СОДЕРЖАНИЕ
Введение 5
1. Геологическая часть 7
Общие сведения о шахтном поле 7
Геологическое строение шахтного поля 9
Качественная характеристика калийного горизонта 18
Промышленные и извлекаемые запасы проектируемого горизонта 20
1.5 Краткая геологическая характеристика проектируемого горизонта 22
2 Горная часть 23
2.1 Вскрытие и подготовка шахтного поля 23
2.2 Выбор системы разработки 27
2.3 Расчет числа работающих панелей и главных направлений 31
2.4 Расчет срока отработки проектируемого горизонта 32
3 Специальная часть 33
3.1 Краткая геологическая характеристика проектируемого участка 33
3.2 Выбор системы разработки и ее варианта для отработки выемочного пласта 34
3.3 Горно-подготовительные работы 37
3.3.1 Выбор способа проведения подготовительных выработок и проходческих горных машин 37
3.3.2 Выбор и обоснование формы и размеров поперечного сечения подготовительных выработок 40
3.3.3 Охрана и крепление подготовительных выработок 44
3.3.4 Схема подготовки выемочного участка, параметры системы 46
3.3.5 Технология подготовки панели 47
3.4 Очистные работы 48
3.4.1 Выбор горных машин и оборудования для ведения очистных работ 48
3.4.2 Расчёт размеров междукамерных целиков 49
3.4.3 Разделка и крепление камер разворота комбайна 50
3.4.4 Режим работы очистного забоя. Состав бригады и сменного звена 51
3.4.5 Технология ведения очистных работ 51
3.4.6 Расчёт производительности проходческо-очистного комплекса 52
3.5 Нормативное извлечение руды и полезного компонента по системе разработки 54
3.5.1 Расчет балансовых запасов и полезного компонента (КCl) панели 54
3.5.2 Расчет извлекаемых запасов руды в панели 55
3.5.3 Расчет извлекаемых запасов полезного компонента (KCl) панели 57
4 Проветривание панели 59
4.1 Расчет количества воздуха, необходимого для проветривания лавы 59
4.1.1 Расчет количества воздуха, необходимого для проветривания камер 59
4.1.2 Выбор вентилятора местного проветривания и места его установки 61
4.2 Расчет количества воздуха, необходимого для проветривания панели 62
5. Участковый транспорт 63
5.1 Транспортирование руды от очистного забоя до выработок главного направления 63
5.2 Перевозка людей, оборудования и материалов по горным
выработкам 63
6. Экономическая часть 66
6.1 Организация работ на участке 66
6.2 Расчет затрат на основные и вспомогательные материалы,
используемые при эксплуатации оборудования 68
6.3 Расчет затрат на электроэнергию 70
6.4 Расчет затрат на амортизацию оборудования 72
6.5 Расчет заработанной платы и отчислений от фонда оплаты труда 73
6.6 Составление сметы затрат 78
6.7 Расчет себестоимости добычи 1т руды 79
7. Охрана труда и экологичность проектных решений 81
7.1 Требования правил технической безопасности (ПТБ) к устройству выходов из очистных забоев 81
7.2 Требования ПТБ к забойным машинам и комплексам 83
7.3 Меры по безопасности труда при подготовке забойного
оборудования к работе, во время работы по выемке руды, при
эксплуатации гидромеханизированной крепи и скребковых
конвейеров 85
7.4 Контроль за составом рудничной атмосферы и содержанием
горючих газов 94
7.5 Требования ПТБ при разработке пластов, опасных по
газодинамическим явлениям (ГДЯ) 96
Литература 102
ВВЕДЕНИЕ
Старобинское месторождение калийных солей открыто в 1949 году Белорусcким геологическим управлением. Геологоразведочные работы проводились в 1949 - 1952 и 1958 - 1961 годах.
В 1962 году был введен в эксплуатацию Первый калийный комбинат. В настоящее время добыча калийных солей ведется 4-мя рудоуправлениями на 4-х шахтных полях.
Добыча минеральных солей и продуктов их переработки непрерывно возрастает как на мировом уровне в целом, так и в отдельных странах.
Одной из важнейших задач сегодня и в перспективе на будущее является необходимость развития производства и полного обеспечения потребности народного хозяйства в минеральных удобрениях.
Каждый килограмм калийных удобрений, внесенных в почву, позволяет дополнительно получить до 5кг зерна, 50кг картофеля, 40кг сахарной свеклы, 20кг томатов, 2кг хлопка-сырца.
Ежегодно необходимо вносить в почву 40-200кг калийных удобрений на 1га посевных площадей для восполнения питательных веществ. Поэтому потребность в калийных удобрениях очень велика, а, следовательно, и добыча калийных руд.
Более 95% всех калийных солей добывается шахтным способом на двух месторождениях: Старобинском и Верхнекамском.
Жёсткая конкуренция на рынках сбыта заставляет искать новые организационные подходы к проблеме реализации продукции. Созданная калийными предприятиями Беларуси и России Международная калийная компания успешно работает в этом направлении. Удалось преодолеть сложности на мировом рынке, связанные с дисбалансом между производственными мощностями и реальным производством, определяемым спросом на калийную продукцию.
Постоянно наращиваются объемы выпуска пользующейся спросом вновь освоенной на предприятиях объединения продукции: обеспыленых мелкозернистых калийных удобрений, пищевой и кормовой соли, полностью удовлетворяется потребность населения в высококачественных удобрениях, выпускаемых в расфасованном виде. Одним ив важнейших условий увеличения добычи руды является эффективное использование оборудования.
Для горнодобывающих отраслей промышленности особую актуальность приобретают создание и внедрение машин и агрегатов высокого технического уровня, обладающих значительной производительностью, большой единичной мощностью при одновременном уменьшении их габаритов, снижение металлоемкости, энергопотребления на единицу конечного продукта и повышения надежности и долговечности.
Создание современных машин высокого технического уровня предполагает использование новых прогрессивных методов проектирования, отказ от большинства традиционных методов расчета и широкое применение при конструировании современных ЭВМ.
Анализ горно-геологических условий калийных месторождений и горнотехнических условий добычи калийных руд, а также учет состояния и тенденции развития горного машиностроения позволили определить форму такого перехода, а именно: выемка комбайновыми комплексами на базе машин большой единичной мощности.
Широкое внедрение усовершенствованного оборудования в перспективе позволит значительно улучшить качество добываемой руды, повысить безопасность работ, снизить объемы отходов производства, уменьшить негативные последствия оседания земной поверхности, повысить извлечение полезного ископаемого из недр и др.
Внедрению в производство перспективной технологии селективной выемки калийных пластов Третьего калийного горизонта на полную мощность с закладкой выработанного пространства посвящена данная работа.
1 ГЕОЛОГИЧЕСКАЯ ЧАСТЬ
1.1 ОБЩИЕ СВЕДЕНИЯ О ШАХТНОМ ПОЛЕ
Старобинское калийное месторождение калийных солей расположено в пределах Солигорского, Любанского и Слуцкого района Минской области РБ. Площадь месторождения около 350км2
.
Открыто месторождение в 1949 году Белорусским геологическим управлением. Геологоразведочные работы проводились в 1949-1952 и 1958-1961 годах.
В 1962 году был введен в эксплуатацию Первый калийный комбинат. В настоящее время добыча калийных солей ведется 4-мя рудоуправлениями на 4-х шахтных полях.
В связи с освоением Старобинского месторождения в 135км к югу от столицы Республики Беларусь г. Минска построен промышленный центр по выпуску калийных удобрений г. Солигорск. В 8км от него на юго-запад расположен г.п. Старобин, в 40км к востоку - районный центр г.Любань, в 35км на север - г.Слуцк. Со всеми вышеназванными населенными пунктами г.Солигорск связан асфальтированным шоссе. Территория месторождения покрыта густой сетью грунтовых дорог.
В Центральной части территории месторождения расположена станция «КАЛИЙ» Белорусской железной дороги, построенная у Первого Солигорского калийного комбината, которая связана железнодорожной веткой се станцией г.Слуцк. Через последнюю проходит железная дорога, соединяющая два крупных железнодорожных узла Барановичи и Осиповичи, первый из которых находится на магистральном пути Москва-Брест, а второй - Вильнюс-Киев.
В г.Солигорске, помимо объектов горнохимической индустрии, расположенных на 4-х рудоуправлениях ПО «Беларуськалий», имеются: завод железобетонных конструкций, завод по ремонту горного оборудования, ряд строительных организаций, предприятия легкой и пищевой промышленности.
Промышленные предприятия и населенные пункты получают электроэнергию от общей кольцевой энергетической системы Европейской части бывшего СССР.
Водоснабжение населения и промышленных предприятий осуществляется скважинами и колодцами, эксплуатирующими подземные воды девонских и четвертичных отложений.
На площади залегания калийных солей имеются месторождения строительных материалов (песчано-гравийный материал, строительные пески и другие), часть которых в настоящее время разрабатывается.
В геоморфологическом отношении месторождение лежит в пределах северного окончания Припятской впадины Полесья. Рельеф района месторождения равнинный. Лишь в северной части встречаются холмообразные возвышенности конечно-моренных гряд. Абсолютные отметки земной поверхности изменяются от +137.9 до +173.2м.
Климат района умеренно-континентальный. Среднемесячная температура воздуха колеблется от -5.9 (январь) до +18.2 градусов по Цельсию (июль). Минимальная температура воздуха равна, -37.4 градусов по Цельсию (январь), максимальная +36.2 градусов по Цельсию (июль).
Средняя глубина промерзания почвы в районе месторождения колеблется в зависимости от характера зимы от 0.2 до 0.75м, в отдельные годы-в морозные и малоснежные зимы глубина промерзания достигает 2м. Продолжительность зимнего периода 5 месяцев.
Лето характеризуется умеренной температурой, обильными осадками. Среднемесячная температура самого теплого месяца июля +18 градусов по Цельсию. Среднегодовое количество атмосферных осадков колеблется от 506 до 680 мм, около 70–75 % которых приходится на период с апреля по октябрь.
Преобладающее направление ветров юго-западное, скорость ветра обычно равна 2.9–6.6 м/сек.
На площади месторождения широко развита гидросеть, состоящая из мелких ручьев и мелиоративных каналов. Наиболее крупные из рек – Случь и Морочь.
На реке Случь в районе г.Солигорска создано крупное водохранилище, служащее источником технического водоснабжения предприятий города.
Шахтное поле 1РУ расположено в юго-западной части Старобинского месторождения калийных солей. На западе, севере и востоке граничит с шахтными полями 2, 3 и 4 РУ. На юге граница шахтного поля совпадает с границей распространения Третьего калийного горизонта.
1.2 ГЕОЛОГИЧЕСКОЕ СТРОЕНИЕ ШАХТНОГО
ПОЛЯ
В геологическом строении шахтного поля принимают участие сложнодислоцированные комплексы кристаллического фундамента и осадочный чехол.
Кристаллический фундамент архейско-нижнепротерозойского возраста залегает на глубине 1600 ÷ 2400м. Породы представлены гранитами гранодиоритами и гнейсами. Осадочный чехол залегает на поверхности кристаллического фундамента с угловым и стратиграфическим несогласием. В составе чехлы выделяются отложения верхнего протерозоя, палеозоя, мезозоя и кайнозоя.
Верхний протерозой представлен вендским и рифейским комплексами, в составе которых преобладают песчаники, глины и тиллиты. Мощность отложений верхнего протерозоя составляет 350 ÷ 400м.
В составе палеозойской группы выделяют средний и верхний девон. Отложения среднего девона представлены образованиями наровского горизонта эйфельского яруса и старооскольского горизонта живетского яруса.
Наровский горизонт слагают глинисто-карбонатные породы, мощностью 55 ÷ 96м, а старооскольский – песчаные и глинистые породы изредко с прослоями доломита в подошве, мощностью 129 ÷ 170м.
В составе верхнего девона выделяются отложения франского и фаменского яруса.
Для отложений франского яруса характерен глинисто-карбонатный тип разреза мощностью до 230м. В верхней части яруса распространены сульфатно-карбонатные породы (гипсы, ангидриты, доломиты) относящиеся к нижней соленосной толще.
По литологическим особенностям и положению в разрезе отложения фаменского яруса подразделяються на три толщи: межсолевую, верхнюю соленосную, надсолевую.
Межсолевая толща представляет собой мощную (до 185м) глинисто карбонатную пачку.
Верхняя соленосная толща, мощностью до 1500м, по особенностям литологического состава слагающих её парод подразделяется на нижнюю – галитовую и верхнюю – глинисто-галитовую или калиеносную подтолщи.
Галитовая подтолща представлена найдовскими слоями оресского горизонта, сложенными светло-серой или белой каменной солью с маломощными не солевыми прослоями преимущественно сульфатно-карбонатного состава.
На отложениях галитовой подтолщи залегает калиеносная подтолща. Подтолща представляет собой мощную (до 600м), пространственно протяжённую пластовую залежь, выклинивающуюся на юге и юго-западе. Строений подтолщи характеризуется чередованием пачек соляных и не соляных пород. К соляным пачкам приурочены калийные горизонты.
На шахтном поле, в составе подтолщи, известны четыре калийных горизонта, из которых в настоящее время эксплуатируются два: Первый и Третий. Второй калийный горизонт практически отработан за исключением остаточных объёмов, законсервированных в охранных целиках главных направлений и околоствольного двора.
Надсолевая глинисто-мергелистая толща (ГМТ) залегает без перерыва на соленосных отложениях. Контакт с нижележащей толщей обусловлен процессами древнего подземного выщелачивания. По литологическому составу ГМТ колеблется в пределах 230 ÷ 320м и зависит от структурного положения участка.
В центральной части шахтного поля она, как правило, минимальна, а на флангах, вблизи, контура выклинивания - максимальна.
В составе мезозойской группы выделяются юрские и меловые отложения.
Юрские отложения распространены спародически и представлены чередованием серых слюдистых и песчаных глин с прослоями и линзами песков, обогащённых растительными остатками.
Отложения меловой системы развиты повсеместно и представлены преимущественно пищим мелом.
В составе кайнозойской группы выделяются отложения палеогеновой, неогеновой и четвертичной системы, которые представлены песчано-глинистыми пародами мощностью 50 ÷ 80м.
Старобинское месторождение калийных солей приурочено к северо-западной центриклинальной части Припятского прогиба в пределах Червонослабодской тектонической ступени.
Особенности геологического строения этой территории обусловлены наличием и развитием обрамляющих её региональных разломов.
Кристаллический фундамент на площади месторождения разбит на ряд блоков, наклонённых на северо-восток и ступенчато погружающихся в восточном направлении. Нижние структурные этажи осадочного чехла наследуют структурные элементы поверхности фундамента. Ведущей в строении этих этажей является разрывная тектоника.
На месторождении выявлен ряд субширотных и субмеридиальных блокообразующих тектонических нарушений, которые представляют собой систему ступенчатых сбросов с суммарной амплитудой 20 ÷ 400м. Амплитуды от нижележащих к вышележащим отложениям постепенно затухают.
Шахтное поле 1РУ расположено в пределах центрального тектонического блока отделенного от восточного блока Центральным тектоническим нарушением.
Центральное тектоническое нарушение имеет субмеридиальное простирание и является нормальным сбросом, плоскость сместителя которого наклонена на юго-восток. Угол падения сместителя составляет не мене 60˚. Установленная амплитуда разлома на уровне Третьего калийного горизонта составляет 80 ÷ 100м. Вверх по разрезу амплитуда разлома уменьшается и на уровне Второго калийного горизонта составляет 65м. Общая ширина нарушенной зоны составляет 30 ÷ 35м и сложена блоками пород с соляными брекчиями на их контактах. В лежачем боку образуются подразломные антиклинали, а в висячем – приразломные синклинали. Вдоль тектонического нарушения развиваются зоны замещений сильвинитов каменной солью.
На юге шахтного поля геофизическими исследованиями выявлены тектонические нарушения субширотного простирания, которые группируются в тектоническую зону – Южное тектоническое нарушение. Расположена она в основном за пределами площади распространения калийных горизонтов. Возможно, она контролирует распространение соленосных отложений.
В пределах шахтного поля имеет место несоответствие структурных планов поверхности соленосной толщи и калийных горизонтов. С приближением к границам выклинивания глубина залегания соляного зеркала увеличивается, а калийных горизонтов уменьшается. Поверхность соленосной толщи образует инверсионную структуру, формирование которой связано с процессами древнего подземного выщелачивания, активно протекавшего в краевых частях соленосных отложений и в зонах разрывных нарушений. Выщелачиванию здесь подвергнуты и калийные горизонты, залегающие вблизи кровли соленосной толщи. Остатки их прослеживаются в низах ГМТ в виде серии гематитовых прослойков.
При ведении горных работ в подземных выработках встречено большое количество трещин тектонического генезиса секущих калийные горизонты. Трещины преимущественно вертикальные, смещение пород по ним отсутствует. Исследованиями установлено две системы таких трещин, согласующихся по простиранию с региональными разломами, обрамляющими месторождение.
