Содержание
Реферат
Введение
1. Обзор станов холодной прокатки
2. Непрерывный стан 1200 холодной прокатки Магнитогорского металлургического комбината им. В.И. Ленина
2.1 Подготовка металла к прокатке
2.2 Оборудование и технология прокатки
2.3 Оборудование и технология отделки
3. Выбор режимов обжатий и расчет энергосиловых параметров процесса холодной прокатки
4. Расчет производительности стана
5. Рекомендации по совершенствованию технологии прокатки
Заключение
Перечень ссылок
Приложение А
Приложение Б
Реферат
холодная прокатка стан
Объектом исследования является листовой стан холодной прокатки.
Основная задача данной курсовой работы – выбор цеха холодной прокатки, прокатного стана производительностью 0,25 млн. тонн в год и разработка технологического процесса для производства листа из стали 08КП толщиной 0,35 мм и шириной 1050 мм. В ходе выполнения работы были рассмотрены станы холодной прокатки различной конструкции и производительности.
Для производства заданного проката был выбран непрерывный стан 1200 холодной прокатки Магнитогорского металлургического комбината им. В. И. Ленина. Описание его оборудования так же приводится в расчётно-пояснительной записке.
В ходе выполнения курсовой работы был использован комплекс программных средств по автоматизированному расчету, проектированию и оптимизации технологических режимов обжатий. В результате был выбран оптимальный режим загрузки стана.
Графическая часть курсовой работы состоит из 1 листа формата А1 содержит план расположения оборудования участка, схемы и графики к расчету технологических усилий и калибровки валков (графики изменения обжатий по пропускам (по клетям), усилий деформации, крутящих моментов на валках, скоростей, потребляемой мощности двигателей, схемы калибровки валков).
ПРОКАТНЫЙ СТАН, НЕПРЕРЫВНЫЙ ТРАВИЛЬНЫЙ АГРЕГАТ, ЛЕТУЧИЕ НОЖНИЦЫ, МОТАЛКА, РЕЖИМ ОБЖАТИЙ, СИЛА ПРОКАТКИ, МОМЕНТ ПРОКАТКИ, МОЩНОСТЬ ПРОКАТКИ, ПРОИЗВОДИТЕЛЬНОСТЬ СТАНА.
Введение
Технологический процесс получения готовой прокатной продукции – завершающая стадия металлургического производства. В прокатные цеха металлургического комбината поступает большая часть всей стали (свыше 80%), выплавляемой в сталеплавильных цехах и превращаемой в непрерывнолитые заготовки или в слитки. До 60–70% объема производства тонколистовой стали выпускается в виде холоднокатаных лент, листов и полос.
Прокатный стан - это комплекс машин и агрегатов, предназначенный для пластической деформации металла в валках и его дальнейшей обработки. В прокатных цехах располагают также агрегаты для отделки проката – его термической обработки, нанесения защитных покрытий на поверхность металла и др., необходимые для выпуска готовой продукции высокого качества, которая характеризуется не только формой поперечного сечения прокатываемого профиля, но и физико-механическими свойствами металла, состоянием поверхности проката и др.
Технологический процесс современного прокатного производства состоит из двух стадий: получения полупродукта (заготовки) и готовой продукции (готового проката).
1.
Обзор станов холодной прокатки
Процесс холодной прокатки металла в виде полос и листов толщиной от 2–6 мм до 0,8–0,1 мм и менее (до 0,001 мм) получил широкое распространение благодаря получению готовой холоднокатаной продукции широкого сортамента и высокого качества, характеризующегося высокой степенью точности геометрических размеров, плоскостности и чистоты поверхности, а также повышенными механическими свойствами металла (временным сопротивлением, пределом текучести, твердостью и др.). Исходной продукцией для холодной прокатки служат рулоны горячекатаной полосы толщиной 1,5–6 мм, поступающие с широкополосных станов горячей прокатки.
Современным способом получения холоднокатаной продукции является рулонный способ, который обеспечивает высокую производительность как собственно прокатных станов, так и различных технологических агрегатов, установленных в цехе холодной прокатки, а также увеличения выхода годного. Операция резки рулонной полосы на листы мерной длины является одной из последних в технологическом цикле цеха холодной прокатки.
К современным типам станов холодной прокатки относятся: непрерывные четырех–, пяти– и шестиклетевые и реверсивные, чаще всего одноклетевые, четырехвалковые и многовалковые.
Непрерывные станы холодной прокатки устанавливают в цехах большой производительности для выпуска полос и листов специализированного сортамента. Непрерывные станы отличаются от реверсивных большей степенью механизации и автоматизации и более высокими техническими параметрами по массе рулона, скорости прокатки, мощности главного привода; производительность этих станов выше, чем у реверсивных.
Непрерывные четырехклетевые четырехвалковые станы применяют для холодной прокатки тонких полос (минимальной толщиной 0,22–0,25 мм) шириной 1370–2350 мм и массой до 30–35 т. В соответствии с требуемой шириной полосы длину бочки валков станов принимают равной 1525–2500 мм; скорость прокатки достигает 20–25 м/с.
