Лабораторная работа № 16
Производство валяной обуви.
Ценные свойства валяной обуви объясняются особой структурой ее стенок, которые состоят из компактной массы перепутанных и сцепленных друг с другом волокон шерсти. Малая теплопроводность вещества шерсти – каротина, наличие воздушных включений внутри волокон шерсти и пространства, занимаемого воздухом между волокнами шерсти в стенках валяной обуви, обусловливают способность последней служить надежной защитой ног от переохлаждения и перегрева.
Производство валяной обуви.
В основе производства валяной обуви, так же как и других валяных изделий, лежит использование способности шерсти свойлачиваться и сваливаться при механических воздействиях в кислой среде в присутствии влаги и при повышенной температуре. При этом извитые волокна шерсти тесно переплетаются, образуя сплошную войлокообразную массу, которая в процессе валки уплотняется, уменьшается в размерах и объеме.
Производство валяной обуви складывается из следующих основных процессов: подготовки сырья, составления смеси шерсти, ее расщипывания и чесания, изготовления основы валяной обуви, валки основы, крашения, сушки и отделки.
Технологическая схема производства валяной обуви на механизированных валяльно-войлочных предприятиях приводится на рис. 1.
Сырье для производства валяной обуви
Сырьем для изготовления валяльно-войлочных изделий служит шерсть овец, крупного рогатого скота, коз и других животных.
Качество валяльно-войлочных изделий зависит от тонины, извитости, длины, крепости и упругости исходной шерсти. Важнейшим технологическим свойством шерсти является ее валкоспособносгь, т. е. способность в большей или меньшей степени уплотняться при свойлачивании и валке. Объективных количественных показателей валкоспособности шерсти нет; на валяльно-войлочных предприятиях валкоспособность шерсти оценивают по десятибальной системе.
Для изготовления грубошерстной валяной обуви используют натуральную овечью грубую шерсть с добавлением заводской овечьей и коровьей шерсти, отходов мехового и овчинно-шубного производства, регенерированной шерсти и обратов производства.
Овечьей грубой шерстью называют неоднородную шерсть, состоящую из смеси волокон разного типа. Ее получают от овец всех грубошерстных пород, а также от некоторых, преимущественно первого поколения, помесей от скрещивания грубошерстных овец с баранами тонкорунных и полутонкорунных пород. Ее содержание в смеске может быть 47— 80%.
Валкоспособность грубой шерсти, помимо породы овец, в большой степени обусловливается временем их стрижки. По времени стрижки все виды грубой шерсти подразделяются на поярковую, весеннюю и осеннюю. Поярковая шерсть состригается с ягнят; эта шерсть более мягкая и извитая, чем шерсть осенних и весенних стрижек с этих же животных. Осенняя шерсть отличается меньшей загрязненностью и длиной волокна по сравнению с весенней, содержит меньше пуха, обладает высокой валкоспособностью и поэтому является наиболее ценным сырьем для производства грубошерстной валяной обуви. Каждая партия натуральной овечьей шерсти, поступающая на валяльно-войлочные предприятия, в обязательном порядке должна сопровождаться ветеринарным свидетельством о незараженности овец.
Заводскую шерсть получают в качестве побочного продукта при переработке кожевенного сырья на кожевенных заводах. Для изготовления валяной обуви используют зольную и намазную шерсть. Зольную шерсть удаляют с крупного кожевенного сырья после его обработки в зольниках растворами извести с добавлением сернистого натрия. Намазную шерсть получают при обезволашивании мелкого кожевенного сырья намазыванием мездряной стороны густым раствором извести и сернистого натрия. Из зольной шерсти наилучшей является коровья. Она обладает высокой валкоспособностью, придает валяльно-войлочным изделиям плотность и прочность. Из намазной шерсти лучшей считается овечья хребтовая: она, в отличие от овечьей боковой шерсти, относительно мало повреждена сернистым натрием и по качеству незначительно уступает натуральной овечьей шерсти. Содержание заводской шерсти в смеске — 10—21%.
