МИНИСТЕРСТВО СЕЛЬСКОГО ХОЗЯЙСТВА РФ
ДЕПАРТАМЕНТ НАУЧНО-ТЕХНОЛОГИЧЕСКОЙ ПОЛИТИКИ И ОБРАЗОВАНИЯ
ФГОУ ВПО КОСТРОМСКАЯ ГСХА
Кафедра неорганической и биологической химии
Курсовая работа
по химии
На тему: «Гальванотехника»
Выполнила:
студентка 6 группы 2 курса
экономического факультета
Голикова Мария Николаевна
Руководитель:
Кебец Н. М.,
Доктор биологических наук, профессор
Кострома – 2010
Содержание
Введение. 3
ОБЩИЕ СВЕДЕНИЯ ПО ГАЛЬВАНОТЕХНИКЕ. 3
Понятие об электролите и процессе электролиза. 3
Основные сведения о коррозии металлов. 3
Анодные и катодные покрытия. 3
ПОДГОТОВКА ПОВЕРХНОСТИ МЕТАЛЛИЧЕСКИХ ИЗДЕЛИЙ ПЕРЕД НАНЕСЕНИЕМ ГАЛЬВАНИЧЕСКИХ ПОКРЫТИЙ.. 3
Механическая обработка. 3
Химическая и электролитическая подготовка. 3
ОБОРУДОВАНИЕ ГАЛЬВАНИЧЕСКИХ ЦЕХОВ.. 3
Электрооборудование. 3
Оборудование для покрытий мелких деталей. 3
Сушильные аппараты.. 3
Полуавтоматические и автоматические установки для покрытий. 3
Приспособления для завешивания деталей в ванны.. 3
НИКЕЛИРОВАНИЕ. 3
Виды никелевых покрытий. 3
Характерные дефекты никелевых покрытии. 3
МЕДНЕНИЕ. 3
Электролиты для меднения. 3
ХРОМИРОВАНИЕ. 3
Особенности процесса хромирования. 3
Электролиты для хромирования. 3
Виды хромовых покрытий. 3
СЕРЕБРЕНИЕ, КАДМИРОВАНИЕ И ЛУЖЕНИЕ. 3
Серебрение. 3
Кадмирование. 3
Лужение. 3
ЖЕЛЕЗНЕНИЕ И СВИНЦЕВАНИЕ. 3
Железнение. 3
Свинцевание. 3
ОСАЖДЕНИЕ СПЛАВОВ.. 3
Латунирование. 3
Покрытие белой бронзой. 3
Покрытие сплавами олово — свинец. 3
Заключение. 3
Список использованной литературы.. 3
Гальванотехника, область прикладной электрохимии, охватывающая процессы электролитического осаждения металлов на поверхность металлических и неметаллических изделий. Гальванотехника включает: гальваностегию — получение на поверхности изделий прочно сцепленных с ней тонких металлических покрытий и гальванопластику — получение легко отделяющихся, относительно толстых, точных копий с различных предметов. Открытие и техническая разработка гальванотехники принадлежат русскому учёному Б. С. Якоби, о чём он доложил 5 октября 1838 на заседании Петербургской АН. [10]
Гальванотехника основана на явлении электрокристаллизации — осаждении на катоде (покрываемом изделии в гальваностегии или матрице в гальванопластике) положительно заряженных ионов металлов из водных растворов их соединений при пропускании через раствор постоянного электрического тока. Количественно гальванотехнические процессы регулируются по законам Фарадея с учётом побочных процессов, которые сводятся чаще всего к выделению на поверхности покрываемых изделий наряду с металлом водорода; качественно — типом и составом электролита, режимом электролиза, т. е. плотностью тока, а также температурой и интенсивностью перемешивания. Различают электролиты на основе простых или комплексных соединений. Первые значительно проще, дешевле и при интенсивном перемешивании (чаще воздушном) допускают применение высоких плотностей тока, что ускоряет процесс электролиза.
Гальванические цехи машиностроительных и приборостроительных заводов обычно являются теми завершающими участками производства, где выпускаемым изделиям и деталям придаются особые свойства, повышающие их эксплуатационные качества: коррозионную стойкость, износостойкость, твердость, жаростойкость, декоративный внешний вид и др.
Внедрение в области гальваностегии новой техники, интенсификация процессов электролиза, механизация и автоматизация процессов осаждения металлов являются главной задачей в работе гальванических цехов Для успешного решения этой задачи необходимо, чтобы рабочие — непосредственные исполнители работ — были знакомы с теоретическими основами и прогрессивной технологией электролитических покрытий, знание которых поможет им сознательно и активно участвовать на своих производственных участках в общей борьбе за технический прогресс. [2]
Электролитическая диссоциация.
Молекулы солей, кислот и щелочей при растворении в воде распадаются (диссоциируют) на атомы или группы атомов, несущих положительные и отрицательные заряды электричества. При этом количество положительных зарядов всегда равняется количеству отрицательных зарядов, т. е. раствор остается электрически нейтрален. Этот процесс называется электролитической диссоциацией, а химические соединения, которые при растворении в воде подвергаются электролитической диссоциации— электролитами. Атомы или группы атомов, заряженные определенным электрическим зарядом, называются ионами, причем атомы, обладающие положительным зарядом, называются катионами, а отрицательным зарядом — анионами. [6]
При диссоциации молекул солей, кислот и щелочей в водных растворах металлы и водород приобретают положительный заряд, т. е. становятся катионами, а кислотный или щелочный остаток (группа атомов или один атом) приобретают отрицательный заряд, т. е. становятся анионами. Электрический заряд катионов обозначают точкой или знаком плюс, например Ni··, Fe··· или Ni++, Fe+++, электрический заряд анионов соответственно обозначают штрихом или знаком минус, например SO4
··, PO4
···· или SO4
--, РО4
-----.Число штрихов или точек показывает число зарядов, которыми обладает атомный ион, и одновременно соответствует химической валентности данного иона.
Электролитической диссоциации в водных растворах подвергаются не все молекулы электролита (растворенного вещества). Степень диссоциации, т. е. какая часть из всех молекул, находящихся в растворе, диссоциирована, зависит от природы растворенного вещества и от концентрации раствора. Чем разбавленнее раствор, тем выше степень диссоциации растворенных молекул. Электролиты -с высокой степенью диссоциации называются сильными электролитами, а с низкой степенью диссоциации — слабыми электролитами.
Процессы диссоциации сильных и слабых электролитов существенно отличны между собой, в связи с чем законы, приемлемые для первых электролитов, оказываются совершенно непригодными для вторых. В частности, для каждого слабого электролита, растворимого в воде, устанавливается определенное равновесие между ионами, образующимися при диссоциации молекул, и оставшимися недиссоциированными молекулами. В связи с этим в данном случае, как и при обычной химической реакции, применим известный в химии закон действующих масс, согласно которому отношение произведений концентрации веществ, полученных после реакции, к произведению концентраций веществ, вступивших в реакцию, есть величина постоянная для данной реакции при постоянной температуре.
Из физики известно, что разноименные заряды взаимно притягиваются, а одноименные взаимно отталкиваются, причем силы взаимодействия тем больше, чем меньше расстояние между ними. Поэтому естественно, что находящиеся в растворе катионы и анионы, обладающие разноименными зарядами, находятся в определенном электростатическом взаимодействии, при этом вокруг каждого иона в первую очередь располагаются ионы с противоположным зарядом, а ионы с одноименным зарядом располагаются несколько дальше. [7]
Процесс электролиза.
Существует два рода проводников электрического тока. В процессе проникновения электрического тока через проводники первого рода в веществе самого проводника не происходит никаких химических изменений. К таким проводникам относятся металлы, уголь и некоторые другие вещества. К проводникам второго рода относятся кислоты, щелочи, соли и другие химические соединения как в виде водных растворов, так и в расплавленном состоянии. Проводники второго рода, или электролиты, в процессе прохождения через них постоянного электрического тока в местах его ввода и вывода претерпевают существенные изменения.
Процесс, связанный с прохождением постоянного электрического тока от внешнего источника тока через какой-либо электролит, называется электролизом.
Подвод тока в электролит производится посредством двух металлических (угольных) пластин, погружаемых в электролит и соединенных с источником тока. Эти пластины называются электродами, причем пластина, соединяемая с положительным полюсом источника тока, называется положительным электродом, или анодом, а пластина, соединяемая с отрицательным полюсом источника тока, — отрицательным электродом, или катодом. В гальванотехнике катодами являются изделия, которые подвергаются покрытию, а анодами служат пластины или прутки из того металла, которым изделие покрывается.
В гальванотехнике в качестве электролита обычно применяют раствор соли, содержащий ионы металла, подлежащего осаждению. Катодом служит покрываемое изделие, а анодом — пластины из осаждаемого металла. Помимо осаждения металла на катоде, часто происходит выделение газообразного водорода. Вода (хотя и в небольшой степени) также диссоциируется на ионы водорода и гидроксильные ионы:
Н2
0 = Н' +ОН'.
Выделение водорода на катоде рассматривается как побочный процесс, который в подавляющем большинстве случаев ухудшает качество покрытия, придавая ему хрупкость, и всегда увеличивает продолжительность электролиза
Количественно процесс электролиза подчиняется законам Фарадея:
1. Количество выделившегося при электролизе вещества прямо пропорционально силе тока и времени прохождения тока. Следовательно, количество получающегося при электролизе вещества зависит от количества ампер-часов (а·ч), прошедших через электролит. Таким образом, если при прохождении тока силой в 10 а в течение 3 ч высадилось 10 г какого-либо вещества, то такое же количество высадится при прохождении тока силой в 15 а в течение 2 ч или силой в 30 а в течение 1 ч и т. п.
2. При прохождении одного и того же количества постоянного тока через разные электролиты количество выделившегося при этом вещества пропорционально их эквивалентным весам.
В табл. 1 приведены значения электрохимических эквивалентов некоторых металлов. [11]
Таблица 1
Электрохимические эквиваленты металлов
Наименование металла |
Характеристика электролита |
Валентность |
Атомный вес |
Эквивалентный вес |
Электрохимический эквивалент |
Медь |
Кислый |
2 |
63,37 |
31,78 |
1,186 |
Медь |
Цианистый |
1 |
63,37 |
63,37 |
2,372 |
Никель |
Кислый |
2 |
58,69 |
29,35 |
1,095 |
Хром |
Кислый |
6 |
52,01 |
8,67 |
0,323 |
Цинк |
Кислый |
2 |
65,38 |
32,69 |
1,220 |
Цинк |
Цианистый |
2 |
65,38 |
32,69 |
1,220 |
Кадмий |
Кислый |
2 |
112,41 |
56,20 |
2,097 |
Кадмий |
Цианистый |
2 |
112,41 |
56,20 |
2,097 |
Олово |
Кислый |
2 |
118,70 |
59,35 |
2,214 |
Олово |
Щелочной |
4 |
118,70 |
29,65 |
1,107 |
Серебро |
Цианистый |
1 |
107,88 |
107,88 |
4,025 |
Золото |
Цианистый |
1 |
197,20 |
197,20 |
7,357 |
Разрушение металлов под влиянием химического или электрохимического взаимодействия с внешней средой называется коррозией.
Большинство металлов, несмотря на значительную механическую прочность, сравнительно легко разрушается под влиянием внешней среды — воздуха, воды, растворов кислот, щелочей, солей и т. д. Процессы коррозии очень разнообразны и широко распространены.
По внешнему виду коррозионное разрушение металла бывает весьма разнообразным. Среди типов коррозионных разрушений различают: сплошную, местную (структурно-избирательную), пятнистую, язвенную, точечную, межкристаллитную, внутрикристаллитную и поверхностную.
По физико-химическому характеру коррозионные процессы можно разделить на химические и электрохимические.
При химической коррозии процесс разрушения металла не сопровождается возникновением электрического тока. Примером химической коррозии является разрушение металлов в сухих газах при высоких температурах или в жидкостях, не проводящих электрический ток.
При электрохимической коррозии разрушение металлов сопровождается появлением электрического тока, возникающего в результате перехода электронов из одних участков металла к другим.
К электрохимической коррозии относится разрушение металлов в средах, проводящих электрический ток, т. е. главным образом в водных растворах кислот, щелочей и солей (электролитах). К этому виду коррозии относится также атмосферная коррозия, при которой имеет место взаимодействие металла, практически всегда неоднородного по своей структуре, с агрессивными агентами окружающей среды. Такой средой является главным образом влага с растворенными в ней кислородом и другими газами (т. е. при образовании электролита). Коррозия возникает также в результате неравномерной аэрации, т. е. при неодинаковом доступе кислорода воздуха к отдельным участкам поверхности металла.
При одновременном воздействии на металлы переменных нагрузок и коррозионной среды интенсивность коррозии возрастает, что приводит к коррозионной усталости. Остаточные и упругие деформации и напряжения, возникающие в металлах при плавке, прокатке, штамповке, волочении при термических воздействиях, а также при холодной деформации (изгибе, клепке и т. п.) являются факторами, ускоряющими коррозию.
Под скоростью коррозии понимают скорость коррозионного процесса, определяемую как отношение коррозионных потерь с единицы поверхности к соответствующему промежутку времени. Например, потеря веса металла в г/м2
• ч.
