/2 = 0 (4.3.3)
Определим удельную расчетную окружную силу WHT
: [3, табл. 2.8 , стр 20]
WHT
= 2ЧT1
ЧKH
a
ЧKHв
.
KHV
/(d1
Чbw
) =2·14740·1,12·1,12·1,2/(40·40) = 27,728 H/мм (4.3.4)
Т1
- крутящий момент на ведущем валу (см. п. 3)
KHб
- коэффициент, учитывающий распределение нагрузки между зубьями (см.ниже)
KHв
- коэффициент, учитывающий динамическую нагрузку в зацеплении (см.ниже )
KHV
- коэффициент, учитывающий распределение нагрузки по ширине венца (см. п. 4)
d1
- делительный диаметр шестерни (см. п. 4)
bw
- рабочая ширина венца колеса (см. п. 4 )
Зададимся недостающими коэффициентами:
Коэффициент KHб
определим из таблицы 2.19[3]:
Окружная скорость = 2,985 м/с
Степень точности = 9
Коэффициенты KHA
=1,16
KHB
=1,04
Коэффициент Кнv определим из таблицы 2.20 [З]
Твердость поверхности зубьев < 350 HB
Колеса цилиндрические
Коэффициенты KHV
=1,2
KFV
=1,5

По формуле (4.3.1) рассчитываем
Проверяем условие sH
< [s'H
]
Заключение: расчетное контактное напряжение не превзошло значения допустимого контактного напряжения. Выбор материалов и проведенный расчет были сделаны правильно.
б) Расчет на выносливость при изгибе
Выполним проверочный расчет по условиям: sF
Ј [sF
], согласно рекомендациям табл. 2.9 [3]
Для цилиндрических передач
sF
= YF1
ЧYB
ЧWFT
/m < [sF
] (4.3.5)
YF
- коэффициент формы зуба (см.ниже)
YB
– коэффициент учитывающий наклон зуба (см.ниже)
WFT
- удельная расчетная окружная сила (см.ниже)
m - модуль зуба (см. п. 4)
Зададимся недостающими коэффициентами:
Коэффициент YF
определим по таблице 2.18 [3];
1. Эквивалентное число зубьев:
ZV
= Z/cos3
(b) (4.3.6)
ZV
= 80/13
= 80 - для колеса
ZV
= 20/13
= 20 - для шестерни
Шестерня
ZV
= 20
YF
= 4,08
Колесо
ZV
= 80
YF
= 3,61
Коэффициент YB
определим из таблицы 2.16 [З]
Угол наклона зуба b = 0o
YB
= 1
Определим удельную расчетную окружную силу WFT
WFT
= 2ЧT1
ЧKFб
ЧKFв
ЧKFV
/d1
Чbw
= 2·14740·1·1,15·1,28/(40·44) = 21,649 Н/мм2
(4.3.7)
KFB
- коэффициент , учитывающий распределение нагрузки по ширине венца (см. выше п. 4)
KFV
- коэффициент, учитывающий динамическую нагрузку в зацеплении (см. п. 4)
По формуле (4.3.5) рассчитываем sF
Колесо
sF
= 4,08·1·21,649 /2 = 50,283 H/мм2
Шестерня
sF
= 3,61·1·21,649 /2 = 44,491 H/мм2
Заключение: результаты проверочного расчета на выносливость при изгибе зубьев колес не превзошли допустимых показателей напряжений при изгибе. Выбор материалов и проведенный расчет геометрических параметров произведен верно.
Диаметр вала оцениваем исходя из расчета только на кручение при пониженных допускаемых напряжениях:
(4.4.1)
T - крутящий момент, действующий в расчетном сечении вала (НЧмм)
[tk
]—допускаемое напряжение при кручении для стальных валов согласно табл (3.1) [8]
[tk
] = (10 - 15) Н/мм2
а) быстроходный вал
Шестерню выполняем заодно с валом
1) Диаметр d1
хвостовика вала определяем по формуле (4.4.1); при этом
Т = Т1
- крутящий момент на быстроходном валу (см. n. 3)
[tk
]= 15 Н/мм2
(см. п. 3.1 [8])

