ДЕПАРТАМЕНТ ОБРАЗОВАНИЯ ГОРОДА МОСКВА
Государственное образовательное учреждение
Среднего профессионального образования
ПОЛИТЕХНИЧЕСКИЙ КОЛЛЕДЖ №8
Имени дважды Героя Советского Союза И.Ф.Павлова
(ГОУ ПК №8 им. И.Ф.Павлова)
Борисенко Н.И.
Лабораторный практикум
СОГЛАСОВАНО
На заседании ПЦК
«__________________»
Протокол №________
От «___»_______2009г.
Москва 2009г.
Лабораторный практикум учебного курса "ИНТСРУМЕНТАЛЬНЫЕ ТВЁРДЫЕ СПЛАВЫ имеет целью ознакомить студентов с основными технологическими процессами переработки порошковых материалов и основными проявлениями явлений, приводящих к появлению брака, выявлению его причин и способами борьбы с ним.
Работы лабораторного практикума составлены так, что каждая последующая является продолжением предыдущей, а все вместе - они составляют непрерывную цепь операций единого технологического процесса получения твердосплавного изделия. Работы, включенные в Лабораторный практикум - это типовые задачи и работы, с которыми приходится постоянно сталкиваться цеховому технологу в своей повседневной деятельности.
ВВЕДЕНИЕ
Лабораторный практикум учебного курса "ИНСТРУМЕНТАЛЬНЫЕ ТВЁРДЫЕ СПЛАВЫ " проводится параллельно с чтением лекционного курса.
Задача практикума - ознакомить студента с основными технологическими операциями производства изделий из порошков, в основном на примере, твердосплавных изделий - уже как с чисто технологическими операциями производства и поэтому в практикуме уделено внимание не столько описательно-познавательной стороне, а акцент сделан на содержании конкретных операций технологического процесса, применяемых на практике, и на выявлении причин наиболее распространенных случаев брака и способам борьбы с ним, например - выявить условия возникновения перепрессовки или изменение плотности прессовки при различном давлении прессования и т.п. причин и способами борьбы с браком и дать практические навыки обращения с соответствующим оборудованием.
Студент приступает к каждой работе после ознакомления с литературой по данному вопросу и беседы с преподавателем, на которой выясняется его теоретическая подготовленность и проводится инструктаж по технике безопасного проведения лабораторной работы и правилам промышленной санитарии, что фиксируется регистрацией в соответствующих журналах и других нормативных документах института.
Работы, требующие специального допуска к используемому оборудованию, выполняются штатным сотрудником лаборатории при непосредственном участии студента.
После выполнения работы студент составляет краткий отчет в соответствии с требованиями, изложенными в данном Практикуме и сдает зачет преподавателю. Отчет по работе - рукописный или выполненный печатным способом, подписывается студентом.
По мере поступления нового оборудования и приборов в лабораторию перечень лабораторных работ будет изменяться.
Описания порядка выполнения работ составлены таким образом, чтобы студент мог полностью ознакомиться с поставленной перед ним задачей без привлечения дополнительных материалов и без лихорадочного перелистывания Практикума в поисках описания необходимых действий. Поэтому в ряде однотипных работ повторены описания машин, приборов и установок, повторены необходимые разъяснения. И хотя это и увеличило объем, но при этом упростило пользование книгой.
Введение
|
3
|
Содержание
|
4
|
Тема 1.
|
Изучение технологических свойств шихты.
|
6
|
1
|
1.1. Определение насыпной плотности.
|
24
|
2
|
1.2. Влияние насыпной плотности на степень заполнения прессформы.
|
26
|
3
|
1.3. Зависимость насыпной плотности от формы частиц.
|
28
|
4
|
1.4. Определение текучести.
|
31
|
5
|
1.5. Влияние текучести порошка на скорость его транспортировки по коммуникациям пресса-автомата.
|
32
|
6
|
1.6. Определение угла естественного откоса.
|
34
|
7
|
1.7. Определение влажности шихты.
|
36
|
8
|
1.8. Определение склонности шихты к зависанию и сводообразованию.
|
38
|
Тема 2.
|
Изучение процессов приготовления шихты
|
40
|
9
|
2.1. Зависимость степени измельчения от времени помола.
|
46
|
10
|
2.2. Изучение процесса грануляции шихты окаткой.
|
48
|
Тема 3.
|
Изучение процесса прессования.
|
50
|
11
|
3.1. Зависимость плотности прессовки от давления прессования.
|
54
|
12
|
3.2. Распределение плотности по высоте прессовки при одностороннем прессовании.
|
56
|
13
|
3.3. Распределение плотности по высоте прессовки при двухстороннем прессовании.
|
59
|
14
|
3.4. Определение упругого последействия.
|
63
|
15
|
3.5. Определение формуемости порошка.
|
65
|
16
|
3.6. Зависимость формуемости шихты от размеров частиц.
|
67
|
17
|
3.7. Зависимость формуемостии от физико-механических свойств материала основы шихты (медь, никель, карбид вольфрама).
|
70
|
18
|
3.8. Изучение конструкции прессформ различных конструкций, применяемых в производстве изделий из порошков.
|
72
|
Тема 4.
|
Изучение явлений при спекании твердых сплавов.
|
76
|
19
|
4.1. Отгонка влаги и растворителя.
|
94
|
20
|
4.2. Наблюдение разложения пластификатора при предварительном спекании.
|
95
|
21
|
4.3. Определение усадки.
|
97
|
СОДЕРЖАНИЕ
Тема 5.
|
Изучение свойств спечённых изделий.
|
101
|
22
|
5.1. Изучение искажений формы изделия при спекании.
|
101
|
23
|
5.2. Изучение основных видов брака и причин его возникновения при производстве твердых сплавов.
|
108
|
24
|
5.3. Измерение плотности спеченных заготовок.
|
110
|
25
|
5.4. Определение предела прочности при поперечном изгибе стандартных образцов из спечённых твёрдых сплавов.
|
113
|
26
|
5.5. Измерение твёрдости спечённых изделий.
|
115
|
27
|
5.6. Определение стойкости режущей пластины.
|
118
|
28
|
5.7. Определение энергии разрушения зубка буровой коронки.
|
124
|
Тема 6.
|
Методы анализа порошков и спечённых изделий
|
127
|
29
|
6.1. Ситовый анализ. Классификация порошков по размеру частиц.
|
133
|
30
|
6.2. Определение гранулометрического состава порошка под микроскопом
|
134
|
31
|
6.3. Наблюдение формы частиц.
|
141
|
32
|
6.4. Наблюдение микроструктуры твердых сплавов разных марок.
|
144
|
33
|
6.5. Определение основных характеристик зёрен карбида вольфрама в спечённом твёрдом сплаве
|
146
|
34
|
6.6. Наблюдение основных структурных составляющих: пор, карбида вольфрама, связки, h
-фазы.
|
150
|
35
|
6.7. Определение параметров и вида h
-фазы под микроскопом.
|
156
|
36
|
6.8. Определение пористости спечённых образцов под микроскопом.
|
158
|
37
|
6.9. Определение среднего размера зёрен карбида вольфрама под микроскопом.
|
160
|
38
|
6.10. Определение гранулометрического состава спечённого изделия под микроскопом.
|
163
|
Тема 7.
|
Правила оформления лабораторной работы
|
169
|
Приложение 1. Типовые формы частиц
|
171
|
Приложение 2. Шкала оценки карбидной неоднородности (по Методике ВНИИИнструмента)
|
172
|
Приложение 3. Шкала для оценки видимой пористости по ГОСТ 9391
|
173
|
Приложение 4. Шкала для оценки включений структурно-свободного углерода по ГОСТ 9391
|
174
|
ТЕМА №1. ИЗУЧЕНИЕ ТЕХНОЛОГИЧЕСКИХ СВОЙСТВ ШИХТЫ
Смесь порошков компонентов твёрдого сплава без пластификатора называется товарной смесью
. Обычно её хранят в полиэтиленовых пакетах, помещённых в герметично закрытых – запаянных или завальцованных жестяных барабанах по 5 – 10 – 20 – 25 кг, которые заполняют аргоном. Упакованная таким способом товарная смесь может храниться до шести месяцев без потери свойств.
Перед употреблением в товарную смесь вводят пластификатор. Пластифицированная смесь называется шихтой
или пресспорошком
. Для повышения текучести и насыпной плотности шихту гранулируют (тогда её часто называют гранулятом
) и от гранулята отсеивают пыль.
Определённое количество товарной смеси или шихты одного замеса называют партией. Одна партия товарной смеси или шихты может быть упакована в несколько банок или барабанов в зависимости от количества их в одном замесе.
Шихта может храниться не более одной-двух недель, поскольку в ней сразу после пластифицирования начинают протекать полимеризация пластификатора, которая инициируется кобальтом – катализатором полимеризации, и окисление кобальта, инициируемое свободными радикалами и олигомерами (неполными полимерами), которые всегда содержатся в полимерных пластификаторах: каучуке, полиэтиленгликоле и поливинилацетате. Неограниченно долго могут сохраняться смеси, пластифицированные парафином или d
-камфорой.
Перед прессованием всегда необходимо проверить технологические свойства, поскольку они изменяются со временем и могут выйти за допустимые пределы. Технологическими называют свойства шихты, определяющие выбор способов и режимы транспортировки, дозирования, прессования, спекания и других переделов или операций технологического процесса. Как правило, технологические свойства шихты одного и того же материала, но разных партий отличаются друг от друга. Всё это требует постоянного контроля за технологическими свойствами и обычно в цехах порошковой металлургии имеется специальная лаборатория постоянно наблюдающая за изменением свойств порошков от партии к партии, а если партии большие и их переработка длится более одной смены – то и за изменением свойств шихты в течение смены или суток.
Шихта является сыпучим материалом. Частицы, образующие структуру сыпучего материала, имеют друг с другом различную связь, зависящую от формы частиц, их формы, влажности и других факторов, составляющих технологические свойства шихты. Знания размеров частиц, свойств материала частиц, их формы и состава смеси недостаточно для полного определения свойств порошковой массы и её возможного поведения при проведении технологических операций. Поэтому проводят различные испытания, имитирующие отдельные операции по переработке порошков. Такие испытания позволяют технологам судить о пригодности порошка для изготовления изделий.
Технологические свойства шихты – это:
- гранулометрический состав;
- насыпная плотность;
- текучесть;
- угол естественного откоса;
- связность и слёживаемость;
- сегрегация;
- зависание (сводообразование);
- прессуемость;
- влажность;
- спекаемость и усадка.
Текучесть
определяет способность шихты к транспортировке по коммуникациям - трубопроводам и лоткам пресса и особенно важно знать её, если прессование производится на прессе-автомате. Кроме того, текучесть, в основном, определяет скорость и полноту заполнения прессформы, то есть производительность прессования. Плохая текучесть пресспорошка не только тормозит скорость заполнения полости прессформы, но и вызывает неравномерность заполнения. Средняя текучесть шихты должна быть такой, чтобы полость прессформы заполнялась за 1–2 сек.
Текучесть шихты зависит от множества факторов, из которых основными являются: форма частиц; размеры частиц; однородность шихты по размерам частиц; плотность материала частиц; свойства пластификатора (как клеящего вещества).
Текучесть зависит от множества факторов, учесть и повторить которые практически невозможно. Поэтому величина текучести не нормируется, но Государственный стандарт предусматривает единую методику определения текучести. Для различных групп материалов (стройматериалы, металлические порошки, мука и крупы и т.д.) приборы имеют различные размеры, но методика одинакова – измеряется время истечения определённой массы материала, через калиброванное отверстие. Для порошков твёрдых сплавов, их компонентов и гранулятов – это 50 г, диаметр калиброванного отверстия – 2,5 мм. Текучесть измеряют в секундах.
При большой удельной поверхности, как правило, при частицах менее 60 мкм, трение между частицами и частиц о стенки возрастает настолько, что течение порошка становится практически
невозможным. С увеличением размеров частиц соотношение между силами трения и массой частиц становится меньше и текучесть возрастает, но при дальнейшем увеличении размеров частиц начинают сказываться силы сцепления между частицами, обусловленные формой частиц, и текучесть вновь снижается. Наибольшей текучестью обладают частицы шарообразной, эллипсоидальной и других округлых форм, а наименьшей – дендритной, пластинчатой и игольчатой форм.
Рис.1. Воронка для измерения текучести.
1 – стойка, 2 – воронка, 3 – приёмная ёмкость.
|
|
Именно поэтому пресспорошки гранулируют, придавая конгломератам шарообразную форму. Грануляция преследует и ещё одну важную цель – гранулы стараются делать одинаковыми и этим создаются условия равномерного и одинакового заполнения прессформы. Обычный размер гранул для прессования твёрдых сплавов лежит в пределах от 120 до 300 мкм – больше величины зазора между пуансоном и внутренней поверхностью матрицы – этим устраняется заклинивание пуансона в матрице, так как частицы порошка не попадают в этот зазор.
Текучесть зависит от способа получения частиц порошка: осаждением, распылением, восстановлением и т.д.
Зависит текучесть и от длительности хранения. Поэтому текучесть проверяют непосредственно перед прессованием.
Насыпная плотность
– это отношение массы порошка при свободной насыпке к его объёму.
Величина ей обратная – это насыпной объём
.
Насыпная плотность определяется действительной плотностью материала порошка, размером и формой частиц, гранулометрическим составом, свойствами поверхности частиц и ещё многими факторами. Как и текучесть, насыпную плотность невозможно нормировать, но ГОСТ определяет единую методику определения насыпной плотности.
Насыпная плотность, как технологический фактор, определяет объём прессформы, необходимый для заполнения её при свободной засыпке, высоту подъёма верхнего пуансона, размеры бункера пресса и ёмкостей для хранения заданного количества порошка. Усадка при спекании также находится в прямой связи с насыпной плотностью, поскольку она зависит от гранулометрического состава смеси. Чем меньше насыпная плотность, тем больше усадка и искажения формы спечённого изделия. Смешивая порошки различной насыпной плотности, можно получить безусадочную шихту, вернее – шихту с минимальной усадкой.
Применение порошка постоянной насыпной плотности обеспечивает постоянство усадки и, как следствие этого – постоянство размеров спечённых изделий. Это особенно важно при объёмном дозировании во время прессования.
Одновременно следует отметить, что при одинаковой насыпной плотности порошки могут иметь различный ситовый состав, форму частиц, прессуемость, текучесть и т.д.
Для определения насыпной плотности мерный сосуд емкостью 25 см3
через воронку доверху заполняют порошком, масса которого, умноженная на 0,04, дает насыпную плотность в г/см3
, т. е. массу единицы объема. Очень тонкие порошки при определении этой массы засыпают в мерный сосуд по специальным стеклянным пластинам (прибор называется волюмометр Скотта).
Степень укладки частиц порошка в засыпке определяется их формой, размерами и гранулометрическим составом. Насыпной объем зависит главным образом от взаимного расположения частиц порошка, контактов и сцепления между частицами, а также от междучастичных полостей (в эти полости могут попадать более тонкие частицы). Иногда возможно правильное расположение частиц. Насыпная плотность порошков со сферическими частицами (например, распыленных) больше, чем с угловатыми. Порошки со сферическими частицами менее склонны к образованию мостиков (связок) и вследствие относительно хорошей текучести сравнительно плотно располагаются в засыпке. Их насыпная плотность может составить до 50 % плотности соответствующего компактного вещества. Крайне низки насыпные плотности чешуйчатых порошков, составляющие иногда ~ 10 % плотности компактной массы. Меньшие частицы тех же материалов из-за их большей удельной поверхности (и более сильного трения) обладают меньшей насыпной массой, чем более крупные частицы.
|
|
Рис.2. Воронка для определения насыпной плотности (1 – стойка, 2 – воронка, 3 – сосуд-приёмник) и волюмометр Скотта (справа) : 1- латунное сито, 2 – сторона коробки из стекла, 3 – переходник, 4 – нижняя квадратная воронка, 5 – приемная ёмкость , 6 – боковые стороны коробки из дерева или пластмассы , 7 – стойка.
|
|
Плотность укладки определяется всей совокупностью физических свойств порошка. Чем крупнее и чем более компактную и правильную форму имеют частицы порошка, тем больше будет насыпная плотность; однако большее значение имеет не абсолютный размер частиц, а соотношение частиц разных размеров (кривая распределения зернистости). Например, независимо от абсолютного размера, одинаковые шары имеют постоянный коэффициент заполнения объема; комбинируя же шары разной величины, можно добиться значительного увеличения плотности — в предельном случае — до 100%. Если для идеальных частиц правильной формы возможно путем математического расчёта определить оптимальные соотношения и абсолютные значения размеров частиц, обеспечивающих получение заданной пористости, то для практически применяющихся порошков это невозможно. Более того, как показывает практика, зная насыпные веса двух порошков, нельзя при значительном их различии заранее с достаточной точностью предугадать насыпной вес смеси. Например смесь 1 : 1 порошков одного и того же металла с насыпными весами 1,0 г/см3
и 2,0 г/см3
имеет насыпной вес не 1,5 г/см3
, а 1,7—2,0 г/см3
; при еще большем различии насыпной вес смеси может быть даже выше, чем у более тяжелого порошка. Состояние поверхности порошка также имеет значение: частицы с гладкой «скользкой» поверхностью, естественно, укладываются плотнее, чем шероховатые, покрытые окисными пленками.
Таким образом определение насыпной плотности позволяет косвенно учитывать такие факторы, которые не поддаются прямому количественному определению, но оказывают влияние на технологические свойства порошка.
Насыпная плотность является чрезвычайно важной характеристикой и ряд свойств порошка связан с насыпной плотностью простыми количественными отношениями.
Прежде всего, насыпная плотность (или точнее насыпной объем) учитывается при конструировании прессформ и выборе пресса. Рассмотрим следующий пример: пусть требуется спрессовать цилиндр высотой 40 мм с пористостью 15% из медного электролитического порошка с насыпным весом 1,2 г/см3
. Плотность цилиндра будет 8,93´0,85 = 7,61 г/см3
, степень сжатия порошка » 6 высота контейнера 6´40 = 240 мм и ход плунжера пресса (6—1)´40 = 200 мм. Если же взять для прессования гранулированный медный порошок с насыпным весом 2,8 г/см3
, то степень сжатия будет = 2,5, высота контейнера потребуется равной =2,4 и ход плунжера 1,5´40 = 60 мм.
Дозировка порошка для прессования производится в большинстве случаев объемным методом, при этом соблюдение постоянства насыпного веса является совершенно необходимым условием.
В производстве обычно задаются точными размерами детали и допусками по плотности. Пусть, например, объем детали (спрессованной из железного порошка со средним насыпным весом 2,0 г/см3
) равен 20 см3
, плотность же gÎ
задана в пределах 75—85%. Тогда средний вес детали Р » 126 г, допустимые колебания веса (в соответствии с допусками по плотности) составляют ±7,5 г. Отсюда объем мерки будет = 63 см3
, а допустимые пределы колебаний насыпного веса:
максимум = » 2,12 г/см3
и
минимум = » 1.88 г/см3
.
Зависание (сводообразование)
– это явление застревания порошкового материала во внутренних полостях бункера, точек перегиба трубопроводов и в прессформе, которое обуславливается особенностями течения таких материалов, с одной стороны проявляющих свойства жидкости, а с другой – являющимися совокупностью твёрдых частиц, активно взаимодействующих друг с другом (трение, сцепление, схватывание) вследствие неупорядоченного расположения. Порошковые текучие (сыпучие) материалы способны принимать форму сосуда и движутся потоком – в этом они похожи на жидкости. Каждая частица обладает вместе с тем свойствами твёрдого тела и их совокупность также способна воспринимать внешние сжимающие нагрузки – в этом сходство порошкового тела с твёрдым.
Сила сцепления частиц зависит от степени влажности, пористости, размера и формы частиц и так как сила сцепления пропорциональна суммарной площади контактов между частицами материала, то чем мелкозернистей порошок, то тем больше силы поверхностного сцепления между ними.
Если порошок загрузить в бункер, то под действием сил тяжести верхних слоёв в нижних материал уплотняется, сила сцепления увеличивается и текучесть уменьшается, что приводит к увеличению насыпной плотности и числа точек контакта между частицами. При этом из зазоров между частицами частично вытесняется воздух и возникают точки контакта между частицами, в которых действуют межмолекулярные силы. В результате этого затрудняется истечение порошка из отверстия бункера, в трубопроводах возникают зоны уплотнения порошка и пробки, полость прессформы, имеющая сужения, не заполняется.
Зависание и сводообразование – нежелательные явления, которые приводят к нарушению процессов дозирования, транспортировки и прессования порошков и которые следует учитывать при проектировании бункеров, трубопроводов и прессформ.
Диаметр отверстия в бункере или проходное сечение трубопровода dкрит
, в которых начинается зависание могут быть определены по эмпирической формуле
dкрит
= 4,5е0,24А
, где
- 4,5 и 2,4 – эмпирические коэффициенты;
- е – основание натуральных логарифмов;
- А – средний размер зерна по Фишеру.
А Б
Часто для борьбы с явлением зависания в конструкцию пресс-автоматов вводят так называемые "встряхиватели" – небольшие устройства механического или электромеханического типа, которые периодически ударяют молоточком по местам бункеров или трубопроводов, где прогнозируется зависание или сводообразование. Этой же цели служат вибраторы, устанавливаемые в соответствующих местах системы питания пресса.
Гранулометрический состав
– это характеристика распределения частиц порошка по размерам, которая показывает из частиц какого размера и в каких долях составлена данная партия порошка. Интервал размеров частиц называют фракцией.
Размер частиц порошка является важнейшей характеристикой, обязательно оговариваемой в технических условиях. От крупности порошков, в сочетании с другими характеристиками, зависят: удельное давление прессования, усадка при спекании, насыпной вес порошка, конструкция прессформ и, наконец, механические свойства готовых спеченных изделий. Чем мельче порошки, тем больше нужное давление прессования (для достижения заданной плотности), зато тем больше прочность прессовки, тем ниже требуемая температура спекания и тем прочнее готовые (спеченные) изделия. Весьма интересна зависимость усадки при спекании от крупности порошка, наблюдаемая у порошков черных и цветных металлов: мелкие порошки дают при спекании усадку (уменьшение размеров, объемное сжатие), крупные показывают рост (увеличение размеров, объемное расширение). Комбинируя в известных пропорциях различные фракции крупности порошка, можно получить шихту, с незначительной усадкой.
Разнообразные приемы измерения размеров частиц можно подразделить на три группы: разделения, седиментационные и счетные. Важнейшие из них приведены в табл. 11. Выбор метода измерения зависит прежде всего от величины частиц.
Таблица 1
Методы определения размеров частиц.
Методы
|
Размеры определяемых
частиц, мкм
|
Разделение (ситовый анализ):
на тканевых полотнах
на металлических ситах (проволочных и штампованных)
|
>30
>5
|
Воздушная сепарация:
гравитационная
центробежная
|
5 - 60
2 - 60
|
Седиментация:
В гравитационном поле (пипеточный метод, на седиментационных весах, на фотоседиментометре)
В центробежном поле (на центрифуге)
|
1 - 6-
0,05 - 10
|
Счётные:
Прямой (кондуктометрия)
Микроскопия (оптическая)
Микроскопия (электронная)
|
1 - 100
1 - 100
0,004 -1
|
Ситовый анализ - наиболее распространённый способ разделения, которым можно определять размеры частиц от 5 мкм.
Полотно (дки) сита изготавливают различными способами и различные исполнения полотен сит показана на рисунке 4. Рис.4. Виды сеток: А – полотно, Б – плетёные, В – саржевые (крученные), Г – сварные из проволоки, Д – вязаные, Е – стержневые, Ж – штампованные (просечные) с щелевидными окнами, З – штампованные (просечные) с круглыми отверстиями.
Промышленность выпускает сита с отверстиями, имеющими размер ячейки от 5 мкм и выше. Существует несколько стандартов размеров сит, но все они составлены таким образом, что площадь отверстий ("площадь в свету") по отношению ко всей площади сита постоянна и составляет около 36% для сит с размером ячеек до 2,3 мм.
В нашей стране применяются несколько шкал размеров сит, поскольку применяются сита различных производителей.
Шкала ГОСТ 3584 и ISO 565 определяет размер сита по размеру стороны ячейки в мм.
Шкала Риттенгера (стандарт ANS) построена так, что площади отверстий соседних по шкале сит отличаются друг от друга в два раза.
Шкала Ричардсона (стандарт ASTM) построена так, что площади отверстий соседних сит отличаются друг от друга в Ö2 раз.
В обеих этих шкалах определяется количество отверстий на один линейный дюйм, которое называется "меш" (mesh).
Шкала DIN определяет число отверстий на линейный сантиметр при постоянной площади "в свету" ко всей площади сита 36% и соответствует шкалам ISO и ГОСТ.
В таблице 2 показаны системы обозначений сит и соотношения между шкалами.
Таблица 2.
Размеры ячеек сит по стандартам метрическим и дюймовым.
ГОСТ,
ISO
мкм
|
ANS, ASTM
меш
|
|
ГОСТ,
ISO
мкм
|
ANS, ASTM
меш
|
|
ГОСТ,
ISO
мкм
|
ANS, ASTM
меш
|
20
|
80
|
280
|
25
|
90
|
170
|
300 (50)
|
28
|
100
|
315
|
32
|
140 (106)
|
355
|
45
|
36
|
112
|
400
|
400 (38)
|
125
|
120
|
40 (425)
|
40
|
140
|
450
|
45
|
325
|
100 (150)
|
500
|
35
|
50
|
160
|
560
|
270 (53)
|
180
|
80
|
30 (600)
|
56
|
200
|
630
|
63
|
230
|
70 (212)
|
710
|
25
|
71
|
224
|
800
|
270 (73)
|
250
|
60
|
20 (850)
|
ПРИМЕЧАНИЕ. В скобках указаны размеры дюймовых сит в мкм, не имеющих аналогов в
метрической системе.
В ситовом анализе приняты следующие обозначения: класс (фракция) — интервал между размерами отверстий соседних полотен; остаток DR (фракция)— масса порошка, остающаяся на данном полотне, и проход D — разность загруженной в сито массой порошка и остатком.
По режиму работы различают сита с вертикальным и горизонтальным (вибрационные) перемещением рабочих полотен, качающиеся с неподвижными полотнами (воздушные или жидкоструйные), а также разбрасывающие и плоские механические грохоты.
Для аналитических целей наиболее распространены вибрационные грохоты (вибросита).
Наиболее распространенные вибросита для ситового анализа устроены однотипно – в тяжёлой станине монтируется механический или электромагнитный встряхиватель (вибратор), который приводит в возвратно-поступательное движение набор сит, собранный так, что самое мелкое сито находится внизу.
ГОСТ 18318 предписывает следующий порядок проведения ситового анализа металлических порошков. Выбранные сухие и чистые сита укладывают по возрастающему размеру ячеек одно над другим, поддон помещают под нижним ситом. Взвешенную пробу высыпают на верхнее сито и закрывают крышкой. Приготовленный таким образом набор сит помещают на встряхиватель и включают его. Время рассева-пробы составляет 30 мин, если просеивают ситах с сетками 80 мкм и менее.
|
Рис.5. Вибрационный грохот для ситового анализа. 1 – станина грохота с приводом колебательного движения, 2 – фиксирующие колонки, 3 – набор сит, 4 – зажим.
|
|
Рис.6. Аналитические сита с металлической проволочной сеткой.
|
|
Если в наборе самое мелкое сито имеет сетку крупнее 80 мкм, то время рассева определяют из опыта. Оно должно быть таким, чтобы при контрольном просеивании в течение 2 мин через самое мелкое сито набора проходило не более 0,5% массы взятой пробы.
По окончании рассева отдельные фракции высыпают из сит, начиная с сита с большими ячейками. Содержимое на сите осторожно стряхивают на одну сторону и пересыпают на глянцевую бумагу- Порошок, приставший к сетке или рамке сита, осторожно протирают легкой кистью через сетку в следующее сито с меньшими ячейками. Фракцию, высыпанную на глянцевую бумагу, взвешивают с точностью до 0,01 г.
Такую операцию повторяют для каждого сита и поддона. Масса всех фракций в сумме должна составлять не менее 99% массы испытываемой пробы. Разницу между этой суммой масс и массой пробы (100 г или 50 г) определяют по всем анализируемым фракциям пропорционально их массам.
Результаты анализа записывают в виде таблицы, причем содержание фракций, составляющих менее 0,1 %, записывают словом "следы". Для каждого порошка ситовый анализ проводят не менее двух раз. Расхождение между параллельными определениями соответствующих фракций не должно превышать 3 абс. %. За величину фракции принимают среднее арифметическое результатов параллельных определений.
Например, фракция порошка, оставшаяся на сите № 100, т. е. фракция, которая прошла через сетку № 112, но через сетку № 100 не проходит, именуется: фракция —100 +112 мкм (размер частиц от 100 до 112 мкм). Следующая фракция будет —90 +100 мкм (от 90 до 100 мкм) и т. д. вплоть до последней, — 20 мкм. Вес каждой фракции, отнесенный к весу всей пробы и умноженный на 100, представляет процентное содержание в пробе данной фракции. По результатам измерения составляется либо таблица, либо гистограмма, характеризующая гранулометрический состав пробы порошка.
Пример порошка хрома, рассеянного на фракции, показан на рисунке 100, на котором видно, что одинаковое количество частиц порошка занимает различный объём по мере уменьшения их размера.
Рис.7. Порошок хрома, рассеянный на фракции. Число зёрен в каждой кучке одинаково.
Угол естественного откоса.
При истечении сыпучего материала на горизонтальную плоскость образуется горка с некоторым углом откоса, соответствующим равновесию частиц. Угол между горизонтальной плоскостью и линией откоса называют углом естественного откоса. Он является наибольшим углом, который может быть образован плоскостью естественного откоса с горизонтальной плоскостью, и служит одним из основных показателей подвижности материала. Его величина определяется силами трения, которые зависят от формы, размера частиц и влажности. Увлажнение материала приводит к увеличению угла естественного откоса. В большинстве случаев угол естественного откоса сыпучих материалов не превышает 55—60°.
Наибольшая подвижность частиц сыпучего материала соответствует минимальному углу естественного откоса, по мере увеличения этого угла подвижность частиц уменьшается.
Угол естественного откоса необходимо учитывать при определении поперечного сечения ленточного питателя и полезной емкости бункера.
Различают угол естественного откоса материала в покое и в движении на поверхностях транспортирующих устройств. При движении опорная горизонтальная плоскость колеблется, величина угла естественного откоса уменьшается. Таким образом, угол естественного откоса в покое всегда больше угла естественного откоса в движении (fдв
« 0,7f). Угол естественного откоса обычно определяют с помощью специальных приборов. Иногда, если это необходимо, угол естественного откоса с достаточной точностью может быть определен следующим образом: отрезок цилиндрической трубы устанавливают вертикально на горизонтальной плоскости и заполняют испытуемым материалом.
|
Рис.8. Способы определения угла естественного откоса. А – с помощью убираемой трубы, Б – при свободном истечении из воронки. 1 – гладкая плита, 2 – труба, 3 – порошок, 4 – свободно отсыпанный порошок, a – угол естественного откоса
|
|
А Б
Затем трубу медленно поднимают. Высыпавшийся материал располагается на плоскости под углом естественного откоса.
Связность и слёживаемость.
Связными называют порошковые материалы, имеющие большое сопротивление сдвигу при небольших нормальных нагрузках. Связность определяют как сопротивление сыпучего материала силам, стремящимся разъединить его частицы, что является показателем прочности их сцепления.
Явления связности проявляются в основном в мелкофракционных материалах. В сыпучих материалах различают две связности — физико-механическую и физико-химическую. Физико-механическая связность характеризуется физико-механическими процессами, происходящими при взаимодействии частиц сыпучего материала. Физико-механической связностью обладают многие порошки металлов и тяжёлых оксидов (пылевидная трёхокись вольфрама, мелкозернистый карбид вольфрама, карбонильный никель и кобальт и др.)- При такой связности силы сцепления зависят от влажности, степени измельчения, формы частиц, степени взаимного сближения частиц и в основном определяются степенью уплотнения материала под действием сжимающих сил.
Физико-химическая связность заложена в самой природе порошков и обусловливается особенностями химического состава среды, растворимостью, гигроскопичностью и др.
Слёживаемостью называют свойство некоторых материалов терять текучесть при длительном хранении. Особенно благоприятные условия для слёживания создаются при длительном хранении порошков в емкостях в неподвижном состоянии. Под действием сжимающих сил в течение длительного времени многие порошки способны спрессовываться в конгломераты.
Таким образом, явление слёживаемости следует также рассматривать как одно из изменений сил сцепления частиц порошков. Слеживающиеся материалы — вольфрам, оксид кобальта, полиэтиленгликоль и др.
Связность и слёживаемость являются показателями прочности сцепления частиц сыпучего материала и измеряются в кгс/см2
. Значительно ускоряют процесс слёживаемости динамические нагрузки. Присутствующие в порошках влага и пылевидные частицы порядка 1-2 мкм и менее ускоряют процесс слёживаемости. Истечение такого материала из отверстия бункера крайне затруднено. Попытка нарушить сводообразование вибрацией или ударом приводит в таких случаях к образованию пустот, устойчивость которых зависит от сил сцепления частиц и диаметра отверстия. Легко подвергающиеся слёживанию порошки создают большие трудности при хранении и дозировании.
Сегрегация.
При заполнении емкости материалом, имеющим широкий диапазон по гранулометрическому составу, наблюдается явление сегрегации частиц материала.
Загруженный материал располагается в бункере конусообразно (под углом естественного откоса), причем крупные тяжелые фракции скатываются к стенкам бункера, а мелкие частицы сосредоточиваются в зоне канала истечения. Из отверстия бункера уходят преимущественно мелкие фракции.
Поэтому материал, засыпаемый в бункер, отличается от выпускаемого из него фракционным составом. В случае заполнения емкости шихтой, которая является смесью различных фракций, борьба с сегрегацией частиц является постоянной проблемой. Сегрегацию следует считать динамическим фактором, возникающим при свободном падении частиц.
Сегрегация увеличивает неоднородность порошка, поступающего из бункера в прессформу и как следствие – неоднородность прессовки, которая в дальнейшем, при спекании, вызывает неоднородность спечённого материала и неоднородность его механических свойств.
Только в бункерах непрерывного действия при одинаковых скоростях загрузки и истечения из выпускного отверстия выдается однородная смесь, не отличающаяся от загружаемой.
Эффективным способом подавления сегрегации является гранулирование шихты, при которой гранулы получают примерно одинакового размера и формы, а образующееся при гранулировании небольшое количество пыли отсеивают.
Прессуемость.
Способность порошка под влиянием сжимающего усилия приобретать и удерживать определенную форму и размеры (соответственно размерам прессформы) называют «прессуемостью» порошка. Далеко не всякий порошок обладает удовлетворительной прессуемостью, иначе говоря, некоторые порошки не могут быть спрессованы при практически осуществимых условиях прессования. Для достижения определенной степени прочности, порошок (или смесь порошков) данных химического состава и физических характеристик требует вполне определенных условий прессования (удельное давление, скорость, температура прессования и т. д.)
Крупность порошка резко сказывается на прессуемости. В то время как тонкий (—45мкм) и легкий (насыпной вес 0,8 г/см3
) электролитический медный порошок дает достаточно прочные прессовки с пористостью до 55% при удельном давлении 0,25 т/см2
, грубозернистый медный порошок (—140 +160 мкм, насыпной вес 1,8—2,2 г/см3
) начинает спрессовываться только при давлении 0,8—1,0 т/см2
, причем пористость в этом случае не превышает 40%. Наибольшую плотность прессовок дают порошки смешанного гранулометрического состава, с определенным соотношением крупных и мелких фракций; соотношение это определяется опытным путем. Форма частиц, как указывалось выше, также влияет на прессуемость.
