Дипломна робота:
Виготовлення корпуса гідроциліндра Г 29-3
Зміст
Введення
1. Аналіз вихідних даних
1.1 Аналіз службового призначення й умов роботи деталі
1.2 Систематизація й класифікація поверхонь деталі
1.3 Аналіз технологічності конструкції деталі
1.3.1 Технологічність заготівлі
1.3.2 технологічність установки
1.3.3 Технологічність оброблюваних поверхонь
1.3.4 Технологічність загальної конфігурації деталі
1.4 Формулювання завдань дипломного проекту
2. Визначення типу виробництва. Вибір і проектування заготівлі
2.1 Визначення типу виробництва
2.2 Вибір стратегії розробки технологічного процесу
2.3 Вибір і проектування заготівлі
2.3.1 Вибір методу одержання заготівлі
2.3.2 Економічне обґрунтування вибору методу одержання заготівлі
3. Технологічний маршрут і план виготовлення деталі
3.1 Обґрунтування технологічного маршруту виготовлення деталі
3.2 Вибір технологічних баз
3.3 Обґрунтування самоскидального операційних розмірів
3.4 Призначення операційних технічних вимог
3.5 Розрахунок припусків на обробку й проектування заготівлі
4. Вибір засобів технологічного оснащення (СТО)
4.1 Вибір устаткування
4.2 Вибір пристосувань
4.3 Вибір різального інструменту
4.4 Вибір засобів контролю
5. Технологія проведення операції хромування
6. Проектування технологічних операцій
6.1 Розрахунок режимів різання й визначення основного часу на операцію
7. Розрахунок і проектування верстатного пристосування
7.1 Збір вихідних даних
7.2 Розрахунок сил різання
7.3 Розрахунок зусилля затискача
7.4 Розрахунок затискного механізму патрона
7.5 Розрахунок силового привода
7.6 Розрахунок погрішності установки заготівлі в пристосуванні
7.7 Опис конструкції й принципу роботи пристосування
8. Проектування пристосування для контролю биття отвору
8.1 Опис конструкції пристосування
9. Розрахунок і проектування різального інструменту
9.1 Мети й завдання проектування
9.2 Проектування й розрахунок різця
9.3 Опис конструкції різця
10. Лінійна оптимізація режимів різання на токарській операції
10.1 Вихідні дані
10.2. Розрахунок обмежень
10.2.1 Обмеження по кінематиці верстата
10.2.2 Обмеження по потужності привода головного руху:
10.2.3 Обмеження по температурі в зоні різання
10.2.4 Обмеження по точності
10.2.5 Обмеження по стійкості інструмента
10.2.6 Розрахунок цільової функції
10.3 Рішення графічним методом
Висновок
Список джерел
Введення
У наш час питання розвитку виробництва в економіці серйозне й наукомістке завдання, але без розвитку виробництва й вкладення в нього засобів підприємства існувати не можуть. У зв'язку із цим підприємства шукають можливості й засоби для успішної роботи й подальшого розвитку. Зараз помітне прагнення заводів максимально знижувати собівартість своєї продукції, застосовувати більше високопродуктивне встаткування й оснащення, оснащувати верстати промисловими роботами.
Темою даного дипломного проекту є розробка технологічного процесу виготовлення корпуса гідроциліндра типу Г 29-3.
В умовах нинішньої економічної ситуації необхідно використовувати засоби з максимальним ефектом, щоб вони змогли в майбутньому приносити найбільший дохід, це стосується всіх машинобудівних підприємств.
Таким чином, метою дипломного проекту є розробка зовсім нового технологічного процесу виготовлення деталі, підвищення якості обробки, зниження собівартості виготовлення, застосування новітніх розробок в області технології машинобудування.
1.
Аналіз вихідних даних
Завдання даного розділу - на базі аналізу технічних вимог пропонованих до деталі й річного обсягу випуску сформулювати завдання, які необхідно вирішити в дипломному проекті для досягнення мети, сформульованої у введенні.
1.1
Аналіз службового призначення й умов роботи деталі
Деталь "Корпус гідроциліндра", є базовою деталлю гідроциліндра й призначена для базування різних деталей гідроциліндра, що входять у його конструкцію, щодо її поверхонь. До корпуса гідроциліндра деталі пред'являються вимоги підвищеної міцності й високого опору зношування.
1.2
Систематизація й класифікація поверхонь деталі
Всі поверхні на ескізі деталі нумеруємо й систематизуємо по їхньому призначенню, т. Ж. Зробимо кодування розмірів деталі (мал.1.1).
Результати класифікації поверхонь деталі занесемо в таблицю 1.1
ТАБЛИЦЯ 1.1
вид поверхні |
№ поверхні |
ип |
12, 13 |
окб |
12, 4 |
вкб |
13, 12, 4, 6, 5, 10, 11 |
сп |
всі інші |
У таблиці 1.1 уведені наступні позначення: ОКБ - основні конструкторські бази, ВКБ - допоміжні конструкторські бази, ИП - виконавчі поверхні, СП - вільні поверхні.
Схема кодування поверхонь і розмірів деталі
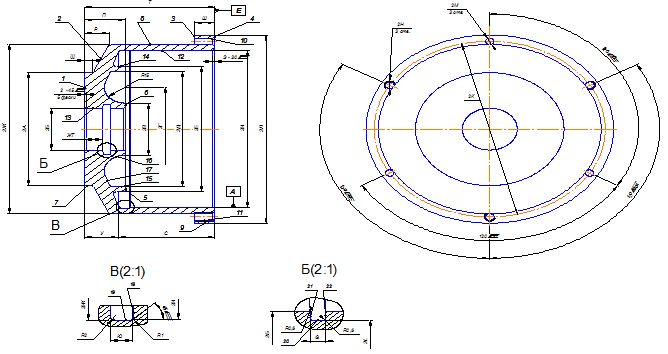
Мал. 1.1
1.3 Аналіз технологічності конструкції деталі
Аналіз технологічності конструкції деталі будемо проводити по наступних групах критеріїв:
технологічність заготівлі;
технологічність установки;
технологічність оброблюваних поверхонь;
технологічність загальної конфігурації деталі.
1.3.1 Технологічність заготівлі
Тому що до деталі пред'являються вимоги підвищеної міцності й високого опору зношування, то як матеріал при виготовленні корпуса гідроциліндра застосовується сталь 45л гост 977-75 з наступної її термообробкою (загартування, відпустка) і хромуванням пов.12,13.
матеріал не є дефіцитним, при відносно невисокій вартості він має гарні ливарні якості: температура початку затвердіння 1480-1490 °з; показник тріщиностійкості кт. в
=0,8; схильність до утворення усадочної раковини ку. р.
=1,2; плинність кж. т.
=1,0; ливарна усадка 2,2% - 2,3%; схильність до утворення усадочної пористості ку. п.
=1,0.
Сталь має гарну обробку різанням у відпаленому стані при нв 200: твердосплавним інструментом кv. тв. спл.
=1,1, інструментом зі швидкорізальної сталі кv. б. ст.
=1,1. до відпускної крихкості не схильна. Однак дана сталь є важкою для зварювання, що може викликати утруднення при одержанні заготівлі у вигляді звареної конструкції. спосіб зварювання: рдс, необхідний підігрів і наступна термообробка.
Межа міцності стали 45л становить 520 мпа, твердість hb148...217. хімічний склад стали 45л представлені в таблиці 1.2 [1].
Таблиця 1.2Хімічний склад стали 45л
марка |
зміст елементів,% |
сталь 45л |
с |
mn |
si |
cr |
ni |
cu |
s |
p |
0,42-0,50 |
0,40-0,90 |
0, 20-0,52 |
не більше |
0.30 |
0.30 |
0.30 |
0.045 |
0,04 |
заготівлю корпуса, можливо, одержати як литтям у земляні форми, так і у вигляді звареної конструкції, що складає із фланця, труби й дна.
в обох випадках заготівля проста по конфігурації й може бути отримана без особливих затрат. найбільш кращий варіант одержання заготівлі визначимо економічним розрахунком. Таким чином, заготівлю можна вважати технологічною.
1.3.2 технологічність установки
Чорновими базами для установки заготівлі на першій операції можуть бути циліндричні й торцеві поверхні заготівлі. надалі за бази прийняті циліндрична пов.12 і торцева пов.4 або циліндрична пов.13 і торцева пов.1, залежно від операції (операції 10, 20, 30, 40, 90, 100); на операції 50 за бази прийняті торцева пов.1 і циліндрична 8; на операції 120, 130 за бази прийняті торцева пов.1 і циліндрична 12, 13 відповідно.
Дані технологічні бази забезпечують надійну орієнтацію й закріплення заготівлі, можливість вільного підведення інструмента при обробці.
Поверхні деталі досить розвинені, тому при обробці не потрібне застосування складних і дорогих верстатних пристосувань.
Вимірювальні бази деталі можна використовувати як технологічні бази, тому що точність і шорсткість цих баз забезпечує необхідну точність обробки.
Таким чином, з погляду установки при обробці, деталь можна вважати технологічною.
1.3.3 Технологічність оброблюваних поверхонь
Передбачається обробляти всі поверхні деталі, крім пов.2, 3, 7, 8, 9, 14, 15, 16, 17 (т.до заданого точність і шорсткість дозволяють їх одержати на заготівельній операції). число оброблюваних поверхонь
14: 4 циліндричних: 12, 13, 10, 11; 4 торцевих: 4, 1, 5, 6; 3 різьбові отвори: пов.11; 2 канавки: пов.18, 19, 20, 21, 22; фаски.
Довжина оброблюваних поверхонь невелика й визначається умовами компонування гідроциліндра.
Для забезпечення нормальної працездатності всіх вузлів гідроциліндра призначені наступні вимоги до геометрії корпуса: допуск на розташування отворів під штифти й різьбові отвори під болти, щоб забезпечити точнее присохлий елементів гідроциліндра щодо корпуса при складанні, допуски на шорсткість призначаємо по [1], точність нарізних сполучень по [1], допуски перпендикулярності торців 4,6; допуск радіального биття призначаємо по [2].
Точність і шорсткість поверхонь 12, 13 (окб) визначається умовами експлуатації корпуса гідроциліндра. зменшення точності приведе до зниження точності установки поршня й вала в корпус гідроциліндра. всі отвори корпуса легко доступні для обробки. поверхні різного призначення розділені, що полегшує обробку. для виходу шліфувального кола, а також хонинговальной головки при обробці пов.12 передбачена канавка. на пов.13 передбачена канавка під ущільнювальне кільце. форма деталі дозволяє обробляти поверхня напроход. обробка поверхонь в упор утруднень не викликає.
Таким чином, з погляду оброблюваних поверхонь, деталь можна вважати технологічною.
1.3.4 Технологічність загальної конфігурації деталі
Деталь має достатню твердість і міцність. радіуси закруглень і фаски виконуються за дст 10948-64, форма й розміри канавок по
ДЕРЖСТАНДАРТ 8820-69. така уніфікація спростить обробку й контроль цих елементів корпуса гідроциліндра.
При обробці на верстаті зі ЧПУ на одній операції можна здійснити: обробку отворів пов.10,11 і нарізування різьблення в отвір 11. устаткування може бути просте, універсальним, оснащення також можна застосовувати універсальну. всі поверхні корпуса доступні для контролю.
Таким чином, з погляду загального компонування деталі її можна вважати технологічною.
Оскільки деталь відповідає вимогам технологічності по всім 4 групам критеріїв, можна зробити вивід об. її достатню технологічність.
1.4
Формулювання завдань дипломного проекту
На базі аналізу технічних вимог до деталі сформулюємо завдання дипломного проекту:
1. Визначити тип виробництва й вибрати стратегію розробки технологічного процесу;
2. Вибрати оптимальний метод одержання заготівлі й маршрут обробки поверхонь;
3. Розробити технологічний маршрут і схеми базування заготівлі
4. Розрахувати припуски на обробку методом Кована на одну поверхню, на інші поверхні призначити припуски відповідно до ДЕРЖСТАНДАРТ 26645-85;
5. Вибрати встаткування, пристосування, різальний інструмент, засоби контролю;
6. Зробити нормування технологічного процесу виготовлення корпуса гідроциліндра;
7. Розрахувати й спроектувати верстатне пристосування для токарської операції й пристосування контролю биття отвору;
8. Розрахувати й спроектувати різальний інструмент для токарської операції;
9. Провести лінійну оптимізацію режимів різання на токарській операції.
2. Визначення типу виробництва.
Вибір і проектування заготівлі
Завдання даного розділу - залежно від деталі й річного обсягу випуску визначити тип виробництва й на його базі вибрати оптимальну стратегію розробки технологічного процесу
2.1
Визначення типу виробництва
Тип виробництва визначаємо з урахуванням річної програми, маси деталі і якісної оцінки трудомісткості її виготовлення. По трудомісткості дану деталь можна віднести до деталей середньої трудомісткості.
Визначимо масу деталі по формулі:
, кг (2.1)
де ρ - щільність матеріалу, для сталі 45Л, приймаємо ρ = 0,00785 кг/см3; V - обсяг деталі, см3
Обсяг деталі визначаємо як алгебраїчну суму обсягів тіл за винятком порожніхіх циліндричних сегментів, що входять у конфігурацію деталі:

Знаючи обсяг деталі й щільність матеріалу, з якого зроблена деталь, визначаємо масу деталі:

Тип виробництва залежить від річного обсягу випуску деталей, її маси й трудомісткості. По трудомісткості дану деталь можна віднести до деталей середньої трудомісткості, тому при річній програмі випуску N = 15000 дет /рік і масі деталі m =9,8 кг по [2] стор.16а приймаємо тип виробництва – середнє серійне.
2.2
Вибір стратегії розробки технологічного процесу
Завдання даного підрозділу - залежно від типу виробництва вибрати оптимальну стратегію розробки технологічного процесу - принципових підхід до визначення його показників ТП, що сприяє забезпеченню заданого випуску деталей заданої якості з найменшими витратами.
При розробці оптимальної стратегії ТП будемо дотримуватися рекомендацій [3].
1. В області організації технологічного процесу:
Вид стратегії - послідовна, в окремих випадках циклічна; лінійна, в окремих випадках розгалужена; тверда, в окремих випадках адаптивна;
Форма організації технологічного процесу - перемінно-потокова форма організації технологічного процесу;
Повторюваність виробів - періодично повторювані партії;
2. Метод одержання заготівлі:
Оптимальний варіант одержання заготівлі - зварена конструкція або лиття в земляні форми;
Вибір послідовності обробки - по таблицях з урахуванням коефіцієнтів питомих витрат;
Припуск на обробку - незначний;
Метод визначення припусків - розрахунково-аналітичний, рішенням операційних розмірних ланцюгів;
3. В області розробки технологічного процесу:
Ступінь уніфікації ТП - розробка технологічного процесу на базі типового ТП;
Ступінь деталізації розробки ТП - маршрутний або маршрутно-операційний технологічний процес;
Принцип формування маршруту - концентрація операцій і сполучення по можливості переходів;
Забезпечення точності - робота на настроєному встаткування, із частковим застосуванням активного контролю;
Базування - з дотриманням принципу сталості баз і по можливості принципу єдності баз на наступних операціях технологічного процесу;
4. В області вибору засобів технологічного оснащення (СТО):
Устаткування - універсальне, у тому числі зі ЧПУ, спеціальне, спеціалізовані;
Пристосування - універсальні, стандартні, нормалізовані, спеціалізоване;
Різальні інструмент - стандартні, нормалізовані, спеціальні;
Засоби контролю - універсальні, спеціальні;
5. В області проектування технологічних операцій:
Зміст операцій - одночасна обробка декількох поверхонь виходячи з можливостей устаткування;
Завантаження встаткування - періодична зміна деталі на верстатах, коефіцієнт закріплення операцій від 10 до 20;
Розміщення встаткування - по групах верстатів, предметно замкнуті ділянки;
Настроювання верстатів - по вимірювальних інструментах і приладам або робота без попереднього настроювання по промірах.
6. В області нормування технологічного процесу:
Визначення режимів різання - по запропастити нормативам і емпіричним формулам;
Нормування – детальне;
Кваліфікація робітників - середня;
Технологічна документація - маршрутно-операційні карти.
Прийнятою стратегією будемо керуватися при розробці технологічного процесу виготовлення кришки, розділи 3-6.
2.3
Вибір і проектування заготівлі
Завдання даного підрозділу - вибрати методи одержання заготівлі й обробки поверхонь, що забезпечують мінімум сумарних витрат на одержання заготівлі і її обробку.
2.3.1 Вибір методу одержання заготівлі
З огляду на конструкцію виготовляється крив, що, і матеріал заготівлі - сталь 45Л ДЕРЖСТАНДАРТ 977-75, можна запропонувати два основних альтернативних методи одержання заготівлі:
1. Лиття в земляні форми;
2. Зварена конструкція.
1. Лиття в земляні форми
По таблиці 9 додаток 1 ДЕРЖСТАНДАРТ 26645-85 при обраному методі лиття й найбільшому габаритному розмірі виливка в діапазоні від 100 до 250 визначаємо клас розмірної точності виливка в діапазоні 8-13т. З огляду на, що даний виливок ставиться до виливків середньої складності й умовам механізованого серійного виробництва, приймаємо 10 клас розмірної точності виливка.
По таблиці 10 додаток 2 ДЕРЖСТАНДАРТ 26645-85 при відношенні найменшого розміру елемента виливка до найбільшого 0,5 визначаємо ступінь жолоблення елементів виливків у діапазоні 3-6. Остаточно для виливка зі сталі приймаємо 5-у ступінь жолоблення.
По таблиці 11 додаток 3 ДЕРЖСТАНДАРТ 26645-85 при обраному методі лиття й найбільшому габаритному розмірі виливка в діапазоні від 100 до 250 визначаємо ступінь точності поверхонь виливків у діапазоні 10-17. З огляду на, що даний виливок ставиться до виливків середньої складності й умовам механізованого серійного виробництва, приймаємо 12 ступінь точності поверхонь виливка.
По таблиці 12 додаток 4 ДЕРЖСТАНДАРТ 26645-85 визначаємо значення шорсткості поверхонь виливків залежно від ступеня точності поверхонь виливка. Ступінь точності поверхонь виливка-12 відповідає значенню шорсткості поверхонь виливка Ra не більше 25 напівтемний.
По таблиці 13 додаток 5 ДЕРЖСТАНДАРТ 26645-85 при обраному методі лиття й найбільшому габаритному розмірі виливка в діапазоні від 100 до 250 визначаємо клас точності маси виливка в діапазоні 7т-14. З огляду на, що даний виливок ставиться до виливків середньої складності й умовам механізованого серійного виробництва, приймаємо 10 клас точності маси виливка. По таблиці 14 додаток 6 ДЕРЖСТАНДАРТ 26645-85 залежно від ступеня точності поверхні виливка визначаємо ряд припусків на обробку виливка в діапазоні 5-8, остаточно приймаємо 5 ряд припусків на обробку виливка. По таблиці 6 ДЕРЖСТАНДАРТ 26645-85 залежно від виду остаточної обробки поверхні, загального допуску елемента поверхні й ряду припуску виливків призначаємо припуск на сторону для кожної з оброблюваних поверхонь виливка. Допуски розмірів виливків призначаємо по таблиці 1 ДЕРЖСТАНДАРТ 26645-85 залежно від класу точності виливка. Далі зробимо розрахунок розмірів заготівлі й зведемо його результати в таблицю 2.1
Таблиця 2.1Допуски й припуски на розміри виливка
Розмір
деталі, мм
|
Поверхн.,
на які призначається припуск
|
Допуск
на розмір
виливка, мм
|
Припуск,
мм
|
Розрахунок розміру відливки |
Розмір |
Æ150 |
12 |
3,2 |
4,6 |
Æ150- (2× 4,6) |
Æ140,8±1,6 |
Æ40 |
13 |
2,2 |
3,4 |
Æ40- (2× 3,4) |
Æ33,2±1,1 |
30 |
5,6 |
2,2 |
3,2 |
30+3,2+2,4 |
35,6±1,1 |
6 |
1 |
1,6 |
2,4 |
6+2,4 |
8,4±0,8 |
15 |
4 |
1,8 |
2,7 |
15+2,7 |
17,7±0,9 |
Æ108 |
7 |
3,2 |
- |
- |
Æ108±1,6 |
Æ162 |
8 |
3,6 |
- |
- |
Æ162±1,8 |
Æ120 |
14 |
3,2 |
- |
- |
Æ120±1,6 |
Æ110 |
15 |
3,2 |
- |
- |
Æ110±1,6 |
Æ50 |
16 |
2,4 |
- |
- |
Æ50±1,2 |
Æ180 |
9 |
3,6 |
- |
- |
Æ180±1,6 |
18 |
2 |
1,8 |
- |
18+2,4 |
20,4±0,9 |
95 |
1,4 |
2,8 |
- |
95+2,4+2,7 |
100,1±1,4 |
Інші вимоги за ДСТ 26645-85 |
Ливарні радіуси закруглень приймаємо 2 мм, ухили 2? за ДСТ 26645-85. Точність виливка одержуваної литтям у земляні форми 10-5-12-10.
Для проведення надалі техніко-економічного обґрунтування вибору заготівлі необхідно визначити коефіцієнт використання матеріалу для даного методу лиття.
Коефіцієнт використання матеріалу визначимо по формулі:
Ки1
=q/Q (2.2)
де q - маса деталі, q = 9,8 кг (див. п.2.1 1);
Q - маса заготівлі
Обсяг заготівлі визначаємо як алгебраїчну суму обсягів тіл за винятком порожніх циліндричних сегментів, що входять у конфігурацію заготівлі:

Знаючи обсяг деталі й щільність матеріалу, визначаємо масу заготівлі:

Підставивши отримані значення мас деталі й заготівлі у формулу 2.2., одержимо коефіцієнт використання матеріалу для лиття в земляні форми: Ки1
=12,8/9,8=0,76.
Зварена конструкція.
Схема комбінованої звареної конструкції заготівлі, представлена на мал.2.1., є не чим іншим як сукупністю декількох окремих заготівель, отриманих різними методами й з'єднаних між собою по засобом зварювання. Зварена конструкція складається з: фланця 1 (лиття), труби 2 (прокат), фланця 3.

Мал.2.1Схема комбінованої звареної конструкції
Коефіцієнт використання матеріалу для конструкцій Ки2
становить 0,85 (згідно рекомендацій [6]). Звідси по формулі (2.2) визначаємо масу заготівлі: Q =q/ Ки2
=9.8/0.85=11.53 кг.
Таким чином, коефіцієнт використання матеріалу у заготівлі трохи вище, ніж виливка отриманої литтям у земляні форми. Однак, для остаточного рішення на вибір методу одержання заготівлі, варто провести порівняльний економічний аналіз по технологічній собівартості.
2.3.2 Економічне обґрунтування вибору методу одержання заготівлі
Оцінку ефективності різних варіантів одержання заготівель найчастіше проводять по двох показниках [6]:
а) коефіцієнту використання матеріалу заготівлі (див. формулу 2.2)
б) технологічної собівартості виготовлення деталі. Сюди включаються тільки ті статті витрат, величини яких змінюються при переході одного варіанта до іншого.
На стадії проектування технологічних процесів оптимальний варіант заготівлі, якщо відомі маси заготівлі й деталі, можна визначити шляхом порівняння технологічної собівартості виготовлення деталі, розрахованої по формулі:
Ст
= Сзаг
·Q + Сміх (Q-q) - Сотх
(Q-q) (2.3)
де Сзаг
- вартість одного кг. заготівлі, грн./кг;
Сміх - вартість механічної обробки, віднесена до одному кг. стружки, що зрізується, грн./кг;
Сотх
- ціна 1 кг. відходів, грн./кг, Сотх
= 0,0144 грн./кг;
Сміх = Сс
+ Ен
·Ск
(2.4)
де Сс
- поточні витрати на 1 кг. стружки, грн./кг;
Ск
- капітальні витрати на 1 кг. стружки, грн./кг;
По табл.3.2 [3] для автомобільного й сільськогосподарського машинобудування Сс
= 0,188 грн./кг, Ск
= 0,566 грн./кг.
Ен
- нормативний коефіцієнт ефективності капітальних вкладень, Ен
= 0,15.
Сміх = 0,188 + 0,15·0,566 = 0,273 грн./кг.
Це значення приймаємо для лиття в земляні форми.
Вартість заготівлі, отриманої такими методом, як лиття в земляні форми, з достатньої для стадії проектування точністю можна визначити по формулі:
Сзаг
= Стільник× kт
× kc
× kв
× kм
× kп
, (2.5)
де Стільник -
базова вартість одного кг виливка, отриманої литтям, грн..:
для лиття в земляні форми Стільник = 0,29 грн.;
kт
- коефіцієнт, що залежить від класу точності, для виливків із чорних металів другого класу точності:
для лиття в земляні форми kт
= 1,03;
kc
- коефіцієнт, що залежить від групи складності виливка, для 4групи складності:
для лиття в земляні форми kc
=1,2;
kв
- коефіцієнт, що залежить від марки матеріалу й маси виливка, для чавуну при масі виливка більше 3 кг відповідно:
для лиття в земляні форми kв
=0,93;
kм
- коефіцієнт, що залежить від марки матеріалу виливка, для чавуну:
для лиття в земляні форми kм
= 1,21
kп
- коефіцієнт, що залежить від марки матеріалу виливка й групи серійності:
для лиття в земляні форми kп
= 0,77;
Підставимо певні значення у формулу (2.5):
Сзаг1
= 0,29×1,03×1,2×0,93×1,21×0,77= 0,31 грн..;
Підставимо отримані дані у формулу (2.3) і розрахуємо технологічну собівартість виготовлення деталі, для даного методу одержання заготівлі: для лиття в земляні форми:
Стд1
= 0,31×12,8+ 0,273 × (12,8-9,8) - 0,0144× (12,8-9,8) = 4,744 грн..;
Собівартість заготівлі визначимо, як суму собівартості її частин:
Труба (поз.2) - прокат
Сзаг
=Спр
* kт (
2.6)
де kт
- коефіцієнт, що враховує форму металопрокату
Спр
- вартість металу, Спр
=3,7 грн./кг [6]
Підставимо отримані дані у формулу (2.6), одержимо:
Сзаг
=3.7* 1.06=3.922 грн./кг;
Для литих фланців (поз.1,2) технологічна собівартість розраховується по формулі (2.3), використовуючи рекомендації [6], аналогічно технологічної собівартості вище описаному методу лиття.
Сзаг1
=0,29*1,03*1,21*1,2*0,93*0,77=0,31 грн..
Сзаг3
=0,29*1,03*1,21*0,83*0,93*0,77=0,21 грн..
Звідси: СзагО
=3,922+0,31+0,21=4,447 грн..
Підставимо отримані дані у формулу (2.3) і розрахуємо технологічну собівартість виготовлення деталі, для даного методу одержання заготівлі:
Стд1
=4,447×12,8+ 0,273 × (12,8-9,8) - 0,0144× (12,8-9,8) = 58 грн.
Вивід: за результатами проведення порівняльного аналізу технологічної собівартості двох методів одержання заготівлі можна укласти, що економічно доцільніше використовувати при одержанні заготівлі деталі метод лиття в земляні форми, повна собівартість одержання заготівлі цим методом істотно нижче чим одержання заготівлі у вигляді звареної конструкції.
Економічний ефект при виготовленні деталі із заготівлі отриманої литтям у земляні форми для річної програми випуску-15000 шт. складе:
Е= (Стд2 -
Стд1
) ·N= (58-4,744) ·15000=798840 грн..
3.
Технологічний маршрут і план виготовлення деталі
3.1
Обґрунтування технологічного маршруту виготовлення деталі
План виготовлення деталі.
Завдання роздягнуло - розробити оптимальний технологічний маршрут, тобто таку послідовність операцій, що забезпечить одержання із заготівлі готової деталі з найменшими витратами, при цьому необхідно розробити таку схему базування заготівлі на кожній операції, що забезпечила б мінімальну погрішність обробки.
Тип виробництва - середнє серійне;
Спосіб одержання вихідної заготівлі - лиття в земляні форми;
Метод досягнення точності - по настроєному встаткуванню.
На малюнку 1.1 представлена схема кодування деталі, тобто зображений ескіз деталі із пронумерованими поверхнями й літерними позначеннями креслярських розмірів.
Технологічний маршрут, обраний у відповідності рекомендаціям [7] представлений у таблиці 3.1:
Таблиця 3.1Технологічний маршрут виготовлення деталі
№ операції |
Найменування операції |
Устаткування
(тип, модель)
|
Зміст операції |
(IT) |
Ra,
мкм
|
000 |
Заготівельна |
_______ |
Лиття в земляні форми |
16 |
25 |
010
|
Токарська
|
Токарно-гвинторізний верстат 1А616 |
перехід 1: |
12
|
12,5 |
перехід 2: підрізати торець 4,6,5; |
020
|
Токарська
|
Токарно-гвинторізний верстат 1А616 |
перехід 1: |
12
|
12,5
|
перехід 2: підрізати торці пов.1; |
030
|
Токарська
|
Токарно-гвинторізний верстат 16Б16П
|
перехід 1: точити циліндричну пов.12; фаску 2×30º. |
9
|
2,5
6,3
|
перехід 2: підрізати торці 4,5,6 |
перехід 3: точити канавку пов.18, 19 |
040
|
Токарська
|
Токарно-гвинторізний верстат 16Б16П
|
перехід 1: точити циліндричну пов.13; фаски 2×45º. |
9
|
2,5
|
перехід 2: підрізати торець 1 |
перехід 3: точити канавку пов. 20,21,22 |
- |
2,5 |
050 |
Свердлильна
|
Вертикально-свердлильний верстат зі ЧПУ 2Р135Ф2
|
перехід 1: засвердлити |
- |
- |
перехід 2:
свердлити 3 отв. пов.10
|
12 |
12,5 |
перехід 3:
зенкеровать 3 отв.10
|
9 |
6,3 |
перехід 4:
розгорнути 3 отв.10
|
7 |
2,5 |
перехід 5:
свердлити 3 отв.11
|
12 |
12,5 |
перехід 6:
нарізати різьблення отв.11
|
7 ст. |
2,5 |
060 |
Термічна (загартування, відпустка до твердості НВ 215±2) |
070 |
Очисна (очистити поверхня від окалини) |
080 |
Контрольна (контролювати твердість) |
090 |
Внутрішліфувальна |
Внутрішліфувальний верстат 3К227Б |
шліфувати пов.12 |
7 |
0,8 |
100 |
Внутрішліфувальна |
Внутрішліфувальний верстат 3К227Б |
шліфувати пов.13 |
7 |
0,8 |
110 |
Хромування |
(покриття пов. Г, Д Хтв 70) |
120 |
Хонинговання |
Вертикально хонинговальний верстат 3К84 |
хонинговать отв. (пов.12) у розмір до
Ra 0.32
|
сохр. |
0,32 |
130 |
Хонингованн |
Вертикально хонинговальний верстат 3К84 |
хонинговать отв. (пов.12) у розмір до
Ra 0.32
|
сохр. |
0,32 |
140 |
Мийна |
150 |
Контрольна |
План виготовлення деталі.
План виготовлення - графічне зображення технологічного маршруту із вказівкою теоретичних схем базування й технічних вимог на операції.
План виготовлення складається із чотирьох граф:
Графа "Операція", що містить у собі назва й номер операції.
Графа “ Устаткування", що містить у собі встаткування, за допомогою якого виробляється обробка поверхонь на даній операції.
Графа "Теоретична схема базування", що містить у собі зображення деталі, схему базування (крапки закріплення), самоскидальний операційних розмірів, позначення оброблюваних поверхонь і вказівка шорсткості одержуваної на даній операції.
Графа “Технічні вимоги", що містить у собі допуски на операційні розміри й відхилення форми.
План виготовлення корпуса гідроциліндра представлений на аркуші графічної частини.
3.2
Вибір технологічних баз
Теоретична схема базування представлена на плані виготовлення деталі і являє собою схему розташування на технологічних базах заготівлі "ідеальних" крапок, що символізують позиційні зв'язки заготівлі із прийнятою схемою координат верстатного пристосування.
При розробці схем базування враховуємо принцип сталості й сполучення баз, тобто для найбільшої точності виготовлення деталі, на всіх операціях обробки по можливості використовувати ту саму базу, як настановну, так і вимірювальну. Так само важливо враховувати правило шести крапок, при якому деталь базується на шести нерухливих крапках, які позбавляють її шести ступенів волі. Обробку деталі починаємо з поверхні, що служить настановною базою для подальших операцій. Для обробки цієї поверхні як настановна база доводиться приймати неопрацьовану поверхню. Після цього, коли оброблена настановна поверхня, обробляємо інші поверхні, дотримуючи при цьому певну послідовність, спочатку обробляємо поверхню, до точності якої пред'являються менші вимоги, а потім поверхні, які повинні бути більше точними.
Індекс біля номера поверхні позначає номер операції, на якій вона отримана. Індекс 00 - ставиться до заготівельної операції, букви А, Б - указують, що поверхня оброблена на даній операції з установа А або Б. Арабські цифри 1,2,3 і т.д. позначають перехід на якому був отриманий даний розмір.
У зв'язку з тим, що корпус являє собою тіло обертання, те спочатку заготівля обробляється на верстатах токарської групи.
На 010 токарській операції в якості чорнових технологічних баз використовуємо технологічні бази зазначені на кресленні заготівлі (див. чорт) і є циліндрична поверхня 13 і торцева поверхня 1. Вісь матеріалізуємо внутрішніми циліндричними поверхнями.
На 020, 040 токарських операціях у якості подвійної опорної бази використовуємо вісь поверхні 12, як настановна база торець 4. Як опорна база приймаємо пов.12.
На 030 токарської операціях у якості подвійної опорної бази використовуємо вісь поверхні 13, як настановна база торець 1. Як опорна база приймаємо пов.13.
На 050 свердлильній операції в якості подвійної опорної бази використовуємо вісь поверхні 8, як настановна база торець 1. Як опорна база приймаємо пов.8.
На 090 і 100 шліфувальних операціях у якості подвійної опорної бази використовуємо вісь поверхонь 12 (операція 100),13 (операція 090); як настановна база торець 1 (операція 090), 4 (операція 100); як опорна база приймаємо пов.12,13 відповідно.
На 110 операції виробляється хромування внутрішніх поверхонь корпуса (пов.12, 13). Докладний опис обраного методу й технології хромування наведено в розділі 5 даного дипломного проекту.
На 120 і 130 хонинговальних операціях як настановна база використовуємо торець 1; як опорна база приймаємо пов.12, 13 відповідно.
Зведемо всі дані по технологічних базах і розмірам, одержуваним на операціях ТП у таблицю 3.2
Таблиця 3.2Технологічні бази
№ операції |
Назва |
№ опорних крапок |
Характер появи |
Реалізація |
Операційні розміри |
Єдність баз |
Явна |
Скрита |
Природна |
Штучна |
1 |
2 |
3 |
4 |
5 |
6 |
7 |
8 |
9 |
010
|
У
К
О
|
1,2,3
4,5
6
|
+
+
|
-
+
|
+
+
+
|
-
|
2И20
Т20
П20
|
+
+
|
020
|
У
К
О
|
1,2,3
4,5
6
|
+
+
|
-
+
|
+
+
+
|
-
|
2Б10
Т10
|
+
+
+
|
030
|
У
К
О
|
1,2,3
4,5
6
|
+
+
|
-
+
|
+
+
+
|
-
|
2И40
, 2ИК40
Т40
, П40
, В40
,
Ю40
|
+
|
040 |
У
К
О
|
1,2,3
4,5
6
|
+
+
|
-
+
|
+
+
+
|
-
|
2Б30
,2L30
Т30
, П30
, G30
Ч30
|
+
|
050 |
У
К
О
|
1,2,3
4,5
6
|
+
+
|
-
+
|
+
+
+
|
-
|
2Н50
,2М50
,2К50
W50
, МХ50
|
+
|
090 |
У
К
О
|
1,2,3
4,5
6
|
+
+
|
-
+
|
+
+
+
|
-
|
2И90
|
+
|
100 |
У
К
О
|
1,2,3
4,5
6
|
+
+
|
-
+
|
+
+
+
|
-
|
2Б100
|
+ |
120 |
У
К
О
|
1,2,3
4,5
6
|
+
+
|
-
+
|
+
+
+
|
-
|
2И120
|
+ |
130 |
У
К
О
|
1,2,3
4,5
6
|
+
+
|
-
+
|
+
+
+
|
-
|
2Б130
|
+ |
3.3
Обґрунтування самоскидального операційних розмірів
Спосіб операційних розмірів вибираємо залежно від методу досягнення точності. Для виконання вище розглянутих операцій застосовуємо метод досягнення точності розмірів за допомогою настроєного встаткування. У цьому випадку має місце кілька варіантів операційних розмірів, одержання яких залежить від технологічних можливостей застосовуваного встаткування. Тому що при розробці технологічного процесу виготовлення деталі використовувалося стандартне й універсальне встаткування, то було б доцільно застосувати координатний спосіб операційних розмірів.
3.4
Призначення операційних технічних вимог
1. Заготівельна операція: всі вимоги, пропоновані до виливка по якості й точності призначаємо відповідно до рекомендацій ДЕРЖСТАНДАРТ 25545-85 (див. п.2.2).
2. Допуски на операційні розміри в осьовому напрямку розраховуємо по наступних формулах:
для операції 010 - токарської:
TAi
= wi
cт
+ с. м., (3.1)
де TAi
- допуск на розмір А на i-тій операції;
wi
cт
- статистична погрішність на i-тій операції;
с. м. - зсув форми й стрижня, що виникає на заготівельній операції;
для операції 020 - токарської;
для операції 030,040 - токарської:
TAi
= wi
cт
+ Üi
, (3.2)
де TAi
- допуск на розмір А на i-ой операції;
wi
cт
- статистична погрішність на i-тій операції;
Üi
- величина торцевого биття, обумовлена по .2 [4].
3. Допуски на діаметральні розміри призначаються, виходячи із квалітету точності, що забезпечує встаткування в радіальному напрямку. Його вибираємо по .1 [2], значення допусків беруться з [8].
4. Значення погрішностей форми на діаметральні розміри призначаємо, керуючись .2 [4]. Величина відхилення від співвісності визначається як половина погрішності радіального биття.
Шорсткість, одержувану при обробці поверхонь, призначаємо з урахуванням рекомендацій (1 [4]).
3.5
Розрахунок припусків на обробку й проектування заготівлі
На саму точну поверхню визначимо припуски розрахунково-аналітичним методом, розробленим В.М. Кутому. Відповідно до цього методу величина мінімального припуску повинна бути такий, щоб при його знятті усувалися погрішності обробки й дефекти поверхневого шару, отримані на попередніх технологічних переходах, а також погрішність установки заготівлі, що виникає на виконуваному переході. На інші поверхні припуски призначаємо табличним способом по [9].
Розрахунок операційних припусків і розмірів виконаємо на діаметр 2Б (поверхня 13). У таблицю 3.3 внесемо всі дані по технологічних переходах на обробку пов.13, а також розраховані припуски.
Визначимо значення мінімального припуску після кожної операції по формулі:
, (3.3)
де Rz
i-1
, h i-1, мм - висота нерівностей і дефектний шар, що утворилися на оброблюваній поверхні при попередній обробці;
Di-1, мм - сумарне значення просторових відхилень;
eуi
, мм - погрішність установки.
Сумарне значення просторових відхилень визначимо по формулі:
(3.4)
де Dк. о.
-загальна кривизна заготівлі (ураховується на першій операції механічної обробки);
Dсм
- величина зсуву заготівлі, т.до обробка ведеться в патроні за ве-личину зсуву приймаємо відхилення від співвісності.
Загальна кривизна заготівлі:
(3.5)
де Dдо
- питома зігнутість і жолоблення заготівлі, напівтемних/мм;
l - ширина заготівлі, мм.