Овечью шерсть в виде отходов мехового и овчинно-шубного производства получают при стрижке шкур и их расчесывании в процессе выделки овчин, а также путем варки в растворе серной кислоты мелкого лоскута, непригодного к использованию в качестве меха.
Регенерированную, или восстановленную, шерсть получают при разработке, т. е. расщипывании лоскута новых и бывших в употреблении шерстяных, тканей и войлока; в регенерированной шерсти волокно короче, чем в натуральной, обладает меньшей крепостью и меньшей способностью сволачиваться. Содержание восстановленной шерсти в смеске — 7—13%.
Обраты представляют собой внутрипроизводственные отходы, полученные на различных стадиях изготовления валяльно-войлочных изделий (6—12%). Наряду с обратами своего производства в валяльно-войлочной промышленности используют также отходы шерстопрядильных предприятий (8— 20%).
Фетровую валяную обувь изготовляют из натуральной овечьей полугрубой шерсти (отличающейся от грубой шерсти значительно меньшим содержанием остевых волокон) с добавлением отходов козьего пуха (козьей шерсти, освобожденной от ости), очесов шерстопрядильных фабрик и обратов производства, а также в ряде случаев штапельного вискозного волокна. Содержание полугрубой шерсти в смеске составляет 42—56%, козьего пуха — до 14%.
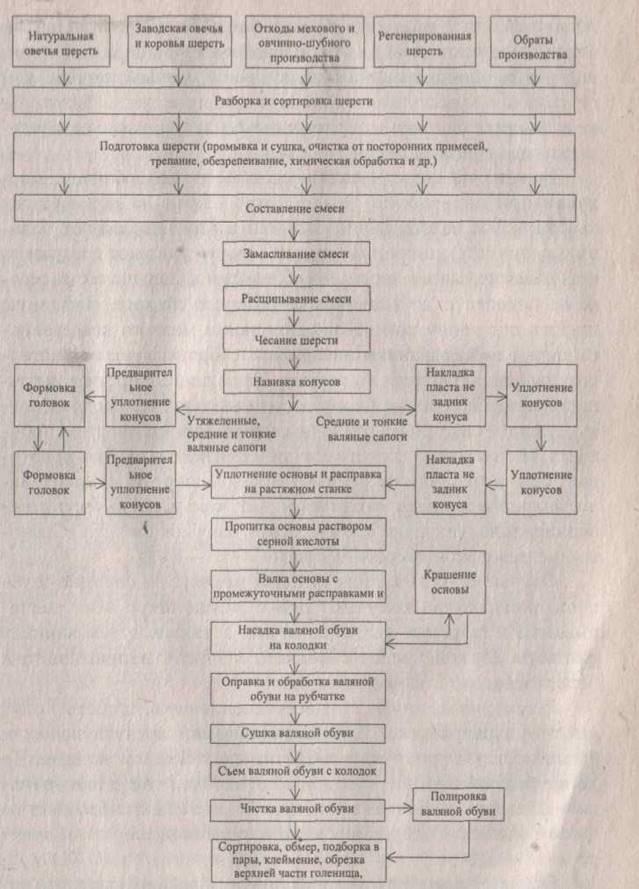
Рис. 1.
Технологическая схема производства валяной обуви
Подготовка сырья
Поступающая на валяльно-войлочные предприятия шерсть неоднородна по длине и толщине и имеет различный цвет волокон. Кроме того, в шерсти содержатся засоряющие примеси. Наиболее вредной примесью в натуральной шерсти является репей: при попадании последнего в валяную обувь и последующем выкрашивании из нее на стенках обуви образуются глубокие впадины и сквозные отверстия.
