Вступ
Становлення ринкових відносин і різноманітних форм власності на засоби виробництва вимагають нового якісного підходу до вирішення проблем сільського господарства. Однією з основних проблем є зміщення строків збирання буряка, коли внаслідок вологості ґрунту знижується технологічна і технічна надійність збиральних машин, зменшується їх продуктивність.
В роки засухи різко підвищуються втрати коренеплодів в результаті їх обриву в ґрунті, погіршується очистка коренів від ґрунту.
Механізовані процеси збирання цукрового буряка представляють собою складний комплекс технологічних і виробничих операцій, які включають в себе викопування, обрізку і очистку, збір, укладання, завантаження і транспортування коренів і гички. Процеси збирання вказують визначний вплив на основі агротехнічної характеристики врожаю, конструкції робочих органів і компоновочно-технологічної схеми бурякозбиральної машини.
Виходячи із способів використання продуктів врожаю цукрового буряка як сировини для виробництва цукру і кормів для тварин, бурякозбиральні машини повинні забезпечувати:
а) збирання гички і коренеплодів одночасно або роздільно в стислікалендарні строки;
б) отримання якісної сировини і кормів без ручної праці і при цьому відходи в зрізаних головках не повинні перевищувати 3%, а інші втрати – 2%, забрудненість – 10%, пошкодження коренеплодів повинно бути не більше 10%;
в) високу технологічну надійність і агротехнічну ефективність;
г) необхідну універсальність з точки зору можливого примінення різних варіантів механізованих процесів збирання буряка в залежності від умов;
д) зниження, за рахунок спрощення конструкції, питомої метало- і енергоємності, підвищення загальної надійності виробничих процесів.
В Україні для збирання буряка використовують коренезбиральну машину КC-6Б. На основі цієї машини розробимо викопуючий робочий орган лемішкового типу вібруючої дії.
1. Вимоги до машини, що проектується і умови її експлуатації
1.1
Призначення машини і вихідні вимоги
Машина коренезбиральна самохідна КС-6Б призначена для збирання коренів цукрового буряка, посіяного з шириною міжряддя 45 см. Гичку попередньо зрізують і прибирають спеціальною машиною БМ-6А.
Машина КС-6Б може працювати практично в різних умовах, але висока якість і задана продуктивність досягаються при нормальних ґрунтопогодніх умовах, достатньо високій культурі землеробства і врожайності буряків від 200 до 600 ц/га.
Найбільш вигідними є вологість ґрунту не вище 25% і твердість ґрунту в горизонті 0–20 см не вище 28 кг/см.
Поле цукрового буряка повинно бути вирівняне і чисте від бур'янів; рядки буряка повинні бути прямолінійними; ширина міжрядь повинна бути точно витримана, а відхилення коренів від осьової лінії рядка не повинна перевищувати 3 см.
Дослідами доведено, що найбільший врожай цукрових буряків з максимальним вмістом цукру забезпечується при збиранні їх у період технічної стиглості, коли прирости маси коренеплодів і цукру вже невеликі чи зовсім припиняються і починається значне відмирання листової поверхні. Збирання цукрових буряків в більш пізні терміни вигідні не тільки в зв'язку з збільшенням урожаю і поліпшенням технологічних показників. Коренеплоди пізніших строків збирання найпридатніші для тривалого зберігання. Аналіз погодних умов у районах бурякосіяння України показує, що стійкий перехід температур нижче 5°С настає в період 26 – 31 жовтня. Тому 25 жовтня потрібно вважати терміном завершення збирання цукрових буряків. Початок збирання – 15 вересня [6].
Сучасні виробничо-технічні вимоги, що пред'являються до бурякозбиральних машин визначаються загальними тенденціями переведення процесів виробництва цієї культури на промислову основу, специфічними агробіологічними властивостями вирощування цукрового буряка, обумовленими зміною сортів, широким впровадженням точного посіву, застосуванням хімічних засобів боротьби з бур'янами.
Важливою вимогою є досягнення максимального кінцевого народногосподарського ефекту, що передбачає взаємокомпромісну ув'язку показників роботи комплексу машин для догляду цукрового буряка, збирального навантажувального транспортного і переробного комплексів по експлуатаційним, агротехнічним і економічним критеріям.
В зв'язку з об'єктивним погіршенням рівномірності розподілу коренеплодів в рядку, яке визнане зменшенням норм висіву і механізованим формуванням насаджень, цілеспрямовано пристосувати бурякозбиральні машини для збирання цукрових буряків з підвищеним вирівнюванням її агротехнічних характеристик.
В цей час індустріальні методи збирання цукрового буряка, що розвиваються пред'являють до бурякозбиральних машин вимоги по збільшенню продуктивності, якості, технологічної надійності машин і комплексів, робочих органів і процесів, а також забезпечення в залежності від ґрунтових та природних умов, що склалися.
Враховуючи довгі строки зберігання і переробки буряка, цукровою промисловістю, повністю обґрунтовано висуваються вимоги до підвищення якостей коренеплодів, головним чином до їх обрізки, зниження забрудненості гичкою, землею і зменшення пошкоджень, виконання яких дозволяло б знизити втрати цукрового буряка в два рази.
Виходячи із способів використання продуктів врожаю цукрового буряка як сировини для виробництва цукру і кормів для тварин, бурякозбиральний комбайн повинен забезпечувати:
– збирання коренеплодів в стислі календарні терміни;
– кількість коренів, що залишились в ґрунті після проходу комбайна не повинно перевищувати 1%, а втрачених на його поверхні – 6%. Загальна забрудненість цукрового буряка, що зібраний поточним або перевалочним способом не повинна перевищувати 12%, в тому числі рослинної маси в буряковому ворсі може бути не більше 3%;
– відходів цукристої маси в зрізаних головках коренів повинно бути не більше 5% по масі коренів з пошкодженими глибокими шарами тканини не більше 12% по масі, діаметр обриву повинно бути не більше 3%. Зібрані корені повинні бути придатними для здачі на цукровий завод без ручної доочистки [6];
– високу технологічну надійність (не нижче 0,96) і агротехнічну ефективність в широко варіюючи природних кліматичних умов (при різній врожайності, параметрах посадки, фізичному стані ґрунту і гички, забрудненості полів), в тому числі при екстремальних умовах (при вологості ґрунту 26 – 30% або твердості 290 – 580 Н і врожайності 450 – 700 ц/га);
– необхідну універсальність з точки зору можливості застосування різних варіантів механізованих процесів збирання буряка в залежності від природно-виробничих умов, що склалися;
– інтенсифікацію процесів збирання буряка за рахунок зниження жорстких технологічних обмежень робочих швидкостей і пропускної здатності бурякозбиральної машини;
– зниження за рахунок спрощенню конструкції питомої метало- і енергоємності, підвищення загальної надійності (коефіцієнт готовності не нижче 0,94). Ресурс до капітального ремонту не менше 3-х років;
– конструкція машини повинна бути зручною для обслуговування, регулювання, проведення технічного обслуговування, очищення, ремонту;
– рух по полю так, щоб не залишати не викопаних буряків. Копачі повинні бути відрегульованими на ширину міжрядь 450±3 мм. Оптимальною глибиною підкопування коренів слід рахувати мінімальну глибину (5–8 см), при якій забезпечується повний підбір коренів. Максимальна глибина ходу лемешів до 12 см.
– в порівнянні з аналогом, комбайн повинен забезпечувати зниження металоємкості, зниження затрат праці на його обслуговування. Термін окупності не більше 3 років;
– особливого значення набувають питання збільшення загального інженерно-технічного рішення конструювання бурякозбиральних машин;
– складні вимоги носять комплексний характер і визначають широке коло задач конструктивного і загально – організаційного характеру, що об'єднуються в загальну проблему вдосконалення компоновочно-технологічних схем, робочих органів і інших конструктивних елементів бурякозбирального комбайна.
1.2 Формулювання вимог технічного завдання на проектування машини
Розробляється самохідна коренезбиральна машина, що виконує наступні операції: викопування коренів, очищення їх від домішок, завантаження коренів в транспортний засіб.
Бурякозбиральний комбайн придатний для використання в усіх природно-кліматичних зонах країни, але переважно в зоні Лісостепу, Полісся і Степу. Комбайн є самохідний, його робочі органи приводяться в дію від двигуна СМД-64 експлуатаційна потужність якого 110 кВт [1].
Даний комбайн розробляється з метою підвищення продуктивності праці, зменшення капітальних витрат, покращення виконання технологічних операцій, зменшення затрат ручної праці.
Комбайн повинен відповідати вимогам безпеки викладеним по ГОСТІ 12042–79 [3].
Загальні вимоги безпеки
1. Місця страховки машини повинні бути позначені по ГОСТ 14192–77.
2. Всі частини, що обертаються або рухаються повинні бути захищені кожухами.
3. Рівень шуму на робочому місці не більше 85 дБл.
4. Всі випробовування, регулювання, налагодження, механізмів повинні проводитись при повній зупинці машини. Машина повинна відповідати: конструктивному рішенню; технології виготовлення матеріалів, що використовуються, особливо тих, що в контакті з людиною; рівню художнього конструювання. Ергономічні показники охоплюють зручністъ монтажу, застосування засобів механізації, зручність управління, фактору робочого середовища (рівень шуму, вібрації, загазованості, запиленості, вологості, освітленості), якість документації (повнота і якість викладення).
Самохідний комбайн повинен бути патентно чистим по країнах СНД, Заходу і США.
Усі матеріали і комплектуючі вироби по найменуваннях і марках повинні відповідати закладеним в технічну документацію на бурякозбиральний комбайн ГОСТ іншим інформативним документам. Матеріали, які використовуються для виготовлення самохідного бурякозбирального комбайна, повинні відповідати діючим стандартам міністерства транспортного і с/г машинобудування. Ведучі і керуючі колеса повинні обертатись на своїх осях вільно, органи керування повинні діяти легко і вільно під дією зусилля руки.
Гальмівна система повинна бути заправлена гальмівною рідиною. Болти кріплення редукторів з різьбою М12 повинні бути розтягнені динамометричним ключем з різьбою М18–80…100 Н∙м [2].