 
 
Погрішність установки для однопозиційної обробки:
(3.6)
де eб
- погрішність базування;
eз
- погрішність закріплення.
Тому що при обробці діаметра вимірювальні й технологічні бази збігаються, погрішність базування eб
= 0 при всіх установках заготівлі.
   
Отримані значення елементів припуску внесемо в графи 2,3,4 табл.4.3




Розраховані припуски запишемо в графі 7 табл.4.3
Визначимо розрахункові розміри для кожної операції. Для діаметра Æ40Н7: D6min
= 40 мм, D6max
= 40,025 мм.
Розрахунковий діаметр дорівнює:
(3.7)
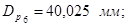




Таблиця 3.3Припуски й операційні розміри на пов.13 O 40Н7
Технолог.
переходи
|
Елементи припуску, напівтемних |
Розрахунковий припуск
2Zmin
, мм
|
Допуск
TD, мм
|
Граничні розміри
заготівлі, мм
|
Rz |
h |
DS
|
eу
|
2Zmax
|
2Zmin
|
2Zср
|
Dmax
|
Dmin
|
Dср
|
1 |
2 |
3 |
4 |
5 |
6 |
7 |
8 |
9 |
10 |
11 |
12 |
1. Виливок |
100 |
200 |
1000 |
- |
- |
- |
- |
2,2 |
36,7 |
34,5 |
35,6 |
2. Токарська (розточування отв). |
50 |
60 |
43,5 |
110 |
4,649 |
2,699 |
3,674 |
0,25 |
39,44 |
39, 19 |
39,315 |
3. Токарська чистий(розточування отв). |
10 |
15 |
26,5 |
90 |
0,608 |
0,420 |
0,514 |
0,062 |
39,859 |
39,797 |
39,828 |
4. Шліфування |
3,2 |
10 |
7 |
5 |
0,161 |
0,124 |
0,142 |
0,025 |
39,983 |
39,958 |
39,941 |
5. Хромування |
Хтв 70 |
- |
- |
- |
- |
- |
- |
- |
6. Хонинговання |
1,28 |
4 |
- |
3 |
0,042 |
0,042 |
0,042 |
0,25 |
40,025 |
40 |
40,0125 |
Разом |
2Z0
min
=3,285 2Z0
max
=5,46 |
Dном
= Dmin дет
-2Z0
max
+ EIзаг
=
=40-5,46+1,1=35,64 мм
|
Вихідний розмір отвору в заготівлі O 35.64±1.1
Допуски, узяті із плану виготовлення, заносимо в графу 9 табл.3.3
Найбільші граничні розміри одержуємо по розрахункових розмірах, округленим до точності допуску відповідного переходу:
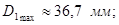 
  
Найменші граничні розміри:
(3.8)




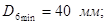
Отримані значення заносимо в графу 10,11 табл.3.3
Визначимо максимальні значення припусків по формулі:
(3.9)




Отримані значення заносимо в графу 6 табл.3.3
Загальний номінальний припуск:
(3.10)
де Zо min
- загальний мінімальний припуск; Zо min
=3,285 мм;
Вз
- верхнє відхилення поля допуску розміру на заготівлі, Вз
= 1,1 мм;
Вд
- верхнє відхилення поля допуску розміру на деталі, Вд
= 0,025 мм;

Перевіримо правильність виконання розрахунків:
 
 
 
