Введение
Целью данной курсовой работы является спроектировать участок механического цеха, определить количество станков на участке и рационально его расставить в зависимости от последовательности операций, определить количество рабочих, рассчитать производственную площадь. Это необходимо уметь для того, чтобы проектируемые производственные процессы обеспечивали выпуск продукции необходимого качества, без которого затраченный на нее труд и исходные материалы будут израсходованы бесполезно. Кроме того, необходимо добиваться производства требуемого количества изделий в единицу времени при минимальных приведенных затратах, также оборудование расставляется таким образом, чтобы были минимальные простои. В зависимости от типа производства выбирать подходящее оборудование, потому что от выбора оборудования зависит разряд рабочего.
К основным этапам производственного процесса могут быть отнесены следующие: получение и складирование заготовок, доставка их к рабочим позициям, различные виды обработки, перемещение полуфабрикатов между рабочими позициями, контроль качества, хранение на складах, сборка изделий, испытание, регулировка, окраска, отделка, упаковка и отправка.
Различные этапы производственного процесса на машиностроительном заводе могут выполняться в отдельных цехах или в одном цехе. Для каждого производства устанавливают определенную программу выпуска, под которой понимают совокупность изделий установленной номенклатуры, выпускаемых в заданном объеме в год.
Состав производственных участков и вспомогательных подразделений определяется конструкцией изготовляемых изделий, технологическим процессом, программой выпуска и организацией производства.
1.
Анализ исходных данных
В данном задании на курсовую работу необходимо спроектировать участок механического цеха по обработке группы деталей типа фланец в условиях мелкосерийного производства с размещением основного и вспомогательного оборудования в РТК по функциональному признаку.
Производственную программу участка определяют исходя из программы выпуска обрабатываемых деталей. В зависимости от типа производства и этапа проектирования производственная программа может быть: точной (разработка подробных ТП обработки с техническим нормированием на все детали в условия МП); приведенной (при многономенклатурном крупно-, средне- и мелкосерийном производстве) и условной (при нечеткой номенклатуре в условиях ЕП). Так как у нас серийное производство необходимо проектировать по приведенной программе.
Проектирование по приведенной программе применяют для проектирования цехов (участков) средне- и мелкосерийном производства. Это объясняется тем, что при значительной номенклатуре объем проектных и технологических разработок становится очень большим и для его сокращения реальную многономенклатурную программу заменяют приведенной, выраженной ограниченным числом представителей, эквивалентной по трудоемкости фактической номенклатурой программе.