Дляі мащення вольниць і поверхонь тертя необхідно використовувати солідол ГОСТ 3 86–76. Для редукторів необхідно використовувати масло ТМ15-ЭФО ТУ38.101.521–75. Вироби і матеріали, що застосовуються, повинні відповідати вимогам не нижче 1-ї категорії якості.
Комбайн повинен працювати посезонно при оптимальних температурах середовища і вологості повітря до 96%. Якісній роботі машини не повинні переш: оджати опади і розтікання ґрунту.
Для бурякозбиральної машини повинні бути встановлені наступні види технічного обслуговування: щоденне технічне обслуговування, ТО-1, ТО-2, після сезонного ТО. Трудомісткість щозмінного технічного обслуговування не повинна перевищувати 0,5 люд.-год. Час готовності бурякозбирального комбайну для використання після транспортування і зберігання визначається часом необхідним для проведення монтажу, налагодження; випробування під навантаженням не повинне складати більше 7 люд. – днів.
На бурякозбиральному комбайні повинно бути нанесено товарний знак підприємства-виготовлювача, або назва підприємства, назва марки і порядковий номер самохідного бурякозбирального комбайна по системі нумерації підприємства-виготовлювача, рік і місяць випуску. Порядковий номер і рік випуску наносяться ударним способом. Монтажне маркування повинне відповідати ГОСТ 24444–80.
Перед упаковуванням всі оброблені і не пофарбовані поверхні збірних одиниць і складових частин повинні бути покриті консервуючим мастилом по ГОС Г 9104–78 і загорнуті в папір по ГОСТ 9589–79. Кріпильні вироби повинні бути вкладені в пакет по ГОСТ 10354–81. Технічна документація повинна бути запакована у водостійкий матеріал по ГОСТ 10354–85 і розміщена у ящику. На кришці ящика надпис «Документація». Комбайн можна доставляти до користувача залізничним, або буксируванням. При виконанні навантажувально-розвантажувальних робіт слід використовувати підйомний кран.
Швидкість транспортування способом буксирування на прямих відрізках доріг 7 км/год., на поворотах – 3 км/год.
Збереження комбайна по ГОСТ 7751–79 в закритих приміщеннях або під навісом. Допускається зберігання на відкритій площадці.
При короткочасному зберіганні (до 90 днів) зберігати комбайн комплексно без розбирання. При цьому відкриті поверхні найбільш відповідальних механізмів і робочих органів законсервувати у відповідності, з вимогами ГОСТу 9.014.78. При довготривалому зберіганні (більше 3-х місяців) ослабити привідні ремені, законсервувати поверхні найбільш відповідальних механізмів по ГОСТу 9.014.78. Комбайн встановити на підставках, а тиск повітря в шинах зменшити до 0,1…0,15 МПа [1].
Самохідний бурякозбиральний комбайн повинен включати наступні вузли: енергетичний засіб, ходову систему, систему автоматичного керування, завантажувальний пристрій.
Габаритні розміри самохідного бурякозбирального комбайна не повинно перевищувати: довжина в робочому і транспортному положенні 6950 мм; ширина в робочому положенні – 4850 мм; ширина в транспортному положенні – 3350 мм; висота в робочому положенні – 3700 мм; висота в транспортному положенні – 3800 мм; маса бурякозбирального комбайна не повинна перевищувати 9200 кг. Усі вузли бурякозбиральної машини повинні комплектуватись запасними деталями.
Комплект інструментів і пристроїв повинен бути достатнім для проведення збирання бурякозбирального комбайна.
Конструкція самохідного бурякозбирального комбайна повинна забезпечувати: продуктивність 1,35 – 2,43 га/год. при робочій швидкості руху 3,27 – 7,7Н км/год., ширину захвату 2,7 м, виконувати за один прохід шість рядків коренів цукрового буряка.
Конструкція самохідного бурякозбирального комбайна повинна забезпечувати якість виконання технічного проекту: кількість коренів, що залишилися в землі після проходження машини не повинна перевищувати 1%, а втрачених на її поверхні 6%. Загальна забрудненість цукрового буряка, що зібраний поточним чи перевалочним способом не повинна перевищувати 12%, в тому числі рослинної маси в буряковому ворсі може бути не більше 3%.
Відходів цукристої маси в зрізаних головках коренів повинна бути не більше 5% по масі, коренів з пошкодженими глибокими шарами тканини – не більше 12% по масі. Діаметр обриву хвостової частини кореня повинен бути не більше 1 см. Коренів з більшим діаметром обриву повинно бути не більше 3%.
1.3 Вихідні дані для проектування і розробки конструкції машини
У більшості бурякосійних господарствах країни цукрові буряки збирають потоковим, перевалочним і потоково-перевалочним способами без ручної доочистки коренів з одиночним збиранням гички при груповому використанні збиральних, навантажувальних і транспортних засобів. Це дозволяє значно знизити затрати праці, а також підвищити валовий збір і якість цукрової сировини.
При поточному способі збирання корені і гичка збиральними машинами подаються на ходу в транспортні засоби. Корені відразу доставляють на бурякозбиральний пункт, а гичку відвозять до місця силосування або згодовування.
При перевалочному способі корені із збиральних машин подають в транспортні самохідні причепи і вивозять до місця тимчасового їх кагатування в межах поля, а потім при появі вільного автотранспорту доставляються на бурякозбиральні пункти.
Поточно-перевалочний спосіб збирання об'єднує два попередніх: частина коренів безпосередньо від збиральних машин вивозиться на бурякозбиральні пункти, а решту вкладають самоскидами в тимчасові польові кагати. Його як правило застосовують при недостатньому забезпеченні господарств автотранспортом. Поточно-перевалочний спосіб дає можливість збільшити виробництво збиральних агрегатів за рахунок своєчасного відвезення коренів.
Групове використання машин при поточно-перевалочному способі збирання дозволяє оперативно маневрувати технічними засобами при поломках, вимушених зупинках збиральних агрегатів, а також організовувати централізоване обслуговування і ремонт техніки.
Гичкозбиральна машина БМ-6А попередньо зрізує гичку і завантажує у транспортні засоби.
Технологічний процес роботи проектованої машини наступний.
За допомогою автомата керування або вручну передні колеса машини направляються точно по центру міжрядь буряка. Завдяки цьому встановлені під кутом один до одного робочі органи лемішкового типу охоплюють корені з обох сторін, заглиблюються на необхідну глибину завдяки коливальним рухом в вертикальній площині інтенсивно деформують шар ґрунту і очищують коренеплоди від землі. Потім завдяки біроту перекидаються буряки на шнековий очисник. Під дією шнеків, які обертаються з різною швидкістю.
Передавальний бітер сприяє кращому заповненню між скребкового простору елеватора і тим самим – підвищенню його продуктивності. Елеватор подає корні в бункер звідки вони стрічковим транспортером передаються на вивантажувальний елеватор, який подає корені в кузов транспортного засобу, що рухається поряд. Для заміни транспортних засобів на ходу передбачена можливість короткочасної (на 20–30 с) зупинки стрічкового транспортера і завантажувального елеватора. При цьому корені накопичуються в невеликому бункері. Після зміни транспортного засобу всі механізми знову включені в роботу.
Проектована машина може використовуватись на всій території України, але переважно у західній області у районах великого бурякосіяння.
До західного лісостепу України входять лісостепові райони Волинської, Рівненської, Львівської, Тернопільської, Івано-франківської, Чернігівської областей.
Найкращими ґрунтами, які поширені в цій зоні є чорноземи (глибокі мало гумусові, неглибокі помірно гумусові, опідзолені). Вони мають значні запаси поживних для рослин речовин, їм властива висока біологічна активність. Ступінь насичення основами високий – 85–92%. На рухомі сполуки фосфору небагаті, тому потребують насамперед фосфорних добрив, з яких найефективнішим є суперфосфат.
Врожаї цукрових буряків на цих ґрунтах вищі, ніж на інших. В цій зоні поширені також перегнійно-карбонатні ґрунти, сформовані на крейдяному марганці. Вони містять 2,5-5,5% перегною, мають лужну реакцію, але характеризуються незначною товщиною гумусного шару (не більше 50 см).
Поширені в цій зоні також темно-сірі, сірі, світло-сірі ґрунти. Темно-сірі ґрунти за механічним складом легкосуглинкові, містять 2–4% гумусу. Краще від інших опідзолених ґрунтів забезпечені рухомими формами поживних речовин.
Кліматичні умови.
Кліматичні райони бурякосійних районів західної України сприятливі для вирощування цукрових буряків. Клімат в цілому помірно-континентальний з м'якою малосніжною зимою, порівняно тривалою весною, дощовим літом та теплою сонячною осінню. В Західному Лісостепу без морозний період триває приблизно 230–240 днів. Температура середньої річки становить +7°С у північній частині і 8°С у південній. В середньому за рік випадає близько 700 мм опадів. Найтепліші місяці липень і серпень, хоча температура повітря і в ці місяці невисока. В кінці жовтня вона знижується, що затримує вегетацію рослин. В другій половині грудня тут наступає зима із сніговим покривом 18–26 см [2].
Урожайність коренів цукрового буряка 250–550 ц/га, гички 240–445 ц/га.
Бурякозбиральний комбайн використовується з 15 вересня по 25 жовтня. Середня кількість опадів за період використання машини 52 мм.
Бур'яни:
· Осот польовий – посівами цукрового буряка наносить шкоду як засмічувач і приманка для довгоносиків;
· Пирій повзучий – один з найбільш шкідливих розповсюджених бур'янів. Сильно осушує ґрунт.
· Хвощ польовий – надає перевагу вологим кислим ґрунтам; сильної шкоди завдають також такі бур'яни як редька дика, Ромашко не пахуча, гірчиця польова.
До моменту збирання цукровий буряк має потовщений конусоподібний головний корінь від якого відходять в сторону (25–30 см) дрібні корені. Основна маса цукру (95–97%) сконцентрована в тілі буряка. Нижня хвостова частина головного кореня входить глибоко в ґрунт і при збиранні, як правило, обривається на діаметрі 8 – 10 мм і залишається в землі.