d1=17
Округляем результат до ближайшего значения из ряда предпочтительных чисел R 40
d2
= 17 мм
Так как диаметр d1
соединен муфтой с валом электродвигателя, то необходимо согласоватьдиаметры вала электродвигателя dэ
и d1
. Вo избежание разработки "специальной" муфты, принимаем d1
= (0,8 - 1,2) Чdэ
Исполнение 90L4/95
Мощность 2,2 кВт
Асинхронная частота вращения 1425 об/мин
Диаметр хвостовика двигателя 24 мм
Окончательно диаметр хвостовика принимаем равным: d1
= 24 мм
2) Диаметр вала под подшипник
Принимаем d1п
= 30 мм
3) диаметр буртика подшипника
d1бп
= d1п
+3.
r = 36 мм
б) Тихоходный вал
1) Диаметр d2
хвостовика вала определяем по формуле (4.4.1); при этом
Т = Т2
- крутящий момент на тихоходном валу (см. n. 3)

[tk
]= 15 Н/мм2
(см. п. 3.1 [8])
d2=26,984
Округляем результат до ближайшего значения из ряда предпочтительных чисел R 40
d2
= 28 мм
2) Диаметр вала под подшипник
Принимаем d2п
= 30 мм
3) диаметр буртика подшипника
d2бп
= d1
п
+3.
r = 36 мм
4) Диаметр посадочного места колеса
Принимаем dк
= 36 мм
5)Диаметр буртика колеса
dбк
= dk
+3f = 39 мм
См. рис.10.18 и табл. 10.2 и 10.3 [1].
Толщина стенок корпуса
d і0,025·аw
+1 = 0,025·100+1 = 3,5 мм
Принимаем d = 8 мм
Толщина стенок крышки
d1
і0,02·аw
+1 = 0,02·100+1 = 3 мм
Принимаем d1
= 8 мм
Толщина фланцев
Верхнего пояса крышки и корпуса
b = b1
=1,5d = 1,5 · 8 = 12 мм
Нижнего пояса корпуса
p = 2,35 · 8 = 19 мм
Принимаем p = 20 мм
Диаметр фундаментных болтов
d1
= (0,03 – 0,036)aw
+12 = 15 мм
Диаметр болтов для крепления крышки к корпусу
d2
= (0,5 – 0,6)d1
= 9 мм
а) Предварительный выбор
По найденным выше диаметрам валов под подшипники подбираем по каталогу (см.[1])
1)Для тихоходного вала подшипники легкой серии :
обозначение 206
тип подшипника радиальный однорядный
грузоподъемность С=15300 Н
СO
= 10200 Н
диаметр внутреннего кольца подшипника, d=30 мм
диаметр внешнего кольца подшипника, D=62 мм
ширина подшипника, Т =16 мм
2) Для быстроходного вала выбираем подшипники легкой серии :
обозначение 7206
тип подшипника радиальный однорядный
грузоподъемность С=29800Н
СO
= 22300Н
диаметр внутреннего кольца подшипника, d=30 мм
диаметр внешнего кольца подшипника, D=62 мм
ширина подшипника, Т =16 мм
б)Построение эпюр моментов быстроходного вала


в)Построение эпюр моментов тихооходного вала

г) Расчет на долговечность (быстроходный вал)
1) Силы действующие в зацеплении (см. рис. 2)
Окружная составляющая
Ft = 2ЧT1
/d1
= 2Ч14740/40 = 736,783 Н (4.6.1)
T1
- крутящий момент на ведущем валу , (НЧмм)
d1
- делительный диаметр шестерни ,(мм)
Радиальная составляющая
Fr = FtЧ(tg(a) /cos(b)) =2,747Ч103
Н (4.6.2)
Ft - окружная сила (см. выше), (Н)
a - угол зацепления a = 20
b - угол наклона зубьев (см. п. 4)
Осевые составляющие
FA
= Ft Чtg(b)= FA12
= FA21
= 0 Н (4.6.3)
Реакции в опорах:
в плоскости XZ
Rrx1
= Rx2
= Ft/2

