Содержание
Задание
1 Обжиговые печи черной металлургии
1.1 Общие сведения
1.2 Обжиговые печи
2 Шахтные печи
2.1 Принцип действия и устройство шахтных печей
2.2 Способы отопления и режимы обжига в шахтных печах
2.3 Особенности теплообмена в слое
Заключение
Список использованных источников
1 Обжиговые печи в чёрной металлургии
1.1 Общие сведения
Печные установки служат для обжига различных сыпучих материалов, суспензий или изделий разнообразных форм и размеров. Показателем успешно проведенного обжига является высокое качество готового продукта, полученного в результате воздействия на материал ряда внешних факторов, называемых режимом обжига. Под режимом обжига понимают совокупность температурных и аэродинамических условий и длительности обжига, а также характера газовой среды, в которой происходит обжиг.
В свете этих положений различают температурный и аэродинамический режимы обжига.
Температурный режим определяется скоростью подъема температуры до максимальной, временем выдержки материала при максимальной температуре и скоростью его охлаждения. Наглядное представление о температурном режиме дает температурная кривая обжига.
Аэродинамический режим печи характеризуется статическим давлением в рабочей полости. Неравномерное распределение давления или разрежения приводит к разной скорости движения газовых потоков вокруг обжигаемого материала и неравномерному нагреву изделий. Особенно отрицательно это сказывается на качестве крупногабаритных изделий.
Наиболее равномерное распределение температур по рабочему пространству печи устанавливается при статическом давлении, близком к нулю. Повышенное давление в рабочем пространстве печи приводит к выбиванию газов в помещение цеха через имеющиеся в печи неплотности. Наоборот, разрежение создает присосы наружного холодного воздуха, вызывающие местное понижение температуры. Аэродинамический режим печи во многом зависит от сопротивления самого обжигаемого материала прохождению газов. Равномерное сопротивление слоя кускового материала или садки изделий в печи способствует равномерному обжигу.
Состав газовой среды в процессе обжига может быть окислительным, если в газах присутствует свободный кислород, восстановительным при содержании в газах водорода Н2
, окиси углерода СО, углерода С в виде мельчайших частиц сажи и нейтральным при отсутствии в газах СО, Н2
и О2
.
Определенный состав газовой среды достигается сжиганием топлива при разных значениях коэффициента избытка воздуха а. На качество обжига гипса, извести, шамота газовый режим не оказывает существенного влияния, но в целях уменьшения потерь теплоты с отходящими газами рекомендуют топливо сжигать с таким количеством воздуха, которое по возможности близко к теоретическому его значению, т. е. при а=1.
Каждые материал или изделие, обжигаемые в той или иной конструкции печи, требуют индивидуального режима обжига. Резкий режим обжига отличается высокими скоростями подъема и снижения температуры. В противоположность ему мягкий режим протекает при малых скоростях подъема и снижения температуры. Большинство кусковых материалов — гипс, известь, цементный клинкер, глина, шамот — можно обжигать при резких режимах. Решающим значением здесь для получения качественной продукции является продолжительность выдержки материала при максимальной температуре для завершения всех физико-химических процессов, протекающих в материале при его обжиге. Формованные же изделия, наоборот, обжигают при мягких режимах. Наряду с достаточной продолжительностью выдержки при максимальной температуре для обжига формованных изделий характерны меньшие скорости подогрева и охлаждения во избежание появления в материале разрушающих напряжений.
Рациональная конструкция печи должна обладать всеми возможностями для регулирования процесса обжига по отдельным его зонам для каждого вида обжигаемого в ней материала, а также отличаться высокими технико-экономическими показателями работы. Оптимальный режим обжига — это совокупность всех внешних условий, обеспечивающих получение готового продукта высокого качества при наилучших технико-экономических показателях печи.