1.1
Расчет приведенной программы
Проектирование по приведенной программе применяют для проектирования цехов (участков) крупно- средне- и мелкосерийного производства. Это объясняется тем, что при значительной номенклатуре объем проектных и технологических разработок становится очень большим и для его сокращения реальную многономенклатурную программу заменяют приведенной, выраженной ограниченным числом представителей, эквивалентной по трудоемкости фактической номенклатурой программе.
Все детали разбивают на группы по конструктивным и технологическим признакам. В каждой группе выбирают деталь представитель, по которой далее ведут расчеты. На детали представители разрабатывают технологические процессы (ТП) обработки и путем технического нормирования определяют трудоемкость их обработки.
Деталь-представитель выбирают из соотношения (1):
0,5mmax
≤ m ≤ 2mmin
0,1Nmax
≤ N ≤ 10Nmin
(1)
0,5∙42,2≤ 31 ≤ 2∙29
21,1 ≤ 31 ≤ 58
0,1 ∙1900 ≤ 1870 ≤ 10∙1100
190 ≤ 1870 ≤ 11000
|
|
mmax
, mmin
– наибольшее, наименьшее значение массы деталей входящих в группу;
Nmax
, Nmin
- наибольший, наименьший годовой объем выпуска деталей, входящих в группу;
m
– масса детали-представителя;
N
– годовой объем выпуска детали-представителя.
В практике проектирования любой объект производства, входящий в группу, может быть приведен по трудоемкости к представителю с учетом различия в массе, программе выпуска, сложности обработки и т.д.
Кпр
= К1
∙ К2
∙ К3
… Кn
|
(2)
|
Для геометрически подобных деталей.
По массе:
,
|
(3)
|
mi
, mnp
– масса детали из группы и детали-представителя.
По серийности
,
|
(4)
|
Ni
, Nnp
– программа выпуска детали из группы и детали-представителя.
α = 0,15 для объектов легкого и среднего машиностроения;
α = 0,2 для объектов тяжелого машиностроения.
По точности
,
|
(5)
|
, - среднее значение квалитета детали из группы и детали-представителя;
, - среднее значение параметра шероховатости детали из группы и детали-представителя;
α1
, α2
– показатели степени, отражающие степень влияния технических параметров на трудоемкость обработки.
Таблица 1. Результат расчета приведенной программы сводится в табл. 1.
Деталь
|
Программа выпуска, N шт.
|
Коэффициент приведения
|
Приведенная программа на годовой выпуск,Nпр
шт
|
По массе
|
По серийности
|
По сложности
|
Общий
|
1
|
1900
|
1,1
|
1
|
1,06
|
1,17
|
2223
|
2
|
1780
|
0,98
|
1
|
1
|
0,98
|
1745
|
3
|
1100
|
1,05
|
1,08
|
1,24
|
1,4
|
1540
|
4
|
1700
|
1
|
1,01
|
1,2
|
1,2
|
2040
|
5
|
1870
|
1
|
1
|
1,1
|
1,1
|
2057
|
Итого:
|
9605
|
1.2
Определение типа производства
Тип производства зависит от заданной программы и трудоемкости изготовления изделия (детали).
Коэффициент серийности:
КС
= 1
|
массовое производство;
|
КС
= 2…10
|
крупносерийное производство;
|
КС
= 10…20
|
среднесерийное производство;
|
КС
> 20
|
мелкосерийное производство.
|