Способность металла сопротивляться воздействию коррозионной среды (определяемая качественно и количественно) характеризует его коррозионную стойкость.
В возникновении и скорости протекания электрохимической коррозии исключительно важную роль играют потенциалы соприкасающихся между собой металлов. Согласно электрохимической теории коррозии, при погружении металла в электролит, содержащий ионы этого металла (например, при погружении цинка в раствор сернокислого цинка), на поверхности металла протекают процессы взаимодействия его атомов с ионами (заряженными электричеством частицами), находящимися в растворе, и возникает разность потенциалов между металлом и электролитом, измеряемая в вольтах, которая называется равновесным, нормальным электродным потенциалом данного металла. [2]
Как было указано выше, при защите железа от коррозии покрытием из других металлов следует руководствоваться положением этих металлов в ряду напряжений, относительно железа, т. е. нужно учитывать, будет ли металл покрытия более электроотрицателен или более электроположителен, чем железо.
В зависимости от характера защиты покрытия разделяются на анодные и катодные. Анодными покрытиями будут такие, у которых электродный потенциал в данных условиях более отрицателен, чем потенциал защищаемого металла. К катодным покрытиям относятся те металлы, у которых потенциал выше потенциала защищаемого металла.
При покрытии какого-либо металла более электроотрицательным металлом в случае возникновения коррозии покрывающий металл будет играть роль анода, переходить в раствор и разрушаться, а основной металл станет катодом и тем самым будет предохраняться от коррозии.
Схема коррозии анодного покрытия показана на фиг .6.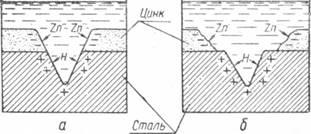
Фиг. 6. Схема коррозии анодного покрытия: а — начало коррозии; б — результат коррозии.
К другого рода покрытиям относятся покрытия, где основной металл покрыт более электроположительным металлом. Например, в случае нанесения хромового покрытия на сталь в образовавшейся гальванической паре хром будет катодом, а сталь, которая является по отношению к хрому анодом, будет разрушаться, что приведет к отслаиванию хрома
При покрытии электроположительным металлом можно получить только механическую защиту, т. е. покрытие будет хорошо предохранять железо только до тех пор, пока оно будет сплошным и не нарушится его слой.
По отношению к стали катодными покрытиями будут, например, являться покрытия из никеля, хрома, олова, свинца, меди, серебра и др.
Схема коррозии катодного покрытия показана на фиг. 7.
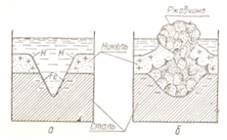
Фиг. 7. Схема коррозии катодного покрытия: а — начало коррозии; б — результат коррозии.
На практике более широко применяют катодные защитные покрытия, используя для этой цели высокую химическую стойкость и хорошие механические свойства некоторых металлов. Основным требованием при этом будет создание сплошных беспористых покрытий, хорошо изолирующих сталь (или другой защищаемый металл) от коррозионной среды.
Коррозионные процессы возникают также (особенно часто в промышленных условиях) при погружении металлов в раствор электролита, содержащего ионы других металлов. При этом возникает электродный потенциал (но не равновесный), величина которого зависит от разнообразных причин: состояния поверхности металла, температуры и т. д. Поверхность технических металлов, будучи неоднородной физически и химически, приводит к образованию на отдельных участках разных электродных потенциалов. Места, где происходит растворение металла, будут анодными участками, места, где будут разряжаться положительно заряженные ионы, — катодными участками. Таким образом, будут возникать гальванические микроэлементы, дающие электрический ток и вызывающие разрушение металла, в случае, если он станет анодом.
Коррозия металлов и сплавов рассматривается, согласно электрохимической теории, как процесс разрушения, вызванный действием огромного количества микроэлементов — гальванических пар. [7]
Качество металлических покрытий.
Качество металлического покрытия, получаемого гальваническим путем, характеризуется структурой осадка, толщиной и равномерностью его распределения на поверхности изделия и другими факторами.
Гальваническое покрытие металлами рассматривается как явление кристаллизации, в результате которого под действием тока на поверхности металла зарождаются отдельные кристаллы. Продолжая расти, эти кристаллы образуют на поверхности детали или изделия сплошное покрытие. Под структурой этого покрытия понимается размер и форма кристаллов, а также расположение их по отношению к поверхности покрываемого металла. Размер и форма кристаллов зависят в основном от скорости образования отдельных кристаллов и их роста.
На структуру металлических покрытий, полученных гальваническим методом, большое влияние оказывает такой фактор, как режим электролиза. Повышение плотности тока приводит к уменьше нию величины кристаллов в осадке. Однако в некоторых случаях такая закономерность замечается только с достижением определенной плотности тока. Повышать плотность тока можно только до определенного предела, после которого в обычных условиях наступает нарушение процесса. Вследствие большого обеднения прикатодного слоя ионами металла наблюдается отложение металла на некоторых выступающих участках катода, где образуются так называемые дендриты. При еще более высокой плотности тока катод покрывается губчатой порошкообразной массой, состоящей из мелких отдельных кристаллов или их сростков, непрочно связанных между собой и основой.
Для защитно-декоративной отделки изделий наиболее пригодными являются мелкокристаллические покрытия, как обладающие наименьшей пористостью и тем самым лучше защищающие изделия от коррозии. В последнее десятилетие в гальванотехнике нашел применение метод отложения металлических осадков токами переменной полярности. Периодическое изменение направления тока при повышенных его плотностях позволяет получать мелкокристаллические гладкие осадки. Объясняется это следующим: во-первых, при этом ликвидируется обеднение прикатодного слоя за счет растворения покрытия, во время переключения катода на анод и соответственно снижается концентрационная поляризация. Во-вторых, те микровыступы (вершины кристаллов), которые образуются на катоде вследствие большой скорости роста на них кристаллов при переключении на анод растворяются в первую очередь, что обеспечивает образование более равномерных, гладких, в некоторых случаях блестящих осадков. [8]
Назначение и толщина металлических покрытий.
В соответствии с их назначением гальванические покрытия можно разделить на следующие основные группы:
1) коррозиеустойчивые, или защитные;
2) защитно-декоративные;
3) износостойкие;
4) специальные.
Защитные свойства коррозиеустойчивого металлического покрытия определяются:
а) величиной электродного потенциала металла покрытия, сравнительно с электродным потенциалом защищаемого металла, т. е. будет ли металл покрытия при образовании гальванической пары катодом или анодом. Исключение представляют металлы, склонные покрываться пассивной пленкой (алюминий, хром). Разность между потенциалом металла покрытия и потенциалом защищаемого металла и контактирующимися с ним незащищаемыми металлами должна быть возможно наименьшей;
б) химической стойкостью металла покрытия против воздействия той срелы, в которой находится изделие. В связи с этим защитные свойства покрытия зависят от того, как по своей химической природе металл покрытия будет относиться к таким химическим реагентам, как влажный воздух, морская вода, кислоты, щелочи и др.;
в) достаточной толщиной, сплошностью и сцепляемостью покрытия, а также его твердостью и сопротивляемостью механическим воздействиям. Исключительно большое значение для противокоррозионной защиты имеет качество сцепления покрытия с основным металлом, выражающееся в сращивании покрытия с основой по всей поверхности изделия. Сцепление покрытия с покрываемым металлом зависит от ряда условий, куда относятся химические свойства основного металла и металла покрытия, режим и условия процесса осаждения и главное — качество подготовки поверхности изделия в механических и гальванических цехах.
Основным требованием к коррозиеустойчивым и защитно-декоративным покрытиям является наличие достаточной для данных условий эксплуатации изделия толщины слоя покрытия.
Выбор покрытий и их толщина зависят от назначения изделий и условий их эксплуатации. Минимальные значения толщин покрытий после их отделки предусматриваются Государственными стандартами.
В зависимости от условий работы изделия устанавливаются три группы покрытий:
· группа Л — для легких условий работы. Эта группа предназначена для эксплуатации изделий в закрытых, сухих, отапливаемых и вентилируемых помещениях (аналогичных жилым);
· группа С — для средних условий работы. Эта группа предназначена для эксплуатации изделий в условиях закрытых помещений и наружной атмосферы, загрязненных промышленными газами, пылью, а также содержащих аэрозоли или испарения морской воды. При этом изделия не должны подвергаться непосредственному воздействию дождя или снега;
· группа Ж — для жестких условий работы. Эта группа предназначена для эксплуатации изделий в условиях закрытых помещений и наружной атмосферы, загрязненных значительным количеством промышленных газов и пыли, а также при непосредственном периодическом воздействии дождя, снега или брызг морской воды.
Толщина покрытия в ряде случаев (например, с целью защиты от коррозии в жидких средах или агрессивных газах, при повышении износостойкости поверхности металла и др.) не может быть стандартизована. В каждом отдельном случае здесь необходимо учитывать интенсивность воздействия коррозионной среды, конструктивные особенности изделия, срок службы и требования к покрытию, обусловленные технологией изготовления деталей. [4]
Поверхность металлических изделий и деталей перед нанесением гальванических покрытий должна быть тщательно подготовлена и очищена от различного рода загрязнений. Окислы металла (окалина и ржавчина), минеральные масла, технические жиры, а также ранее нанесенные покрытия, шлаковые включения, другими словами, все загрязнения, препятствующие осаждению и прочному сцеплению покрытия с металлом, должны быть удалены с поверхности изделий.
Устранение неровностей, шероховатостей, пленки окалины, шлаковых включений и придание поверхности гладкого и блестящего вида достигают механической обработкой — шлифованием и полированием. Однако поверхность металлических изделий и деталей, приобретая в результате механической обработки декоративный вид, остается еще недостаточно чистой, чтобы можно было ее подвергнуть гальваническим покрытиям. Даже незначительные загрязнения, как, например, следы от пальцев на поверхности изделий, сильно ухудшают качество гальванических покрытий и ведут к различного рода дефектам. Поэтому, кроме механической обработки, необходимо применять еще очистку поверхности от окислов и жировых загрязнений химическим путем, дающую требуемую степень чистоты для гальванического покрытия. Это достигается травлением поверхности в кислотах и обезжириванием ее в растворителях и щелочных растворах с последующей промывкой водой. [1]
Механическая обработка поверхности металлических изделий перед нанесением гальванических покрытий имеет своей целью создать гладкую, ровную, блестящую или матовую поверхность и придать металлическим изделиям красивый внешний вид. Механическая обработка поверхности металла с целью ее отделки состоит из шлифования (декоративное шлифование), полирования, применяемого для получения блестящей поверхности, а также крацевания, матирования и гидропескоструйной обработки, применяемых для получения матовой поверхности. От степени механической обработки во многом зависят качество и внешний вид гальванического покрытия, которое как бы копирует поверхность и все ее изъяны. Отложение тонких слоев металла на необработанной негладкой поверхности будет также негладким. Качество поверхности оказывает большое влияние на ряд важнейших свойств металла, износостойкость, а также коррозионную стойкость. Чем глаже поверхность металла, тем выше его коррозионная стойкость.
При изготовлении деталей в механических цехах должен быть выбран такой способ обработки, который позволил бы получить чистоту поверхности детали, соответствующую данному покрытию; при этом имеет существенное значение, какое покрытие наносится — блестящее или матовое.
По степени блеска гальванические покрытия подразделяются на матовые, полуматовые, блестящие, глянцевые и зеркальные. Для деталей, на которые наносятся блестящие гальванические покрытия, чистота поверхности перед полированием должна быть в пределах от 7 до 9-го класса. Детали, на поверхности которых после покрытий допускаются незначительные риски и к которым не предъявляются требования большой точности и отсутствия конусности, овальности и завалов краев, могут обрабатываться по 7-му классу чистоты поверхности. Для деталей, на которые наносят полуглянцевые и матовые покрытия, рекомендуется чистота поверхности от 5 до 7-го класса. Обрабатывать детали до чистоты ниже 5-го класса не следует, так как гальванические покрытия получаются низкого качества.
После обработки гальванических покрытий чистота поверхности деталей повышается на три-четыре класса, достигая 10—14-го класса, за счет полирования перед покрытием и глянцевания после покрытия.
Шлифование.
Этот процесс применяется для получения ровной и гладкой поверхности выполняется снятием с изделий тонкой стружки металла с помощью режущих материалов — абразивных материалов.
Операция декоративного шлифования производится на механических станках с вращающимися эластичными войлочными или фетровыми кругами, на которые нанесены и закреплены клеем абразивные материалы. Наибольшее применение для этих целей имеют двухшпиндельные шлифовально-полировальные станки.
Предварительное шлифование трубчатых, цилиндрических деталей часто производится на бесцентровошлифовальных станках.
Для обработки плоских поверхностей существуют различные типы плоскошлифовальных станков с магнитной плитой. При массовом выпуске однотипных деталей применяют полуавтоматы.
С целью механизации процессов шлифования и полирования применяют разные типы специальных автоматических станков.
Чтобы получить гладкую и ровную поверхность обрабатываемого изделия, процесс шлифования следует в несколько операций, начиная обработку более грубым и заканчивая очень тонким абразивом. Число операций зависит от состояния поверхности, твердости и свойств шлифуемого материала, от крупности абразивных зерен, от скорости вращения шлифовального круга от требуемой степени окончательной отделки.