К технико-экономическим показателям печной установки относят:
а) производительность — количество вырабатываемого в принятую единицу времени готового продукта. Для сравнения производительности отдельных печей при обжиге в них однотипного материала и для удобства нормирования пользуются понятием удельная производительность печи или съем — это количество готового продукта, получаемого с 1 м3
или с 1 м2
площади попе речного сечения рабочего пространства печи в принятую единицу времени;
б)расход топлива на обжиг принятой единицы продукции. Этот показатель определяют отношением расхода условного топлива к количеству готовой продукции. Он характеризует тепловую экономичность печи;
в)расход электроэнергии (кВт-ч) на обжиг принятой единицы продукции. В пламенных печах основными потребителями электроэнергии являются вентиляторы и дымососы;
г)затраты труда на обслуживание печи выражают отношением человеко-часов к количеству готовой продукции; затраты труда зависят от степени механизации печи;
д) капитальные затраты, связанные с расходом и стоимостью материалов на сооружение печи.
Вышеприведенные технико-экономические показатели работы печи дают возможность не только определить стоимость обжига принятой единицы продукции, но и судить о совершенстве той или иной конструкции, наметить пути дальнейшего ее усовершенствования.
1.2 Обжиговые печи
В черной металлургии обжиговые шахтные печи применяют главным образом для обжига железных руд, известняка, магнезита и доломита. По виду используемого топлива обжиговые шахтные печи разделяются на пересыпные и с выносными топками.
Пересыпные шахтные печи применяют преимущественно для обжига тугоплавких материалов: известняка, доломита и др. Топливом служит коксовая мелочь, загружаемая в печь вместе с известняком. В нижней части шахты устанавливают механическое устройство для выгрузки обожженного продукта и регулирования схода шихты. Воздух подают через решетку разгрузочного устройства. Иногда для улучшения распределения шихты на колошнике печи устанавливают засыпной аппарат с одной вращающейся воронкой и конусом. Подогрев и обжиг материалов осуществляется в верхней части шахты. В нижней части обожженный материал охлаждается и одновременно подогревается воздух.
Шахтные печи с выносными топками применяют для обжига сравнительно легкоплавких железных руд. Нагрев и обжиг материала осуществляется продуктами сгорания, поступающими из топок в среднюю часть шахты по специальным каналам. Топки располагают около шахты, они могут иметь с ней общие стенки. В качестве топлива используют горючие газы любого вида, мазут и каменный уголь. Нижняя часть шахты как и в пересыпных печах, служит для охлаждения обожженного материала. Для этого через нее пропускают определенное количество воздуха, который нагревается и в средней части печи смешивается с продуктами сгорания, поступающими из топок.
Продукты сгорания, подводимые по каналам через стенки шахты, устремляются в основном по наиболее легкому пути в периферийных областях слоя. Чтобы прогреть центральные области слоя шихтовых материалов, шахты печей делают узкими (с вытянутым поперечным сечением). В некоторых печах нижнюю часть шахты перегораживают огнеупорными стенками (кернами), в которых предусмотрены каналы для подачи продуктов сгорания в центральные области. Схема такой печи, предназначенной для обжига сидеритов (железных руд, содержащих до 20 % Fe), представлена на (рисунке 1).
Удельная производительность обжиговых шахтных печей значительно ниже, чем для вагранок, около 0,5—1.0 т/(м2
-ч). Расход условного топлива зависит от содержания влаги и карбонатов в обжигаемом материале. При обжиге известняка он составляет 180—200 кг на 1 т готового продукта.
Для повышения производительности и замены кокса на газообразное топливо в зоне горения известковых печей стали устанавливать горизонтальные водухоохлаждаемые балки с вмонтированными в них или под ними газовыми горелками. Куски известняка проходят между этими балками через пламя горящего газа. При установлении по высоте печи двух рядов балок в шахматном порядке достигается значительное улучшение качества обжига.
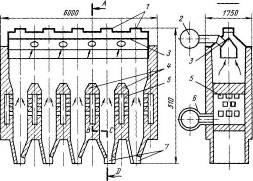
1 — люки для загрузки шихты: 2 — газопровод для отходящих газов;
3 — гребень (разбойник), направляющий руду к стенкам печи; 4 — поперечные стенки (керны); 5 — каналы для подвода горячих газов в слой обжигового материала; 6 – футерованный газопровод для продуктов сгорания газообразного топлива; 7— люки для выгрузки обожженного материала
2 Шахтные печи
2.1 Принцип действия и устройство шахтных печей
Автоматические шахтные печи при относительно небольших размерах просты по конструкции, требуют сравнительно небольших капиталовложений при строительстве и характеризуются сравнительно низким расходом тепла — около 4,200 МДж (1000 ккал) на 1 кг клинкера. Однако производительность их за сутки невысока — не более 270 т. В СССР эти печи имеются лишь на трех предприятиях. Заводы с шахтными печами строят в единичных случаях, так как для эффективного применения этих печей необходимы сырьевые материалы невысокой влажности, пластичный глинистый компонент и твердое короткопламенное топливо (антрацит, кокс, тощий уголь, сланцевый кокс), содержащее не более 7% летучих веществ.