В пределах шахтного поля 1РУ Развиты четыре калийных горизонта: Первый, Второй, Третий и Четвёртый (сверху в низ). Залегают они внутри мощных пачек каменной соли. Представляют собой пластовые залежи, полого падающие в северо-восточном направлении под углом 1 ÷ 3˚, осложнённые складками и разрывами на участках примыкающих к Центральному и Южному тектоническим нарушениям, в зонах замещения, а также в непосредственной близости от контура выклинивания.
Из 4-х калийных горизонтов в настоящее время разрабатывается Первый горизонт и нижний сильвинитовый пласт Третьего калийного горизонта. На Первом калийном горизонте ведутся подземные геологоразведочные и опытнопромышленные работы. Запасы Первого калийного горизонта поставлены на баланс в 2007г. Запасы верхнего сильвинитового пласта Третьего горизонта и продуктивного пласта, выделяемого в разрезе Четвёртого горизонта, являются в настоящее время некандиционными и отнесены к забалансовым. Основной причиной некондиционности руд является повышенное содержание НО и MgCL2.
Южная граница распространения Первого, Второго и Третьего калийных горизонтов постседиментационную природу и её сложная конфигурация обусловлена процессами древнего подземного выщелачивания. В результате сочетания тектонических процессов и подземного выщелачивания протекавших в постседиментационный период в южной краевой зоне Третьего калийного горизонта сформировался Листопадовичский структурный выступ. Выступ распространяется на расстояние до 6 км в запад-северо-западном направлении при минимальной ширине 1км и отделён от основной части месторождения узким заливом шириной 0,5 ÷ 2км.
Первый калийный горизонт приурочен к 29-ой соляной пачке. Распрстранён в центральной и северной части шахтного поля. Развит в основном в осевых частях синклинальных структур субширотного простирания. Глубина залегания кровли горизонта 352 ÷ 451м. На северо-восток происходит постепенное погружение кровли горизонта. Горизонт состоит из 5-ти сильвинитовых прослоев, разделенных прослоями каменной соли и глины. Окраска сильвинитов – красная, различных тонов и оттенков. Характерная особенность строения пласта в сосредоточении глин преимущественно в межслолевой каменной соли в виде прослоев мощностью от нескольких мм до 30 см. Глинистые прослои в сильвинитовых слоях редко превышают 4мм, составляя преимущественно 2 – 3мм.
Калийный горизонт можно условно разделить на 3 пачки: верхнюю сильвинитовую, среднюю глинисто-галитовую и нижнюю сильвинитовую. Верхняя пачка включает слои 3; 3-4; 4; 4-5; 5 и имеет мощность 2,24м. Средняя пачка (слой 2-3) имеет мощность 2м. Нижняя пачка состоит из слоёв 1; 1-2; 2 и имеет мощность 1,38м. Средняя мощность горизонта составляет 5,62м, содержание KCL – 18,89%, НО – 20,20%.
Наиболее перспективной для освоения является верхняя сильвинитовая пачка. В настоящее время, запасы верхней сильвинитовой пачки, из забалансовых переведены в балансовые, ведутся работы по её селективной выемке столбовой системой разработки, а также геолого-разведочные работы по установлению контура границы выклинивания пласта в Южной краевой зоне (1-ая западная панель) и отработка камерной системой разработки участков примыкания к границе выклинивания.
Мощность верхней пачки изменяется от 1,91м до 2,55м при общей тенденции к уменьшению в северо-восточном направлении. Содержание KCL колеблется от 15,03% до 37,87%, содержание нерастворимого остатка (НО) – от 10,01% до 29,19%.
Второй калийный горизонт в пределах шахтного поля распространён повсеместно. По положению в разрезе соленосной толщи, приурочен к 25-ой соляной пачке.
Условия залегания горизонта в границах шахтного поля соответствуют общей конфигурации соляной толщи всего месторождения, а именно: в южном направлении наблюдается повышение гипсометрического уровня (абсолютная отметка подошвы -245м), а в северо-восточной части калийная залежь полого погружается на северо-восток под углом 1 - 3˚(абсолютная отметка подошвы пласта -325м).
Горизонт представляет собой единый продуктивный пласт, мощность которого составляет в среднем 2,36м. Он подразделяется на три слоя: верхний, средний и нижний.
Верхний слой состоит из чередующихся прослоев сильвинита и каменной соли мощностью от нескольких до десятков сантиметров. Мощность слоя в среднем составляет 0,81, содержание KCL – 39,10%, содержание НО – 4,62%.
Средний слой представлен каменной солью с редкой вкрапленностью сильвинита и глинистыми прослоями. Мощность слоя в среднем составляет 0,59м, содержание KCL – 4,23%, содержание НО – 6,34%.
Нижний слой представлен чередованием прослоев сильвинита, каменной соли и глины. Мощность слоя в среднем составляет 0,96м, содержание KCL – 41,81%, содержание НО – 2,96%.
Для горизонта характерны локальные замещения сильвинитовых слоёв каменной солью. Закономерностей в расположении зон замещений не установлено. В настоящее время запасы горизонта практически полностью погашены. Остатки запасов расположены в охранных целиках под промплощадку и выработки, вскрывающие первый калийный горизонт.
Между Вторым и Третьим калийными горизонтами залегает мощная толща каменной соли переслаивающейся глинистыми, глинисто-мергелистыми, мергелисто-доломитными пачками. Здесь выделено два галитовых пласта представляющих промышленный интерес.
Второй соляной пласт (-280м) приурочен к 25-ой соляной пачке и залегает ниже подошвы Второго калийного горизонта в интервале 0,0 ÷ 17,5м. Абсолютные отметки подошвы пласта в юго-западной части составляют – 237,6м, в северо-восточной части составляют – 372,14м. Пласт сложен чередованием сезонных прослоев каменной соли, мощностью 5 ÷ 30см и галопелитов, мощностью от нескольких мм до 15 ÷ 20см. Соль каменная серая, оранжево-серая, тёмно-серая, мелко-среднезернистая со следами первичной кристаллизации, в различной степени загрязнена глинистым материалом. В пласте выделено 9 слоёв (1-9 сверху вниз) различных по мощности и содержанию полезных компонентов и вредных примесей. Содержание NaCL по слоям изменяется от 56,51% до 98,24%, НО – от 0,84% до 37,5%. Опытные работы показали, что при отработке пласта возможно получение только технической соли.
Третий соляной пласт (-305) приурочен к 23-ей соляной пачке и залегает ниже подошвы Второго калийного горизонта в интервале23,2 ÷ 32,6м. Абсолютные отметки подошвы пласта в юго-западной части составляют - -258,5м, в северо-восточной - -396,1м.Пласт средней мощностью 9,22м сложен чередованием прослоев каменной соли мощностью 5 ÷ 45см и галопелитов мощностью от нескольких мм до 5 ÷ 10см. Соль каменная, от светло-серой до тёмно-серой, мелко-среднезернистая со следами первичной кристаллизации, в различной степени загрязнена глинистым материалом. В пласте выделено 5 слоёв: 10; 11; Б1
; С1
; Б2
(сверху вниз). Содержание NaCL по слоям изменяется от 86,73% до 99,09%, нерастворимый остаток НО - от 0,29% до 11,05%. По результатам геологоразведочных и опытно-промышленных работ слои Б1
, С1
, Б2
суммарной средней мощностью 3,57м предусмотрены к отработке для получения технической каменной соли марки А (валовая выемка) и каменной соли пищевых сортов (селективная выемка). Содержание NaCL в этих слоях составляет 98,19% ÷ 98,98%, НО – 0,42% ÷ 0,77%.
Разделяются названные соляные пласты глинисто-карбонатной пачкой мощностью 6,0-6,5м.
Третий калийный горизонт (-430м) приурочен к 13-ой соляной пачке. В пределах шахтного поля распространён повсеместно.
Абсолютные отметки подошвы пласта составляют в южной части -300м, в северо-восточном направлении пласт погружается до -520м.
Горизонт имеет трёхслойное строение и подразделяется на три пачки (сверху вниз): верхнюю сильвинитовую, среднюю глинисто-карнолитовую, нижнюю карнолитовую.
Верхняя сильвинитовая пачка представляет собой горизонтальное переслаивание сильвинита, а иногда сильвинито-карнолитовой породы и каменной соли. Мощность сильвинитовых прослоев колеблется от 0,15м до 0,30м, прослои каменной соли имеют мощность от 0,30м до 0,60м.
Мощность верхней сильвинитовой пачки изменяется от 1,5м (скв.23) до 4,45м (скв.1). Среднее содержание KCL – 17%, НО – 5,45%. Запасы верхней сильвинитовой пачки отнесены к забалансовым.
Средняя глинисто-карнолитовая пачка состоит из чередующихся прослоев глины, карнолитовых, сильвинито-карнолитовых пород и каменной соли. Прослои глины и карнолитовой породы сосредоточены главным образом в средней части пачки. Мощность прослоев глины колеблется от 1-2см до 35см, карнолита – от нескольких сантиметров до 0,65м.
Мощность средней глинисто-карнолитовой пачки изменяется от 4,45м (скв.26) до 16,7м (скв.5).
В разрезе нижней сильвинитовой пачки, состоящей из чередующихся прослоев сильвинита и каменной соли, выделено 6 сильвинитовых слоёв (1-6 снизу вверх). Мощность сильвинитовых слоёв изменяется от 0,15м до 1,30м, разделяющей их каменной соли – от 0,50м до 1,35м. На балансе предприятия стоят запасы сильвинитовых слоёв 2-4.
Нижняя сильвинитовая пачка Третьего калийного горизонта является основным рабочим пластом. Мощность этой пачки колеблется от 2,0м (скв.5) до 9,05м (скв.13).Среднее содержание KCL – 21,5%, НО – 6,67%.
Подстилающие горизонт породы представлены каменной солью с глинистыми прослоями от 1мм до 5 ÷ 7см мощностью около 6м. Ниже залегают породы 12-ой глинисто-карбонатной пачки.
Четвёртый калийный горизонт приурочен к 7-ой соляной пачке. Подстилается и перекрывается горизонт довольно мощными пластами каменной соли. В пределах Старобинского месторождения он является самым нижним из всех калийных горизонтов. Границы его распространения на шахтном поле почти совпадают с границей распространения Третьего калийного горизонта.
Кровля Четвёртого калийного горизонта залегает на глубинах 520 ÷ 870м от поверхности земли и в 160 ÷ 200м от почвы третьего калийного горизонта. Общая тенденция погружения – на восток.
Мощность горизонта изменяется в широких пределах от 1 ÷ 1,5м на юге (область его седиментационного выклинивания) до 5 ÷ 6м на севере и северо-востоке шахтного поля.
Разрез Четвёртого калийного горизонта представлен ритмичным чередованием прослоев сильвинита, каменной соли и галопелитов. Имеется довольно большое количество мощных (от 2 до 10см, реже15 ÷ 20см, в отдельных случаях до 60 ÷ 90см) прослоев галопелитов. Более мощные галопелитовые прослои обычно находятся в основании ритмов. Общая тенденция к увеличению глинистости разреза отмечается с юга на север и северо-восток. Каменная соль горизонта представлена прослоями от 1 ÷ 2 до 8 ÷ 10см, чаще 3 ÷ 8см, окрашенными в красный, жёлтый и оранжевый цвета различных оттенков. В южной и юго-восточной частях площади распространения горизонта появляются светлоокрашенные разности каменной соли.
Мощность прослоев сильвинитов изменяется от 0,5 ÷ 1,0 до 7 ÷ 10см, составляя в среднем 1 ÷ 5см. Для них характерна красная окраска различных оттенков. Довольно широко распространён и молочно-белый сильвинит. Сближенные группы сильвинитовых прослоев слагают сильвинитовые слои. В полном разрезе горизонта выделяют до 18 сильвинитовых слоёв. В пределах шахтного поля распространены до 10 слоёв.
Несмотря на незначительную мощность горизонта и его повсеместное площадное распространение, в нём выделены, лишь 2-а продуктивных пласта.
Основу продуктивных пластов Четвёртого калийного горизонта составляют сильвинитовые слои 6, 7, 8 (нижний продуктивный пласт) и слой 10 (верхний продуктивный пласт). Расстояние между продуктивными пластами по вертикали 3м.
Нижний продуктивный пласт развит только в северной части шахтного поля. Общая мощность пласта изменяется от 1,4 до 2,7м. Средняя суммарная мощность сильвинитовых прослоев 6, 7 и 8,включенных в подсчёт запасов, составляет 1,18 м. Содержание KCL в них составляет 36,20%, MgCL2
– 0.04%, НО – 3,32%.
Верхний продуктивный пласт имеет ограниченное распространение в крайней северной точке шахтного поля. Мощность его составляет 0,13м. Содержание KCL – 49,61%, НО – 0,96%.
Разрабатываемые пласты и вмещающие породы Старобинского месторождения содержат в свободном и связном (микровключённом и сорбированном) виде природные газы,в состав которых входят: азот, мета, тяжёлые углеводороды, оксид и диоксид углерода и др. Газы в породах находятся в виде очаговых (гнездовых) и межслоевых скоплений, а также в микровключённом состоянии. Давление газов в очаговых скоплениях достигает 9МПа. Распределение газов, их количество и качественный состав в пределах шахтного поля, панелей, блоков крайне неравномерно и носит зональный характер. Общая газоносность пород в выбросоопасных зонах достигает 1,3м3
/м3
. Газоносность пород Третьего горизонта по горючим газам составляет в среднем 0,2м3
/м3
породы, пород Первого и Второго горизонтов – 0,1м3
/м3
породы.
К выбросоопасным отнесён Третий калийный горизонт, включающий нижнюю промышленную пачку, среднюю глинисто-карнолитовую пачку и верхнюю забалансовую сильвинитовую пачку.
При отработке калийных пластов на шахтном поле имеют место газодинамические явления в виде: внезапных выбросов соли и газа; обрушений пород кровли, сопровождающихся газовыделениями; отжима призабойной части пород, сопровождающегося звуковыми эффектами, иногда разрушением и выносом разрушенной породы в выработку.
Указанные явления могут происходить как в момент проведения выработки и отбойки руды в лаве, так и после этого, причём,они могут иметь место в призабойном пространстве и вне его (запоздалые ГДЯ).
Большинство ГДЯ связано с разрывными и складчатыми геологическими нарушениями в залегании калийных пластов (мульды, тектонические трещины и т.д.).
Старобинское месторождение расположено в краевой северо-западной части Припятского артезианского бассейна. В пределах месторождения различают:
- надсолевой водоносный комплекс в мезозойско-кайнозойских отложениях;
- подсолевой водоносный комплекс в породах девона и верхнего протерозоя.
Названные водоносные комплексы образуют верхний и нижний гидрогеологические этажи, которые разделены водоупорными породами глинисто-мергелистой и соленосной толщ.
Водоносный комплекс в мезозойско-кайнозойских отложениях мощностью 100-120м относится к зоне активного водообмена и подстилается регионально выдержанными водоупорными породами ГМГ. Воды его преимущественно пресные используются для хозяйственного питьевого водоснабжения.
Подсолевой водоносный комплекс общей мощностью около 1000м приурочен к карбонатным породам фаменского и франского ярусов верхнего девона, к терригенным породам среднего и верхнего протерозоя, разделенных относительно водоупорными породами ливенского, пашийско-кыновского и пярнуско-наровского горизонтов. Водовмещающие карбонатные породы верхнего девона характерезуются низкой водообильностью и плохой проницаемостью. Водоносные горизонты терригенных пород среднего девона и верхнего протерозоя включают хорошо проницаемые обводненные песчаники соответственно старооскольского возвраста и пинской свиты.
Надсолевой и подсолевой водоносные комплексы разделены породами ГМТ и соленосной толщ мощностью 500-1000м, служащих надежными водоупорами, обеспечивающими гидрогеологическую закрытость нижнего гидрогеологического этажа. Взаимосвязь вод надсолевого и подсолевого комплексов исключается как по площади месторождения, так и в зонах дизъюктивных нарушений, где породы соляных отложений крепко спаяны соляным цементом, безводны и водоупорны.
Верхняя часть осадочного чехла сложена проницаемыми породами, создающими благоприятные условия для инфильтрации атмосферных осадков и пополнения запасов подземных вод. Все водоносные горизонты этой части разреза гидравлически связаны между собой.
Воды подсолевого водоносного комплекса представлены преимущественно крепкими рассолами.
Водоносный горизонт песчаников пинской свиты мощностью 300-350м перекрыт слабопроницаемыми туфопесчаниками вулканогенно-осадочной толщи мощностью около 100м и подстилается породами кристаллического фундамента.
1.3 КАЧЕСТВЕНАЯ ХАРАКТЕРИСТИКА
КАЛИЙНОГО ГОРИЗОНТА
В Третьем соляном пласте выделено 5 слоёв: 10,11, Б1
, С1, Б2
(сверху вниз). Содержание NaCl по слоям изменяется от 86.73% до 99.09%, Н.О. – от 0.29% до 11.05%. По результатам геологоразведочных и опытно-промышленных работ слои Б1
, С1, Б2
суммарной средней мощностью 3.4м . Содержание NaCl в этих слоях составляет 98.19 – 98.98%, Н.О. – 0.42 – 0.77%.
Качественная характеристика продуктивных слоев, подлежащих выемке, приведена в таблице 1.3.
Таблица1.3.1
Качественная характеристика продуктивных слоёв
Слои
|
Мощность, м
|
Содержание,%
|
от
|
до
|
средняя
|
NaCl
|
Н.О.
|
Б1
|
1,32
|
1,36
|
1,34
|
98.40
|
0.71
|
С1
|
1,05
|
1,07
|
1,06
|
98.08
|
1.01
|
Б2
|
0,9
|
1,1
|
1
|
98.74
|
0.53
|
Структурная колонка пласта
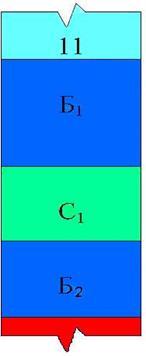
Рис.1
Б1
– мощность – 1,34м, содержание NaCl – 98.40%, содержание Н.О. – 0,71%
С1
- мощность – 1,06м, содержание NaCl – 98.08%, содержание Н.О. – 1,01%
Б2
- мощность – 1м, содержание NaCl – 98.74%, содержание Н.О. – 0,53%
1.4 ПРОМЫЩЛЕННЫЕ И ИЗВЛЕКАЕМЫЕ ЗАПАСЫ ПРОЕКТИРУЕМОГО ГОРИЗОНТА
Все запасы полезного ископаемого выявленные в пределах шахтного поля (горизонта), которые экономически выгодно разрабатывать при современном уровне развития технологии добычи полезных ископаемых называются балансовыми.
Балансовые запасы калийного пласта в пределах горизонта рассчитываются по формуле:
, (1.4.1)
где S
– площадь калийного пласта в шахтном поле, м2
;
m
– средняя мощность балансовой части пласта, м;
γ
– плотность руды, т/м3
.
Балансовые запасы составят:

Балансовые запасы включают промышленные запасы и общешахтные (проектные) потери. К общешахтным потерям относят те запасы, которые не планируются к извлечению по техническим причинам (например, оставляемые в охранных целиках, под горнотехническими сооружениями и т.д.)
Промышленные запасы определяются по формуле:
, (1.4.2)
где К
– коэффициент, учитывающий общешахтные потери, определяемый по формуле:
, (1.4.3)
где П
– общешахтные (проектные) потери (коэффициент, учитывающий общешахтные потери, составляет 0,93 ÷ 0,95)
Промышленные запасы составят:


Для расчета срока отработки горизонта необходимо определить количество извлекаемых из недр балансовых запасов, т.к. при разработке часть промышленных запасов остается не извлеченным, например, в целиках около подготовительных выработок, в целиках внутри выемочного участка, в целиках около геологических нарушений, в результате смешивания при выемке с пустой породой, при оставлении на контуре с вмещающими породами и т.д. Эта не извлеченная часть полезного ископаемого называется эксплуатационными потерями.
В отличие от проектных потерь эксплуатационные потери зависят от способа разработки пласта. Так, например, эксплуатационные потери при столбовой системе разработки меньше чем при камерной системе, так как при камерной системе в отработанном пространстве оставляются целики, поддерживающие кровлю от обрушения.
Промышленные запасы за вычетом эксплуатационных потерь называются извлекаемыми запасами. Полнота извлечения промышленных запасов характеризуется коэффициентом извлечения Ки. Коэффициент извлечения в значительной степени зависит от глубины разработки. При извлечении глубины разработки возрастает горное давление и для поддержания выработок в безопасном состоянии требуется увеличение ширины целиков.
При небольшой глубине разработки целики оставляются меньших размеров, а при большой глубине ширина целиков увеличивается и соответственно коэффициент извлечения руды при большой глубине разработки будет меньше.
При разработке Старобинского месторождения коэффициент извлечения можно ориентировочно принимать:
- при камерной системе разработки с оставлением жестких целиков Ки
принимается от 0,35 до 0,5;
- при камерной системе разработки с оставлением податливых целиков Ки
принимается от 0,65 до 0,75;
- при столбовой системе разработки Ки
принимается от 0,65 до 0,8;
В настоящее время на рудниках РУП ПО «Беларуськалий» осваиваются технологии разработки калийных пластов с увеличением длины лавы до 300м, а также с частичным извлечением междупанельных целиков и с отработкой смежных панелей «в присечку» (без оставления междупанельных целиков). Внедрение этих технологий позволит повысить коэффициент извлечения промышленных запасов и продлить срок службы рудников.
Извлекаемые запасы горизонта определяется по формуле:
, (1.4.4)
Извлекаемые запасы для горизонта -305м составят:
,
где Ки
– коэффициент извлечения для горизонта -305м, который составляет 0,4
1.5 КРАТКАЯ ГЕОЛОГИЧЕСКАЯ
ХАРАКТЕРИСТИКА ПРОЕКТИРУЕМОГО
ГОРИЗОНТА
Между Вторым и Третьим калийными горизонтами залегает мощная толща каменной соли, переслаивающаяся глинистыми, глинисто-мергелистыми, мергелисто-доломитовыми пачками. Промышленный интерес представляет Третий соляной пласт.
Третий соляной пласт (- 305м) приурочен к 23-й соляной пачке и залегает ниже подошвы Второго калийного горизонта в интервале 23.2 - 32.6м. Абсолютные отметки подошвы пласта в юго-западной части составляют – -258.5м, в северо-восточной части – -396.1м. Пласт средней мощностью 9.22м сложен чередованием сезонных прослоев каменной соли мощностью 5 – 45см и галопелитов мощностью от нескольких мм до 5–10см. Соль каменная, от светло-серой до темно-серой, мелко-среднезернистая со следами первичной кристаллизации, в различной степени загрязнена глинистым материалом.
Выше Третьего соляного пласта залегает 24-я глинисто-карбонатная пачка мощностью 6.0 – 6.5м. Глинисто-карбонатные породы содержат поровые рассолы хлоридно-кальциевого состава. При бурении шпура в кровлю в кроссинге 2 опытной панели Северного главного направления в 2002г. зафиксировано выделение газа с содержанием СН4
до 2%.
2. ГОРНАЯ ЧАСТЬ
2.1ВСКРЫТИЕ И ПОДГОТОВКА ШАХТНОГО ПОЛЯ
2.1.1 Вскрытие шахтного поля
Шахтное поле рудника Первого РУ Вскрыто четырьмя вертикальными стволами по центральной схеме. Диаметр стволов в свету – 7,0м. Второй калийный горизонт вскрыт всеми четырьмя стволами. Третий калийный горизонт – стволами №1, 3, 4.Первый калийный горизонт вскрыт тремя бремсбергами: транспортным, конвейерным и вентиляционным, пройденными из выработок 7-ой восточной панели Второго калийного горизонта (район скв. №121). Длина бремсбергов от 700 до 760м. На участках пересечения 26 и 28 глинисто-карбонатных пачек сечение выработок в проходке 13,48м2
, они закреплены металлической арочной крепью АП-3 из спецпрофиля СВП-19 (вентиляционный бремсберг) и СВП-27 (транспортный и конвейерный бремсберги). Третий соляной пласт (-305), залегающий ниже подошвы Второго калийного горизонта в интервале 23,2 ÷ 32,6м вскрыт тремя уклонами: транспортным, конвейерным и вентиляционным, пройденными из выработок околоствольного двора Второго калийного горизонта. Длина уклонов от 490 до 520м. На участках пересечения 22 и 24 глинисто-карбонатных пачек сечение выработок в проходке – 13,48м2
, они закреплены металлической арочной крепью АП-3 из спецпрофиля СВП-19. Вентиляционный уклон пройден до Второго соляного пласта (-280м) и пересекает только 22 глинисто-карбонатную пачку. Остальная часть его пройдена как вентиляционный штрек по третьему соляному пласту (-305м) и сбита с вентиляционным уклоном вентиляционным гезенком, закрепленным металлической арочной крепью АП-3 из спецпрофиля СВП-19. Высота гезенка ~ 18м, диаметр в проходке – 1,0м.
Характеристик вскрывающих выработок:
Ствол №1 – пройден до Третьего калийного горизонта. Ствол оборудован скиповым и клетевым подъёмами. Ствол служит для выдачи калийной руды с Третьего горизонта.
Ствол оборудован двухскиповой подъёмной машиной – БЦК-8/5×1,7; клетевой подъёмной машиной – ЦР-5×3,5. Грузоподъёмность скипов до 25 тонн, разгрузка донная; скип СН-19 с секторным затвором. Клеть типа 1НОВ-400 с противовесом. Ствол оборудован для спуска и подъёма грузов с Третьего горизонта, используется для подачи свежего воздуха на Третий горизонт.
Ствол №2 – пройден до соляного горизонта -305м. Ствол оборудован скиповым и клетевым подъёмами. Двухскиповая подъёмная машина – БЦК-8/5×1,7; клетевая подъёмная машина - ЦР-5×3,5. Грузоподъёмность скипов СН-19 до - 25 тонн. Клеть с противовесом 1НОВ-400. Ствол предназначен для выдачи каменной соли, добываемой на пласте -305, спуска подъёма грузов и для подачи свежего воздуха на Второй и Первый калийные горизонты, а также пласт каменной соли -305.
Ствол №3 – пройден до Третьего калийного горизонта. Предназначен для удаления отработанного воздуха со всех действующих горизонтов рудника, спуска и подъёма людей и грузов. Оборудован двухклетевым подъёмом. Тип подъёмной машины – ЦР-5×3,5. В стволе имеется лестничное отделение. Тип клети - 1НОВ-400.
Ствол №4 – пройден до третьего калийного горизонта. Ствол предназначен для выдачи руды с Третьего горизонта, оборудован двумя скиповыми подъёмами. Тип подъёмных машин – 2Ц-2,84, грузоподъёмность скипов СН-19 - до 25 тонн. Ствол может быть использован для подачи воздуха на все рабочие горизонты рудника. В 1999 году скиповой подъём 4-1 переоборудован для выдачи калийной руды со Второго калийного горизонта, через который осуществляется выдача руды с Первого калийного горизонта.
Отметки горизонтов и глубина стволов приведены в таблице 2.1.1.1
Стволы
|
№1
|
№2
|
№3
|
№4
|
Отметка устья
Отметка второго горизонта
Глубина Второго горизонта
Отметка пласта каменной соли -305
Глубина пласта каменной соли -305
Отметка Трётьего горизонта
Глубина Третьего горизонта
Отметка дозаторной
Отметка камеры улавливания просыпи
Отметка зумпфа
Глубина ствола
|
154,4
-263,7
418,1
-299,0
453,4
-431,5
585,9
-483,5
-516,9
-529,1
683,5
|
154,4
-264,0
418,4
-
-
-
-
-307,5
-336,07
-348,6
503,0
|
154,0
-264,0
418,0
-297,1
451,1
-435,0
589,0
-
-
-446,0
600,0
|
152,8
-275,5
428,3
-
-
-444,5
597,3
-
-
-507,2
660,0
|
Таблица 2.1.1.1
Отметки горизонтов и глубина стволов
Основные данные бремсбергов, вскрывающих Первый калийный горизонт приведены в таблице 2.1.1.2
Таблица 2.1.1.2
Основные данные бремсбергов
Бремсберг
|
Транспортный
|
Конвейерный
|
Вентиляционный
|
Сечение в свету
|
10,0м2
|
8,95м2
|
8,95м2
|
Отметка устья
|
-280,5
|
-280,0
|
-280,0
|
Угол подъёма
|
4˚30΄
|
4˚30΄
|
4˚30΄
|
Длина
|
760
|
760
|
700
|
Отметка верхнего горизонта
|
-222.9
|
-223.3
|
-222.0
|
Основные данные уклонов, вскрывающих пласт каменной соли -305м, приведены в таблице 2.1.1.3
Таблица 2.1.1.3
Основные данные уклонов
Уклон
|
Транспортный
|
Конвейерный
|
Вентиляцион-ный
|
Сечение в свету
|
8,0м2
|
8,0м2
|
8,0м2
|
Отметка устья
|
-253,96
|
-253,78
|
-254,0
|
Угол подъёма
|
4˚30΄
|
4˚30΄
|
4˚30΄
|
Длина
|
500
|
520
|
490
|
Отметка нижнего горизонта
|
-294,4
|
-293,3
|
-289,5
|
2.1.2 Подготовка шахтного поля
Шахтное поле рудника Первого РУ на всех рабочих горизонтах подготовлено горизонтальными горными выработками главных направлений, пройденных от центра флангам.
На Первом горизонте (-200м) – Главное Северное направление.
На пласте каменной соли (-305м) – Главное Северное направление и Западное разведочное направление.
На Третьем горизонте (-430м) – Главное Северное, Главное Южное и Главное Юго-Восточное направление.
С учётом горногеологических, технологических и экономических факторов применена рудная схема подготовки шахтного поля. Исключение составляют выработки околоствольных дворов, где полевая подготовка обусловлена технологическими причинами.
Выработки главных направлений представляют собой сгруппированные, расположенные параллельно друг другу однотипные выработки – транспортные и вентиляционные. На каждом главном направлении пройдено по 3 транспортных выработки (4 на юго-востоке Третьего горизонта) и по 1-2 вентиляционных. Выработки соединяются сбойками через каждые 200 ÷ 250м.
Некоторые участки шахтного поля отрабатываются по панельной схеме, при которой от главных транспортных выработок перпендикулярно к ним проходятся панельные конвейерные, транспортные, вентиляционные и вспомогательные выработки с интервалами, зависящими от ширины панелей. Панели односторонние и двухсторонние.
В первом случае панельные выработки сгруппированы у границы со смежной панелью со стороны массива. В условиях доработки участков шахтного поля применяются двухсторонние панели, когда панельные выработки расположены по центру панели. Направление отработки панелей – обратное (от границы шахтного поля).
Длина панели определяется размерами шахтного поля и составляет 1,8 ÷ 3,5км. Ширина устанавливается в зависимости от применяемой системы разработки: при камерной системе 300,0 ÷ 500,0м, при столбовой – 270,0 ÷ 370,0м (в зависимости от расположения столба и глубины разработки).
Панельные выработки представлены конвейерным, транспортным (одним или двумя), вентиляционным и вспомогательными выработками (закладочными, объездными), а также камерами различного назначения: камеры приводных и натяжных станций ленточных конвейеров, камеры для установки электрооборудования, камеры разворота самоходного транспорта и др.
На гор.-430 горно-подготовительные выработки в основном проходятся комбайновыми комплексами ПК-8МА. Сечение этих выработок имеет арочную форму, размеры выработок: ширина – 3,0м, высота – 3,0м, площадь сечения - 8,0м2
.
При использовании на горнопроходческих работах комбайновых комплексов Урал-10А при камерной системе разработки размеры подготовительных выработок следующие: площадь сечения 9,0 ÷ 10,5м2
, ширина – 4,1 ÷ 4,3м, высота – 2,4 ÷ 3м.
2.2 ВЫБОР СИСТЕМЫ РАЗРАБОТКИ
Система разработки – порядок ведения подготовительных и очистных выработок, увязанный во времени и пространстве.
В связи с лёгкой растворимостью солей к системам разработки калийных месторождений предъявляются повышенные требования, обусловленные необходимостью надёжной изоляции горных выработок от проникновения в них подземных и поверхностных вод и рассолов.
На Старобинском месторождении калийных солей применяются следующие системы разработки : камерная, столбовая, комбинированная.
Камерная система разработки
Применение камерных систем разработки обусловлено наличием водоносных горизонтов в покрывающих породах, необходимостью оставления над горными выработками водонепроницаемой толщи пород с целью защиты их от проникновения агрессивных вод или рассолов из надсолевой толщи, охраны поверхностных зданий и сооружений от вредного влияния горных работ. На рудниках Старобинского месторождения калийных солей применяются следующие камерные системы разработки:
- разработка с оставлением податливых целиков;
- разработка с оставлением жёстких целиков;
- разработка с регулярным оставлением жёстких и податливых целиков.
Таблица 2.2.1
Параметры системы с податливыми целиками:
Параметры
|
Размер
|
ширина очистного хода
|
4,1 – 4,37м
|
высота очистного хода
|
2,4 – 2,6м
|
ширина межходового целика
|
1,2 – 2,0м
|
длина очистного хода
|
до 200м
|
Расстояние между фронтами очистных работ в смежных блоках панели должно составлять не менее 50м. При этом указанный фронт в блоке, примыкающем к отработанной части панели, должен быть опережающим.
Запрещается в одном блоке вести очистные работы одновременно двумя комбайнами. Использование второго комбайна допускается лишь для проведения камер разворота.
Камеры разворота комбайнов проводятся с опережением до 50м фронта очистных работ. Минимальное количество подготовленных камер разворота, должно быть не менее двух (за исключением стадии доработки последних камер в блоке).
Таблица 2.2.2
Параметры системы с жесткими целиками:
Параметры
|
Размер
|
ширина очистного хода
|
4,1 – 4,37м
|
высота очистного хода
|
2,4 – 2,6м
|
длина очистного хода
|
до 200м
|
ширина межходового целика
|
1,5м
|
ширина междукамерного целика
|
4,0 – 6,0м
|
При камерной системе разработки с блоковой схемой подготовки каждая очистная камера состоит из 2-3 комбайновых ходов, разделенных поддерживающими целиками и проходимых из общей камеры разворота, разделываемой на блоковых штреках.
Столбовая система разработки.
В зависимости от конкретных горно-геологических и горно-технических
условий могут применяться различные варианты столбовой системы разработки с валовой и селективной выемкой пласта, с разделением и без разделения его на слои, с общей и раздельной подготовкой лав.
Выемка пласта (слоя) должна осуществляться преимущественно с применением панельного способа подготовки. Допускается применение других способов подготовки в зависимости от конфигурации и раскройки шахтного поля.
Для отработки III калийного горизонта рудника 1РУ применяется вариант со слоевой выемкой пласта и раздельной подготовкой лав.
Таблица 2.2.3
Параметры выемки верхнего столба (IV сильвинитового слоя):
Параметры
|
Размер
|
длина столба
|
2,0 – 3,5км
|
длина лавы
|
180,0 – 200,0м
|
вынимаемая мощность
|
1,05 – 1,35м
|
технология выемки
|
двухкомбайновая
|
Таблица 2.2.4
Параметры выемки нижнего столба (II-III сильвинитовые слои):
Параметры
|
Размер
|
длина столба
|
2,0 – 3,5км
|
длина лавы
|
135 – 150,0м
|
вынимаемая мощность
|
2,1 – 2,2м
|
технология выемки
|
однокомбайновая
|
Слоевая выемка III пласта предполагает опережающую отработку IV сильви-нитового слоя (верхнего столба). Отставание фронта очистных работ нижнего столба по слоям II-III составляет, как правило, 1,5 и более километров, или до 2 3 лет. При этом максимально используется эффект разгрузки массива в надработанном пространстве, что обеспечивает устойчивость подготовительных выработок нижнего столба. В качестве защитной потолочины над выработками нижнего столба используется каменная соль III-IV мощностью 1,0 - 1,3м.
Комбинированная система разработки.
Комбинированная система разработки представляет собой сочетание двух систем разработки при отработке пласта III калийного горизонта: системы разработки длиными столбами с управлением кровлей полным обрушением для выемки IV сильвинитового слоя и камерной системы для отработки слоёв II-III. При этом межслоевая каменная соль III-IV используется в качестве защитной потолочины в период отработки II-III сильвинитовых слоёв. Опережение выемки верхнего слоя относительно фронта очистных работ по нижним слоям должно быть не менее 150м и, как правило, составляет несколько лет (3-4 года).
Расстояние между фронтами очистных работ в смежных блоках при камерной системе должно составлять не менее 50м.
Камеры разворота комбайнов проводятся в одну стадию с очистными работами или же с опережением на расстояние до 50м.
В случае отставания во времени очистных работ в нижних слоях более 3-х лет:
- в блоковых штреках необходимо : в межслоевой пачке (потолочине) оставлять слой сильвинита мощностью 0,2-0,4м; в кровле блоковых конвейерного и вентиляционного штреков проводить вертикальную компенсационную щель глубиной 0,8-0,9м; щель прорезать после возведения анкерной крепи и не позднее, чем через 1,5месяца с момента проведения выработки;
- для устранения пучения пород в блоковом конвейерном штреке необходимо проводить щель в почве по центру выработки на глубину 0,9-1,2м;
Таблица 2.2.5
Параметры отработки IV сильвинитового слоя:
Параметры
|
Размер
|
длина столба
|
2,0 – 3,5км
|
длина лавы
|
180,0 – 200,0м
|
вынимаемая мощность
|
1,05 – 1,35м
|
технология выемки
|
двухкомбайновая
|
Таблица 2.2.6
Параметры отработки II-III сильвинитовых слоёв:
Параметры
|
Размер
|
длина блока
|
180,0м
|
длина очистных камер
|
140,0 – 210,0м
|
ширина межходового целика
|
1,5 – 2,5м
|
ширина очистного хода
|
4,1м
|
высота очистного хода
|
2,4м
|
Очистная камера состоит из двух выработок, которые проходятся из общей камеры разворота, разделываемой на блоковых штреках.
Выбранная система разработки должна отвечать следующим требованиям:
- обеспечивать безопасные условия труда;
- иметь высокие технико-экономические показатели;
- обеспечивать высокое качество добываемой руды;
- обеспечивать наименьшие потери полезного ископаемого в недрах земли.
В настоящее время столбовые системы разработки являются основными при добыче калийных солей на Старобинском месторождении , так как имеют ряд существенных преимуществ по сравнению с камерными и обеспечивают:
- более безопасные условия труда в забое;
- высокую нагрузку на очистной забой;
- более полное извлечение полезного ископаемого из недр;
- возможность селективной выемки сильвинита, что существенно повышает качество добываемой руды и уменьшает объем рудной массы, выдаваемой на поверхность.
Но применение столбовой системы разработки возможно только на тех участках месторождения, где исключается прорыва воды в подземные выработки, вследствие подработки водозащитной толщи.
Столбовую систему разработки нельзя применять на участках притектонических и краевых зон, т.к. ожидаемая высота зоны распространения трещин в этих зонах выше, а мощность водозащитной толщи меньше.
Применение столбовой системы нецелесообразно для отработки небольших участков длиной до 2км и неправильной конфигурации.
Камерные системы разработки имеют более низкую производительность, чем столбовые, а потери руды выше. Поэтому их применение ограничено. Они применяются на участках притектонических и краевых зон, а также участков небольших размеров и неправильной конфигурации.
2.3 РАСЧЁТ ЧИСЛА РАБОТАЮЩИХ ПАНЕЛЕЙ И ГЛАВНЫХ НАПРАВЛЕНИЙ
Число панелей определяется по формуле:
, (2.3.1)
где – годовая производительность горизонта, тыс.т., принимается 600000тыс.т/мес.;
– годовая производительность панели (очистного комплекса) тыс. т.;
тыс.т.;
(2.3.2)
Отсюда:
тыс.т./год;
– среднемесячная производительность очистного комплекса на панели, тыс.т.;
– коэффициент, учитывающий добычу руды камерной системой, принимается 0,21 ÷ 0,26;
– коэффициент неравномерности работы очистных забоев, принимается 1,1 – 1,15.
Отсюда число панелей составит:
панель.
Поскольку на действующей панели могут возникнуть аварийные ситуации, к рассчитанному числу панелей можно прибавить одну резервную панель, отсюда число панелей составит 2.
2.4 РАСЧЁТ СРОКА ОТРАБОТКИ
ПРОЕКТИРУЕМОГО ГОРИЗОНТА
По состоянию на 01.01.2009 балансовые запасы калийной руды по категориям А+В+С1
на руднике 1РУ составили 290,4млн.тонн,балансовые запасы каменной соли составили 63,7млн.тонн.
На проектируемом горизонте (горизонт -305м) запасы каменной соли составляют 63,7млн.тон.
Срок отработки горизонта -305м рассчитывается по формуле:
, (2.4.1)
где Q
и
- извлекаемые запасы горизонта, млн.т
Расчёт Q
и
приведён в формуле (1.4.4)
А
- годовая производственная мощность горизонта, млн.т/год
Отсюда срок отработки проектируемого горизонта составит:

Выдача каменной соли пласта -305м осуществляется по стволу №2.
Режим работы рудника по добыче руды – непрерывный с выходными днями по скользящему графику. Продолжительность смены – 7 часов (от клети до клети), в том числе 6 часов в забое. Количество смен по добыче руды в сутки – 3, одна смена ремонтная.
3. СПЕЦИАЛЬНАЯ САЧТЬ
3.1 КРАТКАЯ ГЕОЛОГИЧЕСКАЯ
ХАРАКТЕРИСТИКА ВЫЕМОЧНОГО УЧАСТКА
Между Вторым и Третьим калийными горизонтами залегает мощная толща каменной соли, переслаивающаяся глинистыми, глинисто-мергелистыми, мергелисто-доломитовыми пачками. Промышленный интерес представляет Третий соляной пласт.
Абсолютная отметка подошвы выемочного участка составляет –258.5м. Пласт средней мощностью 9.22м сложен чередованием сезонных прослоев каменной соли мощностью 5 – 45см и галопелитов мощностью от нескольких мм до 5 – 10см. Соль каменная, от светло-серой до темно-серой, мелко-среднезернистая, со следами первичной кристаллизации, в различной степени загрязнена глинистым материалом. В пласте выделено 5 слоёв: 10,11, Б1
, С1, Б2
(сверху вниз).
Глинисто-карбонатные породы содержат поровые рассолы хлоридно-кальциевого состава. При бурении шпура в кровлю в кроссинге 2 западной панели Северного главного направления в 2002г. зафиксировано выделение газа с содержанием СН4
до 2%.
Водозащитная толща над проектируемым участком составляет 175 – 205м.
Средняя мощность пласта проектируемого участка составляет 3,57м.
Геологическая характеристика проектируемого участка приведена в таблице 3.1.1
Таблица 3.1.1
Геологическая характеристика участка
Слой
|
Мощность
|
Содержание NaCl
|
Б1
|
1.34м
|
98,40%
|
С1
|
1.05м
|
98,08%
|
Б2
|
1.18м
|
98,74%
|
3.2 ВЫБОР СИСТЕМЫ РАЗРАБОТКИ И ЕЁ ВАРИАНТА ДЛЯ ОТРАБОТКИ ВЫЕМОЧНОГО УЧАСТКА
На Старобинском месторождении калийных солей первого рудоуправления очистные работы ведут с применением камерной, столбовой и комбинированной систем разработки. Система разработки должна отвечать следующим требованиям:
- обеспечивать безопасные условия труда;
- иметь высокие технико-экономические показатели;
- обеспечивать высокое качество добываемой руды;
- обеспечивать наименьшие потери полезного ископаемого в недрах земли.
Наиболее эффективными являются столбовые системы разработки, и они являются основными при добыче калийных солей на Старобинском месторождении, так как они имеют ряд преимуществ по сравнеию с камерными и обеспечивают:
- более безопасные условия труда в забое;
- высокую нагрузку на очистной забой;
- более полное извлечение полезного ископаемого из недр;
Проведём анализ столбовой системы разработки на достаточность мощности водозащитной толщи (ВЗТ) исходя из условий безопасной отработки, исключающей прорыв воды в горные выработки. Допустимая выемочная мощность пласта при этом будет определяться по формуле:
 (3.2.1)
где Т
– мощность ВЗТ,м;
n
– кратность, равная 40.