Для отделочного шлифования обычно применяют войлочные (валяные) круги, обладающие некоторой эластичностью, что имеет значение при обработке профилированных деталей. Для шлифования плоских поверхностей находят применение кожаные круги (набранные из кусочков кожи или обтянутых кожей), а также круги, состоящие из проклеенных войлочных или хлопчатобумажных дисков.
Последующими операциями являются грубое, среднее и окончательное, или тонкое, шлифование. Эти операции выполняются эластичными войлочными или фетровыми шлифовальными кругами.
Заключительной операцией шлифования является обработка деталей на кругах с наклеенной абразивной оболочкой, смазанных наждачными жировыми пастами, стеарином или техническим салом. Этот процесс называют салкой или матированием, так как поверхность получается гладкая, но матовая.
Салка является завершающей и наиболее ответственной операцией механической подготовки поверхности перед нанесением гальванических покрытий. Режущие свойства зерен абразива, смазанных жировой пастой или техническим салом, значительно ослабляются, органические кислоты, имеющиеся в сале, способствуют удалению пленки окислов с деталей, а в результате салки поверхность становится значительно ровнее, чем после сухого шлифования.
Важное значение в процессе шлифования имеют твердость шлифовальных кругов и их пористость.
Полирование
. Этот процесс применяют для окончательной отделки поверхности после шлифования и достижения высокой степени блеска. Полирование ведется мягкими кругами из материи (бязь или хлопчатобумажная ткань) с помощью полировальных паст, которые наносятся непосредственно на периферию круга. Для полирования плоских или трубчатых деталей применяются также войлочные или фетровые круги.
В отличие от шлифования, которое является чисто механическим процессом снятия стружки, при полировании имеют место химические, термические и электрические процессы. Весьма существенным является наличие в полировальной пасте слабых органических кислот (олеиновой, стеариновой и др.).
Процесс полирования происходит следующим образом. Вращающийся круг удаляет с поверхности, обрабатываемой детали пленку окисла металла. При этом поверхностно-активные вещества, входящие в состав пасты (стеарин, силикагель и др.), способствуют образованию большого количества новых пленок, также удаляемых кругом.
В результате такого процесса происходит удаление даже незначительных неровностей и достигается зеркальный блеск поверхности. Большое значение при этом имеет разогревание поверхности металла, способствующее ее разглаживанию, поэтому окружная скорость при полировании должна быть выше, чем при шлифовании.
Большое значение при полировании имеет надлежащий выбор полировальных паст и содержание в них жира (стеарина). Количество пасты, наносимой на круг, устанавливается в каждом конкретном случае в зависимости от конфигурации детали. Избыток пасты или ее недостаток одинаково вредны.
На качество полирования сильное влияние оказывает степень предварительного шлифования, к которому необходимо предъявлять определенные требования. При плохом шлифовании полирование не дает нужного эффекта.
Материалы, применяемые при шлифовании и полировании.
Для шлифования применяются материалы естественного или искусственного происхождения, обладающие большой твердостью (абразивы). Наибольшее применение для шлифования и полирования имеют такие абразивы: корунд, карборунд, наждак, кремнезем, трепел, пемза, крокус, известь, окись железа, окись алюминия и окись хрома.
Искусственные абразивные материалы — электрокорунд, карборунд и карбид бора применяются для точного шлифования. Естественные корундовые порошки и наждак применяются главным образом для декоративного шлифования.
Корунд. Этот абразив почти исключительно состоит из чистой кристаллической окиси алюминия. Природный корунд содержит 90—95% окиси алюминия. Для шлифования больше применяют искусственный корунд (известный также под названием алундиалоксит, экстра), получаемый в специальных электрических печах путем обработки бокситов — продуктов, содержащих окись алюминия в смеси с углем или коксом. Лучшие сорта корунда содержат 92—99% окиси алюминия. Корунд является лучшим материалом для грубого шлифования на кругах, так как хрупкость его меньшая, чем других абразивов, а зерна более многогранны.
Карборунд. Этот абразив представляет собой соединение углерода с кремнием (карбид кремния) и получается путем сплавления в электрических печах кварцевого песка с коксом, антрацитом или древесным углем. Зерна карборунда имеют очень острые грани; твердость этого материала выше твердости корунда и приближается к алмазу.
Карборунд применяется главным образом для грубого шлифования хрупких металлов: чугуна, бронзы, латуни, цинка и др.
Наждак. Этот материал представляет собой мелкозернистую синевато-серую или коричневую горную породу, состоящую из корунда и окиси железа. Твердость наждака зависит от содержания в нем корунда (обычно 50—60% ). Лучшие сорта содержат до 90% корунда. Твердость хорошего наждака близка к твердости корунда.
Венская известь. Под таким названием известна широко применяемая при полировании, а также при обезжиривании известь, состоящая из окиси кальция и углекислого кальция. Венская известь готовится из отборного известняка или доломита путем обжига и гашения. Гашеную известь (или доломит) добавлением воды превращают в густое тесто, которое намазывают тонким слоем на дощечки и подвергают действию углекислоты воздуха. После этого массу снимают с дощечек, формуют в виде кирпичиков, которые оставляют на воздухе, пока они не перестанут быть жирными на ощупь, и сушат.
Необходимо следить за тем, чтобы в венской извести совершенно отсутствовали примеси глины, которые могут царапать полируемое изделие. Хорошая венская известь должна отличаться исключительной мелкозернистостью, не должна содержать влаги и примесей железа и по внешнему виду быть жирной. Хранить венскую известь следует в тщательно закрытой или в запаянной посуде. .
Для закрепления абразивных порошков на шлифовальных кругах могут применяться также карбомидный и другие синтетические клеи. При полировании связующими веществами служат различные полутвердые жиры: стеарин, олеин, техническое сало, солидол, воск, парафин и др.
Пасты для полирования
. Наилучшей полирующей пастой, типовой по составу, по свойствам и действию, считается паста из венской извести и олеиновой кислоты. Приготовляют ее следующим образом. В зависимости от требуемой консистенции пасты на слабом огне расплавляют от 2 до 6 частей стеарина, прибавляют 10 частей олеина, одну часть серы и медленно при перемешивании добавляют (в зависимости от необходимой твердости) около 50—60 частей венской извести. Готовую пасту формуют в кубики, свечи и т. д.
Из паст быстрого действия широко применяют пасты с окисью хрома. Эти пасты состоят из разных количеств окиси хрома, кремнезема, стеарина и керосина и известны под названием паст ГОИ.
Различают пасты жировые, применяемые для окончательного шлифования (подмазка при салке) и полировальные — для окончательной отделки основного металла и гальванических покрытий.
Приспособления для шлифования и полирования.
Большое значение при шлифовании и полировании имеют различного рода приспособления для закрепления обрабатываемых деталей, благодаря которым обработка значительно ускоряется и условия труда становятся безопасными. Рационально продуманные конструкции различных державок, оправок, подкладок, одноместных и многоместных приспособлений позволяют во много раз увеличивать производительность и предохранить от травм.
Приспособления должны быть легки, прочны, удобны для пользования, набор и снятие деталей не должны занимать много времени.
Другие методы обработки.
Наряду со шлифованием и полированием применяются и другие методы механической обработки.
Крацевание и обработка щетками. Под этим названием известен процесс обработки изделий круглыми проволочными щетками для очистки поверхности. Видоизмененным крацеванием является матирование, т. е. получение матовой поверхности путем применения специальных щеток из тонкой (00,5 мм) стальной, латунной или реже медной проволоки. При быстром вращении такой щетки острые концы закрепленной пучками проволоки ударяют по поверхности металла и снимают с нее очень мелкую стружку. Получающиеся при этом мелкие царапины точечного характера придают поверхности матовый вид. Степень матовости зависит от скорости вращения щеток: чем больше число оборотов, тем чаще точки и тем меньше царапины.
При крацевании изделие смачивается раствором мыла или мыльного корня. Для крацевания применяются станки такого же типа, как и полировальные, но облегченные, часто их устанавливают на верстаках. Крацевание применяется также для уплотнения гальванических отложений, особенно серебряных и оловянных, при нанесении толстых слоев металлов. В этом случае крацеваниё в процессе гальванического покрытия производится несколько раз.
Профилированные детали часто обрабатывают волосяными щетками.
Дисковые щетки, изготовленные из конского волоса, при шлифовании металлов применяются:
1) для шлифования с жировой пастой фигурных изделий с рисунками и углублениями;
2) для окончательного шлифования стальных изделий с жировой пастой после обработки мелким наждаком;
3) для снятия различных дефектных покрытий и подготовки поверхности под вторичное покрытие.
Во многих из указанных случаев вместо волосяных щеток пользуются щетками, изготовленными из манильской или так называемой мексиканской травы (фибера).
При шлифовании волосяной или травяной щеткой пользуются жировой пастой, изготовленной из весьма мелкого наждака—пыли в смеси со стеарином и машинным маслом или техническим салом. Для того чтобы паста хорошо приставала к щетке, ее предварительно смачивают в машинном масле.
Обработка в барабанах— галтовка. Для подготовки поверхности мелких изделий и деталей их подвергают обработке в барабанах или колоколах. Процесс шлифования в барабане с целью удаления с поверхности изделий грубых неровностей называется галтовкой.
Галтовка производится сухим или мокрым способом, в зависимости от характера требуемой обработки. При мокром способе применяют обычно растворы слабых щелочей, действующих на полирующую способность абразивов (мыльная вода, растворы щелочи и аммиачных солей). Также применяют и слабые растворы кислот (соляной или серной), способствующих удалению окислов.
Если обработка ведется с абразивными материалами, то происходит также шлифование и полирование поверхности.
Крупные детали и изделия галтуются обычно в барабанах при 10—30 об/мин, мелкие —при 20—60 об/мин.
Процесс барабанного шлифования длителен и зависит от состояния поверхности обрабатываемых предметов, веса изделий, материала и скорости вращения барабана. Галтовка мелких изделий, полученных холодной штамповкой, длится от 2 до 8 ч.
Длительность процесса для различных изделий устанавливается пробой.
Кроме барабанов, для галтовки применяются также и колокола. Для мокрой галтовки мелких изделий и деталей хорошие результаты дает применение барабана колокольного типа, устройство которого позволяет устанавливать угол наклона в зависимости от количества и величины деталей.
После обработки в барабанах изделия непосредственно подвергаются гальваническим покрытиям или полированию. Иногда процесс галтовки является окончательной операцией.
Из других способов обработки мелких изделий и деталей хорошую отделку поверхности дает обработка полировальными стальными шариками.
Полирование стальными шариками производится в барабанах различной формы с применением мыльно-щелочных полировальных составов. Шарики, вращаясь вместе с изделиями в барабане, своим давлением и трением выравнивают и сглаживают поверхность изделий, не снимая при этом стружки. Область применения полирования шариками очень велика. Полировать шариками можно все металлы, за исключением лишь тонких изделий, которые в процессе обработки могут погнуться или быть повреждены.
Пескоструйная и гидроабразивная очистка. Очистка металлических поверхностей путем обдувки песком является эффективным и экономичным методом подготовки перед такими защитными покрытиями, как цинкование, кадмирование, фосфатирование, где требуется чистая матовая поверхность металла. Однако высокая профессиональная вредность обдувки сухим кварцевым песком побуждает заменять этот способ другими, менее вредными, куда относятся очистка влажным песком, металлическим песком, гидропескоочистка и дробеструйная очистка, а также жидкостно-абразивная обработка.
Установка для гидропескоочистки состоит из сборника, снабженного мешалкой или центробежным насосом и наполненного песком с водой, который под действием сжатого воздуха через сопло подается на поверхность деталей, подвергаемых очистке. Необходимое при этом давление воздуха должно быть не ниже 3,5 ат. [2]
Операции химической подготовки поверхности перед нанесением гальванических покрытий — травление в кислотах, обезжиривание, химическое и электрохимическое полирование, а также декапирование и промывка в воде — являются весьма ответственными операциями в общем процессе гальванических покрытий, так как только химическая чистота поверхности обеспечивает хорошее качество покрытия и прочность сцепления его с поверхностью покрываемого металла.
Травление применяется для снятия продуктов коррозии (окислов, окалины и ржавчины) с поверхности металлов и легкого выявления его структуры с целью улучшения сцепления покрытия с основным металлом. Применяется оно перед штамповкой, шлифованием и непосредственно перед нанесением гальванических покрытий, если производятся неблестящие покрытия.
На скорость процесса травления существенно влияют концентрация кислоты в растворе, температура травильных растворов, перемешивание их и накопление в растворе продуктов реакции в виде осадка сернокислых солей железа.
Перед травлением в случае, если поверхность металла или деталей покрыты слоем жира или масла, ее необходимо обязательно обезжирить.
Процесс травления листового материала, проволоки, деталей или заготовок подразделяется на ряд имеющих важное значение операций:
1. Травление. Металл в листах, заготовки или детали, закрепленные на рамах, сетках или приспособлениях, изготовленных из кислотоустойчивого материала, погружают в нагретый травильный раствор и выдерживают до тех пор, пока поверхность металла освободится от окалины, а отдельные места, покрытые еще пленкой разрушенной окалины, могут очищаться при легком механическом воздействии. Температура свежесоставленных растворов поддерживается в пределах 40—50° С с увеличением ее под конец работы раствора до 60—85° С. Время выдержки при травлении составляет 20—90 мин и зависит от состояния металла и степени истощения раствора.
