Московский государственный строительный университет.
Строительно-технологический факультет.
Кафедра технологии вяжущих веществ и бетонов.
Курсовой проект
По дисциплине
«Проектирование предприятий»
Тема: «Завод наружных панелей для 16-ти этажных домов»
Москва 2007 г.
Введение
С каждым годом возрастает разнообразие бетонов, вяжущих, заполнителей, технологических приёмов производства сборного и монолитного железобетонов, применяемых в строительстве. Технология бетона заметно развивается. На производстве имеются значительные резервы для его совершенствования. Находят применение новые виды вяжущих, позволяющие обеспечить быстрое твердение бетона, сокращение сроков схватывания, в том числе предварительно напряженного железобетона. Более широко используются в технологии бетона химические добавки, в первую очередь суперпластификаторы и комплексные добавки на их основе. Это позволяет расширить производство высокопрочных и высокоподвижных бетонных смесей, обеспечить значительную экономию цемента, улучшает условия труда на предприятиях, а также способствует механизации и автоматизации производства. Производится значительная модернизация оборудования для приготовления бетонной смеси с комплексной автоматизацией процесса, с использованием активации цемента, сухих смесей, приближения приготовления бетонной смеси к посту её укладки. При формовании сборного железобетона получает более широкое развитие применение низкочастотных режимов виброколебаний с частотой до 25 Гц. Нуждается в дальнейшем совершенствовании технология отделки железобетонных изделий, повышение качества их поверхности. Необходимо многое сделать в улучшении тепловлажностной обработки изделий, сокращении топливно-энергетических затрат на этот процесс. Наряду с модернизацией пропарочных камер с целью сокращения теплопотерь будут внедрятся более прогрессивные режимы тепловой обработки с использованием средств её автоматизации, применяться эффективные способы тепловой обработки с использованием природного газа, солнечной энергии и других ,более совершенных теплоносителей. В производстве сборного железобетона будут развиваться конвейерная и кассетно-конвейерная технологии, технологические линии с непрерывным армированием изделий, линии безопалубочного изготовления предварительно напряженных изделий на специальных стендах, производство изделий с использованием высокоподвижных и литых бетонных смесей.
В настоящее время увеличивается объём изготовления конструкций из монолитного бетона. Использование эффективной инвентарной опалубки, арматурных каркасов заводского изготовления, сухих бетонных смесей, эффективных способов приготовления и транспортирования бетонных смесей, комплектов химических добавок, обеспечивающих твердение бетона при широких изменениях температуры - все это позволяет существенно повысить эффективность монолитного бетона.
Сегодня необходим творческий подход к решению задач технологии бетона, позволяющей коренным образом перестроить и усовершенствовать производство сборного и монолитного железобетона. Достижения науки и техники в области технологии бетона открывают широкие возможности для работы в этом направлении. По условиям транспортного оборудования длина элементов, как правило, не превышает 25м, ширина 3 м, масса 25 т. Армируют изделия в основном сварными сетками, каркасам и укрупненными арматурными блоками.
Панели наружных стен изготавливаются сплошными или с оконными и дверными проёмами, однослойными из легкого бетона на пористом заполнителе 700-1000 кг/мЗ, марок М50-М100, а также из ячеистого бетона плотностью 550-700 кг/м3
, марок М35 и М5
Панели наружных стен жилых домов производят размером на комнату или на две комнаты с двумя оконными проёмами. Для облегчения наружных стен и повышения их термоизоляции применяют трехслойные панели с наружным и внутренним слоем из легкого бетона и утеплителем, толщина таких стен снижается до 300-250 мм, а масса -до 50%.
Выбор метода изготовления различных изделий и конструкций зависит от номенклатуры, технологических особенностей каждого метода и объёма производства. При этом решающее значение имеют технико-экономические показатели производства конкретных изделий тем или иным методом. Однотипные изделия различают по типоразмерам, если размеры и конструкция различны, а также по маркам, если изделие одного типоразмера имеют различное армирование, закладные детали или технологические отверстия. Оптимальная мощность, обеспечивающая лучшую рентабельность предприятия, определяется капиталовложениями, себестоимостью продукции и транспортными расходами. С увеличением мощности предприятия в 2 раза удельные капиталовложения уменьшаются на 15-20%, а себестоимость сборного железобетона снижается на 5-8%. В промышленности сборного железобетона в зависимости от номенклатуры и вида изготовленной продукции различают следующие типы предприятий: специализированные домостроительные комбинаты (ДСК); заводы и цеха крупнопанельного домостроения (КПД); заводы объёмно-блочного домостроения (ОБД), заводостроительные комбинаты, сельские строительные комбинаты (ССК), узкоспециализированные заводы и цеха по производству труб, шпал, опор ЛЭП и других изделий специального назначения, универсальные заводы железобетонных изделий, полигоны железобетонных изделий. В нашем случае цех по изготовлению стеновых панелей относится к ДСК. Эти комбинаты выпускают комплекты изделий и конструкций для различных типов жилых домов: наружные и внутренние стены, плиты перекрытий и покрытий, санитарно-технические кабины, лестничные марши, доборные элементы. Помимо этого подобные предприятия и организации осуществляют монтаж этих элементов и конструкций. Таким образом, конечная продукция ДСК - жилой дом.
В нашей стране накоплен опыт крупнопанельного домостроения и разработаны типовые проекты комбинатов мощностью на 100-140 тыс. м жилой площади в год, которые рассчитаны на изготовление нескольких типов 9-16 этажных домов и выше.