Основным элементом автоматической шахтной печи (рисунок 2) является сварной цилиндрический кожух диаметром 2—3 м и высотой 8—12 м, облицованный внутри шамотным кирпичом и хромомагнезитом. Нижнюю часть шахты облицовывают чугунными плитами. Верхняя часть шахты расширена (примерно на 25%) в виде воронки. К верхней части шахты, закрытой специальным колпаком, примыкает труба для удаления отходящих газов.
Над шахтой расположены бункера сырьевой смеси и топливной крупки, весовые или винтовые дозаторы, смесительный шнек и тарельчатый гранулятор. Кроме сырьевой смеси и топливной крупки на тарелку гранулятора подается распыленная вода, вокруг брызг, которой образуются сырьевые гранулы, скатывающиеся во вращающуюся течку загрузочного устройства, распределяющего гранулы равномерно по сечению шахты. Внизу шахта закрыта вращающейся решеткой, жестко посаженной на вертикальный вал, и многошлюзовым затвором, предупреждающим потери воздуха высокого давления. Воздух для горения подается в печь от воздуходувки, обеспечивающей давление до 2500 мм вод. ст., по разветвленному воздухопроводу частично под решетку и частично для улучшения сгорания топлива в зоны подогрева и кальцинирования. В эти же зоны для дожигания обычно образующейся в печи окиси углерода иногда по центральной трубе подают кислород. Во избежание утечки сжатого воздуха через разгрузочное отверстие клинкер выгружают из печи через двух -, трех-шлюзовой затвор, клапаны которого открывают и закрывают попеременно специальным гидропривводом.
Таким образом, автоматическая шахтная печь представляет собой печь непрерывного действия с механизированной подготовкой и загрузкой сырьевых гранул, а также разгрузкой клинкера.
Печи последних конструкций оборудуют контрольно-измерительными приборами и приборами автоматического регулирования процесса.
Производительность шахтной печи прямо пропорциональна квадрату диаметра шахты, высоте шахты, давлению дутья и количеству воздуха, подаваемого в печь, и обратно пропорциональна размеру кусков обжигаемого материала. Съем клинкера с единицы объема шахтной печи составляет 100—135 кг/(м3
-ч).
Качество клинкера шахтных печей несколько ниже качества клинкера, обожженного во вращающихся печах. Оно может быть повышено в результате тонкого помола (до 8% остатка на сите с сеткой № 009) сырья при точной дозировке и тщательном перемешивании сырьевой смеси и топлива, хорошем гранулировании смеси (прочные гранулы размером 10—20 мм), равномерном распределении гранул при подаче воздуха с наибольшим давлением.
Существенным недостатком шахтных печей является их низкая производительность. Однако технико-экономический анализ показывает целесообразность применения автоматизированных шахтных печей в ряде случаев, например при небольшой производительности (до 600 т/сутки) завода.
Шахтные печи усовершенствованной конструкции, изготовляемые фирмами Леше и Де Ролль (Швейцария), работают по способу «черной муки» и имеют высокие технико-экономические показатели. Расход тепла в них составляет 3,35 МДж (800 ккал) на 1 кг клинкера. Из клинкеров шахтных печей 20 цементных заводов ФРГ получают цемент 325—425 (по стандарту ФРГ). Сланцевский цементный завод в шахтных печах получает клинкер марки 400 (по ГОСТ 10178—62).
Рисунок 2 - Шахтная печьВ последние годы производительность шахтных печей за сутки достигла 300 т, а фирма Леше проектирует и более крупные шахтные печи (диаметром 3,6—4 м, высотой 11,2—12 м) производительностью 400—500 т за сутки. Ведутся исследования по применению жидкого и газообразного топлива для обжига клинкера в шахтных печах, что обеспечит дальнейшее развитие и распространение этих экономичных установок.