Для правильного использования сырья и обеспечения необходимого качества валяной обуви шерсть, поступающую на валяльно-войлочные предприятия, подвергают специальной подготовке; она заключается в разборке шерсти по цветам, отделении посторонних примесей и загрязнений, разрыхлении шерсти и т. д.
Разбирают и сортируют главным образом натуральную овечью шерсть; заводская шерсть обычно поступает на валяльно-войлочные предприятия в рассортированном виде. Шерсть, засоренную репьем, обрабатывают на репье-очистительных машинах. Удаление пыли из шерстяного лоскута достигается обработкой на пылевыколачивающих машинах. Очищенная от загрязнений и разрыхленная шерсть поступает на составление смеси.
Составление смеси, расщипывание и чесание шерсти
Валяную обувь вырабатывают из смесей, составленных из различных видов шерсти. Применение одного какого-либо вида шерсти для изготовления валяной обуви нецелесообразно по техническим и экономическим соображениям. Лишь правильный подбор компонентов смеси обусловливает хороший внешний вид валяной обуви, ее плотность, прочность, малую теплопроводность и другие необходимые свойства. При составлении смеси учитываются: вид обуви и требования, предъявляемые к ее качеству, особенности каждого вида шерсти (длина волокна, упругость, крепость, способность к свойлачиванию и т. д.). Состав смеси для изготовления валяной обуви устанавливается действующими техническими условиями на эту обувь.
Процесс составления смеси шерсти состоит в образовании более или менее однородной по волокнистому составу массы путем последовательного наслоения (настилки) одного вида шерсти на другой и дальнейшего перемешивания всех слоев. При настилке слоев чередуют шерсть с различной длиной волокна, крепостью и валкоспособностью: на слой длинноволокнистой шерсти настилают слой коротковолокнистой, а на слой валкоспособной шерсти — слой менее валкоспособной. После настила вручную 30—40 слоев шерсть отбирают в вертикальном направлении сверху вниз, перемешивают и перекидывают на новое место, пока волокнистая масса не станет однородной. На крупных валяльно-войлочных предприятиях настилка слоев шерсти, отбор смеси по вертикали и перемешивание шерсти осуществляются при помощи соответствующих механизированных установок.
Полученную смесь перед поступлением в дальнейшую обработку замасливают. Шерсть замасливают для предохранения волокна от разрыва, уменьшения потерь волокна и его повреждения при последующем расщипывании и расчесывании, а так же для того, чтобы облегчить выполнение этих операций. Для замасливания смеси используют эмульсии, содержащие минеральное масло, мыло, соду и воду, в последнее время стали применять эмульсии, в которые входят эмульгирующая паста, триэтаноламин, минеральное масло и др.
Приготовленная смесь шерсти поступает на щипальные машины, в которых одновременно с разделением шерсти на более мелкие клочки происходит дальнейшее- перемешивание шерсти и удаление посторонних примесей. Разрыхление смеси на щипальных маслинах способствует меньшему повреждению шерстяных волокон при последующем чесании.
При чесании шерсть разделяется на отдельные волокна и окончательно перемешивается. Производится эта операция на чесальных машинах различной конструкции. В процессе прохождения через чесальную машину шерсть многократно обрабатывается движущимися игольчатыми поверхностями. С чесальной машины шерсть сходит в виде рыхлой ваты, однородной по характеру волокна, толщине и плотности; волокна шерсти удерживаются в вате благодаря их извитости и способности взаимно сцепляться. При расчесывании шерсти одновременно происходит ее тщательная очистка, так как растительные примеси разрушаются игольчатыми поверхностями и отделяются от шерсти. Шерсть, сходящая со съемного барабана чесальной машины, навивается на конусообразные или фигурные валики (патроны), а также на ватный барабан. Снимаемая с ватного барабана чесальной машины вата служит для изготовления пластов и для заростки основы валяной обуви.
При навивке на конусообразные патроны образующаяся ватная заготовка (конус) по форме напоминает голенище сапога. Узкий конец конуса служит для формования головки сапога, поэтому конус навивается большей длины, чем это необходимо для образования голенища.