1. Номенклатура изготовляемой продукции
При выборе номенклатуры изделий за основу принимаются следующие показатели: распространение крупнопанельного жилищного, культурно бытового строительства, что приводит к увеличению применения наружных панелей; повышение этажности зданий и более широкое внедрение каркасной схемы в жилищном гражданском строительстве, уменьшение сборного железобетона на фундаменты; более широкое использование сборного железобетона для строительства инженерных сооружений, подземных коммуникаций и т.п., что вызывает повышение производства специальных железобетонных изделий; увеличение объёмов производства предварительно напряженных конструкций; развитие производства объёмно-блочного домостроения.
Наружные стеновые панели относятся к плоскостным конструкциям. По условиям транспортного оборудования длина элементов, как правило, не превышает 25 м, ширина 3 м и масса 25 тонн. Сечение изделий назначают из условия эффективности и работы род нагрузкой с учетом технологичности изготовления. Армируют элементы в основном сварными сетками и каркасами, но по возможности укрупненными арматурными блоками. Для устройства стыков элементов конструкций широко применяют выпуск из бетона концов арматурных стержней. В соответствии с требованиями наружные стеновые панели из керамзитобетона должны изготавливаться по ГОСТ 11024-72.
Эскизы наружных стеновых панелей из керамзитобетона
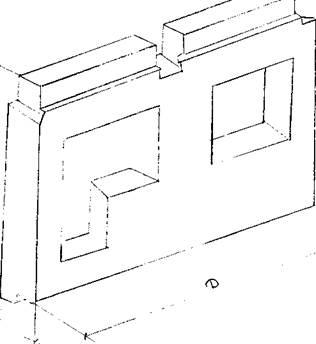
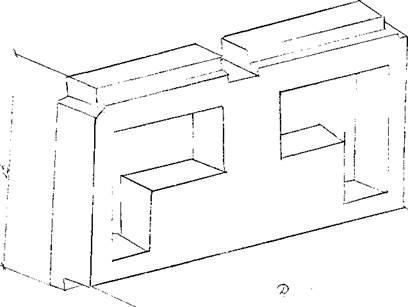
2. Определение потребности цеха в сырье, материалах и полуфабрикатах
Для приготовления лёгких бетонов используют различные виды пористых заполнителей: искусственные (керамзит, аглопорит, перлит, шлаковую пемзу и др.) и естественные (туф, пемзу и др.). Лёгкие бетоны на пористых заполнителях применяют в ограждающих конструкциях для снижения собственной массы несущих конструкций.
Пористые неорганические заполнители применяют для изготовления лёгких бетонов плотностью 500-1800кг/м3
Насыпная плотность заполнителей должна быть не более 1000 кг/м для гравия и щебня (крупностью более 5 мм.) и не более 1200кг/м для песка (крупностью до 5 мм.). К крупному пористому заполнителю предъявляются требования по качеству: содержание водорастворимых сернистых и сернокислых соединений не более 1%, потеря массы после 15 циклов замораживания и оттаивания для бетонов с Мрз150 -менее 10%, коэффициент размягчения в конструкционно-теплоизоляционных материалах 0,6.
В производстве наружных стеновых панелей используется керамзитобетон. Мелким заполнителем для бетона является кварцевый песок, который должен удовлетворять требованиям ГОСТ 8736-72 и может применяться в естественном состоянии фракционным или обогащенным. Допускается применение песков, полученных только дроблением и фракционированием горных пород. В природном песке содержание зёрен, проходящих через сито с сеткой № 014, допускается до 20% по массе.
Для приготовления керамзитобетона применяют портландцемент марки 400. К нему предъявляются следующие требования: портландцемент должен выдержать испытания на равномерность изменения объёма при кипячении в воде. Начало схватывания должно быть не ранее 45 минут, а конец не позднее 10 часов. Тонкость помола определяют по остатку на сите №008 (ГОСТ 3584-73), который не должен превышать 15% массы просеянного цемента. Содержание в клинкер S03 должно быть не более 3,5%; MgO -не более 5%. Цемент не должен иметь ложного схватывания.
С целью снижения средней плотности бетона применяют воздухововлекающие добавки (СДО).
Для приготовления бетона марки 60 используют следующие материалы
Цемент = 220 кг/м3
;
Вода = 210 дм /м3
;
Керамзит = 612 кг/м3
;
Песок =135 кг/м3
;
Добавка = 0.07%.
Таблица расхода сырьевых материалов
№п.п
|
Наименование сырья
Или полуфабриката
|
Ед. изм.
|
Расход на единицу продукции
|
Расходы:
|
|
|
|
|
В час
|
В смену
|
В сутки
|
В год
|
1
|
Цемент
|
кг
|
719,04
|
4306,4
|
34440
|
68908
|
16882712
|
2
|
Песок
|
кг
|
354,38
|
2122,4
|
16974
|
33961,8
|
8320765,2
|
3
|
Керамзит
|
кг
|
1386,72
|
8305,2
|
66420
|
132894
|
32559516
|
4
|
Вода
|
кг
|
539,28
|
3229,8
|
25830
|
51681
|
12662034
|
5
|
Арматурная сталь
|
кг
|
96,72
|
268,4
|
2147,35
|
4294,7
|
1116623,8
|
З. Технико-экономическое обоснование выбора способа производства
1 .Вид технологической линии...................................... конвейерная
2. Количество рабочих часов в сутках.......................... 16
3. Количество рабочих дней в году............................... 260
4. Объём одновременно формуемых изделий в м ........ 4,64
5. Количество рабочих (в сутках).................................... 30
6. Ритм движения конвейера............................................. 45
7. Время ТВО, в часах...................................................... 11
3. Количество ярусов в пропарочной камере.................. 1
9. Часовая ставка рабочего-сдельщика в руб.................... 10
10. Стоимость бетонной смеси в руб/м'........................... 500
11. Расход арматуры в т. на 1 м3
изделия......................... 0,02084
12.Стоимость оборудования в руб................................... 2970000
13.Количество пара в т. на 1 м изделия............................ 0,23
14.Расход электроэнергии в кВт/час.................................. 12
15 .Производственная площадь цеха, м ........................... 2600
16. Сметная стоимость строительства в руб/м2
................ 1155
17. Количество постов.......................................................... 9
Результаты расчетов
1 .Производительность линии, м /год.............................. 25736,53
2.Количество камер.......................................................... 2
3. Количество форм........................................................... 26
4. Цеховые расходы......................................................... 66,14
5. Общезаводские расходы............................................... 0,303
б. Удельные капиталовложения........................................ 159,42
7. Себестоимость единицы продукции............................. 162,55
8. Приведенные затраты................................................... 181,68
4. Разработка и описание технологической схемы производства
Типы линий и их число выбирают в зависимости от заданной номенклатуры изделий, мощности предприятия или цеха. Выбор технологической линии и оборудования начинается с анализа степени совместимости конструктивных и технологических параметров изделий в процессе их формования и твердения.