Для дальнейшего совершенствования процесса обжига клинкера научно-исследовательские организации в последние годы разрабатывают и исследуют новые конструкции и схемы печных установок и новые методы обжига. Эти изыскания направлены на интенсификацию и повышение тепловой эффективности процесса клинкерообразования путем повышения температуры реакции или обжигом сырьевой смеси во взвешенно-фонтанирующем или в кипящем слое. Однако промышленных установок таких еще нет.
Шахтные печи являются печами непрерывного действия. Они представляют собой высокую шахту, оборудованную механизмами для загрузки и выгрузки материала, вентиляторами для подачи холодного воздуха и отбора отходящих газов и устройствами для сжигания топлива. В работающей печи вся шахта заполнена кусковым материалом, который, двигаясь сверху вниз под действием силы тяжести, последовательно подогревается, обжигается и охлаждается. Готовый продукт выгружается в нижней части шахты через разгрузочное устройство, при этом весь столб материала опускается вниз и на освободившееся вверху место поступает сырой материал. В печи соблюдается принцип противотока: в зоне подогрева и обжига материал движется навстречу дымовым газам, образовавшимся при горении топлива, а в зоне охлаждения — навстречу воздуху. Воздух, охлаждая материал, сам нагревается и горячим достигает зоны обжига, где участвует в процессе горения топлива или смешивается с топочными газами, если топливо сгорает вне печи в специальных топках.
Шахта печи выполнена из кирпича и заключена в металлический кожух. Опорой под шахту печи служит железобетонная плита, лежащая на четырех железобетонных колоннах, которые опираются на фундаментную железобетонную плиту. Для равномерного распределения топлива поперечное сечение шахты может быть круглой или эллипсовидной, реже прямоугольной формы. Вертикальное сечение шахты (профиль) представляет собой прямоугольник, иногда суживающийся кверху или книзу. Стены печи многослойные: внутренний слой выполнен из огнеупорного кирпича толщиной 210—230 мм в зоне подогрева и охлаждения и 345— 460 мм в зоне обжига. За ним следует теплоизоляционный слой из шамотного легковеса толщиной 210—230 мм. Пространство между изоляционным слоем и кожухом шириной 50—60 мм засыпают молотым шамотом или трепелом для компенсации температурного расширения кирпичной кладки.
Загрузочное устройство (рисунок 3) обеспечивает регулярную 3агрузку материала и топлива в печь, равномерное распределение их го шихте и герметичность во избежание присосов наружного воздуха. В период загрузки происходит поочередное открытие клапанов, благодаря чему шахта не сообщается с атмосферным воздухом
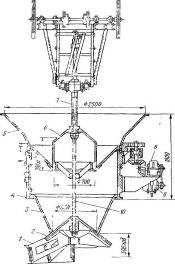
1—отбойная пластина, 2-нижний клапан, 3—конус,
4—цилиндрический корпус, 5—приемная воронка, 6—
верхний клапан, 7—полая тяга, 8—редуктор, 9—
электродвигатель, 10—шток
Рисунок 3 - Двухклапанное загрузочное устройство Гипрострома
Разгрузочные механизмыслужат для непрерывной выгрузки обожженного материала при абсолютной герметичности нижней части шахты, особенно в клинкерообжигательных печах, работающих с высоким давлением дутья. Конструкция разгрузочного устройства зависит от вида выгружаемого материала, который может быть рыхлым, как, например, гипс, известь, или спекшимся — цементный клинкер. Разгрузочное устройство Гипрострома для выгрузки рыхлых материалов (рисунок 4) похоже на сварную каретку-платформу, на раме которой уложены колосники клинообразной формы. Столб материала опирается на ее поверхность и частично на центральный гребень, охлаждаемый воздухом. Каретка совершает поступательно-возвратное движение. При этом часть кусков материала проваливается в прозоры колосников, а более крупные куски скатываются с их поверхности в бункер.
Шлюзовое уплотнительное устройство (рисунок 4) состоит из двух-трех камер, последовательно расположенных за течкой бункера. Каждая камера отделена от предыдущей автоматически открывающимся затвором. Заслонки затворов открываются поочередно. При поступлении материала в первую камеру открывается ее затвор, в то время как затворы последующих двух камер закрыты. При дальнейшем движении материала по камерам открыт один затвор, а два других затвора всегда закрыты. Этим достигается хорошее уплотнение нижней части шахты, препятствующее выходу в атмосферу вдуваемого воздуха.
