ЗМІСТ
Вступ
1. Якість обробки заготовок
2. Обробка заготовок різанням
3. Структура технологічного процесу механічної обробки
4. Проектування технологічних процесів
5. Техніко-економічна оцінка технологічних процесів
6. Термічна і хіміко-термічна обробка заготовок і деталей
7. Технології одержання зварних з'єднань
8. Технологічні процеси паяння, клепання, клеєння
Висновок
Література
Вступ
Тема реферату «Технологічні процеси обробки заготовок».
Для розкриття даної теми треба розглянути такі питання:
- якість обробки заготовок;
- обробка заготовок різанням;
- структуру технологічного процесу механічної обробки;
- проектування технологічних процесів;
- техніко-економічну оцінку технологічних процесів;
- термічну і хіміко-термічну обробку заготовок і деталей;
- технології одержання зварних з'єднань;
- технологічні процеси паяння, клепання, клеєння.
1. Якість обробки заготовок
Під якістю деталі розуміють сукупність усіх її властивостей, котрі повністю забезпечують поставлені до неї експлуатаційні вимоги. Шляхи досягнення потрібної якості вирішуються комплексно з врахуванням усіх стадій технологічного процесу. Якість деталі визначається двома важливими показниками -точністю розмірів і шорсткістю поверхонь.
Під точністю обробки розуміють ступінь відповідності величини розміру, форми, розміщення і шорсткості певної поверхні виготовленої деталі до тих же параметрів, заданих на кресленні. Абсолютно точно виготовити деталь неможливо. При виготовленні деталей мають місце похибки (розмірів, форми, шорсткості поверхонь, їх взаємного розміщення). Основні причини похибок деталей такі: неточність встановлення деталі, інструментів; неточність верстатів та оснащення; деформації деталі в процесі обробки; кваліфікація робітників, неточність вимірювальних інструментів і вимірювання тощо.
З урахуванням цього, встановлюють допустимі відхилення параметрів виготовлених деталей (розмірів) відносно тих, що задані на кресленні. Початком відрахунку відхилень є номінальний розмір - розмір, котрий визначають відповідно до функціонального призначення деталі і вказують на кресленні. Розмір, отриманий вимірюванням після обробки, називають дійсним. Між дійсним і номінальним розмірами є різниця, - відхилення. Ці відхилення не можуть бути великими. Тому при конструюванні деталей встановлюють границі відхилень, тобто є два граничні розміри, між якими можуть коливатися дійсні розміри. Граничні розміри (відхилення) разом з номінальними вказують на кресленнях. Граничні відхилення можуть бути додатними і від'ємними, односторонніми та двосторонніми, симетричними і несиметричними. Різницю між граничними розмірами називають допуском на розмір.
На практиці існують поняття економічної та досяжної точності. Економічної точності досягають у нормальних виробничих умовах, вона забезпечує мінімальну собівартість обробки. Досяжна точність - така, яку досягають в покращених, спеціально створених умовах. При цьому підвищується собівартість деталі.
Ступінь точності визначають рядами допусків, котрі називають квалітетами. Квалітетів є 19, їх позначають ІТ01, ІТО, ІТ1 - IT 17. Чим більший порядковий номер, тим більший допуск, тим нижча точність.
Під шорсткістю поверхні розуміють сукупність нерівностей, що утворюють рельєф поверхні і розглядаються в границях відповідної ділянки. Шорсткість поверхні оцінюють за допомогою спеціальних приладів - профілометрів. На кресленні деталі шорсткість обробки позначають відповідними знаками, що вказують на вид обробки поверхні, базову довжину та умовне позначення напряму нерівностей, параметри шорсткості. Шорсткість визначає якість і термін служби деталей машин, агрегатів, приладів, впливає на корозійну стійкість.
Стандартом встановлено 14класів шорсткості. Із підвищенням порядкового номеру шорсткість поверхні зменшується.
2. Обробка заготовок різанням
Для обробки заготовок деталей машин застосовують: механічну обробку різанням, обробку пластичним деформуванням без зняття стружки, обробку з використанням хімічної, електричної, променевої, світлової та інших видів енергії. Доволі прогресивними є комбіновані способи.
З усіх способів обробки найпоширенішими є способи обробки заготовок різанням. Сьогодні на машинобудівних підприємствах металорізальні верстати становлять 50-80% від загальної кількості обладнання. Частка обробки різанням становить близько 35%,а отже, впливає на темпи розвитку машинобудування.
Обробка різанням - це процес, при якому із заготовки (відливки, поковки) зрізується шар металу з метою одержання деталі певної геометричної форми, точності розмірів і шорсткості поверхонь. Шар металу, що зрізується, називають припуском на механічну обробку. На рисунку 1 показано величину припуску (заштриховано). Бувають припуски загальні та міжопераційні, симетричні й несиметричні. Припуск на обробку впливає як на якість деталі, так і на її собівартість. Він має бути оптимальним.