Для большинства железобетонных изделий учитывают следующие параметры: вид, марку бетона, форму изделий и характер сечения, геометрические размеры и допустимые отклонения от них, вид армирования, насыщенность арматурой и закладными деталями, массу изделия, чистоту поверхности.
Для производства наружных стеновых панелей из керамзитобетона я выбираю конвейерный способ производства.
Конвейерный способ - это усовершенствованный агрегатно-поточный способ производства железобетонных изделий. При конвейерном способе производства технологический процесс расчленяется на элементарные процессы, которые выполняются одновременно на отдельных рабочих постах.
При конвейерном способе формы с изделиями перемещаются от одного поста к другому специальными транспортными устройствами, каждое рабочее место обслуживается закрепленным за ним звеном. Для конвейера характерен принудительный ритм работы, т.к. необходимо одновременное перемещение всех форм по замкнутому циклу с заданной скоростью. Весь процесс изготовления изделии разделяется на технологические операции, причем одна или несколько из них выполняется на определенном посту. Тепловые агрегаты являются частью конвейерного кольца и работают в его системе также в принудительном ритме. Это обуславливает одинаковые или кратные расстояния между технологическими постами (шаг конвейера), одинаковые габариты форм и развернутую длину тепловых агрегатов.
Конвейерные линии по характеру работы могут быть периодического или непрерывного действия, по способу транспортирования - с формами, передвигающимися по рельсам или роликовым конвейером, с формами, образуемыми стальной непрерывной лентой или составленными из ряда элементов и бортовой оснастки; по расположению тепловых агрегатов: параллельно конвейеру, в вертикальной или горизонтальной плоскости, а также в его формовочной части. Наибольшее применение получили конвейеры периодического действия с формами, передвигающимися по рельсам и образующими непрерывную конвейерную линию из 6-15 потов, оборудованных машинами для выполнения операций технологического процесса. Скорость перемещения 0,9-1,3м/с; после выполнения одного элементного цикла вся цепь тележек-поддонов перемещается на длину одного поста; для формования изделия используют современные машины и оборудование, при необходимости выделяют пост для укладки отделочного слоя; по всем постам подают материалы и полуфабрикаты (бетонную смесь, раствор, арматурные каркасы, облицовочную плитку и др.).
Тележечные конвейерные линии различаются между собой формовочным оборудованием и способами тепловой обработки и делятся на линии со щелевыми подземными камерами, с камерой вертикального типа, с бескамерной тепловой обработкой.
Двухветвевая конвейерная линия, размещённая в унифицированном пролёте, включает посты распалубки и сборки форм, подвесное формовочное оборудование на эстакаде, подземные щелевые камеры, портальные манипуляторы для вспомогательных операций, едином транспортном потоке с основной линией решён конвейер отделки с минимальным числом крановых операций. Такая линия обеспечивает компактность технологического процесса, рациональную организацию транспортных потоков, что значительно повышает эффективность. Рациональными областями применения конвейерных технологических линий следует считать специализированное производство изделий одного вида и типа панели перекрытий и покрытий, аэродромных и дорожных плит, панелей внутренних стен наружных стеновых панелей, железобетонных шпал. Наружные стеновые керамзитобетонные панели изготавливают на конвейерах с максимальной механизацией и автоматизацией производства. Конвейер состоит из двух линий: формования и тепловой обработки с доводкой изделий.
Транспортная часть каждой линии состоит из не приводного роликового конвейера форм тележек и цепного привода. Формы передаются с одной линии на другую с помощью самоходных передаточных тележек, на каждом посту форму с изделием устанавливают в строго заданном положении гидравлическими фиксаторами. Конвейер работает с ритмом 15-20 минут.
Цикл работы начинается с очистки форм, затем форма поступает на пост укладки керамических ковров. В процессе перемещения формы, боковые грани, вкладыши и борта, откинутые на 90°, покрываются смазкой с помощь форсунок.
Пост оборудован шарнирно-рычажными механизмами для закрывания бортов и замков с помощью гидроцилиндров. На постах укладки керамических плиток, установки арматурных каркасов и закладных деталей на слой керамических плиток укладывают слой раствора и устанавливают арматурный каркас, закладные детали и оконные вкладыши. На посту укладки и уплотнения керамзитобетонной смеси имеется виброформующая машина с вибронасадкой, на соседнем посту раствороукладчик укладывает верхний слой раствора толщиной 5-10 мм., который заглаживают приводным валком. Затем форму с помощью траверсной тележки перемещают на линию загрузки камеры твердения. Далее из отформованного изделия извлекают верхние оконные вкладыши, после чего обрабатывают откосы оконных проёмов. Очищенные и смазанные вкладыши передают на пост формования.