в плоскости YZ

Рассчитаем
Rrx1
= Rx2
=1,228Ч103
/2=613,983 Н
Ry1
= Ry2
= 1,374Ч103
Н
Определяем суммарные радиальные реакции
(4.6.6)
Pr1
= Pr2
=1,505Ч103
H
Осевые нагрузки для быстроходного вала :
S=0,83.
e.
Fr
= 0,83Ч0,36Ч2,747Ч103
= 820,804 H (4.6.7)
В соответствии с таблицей 9.21 [2], осевые нагрузки:
FaI
= S=820,804 H
FaII
= S + Fa
=820,804 +0 = 820,804 H
Эквивалентная нагрузка см. формулу (9.3) [1]
Рэ
= V Ч Fr
Ч Кб
.
Kt
= 1Ч2,747Ч103
Ч1,2 .
1 = 3296 H (4.6.8)
V - коэффициент , при вращении внутреннего кольца
V = 1
Кб
– коэффициент нагрузки см.[1, табл. 9.19]
Кб
= 1,2
Kt
- температурный коэффициент см.[1, табл. 9.20]
Kt
=1
2) Расчет на долговечность
Расчетная долговечность, ч (см. формулу (9.1.) [1]):
Lh=106
Ч(C/ Рэ
)p
/60Чn (4.6.9)
С - динамическая нагрузка по каталогу, (Н)
Рэ - эквивалентная нагрузка, (Н)
р - показатель степени, для роликоподшипников p = 3,33
n - частота вращения; об/мин
Рассчитываем роликоподшипник
Lh = 106
Ч (29800/3296)3,33
/60 Ч1425 = 1,788 .
104
ч
Lh = 1,788 .
104
> 24Ч103
(заданный срок службы)
Заключение: Выбранные подшипники обеспечивают требуемый запас долговечности и могут быть использованы в опорных узлах редуктора.
д) Расчет на долговечность (тихоходный вал)
1) Реакции в опорах
2) Ft = 2ЧT2
/d2
= 2.
58942,6/160 = 736,783 Н
Т2
- крутящий момент на ведомом валу , (НЧмм)
d2
- делительный диаметр колеса ,(мм)
Радиальная составляющая
Fr = FtЧ(tg(a) /cos(b)) =2,747Ч103
Н
Ft - окружная сила (см. выше), (Н)
a - угол зацепления a = 20
b - угол наклона зубьев (см. п. 4)
Осевые составляющие
FA
= Ft Чtg(b)= FA12
= FA21
= 0 Н
Реакции в опорах:
в плоскости XZ
Rrx1
= Rx2
= Ft/2

в плоскости YZ

Рассчитаем
Rrx1
= Rx2
=1,228Ч103
/2=613,983 Н
Ry1
= Ry2
= 1,374Ч103
Н
Определяем суммарные радиальные реакции