Непрерывные пятиклетевые четырехвалковые станы применяют как для прокатки тонких полос минимальной толщиной 0,17–0,23 мм, шириной до 2150 мм и массой до 40–60 т со скоростью до 25–30 м/с при длине бочки валков до 2000–2200мм, так и для прокатки жести и полос из электротехнической стали минимальной толщиной 0,15–0,18 мм, шириной до 1300 мм и массой до 15 т со скоростью до 30–37 м/с при длине бочки валков до 1200–1420 мм. Производительность непрерывных станов для холодной прокатки тонких полос достигает 1,5–2,5 млн. т. в год.
Реверсивные станы холодной прокатки устанавливают в цехах при небольшом объеме производства (50–120 тыс. т/год) с широким сортаментом полос из малоуглеродистых, легированных и электротехнических сталей. В ряде случаев реверсивные станы устанавливают в цехах холодной прокатки большой производительности в дополнение к непрерывным станам. По конструкции реверсивные станы подразделяют на станы с приводом через рабочие валки и через опорные валки. Реверсивные четырехвалковые станы изготавливают в основном с длиной бочки валков от 1000–1200 до 2000–2300 мм, которые обеспечивают прокатку полос с отношением её ширины к толщине 6000 и более; масса рулонов 30–45 т и скорость прокатки до 10–20 м/с.
Рассмотрим станы холодной прокатки с условием заданного типоразмера.
1.1 Непрерывный стан 1400 новолипецкого металлургического комбината
Непрерывный четырехклетевой стан холодной прокатки предназначен для прокатки полос толщиной 0,35-1,0 мм, шириной 750-1250 мм в рулонах из легированных сталей.
Исходные заготовки - горячекатаные травленые полосы с обрезными кромками толщиной 1,6-3,5 мм, шириной 750-1250 мм в рулонах. Минимальная масса рулона 3,5 т, максимальная 30 т. Состав и расположение оборудования приведены на рисунок 1.1.
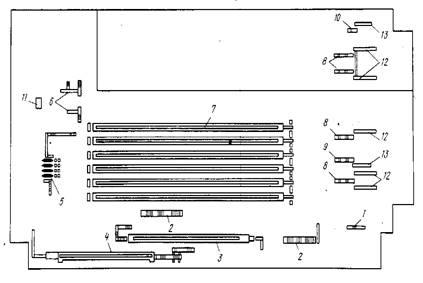
1 - кантователь рулонов, 2 - агрегат подготовки горячекатаных рулонов, 3 - нормализационный агрегат, 4 - травильный агрегат, 5 - четырехклетевой стан, 6 - агрегат подготовки холоднокатаных рулонов, 7 - агрегат термообработки и нанесения покрытия, 8 - агрегат продольной резки, 9 - агрегат продольной резки полосы на две ленты, 10 - агрегат обрезки кромок, 11 - дрессировочный стан, 12 - агрегат упаковки узких рулонов, 13 - агрегат упаковки широких рулонов.
Рисунок 1.1- Схема расположения оборудования стана 1400 холодной прокатки Новолипецкого металлургического комбината.
1.2 Непрерывный стан 1200 холодной прокатки магнитогорского металлургического комбината им. В.И. Ленина
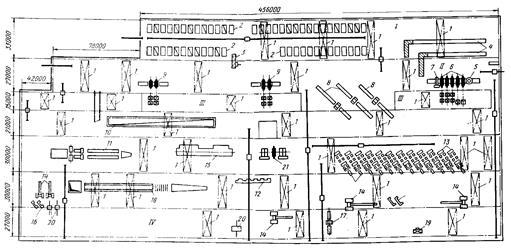
I - отделение отжига, II - пролет стана, III - машинный зал, IV - склад готовой продукции; 1 - мостовые краны, 2 - отжигательные печи, 3 - кантователи, 4 - агрегат электролитической очистки, 5 - разматыватель, 6 - линия стана, 7 - моталка, 8 - агрегат резки, 9 - дрессировочные станы, 10 - непрерывный агрегат, 11 - агрегат электролитического лужения жести, 12 - сортировщик листов, 13 - агрегаты горячего лужения, 14 - сортировочные агрегаты, 15 - агрегат подготовки полосы, 16 - ножницы, 17 - агрегат поперечной резки, 18 - агрегат оцинкования, 19 - весы, 20 - автопогрузчик, 21 - машина для промасливания.
Рисунок 1.2 - Схема расположения основного технологического оборудования стана 1200 Магнитогорского металлургического комбината.
1.3
Стан 1200 новолипецкого металлургического комбината
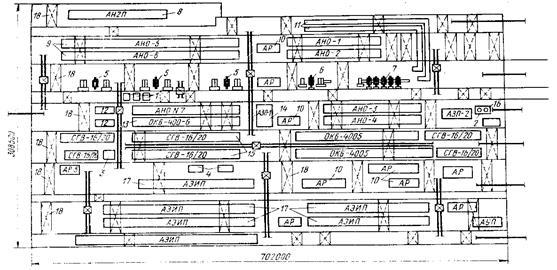
1 - кантователи, 2 - моечный агрегат, 3 - передаточная тележка, 4 - сушильно-моечный агрегат, 5 - рабочая линия 20-валкового стана 1200, 6 - рабочая линия реверсивного одноклетевого стана кварто 1200, 7 - рабочая линия непрерывного пятиклетевого стана 1200, 8 - конвейер горячекатаных рулонов, 9 - агрегат непрерывного отжига, 10 - агрегат резки, 11 - непрерывные травильные агрегаты, 12 - машина для покрытия листов тальком, 13 - вакуумно-водородная электропечь, 14 - агрегат для нанесения защитного покрытия, 15 - колпаковые электрические печи для отжига, 16 - агрегат промасливания, 17 - агрегат электроизоляционного покрытия, 18 - мостовые краны.
Рисунок 1.3 - Схема расположения основного технологического оборудования станов холодной прокатки 1200 Новолипецкого металлургического завода.
В результате литературного обзора заданный типоразмер рациональнее производить на непрерывный стане 1200 холодной прокатки Магнитогорского металлургического комбината им. В. И. Ленина.
2. Непрерывный стан 1200 холодной прокатки магнитогорского металлургического комбината им. В.И. Ленина
Стан, введенный в эксплуатацию в 1956 г., расположен в восьми пролетах (рис.1) общей шириной 195 м, длиной 456 м.
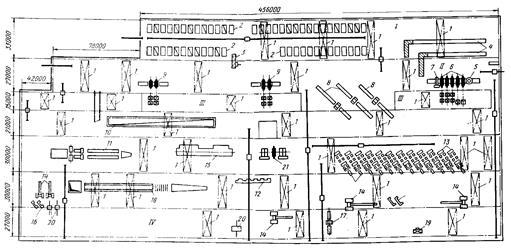