Щелевая камера тепловой обработки работает в одном режиме с конвейером продолжительность тепловой обработки 7-15 ч., расход пара на 1 м изделия 90-130 кг. После тепловой обработки на посту открывают борта форм. На следующем посту форму с изделием устанавливают кантователем в вертикальное положение, изделие навешивается на траверсы и подается на пост отделки, а форма возвращается в исходное положение и цикл повторяется.
Хранение цемента
Цемент поступает железнодорожным транспортом. На заводах ЖБИ цемент хранится в силосных складах закрытого типа. Цемент должен хранится строго по маркам. В расходный бункер в БСУ цемент поступает при помощи пневмотранспорта. Этот способ более совершенен. Ёмкость силосов определяется НТО.
Хранение керамзитового гравия
Гравий поступает железнодорожным транспортом. Приёмку и хранение керамзитового гравия производят в полубункерном эстакадно-траншейном складе, строго по фракциям (отдельно фракция 5-10 и 10-20 мм). Керамзитовый гравий выдают со склада через устроенные в перекрытии галереи и с помощью ленточных конвейеров подают в расходные бункера керамзитового гравия в БСУ. Объём бункеров определяется НТП.
Хранение кварцевого песка Песок поступает автотранспортом, хранится на таком же складе, что и керамзитовый гравий, и таким лее способом подаётся в расходные бункера песка в БСУ. На складе заполнителей в зимнее время происходит подогрев песка.
Температура колеблется в зависимости от марки цемента и его вида. Температура не должна превышать 50°С. Объём бункеров определяется НТП.
Создание запаса цемента
Цемент из силосов автоматизированного прирельсового склада поступает, с помощью пневмотранспорта, в расходный бункер на участок приготовления бетонной смеси. Бункер должен быть снабжен указателем уровня. Ёмкость его определяется НТП.
Создание запаса песка
Песок из приёмных подает через питатель и ленточный конвейер в расходный бункер н участок приготовления бетонной смеси. Бункер должен быть снабжен указателем уровня. Ёмкость бункера определяется НТП.
Создание запаса керамзитового гравия
Керамзитовый гравий подается через питатель и ленточный конвейер в расходный бункер на участок приготовления бетонной смеси. Бункер должен быть снабжен указателем уровня. Ёмкость бункера определяется НТП.
Создание запаса воды Вода из магистрального водопровода поступает в ёмкость запаса воды для приготовлении керамзитобетонной смеси, снабженной указателем уровня и устройством автоматического наполнения при снижении уровня до минимального. Габариты ёмкости определяются НТП. Емкость должна быть снабжена нагревателем и устройством автоматического регулирования, позволяющим поддерживать её температуру в пределах от 30 до 50°С с точностью до±2°С.
Дозирование цемента Цемент из расходного бункера взвешивают автоматическим весовым дозатором. Точность дозирования ±2%. Взвешенная порция цемента, выгружается в бетономешалку принудительного действия, находящуюся на посту загрузки.
Дозирование песка Песок из бункера запаса взвешивают автоматическим весовым дозатором. Точность дозирования ±2,5%. взвешенная порция песка выгружается в бетономешалку принудительного действия, находящуюся на посту загрузки.
Дозирование керамзитового гравия Дозирование керамзитового гравия осуществляется объёмно-весовыми дозаторами с точностью дозирования ±2,5%. Взвешенная порция керамзитового гравия выгружается в бетономешалку принудительного действия, находящуюся на посту загрузки.
Дозирование воды Дозирование воды осуществляется весовыми дозаторами с точностью дозирования ±2%. Взвешенная порция воды выгружается в бетономешалку принудительного действия, находящуюся на посту загрузки.
Приготовление бетонной и растворной смеси
Приготовление бетонной и растворной смеси производится в бетоносмесителе принудительного действия. Перемешивание продолжается до получения требуемой консистенции. Минимальное время перемешивания 180 секунд. Сперва в смеситель загружается керамзит и песок, потом добавляется цемент, после этого заливают воду. Для обеспечения положительной температуры смеси в зимнее время осуществляется подогрев воды затворения до температуры не более 70°С.
Транспортирование бетонной и растворной смеси
Транспортирование бетонной и растворной смеси от смесителя к месту укладки производится бетоновозной тележкой. Время от приготовления бетонной смеси до её укладки 30 минут. Кроме того, доставку смеси производят ленточными конвейерами и питателями и т.д.. На заводах ЖБИ начинают применять адресную подачу бетонной смеси.
Укладка бетонной смеси
Бетонная смесь из раздаточного бункера укладывается в форму, установленную и закреплённую на виброплощадке. В этот момент включают вибраторы. Виброплощадка равномерно распределяет бетонную смесь по форме и уплотняет её. Отформованная плита заглаживается рейкой, перемещающейся в поперечном направлении. Укладку бетона в горизонтально расположенную форму производят при высоте падения не более 1 метра.
Технологическая выдержка перед укладкой раствора
Чтобы раствор не осел в свежеотформованный керамзитобетон с воздухововлекающей добавкой, делается выдержка перед укладкой раствора в форму.
Укладка растворной смеси Для обеспечения требуемого качества верхней поверхности наружных стен, на нее укладывают цементно-песчаный раствор подвижностью 0-3 см. Укладывают его при помощи раствороукладчика с затирочным валом.
Технологическая выдержка перед ТВО Перед тепловой обработкой необходимо произвести выдержку изделия. Она позволяет бетону приобрести первоначальную пригодность, способствующую снижению температурных напряжений возникающих в бетоне при увеличении температуры в камере ТВО. Продолжительность выдержки 80 минут.
Тепловая обработка Тепловая обработка изделий производится в щелевой пропарочной камере. Щелевая камера находится ниже уровня земли, под конвейерной линией. Изделия попадают по конвейерной линии в щелевую камеру при помощи снижателя, а обратно при помощи подъёмника.