Применение столбовой системы разработки возможно, если фактическая выемочная мощность пласта меньше допустимой:
(3.2.2)
Так как промышленный интерес представляют все три слоя Б1
, С1
и Б2
, то фактическая выемочная мощность будет составлять 3,57м. Следовательно:
,что не соответствует условию и делает невозможным применение столбовой системы разработки.
Проведём анализ камерной системы разработки на достаточность мощности водозащитной толщи (ВЗТ) исходя из условий безопасной отработки, исключающей прорыв воды в горные выработки. Допустимая выемочная мощность пласта при этом будет определяться по формуле:
(3.2.3)
где Т
– мощность ВЗТ,м;
n
– кратность, равная 20

Применение камерной системы разработки возможно, если фактическая выемочная мощность пласта меньше допустимой:
(3.2.4)
Отсюда:
, что соответствует условию и делает возможным применение камерной системы разработки.
Согласно проведенному анализу принимает для отработки выемочного участка камерную систему разработки.
Существует два варианта камерной системы разработки: камерная система с оставлением податливых целиков, и камерная система с оставлением жёстких целиков.
Производительность этих систем разработки примерно одинакова, но потери руды при оставлении жёстких целиков составляют 50 - 60 % , а при оставлении податливых целиков в благоприятных условиях могут быть снижены до 25 %.
Однако жёсткие целики обладают высокой несущей способностью, они разрушаются медленнее, деформация пород кровли происходит не столь интенсивно и зона распространения трещин ниже.
Для отработки выемочного участка окончательно принимаем камерную систему разработки с оставлением жестких целиков.
Принципиальная технологическая схема выемки пласта
          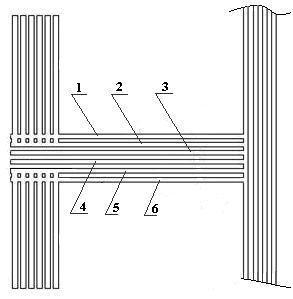
Рис.2
       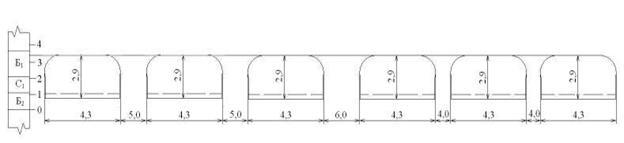
Рис.3
1 – вентиляционный штрек 5 – транспортный штрек №2
2 – стартовый штрек №1 6 – стартовый штрек №2
3 – транспортный штрек №1
4 – конвейерный штрек
3.3 ГОРНО-ПОДГОТОВИТЕЛЬНЫЕ РАБОТЫ
3.3.1 Выбор способа проведения подготовительных выработок и проходческих горных машин
При подготовке участка для выемки каменной соли проводятся следующие подготовительные выработки: вентиляционный штрек, стартовый штрек №1, транспортный штрек №1, конвейерный штрек, транспортный штрек №2, стартовый штрек №2.
В процессе подготовки блока блоковые штреки через каждые примерно 200м соединяются между собой технологическими сбойками, обеспечивающими возможность дальнейшей проходки с отгрузкой руды на скребковый конвейер.
Высота всех блоковых выработок составляет от 2,9м, что обеспечивает монтаж ленточного конвейера, проезд самоходного транспорта. Ширина всех выработок – 4,3м.
Горно-подготовительные работы производятся комбайновым комплексом Урал-10А в состав, которого входят комбайн Урал-10А, бункер перегружатель БП-14А, самоходный вагон 5ВС – 15М.
С учетом технических возможностей комбайна и геологического строения пласта высота выработок первого комбайнового хода составляет 2.6м, затем производится подрубка почвы выработок в соответствии с проектной высотой каждой из них.
Таблица 3.3.1.1
Техническая характеристика комбайна Урал-10А
№
п/п.
|
Наименование технической характеристики.
|
Единицы
измерения.
|
Количество.
|
1
|
Мощность пласта min/max
|
м
|
2,2-2,6
|
2
|
Допустимый угол падения пласта при работе по простиранию/ по восстанию/ падению
|
град.
|
±12
|
3
|
Напряжение
|
В
|
660
|
4
|
Масса
|
т
|
65
|
5
|
Габаритные размеры
|
мм
|
12500x410x2400
|
6
|
Суммарная номинальная мощность двигателей комбайна
|
кВт
|
527
|
Таблица 3.3.1.2
Техническая характеристика БП-14А
№ п/п
|
Наименование технической характеристики.
|
Единицы измерения.
|
Количество.
|
1
|
Грузоподъёмность.
|
Т
|
16
|
2
|
Ёмкость бункера.
|
м3
|
13,8
|
3
|
Время разгрузки 15 т.
|
Сек
|
50
|
4
|
Мощность электродвигателей.
|
кВт
|
30
|
Таблица3.3.1.3
Техническая характеристика 5ВС-15М
№
п/п.
|
Наименование технической
характеристики.
|
Единицы
измерения.
|
Количество.
|
1
|
Грузоподъёмность.
|
Т
|
15
|
2
|
Ёмкость кузова.
|
м3
|
8,6
|
3
|
Скорость движения по горизонтальному пути.
Первая.
Вторая.
Третья.
|
км/час
|
2,5
5
8
|
4
|
Максимальный угол, преодолеваемый вагоном.
|
град
|
15
|
5
|
Минимальный радиус поворота по наружному габариту.
|
М
|
8,5
|
6
|
Вес вагона.
|
Т
|
16,2
|
Для транспортирования отбитой горной породы из подготовительных выработок применяются скребковый конвейер СП-202, который перегружает руду на блоковый ленточный конвейер КЛ-600(КЛЗ-500), который перегружает породу на конвейер главного направления.
Таблица 3.3.1.4
Техническая характеристика скребкового конвейера СП-202
№ п/п
|
Наименование технической характеристики.
|
Единицы измерения.
|
Количество.
|
1
|
Двигатель
|
-
|
ЭДКОФ49/4
|
2
|
Номинальная мощность
|
кВт
|
55 × 2 = 110
|
3
|
Номинальный ток
|
А
|
2 × 62,5 = 125
|
4
|
КПД
|
%
|
86,6
|
5
|
Ширина рештачного става без бортов
|
мм
|
642
|
6
|
Масса конвейера
|
т
|
40,0
|
Таблица 3.3.1.5
Техническая характеристика блокового ленточного конвейера
КЛ-600(КЛЗ-500)
№ п/п
|
Наименование технической характеристики.
|
Единицы измерения.
|
Количество.
|
1
|
Производительность
|
т/ч
|
600
|
2
|
Скорость движения ленты
|
м/сек
|
2,5
|
3
|
Длина конвейера
|
м
|
600
|
4
|
Ширина ленты
|
мм
|
1000
|
5
|
Тип ленты
|
-
|
ПхВ-120
|
6
|
Привод
|
-
|
Двухбарабанный
|
7
|
Мощность привода
|
кВт
|
2×75
|

3.3.2 Выбор и обоснование формы и размеров поперечного сечения
подготовительных выработок
Подготовка блока заключается в проведении следующих подготовительных выработок: вентиляционный штрек, стартовый штрек №1, транспортный штрек №1, конвейерный штрек, транспортный штрек №2, стартовый штрек №2.
Блоковый конвейерный штрек служит для установки в нём блокового ленточного конвейера, который осуществляет транспортировку горной массы на ленточные конвейера главного направления.
Блоковый вентиляционный штрек служит для движения по нему отработанной струи воздуха, а также по нему доставляются крепёжные материалы и вспомогательное оборудование. В случае аварии штрек является запасным выходом.
Блоковый транспортный штрек служит для транспортирования вспомогательного оборудования и крепёжных материалов.
Стартовый штрек служит для осуществления выхода комбайна на зарубку при отработке камеры.
Все горные выработки, по которым производится транспортирование людей, грузов, оборудования должны иметь определенные зазоры между стенкой выработки и размещенного в ней оборудования, а также между стенкой выработки и наиболее выступающей кромкой габарита транспортных средств.
Эти зазоры предусматриваются правилами безопасности.
Для размещения оборудования рассчитывается ширина выработок по формуле:
(3.3.2.1)
где а
– зазор между стенкой выработки и наиболее выступающей частью транспортного средства с непроходной стороны,м;
b
– габариты транспортного средства по наиболее выступающим частям,м;
c
– зазор между стенкой выработки и наиболее выступающей частью транспортного средства с проходной стороны,м.
Ширина конвейерного штрека блока:

Принимаем ширину конвейерного штрека равную 4,3м.
Ширина транспортного штрека блока:
Принимаем ширину транспортного штрека равную 4,3м.
На блоковом конвейерном штреке устанавливается ленточный конвейер шириной 1,2м. Ширина прохода людей с одной стороны должна быть не менее 0,7м, а с другой – не менее 0,4м. Расстояние от верхней плоскости до кровли выработки должно быть не менее 0,5м. С учётом этих зазоров минимальная ширина и высота выработки должна быть соответственно 2,3м и 1,7м. Принимаем ширину и высоту блокового конвейерного штрека соответственно 4,3м и 2,9м.
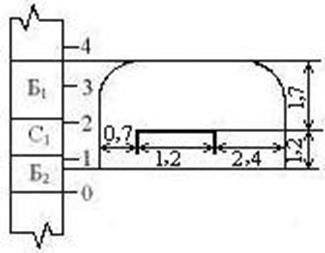
Рис.4
Панельные транспортные штреки №1 и №2 служит для доставки крепёжных материалов и оборудования, а так же для движения по нему самоходного вагона. Принимаем ширину и высоту выработки 4,3м и 2,9м соответственно.
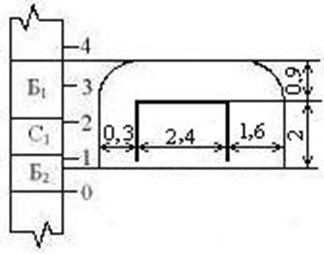
Рис.5
Вентиляционный штрек служит для движения по нему отработанного воздуха. Принимаем ширину и высоту выработки 4,3м и 2,9м соответственно. Штрек не предназначен для движения людей (только при авариях).
 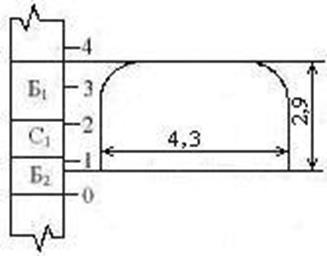
Рис.6
С учётом технических параметров комбайна Урал-10А ширина и высота стартовых штреков №1 и №2 составит 4,3м и 2,9м соответственно.

Рис.7
Площадь поперечного сечения выработок составит: без подрубки почвы – 10,5м2
;после подрубки почвы – 11,79м2
.
3.3.3 Охрана и крепление подготовительных выработок
При проходке подготовительных выработок в массиве породы кровли, почвы, боков будут находиться под воздействием всестороннего давления, что приведёт к расслоению и образованию трещин, нарушению плотности и в дальнейшем к разрушению пород кровли, боков и почвы. Для подержания в устойчивом состоянии кровли и боков горных выработок различного назначения, а также для крепления целиков, в случае их преждевременного разрушения, наиболее эффективным видом крепи (для горно-технических условий Старобинского месторождения) является анкерная крепь, представляющая собой металлические анкеры, которые устанавливаются в кровле выработок и скрепляют обрушающиеся пачки породы с лежащими выше монолитными породами основной кровли. Поэтому для выработок (блоковые конвейерные, транспортные, вентиляционный ; и стартовые штреки) принимается крепление анкерной крепью ЭС-85П (Эстонсланец).
Анкер ЭС-85П (Эстонсланец) состоит из стержня, изготовленного из стали марки Ст.5, который в верхнем конце переходит в клин, а на нижнем имеет резьбу М20, двух распорных полувтулок (“сухарей”), натяжной гайки и
шайбы – опорной плитки. Анкер закрепляется в шпуре посредством расклинивания клиноконической головки в “сухарях”. Несущая способность крепи в сильвините и каменной соли составляет 10 – 11тс.
Анкерная крепь ЭС-85П ”Эстонсланец”
 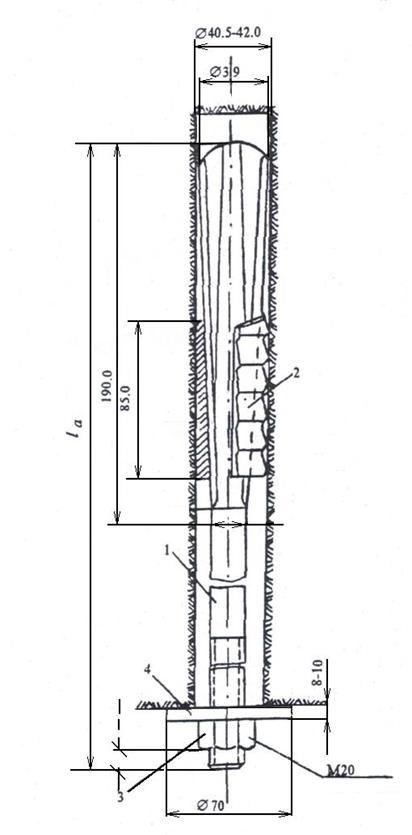
Рис.8
Схема установки крепи для транспортных, конвейерного, стартовых и вентиляционного щтреков
 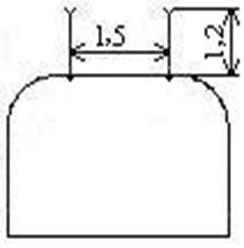 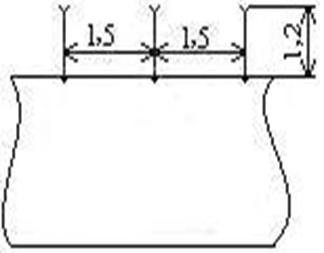
Рис.9
Крепление камер разворота комбайна и сопряжений выработок производится по паспорту крепления горных выработок. Крепление заключается в том, что крепь устанавливается в шахматном порядке (по сетке), этим обеспечивается наилучшее крепление большой обнаженности кровли.
3.3.4 Схема подготовки выемочного участка,
параметры системы
Схема отработки панели будет производиться двухсторонними блоками.
Длина очистного хода принимается 170м(L
оч
), межблоковый целик принимается 30м(амб
), ширина очистного хода комбайна Урал-10АМБ будет равна ширине его исполнительного органа и составит 3,65м(b
оч
), высота очистного хода 3,4м(h
оч
), ширина межпанельного целика принимается 20м(амп
), ширина панели 371,9м(b
п
), ширина всех подготовительных выработок составит 49,8м(b
под
).
Отсюда можно рассчитать длину панели и число блоков.
Зная, что экономичеки выгодно отрабатывать панели длина которых составляет более 2-х километров столбовой системой разработки, делаем вывод, что для отработки панели камерной системой разработки длина панели не должна превышать 2-х километров.
Рассчитаем длину двух блоков:
(3.3.4.1)

Зная, что длина панели не должна превышать 2-х километров, можно узнать число блоков в панели:
(3.3.4.2)

Проверим правильность расчёта. Для этого найдём среднюю длину одного блока:
(3.3.4.3)
Отсюда длина панели составит:
(3.3.4.4)

Что не удовлетворяет условию. Так как схема отработки панели будет производиться двухсторонними блоками, то число блоков составит 8 (nбл
=8). Значит, длина панели составит:
 
3.3.5 Технология подготовки панели
При подготовке панели будут проводиться следующие подготовительные выработки: вентиляционный штрек; стартовый штрек №1; транспортный штрек №1; конвейерный штрек; транспортный штрек №2; стартовый штрек №2. Целики между выработками будут составлять 5,0м; 5,0м; 6,0м; 4,0м; 4,0м в том же порядке, в котором перечислены выработки.
Последовательность проходки блоковых штреков: конвейерный штрек, вентиляционный штрек, транспортный штрек №1, стартовый штрек №1,транспортный штрек №2, стартовый штрек №2.
Подготовка блоков поэтапная, на расстоянии ~250м от панели выполняются технологические узлы, в которых проходятся короткие сбойки, соединяющие все блоковые выработки, разделывается камера монтажа скребкового конвейера.
3.4 ОЧИСТНЫЕ РАБОТЫ
3.4.1 Выбор горных машин и оборудования для ведения очистных работ
Выбор горных машин и оборудования для ведения очистных работ зависит от горно-геологических условий залегания пласта, выбранной системы разработки, вынимаемой мощности пласта и способа управления кровлей.
Так как была выбрана камерная система разработки, а так же мощность выемочного пласта составляет 3,4м, то отработку блоков предусмотрено производить комбайном Урал-10АМБ, в комплексе с бункером-перегружателем БП-14А и самоходным вагоном 5ВС-15М.
Комбайн проходческо-очистной «Урал-10АМБ» предназначен для применения на очистных работах и проходки выработок прямоугольной формы по пластам калийных руд мощностью 1,9-3,4м, при углах падения до ±12°.
Таблица 3.4.1.1
Урал-10АМБ
Технические параметры
|
Количественное значение
|
Единицы измерения
|
1. Размеры выработок:
площадь сечения
|
м2
|
6,9 …12,4
|
высота
|
м
|
1,9 … 3,4
|
2.Габаритные размеры
длина
|
мм
|
12600
|
ширина исполнительного органа
|
мм
|
3650
|
высота по корпусу
|
мм
|
1700
|
3. Суммарная номинальная мощность двигателей комбайна
|
кВт
|
570
|
4.Рабочее напряжение
|
В
|
1140
|
5. Масса комбайна
|
т
|
70
|
6. Тип исполнительного органа
|
барабанный
|
Количество барабанов
|
Шт.
|
1
|
Количество боковых фрез
|
Шт.
|
4
|
Скорость вращения барабана
|
Об./мин.
|
50.15
|
Скорость вращения боковых фрез
|
Об./мин.
|
66.87
|
Количество резцов на барабане
|
Шт.
|
69
|
тип резца
|
Д6-22
|
Количество резцов на боковой фрезе
|
Шт.
|
22
|
тип резца
|
Д6-22
|
7. Тип погрузочного органа
|
Питатель с нагребающими звездами и скребковый конвейер
|
8. Тип ходовой части
|
гусеничный
|
максимальная скорость движения комбайна
при маневрах
|
м/мин
|
3
|
3.4.2 Расчёт размеров междукамерных целиков
При проектировании камерной системы разработки с оставлением жёстких целиков ширина жёстких междукамерных целиков по условию обеспечения безопасной отработки камеры определяется по формуле:
(3.4.2.1)
где N
– число очистных ходов в камере
l
– ширина очистного хода, м
Н
– глубина разработки, м
ai
– ширина поддерживающего (внутрикамерного) целика, м(а
i
=
=
3,0м)
1/
ρ
,
f
– коэффициенты (для пород, относящихся к I и II типу по
Классификации БелГОРХИМПРОМ 1/
ρ
= 1,33; f
= 0,0007;
относящихся к III типу - 1/
ρ
= 0,84; f
= 0,00124)
h
– высота целика в проектируемом очистном ходе, м
h
с
– тоже в стандартном очистном ходе (2,6м)
exp
– экспоненциальная функция
Отсюда размер междукамерного целика составит:

Значит, ширина жёсткого междукамерного целика принимается 5м.
3.4.3 Разделка и крепление камер разворота комбайна
Так как комбайн Урал-10АМБ является опытным комбайном, то разделка камеры разворота осуществляется комбайном Урал-10А. Эти камеры предусмотрены для разворота комбайна в нужном направлении. При отработке блока одна камера разворота разделывается на два очистных хода. Камеры разворота комбайна разделываются с опережением фронта очистных работ до 50м. Минимальное количество подготовленных камер разворота должно быть не менее двух за исключением стадии доработки последних камер в блоке.
Разделка камеры разворота подразделяется на следующие этапы:
- на ранее пройденном и закрепленном стартовом штреке панели обуривается глубокий дренаж в кровлю и почву;
- из стартового штрека панели производится снятие стружки 0,5 – 2,0м вправо, обуривается глубокий дренаж в кровлю и почву, комбайн отгоняется, производится снятие 2-ой стружки, обуривается глубокий дренаж в кровлю и почву, комбайн отгоняется, производится вырубка на транспортный штрек панели, обуривается дренаж в кровлю и почву, производится вырубка на конвейерный штрек панели, комбайн отгоняется, этап крепится анкерами L=1,2м, с шагом крепления 1,5м.
- производится вырубка на ранее пройденный вентиляционный штрек панели, обуривается глубокий дренаж в кровлю и почву, комбайн отгоняется, этап крепится анкерами L=1,2м с шагом крепления 1,5м.
Так как камера разворота имеет большую площадь обнажения кровли, то ее крепят анкерной крепью. Крепь устанавливается в виде сетки.
3.4.4 Режим работы очистного забоя. Состав бригады и сменного звена
На горном участке применяется очистной комплекс Урал-10АМБ.
Комплекс Урал-10АМБ применяется для очистных работ по отработке блока камерной системой разработки. В состав комплекса входят: самоходный вагон 5ВС-15М, бункер перегружатель БП-14А, очистной комбайн Урал-10АМБ.
Для организации бесперебойных работ предусмотрен четырёхсменный режим работы: три смены являются добычными, а одна смена ремонтная. Длительность смены составляет 6 часов.
В добычную смену на комплексе работает звено в составе одного машиниста горно-выемочных машин (МГВМ) и одного или двух горнорабочего очистного забоя (ГРОЗ). МГВМ осуществляет управление комбайном во время выемки, осматривает комбайн после завершения цикла. ГРОЗ занимается доставкой руды на ленточный конвейер с помощью самоходного вагона 5ВС-15М и помогает машинисту при осмотре и обслуживании комбайна.
В ремонтную смену должны присутствовать МГВМ, ГРОЗ и электрослесарь участка. Все ремонтные работы ведутся по указаниям начальника участка (заместителя).
Все работы производятся по утверждённым паспортам и в соответствии с инструкциями, разработанными для конкретного вида работ. Для обеспечения отсутствия простоев в добычные смены должна быть хорошо налажена своевременная доставка запасных частей, материалов, своевременно выполняться текущие и запланированные ремонты.
3.4.5 Технология ведения очистных работ
Очистная выемка в одном крыле блока производится одним комбайновым комплексом. Из каждой камеры разворота проходится по два очистных хода, разделенных междукамерными целиками. Камеры разворота комбайна разделываются с опережением фронта очистных работ до 50м. Минимальное количество подготовленных камер разворота должно быть не менее двух за исключением стадии доработки последних камер в блоке.
Зарубка комбайна на очистной ход осуществляется на длину 15-20м. При зарубке комбайна погрузка породы осуществляется на самоходный вагон 5ВС-15М. При завершении зарубки комбайна производится прицепка бункера-перегружателя БП-14А, после чего отбитая горная масса аккумулируется в бункере-перегружаетеле, а лишь затем производится перегрузка породы на самоходный вагон, который производит отгрузку на скребковый конвейер СП-202, который в свою очередь перегружает породу на блоковый ленточный конвейер КЛ-600 (КЛЗ-500).
Технология работы комбайна Урал-10АМБ:
- установка режущего органа в верхнее рабочее положение (контроль – по монитору);
- подача хода на забой, зарубка режущего органа на глубину 0.2-0.35м;
- прекращение подачи хода комбайна, опускание вращающегося режущего в - нижнее рабочее положение – ниже почвы выработки до 0.05м (контроль – по монитору);
- установка режущего органа в верхнее рабочее положение (контроль – по монитору) – далее операции повторяются.
Отгон машины из пройденной выработки (очистного хода), осуществляется на рабочей скорости только с включенным режущим органом.
3.4.6 Расчёт производительности проходческо-очистного комплекса
Техническая производительность комбайна, т/мин Qк
=4
Грузоподъёмность самоходного вагона, тонн q = 15
Средняя скорость движения вагона ,м/мин v = 150
Время разгрузки вагона (бункера-перегружателя), мин
(принимается tp
= 1,2)
Коэффициент использования комплекса в смене
(принимается α = 0,4…05)
Продолжительность зарубки час
(принимается Tз
= 6…12 час)
Длина участка зарубки, м
(принимается Lз
= 15...20 м)
Продолжительность отгона комбайна, час
(принимается Tо
= 3…5 час)
Длина очистного хода, м L = 170
Площадь поперечного сечения очистного хода, м2
S = 12,41
Длина самоходного вагона, м Lв
= 8,4
Плотность руды, т/м3
γ = 2,15
Техническая средневзвешенная производительность комплекса определяется по формуле:
(3.4.6.1)
Продолжительность проходки одного хода после зарубки комбайна определяется по формуле:
(3.4.6.2)
Продолжительность отработки одного хода:
(3.4.6.3)
где - коэффициент, учитывающий ремонтно-подготовительные смены, обычно k
рп
= 1,33.
Эксплуатационная производительность комплекса:
(3.4.6.4)
где t
см
– продолжительность смены, час
Суточная производительность комплекса:
(3.4.6.5)
где nсм
– общее число смен в сутки.
Проектная месячная производительность комплекса:
(3.4.6.6)
где n
– число рабочих смен по добыче в месяц
(3.4.6.7)
где Тк
– месячный календарный фонд рабочего времени, сутки;
Трп
– месячные затраты времени на планово-предупредительные ремонты,
сутки.
Месячное подвигание фронта очистных работ по длине панели:
(3.4.6.8)
Где n
– число рабочих дней по добыче в месяц, сут. Вк
– ширина очистной камеры, м. Т
– продолжительность отработки одного хода, час. m
– число ходов в камере.
1.
2. 
3. 
4. 
5. 
6. 