I - отделение отжига, II - пролет стана, III - машинный зал, IV - склад готовой продукции; 1 - мостовые краны, 2 - отжигательные печи, 3 - кантователи, 4 - агрегат электролитической очистки, 5 - разматыватель, 6 - линия стана, 7 - моталка, 8 - агрегат резки, 9 - дрессировочные станы, 10 - непрерывный агрегат, 11 - агрегат электролитического лужения жести, 12 - сортировщик листов, 13 - агрегаты горячего лужения, 14 - сортировочные агрегаты, 15 - агрегат подготовки полосы, 16 - ножницы, 17 - агрегат поперечной резки, 18 - агрегат оцинкования, 19 - весы, 20 - автопогрузчик, 21 - машина для промасливания.
Рисунок 2.1 - Схема расположения основного технологического оборудования стана 1200 Магнитогорского металлургического комбината
Стан состоит из пяти последовательно расположенных четырехвалковых клетей, разматывателя и моталки. Станины клетей закрытого типа. Нажимные устройства одинаковой конструкции. Привод нажимных винтов от двух 46-кВт электродвигателей типа Мг-62. Все клети имеют гидравлическое уравновешивающее устройство. Диаметр рабочих валков стана 485-500 мм, материал - сталь 9Х2МФ или 9Х2. Диаметр опорных валков 1220-1340 мм, материал - сталь 9ХФ и 9Х2. Подшипники рабочих валков роликовые, опорных - жидкостного трения. Рабочие валки клетей № 1-№ 3 заменяют раз в сутки, клетей № 4 и № 5 - через 600 т проката. Опорные валки независимо от толщины прокатываемой полосы заменяются: на клетях № 1 и № 2 через 20-25 сут, на клети № 3 - через 10-12 сут, на клетях № 4 и № 5 через 7-10 сут. Бочка опорных валков цилиндрическая, рабочих - выпуклая. Величина выпуклости: клеть № 1- до 0,15 мм, клети № 2-№ 4 - до 0,05 мм, клеть № 5 - до 0,10 мм.
Стан предназначен для прокатки в холодном состоянии полос сечением (0,2-0,36) х (900–1100) мм в ≤ 30-т рулон внутренним диаметром 485-500 мм, наружным ≤ 1950 мм из сталей 08Ю, 08кп, 08пс (ГОСТ 18178-72).
2.1 Подготовка металла к прокатке
Подкатом для стана холодной прокатки служит травленая горячекатаная полоса сечением 1,7-4,0 мм, ширина 630-1050 мм, наружный диаметр рулона максимальный 1230 мм, внутренний 650 мм с промасленной поверхностью.
Рулоны протравленных и промасленных полос подаются к стану с непрерывного широкополосного стана горячей прокатки 1450 через непрерывно-травильные агрегаты трехклетевого стана 1450 холодной прокатки.
На подающий транспортер пятиклетевого стана травленые горячекатаные рулоны укладываются при помощи мостового крана. Подающей балкой рулон устанавливается на тележку загрузочного устройства. На тележке загрузочного устройства рулон передается к головкам разматывателя, которыми центруется по продольной оси стана. Одновременно отгибается наружный конец полосы скребковым отгибателем и происходит задача его в валки первой клети стана.
Прокатанный рулон снимается с барабана моталки, увязывается, переносится на транспортер для передачи в термическое отделение или устанавливается на стеллаж для передачи на АНО и АГНЦ. Упаковка рулонов производится на площадке стана.
2.2 Оборудование и технология прокатки
Стан состоит из пяти последовательно расположенных четырехвалковых клетей, разматывателя и моталки. Станины клетей закрытого типа. Нажимные устройства одинаковой конструкции. Привод нажимных винтов от двух 46-кВт электродвигателей типа Мг-62. Все клети имеют гидравлическое уравновешивающее устройство. Диаметр рабочих валков стана 485-500 мм, материал - сталь 9Х2МФ или 9Х2. Диаметр опорных валков 1220-1340 мм, материал - сталь 9ХФ и 9Х2. Подшипники рабочих валков роликовые, опорных - жидкостного трения. Рабочие валки клетей № 1-№ 3 заменяют раз в сутки, клетей № 4 и № 5 - через 600 т проката. Опорные валки независимо от толщины прокатываемой полосы заменяются: на клетях № 1 и № 2 через 20-25 сут, на клети № 3 - через 10-12 сут, на клетях № 4 и № 5 через 7-10 сут. Бочка опорных валков цилиндрическая, рабочих - выпуклая. Величина выпуклости: клеть № 1- до 0,15 мм, клети № 2-№ 4 - до 0,05 мм, клеть № 5 - до 0,10 мм.
Привод валков осуществляется от двигателя через шестеренную клеть и универсальные шпиндели. Характеристика двигателей приведена в таблице 1, вспомогательного оборудования в таблице 2.
2.3 Оборудование и технология отделки
Участок отделки готового проката состоит из агрегатов электролитического обезжиривания, термических печей, двухклетевых четырехвалковых реверсивных станов, агрегатов поперечной резки, горячего и электролитического лужения, горячего непрерывного цинкования, агрегата подготовки полосы к электролитическому лужению.
Агрегаты электролитического обезжиривания и очистки предназначены для удаления с поверхности стальной холоднокатаной полосы остатков технологической смазки, применяемой при прокатке жести. Электролитически зачищают полосы в рулонах, наружный диаметр которых 1860 мм, внутренний 500 мм, масса 15 т, толщина полосы 0,20-0,50 мм, ширина 730-1050 мм. Агрегат электролитической зачистки по характеру работы оборудования состоит из головной, средней технологической и хвостовой частей.
Оборудование головной части агрегата обеспечивает запас рулонов, подачу к разматывателю, задачу полосы в агрегат, обрезку швов и концов полосы, разматывание рулона, сварку полос, подачу полосы к средней части агрегата.