Весьма важное значение имеет «жесткость» порошка: чем мягче (пластичнее) порошок, тем при меньших давлениях он начинает прессоваться и тем при данном давлении будет выше прочность и плотность прессовки. Неотожжённый электролитический железный порошок начинает прессоваться при давлениях порядка 5 т/см2
(при относительной плотности 60—65%); отожженный электролитический железный порошок прессуется уже при давлениях 0,75 т/см2
(относительная плотность 65— 70%), а при давлении 5 т/см2
дает относительную плотность до 85%. Улучшение прессуемости объясняется тем, что при отжиге удаляется поглощенный водород и снимается наклеп, в результате чего «жесткость» частиц порошка резко уменьшается.
Снижение давления прессования сказывается положительно на стойкости прессформ, снижает нормы расхода энергии и позволяет применить прессы облегченной конструкции, меньшей мощности и большей производительности.
В то время как форма частиц и гранулометрический состав порошка могут контролироваться непосредственно, пластичность обычно характеризуется косвенно-технологической пробой порошка на прессуемость. Эта проба может производиться одним из следующих способов:
1) точная навеска порошка прессуется при определенном давлении; плотность полученного образца не должна быть ниже установленной нормы;
2) прессуется образец определенных формы, веса, размеров (прессование до упора, давление не регистрируется); образец не должен иметь трещин, осыпания нижних граней, сколов;
3) образец, спрессованный по способу 1 или 2, подвергается разрушению при сжатии; сопротивление сжатию не должно быть меньше определенной величины;
4) определяется величина упругой деформации образца, спрессованного по способу 2 "до упора", т.е. увеличение размеров после снятия нагрузки и извлечения из контейнера. Это расширение тем больше, чем менее пластичен порошок, и для порошка данных состава, характеристик и условий прессования имеет вполне устойчивое постоянное значение. При определении упругой деформации удобно сравнивать размеры прессовок из испытуемого порошка, с размерами сравнительных (эталонных) образцов, спрессованных в том же инструменте из неупругих материалов, например парафина, воска и т. п.
Наиболее простой 2-й способ не дает количественных характеристик прессуемости порошка и применяется как метод оперативного контроля в тех случаях, когда для обеспечения высокой пористости, прессование производится при минимально допустимых давлениях. Способы 1-й и 4-й количественно отражают характеристики прессуемости порошка, кроме прочности прессовок. 3-й способ может быть рекомендован в тех случаях, когда прочность сырого полуфабриката имеет существенное значение на дальнейших стадиях технологического процесса (в частности, при прессовании изделий сложной формы или с тонкими стенками).
Во всяком случае характеристики порошка, предназначенного для целей порошковой металлургии, нельзя считать исчерпывающими, если в них не отражена "пластичность" порошка, определенная по меньшей мере одним из указанных способов.
Оценить прессуемость порошков не просто, так как наряду с формой и свойствами поверхности частиц надо учитывать их пластические и упругие свойства, зависящие от способа получения и предыстории порошка.
Также непросто связать давление прессования и плотность спрессованной заготовки применительно к реальному случаю и использовать такую связь практически. Для суждения о прессуемости порошков большей частью выгоднее использовать более близкое к практике технологическое опробование степени уплотнения. Рекомендуется каждый раз использовать для такого опробования количество порошка, позволяющее получать прессованную заготовку, высота которой примерно равна ее диаметру. Плотность такой заготовки и является мерой прессуемости (уплотняемости).Чтобы представить полностью связь между плотностью заготовки и давлением прессования, необходимо спрессовать ряд образцов при различных давлениях. Но можно и уплотнять определенную массу порошка при ступенчатом увеличении давления прессования, измеряя после каждой ступени высоту полученной заготовки (по высоте освобожденного пространства в матрице). Плотность образца определяют, зная поперечное сечение пуансона, массу порошка и высоту спрессованной заготовки. Степень уплотнения можно также вычислить по отношению уровня засыпки порошка к высоте спрессованного образца. Зная зависимость уплотнения от давления прессования, можно определить необходимый уровень засыпки, т. е. высоту матрицы. На уплотняемость наиболее влияют свойства материала порошка: чем он пластичнее, тем лучше его уплотняемость (рис. 9). Все факторы, затрудняющие пластическую деформацию компактного материала (примеси, легирующие присадки, повышенная плотность дислокаций и др.). затрудняют и прессование соответствующих порошков. К этому добавляется еще влияние формы их частиц. Оно особенно сильно при очень малых давлениях прессования и для губчатых порошков; при более высоких давлениях прессования влияния пластических свойств материала усиливаются.
Вследствие межчастичного трения грубые порошки уплотняются лучше тонких. Порошки с широким спектром размеров в области крупных частиц лучше прессуются. Облегчающие прессование присадки, снижающие трение, благоприятствуют уплотнению (рис. 10), но иногда они могут и ухудшить уплотняемость порошков.
Желая получить хорошо прессуемые порошки, к ним предъявляют подчас противоположные требования: они должны характеризоваться хорошей текучестью, малым насыпным объемом, возможно более высокой плотностью при малых давлениях и хорошей формуемостью. Хорошая текучесть и малый насыпной объем присущи порошкам со сферическими частицами. При прессовании таких порошков в тех или иных условиях еще можно достигнуть требуемой
|
|
Рис.9. Зависимость плотности прессовки r от давления прессования для различных порошков: 1 – алюминий, 2 – медь электролитическая, 3 – железо восстановленное, 4 – железо электролитическое, 5 – железо карбонильное, 6 – вольфрам.
|
|
Рис.10. Влияние пластификатора на уплотняемость порошка электролитической меди. 1 – без пластификатора, 2 – 0,1%, 3 – 1,5% пластификатора.
|
|
плотности, но не хорошей формоустойчивости, удовлетворяющей требованиям дальнейшей переработки. Поэтому желательно оценку уплотняемости (прессуемости) дополнять испытанием на формуемость. Для этой цели прессованные заготовки специально испытывают на формоустойчивость: их помещают во вращающийся барабан, обтянутый изнутри тканью для сит, ширина отверстий которых позволяет пропускать продукты истирания. Частное от деления массы заготовки до испытания (истирания в барабане) на ее исходное значение служит мерой формуемости порошка. Для качественной характеристики прессуемости порошка все чаще используют показатель сопротивления прессованной заготовки разрушению при изгибе.
Влажность
определяют как отношение массы испарившегося растворителя (воды, нефраса, спирта и др.) после просушивания к массе всего материала (в весовых процентах).
По содержанию влаги сыпучие материалы делятся на:
- сухие, содержащие конституционную влагу (химически связанную с материалом);
- содержащие гигроскопическую влагу (гигроскопическая влага содержится в порошках, склонных к поглощению влаги из воздуха, таких, как порошок меди, железа и другие);
- сырые и мокрые, содержащие внешнюю влагу; внешняя влага может быть пленочной, образующей водяную пленку на поверхности частиц сыпучего материала (в этом случае сыпучий материал считают сырым), и гравитационной, заполняющей свободные пространства между частицами (в этом случае сыпучий материал считают мокрым, так как он фактически превращается в суспензию) таковой, например, является недосушенная шихта.
Влажностью сыпучего материала определяется подвижность его частиц. Увеличение влажности, как правило, ухудшает характеристику истечения сыпучего материала. Сыпучий материал с повышенной влажностью обладает большими силами сцепления частиц, что способствует образованию комьев и статических сводов над отверстием воронки бункера. Истечение такого материала из отверстия емкости крайне затруднено. Затруднено и заполнение полости прессформы.
Обычно мелкофракционные материалы относят к легкосвязанным материалам, если их влажность не превышает 1,5%.
Поскольку влажность порошка определяет его поведение при транспортировке и прессовании, то эту важную технологическую характеристику всегда определяют для порошков, предназначенных для прессования на автоматах.
Для определения влажности применяют специальные точные весы, установленные в инфракрасной печи. Пробу массой 50 или 100 г помещают на чашу (платформу) весов и взвешивают в исходном состоянии. Включают инфракрасный нагреватель и отмечают уменьшение массы пробы. Испытания завершают при достижении пробой температуры выше температуры кипения увлажняющего вещества. Отношение разности исходной пробы и пробы просушенной к массе исходной пробы и определяет влажность порошка.
Следует отметить, что пересушенные порошки плохо формуются и поэтому влагу из шихты (пресспорошка) полностью удалять не рекомендуется. Обычно путём технологических экспериментов определяют оптимальную влажность шихты, которую затем и оговаривают в технических условиях.
Заметим, что существуют способы "мокрого" прессования, при которых пресспорошок доставляется в прессформу в виде пульпы. Влага отсасывается через систему каналов в прессформе вакуумным насосом в момент прессования. Так прессуют, например заготовки магнитов из ферритов, керамические детали электротехнического назначения и другие изделия из керамических масс.
Спекаемость и усадка.
Все предыдущие технологические свойства относились к операциям, предшествующим спеканию – операции, при выполнении которой формируются окончательные размеры и физико-механические свойства готового изделия: твёрдость, прочность, плотность и другие служебные характеристики. Поэтому важное место в определении качества партии шихты является определение спекаемости и усадки. Поскольку определение большинства физико-механических свойств материалов сопровождается обязательным разрушением (определение пределов прочности, твёрдости ), то, как правило, одновременно с прессованием партии изделий, прессуют и специальные образцы, так называемые "режимки". Эти образцы имеют определённые размеры, установленные стандартами, например - ГОСТ 20019- для образцов из твёрдых сплавов. После спекания одновременно с партией изделий, отпрессованных из одной и той же партии шихты, образцы подвергают различным испытаниям, во время которых определяют: твёрдость, предел прочности при поперечном изгибе, предел прочности при растяжении, предел прочности при сжатии, модуль Юнга, гидростатическую плотность, коэрцитивную силу и все другие служебные характеристики материала. Кроме прочего на образцах исследуются фрактограммы, то есть изломы, и характеристики микроструктуры: пористость, величина и распределение зерен, посторонние включения, ликвация и т.д.
Усадка при спекании – это технологический параметр, характеризующий изменение линейных размеров прессовки. Линейная усадка определяется как простое отношение одного из параметров изделия после спекания к тому же параметру до спекания. Поскольку усадка в направлении прессования и в направлении перпендикулярном оси прессования могут отличаться зачастую определяют и усреднённый параметр – объемную усадку, как отношение объемов изделия до спекания к объёму после него.
Некоторые авторы рекомендуют определять коэффициент усадки равный отношению изменения линейного размера к его величине до спекания. Этот параметр более усреднённый, но не отражает возможного изменения параметров шихты различных партий.
По величине усадки проектируются размеры полости прессформы. Поскольку шихта одной
марки, но разных партий может иметь (и имеет) различную усадку, то на практике обычно рассчитывают и изготавливают прессформы по размерам максимальной, средней и наименьшей из возможных усадок, характерных для данного материала. Это требует изготовления по крайней мере трёх комплектов прессформ, но позволяет мобильно переходить от одной партии шихты к другой, не затрачивая времени на дополнительные определения усадки для каждой партии шихты, проектирования и изготовления по полученный результатам испытаний новой прессформы.
ЛАБОРАТОРНАЯ РАБОТА №1.
1.1. Определение насыпной плотности.
1.1.1. АППАРАТУРА И МАТЕРИАЛЫ
1. Установка для определения насыпной плотности ……………………………ГОСТ 19440-74
2. Весы ………………………………………………………………………………………
3. Плоскопараллельная плитка-калибр с установочным размером 25 мм*
4. Линейка металлическая 100 мм
5. Шихта (порошок) , г ……………….…………………………………………………………100
* Высота плитки – 23 мм, поскольку выходное отверстие воронки заглублено на 2 мм, чтобы удобнее было закрывать отверстие пальцем (23 + 2 = 25 мм).
1.1.2. ПРИНЦИП РАБОТЫ УСТАНОВКИ ДЛЯ ОПРЕДЕЛЕНИЯ НАСЫПНОЙ ПЛОТНОСТИ
Установка для определения насыпной плотности показана на рисунке 11.
Рис.11. Установка для определения насыпной плотности. 1 – штатив (стойка), 2 – Воронка с калиброванным отверстием диаметром 5 мм, 3 – мерная ёмкость объёмом 25 см3
.
|
|
Порядок работы по ГОСТ 19440 при измерении насыпной плотности следующий:
Вначале взвешивают пустую сухую мерку (стакан), изготовленую из полированной нержавеющей стали. Мерку подставляют под отверстие в воронке и устанавливают расстояние между нижним краем воронки и верхним обрезом мерки равным 25 мм при помощи контрольной плоскопараллельной плитки. Затем сухим пальцем снизу закрывают отверстие D = 5 мм воронки 2, заполняют её сухим порошком, открывают отверстие и дают порошку истечь в мерную калиброванную емкость 3. Ребром линейки одноразовым движением, не оказывая давления на поверхность порошка и не встряхивая его, снимают "верх". Для удобства переноски мерки с порошком на весы после выравнивания поверхности порошка слегка постукивают по внешней поверхности мерки, чтобы порошок слегка осел и не рассыпался при перемещении. Мерку с порошком взвешивают с точностью до 0,05 г, от веса заполненной порошком мерки вычитают вес мерки, определённый ранее, и чистый вес порошка делят на объем калиброванной емкости 25 см3
. Определение выполняют на трёх испытуемых порциях.
А Б В
Рис.12. Порядок определения насыпной плотности.
1 - штатив, 2 - воронка, 3 - стакан емкостью 25 см3
, 4 –
мерная плитка. А – Установка воронки на требуемой вы-
соте над меркой, Б – Засыпка порошка в воронку, В – мерка,
заполненная порошком "с верхом".
1.1.3. ПОРЯДОК ВЫПОЛНЕНИЯ РАБОТЫ
Насыпную плотность определяют в порядке описанном в п.1.1.2., затем по формуле
g нас
= г/см3
, где
- G1
- масса мерки, г;
- G2
- масса мерки с порошком, г;
- V - объем мерки, см3
(25 см3
).
Испытания проводят три раза и берут среднее арифметическое.
1.1.4. ТРЕБОВАНИЯ К ОТЧЕТУ
Отчет должен содержать краткое описание технологических характеристик порошковых материалов, с указанием значения определения насыпной плотности при изготовлении деталей из порошков и порядок выполнения работы. В отчёте должен содержаться протокол испытаний.
Объем отчета 2-4 стр.
Отчет подписывается студентом.
1.1.5. ЛИТЕРАТУРА.
1. Кипарисов С.С., Либенсон Г.А. Порошковая металлургия. Учебник. М., Металлургия, 1980, с 198-200.
2. Порошки металлические. Метод определения насыпной плотности. ГОСТ 19440.
1.1.6. КОНТРОЛЬНЫЕ ВОПРОСЫ.
1. Для чего определяется насыпная плотность ?
2. Как насыпная плотность влияет на свойства спрессованных заготовок ?
2. Какие свойства спеченных изделий определяет насыпная плотность ?
1.1.7. ПРОТОКОЛ ИЗМЕРЕНИЙ.
В протоколе записываются: описание порощка (шихты), материал порошка, фракционный состав,
характеристика формы частиц (гранул) по паспортным данным и даётся таблица измерений, шапка которой приведена ниже.
Номер измерения
|
Масса порошка, г
|
Насыпная плотность, г/см3
|
Среднее значение насыпной плотности, г/см3
|
ЛАБОРАТОРНАЯ РАБОТА №2
1.2. Влияние насыпной плотности на степень заполнения прессформы
1.2.1. АППАРАТУРА И МАТЕРИАЛЫ
1. Установка для определения насыпной плотности ……………………………ГОСТ 19440-74
2. Весы ………………………………………………………………………………………
3. Плоскопараллельная плитка-калибр с установочным размером 25 мм*
4. Линейка металлическая 100 мм
5. Три партии порошка хрома различной крупности …………………………………………100
* Высота плитки – 23 мм, поскольку выходное отверстие воронки заглублено на 2 мм, чтобы удобнее было закрывать отверстие пальцем (23 + 2 = 25 мм).
1.2.2. ПОРЯДОК ВЫПОЛНЕНИЯ РАБОТЫ.
Работу проводят, используя установку для определения насыпной плотности, которая показана показана на рисунке 13.
Полость прессформы моделируют с помощью мерки.
Вначале взвешивают пустую сухую мерку (стакан), изготовленую из полированной нержавеющей стали. Мерку подставляют под отверстие в воронке и устанавливают расстояние между нижним краем воронки и верхним обрезом мерки равным 25 мм при помощи контрольной плоскопараллельной плитки. Затем сухим пальцем снизу закрывают отверстие D = 5 мм воронки 2, заполняют её сухим порошком, открывают отверстие и дают порошку истечь в мерную калиброванную емкость 3. Ребром линейки одноразовым движением, не оказывая давления на поверхность порошка и не встряхивая его, снимают "верх". Для удобства переноски мерки с порошком на весы после выравнивания поверхности порошка слегка постукивают по внешней поверхности мерки, чтобы порошок слегка осел и не рассыпался при перемещении. Мерку с порошком взвешивают с точностью до 0,05 г, от веса заполненной порошком мерки вычитают вес мерки, определённый ранее, и чистый вес порошка делят на объем калиброванной емкости 25 см3
. Измерения повторяют три раза, используя порошок хрома различной крупности.
Определяют насыпную плотность по формуле
g нас
= г/см3
, где
- G1
- масса мерки, г;
- G2
- масса мерки с порошком, г;
- V - объем мерки, см3
(25 см3
).
А Б В
Рис.13. Порядок определения зависимости заполнения прессформы от насыпной плотности
1 - штатив, 2 - воронка, 3 - стакан емкостью 25 см3
, 4 – мерная плитка.
А – Установка воронки на требуемой высоте над меркой, Б – Засыпка порошка в
воронку, В – мерка, заполненная порошком "с верхом".
и строят график зависимости массы заполненной мерки, которая является в данном случае моделью полости прессформы, от насыпной плотности соответствующего порошка и от его крупности.
1.2.3. ТРЕБОВАНИЯ К ОТЧЕТУ
Отчет должен содержать краткое описание технологических характеристик порошковых материалов, с указанием значения определения насыпной плотности при изготовлении деталей из порошков и порядок выполнения работы. В отчёте должен содержаться протокол испытаний.
Объем отчета 2-4 стр.
Отчет подписывается студентом.
1.2.4. ЛИТЕРАТУРА.
1. Кипарисов С.С., Либенсон Г.А. Порошковая металлургия. Учебник. М., Металлургия, 1980, с 198-200.
2. Порошки металлические. Метод определения насыпной плотности. ГОСТ 19440-74.
1.2.5. КОНТРОЛЬНЫЕ ВОПРОСЫ.
1. Какова зависимость заполнения прессформы от крупности порошка?
2 Какова зависимость заполнения прессформы от насыпной плотности?
3. Какие свойства спеченных изделий определяет насыпная плотность ?
1.2.6. ПРОТОКОЛ ИЗМЕРЕНИЙ.
В протоколе записываются: описание порощка (шихты), материал порошка, фракционный состав,
характеристика формы частиц (гранул) по паспортным данным и даётся таблица измерений, шапка которой приведена ниже.
Номер измерения
|
Масса порошка,
г
|
Насыпная плотность,
г/см3
|
Размер частиц порошка,
мкм
|
Графики, построенные в результате данной работы должны выглядеть примерно так, как показано на рисунке 14.
ЛАБОРАТОРНАЯ РАБОТА №3
Рис. 14. Примерный вид графиков к работе 1.2
ЛАБОРАТОРНАЯ РАБОТА №3
1.3. Зависимость насыпной плотности от формы частиц.
1.3.1. АППАРАТУРА И МАТЕРИАЛЫ
1. Установка для определения насыпной плотности ……………………………...……ГОСТ 19440
2. Весы ………………………………………………………………………………..……
3. Плоскопараллельная плитка-калибр с установочным размером 25 мм*
4. Линейка металлическая 100 мм
5. Три партии порошков с разнрй формой частиц: округлой, чешуйчатой, произвольной,
но одинакового размера, по 100 г
* Высота плитки – 23 мм, поскольку выходное отверстие воронки заглублено на 2 мм, чтобы удобнее было закрывать отверстие пальцем (23 + 2 = 25 мм).
1.3.2. ПОРЯДОК ВЫПОЛНЕНИЯ РАБОТЫ.
Работу проводят, используя установку для определения насыпной плотности, которая показана показана на рисунке 15.
Вначале взвешивают пустую сухую мерку (стакан), изготовленую из полированной нержавеющей стали. Мерку подставляют под отверстие в воронке и устанавливают расстояние между нижним краем воронки и верхним обрезом мерки равным 25 мм при помощи контрольной плоскопараллельной плитки. Затем сухим пальцем снизу закрывают отверстие D = 5 мм воронки 2, заполняют её сухим порошком, открывают отверстие и дают порошку истечь в мерную калиброванную емкость 3. Ребром линейки одноразовым движением, не оказывая давления на поверх
А Б В
Рис.15. Порядок определения зависимости заполнения прессформы от насыпной плотности
1 - штатив, 2 - воронка, 3 - стакан емкостью 25 см3
, 4 – мерная плитка.
А – Установка воронки на требуемой высоте над меркой, Б – Засыпка порошка в
воронку, В – мерка, заполненная порошком "с верхом".
ность порошка и не встряхивая его, снимают "верх". Для удобства переноски мерки с порошком
на весы после выравнивания поверхности порошка слегка постукивают по внешней поверхности
мерки, чтобы порошок слегка осел и не рассыпался при перемещении. Мерку с порошком взвеши
вают с точностью до 0,05 г, от веса заполненной порошком мерки вычитают вес мерки, опреде-
лённый ранее, и чистый вес порошка делят на объем калиброванной емкости 25 см3
. Измерения
повторяют три раза, используя порошки одинаковой фракции, но с различной формой частиц.
Определяют насыпную плотность по формуле
g нас
= г/см3
, где
- G1
- масса мерки, г;
- G2
- масса мерки с порошком, г;
- V - объем мерки, см3
(25 см3
).
И строят гистограмму зависимости насыпной плотности от формы частиц
1.3.3. ТРЕБОВАНИЯ К ОТЧЕТУ
Отчет должен содержать краткое описание технологических характеристик порошковых материалов, с указанием значения определения насыпной плотности при изготовлении деталей из порошков и порядок выполнения работы. В отчёте должен содержаться протокол испытаний.
Объем отчета 2-4 стр.
Отчет подписывается студентом.
1.3.4. ЛИТЕРАТУРА.
1. Кипарисов С.С., Либенсон Г.А. Порошковая металлургия. Учебник. М., Металлургия, 1980, с 198-200.
2. Порошки металлические. Метод определения насыпной плотности. ГОСТ 19440-74.
1.3.5. КОНТРОЛЬНЫЕ ВОПРОСЫ.
1. Как зависит насыпная плотность от формы частиц одинаковой крупности?
2 Какая форма частиц обеспечивает наиболее полное заполнение посълости прессформы?
3. Какие свойства спеченных изделий определяет насыпная плотность ?
1.3.6. ПРОТОКОЛ ИЗМЕРЕНИЙ.
В протоколе записываются: описание порощка (шихты), материал порошка, фракция, характеристика формы частиц (гранул) по паспортным данным и даётся таблица измерений, шапка которой приведена ниже.
Номер измерения
|
Масса порошка,
г
|
Насыпная плотность,
г/см3
|
Форма частиц порошка
|
Гистограмма, построенная в результате данной работы должна выглядеть примерно так, как показано на рисунке 16.
Рис.16. Примерный вид гистограммы к работе 1.3
1 – округлые частицы порошка, 2 – частицы чешуйчатой формы;
3 – частицы игольчатой формы.
ЛАБОРАТОРНАЯ РАБОТА №4.
1.4. Определение текучести.
Рис.17. Установка для определения текучести. 1 - стойка, 2 - воронка с калиброванным отверстием 2,5 мм, 3 - чашка, 4 - основание.
|
|
1.4.1. АППАРАТУРА И МАТЕРИАЛЫ 1. Установка для определения текучести………….…ГОСТ 19440
2. Весы ………………………………………………………
3. Секундомер
5. Шихта (порошок) , г ……………….…………………………150
1.4.2. ОПИСАНИЕ РАБОТЫ НА УСТАНОВКЕ ДЛЯ ОПРЕДЕЛЕНИЯ ТЕКУЧЕСТИ
Установка для определения текучести показана на рисунке 18.
Порядок работы по ГОСТ 19440 при измерении текучести следующий:
А Б
Рис.18. Порядок определения текучести. А – установка воронки и засыпка порошка в воронку,
Б – истечение порошка. 1 - штатив, 2 - воронка, 3 - приёмный стакан.
Вначале взвешивают пробу порошка массой 50 г с точностью 0,1 г. Затем сухим пальцем снизу закрывают отверстие D = 5 мм воронки 2, заполняют её сухим порошком, открывают отверстие,
включают секундомер и дают порошку истечь в мерную калиброванную емкость 3. В момент прекращения истечения порошка секундомер выключают. Определение выполняют на трёх испытуемых порциях.
1.4.3. ПОРЯДОК ВЫПОЛНЕНИЯ РАБОТЫ
Испытания проводят три раза и берут среднее арифметическое.
1.4.4. ТРЕБОВАНИЯ К ОТЧЕТУ
Отчет должен содержать краткое описание технологических характеристик порошковых материалов, с указанием значения определения текучести порошка при изготовлении деталей и порядок выполнения работы. В отчёте должен содержаться протокол испытаний.
Объем отчета 2-4 стр.
Отчет подписывается студентом.
1.4.5. ЛИТЕРАТУРА.
1. Кипарисов С.С., Либенсон Г.А. Порошковая металлургия. Учебник. М., Металлургия, 1980, с 198-200.
2. Порошки металлические. Метод определения текучести. ГОСТ 19440.
1.4.6. КОНТРОЛЬНЫЕ ВОПРОСЫ.
1. Что такое текучесть порошка ?
2. Для чего определяется текучесть?
2. От каких свойств порошка зависит текучесть?
1.4.7. ПРОТОКОЛ ИЗМЕРЕНИЙ.
В протоколе записываются: описание порощка (шихты), материал порошка, фракционный состав, характеристика формы частиц (гранул) по паспортным данным и даётся таблица измерений, шапка которой приведена ниже.
Номер измерения
|
Масса порошка, г
|
Время истечения порошка, сек
|
Среднее значение текучести, сек
|
ЛАБОРАТОРНАЯ РАБОТА №5.
1.5. Влияние размера частиц (текучести) порошка на скорость его транспортировки по коммуникациям пресса-автомата.
1.5.1. АППАРАТУРА И МАТЕРИАЛЫ
1. Вибропитатель с лотком ………………………………………………………………..
2. Весы ………………………………………………………………………………………
3. Секундомер
4. Линейка 300 мм
5. Шихта (порошок) с различной текучестью (не менее трёх партий) …………. по 100 г каждой.
1.5.2. ОПИСАНИЕ РАБОТЫ НА УСТАНОВКЕ ДЛЯ ОПРЕДЕЛЕНИЯ СКОРОСТИ ТРАНСПОРТИРОВКИ ПОРОШКА ПО ВИБРОЛОТКУ
Установка для определения скорости движения порошка по вибролотку показана на рисунке 19.
Порядок работы на установке следующий. Вначале взвешивают пробу порошка массой 100 г с точностью 0,1 г. Затем пробу высыпают через воронку 1 в лоток установки 2 и включают одновременно привод вибролотка и секундомер. После прохождения порции порошка по вибролотку секундомер выключают и повторяют опыт с порциями порошков другой фракции.
1.5.3. ТРЕБОВАНИЯ К ОТЧЕТУ
Отчет должен содержать краткое описание технологических характеристик порошковых материалов, с указанием значения определения текучести порошка различной крупности по комму-
никациям пресса-автомата и порядок выполнения работы, а также описание различных способов
повышения текучести порошков: придание частицам порошка округлой формы, грануляцию, применение вибраций и встряхиваний и т.д. В отчёте должен содержаться протокол испытаний. Объем отчета 2-4 стр. Отчет подписывается студентом
Рис.19. Установка для определения скорости
транспортировки порошка по вибролотку
1.5.4. ЛИТЕРАТУРА.
|
|
студентом. 1. Кипарисов С.С., Либенсон Г.А. Порошковая металлургия. Учебник. М., Металлургия, 1980, с 198-200.
2. Порошки металлические. Метод определения текучести. ГОСТ 19440.
1.5.5. КОНТРОЛЬНЫЕ ВОПРОСЫ.
1. Что такое текучесть порошка ?
2. Для чего определяется текучесть?
2. Какие способы увеличения текучести Вы знаете?
1.5.6. ПРОТОКОЛ ИЗМЕРЕНИЙ.
В протоколе записываются: описание порощка (шихты), материал порошка, фракционный состав, характеристика формы частиц (гранул) по паспортным данным и даётся таблица измерений, шапка которой приведена ниже.
Номер измерения
|
Фракция порошка, мкм
|
Время прохождения порошка по лотку, сек
|
Скорость движения порошка, мм/мин
|
Отчёт должен содержать график зависимости скорости перемещения порошка от размера частиц, примерный вид которого показан рядом. Для построения зависимость скорости транспортировки порошка от текучести используют значения текучести, полученные в предыдущей лабораторной работе.
|
|
Рис.20. Примерный вид зависимости скорости подачи по вибролотку от размера частиц
|
|
ЛАБОРАТОРНАЯ РАБОТА №6.
1.6. Определение угла естественного откоса.
1.6.1. АППАРАТУРА И МАТЕРИАЛЫ
1. Установка для определения текучести………….. …………………..……………ГОСТ 19440
2. Весы ………………………………………………………………………………………
3. Штангенугломер
5. Шихта (порошок) , г ……………….…………………………………………………………450
1.6.2. ОПИСАНИЕ РАБОТЫ НА УСТАНОВКЕ ДЛЯ ОПРЕДЕЛЕНИЯ ТЕКУЧЕСТИ ПРИ ОПРЕДЕЛЕНИИ УГЛА ЕСТЕСТВЕННОГО ОТКОСА.
Установка для определения текучести показана на рисунке 21.
Порядок работы при измерении угла естественного откоса следующий:
Вначале взвешивают пробу порошка массой 150 г с точностью 0,1 г. Затем сухим пальцем снизу закрывают отверстие D = 5 мм воронки 2, заполняют её сухим порошком, открывают отверстие, и дают порошку истечь на плоскую поверхность основания штатива. Затем, стараясь не повредить поверхность насыпавшейся горки порошка, измеряют угол между плоскостью основания и поверхностью порошка. Угол естественного откоса будет равен 180О
минус значение измеренного угла. Определение выполняют на трёх испытуемых порциях.
А Б
Рис.21. Установка для определения угла естественного откоса.
1 - штатив, 2 - воронка, 3 - штангенугломер.
А – установка воронки и засыпка порошка в воронку,
В – истечение порошка и измерение дополнительного угла
|
|
1.6.3. ТРЕБОВАНИЯ К ОТЧЕТУ
Отчет должен содержать краткое описание технологических характеристик порошковых материалов, с указанием значения определения угла естественного откоса, его роли при проектировании бункеров и транспортёров, а также порядок выполнения работы. Следует особо отметить изменение угла естественного откоса от размеров частиц порошка и формы частиц.
В отчёте должен содержаться протокол испытаний.
Объем отчета 2-4 стр.
Отчет подписывается студентом.
1.6.4. ЛИТЕРАТУРА.
1. Кипарисов С.С., Либенсон Г.А. Порошковая металлургия. Учебник. М., Металлургия, 1980, с 198-200.
2. Порошки металлические. Метод определения текучести. ГОСТ 19440.
1.6.5. КОНТРОЛЬНЫЕ ВОПРОСЫ.
1. Что такое угол естественного откоса порошка ?
2. Как этот угол влияет на конструкцию бункеров и транспортёров?
2. От каких свойств порошка зависит угол естественного откоса?
1.6.6. ПРОТОКОЛ ИЗМЕРЕНИЙ.
В протоколе записываются: описание порощка (шихты), материал порошка, фракционный состав, характеристика формы частиц (гранул) по паспортным данным и даётся таблица измерений, шапка которой приведена ниже.
Номер измерения
|
Размер частиц порошка, мкм
|
Измеренный угол,
град.
|
Угол естественного откоса, град.
|
В отчёте должен быть помещён график зависимости угла естественного откоса, от размера частиц (текучести), примерный вид которого показан на рисунке 21.
Рис.22. Примерный вид графика в
отчёте к лабораторной работе № 6
ЛАБОРАТОРНАЯ РАБОТА №7.
1.7. Определение влажности шихты.
1.7.1. АППАРАТУРА И МАТЕРИАЛЫ
1. Печь камерная лабораторная …………………………………………....
2. Весы ………………………………………………………………………………………
3. Шихта (порошок) , г ……………….…………………………………………………………450
1.7.2. ОПИСАНИЕ РАБОТЫ НА УСТАНОВКЕ ДЛЯ ОПРЕДЕЛЕНИЯ ВЛАЖНОСТИ ПОРОШКОВЫХ МАТЕРИАЛОВ
Влажность порошка или шихты определяют, используя лабораторную печь, показанную на рисунке 23.
Порядок работы при измерении влажности шихты (порошка) следующий:
Вначале взвешивают пробу порошка массой 10 г с точностью 0,01 г. Затем пробу помещают в печь и нагревают со скоростью не выше 5О
/сек до температуры испарения увлажняющих веществ – воды, растворителей и др. Обычно нагревают до температуры 170+
10О
С и выдерживают при этой температуре 20 – 30 мин. После охлаждения образца до комнатной температуры, которое производят вместе с печью, образец взвешивают.
Определяют относительную влажность в процентах, которая равна:
x = , где m1
– масса образца до просушивания;
m2
– масса образца после просушивания.
Определение выполняют на трёх испытуемых порциях.
Рис.23. Лабораторная камерная печь. 1 – кожух печи, 2 – дверца печи со слоем теплоизоляции, 3 - отверстие в дверце для наблюдения ("гляделка"), 4 – камера печи, 5 – тигель с образцом, 6 – теплоизоляция камеры, 7 – приборы контроля и управления.
|
|
1.7.3. ТРЕБОВАНИЯ К ОТЧЕТУ
Отчет должен содержать краткое описание технологических характеристик порошковых материалов, с указанием значения влажности на технологические свойства шихты: насыпную плотность, текучесть, угол естественного откоса и другие, а также порядок выполнения работы. В отчёте должен содержаться протокол испытаний.
Объем отчета 2-4 стр.
Отчет подписывается студентом.
1.7.4. ЛИТЕРАТУРА.
1. Кипарисов С.С., Либенсон Г.А. Порошковая металлургия. Учебник. М., Металлургия, 1980, с 198-200.
1.7.5. КОНТРОЛЬНЫЕ ВОПРОСЫ.
1. Откуда возникает влажность шихты или порошки, подготовленных к прессованию?
2. Как влажность шихты влияет на её основные технологические свойства?
2. Как можно уменьшить влажность порошков, какие при этом следует выполнять защитные меры?
1.7.6. ПРОТОКОЛ ИЗМЕРЕНИЙ.
В протоколе записываются: описание порощка (шихты), материал порошка, фракционный состав,
характеристика формы частиц (гранул) по паспортным данным и даётся таблица измерений, шапка которой приведена ниже.
Номер измерения
|
Масса порошка в исходном состоянии, г
|
Масса порошка после просушивания, г
|
Изменение массы порошка, г
|
Относительная влажность, %
|
ЛАБОРАТОРНАЯ РАБОТА №8.