7.
3.5 НОРМАТИВНОЕ ИЗВЛЕЧЕНИЕ РУДЫ И
ПОЛЕЗНОГО КОМПОНЕНТА ПО СИСТЕМЕ
РАЗРАБОТКИ
3.5.1 Расчёт балансовых запасов и полезного компонента (NaCl) панели
К балансовым запасам калийного пласта (панели) относят только ту часть геологических запасов, которую экономически целесообразно разрабатывать при современных способах добычи и обогащения.
К извлекаемым запасам калийного пласта (панели) относят ту часть балансовых запасов, которую можно извлечь при ведении горно-подготовительных работ и очистных работ.
Балансовые запасы руды в панели составляют:
(3.5.1.1)
где L
0
- длина отрабатываемой части панели, м;
М
- ширина панели, м;
m
- балансовая мощность пласта, м;
γ
- плотность руды, т/м3
.
Содержание NaCl в балансовых запасах руды составляет:
(3.5.1.2)
где mi
– мощность слоев, включенных в балансовые запасы, м;
α
i
NaCl
– содержание NaCl в слоях, %.
Запасы полезного компонента в балансовых запасах руды составляют:
(3.5.1.3)
Приведём пример расчёта
1. 
2. 
3. 
3.5.2 Расчёт извлекаемых запасов руды в панели
Расчет добычи руды из отдельно взятых подготовительных выработок
(
3.5.2.1)
где Li
-
длина выработки, расположенной в отрабатываемой части панели, м;
Si
- площадь поперечного сечения выработки, м2
Добыча из блоковых подготовительных выработок:






Общее число подготовительных выработок составит 24, учитывая то, что в панели имеется 8 блоков.
Расчет содержания NaCl в руде, добытой из отдельно взятых подготовительных выработок
Для определения содержания NaCl в руде, добытой из подготовительных выработок необходимо учитывать, что выработки пройдены не на всю мощность продуктивного пласта и их высота составляет 2,9м.
Содержание NaCl в руде, добытой из отдельных подготовительных выработок:
(3.5.2.2)

Добыча руды из горно-подготовительных выработок
Добыча руды из горно-подготовительных работ составляет:
(3.5.2.3)

Расчёт добычи руды при камерной системе разработки
При панельно-блоковой отработке с оставлением жёстких целиков объём добычи составит:
(3.5.2.4)
где nx
– число очистных ходов в камере;
Sx
– площадь сечения очистного хода, м2
;
lx
–
длина очистного хода(камере), м;
nk
–
число очистных камер в панели;
Что бы узнать число очистных камер в панели рассчитаем число камер в блоке:
(3.5.2.5)
где – ширина панели, м;
20
– ширина межпанельного целика, м;
с
– ширина камеры (с
= 15,3м).

Известно, что в панели будет 8 блоков. Отсюда количество камер в панели составит:

Отсюда объём добычи составит:

3.5.3 Расчёт извлекаемых запасов полезного компонента (NaCl) панели
Расчет средневзвешенного содержания NaCl в руде, добываемой из горно-подготовительных работ
Содержание NaCl в добытой руде:
(3.5.3.1)

Расчёт добычи NaCl из горно-подготовительных работ
(3.5.3.2)
Содержание NaCl в руде, добытой при очистных работах

Расчёт добычи NaCl из очистных работ
(3.5.3.3)

Добыча NaCl из погашенных запасов
(3.5.3.4)

Добыча руды из погашенных запасов панели
(3.5.3.5)

Средневзвешенное содержание NaCl в руде из погашенных запасов панели
(3.5.3.6)

4. ПРОВЕТРИВАНИЕ ПАНЕЛИ
4.1 ПРОВЕТРИВАНИЕ ОЧИСТНЫХ КАМЕР НА СТАДИИ ИХ ПРОВЕДЕНИЯ
Проветривание тупиковых выработок в процессе проходки производится всасывающим способом, вентилятором установленным, на комбайне, при этом должна быть обеспечена возможность быстрого перехода на нагнетательный способ проветривания вентилятором местного проветривания.
Так как отработка блока производится по двухсторонней схеме, то в этом случае производится регулирование воздушного потока путем перекрытия одного из блоковых вентиляционных штреков в зависимости от того, в каком крыле блока производится очистная выемка.
4.1.1 Расчёт количества воздуха, необходимого для
проветривания камер
Расчет количества воздуха, необходимого для проветривания камеры производится с учетом следующих факторов:
- взрывоопасные газы;
- температура воздуха;
- минимальная допустимая скорость движения воздуха;
- наибольшее количество людей;
- выхлопные газы ДВС.
Расчёт необходимого количества воздуха по фактору "взрывоопасные газы".
(4.1.1.1)
где К
п
= 1,43 - коэффициент, учитывающий способ подачи воздуха в тупиковую выработку, ( проветриваемую с помощь ВМП и трубопровода ) ;
К
у
= 1,14 - коэффициент, учитывающий утечки воздуха в трубопроводе при длине трубопровода 200м и f =400 - 600мм ;
g
- газообильность пласта по условному метану (до завершения работ по исследованию газоносности пластов каменной соли в расчетах принимаем данные, аналогичные II горизонту – 0,1 м³
/м³
) ;
К
д
= 0,9 - коэффициент дегазации отбитой горной массы при комбайновом способе отбойки руды;
К
н
= 1,57-коэффициент неравномерности газообильности (для II горизонта);
i
- объёмный вес руды ( для горизонта –305м -215 т/м³
) ;
J
- производительность комбайна для Урал-10АМБ – 4 т/мин);
C
= 0,5% - требуемая расчётная концентрация условного метана ;
C
= 0% - концентрация условного метана в воздухе, поступающем в выработку.

Расчёт необходимого количества воздуха по фактору "температура воздуха".
(4.1.1.2)
где К
п
= 1,43 - коэффициент, учитывающий способ подачи воздуха в тупиковую выработку, ( проветриваемую с помощью ВМП и трубопровода ) ;
К
у
= 1,14 - коэффициент, учитывающий утечки воздуха в трубопроводе при длине трубопровода 200м и Ø =400 - 600мм ;
К
к
= 0,4 – 0,6 – коэффициент, учитывающий условия работы комплекса (для подготовительных выработок) ;
К
з
= 50 – коэффициент, учитывающий тип забоя (тупиковый комбайновый забой );
N
дв
– общая мощность электродвигателей оборудования (для Урал-10АМБ Nдв
=570 кВт);
η
-
средневзвешенный КПД оборудования (для Урал-10АМБ η
=0,91);
T
– температура, поступающего в выработку воздуха (для II горизонта рудника 1РУ – 17С );
Кт
– коэффициент, учитывающий вынос тепла (при всасывающей схеме проветривания тупиковых выработок, принимается равным 0,9).

Расчёт необходимого количества воздуха по "минимальной допустимой скорости".
(4.1.1.3)
Где К
п
= 1,43 - коэффициент, учитывающий способ подачи воздуха в тупиковую выработку, (проветриваемую с помощью ВМП и трубопровода) ;
S
к
- площадь сечения одного комбайнового хода для Урал-10АМБ равна 12,41м².

Расчёт количества воздуха, необходимого для проветривания
выработок по наибольшему количеству людей.
(4.1.1.4)
где g
ч
= 6 м³
/мин. - норма воздуха на одного человека.
N л
= 10 - максимальное количество людей в смене.

Таким образом, количество воздуха, подаваемого к всасу ВМП для проветривания тупиковой выработки, принимается равным 167,27м3
/мин.
Расчёт количества воздуха, необходимого для разжижения
выхлопных газов ДВС.
Количество воздуха, проходящее по транспортным выработкам, в которых предусмотрено периодическое использование машин с ДВС, должно быть достаточным для разжижения выхлопных газов ДВС, т.е. быть не меньше, чем определённое по формуле:
(4.1.1.5)
где N - номинальная мощность двигателей с ДВС;
q - 5м3
/мин. на 1л.с. номинальной мощности одновременно работающих машин с ДВС
- для использования одной единицы МТЗ-80.
По блоковому транспортному штреку воздуха должно подаваться не менее 375м³
/мин.
4.1.2 Выбор вентилятора местного проветривания и места его установки
Для проветривания тупиковых очистных ходов комбайна Урал-10АМБ принимается вентилятор местного проветривания (ВМП) типа ВМЭ-6 с производительностью 205 – 410 м3
/мин и давлением 310 – 770даПа. ВМП устанавливается на блоковом транспортном штреке.
4.2 Расчёт количества воздуха необходимого для проветривания
панели (блока).
Согласно расчётам, проведенным в пункте 4.1.1, для проветривания блока принимается наибольшее количество воздуха подаваемого в блок. Следовательно, для проветривания блока необходимо принять 375м3
/мин подаваемого воздуха.
5 УЧАСТКОВЫЙ ТРАНСПОРТ
5.1 ТРАНСПОРТИРОВАНИЕ РУДЫ ОТ
ОЧИСТНОГО ЗАБОЯ ДО ВЫРАБОТОК ГЛАВНОГО НАПРАВЛЕНИЯ
Транспортирование руды от очистного забоя до выработок главного направления производится по следующей схеме.
Отбитая комбайном соль аккумулируется в бункере перегружателе БП-14А (техническая характеристика БП-14А приведена в таблице 3.3.1.2), откуда перегружается в самоходный вагон 5ВС-15М (таблица 3.3.1.3) и доставляется к скребковому конвейеру СП-202 (таблица 3.3.1.4), который перегружает руду на блоковый ленточный конвейер КЛ-600(КЛЗ-500)(таблица 3.3.1.5), доставляющий соль на панельный ленточный конвейер. Ленточными конвейерами главного направления и околоствольного двора, руда транспортируется к подземному бункеру ствола №2 и скипами выдаётся на поверхность.
5.2 ПЕРЕВОЗКА ЛЮДЕЙ, ОБОРУДОВАНИЯ И
МАТЕРИАЛОВ ПО ГОРНЫМ ВЫРАБОТКАМ
При посадке в клеть, движении, входе и выходе необходимо выполнять требования стволового.
В клети необходимо располагаться вдоль длинных её сторон лицом к ближайшей двери, рукой держаться за поручень, ноги должны быть расслаблены и слегка согнуты в коленях. Запрещается становиться на рельсы в клети, так как это может привести к травме.
Во избежание травмирования или создания опасной обстановки опускающимся в шахту или выезжающим из нее запрещается: открывать предохранительные двери ствола на приемных площадках и двери клети: заходить в клеть или выходить из нее без разрешения стволового; опираться на двери; высовываться из клети, выставлять за борта перевозимые предметы, перевозить с собой громоздкие предметы, мешающие окружающим или выступающие за пределы клети, заходить в клеть или автомашину в количестве свыше допустимой нормы.
Перевозимые совместно с людьми инструменты и предметы с острыми кромками должны быть зачехлены и безопасно расположены, чтобы не причинить повреждений окружающим.
В клети или автомашине необходимо вести себя спокойно, не толкаться, не шуметь, не затевать потасовки.
На действующих и строящихся рудниках перевозка работников обязательна, если расстояние до места работ 1км и более.
Для перевозки работников по горным выработкам должны применяться автомашины, специально оборудованные и допущенные к применению Проматомнадзором.
Кузова автомашин должны быть оборудованы сиденьями заводской конструкции, металлической крышей и боковыми стенками на всю их высоту.
Проёмы в кузовах автомашин для посадки работников должны иметь ширину не менее 0,7м и быть оборудованы ограждающими приспособлениями.
В выработках, по которым движется самоходный транспорт, полотно дороги должно быть ровным, обеспечивающим движение машин без тряски и резких толчков. В тех случаях, когда почва выработок сложена из глинистых пород или подвержена пучению, что приводит к образованию неровностей, дороги должны периодически выравниваться механическим способом.
Предельные уклоны и подъёмы дорог устанавливаются проектной документацией в зависимости от горно-геологических условий, характеристики применяемого самоходного транспорта и условий его эксплуатации.
При перевозке работников автомашинами скорость движения не должна превышать 20км/час. На прямолинейных участках горизонтальных выработок длиной более 500м, имеющих твердое и ровное покрытие, максимальная скорость гружёных и порожних автомобилей для перевозки работников может быть увеличена до 40км/час по разрешению главного инженера рудника.
Во время движения запрещается высовываться из автомашины, производить посадку и высадку работников до её полной остановки.
В автомашинах, предназначенных для перевозки работников, могут совместно перевозиться только инструменты и запасные части, которые не выступают за габариты кузова. При этом они должны располагаться в местах, исключающих травмирование работников. Прицепку груза необходимо производить при полностью остановленном транспортном средстве и заглушенным двигателем, согласовывая свои действия с водителем.
Запрещается:
- доставка в автомашинах, предназначенных для перевозки работников совместно с ними, взрывчатых, легковоспламеняющихся и едких материалов;
- перевозка работников по горным выработкам самоходным транспортом, не предназначенным для этих целей;
- нахождение в автомашине работников сверхустановленного количества посадочных мест
- ходить, ездить на конвейерах, транспортировать грузы на ленточных конвейерах, бросать на конвейеры посторонние предметы (металл, лес и т.д.)
- переходить с одной стороны ленточного конвейера на другую можно только по специальным переходным мостикам. Подниматься на мостик или спускаться с него следует только лицом к конвейеру, держась за поручни.
Для доставки людей к месту работы используются автомашины: Minka-26, МТ-353М2, МГЛ-363М, М-22А.Для дежурства на ПВРКТ, службе автоматизации и для оказания скорой помощи используются автомашины мини-Минка/А, миди-Минка, УАЗ-315/123.
Для доставки материалов и оборудования используется автотракторная техника различных марок. Доставка тяжёлого оборудования производится машинами PGT-10,12 и PST-10, PFL-18 (фирма Паус, Германия), МД-12Т “Амкодор”; доставка материалов, ГСМ, крепления, запасных частей производится тракторами МТЗ-572,82, ТДТ-55, Т-25, СШ-2540, а также грузовыми автомобилями МГЛ-363.
6 ЭКОНОМИЧЕСКАЯ ЧАСТЬ
6.1 ОРГАНИЗАЦИЯ РАБОТ НА УЧАСТКЕ
На горном участке применяется проходческий комплекс Урал-10АМБ.
Комплекс Урал-10АМБ применяется для ведения очистных работ при камерной системе разработки. В состав комплекса входят: самоходный вагон 5ВС-15М, бункер перегружатель БП-14А, очистной комбайн Урал-10 АМБ.
Для организации бесперебойных работ очистных и проходческих комплексов на участке предусмотрен четырёхсменный режим работы: три смены являются добычными, а одна смена ремонтная. Длительность смены составляет 6 часов.
В добычную смену на комплексе работает звено в составе одного машиниста горно-выемочных машин (МГВМ) и одного или двух горнорабочего очистного забоя (ГРОЗ). МГВМ осуществляет управление комбайном во время выемки, осматривает комбайн после завершения цикла. ГРОЗ занимается доставкой руды на ленточный конвейер с помощью самоходного вагона 5ВС-15М и помогает машинисту при осмотре и обслуживании комбайна.
В ремонтную смену должны присутствовать МГВМ, ГРОЗ и электрослесарь участка. Все ремонтные работы ведутся по указаниям начальника участка (заместителя).
Все работы производятся по утверждённым паспортам и в соответствии с инструкциями, разработанными для конкретного вида работ. Для обеспечения отсутствия простоев в добычные смены должна быть хорошо налажена своевременная доставка запасных частей, материалов, своевременно выполняться текущие и запланированные ремонты.
Составление графика планово-предупредительных ремонтов
На предприятиях минеральных удобрений и химической промышленности проводится эксплуатация, техническое обслуживание и ремонт оборудования на основе системы планово-предупредительных ремонтов ППР.
В основе составления графика планово-предупредительных ремонтов (ППР) лежат утвержденные ремонтные нормативы, отраженные в справочнике «Система технического обслуживания и ремонта оборудования» и структура ремонтного цикла.
Ремонтный цикл – это время работы оборудования между двумя капитальными ремонтами.
Структура ремонтного цикла – это количество и последовательность входящих в ремонтный цикл ремонтов и осмотров.
Для составления структуры ремонтного цикла необходимо определить:
1. Количество текущих ремонтов по формуле:
, (6.1.1)
где Дк
– продолжительность работы в часах между капитальными ремонтами;
Дт
– продолжительность работы в часах между текущими ремонтами, К
– количество капитальных ремонтов, К
=1.
2. Длительность ремонтного цикла определяется по формуле:
, (6.1.2)
где 8760 – общее число рабочих часов оборудования в год.
3. Время простоя оборудования во всех видах ремонтов определяется по формулам:
Ппк
= Пк
· Ргод.к
, (6.1.3)
Ппт
= Пт
· Ргод.т
, (6.1.4)
Пп
= Ппк
+ Ппт
, (6.1.5)
где Пк
и Пт
– время простоя оборудования в капитальном и текущем ремонтах соответственно, в часах,
Ргод.к
и Ргод.т
– количество капитальных и текущих ремонтов соответственно.
4. Эффективный фонд времени работы оборудования определяется по формуле:
Фэф
= 8760–Пп
,
(6.1.6)
где 8760
– календарный годовой фонд рабочего времени в часах,
Пп
– время простоя оборудования во всех видах ремонтов, в часах.
Приведем пример расчета:
1. Т = Дк
/ Дт
– 1 = 10800/1200–1=8 текущих ремонтов
2. Ц = Дк
/ 8 760 = 10800/8760=1,23 года
3. Ппк
= Пк
· Ргод.к
=960 ·1=960 часов
4. Ппт
= Пт
· Ргод.т
=96 · 6=576 часов
5. Пп
= Ппк
+ Ппт
=960+576=1536 часов
6. Фэф
= 8760–Пп
=8760–1 536=7224 часов
Таблица 6.1.4
Наименование оборудования
|
Норма времени непрерывной работы между ремонтами и время простоя в ремонте, часы
|
Условные обозначения ремонта
|
Годовой простой в ремонтах часы Пп
|
Эффективный фонд времени работы оборудования, часы, Фэф
|
Дт
|
Пт
|
Дк
|
Пк
|
1
|
2
|
3
|
4
|
5
|
6
|
7
|
8
|
9
|
10
|
11
|
12
|
1. Урал-10АМБ
|
1 200
|
96
|
10 800
|
960
|
Т
|
Т
|
Т
|
К
|
1 536
|
7 224
|
2. 5ВС-15М
|
1 200
|
96
|
10 800
|
960
|
Т
|
Т
|
Т
|
К
|
1 536
|
7 224
|
2. БП-14
|
1 200
|
96
|
10 800
|
960
|
Т
|
Т
|
Т
|
К
|
1 536
|
7 224
|
Годовой график ППР
6.2 РАСЧЁТ ЗАТРАТ НА ОСНОВНЫЕ И
ВСПОМОГАТЕЛЬНЫЕ МАТЕРИАЛЫ,
ИСПОЛЬЗУЕМЫЕ ПРИ ЭКСПЛУАТАЦИИ
ОБОРУДОВАНИЯ
Материалы – это различные вещественные элементы, используемые преимущественно в качестве предмета труда для изготовления продукции и обслуживания производства.
Предметы труда – целиком потребляются в течение одного производственного цикла, изменяют свою натуральную форму, образуя готовый продукт, целиком переносят на него свою стоимость и возмещаются (окупаются) после каждого производственного цикла.
Материалы подразделяются на основные, из которых непосредственно изготавливается продукция (в натуральной форме входят в ее состав), и вспомогательные используемые для производственно-эксплуатационных нужд предприятия и не образующие вещественного содержания изготавливаемой продукции. Одни и те же материалы в зависимости от их использования могут быть основными или вспомогательными.
Расчёт затрат по статье «Основные и вспомогательные материалы» ведут исходя из норм расхода материалов и действующей цены на него.
Затраты на материалы определяются по формуле:
, (6.2.1)
где Рм
– годовой расход материалов;
Ц
–цена за единицу материала, руб.
Наименование основных и вспомогательных материалов, их годовой расход, цены за единицу и затраты на каждый вид материалов приведены в таблице 6.2.1.
Таблица 6.2.1
Затраты на основные и вспомогательные материалы
Наименование материалов
|
Единица измерения
|
Расход материала за год (Рм
)
|
Цена за единицу материала, руб (Ц)
|
Совокупные затраты на материалы, руб (Зм
)
|
Основные материалы:
1. Резцы Д6-22
2. Кабель КГС 4×16
3. Металл
4. Лес
|
шт.
м
кг
м3
|
1822,9
5231,4
82042,5
301,2
|
3053,49
11152
2375,4
5967,566
|
5566206,9
58340572,8
194883754,5
1797430,9
|
Итого по основным материалам
|
260587965,1
|
Вспомогательные материалы:
1. Сырая резина
2. Крепь анкерная
“Эстонсланец”
3. Мыло
4. Лепестки
5. Лакоткань
6. Лампочки на 127 В
|
кг
шт.
шт.
шт.
м
шт.
|
120
5600
811
6800
83
460
|
8568
4054
320
319
5895
800
|
1028160
22702400
259520
2169200
489285
368000
|
Итого по
вспомогательным
материалам
|
27016565
|
Итого совокупные затраты
|
287604530,1
|
6.3 РАСЧЕТ ЗАТРАТ НА
ЭЛЕКТРОЭНЕРГИЮ
Расход энергии планируется отдельно по ее видам и направлениям использования.
Расход электрической энергии на двигательную силу ( ) определяется на основании мощности оборудования и его загрузки по формуле:
, (6.3.1)
где О
– количество единиц оборудования данного типа;
Мд
– мощность двигателя данного оборудования, кВт;
Фэф
– планируемый полезный фонд времени работы оборудования, ч;
Кз.о
.
– коэффициент загрузки оборудования (нормативное значение 0,9-0,96);
Км
– коэффициент машинного времени работы оборудования (нормативное значение 0,6 — 0,7);
Кд
– коэффициент полезного действия (нормативное значение 0,8).
Расход энергии на осветительные цели (Эосв
) рассчитывается как:
, (6.3.2)
где – количество светильников данного типа;
– мощность светильника, Вт;
– продолжительность осветительного периода, ч.
Общий расход электроэнергии определяется как сумма ее расхода по всем направлениям: двигательная, осветительная и прочая (вентиляция, и т. п.).
Затраты на электроэнергию определяются следующим образом:
, (6.3.3)
, (6.3.4)
где – цена за каждый кВт электроэнергии потребленной на технологические цели, руб.;
– цена за каждый кВт электроэнергии потребленной на освещение, руб.
Приведем пример расчета:
Для Урал-10АМБ
Для 5ВС-15М
Для БП-14А