Рис. 1. Ескіз деталі з припуском на обробку
Механічну обробку різанням здійснюють на металорізальних верстатах за допомогою металорізальних інструментів. Різання металів - це складний і трудомісткий процес, що супроводжується рядом фізичних явищ. Пізнання фізичної суті процесу дає змогу керувати цим процесом, забезпечувати максимально можливу продуктивність обробки. При обробці різанням припуск на обробку зрізують за один раз, або за декілька. Кожен елементарний об'єм металу, що зрізується, утворює стружку. Види стружки залежать від властивостей матеріалу заготовки, геометрії і форми заточування різального інструмента, режимів різання. Розрізняють зливну стружку (при обробці пластичних матеріалів), елементну (у твердих, малов'язких), сколювання (у сталей з малими швидкостями різання), надлому (у твердих і крихких матеріалів).
Процес різання супроводжується значним виділенням тепла, що дуже впливає на спрацювання і стійкість металорізальних інструментів, на якість обробленої поверхні.
Тепловий баланс процесу різання підраховують так:
Qд
+ Qn
.
n
+ Qз.п.
= Q1
+ Q2
+ Q3
+ Q4
,
де Qд
- тепло від пластичних деформацій;
Qn
.
n
- тепло від тертя стружки об передню поверхню інструмента;
Qз.п.
- тепло від тертя задніх поверхонь інструмента об заготовку;
Q1
- тепло, що йде в стружку (45-94%);
Q2
- тепло, що залишається в деталі (43-3%);
Q3
-тепло, що переходить в інструмент (8-2%);
Q4
-тепло, що випромінюється в навколишнє середовище (~ 1%).
Зі збільшенням швидкості різання кількість тепла, що відводиться стружкою, збільшується. Небажаним є перегрів інструмента, тому що при цьому знижується його стійкість. Для попередження перегріву застосовують при різанні мастильно-охолоджувальні рідини (МОР). Вони знижують також злипання інструмента зі стружкою. Мастильно-охолоджувальними рідинами є емульсії, розчини соди у воді, солей, мінеральних масел, рослинні олії тощо. Вони підводяться зверху на зрізуваний шар металу.
У процесі обробки різанням заготовка і металорізальний інструмент приводяться в робочий рух металорізальними верстатами і переміщуються один відносно одного. При цьому необхідним є поєднання двох видів руху - головного руху різання і руху подачі.
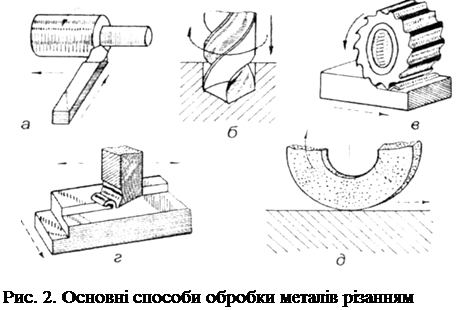
Основні способи обробки різанням такі: точіння, свердління, зенкерування, розвертання, протягування, фрезерування, стругання, шліфування та ін. (рис. 2).
При різних способах обробки взаємодія між оброблюваною заготовкою та інструментом різні. Так, при точінні (рис. 2 а) заготовка дістає рух різання (обертається), а інструмент - рух подачі (інструмент підводиться до заготовки і при обробці переміщується уздовж її осі). При свердлінні (рис. 2 б) і рух різання (обертовий), і рух подачі (поступовий) має інструмент, що обертається і переміщується уздовж своєї осі. При фрезеруванні (рис. 2 в) головним рухом різання є обертання інструмента (фрези), а рухом подачі - поступове переміщення заготовки або інструмента.
Процес обробки різанням характеризується певними елементами різання, сукупність яких називають режимом різання. Основними елементами режиму різання є наступні:
Швидкість різання -шлях точки ріжучого леза інструмента відносно заготовки в напрямі головного руху за одиницю часу:
V= 
де Д -діаметр заготовки, мм;
п -частота обертання заготовки, об/хв.
Подача (S) -величина переміщення точки ріжучого леза інструмента відносно заготовки в напрямі руху подачі за один оберт заготовки або за один подвійний хід заготовки чи інструмента. Подачу вимірюють в мм/об, мм/под.хід, мм/хв - при різних методах обробки. Величину подачі здебільшого вибирають з довідникових матеріалів, іноді задають наперед.
Глибина різання - відстань між оброблюваною і обробленою поверхнями заготовки, виміряна перпендикулярно до її осі, за один робочий хід інструмента відносно оброблюваної заготовки:
t = 
деD, d -діаметри оброблюваної та обробленої поверхонь за один прохід.