Оборудование средней технологической части обеспечивает механическую очистку и электролитическое обезжиривание полосы с использованием переменного тока низкого напряжения промышленной частоты, промывку полосы в горячей воде, отжим влаги и сушку полосы, транспортировку её по агрегату.
Оборудование хвостовой части агрегата обеспечивает центрование и транспортировку полосы, вырезку швов перед моталкой, сматывание полосы в рулон, раскантовку рулона на торец для последующей термической обработки.
Среднечасовая производительность агрегата 20 т. Заправочная скорость агрегата 0,5 м/с. Рабочая скорость движения полосы при обезжиривании 0,5-5,0 м/с. К ваннам обезжиривания подается ток промышленной частоты силой 10-15 кА. Напряжение в ваннах 6-9 В, плотность тока 5-10 А/дм3, температура обезжиривающего и моечного раствора 70-90 °С, температура промывочной воды 70-90 °С. Температура воздуха на сушильной машине 90 °С.
Состав обезжиривающего раствора, г/л: 15-25 каустической соды, 15-25 тринатрийфосфата, 3-4 эмульгаторов ОП-7 и ОП-10.
Для термообработки металла в цехе установлены агрегат непрерывного отжига с проходной печью башенного типа и колпаковые печи для светлого рекристаллизационного отжига. В соответствии с технологическим процессом все оборудование агрегата непрерывного рекристаллизационного отжига условно разделено на три части: головную, среднюю (печную) и хвостовую.
Оборудование головной части агрегата предназначено для приемки и разматывания рулонов, обрезки толстых коробоватых и замятых передних и задних концов полос, создание непрерывной полосы путем сварки концов рулона внахлестку, обрезки и смотки боковых кромок, очистки и обезжиривания полосы от загрязнений и технологической смазки, создания запаса полосы, транспортировки полосы до печной части. В состав головной части агрегата входят: приемный стеллаж, разматыватель, задающее устройство, сдвоенные гильотинные ножницы, сварочная машина, тянущие ролики, петлевая яма, дисковые ножницы с кромкомоталкой, установка электролитической очистки, гильотинные ножницы, тянущие ролики.
Оборудование средней (печной) части предназначено для светлого рекристаллизационного отжига в среде 95-96 % азота и 4-5 % водорода. В состав средней части входят: регулятор натяжения полосы, протяжная вертикальная петлевая печь башенного типа, тележка для заправки полосы в печь, петлевые ямы и другое.
Протяжная печь предназначена для нагрева полосы до 580-720 °С и охлаждения её до 60-70 °С. Производительность печи от 15 до 30 т/ч зависит от ширины полосы.
Хвостовая часть агрегата предназначена для смотки полос в рулоны и выдачи их с агрегата. В состав хвостовой части входят: тянущие ролики, гильотинные ножницы, две моталки и сниматели рулонов.
В цехе установлена 21 колпаковая печь для светлого рекристаллизационного отжига. Металл нагревается в печи до 720 °С, а затем охлаждается до 180 °С. Максимальная масса садки 180 т, максимальная высота стопы 3220 мм. Максимальный диаметр нагреваемого рулона 1860 мм. Производительность печи 3-4 т/ч. Металл для термообработки поступает с агрегата электролитического обезжиривания и очистки ленты.
Непрерывные двухклетевые дрессировочные станы 1200 № 1 и № 2 предназначены для дрессировки холоднокатаных полос из малоуглеродистой стали, свернутых в рулон и прошедших светлый отжиг. Материал полосы - сталь sв 450 МПа. Ширина дрессируемой полосы 500-1050 мм, толщина 0,20-0,63 мм. Внутренний диаметр рулона - 500 мм, наружный 1860 мм.
Максимальное усилие металла на валки 5 МН, наибольший крутящий момент, передаваемый рабочим валком, 9,81 кН·м.
Скорость движения полосы на выходе из второй клети стана № 1 до 24,5 м/с, стана № 2 - до 26 м/с. Заправочная скорость 1,5 м/с. Наибольшее натяжение полосы на моталке 19,6 кН, между клетями 58,9 кН. Диаметр рабочих валков 465-480 мм, опорных 1220-1320 мм.
Агрегат поперечной резки предназначен для правки, обрезки боковых кромок, порезки полосы на листы заданной длины и укладки в пачки после автоматической поточной сортировки. Материал разрезаемой полосы - углеродистая сталь с sв 588 Н/мм2; наружный диаметр поступающих 15-т рулонов 900-1850 мм, внутренний 500 мм. Размеры разрезаемой полосы: толщина 0,18-0,63 мм, ширина 500-1050 мм. Скорость передвижения полосы 1,5-2,0 м/с, заправочная 0,5 м/с.
В состав оборудования агрегата входят: цепной транспортер, приемный стол разматывателя, тянущие ролики, гильотинные ножницы для обрезки утолщенного, неровного или загрязненного переднего конца с усилием реза 147 кН, петлевое устройство, дисковые ножницы для обрезки боковых кромок, кромкомоталка, летучие ножницы для правки полосы и порезки её на мерные длины, состоящие из собственно летучих ножниц, падающих роликов и роликоправильной машины, пакетирующее устройство.