Небольшая высота камер исключает возможность перепада температур среды в поперечном сечении и создаёт одинаковые температурно-влажностные условия твердения для каждого изделия. Температура паро-воздушной среды камер контролируют термометрами, расположенными равномерно по длине камеры в верхнем нижнем ярусе.
Недостатком камер непрерывного действия являются значительные (до 25%) теплопотери в следствие утечки пара через торцы.
Кантование и транспортирование изделий
При помощи кантователя форма приводится в вертикальное положение для распалубки. Последняя производится мостовым краном, оснащенным траверсой с захватом. Далее изделие краном транспортируется на линию отделки.
Чистка, смазка форм
Чистка форм производится при помощи щеточной машины с применением сжатого воздуха. Смазка форм осуществляется удочкой- распылителем( в качестве смазки используется эмульсол).
Укладка арматуры Арматурные каркасы, закладные детали, подъёмные петли укладываются согласно проектным чертежам.
Отделка изделий Отделочная линия является монорельсовым конвейером, состоящим из трех постов: очистка плитки от подтёков цемента и бумаги; очистка откосов от наплывов; приём ОТК.
Складирование На склад готовой продукции изделия поступают на самоходной тележке. Изделия хранят на складе, оборудованном крановым хозяйством и имеющим подъездные пути. Панели следует хранить в рабочем положении. Между панелями должны быть уложены деревянные прокладки прямоугольного сечения толщиной не менее 30 мм. Прокладки под нижний ряд панелей следует укладывать по плотному, тщательно выровненному основанию. Прокладки всех вышележащих панелей должны быть расположены по вертикали одна под другой вблизи монтажных петель.
Керамзитобетонные панели укладываются в штабеля высотой до 2,5 м с прокладками и подкладками. При хранении панели должны быть рассортированы по маркам. На боковой грани каждой панели должно быть нанесено несмываемой краской: краткое наименование предприятия-изготовления, марка панели, дата изготовления, масса изделия. Все операции, связанные с погрузкой, разгрузкой и складированием панелей, должны производиться с соблюдением мер, исключающих возможность их повреждения.
5. Технологический расчет
5.1 Расчет ёмкости склада цемента
Определение запаса цемента на складе производят по формуле, кг:
С= (П х С1 х 3u
x 1,01) / (365 х 0,9)
Где П - годовая производительность завода, м3
; С1-средний расход цемента на 1 м изделий, принимаю на основании таблицы "Норма расхода цемента" Ci = 240кг/м3
;
Зц - запас цемента. В связи с тем, что цемент будет транспортироваться железнодорожным транспортом, принимаю Зц — 10 суток;
1,01- коэффициент, учитывающий потери при разгрузке и транспортных операциях; 0,9 - коэффициент заполнения силосов;
365 - расчетный годовой фонд времени работы оборудования, сут. Число силосов для хранения цемента на данном предприятии производительностью 50000 м3
/год принимаю равным N = 4, Емкость каждого силоса определяют по формуле:
С
В = —,где
N
С - требуемый запас цемента на складе, кг;
N - число силосов, шт.
На основании расчета на ЭВМ были получены следующие данные:
Годовая производительность завода = 50000 м3
;"
Средний расход цемента на 1 м изделия = 240 кг/м ;
Запас цемента -10 суток;
Количество принятых силосов = 4 шт;
Требуемый запас цемента на складе - 368949,8 кг;
Ёмкость каждого силоса - 92237,44 кг.
5.2 Расчет площади склада заполнителей
Определение производственных запасов заполнителей, м
Для щебня
А,= П х Р1 х М х 1,02/365
Для песка
А2
=П х Р2
х М х 1,02/365
Р - средний расход соответственно щебня (Pi) и песка (Р2
), принимаю в соответствии нормативным расходом заполнителей Pi =0,9 ;Р2
=0,5;
М - запас заполнителей, т.к. на данное предприятие заполнитель доставляется железнодорожным транспортом, принимаем М = 10 суток;
П - годовая производительность завода, м3
;
1,02 - коэффициент, учитывающий потери при разгрузке и транспортных операциях;
365 - расчетный годовой фонд времени работы оборудования, сут.
Полный запас заполнителей на складе, м , производится по формуле:
А=А1+А2
На основании расчета на ЭВМ были получены следующие данные:
Производственный запас щебня = 1117,8 м ;
Производственный запас песка = 768,49 м ;
Полный запас заполнителей на складе = 1886,3 м3
;
Вид штабеля: конусообразный -1;
Высоту штабеля:
Для щебня принимаю 10 м;
Для песка принимаю 12 м;
Угол естественного откоса 40 градусов;
Количество штабелей щебня = 0,75 (принимаем равным 1)
Количество штабелей песка = 0,29 ( принимаем равным 1)
5.3.Расчет площади склада арматурной стали
Определение суточной потребности в арматурной стали каждого вида, т, исходя из чертежей изделий, производят по формуле
А=А1 х М х 1,04
Где А] - суточная производительность железобетонных изделий, м3
;
М - потребность арматурной стали на одно изделие, т;
1.04 - коэффициент потерь.
Определение площади для складирования арматурной стали, м, производят по формуле
П=( А х Т х 25) / ( Мр
х 25)
Где Т - срок хранения арматурной стали на складе, принимаю Т = 25 суток;
2.5 - коэффициент, учитывающий проходы при хранении стали на стеллажах и в закрытых складах
Мр -масса стали, размещенной на складе.
На основании расчета на ЭВМ были получены следующие данные: Количество арматурной стали на принятый срок хранения = 249,74 т; Площадь склада арматурной стали = 299,69 м2
.
5.4.Расчет площади склада готовой продукции
Определение вместимости склада готовой продукции, м3
, производится по формуле
B=BixT
Где Bi- суточный объём готовых изделий, м ;
Т - продолжительность хранения, принимаю Т = 14 суткам.