Глибину різання вимірюють в мм. До елементів процесу різання відносять також силу різання, потужність, норми часу та ін. Режим різання вибирають таким, щоб забезпечити найбільшу продуктивність процесу різання.
Для обробки різанням застосовують металорізальні інструменти. Їх назви часто співзвучні зі способами обробки. Вони бувають однолезовими (мають одне різальне лезо) і багатолезовими. Інструментами для точіння є різці. Це найпоширеніші металорізальні інструменти. Залежно від виду, характеру обробки, зовнішнього оформлення буває багато різновидів різців.
Інструменти для свердління - це свердла. За допомогою свердел виконують глухі або наскрізні отвори. Найпоширенішими є спіральні свердла.
Для обробки отворів після свердління застосовують зенкери, а після зенкерування (іноді зразу після свердління) розвертки. Ці інструменти називають чистовими. За допомогою них досягають вищого класу шорсткості поверхні та точніших розмірів отвору.
До чистових інструментів належать протяжки. Це багатолезові інструменти. Ними можна обробляти зовнішні поверхні й отвори, можна змінювати профіль отвору. Після протягування форма отвору може бути циліндричною, квадратною, багатогранною, овальною, фасонною, з канавками різних профілів.
Одним з найпоширеніших металорізальних інструментів є фрези. Це інструменти для обробки (фрезерування) плоских, криволінійних, фасонних та інших поверхонь. За формою зуба фрези бувають з прямими і гвинтовими зубами.
При обробці різанням застосовують також різьбонарізні інструменти (мітчики, плашки, гребінки, різьбонарізні головки та ін.), абразивні інструменти (шліфувальні круги різної форми, бруски, сегменти, головки) та інші спеціальні інструменти.
Продуктивність праці при різанні значною мірою залежить від тривалості роботи різального інструмента, протягом якого зберігається його різальна здатність. А це відповідно залежить від матеріалу, з якого виготовлений інструмент, його фізико-механічних властивостей. Матеріали, котрі використовують для виготовлення металорізальних інструментів, повинні мати такі властивості: високу твердість, значну механічну міцність, достатню в'язкість, червоностійкість, теплопровідність, високу стійкість проти спрацювання, стійкість до адгезії, хорошу оброблюваність. Для виготовлення металорізальних інструментів використовують інструментальні (вуглецеві, леговані, швидкорізальні) сталі, тверді сплави (металокерамічні матеріали), мінералокерамічні матеріали, абразивні матеріали (природні та штучні), конструкційні сталі (для виготовлення держаків, деталей кріплення). Крім того, появилися нові матеріали, що мають дуже високу твердість, червоностійкість, зносостійкість. Це ельбор, Славутич, карбід бору, борсилокарбід та інші. їх використовують для обробки спеціальних матеріалів і виконання спеціальних технологічних операцій.
Механічну обробку різанням здійснюють на металорізальних верстатах, котрі дуже різноманітні. їх якість, технічний рівень на тривалий час визначають продуктивність праці, якість і собівартість продукції в машинобудуванні.
Класифікують металорізальні верстати за такими ознаками:
а) за технологічним призначенням;
б) за універсальністю;
в) за конструктивними особливостями;
г) за ступенем автоматизації;
д) за точністю;
е) за ступенем шорсткості обробки;
є) за розмірами та масою.
Така класифікація зведена у спеціальну таблицю.
Кожній моделі верстата присвоєно певне позначення (марку). Наприклад, марки верстатів 162, 1620, 1А62, 2А125 та ін. Перша цифра означає групу верстату, друга - тип (різновид), третя (або дві останні) - основний параметр верстату. Літера, що стоїть після першої цифри, вказує на модернізацію базової моделі. Іноді літеру ставлять у кінці. Тоді вона вказує на модифікацію (видозміну) базової моделі, часом - на місце де виготовлено верстат.
Роботу металорізальних верстатів, ефективність використання оцінюють з допомогою техніко-економічних показників. Сюди входять точність, продуктивність, ступінь автоматизації, довговічність, надійність у роботі, безпека та зручність в обслуговуванні, собівартість, жорсткість і технологічність конструкції верстату тощо.
3. Структура технологічного процесу механічної обробки
Для забезпечення найбільш раціонального процесу механічної обробки заготовки складають план обробки, де вказують, які поверхні, в якій послідовності і якими способами потрібно обробляти. Тому, весь процес механічної обробки поділяють на окремі складові частини: операції, встановлення, позиції, переходи, проходи, прийоми.
Операцією називається завершена частина технологічного процесу, що виконується на одному робочому місці, охоплює всі дії робітника й обладнання (над однією або декількома деталями). Наприклад, обточування валу спочатку з одного кінця, а потім з іншого після його повертання без зняття з верстату є однією операцією. Якщо ж партію валів спочатку обточують на одному кінці, а потім на другому, то це вже дві операції.