А-А 2600

1—люк, 2—штанга, 3—шток; 4—гидропривод; 5—опорные катки; 6—рельсовые балки, 7—каретка, 8—бункер, 9—шлюзовой затвор; 10— колосники
Рисунок 4 – Выгрузочная решетка Гипрострома
2.2 Способы отопления и режимы обжига
в шахтных печах
Все материалы, обжигаемые в шахтных печах, в зависимости от режима обжига можно разбить на две группы: материалы низко- и высокотемпературного обжига. К первым относят строительный гипс, низкожженый шамот, обжигаемые при температурах 773—1173 К (500—900 °С), ко вторым — известь, высокожженный шамот, цементный клинкер и другие материалы, обжигаемые при 1473—1773 К (1200—1500 °С) и выше. Для осуществления температурного режима, соответствующего обжигу того или иного материала, печи имеют разную систему отопления. Печи низкотемпературного обжига в зоне обжига оборудуют топками полного сжигания топлива, вынесенными за пределы шахты; для них используют любой вид топлива. Топочные газы при входе в шахту разбавляют воздухом, поступающим из холодильника, для образования газовоздушной смеси любой требуемой температуры. В печах высокотемпературного обжига топливо сгорает в самой шахте среди обжигаемого материала. Если топливо твердое, его подают в печь через загрузочное устройство в смеси с материалом или послойно в соотношении, определяемом условиями обжига.
В зоне подогрева температура топлива достигает температуры воспламенения и при поступлении в зону обжига, смешиваясь с горячим воздухом, движущимся вверх по шахте из зоны охлаждения, оно сгорает среди кусков материала. Такие печи называют пересыпными.
В пересыпных печах применяют только короткопламенное топливо, преимущественно антрацит во избежание потери летучих горючих веществ в зоне подогрева. Остающаяся после сгорания топлива зола засоряет обожженный материал, и его качество ухудшается. Это является недостатком пересыпных печей. Длиннопламенное топливо сжигают в полугазовых топках, пристроенных к шахте на уровне зоны обжига. Полученный в них полугенераторный газ имеет высокую температуру и, смешиваясь в шахте с сильно нагретым воздухом, идущим из зоны охлаждения, сгорает среди кусков материала с выделением значительного количества теплоты.
Газообразное топливо сжигают в горелках, смонтированных в стенках шахты в зоне обжига. В печах, работающих на мазуте, шахта в поясе зоны обжига имеет специальные форкамеры, предназначенные для предварительной газификации мазута. Из них продукты газификации, содержащие до 26% горючих газов и имеющие высокую температуру, поступают в шахту и сгорают среди материала с высоким температурным эффектом.
Температурный режим обжига кусковых материалов в шахтной печи характеризуется постепенным подъемом температуры в зоне подогрева домаксимальной, выдержкой материала в зоне обжига при максимальной температуре и постепенным ее снижением в зоне охлаждения. Высота зон пропорциональна продолжительности отдельных периодов обжига.
Главным для получения качественного продукта является время пребывания материала в зоне обжига, необходимое для завершения всех протекающих в нем физико-химических процессов. Время подогрева и охлаждения в целях сокращения всего процесса обжига и увеличения производительности шахтной печи может быть без ущерба для качества минимальным.
Аэродинамический режим шахтной печи обусловлен взаимным расположением тягодутьевых устройств и сопротивлением слоя материала в шахте. Верхняя часть печи — зона подогрева — сообщается с дымососом, поэтому находится под разрежением, постепенно убывающим по направлению к зоне обжига. В зоне обжига разрежение достигает минимального, близкого к нулевому, значения. Нижняя часть шахты — зона охлаждения — находится под давлением, так как в нее дутьевым вентилятором нагнетают холодный воздух. По мере движения воздуха в направлении зоны обжига давление убывает.
Состав газовой среды на качество обжига кусковых материалов не оказывает существенного влияния. Значение коэффициента избытка воздуха в зоне обжига должно соответствовать роду сжигаемого топлива и системе отопления печи при минимальных потерях теплоты от химического и механического недожога и с отходящими из печи газами. Коэффициент избытка воздуха в зоне обжига обусловлен также его количеством, идущим из зоны охлаждения и определяемым потребностью материала в холодном воздухе для охлаждения до температуры выгрузки из печи.