Агрегаты горячего лужения предназначены для нанесения оловянного покрытия на карточки жести погружением в расплав олова. Размеры карточек, поступающих на лужение, мм: ширина 712, длина 512, толщина 0,2-0,36. В потоке каждого агрегата горячего лужения жесть травится, промывается, покрывается оловом с формированием покрытия в жировой среде, обезжиривается, чистится, рассортировывается в потоке и укладывается в пачки. Скорость лужения 30-42 листа в минуту на каждом агрегате. В состав оборудования каждого агрегата входят: задатчик листов, узел травления и промывки жести, узел нанесения и формирования покрытия и узел очистки жести для обезжиривания и полировки жести.
Агрегат электролитического лужения жести предназначен для нанесения оловянного покрытия на полосу, смотанную в рулон.
Ширина обрабатываемой полосы 500-1050 мм, толщина 0,15-0,5 мм, наружный диаметр 15-т рулона 1800 мм, внутренний 500 мм, скорость агрегата 70 м/с.
В состав агрегата входят: подъемно-передвижная тележка для подачи и установки рулонов на барабан разматывателя, разматыватель, гильотинные ножницы для обрезки передних и задних утолщенных концов, сварочная машина для сварки полос внахлестку, дисковые ножницы для обрезки боковых кромок, кромкомоталка, комплект роликов для создания натяжения, гильотинные ножницы для разрезки полосы после намотки рулона на барабан моталки и моталка для сматывания полосы в рулон.
Максимальная скорость прохождения полосы через агрегат: на входном и выходном участках 6,7 м/с, на технологическом участке 5 м/с. Электролит кислый (фенолсульфоновый). Лужение полосы ведется с обеих сторон. В качестве анодов используют бруски олова. Катодная плотность тока 15-30 А/дм2. Сила тока, подаваемого на каждую сторону полосы, зависит от толщины оловянного покрытия, скорости движения полосы и определяется в каждом случае отдельно.
Агрегат непрерывного горячего цинкования предназначен для обработки полос из углеродистой стали, поступающих непосредственно со станов холодной прокатки, с последующей выдачей готовой продукции в виде листов.
Размеры холоднокатаных листов и рулонов, поступающих на цинкование: толщина полосы 0,45-1,45 мм, ширина 700-1320 мм, наружный диаметр рулона 1800 мм, внутренний 500, 600 и 800 мм. Масса 15 т.
В потоке агрегата холоднокатаная полоса подвергается химическому и электрохимическому обезжириванию, промывке, термическому обезжириванию, рекристаллизационному отжигу, покрытию в ванне с расплавленным цинком. Оцинкованную полосу подвергают принудительному и естественному охлаждению, пассивации, промасливанию, а затем разрезают на листы мерной длины.
Размеры оцинкованных листов: толщина 0,5-1,5 мм, ширина 0,7-1,32 м, длина 0,7- 4,0 м. Скорость движения полосы во входной и выходной секциях 1,3 м/с, в технологической 1 м/с.
Оборудование входной секции предназначено для приемки и разматывания рулонов, обрезки толстых, коробоватых и замятых передних и задних концов полос, сварки концов рулонов внахлестку, обрезки и смотки в рулон боковых кромок. Оборудование технологической секции агрегата предназначено для химического, электрохимического и термического обезжиривания поверхности полосы, рекристаллизационного отжига в восстановительной среде, покрытия методом горячего погружения, охлаждения оцинкованной полосы, пассивации цинкового покрытия.
Для отжига служит горизонтальная протяжная печь. Длина участка нагрева 60 м, охлаждения 46 м.
Ванны оцинкования вмещают ~ 75 т расплавленного цинка при 440 °С. Оборудование выходной секции предназначено для транспортировки и создания запаса оцинкованной полосы, измерения толщины покрытия и общей толщины полосы, промасливания, порезки на мерные длины с последующей сортировкой в потоке агрегата и укладкой в пачки.
3 Выбор режимов обжатий и расчет энергосиловых параметров процесса холодной прокатки
Величина суммарного обжатия при холодной прокатке выбирается, исходя из требований, предъявляемых к структуре, механическим и технологическим свойствам готовой полосы, с учетом химического состава прокатываемой стали, мощности приводов рабочих клетей, технологической смазки и т.д. Кроме того, учитывается возможность и целесообразность получения требуемой толщины подката на стане горячей прокатки.
В качестве заготовки для производства листа сечением 0.35х1050 мм из стали 08кп выбираем горячекатаную полосу сечением 2.5х1050 мм. Суммарное обжатие при прокатке листов не превышает 90%. Обжатие на стане изменяется от 45% в первой клети до 8–15% в последней, которую используют в качестве калибрующей. Обжатие зависит от величины контактных напряжений, которые растут от клети к клети по мере наклепа и отношения . Ограничивающим фактором при назначении режимов обжатий выступает контактная прочность валков. Как правило, прокатку полосы на непрерывном стане осуществляют за один проход, однако в некоторых случаях для получения требуемых толщины готовой полосы и её свойств после первого прохода рулон подвергают отжигу и затем прокатывают вторично на этом же стане.
1. Величина абсолютного обжатия