|
(6)
|
tв
– такт выпуска, в мин/шт.
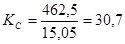
,
|
(7)
|
где N
–программа запуска деталей в производство, шт.;
мин/шт.
Фдо
– действительный годовой фонд времени работы оборудования:
,
|
(8)
|
Р
– коэф., учитывающий пребывание оборудования в ремонте (от 2 до 6%).
,
Фн
– номинальный фонд времени работы оборудования в год:

|
(9)
|
d
– количество рабочих дней в году (согласно производственному календарю); t
– нормальная продолжительность смены, час;
n
– количество рабочих смен в сутках при принятом режиме работы.

- среднее штучное или штучно-калькуляционное время, мин:
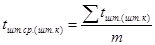
|
(10)
|
т
– число операций.

Трудоемкость годового выпуска рассчитывается по приведенной программе по каждой операции.

|
(11)
|
Таблица 2.
Результат расчета трудоемкости по каждой операции сводится в табл. 2.
Наименование технологической операции
|
Модель станка
|
Норма времени
|
Трудоемкость годового выпуска, час
|
То
,мин
|
Тшт
, мин
|
Токарная
|
16К20Ф3
|
21,2
|
30,0
|
4802,5
|
Сверлильная
|
2Н135
|
11,3
|
14,2
|
2273,2
|
Шлифовальная
|
3А110В
|
7,2
|
12,0
|
1921
|
Шлифовальная
|
3Г71
|
2,1
|
4,0
|
640,3
|
Итого:
|
|
41,8
|
60,2
|
9637,1
|
2.
Расчет потребного оборудования и его загрузка
Определение потребного оборудования производится по трудоемкости технологической операции с прибавлением (2-7)% на непредвиденные работы и услуги другим цехам и собственные нужды.
Количество станков по технологической операции (токарной, фрезерной, сверлильной)
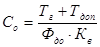
|
(12)
|
Где Тг
– трудоемкость годовой программы по данной операции;
Тдоп
– непредвиденные работы и услуги другим цехам (2-7)%;
Фдо
– действительный годовой фонд времени работы оборудования;
Кв
– коэффициент загрузки оборудования во времени, учитывающий неизбежные потери по организационно-техническим причинам (принимается 0,9).
При получении дробного числа, результат округляется в большую сторону. Количество станков на участке
Токарная операция: 
Принимаем Сп
=4шт.
Сверлильная операция: 
Принимаем Сп
=2шт.
Шлифовальная операция: 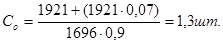
Принимаем Сп
=2шт.
Шлифовальная операция: 
Принимаем Сп
=1шт.
Суч
=ΣСп
=9шт.
Количество станков по каждому отделению вспомогательного производства берется в процентах от суммарного оборудования. При укрупненных расчетах:
Количество заточных станков 5%
9∙0,05=0,45; 0,45<0,5 станок не берем.
Количество станков ремонтного отделения 2,5%
9∙0,025=0,225; 0,225<0,5 станок не берем.
Количество станков по ремонту инструмента и приспособления 3%
9∙0,03=0,27; 0,27<0,5 станок не берем.
Загрузка оборудования по операциям рассчитывается по формуле:
.
|
(14)
|
Где Со
– расчетное количество станков;
Сп
– принятое количество по операциям.
Токарная операция: 
Сверлильная операция: 
Шлифовальная операция: 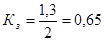
Шлифовальная операция: 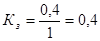
Средний коэффициент загрузки оборудования рассчитывается по формуле:

|
(15)
|

Коэффициент использования оборудования по времени рассчитывается по ф-ле:

|
(16)
|
Токарная операция: 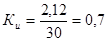
Сверлильная операция: 
Шлифовальная операция: 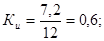
Шлифовальная операция: 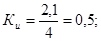
Средний коэффициент использования оборудования по времени:
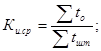
|
(17)
|
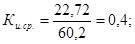
Загрузку оборудования и коэффициент его использования представляют графически в виде гистограмм.
Рис. 1. График загрузки основного оборудования.

Рис. 2. График использования оборудования по времени.
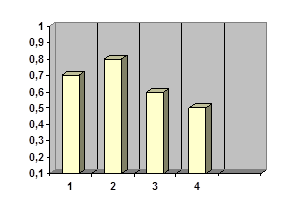
Таблица 3.
Сводная ведомость оборудования сводится в табл. 3.
Наименование станка
|
Марка станка
|
Габариты
|
Принятое кол-во станков
|
Коэффициент загрузки
|
Основное оборудование
|
1. Токарный с ЧПУ
|
16К20Ф3
|
3360×1710
|
4
|
0,57
|
2. Сверлильный
|
2Н135
|
1085×920
|
2
|
0,97
|
3. Шлифовальный
|
3А110В
|
1880×2025
|
2
|
0,78
|
4. Шлифовальный
|
3Г71
|
1870×1550
|
1
|
0,98
|
ИТОГО:
|
|
|
9
|
0,9
|
3.
Расчет потребного числа работающих
Для организации производства в цехе (на участке) должна быть определенная численность следующих категорий работающих:
-основные рабочие;
-вспомогательные рабочие;
-инженерно-технические работники;
-служащие.
Расчет численности основных рабочих производится по каждой специальности отдельно