Конструкции шахтных печей для обжига отдельных материалов
Печи для обжига извести. В шахтных печах обжигают более или менее плотные породы известняков. Мел, не обладающий достаточной механической прочностью, будет раздавлен и забьет шахту, появится препятствие фильтрации газов через слой материала, поэтому мел обычно обжигают во вращающихся печах. Температура обжига известняков колеблется в пределах от 1173 до 1473 К (900 до 1200 °С) в зависимости от их прочности и химического состава.
Известково-обжигательные печи могут быть пересыпными в случае применения короткопламенного топлива, либо иметь выносные полугазовые топки при использовании длиннопламенного топлива. Они также могут работать на газе или мазуте. Шахта пересыпной шахтной печи производительностью 200 т/сут (рисунок 5)цилиндрической формы с внутренним диаметром 4,3 м и рабочей высотой 25 м. Печь снабжена двухклапанным загрузочным устройством с поворотной чашей для послойной подачи материала и топлива — антрацита.
Автоматизация загрузки способствует поддержанию в шахте постоянного уровня материала. Выгрузочным механизмом печи служат движущиеся каретки. Уплотнение нижней части шахты достигается трехшлюзовым затвором.
Удельная производительность составляет 0,75 т/(м3
-сут). Расход условного топлива 133 кг/т извести.
Более поздние проекты Гипрострома высокопроизводительных шахтных печей для обжига извести ориентированы на отопление их газообразным и жидким топливом. Шахтная печь производительностью 200 т/сут на газообразном топливе представлена на (рисунке 6) Прямоугольное со скругленными углами сечение шахты в зоне обжига переходит в круглое в зоне подогрева. В целях интенсификации охлаждения профиль шахты книзу сужают. Подачу газа в зону обжига производят в два яруса. В нижний ярус газ подают через шесть диффузионных горелок, встроенных в стены шахты, и в центральную часть печи через многосопловые балочные горелки. Такие же горелки расположены в верхнем ярусе, только расположение центральных горелок перпендикулярно таковым нижнего яруса.
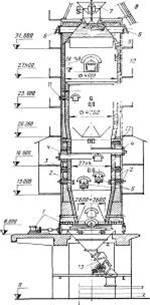
1—выгрузочная решетка; 2—периферийные горелки нижнего яруса; 3, 12—отверстия для установки датчиков давления и температуры, 4—две балочные горелки верхнего яруса; 5—две балочные горелки нижнего яруса; 6—предохранительный взрывной клапан; 7—двухклапанное загрузочное устройство; 8—скиповый подъемник; 9—отверстия для датчиков уровнемера шихты; 10—короб отсоса дымовых газов; 11—гляделка; 13—трехшлюзовой затвор
Рисунок 6 – Шахтная печь конструкции Гипрострома на газообразном топливе
Часть необходимого для горения воздуха (25—30%) поступает через диффузионные горелки, остальной воздух — через зону охлаждения печи. Удельная производительность по извести составляет 0,8 т/(м3
-сут); удельный расход условного топлива 155 кг/т извести.
Шахтная печь на мазуте конструкции Гипрострома (рисунок 7) имеет производительность 30 т/сут.
Форма поперечного сечения сходна с печью, работающей на газе. Размер сечения в зоне обжига 2x2 м, в зоне охлаждения 1,6x1,6. Рабочая высота шахты 19,2 м. Мазут поступает в шесть механических форсунок. Две из них вводят мазут в подбалочное пространство центральной части шахты, остальные распыляют его в специальных форкамерах для предварительной газификации. Продукты газификации, поступая в шахту, смешиваются со вторичным воздухом, подаваемым из холодильника печи, и сгорают среди материала.
Печи для обжига цементного клинкера. Шахтные печи для обжига цементного клинкера (рисунок 8) нашли распространение при получении цемента из пластичных природных мергелей. Перед обжигом в шахтных печах к сырью добавляют размолотое до крупности 0,3—0,5 мм топливо и из полученной шихты изготовляют так называемый «черный брикет» или черные гранулы размером 15—25 мм, загружаемые в печь на обжиг.