2. Относительное обжатие
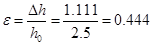
3. Длина дуги контакта

4. Фактический предел текучести [4, с 11.]

5. Значение удвоенного сопротивления чистому сдвигу

6. Коэффициент, учитывающий влияние контактного трения и внешних зон

7. Толщина полосы в нейтральном сечении

8. Величина коэффициента напряженного состояния
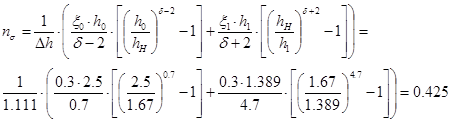
9. Среднее нормальное контактное напряжение в очаге деформации

10. Длина дуги контакта с учетом упругого сплющивания



11. Величина силы прокатки

12. Величина момента прокатки
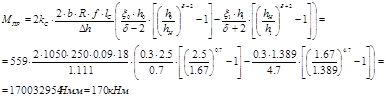
13. Мощность прокатки

При выбранном режиме прокатки энергосиловые параметры не превышают предельно допустимых значений.
Дальнейший расчет производим на ЭВМ. Результаты расчета приведены в таблице 3.
Таблица 3.1– Результаты расчёта обжатий на стане холодной прокатки
i |
H0
мм
|
h0
мм
|
h1
мм
|
e |
K2c
МПа
|
P
МН
|
M
кНм
|
N
МВт
|
V
м/с
|
1
|
2.50 |
2.500 |
1.389 |
0.444 |
559 |
7.89 |
170.0 |
4.080 |
4.00 |
2
|
2.50 |
1.389 |
0.930 |
0.403 |
778 |
10.40 |
169.8 |
7.335 |
9.80 |
3
|
2.50 |
0.830 |
0.574 |
0.308 |
842 |
9.76 |
110.5 |
7.990 |
12.18 |
4
|
2.50 |
0.574 |
0.438 |
0.237 |
879 |
9.15 |
76.0 |
7.947 |
21.14 |
5
|
2.50 |
0.438 |
0.350 |
0.162 |
900 |
8.82 |
57.7 |
7.905 |
26.28 |
Энергосиловые параметры не превышают допустимых значений, следовательно, данный режим загрузки стана является наиболее оптимальным и рациональным.
4. Расчет производительности стана
1. Время прокатки на заправочной скорости
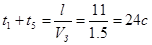
2. Время ускорения стана