 
Всі розрахунки виконані, вірно, у завершення побудуємо схему розташування припусків і операційних розмірів для оброблюваного отвору Æ40+0,025 (
мал.3.1).
На всі інші поверхні припуски були визначені табличним способом, з огляду на рекомендації [5] (див. п.2.2 даного дипломного проекту).
Схема розташування припусків і операційних розмірів на обробку отвору Æ40+0,025
Мал..3.1
4.
Вибір засобів технологічного оснащення (СТО)
Завдання роздягнуло - вибрати для кожної операції ТП такі встаткування, пристосування, різальний інструмент (РИ) і засобу контролю, які б забезпечили заданий випуск деталей заданої якості з мінімальними витратами.
4.1
Вибір устаткування
При виборі типу й моделі металорізальних верстатів будемо керуватися наступними правилами:
1. Продуктивність, точність, габарити, потужність верстата повинні бути мінімальними, але достатніми для того, щоб забезпечити виконання вимог пропонованих до операції.
2. Верстат повинен забезпечити максимальну концентрацію переходів на операції з метою зменшення числа операцій, кількості встаткування, підвищення продуктивності й точності за рахунок зменшення числа перестановок заготівлі.
3. У випадку недостатнього завантаження верстата його технічні характеристики, повинні дозволяти обробляти інші деталі, що випускаються даним цехом або ділянкою.
4. Устаткування не повинне бути дефіцитним, але в достатньому ступені модернізованим
5. У серійному виробництві поряд з верстатами зі ЧПУ й обробними центрами варто застосовувати спеціалізовані верстати, гнучкі технологічні модулі, гнучкі автоматичні лінії. На кожному верстаті на місяць повинне виконуватися не більше 40 операцій при зміні деталей по певній закономірності.
6. Устаткування повинне відповідати вимогам безпеки, ергономічності й екології.
Вибір устаткування проводимо, використовуючи рекомендації [9] у наступній послідовності:
1. Виходячи з форми оброблюваної поверхні й методу обробки, вибираємо групу верстатів;
2. Виходячи з положення оброблюваних поверхонь, вибираємо тип верстата;
3. Виходячи з габаритних розмірів заготівлі, розмірів оброблюваних поверхонь і точності обробки вибираємо типорозмір верстата.
Дані на вибір устаткування заносимо в таблицю 4.1
Таблиця 4.1Вибір устаткування
Номер операції |
Верстат |
найбільши габарити заготівлі мм |
Потужність головного
Приводаквт
|
Частота обертання шпинделя об./хв |
Габарити верстата, мм |
Маса, т |
1 |
2 |
3 |
4 |
5 |
6 |
7 |
010
020
|
Токарно-гвинторізний
верстат 1А616
|
320×710 |
6,0 |
9-1800 |
2135×1225×1220 |
1,5 |
030
040
|
Токарно-гвинторізний верстат16Б16П |
460×250 |
8,0 |
20-2000 |
2235×1060×1450 |
2,1 |
050 |
Вертикально-свердлильний 2Р135Ф2 |
400×710 |
3,7 |
45-2000 |
1800×2170×2700 |
4,7 |
060 |
Термічна |
090
100
|
верстат
3К227Б
|
100?100
|
4,0/11,8 |
320-800 (деталі)
9000-24000
(шл. кола)
|
2815×1900×1750 |
4,5 |
110 |
Хромування |
120
130
|
верстат 3К84 |
200***
(50-800) **
|
13 |
63-400 |
2320×2650×4170 |
4,85
(6,2) *
|
140 |
Мийна |
Мийна машина |
* Вага
** Хід шпинделя (min/max)
*** Найбільший діаметр хонинговання
4.2
Вибір пристосувань
При виборі пристосувань будемо керуватися наступними правилами:
1. Пристосування повинне забезпечувати матеріалізацію теоретичної схеми базування на кожній операції за допомогою опорних і настановних елементів
2. Пристосування повинне забезпечувати надійне закріплення заготівлі при обробці й повинне бути швидкодіючим
3. Затискач заготівлі повинен здійснюватися по можливості автоматично
4. Варто віддавати перевагу стандартним нормалізованим, універсально-збірням пристосуванням, і тільки при їхній відсутності проектувати спеціальні пристосування
Виходячи з типу, моделі верстата й методу обробки вибираємо тип пристосування.
Вибір пристосування, використовуючи рекомендації [10] будемо робити в наступному порядку:
1. Виходячи з розташування базових поверхонь і їхнього стану (точність і шорсткість), форми заготівлі й розташування оброблюваних поверхонь вибираємо конструкцію пристосування
2. Виходячи з габаритів заготівлі й розмірів базових поверхонь, вибираємо типорозмір пристосування.
Дані на вибір пристосувань заносимо в таблицю 4.2
Таблиця 4.2Вибір пристосувань
Номер операції |
Найменування операції |
Пристосування |
1 |
2 |
3 |
010 |
Токарська чорнова |
Оправлення цангова 7112-1509 ДЕРЖСТАНДАРТ 12593-93 |
020 |
Токарська чорнова |
Патрон 3-х кулачковий клиновий ДЕРЖСТАНДАРТ 24351-80 |
030 |
Токарська чистова |
Оправлення з розрізними цангами 7112-1496 ДЕРЖСТАНДАРТ 31.1066.02-85 |
040 |
Токарська чистова |
Патрон 3-х кулачковий клиновий ДЕРЖСТАНДАРТ 24351-80 |
050 |
Свердлильна зі ЧПУ |
Пристосування спеціальне |
090
100
|
Внутрішліфувальна |
Патрон мембранний ДЕРЖСТАНДАРТ 16157-70 |
120
130
|
Хонинговальна |
Пристосування спеціальне
Патрон для кріплення твердих хонинговальних головок;
Головка хонинговальна тверда;
Головка хонинговальна для обробки глухих отворів;
|
Після вибору пристосувань одержали наступне:
1. Пристосування забезпечують матеріалізацію теоретичної схеми базування на кожній операції.
2. Пристосування забезпечують надійне закріплення заготівлі при обробці, пристосування - швидкодіючі
4.3 Вибір різального інструменту
При виборі різального інструменту будемо керуватися наступними правилами:
1. Вибір інструментального матеріалу визначається вимогами, з однієї сторони максимальної стійкості, а з іншої мінімальної вартості.
2. Варто віддавати перевагу нормалізованим і стандартним інструментам.
Вибір різального інструменту будемо робити в наступному порядку:
1. Виходячи з типу й моделі верстата, розташування оброблюваних поверхонь і методу обробки, визначаємо вид різального інструменту
2. Виходячи з марки оброблюваного матеріалу його стану й стани поверхні, вибираємо марку інструментального матеріалу
3. Виходячи з форми оброблюваної поверхні, призначаємо геометричні параметри ріжучої частини інструмент4. Виходячи з розмірів оброблюваної поверхні, вибираємо конструкцію інструмента
Дані на вибір різального інструменту заносимо в таблицю 4.3
Таблиця 4.3Вибір різального інструменту
№ |
Найменування операції |
ЇМ |
Різальний інструмент |
1 |
2 |
3 |
5 |
10
|
Токарська чорнова |
Т5К10 |
Різець розточувальної цільної зі сталевим хвостовиком для глухих отворів ДЕРЖСТАНДАРТ 18063-72 |
Різець прохідний упорний відігнутий з кутом у плані 90º с пластинами із твердого сплаву ДЕРЖСТАНДАРТ 18879-73 |
Різець розточувальної з кутом у плані 90º с пластинами із твердого сплаву за ДСТ 10044-73 |
020
|
Токарська чорнова |
Т5К10 |
Різець розточувальної з кутом у плані 60º с пластинами із твердого сплаву за ДСТ 18882-73 |
Т5К10 |
Різець прохідний упорний відігнутий з кутом у плані 90º с пластинами із твердого сплаву ДЕРЖСТАНДАРТ 18879-73 |
030 |
Токарська |
Т15К6 |
Різець розточувальної цільної зі сталевим хвостовиком для глухих отворів ДЕРЖСТАНДАРТ 18063-72 |
Різець прохідний упорний відігнутий з кутом у плані 93º с пластинами із твердого сплаву ДЕРЖСТАНДАРТ 18879-73 |
Різець розточувальної з кутом у плані 90º с пластинами із твердого сплаву за ДСТ 10044-73 |
Різець вставка канавковий спеціальний |
040 |
Токарська |
Т15К6 |
Різець розточувальної з кутом у плані 60º с пластинами із твердого сплаву за ДСТ 18882-73 |
Різець прохідний упорний відігнутий з кутом у плані 93º с пластинами із твердого сплаву ДЕРЖСТАНДАРТ 18879-73 |
Різець вставка канавковий спеціальний К01-4112-000 |
050 |
Свердлильна |
Р6М5 |
Свердел спіральне центрувальне з конічним хвостовиком для зацентрування під свердління Ø4,5 ОСТ 2420-5-80 |
Р6М5 |
Свердел східчасте спіральне O4,5
ОСТ 2 И21-2-76
|
Т14К8 |
Зенкер цільної з конічним хвостовиком Ø5,5 ДЕРЖСТАНДАРТ 21544-76 |
Т5К6 |
Розгорнення машинна цільна Ø6 ДЕРЖСТАНДАРТ1672-80 |
Р6М5 |
Свердел східчасте під різьблення М8
ОСТ 2И21-2-76
|
Р18 |
Мітчик М8×1,5-7Н ДЕРЖСТАНДАРТ 3266-81 |
090
100
|
Внутришлифо-Вальна |
Коло шліфувальний ПП 30?35?10 2А16СМ28К5
Коло шліфувальний ПП 130?110?40 2А16СМ28К5
|
120
|
Хонинговальна |
Головка хонинговальна для обробки глухих отворів
Алмазні бруски:
1-АСР 63/ 100-МС2 ДЕРЖСТАНДАРТ16606-71
|
130 |
Хонинговальна |
Головка хонинговальна тверда
Алмазні бруски:
1-АСР - 63/ 100-МС2 ДЕРЖСТАНДАРТ16606-71
|
4.4
Вибір засобів контролю
При виборі засобів контролю будемо, використовуючи рекомендації [9,10] і керуватися наступними правилами:
1. Точність вимірювальних інструментів і пристосувань повинна бути істотно вище точності вимірюваного розміру, однак виправдане підвищення точності веде до різкого подорожчання.
2. Варто віддавати перевагу стандартним і нормалізованим засобам контролю.
Дані на вибір засобів контролю заносимо в таблицю 4.
Таблиця 4.4Вибір засобів контролю
Номер операції |
Найменування операції |
Засіб контролю |
1 |
2 |
3 |
010 |
Токарська чорнова |
Штангенциркуль ШЦ-III ДЕРЖСТАНДАРТ 166-80
Штангеглубиномер ШГ-160 ДЕРЖСТАНДАРТ162-80
|
020 |
Токарська чорнова |
Штангенциркуль ШЦ-III ДЕРЖСТАНДАРТ 166-80 |
030
040
|
Токарська |
Штангенциркуль ШЦ-III ДЕРЖСТАНДАРТ 166-80
Штангеглубиномер ШГ-160 ДЕРЖСТАНДАРТ162-80
Мікрометр МК-50 ДЕРЖСТАНДАРТ 6507-78
Калібр-пробка гладкий ДЕРЖСТАНДАРТ24853-81
|
050 |
Свердлильна зі ЧПУ |
Калібри-Пробки гладкі ГОСТ24853-81
Штангеглубиномер ШГ-160 ДЕРЖСТАНДАРТ162-80
Калібр - різьбовий ДЕРЖСТАНДАРТ24939-81
|
090
100
|
Внутрішліфувальна |
Калібри-Пробки гладкі ГОСТ24853-81
Датчик активного контролю БВ-4100
|
120
130
|
Хонинговальна |
Контроль отвору безконтактним пристроєм
Профілограф-Профілометр А1 ДЕРЖСТАНДАРТ19299-73
|
150 |
Контрольне |
Профілограф-Профілометр А1 ДЕРЖСТАНДАРТ19299-73,ППС-7, Биениемер Б-10М ТУ 2-034-216-85 |
5.
Технологія проведення операції хромування
Хромування використовують для збільшення зносостійкості, твердості, хімічній стійкості без тертя, забезпечення рідинного тертя, відновлення розмірів зношених деталей, а також для декоративних цілей. Опади хрому розрізняють по зовнішньому вигляді й по фізичних і механічних властивостях. Для поліпшення адгезії з металом і одержання хімічно стійких покриттів нарощування хромом часто здійснюється з підшарами з інших металів.
Хромування одержало саме широке поширення серед гальванічних покриттів. Причиною такого швидкого й широкого поширення є висока хімічна стійкість і зносостійкість електролітичного хрому. У процесі хромування не порушується структура металу виробу. Нанесений шар хрому має високу зносостійкість (при товщині покриття від10 до 400 напівтемних). Оброблена таким способом поверхня добре пручається корозії, впливу високих температур і органічних кислот. Таке покриття наноситься на сталь, чавун, мідь, латунь і інші метали. Нанесений хром має надійне зчеплення з основним металом деталі.
Хромування ведеться у двох напрямках:
захисно-декоративне;
При захисно-декоративному хромуванні виробу перед нанесенням хрому покриваються нікелем або міддю й нікелем. Товщина шару хрому при цьому досягає 0,1-0,2 напівтемний. Таким чином, хромують звичайно блискучі частини автомобілів, велосипедів, деталі всіляких приладів і ін. Хромування з метою підвищення зносостійкості деталі, на відміну від захистів - декоративного, виробляється безпосередньо на поверхні, товщина шару нанесеного хрому при цьому досягає 0.15-0.20 мм. Для підвищення опору утоми хромованих деталей застосовують високотемпературна відпустка й наклеп поверхні перед хромуванням.
Друга умовна група складається з тертьових деталей, що працюють при малих і середніх питомих тисках і окружних швидкостях, при постійному або змінному навантаженні. До таких деталей ставляться вали, плунжери циліндри, поршні, міряльний інструмент.
До деталей третьої групи можуть бути віднесені деталі, що працюють при більших питомих тисках і значних знакозмінних навантаженнях і потребуючій максимальній міцності зчеплення шару хрому з поверхнею деталей і в'язкості опадів хрому.
У машинобудуванні зносостійкому хромуванню піддаються не тільки деталі, що працюють в умовах динамічних навантажень (наприклад, в автомобільній промисловості: вісь шестірні, поршневі кільця двигунів, хрестовина кардана й ін.), але й деталі, що працюють без переміщення.
Хромуванню піддаються як мало навантажені, так і високо навантажені деталі, напруги в які циклічно змінюються протягом робочого процесу. При хромуванні спостерігається зниження опору утоми (до 22%), що пояснюється більшими напругами, що розтягують, виникаючими в шарі хрому при його формуванні в гальванічній ванні. Однак спуск хромованих виробів трохи поліпшує опір утоми. Якщо за умовами експлуатації деталі піддаються високим циклічним мінливим напругам, то необхідно враховувати, що при хромуванні їх також знижується опір утоми, міцність, обумовлена статичними навантаженнями, при хромуванні не змінюється. Міцність зчеплення хромового шару зі сталлю на відрив більше міцності хромового шару на розрив.
Якість хромового покриття в основному залежить від состава електроліту, щільності струму, температури й інтенсивності перемішування ванни. Змінюючи зазначені елементи технологічного процесу й час осадження, одержують покриття різної товщини з різними фізико-механічними властивостями й рівномірністю
ТОМУ ЩО КОРПУСУ ГІДРОЦИЛІНДРА ПРЕД'ЯВЛЯЮТЬСЯ ВИМОГИ ПІДВИЩЕНОЇ МІЦНОСТІ Й ВИСОКОГО ОПОРУ ЗНОШУВАННЯ, ТО ДОЦІЛЬНО ЗАСТОСУВАТИ ТВЕРДЕ ЗНОСОСТІЙКЕ ХРОМОВЕ ПОКРИТТЯ.
Зносостійкі хромові покриття наносяться для підвищення зносостійкості різних тертьових деталей, інструмента, покриття деталей штампів і т.д., для відновлення розмірів, зношених або бракованих деталей. До цього виду покриттів ставляться й так звані "тверді" хромові покриття. Але необхідно відзначити, що в цілому ряді випадків між твердістю й зносостійкістю хромових покриттів немає пропорційної залежності, тому що зносостійкість характеризується також в'язкістю й пластичністю покриття й залежить від умов припрацьовуваності, змащення й експлуатації хромованих деталей. Найбільш ефективне хромування при роботі деталей з питомими навантаженнями не більше 250-300 Мпа.
Зносостійкі й тверді хромові покриття можна безпосередньо осаджувати на більшість чорних і кольорових металів:
сталі (як загартовані, так і незагартовані);
сталі з малим змістом хрому й нікелю;
більшість кольорових металів і їхніх сплавів, на яких є товсті оксидні плівки.
Тверде зносостійке хромування варто проводити в стандартному універсально розведеному електроліті різної концентрації або в саморегулюючому.
Швидкість протоки електроліту підтримують у межах 1,50 м/с при щільності струму 200-2000 А/м2
і співвідношенні між цими величинами від 1: 200 до 1:40. При цьому вихід хрому по струму становить 45-60%, і більш ніж в 10 разів зростає швидкість осадження хромового покриття. Отримані по описаному способі опади хрому мають висока якість і твердість 1050-1150 HV.
Перед хромуванням виробу необхідно прогрівати безпосередньо у ванні для хромування, а потім протягом 0,5-1 хв при щільності струму 3500-4000 А/м2
. При хромуванні виробів складної форми треба на 1-2 хв збільшити щільність струму в 2 рази.
Технологічний процес хромування представлений у таблиці 5.1.
Таблиця 5.1. Технологічний процес хромування
Nº операції |
Nº переходу |
Найменування операції й переходу |
Найменування встаткуванні |
Матеріал ванни |
Компоненти |
Зміст г/л |
Температура, з |
Щільність тога, А/м |
Тривалість процесу, з |
Примітка
|
I |
Очищення, мийка
і дефекаціядеталей
|
Мийні
машини
|
Стльлистова |
Спеціальні
состави
|
8090 |
1030 |
Повне видалення жи рів, масел, окалини, а також очищення отворів і стінок.
Хромування дета лий із тріщинами недопускається.
|
II |
Механічнаобробка(шліфування,гостріння й т.п.) |
Шліфувальний
Іншіверстати
|
Виконується ввідповідності з
Технічнимиумовамимеханічнаобробка передметалопокриттями.
|
II |
Знежирення в органічних розчинниках |
ванна з
органічними розчинниками
|
Стальлистова |
Хладон,Состави,що знежирюють |
320 |
Після знежирення
деталі сушаться на повітрі або в струмені стисненого повітря.
|
IV |
1 |
Монтаж на
підвіску
|
Робітник
стіл, шафа з набором
підвісок
|
Місця деталей, не підлежачих хромированию, ретельноізолюють. Конструкція підвіски повиннавиключати (або допускати мінімальну) циркуляціюелектроліту біля місць, не підметівхромуванню |
2 |
Знежирення віденськоївапном абоїї замінниками |
Ванна длязнежирення,волосяні щітки |
Стальлистова |
Віденська
Вапноабо їїзамінники
|
Знежиреннявиробляєтьсящо знежирюєсоставом,розведенимводою до кашкоподібного стану |
3
|
Промивання
Холодноїпроточною водою
|
Ванна для
проточної води
|
Стальлистовас винипластовой облицюванням
|
1020 |
1520 |
Необхіднопромиватидеталі доповноговидалення слідівхімічного знежирення |
4 |
Знежирення електрохімічне |
Ванна
електрохімічного знежирення
|
Сталь
листова
кераміка
|
Їдкий натрій,
вуглекислий
натрій тринатрий фосфатРідкестекло йдр. состави
|
510
3050
3050
15
|
7080
|
310
|
5030
|
Деталь єкатодом. Передзакінченням об. цесса знежиреннянеобхідно перейти від катодної до анодної обробки дета лий протягом 12хв |