Матеріал коренеплоду – крихкий, анізотропний, неоднорідний по довжині і поперечному січенні. Поблизу хвостової частини (діаметр 10 – 30 мм) коренеплід менш крихкий і при навантаженні виявляються помітні ознаки пластичної деформації. В цій частині коренеплоду тимчасовий опір матеріалу і критичні кути згину значно більші, а жорсткість на згин менша чим в основної.
Головка кореня цукрового буряка може розміщуватись як нижче рівня (до 30 мм) ґрунту, та і вище його (до 80 мм і більше). Маса кореня цукрового буряка обумовлюється його розмірами і варіюється в широких межах від 0,4 до 0,8 кг.
Сильного пошкодження корені отримують при падінні з висоти більш 1,5 м, що відповідає швидкості співударяння 5,4 м/с. Підкопування коренів, при якому розрихлюється ґрунт різко знижує силу витягування його із ґрунту. Характеристики цукрового буряка приведені в табл. 1.1 [3].
Таблиця 1.1. Усереднено розмірно-вагові і механічні характеристики цукрового буряка
показники |
значення |
Міжряддя, мм |
450 |
Крок, мм |
200–350 |
Висота розміщення головки над рівнем грунту, мм |
15–35 |
Загальна довжина кореня, мм |
1200–1600 |
Діаметр кореня, мм |
80–150 |
Технічна довжина кореня, мм |
220–300 |
Густина кореня, кг/м3
|
550–650 |
Маса кореня, кг |
0,4–0,8 |
Врожайність, ц/га |
250–550 |
Модуль пружності, МПа |
18,4 |
Момент інерції кореня, кг-м2
|
0,053 |
Коефіцієнт питомого опору, Н/мм |
2,16–2,65 |
Питомий опір при згині, МПа |
статичне навантаження |
1,8 |
динамічне навантаження |
1,15 |
Аналогом проектованої машини є бурякозбиральний комбайн КС-6Б. Основні показники комбайна КС-6Б приведені в таблиці 1.2.
Таблиця 1.2
Показники |
Значення |
Ширина захвату, м |
2,7 |
Швидкість руху, км/год |
5–7,78 |
Час повороту, хв. |
0,78 |
Ємність технологічного транспорту, т |
0,80 |
Кількість технологічного транспорту, од |
2 |
Напрацювання до відмови, год |
1200 |
Час відновлення, хв. |
43,2 |
Коефіцієнт готовності |
0,04 |
Напрацювання до технологічної відмови, год |
600 |
Час усунення технологічної відмови, хв. |
24 |
Коефіцієнт надійності технологічного процесу |
0,96 |
Для збирання цукрового буряка необхідний комплекс машин, в які входять наступні машини: гичкозбиральна машина БМ-6А, бурякозбиральний комбайн, навантажувач СПС – 4,2, а також транспортні засоби для перевезення основного і побічного врожаю.
Тому для проектування бурякозбиральної машини слід врахувати характеристику машин, що утворюють єдиний комплекс для збирання цукрового буряка.
Характеристика машини для збирання цукрового буряка приведена в таблиці 1.3.
Таблиця 1.3
Показники |
Значення |
Ширина захвату, м |
2,7 |
4,2 |
Швидкість руху, км/год |
робоча |
5…9 |
0,05…0,74 |
транспортна |
до 20 |
15 |
Продуктивність, га/год |
1,3…2,43 |
200 (т/год) |
Навантажувальна висота, м |
2,72 |
2,67…3,5 |
Число зібраних рядків |
6 |
-
|
Ширина міжрядь, м |
45 |
-
|
Габаритні розміри, робочі, мм |
довжина |
7500 |
7600 |
ширина |
4500 |
7000 |
висота |
3500 |
3600 |
транспортні |
довжина |
7600 |
7000 |
ширина |
3300 |
3600 |
висота |
3800 |
3500 |
2.
О
бґрунтування параметрів машини
2.1 Розрахунок продуктивності викопувального органа
Для ефективної роботи бурякозбирального комбайна, необхідно, щоб продуктивність викопувального пристрою зокрема коренезабірника коренеплодів була більшою або рівною за продуктивність самого комбайна.
Це можливо, коли швидкість коренезабірника рівна або більша за максимальну швидкість агрегату.
Qk
= 0,1 ∙ Ak
∙ BM
∙ VM
, т/год (2.1)
де Ак
– урожайність коренеплодів, т/га, Ак
= 45 т/га;
Вм
– ширина захвату машини, м, Вм
= 2,7 м;
VM
– швидкість руху машини, км/год, VМ
= 7,2 км/год.
Підставивши значення у формулу (2.1.) отримаємо
QK
= 0,1 ∙ 45 ∙ 2,7 ∙ 7,2 = 87,48 т/год.
Продуктивність коренезабірника визначається за формулою:
Qc
= 0,1 АК
ВМ
VН
max, т/год (2.2)
VН
max
– максимальна швидкість руху бурякозбирального комбайна.
VH
max
≤ Rω (2.3)
ω – кутова швидкість коренепідбирача, с–1
;
R – радіус руху шатуна, м.
Qc
= 0,1AK
BM
Rω, т/год (2.4)
З формули (2.4) випливає, що
(2.5)
ω = 1,57 с –1
.
2.2 Теоретичне обґрунтування геометричних параметрів викопуючих органів
При проведенні розрахунків геометрії них параметрів лемешів ставилися наступні вимоги: вісь коренеплоду повинна зберігати положення перпендикулярно до осі рядка або максимально наближено, при такому положенні виключається необхідність в силах підпору ґрунту. Цей фактор дозволить виключити негативний вплив стану ґрунту на якість роботи копачів. В процесі витягування коренеплоду потрібно забезпечити виконання двох функцій: розрізання пласта ґрунту різальною кромкою і порушення зв’язків системи «ґрунт – коренеплід»
Для ефективної роботи викопувального органу, потрібно щоб всі його елементи працювали злагоджено, щоб не створювалися затори на лемішах. Також потрібно спроектувати так щоб в руслі копача у вертикальному напрямку переміщуватися могло лише вертикально стояче тіло, що нагадує форму коренеплоду. Тому частини ґрунту, утворення яких можливе при дії на нього копача, в зону дії захоплюючого пристрою не попадали.
Визначення довжини леміша:
(2.6)
де l
– відстань між коренеплодами, l
= 180…350 мм;
dk
– діаметр коренеплоду, dk
= 67… 122 мм;
– повздовжнє зміщення коренеплоду по осі рядка.
L
= 240 + + 2 ∙ 5 = 312,5 мм
Викопувальний орган складається з двох частин: передні частини копачів розрихлюють грунт, руйнують зв'язки коренеплоду і ґрунту, а задніми частинами захоплюють коренеплід і виконують викопувальну функцію. Враховуючи фактори, які можуть впливати на ці процеси, визначимо наступні параметри.
Відстань між передніми крайніми точками лемешів:
Ln
= dk
+ 2 ∙ + 2 ∙ m; (2.7)
де dk
– діаметр коренеплоду, dk
= 67… 122 мм;
– поперечне зміщення коренеплоду від осі рядка, (можливе зміщення
до 60 мм);
m– можливе зміщення копача.
Ln
= 85 – 2 ∙ 30 + 2 ∙ 15 = 175 мм
Відстань між задніми крайніми точками лемешів:
LЗ
= dk
– 2 ∙ , (2.8)
де dk
– діаметр коренеплоду, dk
= 67 … 122 мм;
– горизонтальне зміщення крайніх точок максимального діаметру
коренеплоду.
Де визначається по формулі:
(2.9)
де – кут конусності коренеплоду, = 12о
;
– відстань між центром ваги коренеплоду і задніх крайніх точок
лемешів, = 10 мм.
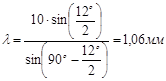
LЗ
= 89 – 2 ∙ 1,06 ≈ 87 мм,
Повне вертикальне переміщення коренеплоду під час викопування визначається по формулі:
S = cО
+ n
+ ; (2.10)
де сО
– початкова відстань між центром ваги коренеплоду і поверхнею ґрунту;
n
– висота між поверхнею ґрунту та задніми крайніми точками лемешів, п
= 60 мм.
В свою чергу с0
визначимо з табличних даних:
сО
=
cp
–
h
k;
(2.11)
де ср
–
координата центра ваги коренеплоду;
hk
–
висота коренеплоду над рівнем ґрунту.
сО
=94–30 = 64 мм
S = 64 + 60 +10 = 134 мм.
При визначенні ширини леміша враховуємоконуcність коренеплоду та його довжину і визначаємо по формулі:
(2.12)
де –
кут конусності коренеплоду, =12°;
– довжина коренеплоду, = 200 мм.
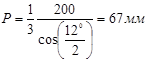
В формулі (2.13) визначаємо поперечне зміщення передніх крайніх точок леміша:
;(2.13)

Кут між осями рядка та леміша:
; (2.14)
.
2.3 Кінематичний розрахунок
Для визначення діаметру привідної зірочки вала коренезабірника проведемо кінематичний розрахунок ланцюгової передачі. Проектний розрахунок Визначаємо крок ланцюга р, мм:
(2.15)
де Мкр
= 7,74 Н∙м – крутний момент на ведучій зірочці;
Кэ
– коефіцієнт експлуатації, який представляє собою добуток коефіцієнтів, які враховують різні умови роботи передачі таблиця 5.7. [12]
КЭ
= КД
КС
Кυ
Крег
Кр
(2.16)
Отже, КЭ
= 1 ∙ 1,5 ∙ 1,25 ∙ 1,25 ∙ 1 = 1,875;
z1
– число зубців ведучої зірочки
z1
= 29 – 2u (2.17)
де u – передавальне число ланцюгової передачі, яке визначається за формулою:
(2.18)
Отже, z1
= 29 – 2 · 1,05 = 24,8
приймаємо z1
= 25.
[рЦ
] – допустимий тиск в шарнірах ланцюга, Н/мм2
, його можна визначити по швидкості ланцюга , м/с. [12] ст. 91;
v
– число рядків ланцюга. Для однорядних ланцюгів типу ПР v
= l.
Отже, 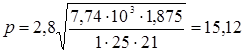
Отримане значення кроку р
округлюємо до найближчого стандартного по таблиці К32 [12]. Отже, р
приймаємо 19,05.