Pr1
= Pr2
=1,505Ч103
H
Осевые нагрузки для тихоходного вала :
S=e.
Fr
= 0,36Ч2,747Ч103
= 988,92 H
В соответствии с таблицей 9.21 [2], осевые нагрузки:
FaI
= S=988,92 H
FaII
= S + Fa
=988,92 +0 = 988,92 H
Эквивалентная нагрузка см. формулу (9.3) [1]
Рэ
= V Ч Fr
Ч Кб
.
Kt
= 1Ч2,747Ч103
Ч1,2 .
1 = 3296 H
V - коэффициент , при вращении внутреннего кольца
V = 1
Кб
– коэффициент нагрузки см.[1, табл. 9.19]
Кб
= 1,2
Kt
- температурный коэффициент см.[1, табл. 9.20]
Kt
=1
2) Расчет на долговечность
Расчетная долговечность, ч (см. формулу (9.1.) [1]):
Lh=106
Ч(C/ Рэ
)p
/60Чn (4.6.9)
С - динамическая нагрузка по каталогу, (Н)
Рэ - эквивалентная нагрузка, (Н)
р - показатель степени, для шарикоподшипников р = 3
n - частота вращения; об/мин
Рассчитываем
шарикоподшипник
Lh=106
Ч(C/ Рэ
)p
/60Чn = 106
Ч(15300/3296)3
/60Ч360 =4,631.
104
ч
Lh = 4,631.
104
> 24Ч103
(заданный срок службы)
Заключение: Выбранные подшипники обеспечивают требуемый запас долговечности и могут быть использованы в опорных узлах редуктора.
Шпонки призматические
Материал шпонки: сталь 45 чисто тянутая
Предел текучести материала шпонки sв
>600 Н/мм2
см. параграф 8.4 [1]
Допускаемое напряжение смятия [s]см
= 70 МПа
1) Ведомый вал
диаметр вала d2
= 28 мм
длина l = 32 мм
высота шпонки h = 7 мм
ширина шпонки b = 8 мм
глубина паза вала t1
=4,0 мм
втулки t2
=3,3 мм
Проверочный расчет на смятие
Напряжения смятия и условия прочности определяем по формуле (п. 3.3) [7]
sсм
max
=2ЧT / dЧlЧ(h- t1) < [sсм
] (4.7.1)
Т - передаваемый вращающий момент (см. п. 3) (НЧмм)
d - диаметр вала в месте установки шпонки (см. выше) (мм)
h - высота шпонки (см. выше) (мм)
b - ширина шпонки (см. выше); (мм)
l - длина шпонки (см. выше) (мм)
[sсм
] - допускаемое напряжение смятия при стальной ступице:
Рассчитываем по формуле (4.7.1):
sсм
max
= 2.
58940/28 .
32 .
(7 - 4) = 43 МПа
3аключвние: проверочный расчет шпонки на смятие показал, что напряжение смятия не превосходит допустимого значения. Использование шпонок данного типа и с данными геометрическими параметрами вполне допустимо в рамках проектируемой передачи.
Определение точек приложения радиальных нагрузок на валу (расстояний L1 и
L2
)
Определим расстояние от внутреннего кольца подшипника до точки приложения нагрузки

(см. формулу 9.11 [1])
Коэффициенты T,d,D,e, - размеры подшипника см. выше
а = 16.3
Расстояния L1
и L2
(определяем из первого этапа компоновки редуктора)
L1
= L2
= 61 мм
Материал вала
Сталь 45 . Термическая обработка – улучшение
Среднее значение sв
= 780 Мпа
Предел выносливости при симметричном цикле изгиба
s-1
@ 0,43 *sв
s-1
= 0,43*780 = 335 Мпа
Предел выносливости при симметричном цикле касательных напряжений t-1
= 0.58*s-1
t-1
= 0,58*335 = 193 Мпа
а)Сечение А-А
Это сечение при передаче вращающего момента от электродвигателя через муфту расчитываем на кручение

Коэффициент запаса прочности (см. формулу 8.19 [1])

Aмплитуда нормальных напряжений кручения
Wk
– момент сопротивления кручению

b – ширина шпонки
t1
– глубина паза
Wk
= 3,14*263
/16-8*4*(26-4)2
/2/26 = 3151 мм3
tu
= tm
= 41446/2/3151 = 6.6 МПа
Из таблиц 8.5 ; 8.8 [1]
kt
= 1.68
et
= 0.79
Для принятого материала вала yt
= 0.1
S = St
= 13.6
Такой большой запас прочности обьясняется необходимостью увеличения диаметра под стандартную муфту.
Заключение: прочность в сечении А-А обеспечена
б) Сечение B-B
Принимаем диаметр вала d @ df1
@32 мм

Коэффициент запаса прочности
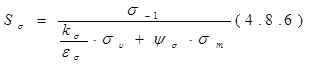
Коэффициент запаса прочности по нормальным напряжениям
Коэффициенты :
yt
=0.1; и ys
=0.2 (см стр 163 и стр166 [1])
ks
=1.78; kt
= 1.67 (см. табл. 8.6 [1])
es
= 0.90; et
= 0.76 (см. табл. 8.8 [1])
Изгибающий момент в горизонтальной плоскости
Мx
=RxII
*L2
Мx
= 506,8*61 = 68076 Н*мм
Изгибающий момент в вертикальной плоскости
Мy
=RyII
*L2
Мy
= 331,4*61 = 30915 Н*мм
Суммарный изгибающий момент
Н*мм
Момент сопротивления кручению
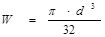
W=3,14*323
/32 = 3215 мм3