Встановленням називають частину операції, виконувану при одному закріпленні деталі. У наведеному вище прикладі вал обточують при двох встановленнях. При кожному повертанні на будь-який кут здійснюють нове встановлення.
Позицією називається кожне окреме положення деталі, котрі вона займає відносно верстату при своєму незмінному закріпленні.
Операції поділяються на переходи.
Перехід- закінчена частина операції, що характеризується незмінністю інструментів, оброблюваних поверхонь, режимів роботи машин. Зміна хоча б одного з цих елементів визначає новий перехід. Переходи поділяються на проходи.
Під проходом розуміють частину переходу (неподільної операції), що характеризується одноразовим переміщенням інструменту відносно заготовки і зняттям одного шару металу.
Закінчену дію робітника називають прийомом. Звичайно ними є допоміжні дії - встановлення чи зняття заготовки, переключення швидкості або подачі та ін.
Операціям і переходам присвоюють порядкові номери. Операції формулюють коротко, за видом обробки, наприклад: токарна, фрезерна, свердлильна; переходи - більш докладно, вказуючи найменування, номер і розмір оброблюваної поверхні.
4. Проектування технологічних процесів
Проектування технологічних процесів є одним з найвідповідальніших етапів виробництва і має за мету встановити найбільш раціональний та ефективний метод обробки.
Вихідними даними для проектування технологічних процесів є такі, як: виробнича програма; робочі креслення заготовки і деталі (виробу); технічні умови на виготовлення деталі (машини), їх випробування і здачу; описи конструкцій; керівні та довідкові матеріали.
Проектування технологічних процесів відзначається складністю і трудомісткістю. Його виконують за декількома послідовними стадіями. На початковій стадії проводять укрупнені розрахунки та розробки (попередні намітки) технологічного процесу, на наступних стадіях їх уточнюють і конкретизують на основі детальних технологічних розрахунків.
При проектуванні технологічного процесу розв'язують наступні питання.
1. Встановлення типу виробництва та організаційних форм виконання технологічного процесу.
2. Визначення величини партії деталей, що запускаються у виробництво одночасно (для серійного виробництва), і такту випуску деталей (для масового виробництва).
3. Вибір виду заготовки і визначення її розмірів.
4. Встановлення плану і методів механічної обробки з вказаною послідовністю технологічних операцій.
5.Вибір типів і визначення технічних характеристик верстатів, пристосувань, металорізальних і вимірювальних інструментів.
6. Вибір технологічних баз.
7. Визначення режимів роботи на вибраних верстатах для кожної операції.
8. Визначення норм часу на обробку для кожної операції, визначення кваліфікації роботи.
9. Оцінювання техніко-економічної ефективності технологічного процесу.
10. Оформлення технологічної та технічної документації.
При проектуванні технологічних процесів можна запропонувати декілька варіантів. Навіть для порівняно простих деталей може бути розроблено декілька технологічних процесів, що повністю забезпечують вимоги робочого креслення і технічні умови. Спростити і прискорити розробку технологічних процесів може їх типізація. Для цього здійснюють класифікацію деталей і їх поверхонь за конструктивно-технологічними ознаками на базі спільності обладнання й оснащення. Відповідно до цієї класифікації встановлено вісім класів деталей, за якими деталі машин відрізняються формою і подібністю процесів їх виготовлення: корпусні деталі, круглі стержні, порожнинні циліндри, диски, не круглі стержні, невеликі деталі складної форми, кріпильні деталі, спеціальні деталі.
Типовий технологічний процес проектують для найбільш складної деталі певного класу (типу). Простіші деталі можна обробляти приблизно за тим же технологічним маршрутом, за винятком операцій, котрі не потрібно виконувати.
5. Техніко-економічна оцінка технологічних процесів
Для порівняння та визначення техніко-економічної оцінки декількох запроектованих технологічних процесів і вибору оптимального варіанту використовують техніко-економічні показники. До найхарактерніших із них належать наступні:
1. Собівартість деталі S, що визначається витратами на матеріал М, основною заробітною платою робітників Р і цеховими накладними витратами R:
S = М + Р + R.
2. Собівартість обробки деталі:
So=P + R.
3. Норми часу (штучного і штучно-калькуляційного) повної обробки деталі:
Тшт
=
Тк
= 
де Тшт
-штучний час на виконання всіх операцій обробки даної деталі;
tuim
- штучний час однієї операції;
Тк
-штучно-калькуляційний час на виконання всіх операцій обробки даної деталі;
tK
-штучно-калькуляційний час однієї операції обробки.