2. Промывка в проточной воде. Для удаления травильного раствора и оторванной, но прилипшей окалины протравленный металл тщательно промывают проточной холодной водой под давлением и протирают щетками.
3. Промывка в горячей воде. Одна промывка в холодной воде не позволяет полностью удалить из пор металла остатки травильной жидкости и солей, которые затем способствуют его быстрому ржавлению. Поэтому дополнительно следует производить промывку травленого металла повторным опусканием его в бак с горячей водой (60—100° С). Когда вода становится грязно-бурой, ее необходимо заменить свежей.
4. Промывка в горячей щелочи. Для нейтрализации следов кислоты и предохранения металла от ржавления его промывают в горячем растворе щелочи. Для этого сразу после промывки в горячей воде травленый металл опускают на несколько минут в бак с кипящим раствором известкового молока или 0,5%-ный раствор каустической соды.
5. Сушка. Этот процесс позволяет устранить травильную хрупкость, появляющуюся при травлении в результате поглощения водорода и восстановить первоначальные свойства металла.
При горячей сушке травильная хрупкость уничтожается в течение 2—3 ч при температуре сушки 110—115° С. Если травление производится как подготовка перед гальваническими покрытиями, то сушка не применяется и детали после промывок поступают в гальванические ванны.
Химическое полирование наиболее часто применяют для отделки меди и ее сплавов (бронза, латунь, мельхиор и др.). Процесс производится в два приема.
1. Предварительное травление в растворе состава:
азотная кислота (уд. вес 1,44).....1000 г
соляная кислота (уд. вес 1,19).....10 мл/л
Перед травлением детали необходимо обезжиривать, промывать и обязательно высушивать, чтобы не разбавлять травильных смесей, иначе травление будет происходить слишком быстро и неравномерно.
2. Химическое полирование в растворе состава:
азотная кислота (уд. вес 1,38—1,44) . 750—800 г
серная кислота (уд. вес 1,80—1,84) . 1000 »
хлористый натрий или соляная кислота ............... 10—20 »
сажа (ламповая).......... 10 »
В этот раствор изделия погружают на 2—3 сек и затем быстро и тщательно промывают в большом количестве воды, после чего высушивают и покрывают бесцветным лаком или подают в ванну гальванического покрытия.
Электролитическое травление производится в 10—20%-ном растворе серной кислоты с добавлением необходимого количества соляной кислоты и поваренной соли под действием постоянного электрического тока. В качестве электродов в ванну завешивают пластины из свинца или кремнистого чугуна.
По применяемым способам различают анодное и катодное травление. При анодном травлении происходит электролитическое растворение металла и механическое отрывание с поверхности пленки окислов выделяющегося пузырьками кислорода. Травление на катоде происходит за счет химического восстановления и механического отрывания окислов бурно выделяющимся водородом.
Наиболее распространенным способом является анодное травление, при котором изделия приобретают совершенно чистую, слегка шероховатую поверхность, благодаря чему покрытие хорошо пристает к металлу. В то же время этот процесс требует к себе большого внимания в части режима и продолжительности, так как поверхность металла можно легко перетравить.
Плотность тока при электролитическом травлении должна быть Dк
= 5 ÷ 1 а/дм2
, напряжение 3—10 в.
Для электролитического травления железа и стали применяются следующие растворы:
серная кислота............150 г/л
хлористый натрий........... 20 »
Режим работы: плотность тока Dк
= 5 ÷ 10 а/дм2
, температура 20—50°С. Аноды — свинцовые.
серная кислота............48 г/л
соляная кислота ........... 12 »
хлористый натрий........... 25 »
Режим работы: плотность тока Dк
= 8 а/дм2
, время выдержки 3—10 мин. Для катодного травления применяются аноды из кремнистого чугуна. Применяется также раствор, состоящий из солей:
сернокислое железо.......... 250 г/л
сернокислый магний......... 50 »
серная кислота............ 20 »
Электролитическое полирование — один из новых методов обработки поверхности металлов — представляет собой процесс выравнивания поверхности металла путем анодного растворения и применяется для повышения качества поверхности металлических изделий в дополнение к механическому шлифованию и полированию. Обрабатываемые детали завешивают в ванну с электролитом в качестве анодов, катодами служат электроды из таких металлов, которые не растворяются в данном электролите. Состав электролита и режим процесса должны обеспечивать преимущественное растворение микроскопических выступов поверхности, в результате чего поверхность становится весьма гладкой и приобретает сильный блеск. При электрополировании решающую роль играют напряжение тока на ванне и плотность тока, которая значительно выше, чем применяемая при осаждении металла.
Метод электрополирования освоен больше всего для нержавеющих сталей, меди и ее сплавов, алюминия, никеля, цинка, серебра и других металлов и является наилучшим способом подготовки поверхности перед гальваническими покрытиями, так как обеспечивает высокую прочность покрытия с основой.
При выполнении технологического процесса электрополирования детали предварительно подвергают обезжириванию органическим растворителем, затем химическому обезжириванию в щелочном растворе с последующей промывкой в горячей и холодной проточной воде. После электрополирования детали промывают сначала в непроточной воде, а затем в холодной проточной воде, после чего их завешивают в ванну для гальванического покрытия. В случае, если после электрополирования покрытие не производится, детали рекомендуется подвергнуть обработке в щелочном растворе, состоящем из 10%-ного едкого натра, при температуре 70—80° С в течение 10—15 мин. Обезжиривание. Назначением обезжиривания является наиболее полная очистка поверхности деталей от всех видов жировых загрязнений, образующихся в результате различных стадий производственной обработки и препятствующих нормальному осаждению гальванических покрытий. Удаление жиров и масел с поверхности может производиться химическими или электролитическими методами.
Для правильного выбора метода обезжиривания необходимо иметь в виду, что по своей химической природе жировые вещества делятся на две основные группы: омыляемые и неомыляемые. Животные и растительные жиры при действии на них горячих растворов щелочи, например каустической соды, разрушаются, образуя мыло, которое смывается горячей водой. Минеральные масла (например, смазочные масла) не образуют со щелочью мыла, т. е. не омыляются, и действие щелочей в этом случае основано на образовании эмульсии, которая способствует отделению масел от металла.
В зависимости от вида жировых загрязнений применяются следующие способы обезжиривания.
1. Обезжиривание в растворителях (керосин, бензин, трихлорэтилен). Этот способ применяется для очистки сильно загрязненных поверхностей от минеральных масел и неомыляемых жиров как предварительная очистка перед химическим и электролитическим обезжириванием.
2. Химическое обезжиривание в горячих растворах щелочей (соды, едкого натра, тринатрийфосфата). Этот способ применяется для очистки поверхностей от жиров растительного и животного происхождения омыливанием их, а также эмульгамированием неомыляемых жиров.
3. Электролитическое обезжиривание. Этот способ применяется для очистки не сильно загрязненных жирами поверхностей, имеющих более или менее правильную, простую, несложную форму, без глубоких впадин и узких глубоких отверстий. Не рекомендуется он для очистки мелких деталей и пружин.
4. Обезжиривание венской известью. Этот способ применяется как самостоятельная операция по подготовке поверхности к покрытию, а также как дополнительная к другим операциям — после химического и электрохимического обезжиривания, травления, шлифования и полирования, а также после частичного изолирования деталей.
Электролитическое обезжиривание. При этом способе обезжиривания детали завешивают в ванну на катодную штангу и обрабатывают катодным током в течение 3—4 мин. Ввиду того, что при катодном обезжиривании на поверхности деталей выделяется большое количество водорода, который, частично проникая внутрь металла, изменяет его физические свойства и вызывает хрупкость, необходимо при помощи перекидного рубильника переключать детали в конце процесса на анод и обрабатывать анодным током в течение 0,5—1 мин.
По окончании обезжиривания детали тщательно промывают в горячей, потом в холодной проточной воде и проверяют на качество обезжиривания. Хорошо обезжиренная деталь должна полностью смачиваться водой.
В связи с внедрением в промышленность ускоренных методов гальванических покрытий предложены скоростные методы обезжиривания и в числе их электролитическое обезжиривание переменным током промышленной частоты. Обезжиривание стальных деталей с помощью переменного, тока производится в электролите следующего состава и режима:
едкий натр............ 10 г/л
кальцинированная сода....... 25 »
тринатрийфосфат......... 25 »
эмульгаторы (ОП-4, ОП-7, ОП-10 или ОС-20) ............. 5—10 г
температура............ 70° С
плотность тока.......... 2—4 а/дм2
напряжение............ 12—15 в
На ванну подается переменный ток низкого напряжения промышленной частоты через понижающий автотрансформатор типа ЛАТР.
Обезжиривание известью. Этот способ имеет целью удаление всех остатков паст, мастики жиров, остающихся в углублениях и в местах стыка деталей. Очистка венской известью применяется также после нанесения изоляции на не подлежащие покрытию места деталей (например, перед хромированием), а также для окончательной очистки после полирования и глянцевания деталей, покрытых медью и никелем. При обезжиривании применяется тонко измолотая венская известь, по составу представляющая смесь из окиси кальция и магния, разведенная в воде до густоты кашицы. Можно применять также гашеную известь в виде густой кашицы с добавлением мела в отношении 1 : 3 или 1 : 2. Обезжиривание обычно производится вручную протиркой щетками или тряпками. Обезжиривание венской известью имеет преимущественное применение для подготовки поверхности перед серебрением, золочением, латунированием и некоторыми другими гальваническими процессами.
Промывка. В процессе подготовки поверхности изделий перед покрытием широко применяются промывки в горячей и холодной проточной воде. Целью промывок является тщательное удаление с поверхности изделий остатков кислых и щелочных растворов, могущих загрязнять электролиты гальванических ванн.
Декапирование. В процессе обезжиривания и промывок на поверхности металлических деталей образуются тонкие окисные пленки, которые, являясь как бы изолирующим слоем, ухудшают прочность сцепления покрытия с основным металлом. Для снятия этих окислов применяется операция, называемая декапированием и заключающаяся в легком протравливании деталей в слабом растворе кислоты.
Декапирование производится в 5—7%-ном растворе соляной или серной кислоты или в смеси этих кислот путем погружения на 20—30 сек и последующей промывки в проточной холодной воде. Эта операция является заключительной в процессе подготовки поверхности деталей к покрытию. После декапирования в результате легкого выявления структуры поверхность металла становится очень активной и легкоокисляемой, поэтому детали следует немедленно завешивать в ванну покрытия. [11]
Источники тока. Основным источником тока для гальванических покрытий являются низковольтные генераторы постоянного тока различной мощности, вырабатывающие ток напряжением 6/12 или 9 В и силой от 250 до 10 000 а. Генераторы марки ЯЭМЗ с силой тока до 1500 а изготовляются с самовозбуждением, более мощные имеют отдельный возбудитель в виде динамомашины напряжением 110 в, смонтированной на общей фундаментной плите с генератором (фиг. 33).

Фиг. 33. Низковольтный генератор постоянного тока.
Возле агрегата устанавливается электрораспределительный щит с измерительными приборами, амперметрами и вольтметрами, предохранителями и рубильниками. Генератор должен иметь пусковой и регулирующий шунтовой реостаты.
При пуске агрегата необходимо сначала включать двигатель и по достижении требуемого напряжения генератором производить включение нагрузки. Выключение следует производить в обратном порядке.
Выпрямители. Для питания гальванических ванн постоянным током находят широкое применение купроксные (меднозакисные) и селеновые выпрямители. Они отличаются простотой ухода, бесшумностью, малыми габаритами, возможностью индивидуального использования.
Наиболее распространены купроксные выпрямители типа ВКГ-1 на 600 а при 6 в и ВКГ-1 на 600 а при 9/12 в.
Токопроводящая сеть. Ток от источников тока к электролитическим ваннам передается по медным, алюминиевым шинам или по круглым проводам. Правильный расчет и подбор сечения шин и проводов с целью обеспечения минимальных потерь электроэнергии в сети имеет для гальванического цеха большое значение, особенно потому, что применяется ток низкого напряжения, но значительной силы.
Подвод тока к самим ваннам осуществляется через укрепленные на бортах ванн на изоляторах анодные и катодные штанги. Система расположения штанг на ванне бывает различной. Очень часто укрепляют катодную штангу между двумя анодными. В более широких ваннах укрепляют две катодные штанги с одной анодной посередине и двумя анодными по краям. Электропроводка к ваннам должна быть выполнена так, чтобы обеспечивался хороший контакт и не случались короткие замыкания. Во избежание утечки тока и нарушения режима работы гальванические ванны должны быть хорошо изолированы от земли, для чего под подставки ванн помещают фарфоровые или резиновые прокладки.
Реостаты. Для регулирования силы тока, поступающего для питания электролитической ванны, применяют специальные приборы — реостаты. Регулирование силы тока при помощи реостата производится в результате введения в цепь добавочного сопротивления определенной величины.
Добавочные сопротивления состоят из проволочных спиралей, изготовленных из металла с большим электрическим сопротивлением (константан, нихром).