1.8. Определение склонности шихты порошка к зависанию и сводообразованию.
1.8.1. АППАРАТУРА И МАТЕРИАЛЫ
1. Установка для определения склонности шихты к зависанию
5. Шихта (порошок) , г ……………….…………………………………………………………450
1.8.2. ОПИСАНИЕ РАБОТЫ НА УСТАНОВКЕ ДЛЯ ОПРЕДЕЛЕНИЯ СКЛОННОСТИ ШИХТЫ К ЗАВИСАНИЮ И СВОДООБРАЗОВАНИЮ.
Установка для определения склонности шихты (порошка) к зависанию и сводообразованию показана на рисунке 24.
Порядок работы на установке следующий:
В воронку вставляют калиброванную дюзу (фильеру) диаметром 5 мм. Затем сухим пальцем снизу закрывают отверстие, заполняют воронку сухим порошком, открывают отверстие, и дают порошку истечь в приёмную ёмкость. Затем дюзу с диаметром отверстия 5 мм заменяют на дюзу с отверстием диаметром 4 мм и опыт повторяют. Постепенно заменяя дюзы, определяют момент прекращения истечения порошка через отверстие – дюза с таким отверстием и будет той, при которой начинается зависание шихты и сводообразование.
Определение выполняют на трёх испытуемых порциях.
1.8.3. ТРЕБОВАНИЯ К ОТЧЕТУ
Отчет должен содержать краткое описание технологических характеристик порошковых материалов, с указанием значения определения склонности порошков к сводообразованию и зависанию, значение этого параметра при проектировании бункеров, требопроводов и прессформ. Следует особо отметить влияние размеров частиц и их формы на склонность порошков к зависанию и сводообразованию
В отчёте должен содержаться протокол испытаний.
Объем отчета 2-4 стр.
Отчет подписывается студентом.
А Б
Рис.24. Установка для склонности шихты к сводообразованию и зависанию.
1 - штатив, 2 - воронка, 3 - приёмная ёмкость, 4 – сменные сопла (дюзы), 5 – свод при зависании порошка. А – установка воронки и засыпка порошка в воронку, В – истечение порошка.
|
|
1.8.4. ЛИТЕРАТУРА.
1. Кипарисов С.С., Либенсон Г.А. Порошковая металлургия. Учебник. М., Металлургия, 1980, с 198-200.
1.8.5. КОНТРОЛЬНЫЕ ВОПРОСЫ.
1. Что такое зависание и сводообразование?
2. Как это явление сказывается на работе технологических установок?
2. От каких свойств порошка зависит это явление?
1.8.6. ПРОТОКОЛ ИЗМЕРЕНИЙ.
В протоколе записываются: описание порощка (шихты), материал порошка, фракционный состав,
характеристика формы частиц (гранул) по паспортным данным и даётся таблица измерений, шапка которой приведена ниже.
Номер измерения
|
Диаметр дюзы, мм
|
Отметка о наличии явления
|
ТЕМА №2 ИЗУЧЕНИЕ ПРОЦЕССОВ ПРИГОТОВЛЕНИЯ ШИХТЫ
Измельчение различных порошков металлов и тугоплавких соединений, смешивание их в необходимых пропорциях в соответствии с составом порошковой композиции, замешивание с пластификатором, сушка, рассев смеси и её грануляция являются теми операциями, на которых закладываются основные технологические свойства шихты, определяющие её поведение при прессовании и спекании, а также основными переделами, при которых устанавливаются физико-механические свойства будущего спечённого материала. Особенность операций по приготовлению шихты заключается в том, что любые отклонения от установленной технологии при операциях приготовления шихты являются необратимыми и приводят к неисправимому браку и это требует особой тщательности при проведении операций дозирования порошков, подбора гранулометрического состава смесей, смешивания, сушки и грануляции.
Механическое измельчение материалов широко распространено в технологии изготовления изделий из порошков.
Применяются различные способы механического измельчения, но в их основе лежит разрушение под действием внешних усилий, преодолевающих внутренние силы сцепления.
Способами механического разрушения можно превратить в порошок, а вернее - в частицы требуемого размера, любой из известных материалов.
Основными технико-экономическими показателями работы машин для измельчения материалов являются:
- степень измельчения;
- удельный расход энергии;
- эксплуатационные расходы на единицу массы порошка.
Эти показатели меняются в зависимости от способа измельчения, типа машины и измельчаемого материала.
Степенью измельчения называется отношение размера поперечника куска материала до измельчения к размеру поперечника куска (частиц) после измельчения:
D
i = ─── ;
d
где i - степень измельчения;
D - средний размер поперечника куска материала до измельчения;
d - средний размер поперечника куска материала после измельчения.
В существующих машинах измельчение материалов производится, в осноном, путем обработки материалов резанием с получением мелких стружек или опилок на токарных, фрезерных или шлифовальных станках, либо путем дробления в дробилках: щековых (челюстных), конусных, вальцевых, молотковых, дезинтеграторах и т.п. и истирания в мельницах: барабанных шаровых, центробежных, вибрационных, аттриторах и т.п.
Во многих машинах различные способы измельчения материала: раздавливание, раскалывание, истирание, удар, резание комбинируются для повышения эффективности процесса.
Процесс измельчения является весьма сложной операцией и зависит от многих факторов, основными из которых являются свойства измельчаемого материала: однородность, плотность, вязкость, твердость, прочность, форма кусков, степень влажности и другие сойства, трудно подда-
ющиеся учету.
Именно поэтому важное значение приобретает определение основных параметров процесса измельчения путем проведения технологического эксперимента и установления основных нормируемых параметров того оборудования, которое установлено, или планируется к установке, в цехе.
Основным процессом, протекающим при измельчении, является деформация исходного куска (твердого тела) под действием подведенной механической энергии. Подведенная энергия затрачивается в основном на упругую и пластическую деформацию, на теплоту и образование новых поверхностей.
Процесс разрушения твердых тел заключается в том, что под действием внешних сил, напряжения, возникающие в твердом теле, оказываются достаточными для разрыва связей между атомами (Р = 0,1Е). Это значение напряжения называют теоретической прочностью. После достижения этой величины напряженное тело должно взрывообразно рассыпаться на отдельные атомы или атомные слои, перпендикулярные оси деформации. Реально механическое разрушение происходит гораздо спокойнее: тело распадается на небольшое количество частей при напряжении, в большинстве случаев много меньшем теоретической прочности. Это происходит потому, что в наиболее слабых местах тела возникают микротрещины. Если действие внешних сил прекращается, то трещины под действием молекулярных сил смыкаются и тело восстанавливает первоначальную форму, подвергаясь лишь упругой деформации. Если же действие внеших сил продолжается и оно велико, то микротрещины перерастают в макротрещины, которые растут по всему сечению в одном (при резании) или нескольких направлениях (при раздавливании) и если напряжения в разрушаемом теле превысят предел прочности материала то наступает деформация разрушения и тело разваливается.
По теории измельчения, предложенной академиком АН СССР П.А.Ребиндером, работа, затрачиваемая на измельчение, в общем случае является суммой двух энергий: энергии, расходуемой на образование новых поверхностей раздела и энергии деформации данного объема тела.
По "поверхностной" части теории, работа, затрачиваемая на измельчение тела, прямо пропорциональна вновь образующимся поверхностям.
Предположим, что для разделения кубика (см. рисунок 25) с ребром а по одной плоскости требуется работа А. Тогда для дробления его по всем трем плоскостям потребуется работа, равная 3А, но при этом получится 23
= 8 кубиков.
Аналогично, если мы разделим кубик на еще более мелкие части со сторонами в 1/3, 1/4, 1/5, ..., 1/n, ..., 1/m, то получим 23
, 33
, 43
, 53
, ..., n3
...,m3
кубиков, а плоскостей раздела будет 6, 9, 12, ..., 3(n-1), ..., 3(m-1). Работа, затрачиваемая на измельчение составит 6А, 9А, 12А, ..., 3А(n-1), ..., 3A(m-1). Рис.25. Схема измельчения кубика материала.
Таким образом, для дробления материала в форме куба на кубики со стороной 1/n требуется работа Аn
= 3А(n-1), а для разделения на кубики со стороной 1/m - работа Am
= 3A(m-1).
Отношение этих работ
An
3A(n-1) (n-1)
─── = ─────── = ───── , при достаточно больших
Am
3A(m-1) (m-1)
величинах n и m единицей можно пренебречь и тогда
An
n
─── = ─── = i
Am
m
Таким образом, при больших степенях измельчения работа дробления прямо пропорциональна степени измельчения. Иначе - чтобы размолоть тело на мелкие частицы, требуется затратить большое количество энергии, возрастающее в обратной пропорциональной зависимости, как это показано на рисунке 26.
|
Рис.26. Зависимость работы измельчения от степени измельчения.
|
|
Из этого же соотношения можно сделать еще одно важное заключение - увеличение времени размола (измельчения) для данной конструкции устройства не позволяет измельчить материал менее определенного предела.
А это означает одно - определенный выбор типа измельчающего устройства в зависимости от технологических задач.
Для иллюстрации можно привести такие данные. Дробилки, независимо от типа, позволяют получить частицы размером не менее 500 мкм, шаровые мельницы - не менее 5 мкм, центробежные мельницы - не менее 0,5 мкм, аттриторы - 0,5 мкм, мельницы-ступки - не менее 0,1 мкм. Это ограничивает технолога, выбирающего оборудование.
По "объемной" части теории, работа, затрачиваемая на измельчение тела, прямо пропорциональна пределу прочности при сжатии размалываемых частиц. Когда напряжение достигает предела прочности при сжатии, материал разрушается.
Если принять допущение, что разрушаемый материал подчиняется закону Гука, то есть линейному закону деформации
Pl
l = ──── , где
FE
l - деформация материала;
P - сжимающая сила;
L - длина куска;
F - площадь его поперечного сечения;
E
- модуль упругости материала.
Отсюда следует вывод, что энергия, требуемая для измельчения материала, то есть для изменения его формы и размеров, изменяется пропорционально объемам или весам этих тел.
Практика показала, что "объемная" часть теории оправдывается при грубом помоле тел, а "поверхностная" - при тонком.
Весьма важным в практике дробления является принцип не дробить ничего лишнего, так как пребывание в машине уже измельченного материала приводит только к излишнему расхо-ду мощности на дробление.
Замешенная смесь без предварительной подготовки может прессоваться на гидравлических прессах. Для прессования на прессах-автоматах приготовленная смесь обладает недостаточной текучестью, насыпной плотностью, а мелкие частицы (1 - 3 мкм), соизмеримые с величиной зазоров между пуансонами и матрицей в прессформе, способны заклинить пуансон в матрице и вызвать его поломку, попадая в этот зазор. Смесь, составленная из компонентов с различной плотностью или размерами частиц способна расслаиваться при транспортировке и хранении.
Для того, чтобы избежать заклинивания пуансонов, расслоения смеси и повысить технологические смвойства шихты. её гранулируют.
Гранулированием называют переработку первичных частиц порошка во вторичные зерна — гранулы. Гранулам стараются придать шарообразную форму. Отдельные частицы порошка связывают вместе с помощью пластификатора.
Из многочисленных известных способов гранулирования в порошковой металлургии применяют, в частности, используя надлежащие присадки-пластификаторы, механическое и термическое гранулирование и комбинацию этих способов. Очень тонкие порошки (в основном с частицами <5 мкм) можно гранулировать, применяя сушку распылением. При гранулировании с присадками их часто добавляют в составе раствора, равномерно распределяющегося по поверхности частиц порошка.
При механическом гранулировании порошок уплотняют в виде заготовки-шашки, которую затем измельчают, протирая через сито. Давление прессования выбирают таким, чтобы не затруднялось измельчение, а полученные гранулы обладали хорошей текучестью.
В порошковой металлургии особое применение нашло термическое гранулирование. Порошок или смесь порошков в свободно насыпанном виде или после предварительного прессования подвергают первичному спеканию. Правильный выбор температуры такого спекания обеспечивает получение агломерата, подвергаемого затем измельчению. Гранулы состоят из спекшихся частиц исходного порошка; агломерат просеивают до желательного гранулометрического состава, обеспечивая хорошую текучесть. В пластичных металлах (меди, серебре) вследствие высоких местных уплотнений возможны газовые включения, обусловливающие при спекании гранулята вспучивание, трещины или нежелательные изменения формы заготовки. У материалов такого рода плотность гранулята не должна превышать плотности прессованной заготовки.
Способы гранулирования можно комбинировать. При механическом гранулировании можно применять присадки, а перед термическим — прессовать порошок. Термическое гранулирование применяют также, если при получении или подготовке порошков используют восстановительный или неполный отжиг. Такое гранулирование проводят при температурах начала спекания частиц порошка. Следующие за этим грубое и тонкое измельчения агломерата проводят так, чтобы при просеивании получить продукт с хорошей текучестью.
Все шире применяют новый метод гранулирования — сушку распылением (например, при получении твердых сплавов). Порошок в виде пульпы распыляют через форсунки или разбрызгиванием с поверхности быстровращающегося диска. Капли, падая в сушильной камере, принимают шаровую форму и высушиваются .Распыленный материал сушат вводимым в камеру горячим потоком азота или аргона и собирают в виде гранул в нижней части скруббера. Сушку распылением часто проводят в замкнутом цикле: горячий газ охлаждают, удаляя из него испарением жидкость, очищенный газ через нагреватель возвращают снова в скруббер.
Из механических способов гранулирования наиболее распространены: гранулирование окаткой во вращающемся барабане-смесителе или на поддоне с возвратно-поступательными движениями (качаниями).
Гранулирование во вращающемся смесителе. Замешенную смесь помещают в смеситель (конусный или сигарообразный) и обрабатывают в нем в течение некоторого времени. При вращении смесь скатывается в гранулы шарообразной формы диаметром 0,5— 3 мм.
Гранулы рассевают по фракциям на вибрационном сите с набором различных сеток. Для прессования отбирают фракцию, состоящую из гранул размером от 0,1 до 0,5 мм.
Более крупную фракцию гранул протирают через сито и добавляют к последующей партии смеси, поступающей на грануляцию. Более мелкие гранулы, представляющие собой очень твердые комочки смеси, выводят из процесса в отходы.
Недостатки указанного способа грануляции: значительное количество отходов, большая твердость гранул, для прессования которых требуются большие давления, привели к замене его другими методами.
Последовательный рассев замешенной смеси на вибрационном сите через сетки с различной частотой отверстий. В этом случае смесь под действием вибрации скатывается в комочки различной величины, которые обладают достаточно хорошей текучестью для заполнения гнезда прессформы.
Комочки смеси очень мягкие и хорошо уплотняются при прессовании, в связи с чем брак по "непропрессовке", а также крупные поры в изделиях, спрессованных из таких гранул, почти исключаются.
Указанный способ гранулирования не сопровождается образованием отходов в связи с тем, что та часть смеси, которая не используется как гранулы, присоединяется к следующей партии, поступающей на грануляцию.
Данный способ грануляции имеет разновидности, при которых замешенную смесь перед гранулированием либо увлажняют бензином, либо предварительно брикетируют, а затем снова растирают. Брикетирование способствует некоторому упрочнению гранул, но не столь большому, чтобы вызвать «непропрессовку».
Все известные способы гранулирования позволяют получать гранулы, обеспечивающие изготовление качественных изделий при условии прессования на прессах-автоматах.
ЛАБОРАТОРНАЯ РАБОТА №9 .
2.1. Зависимость степени измельчения от времени помола
2.1.1. АППАРАТУРА И МАТЕРИАЛЫ
1. Активатор (барабанная мельница)
2. Весы аналитические
3. Виброгрохот
4. Часы
5. Сито для отделения размольных тел
6. Измельчаемый материал * ................. 1 кг
* Руководитель работ может выбрать различные материалы для измельчения: товарная смесь твердых сплавов ВК или ТК, оксидную керамику для магнитов, периклаз и т.д.
|
|
Рис.27. Лабораторная шаровая мельни-
ца-активатор тип Т-445. 1 – привод, 2 –
барабан, 3 – размольные тела.
2.1.2. ПОРЯДОК ВЫПОЛНЕНИЯ РАБОТЫ.
Партию порошка массой 800 - 1000 грамм рассеивают на виброгрохоте, отделяя фракцию 50 мкм. Отсеянную фракцию в дальнейшей работе не используют.
Оставшийся порошок взвешивают на весах и загружают в барабан активатора Т445, который в данном случае работает как шаровая мельница, загружают туда же размольные тела до уровня 1/3 по объему. Барабан закрывают, устанавливают на привод, включают его и производят размол в течение двадцати минут.
Открывают барабан мельницы и выгружают порошок и размольные тела в крупное сито для отделения размольных тел.
Отсеивают фракцию 50 мкм и взвешивают отсеянный порошок, определяя Р.
Затем отсеянную фракцию, весь оставшийся порошок и размольные тела вновь загружают в барабан и процесс размол - отсев - взвешивание повторяют 5 раз.
2.1.3. ТРЕБОВАНИЯ К ОТЧЕТУ
По окончании работы оформляют протокол измерений и определяют зависимость выхода мелкой фракции от времени помола
Рi
Di = ──
Тi
Отчет должен содержать краткое описание физических основ процесса помола в шаровой мельнице, рисунок (схему) активатора Т445 с обозначением его основных узлов, порядок выполнения работы, протокол измерений с результатами расчетов и график полученной зависимости.
Объем отчета 3-4 страницы.
Отчет подписывается студентом.
2.1.4. ЛИТЕРАТУРА.
Кипарисов С.С., Либенсон Г.А. Порошковая металлургия., М., Металлургия, 1980г., с. 22-32.
2.1.5. КОНТРОЛЬНЫЕ ВОПРОСЫ.
1. Каковы преимущества и недостатки дробления материалов в барабанных шаровых мельницах ?
2. От чего зависит производительность размола в шаровой мельнице ?
3. Какие наименьшие частицы могут быть получены этим способом ?
4. Что такое критическая скорость вращения барабана шаровой мельницы ?
2.1.6. ПРОТОКОЛ ИЗМЕРЕНИЙ.
Таблица измерений
№№
|
Время размола, мин
|
Масса порошка фракции 50 мкм, г
|
Отношение выхода от времени размола, г,мин
|
График зависимости выхода мелкой фракции от времени размола.
Рис.28. Примерный вид графика к
отчёту в лабораторной работе №9
ЛАБОРАТОРНАЯ РАБОТА №10.
2.2. Изучение грануляции шихты окаткой.
Перед началом работы просеивают шихту через сито 060 и затем производят её грануляцию.
Грануляцию производят способом окатки на плоском поддоне из нержавеющей стали.
Принцип грануляции окаткой заключается в том, что частицы шихты заставляют перекатываться по поверхности плоского листа из нержавеющей стали. При этом частицы, как снежинки в снежном коме, слипаются друг с другом и перекатываются, образуя шарик из шихты. Размеры этого шарика зависят от амплитуды колебаний, времени грануляции, влажности шихты, типа пластификатора и других условий проведения процесса.
Увеличение амплитуды колебаний, их частоты и удлинение времени грануляции вызывают увеличение размеров гранул, которые иногда называют окатышами.
К увеличению размеров гранул приводит и увлажнение шихты.
В условиях производства грануляцию методом окатки чаще производят во вращающихся барабанах вроде тех, которые применяются в шаровых мельницах, но без загрузки шарами, либо в специальных наклонных барабанах, в которые шихта подается с одной стороны, а гранулят высыпается с другой. Встречаются и грануляторы с наклонным столом, по которому частицы порошка катятся вниз, комкуясь, окатываясь и образуя гранулы.
Для окатки порцию шихты масой около 1000 г насыпают в поддон, берут его двумя руками и энергично качают в горизонтальной плоскости с амплитудой качаний 200-250 мм и частотой 2-3 колебания в секунду в течение 15-20 сек. После этого шихту просеивают на ситах, отделяя частицы фракций -150+100, -200+150, -250+200, -300+250. Грануляцию и отсев шихты производят столько, чтобы набрать по 120-150 г шихты каждой фракции.
После получения трех-четырех фракций производят определение текучести гранулята.
Установка для определения текучести гранулята, аналогичная той, что применена для определения текучести порошков показана на рисунке Рис.29. Порядок определения текучести.
1 - штатив, 2 - воронка, 3 - приёмный стакан.
А – установка воронки и засыпка порошка в воронку, Б – истечение порошка.
|
|
А Б
Устройство работает следующим образом.
Пальцем закрывают отверстие D = 2,5 мм воронки 2, заполняют ее сухим гранулятом в количестве 50 г, а затем открывают отверстие, одновременно включают секундомер и дают порошку истечь в емкость 3. Как только последние частицы порошка выпадут из отверстия, секундомер выключают. Испытания проводят пять раз и берут среднее арифметическое.
Затем испытания повторяют для каждой фракции.
2.2.1. ТРЕБОВАНИЯ К ОТЧЕТУ
Отчет должен содержать краткое описание физических и технологических характеристик порошковых материалов, порядок выполнения работы, график зависимости текучести от фракционного состава и протокол испытаний.
Объем отчета 2-4 стр.
Отчет подписывается студентом.
2.2.2. ЛИТЕРАТУРА.
Кипарисов С.С., Либенсон Г.А. Порошковая металлургия. Учебник. М., Металлургия, 1980, с 202-203.
Порошки металлические. Метод определения текучести. ГОСТ 20899-75
2.2.3. КОНТРОЛЬНЫЕ ВОПРОСЫ.
1. Какие свойства порошков определяет текучесть ?
2. Какие свойства спеченных изделий определяет текучесть ?
2.2.4. ПРОТОКОЛ ИЗМЕРЕНИЙ
Таблица измерений имеет вид, показанный на рисунке
№ измерения
|
Фракция, мкм
|
Время истечения, сек
|
Среднее значение текучести, сек
|
Рис. 30. График зависимости теку-
чести от времени грануляции в от-
чёте к лабораторной работе №10
ТЕМА №3. ИЗУЧЕНИЕ ПРОЦЕССА ПРЕССОВАНИЯ
При прессовании заготовок из порошков формируется основа будущей структуры спечённого материала и от качества прессования во многом зависит работоспособность будущего изделия.
Прессование в закрытой прессформе происходит в четыре стадии: на первой после свободной засыпки порошка в прессформу, когда верхний (прессующий) пуансон входит в контакт к поверхностным слоем порошка, происходит простое перемещение порошка под воздействием пуансона и при этом частицы порошка, перемещаясь, движутся одна относительно другой сравнительно свободно, занимают новые места за счёт вытеснения воздуха из зазоров между частицами.
Во второй стадии, когда воздух из зазоров между частицами почти весь удалён и частицы заняли уже фиксированные положения, происходит дальнейшее перераспределение частиц за счет вытеснения пластификатора (он вытесняется в переферийные слои прессовки) и, частично, за счёт перемещения частиц относительно друг друга.
На третьей стадии происходит уплотнение порошкового тела за счёт смятия выступающих частей частиц, их взаимного стеснённого поворота и начала упругой деформации частиц - на этой стадии возрастает усилие прессования и возникает трение уплотнённого порошкового тела о боковые стороны прессформы.
На четвёртой стадии частицы деформируются и упруго и пластично, форма их искажается, зазоры между частицами почти исчезают, возникают силы упругого последействия и сила трения о стенки прессформы достигает 20-30% от усилия прессования.
Рис.31. Схема одностороннего прессования. А - шихта свободно засыпана в прессформу, Б - свободное перемещение частиц, вытеснение воздуха; В - упругая деформация частиц, которые заняли окончательное положение; Г - пластическая деформация частиц и окончательное формирование порошкового тела; Д - упругое расширение прессовки после извлечения её из прессформы.
|
|
На четвёртой стадии прессования обычно процесс останавливают и некоторое время выдерживают порошковое тело под нагрузкой - при этом перераспределяются напряжения, возникшие в прессовке и происходит некоторое уменьшение напряжений в ней. Релаксация напряжений сопровождается громкими щелчками, частота и громкость которых постепенно снижается.
После завершения релаксации - это время составляет от нескольких секунд до нескольких минут и зависит от природы и свойств прессуемого порошка, типа пластификатора, температуры прессования, размеров заготовки и ряда других факторов, производят расспрессовку заготовки, то есть её извлечение из прессформы, в которой прессовка "сидит" довольно прочно, поскольку силы бокового давления на стенки прессформы могут иметь значительную величину, составляющую по наблюдениям до 30-ти процентов от усилия прессования.
При извлечении прессовки из прессформы может наблюдаться так называемая "перепрессовка" - явление разрыва заготовки на части под воздействием сил упругого последействия, возникающего в прессовке вследствие упругой деформации частиц порошка.
Рис.32. Прессовка, разорванная упругими силами после извлечения её из прессформы. Видно, что разрывающие усилия направлены под углом 45-60О
к оси заготовки в направлении тангенциальных напряжений.
|
|
|
При прессовании стараются достичь максимального уплотнения порошкового тела, чтобы обеспечить минимальные искажения формы изделия при спекании, минимальной пористости и максимальной прочности. Поэтому, зачастую, приходится прессовать на пределе сил прессования, после которого и наступает перепрессовка. Обычно при подборе усилия прессования, особенно если материал основы шихты жёсткий как, например, карбид вольфрама, карбид титана и другие подобные вещества, производят опытное прессование при нескольких усилиях прессования до появления перепрессовочных трещин, затем снижают усилие прессования на 20-30% и дальнейшее прессование всей партии изделий производят при выбранном таким образом усилии.
При прессовании вначале уплотняются верхние слои порошковой массы, а лишь затем усилие передаётся слоям более удалённым от прессующей поверхности пуансона. Трение между частицами порошка постепенно гасит усилие, передаваемое от частицы к частице и величина усилия прессования постепенно снижается. Часть усилия прессования гасится трением порошкового тела о стенки матрицы. Поэтому длинная прессовка уплотняется неравномерно: слои, прилегающие к прессующему пуансону уплотняются до максимальной степени уплотнения, а по мере удаления от прессующего пуансона уплотнение материала снижается. В целом картина уплотнения порошкового тела выглядит так, как это показано на рисунке 23. Заметное уменьшение усилия прессования наблюдается, если отношение так называемого характеристического размера поперечного сечения заготовки к её высоте становится больше 2-х.
Характеристические размеры сечений заготовок простейших форм показаны на рисунке 33.
Рис.33. Распределение напряжений в заготовке при одностороннем прессовании (А) и
изменение плотности по высоте заготовки (Б). В - характеристические размеры заго-
товок для некоторых конфигураций. Следует обратить внимание, что для трубчатых
заготовок характеристический размер В - это наименьшая толщина стенки.
Чтобы избежать большой неравномерности плотности заготовки по высоте при соотношении характеристических размеров от 2-х до 4-х применяют двухстороннее прессование, при котором прессуют заготовку вначале движением верхнего пуансона, а затем - движением нижнего пуансона (или наоборот). При этом усилие прессования нижним пуансоном подбирают таким, чтобы плотность прессовки в нижней части равнялась плотности прессовки в верхней её части. Обычно усилие второго прессования составляет 80-90% от усилия прессования верхним пуансоном.
Схема двухстороннего прессования и картина распределения напряжений и плотности в заготовке при двухстороннем прессовании показана на рисунке 34. Рис.34. Схема двухстороннего прессования. А - шихта свободно засыпана в прессформу; Б - прессование верхним пуансоном с одной стороны; В - прессование нижним пуансоном с другой стороны; Г - распределение напряжений в прессовке.
1 - матрица; 2 - нижний пуансон; 3 - верхний пуансон.
|
|
Если требуется прессовать изделия с соотношением характеристических размеров более 4-х, то прибегают либо к способам экструдирования заготовок через фильеры (в открытую матрицу), либо прессуют заготовку большой длины из нескольких заготовок меньшего размера, по способу прессования из составных заготовок, как это показано на рисунке 35.
А Б В Г Д
Фиг. 35. Схема прессования удлинённых изделий из нескольких промежуточных прессо- вок. А - засыпка шихты в промежуточную прессформу для укороченных заготовок, Б - одностороннее прессование укороченных заготовок; В - загрузка нескольких укороченных заготовок в конечную прессформу ( в примере на схеме показана загрузка 3-х заготовок); Г - двухстороннее прессование составной заготовки; Д - составная заготовка.
1 - воронка для засыпки шихты; 2 - матрица; 3 - нижний пуансон; 4 - засыпанная шихта; 5 - верхний пуансон; 6 - промежуточная укороченная заготовка; 7 - матрица для окончательного прессования длинной заготовки; 8 - окончательно отпрессованная удлинённая заготовка.
В любом случае и при одностороннем, и при двухсторннем прессовании, и при экструдировании, и при прокатке порошковой заготовки, и при других любых способах получения порошковых заготовок прессованием наблюдается упругое последействие - увеличение размеров прессовки после прекращения действия внешнего давления вызванное действием растягивающих упругих сил, возникших в прессовке. Величина упругого последействия невелика и измеряется десятыми долями миллиметра, но его последствия могут быть разрушительными. Если возникшие в прессовке при упругом последействии растягивающие усилия превысят силу сцепления частиц, то есть если эти силы превысят силы склеивания (адгезии) частиц пластификатором, то заготовка будет разорвана. Опасно то, что разрушение заготовки может произойти не сразу после извлечения прессовки из прессформы, а позже - иногда через несколько часов, а иногда - только в момент спекания.
Чтобы избежать опасных последствий упругого последействия или "перепрессовки", обычно проводят технологические испытания шихты, определяя её формуемость и прессуемость.
Прессуемость
— способность порошка образовывать брикет заданной формы и минимально допустимой плотности под воздействием данного давления.
Прессуемость порошка определяется двумя технологическими характеристиками: уплотняемостью и формуемостью.
Уплотняемость
— зависимость плотности брикета от величины давления прессования. Характеристикой уплотняемости является диаграмма прессования, построенная в координатах "плотность — давление прессования".
Формуемость
— способность порошка сохранять заданную форму при определенном значении плотности.
Формуемость порошка характеризуется интервалом плотности, ограниченным значениями минимальной и максимальной плотности, при которых брикет не имеет разрушений после извлечения из пресс-формы.
Определение этих параметров позволяет избежать "перепрессовки" и назначить оптимальное усилие прессования, при котором получается максимально плотная заготовка без опасной величины упругого последействия.
ЛАБОРАТОРНАЯ РАБОТА № 11.
3.1. Зависимость плотности прессовки от давления прессования.
3.1.1. АППАРАТУРА И МАТЕРИАЛЫ
1. Пресс гидравлический ручной……………….
2. Прессформа образцовая
3. Весы лабораторные с разновесами …………..
4. Микрометр 0-25
5. Шихта гранулированная ...........……………..... 1 кг
Рис.36. Пресс гидравлический ручной П6316А.
1 - клапан для регулирования давления в гидросистеме,
2 - манометр, 3 - шток пресса, 4- пульт управления, 5 -
стол, 6 - станина, 7 - подставка.
3.1.2. ПОРЯДОК ВЫПОЛНЕНИЯ РАБОТЫ
Прессование заготовок (брикетов, образцов, прессовок) производится на гидравлическом прессе с переменным усилием прессования, которое устанавливается с помощью предохранительного клапана и контролируется манометром.
Схема пресса для прессования образцов показана на рисунке 37.
Усилие прессования регулируется предохранительным (регулировочным, перепускным) клапаном 9, присоединенным к нагнетательному трубопроводу 7. При достижении в системе давления, установленного заранее и контролируемого манометром 10, пружина клапана сжимается и излишек жидкости переливается в сливной патрубок 8, присоединенный к расширительному баку пресса. Таким образом в гидравлической системе пресса поддерживается постоянное давление.
Для проведения работы заранее подготавливается гранулированная шихта с одним содержанием пластификатора (желательно - 2%). Перед началом работы подготавливают пять навесок из подготовленной шихты массой 50 г.
Рис.37. Схема гидравлического пресса. 1 - станина пресса, 2 - шток поршня гидравлического пресса, 3 - верхний пуансон прессформы, 4 - матрица, 5 – нижний пуансон прессформы, 6 - полость прессования с засыпанной шихтой, 7 - нагнетательный трубопровод, 8 - сливной трубопровод, 9 - клапан для регулирования давления нагнетания, 10 - контрольный манометр.
Рис.38. Прессформа для проведения лабораторных работ. 1 – нажимная пята, 2 - дистанционное кольцо, 3 – матрица, 4 – верхний пуансон, 5 – спрессованное порошковое тело, 6 – нижний пуансон, 7 – опорная пята, 8 – распрессовочное кольцо.
|
|
Из них прессуют образцы, каждый раз меняя давление прессования. Рекомендуемые значения давления по манометру - 40, 60, 80 и 100 ати.
Затем оценивают плотность полученных прессовок путем сравнения их высоты. В основе такого способа оценки плотности лежит следующее утверждение. Поскольку плотность прессовок равна площади поперечного сечения прессовки на её высоту, а масса прессовок одинакова, то при изменении плотности будет меняться только высота прессовки, поскольку площадь поперечного сечения, определяемая сечением окна в матрице практически, если не учитывать упругого последействия, постоянна. Такое допущение значительно упрощает измерения, поскольку достаточно измерить только высоту прессовки.
3.1.3. ЛИТЕРАТУРА.
Кипарисов С.С., Либенсон Г.А. Порошковая металлургия. Учебник. М., Металлургия, 1980, с 215-246.
3.1.4. КОНТРОЛЬНЫЕ ВОПРОСЫ.
1. Какие свойства прессовки определяет уплотнение при прессовании ?
2. Как изменяются размеры прессовки при различном давлении прессования ?
3.1.5. ПРОТОКОЛ ИЗМЕРЕНИЙ
Таблица измерений имеет вид, показанный на рисунке
№№
|
Величина навески, г
|
Масса прессовки, г
|
Давление прессования, кгс/см2
|
Высота прессовки,
мм
|
Приведённая высота прессовки, мм/г
|
Рис.39. График зависимости приведённой высоты прессовки в зависимости от усилия прессования выглядит примерно как показано на рисунке.
|
|
ЛАБОРАТОРНАЯ РАБОТА N°12.
3.2. Распределение плотности прессовки по высоте прессовки при одностороннем прессовании.
3.2.1. АППАРАТУРА И МАТЕРИАЛЫ
1. Пресс гидравлический ..................……………………………………………….....
2. Прессформа образцовая с верхним дистанционным кольцом
3. Набор промежуточных колец
4. Микрометр 0-25
5. Шихта гранулированная ..............……………………………………………….... 1 кг
3.2.2. ПОРЯДОК ВЫПОЛНЕНИЯ РАБОТЫ
Прессование заготовок производится на гидравлическом прессе. Давление прессования устанавливают равным 100 ати и оно выдерживается неизменным в ходе всего опыта. Усилие прессования определяется верхним дистанционным кольцом и оно также неизменно. Перед началом работы подготавливают пять навесок из подготовленной шихты массой 10 +
0,01 г.
Схема прессования образцов с дистанционным кольцом и промежуточными кольцами показана на рисунке 41.
Образцовую прессформу устанавливают на плиту пресса и засыпают первую навеску массой 10 г. Затем разравнивают и слегка утрамбовывают поверхность шихты в прессформе и на нее укладывают промежуточное кольцо (прокладку). Затем засыпают вторую навеску в 10 г, выравнивают и уплотняют ее поверхность, на которую затем вновь укладывают следующее промежуточное кольцо. Так поступают, засыпая последовательно все пять навесок, одну за другой.
Прессование производят под упор верхнего кольца. Схема такого прессования показана на рисунке 40
Рис.40. Схема гидравлического пресса. 1 - станина, 2 - шток поршня гидравлического пресса, 3 - верхний пуансон прессформы, 4 - матрица, 5 – нижний пуансон прессформы, 6 - полость прессования с засыпанной шихтой, 7 - нагнетательный трубопровод, 8 - сливной трубопровод, 9 - клапан для регулирования давления нагнетания, 10 - контрольный манометр.