5 |
Промивання
гарячою водою
|
Ванна згарячоїводою |
те ж |
8090 |
2 |
1525 |
6 |
Промивання
холодною водою
|
Ванна зпроточноїводою |
Сталь листова з винипластовой облицюванням
|
1020 |
1520 |
V |
1 |
Хімічне травлення |
Ванна для хімічного травлення |
Вініпласт, кераміка, що не іржавіє
сталь,
гумоване
залізо
|
Сірчана кислота Соляна кислота |
50
50
|
1620 |
біля
30
30
|
2, 3 |
Промивання холодною водою у двох ваннах |
Ванни із проточною водою |
Сталь листова з винипластовой
облицюванням
|
1020 |
1525 |
VI |
1 |
Хромування |
Ванна
хромування
|
Сталь,
облицьована з вініпластом,
діабазовими
плитками
свинцем
або ін
кислотостойкими маті ріалами
|
Cr03
|
200
|
4555 |
20005500 |
9000 |
матеріал
анодів:
сплав свинецолово (Sn до 10%)
|
2 |
Промивання в
збірнику
електроліту
|
Збірник
електроліту
|
Сталь
листова
с винипластовой
облицюванням, кераміка
|
Вода
(краще
дистильована)
|
1620 |
1530 |
Рівень води в
ванні хромування
підтримується
постійним за рахунок води.
|
3 |
Промивання
холодної
проточною водою
|
Ванна з
проточною водою
|
Сталь
листова
|
1020 |
1525 |
До повного
видалення слідів
електроліту.
|
4 |
Зняття деталей
с підвіски
|
Робітник
стіл, шафа для підвісок
|
5 |
Нейтралізація |
Ванна для
нейтралізації
|
Сода
кальцинована
|
30 |
1620 |
3060 |
6 |
Промивання
холодною водою
проточної
|
Ванна з
проточною водою
|
Листова
сталь
|
1020 |
1520 |
До повного видалення
Хімікатів нейтралізуючого состава
|
7 |
Промивання
гарячою водою
|
Ванна з
гарячої
водою
|
Сталь
листова,
кераміка
|
8090 |
1525 |
До повного видалення
хімікатів з важко доступних місць підвісок і деталей
|
8 |
Термічна
обробка
|
Сушильна шафа або ванна з
маслом
|
Масло
"Вапор
|
150200 |
90120 |
Відповідно до технічних умов
(діючими) для різних матеріалів
|
9 |
Контроль
якості
покриття
|
Робочий стіл з
Набором інструментів і
приладів
|
Відповідно до технічних умов на контроль якості
покриттів після хромування
|
VII |
1 |
Механічна бробка
|
верстат |
Відповідно до технічних умов на механічну
обробку деталей після хромування.
|
VII |
Консервація |
Ванна для
составів, що консервують, робочий стіл
|
спеціальні
состави
|
Повне виключення
загальної й місцевої
корозії при зберіганні відповідно до
технічними умовами.
|
6. Проектування технологічних операцій
Завдання роздягнуло - розрахувати такі режими різання на операції технологічного процесу, які забезпечили б заданий випуск деталей необхідної якості з мінімальними витратами.
6.1
Розрахунок режимів різання й визначення основного часу на операцію
Розрахунок режимів різання по емпіричних залежностях [9] зробимо для двох операцій технологічного процесу 050-свердлильної й 100-шліфувальної для інших операцій технологічного процесу розрахунок режимів різання виконаємо табличним способом, з огляду на рекомендації [11]. Основне часу на операцію будемо визначати використовуючи рекомендації [12, 10]
Загальні вихідні дані для всіх операцій ТП:
Деталь - корпус гідроциліндра;
Матеріал - сталь 45Л ДЕРЖСТАНДАРТ 977-75;
Заготівля - виливок 10-5-12-10;
Розрахункова довжина робочого ходу інструмента (L) для токарських операцій, визначається згідно рекомендацій [10, с.610] по формулі:
L=l+l1
+l2 (
6.1)
де l - довжина оброблюваної поверхні, мм;
l1
- величина врізання інструмента, приймаємо по табл.2 [10, с.610] l1
=3мм;
l2
- величина переперегони інструмента, приймаємо по табл.2 [10, с.610] l2
=2мм.
Операція 010 Токарська (чорнова)
Устаткування - Токарно-гвинторізний верстат 1А616;
Пристосування - Оправлення цангова 7112-1509 ДЕРЖСТАНДАРТ 12593-93
Вихідні дані для розрахунку й зведемо в табл.6.1.
Таблиця 6.1.
Зміст
переходу
|
Розрахункова довжина робочого ходу інструмента-L, мм |
Глибина різання |
IT
|
RRa
|
Різальний інструмент
|
перехід 1: точити цилиндрич. пов.12 |
68,5
|
2
|
12
|
12,5
|
Різець розточувальної цільної зі сталевим хвостовиком для глухих отворів ДЕРЖСТАНДАРТ 18063-72, Т5К10 |
перехід 2,3: підрізати торець 4,6,5; |
25
|
2
|
Різець прохідний упорний відігнутий з кутом у плані 90º ДЕРЖСТАНДАРТ 18879-73, |
37 |
Різець розточувальної з кутом у плані 90º за ДСТ 10044-73, Т5К10 |
По табл.28 [9] з обліком вихідних даних визначаємо табличне значення подачі Sот
, мм/об..: Sот
=0,6мм/об..
Подача на оберт:
Sо
=SОт
×КSо
, (6.2)
де SОт
-
таблична подача на оберт, SО= 0,6 мм/об.;
КSо
- загальний поправочний коефіцієнт на подачу:
КSо
= КSп
×КSи
×KSф
×KSз
×KSж
×KSм
, (6.3)
де КSп
- коефіцієнт, що враховує стан оброблюваної поверхні (кірка), по табл.30 [11] приймаємо КSп
= 0,8;
КSи
- коефіцієнт, що враховує матеріал інструмента, по табл.30 [11] приймаємо КSи
= 1,0;
KSф
- коефіцієнт, що враховує форму оброблюваної поверхні, по табл.30 [11] приймаємо КSф
= 1,0;
KSз
- коефіцієнт, що враховує вплив загартування, приймаємо рівним 1,0
KSж
- коефіцієнт, що враховує твердість технологічної системи, по табл.30 [11] приймаємо КSж
=0,95 (перехід1), КSж
=1 (перехід2);
KSм
- коефіцієнт, що враховує матеріал оброблюваної деталі, по табл.30 [11] приймаємо КSм
= 1,07;
Sо1
= 0,6×0,8×1,0×1,0×1,0×0,95×1,07 = 0,49 мм/об..
Sо2,3
= 0,6×0,8×1,0×1,0×1,0×1,0×1,07 = 0,51 мм/об.
Швидкість різання визначаємо по формулі:
V = Vт
×Kv
, (6.4)
де Vт
- табличне значення швидкості різання, по табл.36 [11] приймаємо залежно від Sо
: Vт
= 171 м/хв (перехід1), Vт
= 171 м/хв (перехід2,3);
KV
- загальний поправочний коефіцієнт на швидкість різання, що враховує фактичні умови різання:
Kv
= KVм
×KVи
×KVm
×KVж
×KVп
×KVо
×KVφ
, (6.5)
де КVм
- коефіцієнт оброблюваності матеріалу, по табл.37 [11] приймаємо КVм
= 0,65;
КVи
- коефіцієнт, що враховує матеріал інструмента, по табл.37 [11] приймаємо КVи
= 0,81;
KVm
- коефіцієнт, що враховує вид обробки, по табл.37 [11] приймаємо КVm
= 1,0;
KVж
- коефіцієнт, що враховує твердість технологічної системи, по табл.35 [11] приймаємо КVж1
= 0,8 (перехід1); КVж2,3
= 1,2 (перехід1);
KVп
- коефіцієнт, що враховує стан оброблюваної поверхні, по табл.35 [11] приймаємо КVп
= 0,85;
KVо
- коефіцієнт, що враховує вплив СОЖ, КVо
= 1,0;
KVφ
- коефіцієнт, що враховує вплив кута в плані, по табл.35 [11] приймаємо KVφ
=0,81.
V1
= 171× 0,65×0,81×1,0 0,8×0,85×1,0×0,81= 50 м/хв;
V2,3
= 171× 0,65×0,81×1,0×1,2×0,85×0,81 = 74 м/хв,
Частоту обертання шпинделя визначаємо по формулі:
, (6.6)
де V - швидкість різання;
d - діаметр заготівлі (інструмента);
n1
= 1000×50/3,14×144,8= 110 об./хв.
n2
= 1000×74/3,14×50 = 471 об./хв
Остаточно приймаємо частоту обертання шпинделя для обробки всіх поверхонь за паспортним даними, такою частотою обертання є: nф
= 200о/мі.
Визначимо фактичну швидкість різання відповідно до прийнятої частоти обертання шпинделя по формулі:
Vф
= π·d·n/1000, м/хв; (6.7)
Vф1
= 3,14·144,8·200/1000 = 91 м/хв;
Перевіримо правильність обраних режимів різання по потужності привода головного руху верстата по формулі:
N = NT
· (Vф
/V·) KN
, кВт (6.8)
де KN
- коефіцієнт, що враховує потужність різання, KN
= 0,60;
NT
- табличне значення потужності різання обумовлене по карті [9], воно становить NT
= 3,6 кВт для всіх оброблюваних поверхонь.
Визначимо потужність різання переходів 1, 2, 3:
N1
=3,6· (91 /50) ·0,6=3,93 кВт;
N2,3
=3,6·31 /74 ·0,6=1,5 кВт.
Отримані значення потужності різання не повинні перевищувати значення потужності різання верстата зазначеної в паспортних даних помножене на коефіцієнт корисної дії (КПД) устаткування, тобто N ≤ Nпаспорт
·η, где η = 0,8; Nпаспорт
= 6 кВт. Розрахунок основного часу на операцію 010.
Основний технологічний час - час, протягом якого відбувається безпосередній вплив інструмента на заготівлю й зміну її стану. При верстатній обробці визначається по формулі:
(6.9)
де Lр. х.
- довжина робочого ходу, мм (див. табл.6.1);
i - число робочих ходів;
Sо
- подача на оберт шпинделя, мм/об..
Підставивши вихідні дані у формулу (6.9), одержимо:
перехід 1: ;
перехід 2: 
перехід 3: 
Разом основний час на операцію 010:
Те= Т1
+Т1,2
=1,37+0,3+0,3=1,97 хв.
Операція 020 Токарська (чорнова).
Устаткування - Токарно-гвинторізний верстат 1А616;
Пристосування - Патрон 3-х кулачковий клиновий ДЕРЖСТАНДАРТ 24351-80
Вихідні дані для розрахунку й зведемо в табл.6.2.
Таблиця 6.2.
Зміст
переходу
|
Розрахункова довжина робочого ходу інструмента-L, мм |
Глибина різання |
IT |
RRa |
Різальний інструмент |
перехід 1: точити пов.13 |
36
|
2
|
12
|
12,5
|
Різець розточувальної з кутом у плані 60º ДЕРЖСТАНДАРТ 18882-73, Т5К10 |
перехід 2: підрізати торці пов.1; |
42 |
1,5 |
Різець прохідний упорний відігнутий з кутом у плані 90º с ДЕРЖСТАНДАРТ 18879-73, Т5К10 |
По табл.28 [9] з обліком вихідних даних визначаємо табличне значення подачі
Sот
, мм/об..: Sот
=0,6мм/о.
Подачу на оберт обчислюємо по формулі (6.2);
Загальний поправочний коефіцієнт на подачу КSо
, обчислюємо по формулі (6.3):
КSп
- коефіцієнт, що враховує стан оброблюваної поверхні (кірка), по табл.30 [11] приймаємо КSп
= 0,8;
КSи
- коефіцієнт, що враховує матеріал інструмента, по табл.30 [11] приймаємо КSи
= 1,0;
KSф
- коефіцієнт, що враховує форму оброблюваної поверхні, по табл.30 [11] приймаємо КSф
= 1,0;
KSз
- коефіцієнт, що враховує вплив загартування, приймаємо рівним 1,0
KSж
- коефіцієнт, що враховує твердість технологічної системи, по табл.30 [11] приймаємо КSж
=0,5 (перехід1), КSж
=0,85 (перехід2);
KSм
- коефіцієнт, що враховує матеріал оброблюваної деталі, по табл.30 [11] приймаємо КSм
= 1,07;
Sо1
= 0,6*0,8*1,0**1,0*1,07*0,5*1,0=0,26 мм/об..
Sо2
= 0,6×0*0,8*1,0**1,0*1,07*0,85*1,0=0,43 мм/об.
Швидкість різання визначаємо по формулі (6.4):
Vт
- табличне значення швидкості різання, по табл.36 [11] приймаємо залежно від
Sо
: Vт
= 228 м/хв (перехід1), Vт
= 200 м/хв (перехід2);
KV
- загальний поправочний коефіцієнт на швидкість різання, що враховує фактичні умови різання, розраховується по формулі (6.5):
КVм
= 0,65, табл.37 [11], КVи
= 0,81, табл.37 [11]
КVm
= 1,0; табл.37 [11]
КVж1
= 0,6 (перехід1); КVж2
= 1,2 (перехід2); табл.35 [11]
КVп
= 0,85; табл.35 [11], КVо
= 1,0;
KVφ
=0,92 (перехід1); KVφ
=0,81 (перехід1), табл.35 [11]
V1
= 228*0,65*0,81*1,0*0,6*0,85*1,0*0,92= 60 м/хв;
V2,3
= 200*0,65*0,81*1,0*1,2*0,85*1,0*0,81= 87 м/хв,
Частоту обертання шпинделя визначаємо по формулі (6.6): 
n1
= 1000×60/3,14×39,315= 486 об./хв.
n2
= 1000×87/3,14× (108-39) = 401,5 об./хв
Остаточно приймаємо частоту обертання шпинделя для обробки всіх поверхонь за паспортним даними, такою частотою обертання є: nф
= 450про/мі. Визначимо фактичну швидкість різання відповідно до прийнятої частоти обертання шпинделя по формулі (6.7):
Vф1
= 3,14·39,315*450/1000 = 56 м/хв;
Vф2
= 3,14× (108-39) *450/1000 = 92 м/хв;
Перевіримо правильність обраних режимів різання по потужності привода головного руху верстата по формулі (6.8), KN
= 0,60; NT
= 3,6 кВт
Визначимо потужність різання переходів 1, 2:
N1
=3,6· (56 /60) ·0,6=2.02 кВт;
N2,3
=3,6· (92 /87) ·0,6=2.3 кВт.
Отримані значення потужності різання не повинні перевищувати значення потужності різання верстата зазначеної в паспортних даних помножене на коефіцієнт корисної дії (КПД) устаткування, тобто N ≤ Nпаспорт
·η, где η = 0,8; Nпаспорт
= 6 кВт. Розрахунок основного часу на операцію 020
Підставивши вихідні дані у формулу (6.9), одержимо:
перехід 1: ;
перехід 2: 
Разом основний час на операцію 020:
Те= Т1
+Т1,2
=0,31+0,22=0,53 хв.
Аналогічно, за допомогою рекомендацій [11], визначимо режими на 030 токарську операцію, результати розрахунків зведемо в таблицю 6.6.
Операція 040 Токарська (чистова)
Устаткування - Токарно-гвинторізний верстат16Б16П;
Пристосування - Патрон 3-х кулачковий клиновий ДЕРЖСТАНДАРТ 24351-80
Вихідні дані для розрахунку й зведемо в табл.6.3.
Таблиця 6.3.
Зміст
переходу
|
Розрахункова довжина робочого ходу інструмента-L, мм |
Глибина різання |
IT
|
RRa
|
Різальний інструмент
|
перехід 1: точити циліндричну пов.13; фаски 2×45º. |
34
|
0,27 |
9
|
2,5
|
Різець розточувальної з кутом у плані 60º ДЕРЖСТАНДАРТ 18882-73, Т15К6 |
перехід 2: підрізати торець 1 |
40 |
0,9 |
Різець прохідний упорний відігнутий з кутом у плані 90º ДЕРЖСТАНДАРТ 18879-73, Т15К6 |
перехід 3: точити канавку пов. 20,21,22 |
6 |
4 |
Різець канавковий спеціальний К01-4112-000, Т15К6 |
По табл.28 [11] з обліком вихідних даних визначаємо табличне значення подачі Sот
, мм/об..: Sот
=0,19 мм/об..
Подачу на оберт обчислюємо по формулі (6.2);
Загальний поправочний коефіцієнт на подачу КSо
, обчислюємо по формулі (6.3):
КSп
= 1,0 - табл.30 [9] ;
КSи
= 1,0 - по табл.30 [9] ;
КSф1,2
= 1,0; КSф32
= 0,7
KSз
=1,0
КSж
=0,5 (перехід1,3), КSж
=0,85 (перехід2);
КSм
= 1,07;
Sо1
= 0, 19*1,0*1,0*1,0*1,0*0,5*1,07=0,1 мм/об..
Sо2
= 0, 19*1,0*1,0*0,7*1,0*0,85*1,07=0,12 мм/об.
Sо3
= 0, 19*1,0*1,0*1,0*1,0*0,5*1,07=0,1 мм/об..
Швидкість різання визначаємо по формулі (6.4):
Vт
- табличне значення швидкості різання, по табл.36 [11] приймаємо залежно від Sо
: Vт
= 340м/хв (перехід1), Vт
= 250м/хв (перехід2);
Vт
= 240м/хв (перехід3);
KV
- загальний поправочний коефіцієнт на швидкість різання, що враховує фактичні умови різання, розраховується по формулі (6.5):
КVм
= 1,0, табл.37 [11]
КVи
= 1,0, табл.37 [11]
КVm
= 1,0; КVm
= 0,6 (перехід1,3); табл.37 [11]
КVж1
= 0,5 (перехід1,3); КVж2
= 0,9 (перехід2); табл.37 [11]
КVп
= 1,0; табл.37 [11]
КVо
= 1,0;
KVφ
=0,92 (перехід1); KVφ
=0,81 (перехід1), табл.37 [11]
V1
= 340*1,0*1,0*0,6*0,5*1,0*1,0*0,81= 94 м/хв;
V2
= 250*1,0*1,0*1,0**0,9*1,0*1,0*0,92= 207 м/хв,
V3
= 240*1,0*1,0*0,6*0,5*1,0*1,0*1,0=72 м/хв
Частоту обертання шпинделя визначаємо по формулі (6.6): 
n1
= 1000×94/3,14×39,8= 752 об./хв.
n2
= 1000×207/3,14× (108-39) = 955 об./хв
n3
= 1000×72/3,14×48= 478 об./хв
Остаточно приймаємо частоту обертання шпинделя для обробки всіх поверхонь за паспортним даними, такою частотою обертання є: nф
= 700про/мі.
Визначимо фактичну швидкість різання відповідно до прийнятої частоти обертання шпинделя по формулі (6.7):
Vф1
= 3,14·39,8*700/1000 = 90 м/хв;
Vф2
= 3,14× (108-39,8) *700/1000 = 110 м/хв;
nф2
= 500про/мі.
Vф3
= 3,14·48*500/1000 = 74 м/хв;
Перевіримо правильність обраних режимів різання по потужності привода головного руху верстата по формулі (6.8), KN
= 0,60; NT
= 3,6 кВт
Визначимо потужність різання переходів 1, 2,3:
N1
=3,6· (94 /90) ·0,6=2.25 кВт;
N2
=3,6· (207 /110) ·0,6=5,3 кВт;
N3
=3,6· (72 /74) ·0,6=2,1кВт.
Отримані значення потужності різання не повинні перевищувати значення потужності різання верстата зазначеної в паспортних даних помножене на коефіцієнт корисної дії (КПД) устаткування, тобто N ≤ Nпаспорт
·η, где η = 0,8; Nпаспорт
= 8 кВт.
перехід 1: ;
перехід 2: 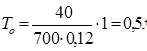
перехід 3: 
Разом основний час на операцію 040: Те= Т1
+Т3,2
=0,5+0,5+0,4=1,4 хв
Операція 050 Свердлильна
Устаткування - вертикально-свердлильний верстат зі ЧПУ 2Р123Ф2;
Пристосування - пристосування спеціальне;
Вихідні дані для розрахунку й зведемо в табл.6.4.
Таблиця 6.4.
Зміст
переходу
|
Розрахункова довжина робочого ходу -L, мм |
Глибина різання |
IT
|
Ra
|
Різальний інструмент
|
перехід 1:
засвердлити
|
5 |
2,25
|
_ |
_ |
Свердел спіральне для зацентрування під свердління O4,5
ОСТ 2 И21-2-76, Р6М5
|
перехід 2
свердлити 3 отв. пов.10
|
20
|
2,25 |
12 |
12,5 |
Свердел східчасте Ø4,5 ОСТ 2 И21-2-76, Р6М5 |
перехід 3
зенкеровать 3 отв. пов.10
|
20 |
0,5 |
9 |
6,3 |
Зенкер цільної O5,5
ДЕРЖСТАНДАРТ 21544-76, 14К8
|
перехід 4
розгорнути 3 отв. пов.10
|
20
|
0,25 |
7 |
2,5 |
Розгорнення цільна Ø 6 ДЕРЖСТАНДАРТ 1672-80 |
перехід 5
свердлити 3 отв. пов.11
|
20
|
3,2 |
12 |
12,5 |
Свердел східчасте Ø6,4 ОСТ 2 И21-2-76, Р6М5 |
перехід 5
нарізати різьблення в 3-х отв.11
|
20
|
- |
7 ст. |
2,5 |
Мітчик М8-7Н
ДЕРЖСТАНДАРТ 3266-81, Р18
|
Розрахунок режимів зробимо за методикою викладеної в с.273 [12].
По табл.25,26,27 [9] залежно від вихідних даних вибираємо подачі при свердлінні, зенкеровании, розгортанні:
перехід 1-S=0.15 мм/об.;
перехід 2-S=0,15 мм/об. - табл.25 [12] ;
перехід 3-S=0.6 мм/об.; табл.26 [12] ;
перехід 4-S=0.6 мм/об. - табл.27 [12] ;
перехід 5-S=0.15 мм/об. - табл.25 [12] ;
Швидкість різання по формулі при свердлінні V, м/хв:
, (6.10а)
Швидкість різання по формулі при зенкерованії й розгортанні V, /хв:
, (6.10б)
Швидкість різання по формулі при нарізуванні різьблення мітчиком V, м/хв:
корпус гідроциліндр машинобудування токарська
, (6.10в)
де СV
, m, x,y - коефіцієнт і показники ступеня при обробці свердлами, зенкерами, нарізуванні різьблення мітчиком, приймаємо по табл.49,29 [9] ;
T - стійкість інструмента, хв - приймаємо T1
=25 хв, T2
=25 хв, T3
=30 хв, T4
=20 хв, T5
=25 хв, T6
=90 хв.
t - глибина різання, мм (див. табл.6.5);
S - подача на оберт шпинделя, мм/об.;
, (6.11)
де KMV
-коефіцієнт, що враховує вплив матеріалу заготівлі, табл.1; Kи -коефіцієнт, що враховує матеріал інструмента, табл.6 [9]; KlV
- коефіцієнт, що враховує глибину свердління, по табл.31 [9]; Для нарізування різьблення мітчиком:
КV
= КMr·
Кис·
Ксr
. (6.12)
де КM-Коефіцієнт, що враховує матеріалу заготівлі, по табл.1 [9];