Визначити число зубців веденої зірочки:
z2
= z1
· u
(2.19)
Підставивши,
z2
= 25 · 1,05 = 26,5
Отримане значення z2
округлити до цілого непарного числа.
Тобто z2
= 27.
Визначаємо фактичне передавальне число u
ф
і перевіряємо його відхилення ∆u
від заданого u
:
(2.20)
Підставивши, отримаємо:
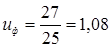
; (2.21)
Звідси

Визначити оптимальну між осьову відстань а
, мм. З умови довговічності ланцюга а
= (30…50) р
, де р
– стандартний крок ланцюга.
Тоді, – міжосьова відстань в кроках.
Визначаємо число ланок в ланцюзі 1р
:
; (2.22)
Звідси
.
Отримане значення округлюємо до цілого lp
=86.
Визначити довжину ланцюга l
,мм:
l
= l
р
∙ р
; (2.23)
підставивши отримаємо:
l
= 86 ∙ 19,5 =688 мм.
Визначаємо діаметр зірочок, мм.
Діаметр ділильного кола:
Ведучої зірочки веденої зірочки
/ /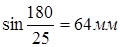
/ /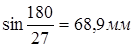
Діаметр виступів ведучої зірочки
.
Діаметр виступів веденої зірочки
,
де К
= 0,7 – коефіцієнт висоти зубця;
К7
– коефіцієнт числа зубців.
В силовій схемі ланцюгової передачі можна розрізнити F1
і F2
– відповідно ведучої і веденої вітки ланцюга, Н
;
F1
– колова сила, Н
;
F2
– сила попереднього натягу, Н
;
Ft
– натяг від центральних сил, Н
.
Для ланцюгової передачі, яка працює по принципу зачеплення, а не тертя, значення F0
не має такого значення як для ремінної передачі (F
0
складає всього декілька відсотків від Ft
). Для розповсюджених на практиці тихохідних і середньо швидкісних передач ( = 10 м/с) також невеликий і натяг . Виходячи з цього, для практичних розрахунки, приймаємо такі відношення:
F1
≈ Ft
F2
≈ 0 [12]
Тоді нова сила Ft
на даній зірочці визначається за формулою:
(2.24)
де Мкр
– крутний момент на зірочці, Н·м
;
d
– ділильний діаметр зірочки, м
.
Отже
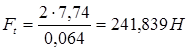
звідси
F1
= F
t
= 241,839 H
.
Сила F1
діє на зірочку під кутом = 00
.
2.4 Силовий розрахунок валу
Крутний момент ексцентрика:
М
= В
∙ l max
(2.25)
де В
– реакція ексцентрика, Н
;
l max
– ексцентриситет, м
.
М
= 214,7 · 0,006 = 1,29 Н∙м
Потужність ланцюгової передачі:
, (2.26)
де n
– частота обертання вала.
.
Крутний момент ланцюгової передачі:
(2.27)
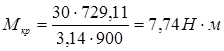
Консольна сила від муфти:
(2.29)
де D
муфти
– діаметр муфти, м
.
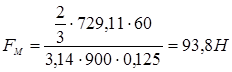
Прикладемо всі сили, які діють на вал та реакції підшипників рис. 2.1.Розкладемо всі сили на складові, які паралельні осям координат.
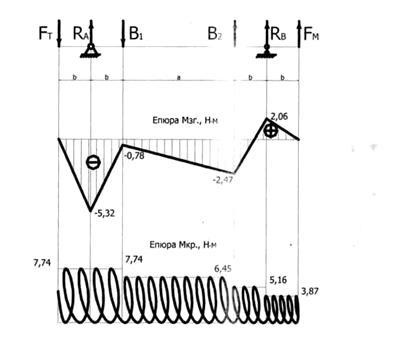
Рис. 2.1 Розрахункова схема вала з епюрами моментів
Розрахуємо опорні реакції.
Горизонтальна площина.
;
– Ftг
· b
+ В1г
– b
– B2г
∙ (b
+ а
) – R
Вг
· (b
+ b
+ a
) – FM
∙ (b
+ b
+ b
+ a
) = 0
звідки
(2.30)
Підставимо дані у формулу (2.25) одержимо:
.
;
– FМ
· b
+ В2г
b
– B1г
∙ (а + b
) + R
Аг
· (2b
+ a
) – F
t
г
∙ (3b
+ a
) = 0.
Звідки
(2.26)
Підставивши дані у формулу (2.26) одержимо:

Перевірка:
= – Ftг
+ RAг
+ В2г
– В1г
+ R
Вг
+ FM
г
=
= – 241,84 + 448,36 + 214,7 – 214,7 – 300,31 + 93,8 = 0.
Знайдемо значення згинальних моментів у характерних січеннях вала і побудуємо епюри згинальних моментів.
Січення А:
Мгор
= – F
t
· b
= – 241,84 ∙ 0,022 = – 5,32 Н∙м
.
Січення 2:
Мгор
= – F
t
· b
= – 241,84 ∙ 2 ∙ 0,022 +448,36 ∙0,022 = – 0,78 Н∙м
.
Січення 3:
Мгор
= – Ft
(2b
+ a
) + RA
(b
+ a
) – B1
∙ a
=
= – 241,84 · 0,252 + 448,36 · 0,23 – 214,7 · 0,208 = – 2, 47 Н·м
.
Січення В:
Мгор
= – Ft
· (3b
+ a
) + RA
· (2b
+ a
) – B1
(a + b) + B2
· b
=
= – 241,84 · 0,274 + 448,36 · 0,252 · 214,7 · 0,23 + 214,7 · 0,022 = 2,06 Н·м
.
У вертикальній площині проекції сил на вісь X рівні 0. Отже визначимо значення згинальних моментів:
(2.31)
З епюр Мкр
Мзг
видно, що небезпечним є січення вала, що співпадає з вольницею А
, де Mkp
=
7,74 Н·
м
,Мзг
= 5,32Н∙м
.
Розрахунковий момент визначимо за формулою:
(2.32)
Отже,

З умови міцності [7]
(2.33)
де М
= Мроз
W
– осьовий момент опору, м3
,
[ ] – границя міцності, [ ] = 250 МПа
[7].
Із формули (2.29) визначаємо:
(2.34)
підставивши отримаємо:
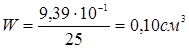
З іншої сторони
(2.35)
де d
– зовнішній діаметр вала.
Тоді з умови
(2.36)
знаходимо діаметр вала:
(2.37)
звідси
.
Розрахунковий діаметр вала визначаємо за формулою:
dpoз
= d · к,
м (2.38)
де k
– коефіцієнт запасу міцності:
к
= 1…1,7
підставивши у формулу (2.38) отримаємо:
d
роз
= 0,1 ∙ 1,7 = 0,017 м
.
Для розрахунків приймаємо d
= 30 мм
.
Перевіряємо вал на міцність за 4 теорією міцності [7] за формулою:
(2.39)
де – напруження згину, МПа
;
– напруження кручення, МПа
.
Напруження згину розраховуємо за формулою:
, МПа
(2.40)
де Мзг
– сумарний згинальний момент в небезпечному перерізі, Н·м
;
d
– діаметр вала в небезпечному перерізі, м.
Отже за формулою (2.40.)

напруження кручення за наступною формулою:
(2.41)
де Мкр
– крутний момент в небезпечному січенні, Мкр
= 7,74 Н·м
. Підставивши отримаємо:
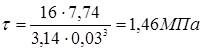
Тоді за формулою (2.39) одержимо:
.
Отже, умова міцності виконується.
У кріпленнях шатуна попередньо вибрані підшипники кулькові радіальні однорядні за ГОСТ 8338–75 d x D х В
= 33 х 55 х 13 мм.
Придатність попередньо вибраних підшипників визначається співставленням розрахункової динамічної вантажопідйомності Сгр
, Н
, з базовою Сг
, або базової довговічності L10h
, год із необхідною L
h
, год по умовам:
Сгр
< Сг
або L
10
h
>Ph
(2.42)
базова динамічна вантажопідйомність підшипника Сг
представляє собою постійне радіальне навантаження, яке підшипник може сприйняти при базовій довговічності, що складає 106 обертів внутрішнього кільця Сг
= 15,9 кН
[12].
Необхідна довговічність підшипників L
h
, передбачена ГОСТом 16162–85. Lh
=(8…12)∙103
,год, розрахункова динамічна вантажопідйомність
(2.43)
де R
E
– еквівалентне динамічне навантаження, Н
;
– кутова швидкість обертання вала, с-1
; =1,57 с-
1
;
m
– показник степені: m
=3 для кулькових підшипників.
Відношення для аналізу і вибору відповідної формули для визначення еквівалентного динамічного навантаження
(2.44)
де Ra
– осьове навантаження підшипника, Н;
е
– коефіцієнт осьового навантаження, приймаємо е
= 0,244;
v
– коефіцієнт обертання, приймаємо v
= l – при обертанні внутрішнього кільця підшипника;
Rr
– радіальне навантаження підшипника, Н
, Rr
= R
– сумарна реакція підшипників.
Осьової сили, що діє на підшипник не буде. Це пояснюється тим, що при захопленні коренеплоду на копачі діють однакові бічні сили. Для вибору підшипника припустимо, що при встановленні валу відбудеться його деякий перекіс або в результаті удару відбулося скривлення валу. Так, як вибраний клас підшипників дозволяє вузлу функціонувати при переносі осі внутрішнього кільця до 3°, то на підшипниках можливе осьове навантаження рівне:
(2.45)
де n
– кількість лемешів, n
= 6;
F
в
– навантаження вала у вертикальній площині, Н
, Fв
= 0;
F
г
– навантаження вала у горизонтальній площині, Н
, F
г
= 93,8 H
;
Н
– коефіцієнт можливих осьових навантажень в роботі, = 2.
Підставивши значення у формулу (2.45) отримаємо:

Сумарна реакція підшипників R
, Н
:
(2.46)
підставивши значення у формулу (2.40) одержимо:
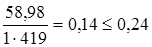
звідси випливає, що еквівалентне динамічне навантаження розраховується за формулою:
RЕ
= VRr
K6
KT
, H
(2.47)
де Кб
– коефіцієнт безпеки, Kб
= 1,1 [12]
KТ
– температурний коефіцієнт, КТ
= 1,1 [12].