Рис.41. Схема прессформы, снаряжённой для лабораторной работы. 1 – нажимная пята, 2 – дистанционное кольцо, 3 – верхний пуансон, 4 – матрица, 5 – шихта, 6 – промежуточное кольцо, 7 – нижний пуансон, 8 – нижняя пята, 9 – распрессовочное кольцо.
|
|
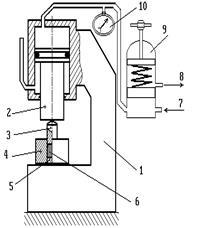
После распрессовки образец осторожно разбирают на составляющие его кольца и определяют плотность каждого из колец гидростатическим методом.
Для определения плотности собирают приспособление, показанное на рисунке 42.
Рис.42. Схема определения плотности гидростатическим взвешиванием. 1 - электронные весы, 2 - подставка для стакана, 3 - взвешиваемый образец, 4 - химический стакан, 5 - кронштейн для подвески образца, 7 - нить с крючком, 8 - термометр.
|
|
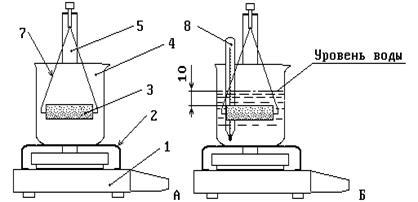
Взвешивание осуществляют следующим образом. На платформу электронных весов 1 устанавливают кронштейн для подвески образца 5. Сверху кронштейна, между его стойками помещают подставку для стакана 2 так, чтобы она не соприкасалась с платформой весов и кронштейном. На подставку 2 устанавливают стакан 4, также устанавливая его без соприкосновения с кронштейном. На кронштейн укладывают нить с крючком 6 для подвески образца.
Включают весы и сбрасывают их показания в нуль.
Затем образец закрепляют с помощью нити с крючком 6 на кронштейне 5 и производят взвешивание образца. Этим определяют вес образца в воздухе М1
.
Затем в стакан наливают кипяченую (обезгаженную) холодную воду и измеряют ее температуру термометром 7. После измерения температуры измеряют вес образца в воде М2
.
По формуле
M1
´rm
r = ───── , где
M1
– M2
М1
- масса образца в воздухе, г
М2
- масса образца в воде, г
rm
-плотность воды при данной температуре, г/см3
Плотность воды при температуре измерения определяют по таблице.
Таблица 3
Зависимость плотности воды от температуры
Температура,
О
С
|
Плотность,
г/см3
|
|
Температура,
О
С
|
Плотность,
г/см3
|
15
|
0,9981
|
23
|
0,9965
|
16
|
0,9979
|
24
|
0,9963
|
17
|
0,9977
|
25
|
0,9960
|
18
|
0,9976
|
26
|
0,9958
|
19
|
0,9974
|
27
|
0,9955
|
20
|
0,9972
|
28
|
0,9952
|
21
|
0,9970
|
29
|
0,9949
|
22
|
0,9967
|
30
|
0,9946
|
Расчет плотности проводят с точностью до 2-го знака. За показатель плотности принимают значение рассчитанной плотности, округленное до 0,1 г/см3
.
Результаты испытаний заносят в протокол. По результатам определения плотности строят картину распределения плотности по высоте прессовки.
3.2.3. ТРЕБОВАНИЯ К ОТЧЕТУ
Отчет должен содержать краткое описание физических основ прессования, описание установок и методики определения плотности прессовки, порядок выполнения работы и таблицу наблюдений.
Объем отчета 2-4 стр.
Отчет подписывается студентом.
3.2.4. ЛИТЕРАТУРА.
Кипарисов С.С., Либенсон Г.А. Порошковая металлургия. Учебник. М., Металлургия, 1980, с 215-246.
Сплавы твердые спеченные. Метод определения плотности. ГОСТ 20018.
3.2.5. КОНТРОЛЬНЫЕ ВОПРОСЫ.
1. Какие свойства прессовки определяет уплотнение при прессовании ?
2. Как изменяются размеры прессовки при различном давлении прессования ?
3.2.6. ПРОТОКОЛ ИЗМЕРЕНИЙ
Таблица измерений
№№
|
№ кольца
|
М1
, г
|
М2
, г
|
Т, О
С
|
Плотность воды, г/см3
|
Плотность образца, г/см3
|
Рис. 43. Примерный вид гистограммы распределения плотности по высоте пресовки
ЛАБОРАТОРНАЯ РАБОТА N°13.
3.3. Распределение плотности прессовки при двухстороннем прессовании
3.3.1. АППАРАТУРА И МАТЕРИАЛЫ
1. Пресс гидравлический ................…………………………………………………......
2. Прессформа образцовая с верхним и нижним дистанционными кольцами
3. Набор промежуточных колец
4. Микрометр 0-25
5. Шихта гранулированная .............……………………………………………………... 1 кг
3.3.2. ПОРЯДОК ВЫПОЛНЕНИЯ РАБОТЫ
Прессование заготовок производится на гидравлическом прессе. Давление прессования устанавливают равным 100 ати и оно выдерживается неизменным в ходе всего опыта. Усилие прессования определяется верхним и нижним дистанционным кольцом и оно также неизменно. Перед началом работы подготавливают пять навесок из подготовленной шихты массой 10 +
0,01 г.
Схема прессования образцов с дистанционным кольцом и промежуточными кольцами показана на рисунке 44 Образцовую прессформу устанавливают на плиту пресса и засыпают первую навеску массой 10 г. Затем разравнивают и слегка утрамбовывают поверхность шихты в прессформе и на нее укладывают промежуточное кольцо (прокладку). Затем засыпают вторую навеску в 10 г, выравнивают и уплотняют ее поверхность, на которую затем вновь укладывают следующее промежуточное кольцо. Так поступают, засыпая последовательно все пять навесок, одну за другой. Прессование производят под упор верхнего кольца.
Рис.44. Схема двухстороннего прессования. А – первое прессование, кольцо 8 установлено, Б – второе прессование, кольцо 8 удалено. 1 – пята, 2 – верхнее дистанционное кольцо, 3 – верхний пуансон, 4 – матрица, 5 – слой шихты, 6 – промежуточное кольцо-перегородка, 7 – нижний пуансон, 8 – нижнее дистанционное кольцо, 9 – пята, 10 – распрессовочное кольцо.
|
|
Затем удаляют верхнее дистанционное кольцо и производят повторное прессование с одним нижним дистанционным кольцом.
После распрессовки образец осторожно разбирают на составляющие его кольца и определяют плотность каждого из колец гидростатическим методом.
Для определения плотности собирают приспособление, показанное на рисунке 5.
Взвешивание осуществляют следующим образом. На платформу электронных весов 1 устанавливают кронштейн для подвески образца 5. Сверху кронштейна, между его стойками помещают подставку для стакана 2 так, чтобы она не соприкасалась с платформой весов и кронштейном. На подставку 2 устанавливают стакан 4, также устанавливаяя его без соприкосновения с кронштейном. На кронштейн укладывают нить с крючком 6 для подвески образца.
Рис.45. Схема гидростатического взвешивания. А – взвешивание на воздухе, Б – взвешивание образца в воде. 1 - электронные весы, 2 - подставка для стакана, 3 - взвешиваемый образец, 4 - химический стакан, 5 - кронштейн для подвески образца, 7 - нить с крючком, 8 - термометр.
|
|
Включают весы и сбрасывают их показания в нуль.
Затем образец закрепляют с помощью нити с крючком 6 на кронштейне 5 и производят взвешивание образца. Этим определяют вес образца в воздухе М1
.
Затем в стакан наливают кипяченую (обезгаженную) холодную воду и измеряют ее температуру термометром 7. После измерения температуры измеряют вес образца в воде М2
.
По формуле
M1
´rm
r = ───── , где
M1
– M2
М1
- масса образца в воздухе, г
М2
- масса образца в воде, г
rm
-плотность воды при данной температуре, г/см3
Плотность воды при температуре измерения определяют по таблице.
Расчет плотности проводят с точностью до 2-го знака. За показатель плотности принимают значение рассчитанной плотности, округленное до 0,1 г/см3
.
Результаты испытаний заносят в протокол. По результатам определения плотности строят картину распределения плотности по высоте прессовки.
Таблица 4
Зависимость плотности воды от температуры
Температура,
О
С
|
Плотность,
г/см3
|
|
Температура,
О
С
|
Плотность,
г/см3
|
15
|
0,9981
|
23
|
0,9965
|
16
|
0,9979
|
24
|
0,9963
|
17
|
0,9977
|
25
|
0,9960
|
18
|
0,9976
|
26
|
0,9958
|
19
|
0,9974
|
27
|
0,9955
|
20
|
0,9972
|
28
|
0,9952
|
21
|
0,9970
|
29
|
0,9949
|
22
|
0,9967
|
30
|
0,9946
|
3.3.3. ТРЕБОВАНИЯ К ОТЧЕТУ
Отчет должен содержать краткое описание физических основ прессования, описание установок и методики определения плотности прессовки, порядок выполнения работы и таблицу наблюдений.
Объем отчета 2-4 стр.
Отчет подписывается студентом.
3.3.4. ЛИТЕРАТУРА.
Кипарисов С.С., Либенсон Г.А. Порошковая металлургия. Учебник. М., Металлургия, 1980, с 215-246.
Сплавы твердые спеченные. Метод определения плотности. ГОСТ 20018.
3.3.5. КОНТРОЛЬНЫЕ ВОПРОСЫ.
1. Какие свойства прессовки определяет уплотнение при прессовании ?
2. Как изменяются размеры прессовки при различном давлении прессования ?
3.3.6. ПРОТОКОЛ ИЗМЕРЕНИЙ
Таблица измерений
№№
|
№ кольца
|
М1
, г
|
М2
, г
|
Т, О
С
|
Плотность воды, г/см3
|
Плотность образца, г/см3
|
Рис.46. Примерный вид гистограммы распределения плотности по высоте прессовки
ЛАБОРАТОРНАЯ РАБОТА № 14.
3.4. Определение упругого расширения.
3.4.1. АППАРАТУРА И МАТЕРИАЛЫ
1. Пресс гидравлический .............…………………………………………………….........
2. Прессформа образцовая
3. Микрометр .................……………………………………………………………............ 0-25 мм
4. Шихта гранулированная .....………………………………………………………........... 1 кг
3.4.2. ПОРЯДОК ВЫПОЛНЕНИЯ РАБОТЫ
Прессование заготовок (брикетов, образцов, прессовок) производится на гидравлическом прессе с переменным усилием прессования, которое устанавливается с помощью предохранительного клапана и контролируется манометром.
Схема пресса прессования образцов показана на рисунке 47.
Усилие прессования регулируется предохранительным (регулировочным, перепускным) клапаном 9, присоединенным к нагнетательному трубопроводу 7. При достижении в системе давления, установленного заранее и контролируемого манометром 10, пружина клапана сжимается и излишек жидкости переливается в сливной патрубок 8, присоединенный к расширительному баку пресса. Таким образом в гидравлической системе пресса поддерживается постоянное давление, определяемое силой предварительно.
Рис.47. Схема гидравлического пресса. 1 - станина пресса, 2 - шток поршня гидравлического пресса, 3 - верхний пуансон прессформы, 4 - матрица, 5 – нижний пуансон прессформы, 6 - полость прессования с засыпанной шихтой, 7 - нагнетательный трубопровод, 8 - сливной трубопровод, 9 - клапан для регулирования давления нагнетания, 10 - контрольный манометр.
Рис.48. Прессформа для проведения лабораторных работ. 1 – нажимная пята, 2 -
|
|
дистанционное кольцо, 3 – матрица, 4 – верхний пуансон, 5 – спрессованное порошковое тело, 6 – нижний пуансон, 7 – опорная пята, 8 – распрессовочное кольцо.
Для проведения работы заранее подготавливается гранулированная шихта с одним содержанием пластификатора (желательно - 2%). Перед началом работы подготавливают пять навесок из подготовленной шихты массой 50 г.
Из них прессуют образцы, каждый раз меняя давление прессования. Прессование производят при усилии 3 +
0,1 и 4 +
0,1 тонны.
Для этого образцовую прессформу устанавливают на плиту реверсора и засыпают первую навеску. Включают насос пресса и производят прессование.
Затем производят распрессовку.
Для этого устанавливают на плиту реверсора распрессовочное кольцо, устанавливают фиксирующую стрелку на индикаторе в нулевое положение и производят прессование в том же направлении, какое было при основном прессовании.
Аналогично прессуют образцы при усилии пресса равном 4 тонны.
Всего изготавливают по три образца.
По окончании распрессовки измеряют диаметр прессовок и сравнивают его с диаметром полости прессформы, считая ее абсолютно жесткой.
Рассчитывают величину упругого расширения по формуле:
D1
– D2
d = ------- ´ 100% , где
D1
D1
- диаметр полости прессформы, мм
D2
- диаметр брикета после расспрессовки, мм
Результаты испытаний и среднее арифметическое показаний заносят в протокол.
3.4.3. ТРЕБОВАНИЯ К ОТЧЕТУ
Отчет должен содержать краткое описание физических основ прессования, описание гидравлического пресса и прессформы, порядок выполнения работы и таблицу наблюдений.
Объем отчета 2-4 стр.
Отчет подписывается студентом.
3.4.4. ЛИТЕРАТУРА.
Кипарисов С.С., Либенсон Г.А. Порошковая металлургия. Учебник. М., Металлургия, 1980, с 232-239.
3.4.5. КОНТРОЛЬНЫЕ ВОПРОСЫ.
1. Чем объясняется увеличение размеров прессовки после извлечения ее из прессформы ?
2. Как снизить величину упругого расширения?
3.. Какие виды брака вызывает наличие упругого расширения?
3.4.6. ПРОТОКОЛ ИЗМЕРЕНИЙ
Таблица измерений имеет вид, показанный на рисунке 49
№№
|
Усилие прессования, тс
|
D1
, мм
|
D2
, мм
|
D1
– D2
, мм
|
d, %
|
ЛАБОРАТОРНАЯ РАБОТА № 15.
3.5. Определение формуемости порошка.
|
Для определения формуемости применяется специальная прессформа по ГОСТ 10937, общий вид которой показан на черт.50.
Рис.50. Прессформа для прессования образцов при определении формуемости по ГОСТ 10937. 1 - верхний пуансон, 2 - распрессовочная скоба, 3 - матрица, 4 - нижний пуансон, 56 - ручка, 6 - обойма, 7 - нижняя распрессовочная скоба.
|
|
Для испытания формуемости берут навеску порошка в количестве 20 г,
взвешенную с точностью до 0,02 г, засыпают в прессформу и тщательно разравнивают поверхность засыпки.
Формуемость порошка определяют на брикетах специальной формы, обеспечивающей линейное распределение плотности по длине брикета; форма и размеры брикета, получаемого в процессе прессования, указаны на черт. 3.
Прессование брикета ведется до упора без смазки рабочих поверхностей матрицы и пуансонов. По окончании прессования брикет извлекают из пресс-формы и по делениям, отпечатанным на его основании, определяют длину той части брикета, грани которой четко выражены и не имеют трещин при рассмотрении под лупой с увеличением 2х
.
Пользуясь диаграммой для определения формуемости порошка, изображенной на черт. 51, определяют величину минимальной и максимальной плотности, при которых грани брикета не имеют сколов, трещин и следов осыпания.
Испытание формуемости повторяют три раза. Значения минимальной и максимальной плотности вычисляют как среднее арифметическое результатов трех определений.
3.5.1. АППАРАТУРА И МАТЕРИАЛЫ 1. Гидравлический пресс с усилием 4тс ………….
2. Прессформа по ГОСТ 10937
3. Лупа 2х
4. Линейка 100 мм
5. Товарная смесь
Рис.51. Номограмма для определения формуемости и эскиз отпрессованного образца.
3.5.2. ТРЕБОВАНИЯ К ОТЧЕТУ
Отчет должен содержать краткое описание физических основ прессования, описание гидравлического пресса и прессформы, порядок выполнения работы и протокол измерений. наблюдений.
Объем отчета 2-4 стр.
Отчет подписывается студентом.
3.5.3. ЛИТЕРАТУРА.
Кипарисов С.С., Либенсон Г.А. Порошковая металлургия. Учебник. М., Металлургия, 1980, с 232-239.
3.5.4. КОНТРОЛЬНЫЕ ВОПРОСЫ.
1. Для чего определяют формуемость порошка ?
2. Как увеличить формуемость порошка ?
3.5.5. ПРОТОКОЛ ИЗМЕРЕНИЙ
Протокол измерений должен содержать значения минимальной и максимальной плотности, а также среднее арифметическое трёх измерений.
Таблица измерений имеет вид, показанный на рисунке 52
№ измерения
|
Усилие прессования, тс
|
Минимальная плотность, г/см3
|
Максимальная плотность, г/см3
|
Среднее значение плотности, г/см3
|
ЛАБОРАТОРНАЯ РАБОТА № 16.
3.6. Изучение зависимости формуемости шихты от размера частиц.
Формуемость и прессуемость шихты зависят от многих факторов и в частности зависят от размера частиц шихты. Эта зависимость нелинейна и существует для каждой конкретной шихты максимум формуемости, задача определить который и является задачей цехового технолога.
Общая же тенденция такова: плохо прессуются и формуются как шихта из мелкого, менее 2-3 мкм, порошка, так и шихта, составленная из частиц более 10 мкм.
Комбинируя размер частиц, можно достичь желаемой прессуемости и формуемости, то есть, составляя смесь из частиц различного размера, можно существенно улучшить эти важные технологические показатели.
Для определения формуемости применяется специальная прессформа по ГОСТ 10937, общий вид которой показан на черт.53.
|
Рис.53. Прессформа для прессования образцов при определении формуемости по ГОСТ 10937. 1 - верхний пуансон, 2 - распрессовочная скоба, 3 - матрица, 4 - нижний пуансон, 5 - ручка, 6 - обойма, 7 - нижняя распрессовочная скоба.
Для испытания формуемости берут навеску порошка в количестве 20 г
,
взвешенную с точностью до 0,02 г, засыпают в прессформу и тщательно разравнивают поверхность засыпки.
Формуемость порошка определяют на брикетах специальной формы, обеспечивающей линейное распределение плотности по длине брикета; форма и размеры брикета, получаемого в процессе прессования, указаны на эскизе рисунка 51.
|
|
Прессование брикетов из различных товарных смесей ведется до упора без смазки рабочих поверхностей матрицы и пуансонов. По окончании прессования брикет извлекают из пресс-формы и по делениям, отпечатанным на его основании, определяют длину той части брикета, грани которой четко выражены и не имеют трещин при рассмотрении под лупой с увеличением 2х
.
Пользуясь диаграммой для определения формуемости порошка, изображенной на черт. 51, определяют величину минимальной и максимальной плотности, при которых грани брикета не имеют сколов, трещин и следов осыпания.
Испытание формуемости повторяют три раза для шихт с различной величиной частиц. Значения минимальной и максимальной плотности вычисляют как среднее арифметическое результатов трех определений.
3.6.1. АППАРАТУРА И МАТЕРИАЛЫ
1. Гидравлический пресс с усилием 4тс ……………………………………..…………
2. Прессформа по ГОСТ 10937
3. Лупа 2х
4. Линейка 100 мм
5. Шихта из порошков с различным размером частиц (рекомендуются: 1 мкм, 3 мкм и 8 мкм)
3.6.2. ТРЕБОВАНИЯ К ОТЧЕТУ
Отчет должен содержать краткое описание физических основ прессования, описание гидравлического пресса и прессформы, порядок выполнения работы и протокол измерений. наблюдений.
Объем отчета 2-4 стр.
Отчет подписывается студентом.
3.6.3. ЛИТЕРАТУРА.
Кипарисов С.С., Либенсон Г.А. Порошковая металлургия. Учебник. М., Металлургия, 1980, с 232-239.
3.6.3. КОНТРОЛЬНЫЕ ВОПРОСЫ.
1. Для чего определяют формуемость порошка ?
2. Как увеличить формуемость порошка ?
3.6.4. ПРОТОКОЛ ИЗМЕРЕНИЙ
Протокол измерений должен содержать значения минимальной и максимальной плотности, а также среднее арифметическое трёх измерений.
Таблица измерений имеет вид, показанный на рисунке 55.
№ измерения
|
Средний размер частиц, мкм
|
Усилие прессования, тс
|
Минимальная плотность, г/см3
|
Максимальная плотность, г/см3
|
Среднее значение плотности, г/см3
|
Рис. 55. Таблица измерений к лабораторной работе № 16
ЛАБОРАТОРНАЯ РАБОТА №17.
3.7. Изучение зависимости формуемости от физико-механических свойств материала основы шихты (медь, никель, твёрдый сплав).
Формуемость и прессумость порошков зависят от пластичности и упругих свойств частиц порошка. Например, порошок меди прессуется в плотный брикет даже без применения пластификатора при умеренных усилиях прессования, а порошок вольфрама, обладающий большой жёсткостью, может быть спрессован в брикет только в присутствии пластификатора и при значительном усилии прессования. Следует учесть, что даже пластичные порошки могут иметь низкую формуемость, если поверхность частиц порошка покрыта жёстким окислом - таким свойством обладает порошок титана и алюминия.
Для определения формуемости применяется специальная прессформа по ГОСТ 10937, общий вид которой показан на черт. 56.
Для испытания формуемости берут навеску порошка в количестве 20 г
,
взвешенную с точностью до 0,02 г, засыпают в прессформу и тщательно разравнивают поверхность засыпки.
Формуемость порошка определяют на брикетах специальной формы, обеспечивающей линейное распределение плотности по длине брикета; форма и размеры брикета, получаемого в процессе прессования, указаны на черт. 57.
Испытание формуемости повторяют три раза. Значения минимальной и максимальной плотности вычисляют как среднее арифметическое результатов трех определений.
Прессование брикета ведется до упора без смазки рабочих поверхностей матрицы и пуансонов. По окончании прессования брикет извлекают из пресс-формы и по делениям, отпечатанным на его основании, определяют длину той части брикета, грани которой четко выражены и не имеют трещин при рассмотрении под лупой с увеличением 2х
.
3.7.1. АППАРАТУРА И МАТЕРИАЛЫ
1. Гидравлический пресс с усилием 4тс …………………………………………….
2. Прессформа по ГОСТ 10937
3. Лупа 2х
4. Линейка 100 мм
5. Пресспорошок из различных материалов (рекомендуются: медь, никель, ВК8ВК)
3.7.2. ТРЕБОВАНИЯ К ОТЧЕТУ
Отчет должен содержать краткое описание физических основ прессования, описание гидравлического пресса и прессформы, порядок выполнения работы и протокол измерений. наблюдений.
Объем отчета 2-4 стр.
Отчет подписывается студентом.
3.7.3. ЛИТЕРАТУРА.
Кипарисов С.С., Либенсон Г.А. Порошковая металлургия. Учебник. М., Металлургия, 1980, с 232-239.
3.7.4. КОНТРОЛЬНЫЕ ВОПРОСЫ.
1. Для чего определяют формуемость порошка ?
2. Как увеличить формуемость порошка ?
3.7.5. ПРОТОКОЛ ИЗМЕРЕНИЙ
Протокол измерений должен содержать значения минимальной и максимальной плотности, а также среднее арифметическое трёх измерений.
Таблица измерений имеет вид, показанный на рисунке 58.
№ измерения
|
Материал порошка
|
Усилие прессования, тс
|
Минимальная плотность, г/см3
|
Максимальная плотность, г/см3
|
Среднее значение плотности, г/см3
|
Рис.58. Таблица измерений к лабораторной работе №17
ЛАБОРАТОРНАЯ РАБОТА № 18
3.8.
Изучение конструкции прессформ различных конструкций, применяемых в производстве изделий из порошков.
В настоящее время в производстве твердых сплавов применяется большое количество разнообразных способов формования, где требуется получение сложных и особо сложных единичных деталей или мелких серий. Наиболее широкое распространение получил традиционный метод прессования смесей под давлением 0,5—1,5 т/см2
в металлических пресс-формах — так называемый метод прямого прессования.
Метод прямого прессования.
Для прессования твердосплавных смесей применяются различные пресс-формы (от простых цельных до сложных сборных), состоящие из нескольких частей, соединенных болтами, клиньями. Для конструирования пресс-форм необходимо определить соотношение между насыпанным порошком в пресс-форме и объемом спрессованного брикета:
Vнас
= ; Vgh
= ;
где Vнас
— объем свободно насыпанного порошка в пресс-форме, см3
; Vпр
— объем спрессованного тела (брикета), см3
; G — навеска порошка, г; gнас
— насыпная масса порошка, г/см3
; gпр
— плотность брикета, г/см3
.
Степень сжатия порошка bсж
определяется по уравнению
bсж
= = ´ =
Так как плотность брикета определить практически трудно, то обычно пользуются следующей формулой:
bсж
=
Здесь gсп
— удельная масса спеченного сплава, г/см3
; K—коэффициент линейной усадки
при спекании.
Например, в случае смеси ВК8, для которой gсп
= 14,5 г/см3
, K =
1,22, gнас
= 3.2г/гм3
. находим
bсж
= 14,5 / 3,2´1,223
= 2,7.
Таким образом, при сжатии порошка в процессе прессования высота пресс-формы должна быть не менее чем в 2,7 раза больше высоты брикета.
При проектировании рабочих размеров прессформы следует учитывать коэффициент усадки, увеличивая рабочие размеры прессформы путём умножения размеров спечённой детали на этот коэффициент с учётом припуска на механическую обработку шлифование и заточку) спечённого изделия.
Прессформы делятся на две группы:
- для прессования на ручных прессах, то есть на прессах с ручным управлением, так называемые ручные прессформы;
- для прессования на прессах-автоматах - автоматные прессформы.
Наибольшим разнообразием конструкций отличаются ручные прессформы, которые по конструкции матрицы называют цельными либо разъёмными.
Простая по конструкции прессформа показана на рисунке 58
Прессование в данной прессформе ничем не отличается от прессования в предыдущей с той лишь разницей, что сборка прессформы производится на калиброванных штифтах - это упрощает изготовление, но ресурс этой прессформы меньше, чем у собираемой на призмах.
3.8.3. ЛИТЕРАТУРА.
1. Кипарисов С.С., Либенсон Г.А. Порошковая металлургия. Учебник. М., Металлургия, 1980, с 215-246.
3.8.4. КОНТРОЛЬНЫЕ ВОПРОСЫ.
1. Из каких материалов изготавливают прессформы?
2. Как определяют рабочие размеры формообразующих поверхностей прессформы?
3. Как обеспечивается кинематическая точность перемещения рабочих элементов автоматных и ручных прессформ?
ТЕМА №4. ИЗУЧЕНИЕ ЯВЛЕНИЙ ПРИ СПЕКАНИИ
Спрессованные полуфабрикаты (заготовки, прессовки, брикеты) в подавляющем большинстве случаев обладают недостаточной прочностью для применения их в качестве готовых изделий. Необходимая прочность, твердость и другие служебные свойства изделий, например - пористость, магнитные свойства, корозионностойкость и тому подобное, достигаются в результате спекания, как правило осуществляемого путем термической обработки (но не обязательно).
Спекание - одна из основных технологических операций в производстве изделий из порошков, в процессе которой происходит превращение брикета в прочное спеченное тело со свойствами, приближающимися к свойствам компактного материала. При этом происходит уплотнение свободно насыпанной или спрессованной массы порошка, а также ряд в основном физических процессов, обеспечивающих большее или меньшее заполнение пор.
Роль спекания в изготовлении конечного продукта различна. При производстве высокопористых изделий - фильтров, или в случае невысоких требований к механическим свойствам материала, спекание является конечной операцией. В некоторых случаях для повышения плотности, прочности и пластичности изделий применяют допрессовку и вторичное спекание.
Единого взгляда на процессы, происходящие при спекании пока не существует и теоретического обоснования многих физико-химичеких процессов, проходящих при спекании нет. На практике многие параметры процесса спекания, такие как температура, длительность выдержки, скорость подъема температуры, атмосфера печи и тому подобное - определяются опытным путем без должного теоретического объяснения и обоснования.
Поэтому на долю заводского технолога ложится огромная ответственность при определении условий проведения операции спекания и отслеживании возможных колебаний и допусков на параметры процесса.
Именно поэтому на предприятиях выработана практика предварительного изготовления опытных деталей и образцов-свидетелей, которые изготавливаются в небольших количествах (обычно не более 10-ти) перед изготовлением основной партии изделий в данной серии из конкретной партии подготовленной шихты.
В соответствии с современными представлениями о спекании различают несколько основных видов спекания, каждый из которых отличается состоянием вещества, участвующего в процессе:
- твердофазное спекание, при котором все участвующие в спекании вещества, составляющие шихту находятся в твердом состоянии, то есть в твердой фазе;
- спекание с переносом атомов через газовую фазу;
- жидкофазное спекание, при котором хотя бы один из компенентов смеси находится в расплавленном, жидком состоянии.
В свою очередь жидкофазное спекание подразделяется на несколько видов:
- спекание с образованием жидкой фазы, присутствующей до конца изотермической выдержки при нагреве.
- спекание с образованием жидкой фазы, исчезающей в процессе нагрева.
- спекание, при котором жидкая фаза образуется как результат твердофазного взаимодествия компонентов с образованием эвтектики, остающейся в жидком состоянии до конца выдержки.
Основным процессом при любом из видов спекания является переход от порошкового тела, обладающего избыточной свободной энергией (на поверхности частиц) к более стабильному спеченному телу большей плотности. Движущей силой самопроизвольно протекающего процесса спекания является разность свободных энергий исходного (порошкового) и конечного (плотного) состояний.
Конкретные пути снижения этой разности состоят в значительном уменьшении внешних (поверхность заготовки, открытые поры) и внутренних поверхностей (внутренние поры, границы зерен), а также существенное устранение дефектов структуры (вакансий и дислокаций - вследствие объемной и поверхностной диффузии) и неравновесных состояний.
В спекаемой массе перемещается большой объем материи, в зависимости от характера и состояния системы в таком перемещении используются (самопроизвольно) различные механизмы перемещения (миграции).
Образование и рост контактов.
Процесс спекания в однокомпонентных системах рассматривают как состоящий из двух последовательных этапов: образование и рост контактов между частицами на начальной, ранней стадии процесса и повышение плотности спекаемого тела вследствие уменьшения числа и объема пор напоздней стадии процесса. В макроусловиях, то есть во всем объеме спекаемого тела, эти оба условия не имеют четкой временной границы, поскольку протекают практически одновременно.
В идеализированном виде спекание происходит следующим образом, как это показано на рисунке 62. Две соприкасающиеся частицы (см. рис. 62-а) постепенно сближаются, граница между ними исчезает (рис.62-б), а массы объединяются в общее тело (рис.62-д). Это происходит под действием капиллярных сил Лапласа путем уменьшения их суммарной поверхности на промежуточных стадиях спекания (рис 62 б-д). Объясняется это явление тем, что атомы частиц, находящиеся в зоне контакта обладают меньшей энергией и подвижностью, поскольку часть поверхностной энергии задействована на преодоление контактных сил, а атомы на поверхности частиц вне зоны контакта - более "энергичны" и подвижны. Поэтому они стремятся тоже отдать часть своей энергии путем перехода в зону контакта. Зона контакта расширяется. Следующий этап связывания энергии - это исчезновение общей границы между частицами и переход атомов во внутренние объемы частиц (рис.62-б). Образуется новое тело из двух частиц, имеющее "шейку". На вогнутой поверхности шейки с отрицательной кривизной действуют растягивающие силы, в то время как на сферических выпуклых поверхностях объединенной частицы действуют сжимающие силы (рис.62-в). Под действием этих сил центры частиц сближаются и образуется новая частица. Сближение центров частиц обуславливает уменьшение объема вновь образовавшейся частицы, то есть - усадку тела в целом.
Рис.62. Различные стадии спекания двух сферических частиц.
Если считать, что две частицы имеют одинаковую массу, то при радиусе частиц R1
, объем занимаемый обеими частицами будет
2 V1
= pR1
3
;
а масса:
2 M1
= 2 pR1
3
g;
Новая частица имеет массу 2М1
, отсюда ее радиус R2
.
2М1
= pR2
3
g = 2 pR1
3
g; R2
= R1
Ö2 = 1,44 R1
Две частицы имеют характеристический размер равный 2R1
, а новая частица - 1,44R1
. Отсюда максимальная усадка при спекании составляет
» 1,39
Практика спекания показывает, что максимально достижимая усадка составляет 1,25-1,3, что составляет примерно 93% от теоретической усадки.
Спекание - сложный процесс, во время которого происходит удаление адсорбированных паров и газов, восстановление и диссоциация окисных пленок, диффузионное перемещение атомов, исправление дефектов кристаллических решеток, рекристаллизация, перенос металлов через газовую фазу, образование новых фаз вследствие физико-химических процессов и др.
Дефектами кристаллической решетки называют всякое нарушение периодичности расположения ее структурных элементов.
Наиболее распространенные дефекты - это вакансии и дислокации.
Вакансии - это незанятые, то есть вакантные, узлы решетки. Узловая вакансия решетки образуется вследствие перемещения атома (иона) из нормального положения в междоузлия. При этом атом, освободивший узел решетки, становится межузельным атомом. Вакансии и межузельные атомы являются дефектами-антиподами: аннигиляция вакансии и межузельного атома восстанавливает правильность кристаллической решетки.
Вакансии различают двух типов: типа Френкеля и типа Шоттки.
Вакансия типа Френкеля рождается в паре с межузельным атомом, вакансию типа Шоттки образуют либо две вакансии противоположного знака, либо два межузельных иона противоположного знака (антипод дефекта Шоттки).
Вид вакансий схематически показан на рисунке 63.
Рис.63. Точечные дефекты в кристалле
а - дефект Френкеля, б - дефект Шоттки,
в - антипод дефекта Шоттки.
При образовании вакансий происходит перемещения атомов, окружающих дефект. Атомы вокруг вакансии сдвигаются к незанятому узлу решетки, в то время как межузельный атом "расталкивает" окружающие атомы.
Объединение вакансий может дать трехмерное образование в виде поры или каверны, либо в виде плоского "блина" атомной толщины. И в том и в другом случае возникновение вакансионных дефектов существенно снижает прочность спеченного тела.
Дислокации - это специфические линейные дефекты, нарушающие правильное чередование атомных плоскостей в кристалле. В отличие от вакансий, дислокации искажают всю структуру кристалла.
Кристалл с правильной решеткой можно изобразить в виде семейства параллельных атомных плоскостей, как это показано на рисунке 64-а.
Если одна из плоскостей обрывается внутри кристалла (Рис.64-б), то ее край образует линейный дефект, называемый краевой дислокацией.
Такого вида дислокации образуются при захлопывании "блина" вакансий или внедрения слоя межузельных атомов.
Другой простейший вид дислокации - это винтовая дислокация. В этом случае ни одна из атомных плоскостей не оканчивается внутри кристалла, но сами плоскости лишь приблизительно параллельны и смыкаются друг с другом так, что образуется одна слабоизогнутая атомная плоскость в виде винтовой плоскости с шагом, равным межплоскостному расстоянию, как это показано на рисунке 64-в. Ось винтовой линии образует линию дислокации.
Рис.64. Схема расположения атомных плоскостей в идеальном крис-
талле (а), в кристалле с краевой (б) и винтовой (в) дислокациями.
Вакансии и дислокации играют важную роль в спекании.