Расчет затрат на потребляемую электроэнергию представлен в таблице 6.3.1.
Таблица 6.3.1
Наименование электрооборудования
|
Количество оборудования, штуки
|
Установленная мощность двигателя данного оборудования, кВт (Nуст.
)
|
Суммарная мощность, кВт (Nсум.
)
|
Коэффициент загрузки оборудования (Кз.о.
)
|
Коэффициент машинного времени работы оборудования (Ки.
)
|
Годовой эффективный фонд времени работы электродвигателей, часы (Фэф
)
|
Коэффициент полезного действия, доли (Кд.
)
|
Количество потребленной электроэнергии за год, кВт
|
1
|
2
|
3
|
4
|
5
|
6
|
7
|
9
|
10
|
1. Урал-10АМБ
2. 5ВС-15М
3. БП-14
|
1
1
1
|
570
127
43
|
570
127
43
|
0,96
0,96
0,96
|
0,7
0,7
0,7
|
7224
7224
7224
|
0,8
0,8
0,8
|
3458851,2
770656,32
260930,88
|
Итого
|
-
|
-
|
740
|
-
|
-
|
4490438,4
|
Затраты на электроэнергию
6.4 РАСЧЕТ ЗАТРАТ НА АМОРТИЗАЦИЮ ОБОРУДОВАНИЯ
Амортизация – это постепенное перенесение стоимости основных фондов на производимую продукцию в целях накопления денежных средств для полного их возмещения (воспроизводства) в результате физического или морального износа. Денежным выражением размера амортизации являются амортизационные отчисления, которые соответствуют степени износа основных фондов.
Величина амортизационных отчислений определяется с помощью нормы амортизации. Это установленный в плановом порядке годовой процент возмещения стоимости основных фондов. Нормы амортизации установлены по видам основных фондов, включаемых в группы по классификации.
Амортизационные отчисления рассчитываются методом прямого счета:
, (6.4.1)
где – стоимость оборудования, руб.;
– годовая норма амортизации, %.
Стоимость оборудования определяется по формуле:
, (6.4.2)
где – цена за единицу оборудования, руб.;
– количество единиц однотипного оборудования.
Приведем пример расчета амортизационных отчислений:
Для Урал-10АМБ:

Для 5ВС-15М:


Для БП-14:


Данные расчета амортизационных отчислений представлены в таблице 6.4.1.
Таблица 6.4.1
Затраты на амортизацию
Наименование
оборудования
|
Количество оборудования штуки (n)
|
Цена за единицу оборудования тыс руб (Цед)
|
Стоимость оборудования тыс. руб. (Соб)
|
Норма амортизации, %
|
Годовая сумма амортизационных отчислений, тыс руб (Ао)
|
1. Урал-10АМБ
2. 5ВС-15М
3. БП-14
|
1
1
1
|
544532584
269012223
72854557
|
544532584
269012223
72854557
|
20
25
20
|
544532584
67253055,75
14570911,4
|
Итого
|
-
|
-
|
886399364
|
-
|
626356551,15
|
6.5 РАСЧЁТ ЗАРАБОТНОЙ ПЛАТЫ И
ОТЧИСЛЕНИЙ ОТ ФОНДА ОПЛАТЫ ТРУДА
Для определения затрат по статье «Заработная плата» необходимо определить численность рабочих и служащих по эксплуатации оборудования. Для расчета списочной численности рабочих составляется баланс рабочего времени одного рабочего.
Баланс рабочего времени одного рабочего представлен в таблице 6.5.1
Таблица 6.5.1
Баланс рабочего времени одного рабочего
Наименование показателей
|
По плану за год, часы и дни
|
Календарный фонд времени (дни)
Количество нерабочих дней - всего
в том числе:
- праздничных
- выходных
Номинальный фонд рабочего времени
Неявки на работу – всего
в том числе:
- очередные отпуска
- отпуска по учебе
- по болезни
- разрешенные законом (гос.обязанности)
- разрешенные администрацией
Эффективный фонд времени (дни)
Средняя продолжительность рабочего дня (часы)
Реальное число рабочих часов в год
Внутрисменные простои (чел-часов)
Фактическое число рабочих часов в день
Эффективный фонд рабочего времени одного рабочего (часы)
|
365
110
9
101
255 (365-110)
92
66
15
8
1
2
163 (255-92)
6,45
1051 (163·6,45)
25
6,3
1026
|

Номинальный фонд рабочего времени равен разности между календарным фондом рабочего времени, выходными и праздничными днями:
(6.5.1)
Эффективный фонд рабочего времени в днях равен номинальному фонду рабочего времени за вычетом общей суммы неявок на работу:
(6.5.2)
Эффективный фонд рабочего времени одного рабочего определяется произведением эффективного фонда рабочего времени (в днях) на среднюю продолжительность рабочего дня (часы):
(6.5.3)
Реальное число рабочих часов в год определяется произведением эффективного фонда рабочего времени (в днях) на среднюю продолжительность рабочего дня (часы):
(6.5.4)
Эффективный фонд рабочего времени одного рабочего в часах определяется вычитанием из реального числа рабочих часов льготных часов подросткам, перерывов кормящим матерям, внутрисменных простоев:

(6.5.5)
Фактическое число рабочих часов в день определяется делением эффективного фонда рабочего времени (в часах) на эффективный фонд рабочего времени (в днях):
(6.5.6)
Заработная плата служащим начисляется исходя из установленных для них окладов, и рассчитывается путём умножения должностного оклада на 12 месяцев. Для оплаты труда рабочих используются часовые тарифные ставки. Разряды рабочих и соответствующие им тарифные ставки представлены в таблице 6.5.2.
Таблица 6.5.2
Часовые тарифные ставки
РАЗРЯД
|
IV
|
V
|
VI
|
VII
|
Часовая тарифная ставка, руб.
|
7 105,3
|
7 829,4
|
8 598,8
|
9 187,11
|
Фонд заработной платы рабочих включает основную заработную плату, которая выплачивается работникам за отработанное время, и дополнительную заработную плату, выплаты которой производятся в соответствии с действующим законодательством:
, (6.5.7)
где – основная заработная плата, руб.;
– дополнительная заработная плата, руб.
Основная заработная плата для рабочих рассчитывается по формуле:
, (6.5.8)
где – тарифный фонд заработной платы, руб.;
– доплата за работу в ночное время, руб.;
– доплата за работу в вечернее время, руб.;
– размер премии, руб.;
– доплата за работу в праздничные дни, руб.
1.Тарифный фонд заработной платы определяется по формуле:
, (6.5.9)
где – часовая тарифная ставка, руб.;
 – эффективный фонд рабочего времени одного рабочего в часах;
– численность рабочих одной профессии, человек.
2. Доплата за работу в ночное время производится по повышенным на 40% тарифным ставкам за каждый час ночной работы. Ночным считается время с 2200
вечера до 600
утра.
При 12 часовом рабочем дне в условиях ПО «Беларуськалий» одна смена считается дневной, а другая ночной, тогда доплата за работу в ночное время составит:
(6.5.10)
При 8 часовом рабочем дне одна смена считается дневной, одна вечерней и одна ночной, тогда доплата за работу в ночное время составит:
(6.5.11)
3. Доплата за работу в вечернее время при 8 часовом рабочем дне производится по повышенным на 20% тарифным ставкам. Вечерним считается время с 18 00 до 20 00 часов вечера. Формула расчета доплаты за работу в вечернее время имеет вид:
(6.5.12)
4. Доплата за работу в праздничные дни при продолжительности смены 12 часов определяется по формуле:
Дпр
= ЗПт
/ Фэффект(дни)
· Кпр
· 2/4
, (6.5.13)
где ЗПт
– тарифный фонд оплаты труда, руб.;
Фэффект(дни)
– эффективный фонд рабочего времени одного рабочего в днях;
Кпр
– количество праздничных дней в году, из баланса рабочего
времени.
Доплата за работу в праздничные дни при продолжительности смены 8 часов рассчитывается по формуле:
Дпр
= ЗПт
/ Фэффект(дни)
· Кпр
· ¾
(6.5.14)
5. Размер премии определяется рабочим положением о премировании и начисляется исходя из тарифного фонда, с учетом всех видов доплат кроме доплаты за работу в праздничные дни:
ПР = (ЗПт
+ Дн
+ Дв
) · %ПР / 100%
, (6.5.15)
где %ПР
– процент премии (определяется из положения о премировании).
Фонд дополнительной заработной платы состоит из оплаты отпусков и оплаты дней выполнения государственных обязанностей, рассчитывается по формуле:
ЗПдоп
= Оо
+ Ого
, (6.5.16)
где Оо
– размер оплаты за очередные и дополнительные отпуска, руб.;
Ого
– размер оплаты государственных обязанностей, руб.
1. Размер оплаты за очередные и дополнительные отпуска определяется по формуле:
Оо
= ЗПосн
/ Фэффект(дни)
· Котп
, (6.5.17)
где Котп
– количество дней отпуска, из баланса рабочего времени.
2. Размер оплаты за выполнение государственных обязанностей определяется по формуле:
Ого
= ЗПосн
/ Фэффект(дни)
· Кго
, (6.5.18)
где Кго
– количество дней выполнения государственных обязанностей (берется из баланса рабочего времени).
Общий годовой фонд оплаты труда рабочих определяется по формуле:
ЗПобщ
= ЗПосн
+ ЗПдоп
, (6.5.19)
где ЗПосн
– основной фонд оплаты труда рабочих, руб.;
ЗПдоп
– дополнительный фонд оплаты труда рабочих, руб.
Приведем пример расчета заработной платы для МГВМ:
1
. ЗПт
= Т · Фэффект(дни)
· Ч = 9187,11 · 1026 · 6=56555849,16 руб.
2
. Дн
= ЗПт
· 0,4 / 3 = 56555849,16 · 0,4 / 3 = 7540779,89 руб.
3
. Дв
= ЗПт
· 0,2 / 3 = 56555849,16 · 0,2 / 3 = 3770389,94 руб.
4
. Дпр
= ЗПт
/ Фэффект(дни)
· Кпр
· 3/4 = 56555849,16/163 × ×9·3/4=2342036,7 руб.
5
. ПР = (ЗПт
+ Дн
+ Дв
) · %ПР / 100% =(56555849,16+7540779,89+
+
3770389,94)35/100 = 23753456,65 руб.
6
. ЗПосн
= ЗПт
+ Дн
+ Дв
+ Дпр
+ ПР = 56555849,16+7540779,89+
+3770389,94+ 2342036,7+ 23753456,65 = =93962512,34руб.
7
. Оо
= ЗПосн
/ Фэффект(дни)
· Котп
=93962512,34/163 · 66 = =38046170,64руб.
8
. Ого
= ЗПосн
/ Фэффект(дни)
· Кго
=93962512,34/163 · 1 = 576457,13руб.
9
. ЗПдоп
= Оо
+ Ого
= 38046170,64+576457,13 = 38622627,77руб.
10
. ЗПобщ
= ЗПосн
+ ЗПдоп
= 93962512,34+38622627,77=
=132585140,11руб.
Данные расчетов представлены в таблице 6.5.3
Таблица 6.5.3
Расчет фонда оплаты труда
Показатель
|
Наименование профессии
|
МГВМ
|
ГРОЗ
|
Количество человек, чел.
|
6
|
3
|
Разряд
|
7
|
6
|
Часовая тарифная ставка, руб.
|
7 349,68
|
8 598,8
|
Отработано человеко-часов
|
1 026
|
1 026
|
Тарифный фонд заработной платы, руб.
|
56 555 849,16
|
26 467 106,4
|
Доплата за работу в ночное время, руб.
|
7 540 779,89
|
3 528 947,52
|
Доплата за работу в вечернее время, руб.
|
3 770 389,94
|
1 764 473,76
|
Доплата за работу в праздничные дни, руб.
|
2 342 036,7
|
1 096 030,48
|
Размер премии, руб.
|
23 753 456,65
|
11 116 184,69
|
ИТОГО фонд основной заработной платы, руб.
|
93 962 512,34
|
43 972 742,85
|
Оплата отпусков, руб.
|
38 046 170,64
|
17 804 914,28
|
Оплата гособязанностей, руб.
|
576 457,13
|
269 771,43
|
ИТОГО фонд дополнительной заработной платы, руб.
|
38 622 627,77
|
18 074 685,71
|
ИТОГО общий годовой фонд заработной платы, руб.
|
132 585 140,11
|
62 047 428,56
|
Общий фонд заработной платы составит:
ЗПобщ.
=132585140,11 + 62047428,56=194632568,67 руб.
Социальные отчисления рассчитываются отдельно от фонда заработной платы по следующим формулам:
Отчисления в фонд социальной защиты составляют 35% от общего фонда заработной платы:
ОТЧс.з
= ЗПобщ
· 35% / 100%
(6.5.20)
Отчисления на страхование от несчастных случаев составляют 1% от общего фонда заработной платы:
ОТЧн.с.
= ЗПобщ
· 1% / 100%
(6.5.21)
Приведем пример расчета социальных отчислений от фонда заработной платы основных рабочих:
ОТЧс.з
= ЗПобщ
· 35% / 100% = 194632568,67 · 0,35 =68121399,03руб
.
ОТЧн.с.
= ЗПобщ
· 1% / 100% = 194632568,67 · 0,01 =1946325,69руб.
6.6 СОСТАВЛЕНИЕ СМЕТЫ ЗАТРАТ
Смета затрат представляет собой сводную таблицу, с помощью которой определяют общие годовые затраты на обслуживание оборудования. Смета составляется на основании приведенных выше расчетов по статьям представленным в таблице 6.6.1.
Таблица 6.6.1
Смета годовых затрат на обслуживание оборудования
Наименование статей расходов
|
Сумма затрат, руб.
|
Удельный вес затрат в общей себестоимости, %
|
Основные материалы
Вспомогательные материалы
Затраты на электроэнергию
Затраты на амортизацию
Заработная плата основных рабочих
Отчисления в фонд социальной защиты
Страхование от несчастных случаев
|
260587965,1
27016565
1303446528
626356551,15
194632568,67
68121399,03
1946325,69
|
10,50
1,09
52,51
25,23
7,84
2,75
0,08
|
Итого
|
2482107902,64
|
100
|
6.7 РАСЧЁТ СЕБЕСТОИМОСТИ ДОБЫЧИ 1ТОНЫ РУДЫ
Основные технико-экономические показатели представлены в таблице. Порядок заполнения таблицы следующий:
Стоимость активной части основных фондов выписывается из таблицы расчета амортизационных отчислений.
Фондоотдача определяется по формуле:
ФО = Qгод
/ Соб
(6.7.1)
Фондоемкость определяется по формуле:
ФЕ = Соб
/ Qгод
(6.7.2)
Фондовооруженность определяется по формуле:
ФВ = Соб
/ Ч
, (6.7.3)
где Соб
– стоимость активной части основных фондов, руб.;
Ч
– численность основных (обслуживающих) рабочих, человек.
Количество потребляемой за год электроэнергии выписывается из таблицы.
Энерговооруженность определяется по формуле:
ЭВ = Эпотр
/ Ч
, (6.7.4)
где Эпотр
– количество потребленной электроэнергии за год, кВт.;
Ч
– численность основных (обслуживающих) рабочих, человек.
Фонд заработной платы основных рабочих выписывается из таблицы.
Среднемесячная заработная плата основных рабочих рассчитывается по формуле:
ЗПср.м
= ЗПобщ
/ Ч / 12
, (6.7.5)
где ЗПобщ
– заработная плата основных рабочих, руб.;
Ч
– численность основных рабочих, человек;
12
– число месяцев в году.
Производительность труда рабочих рассчитывается по формуле:
Птр
= Qгод
/ Ч
, (6.7.6)
где Qгод
– производительность очистного комплекса, т /год;
Ч
– численность рабочих, обслуживающих оборудование, чел.
Себестоимость добычи одной тонны руды:
S1
= СЗ / Qгод
, (6.7.7)
где СЗ
– совокупные затраты (итого по таблице), руб.;
Qгод
– годовая производительность очистного комплекса, тонн.
Приведем пример расчета:
ФО = Qгод
/ Соб
= 391485,12/ 886399364= 0,00004 т/руб.
ФЕ = Соб
/ Qгод
= 886399364/ 391485,12=2264
руб/т
ФВ = Соб
/ Ч = 886399364/ 9 = 9848818,22
руб./чел.
ЭВ = Эпотр
/ Ч =
4490438,4/ 9 = 498937,6 кВт/чел.
ЗПср.м
= ЗПобщ
/ Ч / 12 = 194632568,67 / 9 / 12 =1802153,41
руб.
Птр
= Qгод
/ Ч = 391485,12/ 9= 43498,4
т/чел.
S1
= СЗ / Qгод
=
2482107902,64/ 391485,12 = 6340,24 руб./т