3. Длина прокатываемой полосы

3. Время прокатки на рабочей скорости
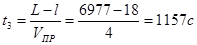
4. Машинное время

5. Ритм прокатки

6. Часовая производительность непрерывного стана холодной прокатки

7. Годовая производительность непрерывного стана холодной прокатки

5. Рекомендации по совершенствованию технологии прокатки
На современных станах холодной прокатки широко применяются различные системы автоматизации, которые являются основным средством повышения точности холоднокатаных полос. К таким системам следует отнести системы регулирования толщины полосы, регулирования натяжения полосы, регулирования профиля и формы полосы, подачи эмульсии на валки, замедления и точной остановки реверсивных станов и др. Имеются полностью автоматизированные станы холодной прокатки, управление которыми осуществляется ЭВМ.
Можно отметить следующие тенденции развития и совершенствования станов холодной прокатки:
1. Разработка новых конструкций рабочих клетей, в том числе предварительно напряженных клетей.
2. Широкое использование многовалковых станов, в том числе непрерывных восьми– и десятиклетевых станов с многовалковыми клетями.
3. Усовершенствование станов бесконечной прокатки.
4. Внедрение комплексной автоматизации на станах холодной прокатки с использованием управляющих ЭВМ.
5. Разработка и внедрение новых более эффективных способов регулирования профиля валков и толщины прокатываемой полосы.
6. Разработка и внедрение систем для подачи и очистки смазочно-охлаждающей жидкости и моющих растворов с целью улучшения качества поверхности прокатываемых полос.
7. Повышение точности обработки рабочих и опорных валков.
8. Применение в качестве главных приводов электродвигателей с широким диапазоном регулирования скорости.
9. Разработка и внедрение моталок с плавающими барабанами, обеспечивающих получение рулонов массой до 50 т и более, с ровными торцами.
10. Разработка и внедрение высокоскоростных механизмов и машин для перевалки рабочих валков всех клетей непрерывного стана в течение 5-10 мин.
Заключение
В ходе выполнения курсовой работы были рассмотрены станы холодной прокатки различной конструкции и производительности. Для производства листа заданного сортамента был выбран непрерывный стан 1200 холодной прокатки Магнитогорского металлургического комбината им. В.И. Ленина. Было рассмотрено входящее в состав стана оборудование и технология производства листовой стали. С помощью ЭВМ был разработан оптимальный режим обжатий, а также рассчитаны энергосиловые параметры – сила, момент и мощность прокатки. Был выполнен расчет технико-экономических показателей производства листовой стали. Расчет производительности стана показал, что выбранный режим работы стана обеспечивает заданную производительность 0.25 млн. т/год.
Перечень ссылок
1. Целиков А.И., Зюзин В.И. Современное развитие прокатных станов.– М.: Металлургия, 1972.
2. Целиков А.И., Полухин П.И., Гребенник В.М. Машины и агрегаты металлургических заводов. В 3-х томах. Т. 3. Машины и агрегаты для производства и отделки проката. Учебник для вузов. – М.: Металлургия, 1988.
3. Василев Я.Д., Сафьянов М.М. Производство полосовой и листовой стали. – Киев: Вища школа, 1975.
4. Методические указания к практическим занятиям по дисциплине “Технологические линии и комплексы металлургических цехов”. \Сост.: В.А. Федоринов, Э.П.Грибков. – Краматорск: ДГМА, 1999.