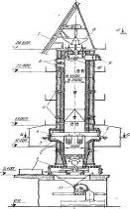 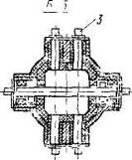
1—выгрузочная решетка; 2— форкамеры; 3— мазутные форсунки;
4—водоохлаждаемая балка; 5—гляделки; 6—отверстия датчиков уровнемера шихты; 7—скиповый подъемник; 8—загрузочное устройство;
9— предохранительный взрывной клапан; 10— отверстие дляотсоса газов; 11—барабанный затвор.
Рисунок 7 – Шахтная печь на жидком топливе
Конструктивное отличие шахтной печи для обжига цементного клинкера обусловлено в основном следующим: условиями сгорания топлива, запрессованного в материал; высокой температурой обжига 1573—1773 К (1300— 1500° С) до спекания обжигаемого материала; особенностью физико-химических процессов, протекающих в обжигаемом материале, и спекшейся структурой готового продукта.
Для осуществления равномерного обжига по сечению шахты ее внутренний диаметр не превышает 2,4—2,8 м. Исключение составляет высокомощная печь Юж-гипроцемента диаметром 4,1 м. Рабочая высота шахты 8—10 м. Верхняя часть шахты высотой 2 м книзу постепенно сужена во избежание образования у ее стенок сквозных каналов, вызванных усадкой материала при нагревании. Нижнюю часть шахты футеруют жаростойкими чугунными плитами. Ввиду большого сопротивления слоя спекшегося клинкера в шахте печи имеют высокое давление воздушного дутья, достигающее 15—25 кПа, поэтому нижняя часть шахты имеет надежное уплотнение в виде многошлюзовых затворов.
Так как обожженный материал характеризуется спекшейся структурой, разгрузочное устройство должно дробить его перед выгрузкой из шахты. С этой целью устройство выполняют в виде вращающейся зубчатой решетки или нескольких пар вращающихся навстречу друг другу зубчатых вальцов. При вращении их клинкер дробится, и кусочки его поступают в нижнюю бункерную часть печи, а затем в камеры шлюзовых затворов.
Для успешного сжигания топлива, запрессованного в материал, требуется не только проникновение кислорода внутрь гранул, но также повышенная концентрация его в окружающей среде. Это вызвано тем, что образовавшаяся при горении кокса углекислота может восстанавливаться до СО при соприкосновении с раскаленными кусочками кокса топлива по реакции СО2
+ С = = 2СО.
Таким образом, присутствие в окружающей атмосфере кислорода должно привести к дожиганию окиси углерода. С этой целью печь имеет позонное дутье. Часть воздуха, необходимого для горения, поступает через зону охлаждения подогретым, другая часть поступает непосредственно в зону обжига по периферии шахты. Кроме этого, в центральную часть шахты предусмотрена подача чистого кислорода.
Удельная производительность печей при обжиге гранул достигает 157 кг/(м3
-ч), при обжиге крупных брикетов 120 кг/(м3
* ч), расход условного топлива от 140 до 200 кг/т.
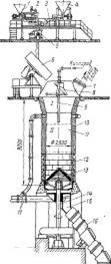
1, 2, 3—зоны; 1—бункер угля; 2, 3—питатели; 4—бункер сырьевой муки; 5—смесительный шнек; 6—гранулятор; 7—газоход; 8—загрузочный желоб; 9—труба подачи кислорода; 10—футеровка; 11— шахта печи; ./2—чугунные плиты, 13—разгрузочная решетка; 14—приводной вал; 15—разгрузочная течка; 16—затвор; 17—воздуховоды
Рисунок 8 – Шахтная печь для обжига, цементного клинкера
2.3 Особенности теплообмена в слое
Топливные печи широко применяются в черной металлургии. Их используют для получения чугуна из железной руды, в них выплавляют сталь, нагревают металл перед обработкой давлением и осуществляют термическую обработку. Все топливные печи черной металлургии могут быть подразделены на две большие группы: слоевые и пламенные.
В слоевых печах с плотным (фильтрующим) слоем используется твердое кусковое топливо. Их применяют для выплавки чугуна из руды, расплавления металла перед литьем, обжига железных руд, известняка, магнезита и доломита. Слоевые печи относятся к шахтным печам, важнейшими из которых являются доменные печи — основные агрегаты любого предприятия с полным металлургическим циклом.