Выше было сказано, что объединение вакансий приводит к образованию пустот, вокруг которых концентрация вакансий велика. Возникший градиент вакансий приводит к оттоку вакансий от поверхности поры и притоку межузловых атомов. Таким образом на поверхности поры происходит аннигиляция вакансия-атом и пора "зарастает" атомами. В случае припекания частицы к частице в месте наибольшей кривизны контакта концентрация вакансий также возрастает и вогнутые области действуют как источники, а сжатые области - выпуклые поверхности, границы зерен - в результате недостатка вакансий действуют как стоки. Эквивалентные потоку вакансий, но направленные в противоположную сторону потоки межузловых атомов усиливают контактирование частиц посредством объемной или поверхностой диффузии.
Переносу вещества в контактную зону способствуют и дислокации, так как они действуют в качестве стоков вакансий.
В подавляющем большинстве случаев плотность спекаемых тел возрастает, причем пористость уменьшается вследствие зарастания пор.
Различают три стадии уплотнения (усадки):
- ранняя стадия. Плотность прессовки мала и уплотнение определяется процессами в приконтактных областях - движением вакансий, межузловых атомов и состоянием структуры и геометрии приконтактных областей; для ранней стадии спекания характерна высокая скорость деформации частиц и повышение прочности заготовок.
- промежуточная стадия. Плотность прессовки возрастает и уменьшение объема каждой из пор происходит независимо, а пористое тело ведет себя как очень вязкая среда. Происходит уплотнение тела по всему объему.
- поздняя стадия. Тело сформировано. Прессовка содержит отдельные изолированные поры, которые залечиваются в результате дифузионного "растворения" в матрице. На этой стадии возможен процесс объединения пор (коалесценция пор), когда их суммарная поверхность уменьшается при их неизменном суммарном объеме, то есть, поры укрупняются. Скорость усадки уменьшается.
Рекристаллизация при спекании
Также как и в литых металлах, при спекании наблюдается рост зерен в спекаемом теле.
Крупные зерна образуются в результате переноса вещества при общей границе от зерна малого размера на зерно большего размера. Перенос вещества происходит путем перемещения атомов через границу зерна в сторону зерна с меньшей величиной свободной энергии, то есть туда, где меньше суммарная поверхность границ. Разница свободной энергии кристаллов по обе стороны границы между ними определяет движение границы к центру ее кривизны.
С ростом межчастичных контактов вследствие роста, зерна получают возможность "прорастать" друг в друга. Этот процесс называют межчастичной рекристаллизацией. Межчастичная кристаллизация, теоретически, должна приводить к образованию из множества частиц, составляющих порошковое тело, одной - монокристалла, занимающего объем прессовки. Но на практике этого никогда не происходит, поскольку всегда сказывается тормозящее влияние загрязнений, примесей, пленок окислов и тому подобных включений.
При спекании наблюдается еще один вид рекристаллизации, вызываемый последствиями деформирования зерен перед спеканием в процессе подготовки шихты, размола и других процессов, связанных с искажением формы зерна.
Рекристаллизация в пористых телах имеет определенные температурные интервалы:
- поверхностная рекристаллизация - 0,3 - 0,4 ТПЛ
- объемная рекристаллизация - 0,4 - 0,45 ТПЛ
- собирательная межчастичная - 0,4 - 0,45 ТПЛ
и выше.
При температуре равной 0,75-0,85 ТПЛ
собирательная межчастичная рекристаллизация протекает интенсивно.
Рекристаллизация завершает перестройку структуры, подготовляемую прессованием, восстановлением окислов при спекании и усадкой.
Рекристаллизация является вредным явлением, поскольку при большом росте зерна изделие охрупчивается и теряет прочность. Поэтому процесс спекания ведет так, чтобы рекристаллизация была наименьшей, так как вообще избежать ее невозможно.
Перенос атомов через газовую фазу
Перенос атомов через газовую фазу в процессе спекания имеет существенное значение, особенно при спекании композиций, содержащих металлы с восстанавливающимися при этом окислами, например никелем и кобальтом.
Перенос вещества через газовую фазу связан с его испарением на нагретых поверхностях частиц и осаждением его на более холодных. Частицы с большей кривизной поверхности имеют большую упругость пара, поэтому с их поверхности вещество уносится, а оседает на частицах с меньшей кривизной поверхности, то есть большего размера. Особенно заметно идет оседание пара на поверхностях с отрицательной кривизной - на участках межчастичного контакта. Поэтому основной перенос вещества наблюдается в направлении межчастичного контакта: вначале образуется мостик, затем перемычка между частицами, которая затем "зарастает" атомами. После завершения зарастания процесс затормаживается и затухает.
Роль переконденсации возрастает с повышением температуры. Переконденсация играет основную роль как процесс, способствующий "залечиванию" дефектов, скруглению внутренних поверхностей пор и усиливает эффект припекания частиц - все это приводит к снижению концентрации напряжений в спеченном теле.
Активирование спекания с помощью жидких фаз
Для большинства случаев спекание происходит в присутствии жидкой фазы, образующейся в результате расплавления более легкоплавкого компонента или за счет образования эвтектики.
Различают несколько случаев спекания с помощью жидких фаз:
- спекание с образованием жидкой фазы, присутствующей до конца изотермической выдержки при нагреве.
- спекание с образованием жидкой фазы, исчезающей в процессе нагрева.
- спекание, при котором жидкая фаза образуется как результат твердофазного взаимодействия компонентов с образованием эвтектики, остающейся в жидком состоянии до конца выдержки.
Во всех этих случаях основной вклад в процесс объединения порошкового тела в твердое играет смачивание, мерой которого является величина краевого угла q, показанного на рисунке 65.
Рис.65. Схема смачивающей (а) и несмачивающей (б) жидкостей на твердой поверхности.
При полном смачивании угол смачивания равен нулю.
При полном несмачивании - 180°.
Чем лучше смачивание, тем эффективнее проходит процесс спекания, тем выше уплотнение при усадке, тем выше физико-механические свойства готового изделия.
Процесс уплотнения проходит по стадиям. На первой - образуется жидкая фаза, заполняющая поры с перегруппировкой твердых частиц, что приводит к плотной упаковке под действием сил поверхностного натяжения.
Этот процесс протекает очень быстро (секунды) и он в основном и определяет усадку. При содержании жидкой фазы 25-35 %об. может быть достигнута теоретическая плотность.
Вторая стадия - растворение мелких частиц в расплаве в местах взаимного контакта, а иногда - и во всем объеме.
На третьей стадии замедляется процесс проникновения жидкости в промежутки между частицами, и чем больше срастаются частицы, тем больше замедляется уплотнение.
Одновременно, вследствие взаимодействия жидкой фазы и поверхностных слоев частицы, образуется новая поверхность с иным, чем у исходного углом смачивания. Как правило угол смачивания возрастает. Поэтому смачивание ухудшается. То есть при увеличении выдержки при спекании с жидкой фазой наивысшие значения плотности и прочности материала получаются в первые секунды спекания. Как правило, выдержка свыше 20-30 минут ухудшает свойства изделия.
Это наблюдается еще и потому, что начинают развиваться процессы рекристаллизации через жидкую фазу, образование новых, как правило более хрупких, фаз.
Практика спекания
Сокращение времени достижения максимальной плотности и прочности и устранение неравномерности в объеме спеченного тела, уменьшение температуры спекания, выравнивание концентрации при спекании многокомпонентных систем достигаются грамотным использованием и пониманием процессов, протекающих в порошковом теле при спекании.
Практика спекания оопределила ряд приемов, позволяющих активировать спекание.
Активирование поверхностных процессов.
На стадии роста контактов, когда температура невысока, а поверхность пор еще велика, активирование процессов спекания достигают за счет применения предварительно окисленных порошков с целью осуществления затем циклов окисление-восстановление в процессе спекания. Поверхностная диффузия усиливается при восстановлении оксидов и образование контактов ускоряется.
Существует оптимальная толщина оксидной пленки, благоприятствующая спеканию, например: для меди 0,05 мкм, железа и никеля - 0,063 мкм.
Активирование миграции вещества
через газовую фазу важное также на стадии припекания частиц, достигается введением газовых присадок в атмосферу спекания и образующих с металлом газообразные соединения, распадающиеся затем на нагретых поверхностях.
Наиболее изучены присадки галогенов и их соединений, участвующих в пересносе вещества по уравнению
Ме + G = MeG = Me + G
На поверхности частиц образуются летучие вещества (левая часть уравнения), которые омывают более нагретые части частицы и разлагаются на них, осаждая порции металла (правая часть уравнения).
При благоприятных условиях протекание этого процесса способствует весьма эффективному залечиванию дефектов и упрочнению контактов.
Аналогично действуют присадки 0,01-0,1 %масс. никеля или палладия при спекании вольфрама и молибдена.
Активирование объемного течения
материала путем увеличения концентрации вакансий, плотности дислокаций, интенсификации диффузии и увеличения числа структурных границ.
Для этого применяют интенсивное энергонасыщенное измельчение материала на операции приготовления порошка или шихты в аттриторах и центробежных планетарных мельницах (механическое активирование) или высокоскоростное уплотнение при прессовании, или же получение электролитичекого порошка при высоких плотностях тока. Эффективным способом увеличения числа границ является плакирование частиц порошка металлом, растворимым в основном материале.
Присутствие вакансий и других дефектов быстро "залечивается" - менее чем за 0,01 с.
Отсюда вытекает важный практический вывод: чтобы эффективно использовать повышенную плотность дефектов для течения материала нужно как можно быстрее вести нагрев до температуры спекания. Ограничение существует только по скорости отгонки пластификатора, выделяющиеся пары которого могут разорвать заготовку. Чтобы избежать этого процесс спекания проводят в две стадии. На первой - отгоняют пластификатор при температуре ниже температуры диффузионно-вязкого течения материала, на второй - производят быстрый нагрев до температуры спекания.
Активирование с помощью жидких фаз
осуществляют самыми разнообразными способами, из которых можно отметить применение более легкоплавких металлов для связки, применение в качестве связок эвтектик, применение для связок аморфных металлов.
Применяется "эффект расплавления", который заключается в том, что в процессе нагрева в точках контактов вследствие диффузии одного из компонентов образуется эвтектика, которая расплавляется и впитывается в тугоплавкий компонент. Происходит усадка. При дальнейшем нагреве состав образовавшегося сплава вследствие продолжающейся диффузии изменяется и он затвердевает. При достижении конечной температуры снова образуется расплав с другой концентрацией компонентов и тело продолжает уплотнение.
В заключение краткого обзора современного состояния представлений о процессах происходящих при спекании, заметим, что, как это показывает практика, решающее слово в определении конкретных режимов спекания в условиях действующего производства остается за технологическим экпериментом, который проводит технолог в цехе, определяя действительные режимы спекания в каждом отдельном случае.
Спекание - важнейшая технологическая операция производства твердых сплавов. Оно состоит в нагреве прессовки до температуры 1350-1550°С, выдержке заготовки при этой температуре и охлаждения.
На этой операции формируются фазовый состав и микроструктура сплавов, достигаются трребуемые физико-механические и служебные свойства.
Спекание - многостадийный процесс, на начальных стадиях которого происходит подготовка материала заготовки к последующему, так называемому, окончательному спеканию.
Первым процессом, предшествующим спеканию, является процесс отгонки остатков растворителя и адсорбированной влаги, сохранившейся в прессовке и получивший название сушка заготовок, которая производится непосредственно после прессования.
Сушка, во-первых увеличивает прочность брикетов и этим облегчаются транспортные операции, а во-вторых при сушке удаляются следы растворителя и адсорбированной влаги, которая всегда присутствует в спрессованных заготовках.
Удалять остатки растворителя и влагу особенно важно для крупногабаритных, массой более 100 г изделий и для изделий с малыми размерами - менее 1-2 мм (речь идет о характеристических размерах).
Влага всегда присутствует в любом растворителе. Влага адсорбируется частицами порошка из воздуха.
Кроме того при сушке брикетов с пластификатором-каучуком, последний при сушке полимеризуется и прочность брикетов возрастает, что позволяет применить в дальнейшем механическую обработку пластифицированных заготовок.
В процессе сушки из прессовок (брикетов) удаляется растворитель пластификатора: бензин, если пластификатором является каучук и спирт - если пластификатор - полиэтиленгликоль (ПЭГ). Происходит и частичная полимеризация каучука и высыхание ПЭГ, что повышает прочность заготовок и позволяет упростить транспортные операции и производить механическую обработку заготовок.
В зависимости от вида пластификатора температура сушки должна быть:
120-180°С - для каучука;
140-150°С - для парафина;
110-120°С - для гликолей;
150-180°С - для d
-камфары;
Общий принцип выбора температуры сушки - она должна быть ниже на 20-30°С, чем температура плавления или разложения пластификатора, но, естественно выше температуры кипения растворителя.
Увеличение температуры сушки значительно ускоряет процесс сушки, но при нагреве до температуры свыше 200-300°С в капиллярах заготовки создаются большие давления вследствие испарения пластификатора, растворителя и влаги. Это давление может превысить прочность заготовки и заготовка разрушается, образуются отдельные трещины, расслоения и сеть мелких трещин.
При температуре нагрева выше 200°С начинается окисление заготовки и появляется сеть мелких трещин в разных направлениях, в конце концов заготовка может и разрушиться.
Для предотвращения многих нежелательных явлений следует применять способ сушки в с выдержкой заготовки в парах растворителя.
При таком способе выделяющиеся пары из сушильного шкафа отсасываются только избыточные пары и сушка изделия происходит более плавно. А это, в свою очередь, позволяет на 30-50°С повысить температуру сушки и интенсифицировать процесс.
При сушке в парах растворителя полностью блокируется окисление, так как в сушильном шкафу возникает атмосфера паров растворителя, препятствующих доступу кислорода к поверхности заготовки.
Обычно для создания соответствующей атмосферы достаточно того количества растворителя, который остался в брикете, однако при сушке особо ответственных и разнотолщинных деталей в сушильный шкаф можно установить небольшую емкость с растворителем. Например для шкафа СНВС 4.4.4/0,3И3 при сушке изделия 60´60´120 достаточно поместить емкость с 30-40 мл бензина.
Это особенно важно, если в качестве пластификатора применен парафин, поскольку в этом случае процесс сушки совмещают с выплавлением излишнего парафина из заготовки.
При сушке заготовок, пластифицированных парафином, часть пластификатора удаляется из заготовки в жидком состоянии, а часть - выгорает или испаряется. Удаление парафина требует особо тщательного соблюдения режима нагрева, без превышения предела в 120-140°С, чтобы избежать окисления и разрывов, поскольку пластифицированные парафином заготовки содержат его в большом количестве, до 10% масс.
Чтобы ускорить процесс удаления парафина заготовку помещают в пористую среду: засыпку из графита, древесного угля, шамота и т.п. "отсасывающих" адсорбентов, а заготовку устанавливают наклонно для ускорения вытекания расплавленного парафина.
Сушку в парах растворителя не следует затягивать, так как уже после 20-30 мин выдержки при номинальной температуре заготовки, как правило уже сухи.
Значения температур при сушке в парах растворителя:
180-210°С - для каучука (растворитель - бензин);
180-250°С - для парафина (без растворителя, в парах самого парафина);
140-160°С - для гликолей (растворитель - этанол);
200-250°С - для d
-камфары(растворитель - бензин);
160-180°С - для d
-камфоры(растворитель - ацетон).
Для устойчивого проведения процесса вакуумный сушильный шкаф СНВС модернизируется - вместо вакуумных насосов устанавливается маломощный центробежный насос (реверсированный ЦБ-вентилятор), а в камеру шкафа устанавливают ванну для растворителя объемом 1000-1500 мл.
Отсасываемые из камеры пары конденсируют в обратном холодильнике, из которого они вновь возвращаются в камеру печи. Необходимое избыточное давление паров растворителя, таким образом, поддерживается автоматически. Выделяющиеся другие газы в холодильнике не конденсируются и уходят в отсос.
Схема сушильного шкафа с выдержкой в парах растворителя показана на рисунке 66.
Рис.66.Схема модернизированного вакуум-
ного сушильного шкафа для сушки
в парах растворителя
1 - вакуумный сушильный шкаф, 2 - обратный холодильник,
3 - эжекционный насос, 4 - центробежный насос, 5 - отпрессо-
ванные заготовки, 6 - емкость с растворителем.
Устройство работает следующим образом. При включен-
ном нагреве из брикетов 5, размещенных в печи 1, и дополни-
тельной емкости с растворителем 6 выделяются пары растворителя, заполняющие внутренний объем.
Пары растворителя вытесняют воздух и поступают в обратный холодильник 2, охлаждаемый водой. В холодильнике 2 пары растворителя конденсируются и стекают обратно в камеру. Излишек паров отсасывается эжекционным насосом 3 и поступает в центробежный насос 4, а затем выбрасываются в атмосферу. Такая схема отсоса обеспечивает поддержание в камере печи небольшого (10-20 мм водяного столба) избыточного давления, тем не менее не препятствующего испарению растворителя и удалению его из массы прессовки.
Хорошо высушенная заготовка не имеет следов окислов, не крошится и имеет близкий к металлическому звук при легком ударе о железный предмет.
Второй стадией процесса спекания является процесс разложения (деструкции) пластификатора, который производится при температуре 600 - 1000°С.
Для улучшения прессуемости и для предотвращения рассыпания прессовки (брикета) в пресспорошки добавляют различные связующие вещества: пластификаторы и смазки, в результате чего уменьшается трение между частицами порошка и между прессовкой и стенками прессформы. До начала окончательного спекания смазку (пластификатор) необходимо удалить, чтобы не сдерживалось образование и рост межчастичных контактов.
Пластификаторы должны обладать следующими свойствами:
- хорошо смачивать зерна порошков смеси и образовывать пленки на поверхности частиц порошка;
- обладать высокой склеивающей способностью;
- иметь антифрикционные свойства;
- легко растворяться в органическом растворителе или иметь невысокую температуру плавления (50-60°С);
- удаляться без большого газообразования и следов примесей из спрессованной заготовки при нагревании до температуры 600-700°С;
- не вступать в химические реакции с компонентами смеси и с окружающей атмосферой;
- иметь низкую упругость паров (для пластификаторов, применяемых при вакуумном спекании);
- не оказывать токсического воздействия на окружающий персонал.
К настоящему времени сложился определенный список веществ, применяемых в качестве пластификаторов при производстве твердых сплавов, свойства некоторых из них приводятся в таблице.
Определим значимость отдельных свойств пластификаторов.
Пластификатор должен хорошо смачивать зерна порошков смеси и образовывать пленки на поверхности частиц порошка. Это свойство определяет равномерность смешивания порошка смеси с пластификатором, защиту частиц порошка от окисления, высокую текучесть порошка и снижение усилие прессования.
Высокая склеивающая способность определяет количество пластификатора, вводимого в смесь и плотность получаемой прессовки. Чем она выше, тем меньше пластификатора необходи
Таблица 5
Технологические свойства распространённых пластификаторов
Название
|
Температура, О
С
|
Технологическая характеристика
|
плавления
|
кипения
|
Стеарат цинка
|
140
|
>335
|
Нерастворим в спирте и бензине, растворим в четыреххлористом углероде, низкая склеивающая способность, отлично снижает трение, разлагаясь при отгонке загрязняет материал окисью цинка и образует поры, малотоксичен.
|
Кислота стеариновая
|
69,4
|
360
|
Применяют в расплавленном состоянии, высокая склеивающая способность при добавке 5-10% масс. хорошо снижает, трение, легко и полностью удаляется без разложения, малотоксична
|
Кислота олеиновая
|
13
|
206
|
Применяют в расплавленном состоянии, имеет температуру плавления ниже комнатной, поэтому требуется производить прессование в охлаждаемых матрицах, хорошо смачивает порошки, обладает невысокой склеивающей способностью, хорошо снижает трение, малотоксична, реагирует с железом и молибденом.
|
Парафин
|
40-60
|
320-390
|
Применяется в расплавленном состоянии, хорошо смачивает порошки, образует устойчивые пленки, обладает высокой склеивающей способностью при ведении в смесь 10-12% масс. и дает очень прочные прессовки, смеси дают большую усадку при выпаривании пластификатора, нетоксичен, химически инертен.
|
d-камфара
|
178
|
209
|
Растворима в воде и спирте и др. растворителях, обладает исключительной склеивающей способностью и дает прессовки большой прочности даже при содержании в смеси 0,2-0,3 % масс., при отгонке отгоняется полностью, обладает фармакологическим действием (успокаивающее), огнеопасна. Имеет высокую стоимость.
|
Каучук натрий-бутадиеновый
(СКБ)
|
Разлагается на неполные полимеры (олигомеры), начиная с 90О
С
|
Растворим в бензине и толуоле, обладает высокой склеивающей и пленкообразующей способностью и обеспечивает высокую прочность прессовок, при удалении оставляет 0,1-0,2% свободного углерода, нетоксичен.
|
Полиэтиленгликоль (ПЭГ)
|
Разлагается на воду и углекислый газ, начиная с 120О
С
|
Растворяется в воде, этиловом спирте, ацетоне и других органических растворителях, обеспечивает получение плотных и прочных прессовок, склонных к обкрашиванию острых кромок, удаляется из прессовки с разложением на воду и углекислый газ, инертен, нетоксичен, неогнеопасен.
|
Поливинилацетат (ПВА)
|
Разлагается на воду и углекислый газ, начиная с 120О
С
|
Растворим в воде и этаноле, обладает удовлетворительной склеиваемостью, прессовки достаточно прочны, но требуют осторожного обращения, зольность не обнаружена, нетоксичен.
|
мо вводить в смесь и тем выше плотность прессовки, тем меньше искажения формы, возникающие при сушке и спекании. Пластификатор считается хорошим по этому свойству, если достаточно ввести в смесь 0,2-1% по массе, пластификаторов среднего качества требуется вводить от 1 до 2 процентов, пластификаторы невысокого качества вводятся в количестве от 2-х до 10% масс. при прессовании в закрытых прессформах. Если применяют мундштучное (экструзионное) прессование, то хорошим считается пластификатор, которого достаточно ввести от 8 до 12-ти процентов.
Антифрикционные свойства пластификатора приводят к снижению трения между частицами порошка при прессовании и способствуют более высокому уплотнению прессовки, а понижение сил трения прессовки о стенки матрицы снижает усилия прессования, расспрессовки и увеличивает срок службы матрицы.
Равномерное и полное разложение или испарение пластификатора при нагреве способствует полному его удалению из прессовки при спекании и обеспечивает возникновение контактов между частицами при более низкой температуре и определяет отсутствие пористости в спеченной заготовке.
Типичный график разложения наиболее распространенных пластификаторов - ПЭГ-155 и СКБ показан на рисунке 67, из которого видно, что разложение ПЭГ-155 начинается при температуре около 120°С и медленно растет до температуры около 350°С, затем скорость разложения резко увеличивается и пластификатор полностью распадается при температуре около 600°С.
Рис.67. Термогравиметрические кривые
разложения: А- ПЭГ-115, Б- кау-
чук.
Аналогично, но в другом, более высоком интервале температур, протекает удаление каучука (СКБ). Однако полного удаления каучука не происходит, так как часть его разлагается с образованием свободного углерода, около 0,1-0,2% масс.
Рассматривая кривые разложения пластификаторов, можно сделать вывод, что в интервале температур, при котором происходит наиболее бурное разложение пластификатора, нагрев заготовок следует производить медленно и плавно, в то время как в интервале температур, при котором газовыделение незначительно, нагрев можно производить с высокой скоростью.
Задача цехового технолога и состоит в том, чтобы, проведя эксперимент в условиях цеха, определить скорости нагрева заготовок в различных интервалах температур, в зависимости от массы заготовок.
При изучении разложения пластификатора важно учесть и вид продуктов разложения пластификатора - это могут быть вода, метан, водород, окись углерода и двуокись углерода и другие соединения, обладающие химической активностью по отношению к твердосплавной смеси.
После отгонки пластификатора заготовка приобретает металлический блеск, прочность, хорошо обрабатывается на металлорежущих станках.
Процессы, происходящие при спекании твердых сплавов можно описать в следующем порядке:
1) При температуре 60-300°С испаряются остатки растворителя и адсорбированная влага. Нагрев изделий в этом интервале температур следует производить медленно во избежание разрушения сырой и еще не прочной заготовки парами отделяющихся соединений. Рекомендуется начальное отделение растворителя и влаги производить в отдельной печи - сушильном шкафу при температуре не более 180°С с выдержкой в парах растворителя и при небольшом разряжении порядка 15-20 мм вод. ст. Эта часть процесса изучена в работе N°4.
2) При температуре 500-700°С разлагается и удаляется пластификатор, частично удаляются адсорбированные газы, восстанавливаются окисные пленки на частицах кобальта, железа, никеля и вольфрама. В этом интервале температур также следует производить медленный нагрев, поскольку количество отделяющихся газов велико, например, при нагреве 1 кг заготовок, содержащих 2% пластификатора (каучука), то-есть около 20-ти грамм, выделится до 35-ти литров паров бензина.
3) В интервале температур 800-1000°С свариваются отдельные карбидные зерна в местах их соприкосновения, начинается упрочнение изделия.
4) При температуре 1150-1300°С наблюдается диффузионное растворение карбида вольфрама в кобальте, которое завершается в точке "а" на рисунке 67. образуются твердые растворы на основе кобальта с температурой плавления 1300-1500°С и появляется жидкая фаза. Количество жидкой фазы растет и приблизительно при 20% карбида вольфрама в растворе (точка "b") весь кобальт преходит в состав жидкой фазы. Этот процесс сопровождается активной усадкой - уменьшением линейных размеров спекаемого изделия и уплотнением материала.
Рис.67. Диаграмма системы WC-Co.
При достижении температуры плавления эвтектики, состоящей из кобальта с растворенным в нем карбидом вольфрама и углеродом, вступают в действие силы поверхностного натяжения. Происходит перемещение карбидных зерен - так называемое "жидкое" течение. Процесс происходит при 1300-1400°С и заканчивается почти полным уплотнением спекаемого изделия.
5) По мере повышения температуры до полной температуры спекания продолжается растворение зерен карбида вольфрама в кобальте, пока его содержание в жидкой фазе не достигнет около 38% - этот момент соответствует точке "с" не рисунке 67. В этот момент завершается процесс сварки карбидных зерен и растворение их в кобальте. Расплавленная смесь заполняет все промежутки и поры между карбидными зернами и достигается максимальная плотность изделия. В это же время из композиции полностью удаляются все растворенные газы.
Одновременно начинается и происходит вредное явление, сопровождающее спекание - перекристаллизация карбида вольфрама через жидкую фазу, при которой карбид вольфрама вначале растворяется в кобальте, а затем кристаллизуется в виде равноосных крупных кристаллов, обладающих пониженной прочностью.
6) После выдержки при максимальной температуре, во время которой завершаются процессы, определяющие формирование будущей структуры твердого сплава, сплав охлаждают. При охлаждении в интервале температур 1500-1300°С из жидкости на затравках - оставшихся зернах карбида вольфрама или специально введенного карбида тантала или карбида ниобия выпадает растворенный в жидкой фазе карбид вольфрама, что приводит к еще большему увеличению зерен карбида вольфрама. Это приводит с одной стороны к усилению контакта между зернами (это хорошо) и к увеличению размеров зерен - это плохо, так как снижается интегральная (общая) прочность материала, правда, возрастает сопротивление изнашиванию при трении (это иногда требуется).
Далее из расплава начинает выделяться растворенный в нем углерод, который выпадает в виде отдельных частиц графита, либо в виде скоплений таких частиц, снижая общую прочность и твердость материала.
Проведение процесса спекания требует тщательного соблюдения температур нагрева, темпа их достижения и соблюдения соответствующих выдержек. Только при этом можно получить твердые сплавы с заданными физико-механическими свойствами.
Температура окончательного спекания в вакууме зависит от состава и зернистости исходной смеси. Температуры спекания некоторых твердых сплавов даны в таблице 6.
Таблица 6
Температуры спекания некоторых твёрдых сплавов в зависимости от величина частиц шихты
Марка сплава
|
Зернистость
(сравнительная)
|
Средняя температура спекания, °С
|
ВК6
|
Мелкозернистый
Среднезернистый
Крупнозернистый
Особокрупнозернистый
|
1400
1430
1450
1480
|
ВК8
|
Мелкозернистый
Среднезернистый
Крупнозернистый
Особокрупнозернистый
|
1400
1450
1480
1500
|
ВК10
|
Мелкозернистый
Среднезернистый
Крупнозернистый
Особокрупнозернистый
|
1400
1420
1450
1450
|
Т15К6
|
1450
|
Т5К10
|
1480
|
КНТ16
|
1480
|
ТН20
|
1500
|
Т63НМВ
|
1450
|
Т78НЖД
|
1250
|
ЛАБОРАТОРНАЯ РАБОТА № 19
4.1.
Отгонка влаги и растворителя.
4.1.1. АППАРАТУРА И МАТЕРИАЛЫ
1. Печь лабораторная....……....
2. Весы электронные ..................………...
3. Чертилка
4. Прессовка, полученная при выполнении
Рис.68. Печь лабораторная. 1 -корпус, 2 - дверца со слоем теплоизоляции, 3 - "гляделка", 4 - камера печи, 5 - чашка с образцами, 6 - слой теплоизоляции, 7 - панель управления.
|
|
лабораторных работ по теме 3............... 5 шт. 4.1.2. ПОРЯДОК ВЫПОЛНЕНИЯ РАБОТЫ
В ходе работы используют заготовки, полученные при выполнении работ 1-3. Студент получает пять заготовок, оставленных от предыдущей лабораторной работы, маркирует их, нанося чертилкой номера на плоские поверхности заготовки, взвешивает и записывает их массу. Взвешивание производится на электронных весах с точностью +
0,01 г.
Затем заготовки помещают в сушильный шкаф, включают его в соответствии с технической инструкцией по эксплуатации и производят сушку изделия в парах растворителя в течение 2+
0,2 часов. затем сушильный шкаф отключают, заготовки охлаждают вместе со шкафом до комнатной температуры, заготовки извлекают и вновь взвешивают.
При обработке результатов измерений определяют величину потери массы заготовки при сушке, вычитая из массы исходной заготовки массу просушенной, и определяют относительное изменение массы в процентах как отношение полученной разности к массе исходной заготовки. затем по результатам расчетов определяют средний результат.
4.1.3. ТРЕБОВАНИЯ К ОТЧЕТУ
Отчет должен содержать краткое описание процесса сушки заготовок с описанием нежела-тельных явлений, которые следует избегать при выполнениии этого процесса, и перечень путей их предотвращения, описание установок, описание действий при выполнении работы и таблицу наблюдений.
Объем отчета 2-3 стр.
Отчет подписывается студентом.
4.1.4. ЛИТЕРАТУРА.
1. Кипарисов С.С., Либенсон Г.А. Порошковая металлургия. Учебник. М., Металлургия, 1980, с 215-246.
4.1.4. КОНТРОЛЬНЫЕ ВОПРОСЫ.
1. Для чего производится сушка спрессованных изделий ?
2. Какие опасные моменты возникают при сушке прессовок ?
3. Каким образом можно избежать растрескивания заготовок при сушке ?
4.1.5. ПРОТОКОЛ ИЗМЕРЕНИЙ
Таблица измерений имеет вид представленный на рисунке 69
№№
|
Масса образца
до сушки, г
|
Масса образца
после сушки, г
|
Величина
изменения массы, г
|
Относительное изме-
нение массы, %
|
Рис.69. Таблица наблюдений к работе № 19
ЛАБОРАТОРНАЯ РАБОТА № 20
4.2.
Наблюдение разложения пластификатора при предварительном спекании.
4.2.1. АППАРАТУРА И МАТЕРИАЛЫ
1. Печь вакуумная .........……….....
2. Весы электронные .......................
3. Прессовка, полученная при выполнении
лабораторной работы N°4 ................ 5 шт.
Рис.70. Общий вид вакуумной печи СНВС 1.3.1/16И3. 1- пульт управления, 2 - нагревательная камера, 3 - вакуумный диффузионный насос, 4 - вентили и трубопроводы, 5 - механические (форвакуумные) насосы.
|
|
4.2.2. ПОРЯДОК ВЫПОЛНЕНИЯ РАБОТЫ
В ходе работы используют заготовки, полученные при выполнении работы N°4. Студент получает пять заготовок, оставленных от предыдущей лабораторной работы, взвешивает и записывает их массу. Взвешивание производится на электронных весах с точностью +
0,01 г.
Затем заготовки помещают в вакуумную печь, включают ее в соответствии с технической инструкцией по эксплуатации и производят так называемое предварительное спекание, при котором отгоняется пластификатор и возникают первичные контакты между частичками. Затем печь отключают, заготовки охлаждают вместе с печью до комнатной температуры, заготовки извлекают и вновь взвешивают.
Вакуумная печь обеспечивает эффективное удаление пластификатора путем его испарения при температуре 300-350°С и разложение оставшейся части в интервале температур 700-1000°С. Одновременно при термообработке заготовок в печи происходит науглероживание материала углеродом, выделяющимся из разлагающегося пластификатора. Поэтому в печи поддерживается неглубокий вакуум, так называемый форвакуум.
Камерная печь сопротивления с нагревателем из вольфрама типа СНВЭ 1.3.1/16 И4 рассчитана на длительную работу при температуре 700-1000°С.
Вакуумная система печи обеспечивает достижение исходного вакуума в холодном состоянии печи до 2 Па и снабжена уловителем-осадителем отсасываемых паров пластификатора, роль которого выполняет камера диффузионного насоса.
Предельное рассчетное газовыделение - до 8 л/с при давлении до 0,3 КПа соответствует паспортной производительности двух вакуумных насосов НВР-0,5.
Объем печи - 3 дм3
(100´300´100 мм). Печь снабжается тиристорным регулятором с фотоэлектрическим программатором, в котором применен задающий шаблон из бумаги, вырезанный по контуру в соответствии с требуемой циклограммй нагрева. Печь оснащена контрольно-измерительными приборами: самопишущим термометром, мановакуумметром, амперметром и ваттметром
|
|
Мощность нагревателя 20 квт. Рис.71 Циклограмма работы печи для
предварительного спекания.
|
|
для контроля работы нагревателя и манометром для контроля давления охлаждающей воды.
В схеме печи имеются следующие блокировки, исключающие несанкционированные включения нагревателя: по расходу воды, по предельному току, по вакууму.
Циклограмма работы печи приведена на рисунке 71.
При обработке результатов измерений определяют величину потери массы заготовки при сушке, вычитая из массы исходной заготовки массу просушенной, и определяют относительное изменение массы в процентах как отношение полученной разности к массе исходной заготовки. затем по результатам расчетов определяют средний результат.
Рис.72. Схема печи для предварительного спекания. 1 - герметичный корпус печи, 2 - нихромовый нагреватель, 3 - теплоизоляция, 4 - выхлоп отсосанных газов, 5 - вакуум-насос, 6 - уровень масла в поглотителе, 7 - расширитель, 8 – корпус поглотителя, 9 - вакуумные трубопроводы (показаны утолщенной линией).
|
|
4.2.3. ТРЕБОВАНИЯ К ОТЧЕТУ
Отчет должен содержать краткое описание процесса сушки заготовок с описанием нежелательных явлений, которые следует избегать при выполнении этого процесса, и перечень путей их предотвращения, описание установок, описание действий при выполнении работы и таблицу наблюдений.
Объем отчета 2-3 стр.
Отчет подписывается студентом.
4.2.4. ЛИТЕРАТУРА
1. Кипарисов С.С., Либенсон Г.А. Порошковая металлургия. Учебник. М., Металлургия, 1980, с 215-246.
4.2.4. КОНТРОЛЬНЫЕ ВОПРОСЫ.
1. Для чего производится предварительное спекание ?
2. Какие опасные моменты возникают при предварительном спекании ?