4. Основний (технологічний) час Та
за всіма операціями даної деталі:
То
= 
деtо
- основний технологічний час однієї операції обробки.
5. Коефіцієнт використання верстату за основним часом, що дорівнює відношенню основного часу до штучного або штучно-калькуляційного (залежно від виду виробництва):
η= і ηо
=
Чим більший цей показник, тим більшою є питома вага в структурі норми машинного часу.
6. Коефіцієнт завантаження обладнання за часом, що визначається відношенням розрахункової кількості верстатів С до фактичної (прийнятої) їх кількості Спр:
η з
=
7. Ступінь автоматизації виробництва, що характеризується відношенням числа верстатів з автоматизованим встановленням і зняттям деталей до загальної кількості одиниць виробничого обладнання цеху (відділу, дільниці).
Крім вказаних, для оцінки техніко-економічної ефективності технологічного процесу використовують ряд інших показників. Результати техніко-економічних розрахунків аналізують і приймають той варіант, котрий дає найбільш економічні рішення при задоволенні всіх технічних вимог.
6. Термічна і хіміко-термічна обробка заготовок і деталей
Термічна обробка- це теплова дія на заготовки і деталі з метою надання їм відповідних властивостей. При термічній обробці заготовки або деталі нагрівають до певної температури, витримують при цій температурі й охолоджують з певною швидкістю. За допомогою такої обробки можна змінювати властивості заготовок або деталей. Процесами термічної обробки можна керувати.
Якщо термічна обробка проводиться для підготовки наступних технологічних операцій, то її називають проміжною, якщо термічна обробка забезпечує ті властивості, що потрібні при експлуатації виробів, її називають кінцевою.
Технологічний процес термічної обробки можна зобразити графічно (рис. 3). На графіках показано ділянки нагрівання (0-1), витримування (1-2 і 3—4) та охолодження (2-3, 4-5). Із графіків видно, що охолоджувати можна з різною швидкістю і при охолодженні можливе проміжне витримування (ступінчаста термічна обробка).
Результати термічної обробки залежать від швидкості і температури нагрівання, часу витримування і швидкості охолодження. Вибір цих факторів проводять відповідно до виду обробки, розмірів виробів і їх матеріалу, мети досягнення конкретних якостей виробів.
Термічно обробляють як заготовки, так і готові деталі. При обробці заготовок поліпшуються їх оброблювальні властивості (знижується твердість, крихкість, підвищується пластичність, в'язкість, зменшується величина внутрішніх напружень, покращується оброблюваність різанням). При термічній обробці деталей поліпшуються їх експлуатаційні властивості (підвищується твердість, міцність, корозійна стійкість, стійкість до зношування та ін.).

Рис.3. Графічне зображення термічної обробки
В основі теорії термічної обробки лежать структурні фазові перетворення, що відбуваються в металах і сплавах (чорних і кольорових) при зміні температури (нагріванні та охолодженні).
Основними видами термічної обробки є відпалювання, гартування і відпускання. Відпалювання використовують для заготовок, гартування і відпускання - для деталей. Є декілька видів відпалювання. Розрізняють також повне (різні види) і поверхневе гартування та різні види відпускання. їх вибір залежить від конкретних ситуацій.
Хіміко-термічна обробка.
Хіміко-термічною обробкою називають процес зміни хімічного складу, структури і властивостей поверхневого шару деталей. Цей процес ґрунтується на дифузії в атомно-кристалічну решітку заліза атомів інших хімічних елементів при нагріванні деталей в середовищі багатому на ці елементи. При хіміко-термічній обробці поверхня деталей зміцнюється (підвищується твердість, стійкість до стирання, зношування), зростає їх стійкість до дії агресивних середовищ при нормальній і підвищеній температурах, жаростійкість.
При хіміко-термічній обробці мають місце такі фізико-хімічні процеси:
-дисоціація - розпад молекул і утворення активних атомів;
-адсорбція - поглинання поверхнею деталі цих активних атомів;
-дифузія - проникнення активних атомів в поверхневий шар деталі.
Для проведення хіміко-термічної обробки деталі повинні бути вміщені у відповідне середовище, багате на елемент, яким потрібно наситити їх поверхню, і нагріті до певної температури. Середовище може бути твердим, рідким, газоподібним, його називають карбюризатором. Насичувати поверхні можна вуглецем, азотом, алюмінієм, кремнієм та іншими елементами. Крім цього, насичення можна проводити одним або декількома елементами. Залежно від того, яким елементом насичують деталі, розрізняють цементацію, азотування, ціанування, дифузійну металізацію. При цементації насичення проводять вуглецем, при азотуванні — азотом, при ціануванні - одночасно вуглецем та азотом, при дифузійній металізації - металами.
Техніко-економічні показники.