Киснув -коефіцієнт, що враховує матеріал інструмента, по табл.6 [9] ;
Ксr
-коефіцієнт, що враховує спосіб нарізування різьблення.
перехід 1 - СV
=7; q=0,40; y=0,70; m=0.2, KV
=0,72
перехід 2 - СV
=7; q=0,40; y=0,70; m=0.2, KV
=0,72;
перехід 3 - СV
=18; x=0,2; y=0.3; m=0.25, q=0,6; KV
=0,6;
перехід 4 - СV
=100,6; q=0.3; y=0.65; m=0.4, KV
=0,6;
перехід 5 - СV
=7; q=0,40; y=0,70; m=0.2, KV
=0,72;
перехід 6 - СV
=64,8; q=1,2,y=0.50; m=0.9, KV
=0,9.
Підставивши вихідні дані й певні значення у формулу (6.10а, 6.10б, 6.10в), визначимо за допомогою програми Microsoft Excel швидкості різання для всіх технологічних переходів операції 050, одержимо:
Частота обертання шпинделя:
перехід 1 - n1
= 1000×18,23/3,14×4,5= 1290 об./хв;
перехід 2 - n1
= 1000×18,23/3,14×4,5= 1290 об./хв;;
перехід 3 - n1
= 1000×21/3,14×5,5= 1216 об./хв;;
перехід 4 - n1
= 1000×53,4/3,14×6= 2835 об./хв;;
перехід 5 - n1
= 1000×16,8/3,14×6,4= 8363 об./хв;;
перехід 6 - n1
= 1000×13,4/3,14×8= 534 об./хв. .
Остаточно приймаємо частоту обертання шпинделя для обробки всіх поверхонь за паспортним даними, такою частотою обертання є: nф
= 1650 об./хв.
Визначимо фактичну швидкість різання відповідно до прийнятої частоти обертання шпинделя по формулі (6.7):
перехід 1 - Vф
= 3,14·4,5·1650/1000 = 23,3 м/хв;
перехід 2 - Vф
= 3,14·4,5·1650/1000 = 23,3 м/хв;
перехід 3 - Vф
= 3,14·5,5·1650/1000 = 29 м/хв;
перехід 4 - Vф
= 3,14·6·1650/1000 = 31,1 м/хв;
перехід 5 - Vф
= 3,14·6,4·1650/1000 = 33,2 м/хв;
перехід 6 - Vф
= 3,14·8·1650/1000 = 41 м/ми.
Разом основний час на операцію 050:
Те=0,077+0,242+0,06+0,06+0,242+0,025=0,706 хв.
Операція 100 Шліфувальна
Устаткування - Внутрішліфувальний верстат 3А227А;
Пристосування - Патрон мембранний ДЕРЖСТАНДАРТ 16157-70;
Вихідні дані для розрахунку й зведемо в табл.6.5.
Таблиця 6.5
Зміст
переходу
|
Lрх
, мм |
t |
IT |
Ra |
Різальний інструмент |
Шліфувати отвір пов.13 |
35 |
0,142(2 хо-д, т.е.0,071) |
7 |
0,8 |
Коло шліфувальний ПП 30×35×10 2А16СМ28К5 |
Радіальна подача:
SВ
=SВт
×КSВ
, (6.13)
Поздовжня подача:
St
=Stт
×КSt
, (6.14)
KSB
(KSt
) = KM
×KD
× KT
×KVк
× Kh
×KlT
, (6.15)
де SВт
- табличне значення радіальної подачі;
Stт
- табличне значення поздовжньої подачі;
Kм
- коефіцієнт, що враховує матеріал оброблюваної деталі; Км
= 1,0;
КD
- коефіцієнт, що враховує діаметр шліфувального кола, КD
= 1,0;
KT
- коефіцієнт, що враховує стійкість кола KT
= 0,74;
KVк
- коефіцієнт, що враховує швидкість кола, KVк
= 1,0;
Kh
- коефіцієнт, що враховує припуск на обробку, Kh
=1,16;
KlT
- коефіцієнт, що враховує точність обробки, KlT
= 0,75;
KSB
(KSB
) = 1,0×1,0×0,74×1,0×1,16×0,75 ×0,75=0,64
SВ
=0,0075×0,64=0,005 мм/об.. St
=0,0011×0,64=0,0007 мм/об..
Швидкість різання: V= 30 м/с.
Частота обертання шпинделя: n = 1000 об./хв.
Розрахунок основного часу на операцію 100.
Основний технологічний час визначаємо відповідно до рекомендацій [13] по формулі:
TO
= 1,8·D·L·10-3
, хв (6.16)
де D-Оброблюваний діаметр, D=40 мм;
L - довжина оброблюваної поверхні, L=30+2+3=35 мм
TO
= 1,8·40·35·10-3
=3,5 хв;
Аналогічно, за допомогою рекомендацій [9], визначимо режими на 090 шліфувальну операцію, результати розрахунків зведемо в таблицю 6.6.
Операція 130 Хонинговальна.
Режим обробки при хонингованії включає сукупність окремих параметрів, основними з яких є: окружна швидкість обертання головки (Vок
), швидкість зворотно-поступального руху головки (Vвп
), співвідношення між ними (λ), радіальна подача брусків (Sр
) і состав СОЖ.
Відповідно до рекомендацій [16], визначимо вище перераховані параметри:
Тому що 2t=0,042 мм, те застосовуємо дворазове хонинговання на верстаті 3К84.
1 хід: Vок
=60м/хв 1 хід: Vок
=40 м/хв
Vвп
=18 м/хв Vвп
=10 м/хв
?=3,3 ?=3,3
Sр
=1,7 напівтемних Sр
=0,4 напівтемних
2t= 3,4 напівтемних 2t= 0,8 напівтемних
Аналогічно, за допомогою рекомендацій [16], визначимо режими хонинговання на 120 хонинговальну операцію, результати занесемо в табл.6.6.
Складемо зведену таблицю режимів різання по всіх операціях технологічного процесу:
Таблиця 6.6.Зведена таблиця по режимах різання
№ |
Назва
операції
|
№ перехід |
Глибина різання
t, мм
|
Подача на оберт So, мм/об. |
Швидкість різання V, м/хв |
Частота обертання шпинделя n, об./хв |
010 |
ТОКАРСЬКА |
1 |
2 |
0,49 |
91 |
200 |
2,3 |
2 |
0,51 |
31 |
200 |
200 |
ТОКАРСЬКА |
1 |
2 |
0,26 |
56 |
450 |
2 |
1,5 |
0,43 |
92 |
450 |
030 |
ТОКАРНЯ
|
1 |
0,4 |
0,12 |
118 |
250 |
2 |
0,9 |
0,12 |
100 |
250 |
3 |
0,5 |
0,1 |
55 |
125 |
040 |
ТОКАРСЬКА |
1 |
0,27 |
0,1 |
90 |
800 |
2 |
0,9 |
0,12 |
110 |
800 |
3 |
4 |
0,1 |
74 |
500 |
050 |
СВЕРЛИЛЬНА ЗІ ЧПУ |
1 |
2,25 |
0,15 |
23,3 |
1650 |
2 |
2,25 |
0,15 |
23,3 |
1650 |
3 |
0,5 |
0,6 |
29 |
1650 |
4 |
0,25 |
0,6 |
31,1 |
1650 |
5 |
3,2 |
0,15 |
33,2 |
1650 |
6 |
- |
1,5 |
41 |
1650 |
100 |
ШЛІФУВАЛЬНА |
0,14 |
0,0007 |
30 |
1000 |
130 |
Хонинговальна |
3,4
0,8
|
1,7
0,4
|
1) Vок
=60
Vвп
=18
2) Vок
=40
Vвп
=10
|
480
320
|
120 |
ХОНИНГОВАЛЬНАЯ |
3,
0,8
|
1,7
0,4
|
1) Vок
=80
Vвп
=25
2) Vок
=50
Vвп
=16
|
170
100
|
6.2
Нормування технологічного процесу
Технологічний процес виготовлення виробу повинен виконуватися з найбільш повним використанням технічних можливостей засобів виробництва при найменших витратах часу й найменшої собівартості виробів. Для того щоб оцінити витрати часу, необхідно вести нормування техпроцесу, тобто мати дані по нормах часу. Такими нормами можуть бути тільки технічно обґрунтовані норми часу - установлені для певних технічних-організаційно-технічних умов на виконання частини технологічного процесу, виходячи з повного й раціонального використання технічних можливостей засобів технологічного оснащення й з обліком передового виробничого досвіду.
При нормуванні ТП виготовлення деталі скористаємося аналітично-розрахунковим методом. Він передбачає визначення витрат часу на кожний елемент операції й на операцію в цілому по заздалегідь установленим, технічно обґрунтованим нормативам часу й оптимальних режимів роботи встаткування.
У серійному виробництві, коли обробка йде періодично повторюваними партіями, за норму часу приймають штучно-калькуляційний час:
(6.17)
де тпз
- підготовчо-заключний час, хв; n-обсяг партії запуску заготівель, n=15000/278=5 шт; тшт
- штучний час, хв.
(6.18)
де те - основний технологічний час, хв;
тв
- допоміжний час, хв;
тоб
- час обслуговування, хв;
тпер
- час перерв у роботі, хв.
основний технологічний час - час, протягом якого відбувається безпосередній вплив інструмента на заготівлю й зміну її стану. при верстатній обробці те, визначаємо по формулі (6.1).
(6.19)
де l - довжина оброблюваної ділянки, мм;
lвр
- довжина ділянки інструмента, що врізається, мм;
lпер
- довжина ділянки переперегони інструмента, мм.
Сума основного й допоміжного часу становить оперативний час:
(6.20)
При розрахунку основного технологічного часу скористаємося даними, певними в п.6.1. (Те), допоміжне, час обслуговування, час перерв, підготовчо-заключний час призначаємо по [12]. Штучно-Калькуляційний час розраховуємо тільки на окремі операції.
З огляду на навчальний характер проектування Тшт-До визначимо використовуючи рекомендації [13] по формулі:
Тшт-До= φ ·То,
хв (6.21)
де ? - поправочний коефіцієнт на тип виробництва, визначається по [13] стор.147.
Основний технологічний Той час був розрахований у п.6.1., зведемо результати розрахунків у табл.6.7.
Таблиця 6.7.Технічні норми часу
№ |
Найменування
операції
|
Основне
час Те, хв
|
Значення коефіцієнта φ |
Штучно-Калькуляційний час Тштк
|
010 |
ТОКАРСЬКА |
0,73 |
3,25 |
2,4 |
020 |
ТОКАРСЬКА |
0,53 |
3,25 |
1,7 |
030 |
ТОКАРСЬКА |
2,16 |
3,25 |
7,02 |
040 |
ТОКАРСЬКА |
1,4 |
3,25 |
4,55 |
050 |
СВЕРДЛИЛЬНА ЗІ ЧПУ |
0,706 |
2,72 |
1,92 |
090 |
ШЛІФУВАЛЬНА |
3 |
2,10 |
6,3 |
100 |
ШЛІФУВАЛЬНА |
2,5 |
2,10 |
5,25 |
120 |
Хонинговальна |
1,5 |
2,10 |
3,15 |
130 |
Хонинговальна |
1,2 |
2,10 |
2,52 |
7.
Розрахунок і проектування верстатного пристосування
Зробимо опис конструкції й розрахунок токарського 3-х кулачкового патрона, що самоцентрує, для обробки деталі на 020 токарській операції.
7.1
Збір вихідних даних
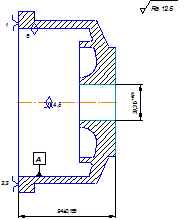
Мал..7.1.Операційний ескіз
Вид і матеріал заготівлі - виливок, сталь 45Л ДЕРЖСТАНДАРТ 977-75, твердість
НВ 215±2.
Вид обробки - чорнова. Обробка ведеться в 2 переходи. Матеріал і геометрія ріжучої частини різця:
перехід 1- різець розточувальної з ?= 60? с пластинами із твердого сплаву за ДСТ 18882-73, Т5К10;
перехід 2 - різець прохідний упорний відігнутий з ?= 90? с пластинами із твердого сплаву за ДСТ 18879-73, Т5К10.
Режими різання (див. п.6.1):
перехід 1 - глибина t=2 мм, подача S= 0,26 мм/об., швидкість рез. V=56 м/хв;
перехід 2 - глибина t=1,5 мм, подача S= 0,43 мм/об., швидкість рез. V=92 м/хв.
Тип пристосування - одномісне універсальне налагоджувальне (УНП) зі змінними зворотними кулачками.
Металообробний верстат - 1А616 (найбільший діаметр патрона - 320 мм, внутрішній конус шпинделя - Морзе 6 [10], основні розміри кінців шпинделя за ДСТ 12595-72 [10].
7.2
Розрахунок сил різання
Розрахунок сил різання виконаємо за методикою викладеної в [11]. Розрахунок ведемо по найбільш навантаженому першому переході.
При зовнішнім поздовжнім і поперечному гострінні, а також розточуванні РZ
, PY,
Pх
сили різання розраховуються по формулі:
, Н (7.1)
де CP
, x, y, n - постійна й показники ступеня для конкретних умов обробки;
t - глибина різання, мм;
S - подача на оберт, мм/об.;
V - швидкість різання, м/хв;
n - частота обертання шпинделя, об./хв.
При обробці стали різцем із твердого сплаву значення коефіцієнта Ср
і показників ступеня у формулах сили різання при гострінні для сил РZ
, PY
, Pх
складуть:
для РZ
: CP
= 300; x= 1,0; y= 0,75; n= - 0,15 [9] ;
для Ру
: CP
= 243; x= 0,9; y= 0,6; n= - 0,3 [9] ;
для Рх
: CP
= 339; x= 1,0; y= 0,5; n= - 0,4 [9].
Поправочний коефіцієнт KP
являє собою добуток ряду коефіцієнтів, що враховують фактичні умови різання.
, (7.2)
де КМ - поправочний коефіцієнт, що враховує вплив якості оброблюваного матеріалу на силові залежності:
, (7.2.1)
де НВ - твердість;
n - показник ступеня; n = 0,75 [9]
Тоді: 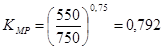
Кj
p
, Кg
p
, Кl
р
, Кrр
- поправочні коефіцієнти, що враховують вплив геометричних параметрів ріжучої частини інструмента на тридцятимільйонні сили різання:
для РZ
: Кj
р
=0,94; Кg
р
=1,1; Кl
р
=1,0; Кrр
=0,93 [9] ;
для Ру
: Кj
р
=0,77; Кg
р
=1,4; Кl
р
=1,25; Кrр
=0,82 [9].
для Рх
: Кj
р
=1,11; Кg
р
=1,1; Кl
р
=0,85; Кrр
=1,0 [9] ;
Підставивши вихідні дані у формулу (7.2) одержимо:
КPZ
=0,792×0,94×1,1×1,0×0,93= 0,762;
КPу
=0,792×0,77×1,4×1,25×0,82= 0,875;
КPХ
=0,792×1,11×1,1×0,85×1,0= 0,822.
Підставивши вихідні дані у формулу (7.1) одержимо:
PZ
= 10×300×21,0
×0,260,75
×56-0,15
×0,762 = 910,14 Н;
Pу
= 10×243×2,0,9
×0,260,6
×56-0,3
×0,875 = 528,53 Н;
PХ
=10
×339×21,0
×0,260,5
×56-0,4
×0,822= 567,95
7.3
Розрахунок зусилля затискача
У процесі обробки на заготівлю впливає система сил. З однієї сторони діє сила різання, що прагнути вирвати заготівлю з кулачків, з іншої сторони сила затискача, що перешкоджає цьому. З умови рівноваги моментів даних сил і з урахуванням коефіцієнта запасу визначаємо необхідне зусилля затискача.
Схема закріплення заготівлі представлена на малюнку 7.2.
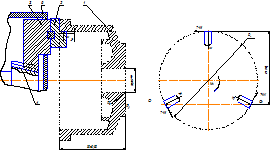
1-заготівля; 4-затискної механізм (клиновий); 2-кулачок змінний; 3-кулачок постійний; 5-корпус.
Мал..7.2.Схема закріплення заготівлі
Сумарний крутний момент від дотичній тридцятимільйонної сили різання прагнути провернути заготівлю в кулачках і дорівнює:
, (7.3)
Повороту заготівлі перешкоджає момент сили затискача, обумовлений у такий спосіб:
, (7.4)
де W - сумарне зусилля затискача доводиться на три кулачки, Н;
f - коефіцієнт тертя на робочій поверхні змінного кулачка, f=0,3;
D1
- діаметр оброблюваної поверхні, мм; d1
= 39,315 мм.
D2
- діаметр, мм; d2
= 146 мм.
З рівності моментів МР
і МЗ
визначимо необхідне зусилля затискача, що перешкоджає провороту заготівлі в кулачках.
(7.5)
де К - коефіцієнт запасу;
PZ
- тангенціальна сили різання, Н;
Значення коефіцієнта запасу К, залежно від конкретних умов виконання технологічної операції, визначається по формулі [9, c.382]:
K = К0
×К1
×К2
×К3
×К4
×К5
×К6
, (7.6)
де K0
- гарантований коефіцієнт запасу;
K0
=1,5 [9, c.382] ;
K1
- коефіцієнт, що враховує збільшення сили різання через випадкові нерівності на оброблюваних поверхнях заготівлі;
K1
=1,2 - при чорновій обробці [9,c.382] ;
K2
- коефіцієнт, що враховує збільшення сили різання внаслідок затуплення різального інструменту;
K2
=1,0 - при чорновій обробці чавуну для PZ
[9,c.383] ;
K2
=1,4 - при чорновій обробці чавуну для Pу
[9,c.383] ;
K3
- коефіцієнт, що враховує збільшення сили різання при переривчастому різанні;
K3
=1,2 [9,c.383] ;
K4
- коефіцієнт, що характеризує сталість сили, що розвивається затискним механізмом;
K4
= 1,0 - для механізованих приводів [9,c.383] ;
K5
- коефіцієнт, що характеризує ергономіку немеханізованого затискного механізму;
K5
= 1,0 - для механізованих приводів [9,c.383] ;
K6
- коефіцієнт, що враховується тільки при наявності моментів, що прагнуть повернути заготівлю, установлену плоскою поверхнею;
K6
= 1,0 [9,c.384].
Підставивши вихідні дані у формулу (7.6) одержимо:
Кz
=1,5×1,2×1,0×1,2×1,0×1,0×1,0 = 2,16;
Кy
=1,5×1,2×1,4×1,2×1,0×1,0×1,0 = 3,024.
Якщо К<2,5, то по рекомендаціях [9,c.384] приймаємо К=2,5.
Підставивши вихідні дані у формулу (7.5) одержимо:
 Н.
Сила Ру
прагнути вивернути заготівлю з кулачків щодо осі ОО1 (
див. мал.7.1) створюючи момент від сили затискача:
, (7.7)
Даному моменту перешкоджає момент від сили затискача:
, (7.7)
Необхідна сила затискача дорівнює:
= 5145,13 Н
Для подальших розрахунків приймаємо найгірший випадок W=5145,13 H.
Величина зусилля затискача W1
, що прикладається до постійних кулачків, трохи збільшується в порівнянні із зусиллям затискача W і розраховується по формулі:
, (7.8)
де f1
- коефіцієнт тертя напрямного постійного кулачка й корпуса патрона; f1
=0,1;
LК
- виліт кулачка, мм; LК
= 30 мм;
НК
- довжина напрямного постійного кулачка, мм; НК
= 50 мм.
У процесі конструювання патрона дані розміри можуть трохи змінитися, але це, як показує практика, не внесе істотних змін у розрахунок зусиль.
Підставивши вихідні дані у формулу (7.8) одержимо:
Н.
7.4
Розрахунок затискного механізму патрона
Визначаємо зусилля Q, створюване силовим приводом, що збільшується затискним механізмом і передане постійному кулачку:
, (7.8)
де iC
- передатне відношення по силі затискного механізму (виграш у силі).
Для клинового механізму:
, (7.9)
де ( - кут нахилу клина, приймаємо 15?.
j і j1
- кути тертя на поверхнях кулачка й втулки й обумовлені по формулі: j= arctg f1
= arctg 0.1=5˚43, приймаємо j = j1
=6˚.
Підставивши вихідні дані у формулу (7.9) одержимо:
,
приймаємо найближче стандартне значення
Підставивши вихідні дані у формулу (7.8) одержимо:
Q=6274,55/2,3=2728 Н.
Приймаємо клиновий затискної механізм.
7.5
Розрахунок силового привода
На початку спробуємо застосувати пневматичний привод, тому що в будь-якому виробництві є трубопроводи для подачі стисненого повітря. Діаметр поршня пневмоцилиндра визначається по формулі [17,c.449]:
, (7.10)
де р - надлишковий тиск повітря, прийняте в розрахунках 0,4 Мпа;
( = 0,9 - КПД привода.
Підставивши вихідні дані у формулу (7.10) одержимо:
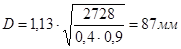
При розрахунку по формулі (7.10) діаметр поршня вийшов більше 80 мм, отже по рекомендаціях [17] будемо застосовувати гідравлічний привід, де за рахунок регулювання тиску масла можна одержати більші вихідні зусилля. При заданому зусиллі Q підбираємо тиск масла (Рг
=1,0; 2,5; 5,0; 7,5 Мпа) так, щоб діаметр поршня не перевищував 80 мм.
Як привод приймаємо гідроциліндр двосторонньої дії з робочим тиском 1,0 Мпа.
Визначимо діаметр поршня гідроциліндра, підставивши вихідні дані у формулу (7.10):
мм.
Приймаємо за ДСТ15608-81 найближче значення D= 63 мм.
Хід поршня циліндра розраховується по формулі:
, (7.11)
де Sw
- вільний хід кулачків, по рекомендаціях [17], приймаємо5 мм;
iп=
1/ ic
- передатне відношення затискного механізму по переміщенню, приймаємо 2,3;
Значення по рекомендаціях [14] приймаємо із запасом 10...15…15 мм.
Підставивши вихідні дані у формулу (7.11) і з огляду на рекомендації [14] одержимо: 15 мм.
За результатами розрахунків виконуємо креслення пристосування.
7.6
Розрахунок погрішності установки заготівлі в пристосуванні
Погрішність установки визначається по формулі:
, (7.12)
де εб
- погрішність базування, рівна в цьому випадку εб
=0, т.до вимірювальна база використовується в якості технологічної; εз
- погрішність закріплення (зсув вимірювальної бази під дією сил затискача), у цьому випадку εб
=0; εпр
- погрішність елементів пристосування, що залежить від точності їхнього виготовлення. На малюнку 7.3. представлена розмірна схема патрона із клиновим затискним механізмом.