3. Каким образом можно избежать растрескивания заготовок при предварительном спекании ?
4.2.5. ПРОТОКОЛ ИЗМЕРЕНИЙ
Таблица измерений имеет вид, показанный на рисунке 73
№№
|
Масса образца
до сушки, г
|
Масса образца
после сушки, г
|
Величина
изменения массы, г
|
Относительное изме-
нение массы, %
|
Рис.73. Таблица измерений к работе №20
ЛАБОРАТОРНАЯ РАБОТА № 21
4.3.
Определение усадки.
4.3.1. АППАРАТУРА И МАТЕРИАЛЫ
1. Вакуумная печь .................………………………………………………..
2. Весы электронные ...........…………………………………………………..........
3. Штангенциркуль .......................…………………………………………………....
4. Прессовка, полученная при выполнении лабораторной работы N°5 ................. 5 шт.
4.3.2. ПОРЯДОК ВЫПОЛНЕНИЯ РАБОТЫ
Третьим, заключительным и наиболее ответственным, этапом операции спекания является окончательное спекание, осуществляемое при температуре, в нашем случае, 1400°С.
В ходе работы используют заготовки, полученные при выполнении работы N°20. Студент получает пять заготовок, оставленных от предыдущей лабораторной работы, взвешивает и записывает их массу. Взвешивание производится на электронных весах с точностью +
0,01 г. Измеряют и записывают линейные размеры заготовок: длину, ширину, высоту с точностью +
0,1 мм
Затем заготовки помещают в вакуумную печь, включают ее в соответствии с технической инструкцией по эксплуатации и производят окончательное спекание, при котором формируются окончательные свойства изделия.
Типовая циклограмма работы печи приведена на рисунке 75.
Рис.75. Циклограмма работы печи для
окончательного спекания.
Затем печь отключают, заготовки охлаждают вместе с печью до комнатной температуры, заготовки извлекают и вновь взвешивают.
Вакуумная печь для окончательного спекания типа СНВС 1.3.1/16 И3 - это камерная печь сопротивления с нагревателем из вольфрама рассчитана на длительную работу при температуре 1400-1600°С (Рис. 76). Вакуумная система печи обеспечивает достижение исходного вакуума в холодном состоянии печи до 2 Па при газовыделении - до 8 л/с при давлении до 0,3 КПа.
Рис.76. Вакуумная печь для окончательного спекания типа СНВЭ 1.3.1/16И3.
1 -двухслойный корпус печи с водяной рубашкой, 2, 9 - двухслойные крышки с во-
дяной рубашкой, 3 - торцевой экран, 4 - нижний водоохлаждаемый экран, 5 - торце
вой нагреватель из вольфрама, 6 - токоподводящая шина, 7 - водоохлаждаемый
токоподвод, 8 - гляделка, 10 - боковой нагреватель из вольфрама.
Система охлаждения печи - водяная, замкнутая.
Объем печи - 3 дм3
.
Мощность нагревателя - 20 квт.
Печь оснащена контрольно-измерительными приборами: самопишущим термометром, мановакуумметром, амперметром и вольтметром для контроля работы нагревателя и манометром для контроля давления охлаждающей воды.
На первой стадии нагрева из шихты отгоняются остатки газов и пластификатора. На второй стадии нагрева происходит окончательное спекание и формируется заданная структура материала.
После завершения процесса печь охлаждают, открывают и извлекают из нее готовые изделия.
При обработке результатов измерений определяют величину потери массы заготовки при спекании, вычитая из массы исходной заготовки массу спеченной, определяют относительное изменение массы в процентах как отношение полученной разности к массе исходной заготовки. Затем по результатам расчетов определяют средний результат. Одновременно измеряют размеры спеченной заготовки с точностью +
0,1 мм и по формуле:
L2
К = ──, где
L1
L2
- размер изделия после спекания;
L1
- размер заготовки перед спеканием,
рассчитывают коэффициент линейной усадки.
Коэффициент линейной усадки определяют по величине изменения длины, толщины и высоты изделия.
4.3.3. ТРЕБОВАНИЯ К ОТЧЕТУ
Отчет должен содержать краткое описание процесса спекания заготовок с описанием нежелательных явлений, которые следует избегать при выполнении этого процесса, и перечень путей их предотвращения, описание установок, описание действий при выполнении работы и таблицу наблюдений.
Объем отчета 2-3 стр.
Отчет подписывается студентом.
4.3.4. ЛИТЕРАТУРА.
1. Кипарисов С.С., Либенсон Г.А. Порошковая металлургия. Учебник. М., Металлургия, 1980, с 215-246.
4.3.5. КОНТРОЛЬНЫЕ ВОПРОСЫ.
1. Для чего производится окончательное спекание ?
2. Какие явления сопровождают окончательное спекание ?
3. Какие виды брака возникают при окончательном спекании ?
4.3.5. ПРОТОКОЛ ИЗМЕРЕНИЙ
Таблица наблюдений имеет вид показанный ниже.
№№
|
Масса до нагрева, г
|
Масса после
нагрева, г
|
Величина
изменения массы, г
|
Длина образца до нагрева, мм
|
Длина образца после нагрева, мм
|
Линейная усадка по длине образца
|
Ширина образца до нагрева, мм
|
1
|
2
|
3
|
4
|
5
|
6
|
7
|
8
|
Ширина образца после нагрева, мм
|
Линейная усадка по ширине образца, мм
|
Высота образца до нагрева, мм
|
Высота образца после нагрева, мм
|
Линейная усадка по высоте образца
|
Объём образца до нагрева,
мм3
|
Объём образца после нагрева,
мм3
|
Объёмная усадка
|
9
|
10
|
11
|
12
|
13
|
14
|
15
|
16
|
Тема №5. ИЗУЧЕНИЕ СВОЙСТВ СПЕЧЁННЫХ ИЗДЕЛИЙ
Спечённые изделия в обязательном порядке проходят различные виды контроля, цель которого - не пропустить детали или полуфабрикаты, содержащие недопустимые дефекты и отклонения от технических условий, задаваемых нормативной документацией.
В первую очередь отбраковываются детали, имеющие недопустимые искажения формы и отклонения размеров от задаваемых чертежом. Затем проверяются такие физико-механические параметры как твёрдость материала, прочность при поперечном изгибе, плотность и служебные свойства, такие как:
- стойкость - для режущих пластин;
- энергия разрушения - для горного инструмента;
- коэффициент трения и параметры изнашивания (унос массы, равномерность и характер износа) - для подшипников;
- гидравлическое сопротивление - для пористых изделий (фильтров и сит);
- малоцикловая усталость (ползучесть) - для жаропрочных материалов;
- магнитная энергия и коэрцитивная сила - для магнитотвёрдых материалов и так далее в зависимости от служебного назначения изделия.
Контроль размеров спечённых деталей производится с использованием всех видов измерительных инструментов, применяемых в машиностроении: линеек, кронциркулей, штангенциркулей, штангенглубиномеров, штангенрейсмассов, микрометров, измерительных микроскопов и измерительных машин в зависимости от конфигурации обмеряемой формы и требуемой точности измерений. При проверке изделий по предельным отклонениям используют калибры: пробки, скобы, профильные калибры-шаблоны и так далее.
Специальные методы контроля параметров спечённых изделий описаны в соответствующих лабораторных работах - это измерение твёрдости, определение предела прочности при поперечном изгибе, а также технологические испытания при резании и определение энергии разрушения, которая является характеристикой работоспособности твёрдосплавных вставок (зубков) в буровом инструменте.
ЛАБОРАТОРНАЯ РАБОТА № 22
5.1.
Изучение искажений формы изделия при спекании.
Конфигурация изделия, далее - детали, полностью определена, если заданы допуски на все ее элементы: размеры, форму и взаимное расположение поверхностей.
Искажения формы детали связаны с нарушением формы и взаимного расположения поверхностей.
Отклонением формы поверхности (или профиля) называют отклонения формы реальной поверхности (реального профиля) от формы номинальной поверхности (номинального профиля), задаваемого чертежом. То же можно сказать и об отклонении взаимного расположения.
В основу нормирования и количественной оценки отклонений формы и расположения положен принцип введения прилегающих прямых, поверхностей и профилей.
Прилегающая прямая (или плоскость) - это прямая (плоскость) соприкасающаяся с реальным профилем и расположенная вне материала детали так, чтобы отклонение от нее наиболее удаленной точки реального профиля в пределах участка, на котором производится измерение, имело минимальное значение.
Прилегающая окружность (или цилиндр) - это окружность (или цилиндр) минимального диаметра, описанные вокруг реального профиля наружной поверхности тела вращения или максимального диаметра, вписанные в реальный профиль внутренней поверхности вращения (отверстия)
При измерении прилегающими поверхностями служат рабочие поверхности контрольных плит, интерференционных стекол, лекальных и проверочных линеек, калибров, контрольных оправок, шаблонов и т.п.
Количественно отклонение формы оценивается наибольшим расстоянием от точек реальной поверхности (профиля) до прилегающей поверхности (профиля) по нормали к последней.
Отклонения формы цилиндрических поверхностей.
Отклонением от цилиндричности называют наибольшее расстояние от точек реальной поверхности до прилегающего цилиндра, как это показано на рисунке 77.
Рис.77. Отклонение от цилиндричности.
Отклонением от круглости называют наибольшее расстояние от точек реального профиля до прилегающей окружности, как это показано на рисунке 78-а.
Частными видами отклонений от круглости являются овальность (рис.78-б) и огранка (рис.78-в).
Рис.78. Отклонения от круглости. А - общий случай, Б - овальность, В - огранка.
|
|
Отклонения от профиля цилиндрической поверхности в продольном сечении показаны на рисунке 79.
Рис.79. Формы отклонений от цилиндричности в продольном направлении.
А - общий случай, Б - бочкообразность, В - седлообразность (талия), Г - конусность.
Отклонение от прямолинейности оси в пространстве - это минимальное значение диаметра цилиндра, внутри которого располагается реальная ось поверхности тела вращения (см. рис. 80) Рис.80. Отклонение от прямолинейности
оси (линии) в пространстве.
|
|
Отклонения формы плоских поверхностей
Отклонением от прямолинейности в плоскости называют наибольшее расстояние от точек реального профиля до прилегающей прямой. Это показано на рисунке 81. Рис.81. Отклонение от прямолинейности.
На рисунке 82 показано отклонение от плоскостности, определяемое наибольшим расстоянием от реальной поверхности до прилегающей плоскости.
Рис.82. Отклонение от плоскостности.
Отклонением расположения поверхности или профиля называют отклонение реального расположения поверхности или профиля от его номинального расположения, задаваемого чертежом.
Отклонение от параллельности плоскостей показано на рисунке 83-а, а отклонение от перпендикулярности - на рисунке 83-б. Рис.83. А - отклонение от параллельности
поверхностей, Б - от перпендику-
лярности.
Отклонение от параллельности осей показано на рисунке 84, на котором базовая плоскость совпадает с плоскостью рисунка. Рис.84. Отклонение от параллельности осей.
Отклонение от соосности относительно общей оси - это наибольшее расстояние между общей осью двух или нескольких поверхностей вращения, на рисунке 85 - поверхностей отверстий.
Рис.85. Отклонение от соосности и отклонение от симметричности (D)
|
|
Отклонение от симметричности относительно базовой плоскости- наибольшее расстояние между базовой плоскостью симметрии рассматриваемой поверхности и реальной плоскостью симметрии. На рисунке 85 это отклонение обозначено буквой дельта.
Перечисленные отклонения - это наиболее часто встречающиеся виды отклонений, в реальных условиях многие из них сочетаются вместе в пределах поверхностей одной детали. Некоторые суммарные отклонения формы и расположения поверхностей нормируются совместно, как например радиальное и тоцевое биение и т.д.
5.1.1. АППАРАТУРА И МАТЕРИАЛЫ
1. Контрольная плита
2. Стойка с индикатором
3. Призма
4. Образцовая деталь
5.1.2. ПОРЯДОК ВЫПОЛНЕНИЯ РАБОТЫ.
Для выполнения работы студент получает образцовую деталь и производит замер тех видов отклонений от формы поверхности и их взаимного расположения, которые задает ему преподаватель. Определение некруглости выполняется на приспособлении, показанном на рисунке 86.
Обмеряемую деталь 3 устанавливают на призму 2 и, поворачивая деталь, отмечают показания стрелочного индикатора 4 через каждые 20-30°. Затем таким же образом обмеряют деталь в сечении, расположенном на 10-15 мм от первоначального. Всего обмеряют 5-6 сечений.
Определение отклонения от профиля цилиндрической поверхности в продольном сечении.
На том же приспособлении, что и в предыдущем случае, призму с деталью перемещают под щупом индикатора вдоль оси детали, производя измерения через каждые 10-12 мм. Затем деталь поворачивают на 40-45° и вновь производят замеры. Обмеряют величину отклонений в 5-6-ти сечениях, как это показано на рисунке 86.
Рис.86. Определение некруглости и отклонения профиля. 1 - стрелочный индикатор часового типа, 2 - образец,
3 - установочная призма, 4 - основание прибора.
При измерении некруглости образец поворачивают относительно горизонтальной оси, при измерении отклонения профиля - перемещают вдоль образующей образца.
|
|
Определение неплоскостности по соприкасающейся линии выполняют, обмеряя призматическую деталь, установленную на основание приспособления с индикатором, как это показано на рисунке 87.
Для облегчения контроля за перемещением деталь под щупом индикатора на поверхности деталь прочерчивают карандашом с помощью линейки прямую линию в направлении обмера.
Показания индикатора снимают через каждые 10-12 мм.
При определении неплоскостности по соприкасающейся плоскости на поверхности детали наносят карандашом сетку из взаимноперпендикулярных линий с шагом 10-12 мм. Обмер плоскости детали производят вначале в продольном, а затем - в поперечном направлении. Рис.87. Определение неплоскостности.
1 - стрелочный индикатор часового типа на стойке, 2 - обмеряемая деталь, 3 - плоскопараллельная подставка, 4 - основание прибора.
|
|
5.1.3. ТРЕБОВАНИЯ К ОТЧЕТУ
Отчет должен содержать описание видов искажений формы и взаимного расположения поверхностей, описание примененного приспособления, а также таблицу измерений и построенные по данным измерений реальные профили поверхностей.
5.1.4. ЛИТЕРАТУРА.
1. Якушев А.И., Воронцов Л.Н., Федотов Н.М. Взаимозаменяемость, стандартизация и технические измерения. Учебник для втузов. М., Машиностроение. 1987г. 174-185 с.
5.1.5. КОНТРОЛЬНЫЕ ВОПРОСЫ.
1. Какие отклонения от формы поверхностей Вы знаете ?
2. Какие отклонения от взаимного расположения поверхностей известны Вам ?
3. Какие виды брака и причины их вызывающие могут проявляться при спекании ?
5.1.5. ПРОТОКОЛ ИЗМЕРЕНИЙ.
Таблица измерений содержит наименование определяемого отклонения и имеет вид, показанный на рисунке 88 (см. ниже)
№№
|
Координаты точки измерения, мм
|
Показания индикатора, мкм
|
Величина отклонения с учётом знака, мкм
|
В отчёте приводится профиль обмеренной поверхности (сечения).
Ниже показан пример выполнения профиля поперечного сечения цилиндрической детали с отклонениями от цилиндричности. Рис.89. Схема (для примера) профиля ци-
линдрической поверхности в нор-
мальной плоскости.
ЛАБОРАТОРНАЯ РАБОТА № 23
5.2.
Изучение основных видов брака и причин его возникновения при производстве твердых сплавов.
"Корочка"
- разрыв поверхности изделия или приподнятый слой. Разрушение изделия происходит путем отделения (шелушения) поверхностного слоя. (рис. 90-а). Часто внешний вид изделия не меняется. Наиболее часто "корочка" проявляется в слабоспрессованных изделиях или отдельных его участках. Причиной появления "корочки" является:
- появление в атмосфере печи углеводородов вследствие разложения пластификатора,
- большая скорость нагрева изделий,
- перегрузка лодочек изделиями, при которой они экранируют друг друга,
- недостаточно быстрый обмен в атмосфере печи, особенно при спекании в водороде или вакууме, при котором не успевают удаляться продукты термического разложения примесей, что дает им возможность накапливаться в поверхностном слое заготовки.
Брак неисправим.
"Расслой"
- крупные продолговатые вздутия на поверхности изделия, расположенные вблизи ребер, или трещины, параллельные ребрам. В изломе трещины идут под углом или параллельно направлению прессования (рис. 90-б)
Причина "расслоя" - завышение давления прессования (перепрессовка), неравномерное распределение пресспорошка в прессформе, перекос пуансонов в процессе прессования, окисленная смесь, наличие примесей в смеси, неполное удаление растворителя при сушке заготовок.
Брак неисправим.
Недопекание (недоспекание)
- в результате занижения температуры спекания снижены физико-механические свойства материала изделия.
Брак исправим путем повторного спекания на положенных режимах.
Трещины
- возникают при локальных перенапряжениях при прессовании, но на прессовке незаметны, и появляются в виде сетки трещин либо одиночных трещин только после спекания. (рис. 90-в) Причиной трещинноватости изделий является неправильная конструкция прессфомы, вызывающей перенапряжение при прессовании в отдельных участках прессовки, неравномерный нагрев изделия при спекании, завышение скорости нагрева при отгонке пластификатора, при котором бурно выделяющиеся пары разрывают заготовку.
Брак неисправим.
Пережог
- сильное завышение температуры спекания вызывает появление сферических вздутий, проплавленных мест, пузырей, раковин, общее повышение пористости. (рис. 90-б)
Брак неисправим.
Бой
- скалывание или выкрашивание углов и ребер изделий. Причинами его возникновения является неаккуратное обращение с сырыми ("зелеными") заготовками, особенно при укладке их на лодочки.
Этот вид брака нормирован стандартами и техническими условиями на изделия.
Коробление
- искажение формы изделия, связанное с неравномерной усадкой вследствие неравномерной плотности прессовки, либо с прогибом - искривлением изделий под действием собственного веса. (рис. 90-г) Причиной может быть неравномерный нагрев заготовки, при котором отдельные ее участки нагреваются сильнее, а также нарушение основного правила при укладке изделий на лодочку - прессовки надо укладывать в направлении прессования.
Этот вид брака нормирован стандартами и техническими условиями.
Изменения поверхностного слоя: науглероживание, декарбидизация, цианирования (нитроцементация) и др.,
связанные с удалением или пересыщением поверхностного слоя теми или иными элементами. Вызываются недопустимыми изменениями состава атмосферы печи с одновременным превышением температуры спекания.
Брак неисправим.
Рис.90. Различные виды брака поверхности твердосплавных изделий.
А - корочка, Б - пережог и расслой, В - трещины, Г - коробление.
5.2.1. АППАРАТУРА И МАТЕРИАЛЫ
1. Образца брака
5.2.2. ПОРЯДОК ВЫПОЛНЕНИЯ РАБОТЫ.
По стандарту брак выявляется путем внешнего осмотра спеченного изделия без применения оптических средств и средств измерения.
Студент получает комплект образцов изделий с установленным видом брака и рассматривает их. Затем составляет описание образцов и зарисовывает их.
5.2.3. ТРЕБОВАНИЯ К ОТЧЕТУ
В отчете должны быть описаны виды брака, причины его появления и методы устранения.
Отчет должен содержать зарисованные образцы бракованных изделий.
Отчет содержит 2-3 стр.
Отчет подписывается студентом.
5.2.4. ЛИТЕРАТУРА.
Романова Н.И., Чекулаев П.Г., Дусев В.И. и др. Металлокерамические твердые сплавы. Учебник. М., Металлургия 1970г. с. 170-178.
5.2.5. КОНТРОЛЬНЫЕ ВОПРОСЫ.
1. Какие виды брака спеченных изделий из твердых сплавов Вы знаете ?
2. Какие основные причины вызывают появление брака ?
3. Какие основные меры предупреждения появления брака ?
ЛАБОРАТОРНАЯ РАБОТА № 24
5.3.
Измерение плотности спеченных заготовок.
5.3.1. АППАРАТУРА И МАТЕРИАЛЫ
1. Приспособление для измерения плотности
2. Весы электронные ...........................
3. Специальный образец
5.3.2. ОСНОВЫ ИЗМЕРЕНИЯ ПЛОТНОСТИ
Плотностью тела называется отношение массы тела к его объему.
M
r = ─── , где
V
M - масса тела, г
V - объем тела, смЗ
.
Плотность спеченных заготовок определяют гидростатическим способом, в основе которого лежит закон Архимеда: на тело, погруженное в жидкость действует выталкивающая сила, которая численно равна весу жидкости, вытесненной телом. Таким образом, гидростатическая сила выталкивания численно равна объему исследуемого тела при плотности жидкости, равной единице.
5.3.3. ПОРЯДОК ВЫПОЛНЕНИЯ РАБОТЫ.
Для определения плотности собирают приспособление, показанное на рисунке 91
Рис. 91. Схема гидростатического взвешивания. А – взвешивание на воздухе, Б – взвешивание образца в воде. 1 - электронные весы, 2 - подставка для стакана, 3 - взвешиваемый образец, 4 - химический стакан, 5 - кронштейн для подвески образца, 7 - нить с крючком, 8 - термометр.
|
|
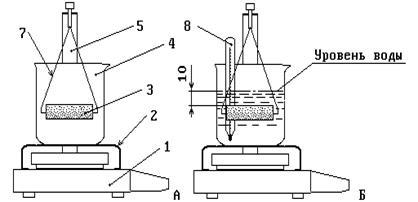
Взвешивание осуществляют следующим образом. На платформу электронных весов 1 устанавливают кронштейн для подвески образца 5. Сверху кронштейна, между его стойками помещают подставку для стакана 2 так, чтобы она не соприкасалась с платформой весов и кронштейном. На подставку 2 устанавливают стакан 4, также устанавливая его без соприкосновения с кронштейном. На кронштейн укладывают нить с крючком 6 для подвески образца.
Включают весы и сбрасывают их показания в нуль.
Затем образец закрепляют с помощью нити с крючком 6 на кронштейне 5 и производят взвешивание образца. Этим определяют вес образца в воздухе М1
.
Затем в стакан наливают кипяченую (обезгаженную) холодную воду и измеряют ее температуру термометром 7. После измерения температуры измеряют вес образца в воде М2
.
По формуле
M1
´rm
r = ───── , где
M1
– M2
М1
- масса образца в воздухе, г
М2
- масса образца в воде, г
rm
-плотность воды при данной температуре, г/см3
Плотность воды при температуре измерения определяют по таблице 7.
Таблица 7
Зависимость плотности воды от температуры
Температура,
О
С
|
Плотность,
г/см3
|
|
Температура,
О
С
|
Плотность,
г/см3
|
15
|
0,9981
|
23
|
0,9965
|
16
|
0,9979
|
24
|
0,9963
|
17
|
0,9977
|
25
|
0,9960
|
18
|
0,9976
|
26
|
0,9958
|
19
|
0,9974
|
27
|
0,9955
|
20
|
0,9972
|
28
|
0,9952
|
21
|
0,9970
|
29
|
0,9949
|
22
|
0,9967
|
30
|
0,9946
|
Расчет плотности проводят с точностью до 2-го знака.
За показатель плотности принимают значение рассчитанной плотности, округленное до 0,1 г/см3
.
Результаты испытаний заносят в протокол. По результатам определения плотности строят картину распределения плотности по высоте прессовки.
5.3.4. ТРЕБОВАНИЯ К ОТЧЕТУ
Отчет должен содержать краткое описание физических основ прессования, описание установок и методики определения плотности прессовки, порядок выполнения работы и таблицу наблюдений.
Таблица наблюдений показана на рисунке 92 (см. ниже)
№№
|
Масса образца на воздухе, г
|
Масса образца в воде, г
|
Температура воды, О
С
|
Плотность воды, г/см3
|
Плотность образца, г/см3
|
Среднее значение плотности образца -
Объем отчета 2-4 стр.
Отчет подписывается студентом.
5.3.5. ЛИТЕРАТУРА.
1. Кипарисов С.С., Либенсон Г.А. Порошковая металлургия. Учебник. М., Металлургия, 1980, с 215-246.
2. Сплавы твердые спеченные. Метод определения плотности. ГОСТ 20018.
ЛАБОРАТОРНАЯ РАБОТА № 25
5.4.
Определение предела прочности при поперечном изгибе стандартных образцов из спечённых твёрдых сплавов.
5.4.1. АППАРАТУРА И МАТЕРИАЛЫ
1. Разрывная машина с реверсором .......
2. Приспособление для измерения предела
прочности при поперечном изгибе
3. Специальный образец по ГОСТ 20019
Рис.93. Разрывная машина ИР-5145 (Р-5).
5.4.2. ОСНОВЫ ИЗМЕРЕНИЯ ПРЕДЕЛА ПРОЧНОСТИ ПРИ ПОПЕРЕЧНОМ ИЗГИБЕ
При исследовании прочности малопластичных и хрупких порошковых материалов таких как пористые фильтры, композиционные материалы, тугоплавкие металлы, керметы, твердые сплавы и тому подобных производят испытания на изгиб.
Испытания на изгиб проводят с использованием балки на двух опорах, как это показано на схеме слева на рисунке 94. Рис.94. Приспособление ля измерения предела прочности при поперечном изгибе и схема измерения.
1 - основание, 2 - призма, 3 - самоустанавливающаяся опора, 4 - верхний нажимной ролик, 5 - шток, 6 - образец, 7 - нижние опорные ролики, l - расстояние между опорами. P - нагрузка, D - прогиб образца под нагрузкой.
|
|
Испытания на изгиб проводят на стандартных образцах определенного размера, например для твердых сплавов - сечением 5 ´ 5 мм и длиной не менее 35 мм (ГОСТ 20019). Образец устанавливают на опорах, расстояние между которыми - l = 30+
0,5 мм. Нагрузка прикладывается посередине между опорами приспособления.
Приспособление для измерения состоит из массивного основания 1 с установленной на нем между двумя цилиндрическими стойками призмой 2, на которой установлена с возможностью перемещения самоустанавливающаяся опора 3. На опоре 3 закреплены на расстоянии 30 мм друг от друга два параллельных опорных ролика 7 из высокопрочного материала. В штоке 5 приспособления закреплен нажимной ролик 4, ось которого параллельна осям опорных роликов 7.
5.4.3. ПОРЯДОК ВЫПОЛНЕНИЯ РАБОТЫ.
На опорные ролики устанавливают стандартный образец и подводят к нему шток с нажимным роликом 7. Включают разрывную машину и со скоростью перемещения траверсы
разрывной машины не более 2 мм/мин производят нагружение образца до разрушения.
Предел прочности при поперечном изгибе sи
, МПа вычисляют по формуле без учета влияния возможной пластической деформации
3F´ l
sи
= ─────── , где
2h2
´ b
F - наибольшая нагрузка, соответствующая моменту разрушения образца, кН,
l - расстояние между осями опор, мм,
h - высота образца - размер в направлении приложения нагрузки при испытании, мм,
b - ширина образца, мм.
Результаты вычислений округляют до 1 МПа.
Испытание считают недействительным, если место излома со стороны растяжения при изгибе (нижняя сторона) отстоит от линии приложения нагрузки более, чем на 5 мм.
По результатам испытаний определяют среднее арифметическое.
Испытания проводят 5-6 раз.
5.4.4. ТРЕБОВАНИЯ К ОТЧЕТУ
Отчет должен содержать методику проведения испытаний на изгиб, описание примененного приспособления, а также таблицу измерений.
5.4.5. ЛИТЕРАТУРА.
Сплавы твердые спеченные. Метод определения предела прочности при поперечном изгибе. ГОСТ 20019.
5.4.6. КОНТРОЛЬНЫЕ ВОПРОСЫ.
1. Для каких материалов определятся предел прочности при поперечном изгибе ?
2. Опишите методику проведения испытаний.
3. В чем причина большого разброса величины предела прочности, получаемого при испытаниях ?
5.4.7. ПРОТОКОЛ ИЗМЕРЕНИЙ.
Таблица измерений показана на рисунке 95 (см. ниже)
№№
|
Высота образца, мм
|
Ширина образца, мм
|
Разрушающая сила, кН
|
Предел прочности при поперечном изгибе, МПа
|
Среднее значение предела прочности - [указать значение
]
ЛАБОРАТОРНАЯ РАБОТА № 26
5.5.
Измерение твёрдости спечённых изделий.
5.5.1. АППАРАТУРА И МАТЕРИАЛЫ
1. Пресс Роквелла ..................……………………………………………………….....
2. Образцовая деталь
5.5.2. ОСНОВЫ ОПРЕДЕЛЕНИЯ ТВЕРДОСТИ МЕТОДОМ РОКВЕЛЛА
Метод Роквелла применяется в промышленности с 1919 года. В настоящее время он является одним из наиболее распространенных методов технологического контроля металлических деталей.
Измерение твердости по методу Роквелла для металлов регламентировано ГОСТ 9012. Для твердых сплавов - ГОСТ 20017.
У метода Роквелла по сравнению с другими методами измерения твердости (Бринеля, Виккерса, Шора и т.п.) следующие преимущества:
- возможность производить измерения поверхностей с высокой твердостью,
- простота определения числа твердости прямым отсчетом по шкале индикатора без использования номограмм,
- малая повреждаемость испытуемой поверхности,
- отсутствие остаточных напряжений в проверяемой детали,
- высокая производительность измерений,
- возможность обслуживания приборов малоквалифицированным персоналом.
Недостатки метода:
- отсутствие единой шкалы твердости (15 независимых шкал),
- невозможность повторной проверки полученных результатов,
- изменение характера вдавливания при применении алмазного конуса и стального шарика,
- твердость по шкале Роквелла выражена в условных единицах.
По шкалам А и С измеряют твердость при помощи алмазного конуса с углом при вершине 120О
+
30' и закругленной вершиной с радиусом сферы 0,2 +
0,005 мм.
Твердость по Роквеллу (см. рис.96)
h - h0
HR
= A - ────── , где
C
А - постоянная величина, выбираемая по применяемой шкале, h1
- глубина вдавливания наконечника под действием предварительной нагрузки Р0
,
h - глубина вдавливания наконечника под действием общей нагрузки (Р0
+ Р1
), измеряемая после снятия основной нагрузки Р1
при наличии предварительной нагрузки Р0
,
С - цена деления шкалы измерительного индикатора в условных единицах твердости. Для шкал А и С величину С выбирают равной 200 мкм.
|
|
5.5.3. ПОРЯДОК ВЫПОЛНЕНИЯ РАБОТЫ.
Измерения производят следующим образом. На стол 4 укладывают деталь так, чтобы она не имела возможности качаться и с помощью подъемного винта осторожно подводят алмазный наконечник (индентор) 3 к поверхности детали.
Рис.96. Схема измерения по Роквеллу и Рис.97. Прибор (пресс) Роквелла
выбора величины А для шкалы С 1-станина,2-индикатор, 3 - алмазный
наконечник (индентор), 4 - стол; 5 -
ручка рычага нагрузки.
Точка, в которой необходимо измерить твердость, должна отстоять от края детали не менее, чем на 8-10 мм во избежание сколов или опрокидывания детали.
Вращая ходовой винт стола, осторожно осуществляют предварительное нагружение силой Р0
, контролируемой по стрелочному индикатору. Малая стрелка индикатора устанавливается на ноль.
Вращая ободок шкалы индикатора, устанавливают на отметку 0 внешнюю шкалу индикатора (красного цвета).
Затем осторожно отпускают ручку 5, связанную с грузом Р1
, расположенную с правой стороны прибора. Освободив ручку отпускают ее и в течение 10-15 сек. дожидаются остановки стрелки индикатора.
После этого ручку возвращают в исходное положение, а по шкале RA
определяют полученное значение твердости. Опускают стол прибора, сдвигают деталь на 8-10 мм и повторяют измерения. Так поступают 5-6 раз.
5.5.4. ТРЕБОВАНИЯ К ОТЧЕТУ
Отчет должен содержать описание принципа измерения твердости методом Роквелла, описание прибора и методики проведения измерения, а также таблицу измерений.
5.5.5. ЛИТЕРАТУРА.
1. Испытательная техника. под ред. В.В.Клюева. книга 1. М., Машиностроение. 1982г. 246-253с.
2. Сплавы твердые спеченные. Определение твердости по Роквеллу. ГОСТ 20017.
3. Металлы. Метод измерения твердости по Роквеллу. ГОСТ 9012.
5.5.6. КОНТРОЛЬНЫЕ ВОПРОСЫ.
1. Каким образом производится измерение твердости по Роквеллу ?
2. Перечислите достоинства метода измерения твердости по Роквеллу ?
3. Какие недостатки у этого метода измерения твердости ?
5.5.7. ПРОТОКОЛ ИЗМЕРЕНИЙ.
Таблица измерений имеет вид, показанный на рисунке 98 (см. ниже)
№№
|
Значение твёрдости, HRA
|
Среднее значение твёрдости, HRA
|
ЛАБОРАТОРНАЯ РАБОТА № 27
5.6. Определение стойкости режущей пластины.
Пластины для режущего инструмента являются одним из основных видов продукции из твердых сплавов - их доля в общем объеме производства составляет почти 40%.
Режущие пластины работают в очень тяжелых условиях: высокие контактные напряжения, интенсивное трение в условиях высоких температур и вакуума, активное химическое, диффузионное и электроконтактное взаимодействие материалы пластины с обрабатываемым материалом предъявляют очень жесткие требования к качеству инструмента, который должен выдерживать такие интенсивные нагрузки в течение определенного гарантированного времени, в течение которого не должны меняться основные параметры инструмента: размеры и форма режущей кромки, твердость, прочность, и т.п.
Каждая партия режущих пластин проходит испытания с целью определения режущих свойств изготовленного материала. Эти испытания - натурный эксперимент в аттестованных условиях, то есть проводятся в реальных условиях резания, причем для получения сопоставимых результатов условия проведения испытаний стандартизованы: применяется отобранный инструмент определенного вида со стандартной геометрией, обрабатывается определенный материал на установленных режимах обработки.
Для получения достоверных результатов испытания проводятся многократно с набором данных, составляющих достаточно большой статистически достоверный массив данных. Объем выборки - не менее 5-ти штук.
Минстанкопромом СССР разработаны "Типовая программа и методика Государственных испытаний режущего инструмента", которые действуют до 2000 года и на основании которых, при составлении утвержденных протоколов испытаний, выносится заключение о работоспособности инструмента данной партии.
Испытания значительно превышают стоимость изделия, так как в процессе испытаний режущего инструмента обрабатывается образец, переводимый в стружку.
Несложно рассчитать, что при стандартном режиме испытаний при скорости резания 150 м/мин., подаче 0,4 мм/об и глубине резания 3 мм за минуту испытаний в стружку переходит
g S0
tV 7,8´ 0,4´ 3´ 150
P = ───── = ─────────── = 1,4 (кг)
1000 1000
что при стойкости, например 30 мин. составит около 40 кг на одно измерение или с учетом не менее одиннадцати испытаний - 440 кг.
Высокая трудоемкость свыше 20-ти часов и материалоемкость делает проблему повышения эффективности испытаний чрезвычайно актуальной.
Повысить эффективность испытаний режущего инструмента можно за счет снижения трудоемкости и удешевления испытаний путем сокращения объемов испытаний и расхода материалов образцов.
Износостойкость инструмента в зависимости от скорости резания в случае работы твердосплавными резцами имеет, в общем случае, вид, представленный на рисунке 99, а кривые износа по времени ничем не отличаются от типовой кривой износа (рис.100).