Определение площади склада готовой продукции, м2
производят по формуле
П=(ВхК,хК2
)/В2
Где К\- коэффициент, учитывающий площадь склада на проходы и проезды, К,= 1,5;
К2
-коэффициент, учитывающий увеличение склада при применении различных кранов, К2
= 1,3 для мостовых кранов;
В2
-нормативный объём изделий, допускаемый на 1 м площади; В2
=1,8 м На основании расчета на ЭВМ были получены следующие данные: Суточный объём готовых изделий = 192,3 м3
; Продолжительность хранения =14 суток; Коэффициент для крана = 1,3;
Нормативный объём изделий, допускаемый на 1 м2
площади =1,8 м3
; Вместимость склада готовой продукции — 2692,2 м ; Площадь склада готовой продукции = 2916,55 м .
5.5 Расчет бетоносмесительного отделения (цеха)
Определение часовой производительности бетоносмесительного цеха, м3
/ч
Пч
= ( П х 1,4 х 1,2 ) / (260 х Н ) ,где
П - годовая потребность в бетонной смеси, м3
;
1,4 - коэффициент неравномерности работы; 1,2 -коэффициент запаса мощности;
260 - число рабочих дней в году;
Н - число рабочих часов в сутки.
Определение часовой производительности смесительных машин, м час:
ПЧ. М=БхВх 43x0,001
Где Б - вместимость смесительного барабана по загрузке, дм3
;
В - коэффициент выхода бетонной смеси; Чз- число замесов.
Требуемое количество бетоносмесительных машин:
Годовая производительность завода = 50000 м3
/час;
Число рабочих часов в сутки =16 часов;
Вместимость смесительного барабана = 1500 м ;
Плотность бетона = 1000... 1400 кг/м3
;
Вид смеси: бетонные смеси легкие для теплоизоляционного бетона;
Тип смесителя: принудительного действия;
Часовая производительность бетоносмесительного цеха = 21 м /час;
бетоносмесительной машины = 16,88 м3
/час; Количество бетоносмесительных машин = 2 шт; Коэффициент выхода бетонной смеси = 0,75 Число замесов = 15
6. Творческая часть
Приготовление бетонной смеси, её свойства и качество компонентов имеют огромное значение для последующего производства изделий, а также оказывают большое влияние на себестоимость продукции. Одним из самых дорогостоящих компонентов бетонной смеси является цемент. В данном производстве наружных стеновых панелей из легкого бетона применяется портландцемент марки М400. Для экономии цемента предлагается его частичная замена С-3 и наполнителями, в качестве которых используются малоактивные добавки, такие как золы, шлаки, кварцевый песок, другими словами, предполагается использование ВНВ.
Практика показала, что фактически 50% цемента не вступает в реакцию, следовательно, целесообразно заменить определённую часть цемента на более дешевые компоненты, введение которых не скажется на свойствах бетонной смеси и готового изделия, или даже наоборот улучшит их. В данной работе, как было сказано выше, предлагается применение суперпластификатора С-3 и в качестве наполнителя кварцевого песка.
При использовании ВНВ расход цемента уменьшается примерно в 2 раза, что значительно сократит расходы, связанные с применением дорогостоящего вяжущего высокой марки. В данном производстве можно предусмотреть два пути решения получения ВНВ. В первом случае предполагается получение ВНВ непосредственно на проектируемом заводе, путем совместного домола портландцемента с С-3 и наполнителем, но данный вариант влечет за собой дополнительные затраты, а именно увеличение производственных площадей, связанное с размещением технологического оборудования для помола, а также затраты на приобретение данного оборудования. Второй вариант предполагает приобретение готового ВНВ на заводах по производству вяжущих веществ, что влечет за собой затраты на транспортировку и покупку данного вида вяжущего. Однако несмотря на это, применение ВНВ эффективно и с экономической точки зрения получения высококачественных изделий, удовлетворяющих практически всем требованиям по проектированию (с применением ВНВ улучшаются практически все характеристики ЖБИ).
7. Мероприятия по охране окружающей среды
Сборный железобетон в обозримом будущем остается основным элементом в строительстве.
При производстве 1 м сборного железобетона расходуется тепловой энергии 0,4-0,45 Гкал (на 1 Гкал тепловой энергии расходуется 180 кг условного топлива);
воды 5-6 м~, в том числе 3 м" сбрасывается в канализацию;
электроэнергии 40-56 кВт/час, в том числе 50% на выработку сжатого воздуха;
сжатого воздуха 160-200 Им3
.
Эти энергоносители, при использовании их в технологическом процессе производства сборного железобетона увлекают в атмосферу, почву и ближайшие водоёмы углекислый газ, пыль, масла и механические взвеси, а также технологические отходы бетона и железобетона в виде некондиционных и бракованных изделий.
При производстве 1 м"' сборного железобетона в атмосферу выбрасывается около 900 м продуктов сгорания, из которых 10-12% составляет СО2.
Тепловой КПД заводских котельных на газообразном топливе достигает 85-88% и 70-75% на твердом топливе.
Основной частью потерь энергии топлива являются дымовые газы. Задача состоит в том, чтобы понизить температуру уходящих газов до 20-25 °С и полезно использовать тепло, что уменьшит количество сжигаемого топлива.
Для решения этой проблемы на заводе разработана и внедрена установка, узлы которой уже прошли эксплутационные испытания. Тепло уходящих газов от котельных установок, работающих на природном газе, используется в контактных аппаратах, включенных в замкнутый контур теплоснабжения. Дымовые газы из котла подаются в контактный аппарат, где они охлаждаются до температуры 30-40°С и отводятся в атмосферу, а вода нагревается до 60-70°С и подается на теплообменник и дозатор, после чего она поступает в систему отопления и на бойлеры горячего водоснабжения. Затем вода поступает на контактно-поверхностные агрегаты вентиляции и воздушного отопления, где охлаждается до 20-30°С. после чего поступает в бак-аккумулятор, а оттуда насосом подается на повторный цикл.