Мал..7.3.Розрахункова схема погрішностей патрона
, (7.13)
де ωАΔ
- коливання замикаючого розміру АΔ
;
Δ1...
…Δ5
-погрішності, що виникають внаслідок неточності виготовлення розмірів, через коливання зазорів у сполученнях.
Точність тридцятилітніх розмірного ланцюга задаємо по 7 квалітету.
Підставивши вихідні дані у формулу (7.13) одержимо:

Погрішність установки не повинна перевищувати величини мінімального припуску на чистову обробку :
, 0,0234<0.0652
Погрішність установки не перевищує встановленої величини , отже, точність пристосування задовольняє вимогам.
7.7
Опис конструкції й принципу роботи пристосування
Що самоцентрує 3-х кулачковий патрон із клиновим затискним механізмом призначений для базування й закріплення деталі "Корпус гідроциліндра" на токарському верстаті.
Патрон складається з корпуса 1, у якому встановлений клин 4, у похилі пази якого входять підкуркульники 5. До підкуркульників гвинтами 32 за допомогою сухарів 6 кріпляться кулачки 7. Деталь установлюється до упору в опору 8, що кріпиться до стійки 9 корпуса 1 гвинтами 27. До клина 4 за допомогою втулки 2, зафіксованої гвинтом 13 кріпиться гвинт 30. Гвинт 13 входить в отвір вала. Щоб визначити радіальне положення цього отвору, у втулці встановлений фіксатор 34 з конічною головкою. Між корпусом 1 і корпусом 3 установлені дві пружини 12. До корпуса 3 гвинтами 25 кріпиться кришка 10. В отворах корпуса 1 і корпуси 3 установлені напрямні шпонки 16 і 11. Патрон кріпиться до шпинделя за допомогою гвинтів 29. Гвинт 30 за допомогою муфти з'єднаний зі штоком 19 гідроциліндра.
Гідропривід установлений на кінець шпинделя й кріпиться до верстата гвинтами. Гідропривід містить корпус 14, у якому на підшипниках 26 установлена кришка 9, що кріпиться гвинтами 18 до корпуса 14 гідроприводу. На кінці штока 19 установлений поршень 12, закріплений гайкою 30 зі стопорною шайбою 20. Для запобігання ударів поршня об стінки гідроциліндра на ньому встановлені демпфери 25. Між підшипниками 26 установлена втулка 13. Лівий підшипник фіксується кільцем 21. Для підведення масла до гідроциліндра в корпусі 14 є два отвори з конічним різьбленням для кріплення шлангів. Для подачі масла в робочі порожнини гідроциліндра в кришці 9 є канали, вихідні отвори яких закриті пробками. Для ущільнення в гідроциліндрі встановлені ущільнювальні кільця 22,23,24.
Патрон, що самоцентрує, працює в такий спосіб. Заготівля встановлюється до упору в опору 8. При подачі повітря в ліву порожнину гідроциліндра клин 4 відходить вправо, підкуркульники сковзають по похилому пазу нагору й кулачок піднімається, закріплюючи заготівлю.
При подачі повітря в праву порожнину гідроциліндра клин 4 відходить уліво, підкуркульники сковзають по похилому пазу долілиць і кулачок опускається, розкріплюючи заготівлю.
8.
Проектування пристосування для контролю биття отвору
8.1
Опис конструкції пристосування
Пристосування призначене для контролю радіального биття отвору корпуса гідроциліндра.
Пристосування містить: плиту 1 до якої по засобом болтів 20 і гайок 23 приєднується чавунна стійка 8. У стійці 8 за допомогою підшипників 6 і втулки 5 базується шпиндель 3, на передньому кінці якого за допомогою болтів 2 кріпиться клиновий патрон 1. На задній кінець шпинделя 3 монтується силовий привод (пневмоцилиндр.) 9 з муфтою 10. З'єднання клинового патрона 1 зі штоком пневмоцилиндра здійснюється за допомогою тяги 4, що проходить через центральний отвір шпинделя. Також пристосування містить: щуп 11, передачу важільну 13, тримач індикатора 14, що кріпиться до передачі важільній гвинтом 21, пружину стиску 22 і індикатор 15, за допомогою яких відбувається вимір і зняття даних; передача важільна 13 кріпиться до опори 17 гвинтами 16, опора у свою чергу прикріплена до плити за допомогою болтів 18 і гайок 19.
Пристосування для контролю биття отвору корпуса гідроциліндра працює в такий спосіб: деталь установлюється й закріплюється в патроні, за допомогою щупа 11 здійснюється контроль биття отвору деталі за рахунок обертання кришки вручну й пересування щупа 11, що забезпечується переміщенням опори 17 по Т-Образних пазах плити 24, дані вимірів контролер зчитує з індикатора годинного типу 15.
9.
Розрахунок і проектування різального інструменту
9.1
Мети й завдання проектування
На токарських операціях застосовуються різці з механічним кріпленням ріжучої пластини за ДСТ 20872-73. Недоліками таких різців є недостатня продуктивність внаслідок низької надійності закріплення ріжучої пластини, великий час заміни пластини. Тому, основне завдання проектування - удосконалення конструкції токарського різця з метою усунення зазначених вище недоліків.
9.2
Проектування й розрахунок різця
Як об'єкт проектування приймемо токарський упорний різець, використовуваний при обробці торцевої поверхні заготівлі на 040 токарській операції.
Як матеріал для корпуса різця вибираємо сталь 40Х с
в
= =690МПа й допустимим напруженням на вигин и. буд.
= 200 МПа, що ріже частина твердий сплав Т15К6.
2. Головна сили різання
Pz
= 10·Cp
·tx
·Sy
·Vn
· Kp
, H (9.1), Kp
= Kмр
·Kj
р
·Kg
р
·Kl
р
(9.2),
де Kмр
= 0,94. Kj
р
-
коефіцієнт, що враховує вплив головного кута в плані, приймаємо по [9]: Kj
р
z
= 0,89; Kj
р
y
= 0,5; Kj
р
x
= 1,17; Kg
р
- коефіцієнт, що враховує вплив переднього кута, приймаємо по [9]: Kg
р
z
= 1,25; Kg
р
y
= 2,0; Kg
р
x
= 2,0. Kl
р
- коефіцієнт, що враховує вплив кута нахилу головної ріжучої крайки, приймаємо по [9]:
Kl
р
z
= 1; Kl
р
y
= 1,25; Kl
р
х
= 0,85.
Kp
z
= 0, 94 ·0,89·1,25·1 = 1,05;
Kp
y
=0,94·0,5·2,0·1,25=0,94;
Kp
x
= 0,94·1,17·2,0·0,85=1,87.
Режими різання на 2-ом переході операції 040: t=0,9мм; S=0,12 мм/об.; V=110м/хв [див. табл.6.6.]
Розрахунок тридцятимільйонні сили різання зробимо за методикою викладеної в [9]: для Pz
:
Cp
= 300; x = 1.0; y= 0.75; n = - 0,15;
для Py
: Cp
= 243; x = 0,9; y= 0.6; n = - 0,3;
для Pх
: Cp
= 339; x = 1.0; y= 0.5; n = - 0,4.
Pz
= 10·300·0,91
·0.120.75
·110-0,15
·1,05 = 2865,6 H;
Py
= 10·243·0,90.9
·0.120.6
·110-0,3
·0.94 = 142 H;
Px
= 10·339·0,91
·0.120.5
·110-0,4
·1,87 = 260,5 H.
3. Розрахунок перетину корпуса різця зробимо за методикою викладеної в [18] з 50. За умови, що державка має квадратний перетин, тобто h??b
Ширину державки визначимо по формулі:
b = (9.3)
де L-Виліт різця, приймаємо L=70 мм.
Підставивши дані у формулу (9.3), одержимо:
b = = 0,0182м = 18,2 мм;
Приймаємо найближчий більший перетин корпуса (b=20мм). Керуючись наведеними співвідношеннями, одержимо висоту корпуса різця h b =20 мм. Приймаємо: h( b??20(20 мм.
4. Перевіряємо корпуса різця на міцність і твердість:
Максимальне навантаження, що допускається міцністю різця:
Pz. доп
. =b×h2
и. буд.
/6×L=20×10-3 (
20 ×10-3
) 2
200 /6×70×10-3
= 914,3 Н
Максимальне навантаження, що допускається твердістю різця:
Pz. ж.
=3f E J /L3
=3 ×0,05×10-3
×2×10 11
×10-3
1,33 ×10-8
/ (70 ×10-3
) 3
=326 Н
де f - допускається стріла, що, прогину різця при чистовому гострінні f=0,05мм
Е - модуль пружності матеріалу корпуса різця Е=2×10 11
Па.
J - момент інерції прямокутного перетину корпуса:
J = bh 3/12
=20×10-3
(20×10-3
) 3/12
=1333 мм 4
Різець має достатню міцність і твердістю, т.до виконується умова: Pz. доп
. Pz
Pz. ж.
914,3 Н 286,5Н326 Н - умова виконується.
5. Конструктивні розміри різця беремо за ДСТ 20872-80; загальна довжина різця L=150 мм; ріжуча пластина із твердого сплаву Т15К6 № 01114-220408, за ДСТ 19046-80.
6. Геометричні параметри леза різця: головний кут у плані 93
7. За ДСТ 5688-61 приймаємо: якість обробки (параметри шорсткості) передньої й задньої поверхні леза різця й опорної поверхні корпуса; граничні відхилення габаритних розмірів різця; марку твердого сплаву пластини й матеріалу корпуса; зміст і місце маркування.
8. Вибираємо матеріал різця: для корпуса - сталь 40Х (твердість 40...45 HRCЕ), оксидувати, для пластини - твердий сплав Т15К6 для гвинта й гайки - сталь 45 (головку гвинта, скіс, ролик до 32...37 HRCЕ).
9. Технічні вимоги на різець приймаємо за ДСТ 266613-85.
Для вдосконалення конструкції різця змінимо, спосіб кріплення ріжучої пластини, це дозволить підвищити надійність кріплення пластини й знизити час заміни пластини. Пластина в стані витримати велике зусилля різання, що дозволяє збільшити подачу інструмента, а отже, і продуктивність обробки. Скорочується час на заміну або поворот ріжучої пластини при затупленні. Різець зручний в експлуатації, простий по конструкції, не складний у виготовленні.
9.3
Опис конструкції різця
Різець токарський збірний з механічним кріпленням пластини 2 містить державку 1, у різьбові отвори якої загвинчені гвинти 7 і 8, які служать для регулювання положення різця. Для закріплення пластини служить гвинт 3 з гайкою 6 і шайбою 5, що своїм скосом упирається в ролик 4.
Складальне креслення різця із вказівкою всіх граничних відхилень і технічних вимог представлений на аркуші графічної частини дипломного проекту.
10.
Лінійна оптимізація режимів різання на токарській операції
10.1
Вихідні дані
Перехід чистового гостріння отвору пов. Æ39,828+0,062 мм на токарно-гвинторізному верстаті 16Б16П різцем з кут у плані - = 600
.
оброблюваний матеріал - сталь 45Л ДЕРЖСТАНДАРТ 977-75;
межа міцності матеріалу інструмента = 690 МПа;
діаметр оброблюваної поверхні -. Æ39,828+0,062 мм;
різальний інструмент - Різець розточувальної із пластинами із твердого сплаву за ДСТ 18882-73, Т15К6;
головний кут у плані - = 600
;
6) глибина різання - t = 0,26мм;
7) устаткування - токарський - гвинторізний верстат 16Б16П:
7.1) потужність електродвигуна = 8 кВт;
7.2) Подача мінімальна (хвилинна) = 2 мм/хв;
Подача максимальна (хвилинна) = 1200 мм/хв;
7.3) Частота обертання мінімальна = 20 об./хв;
Частота обертання максимальна = 2000 об./хв.
10.2 Розрахунок обмежень
10.2.1 Обмеження по кінематиці верстата
а) Розрахуємо обмеження, що встановлюють зв'язок між розрахунковою подачею й кінематичними, відповідно мінімальними й максимальними, можливостями верстата: 
> , мм
/об.
; ; ;
 , мм
/об.
; ; ;
; 
; 
.
б) Розрахуємо обмеження, що встановлюють зв'язок між швидкістю різання й кінематичними, відповідно мінімальними й максимальними, можливостями верстата:
, , ,
  