Процеси термічної і хіміко-термічної обробки забезпечують високу якість заготовок або деталей (потрібні властивості і структуру). Важливим є одночасне забезпечення корозійної стійкості деталей. Більшість із них відзначаються високою продуктивністю, можливістю автоматизації. Нагрівання заготовок або деталей відбувається в печах простої конструкції, де можна використовувати різні види палива, що дає можливість впливати на енергетичні витрати. Тут можна також використовувати прогресивні способи нагрівання, охолодження, вимірювання.
7. Технології одержання зварних з'єднань
Досить часто заготовки перед обробкою і деталі при складанні машин, з'єднують. З'єднання бувають роз'ємні і нероз'ємні. Роз'ємні з'єднання виконують за допомогою з'єднувальних деталей. В разі потреби їх можна розібрати. Нероз'ємні з'єднання найчастіше виконують зварюванням, паянням, клепанням, склеюванням. Такі з'єднання при розборі руйнуються. З усіх нероз'ємних з'єднань найчастіше застосовують зварювання.
Зварюванням називається технологічний процес одержання нероз'ємних з'єднань за рахунок міжатомної взаємодії, що має місце при місцевому сплавленні або спільному пластичному деформуванні з'єднуваних частин. Для цього заготовки потрібно наблизити на відстані, що дорівнюють атомному радіусу. Поверхні, котрі зварюють, очищають і нагрівають до розплавлений країв або до пластичного стану. Нагріті до пластичного стану заготовки додатково стискають. При зварюванні у рідкій фазі використовують додатковий матеріал, щоб заповнити відстань між заготовками. Розплав кристалізується і утворюється з'єднання, яке називається швом. Шви бувають основні та допоміжні, одно- і двосторонні, горизонтальні та вертикальні, нижні і верхні.
Сучасні способи зварювання дуже різноманітні. їх класифікують за видом використовуваної енергії, за станом металу під час зварювання, за способом утворення зварного шва, за ступенем автоматизації та іншими ознаками. Розглянемо декілька з них.
Електричне дугове зварювання.
Це найпоширеніший сьогодні спосіб. Для розплавлення поверхонь зварюваних заготовок використовують електричну дугу - потужний електричний розряд, який супроводжується виділенням великої кількості теплової та світлової енергії. Можна використовувати постійний і змінний струм, плавкі (металеві) і неплавкі (графітові або вугільні) електроди. Джерелом постійного струму є зварювальні генератори і випрямлячі електричного струму, джерелом змінного струму є зварювальні трансформатори і генератори. Коли використовують неплавкі електроди, потрібен додатковий металевий стрижень або дріт, щоб заповнити відстань між заготовками. Плавкий електрод цю функцію виконує сам. Існує декілька способів електродугового зварювання (рис. 4).

Крім того, електродугове зварювання буває ручним, напівавтоматичним та автоматичним. Автоматичне виконують під шаром флюсів, що забезпечує високу якість і міцність зварних швів, а також високу продуктивність. Для зварювання заготовок великої товщини (більше 30-40 мм) використовують електрошлакове зварювання. Це бездугове електричне зварювання. Воно здійснюється за рахунок теплоти, що виділяється розплавленим шлаком при проходженні через нього струму. Автоматичне зварювання під шаром флюсів та електрошлакове зварювання розроблені в Україні, у Науково-дослідному інституті електрозварювання АН України ім. Е. О. Патона. Ці способи використовують у багатьох країнах світу.
Електродугове зварювання застосовують в усіх виробничих сферах - при прокладанні трубопроводів, спорудженні мостів, різних будівель і споруд, при виготовленні котлів, різних місткостей, машин, приладів, механізмів.
Газове зварювання.
При такому зварюванні джерелом тепла є хімічна енергія, утворена від згоряння горючого газу в атмосфері кисню. В якості горючих газів можна використовувати природний газ, водень, пари бензину, ацетилен та ін. Ацетилен при згорянні виділяє найбільше теплоти (3200°С), і його використовують найчастіше. Одержують ацетилен в газогенераторах із карбіду кальцію при його взаємодії з водою. Його можна одержувати просто на місці зварювання, або ж використовувати ацетилен заводського одержання. Цей газ зберігають в балонах білого кольору під тиском 1,6 МПа. Кисень для газового зварювання зберігають у балонах синього кольору під тиском 16 МПа.
Інструментом для газового зварювання є пальник. За його допомогою дозують і змішують кисень та ацетилен, утворюється стійке і концентроване полум'я. Для утворення шва при газовому зварюванні використовують додатковий стержень або дріт. Він повинен мати такий склад і структуру, як зварюваний матеріал.
Розрізняють два основні способи газового зварювання: правий і лівий (рис. 5). При правому можна зварювати заготовки товщиною більше 5мм, при лівому - до 5мм.