Сравнение этих кривых показывает, что участки, при которых работает инструмент, находятся во всех случаях в области линейной зависимости
T = f(V) и
hзадн
= f (T)
и, следовательно, можно считать, что интенсивность износа резца не зависит от величины текущего износа, тем более, что, как это показано академиком Т.Н.Лоладзе, одним и тем же температурам резания и коэффициенту трения соответствует одна и та же стойкость и усадка стружки независимо от обрабатываемого материала и режима резания.
Таким образом, поскольку известен характер изменения износа от времени - это прямолинейная зависимость (на эксплуатационном участке), а изнашивание инструмента является стационарным, то становится возможным, определив несколько точек на кривой износа, распростра-
har_32.pcx
Рис.100. Износ по задней поверхности резца в зависимости от времени. 1 - период притупления передней кромки (приработка), 2 - период установившегося износа (рабочий режим), 3 - период катастрофического износа.
|
|
Рис.99. Стойкость сплавов ВК и ТК при обработке стали. 1 и 2 - области устойчивой работы.
|
|
нить знание параметров на начальном участке изнашивания на всю картину износа инструмента, проведя двойную экстраполяцию - по времени и по нагрузке, изменяя скорость резания.
Именно в этом и заключается отличие разработанной методики от стандартной, при которой измерение износа проводят на стационарной нормативной скорости. Такой метод ускоренных ипытаний получил название метод Кондратьева. Он не нашел применения в практике, так как требует значительного, недоступного ранее, расчетного аппарата и преимущества от сокращения времени измерения пропадают.
Дополнительную неопределенность вносит и то, что для каждой конкретной партии твердого сплава неизвестны параметры, соответствующие критическим скоростям резания, при которых катастрофический износ возникает в момент касания резца к поверхности детали. А само определение этой скорости достаточно трудоемко и связано с необходимостью проведения большого количества испытаний по определению критической скорости.
Если же принять во внимание, что режущий инструмент никогда не работает до области катастрофического износа, а нормативный износ регламентирован соответствующими стандартами, то область необходимых измерений сокращается и практически необходимо определить только две точки на кривой износа на рисунке 99, соответствующие скорости резания
заведомо ниже скорости резания, соответствующей скорости катастрофического износа режущей кромки.
Для получения соизмеримого со стандартным результата испытания следует проводить в области износа, соответствующей середине участка 2 на рисунке 100.
В этом случае мы получаем заведомо заниженную величину стойкости инструмента и скорости минутной стойкости, но это снижение, как показал опыт, не превышает 20%.
Испытания проводят следующим образом.
Предварительно производят обточку образца на низкой скорости резания V1
в течении времени Т2
до достижения износа около 0,1 мм. После этого при постоянной глубине резания и подаче (например t =3 мм и S0
= 0,4 мм/об) производят обточку с различными скоростями резания V2
, V3
, V4
.... Vn
. Чтобы не попасть в область скоростей резания, соответствующих катастрофическому мгновенному износу или превышающих скорость резания минутной стойкости, максимальную скорость резания не следует выбирать большой, например не более 200 м/мин.
Для каждого значения скорости резания фиксируют прирост линейного износа h1
, h2
, h3
... hn
, соответствующий времени работы t1
, t2
, t3
... tn
.
Определяют интенсивность износа
Dhi
hзадн.
i
= ────
hi
и определяют фиктивную стойкость
0,4
Ti
= ──── ti
hзадн.
i
где 0,4 - расчетный износ задней поверхности
Далее в двойной логарифмической сетке строят зависимость Ti
= f(V), представляющую собой прямую линию (Рис.7), тангенс угла наклона которой к оси абсцисс равен показателю m в формуле
l
V = ──
Tm
где m - коэффициент Тейлора
Поскольку график T = f(V) линеен, то можно производить измерения всего при двух-трех значениях скоростей резания, которые следует выбирать кратными пяти или десяти, например 50, 100, 150, 200 м/мин.
Подача и глубина резания фиксированы и соответствуют стандартному режиму обработки для данного вида резцов.
Предлагаемая методика удобна еще и тем, что не требует выбора в качестве образцового материала заготовки стали 45 или 40Х. Возможно применение широкой гаммы материалов: Сталь 3, 40, 45, 30ХГСА, 12Х18Н9Т и т.п. поскольку угол наклона прямой на графике 101 не зависит от марки обрабатываемого материала. Единственное, что потребуется при переходе на другие марки сталей или сплавов - это подбор максимальной скорости резания при испытании, который не должен превышать величины скорости минутной стойкости и, тем более, критической скорости резания.
При соблюдении этих условий машинное время испытания составляет 3-5 мин., а с учетом обработки результатов - 30-40 мин., расход металла образца не превышает 1 кг на все.
Сопоставление результатов испытаний по этому методу с результатами стандартных испытаний показывает, что результаты их совпадают с разбросом, не превышающим 20% и по ним можно оценить работоспособность данной партии твердого сплава. Рис.101. Расчетная схема ускоренных испытаний
По полученному графику можно определить расчётную стойкость при скорости резания V = 150 м/мин и скорость минутной стойкости, необходимые при определении эффективности применения данного твердого сплава в данном конкретном случае обработки материалов по способу Хитоми, что важно
|
|
при назначении режимов обработки для резцов, работающих на станках с ЧПУ или в составе ОЦ и ГАП.
Методика ускоренных испытаний сопровождается программой обработки результатов измерений на любом ПК, поскольку составлена на доступном языке Бейсик, с распечаткой результатов в виде протокола и представлением его на экране дисплея в виде наглядного графика (рис. 102)
Рис.102. Представление результатов испытаний режущих пластин на экране ПЭВМ.
|
|
5.6.1. АППАРАТУРА И МАТЕРИАЛЫ
1. Токарный станок .................……………………………………………………………
2. Резец образцовый с пластиной ....………………………………………………
3. Лупа Бринеля ...........……………………………………………………………….........
4. Секундомер ....………………………………………………………………...................
5. Тахометр ...................………………………………………………………………….....
5.6.2. ПОРЯДОК ВЫПОЛНЕНИЯ РАБОТЫ
При выполнении работы студент производит измерения, а на станке работает оператор-лаборант.
Подготовленный резец, оснащенный пластиной CNUM-120408, устанавливают в резцедержателе станка так, чтобы главный угол в плане составил 90°. Устанавливают заранее подготовленную заготовку из стали 45, 40Х или 30ХГСА и устанавливают следующий режим резания:
- глубина резания ....................... 2 мм,
- подача ................................. 0,2 мм/об
Затем с помощью тахометра устанавливают скорость резания 20 м/мин и производят резание в течение 10-15 сек. Это время в дальнейшем не учитывается, поскольку соответствует времени приработки инструмента.
Затем производят контрольное резание на установленной скорости в течение 90-100 сек. Резец снимают и измеряют износ по задней поверхности с помощью лупы Бринеля с точностью +
0,01 мм.
А Б В
Рис.103. Картина износа, наблюдаемая в лупу Бринеля. А - типичный износ, видны следы пропахивания, Б - износ с вырывам блока, В - равномерный износ мелкозернистого твёрдого сплава.
С помощью тахометра устанавливают скорость резания 100 +
20 м/мин и проводят резание в течение еще 30-40 сек. Измеряют фаску износа.
Повторяют эксперимент, установив скорость резания 150 +
20 м/мин и произведя резание еще в течение 20-30 сек. Измеряют фаску износа.
Полученные значения скорости, подачи и времени измерения вводят в ПЭВМ и получают результаты испытаний в виде протокола, распечатываемого принтером.
5.6.3. ТРЕБОВАНИЯ К ОТЧЕТУ
Отчет должен содержать краткое описание процесса определения режущих свойств инструмента и методику обработки результатов измерений с помощью ПЭВМ.
Объем отчета 2-3 стр.
Отчет подписывается студентом.
5.6.4. ЛИТЕРАТУРА.
1. Третьяков В.И. Основы металловедения и технологии производства спеченных твердых сплавов. М., Металлургия, 1976, с 485-490.
5.6.7. КОНТРОЛЬНЫЕ ВОПРОСЫ.
1. Для чего производится испытание резанием ?
2. В чем неудобство стандартной методики натурных испытаний ?
3. Какие виды износа режущего инструмента Вы знаете ?
5.6.8. ПРОТОКОЛ ИЗМЕРЕНИЙ
Таблица наблюдений ( в виде протокола, распечатанного ЭВМ)
ЛАБОРАТОРНАЯ РАБОТА № 28
5.7.
Определение энергии разрушения зубка буровой коронки.
Твёрдые сплавы для бурового инструмента должны обладать повышенной вязкостью, так как работают в условиях ударных нагрузок - это и удары при разрушении горной породы и удары, вызываемые неравномерным и безопорным вращением длинной буровой штанги.
Твёрдые сплавы для бурового инструмента должны обладать повышенным сопротивлением абразивному изнашиванию, поскольку горные породы, весьма неоднородные по строению, все являются материалами абразивными.
Твёрдость сплавов для породоразрушающего инструмента должна быть уж не как не менее твёрдости кварца и ему подобных руд: серебряно-цинковых, медных и так далее, то есть не менее 88-89 ед. HRA.
Измерения твёрдости, определение предела прочности при поперечном изгибе, испытания при резании металлов не дают представления о действительной пригодности того или иного твёрдого сплава при использовании его в породоразрушающем инструменте.
Н.А.Кудря предложил способ оценки пригодности твёрдого сплава для использования в качестве породоразрушающего путём определения интегральной характеристики, связанной со способностью определённого объёма твёрдого сплава выдерживать потоки механической энергии. Дело в том, что породоразрушающий инструмент, в отличие от металлообрабатывающего, участвует в процессе разрушения не только в точке контакта поверхности зубка с породой, но и всей массой твёрдосплавной вставки (зубка), которая передаёт удары горной породы в тело оправки по всему сечению зубка. В металлорежущем инструменте во время работы нагружена примерно треть - две трети от всей массы режущей пластины. А характер нагружения металлорежущей пластины - это изгибающие нагрузки и смятие в точке контакта вершины резца со стружкой, то есть на резец действуют силы достаточно хорошо рассчитываемые по формулам дисциплины "Сопротивления материалов".
Пластина режущего инструмента прижата к державке небольшой поверхностью и усилие прижима относительно невелико, то есть усилие резания почти всё приложено к пластине и державка воспринимает незначительную его часть.
В породоразрушающем инструменте зубок вставлен в своё гнездо со значительным натягом, как правило - при помощи горячепрессовой посадки и находится в объёмносжатом состоянии. Поэтому возникающие в зубке напряжения частично компенсируются напряжениями, созданными при посадке зубка в корпус. Это увеличивает нагрузочную способность зубка в несколько раз.
Изучение ударов горной породы по зубку показало, что эти удары - центральные. Это и позволяет оценить работоспособность зубка, моделируя удары горной породы, ударами "бабы" копра. По мере накопления энергии зубок начинает разрушаться и от него начинают откалываться частицы. Масса отколовшихся частиц пропорциональна накопленной энергии, то есть совершённой работе разрушения. Определяя количество отколовшихся частиц определённого размера после 10, 20, 30 и так далее ударов можно оценить способность материалы сопротивляться центральным ударам.
Затем, нанося аналогичные удары по куску горной породы, можно определить работу разрушения горной породы, а по соотношению работы разрушения зубка и породы - относительный коэффициент сопротивления, который позволяет определить возможность бурения данной породы этой маркой твёрдого сплава. Этот коэффициент должен быть не менее 1,1.
5.7.1. АППАРАТУРА И МАТЕРИАЛЫ
1. Копёр
2. Сито размером 300 мкм
3. Аналитические весы
4. Образец - зубок
5. Образец горной породы
Рис.104. Копёр для определения энергии разрушения зубков и горных пород.
1 - баба массой 10 кг, 2 - труба, 3 - образец-зубок, 4 - пята, 5 - основание.
|
|
5.7.2. ПОРЯДОК ВЫПОЛНЕНИЯ РАБОТЫ.
На опорную плиту копра устанавливают образец-зубок, поднимают груз (бабу) на высоту 1 м, закрывают кожух установки и отпускают бабу, нанося удар по образцу. Так повторяют 10 раз. После этого собирают осколки, отсеивают их на сите и взвешивают с точностью до +
10 мг.
Повторяют измерения 10-15 раз.
Аналогично поступают с образцом горной породы.
Строят зависимость - "количество осколков в г - серия ударов" для образцов и рассчитывают соотношение между общим количеством осколков в граммах после 10 - 15 серий ударов, определяя соотношение сопротивлению ударному разрушению образца-зубка и образца породы.
5.7.3. ТРЕБОВАНИЯ К ОТЧЕТУ
Отчет должен содержать методику проведения испытаний на разрушение, описание примененного приспособления, а также таблицу измерений и график зависимости массы отколовшихся частей от числа ударов.
5.7.4. КОНТРОЛЬНЫЕ ВОПРОСЫ.
1. В чём состоят особенности работы породоразрушающего инструмента по отношению к режущему?
2. Опишите методику проведения испытаний.
3. Как влияет объёмное сжатие зубка на его сопротивление ударному разрушению ?
5.7.4. ПРОТОКОЛ ИЗМЕРЕНИЙ.
Таблица измерений показана на рисунке 105 (см. ниже)
№№
|
Вид образца
|
Количество ударов в серии
|
Количество частиц , отбитых от образца, г
|
Общее количество отбитых частиц, г
|
Среднее значение соотношения масс отбитых частиц образцов -
Рис.106. Примерный вид графиков зависимостей
массы отколовшихся частей от числа ударов для
зубка и горной породы.
ТЕМА №6. МЕТОДЫ АНАЛИЗА ПОРОШКОВ И СПЕЧЁННЫХ ИЗДЕЛИЙ
При анализе порошков компонентов, входящих в состав порошковой смеси, определяют (при входном контроле) химический и гранулометрический состав, форму частиц и напряжённое состояние частиц.
Химический состав определяют различными способами: химическим анализом, спектроскопическим и рентгеновским анализом, а при необходимости - и методами масс-спектроскопии. Напряжённое состояние частиц, знание которого необходимо при создании магнитных материалов определяют рентгеноструктурным и голографическим методами.
Гранулометрический состав
– это характеристика распределения частиц порошка по размерам, которая показывает из частиц какого размера и в каких долях составлена данная партия порошка. Интервал размеров частиц называют фракцией.
Подробно о ситовом анализе порошков смотри в главе 1 (тема 1). В данной теме рассмотрен способ определения гранулометрического состава при наблюдении в микроскоп.
Методика микроскопического метода определения гранулометрического состава порошков определена ГОСТ 23402 и описана в лабораторной работе.
Свойства спечённых порошковых материалов, в том числе и твёрдых сплавов, зависят не только от их химического состава, но на эти свойства оказывают значительное влияние размеры зерна, гранулометрический состав спечённого сплава, находящиеся в структуре сплава поры и некоторые структурные составляющие, образующиеся в материале при спекании, такие как, например, h-фаза в твёрдых сплавах.
Поры действуют как надрезы и из-за неравномерного их распределения по структуре материала наблюдаются значительные колебания результатов испытаний.
Общая пористость Побщ
определяется как отношение плотности пористого тела r, измеренного, например гидростатическим взвешиванием на весах Моора, к теоретической плотности rтеор,
соответствующего компактного материала и выражается в процентах. Часто в качестве "теоретической" принимают плотность прокатанного или кованного металла.
Побщ
= (1 - r / rтеор
)´ 100
Для определения плотности порошковых деталей применяют гидростатическое взвешивание (весы Моора) или пикнометр.
В первом случае образец вначале взвешивают на воздухе, а затем - в жидкости, как это было описано выше. Если заведомо известно, что образец имеет большую открытую пористость, то его покрывают каким-либо водоотталкивающим веществом: например, при взвешивании в воде деталь пропитывают парафином.
Существуют и другие способы определения пористости - по электросопротивлению, по изменению магнитных свойств и тому подобные, но чаще всего применяют метод сравнения микрофотографии поверхности нетравленного полированного шлифа с образцовыми (эталонными) фотографиями, которые приведены в соответствующих стандартах. Например величина пористости твёрдых сплавов регламентирована ГОСТ 9391, этот же стандарт регламентирует размеры и расположение различных включений, ослабляющих прочность материала - величину и расположение графитовых включений, величину, характер и количество включений h-фазы.
Сравнительно малые размеры спечённых деталей и опасность их разрушения при испытаниях делают эти изделия непригодными для непосредственного измерения прочности и твёрдости. Поэтому вместе с изготовлением деталей, изготавливают образцы-свидетели определённой, строго регламентированной формы, из того же материала в одинаковых условиях прессования и спекания. Для увеличения достоверности измерений количество образцов-свидетелей выбирают не менее 11 (ГОСТ 20017) и более.
Исследование микроструктуры
.
Достоверную и полную информацию о состоянии материала спечённого изделия можно получить, изучая его микроструктуру.
Исследование микроструктуры позволяет определить количество, форму и распределение твёрдых фаз и полостей (пор), распределение связки и однородность структуры - все эти параметры оказывают существенное влияние на служебные характеристики материала: прочность, твёрдость, сопротивление изнашиванию, коэрцитивную силу, электросопротивление, проницаемость (важно для фильтров) и тому подобное.
Изучая микроструктуру сплава, можно с высокой степенью достоверности оценить такие характеристики твёрдого сплава, как твёрдость, предел прочности при поперечном изгибе и что особенно важно - ползучесть при высоких температурах, модуль Юнга, ударную вязкость и сопротивление изнашиванию, которые невозможно измерять у твёрдых сплавов непосредственно, ввиду их низкой пластичности.
Прочность, твёрдость, плотность и другие макроскопические свойства материала непосредственно зависят от особенностей его микроструктуры.
Закономерности, связывающие микроструктуру материала с его физическими и механическими свойствами в макрообъёмах определяются в основном эмпирическим путем, поскольку не существует единой теории, связывающей все эти свойства математическими зависимостями, полученными из основных законов физики. Значительная часть этих эмпирических зависимостей имеет качественный или полуколичественный характер. Тем не менее, накопленных данных вполне достаточно, чтобы выразить эти соотношения в количественной форме и получить простой и легко воспроизводимый метод контроля качества продукции.
Практические выгоды, которые можно получить из знания соотношений между микроструктурой и физическими и механическими свойствами металла, в сочетании с быстрым развитием и широким распространением приборов для автоматизированного анализа изображений, позволяют получать достоверную информацию из металлографических наблюдений, т. е. применять количественное описание структур. Это направление исследований привело к развитию области науки о металлах, которая получила название количественная
металлография
.
Количественный подход ведет к более глубокому пониманию наблюдаемых явлений, их причин и следствий, особенно применительно к макроскопическому, т. е. наиболее важному для практики поведению металлов. Более того, количественный подход позволяет выявить ту оптимальную структуру, которая в наибольшей мере соответствует условиям службы материала. В конечном итоге это может привести, например, к созданию новых сплавов и композиционных материалов, имеющих заранее заданный комплекс свойств после соответствующей обработки.
Достоверность результатов количественной металлографии и, следовательно, ценность соотношений, выведенных на основании ее данных, базируется на:
- точном и однозначном определении параметров, используемых для описания микроструктуры;
- точности, объективности и максимально возможной скорости метода измерений;
- достоверной интерпретации полученных данных.
Параметр, характеризующий микроструктуру, в каждом конкретном случае должен быть выбран таким образом, чтобы являться функцией и микроструктуры и того механического свойства, с которым этот параметр соотносится. Сделать этот выбор целесообразным можно лишь при использовании эмпирического опыта и некоторых теоретических представлений физики твердого тела. Некоторые общие принципы можно сформулировать на базе накопленного опытного материала.
Например, один из главных параметров микроструктуры, контролирующих прочность металла, — это расстояние между двумя «барьерами» (границами зерен, дисперсными выделениями, полигональными субграницами); средняя длина свободного пробега дислокаций в матрице и связанная с этим прочность и ползучесть зависит от этого расстояния между различными барьерами в конкретном сплаве или композиции.
В то же время вязкость и способность к формоизменению зависят не только от среднего расстояния между барьерами, но также и от формы и распределения дисперсных частиц в матрице, природы (проницаемости) этих барьеров, равно как и от анизотропии микроструктуры.
На каждой стадии измерения микроструктурных параметров необходимо принимать многочисленные меры предосторожности, направленные на повышение точности и воспроизводимости результатов. В зависимости от выбранного метода расчета для получения достоверных результатов необходимо соблюдать следующие условия:
- образец должен достоверно характеризовать анализируемый материал - это условие касается как расположения образца (того, как он вырезан) в исследуемом материале, так и исследуемой области в каждом образце;
- контраст микроскопических изображений или микрофотографий должен быть достаточно высоким, а увеличение должно соответствовать размеру измеряемого параметра;
- счет необходимо проводить при оптимальных условиях наблюдения микрострукту- ры (увеличение, травление и т. д.);
- число наблюдений должно быть достаточно большим, чтобы можно было получить стати- стически значимые результаты с учетом необходимой точности.
Влияние пористости сказывается на том, что с её увеличением снижается прочность материала. При пористости более 7% предел прочности снижается ниже значений допускаемых ГОСТ-ом на твёрдые сплавы.
Аналогично влияют включения других фаз: графита и h-фазы (сложного карбида вольфрама и кобальта).
Влияние h-фазы неоднозначно - увеличение количества вкраплений этой фазы, особенно кружевной и цепочной формы, однозначно и сильно - до 25% - снижает прочность твёрдого сплава, но если частицы h-фазы распределены по сечению, то возрастает твёрдость и повышается сопротивление абразивному изнашиванию.
Поэтому задача технолога - найти ту "золотую середину", при которой количество и распределение частиц h-фазы оказывает положительное влияние на эксплуатационные свойства конкретного изделия. Это тем более важно, что полностью избавиться от h-фазы практически невозможно.
Интересно изучение влияние размеров карбидной фазы на служебные характеристики твёрдого сплава поскольку регулированием размеров зёрен карбида вольфрама в однокарбидных твёрдых сплавах и размером зёрен сложного титано-вольфрамового карбида в двухкарбидных сплавах можно сравнительно простыми мероприятиями технологического характера: изменением температуры спекания, длительности выдержки при спекании, условиями прессования и так далее, получать сплавы с различной твёрдостью, пределом прочности при поперечном изгибе, сопротивлением изнашиванию при резании (резцы и зубки) или трении (подшипники и уплотнения) и плотностью.
В таблице 8 показано влияние среднего размера зерна на некоторые параметры твёрдых сплавов ВК6 и ВК8
Таблица №8
Влияние среднего размера зерна на прочность, твёрдость и стойкость твёрдых сплавов
Марка сплава
|
Средний размер зёрен, мкм
|
Предел прочности при поперечном изгибе, МПа
|
Твёрдость, HRA
|
Стойкость, мин
|
ВК6
|
1,64
|
136
|
90,4
|
25
|
1,8
|
140
|
90,1
|
18
|
3,0
|
160
|
16
|
3,3
|
150
|
88,7
|
15
|
3,8
|
157
|
91,0
|
12
|
4,5
|
168
|
90,5
|
9
|
4,8
|
168
|
87,2
|
8
|
4,95
|
155
|
88,1
|
5,2
|
185
|
5,5
|
185
|
89,2
|
ВК8
|
1,64
|
164
|
90,3
|
28
|
3,3
|
181
|
18
|
4,95
|
193
|
86,0
|
8
|
На рисунках 107 и 108 показан характер изменений предела прочности при поперечном изгибе и размерной стойкости от количества мелких зёрен в структуре твёрдого сплава.
БРАКОВОЧНЫЕ ПРИЗНАКИ СТРУКТУРЫ
На основании опыта работы, накопленного за годы эксплуатации твёрдых сплавов в промышленности и проведенных исследований составлена таблица браковочных признаков структуры твердых сплавов (табл. 9). В ней указаны границы колебаний того или иного параметра структуры сплава, в которых пластинки имеют наиболее высокую прочность и износостойкость и вне которых качество пластинок понижается.
Таблица 9
Пределы содержания различных фаз в структуре твёрдых сплавов
Браковочные признаки структуры, приведенные в табл. 9, могут быть положены в основу оценки качества пластинок из твердых сплавов. В идеальном случае структура металлокерамических твердых сплавов должна быть свободной от пористости, графитных включений, обезуглероживания, карбидной неоднородности и кольцевых зерен сложного карбида титана. Заметно не снижая качество пластинок, эти дефекты могут присутствовать в пределах, ориентировочно указанных в табл.9.
ЛАБОРАТОРНАЯ РАБОТА № 29
6.1.
Ситовый анализ.
Классификация порошков по размеру частиц.
6.1.1. АППАРАТУРА И МАТЕРИАЛЫ
1. Сито вибрационное
2. Весы ................................…………………………………………………………….....
3. Шихта (порошок),г. ..................……………………………………………………………... 100
6.1.2. ПОРЯДОК ВЫПОЛНЕНИЯ РАБОТЫ
Выбранные сухие и чистые сита укладывают в возрастающем порядке одно над другим, поддон помещают под нижним ситом.
Взвешенную пробу высыпают на верхнее сито, закрывают крышкой и включают привод вибросита.
Время рассева - 15-20 минут.
По окончании рассева отдельные фракции высыпают из сит на глянцевую бумагу. Содержимое на сите стряхивают в одну сторону, а частицы порошка, застрявшие в ячейках осторожно мягкой кистью в следующее сито с меньшим размером ячеек.
Взвешивают каждую фракцию отдельно. Сумма масс всех фракций должна быть не менее 99% от массы пробы.
6.1.3. ТРЕБОВАНИЯ К ОТЧЕТУ
Отчет должен содержать краткое описание физических и технологических характеристик порошковых материалов, порядок выполнения работы и протокол испытаний.
Объем отчета 2-4 стр.
Отчет подписывается студентом.
6.1.4. ЛИТЕРАТУРА.
1. Кипарисов С.С., Либенсон Г.А. Порошковая металлургия. Учебник. М., Металлургия, 1980, с 184-188.
2. Порошки металлические. Метод ситового анализа. ГОСТ 18318-73.
6.1.4. КОНТРОЛЬНЫЕ ВОПРОСЫ.
1. Каковы преимущества и недостатки ситового анализа ?
2. Какие свойства порошков определяет гранулометрический состав порошка ?
3. Какие свойства спеченных изделий определяет гранулометрический состав порошка ?
6.1.5. ПРОТОКОЛ ИЗМЕРЕНИЙ.
Содержание отдельной фракции в процентах вычисляют с точностью до 0,1% по формуле
mn
X = ──´100; где
m
mn
- масса данной фракции, г
m - масса пробы, гт
Результаты анализа записывают в виде таблицы, причем содержание
фракций, составляющих менее 0,1%, записывают словами "следы".
Таблица измерений имеет вид, показанный на рисунке 109 (см. ниже)
Фракция частиц, мкм
|
Масса фракции, г
|
Содержание фракции, %
|
ЛАБОРАТОРНАЯ РАБОТА № 30
6.2.
Определение гранулометрического состава порошка под микроскопом.
6.2.1. АППАРАТУРА И МАТЕРИАЛЫ
1. Микроскоп с увеличением 100, 600 и 1400
. Окуляр-микрометр .....................………………………………………………………….....
3. Объект-микрометр ...........………………………………………………………….............
4. Стеклянная плитка
5. Стеклянная палочка
6. Стеклянная пипетка
7. Предметное стекло
8. Покровное стекло
9. Шпатель
10. Фильтровальная бумага
11. Глицерин
12. Шихта (порошок),г. ............…………………………………………………………........... 10
6.2.2. ПОРЯДОК ВЫПОЛНЕНИЯ РАБОТЫ
.Для испытаний отбирают пробу массой 5—7 г.
Пробу для испытаний массой 5—7 г тщательно перемешивают на стеклянной плитке, рассыпают полосой длиной 7—8 см и разделяют на 7 или 8 приблизительно равных частей. Четные части отбрасывают, а нечетные смешивают и повторно сокращают таким же образом. Повторяют до получения пробы массой 0,5—1 г. Затем переносят на кончике стеклянной палочки небольшое количество порошка на предметное стекло, добавляют 1—2 капли диспергирующей жидкости, распределяют равномерно смесь палочкой по стеклу, накладывают покровное стекло и надавливают на него осторожно во избежание выхода больших частиц за пределы стекла. Избыток жидкости удаляют фильтровальной бумагой. Из пробы для испытаний готовят два препарата и сравнивают их под микроскопом. Если они совпадают, то измерение про водят на одном из них. Считают, что приготовленные микроскопические препараты совпадают, если в поле зрения, ограниченном полем основного прямоугольника или круга, находится от 6 до 30 частиц при измерениях при непосредственном визуальном наблюдении микроскопического изображения При этом расстояние между частицами должно быть не меньше размера большей из соседствующих между собой частиц. При несоблюдении этих условий приготовление микроскопического препарата повторяют.
Измерения можно проводить по снимкам микроскопических изображений.
Увеличение микроскопа следует подбирать в зависимости от размеров измеряемых частиц, при этом оно не должно превышать 1000-кратную величину апертуры объектива. Применяемый при измерении конденсор должен иметь апертуру не меньшую, чем объектив, с которым он применяется. Для измерения частиц 1 мкм требуется увеличение 1400.
6.2.3. ПРОВЕДЕНИЕ ИСПЫТАНИЙ
Измерение размеров частиц проводят при непосредственном наблюдении микро-скопического изображения или по микроскопическим снимкам.
Интервал размеров частиц разбивают не менее чем 6 частей (классов). Частицы, размер которых соответствует нижнему пределу класса, относят к классу более мелкому.
Размеры частиц измеряют при наблюдении отдельных полей зрения. Отдельные поля зрения выбирают на препарате, перемещая его на величину, большую диагонали прямоугольника или диаметра круга, ограничивающего поле зрения. Площадь, на которой проводят измерения и счет частиц, равна при наблюдении отдельных полей зрения — сумме их площадей.
Если порошок содержит частицы в большом интервале размеров и это из-за недостаточной глубины резкости объектива микроскопа не позволяет получать резкое изображение одновременно всех частиц, то малые и большие частицы наблюдают и измеряют при разных увеличениях. При малом увеличении учитывают только большие частицы, пpи большом увеличении — только малые частицы.
Результаты измерений при разных увеличениях соответственно пересчитывают в соответствии с п. 3.8. Все измерения проводят при трех увеличениях или менее.
Допускается, чтобы в поле зрения находилось не более 150 частиц. Расстояние между частицами должно быть не меньше размера большей из соседствующих между собой частиц.
Измерения частиц проводят в поле зрения, ограниченном прямоугольником или кругом с нанесенным диаметром.
Частицу считают принадлежащей к рассматриваемому полю, если она находится на одной из половинок границ поля. Например, в случае прямоугольника учитывают частицы, находящиеся внутри его, на левой вертикальной и верхней горизонтальной сторонах, на пересечении этих сторон и на другом конце одной из них. Частицы, находящиеся на остальных сторонах и в углах, не учитывают. В случае круга учитывают все частицы, находящиеся внутри его, а также все частицы, находящиеся на одной полуокружности и на одном конце проведенного диаметра как это показано на рисунке 109 Рис.109. Выбор поля зрения при наблюдении в микроскопе.
Измерение частиц на отдельных полях зрения производят с помощью линейки на матовом стекле, на экране проектора или на микроскопических снимках. Линейку перед применением следует проградуировать с помощью объект-микрометра. Увеличение должно быть подобрано так, чтобы измеряемые изображения частиц имели размер не менее 1 мм. Измеряют максимальную хорду частиц в горизонтальном или вертикальном направлениях.
Количество измеренных частиц (при использовании одного увеличения) или расчетное количество измеренных частиц (при использовании двух или трех увеличений) должно быть не менее 625
Под расчетным количеством частиц понимают количество частиц, отнесенное к одному выбранному увеличению и рассчитанное по формуле
(использовано три увеличения)
где: N
рас
- расчетное количество частиц;
N
б
i
- количество частиц i-го класса, измеренных при большем увеличении;
N
ср
i
- количество частиц i-го класса, измеренных при среднем увеличении;
N
м
i
— количество частиц i-го класса, измеренных при малом увеличении;
F
б
- большое увеличение;
F
ср
- среднее увеличение;
F
м
- малое увеличение;
l
б
, l
ср
, l
м
— число классов, просмотренных при данном увеличении.
Число полей зрения, просмотренных при разных увеличениях, должно быть одинаковым. Если результатом испытаний должно быть объемное (массовое) распределение частиц по размерам, то класс самых крупных частиц, составляющих не менее 5%, принимают за контрольный.
Количество измеренных частиц контрольного класса должно быть таким, как указано в таблице 10. (см. ниже)
Содержание контрольного класса, %
|
Минимальное количество измеренных частиц
|
От 5 до 10
|
25
|
От 11 до 15
|
50
|
От 16 до 24
|
75
|
Свыше 25
|
100
|
Если после измерения 625 частиц число их в контрольном классе меньше, чем требуется по таблице, то следует на дополнительно выбранных полях зрения или на дополнительных площадях препарата провести дальнейшее измерение частиц с размерами только контрольного класса с тем, чтобы получить необходимое количество частиц.
6.2.4. ОБРАБОТКА РЕЗУЛЬТАТОВ
Количественное распределение частиц по размерам получают относя количество измеренных частиц i-тогo класса к общему количеству измеренных частиц.
Общее количество измеренных частиц при использовании одного увеличения равно сумме всех измеренных частиц.
Общее количество измеренных частиц при использовании двух или трех увеличений равно расчетному количеству частиц (п. 3.8). Каждое произведение количества измеренных частиц i-гo класса на поправочный коэффициент принимают за количество частиц i
-
гo класса.
Средний размер частиц класса равен среднеарифметическому значению верхнего и нижнего пределов класса.
Объемное (массовое) распределение частиц по размерам получают, возводя в третью степень средний размер частиц класса и умножая результат на количество частиц в этом классе, относя полученное произведение к сумме произведений для всех классов (см. табл. 1 приложения).
Объемная доля отдельного класса равна его массовой доле, если частицы порошка имеют одинаковую плотность.
При измерении крупных частиц на дополнительных полях зрения в соответствии с п. 3.9 результаты анализа пересчитывают. Для этого количество частиц мелких классов умножают на поправочный коэффициент, равный отношению числа полей зрения, на которых были измерены частицы контрольного класса, к числу полей, на которых были измерены частицы других классов (см. табл. 2—5 приложения).
Погрешность измерения возникает из-за конечного количества измеренных частиц. Приведенные в дальнейшем формулы для вычисления этой погрешности справедливы при условии статистически случайной ориентации частиц в препарате.
Погрешность измерения не должна превышать 2% как в случае определения количественного, так и объемного (массового) распределения частиц по размерам.
В случае количественного распределения частиц по размерам погрешность измерения SP
1
.
вычисляют по формуле
SP1
= w Р1
а в случае объемного распределения погрешность измерения (Sq
1
) вычисляют по формуле
q1
( 1 - ) Ö
Sq
1
= ¾-¾-¾-¾-¾-¾-¾-¾-
100Ö
где P1
— количественная доля частиц i-ro класса;
q1
— объемная (массовая) доля частиц i-ro класса, %;
n1
— количество измеренных частиц i-ro класса.
Погрешность измерения количественного распределения при подсчете 625 частиц всегда менее 2%.
В случае определения масс объемного (массового) распределения частиц по размерам следует для каждого класса величин частиц вычислить погрешность измерения по формуле, независимо от количества просчитанных частиц.
Результаты испытаний оформляют в виде протокола, который должен содержать следующие данные:
- наименование порошка;
- результаты испытаний с указанием, в каких процентах они выражены;
- указания, были ли в порошке частицы менее 1 мкм.
Пример расчёта гранулометрического состава шихты проведённый при трёх увеличениях микроскопа показан в таблице 11. Измерения производились по микрофотографиям.
По результатам расчёта сроится гистограмма гранулометрического состава или кривая распределения.