Отже RE
= 1· 419 · 1,1 · 1 = 460,9 H
підставивши значення у формулу (2.43) розрахуємо динамічну вантажопідйомність:

Базова динамічна вантажопідйомність підшипника Cr
=15900 H
, отже умова придатності виконується, оскільки:
С
r
=15900>Сгр
=958,57Н
Розрахункова базова довговічність:
, год (2.48)
отже,
год
необхідна довговічність Lh
= 10 ∙ 103
=104
год.
Отже,L
h
= 45643015 >10000год.
Так як умова Crp
<Cr
, і L
1
0h
> Ц
, то попередньо вибрані підшипники придатні для конструювання вузла.
2.5 Визначення потужності на привід викопувального органа
Потужність, яка затрачається на привід копача розраховується заформулою:
N
заг
= N
вібр
+ N
тяг.опір
(2.49)
де Nвiб
– потужність на вібрацію копача, Вт
;
, кВт
(2.50)
де Nл.п
– потужність на здійснення ланцюгової передачі, Вт
;
– ККД ланцюгової передачі, = 0,94;
– ККД кулькових підшипників, = 0,99;
– ККД редуктора, = 0,96;
– ККД клинопасової передачі, = 0,9;
– ККД муфти, = 0,98.
Отже
Вт
Nтяг.oпір
– потужність, що затрачається на пересування копача в ґрунті, Вт, обчислюється за формулою:
Nтяг.oпір
= N
тяг.зв
· q
. (2.51)
деNтяг.oпір
– потужність, що затрачається на пересування звичайного лемеша в ґрунті, Nтяг.зв
= 14 кВт [10]
q
– коефіцієнт зменшення тягового опору q
= 0,71.
Підставивши, отримаємо
Nтяг.oпір
= 1400 ∙ 0,71 = 9946,98 Вт
Nзаг
= 2053,02 + 9946,98 = 12000 Вт =12кВт.
3.
Обґрунтування побудови схеми машини
3.1 Обґрунтування функціональної схеми
Водій направляє передні колеса 1 (лист 2 графічної частини), а відповідно, і лемешеві копачі 2 захвачують і видаляють корені з ґрунту. Лопатеві бітери 3 передають корені на шнековий очисник.
Шнеки 4 і вальці 5 очисника видаляють із вороху ґрунт, рослинні домішки і одночасно транспортують корені до поздовжнього елеватора 6. Елеватором корені передаються на горизонтальний стрічковий транспортер 7, розміщений на бункері. Потім корені поступають на перший вал грудкоподрібнювача 9, кулачки якого руйнують залишкові грудки ґрунту і видаляють їх з вороху. Далі корені вивантажувальним елеватором 8 подаються в кузов транспортного засобу, який рухається поряд. Коли у воросі немає міцних ґрунтових грудок, то напрямок руху стрічки транспортера 7 можна змінити на зворотній; корені при цьому відразу ж будуть направлятись на вивантажувальний елеватор, минаючи грудкоподрібнювач.
3.2
Обґрунтування принципової схеми
Коренезбиральна машина складається з самохідного шасі і навішеного коренезабірника (лист 4 графічної частини). Шасі в свою чергу складається з рами, яка спирається на мости ведучих і ведених коліс, силового агрегату, варіатора площадки водія з кабіною, а також електричної і гідравлічної систем.
Коробка передач в поєднанні з варіатором приводу ходової частини забезпечує безступінчату зміну швидкості.
Частина вузлів коренезабірника змонтована безпосередньо на рамі грудкоподрібнювач, бункер і поздовжній елеватор), друга частина (копачі, шнековий очисник) – на окремій рамі, приєднаній на несучій рамі шасі. В робочому положенні, коли копачі заглиблені в ґрунт рама опирається на міст ведучих коліс, а в транспортному – утримується гідроциліндром.
Машина обладнана автоматичною системою, яка контролює роботу основних вузлів, а також автоматом водіння. Машина оснащена зовнішніми освітлювальними пристроями для роботи в нічний час \ русі по дорогам.
3.
3 Обґрунтування кінематичної схеми
Крутний момент передається від двигуна СМД – 64 потужністю 110 кВт через клинопасову передачу на вал з частотою обертання 945 об/хв, на якому знаходиться ведуча зірочка Оо 200 мм, закріплена за допомогою шпонкового з'єднання і кріпильного болта. Ведуча зірочка через ланцюг ГТР–8–460 з кроком р = 8 мм передає на ведену зірочку Ø210 мм крутний момент навал з частотою обертання 900 об./хв, на якому містяться ексцентрики.
За допомогою ексцентрикового механізму закріпленого шпонкою, приводиться в рух шатун, що примушує копач здійснювати коливальні рухи. На одному валі ексцентрики розвернуті на 180° один відносно одного. Це забезпечує коливання копачів в протифазі.
Три пари валів з'єднуються пів муфтами 125–30–2-УЗ ГОСТ 20284–82.
З центрального розподільчого редуктора через ланцюгову передачу крутний момент передається на шнековий очисник, частота обертання якого 500 об./хв. і на елеватор.
4.
Розробка конструкції збірних одиниць і деталей
У відповідності з проектованими рішеннями розробляємо конструкцію складальних одиниць і деталей Заключним етапом створення графічної частини дипломного проекту, а також завершення роботи конструктора над виконанням вимог технічного завдання є розробка робочих креслень конструкцій складальних одиниць і деталей. Всі складальні одиниці і деталі встановлюються на окремій рамі комбайна.
Викопуючий пристрій призначений для викопування коренеплодів і подачі їх на шнековий очисник, складається з двох частин: передньою частиною леміш розрихлює ґрунт, а задня частина захоплює коренеплід і витягує його.
Коренезабірний пристрій складається з двох лемешів до яких приварюються кронштейни та кріплення, двох шатунів, ексцентриків, трьох валів, на яких встановлені, шість підшипникових вузлів, дві півмуфти і кріпиться ведена зірочка, яка приводить в рух коренезабірний пристрій. Привід коренезабірного пристрою здійснюється за допомогою ланцюга ПР-8–460 з кроком р = 19,5, діаметр ролика для якого d=2,31 мм.
Число зубців ведучої зірочки приводу коренезабірного пристрою Zl=25;
діаметр ділильного кола dD
i=64 mm;
діаметр кола виступів Del
=68,21 mm;
діаметр кола впадин Dn=63,09 mm.
Зірочка посаджена на валу за допомогою шпонки h-b=12–8 ГОСТ 23360–78.
Число зубців веденої зірочки приводу коренезабірного пристрою Z2=27;
діаметр кола впадин Dі2
=67,04 мм;
діаметр кола виступів De
2
=73,33 мм;
діаметр ділильного кола dd
2
=68,9 мм.
Зірочка посаджена на валу за допомогою шпонки h·b = 10–8 ГОСТ 23360–78.
Ведуча і ведена зірочки розміщені на постійній відстані одна від одної. Півмуфта посаджена також на шпонку h· b = 10–8 ГОСТ 23360–78 і фіксується гвинтом АМ6–8 ГОСТ 17475–80.
Вал, як складальна одиниця кріпиться до рами за допомогою двох підшипникових вузлів. Діаметр вала під підшипник Ø30 кб. Вал виготовляється із сталі 45 ГОСТ 1050–74.
Підшипниковий вузол складається із кулькового радіального однорядного підшипника dxDх В = 30 х 55 х 13 ГОСТ 8338–75. підшипник знаходиться у корпусі, який виливається з чавуну С415 ГОСТ 1412–79.Корпус підшипника з'єднується за допомогою різьбового з'єднання. На вал напресовується ексцентрик з підшипником. Внутрішнє кільце підшипника фіксує прижимна втулка, яка одягається на вал. На підшипник одягається шатун, після чого з обох боків фіксується кришками і шплінтами. Зовнішнє кільце підшипника фіксується також кришкою.
З обох сторін вала є отвори для гвинтів, які фіксують положення з одного боку муфти з другого – зірочки.
На валу просвердлено два отвори о8 мм для шплінтів, які фіксують положення шатуна.
Є три пари валів, які з'єднуються між собою півмуфтами.
До лемеша приварене кріплення до якого за допомогою пальця кріпиться шатун з впресованим підшипником dхDxB = 45x75xl6.
ГОСТ 8338–75. Для регулювання ширини міжрядь на пальці з обох боків є три регулювальні пластини. їх можна переміщувати з одного боку в інший. Завдяки шатунам лемеші набувають коливальних рухів.
В передній частині лемеша приварене кріплення, через яке проходить вал, який кріпиться до рами. На валу з обох боків містяться чотири регулювальні пластини для регулювання ширини міжряддя.
Лемеші виготовляються з листової сталі Ст. 45. Передня частина лемешів заточується під кутом 18°.
5. Організація робіт з застосуванням розроблюваної техніки
5.1 Експлуатація розроблюваної машини
Експлуатація бурякозбирального комбайна – це процес, що включає в себе використання машини по своєму призначенню, підтримання її робото здатності (технічне обслуговування) і забезпечення її функціонування (підготовка до використання і технічного обслуговування, технічне обслуговування, зберігання транспортування та ін.).
Для зниження затрат ручної праці, збільшення продуктивності, і скорочення термінів збирання цукрових буряків розробимо технологічну схему збирання цукрових буряків. Проектована машина працює в комплексі з гичкозбиральною машиною БМ-6А, навантажувачем СПС – 4,2 та транспортними засобами для відвезення основного і допоміжного урожаю.
Гичкозбиральна машина зрізує гичку і завантажує в транспортні засоби, які відвозять їх до місць силосування.
Після цього бурякозбиральний комбайн викопує корені і завантажує в транспортні засоби, які відвозять їх на край поля у бурти або прямо на цукровий завод в залежності від кількості транспортних засобів і чистоти коренів. Корені, вивезені на край поля, завантажуються у транспортні засоби за допомогою навантажувача СПС – 4,2 і відвозяться на цукровий завод.