Общая сила тока всех секций должна определять максимальную силу тока на ванне. Реостаты монтируются на электрощите каждой ванны, для контроля напряжения и силы тока там же устанавливаются амперметр и вольтметр.
Стационарные ванны для электролитов представляют собой сварные прямоугольные резервуары, изготовленные из листовой стали толщиной 4—6 мм, сверху вдоль всех стенок ванн привариваются борта; ванны больших размеров имеют ребра жесткости. Ванны небольших размеров могут изготовляться из винипласта, керамики, фарфора, фаолита и бакелитированной фанеры, а также из дерева (для слабокислых электролитов).
Одним из лучших материалов для футеровки ванн с кислыми электролитами (никелирование, цинкование, меднение и др.) является винипласт, заменяющий листовой свинец. Винипласт представляет собой негорючую пластмассу коричневого или черного цвета (уд. вес 1,34), легко поддающуюся механической обработке, обладающую высокой химической стойкостью к различным кислотам и щелочам и достаточной механической прочностью до температуры 60° С. [8]
Покрытие мелких деталей в стационарных ваннах нецелесообразно, так как их навешивание для погружения в гальванические ванны является длительным и непроизводительным процессом, особенно при массовом производстве. В связи с этим для покрытия мелких деталей применяются барабанные, колокольные и ковшовые ванны, в которых покрытие мелких деталей осуществляется насыпью без подвешивания.
Барабанные ванны. Барабаны обычно делают гранеными, причем одна из граней — подвижна и служит загрузочным отверстием. В качестве материалов для барабанов применяются пластмассы (текстолит, винипласт, целлулоид) и дерево.
По конструкции барабаны подразделяются на барабаны полного и неполного погружения.
Барабаны снабжаются индивидуальным приводом от электродвигателя, укрепленного на внешней стороне ванны.
Колокольные ванны. Для покрытия мелких деталей, особенно резьбовых и тонкостенных, пользуются колокольными ваннами. Сосудом для электролита служит опрокинутый колокол, круглый или граненый, изготовленный из токонепроводящего материала, не поддающегося разрушению электролитом (пластмасса, гуммированная сталь, дерево). Колокол укреплен на валике. Вращение колокола осуществляется при помощи приводного ремня или зубчатой передачи от электропривода, снабженного редуктором для уменьшения числа оборотов.
Недостатком колокольных ванн является несоразмерность поверхностей анода и катода (последняя несравненно больше первой), вследствие чего невозможно работать при повышенных плотностях тока, так как анод быстро пассивируется и требуется значительное напряжение на полюсах.
Колокольные барабаны. Для гальванических покрытий мелких деталей как в кислых, так и в щелочных электролитах хорошие результаты дают колокола, вращающиеся в ванне, так называемые колокольные барабаны.
При покрытии в колоколах деталей с наружной резьбой скорость вращения колокола должна быть снижена до 3 — 6 об/мин.
Колокольный барабан обычно погружают в ванну достаточной емкости, что устраняет возможность перегрева, а также быстрого загрязнения электролита. Завешенные в ванну аноды обеспечивают необходимый для нормального соотношения с катодной поверхностью размер анодной поверхности, улучшение качества покрытия и чистоту рабочего места.
Ковшовые ванны. Ковшовые ванны применяются для покрытия мелких изделий, которые нельзя подвергать значительным сотрясениям, вызываемым вращением и пересыпанием (как в барабанах и колоколах), особенно если желательно сохранить без изъянов полированную поверхность. Во многих случаях ковшовые ванны дают лучшие результаты, чем колокольные и барабанные. Скорость покрытия в таких ваннах значительно выше, чем в колокольных.
Ковш для изделий, изготовленный из токонепроводящего перфорированного материала, во время процесса покрытия частично погружается в электролит и совершает колебательные движения. Аноды завешиваются снаружи и внутри ковша, что обеспечивает равномерное распределение тока на покрываемых изделиях. Ток к катоду подается с помощью медных контактных полос, укрепленных на днище ковша. [9]
Сушка деталей и изделий после покрытий производится обычно горячим воздухом в сушильных шкафах, снабженных вентиляцией. Подогрев воздуха производится при помощи пара, газа или электричества.
Шкафы устраиваются с несколькими отделениями, размеры которых зависят от количества подлежащих сушке деталей и изделий. При большой производительности цеха устраиваются конвейерные сушильные аппараты и сушильные ванны, в которых обогрев деталей и высушивание производятся путем обдувки горячим воздухом.
Все более широкое применение, особенно для сушки мелких деталей, находят также сушильные центрифуги.
С целью механизации производства и увеличения производительности в гальванических цехах применяются полуавтоматические и автоматические установки для покрытий.
Полуавтоматы предназначаются для выполнения какой-либо одной операции и представляют собой ванны, оснащенные механизмами для непрерывного перемещения подвесных приспособлений с изделиями, подвергаемыми покрытию, от места загрузки до места выгрузки. Они могут быть прямолинейными, когда загрузка и выгрузка изделий осуществляется с противоположных сторон ванны, а также овальными и кольцевыми. При обработке в полуавтоматах операции предварительной подготовки и заключительные операции выполняются в стационарных ваннах.
Прямолинейные полуавтоматические ванны требуют двухстороннего обслуживания. Обрабатываемые изделия перемещаются вдоль ванны с помощью бесконечных пластинчатых цепей; продолжительность процесса устанавливается в соответствии с заданной толщиной покрытия и регулируется изменением скорости движения при помощи вариатора приводной станции. Скорость движения от 0,1 до 1 м/мин.
При помощи полуавтоматических ванн можно обеспечить определенную стабильность технологического процесса. Наиболее полной стабильности технологического процесса можно достигнуть путем применения автоматов.
По конструкции автоматы для покрытий подразделяются на прямолинейные и овальные. Прямолинейные автоматы применяются в тех случаях, когда поток деталей по ходу технологического процесса должен быть направлен в одну сторону.
Большое распространение имеют овальные и П-образные автоматы. Применение автоматов является целесообразным при значительной производственной программе покрытия однотипных деталей.
В автоматических конвейерных установках все операции нанесения покрытий механизированы, начиная от обезжиривания и кончая сушкой деталей.
В автомате производятся следующие операции: химическое и электролитическое обезжиривание, декапирование, меднение цианистое с реверсированием тока, никелирование, сушка и все промежуточные промывки.
Питание ванны электрическим током осуществляется следующим образом. Постоянный ток от генераторов подается на шину, расположенную выше толкающей планки, а скользящая по шине контактная медная щетка передает ток через гибкий кабель на несущий и поддерживающий рычаги.
Производительность автомата в смену 400-500 циклов, что составляет 120—150 м2
покрытой поверхности. Ритм работы автомата рассчитывается в соответствии с требованиями процесса. [4]
Для завески деталей в ванны, а также в полуавтоматы и автоматы применяются специальные контрактирующие приспособления для завешивания. Устройство подвесок зависит от числа и конфигурации монтируемых деталей и может быть самым разнообразным.
При конструировании и изготовлении подвесок необходимо учитывать следующие основные требования:
а) материал подвесок должен быть достаточного сечения, чтобы проводить ток соответствующей силы;
б) подвеска должна иметь хороший контакт с покрываемыми деталями и катодной штангой ванны;
в) для получения равномерного покрытия подвеска должна обеспечивать свободный доступ тока к деталям;
г) для устранения возможности покрытия подвески осаждаемым металлом она должна быть покрыта, за исключением мест контакта, изоляционным материалом;
д) конструкция подвески должна рационально использовать объем ванны;
е) монтаж и демонтаж деталей с подвесок не должны быть затруднены;
ж) подвески для покрытия в полуавтоматах и автоматах должны обеспечивать прочное закрепление деталей, исключающее их выпадение при толчках.
Детали в подвесках должны быть расположены так, чтобы они не экранировали одна другую, а образовавшиеся газы легко удалялись с поверхности деталей, не создавая «газовых мешков».
Контактные крючки, штыри и пружины, на которые крепятся детали, рекомендуется делать из проволоки фосфористой бронзы. В качестве материала для подвесок рекомендуется применять сталь. Сечение стальных подвесок выбирают с таким расчетом, чтобы они в процессе электролиза не нагревались. Удельная сила тока на стальных подвесках не должна превышать 1 а/мм2
, латунных 1,5 а/мм2
, медных 2—3 а/мм2
.
На поверхности подвесок, не изолированных от действия электролитического тока, в процессе осаждения отлагается большое количество металла, что ведет к непроизводительным потерям цветных металлов. Поэтому подвески за исключением мест контактов необходимо изолировать, а так как детали обрабатываются в щелочных и кислых растворах, материал, применяемый для изоляции, должен быть стоек к этим растворам. Необходимо также, чтобы изоляционный материал не загрязнял электролит и не приводил к преждевременному выходу его из строя.
Для изоляции подвесок можно применять:
1) перхлорвиниловые химически стойкие лаки (ХСЛ, ПХВ, ХВЛ и ОНИЛХ);
2) нитролаки и нитроклеи (цапонлак, эмалит);
3) клеи типа БФ-2, БФ-4, БФ-6, резиновые клеи типа № 88, термопреновый клей и клей № 4508;
4) ленты из химически стойких специальных пластмасс (полиэтилен, фторпласт-3, хлорвинил, резина и др.);
5) массы из игелита и дибутилфталата.
Кроме того, в качестве материалов для изготовления подвесок можно применить бакелитизированную фанеру, пропитанную фенольно-формальдегидными смолами. В этом случае ствол подвески изготовляют из бакелитизированной фанеры, винипласта или из пропитанной парафином древесины и только контактные крючки, соединенные между собой проволокой,— из металла. Такие подвески весьма прочны и благодаря своей легкости удобны в работе.
Внедряется также метод изоляции подвесок путем напрессовки (заливки) капроном и метод вихревого напыления пластмасс (полиэтилена). [8]
Никель—металл белого цвета, с незначительным желтоватым оттенком, довольно твердый и ковкий, хорошо поддающийся полированию. Атомный вес никеля 58,69, удельный вес 8,9 г/см3, электрохимический эквивалент 1,095 г/а-ч, нормальный потенциал 0,25 в, температура плавления 1452° С. Никелевые отложения имеют обычно мелкокристаллическую структуру, однако особенно в тонких (до 25 мк) слоях отличаются значительной пористостью, которая уменьшается с увеличением толщины слоя. [2]
Никелированием преследуют обычно две цели: защиту от коррозии и придание изделиям красивого внешнего вида. Никелирование широко применяется для окончательной отделки изделий в различных областях промышленности: автомобильной, приборостроительной, а также в производстве изделий широкого потребления. [10]
В тех случаях, когда никелированную поверхность необходимо сохранить блестящей, на никелевое покрытие наносят хромовое. Толщина слоя хрома должна быть в пределах 0,5—1 мм.
Процесс никелирования производится:
1) в стационарных ваннах;
2) в барабанах и колоколах (покрытие мелких деталей);
3) в стационарных ваннах (для интенсифицированного процесса с воздушным перемешиванием или с качающимися катодами);
4) в полуавтоматических установках;
5) в автоматах (при большой производственной программе).
Электролиты для никелирования
Никелирование производится в кислых или слабокислых электролитах, основным компонентом которых является сернокислый никель или никелевый купорос, хлористый никель, борфтористый никель и двойная соль никель-аммония (последняя имеет меньшее применение).
Для никелирования в стационарной ванне рекомендуется следующий состав электролита:
сернокислый никель........ 140—200 г/л
сернокислый натрий........ 50—70 »
сернокислый магний........ 10—20 »
борная кислота .......... 25—30 »
хлористый натрий или хлористый
калий ............. 5—7 »
Режим работы: плотность тока Dк
= 0,5÷1,0 а/дм2
, температура 18—20° С, кислотность рН = 5,2 ÷ 5,8. При подогреве до 30— 50° С и воздушном перемешивании или при помощи качающихся катодных штанг плотность тока можно увеличить до Dк
=1,5÷2,5 а/дм2
.
В последние годы в промышленности находят применение новые борфтористоводородные электролиты, обладающие значительными преимуществами в сравнении с сернокислыми электролитами. [2]
Блестящее никелирование. Никелевые покрытия, применяемые для защитно-декоративной отделки, должны иметь блестящую поверхность, что обычно достигается механическим полированием покрытий. Для блестящего никелирования широкое применение нашел электролит такого состава:
сернокислый никель........ 200—300 г/л
борная кислота.......... 25—30 »
хлористый натрий или хлористый калий.............. 3—15 »
фтористый натрий или фтористый калий.............. 4—6 »
2,6 и 2,7 дисульфонафталиновая кислота 2—3 »
формалин (40 %-ный)........ 1 мл/л
Режим работы: плотность тока Dк
= 1,5 ÷2,5 а/дм2, температура электролита 20—30° С, кислотность рН = 5,8÷6,3; выход по току 95—96%; необходимо перемешивание электролита и чистая или непрерывная фильтрация, без перемешивания плотность тока не выше Dк
= 0,5÷0,6 а/дм2
.
При барабанном никелировании массового производства изделий последние, вследствие продолжительного трения, приобретают покрытие, отличающееся некоторой глянцевитостью..
Химическое никелирование. Химическое (безэлектролизное) никелирование стальных деталей и деталей из меди и ее сплавов осуществляется из растворов, содержащих простые соли никеля, под действием гипофосфита натрия или кальция, являющегося восстановителем.