Фигурный патрон состоит как бы из двух совмещенных усеченными поверхностями конусов: удлиненного, служащего для формования голенища сапога, и короткого, служащего для образования головки сапога. В коротком конусе конец, предназначенный для формования головки сапога, имеет расширенную форму.
Размеры конусообразных и фигурных патронов подбираются в соответствии с размерами изготовляемых сапог. Толщина навиваемого на патроны слоя шерсти устанавливается исходя из необходимой толщины и веса изготовляемой обуви. На патроны перед навивкой конусов надевают полотняные чехлы: навитые конусы снимают с патронов вместе с чехлами и далее передают на изготовление основы валяной обуви.
Изготовление основы валяной обуви
Изготовление основы является одним из наиболее ответственных процессов в производства валяной обуви. От правильного изготовления основы в решающей степени зависят качество валяной обуви и расход шерсти.
Для получения валяной обуви определенных размеров при изготовлении основы учитывают ее усадку при последующих свойлачивании и валке. Обычно размеры основы превышают размеры валяной обуви в 2,5 раза по длине и ширине верха голенищ и в 2 раза по длине головок и ширине низа голенища. Изготовление основы состоит из большого числа ручных и механизированных операций, посредством которых рыхлая волокнистая масса навитых ватных заготовок превращается в полуфабрикат сапогообразной формы установленных размеров, веса, толщины и плотности. Состав и последовательность операций изготовления основы для разных видов валяной обуви не вполне совпадают.
Процесс изготовления основы для валяных сапог по наиболее распространенной технологии складывается из предварительного уплотнения ватных заготовок (конусов), формования головок, окончательного уплотнения ватных заготовок (конусов) и их расправки, подготовки пластов, заростки основы, уплотнения основы и ее расправки.
Предварительное уплотнение конусов производится для предупреждения нарушения правильности расположения шерсти при транспортировании и дальнейшей обработке полуфабриката. Уплотняют конусы на притирочных машинах. Рабочим органом последних является легкая деревянная плита и стол с ровной поверхностью. Конус вместе с находящимся в нем полотняным чехлом кладется на стол под плиту, после чего плита опускается и приводится в возвратно-поступательное движение.
Окончательное уплотнение конусов производится в несколько приемов на свойлачивающих плиточных или катальных трехвалковых машинах при повышенной температуре и увлажнении шерсти. На плиточных машинах конусы (с чехлами внутри) уплотняются под влиянием механических воздействий плиты, приводимой в возвратно-поступательное движение. В результате вертикального давления и горизонтального сдвига происходит сближение и перепутывание волокон шерсти; уменьшается толщина конусов и рыхлая вато-образная масса шерсти приобретает вид войлока. В катальных машинах полотняный сверток с конусами, вращаясь между валами, подвергается попеременно сжатиям и сдвигам. В процессе уплотнения сверток несколько раз извлекают из катальной машины, развертывают, расправляют конусы и укладывают на полотно свертка другой стороной. Окончательное уплотнение конусов чередуется с формованием головок основы, т. е. конусы уплотняют сначала до формования головок, а затем после него.
Сущность формования головок основы для валяной обуви заключается в вытягивании нижнего узкого конца конуса и придании ему формы замкнутого чулка. Для удобства формования головки основы на диаметрально противоположных стенках нижнего конуса делают надрывы.
Надорванные концы конуса вручную вытягивают по длине и ширине, а затем им придают необходимую форму, огибают края и сращивают их, получая при этом свойлоченный замкнутый чулок. Для лучшего сращивания надорванных концов конуса и более удобного загибания соединяемые края (кромки) утоняют; между кромками прокладывают тонкий слой чесаной шерстяной ваты повышенной валкоспособности для связывания загнутых одна на другую кромок концов конуса. Конусы с отформованными головками, освобожденные от полотняных чехлов и окончательно уплотненные, подвергают расправке на соответствующих расправочных станках для придания им более правильной формы и размеров, а затем направляют на заростку основы.