Конденсат от тепловых агрегатов через локальную очистку поступает в аккумулятор, а оттуда на технические нужды завода.
Значительные объемы неочищенных сточных вод в настоящее время сбрасываются в водоёмы, чем наносится ущерб водным ресурсам. Одним из путей решения этой проблемы является локальная очистка этих вод на предприятиях или группах предприятий. Разработана и но узлам: испытана система очистки промышленных сточных вод, обеспечивающая необходимое качество их сброса в открытые водоёмы или для технических нужд предприятия. Все сточные воды разделяются на два основных потока: производственные от цехов завода;
Промдождевые, в которые входят дождевые воды и промышленные воды, которые по характеру загрязнения аналогичны дождевым. Производственные сточные воды поступают от камер тепловой обработки железобетонных изделий, постов шлифовки лестничных площадок и маршей, от катионовых фильтров котельной.
Промдождевые стоки включают стоки с поверхности дорог, газонов и покрытий крыши, от мойки автомобилей, от складов готовой продукции.
Очистка производственных и промдождевых стоков с оборотным водоснабжением для использования их для мойки автомашин, территорий цехов, затворения бетон производится по технологической схеме.
При подаче цемента от цементовозов до ёмкостей и из ёмкостей до бункеров бетоносмесительных цехов происходит загрязнение атмосферы аспирационным воздухом. На производство 1 м сборного железобетона расходуется в среднем до 0,5 тонн цемента.
На транспортировку I тонны цемента расходуется до 120-150 Нм3
воздуха, а в год для заводах выпуском 300,0 тыс.м сборного железобетона примерно 18,Омлн.м воздуха.
Доведя цемент до бункера, воздух очищается в рукавных фильтрах. От совершенства конструкции и материала фильтров и автоматизации их регенерации зависит качество очистки воздуха от цементной пыли.
Эффективная схема аспирационных систем склада цемента и бетоносмесительных узлов с рукавными фильтрами ФРКИ-30, ФРКИ-90 внедрена на Ростокинском заводе ЖБИ. Испытания фильтров показали, что степень очистки воздуха в них близка к паспортной. В фильтре ФРКИ-30 - 36 рукавов, диаметр рукава 300 мм, длина 2000 мм, эффективная фильтрующая поверхность - 30,24 м2
. В фильтре ФРКИ-90 -108 рукавов, диаметр рукавов 130 мм, длина 2000 мм, эффективная фильтрующая поверхность - 90,72 м2
.
Корпус фильтра сварной. Состоит из стенок с ребрами жесткости. В верхней части корпуса находится штуцер с клапанами для выпуска обеспыленных газов. Внутри корпуса смонтирована плита - носитель рукавных фильтров, под которой расположена камера обеспыленных газов с трубками распределения внутри для импульсивной продувки.
Запыленный воздух направляется в корпус фильтра через нижнюю его часть. Пыль задерживается на фильтрующей ткани, а обеспыленный воздух удаляется через камеру очищенного воздуха в выпускной трубопровод.
Расход воздуха для продувки составляет 0,1-0,2% от количества очищенного воздуха. Нормальная продолжительность работы рукава находится в пределах 8000-10000 часов.
Таким образом, решаются две задачи: охрана воздушного бассейна и сохранение дорогостоящего строительного материала (цемента).
Серьёзным вопросом является также утилизация некондиционных железобетонных изделий. Объём выхода некондиционных железобетонных изделий на заводе составляет 0,2-0,5%. Часть этих изделий реализуется в народном хозяйстве. Остальная часть из-за специфичности их формы не имеет потребителей. Для извлечения из изделия металла, щебня, пригодного для подстилающего слоя дорожных покрытий, насыпей и т.д. существуют технические комплексы.
Технический комплекс состоит из опорной рамы, грузоподъёмного устройства с затворами, системы транспортеров, дробилки, накопительных бункеров. Комплекс перерабатывает некондиционные железобетонные и бетонные изделия. Максимальная производительность при переработке бетонных отходов - 10 м /час, при переработке железобетонных отходов -7м /час. Годовая производительность при двухсменной работе - 25000 м . Материал дробится от 0 до 50 мм. Переработка некондиционных изделий позволяет сохранять почву от завалов железобетонными плитами, получать металл в виде лома.
Экологические мероприятия на заводе сборного железобетона должны пониматься как комплексный процесс внедрения: обоснование норм расхода основных материалов (цемента, стали, гравия, песка и: т.д.); экологически обоснованных схем, агрегатов и технологий при производстве железобетона.
Все перечисленные мероприятия обеспечат: уменьшение заболеваемости трудящихся на предприятии и проживающих в прилегающих районах и, следовательно, сокращение выплат населению из фонда социального страхования за период временной нетрудоспособности, а также уменьшения затрат в сфере здравоохранения на лечение трудящихся от болезней, вызванных загрязнением среды снижение потерь чистой продукции за время болезни трудящихся, занятых в сфере материального производства.
Промышленность сборного железобетона является значительным потребителем энергоресурсов (топливо, вода, электроэнергия) и один из путей экологизации отрасли в целом, что видно на примере завода, есть упорядоченное их использование.
Технология сборного железобетона такова, что не исключает загрязнения атмосферного воздуха, ближайших водоёмов, почвы. Поэтому необходима разработка мероприятий, исключающих отрицательное воздействие на среду обитания человека.