Данный способ не требует наличия источников тока и электрического оборудования. Химическим путем можно покрывать никелем детали любого профиля, причем толщина отложений получается одинаковой на любом участке поверхности, в том числе и на внутренних поверхностях. Химическое никелирование осуществляется в стеклянных или керамических ваннах. Этот способ нашел применение в медицинской промышленности, в производстве часов и по мере увеличения выпуска гипофосфита внедряется в других отраслях. [11]
Сернокислые электролиты для никелирования очень чувствительны ко всякого рода примесям, загрязнениям и нарушениям процесса осаждения, являющимся причиной разных дефектов покрытия. Наиболее часто встречающимся дефектом является отслаивание покрытия. Причиной этого явления обычно бывает плохая предварительная очистка поверхности и недостаточно хорошо выполненные обезжиривание и декапирование.
Контроль качества никелевых покрытий производят по таким основным показателям: внешний вид, толщина покрытия, отсутствие пор и прочность сцепления с основным металлом. Контроль толщины никелевых покрытий производят по ГОСТ 3303-58. [8]
Медь — пластичный, легко полирующийся металл, являющийся хорошим проводником электрического тока. Удельный вес меди 8,9 г/см3, атомный вес 63,54. Температура плавления 1084° С. В химических соединениях медь может быть одновалентной (в цианистых электролитах) и двухвалентной (в кислых электролитах), соответственно и электрохимический эквивалент меди будет 2,372 и 1,186 г/а·ч. Гальванически осажденная медь имеет красивый розовый цвет. Медь легко растворяется в азотной и хромовой кислотах, слабее в серной и соляной кислоте. [2]
На воздухе медь легко окисляется, особенно при нагревании, в результате чего она теряет свой обычный цвет и блеск.
Метод гальванического осаждения меди, открытый в 1838 г. русским ученым Б. С. Якоби, является старейшим методом гальванических покрытий.
Обычно медные покрытия применяют с целью экономии никеля как подслой при никелировании и хромировании. Вследствие промежуточного покрытия стали и чугуна медью достигается лучшее сцепление между основным металлом и металлом покрытия и уменьшается сквозная пористость покрытия.
Медные покрытия широко применяются для целей гальванопластики при изготовлении архитектурных художественных изделий (барельефов, скульптур), а также в приборостроении при производстве отражателей, полых тонкостенных бесшовных медных трубок и других сложнейших полых деталей.
Медные покрытия применяются: для придания притирочных свойств поверхности деталей машин, станков и механизмов, для уменьшения шума при трении, для замены в целях экономии цветного металла медной аппаратуры, валов и других изделий из меди стальными и медненными, для восстановления деталей до нормальных размеров при ремонте различных изделий, а также с целью оксидирования медных покрытий и химической окраски для декоративных целей.
Свойства медных покрытий — твердость, эластичность и прочность сцепления, а также структура зависят главным образом от составов электролитов, из которых они были получены. [10]
Электроосаждение меди практически производят из электролитов двух типов: кислого и цианистого.
Кислые электролиты. Для меднения из кислых электролитов применяют сернокислые, пирофосфорнокислые, борфтористые и щавелевокислые. Наиболее простым электролитом является раствор сернокислой меди с добавлением (для улучшения электропроводности) серной кислоты. Кислые электролиты отличаются стабильностью в работе и позволяют применять высокие (до 30 а/дм2
) плотности тока. Выход по току составляет около 100%. Основными недостатками этих электролитов является их низкая рассеивающая способность, а также невозможность осаждения меди непосредственно на сталь и чугун. При погружении этих металлов в электролит на поверхности их выделяется осадок контактной (без действия тока) меди, непрочно держащийся на поверхности покрываемого металла и обладающий большой пористостью.
Широкое применение для меднения имеет кислый электролит такого состава:
сернокислая медь....... 240—260 г/л
серная кислота ........ 50—70 »
Режим работы: плотность тока без перемешивания Dк = 2 ÷ 4 а/дм², а с перемешиванием 5 ÷ 10 а/дм²; температура 20—25° С.
Цианистые медные электролиты. Главной составной частью цианистых электролитов является комплексная цианистая соль меди и натрия или меди и калия. В цианистых электролитах получаются мелкокристаллические и плотные осадки меди. Электролит обладает хорошей рассеивающей способностью.
В цианистых электролитах медь осаждается на катоде из одновалентных ионов. Электрохимический эквивалент ее 2,372 г/а·ч. Поэтому при прохождении тока 1 а·ч должно получаться меди вдвое больше, чем из кислых ванн, где медь находится в виде двухвалентных ионов.
Основным недостатком цианистых ванн является их вредность, так как входящие в их состав цианистый натрий или цианистый калий являются сильнейшими и очень опасными ядами, работа с которыми требует соблюдения большой осторожности и специальных условий.
В обычных условиях для меднения применяется цианистый электролит следующего состава:
медноцианистая комплексная соль . . 40—50 г/л
цианистый натрий.........10—20 »
Режим работы: плотность тока Dк
=0,3 ÷ 1,0 а/дм2
, температура 20—25° С, выход по току 60—70%.
Наиболее простым способом приготовления медноцианистых электролитов является способ приготовления электролита из цианистой меди, которая с цианистым натрием образует комплексную медноцианистую соль. При отсутствии цианистой меди электролит приготовляют из сернокислой меди (медного купороса) по двум способам: предварительно готовят основную углекислую медь или приготовляют соль Шевреля. Основная углекислая медь приготовляется действием углекислого натрия на раствор медного купороса.
Нецианистые электролиты. Из нецианистых медных электролитов, пригодных для непосредственного осаждения меди на сталь, удовлетворительные результаты дает фосфорнокислый электролит следующего состава:
сернокислая медь............35 г/л
пирофосфорнокислый натрий.......140 »
фосфорнокислый натрий двузамещенный . 95 »
сегнетова соль.............25 »
Режим работы: плотность тока Dк
= 0,5 ÷ 1 а/дм2
, температура 25—35° С, загрузка деталей производится под током при первоначальной (в течение 5—10 сек) плотности 5 ÷ 6 а/дм2
; через 5 мин после начала электролиза рекомендуется перемешивание раствора сжатым воздухом.
Аммиачный электролит для меднения. С целью замены весьма ядовитых и неустойчивых цианистых электролитов предложен аммиачный электролит следующего состава:
сернокислая медь ......... 80—100 г/л
сернокислый никель........ 20 »
сернокислый натрий........ 40 »
сернокислый аммоний....... 80 »
аммиак (25%-ный).........180 мл/л
В этом электролите исходным материалом для образования аммиачно-медного комплекса является сернокислая медь и водный 25%-ный раствор аммиака, который для увеличения устойчивости комплекса вводится с избытком.
Режим работы: плотность тока на катоде Dк
= 2,5 ÷ 3,0 а/дм2
, плотность тока на аноде Dа
=5 ÷ 6 а/дм2
, температура 20—25° С, в начале электролиза необходим двукратный толчок тока. Лучшие результаты дают никелевые аноды, которые не пассивируются. Выход по току составляет 90 — 95%. Для улучшения прочности сцепления меди с основой после обычной подготовки поверхности рекомендуется кратковременное травление в 10%-ном растворе азотной кислоты. Детали необходимо завешивать в ванну меднения под током.
Контроль медных покрытий заключается в оценке качества по внешнему виду. Проверка толщины слоя производится в соответствии с ГОСТ 3003-58. [2]
Хром — твердый, хрупкий металл серебристо-стального цвета. Атомный вес хрома 52,01, удельный вес 6,92—7,2 г/см3
, температура плавления 1520° С. Электрохимический эквивалент 0,323 г/а·ч. Все хромовые покрытия обладают хорошим сцеплением со сталью, медью, латунью, никелем и другими металлами и придают изделиям, особенно после полирования, красивый блестящий голубоватый оттенок. Хром характеризуется высокой твердостью, износостойкостью, жаростойкостью; только при температуре 480—500° С он начинает приобретать цвета побежалости. Хром имеет большую склонность к пассивированию, благодаря чему хромовые покрытия длительное время сохраняют блестящий вид, что выгодно отличает их от других гальванических покрытий.
Зеркальные хромовые покрытия по отражательной способности уступают лишь отражательной способности серебра, но превосходят ее длительностью сохранения блеска. Хромовые покрытия устойчивы к действию влажной атмосферы, щелочей, органических кислот, концентрированной азотной кислоты; разбавленная азотная и соляная кислоты растворяют хром. Органические кислоты на хром не действуют. Хром хорошо растворяется в соляной кислоте, а также в горячей концентрированной серной кислоте и в щелочах под действием электрического тока. [2]
Благодаря высоким физико-химическим свойствам хрома электролитическое покрытие хромом — хромирование — находит широкое применение в машиностроении.
Основная цель хромирования — сохранение красивой, блестящей поверхности изделий (декоративное хромирование) и повышение сопротивления механическому износу (твердое износостойкое хромирование). Для улучшения коррозийной стойкости при декоративном хромировании в качестве подслоя наносят никель, медь или комбинируют слои этих металлов.
Декоративное хромирование применяется во многих отраслях промышленности.
Другой областью широкого применения хрома как средства против износа является твердое хромирование, имеющее большое значение для инструментального производства. [10]
Процесс электролитического осаждения хрома значительно отличается от других процессов гальваностегии как по составу электролита, так и по условиям протекания процесса. Отличием является также и применение нерастворимых (свинцовых) анодов. Электролиты для хромирования состоят в основном из хромового ангидрида (хромовая кислота). Получение удовлетворительных хромовых покрытий из такого электролита возможно только при добавлении в малых количествах определенных анионов — обычно анионов серной кислоты. Для осаждения хрома в таких электролитах требуется значительно более высокая плотность тока, чем при других покрытиях, что требует применения мощных источников тока.
Процесс хромирования металла отличается весьма малым выходом по току, который для большинства электролитов колеблется в пределах 12—15%. Электрохимический эквивалент хрома в связи с осаждением хрома из шестивалентных соединений также невелик. Поэтому, несмотря на применяемую высокую плотность тока, осаждение хрома происходит довольно медленно.
Особенностью хромирования является крайне низкая рассеивающая способность электролита, что затрудняет хромирование профилированных деталей и вызывает необходимость применения дополнительных анодов и экранов.
Свойства осадков хрома, которые подразделяются на матовые, блестящие и молочные, зависят от условий осаждения, т. е. от состава и концентрации электролита, плотности тока, температуры, величины анодов и их расположения и т. п.
Процесс хромирования очень чувствителен к колебаниям температуры и плотности тока. Оба эти фактора находятся во взаимной зависимости. Повышение температуры снижает выход по току, ь повышение плотности тока повышает его. Блестящие покрытия получаются при высоких плотностях тока только в случае, если одновременно повышаются температура и плотность тока. При температурах ниже 40° С получаются матовые серые осадки хрома, хотя выход по току увеличивается. При температуре ниже 50° С с повышением концентрации интервал блестящих осадков гюзрастает, т. е. более концентрированные растворы дают блестящие осадки при более низкой температуре. При температуре выше 50° С, наоборот, зона блестящих осадков с понижением концентрации хромовой кислоты возрастает. Это значит, что при более высокой температуре получаются блестящие осадки в ваннах малой концентрации. Наиболее широкие возможности дает температура 45—55° С. [6]
Для разных условий производства могут быть рекомендованы следующие практически проверенные составы электролитов и режимы хромирования.
1. Нормальный электролит (универсальный):
хромовый ангидрид...... 250 г/я
серная кислота........ 2,5 »
Режим работы: плотность тока Dк
= 15 а/дм2
при температуре 45°С, Dк
= 25 а/дм2
при температуре 50° С и Dк
= 35 а/дм2
при температуре 55° С. В этом электролите можно производить как декоративно-защитное, так и твердое хромирование.
2. Электролит для износостойкого твердого хромирования профилированных изделий:
хромовый ангидрид..... 120—150 г/л
серная кислота.......1,0—1,5 »
Режим работы: плотность тока Dк
=30 / 40 а/дм2
при температуре 50—55° С.
Электролит для хромирования готовится следующим образом.
Вначале хромовый ангидрид растворяют в необходимом количестве воды. Раствор, взятый по расчету, тщательно перемешивают и в случае, если он окажется мутным, отстаивают. Прозрачный раствор сифоном переливают в другой сосуд.
Хромирование в саморегулирующихся электролитах. Для повышения устойчивости хромовых электролитов в работе предложен метод добавок солей, имеющих ограниченную растворимость в хромовом электролите. В качестве таких солей применяют сульфат стронция SrS04
и кремнефторид калия K2
SiF6
. Введенные в хромовый электролит в количествах, превышающих их растворимость, эти соли будут находиться в небольшом избытке на дне ванны в виде твердой фазы; содержание посторонних анионов в растворе при постоянной температуре и изменении концентрации хромового ангидрида будет автоматически поддерживаться постоянным за счет частичного растворения этого избытка.
Рекомендуется электролит такого состава:
хромовый ангидрид (очищенный от
примеси сульфатов)....... 250 г/л
сульфат стронция ......... 6 »
кремнефторид калия ........ 20 »
Режим работы: плотность тока Dk=40 / 80 а/дм2
, температура 55—65°С, выход металла по току 18—20%.