Aмплитуда нормальных напряжений изгиба
su
= 23.2 МПа
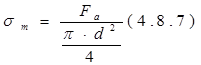
Среднее напряжение цикла нормальных напряжений
sm
= 566,8/3,14/322
*4 = 0.71 МПа
В дальнейших расчетах не учитываем (величина пренебрежимо мала)
Ss
= 7.3
Коэффициент запаса прочности по касательным напряжениям
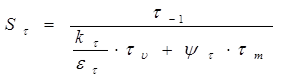
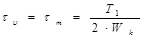
Aмплитуда нормальных напряжений кручения

Wk
– момент сопротивления кручению
Wk
= 3,14*323
/16 = 6430 мм3
tu
= tm
= 41446/2/6430 = 3.2 МПа
St
= 28.5
S=7.0
Заключение: прочность в сечении В-В обеспечена
Определение точек приложения радиальных нагрузок на валу (расстояний L1 и
L2
)

Определим расстояние от внутреннего кольца подшипника до точки приложения нагрузки (см. формулу 9.11 [1])
Коэффициенты T,d,D,e, - размеры подшипника
а = 16.3 мм
Расстояния L1
и L2
(определяем из первого этапа компоновки редуктора)
L1
= L2
= 61 мм
Материал вала
Сталь 45 . Термическая обраьотка – нормализация
Среднее значение sв
= 570 Мпа
Предел выносливости при симметричном цикле изгиба s-1
@ 0.43 *sв
s-1
= 0,43 * 570 = 246 Мпа
Предел выносливости при симметричном цикле касательных напряжений t-1
= 0.58*s-1
t-1
= 0,58*246 = 142 Мпа
а)Сечение С-С
Это сечение при передаче вращающего момента от электродвигателя через муфту расчитываем на кручение

Коэффициент запаса прочности (см. формулу 8.19 [1])
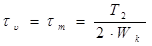
Aмплитуда нормальных напряжений кручения
Wk
– момент сопротивления кручению
b – ширина шпонки

t1
– глубина паза
Wk
= 3,14*403
/16-8*5*(40-5)2
/2/40 = 11648 мм3
tu
=tm
=248676/2/11648 = 10.2
Из таблиц 8.5 ; 8.8 [1]
kt
= 1.50
et
= 0.73
Для принятого материала вала yt
= 0.1
S = St
= 6.4
Заключение: прочность в сечении С-С- обеспечена
б) Сечение D-D
Концентрация напряжений обусловлена наличием шлицевого соединения
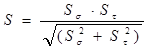
Коэффициент запаса прочности
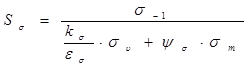
Коэффициент запаса прочности по нормальным напряжениям
Коэффициенты :
yt
=0.1; и ys
=0.2 (см стр 163 и стр166 [1])
ks
=1.55; kt
= 2.35 (см. табл. 8.6 [1])
es
= 0.85; et
= 0.73 (см. табл. 8.8 [1])
Изгибающий момент в горизонтальной плоскости
Мx
=RxII
*L2
Мx
=1116*61 = 68076 Н*мм
Изгибающий момент в вертикальной плоскости
Мy
=RyII
*L2
Мy
=331,4*61 = 30915 Н*мм
Суммарный изгибающий момент
Н*мм

Момент сопротивления кручению
W=3,14*523
/32 = 13797 мм3

Aмплитуда нормальных напряжений изгиба
su
= 74767/13797 = 5.4 МПа
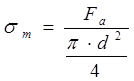
Среднее напряжение цикла нормальных напряжений
sm
= 566,8/3,14/522
*4 = 0.27 МПа
В дальнейших расчетах не учитываем (величина пренебрежимо мала)
Ss
= 23
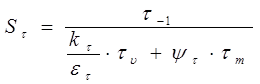
Коэффициент запаса прочности по касательным напряжениям