Таблица 6.7.1
Основные технико-экономические показатели
Наименование показателей
|
Единица измерения
|
Величина
|
1. Производительность проходческого комплекса
|
т / год
|
391485,12
|
2.Стоимость активной части основных фондов
|
рублей
|
886399364
|
3.Фондоотдача
|
т / руб.
|
0,00004
|
4.Фондоемкость
|
руб. /т
|
2264
|
5.Фондовооруженность труда основных рабочих
|
руб. /чел
|
9848818,22
|
6.Количество потребляемой за год электроэнергии
|
кВт / год
|
4490438,4
|
7.Энерговооруженность труда основных рабочих
|
кВт / человека
|
498937,6
|
8.Фонд заработной платы основных рабочих
|
рублей
|
194 632 568,67
|
9.Среднемесячная заработная плата основных рабочих
|
рублей
|
1 802 153,41
|
10. Производительность труда основных рабочих
|
т / человека
|
43498,4
|
11. Себестоимость добычи одной тонны руды
|
руб./т
|
6340,24
|
7. ОХРАНА ТРУДА И ЭКОЛОГИЧНОСТЬ ПРОЕКТНЫХ РЕШЕНИЙ
7.1 ТРЕБОВАНИЯ ПРАВИЛ ТЕХНИЧЕСКОЙ БЕЗОПАСНОСТИ (ПТБ) К УСТРОЙСТВУ ВЫХОДОВ ИЗ ОЧИСТНЫХ ЗАБОЕВ
На каждом действующем руднике должно быть не менее двух (основной и запасной) отдельных выходов на поверхность из подземных горных выработок, приспособленных для передвижения (подъёма) работников и расположенных так, чтобы в одном из них направление вентиляционной струи было противоположным направлению вентиляционных струй в других выходах.
Каждый горизонт рудника должен также иметь не менее двух отдельных выходов на вышележащий горизонт или поверхность, приспособленных для передвижения (перевозки) работников. На вновь строящихся и реконструируемых рудниках, а также при подготовке новых горизонтов на действующих рудниках расстояние между выходами должно быть не менее 30м, а когда надшахтные здания и копры построены из несгораемого материала – не менее 20м.
На всех разветвлениях (сопряжениях) выработок, ведущих к выходам из рудника, должны быть прикреплены указатели с обозначениями наименования выработки, направлений к выходам на поверхность и расстояния до них. Указатели должны быть выполнены из светоотражающих материалов или освещены.
Две или несколько аэродинамически взаимосвязанных между собой выработок с одним направлением вентиляционной струи, приспособленные для передвижения работников, считаются одним запасным выходом.
После проходки новых центрально-расположенных шахтных стволов рудника до проектных горизонтов или углубки их до нового горизонта в первую очередь до начала проведения горизонтальных вскрывающих выработок должны проводиться работы по: проходке выработки для сбойки шахтных стволов между собой; армировке шахтных стволов и оборудованию постоянного или временного клетевого подъёма с парашютными устройствами. При фланговом расположении шахтных стволов в первую очередь (до проведения выработок, обеспечивающих второй выход) должны проводиться работы по армировке и оборудованию шахтных стволов постоянными или временными клетевыми подъёмами с парашютными устройствами.
В случае вскрытия нового горизонта одним шахтным стволом или вскрытия его уклонами в первую очередь проводятся выработки для обеспечения горизонта двумя выходами на поверхность или на верхний горизонт и эффективным проветриванием.
Если из рудника помимо двух выходов имеются и другие выходы без постоянного обслуживания, то последние должны охраняться или закрываться на запоры, открывающиеся изнутри без ключа, а снаружи ключом.
Если двумя выходами их подземных выработок на поверхность служат шахтные стволы, то они должны быть оборудованы кроме механических подъёмов (из которых один должен быть клетевым) лестничными отделениями. Лестничное отделение в одном из шахтных стволов может отсутствовать при условии, если в нём имеются два механических подъёма с независимым подводом электроэнергии.
При наличии двух шахтных стволов, они должны быть оборудованы так, чтобы по каждому из них все рабочие со всех горизонтов могли выехать (выйти) на поверхность. Лестничное отделение в шахтных стволах глубинной более 500м может отсутствовать при условии, если в обоих шахтных стволах имеются по два механических подъёма с независимым подводом электроэнергии или каждый шахтный ствол оборудован кроме основного подъёма аварийно-ремонтным подъёмом.
Требования не распространяются на период строительства или реконструкции рудников, проведения ремонтных работ на одной из подъёмных установок.
В лестничных отделениях шахтных стволов и других выработок с углом наклона от 45˚ до 90˚ лестницы должны быть установлены с уклоном не более 80˚. Над устьем выработки и над каждым полком в выработке, лестницы должны выступать на 1м или же над отверстием полка в крепь выработки должны быть прочно заделаны металлические скобы. Внутренняя сторона скоб должна отстоять от крепи не менее 0,04м, расстояние между скобами не должно превышать 0,4м, а ширина скоб должна быть не менее 0,4м.
Установка лестниц в целях обеспечения возможности свободного передвижения горноспасателей в респираторах должна удовлетворять следующим условиям:
-свободные размеры лазов без учёта площади, занятой лестницей, должно быть по длине лестницы не менее 0,7м, а по ширине не менее 0,6м;
-расстояние от основания лестницы до крепи выработок – не менее 0,6м;
-расстояние между полками – не более 8м;
-лестницы должны быть прочными, устойчиво закреплены и расположены так, чтобы они не находились над отверстиями в полках.
Ширина лестницы должна быть не менее 0,4м, расстояние между ступеньками – не более 0,4м, а расстояние между тетивами лестницы – не менее 0,28м.
Отверстие над первой верхней лестницей должно закрываться лядой.
Лестницы и полки должны содержаться в исправном состоянии и очищаться от грязи и рудной просыпи.
На действующих рудниках, вскрытых вертикальными шахтными стволами, при эксплуатации нового горизонта выход на другой горизонт допускается по наклонным выработкам, в которых должна быть предусмотрена механизированная доставка работников. На случай выхода средств доставки из строя должна быть предусмотрена возможность выхода работников по наклонной выработке. Для этого она должна быть оборудована: при угле наклона от 15˚ до 30˚ - сходнями со ступеньками и перилами; от 35˚ до 45˚ - лестницами со ступеньками и перилами. При угле падения наклона более 45˚ установка лестниц осуществляется так же как и вертикальных выработок.
Из каждого очистного блока, лавы должны быть два ничем не загромождённых выхода: один на вентиляционный и другой на конвейерный (транспортный) штреки.
На сопряжениях лав со штреками должны обеспечиваться свободные проходы в лаву (при необходимости под эстакадами) шириной не менее 0,6м и высотой не менее 0,7м.
При пересечении горных выработок на уровнях более 0,5м в местах прохода людей должны устанавливаться лестницы шириной не менее 0,4м, расстояние между ступеньками – не более 0,4м.
7.2 ТРЕБОВАНИЯ ПТБ К ЗАБОЙНЫМ МАШИНАМ И КОМПЛЕКСАМ
Забойные машины и комплексы должны соответствовать следующим правилам технической безопасности:
1. Опытные образцы новых технических устройств для подземных горных работ должны проходить приёмочные испытания. Порядок проведения приёмочных испытаний и применения технических устройств определяется Проматомнадзором.
2. Изменения конструктивных элементов забойных машин и комплексов, затрагивающие параметры взрывозащиты электрооборудования и уровень безопасности, допускаются по технической документации, согласованной с Проматомнадзором и выполненной разработчиком изделия или проектно-конструкторской организацией, имеющей специальное разрешение (лицензию) на данный вид деятельности в Республике Беларусь.
3. Система управления забойными машинами должна обеспечивать:
- включение и отключение машины путём кратковременного воздействия на систему управления. При наличии в холодильных и других подобных машинах датчиков давления рабочего хладагента, разрешающих включение выемочной машины при достижении определенной величины давления в системе охлаждения, допускается увеличение времени воздействия на орган включения до времени действия предупредительной сигнализации, но не более 15с;
- подачу предупредительного сигнала перед началом работы машины;
- двухстороннюю громкоговорящую связь в лаве;
- дистанционное аварийное отключение;
- наличие необходимых блокировок, связанных с технологией работы, а также предусмотренных для обеспечения безопасности эксплуатации машины (комплекса).
4. Конструкция механизированных крепей очистных комплексов должна обеспечивать крепление лавы по всей длине безопасное передвижение работников по лаве во время работы машин комплекса и доступе к элементам управления крепью, выемочной машине и к остальным частям комплекса (оборудование для закладки и других).
5. Управление передвигаемой секции (комплектом) должно производиться с блока управления, расположенного на другой секции (комплекте) крепи, согласно паспорту крепления и управления кровлей в очистном забое. Допускается выполнение отдельных операций, не связанных с разгрузкой гидростоек и передвижкой секции, на которой он расположен. При групповой передвижке части секций крепи лавы пульт управления должен располагаться под распёртой секцией, причём количество одновременно перемещаемых секций должно определяться проектом и паспортом крепления и управления кровлей в очистном забое.
6. Пульт управления крепью сопряжения должен быть вынесен за пределы крепи или располагаться под защитой её элементов таким образом, чтобы обеспечивалась безопасность при передвижке крепи.
7. Системы управления забойными машинами и комплексами, эксплуатация которых ведётся на пластах, опасных по внезапным выбросам соли и газа, должны предусматривать полуавтоматическое или дистанционное управление включением и выключением комбайна во время очистной выемки с бортового штрека лавы, или при проходке выработки с устья камеры (сопряжения, сбойка) при нахождении машиниста и других работников вне створа выработки. Проходческие комбайны с роторным исполнительным органом, кроме того, должны быть оборудованы предохранительными щитами в разгрузочном окне рабочего органа комбайна и перед пультом управления комбайном.
8. При проходке выработок, требующих анкерного крепления или дренажного бурения, комбайны должны быть оборудованы средствами бурения шпуров.
9. Проходческие комбайны должны соединяться с бункером-перегружателем с помощью жёсткой сцепки.
10. Проверка технической исправности забойных машин и комплексов должна осуществляться ежесменно руководителем смены, еженедельно – электромехаником и механиком участка, ежемесячно – заместителями главного механика рудника с записью результатов проверки в журнал осмотра комплекса.
7.3 МЕРЫ ПО БЕЗОПАСНОСТИ ТРУДА ПРИ
ПОДГОТОВКЕ ЗАБОЙНОГО ОБОРУДОВАНИЯ К РАБОТЕ, ВО ВРЕМЯ РАБОТЫ, ПРИ
ЭКСПЛУАТАЦИИ САМОХОДНОГО ВАГОНА, СКРЕБКОВОГО КОНВЕЙЕРА
Правила безопасности при работе проходческого комплекса
Осмотр узлов проходческого комплекса, машины (замена электродвигателей, осмотр режущих органов, гидравлической системы, ремонт механической части, ремонт бункера-перегружателя, проверка смазки), а также замена зубков производится звеном под руководством МГВМ. Перед выполнением данных работ необходимо:
- отключить и заблокировать автоматы, подающие напряжение на проходческий комплекс, машину
- на приводе автоматов вывесить плакат “Не включать – работают люди”
- после отключения автоматов и вывешивания плаката убедиться в невозможности включения оборудования проходческого комплекса, машины путём нажатия кнопки включения предупредительной звуковой сигнализации и кнопок пуска электродвигателей
Замена зубков и осмотр исполнительных органов комбайна, машины должны выполняться при соблюдении следующих требований:
- отогнать комбайн, машину от забоя не менее чем на 3м
- снять напряжение с комбайна, машины путём отключения коммутационных аппаратов с ручным приводом и включения их механической блокировки, на рукоятку аппарата вывесить плакат “Не включать – работают люди”. При наличии на комбайне, машине кнопки аварийного отключения напряжения (блокировочной кнопки “стоп”) нажать и зафиксировать её во включенном состоянии
- проверить путём осмотра и остукивания состояние кровли и стенок выработки, опустить имеющиеся заколы и отслоения
- проворачивание исполнительных органов в удобное для замены зубков положение должно производиться вручную специальной монтировкой. Проворачивание исполнительных органов с помощью электродвигателей запрещается. С помощью специальных приспособлений произвести замену зубков на исполнительном органе
- замена зубков производится МГВМ. ГРОЗ может оказывать помощь при замене зубков, но при этом выполнять только команды МГВМ
- замена зубков на вспомогательных исполнительных органах (бермовых фрезах, отрезных барабанах, верхнем отбойном устройстве) должна производиться в камерах разворота или на сопряжениях выработок.
Включение электродвигателей комбайна, машины разрешается машинисту горно-выемочных машин (МГВМ) или горно-рабочему очистного забоя (ГРОЗ). Перед включением электродвигателей в работу МГВМ или ГРОЗ должен убедиться в отсутствии людей вблизи комбайна или машины; громким голосом за 5 – 10 секунд до пуска предупредить: “Берегись – включаю!” и подать звуковой сигнал.
Во время работы комбайна, машины запрещается допускать нахождение людей в зоне между забоем и пультом управления, между комбайном и бункером-перегружателем, а также в непосредственной близости от бункера перегружателя на трассе движения самоходного вагона.
В целях предупреждения несчастных случаев во время работы комплекса, машины запрещается:
- нахождение посторонних лиц в проходимой выработке и на пути движения комбайна, машины, самоходного вагона
- работать при неисправном оборудовании
- производство всевозможных ремонтов и обслуживание оборудования
- проходка выработки без наличия необходимой документации
- работа при неисправности электросхемы, взрывозащиты электрооборудования, заземления, защит или блокировок
- ведение проходки без выдвинутого защитного козырька перед (над) рабочим местом машиниста комбайна на третьем калийном горизонте
- нахождение людей спереди и сбоку от режущего органа комбайна, машины при его работе
- работа при повреждённой оболочке гибкого кабеля
- транспортировка на конвейере комбайна негабаритных кусков руды (породы), сбивание с кровли во время отгона комбайна режущим органом оставшиеся при проходке прослойки (утюги)
Кровлю выработки и глубину проходимой щели необходимо держать по указанному в паспорте крепления и управления кровлей контакту. В случае оставления в кровле не предусмотренных паспортом крепления и управления кровлей прослойков или появления “коржей” и отслоений проходку немедленно прекратить, выйти самому и вывести людей из опасной зоны, произвести оборку кровли или подрубку отслоений. Если МГВМ сам не может решить, каким образом привести забой в безопасное состояние, то необходимо остановить и выключить комбайн, машину, выйти самому и ГРОЗ из опасной зоны и поставить об этом в известность руководителя смены.
Проходка и крепление выработки должны производиться в соответствии с утвержденным паспортом крепления и управления кровлей. Перед заходом в призабойную незакрепленную часть выработки необходимо проверить состояние кровли и опустить отслоившиеся пачки (слои) породы.
При обнаружении любой неисправности проходческого комплекса, машины МГВМ обязан немедленно остановить комплекс и до устранения неисправности никаких работ по проходке выработки не проводить.
МГВМ, отходя от пульта управления комбайна, машины, обязан выключить их двигатели.
Отставание вентиляционных труб от груди забоя должно соответствовать проекту на установку ВМП
При работе комбайна на очистной выемке и подготовке разрешается прокладка питающего кабеля по почве выработки таким образом, чтобы он не находился на трассе самоходного вагона.
Кабель между передвижной подстанцией и камерой, где производится его укладка, необходимо подвешивать. На подвеске расстояние между кабелями должно быть не менее 5см; а расстояние между подвесками должно быть не более 3м
При зарубке комбайна, на закруглениях, при проходке сбоек (перерубок) между выработками, при очистной выемке работа комбайна может вестись без бункера-перегружателя.
Управление агрегатами проходческого комбайна, машины должно производиться со специального сидения предусмотренного заводской конструкцией. Во время работы комбайна, машины МГВМ должен сидеть на специальном сидении у пульта управления комбайном, машиной, вставать в это время запрещается.
Не доезжая 5м до комбайна, ГРОЗ должен остановить самоходный вагон, предупредить МГВМ сигналом и только после этого поставить вагон под загрузку.
При работе самоходного вагона в комплексе с передвижным, стационарным или съёмным бункером-перегружателем (накопителем) последний должен быть оснащён световой сигнализацией о заполнении приёмного устройства, хорошо видимой с места управления самоходным вагоном.
Правила безопасности при работе очистного комплекса
Запрещается входить в выработанное пространство лав за ограждение секции крепи. Проходы, ведущие в выработанное пространство лав, со стороны крепи сопряжения должны быть перекрыты запрещающими знаками.
Запрещается работать на комплексе по выемке руды менее чем двумя рабочими. Конкретное количество МГВМ и ГРОЗ определяется паспортом крепления и управления кровлей.
При работе комплекса по выемке руды МГВМ и ГРОЗ должны находиться под защитным козырьком крепи, при переходе между секциями крепи контролировать состояние кровли между верхняками крепи и в призабойном пространстве.
МГВМ (ГРОЗ) должен управлять очистным комбайном при выемке очистной полосы и при его отгоне. Запрещается отлучаться от комбайна до его отключения.
Очистной забой должен быть освещён, комплекс оборудован системой предпусковой звуковой сигнализации и громкоговорящей связью, аппаратурой автоматического контроля содержания горючих газов. Аппаратурой контроля горного давления, если она предусмотрена проектом производства работ (паспортом крепления и управления кровлей). При включении предпусковой звуковой сигнализации необходимо выйти из зоны действия запускаемого оборудования.
Запрещается производить очистку, ремонт, регулировку и смазку оборудования во время его работы, а так же без принятия должных мер против его случайного или самопроизвольного запуска.
В течение смены МГВМ (ГРОЗ) обязаны контролировать:
- состояние безопасности рабочего места во время перемещения по нему, наличие в забое характерных признаков ГДЯ, своевременно производить оборку появившихся отслоений и навесов на прилегающих штреках, на сопряжениях лавы и в призабойном пространстве лавы
- исправность реек цевочного зацепления и приводных колёс механизма подачи комбайна, обратив особое внимание на то, чтобы колёса цевочной передачи не опирались на продольные лонжероны элементов цевочной передачи
- исправность конвейерного става (перепады и сдвиги рештаков относительно друг друга свыше 10мм запрещаются), трубчатых направляющих, подборщика и болтового крепления их к рештакам
- отсутствие деформированных скребков, а также скребков вышедших из направляющих рештаков. При их наличии: остановить конвейер, заменить деформированные скребки, а вышедшие из направляющих заправить в направляющие рештаков
- наличие, исправность и надёжность крепления защитных кожухов и ограждений на вращающихся частях механизированного комплекса
- по манометрам, установленным на гидростойках механизированной крепи, контролировать герметичность гидростоек и гидросистемы крепи
- исправность оболочек силовых и контрольных кабелей.
Показатели приборов непрерывного действия контроля метана в лаве должны фиксироваться в специальном журнале, находящемся на рабочем месте не менее двух раз в смену (в том числе один раз в начале смены), бригадиром (старшим рабочим). При обнаружении метана в забое выработки в концентрации более 1% (при аварийном отключении напряжения в забое лавы прибором автоматического контроля концентрации метана) все работы по добыче руды должны быть прекращены, рабочие должны выйти на свежую струю воздуха, должен быть поставлен в известность руководитель смены и по телефону – диспетчер.
При обнаружении неисправности или неправильных показаний автоматических стационарных средств измерения содержания метана руководитель смены должен сообщить об этом диспетчеру рудника, который должен принять меры по замене неисправных средств измерения. До замены неисправных автоматических стационарных средств измерения содержания метана, работы по очистной выемке запрещаются.
На сопряжениях лав со штреками должны обеспечиваться свободные безопасные проходы в лаву (при необходимости под эстакадами) шириной не менее 0,6м и высотой не менее 0,4м с расстоянием между ступеньками не более 0,4м, установленным на эстакаде в соответствии с требованиями охраны труда. В случаях перехода через забойный конвейер лавы необходимо отключить и заблокировать забойный конвейер кнопкой управления, установленной в районе эстакады забойного конвейера (там же вывешивается плакат с соответствующей надписью), и лишь после его остановки переходить конвейер.
При работе с зубилом, другими инструментами ударного действия, разбивке кусков породы кувалдой, долблении лунок под стойки в почве выработок, бурении шпуров необходимо применять защитные очки.
При работе забойного оборудования необходимо пользоваться средствами индивидуальной защиты (СИЗ): респираторами, берушами, при необходимости средствами защиты рук.
Меры безопасности при эксплуатации самоходного вагона
Ответственность за безопасную эксплуатацию самоходного вагона в течение смены несёт ГРОЗ, работающий на данном вагоне.
Ответственным за техническое состояние вагона является механик участка, в отсутствии его – электромеханик участка.
В случае обнаружения каких-либо неисправностей или нарушений в техническом состоянии самоходного вагона ГРОЗ должен вывести его из эксплуатации в ремонт.
На подземном горном участке должен быть заведён ремонтный журнал, в который заносятся все виды ремонтов каждого самоходного вагона, хранящийся в отделе главного механика рудника.
Не реже одного раза в неделю механиком участка или по его письменному поручению другим лицом (имеющим достаточную квалификацию) производится осмотр технического состояния каждого самоходного вагона, работающего на участке. Особое внимание обращается на устройства, обеспечивающие безопасность движения (тормоза, рулевое управление, трубопроводы, электрическую часть, состояние ободов, бортовых и замочных колец колёс). Результаты осмотра заносятся в ремонтный журнал.
ГРОЗ разрешается устранять мелкие неисправности механической части самоходного вагона.
При остановке самоходного вагона на ремонт, а также при необходимых отлучках ГРОЗ необходимо затормозить вагон, отключить автомат магнитной станции вагона и питающий кабель, снять рукоятку включения автомата магнитной станции самоходного вагона.
ГРОЗ имеет право входить в состав звена, производящего ремонт электроаппаратуры и кабеля в качестве члена звена. Руководителем работ в этом случае назначается старший рабочий, имеющий не ниже третьей квалификационной группы по электробезопасности.
Самоходный вагон должен быть оснащён передними и задними фарами.
На кузов самоходного вагона разрешена установка дополнительных надставок (шор) с целью уменьшения просыпи руды при транспортировке. Боковые надставки имеют высоту не более 150мм и выполняются из конвейерной ленты.