Газове зварювання найчастіше застосовують при зварюванні трубчастих і листових заготовок з маловуглецевих і низьколегованих сталей, для виправлення ливарного браку, в ремонтних роботах, у польових умовах.
Електроконтактне зварювання - це один із доволі поширених способів зварювання. Суть його в тому, що виникає короткочасне проходження струму через місце контакту і швидка пластична деформація (стискання). З'єднання відбувається дуже швидко. У місці контакту деталей електричний опір зростає, порівняно з іншими ділянками кола. Сила струму досягає сотень і тисяч ампер.

Електроконтактне зварювання поділяється на стикове, точкове і шовне (рис. 6). Воно може бути без оплавлення і з оплавленням. Якщо заготовки наближають при включеному зварюваному струмі, їх поверхні оплавляються. Якщо ж стискають і одночасно вмикають струм, заготовки не оплавляються.

Електроконтактне зварювання відбувається на зварювальних автоматах. Його використовують в усіх галузях промисловості, в будівництві, на транспорті, при виготовленні труб, тонкостінних посудин для зберігання рідин, газів. Цим способом можна зварювати різні матеріали.
Зварювання тертям.

При такому зварюванні відбувається взаємне переміщення зварюваних заготовок, короткочасний нагрів від нього і стискання силою Р (рис. 7). Тертя поверхонь здійснюється обертанням або зворотно-поступальним переміщенням заготовок. Внаслідок нагріву і стискання виникає взаємна пластична деформація.
Тертям з'єднують однорідні та різнорідні метали і сплави з різними властивостями (мідь зі сталлю, мідь з алюмінієм, алюміній з титаном та ін.). Застосовують таке зварювання при виготовленні металорізальних інструментів, валів, штоків з поршнями, пуансонів, при зварюванні труб тощо.
Дифузійне зварювання у вакуумі.
Це зварювання належить до прогресивних і перспективних способів. При дифузійному зварюванні з'єднання утворюється в результаті тривалого нагріву і стискання заготовок у вакуумі (або в атмосфері інертних газів). Нагрівають заготовки за допомогою вольфрамового або молібденового нагрівника чи індуктора. Може бути використаний електронний промінь, наприклад, при нагріві тугоплавких металів і сплавів. Після досягнення потрібної температури до заготовок прикладають невелике стискуюче зусилля (1-20 МПа) протягом 5-20 хв. Таке тривале витримування збільшує площу контакту. Контактні поверхні можуть бути плоскими, сферичними, конічними, рельєфними. їх потрібно добре очищати.
При дифузійному зварюванні можна з'єднувати різнорідні й однорідні матеріали, не беручи до уваги їх твердість і взаємну змочуванність. Такі з'єднання міцні і щільні. Можна одержати біметалеві, триметалеві, тетраметалеві деталі. Після зварювання не потрібна механічна обробка для видалення шлаку, окалини.
Дифузійне зварювання застосовують в електронній техніці та радіоелектроніці, у приладо-, суднобудуванні, космічній техніці, текстильному машинобудуванні, в харчовій промисловості та інших галузях.
Техніко - економічні показники.
Зварювання належить до високопродуктивних процесів. Зварні з'єднання відзначаються високою якістю і надійністю. Зварювати можна метали, сплави, скло, кераміку, тканини, шкіру, метали зі склом, керамікою. Заготовки складної конфігурації, великорозмірні найчастіше одержують зварюванням. Зварювання забезпечує економію металів (не потрібні з'єднувальні деталі), зменшення маси конструкцій.
Процеси зварювання мають високий рівень механізації і автоматизації, що робить їх ефективнішими порівняно з іншими видами з'єднань. Зварювання можна поєднувати з іншими технологічними процесами (штампуванням, клепанням, клеєнням), що дає можливість виготовляти деталі складної конфігурації і точних розмірів. Зварювання застосовують для виправлення дефектів лиття, відновлення деталей. Деякі з'єднання можна одержати тільки зварюванням.
8. Технологічні процеси паяння, клепання, клеєння
Паянням називають процес нероз'ємного з'єднання металевих і неметалевих заготовок, які перебувають у твердому стані, за допомогою розплавленого металу - припою. Температура плавлення припою має бути нижчою від температури плавлення матеріалу з'єднуваних заготовок. Припій заповнює щілину між заготовками за рахунок дії капілярних сил. При охолодженні він кристалізується й утворює міцне з'єднання між заготовками. У процесі паяння поверхні заготовок треба очищати від оксидних плівок. Припоями є олово, цинк, свинець, мідь, їх сплави.
Процес утворення з'єднання при паянні включає такі операції: прогрівання заготовок до температури, близької до температури плавлення припою; розплавленім припою; змочування припоєм поверхонь заготовок і заповнення паяного шва; охолодження і кристалізація припою. Якість паяного шва залежить від міцності зв'язку між припоєм і металом заготовок.