В комплекс робіт по підготовці розробленого бурякозбирального комбайна до експлуатації входять:
1. дозбирання;
2. монтаж допоміжних агрегатів;
3. регулювання робочих органів;
4. заправка,
Дозбирання комбайна проводити в такій послідовності:
1. встановити перила, драбини, провести монтаж енергетичного засобу на раму комбайна;
2. провести монтаж вивантажувального пристрою;
3. встановити демонтовані клинові паси;
4. провести монтаж електрообладнання (фар, підфарників, фонарів, звукового сигналу, акумуляторної батареї) дзеркал заднього виду;
5. встановити термос, аптечку і проти пожежні засоби (вогнегасник, лопати);
6. відновити пошкоджені при транспортуванні, завантажувально-розвантажувальних роботах або до збиральні лакові і фарбовані покриття.
Технологічні регулювання робочих органів здійснюються з ціллю попереднього налагодження комбайна на збирання певних видів культур і при певних умовах. Регулювання основних робочих органів здійснюється з кабіни за допомогою відповідних рукояток і важелів.
Заправку комбайна паливом, робочими рідинами і мастильними матеріалами проводити у відповідності з правилами «Технічного обслуговування». Якщо в процесі експлуатації комбайна мають місце випадки підтікання мастильних матеріалів, тому несправні механізми, то до усунення неполадок змащування потрібно проводити частіше ніж вказано у відповідних операціях технічного обслуговування з метою забезпечення робото здатності комбайна і попередження поломок механізмів.
Запуск двигуна, його випробування і обкатку провести у відповідності з інструкцією по експлуатації двигуна.
5.2 Організація технічного обслуговування
Технічне обслуговування – це комплекс планово-попереджувальних робіт, направлених на підтримання довготривалої робото придатності комбайна. В систему технічного обслуговування входять:
1. технічне обслуговування при підготовці до роботи;
2. щозмінне технічне обслуговування (ЩТО, через 8-10мотогод.);
3. перше технічне обслуговування (ТОЇ, проводиться через 60 мотогод.);
4. друге технічне обслуговування (ТО-2, при напрацюванні комбайна не менше 240 мотогод., співпадає з технічним обслуговуванням при зберіганні).
Кількість ремонтів і обслуговувань визначаємо залежно від запланованого напрацювання на одну машину.
Кількість капітальних ремонтів визначаємо за формулою:
(5.1)
де Нр
=150 га– заплановане річне напрацювання на одну машину;
N=1 – кількість машин даної марки в господарстві;
Мкр
= 900 га – міжремонтне напрацювання машини від останнього капітального ремонту.
Отже, .
Кількість поточних ремонтів розрахуємо за формулою:
(5.2.)
Кількість періодичних ТО-1 буде рівною:
де М
n
=300 га– напрацювання машини від останнього капітального або поточного ремонту.
Тоді за формулою (5.2) одержимо
.
Для машини будуть проводитись наступні ТО: щозмінне ТО, періодичне ТО-1 і після сезонне ТО.
(5.3)
де МТО-1
= 95 га– напрацювання машини від останнього капітального або поточного ремонтів, або ТО-1.
Отже, 
Необхідну кількість щоденних ТО визначають за формулою:
(5.4)
де МЩТО
= 12 га – напрацювання машини між щоденним ТО. Таким чином
.
По закінченні сезонних робіт для машини потрібно проводити після сезонне ТО при установці машини на зберігання. Тому кількість То буде рівною кількості машин в господарстві.
Отже, Nm
on
= 1.
Загальну річну трудомісткість ремонтних робіт і ТО розраховують за формулою:
ТН
= Тк
∙ N
k
+ ТП
∙ N
п
+ ТТО-1
∙ N
ТО-1
+ ТЩТО
∙ N
ЩТО
+ ТТОП
∙ N
ТОП
(5.5)
де Тк
– трудомісткість капремонту, год. Тк
= 48 год.
Тп
– трудомісткість поточного ремонту, год. Тп
= 25 год.
Тто-1
– трудомісткість То-1
, год Тто-1
= 5 год
Тщто
– трудомісткість щоденного ТО, год. ТЩТО
= 0,5 год
Тmon
– трудомісткість після змінного ТО, год. Tmon
= 10 год.
Отже, за формулою (5.5) одержимо, що загально річна трудомісткість буде рівною:
Тн
=48–0,17 + 25 – 0,33 + 5 – 1,08 + 0,5 – 10,9 + 10 – 1 = 36,8 год.
Таблиця 5.1. Роботи, що виконуються по кожному виду технічного обслуговування
Зміст робота і методика їх проведення |
Технічні вимоги |
Прилади, інструменти, матеріали |
примітка |
1 |
2 |
3 |
4 |
Щозмінне технічне обслуговування (ІДТО) |
Перевірити і при необхідності долити охолоджуючу рідину в бачок основного двигуна |
Вода повинна бути не нижче кромки горловини бачка. |
Відро. Вода |
Очистити від землі і залишків частини машини. Перевірити шляхом зовнішнього огляду надійність кріплення всі складових частин, підтягнути ослаблені різьбові з'єднання. |
Складові частини машини повинні бути чистими. Всі складові повинні бути укомплектовані, зовнішні болти і гайки надійно загвинчені |
Щітка, чистик, обтираючий матеріал Інструмент, що додається до машини |
Перевіряють відсутність протікання |
Протікання води, масла, палива, |
Інструмент, що додається до |
води, масла, пального, електроліту, гальмівної рідини. |
електроліту, гальмівної рідини – не допускається. |
машини. |
/
|
Перевірити і долити гальмівну рідину в головні гальмівні циліндри. Перевірити натяг поздовжнього, і стрічкового елеваторів. Через 30 год роботи підтягують болти кріплення копачів Перевірити рівень і долити пальне в бак основного пускового двигуна. |
Рівень на 10–15 мм нижче верхнього краю бачка. Відстань між верхньою і нижньою вітками повинна бути 300–320 мм. Копачі повинні бути жорстко
Закріплені. Пальне повинне бути чистим і відстояним
|
Гальмівна
рідина БСК ТУ 6–10–1533–75 або «Нева» Інструмент, що додається Інструмент, що додається Дизельне паливо
|
Перше технічне обслуговування (ТО-1) |
Перевірити і при необхідності
відрегулювати:
• тиск повітря в шинах колес
|
Нормальний тиск – 2,5–3,5 кгс/см2
|
Манометр шинний, насос |
• механізм керування головним і пусковим двигунами |
Злити відстій з паливного бака |
Перевірити на слух роботу всіх складових частин машини |
Виявити причини, що Викликають ненормальні шуми стук і усунути їх |
Інструмент, що додається до машини |
Промити фільтр бака гідравлічної системи |
Ванна, волосяна щітка, керосин,викрутка гаєчні ключі 12, 14, 10 мм |
Розбирати клапан при промиванні фільтра забороняється |
Запустити головний двигун і перевірити роботу рульового |
Несправності усунути |
Інструмент, що додається до машини |
Керування, гальм, контрольних приладів, освітлення, світлової, звукової сигналізації, механізмів керування |
Відрегулювати робочі органи машини в залежності від ґрунтово-кліматичних умов |
Інструмент, що додається до машини |
Друге технічне обслуговування (ТО-2) |
Перевірити стан електропроводки і ізолювати її |
Пошкодження проводки не допускається |
Ізоляційна Стрічка |
Перевірити і принеобхідності очистити фільтруючий елемент повітроочисника |
Паперові фільтри повинні бути чистими |
Ключ 19 мм, відро, м'який дріт 00,5–1,0мм |
Перевірити шляхом зовнішнього огляду технічний стан робочих органів, надійність кріплення всіх складових частин |
Всі складові частини повинні бути укомплектовані, зовнішні болти і гайки надійно загвинчені |
Інструмент, що додається до машини |
Запустити головний двигун і перевірити роботу рульового керування, гальм, контрольних приладів, освітлення, світлової, звукової сигналізації, механізмів керування |
Несправності усунути |
Інструмент, що додається до машини |
Відрегулювати робочі органи машини в залежності від ґрунтово-кліматичних умов |
Інструмент, що додається до машини |
Перевірити і при необхідності очистити фільтруючий елемент повітроочисника |
Паперові фільтри повинні бути чистими |
Ключ 19 мм, відро, м'який дріт 00,5–1,0мм |
Перевірити шляхом зовнішнього огляду технічний стан робочих органів, надійність кріплення всіх складових частин |
Всі складові частини повинні бути укомплектовані, зовнішні болти і гайки надійно загвинчені |
Інструмент, що додається до машини |
Перевірити і відрегулювати зазори між клапанами і коромислами |
Щуп повинен проходити в зазор між стержнем клапана і бойном коромисла від невеликого зусилля руки. |
Ключігаєчні 12, 17,27 мм, викрутка, щуп 0,5 мм, пускова рукоятка, волосяна щітка |
Перевірити надійність кріплення:
• балки жорсткості і картера ведучого моста;
• ведучих і керованих коліс
|
Різьбові з'єднання з відповідним крутним моментом |
Комплект баєчних ключів |
Перевірити натяг полотен поздовжнього і вивантажувального елеваторів |
Відстань між верхньою і нижньою вітками повинна бути 300–320 мм |
Лінійка |
Злити відстій палива з бака основного двигуна і очистити вентиляційний отвір в кришці горловини |
Кількість злитого палива повинна складати 5–7 л |
Ключ гаєчний 19 мм, м'який дріт, обтираючий матеріал |
В процесі експлуатації комбайна можуть виникнути несправності, які викликані зношенням деталей, порушенням регулювань чи неправильним обслуговуванням.