Заросткой основы называется операция наращивания толщины стенок основы в местах наибольшего износа валяных сапог. Для утолщения основы в головке (подошве) и в нижней части голенища шерсть, накладываемую дополнительно на эти места основы, подготавливают в виде пластов, настилаемых из отдельных слоев ватки. Пласты настилают определенной конфигурации, необходимой для облегания головки, подошвы и нижней части голенища.
Подготовленные пласты перед их применением для наращивания отдельных участков основы уплотняют на свойлачивающих плиточных или катальных машинах. При излишнем уплотнении пластов они плохо сращиваются с основой, что приводит к скрытому дефекту — внутреннему расслоению стенок валяной обуви.
В процессе заростки основы ее головку, подошву и нижнюю часть голенища обкладывают вручную в определенном порядке уплотненным пластом. Иногда, в частности при изготовлении средней и тонкой валяной обуви, операцию заростки основы объединяют с формованием головки основы. Заро-щенную основу уплотняют при увлажнении и нагревании на катальных или плиточных машинах, а также на маятниковых свойлачивающих машинах.
После уплотнения основу расправляют на специальном станке; в процессе расправки основе придают требуемые размеры и форму.
Валка основы, крашение, сушка и отделка валяной обуви
Основа валяной обуви обладает недостаточной плотностью и прочностью; дальнейшее уплотнение основы достигается валкой в молотовых валяльных машинах. В процессе валки под влиянием ударов и сжатий происходят перемещение волокон и односторонние их сдвиги в направлении корневых концов; при этом волокна шерсти сокращаются в длине, изменяют свою форму, переплетаются в сплошную плотную массу. Под влиянием валки наблюдается резкая усадка основы в продольном и поперечном направлениях.
Для увеличения валкоспособности шерсти и облегчения выполнения процесса валки основу предварительно, а иногда и в процессе валки пропитывают слабым раствором серной кислоты (2,5—4,5%) при +30—35°С. Избыток кислоты удаляют, отжимая основу или давая кислоте стечь.
Валку основы валяной обуви обычно выполняют в четыре периода с промежуточными расправками и растяжками основы в поперечном и продольном направлениях. При валке основа смачивается горячей водой (от 40 до 60—65°С), что способствует лучшей ее увалке. Промежуточные расправки и растяжки основы проводятся для сохранения правильной ее формы, а также для предупреждения сращивания внутренних поверхностей стенок валяной обуви, образования рубцов и других дефектов.
При изготовлении крашеной валяной обуви полуфабрикат в зависимости от состояния шерсти, от того, какой цвет необходимо получить, и других условий окрашивают в той или другой стадии валки основы.
После валки, расправки и крашения полученные валяные сапоги обрабатывают горячей водой или паром, растягивают голенища на рычажном станке и насаживают обувь на колодки механическим или ручным способом. Насадка на колодки необходима для придания валяной обуви устойчивой формы и нужных размеров. При насаживании сапог на колодки происходит некоторое растяжение обуви; величина растяжения должна находиться в определенных пределах, так как при излишнем растяжении возможна значительная усадка валяной обуви при ее намокании и последующем высушивании в процессе носки.
Конструкция колодок видоизменяется в зависимости от применяемого способа насадки валяной обуви. Колодки для ручной насадки, применяемые на мелких валяльно-войлочных предприятиях, состоят из головки, переднего, заднего и среднего клиньев и дополнительной расклинки.
Колодки для механической насадки, используемые на более крупных предприятиях, значительно сложнее по конструкции. Насаживают валяную обувь на эти колодки при помощи машин. Сапог надевается на сложенную (выпрямленную) колодку; рабочие органы насадочной машины осуществляют поворот головки колодки и одновременно расширение нижней части обуви и голенища.