Преимуществом этого электролита является отсутствие необходимости в частой корректировке, кроме того, он менее чувствителен к изменениям температуры и благодаря повышенному выходу, но току значительно производительнее (в 1,5 раза) обычных хромовых электролитов. [2]
Черное и цветное хромирование. Хромовое покрытие черного цвета может быть получено в электролите, состоящем из 350 г/л хромового ангидрида и 5 мл/л уксусной кислоты, при плотности тока Dк
= 100 а/дм2
, температуре 10—20° С, в течение 10—20 мин. Для получения декоративного «агатового» покрытия, представляющего сложный рисунок тонких серо-голубых полос на темно-синем фоне, применяется электролит следующего состава:
хромовый ангидрид............ 300—400 к/г
углекислый барий............ 5—10 »
уксуснокислый кальций.......... 4—8 »
уксуснокислый цинк........... 2—5 »
Режим работы: плотность тока Dк
=30 ÷100 а/дм2
, температура 25—40° С, время обработки 10—20 мин.
Комбинированные покрытия двухслойным хромом. Противокоррозийная устойчивость хромовых покрытий находится в прямой зависимости от их пористости. Наименьшей пористостью обладают осадки «молочного» хрома, получаемые при повышенной температуре. Это свойство молочного хрома позволяет применять противокоррозийное хромирование стальных изделий без подслоя, например для хромирования хирургических инструментов с осаждением слоя 6—7 мк.
Для улучшения износостойкости предложен метод двухслойного покрытия хромом, заключающийся в осаждении блестящего твердого покрытия поверх молочного, беспористого. Это позволяет одновременно защищать изделия от коррозии и от механического износа. Производственные испытания показали хорошие эксплуатационные качества таких комбинированных покрытий.
Скоростное коррозиеустойчивое хромирование. В промышленности успешно применяется новый способ холодного хромирования с применением раствора тетрахромата, позволяющий получать практически беспористые покрытия хрома, отличающиеся высокой коррозийной стойкостью. В отличие от осадков обычного хромирования осадки хрома, полученные из тетрахроматного электролита и осажденные непосредственно на полированный металл, имеют матовый серый цвет. Однако эти осадки довольно легко полируются, приобретая блеск, присущий хрому. Полировать рекомендуется войлочными кругами с пастой ГОИ. Твердость осадков хрома приближается к твердости электролитического никеля. Состав электролита:
хромовый ангидрид......... 375—450 г/л
едкий натр............. 50—70 »
серная кислота...........0,8—1 »
сернокислый магний........ 2—3 >
трехвалентный хром (образуется
в электролите) :........5,0—20 »
Хромирование производится при плотности тока Dж
=20 ÷ 30 а/дм2
и температуре 15—25° С. Повышение температуры электролита выше 35° С ведет к получению дефектных покрытий, поэтому ванну необходимо охлаждать и следить, чтобы объемная плотность тока не превышала 1 —1,5 а/л. Рассеивающая способность тетрахроматного электролита значительно выше, чем стандартных электролитов, что позволяет успешно хромировать рельефные изделия. [9]
Серебро — белый, мягкий и ковкий металл. Атомный вес серебра 107,88, удельный вес 10,5 г/см3, температура плавления 960° С, электрохимический эквивалент 4,025 г/а-ч.
Серебро обладает самой высокой электропроводностью, хорошо полируется и имеет большую отражательную способность. Серебро очень стойко в едких щелочах; разбавленная соляная и серная кислоты на него не действуют. В горячей концентрированной серной кислоте оно легко растворяется. Легко растворяет серебро и азотная кислота. Серебряные гальванические покрытия имеют довольно широкое применение в приборостроении для покрытия электроконтактов и изготовления зеркал. Широко применяется серебрение и в декоративных целях для изделий домашнего обихода: для столовых приборов, посуды и ювелирных изделий.
Непосредственное серебрение стальных деталей производится редко, перед серебрением детали обычно меднят с последующим глянцеванием. Чаще всего серебрят изделия из меди и ее сплавов. При содержании в атмосфере даже незначительного количества сероводорода серебряные покрытия темнеют, покрываясь налетом сернистого серебра. Для предохранения от потускнения серебряные покрытия дополнительно покрывают тонкими слоями палладия или бериллия.
Для серебрения в промышленности в основном применяют цианистые электролиты, в составе которых серебро находится в виде сложных цианистых соединений.[10]
Содержание серебра в электролите может колебаться в больших пределах и зависит от требований, предъявляемым к покрытию. Так, толстые покрытия серебра рекомендуется получать из электролитов, содержащих серебро (в пересчете на металл) в пределах 30 г/л, низкая концентрация серебра (до 5—10 г/л) применяется при нанесении тонких серебряных покрытий и в случае применения низких плотностей тока.
Для получения серебряных покрытий с повышенной твердостью и износостойкостью рекомендуется следующий состав электролита:
серебро (в пересчете на металл) .... 30 г/л
кобальт (в пересчете на металл) . . . . 1 »
цианистый калий (свободный) 20 »
поташ................ 30 »
Режим работы: плотность тока Dк = 0,8 / 1 а/дм2
, температура 15—25° С.
Твердость серебряного покрытия из этого электролита повышена в 1,5, а износостойкость — в 3 раза по сравнению с покрытиями из обычных электролитов. [2]
Кадмий — мягкий, пластичный и весьма ковкий серебристо-белый металл. Атомный вес кадмия 112,41, удельный вес 8,6 г/см3, температура плавления 521° С.
По своим химическим свойствам кадмий близок к цинку. Кадмиевые покрытия, так же как и цинковые, являются анодными покрытиями по отношению к железу и его сплавам. Однако в отличие от цинка кадмий более стоек к действию растворов солей, щелочей и слабых кислот. Благодаря этим свойствам и высокой пластичности кадмий, несмотря на значительно более высокую стоимость по сравнению с цинком, находит применение для покрытия изделий, соприкасающихся с морской водой и для притирки резьб крепежных деталей, Кадмирование производят из кислых и цианистых электролитов, причем в первом случае для покрытия деталей или изделий простой формы и во втором случае для покрытия деталей сложного профиля. Структура кадмиевых покрытий из кислого электролита получается более крупной, чем из цианистого). По этой причине кислые электролиты не нашли широкого применения.
Состав кислого электролита:
сернокислый кадмий......... 64 г/л
сернокислый аммоний......... 33 »
сернокислый алюминий........ 28 »
клей .............. 0,5 »
Режим работы: плотность тока Dk= 0,5 / 1,0 а/дм2, температура 18—20° С, кислотность рН = 3,5.
В качестве анодов применяют кадмий марки Кd1-0 или Кd-1.
Для покрытия изделий сложного профиля применяют следующий цианистый электролит:
- окись кадмия ........... 40—45 г/л
цианистый натрий.........150 —175 »
сернокислый натрий ........ 40—50 »
сернокислый никель......... 1—5 »
каустическая сода .........15—20 »
сульфитный щелок......... 8—10 »
Режим работы: плотность тока Dк=2 / 4 а/дм2, температура 15—25° С, выход по току 95%.
Существует ряд примесей-металлов (серебро, свинец, олово, мышьяк и сурьма), которые резко ухудшают качество покрытия. Особенно вредное действие оказывают серебро, свинец и олово. При загрязнении этими примесями электролита покрытия получаются губчатыми, темными и плохо сцепляются с основным металлом. Попадают эти металлы в электролит из кадмиевых анодов, в которых они иногда присутствуют.[2]
Лужение (покрытие оловом) находит применение в промышленности благодаря специфическим свойствам олова.
Олово — серебристо-белый мягкий и пластичный металл. Атомный вес олова 118,70, удельный вес 7,3 г/см3, температура плавления 232° С. В ряде органических кислот олово по отношению к железу является анодом. Соединения олова безвредны для человеческого организма. Эти два свойства олова обеспечили применение его в качестве защитного покрытия на изделиях, применяемых для изготовления и хранения пищевых продуктов.
Оловянные покрытия можно наносить горячим и электрохимическим способами. Химическая стойкость покрытий, полученных электролитически, и их защитные свойства ниже покрытий, полученных горячим способом. Этим и объясняется тот факт, что лужение хозяйственных предметов, предназначенных для изготовления и хранения пищевых продуктов (мясорубки, котлы для варки пищи, молочные бидоны, чайники, самовары и т. д.) производится горячим способом.
Лужение применяется также для приготовления деталей приборов, механизмов и электролитических контактов под пайку, для предохранения электрических контактов от окисления, медных проводов от действия серы в случае вулканизации резиновой оболочки, для притирки. В последнее время лужение находит широкое применение для декоративной отделки различных приборов бытового назначения и предметов хозяйственного обихода методом «кристаллит».
Ниже приведен распространенный состав электролитов для лужения:
сернокислое олово .......... 50 г/л
серная кислота ............ 50 »
сернокислый натрий.......... 50 »
крезол или фенол........... 10 »
клей столярный............ 2 »
Режим работы: плотность тока Dк =1,2 а/дм2, температура электролита не выше 25° С.
При нормальной работе осадки олова на катоде получаются плотными, гладкими и светлыми.
Кристаллит. В последнее время для декоративной отделки предметов бытового назначения и хозяйственного обихода находит широкое применение новый вид лужения с последующей отделкой, названной его автором А. П. Эйчисом кристаллитом.
Это покрытие основано на способности тонких пленок олова, при определенных режимах их получения и обработки, образовывать очень красивую кристаллическую текстуру, напоминающую перламутр или «мороз». Если поверхность с таким узором покрыть бесцветным лаком, то узоры становятся значительно рельефнее и красивее. Подкрашивая бесцветный лак различными светостойкими красителями или окрашивая поверхность изделий электрохимически в специальном медном электролите, можно получить любую окраску узоров с различными переливами и оттенками. [6]
Железо, осажденное из электролита, имеет удельный вес 7,7 г/см2
, температуру плавления 1534° С. Осаждение железа обычно производят из электролитов, содержащих двухвалентное железо, для которого нормальный потенциал равен —0,44 в, электрохимический эквивалент 1,042 г/а·ч. Твердость покрытий без термообработки находится в пределах НВ 150—400 и зависит от режима осаждения и состава электролита.
Электролитическое осаждение железа применяется только для специальных целей и осуществляется относительно редко. Железо, полученное электролитически, благодаря своей химической чистоте и однородности, менее подвержено коррозии, но все же не может служить защитным покрытием и материалом для декоративной отделки.
Вместе с тем железо, обладая большим сопротивлением механическому износу, удлиняет срок службы покрываемых объектов, благодаря чему железнение находит применение на авторемонтных заводах и других предприятиях для восстановления размеров деталей грузовых автомашин, сельскохозяйственных машин, двигателей внутреннего сгорания судового типа и т. д.
Наибольшее распространение железнение получило в полиграфической промышленности для увеличения срока службы медных клише или печатных досок, предохраняя их от действия красок на медь.
Некоторое применение находит железнение для покрытия железом чугунных изделий перед горячим лужением и цинкованием, так как электролитически осажденное железо способствует лучшему сцеплению основного металла с покрытием.
Для железнения применяют сернокислые и хлористые электролиты. Эти электролиты подразделяются на холодные и горячие.
Сернокислые холодные электролиты железнения дают осадки железа повышенной твердости и хрупкости, хлористые горячие электролиты — осадки мягкие и пластичные, близкие по своим механическим характеристикам к меди. [10]
Скорость осаждения железа зависит от температуры электролита; в холодных электролитах осадки образуются медленно из-за низкой плотности тока, не превышающей Dк =0,1 / 0,2 а/дм2. В горячих электролитах плотность тока достигает Dк = 5 / 20 а/дм2, что обеспечивает за короткий срок относительно толстые осадки железа.
В полиграфической промышленности находят применение сернокислые электролиты следующего состава:
железный купорос......... 150—200 г/л
хлористый натрий........ 40—50 »
Режим работы: плотность тока Dк = 0,10 / 0,25 а/дм2, температура 15—25° С, кислотность рН = 5, выход по току 95—98%.
Свинец — мягкий металл серого цвета. Атомный вес свинца 207,22, удельный вес 11,9 г/см3, температура плавления 327° С. Нормальный потенциал свинца — 0,136 в.
Электролитическое свинцевание широкого применения в промышленности не имеет и применяется только для специальных целей. Объясняется это тем, что нанесение гальваническим путем толстых слоев свинца затруднительно, в то же время нанесение толстых слоев свинца необходимо в виду мягкости этого металла.
Свинцовые покрытия до недавнего времени наносили в основном горячим способом — методом окунания или наплавкой на поверхность металла. Горячий способ при всех его преимуществах (получение толстых покрытий за относительно короткий срок) обладает существенным недостатком: благодаря наличию примесей в свинце (в основном олова) за счет лужения поверхности перед свинцеванием, химическая стойкость покрытия значительно ниже стойкости покрытия свинцом гальваническим способом, при котором свинец в покрытии находится в химически чистом состоянии. Наибольшее применение свинцовые покрытия, отличающиеся высокой химической стойкостью, находят для предохранения металла от действия серной кислоты, сернистых газов и других сернистых соединений. Для этих целей свинцом покрывают химическую аппаратуру, металлические конструкции химических цехов и т. д.