ГРОЗ запрещается выходить из кабины самоходного вагона до тех пор, пока он не убедится, что вагон надёжно заторможен и не может самопроизвольно съехать под уклон, независимо от угла наклона выработки в месте стоянки.
Проверку действия рабочего и стояночного тормозов вагона производит ГРОЗ на порожнем вагоне перед началом работы на горизонтальном (пологом) участке выработки на максимальной скорости, при этом тормозной путь должен быть не более 2,5м.
Проверка стояночного (аварийного) тормоза самоходного вагона производится в следующей последовательности:
- порожний вагон выводят на максимальный уклон, имеющийся на участке движения вагона
- затормаживается рабочим тормозом без выключения маслостанции
- одновременно с затормаживанием рабочим тормозом кран включения стояночного тормоза переводится в положение “заторможено”
Если при проверке стояночного тормоза вагон на данном уклоне не удерживается стояночным тормозом, то работа вагона запрещается и производится регулировка стояночного тормоза согласно заводской инструкции по регулировке стояночных тормозов для самоходных вагонов типа 5ВС-15М. При нормально отрегулированных стояночных тормозах срабатывание их происходит через 6-10 секунд после включения крана стояночного тормоза или после отключения маслостанции. ГРОЗ может покинуть кабину водителя, только убедившись в остановке вагона.
В случае, когда стояночный тормоз самоходного вагона не поддаётся регулировке, ГРОЗ обязан надёжно затормозить (застопорить) вагон, подложив под одно из колёс с двух сторон тормозные башмаки, выключить самоходный вагон, питающий кабель и сообщить об этом руководителю смены. Оставлять вагон на уклоне запрещено.
Запрещается эксплуатация неисправных самоходных вагонов, в том числе при:
А) неисправных тормозах;
Б) неисправном рулевом управлении;
В) несветящихся фарах;
Г) неисправных сигнальных устройствах
Д) поврежденном кабеле (допускается наличие в кабеле вагона счалок только вулканизированных горячим способом и не более 6-ти на 100м длины кабеля);
Е) неисправности схемы контроля целостности заземляющей жилы питающего кабеля;
Ж) неисправности нулевой защиты схемы управления и неисправности электрических блокировок схемы управления самоходного вагона
З) при отсутствии соответствующего количества прижимных планок диска колеса; деформированных ободах, бортового или замочного кольца; износе покрышки до корда;
И) неисправности взрывозащиты электрооборудования (отсутствии в комплекте или незатянутых болтах на крышках электрооборудовании, неуплотнённых кабельных вводах);
К) при давлении в газовой полости пневмогидроаккумулятора менее 2,5МПа.
Перед троганием на самоходном вагоне, в зависимости от направления и расстояния передвижения, ГРОЗ обязан в следующей последовательности: включить фары освещения по ходу движения; сесть за руль лицом в сторону движения; убедиться в отсутствии людей впереди по ходу движения вагона и сбоку, подать звуковой сигнал за 5-7 секунд до трогания.
Работа самоходного вагона разрешается в выработках, ширина которых превышает габаритный размер вагона по ширине не менее, чем 0,40м (по 0,2м с каждой стороны). По высоте зазор между кровлей выработки и наиболее выступающими частями вагона (груза) должен быть не менее 0,3м, а от сиденья до наиболее выступающей части кровли не менее чем 1,3м.
Движение самоходного вагона запрещается в выработках, которые захламлены, загромождены, а также уменьшено их сечение против установленного паспортом крепления и управления кровлей. Запрещается установка на самоходном вагоне АП-4, АПШ-1 со стороны кабины.
Максимальная скорость движения гружёного вагона в выработках шириной по низу от 3-х до 3,8м должна быть не более 7км/час, а порожнего – 9км/час.
В выработках шириной по низу более 3,8м скорость движения гружёного и порожнего вагона должна соответствовать правилам технической эксплуатации вагона.
Передвижение людей в выработках, где проходит движение самоходного вагона, разрешается допускать при условии, если ширина выработки по низу больше габарита вагона, не менее чем на 1,3м.
Фары самоходного вагона по ходу движения во время его работы должны быть постоянно включены.
Во время работы самоходного вагона запрещается допускать нахождение на нём людей.
При ведении взрывных работ запрещается в опасной зоне нахождение самоходного вагона.
Требования безопасности при эксплуатации скребковых конвейеров
Перемещение штрековых конвейеров лебёдкой производить не менее чем двумя рабочими, один из которых при выдаче сменного задания назначается старшим с его подписью в книге сменных заданий. Руководитель смены проводит дополнительный инструктаж по безопасному ведению работ. Все работы должны производиться по заранее согласованным сигналам.
При укорачивании штрекового конвейера или его перемещении запрещается заходить за ограждение крепи сопряжения.
Перед передвижкой или разборке става конвейера необходимо, обеспечить следующее:
- крепление лебёдки выполнено согласно паспорту;
- рештачный став надёжно соединён согласно заводской конструкции, освобождён от руды и нигде не удерживается;
- канат лебёдки не имеет порывов прядей и надёжно закреплён за привод конвейера согласно паспорту;
- отсутствуют люди в зоне действия каната (т.е. ближе 5м от него), в зоне действия отклоняющих блоков и на конвейере;
- пусковая аппаратура, питающая конвейер, отключена, разъединитель выключен и заблокирован, а на его рукоятке вывешен плакат “Не включать! Работают люди!”.
Применение полиспаста при передвижке конвейера должно производиться по утвержденной схеме строповки, элементы которой рассчитаны на применяемую нагрузку.
Передвижка конвейера должна производиться по звуковым командам, подаваемым с помощью специального двухстороннего сигнального устройства, один пульт которого располагается в месте нахождения лица, управляющего лебёдкой, а другой – на сопряжении с лавой и в таком месте, с которого хорошо видна концевая головка передвигаемого конвейера. Один сигнал – команда “Стоп”, два сигнала – “Тяни”.
Передвижение штрекового конвейера может осуществляться с помощью гидравлического передвижчика, при этом пусковая аппаратура штрековых конвейеров должны быть отключены, заблокированы и на их рукоятках вывешены плакаты “ Не включать! Работают люди!”.
При передвижке конвейера гидропередвижчиком необходимо:
-управлять передвижкой штрекового конвейера только с пульта управления передвижчика;
-контролировать давление распора гидравлических стоек передвижчика по манометру;
Не допускать нахождение людей на передвигаемом конвейере. Во время передвижения конвейера работники, участвующие в этом процессе, должны находиться в безопасном месте.
7.5 КОНТРОЛЬ ЗА СОСТАВОМ РУДНИЧНОЙ
АТМОСФЕРЫ И СОДЕРЖАНИЕМ ГОРЮЧИХ
ГАЗОВ
На каждом руднике должны составляться вентиляционные планы с указанием на них направлений струй, а также всех вентиляционных и противопожарных устройств.
Эти планы должны ежемесячно пополняться и один раз в полугодие составляться заново в соответствии с инструкцией о порядке составления вентиляционных планов, утвержденной организацией.
Для проверки правильности распределения воздуха по горизонтам, направлениям, панелям и блокам (камерам) должны производиться замеры его количества не реже одного раза в месяц, а также при всяком значительном изменении вентиляционного режима.
Контроль загазования забоя после взрывных работ и проветривания перед допуском людей в забой должен производиться при помощи переносных приборов.
На рудниках, опасных по выделению природных ядовитых газов, должны регулярно в сроки и в местах, установленных главным инженером рудника, отбираться пробы воздуха, а содержание ядовитых газов в них должно определяться при помощи переносных приборов или отбором проб в шахте и последующем их анализом в лаборатории.
Контрольная проверка качественного состава воздуха при проходке стволов должна производиться: в стволах рудников с газовым режимом – не реже двух раз, а в стволах с негазовым режимом – не реже одного раза в месяц. Отбор проб воздуха должен производиться в двух местах: в забое и на рабочем полке.
В рудниках с температурой воздуха на рабочих местах более +26˚С
должны производиться замеры температуры воздуха.
Результаты замеров температуры, а также анализы качественного состава воздуха заносятся в вентиляционный журнал.
Каждый рудник должен быть обеспечен замерными станциями. В местах замера количества воздуха на главных входящих и исходящих струях горизонтов, на флангах рудника должны быть устроены замерные станции длиной не менее 4м. Допускается для устройства замерных станций использование участков выработки, закрепленных бетоном или пройденных комбайнами и имеющие гладкие поверхности.
В других выработках замер количества воздуха должен производиться на прямолинейных незаграмождённых участках с крепью, плотно прилегающей к стенкам выработки, или со специально обобранными стенками и кровлей выработки.
Во всех местах замера количества воздуха должны быть доски, на которых записываются: дата замера, площадь поперечного сечения выработки (замерной станции), расчётное и фактическое количество воздуха, скорость воздушной струи и фамилия работника, производившего замер.
На всех рудниках не реже одного раза в три года должна производиться воздушно-депрессионная съёмка. В труднопроветриваемых рудниках с эквивалентным отверстием менее 1м2
воздушно-депрессионные съёмки должны производиться не реже одного раза в год.
По результатам воздушно-депрессионных съёмок главным инженером рудоуправления (рудника) должны быть утверждены мероприятия и сроки по устранению выявленных недостатков.
Для определения количества и состава воздуха на рудниках должна быть соответствующая аппаратура, которая должна содержаться в порядке и периодически проверяться.
Запрещается назначать начальником ПУВ лиц, не имеющих высшего горно-технического образования.
Газомерщиками должны назначаться рабочие, обученные по учебным программам, утвержденным в установленном порядке, и сдавшие экзамен по данной специальности.
Согласно требованиям правил безопасности контроль за содержанием метана в рудничной атмосфере должен осуществляться с помощью:
1. переносных приборов периодического действия (например, ШИ-10 и другие), с их помощью можно измерять и содержание углекислого газа;
2. автоматических стационарных приборов (анализаторы) непрерывного действия (например, анализатор метана типа АТ-1-1 или АТ-1-3; метан-реле ТМРК-3 и другие);
3. автоматических переносных приборов (сигнализаторы) непрерывного действия (например, прибор СИГНАЛ-2, метанометр ИКР-4Р и другие);
4. лабораторных анализов проб воздуха.
7.5 ТРЕБОВАНИЯ ПТБ ПРИ РАЗРАБОТКЕ ПЛАСТОВ ОПАСНЫХ ПО ГАЗОДИНАМИЧЕСКИМ ЯВЛЕНИЯМ (ГДЯ)
Пласты на которых имели место ГДЯ, а также пласты, для которых возможность подобных явлений установлена прогнозом, переводятся в разряд выбросоопасных.
Отнесение пластов к выбросоопасным устанавливается ежегодно совместным приказом Проматомнадзором и организации.
Разработка пластов, отнесенных к выбросоопасным, должна осуществляться в соответствии с инстукцией по безопасному ведению горных работ на пластах, опасных по ГДЯ, утверждаемой организацией.
Для каждого пласта, горизонта месторождения должны быть определены виды выбросоопасных геологических нарушений, предупредительные признаки и предвестники выброса, при встрече с которыми горные работы должны производиться по проекту, утвержденному главным инженером рудоуправления.
На рудниках, разрабатывающих выбросоопасные пласты, должны проводиться научно-исследовательские работы по изучению ГДЯ. При выявлении новых видов выбросоопасных геологических нарушений опасных по ГДЯ, методы их прогноза, контроля за появлением предупредительных признаков (предвестников) и мероприятия по предотвращению ГДЯ разрабатываются на основании научно-исследовательских работ и промышленных испытаний. При этом вносятся изменения и дополнения в инструкцию по безопасному ведению горных работ на пластах опасных по ГДЯ. При отработке калийных пластов Старобинского месторождения имеют место газодинамические явления (ГДЯ) в виде: внезапных выбросов соли газа, обрушений пород кровли, сопровождающихся газовыделениями, отжима призабойной части пород, сопровождающегося звуковыми эффектами, иногда разрушением и, выносом разрушенной породы в выработку. Указанные явления могут происходить как в момент проведения выработки и отбойки руды в забое, так и после этого, причем они могут иметь место в призабойном пространстве и вне его (запоздалые ГДЯ).
Все связанные с подземными работами инженерно-технические работники и рабочие Рудников должны быть обучены распознаванию предупредительных признаков и предвестников, предшествующих ГДЯ.
Газодинамическим явлениям предшествуют сначала предупредительные признаки, а затем и предвестники. Достаточным для действий рабочих и ИТР при появлении в забое выработки предупредительных признаков и предвестников ГДЯ считается появление в забое подготовительной или очистной выработки одного из предупредительных признаков или предвестников, указанных ниже.
Предупредительные признаки внезапного выброса в лавах по IV
сильвинитовому слою
- появление прогиба IV сильвинитового слоя и слоя IV—V размером до 30 м по длине лавы, с величиной прогиба в замковой части 0,2м и приращением величины прогиба слоев после 'каждой снятой стружки 0,05м и более;
- постепенное утончение и замещение каменной солью IV сильвинитового слоя.
Предвестники внезапного выброса соли и газа в лавах по VI
сильвинитовому слою:
- прогиб IV сильвинитового слоя и слоя IV—V по забою лавы с величиной прогиба в замковой части 0,3 м и более при углах погружения крыльев в плоскости забоя 5° и более;
- появление в забое лавы V сильвинитового слоя;
- появление в плоскости забоя лавы'вертикальных секущих трещин, заполненных карналлитом;
- появление газовыделений;
- потрескивание массива и отскакивание кусочков породы;
- развивающийся прогиб пород кровли с образованием зияющих (открытых) трещин.
Предупредительные признаки внезапного выброса соли и газа в
подготовительной выработке, кровля которой расположена в IV
сильвинитовом слое и выше
- локальный прогиб IV сильвинитового слоя под углом от 5° до 10°;
- постепенное утончение или замещение каменной солью IV сильвинитового слоя.
Предвестники внезапного выброса соли и газа в подготовительной
выработке, кровля которой расположена в IV сильвинитовом слое
и выше
- появление в забое выработки V сильвинитового слоя
- появление в забое' выработки вертикальных секущих трещин, заполненных карналлитом;
- погружение слоев под углом 10° и более;
- появление газовыделений;
- потрескивание массива и отскакивание кусочков породы;
- развивающийся прогиб пород кровли с образованием зияющих (открытых) трещин.
Предупредительные признаки внезапного выброса соли и газа при ведении подготовительных и очистных горных работ по слоям II и III:
- погружение слоёв под углом от 15˚ до 30˚
- полное замещение, продуктивных слоев или их частичное замещение каменной солью более чем на 50%;
- постепенное утончение верхних сильвинитовых прослойков по III слою;
- появление в кровле лавы трещин разрыва в плоскости глинистых прослойков, ориентированных по касательной относительно контура выбросоопасной зоны.
Предвестники внезапного выброса соли и газа по слоям II и III
- погружение слоёв под углом 30˚ и более;
- потрескивание массива и отскакивание кусочков породы;
- усиленное выделение газа;
- развивающийся прогиб пород кровли с образованием зияющих (открытых) трещин;
- полное или частичное замещение продуктивных слоев глинисто-карналитовыми породами;
- появление IV сильвинитового слоя на стенках или в забое горной выработки.
Предупредительные признаки обрушений пород кровли, сопровождающихся газовыделением, отсутствуют
Предвестники обрушений, сопровождающихся газовыделениями:
- потрескивание массива и отскакивание кусочков породы;
- усиленное выделение газа из шпуров и трещин;
- развивающийся прогиб пород кровли;
- образование открытых трещин.
Предупредительные признаки и предвестники отжима призабойной части пород отсутствуют.
Контроль за появлением предупредительных признаков и предвестников внезапного выброса соли и газа
При отработке выбросоопасных пластов во всех очистных и подготовительных выработках должен осуществляться контроль за появлением предупредительных признаков и предвестников внезапного выброса соли и газа. Такой контроль осуществляется:
Машинист горно-выемочных машин обязан постоянно следить за поведением пласта, как в лаве, так и при проходке выработки, причём при проходке выработки за поведением пласта необходимо постоянно следить по обеим стенкам выработки.
На горно-выемочных машинах должны быть приспособления для определения углов падения слоев Третьего пласта (транспортир с отвесом или горный компас). На горно-проходческих комбайнах типа ПК-8 и Урал-10, кроме этого, должны быть приспособления для контроля параметров профилактического бурения дегазационных шпуров (мерные рейки, рулетки).
В случае обнаружения в горной выработке (капитальной, подготовительной, очистной, в том числе в лавах) предупредительных признаков, машинист комбайна должен прекратить работу, вызвать лицо горного надзора и вместе с ним произвести осмотр выработки.
При отсутствии предвестников выброса в выработке, лицо горного надзора, поставив в известность начальника участка (заместителя), разрешает продолжение ведения работ (проходку, очистную выемку) только в дистанционном режиме управления включением и выключением комбайна при отсутствии людей в подготовительной выработке или лаве. После подвигания забоя, соответствующего не более, чем одной загрузке бункера-перегружателя в очистных камерах или подготовительных выработках, либо подвигания забоя лавы на одну выемочную полосу, комбайн должен останавливаться после чего производится дополнительный осмотр поведения пласта в данной зоне.При повторном подтверждении предупредительных признаков выброса лицо горного надзора действует в соответствии с требованиями, изложенными в предыдущем абзаце данного пункта.
При исчезновении предупредительных признаков выброса в выработке вводится обычный режим работы. При обнаружении предвестников выброса лицо горного надзора немедленно прекращает работы, выводит рабочих в безопасное место – в выработку, проветриваемую за счёт общешахтной депрессии и сообщает о случившемся диспетчеру рудника.
Всё электрооборудование в выработке, где обнаружены предвестники выброса, должно быть отключено.
Все указанные работы должны производиться в присутствии лица горного надзора.
При обнаружении в забое лавы или подготовительной выработке предвестников выброса рабочие должны немедленно прекратить работу, удалиться в безопасное место и поставить в известность лицо горного надзора, которое обязано проверить выход рабочих в безопасное место и сообщить о случившемся диспетчеру рудника.
Начальник участка (его заместитель), получив сообщение о наличии предвестников выброса, принимает меры к образованию комиссии для проверки на месте состояния забоя и решения вопроса о порядке дальнейшего ведения работ. Комиссия в составе заместителя главного инженера рудника по горизонту, заместителя главного энергетика по горизонту, начальника участка или его заместителя и участкового геолога, прибыв на место, обязана осмотреть выработку и принять решение (с составлением акта) о прекращении работы в данной выработке или о возможности дальнейшей проходки.
В случае установления комиссией наличия в очистной или подготовительной (капитальной) выработке предвестников выброса для дальнейшего безопасного ведения работ в данной зоне должен быть составлен проект, утверждаемый главным инженером рудоуправления. В проекте необходимо предусматривать порядок проведения работ по предотвращению внезапного выброса, применяемое оборудование и дополнительные меры безопасности.
Указанные проекты должны составляться на основе типовых технологических схем (инициирование выбросов буровзрывными работами, обхода опасной зоны, пересечения опасной зоны, предварительной разгрузки и дегазации массива путем его профилактической обработки и других).
Не допускается проносить курительные принадлежности в шахту. Запрещается курить и разводить открытый огонь в шахте и надшахтных зданиях, не относящийся к газоэлектросварочным, газорезательным и паяльным работам, которые проводятся по особому распоряжению и специальному наряду.
Для предупреждения курения в шахте и проноса в нее курительных принадлежностей осуществляется периодический осмотр всех спускающихся и находящихся в шахте работников. Лица, уклоняющиеся от осмотра, считаются нарушителями газового режима. Осмотр проводится лицами старшего звена технадзора или непосредственным руководителем работ, а также специальными комиссиями.
ЛИТЕРАТУРА
1. Агашков М.И., Борисов С.С., Боярский В.А. Разработка рудных и нерудных месторождений. – Москва: «Недра», 1983 – 424с.
2. Истомин И.В. Методика и производство ведения горных работ на Старобинском месторождении калийных солей. – Слуце – Солигорск – Минск: 1995
3. Пермяков Р.С. Справочник по разработке соляных месторождений. – М.: «Недра», 1986
4. Пермяков Р.С., Романов В.С., Бельды М.П. – Технология добычи калийных солей. – М.: «Недра», 1981
5. Смычник А.Д., Богатов Б.А., Шемет С.Ф. Технология и механизация разработки калийных месторождений. – Минск: «Юнипак», 2005
6. Щерба В.Я., Башура А.А., Андрейченко С.С. Управление газодинамическими процессами. – М.: Издат. МГГУ, 2004
7. Вопросы геомеханики подземной добычи калийных солей. Сборник статей. – Издат. МГГУ, 2004
8. Инструкция Р-2 по охране труда для машинистов горных выемочных машин и горнорабочих очистного забоя при эксплуатации проходческих комплексов, щеленарезных машин, почвоподдирочных машин на рудниках РУП «ПО «Беларуськалий» - Солигорск, 2003
9. Инструкция Р-4 по охране труда для машинистов горных выемочных машин и горнорабочих очистного забоя при эксплуатации очистных механизированных комплексов при добыче сильвинита системами разработки длинными столбами на рудниках РУП «ПО «Беларуськалий» - Солигорск, 2003
10. Нормативные и методические документы по ведению горных работ на Старобинском месторождении калийных солей. – Солигорск – Минск, 1998
11. Правила технической безопасности при разработке подземным способом соляных месторождений Республики Беларусь. – Солигорск, 2006
12. Сборник технических характеристик горного оборудования. – Солигорск, горный отдел, 2001
13. Задорожный В.Н. Экономика, организация и планирование горного производства: Учебное пособие для техникумов. – М.: НЕДРА, 1992. – 286с.
14. Зайцев Н.Л. экономика промышленного предприятия. Практикум: Учебное пособие. – М.: ИНФРА-М, 2000.-192с.
15. Зуев В.И. и Никитин А.В. Практикум по экономике, организации и планированию в горной промышленности: Учебное пособие для техникумов. – М.: НЕДРА, 1990 – 252с.
16. Экономика, организация и планирование промышленного производства/ Под общ. ред. Карпей Т.В. и Лазученковой Л.С. – Мн.: Дизайн ПРО, 2001. – 272с.
17. Экономика предприятия./В.Я. Хрипач, Г.З. Суша, Г.К. Оноприенко; Под ред. В.Я. Хрипача. – Мн.: Экономпресс, 2001. – 464с.
18. Экономика предприятия. Практикум: Учебное пособие
А.Н. Сенько, Э.В. Крум. – Мн.: Выш. шк., 2002. – 224с.
|