Колодки для насадки валяной обуви изготовляют симметричными относительно плоскости, проходящей через осевую линию следа, т. е. без различия левой и правой полупары.
Размеры и форма колодок для механической насадки нормируются техническими условиями на эти колодки; головки колодок для ручной насадки должны по форме и размерам совпадать с головками соответствующих колодок для механической насадки.
Насаженную на колодки валяную обувь подвергают оправке ударами колотушки для исправления неправильностей формы обуви, разогревают в горячей воде и обрабатывают на рубчатке, т. е. вращающемся валике с зубчатой поверхностью. Тупые зубья валика, воздействуя на стенки валяной обуви, несколько выравнивают их по толщине и дополнительно уплотняют, что способствует уменьшению усадки обуви при носке.
После обработки на рубчатке валяную обувь для удаления избыточной влаги высушивают при +80—110°С в течение 7—8 часов и более.
Снятая с колодок высушенная валяная обувь поступает в чистку, в процессе которой с поверхности обуви снимают грубые торчащие концы волокон шерсти (ворс). При чистке валяной обуви поверхность голенищ головок, задников и подошв обрабатывают на чистильных (шлифовальных) станках вращающимися абразивными валиками. Поверхность валяной обуви дополнительно чистят изнутри для удаления рубцов и полируют снаружи вращающимися валиками, обтянутыми войлоком для улучшения внешнего вида.
Готовую валяную обувь сортируют, устанавливают ее размер (номер), подбирают в пары по наружным размером и внешнему виду, обрезают по верхнему краю голенища и сшивают попарно.
Определение сортности валяной обуви
Валяная обувь подразделяется на два сорта: 1-й и 2-й. Сорт определяют не по одному, наиболее резко выраженному, дефекту, а по их совокупности в худшей полупаре. Независимо от сорта, валяная обувь должна соответствовать требованиям технических условий по физико-химическим свойствам, линейным размерам, толщине, весу и разнице в линейных размерах и толщине в паре.
Основными дефектами, встречающимися в валяной обуви, являются: разнооттеночнюсть от раздельной чистки головок и голенищ сапог; неровность окраски и пятнистость, наличие мелких частиц репья, неразработанных ниток и растительных примесей с различной глубиной вкрапления, недостаточная прочность окраски при испытании на сухое трение с внутренней стороны голенища, выражающаяся в закрашивании белой бязи, отклонение формы пятки задника и носка от фасона насадочной колодки, зачищенная неровность внутри сапог, получающаяся от зажимов, несростки и рубцов; местные впадины, выхваты (прочистка) и утонения; зажимы внутри сапог; рубцы на поверхности сапог, расслоение войлока внутри сапог и др. В зависимости от степени выраженности и влияния на эксплуатационные свойства валяных сапог перечисленные дефекты допускаются в обуви 1-го или 2-го сорта или же не допускаются в обуви обоих сортов.
К 1-му сорту относятся валяные сапоги при наличии в них не более двух следующих дефектов, не ухудшающих эксплуатационные свойства и внешний вид сапог: мелких частиц репья с глубиной вкрапления не более 1 мм, местных впадин внутри сапога с разницей в толщине по сравнению с соседними местами не более 1,5 мм.
Ко 2-му сорту относятся сапоги при наличии не более четырех из перечисленных ниже дефектов: пятнистости из за разного цвета сырья или неудовлетворительной окраски, а также до двух масляных пятен в сапоге общей площадью до 6 см2
, мелких частиц репья, неразработанных ниток и растительных примесей с глубиной вкрапления не более 1,5 мм, рубцов и заломов на поверхности сапог с разницей в толщине по сравнению с соседними местами не более 2 мм, следов в местах сростки кромок внутри сапога. Валяная обувь, не удовлетворяющая требованиям 2-го сорта, не подлежит реализации.
|