В пламенных печах используется газообразное или жидкое топливо, которое (как говорит само название печей) сжигается с образованием пламени (факела) в рабочем пространстве печей. Факельный метод сжигания топлива применяется в мартеновских печах при выплавке стали, в нагревательных печах прокатных и кузнечных цехов, в печах для термической обработки стали.
К исследованию теплообмена в условиях слоя кусковых материалов, двигающихся навстречу потоку газов, как это имеет место в шахтных печах, многие десятилетия привлечено внимание ученых и инженеров. В нашей стране наиболее значительные работы в этой области выполнены во Всесоюзном научно-исследовательском институте металлургической теплотехники (ВНИИМТ) и Уральском политехническом институте.
Теплообмен в слое представляет собой крайне сложный случай теплообмена. Плотный слой образуется кусками различной формы и размеров, имеющими различные теплофизические свойства. Сложный характер движения кусков значительно затрудняет определение реальной поверхности теплообмена. Различная величина зазоров между кусками влияет не только на особенности омывания их газами, но делает неразделимыми процессы теплопроводности, излучения и конвекции, действующие в слое. Поэтому приходится применять общий коэффициент, учитывающий все три вида теплообмена. Из-за неопределенности поверхности теплообмена более удобно использовать объемный коэффициент теплоотдачи αv
[Вт/(м3
· К)]. Связь его с обычным коэффициентом теплоотдачи α [Вт/(м2
· К)] выражается следующим образом: αv
= αF, где F— поверхность нагрева, заключенная в 1 м3
слоя кусковых материалов, м2
.
Кроме того, слой кусковых материалов характеризуется порозностью f, которая представляет собой отношение объема пустот к полному объему слоя. Для двигающегося слоя, перемещающегося вертикально сверху вниз по высоте какой-то шахты Н, используют понятие объемного напряжения сечения шахты р [м3
/(м2
· с )], показывающего, какой объём кусковых материалов перемещается через 1 м2
сечения шахты в течение 1 ч, т. е. Н - рt, где t— время полного перемещения сверху вниз, с.
Как уже подчеркивалось, шихтовые материалы в слоевых печах обычно имеют самые разнообразные размеры и теплофизические свойства. Мелкие куски, например, железорудного сырья, обладающие относительно высокой теплопроводностью, приближаются по свойствам к термически тонким телам, а крупным кускам агломерата и особенно известняка присущи свойства, характерные массивным в тепловом отношении телам. В результате этого необходимо выполнять анализ условий нагрева кусков шихты в очень широком диапазоне значений их теплового сопротивления. Очень часто в шахтных печах нагрев слоя кусков шихты происходит в условиях наличия источников (стоков) тепловой энергии.
В большинстве шахтных печей движение шихты и газов происходит по принципу противотока. В доменной печи к тому же противоточная схема движения сред дополняется завершенностью теплообмена в результате значительной величины поверхности нагрева и интенсивного охлаждения газов.
Заключение
Технико-экономическая оценка
работы шахтных печей
Печи отличаются большой производительностью и тепловой экономичностью благодаря полному использованию рабочего объема шахты, утилизации теплоты газов и обожженного материала непосредственно в самой печи для подогрева сырья и воздуха, поступающего на горение топлива. Качество обожженного материала невысоко из-за неизбежного пережога поверхности кусков и более слабого обжига середины их.
Современные шахтные печи полностью механизированы и многие из них имеют автоматическое управление. Печи отличаются повышенным расходом электроэнергии на работу тягодутьевых устройств. Так как шахтные печи не требуют здания и не являются металлоемкими, капитальные затраты на их постройку относительно невелики.
Пути усовершенствования шахтных печей направлены на повышение их производительности, улучшение качества обжига и культуры обслуживания.
Список использованных источников
1 Никифорова Н.М. Теплотехника теплотехническое оборудование предприятий промышленности, строительных материалов и изделий / Н.В. Тресковой – Москва: Металлургия, Высшая школа, 1981 г.
2 Кривандин В.А. Металлургическая теплотехника – 2 том / В.А. Кривандин; профессор, доктор техн. наук. – Москва: Металлургия, 1986 г. – 590 с.
|