|
(18)
|
где Фдр
– действительный фонд времени одного рабочего (согласно производственному календарю);
Кмо
– коэффициент многостаночного обслуживания (для механических цехов крупносерийного производства составляет 1,5…1,8; серийного производства 1,3…1,5; мелкосерийного производства 1,1…1,2).
Токарная операция: 
Сверлильная операция: 
Шлифовальная операция: 
Шлифовальная операция: 
Составим план-график оборудования и рабочих мест.
Таблица 4.
График оперативной загрузки сводим в табл. 4.
Технологический процесс
|
Загрузка рабочих мест
|
Рабочие
|
График работы оборудования и рабочих
|
Операция
|
tшт
, мин
|
Расчетное количество оборудования
|
Принятое
количество оборудования
|
№
|
Процент загрузки
|
1 смена
|
2 смена
|
1
|
30,0
|
3,3
|
4
|
1
|
|
|
|
|
2
|
|
|
|
|
2
|
14,2
|
1,6
|
2
|
1
|
|
|
|
|
2
|
|
|
|
|
3
|
12,0
|
1,3
|
2
|
1
|
|
|
|
|
2
|
|
|
|
|
4
|
4,0
|
0,4
|
1
|
1
|
|
|
|
|
Таблица 5.
Группа работающих
|
Должность
|
Всего
|
I смена
|
Токарь
|
1
|
|
Сверловщик
|
1
|
|
Шлифовальщик
|
1
|
|
Итого:
|
3
|
|
Вспомогательные:
|
|
|
Наладчик оборудования
|
1
|
|
Итого:
|
1
|
|
ИТР РАБОЧИХ:
|
|
|
Сменный мастер
|
1
|
|
Итого:
|
1
|
|
ВСЕГО РАБОТАЮЩИХ:
|
5
|
|
4.
Определение производственной площади
Производственная площадь цеха определяется исходя из количества оборудования и средних удельных норм площади на единицу оборудования.
для мелких станков (1500×750)
|
9…12м2
|
для средних станков (от 1500×750 до 3500×2000)
|
13…18м2
|
на одно рабочее место слесаря
|
4…5м2
|
Для механических цехов в машиностроении распространена ширина пролетов – 12м (легкое машиностроение); 12…18м (среднее машиностроение); 18 21, 24, 27, 30, 36м (тяжелое машиностроение).
Т.к. на участке 9 средних станков, то 9×15=135м2
;
На рабочие места слесарей 16м2
;
Вспомогательные помещения 27м2
;
Бытовые помещения 27 м2
;
Исходя из выше приведенных расчетов и с учетом ширины пролетов, общая производственная площадь участка механического цеха будет равна 335м2
///
Потребное количество электрокаров:
;
Gсм
– масса груза перевозимая за смену; Lпр
– длина перевозок;
Vcp
-скорость средняя;
tпогр,
tразг
– время погрузки и разгрузки;
Тсм
- количество чаов в смене;
gтр
- грузоподьеность тележки;
hтр
– коэффицент рузоподьемности ;
;
Коэффициент механизации:
Кмех
=Qмех
/Qобщ
;
Кмех
= 2/11*100%=18%;
Заделы:
Змах
= под
- потр
;
Змах
= под
- потр
=0,08
Змах
= под
- потр
=0,19
Зм
x
х
= под
- потр
=1,56
Количество груза за смену:
Nсм
= 
Nсм
= шт
Dр
– количество рабочих дней в году
Грузоподъемность тележки:
gтр
= 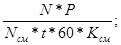
gтр
= т
Масса груза, перевозимая за смену:
Gсм
= 
Gсм
= 
Потребляемое количество кран-балка:
; шт
Заключение
После расчета всех необходимых данных получили:
- среднесерийное производство;
- приведенная программа выпуска Nпр.
=9605 шт.;
- количество оборудования на участке Суч.
=9 станков
- общее количество работающих: 5 человек из них
основных - 3 человек;
вспомогательных -1 человека;
ИТР - 1 человек;
- производственная площадь от 335…350 м2
.
Для перемещения грузов используются 3 электрокара и 2 мостовых крана.
Список литературы
1. Методические указания к выполнению курсовой работы по дисциплине "Проектирование машиностроительного производства" для студентов специальностей 120100 всех форм обучения.
2. Мельников Г.Н., Вороненко В.П. Проектирование механосборочных цехов. М.: Машиностроение, 1990. – 352с.
3. Егоров М.Е. Основы проектирования машиностроительных заводов. М.: Высшая школа, 1969. 480с.
4. Справочник технолога-машиностроителя. Под ред. А.Г. Косиловой, Р.К. Мещерякова. Т.1,2 М.Машиностроение, 2005г.
|