Aмплитуда нормальных напряжений кручения
Wk
– момент сопротивления кручению
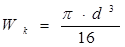
Wk
= 3,14*523
/16 = 27594 мм3
tu
= tm
= 248676/2/27594 = 4.3 МПа
St
= 14.8
S=12.4
Заключение: прочность в сечении D-D обеспечена
Материал штифта: сталь 45, закаленная до HRC 38 – 43
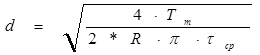
Диаметр срезного штифта см.формулу 11.3 [1]
где :
Тm
– максимальный момент
R – расстояние от осивала до оси штифта
tср
–предел прочности на срез для материала штифта
tср
= 400 Мпа см. параграф 11.2 [1]
Tm
= 1,05kTном
= 1,05*2,5*248676 = 626664 Нмм
k=2,5 см. табл. 11.3 [1]

Принимаем R = 65 мм
Округляем значение d вверх до стандартного значения по ГОСТ 3128 – 70
d = 4 мм
Смазывание шевронного зацепления производится окунанием шевронного колеса в масло заливаемого внутрь корпуса до уровня, обеспечивающего погружение колес.
По табл. 10.18[1] устанавливаем вязкость масла:
Контактные напряжения,sH
: до 550 МПа
окружная скорость V: до 1.5 м/с
вязкость масла: 34Ч10-6
м2
/с
Согласно табл. 10.10 [1] осуществляем выбор масла:
Вязкость масла: 34Ч10-6
м2
/с
Сорт масла: индустриальное.
Марка: И-40А.
Камеры подшипников заполнять пластичным смазочным материалом УТ-1, натриевой основы(см, табл. 9.14 [1])
Сопрягаемые детали
Посадка
|
Предельные отклонения
Предельные размеры, мм
|
Схемы посадок
|
Наиб. наим. натяги зазоры, мкм
|
   Подшипник
Качения – вал

|
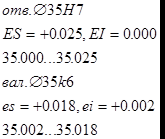
|
+
-
|
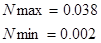
|
   Подшипник
Качения – корпус

|

|
+
-
|

|
   Крышка подшипника – корпус

|

|
+
-
|

|
   Подшипник качения – вал

|

|
+
-
|

|
   Подшипник качения – корпус

|

|
+
-
|

|
8
СПИСОК ИСПОЛЬЗОВАННЫХ ИСТОЧНИКОВ
1. Курсовое проектирование деталей машин. С.А. Чернавский, К. Н. Боков; И. М. Чернин и др. М.: машиностроение, 1987.
2. Проектирование механических передач /Под ред. С. А. Чернавского 5-е изд.: Машиностроение; 1984, 558 с.
3. Методические указания к практическим и лабораторным занятиям по курсам "Основы конструирования " и "Основы инженерного проектирования". Механические передачи. С. ф. Мороз, Н. А. Аксенова, В. В. Баранов и др., М.: Изд-во МЭИ, 1987.
4. Методические указания к курсовому проектированию по курсам "Основы конструирования", "Конструирование машин", "Инженерное проектирование". Ю. И. Сазонов. М.: Изд-во МЭИ, 1991.
5. Общетехнический справочник /Под ред. Е. А, Скороходова - 2-е изд., перераб., и доп. - М.: Машиностроение. 1982.415 с.
6. Оформление расчетно-пояснительной записки (РПЗ) к курсовому проекту и типового расчета (ТР). А. Г. Фролов - М.: Изд-во МЭИ,1989.
7. Методические указания к практическим и лабораторным занятиям по курсу "Основы конструирования". Соединения /Под ред. С. Ф. Мороз -М.: Изд-во МЭИ, 1981.
8. Машиностроительное черчение /Под ред. Г. П. Вяткина - 2-е изд., перераб, и доп. - М,: Машиностроение, 1985.368 с.
9. "Конструирование узлов и деталей машин", П. Ф. Дунаев, О. П. Леликов, М.: Высшая школа, 1985.
10. "Детали машин", П. Г. Гузенков, 3-е изд., перераб. и доп. -М.: Высш. Школа, 1982ю-351 с., ил.
11. "Детали машин" атлас конструкций 1, 2 части; /Под. Ред. Д.Н. Решетова, 5-е изд., перераб. и доп. -М.: Машиностроение, 1992 г.
|