8. Мероприятия по охране труда и противопожарной безопасности
На предприятиях по выпуску керамзитобетонных панелей в целях обеспечения безопасных и нормальных санитарно-гигиенических условий труда следует руководствоваться действующими правилами техники безопасности и производственной санитарии, а также правилами по технике безопасности действующими в каждом ведомстве.
При проведении работ в цехах следует соблюдать правила пожарной безопасности в соответствии с требованиями ГОСТ 12.1.004-76
Концентрация вредных веществ в воздухе рабочей зоны, их температура, влажность, скорость движения потоков установлены ГОСТом 12.1.005-76. Во всех производственных и бытовых помещениях следует устанавливать естественную и искусственную вентиляцию, обеспечивающую чистоту воздуха. Естественное и искусственное освещение цехов и помещений должно соответствовать СНиП 3-4-79.
Уровень вибрации на рабочих местах не должен превышать установленных ГОСТом 12.1.012-78 значений.
Уровень шума на рабочих местах нормируется ГОСТом 12.1.003-83. Общие требования.
Данный технологический процесс должен соответствовать требованиям безопасности по ГОСТ 12.3.002-75* ССБТ «Процессы производственные. Общие требования безопасности», «Правила техники безопасности и производственной санитарии в производстве сборных ж/б и бетонных изделий и конструкций», «Санитарным правилам организации технологических процессов и гигиеническим требованиям к производственному оборудованию», и другим нормативным документам.
При введении новых технологических процессов, применение новых материалов, внедрение новых видов машин, механизмов, оборудования, форм оснастки и инструментов, по которым требования безопасного производства не предусмотрены «Правилам техники безопасности и производственной санитарии в промышленности строительных материалов», администрация предприятия совместно с комитетом профсоюза должны принять меры, обеспечивающие безопасность труда.
Организация и проведение технического процесса должны предусматривать меры безопасности я безвредности для работающего персонала, близ расположенных жилых массивов и окружающей среды.
Производственный процесс должен быть пожаро - и взрывобезопасен.
Средства индивидуальной защиты
Рабочие и служащие, занятые на работах с вредными и опасными условиями труда, также на работах, связанные с загрязнением, должны быть обеспечены средствами индивидуальной защиты (специальной одеждой, специальной обувью, рукавицами, касками, респираторами, противошумными наушниками, защитными очками, предохранительными поясами и др.)
Профессии, для которых предусмотрены средства индивидуальной защиты, номенклатура и сроки пользования средствами защиты индивидуальной по профессиям, определены типовыми отраслевыми нормами, бесплатной выдачи рабочим и служащим специально одежды, специальной обуви и других средств индивидуальной защиты.
Выдаваемые в пользования средства индивидуальной защиты должны подходить по размерам рабочим и служащим и соответствовать требованиям государственных, отраслевых или республиканских стандартов; или утвержденным в установленном порядке техническим условиям. Запрещается выдача и использования средств индивидуальной защиты с истекшим сроком годности. Запрещается выполнение работ без использования средств индивидуальной защиты, предусмотренных типовыми отраслевыми норами.
Контроль за обеспечением и использованием работающих средств индивидуальной защиты возлагается на службу техники безопасности предприятия.
Заявки на средства индивидуальной защиты составляются начальником цеха или утверждаются руководителем предприятия. Требования по профессиональному отбору и проверки знаний работающих установленный профессиональной и психофизиологической пригодности к ведению работ, должен осуществляться в соответствии с приказом Минздрава РФ «О порядке проведении предварительных и периодических медицинских осмотров работников и медицинских регламентах допуска к профессии». На предприятии должно быть обеспечено проведения обучения и инструктажа.
Инструктаж по своему содержанию и времени проведения подразделяется на: вводный, первичный, повторный внеплановый, при выполнении работ повышенной опасности -целевой.
Все лица, впервые поступающие на работу или меняющие профессию, перед допуском к самостоятельной работе после прохождения вводного и первичного инструктажем должны пройти обучение по безопасности труда в процессе их профессионально-технической подготовки с последующей сдачей экзаменов и стажировки на рабочем месте.
Знания по безопасности труда работники должны получить при повышении квалификации или обучению вторым профессиям по специальным программам.
Вновь поступающие на работу руководители и специалисты должны пройти проверку знаний не позднее одного месяца после назначения на должность, работающие -периодически, не реже одного раза в три года.
Проверка знаний по охране труда руководителей и специалистов осуществляется комиссиями с участием государственного инспектора по охране труда.
Список использованной литературы.
1. Баженов Ю.М., Комар А.Г. Технология бетонных и железобетонных изделий. М: Стройиздат, 1984,
2. Чаус К.В., Чистов Ю.Д., Лабзина Ю.В. Технология производства строительных материалов, изделий и конструкций: Учеб. для вузов. М, 1988.
З. Стефанов Б.В. Технология бетонных и железобетонных изделий. Киев: В.Ш., 1972.
4. СНиП 3.09.01-85. Производство сборных железобетонных конструкций и изделий. М., ЦИТП, 1985.
5. СНиП 5.01.23-8. Типовые нормы расхода цемента для приготовления бетонов, сборных и монолитных бетонных конструкций и изделий. М., 1989.
6. Баженов Ю.М., Чистов Ю.Д., Чаус К.В., Коровяков В.Ф., Гребеник Е.А Методические указания к выполнению проекта для студентов специальности 290 "Производство строительных материалов, изделий и конструкции". М., 1998. У.Воронин В.В., Алимов Л.А., Чистов Ю.Д., Чумаков Л.Д., Чаус К.В. Методические указания по технологическим расчетам к дипломному проектированию для студентов специальности 2906 "Производство строительных изделий и конструкций". М., 1991.
7. Баженов Ю.М. Технология бетона, уч. для ВУЗов., М. 2002.
|