Таблиця 5.2.Несправності машин та способи їх усунення
Несправність |
Причина |
Спосіб усунення |
1 |
2 |
3 |
Неповне вибирання і пошкодження коренеплодів лемешами |
Мала глибина ходу копачів |
Збільшити глибину ходу лемешів |
Неоднакова глибина ходу копачів |
Перекіс рами машини |
Перевірити тиск у колесах машини, який повинен становити:
у передніх – 0,34 МПа, задньому правому 0,16 МПа, задньому лівому – 0,25 МПа
|
Нестійка робота автомата водіння |
Недостатнє або надмірне заглиблення копірів-розпушувачів |
Встановити копіри-розпушувачі на глибину ходу 20–30 мм зміною довжини верхньої тяги паралелограмної підвіски, регулюючи кут входження лапи у ґрунт |
Втрати окремих дрібних коренеплодів |
Передчасне відключення ВВП комбайна (до вивантаження коренеплодів з машини) |
ВВП потрібно вимикати після повного вивантаження коренеплодів з машини |
Викопувальні лемеші рухаються збоку рядків |
Копіри-водії зміщені відносно викопувальних лемешів |
Змістити у бік лемешів кронштейни кріплення пралелограмних підвісок на передньому брусі рами автомата керування |
Ланцюги набігають на ведучі зірочки |
Забруднення ланцюгів |
Очистити і змастити ланцюги |
Машина зміщується вбік |
Порушення регулювання сходження напрямних коліс малий зазор між нижньою тягою паралелограма і вилкою – уловлювачем Рульове колесо не знаходиться в середньому положені |
Встановити кут сходження напрямних коліс, різниця між замірами по висоті центрів коліс повинна бути 40–80 мм Перевести копіри гідросистемою в робоче положення; опустити копіри кронштейнів у нижнє положення (зазор повинен бути не менше 30 мм) Встановити рульове колесо в |
Повільний поворот керованих коліс або не повертаються зовсім при переміщенні золотника коліс |
Недостатня кількість масла в корпусі гідро підсилювача |
Перевірити рівень масла і долити його до необхідного рівня |
6. Економічна частина
6
.1
Доцільність та значення впровадження бурякозбирального комбайна
новим викопуючим пристроєм
У сільському господарстві для збирання буряків використовується машина КС-6 з
дисковим викопувальним органом, який включає 12 викопувальних дисків, 6 з яких – активні. Привід активних дисків включає конічний редуктор з круговими зубами, карданні передачі роздаточного циліндричного редуктора.
Загальна маса приводу в зборі 1450 кг, а ціна – 8900 грн. (конічний редуктор, складний у виготовленні і коштує 550 грн.).
У розроблюваному лемішному викопувані є 12 лемешів, шатунів, ексцентрикових валів та дві ланцюгові передачі. Це дозволило знизити масу викопувальних частин до 560 кг і значно знизити ціну вузла.
Вихідні дані необхідні для визначення ефективності застосування бурякозбирального комбайна з новим коренепідбирачем приведені в таблиці 6.1.
Таблиця 6.1. Вихідні дані
Показники |
Одиниця виміру |
Позначення |
Розробка |
Базового |
нового |
Ширина захвату комбайна |
м |
В |
2,7 |
2,7 |
Швидкість руху комбайна |
м/с |
v |
1,8 |
2,0 |
Коефіцієнт використання робочого часу |
τ |
0,8 |
0,85 |
Тривалість робочого дня |
год |
Т |
8 |
8 |
Максимальна допустима кількість днів збирання |
ДНІВ |
Д |
30 |
30 |
Кількість обслуговуючого персоналу для збирання буряків |
людей |
Л |
2 |
2 |
Маса коренезабірника в зборі |
кг |
 |
1450 |
1000 |
Чиста маса підбирача без покупних частин |
кг |
 |
820 |
450 |
Ціна бральної частини |
грн |
Цб |
8900 |
- |
Собівартість бральної частини |
грн |
Сб
|
4800 |
- |
Вартість матеріалів в собівартості коренепідбирача |
грн |
Сн
|
3500 |
Вартість покупних виробів в бральній частині в оптових цінах з затратами на доставку |
грн |
Спв
|
- |
200 |
Нормативний коефіцієнт відрахувань на реновацію |
% |
а
|
16,6 |
16,6 |
Щорічні відрахування на капітальний поточний ремонт і техогляди |
% |
г |
12 |
12 |
Ефективна потужність двигуна комбайна |
кВт |
Ne
|
ПО |
ПО |
Потужність необхідна для приводу бральної частини |
кВт |
N0
|
14 |
12 |
Вартість дизпалива |
грн |
Цл
|
6,70 |
6,70 |
Тарифна годинна ставка: |
Комбайнера |
Грн./год |
f
гк
|
3,5 |
3,5 |
Помічника |
Грн./год |
f
г
п
|
2,8 |
2,8 |
Слюсаря |
Грн./год |
f
гс
|
1,3 |
1,3 |
6.3 Розрахунок основних техніко-економічних показників впровадження бурякозбирального комбайна новим викопуючим пристроєм
Продуктивність бурякозбирального комбайна визначаємо за формулою:
W
= 0,36 BVM
τ
, га/год, (6.1)
де В -
ширина захвату бральної частини комбайана, м;
Vм
– швидкість руху машини, м/с;
τ
– коефіцієнт використання робочого часу.
Отже, для нового комбайна
WH
= 0,36 ∙ 2,7 ∙ 0,85 = 1,65 га/год
для базового
W
б
= 0,36 ∙ 2,7 ∙ 1,8 ∙ 0,8 = 1,4 га/год
Продуктивність машини за зміну
W3M
= WT
, га/зміну (6.2.)
де W
– годинна продуктивність комбайна, га/год;
Т
– тривалість робочого дня, год.
Нового
W3M,
Н
= 1,65 ∙ 8 = 13,2 га/зміну
Базового
Wзм,б
= 1,4 ∙ 8 = 11,2 га/зміну;
Річний об'єм збиральних робіт
Q
= W
∙ tp
, га/рік, (6.3)
де tр
– річне завантаження машини;
W
– годинна продуктивність комбайна, га/год
tp
= TD, год (6.4)
Т
– тривалість робочого дня, год,
D
– максимально допустима кількість днів збирання, днів
t
p.н
=8∙30 = 240 год,
tp.
б
= 8 ∙ 30 = 240 год,
Отже, для нової машини
QH
= 1,65 ∙ 240 = 392 га
для базової
Qб
= 1,4 ∙ 240 = 336 га,
Приймаємо, що річний об'єм збиральних робіт
QH
= Qб
= 392 га,
Затрати праці при збиранні цукрових буряків:
, люд-год/га; (6.5)
де Л
– кількість людей, що обслуговують машину;
W
– продуктивність комбайна за год, га/год;
Отже, для нового картоплекопача
люд.-год/га,
для базового
люд.-год/га
Річна економія затрат праці при застосуванні нового підкопуючого органу
(6.6)
де – затрати праці при збиранні буряка базовим і новим комбайном, люд-год/га,
Q
– річний об'єм збиральних робіт, га.
Отже, = (1,43 + 1,21) · 392 = 86,24 люд.-год.
6.4 Визначення економічної ефективності застосування розроблювальної бральної частини
Вартість 1 кг чистої маси матеріалів, що йдуть на виготовлення підкопуючого робочого органу
грн./кг, (6.7)
де Сн
– вартість матеріалів у собівартості підкопуючого робочого органу, грн.;
– чиста маса підкопуючого робочого органу базової машини без покупних частин, кг
грн./кг;
Затрати на виготовлення нового підкопуючого робочого органу без вартості матеріалів і покупних частин, що йдуть на 1 кг його чистої маси.
грн/кг (6.8)
де Сб
– собівартість підкопуючого робочого органу, грн.;
Сп.в
– вартість покупних виробів, що використовуються у новому підкопуючому органі в оптових цінах із затратами на доставку, грн.;
– маса підкопуючого робочого органу без покупних виробів, кг.
грн./кг,
Галузева собівартість нового підкопуючого робочого органу на стадії технічного завдання
С0
= Gг.н
(λНКН
+ М
) + Сп.в
Ктз
, грн., (6.9)
де – чиста маса підкопувача, кг;
λ = 0,8 – коефіцієнт конструктивної складності нового підкопувача у порівнянні з технологією виготовлення базового підкопувача.
Н
– затрати на виготовлення нового підкопуючого робочого органу без покупних виробів, що припадають на 1 кг його чистої маси, грн./кг;
К
н
– коефіцієнт зміни «Н» в залежності від обсягу випуску Кн
= 1,1;
М
– вартість 1 кг чистої маси матеріалів для нового підкопувана, грн./кг;
Спв
– вартість покупних виробів нового підкопуючого робочого органу, грн.;
Ктз
= 1,05… 1,1 – коефіцієнт транспортно-заготівельних витрат, маємо
Ктз
= 1.0
Отже,
С0
= 450 (0.8 · 1.83 · 1.1 + 4.27) + 200 · 1.0 = 2845.89 грн.
Нормативний прибуток
, грн.; (6.10)
де С0
– галузева собівартість нового підкопуючого робочого органу;
Р0
= 14… 16% – норматив галузевої рентабельності, приймаємо
Р0
= 15%.
Отже
грн.
Оптова ціна нового підкопуючого робочого органу
U
0
=С0
+Пн
, (6.11)
U
0
= 2045,89 + 426,88 = 3272,7 грн.
Ціна нового підкопуючого робочого органу
Цбн
= 1,2 ∙ Ц0
=
1,2 ∙ 3273 = 3927,6 грн.
Питомі капіталовкладення в сфері експлуатації підкопуючого робочого органу органу.
, грн../га,(6.12)
де Цб
– балансова ціна підкопувана, грн.;
W
–
годинна продуктивність комбайна, га/год;
t
– річне завантаження підкопувана, год.
Отже, для нового викопувального органа
грн./га
для базового
грн./га.
Питома металомісткість підкопувача
кг/га (6.13)
де – маса зібраного підкопувана, кг;
Q
–
річний об'єм збиральних робіт, га.
Отже, для нового
кг/га,
для базового
кг/га
Собівартість збиральних робіт
С3
=
3
П
+
A
+
R
+
P
+
Z
+
Ue
м
(6.14)
де ЗП
–
заробітна плата комбайнера і помічника, грн./га;
А
–
амортизаційні затрати на реновацію, грн./га;
R
– затрати на ремонт і техобслуговування, грн./га;
Р
– затрати на пальне, необхідне для роботи машини, грн./га;
Z – затрати на зберігання підкопуючого робочого органу, грн./га;
Цем
– затрати на експлуатаційні матеріали, грн./га.
Затрати на заробітну плату механізатора
грн./га, (6.15)
де f
гк
f
г
n
– тарифна ставка відповідно комбайнера і його помічника, грн./год;
W
– годинна продуктивність копача, га/год.