Приложение А
Текст программы для расчёта энергосиловых параметров процесса прокатки
CLS
'Программа для расчета режимов обжатий
'ТЛКМЦ курсовой
INPUT "Количество клетей в непрерывной группе стана"; N
INPUT "a0="; a0: INPUT "a1="; a1: INPUT "a2="; a2: INPUT "a3="; a3
INPUT "R="; R
INPUT "f="; f
INPUT "V0="; V
INPUT "b="; b
INPUT "Исходная толщина металла в отоженном состоянии"; Hh0
INPUT "Исходная толщина металла перед пропуском"; h0
INPUT "Допустимое значение силы прокатки .....(МН) [P]="; Pd: Pd = Pd * 1000000!
INPUT "Допустимое значение момента прокатки (кНм) [M]="; Md: Md = Md * 1000000!
INPUT "Допустимое значение мощности прокатки (МВт) [N]="; Nd: Nd = Nd * 1000000!
OPEN "2.txt" FOR OUTPUT AS 1
Hh0 = h0
f = .09
S0 = .5: S1 = .5
V = 4
PRINT " РЕЗУЛЬТАТЫ РАСЧЕТА ОБЖАТИЙ НА НЕПРЕРЫВНОМ СТАНЕ Х.ПР."
PRINT "┌──┬────┬─────┬─────┬─────┬────┬──────┬──────┬──────┬─────┐"
PRINT "│i │ H0 │ h0 │ h1 │ e │K2c │ P │ M │ N │ V │ "
PRINT "├──┼────┼─────┼─────┼─────┼────┼──────┼──────┼──────┼─────┤"
PRINT "│ │ мм │ мм │ мм │ │МПа │ МН │ кНм │ МВт │ м/с │ "
PRINT "├──┼────┼─────┼─────┼─────┼────┼──────┼──────┼──────┼─────┤"
PRINT #1, " РЕЗУЛЬТАТЫ РАСЧЕТА ОБЖАТИЙ НА НЕПРЕРЫВНОМ СТАНЕ Х.ПР."
PRINT #1, "┌──┬────┬─────┬─────┬─────┬────┬──────┬──────┬──────┬─────┐"
PRINT #1, "│i │ H0 │ h0 │ h1 │ e │K2c │ P │ M │ N │ V │ "
PRINT #1, "├──┼────┼─────┼─────┼─────┼────┼──────┼──────┼──────┼─────┤"
PRINT #1, "│ │ мм │ мм │ мм │ │МПа │ МН │ кНм │ МВт │ м/с │ "
PRINT #1, "├──┼────┼─────┼─────┼─────┼────┼──────┼──────┼──────┼─────┤"
FOR i = 1 TO N
h1 = h0* .44
10 :
IF h1 > h0 THEN INPUT "h0>h1"; asd$
dh = h0 - h1
e = dh / h0
e0 = (Hh0 - h0) / Hh0
x1 = a0 + a1 * e0 + a2 * e0 ^ 2 + a3 * e0 ^ 3
x2 = 2 / 3 * (a1 + 2 * a2 * e0 + 3 * a3 * e0 ^ 2) * e
x3 = 8 / 15 * (1 - e0) ^ 2 * (a2 + 3 * a3 * e0) * e ^ 2
x4 = 16 / 35 * (1 - e0) ^ 3 * a3 * e ^ 3
K2c = 1.15 * (x1 + x2 + x3 + x4)
L = SQR(R * dh)
ksi0 = 1 - S0: ksi1 = 1 - S1
DO
delta = 2 * f * L / dh: IF delta = 2 THEN delta = 2.1
Hn = (ksi0 / ksi1 * h0 ^ (delta - 1) * h1 ^ (delta + 1)) ^ (1 / 2 / delta)
IF Hn = 0 OR h1 = 0 THEN INPUT "h=0"; ads$
y1 = (h0 / Hn) ^ (delta - 2) - 1
y1 = y1 * ksi0 * h0 / (delta - 2)
y2 = (Hn / h1) ^ (delta + 2) - 1
y2 = y2 * ksi1 * h1 / (delta + 2)
nG = (y1 + y2) / dh
Pcp = K2c * nG
x2 = 8 * Pcp * R * 2 * (1 - .3 ^ 2) / 3.14 / 210000!
Lc = SQR(R * dh + x2 ^ 2) + x2
dL = ABS(Lc - L) / L * 100
L = Lc
LOOP UNTIL dL > 5
P = Pcp * b * L
M = 2 * K2c * (y1 - y2) * R * f / dh * b * L
Nw = M * V / R
IF P > Pd OR M > Md OR Nw > Nd THEN h1 = h1 + .001: GOTO 10
PRINT USING "│##│#.##│#.###│#.###│#.###│####│###.##│####.#│##.###│##.##│"; i; Hh0; h0; h1; e; K2c; P / 1000000!; M / 1000000; Nw / 1000000; V
PRINT #1, USING "│##│#.##│#.###│#.###│#.###│####│###.##│####.#│##.###│##.##│"; i; Hh0; h0; h1; e; K2c; P / 1000000!; M / 1000000; Nw / 1000000; V
V = V * h0 / h1: h0 = h1
NEXT
PRINT "└──┴────┴─────┴─────┴─────┴────┴──────┴──────┴──────┴─────┘"
PRINT #1, "└──┴────┴─────┴─────┴─────┴────┴──────┴──────┴──────┴─────┘"
CLOSE 1
END
Приложение Б – Графики распределения параметров прокатки по
проходам
ИЗМЕНЕНИЕ ОБЖАТИЯ
Е
ИЗМЕНЕНИЕ СИЛЫ ПРОКАТКИ
Р,МН
ИЗМЕНЕНИЕ МОМЕНТА ПРОКАТКИ
М,кН*м
ИЗМЕНЕНИЕ МОЩНОСТИ
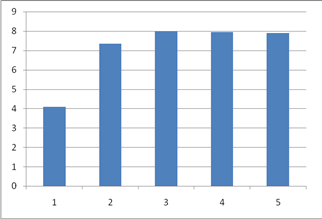
N,МВт
ИЗМЕНЕНИЕ СКОРОСТИ
V,м/с
|