.

мал.10.1. Обмеження по кінематиці верстата
10.2.2 Обмеження по потужності привода головного руху:
(10.1)
(10.2)






Мал..10.2.Обмеження по потужності привода головного руху
10.2.3 Обмеження по температурі в зоні різання
(10.3)
, 

Мал..10.3. Обмеження по температурі в зоні різання
10.2.4 Обмеження по точності:
, (10.4)
де ? - допуск на діаметр, мм;
g - коефіцієнт, що враховує спосіб установки заготівлі, приймаємо g=3 (для установки заготівлі в патроні);
t - глибина різання;
D - діаметр оброблюваного отвору;
l - довжина заготівлі;
kу
- коефіцієнт, що враховує вплив геометрії різального інструменту на тридцятилітній сили різання Ру
. Коефіцієнт kу
визначаємо по формулі:
kу
= kуγ
· kуφ
· kуλ
· kуr
(10.5)
де kуγ -
коефіцієнт, що враховує вплив на Ру
переднього кута, приймаємо kуγ
=1,35;
kуφ
- коефіцієнт, що враховує вплив на Ру
головного кута в плані, приймаємо kуφ
=0,75;
kуλ
- коефіцієнт, що враховує вплив на Ру
кута нахилу ріжучої крайки, приймаємо kуλ
=0,75;
kуr
- коефіцієнт, що враховує вплив на Ру
радіуса при вершині різця, приймаємо kуr
=1.
Підставивши певні значення у формулу (10.5) і нерівність (10.4), одержимо:
kу
=1,35·0,75?0,75?1=0,76;







логарифмуємо вираження:
0,6?lg (100S) - 0,3? lg V ? lg 11,76
Нехай lg (100S) =x1
; lg V =x2
, тоді
0,6· x1
-0,3· x2
≤ 1,069
2x1
- x2
≤ 3,56

Мал.10.4.Обмеження по точності
10.2.5 Обмеження по стійкості інструмента
,
де Сv
=350, табл.17, стор.270 [12] ;
x=0.15, табл.17, стор.270 [12] ;
y=0.35, табл.17, стор.270 [12] ;
m=0.2, табл.17, стор.270 [12] ;
KV
=1,72·1,0·1,0·1,0=1,72.


Мал..10.5.Обмеження по стійкості інструмента
10.2.6 Розрахунок цільової функції:
(10.6)
 

10.3
Рішення графічним методом
Система обмежень:
(10.7)
На графіку (див. аркуш графічної частини №) побудуємо систему обмежень і цільову функцію.
Знайдемо оптимальну крапку, тобто ту, у якій цільова функція Z буде максимальною. Розглянемо крапки фігури, найбільш вилучені від початку координат - крапки А, Б и В.
Визначимо їхньої координати:
т. А:  , т. Б:  
т. В:  
Знайдемо значення цільової функції в цих крапках:



ZБ
®max Þ т. Б - оптимальна.
Розрахуємо швидкість різання й подачу, використовуючи отримані дані:

Звідси:   
Висновок
При розробці дипломного проекту запропоновані наступні шляхи вдосконалювання технічного процесу:
розроблено новий технологічний процес виготовлення деталі в умовах середнє серійного виробництва;
розроблено заготівлю, отримана методом лиття в земляні форми;
визначено оптимальні режими проведення обробки на токарській операції;
спроектовано різець із механічним кріпленням ріжучої пластини, застосування якого дозволить скоротити час заміни ріжучої пластини й підвищити надійність кріплення ріжучої пластини;
спроектовано пристосування для контролю биття отвору;
спроектовано патрон токарський клинової з торцевим піджимом.
Зміни, внесені в технічний процес виготовлення деталі дозволили досягти основних цілей проекту, забезпечити заданий обсяг випуску деталей, знизити собівартість її виготовлення й підвищити якість виготовлення в порівнянні з базовим варіантом технологічного процесу.
Список джерел
1. Марки сталей і сплавів - Під ред. В.Г. Сорокіна – К., 2002
2. Методичні вказівки до виконання курсових проектів по дисципліні "Технологія галузі". Розмірний аналіз технологічних процесів виготовлення деталей машин. Сост. Михайлов А.В. – К., 2002.
3. Методичні вказівки до виконання курсових проектів по дисципліні "Технологія галузі". Сост. Михайлов А.В. – К., 1998
4. Михайлов А.В., Расторгуєв Д.А., Схиртладзе А.Г. Основи проектування технологічних процесів механоскладального виробництва. – К., 2004.
5. ДЕРЖСТАНДАРТ 26645-85. Виливка з металів і сплавів
6. Методичні вказівки: Економічне обґрунтування вибору заготівель при проектуванні заготівель. Сост. Боровков В.М. –К., 1999
7. Методичні вказівки: Вибір маршрутів обробки поверхонь деталей машин. Сост. Михайлов А.В., Пашко Н.М. –К., 2003г
8. Допуски й посадки ДЕРЖСТАНДАРТ25347-82, стр12-25.
9. Довідник технолога-машинобудівника. Т.2/ під ред.А.Г. Косиловой, Р.К. Мещерякова. – К., 2003.
10. Панов А.А. і ін. Обробка металів різанням: Довідник технолога. – К., 2005
|