Отже, для нового
грн./га,
для базового
грн./га,
Амортизаційні витрати на реновацію підкопувача
грн./га, (6.16)
де Цб
– ціна підкопувача, грн.;
а –
нормативний коефіцієнт відрахувань на реновацію, %;
W
–
годинна продуктивність комбайна, га/год;
t
–
річне завантаження підкопуючого робочого органу, год.
Отже для нового
грн./га,
для базового
грн./га.
Витрати на капітальний, поточний ремонт і техогляди підкопуючого робочого органу
(6.17)
де Цб
–
балансова ціна підкопувана, грн.;
r
–
норматив щорічних відрахувань на капітальний, поточний ремонт і техогляди, %;
W
– годинна продуктивність комбайна, га/год;
tp
– річне завантаження підкопуючого робочого органу, год.
Отже, для нового
гнр/га,
для базового
грн./га.
Витрати на дизпаливо, необхідне для роботи двигуна комбайна для приводу бральної частини:
(6.18)
де, Ne
– потужність на привід бральної частини;
qn
– питома витрата пального, г/екс.год;
Цп
– вартість дизпалива, грн./кг;
W
– продуктивність комбайна, га/год.
Отже для нової
грн./га
для базової
грн./га
Витрати та зберігання підкопуючого робочого органу
грн./га, (6.19)
де Тн
– норматив витрат праці на підготовку для зберігання, люд-год.
f
гс
–
годинна тарифна ставка слюсаря при виконанні робіт, пов'язаних з підготовкою підкопувана до зберігання, грн./год;
Q
–
річний об'єм збиральних робіт.
Приймаємо, що витрати на зберігання нового і базового підкопувана будуть рівними
грн./га.
Витрати на матеріали, що використовуються при експлуатації підкопувана
грн., (6.20)
де q
м
– питома витрата матеріалів на експлуатацію підкопувана;
Цм
– прейскурантна ціна матеріалів.
Зведені дані виробів матеріалів приведемо у таблиці 7.2
Таблиця 7.2
Назва матеріал |
Кількість |
Ціна |
Вартість |
q
, кг |
грн./кг |
Uм
, грн. |
1 |
2 |
3 |
4 |
Мастило консерваційне СКК, ГОСТІ 1099–64
Мастило захисне НГ-204, МРТУ 12Н №69–63
Гас тракторний
Фарба
Уайт-спірит ГОСТЗ134–52
Обтиральний матеріал
Шкірка шліфувальна, ГОСТ 6456–62, дм2
Масло автотракторне АК-15 ГОСТ 1862–63
|
0,64
0,33
1,75
0,1
0,05
0,20
2,0
1,0
|
2,2
37,9
14,0
9,0
2,4
0,8
0,75
2,5
|
1,41
12,51
1,75
0,09
0,12
0,16
1,5
2,3
|
Разом |
20,04 |
Приймаємо, що витрати на матеріали в розрахунку на 1 га зібраної площі можна визначити за формулою
грн./га, (6.21)
де Цм
– витрати на матеріали, що використовуються при експлуатації підкопувана, грн.;
Q
–
річний об'єм збиральних робіт, га.
Отже, для нового і базового підкопувача, ці відрахування становитимуть
грн./га
Отже, повна собівартість збиральних робіт:
для нового
Сзн
=
3,82 +1,94 +1,19 +1,42 + 0,04 + 0,05 = 8,46 грн./га,
для базового
Сзб
=
4,5 + 4,39 + 3,17 +1,95 + 0,04 + 0,05 = 14,4 грн./год.
Експлуатаційні витрати на підкопувач
U
= 3П +
R
+
Z
+
Ue
м
, (6.22)
де ЗП –
витрати на зарплату, грн./га;
R
– в итрати на капітальний, поточний ремонт і техобслуговування, грн./га;
Z
– витрати на зберігання підкопувана, грн./га;
Ue
м
–
витрати на експлуатаційні матеріали, грн./га.
Отже, для нового
UH
=
3,82 +1,19 +1,42 + 0,4 + 0,5 = 6,52 грн./га;
для базового
U
6
=
4,5 + 3,17 +1,95 + 0,04 + 0,05 = 10,01грн./га.
6
.5
Визначення економічної ефективності бурякозбирального комбайна з новим виконуючим органом
Річна економія грошових засобів на експлуатаційних витратах при використанні одного підкопувача.
ε
p
.о
=
Q
(
U
6
–
U
н
),
(6.23)
деQ
–
річний об'єм збиральних робіт, га;
U
б
, U
н
– прямі експлуатаційні витрати відповідно базового і нового підкопувана, грн./га.
Отже, ε
p
.о
= 392 (10,01 – 6,52) = 1368,08 грн.
Річна економія на експлуатаційних витратах при застосуванні випущеної партії нових підкопуючих робочих органів
ε
p
.н
= ε
p
.о
Вр
(6.24)
де ε
p
.о
– річна економія на експлуатаційних витратах при застосуванні нового підкопувана, грн.
Вр
= 1 шт. – річний випуск нових підкопувачів.
Єрп
= 1368,08 · 1 = 1368,08 грн.
Розмір додаткових капіталовкладень, необхідних для річного випуску нових підкопувачів
, грн. (6.25)
де Вр
– річний випуск нових підкопувачів, шт.;
Цб.б,
Цб.н
– балансова ціна відповідно базового та нового підкопувана, грн.;
Q
н
, Q6
– річний об'єм збиральних робіт відповідно з новим і базовим підкопувачем, га.
грн.
Строк окупності капіталовкладень на придбання нового підкопувача
, років (6.26)
де Кн
– капіталовкладення на придбання нового підкопувача і вони становлять
ε
p
.о
– річна економія грошових засобів
Кп
=Цвн
=3927,6 грн.
Економічна ефективність проекту
року
Економічна ефективність проекту
(7.27)
Отже, впровадження проекту є економічно доцільним.
Таким чином, приведені розрахунки показали, що новий підкопуючий робочий орган має перевагу у порівнянні з базовим варіантом, поскільки дає річну економію на експлуатаційних витратах у розмірі 1368,08 грн.
Зведені дані економічних обґрунтувань доцільності застосування нового підкопувача приведемо у таблиці 6.3.
Таблиця 6.3. Економічна ефективність використання розробленого бурякозбирального комбайна з новим підкопуючим робочим органом.
№ |
Показники |
Одиниця виміру |
Розробка |
Різниця |
Базова |
Нова |
1 |
2 |
3 |
4 |
5 |
6 |
1 |
Продуктивність комбайна |
– за годину змінного часу |
га/год |
1,4 |
1,65 |
+0,25 |
– зміну |
га/зм. |
11,2 |
13,2 |
+2 |
2 |
Річний об'єм збиральних робіт |
га |
336 |
392 |
+56 |
3 |
Кількість обслуговуючого персоналу |
чо л. |
2 |
2 |
4 |
Затрати праці на збиранні буряка |
люд. год./га |
1,43 |
1,21 |
-0,22 |
5 |
Річна економія затрат праці при застосуванні нового копача |
люд. год |
-
|
86,24 |
-
|
6 |
Собівартість збиральних робіт |
грн./га |
14,4 |
8,46 |
-5,94 |
7 |
Експлуатаційні витрати на підкопувач |
грн./га |
10,01 |
6,52 |
-3,49 |
8 |
Річна економія грошових засобів на експлуатаційних витратах при застосуванні нового підкопувача |
грн. |
-
|
1368 |
-
|
9 |
Питомі капіталовкладення в сфері експлуатації підкопуючого робочого органа |
грн./га |
26,49 |
9,92 |
-16,57 |
10 |
Питома металомісткість технологічного процесу підкопування |
грн./га |
4,32 |
2,55 |
-1,77 |
11 |
Строк окупності капітальних вкладень на придбання нового підкопувача |
років |
-
|
2,87 |
-
|
12 |
Економічна ефективність проекту |
-
|
35 |
-
|
Висновки
бурякозбиральний комбайн привод міцність
На основі виконаного проекту на тему: «Проект бурякозбирального комбайна з конструктивною розробкою вібраційного лемішного копача» можливе виготовлення і використання органа.
В результаті проведеної роботи зроблений розрахунок основний параметрів робочого органа, потужності, що необхідна для його приводу. Вибрані матеріали зірочок і муфт, визначені їх основні розміри. Проведено перевірку вала на міцність. Проведено перевірочний розрахунок підшипників.
Розроблені конструкції збірних одиниць і деталей вібраційного лемішного копача.
Розроблений робочий орган має ряд переваг:
1. При викопуванні коренеплодів зменшуються їх пошкодження.
2. Зменшується забрудненість буряків.
3. Зменшується маса вузла коренезабірного пристрою.
4. Зменшується потужність на привід копача.
Проведені розрахунки показали, що новий підкопуючий робочий орган має перевагу у порівнянні з базовим варіантом, оскільки дає річну економію на експлуатаційних витратах у розмірі 1368,08 грн.
Список
літератури
1. Гудован Л.И. Машина коренеуборочная самоходная КС-6Б. – Т.: Збруч, 1979.
2. Довідник з охорони праці в сільському господарстві. Під ред. В.Д. Лехмана. – К.: Урожай, 1990.
3. Карпенко. А.Н., Хасанський. В.М. Сельскохозяйственныемашины – М.: Агропромиздат, 1989.
4. Охрана труда в сельском хозяйстве: учебное пособие К.: Высшая школа, 1989.
5. Плоткін Я.Д., Янушевич O.K. Організація і планування виробництва на машинобудівному підприємстві: Навчальне видання. – Львів: Світ, 1996.
6. Погорелый Л.В., Татьянко М.В., Брей В.В. Свеклоуборочные машины–К.: 1983.
7. Посацький С. Опір матеріалів – видавництво Львівського університету, 1973.
8. Правила охорони праці у сільськогосподарському виробництві: К: Форт, 2001.
9. Справочник по охране труда на промышленном предприятии /К.Н. Ткачук и др. – К.: Техника, 1991.
10. Теория, конструкция, расчет с/х машин под ред. Е.С. Босого. –М: Машиностроение, 1987.
11. Шведик М.С. Дипломне проектування / Луцьк, ЛДТУ, 2000.
12. Шейнблит А.Е. Курсовое проектирование деталей машин – М.: Машиностроение, 1987.
|