Электролитическое свинцевание находит применение при изготовлении рентгеновских приборов и аппаратуры, поскольку свинцовое покрытие не пропускает рентгеновские лучи, тем самым защищает обслуживающий персонал от вредного его воздействия.
Свинец не стоек к действию органических кислот (уксусная, щавелевая, молочная), в связи с чем не допускается соприкосновение свинца с пищевыми продуктами. Соли свинца ядовиты. [10]
Электролиты для электролитического свинцевания обычно изготовляют на основе борфтористоводородных или кремнефтористоводородных солей свинца. Соли борфтористоводородной и кремнефтористоводородной кислот обычно готовят на месте перед зарядкой гальванических ванн.
При изготовлении борфтористоводородных электролитов вначале готовят борфтористоводородную кислоту смешением плавиковой кислоты с борной кислотой в свинцовом или винипластовом баке. В бак заливают 80 г плавиковой кислоты (в пересчете на 100%-ную) на 1 л электролита и 62 г/л борной кислоты. При смешивании этих двух компонентов масса сильно разогревается, для ее охлаждения раствор охлаждают, разбавляя водой. Работу эту необходимо проводить под тягой. После получения борфтористоводородной кислоты приступают к приготовлению ее свинцовой соли растворением в этой кислоте основной углекислой соли свинца.
Кремнефтористоводородный электролит более дешев по сравнению в борфтористоводородным, но для покрытия стальных изделий требуется предварительный подслой меди.
В настоящее время рекомендуется фенолсульфоновый электролит, имеющий значительные преимущества по сравнению с двумя вышеприведенными: не дефицитен, не ядовит, следовательно, не требует установки дорогих вентиляционных устройств, транспортировка сырья удобнее, а стоимость его значительно ниже, чем для борфтористоводородных электролитов. Кроме того, этот электролит стабилен в эксплуатации и легко поддается корректировке.[2]
Электролитическим путем можно осаждать сплавы, если условие электролиза подобраны так, что допускают совместное осаждение двух, трех и более металлов с образованием сплава.
По своему назначению электрохимические покрытия сплавами подразделяются на следующие группы:
а) защитно-декоративные (цинк — кадмий, медь — олово, никель — кобальт, медь — цинк);
б) декоративные (золото — медь, золото — никель, золото — серебро и др.);
в) технические для улучшения приработки трущихся поверхностей (свинец — олово, свинец — олово — сурьма);
г) технические для улучшения сцепления металла с резиной (медь — цинк и др.).
Наибольшее промышленное значение приобретает осаждение латуни, бронзы, сплавов свинца с оловом, никеля с кобальтом и др. [11]
Латунь представляет собой сплав двух металлов: меди 60—80%, и цинка 40—20%. Удельный вес латуни около 8,5 г/см3
, она тверже меди. Электрохимический эквивалент латуни складывается из электрохимических эквивалентов меди и цинка в зависимости от их содержания. Латунирование применяется обычно как подслой при серебрении для улучшения сцепления резины со сталью при гуммировании, а также как декоративное покрытие (с последующим химическим окрашиванием и лакированием бесцветным лаком).
Приготовление латунного электролита аналогично приготовлению медного и цинкового цианистых электролитов.
При составлении электролита пользуются либо цианистыми солями меди и цинка, либо (чаще) сернокислыми солями этих металлов и цианистого калия. Если исходят из сернокислой меди, то сначала переводят ее в углекислую медь, которую затем растворяют в цианистом натрии или калии. Для приготовления комплексной цинковой соли берут окись цинка или пользуются свежеосажденным гидратом окиси цинка. Нормальные латунные покрытия начинают получаться после проработки электролита током со случайными катодами в течение 10—12 ч.
Следует иметь в виду, что в процессе латунирования медь вырабатывается в электролите быстрее, чем цинк. Большой избыток цианида или слишком высокая плотность тока ведут к вздутию и отслаиванию латуни, так же как и плохая подготовка поверхности к покрытию.
Из нецианистых электролитов для латунирования находят некоторое применение пирофосфорнокислые или щавелевокислые электролиты. [8]
В последнее время практическое применение находит новое гальваническое покрытие так называемая белая бронза, представляющее собой сплав, в состав которого входит 55% меди и 45% олова. По внешнему виду это покрытие напоминает серебро. Покрытие из белой бронзы является хорошим защитно-декоративным покрытием, легко полирующимся до блеска, который сохраняется продолжительное время. Стойкость белой бронзы против органических кислот позволяет ее применять для покрытия столовых приборов и ряда изделий домашнего обихода вместо серебра.
Осаждение белой бронзы производят из цианистого электролита такого состава:
медь (в виде медноцианистой соли) . 10—15 г/л
олово (в виде станната натрия) . . . 30—45 »
цианистый натрий (свободный) . . . 12—15 »
едкий натрий (свободный)...... 5—7 »
Режим работы: плотность тока Dк
= 2 / 3 а/дм2
, температура раствора 65—70° С, анодами служат медные и стальные пластины.
Наличие стальных анодов вместо оловянных необходимо для регулирования процесса электролиза (предупреждения образования двухвалентных ионов олова) и требует периодического добавления в электролит солей олова в виде станната натрия. Толщина покрытий колеблется от 10 до 20 мк. По твердости белая бронза уступает хрому, но превосходит никель. [2]
Получение покрытия в виде сплава олово — свинец типа припоя (ПОС) нашло в промышленности широкое применение для следующих целей: а) защиты металлических изделий от коррозии; б) в качестве покрытия, облегчающего пайку деталей; в) в качестве антифрикционного покрытия.
Для этих целей применяют обычно сплавы, содержащие 5—60% олова. Покрытие сплавом олово — свинец может быть получено из борфтористоводородных, кремнефтористоводородных и фенолсульфоновых электролитов. Состав борфтористоводородного электролита для осаждения сплава ПОС 40 следующий:
свинец (в пересчете на металл) . . . 45—50 г/л
олово (в пересчете на металл) .... 40—50 »
борфтористоводородная кислота . . . 40—75 »
борная кислота.......... 25—35 »
клей ............... 3 - 5 »
Режим работы: плотность тока на катоде Dк
= 0,8 / 1 а/дм2
, плотность тока на аноде Dи
= 1 / З а/дм2
, температура электролита 18—25 С.[5]
Гальванотехника - процесс получения на поверхности изделия или основы (формы) слоев металлов из растворов их солей под действием постоянного электрического тока.
Электролитический или гальванический метод нанесения металлических покрытий был разработан в середине XIX века, но не сразу получил сколько-нибудь значительное промышленное применение – этому препятствовало отсутствие мощных источников постоянного тока.
Сущность метода заключается в погружении покрываемых изделий в водный раствор электролита, главным компонентом которого являются соли или другие растворимые соединения – металлопокрытия. Покрываемые изделия контактируют с отрицательным полюсом источника постоянного тока, т.е. являются катодами.
Анодами обычно служат пластины или прутки из того металла, которыми покрывают изделия. Они контактируют с положительным полюсом источника постоянного тока и при прохождении электрического тока растворяются, компенсируя убыль ионов, разряжающихся на покрываемых изделиях.[7]
Наряду с электрохимическим методом катодного осаждения металлов широкое применение находят и анодные методы электрохимической обработки поверхности металлов. К ним следует отнести электрохимическое оксидирование, травление, полирование и др. Во всех анодных процессах происходит либо растворение металла, либо превращение поверхностного слоя металла в оксидный или другой слой.
Сделаем выводы по применению гальванотехники:
1) Применение металлических (гальванических) покрытий является одним из наиболее распространенных методов защиты изделий от коррозии в машиностроении и приборостроении. Качество металлических покрытий во многом определяет качество изделий, их долговечность, работоспособность и надежность в эксплуатации. Гальванические покрытия служат не только средством защиты от коррозии, но также и способом повышения износостойкости деталей, электропроводности и других важных свойств поверхности. Гальванические процессы осуществляются в цехах защитных покрытий, в которых трудятся десятки тысяч рабочих, техников и инженеров. Повышение технического уровня цехов защитных покрытий, внедрение современных технологических процессов и средств автоматизации будут способствовать повышению эффективности труда гальванотехников и значительному увеличению производительности труда.
2) Гальванические покрытия разделяют по назначению на три группы:
- защитные, применяемые для защиты деталей от коррозии в различных средах;
- защитно-декоративные, используемые в машиностроении для декоративной отделки деталей и защиты их от коррозии;
- специальные, применяемые для повышения износостойкости деталей машин и других целей.
3) Для подготовки поверхностей перед нанесением гальванических покрытий применяются различные способы:
Шлифование применяют для устранения царапин, забоин, рисок и других дефектов на поверхности деталей, а также для получения гладкой и ровной поверхности перед нанесением на нее защитно-декоративных покрытий.
Галтовка это разновидность шлифования и полирования, заключающийся в очистке и отделке поверхности мелких деталей насыпью для снятия заусенцев, окалины, неровностей и уменьшения шероховатости поверхности.
Химическое обезжиривание поверхности деталей перед нанесением гальванопокрытий, как правило, предшествует электрохимическому обезжириванию; в основном его применяют при наличии на деталях толстой жировой пленки. Химический способ удаления жиров основывается на взаимодействии с ними органических растворителей или растворов щелочей, приводящих к их растворению, омылению или образованию эмульсий
Активация обязательная операция предназначена для удаления тончайших окисных пленок с поверхности деталей. Ее проводят между процессами обезжиривания и нанесения металлопокрытий.
Электрохимический способ травления металлов значительно ускоряет процесс очистки как за счет обильно выделяющегося на деталях газа, так и в результате химического и электрохимического растворения окислов и металла.
Цель промывки — не только тщательно удалить с поверхности изделий растворы и продукты от предыдущей операции, но и при экономном расходе воды обеспечить их минимальное попадание в сточные воды.
4) Для проведения процесса подготовки изделий к покрытию применяют в основном стационарные ванны. Обезжиривание изделий химическим и электрохимическим путем проводят в сварных прямоугольных ваннах, изготовленных из 3— 5 мм листовой стали. Объем ванн зависит от размеров и количества обрабатываемых изделий и колеблется в пределах от 200 до 800 л. Ванны для обезжиривания в большинстве случаев снабжены подогревом и имеют специальные вентиляционные устройства, чаще всего выполненные в виде бортовых отсосов. Ванны для нанесения гальванических покрытий применяются в основном из железа и в случае необходимости выкладываются изнутри различными изоляционными материалами. Для щелочных и цианистых электролитов не требуется специальной обкладки ванн изнутри. Однако во всех случаях применение ванн, выложенных изнутри изолирующими материалами, имеет свои преимущества. Такие ванны не допускают утечки тока через корпус, на них не осаждается металл в процессе электролиза и не создаются дополнительные препятствия для равномерного распределения тока. Для кислых электролитов применяются железные ванны, выложенные изнутри различными стойкими материалами. B настоящее время широкое применение получили так называемые колокольные ванны, оказавшиеся наиболее экономичными в расходовании электролита и вместе с тем обеспечивающие сравнительно быстрое отложение нужного слоя покрытия на изделиях.
5) Увеличение мощностей действующих гальванических цехов в настоящее время осуществляется в результате механизации и автоматизации ручных и трудоемких процессов, замены ручного и механического полирования электролитическим, внедрения блестящих покрытий, не требующих дополнительного полирования, и всемерной интенсификации процесса электролитического осаждения металла.
Последний вопрос заслуживает особого внимания, так как он дает возможность значительно увеличить производительность гальванических цехов во многих случаях без больших материальных затрат, главным образом за счет внедрения быстродействующих электролитов. К тому же нередко, помимо интенсификации процесса электролитического выделения металла из такого электролита, удается получить блестящие металлические осадки, в результате чего может быть полностью или частично заменена последующая механическая обработка гальванического покрытия. Поэтому интенсификация гальванических процессов за счет применения быстродействующих электролитов должна находить все более широкое применение.
1. Б. Бертфаи. Справочник гальваностега. 1960;
2. Блащук Е.Ф., Лаворко П. К. Гальванотехника. 1961;
3. Вячеславов П. М., Волянюк Г. А., Электролитическое формование, Л., 1979;
4. Гальванические покрытия в машиностроении, под ред. М.А. Шлугера, т. 1, М., 1985. P.M. Вишолшрскис.;
5. Гальванотехника в приборостроении, под ред. A.M. Гинберга, М., 1977;
6. Гальванотехника для мастеров: Справ. изд./Вирбилис С. Пер. с польск./Под ред. А. Ф. Иванова. М.: Металлургия, 1990. 208 с.;
7. Кудрявцев Н. Т., Электролитические покрытия металлами, М., 1979;
8. Лайнер В.И. Современная гальванотехника. М.: «Металлургия», 1967;
9. Одноралов Н. В. Занимательная гальванотехника: Пособие для учащихся. — 3-е изд. — М.: Просвещение, 1979. — 106 с, ил.;
10. Химическая энциклопедия: В 5т.:т.1:А – Дорзано/ Ред-кол.: Кнунянц И.Л.(гл.ред.) и др.- М.:Советская энциклопедия,1988. – 623с.:ил.
11. Ямпольский А.М. Ильин В.А. Краткий справочник гальванотехника. Л.: «Машиностроение», 1988;
|