Для видалення оксидів і захисту від окислення металу при паянні використовують флюси. Флюси можуть бути тверді, пастоподібні, рідкі і газоподібні. Найчастіше застосовують борну кислоту, хлористий цинк, каніфоль та ін.
Паяти можна вуглецеві і леговані сталі всіх марок, тверді сплави, ковкі і сірі чавуни, всі кольорові метали та їх сплави. Можна паяти різнорідні матеріали (сталь з твердим сплавом). Застосовують паяння при виробництві автомобілів, велосипедів, приладів, інструментів.
Обладнанням для паяння є мідні паяльники, газові пальники та ін.
Техніко - економічні показники.
Паяння забезпечує високу міцність, якість і чистоту спаю, збереження розмірів і форми спаяних частин, виконується просто, його можна механізувати і автоматизувати. Ефективним є виконання процесу паяння зануренням виробів у розплавлений припій. Підвищується продуктивність, зменшуються трудові витрати. Особливо це є ефективним у масовому виробництві. Доволі ефективним також є паяння-зварювання. З'єднання туї утворюється таке, як при зварюванні, але як присадний метал використовують припій.
Клепання.
При клепанні з'єднання деталей і конструкцій проводять заклепками. Заклепка - це стержень круглого перерізу із наперед виготовленою головкою на одному кінці. На другому кінці головка утворюється в процесі клепання. Заклепки бувають з круглою головкою, потаємною, напівпотаємною, циліндричною, конічною, бувають також спеціальні. Виготовляють заклепки зі сталі, міді, алюмінію, латуні та інших сплавів, зі значною пластичністю (для формування головки). Матеріал заклепок вибирають однорідним з матеріалом з'єднуваних деталей.
Основні операції клепання такі: утворення отвору під заклепку (свердлінням, пробиванням); утворення гнізда під потаємну головку; встановлення заклепки в отвір; утворення головки з другого боку (ударом, пресуванням). При клепанні використовують клепальні машини (преси, автомати), клепальні молотки та ін.
Застосовують клепання для з'єднання листового і профільного прокату при виготовленні кузовів автобусів, тролейбусів.
Техніко - економічні показники.
Клепальні з'єднання здатні витримувати вібраційні та ударні навантаження і є ефективними в значно навантажених з'єднаннях транспортних машин. Процес клепання можна виконувати на спеціальних машинах-автоматах, що забезпечують виконання всього комплексу робіт і мають високу продуктивність. Продуктивність клепальних автоматів сягає 300-600 заклепок за годину.
Клеєння.
З'єднання деталей клеями широко застосовують в різних галузях для однорідних і різнорідних матеріалів. Для з'єднання прилеглі поверхні деталей мають бути змочені клеєм і міцно прилягати одна до одної. Затвердіння клею відбувається при випаровуванні розчинника або в результаті хімічних реакцій (без нагрівання чи з ним). Товщина прошарку клею становить 0,01-0,1мм.
Основні операції процесу склеювання такі: підготовка поверхонь; нанесення клею; склеювання при відповідних температурах, тиску і часі витримування; очищення з'єднань; контроль якості. При склеюванні потрібно забезпечити добру змочуванність клеєм з'єднуваних поверхонь, їх щільне прилягання, максимальну поверхню склеювання.
Клеї є розчинами високомолекулярних сполук (природних або штучних). Вони бувають з елементів рослинного або тваринного походження і синтетичні.
Техніко-економічні показники.
Клеєні з'єднання мають високу міцність, вібростійкість, герметичність. Вони забезпечують рівномірний розподіл напруг. Найчастіше за допомогою клею виконують з'єднання, що працюють на зсув або рівномірний відрив. Найбільш ефективно використовувати склеювання замість клепання. Нині склеювання набуває щораз більшого застосування.
Висновок
В рефераті ми розглянули такі питання:
- якість обробки заготовок;
- обробка заготовок різанням;
- структуру технологічного процесу механічної обробки;
- проектування технологічних процесів;
- техніко-економічну оцінку технологічних процесів;
- термічну і хіміко-термічну обробку заготовок і деталей;
- технології одержання зварних з'єднань;
- технологічні процеси паяння, клепання, клеєння.
Література
1. Колотило Д.М. Системи технологій і екологія промисловості – К., НМКВО, 1992 – 143 с.
2. Основы технологии важнейших отраслей промышленности. Ч.I, II/ Под ред. И.В. Ченцова – Минск, Вышейшая шк., 1989
3. Технологічні процеси галузей промисловості: Навч. посіб. / За ред.. Д.М. Колотила, А.Т. Соколовського – К, КНЕУ, 2008 – 372 с.
|