6.2.5. ТРЕБОВАНИЯ К ОТЧЕТУ
Отчет должен содержать краткое описание физических и технологических характеристик порошковых материалов, порядок выполнения работы и протокол испытаний.
Объем отчета 2-4 стр.
Отчет подписывается студентом.
6.2.6. ЛИТЕРАТУРА.
1. Кипарисов С.С., Либенсон Г.А. Порошковая металлургия. Учебник. М., Металлургия, 1980, с 188-189.
2. Порошки металлические. Микроскопический метод определения размеров частиц. ГОСТ 23402.
6.2.7. КОНТРОЛЬНЫЕ ВОПРОСЫ.
1. Каковы преимущества и недостатки микроскопического метода определения размеров частиц ?
2. Какие свойства порошков определяет гранулометрический состав порошка ?
3. Какие свойства спеченных изделий определяет гранулометрический состав порошка ?
Увели-чение
|
Класс измеряемых частиц
|
Количество частиц, измеренных на отдельных полях
|
Расчётное количество частиц на отдельных полях
|
Суммар-ное количес-тво частиц при данном увеличе-нии
|
Средний размер частиц класса,
мкм
|
Количест-венная доля частиц класса,
%
|
Суммар-ный
процент классов,
%
|
мкм
|
В делениях линейки,
мм
|
1400´
|
1,0-1,4
|
1,5-2,0
|
0,0,0
0,0,0
|
0
|
686
|
1,2
|
0
|
0
|
1.4-2.0
|
2,0-3,0
|
4,5,7
3,6,4
|
29( )2
=158
|
1,7
|
3,6
|
3,6
|
2,0-2,8
|
3,0-4,0
|
10,13,8
11,15,17
|
74( )2
=402
|
2,4
|
9,3
|
12,9
|
2,8-4,0
|
4,0-5,5
|
12,23,22
23,10,28
|
118( )2
=642
|
3,4
|
14,8
|
27,7
|
4,0-5,6
|
5,5-8,0
|
40,30,35
27,37,31
|
200( )2
=1088
|
4,8
|
25,1
|
52,8
|
5,6-8,0
|
8,0-11,5
|
28,30,18
22,31,15
|
144( )2
=783
|
6,8
|
18,1
|
70,9
|
8,0-11,3
|
11,5-16,0
|
16,18,26
19,25,17
|
121( )2
=658
|
9,65
|
15,2
|
86,1
|
600´
|
11,3-16,0
|
7,0-9,5
|
56,50,45
42,53,44
|
290
|
590
|
13,65
|
6,7
|
92,8
|
16,0-22,4
|
9,5-13,5
|
29,40,30
25,44,46
|
214
|
19,2
|
4,8
|
97,7
|
22,4-32,0
|
13,5-19,0
|
16,19,11
12,15,13
|
86
|
27,2
|
2,0
|
99,7
|
125´
|
32.0-45,0
|
4,0-5,5
|
27.25.20
21.30.31
|
154( )2
@ 7
|
186
|
38,5
|
0,2
|
99,9
|
45,0-63,0
|
5,5-8,0
|
4,6,7
5,7,3
|
32( )2
@ 2
|
54,0
|
0,1
|
100,0
|
Таблица 11
Пример расчёта гранулометрического состава шихты и оформления таблицы наблюдений
( измерения выполнены на фотоснимках, линейкой измерена максимальная хорда частиц
параллельная одной из сторон снимка)
ЛАБОРАТОРНАЯ РАБОТА № 31
6.3.
Наблюдение формы частиц.
6.3.1. АППАРАТУРА И МАТЕРИАЛЫ
1. Микроскоп ..............................………………………………………………………....
2. Окуляр-микрометр .........................…………………………………………………….
3. Стеклянная плитка
4. Стеклянная палочка
5. Стеклянная пипетка
6. Предметное стекло
7. Покровное стекло
8. Шпатель
9. Фильтровальная бумага
10. Глицерин
11. Шихта (порошок),г. ........................ 10
6.3.2. ПОРЯДОК ВЫПОЛНЕНИЯ РАБОТЫ
Из пробы порошка готовят препарат - монослой частиц на подложке, полученный диспергированием порошка в дисперсионной жидкости.
Для этого пробу порошка массой 2-7 г тщательно перемешивают шпателем на стеклянной плитке, рассыпают полосой длиной 80-100 мм и разделяют ее на 7 или 8 приблизительно равных частей. Четные части отбрасывают, а нечетные смешивают и повторно соокращают таким же образом.
Операцию повторяют до получения пробы массой 0,5-1 г. Затем переносят на кончике стеклянной палочки небольшое количество порошка на предметное стекло, добавляют 1-2 капли глицерина, равномерно распределяют смесь стеклянной палочкой по стеклу, накладывают покровное стекло и осторожно давят на него во избежание выхода больших частиц за пределы стекла. Избыток жидкости удаляют фильтровальной бумагой. Проверяют препарат. Препарат не должен содержать конгломератов и скоплений частиц. Распределение частиц должно быть равномерным по всему полю зрения. Количество частиц в поле зрения должно быть таким, чтобы по всей линейке шкалы окуляра находилось 10-20 зерен крупнее одного деления.
Если количество зерен превышает указанное количество, то следует приготовить новый препарат.
Объектом наблюдения являются проекции частиц, ограниченные кругом - только те из них, которые находятся внутри поля зрения.
Измеряют максимальный lmax
и минимальный размер частиц lmin
, а затем рассчитывают фактор формы равный отношению .
6.3.3. ТРЕБОВАНИЯ К ОТЧЕТУ
Отчет должен содержать краткое описание физических и технологических характеристик порошковых материалов, порядок выполнения работы и протокол испытаний.
Объем отчета 2-4 стр.
Отчет подписывается студентом.
6.3.4. ЛИТЕРАТУРА.
1. Кипарисов С.С., Либенсон Г.А. Порошковая металлургия. Учебник. М., Металлургия, 1980, с 182.
2. Порошки металлические. Метод определения формы частиц. ГОСТ 25849.
6.3.5. КОНТРОЛЬНЫЕ ВОПРОСЫ.
1. Каковы преимущества и недостатки микроскопического метода определения формы частиц ?
2. Какие свойства порошков определяет форма его частиц ?
3. Какие свойства спеченных изделий определяет исходная форма частиц порошка ?
6.3.6. ПРОТОКОЛ ИЗМЕРЕНИЙ.
Условное обозначение или марка порошка .....................
Результаты расчетов факторов формы
№ измерения
|
Размеры частиц, мкм
|
Фактор формы
|
lmax
|
lmin
|
Рис.110. Шапка таблицы наблюдений.
Словесное описание формы частиц составляют, пользуясь приложением.
ЛАБОРАТОРНАЯ РАБОТА № 32
6.4.
Наблюдение микроструктуры
твердых сплавов разных марок.
Группа сплавов ВК
. В структуре твердых сплавов группы ВК 80-90% занимают зерна карбида вольфрама - это характерные угловатые кристаллы, треугольной, квадратной и четырехугольной формы. Размеры зерен колеблются от 0,5 до 10 мкм, в отдельных специальных случаях - до 30 мкм в сплавах с увеличенным размером карбидных зерен.
При травлении щелочным раствором железосинеродистого калия (красная кровяная соль) зерна карбида вольфрама не окрашиваются и выглядят под микроскопом блестящими белыми частицами с голубоватым оттенком.
Типичные структуры твердых сплавов группы ВК с различным содержанием кобальта, величиной частиц и их формой показаны на рисунке 111.
Обычно зерна карбида вольфрама равномерно распределены по сечению материала. Однако встречается и карбидная неоднородность, при которой крупные зерна объединяются в скопления. Карбидная неоднородность ухудшает изнашиваемость твердых сплавов - вместо равномерного износа по всей контактирующей поверхности трущихся пар, наблюдается износ в виде вырыва блоков, что приводит к неравномерному и ускоренному изнашиванию. Этот вид искажения микроструктуры крайне нежелателен для прецизионного и особенно - мелкоразмерного инструмента.
Группа сплавов ТК.
Почти весь объем структуры титановольфрамкобальтовых твердых сплавов занимает карбидная фаза, которая у большинства марок состоит из зерен карбида вольфрама и сложного карбида титана. Содержание сложного карбида, зерна которого на снимках вы-
глядят более темными, зависит от марки сплава. В сплаве Т5К10, например, на долю сложного карбида титана приходится 15-20%, в сплавах Т15К6 и Т15К8 - 4-50% и в сплаве Т30К4 - 90-
Рис.111. Структура сплавов ВК. Слева направо: ВК8ВК, ВК8, ВК10М.
95% вссего объема структуры. Остальная часть карбидной фазы этих сплавов - зерна карбида вольфрама.
Типичные структуры твердых сплавов группы ТК показаны на рисунке 112.
Рис.112. Структура сплавов ТК. Карбидная фаза. Слева направо: Т5К10, Т15К6, Т30К4.
Группа сплавов ТН и КХН
. В безвольфрамовых и маловольфрамовых твердых сплавах этой группы используют карбид титана, карбид хрома, карбид ванадия, нитрид титана, карбонитрид титана, зерна которых в процессе спекания не претерпевают изменений ни по химическому составу, ни по величине или форме, поскольку процесс спекания маловольфрамовых и безвольфрамовых сплавов в корне отличается от спекания сплавов групп ВК и ТК.
При травлении зерна карбида титана окрашиваются в темный цвет, в то время как связка остается светлой. Рис.113. Структура сплавов ТН-20 (слева) и КХН (справа). Карбидная фаза.
|
|
6.4.1. АППАРАТУРА И МАТЕРИАЛЫ
1. Металлографический микроскоп (увеличение 1000-1400)……………….............. ММУ3
2. Травленый микрошлиф различных марок твёрдых сплавов групп ВК, ТК, ТТК и др.
6.4.2. ПОРЯДОК ВЫПОЛНЕНИЯ РАБОТЫ.
Студент получает подготовленный микрошлиф, устанавливает его на столик микроскопа и, наблюдая картинку через окуляр-микрометр, производит определение параметров структуры наблюдаемого образца. Микроструктура зарисовывается и описывается.
6.4.3. ТРЕБОВАНИЯ К ОТЧЕТУ
В отчете должны быть описаны виды структурных составляющих сплава и их значение при эксплуатации материала.
Отчет должен содержать зарисованную микроструктуру.
Отчет содержит 2-3 стр.
Отчет подписывается студентом.
6.4.4. ЛИТЕРАТУРА.
1. Сплавы твердые спеченные. Методы определения пористости и микроструктуры. ГОСТ 9391.
2. Методика структурного металлографического анализа твердых сплавов. М., Машгиз, 1962 г.
6.4.5. КОНТРОЛЬНЫЕ ВОПРОСЫ.
1. Что позволяет определить наблюдение микроструктуры ?
2. Опишите методику наблюдения микроструктуры.
3. Какие технологические параметры могут оказать влияние на микроструктуру изделия ?
ЛАБОРАТОРНАЯ РАБОТА № 33
6.5. Определение основных характеристик зёрен карбида вольфрама в спечённом твёрдом сплаве.
6.5.1. АППАРАТУРА И МАТЕРИАЛЫ
1. Металлографический микроскоп ....……………………………………………….........
2. Окуляр-микрометр ......………………………………………………………….................
3. Специальный образец (травленый микрошлиф)
6.5.2. ИССЛЕДОВАНИЕ МИКРОСТРУКТУРЫ
Металлографическое исследование спеченных материалов заключается в идентификации и определении количества, формы и распределения твердых фаз и полостей (пор). Наблюдению пористости посвящена работа 26.
Пространственное расположение фаз сказывается на порошковых материалах значительно сильнее, чем на большинстве литых. Наряду с чисто качественной оценкой структуры нужно определить количество, форму и распределение отдельных фаз.
Непосредственный подсчет, классификация и измерения геометрических элементов микроструктуры позволяют получить представление о пространственном строении материала.
Существует три способа анализа: точечный, линейный и планиметрический. В первом случае выборку проводят системой точек, во втором - случайной прямой, в третьем -случайной плоскостью.(рис. 114)
Рис.114. Методы количественного анализа структуры, заштрихованы сечения
исследуемых фаз. Т - узлы сети, l - секущие, L - измерительная линия,
Ph - пересечения секущей с границей фаз.
В таблице представлены характеристики структуры, которые можно определить названными тремя способами измерений.
Из данных таблицы видно, что наиболее универсальным и полным по числу доступных характеристик является линейный анализ.
Линейный анализ позволяет описать пространственное расположение элементов структуры при помощи различных параметров:
а) объемной доли определенного элемента, например объема фазы
S li
f = ───── ,
L
получаемой путем суммирования длин отрезков секущих, проходящих через зерна фазы 1i
, и длины L самой линии измерения (рис.114)
Таблица 12
Характеристика методов стереологического анализа структур
Метод анализа
|
Измеряемые величины
|
Фиксируемые пространственные параметры
|
Точечный
|
Число точек определяемой фазы, отнесенное к общему числу
точек в измеряемой системе
Npkt
.
|
Объемная доля f.
|
Линейный
|
Длины отрезков измерительной
линии, пересекающие фазу Li
,
Число секущих Ni
.
Число точек пересечения с границами зерен Zk
с границами фаз Zph
.
Число отрезков секущей в функции их длины.
|
Объемная доля f.
Удельная поверхность S.
То же, для границ зерен Sk
.
То же, для меж фазных границ Sk
. Степень контакта С.
Средний диаметр распределения зерен по величине.
|
Планиметрический
|
Площадь А определяемой фазы.
Число сечений измеряемой пло-
щади Na
.
Число плоских сечений как функция их среднего диаметра.
|
Объемная доля f.
Удельная поверхность S однозначно определяемой формы.
Средний диаметр этой же формы.
Распределение размеров зерен по вели-
чине однозначно определяемой формы.
|
б) удельной поверхности элемента структуры, которую рассчитывают по числу отрезков случайных секущих Ni
, проходящих через элемент структуры и их полной длины.
Ni
S = ────────
S li
Получив таким путем поверхность, отнесенную к единице объема соответствующего элемента структуры определяют дисперсность этой фазы.
Рис.115. Зерна сплава при наблюдении в окуляр-микрометре (схема).
в) В многофазных структурах можно определить поверхность раздела фаз, отнесенную к единице объема образца, поделив чиcло пересеченных измерительной линией границ раздела фаз ZPh
к длине этой линии:
2 Zph
Sph
= ───────
L
Аналогично определяют их удельную поверхность по числу Zk
, пересеченных границ зерен:
4 Zk
Sk
= ──────
L
Эту границу следует рассматривать как двойную поверхность , принадлежащую двум прилежащим зернам.
г) Измерение величин Zk
и ZPh
дает еще одну количественную информацию, имеющую значение для порошковых материалов - это степень контакта (смежность), характеризующую отношение поверхности границ зерен ко всей поверхности фазы S:
Sk
2 Zk
С = ─── = ────────
S 2Zk
+ ZPh
Эта величина - правильная дробь. У многофазных тел она определяет объемную долю данной фазы.
д) Механические свойства многофазных материалов могут быть определены по среднему межфазному расстоянию в матрице:
L - S Li
p = 2 ´ ───────
ZPh
Линейный анализ можно проводить с помощью линейки на микроснимке или, наблюдая микроструктуру непосредственно.(Рис.115) В настоящее время аналитические микроскопы оснащаются компьютерными системами анализа микроструктур, самостоятельно выполняющими необходимые расчеты параметров фаз.
6.5.3. ПОРЯДОК ВЫПОЛНЕНИЯ РАБОТЫ.
Студент получает подготовленный микрошлиф, устанавливает его на столик микроскопа и, наблюдая картинку через окуляр-микрометр, производит определение суммарной длины секущих и число пересечений линии в окуляр микрометре с зернами выделенной фазы. Зарисовывает микроструктуру и рассчитывает параметры сплава по приведенным выше формулам.
6.5.4. ТРЕБОВАНИЯ К ОТЧЕТУ
В отчете должен быть описан принцип линейного анализа микроструктуры. Отчет должен содержать зарисованную микроструктуру и таблицу наблюдений с рассчитанными параметрами структуры.
Отчет содержит 2-3 стр.
Отчет подписывается студентом.
6.5.5. ЛИТЕРАТУРА.
1. Сплавы твердые спеченные. Методы определения пористости и микроструктуры. ГОСТ 9391.
6.5.6. КОНТРОЛЬНЫЕ ВОПРОСЫ.
1. Что позволяет определить наблюдение микроструктуры ?
2. Опишите методику наблюдения микроструктуры.
3. Какие технологические параметры могут оказать влияние на
микроструктуру изделия ?
6.5.7. ПРОТОКОЛ ИЗМЕРЕНИЙ.
Таблица измерений показана на рисунке 116.(см. ниже)
№№
|
Ni
|
Zk
|
ZPh
|
f
|
S
|
SPh
|
Si
|
C
|
P
|
ЛАБОРАТОРНАЯ РАБОТА № 34
6.6.
Наблюдение основных структурных составляющих: пор, карбида вольфрама, связки,
h
-фазы.
Металлографическое исследование спеченных твердых сплавов заключается в идентификации и определении количества, формы и распределения твердых фаз и полостей (пор).
Пространственное расположение фаз оказывает сильное влияние на прочность, твердость и износостойкость твердых сплавов. Наряду с чисто качественной оценкой структуры нужно определить количество, форму и распределение отдельных фаз.
Металлографический анализ партий твердого сплава проводят для каждой из выпускаемых партий. В соответствии с ГОСТ 9391 предусмотрено определение следующих фаз и структурных составляющих:
- величина зерна a-фазы, то есть зерна карбида вольфрама,
- величина зерна сложного карбида титана, или TiCW-фазы,
- характер распределения связки, или - b-фазы,
- присутствие и характер распределения h-фазы - двойного карбида вольфрама и кобальта,
- включение свободного углерода (в виде графита),
- степень пористости, характер и величина пор.
КАРБИДНАЯ ФАЗА СТРУКТУРЫ ТВЕРДЫХ СПЛАВОВ
Группа сплавов ВК
. В структуре твердых сплавов группы ВК 80-90% занимают зерна карбида вольфрама - это характерные угловатые кристаллы, треугольной, квадратной и четырехугольной формы. Размеры зерен колеблются от 0,5 до 10 мкм, в отдельных специальных случаях - до 30 мкм в сплавах с увеличенным размером карбидных зерен.
При травлении щелочным раствором железосинеродистого калия (красная кровяная соль) зерна карбида вольфрама не окрашиваются и выглядят под микроскопом блестящими белыми частицами с голубоватым оттенком.
Типичные структуры твердых сплавов группы ВК с различным содержанием кобальта, величиной частиц и их формой показаны на рисунке 117 (ГОСТ 9391).
Рис.117. Сплав ВК8 с различной величиной зерна.
Обычно зерна карбида вольфрама равномерно распределены по сечению материала. Однако встречается и карбидная неоднородность, при которой крупные зерна объединяются в скопления (рис 118). Карбидная неоднородность ухудшает изнашиваемость твердых сплавов - вместо равномерного износа по всей контактирующей поверхности трущихся пар, наблюдается износ в виде вырыва блоков, что приводит к неравномерному и ускоренному изнашиванию. Этот вид искажения микроструктуры крайне нежелателен для прецизионного и особенно - мелкоразмерного инструмента.
Группа сплавов ТК.
Почти весь объем структуры титановольфрамкобальтовых твердых сплавов занимает карбидная фаза, которая у большинства марок состоит из зерен карбида вольфрама и сложного карбида титана. Содержание сложного карбида, зерна которого на снимках выглядят более темными, зависит от марки сплава. В сплаве Т5К10, например, на долю сложного
Рис.118.Структура сплавов ВК. Карбидная фаза. А - нормальное распределение, Б - скопление крупных частиц. 1000х
|
|
А Б
карбида титана приходится 15-20%, в сплавах Т15К6 и Т15К8 - 4-50% и в сплаве Т30К4 - 90-95% всего объема структуры. Остальная часть карбидной фазы этих сплавов - зерна карбида вольфрама.
Типичные структуры твердых сплавов группы ТК с различной величиной зерна карбидной фазы ТК ( g-фаза) показаны на рисунке 119 (ГОСТ 9391).
Рис.119. Структура сплавов ТК. Титановольфрамовая карбидная фаза с различной величиной зерна (сплав Т15К6). 1500Х.
Группа сплавов ТН
. В безвольфрамовых и маловольфрамовых твердых сплавах этой группы используют карбид титана, зерна которого в процессе спекания не претерпевают изменений ни по химическому составу, ни по величине или форме.
При травлении зерна карбида титана окрашиваются в темный цвет, в то время как связка остается светлой.
СЛОЖНЫЙ КАРБИД ТИТАНА
Сложный карбид титана является твердым раствором карбида вольфрама в карбиде титана.
Формирование зерна сложного карбида титана происходит при высокой температуре спекания. В начальный период спекания растворение карбида вольфрама происходит только в поверхностном слое частиц карбида титана и образуется двухфазное зерно, сердцевина которого - это первичный кристаллик карбида титана, окруженный оболочкой из твердого раствора карбида вольфрама в карбиде титана.
С увеличением продолжительности спекания толщина оболочки увеличивается и в конечном итоге кристалл карбида титана полностью исчезает. При полном насыщении зерна карбида
А Б
Рис.120. Структура сложного карбида. А - вольфрам-титановый, Б - титан-
молибден-рениевый. 1500х
титана карбидом вольфрама образуется однородное по химическому составу зерно сложного карбида титана - которое и является конечной целью процесса спекания сплавов ТК, так как режущие свойства пластинок из однородных зерен сложного карбида титана значительно выше, чем у пластинок, содержащих в своей структуре двухфазные зерна.
Зерна сложного карбида титана имеют округлую, приближающуюся к сферической, форму и обособлены друг от друга.
При травлении зерно сложного карбида титана окрашивается в светлокоричневый цвет, а если получены двухфазные зерна, то центр зерна получается светлым.
ЦЕМЕНТИРУЮЩАЯ СВЯЗКА
В качестве материала связки в твердых сплавах использую кобальт, никель, железо и различные сплавы и композиции на основе никеля, железа, меди и т.п.
При травлении шлифа "на связку", она выступает в виде тонких прожилок и точек вокруг зерен основы: в сплавах ВК, ТК, ТТК - темного цвета, в сплавах ТН, КНТ, КХН - темного.
Дефект структуры цементирующей связки - неравномерность распределения по сечению. Наилучшим является равномерное распределение связки в виде тонких прожилок, окружающих зерна основы, толщиной не более 1 мкм.
Наиболее частые случаи распределения связки показаны на рисунке 121.
ГРАФИТНЫЕ ВКЛЮЧЕНИЯ
Твердосплавные пластинки спекаются в науглероживающих условиях: углерод присутствует в атмосфере печи, в засыпке, при разложении пластификатора. При спекании с избыточным содержанием углерода в сплаве появляется свободный углерод в виде графита.
Рис.121.Характер распределения связки.
А - равномерное, Б - включение кобальта. 1000х (ГОСТ 9391)
|
|
А Б
Включения графита выявляются на нетравленных шлифах в виде черных чешуек, распределенных либо равномерно по всему сечению шлифа, либо в виде отдельных групп.
Оптимальным является равномерное распределение, наихудшим - скопление включений графита вытянутых по сечению шлифа, как это показано на рисунке 122.
Графитовые включения, при заметном их количестве, существенно снижают механическую прочность изделий.
Рис.122. Графитовые включения. А - 0,2%, Б - 2,7%, В - 3,5%.
ОБЕЗУГЛЕРОЖИВАНИЕ ИЛИ ОБРАЗОВАНИЕ h-ФАЗЫ
При спекании с недостаточным содержанием углерода происходит обезуглероживание, которое выражается в образовании двойного карбида вольфрама и кобальта, содержание углерода в котором почти в два раза меньше, чем в монокарбиде вольфрама.
Однозначного мнения о влиянии тэта-фазы на эксплуатационные свойства твердых сплавов нет, но в зависимости от формы и распределения тета-фазы существенно меняются прочность и твердость сплава.
Стандартом различают форму включений тета-фазы: в виде "озерков", "кружев", мелких включений и распределение их: по переферии, в центре, по всей площади, в виде отдельных скоплений (см. рис.123.). После травления на тета-фазу участки, содержащие тета-фазу, имеют коричнево-красноватый оттенок.
Рис.123. Обезуглероженные участки и формы h-фазы. А - озерковая, Б - кружевная.
|
|
А Б
ПОРИСТОСТЬ
Все твердые сплавы имеют пористость. Равномерная пористость, если поры не превышают размеров мелких зёрен сплава не влияет на свойства изделий, повышенная - снижает ее.
Стандартом предусмотрена система оценки пористости в баллах, по которой величина пористости разделяется на две основные группы: до 50 мкм, свыше 50 мкм. (Приложение 2)
Дополнительно оценивается количество пор и их распределение по площади шлифа.
Пористость наблюдают на нетравленных шлифах и ее трудно отличить от графитовых включений. Поскольку влияние включений и пористости на прочность материала одинаков, стандартом разрешено определять суммарное количество этих видов дефектов, изменяющих свойства пластинок в одном направлении. Рис.124. Пористость твердых сплавов. А - 0,2%, Б - 2,5%.
|
|
6.6.1. АППАРАТУРА И МАТЕРИАЛЫ
1. Металлографический микроскоп ........……………………………………………....
2. Окуляр-микрометр ..............……………………………………………………..........
3. Специальный образец (травленый микрошлиф)
6.6.2. ПОРЯДОК ВЫПОЛНЕНИЯ РАБОТЫ.
Студент получает подготовленный микрошлиф, устанавливает его на столик микроскопа и, наблюдая картинку через окуляр-микрометр, производит определение параметров структуры наблюдаемого образца. Микроструктура зарисовывается и описывается.
6.6.3. ТРЕБОВАНИЯ К ОТЧЕТУ
В отчете должны быть описаны виды структурных составляющих сплава и их значение при эксплуатации материала.
Отчет должен содержать зарисованную микроструктуру.
Отчет содержит 2-3 стр.
Отчет подписывается студентом.
6.6.4. ЛИТЕРАТУРА.
1. Сплавы твердые спеченные. Методы определения пористости и микроструктуры. ГОСТ 9391.
2. Методика структурного металлографического анализа твердых сплавов. М., Машгиз, 1962 г.
6.6.5. КОНТРОЛЬНЫЕ ВОПРОСЫ.
1. Что позволяет определить наблюдение микроструктуры ?
2. Опишите методику наблюдения микроструктуры.
3. Какие технологические параметры могут оказать влияние на микроструктуру изделия ?
ЛАБОРАТОРНАЯ РАБОТА № 35
6.7.
Определение параметров и вида
h
-фазы под микроскопом.
При спекании с недостаточным содержанием углерода происходит обезуглероживание, которое выражается в образовании двойного карбида вольфрама и кобальта, содержание углерода в котором почти в два раза меньше, чем в монокарбиде вольфрама.
Однозначного мнения о влиянии h
-фазы на эксплуатационные свойства твердых сплавов нет, но в зависимости от формы и распределения h
-фазы существенно меняются прочность и твердость сплава.
Стандартом различают форму включений h
-фазы: в виде "озерков", "кружев", мелких включений и распределение их: по переферии, в центре, по всей площади, в виде отдельных скоплений (см. рис.125.).
Рис.125. Обезуглероженные участки и формы h-фазы. А - озерковая, Б - кружевная.
(ГОСТ 9391)
|
|
А Б
6.7.1. АППАРАТУРА И МАТЕРИАЛЫ
1. Металлографический микроскоп ………………………………………………...........
2. Окуляр-микрометр .....………………………………………………………..................
3. Специальный образец (травленый микрошлиф)
6.7.2. ПОРЯДОК ВЫПОЛНЕНИЯ РАБОТЫ.
Студент получает подготовленный микрошлиф, устанавливает его на столик микроскопа и, наблюдая картинку через окуляр-микрометр, производит определение параметров тэта-фазы. Форма тэта-фазы зарисовывается и описывается.
6.7.3. ТРЕБОВАНИЯ К ОТЧЕТУ
В отчете должны быть описаны вид и форма тэта-фазы и её значение при эксплуатации материала.
Отчет должен содержать зарисованную микроструктуру.
Отчет содержит 2-3 стр.
Отчет подписывается студентом.
6.7.4. ЛИТЕРАТУРА.
1. Сплавы твердые спеченные. Методы определения пористости и микроструктуры. ГОСТ 9391.
2. Методика структурного металлографического анализа твердых сплавов. М., Машгиз, 1962 г.
6.7.5. КОНТРОЛЬНЫЕ ВОПРОСЫ.
1. Что позволяет определить наблюдение микроструктуры ?
2. Опишите методику наблюдения микроструктуры.
3. Какие технологические параметры могут оказать влияние на микроструктуру изделия ?
ЛАБОРАТОРНАЯ РАБОТА №36
6.8. Определение пористости и графитовых включений спечёных образцов под микроскопом
.
ГРАФИТНЫЕ ВКЛЮЧЕНИЯ
Твердосплавные пластинки спекаются в науглероживающих условиях: углерод присутствует в атмосфере печи, в засыпке, при разложении пластификатора. При спекании с избыточным содержанием углерода в сплаве появляется свободный углерод в виде графита.
Включения графита выявляются на нетравленных шлифах в виде черных чешуек, распределенных либо равномерно по всему сечению шлифа, либо в виде отдельных групп и оцениваются путём сравнения с эталонными фотографиями, показанными в Приложении 3.
Оптимальным является равномерное распределение, наихудшим - скопление включений графита вытянутых по сечению шлифа, как это показано на рисунке 126-в.
Графитовые включения, при заметном их количестве, существенно снижают механическую прочность изделий. Рис.126. Графитовые включения. А - 0,2%, Б - 2,7%, В - 3,5%.
ПОРИСТОСТЬ
Все твердые сплавы имеют пористость. Небольшая пристость не влияет на свойства изделий, повышенная - снижает ее.
Стандартом предусмотрена система оценки пористости в баллах, по которой величина пористости разделяется на две основные группы:
- до 50 мкм,
- свыше 50 мкм.
Дополнительно оценивается количество пор и их распределение по площади шлифа, как это показано в Приложении 2 и 3.
Пористость наблюдают на нетравленных шлифах и ее трудно отличить от графитовых включений. Поскольку влияние включений графита и пористости на прочность материала одинаково, стандартом разрешено определять суммарное количество этих видов дефектов, изменяющих свойства пластинок в одном направлении.
Рис.127. Пористость твердых сплавов. А - 0,2%, Б - 2,5%.
|
|
|
6.8.1. АППАРАТУРА И МАТЕРИАЛЫ
1. Металлографический микроскоп ......………………………………………………......
2. Окуляр-микрометр ............………………………………………………………...........
3. Специальный образец (травленый микрошлиф)
6.8.2. ПОРЯДОК ВЫПОЛНЕНИЯ РАБОТЫ.
Студент получает подготовленный микрошлиф, устанавливает его на столик микроскопа и, наблюдая картинку через окуляр-микрометр, производит определение параметров графитовых включений и пористости в наблюдаемом образце. Микроструктура зарисовывается и описывается. По таблицам стандарта ГОСТ 9391 (Приложение 3 и 4) определяется балл структурной составляющей.
6.8.3. ТРЕБОВАНИЯ К ОТЧЕТУ
В отчете должны быть описаны виды графитовых включений и пористости и их балльность.
Отчет должен содержать зарисованную микроструктуру.
Отчет содержит 2-3 стр.
Отчет подписывается студентом.
6.8.4. ЛИТЕРАТУРА.
1. Сплавы твердые спеченные. Методы определения пористости и микроструктуры. ГОСТ 9391.
2. Методика структурного металлографического анализа твердых сплавов. М., Машгиз, 1962 г.
6.8.5. КОНТРОЛЬНЫЕ ВОПРОСЫ.
1. Что позволяет определить наблюдение микроструктуры ?
2. Опишите методику наблюдения микроструктуры.
3. Какие технологические параметры могут оказать влияние на микроструктуру изделия ?
ЛАБОРАТОРНАЯ РАБОТА № 37
6.9.
Определение среднего размера зёрен карбида вольфрама под микроскопом.
В настоящее время существуют достаточно разработанные методы количественной оценки непосредственно элементов структуры.
Количественная размерная оценка структуры имеет ряд бесспорных преимуществ, из которых главное — возможность построения графиков зависимости служебных свойств изделий от их структуры, а также возможность эффективного использования лабораторных наблюдений для улучшения технологического процесса производства.
Наиболее точным из количественных методов оценки является планиметрический, по которому состав структуры сплава определяется путем измерения площадей, занимаемых структурными составляющими на общей площади шлифа. Однако этот метод слишком трудоемок и поэтому не может быть рекомендован для заводской практики исследования структуры.
В основу рассматриваемой здесь методики исследования структуры положен линейный метод количественного анализа, математически базирующийся на геометрическом принципе Кавальери, из которого следует, что отношение линейных отрезков двух геометрических фигур будет равно отношению их площадей и отношению их объемов в условиях параллельно секущих плоскостей:
= =
В применении к элементам структуры это означает, что можно ограничиться измерением относительной длины отрезков, приходящихся на долю отдельных структурных составляющих, и тем самым определить процентное содержание этих составляющих в объеме сплава.
Если пересечь видимую в микроскоп структуру (или ее фотографию) прямой линией, то контуры зерен отдельных фаз структуры рассекут ее на ряд отрезков. На каждую структурную фазу придется определенная (суммарная) длина линейных отрезков, пропорциональная содержанию фазы в объеме сплава. При работе с микроскопами в качестве секущей линии может быть использована линейка-окуляр микроскопа (подсчет производится вдоль обреза линейки).
Процентное содержание искомой фазы определяется отношением числа делений, отсекаемых этой фазой на линейке окуляр-микрометра, к числу делений всей линейки окуляра. Подсчет может проводиться также и в миллиметрах или микронах с учетом цены деления окуляр-микрометра.
Для того чтобы получить достоверные результаты, нельзя ограничиваться однократным измерением. Считают, что для практических целей достаточно надежные результаты дает измерение 200—250 частиц.
Это правило было проверено при определении процентного содержания крупных зерен карбида вольфрама в структуре сплава. Измерения проводились на различных количествах полей зрения (от 1 до 20) одного и того же шлифа.
Результаты последующего и предыдущего опытов сравнивались и на основании этого устанавливалась степень расхождения и ошибка в процентах:
Число замеренных полей
|
1
|
3
|
5
|
7
|
10
|
15
|
20
|
Погрешность (±)
|
-
|
3,1
|
2,3
|
2
|
1,5
|
1,48
|
1,46
|
Средний диаметр замеренных зерен составлял 5 мкм.
При измерении на пяти полях длина секущей была в 100, а при измерении на десяти полях в 200 раз больше среднего диаметра измеряемых зерен.
Техника линейного метода определения среднего размера зерна иллюстрируется приводимым ниже примером.
Пример. Определим средний размер зерен карбида вольфрама в структуре сплава группы ВК.
Линейка окуляр-микрометра накладывается на изображение структуры в поле зрения микроскопа. (Полученное изображение структуры схематически показано на рисунке фиг. 128. Зерна карбида вольфрама схематически изображены в виде многоугольников.) Секущая линия окулярмикрометра пересекает крупные и мелкие зерна структуры сплава. На всем протяжении неподвижной линейки замеряется величина каждого крупного зерна в делениях окуляра. В нашем примере на одно поле зрения приходятся зерна следующих размеров: 7, 7, 7, 10, 4, 5, 7, 2 делений окуляра. Затем поле зрения переносят на другие участки шлифа и вновь замеряют размеры зерен, каждый раз фиксируя результаты в протоколе записи первичных данных. Зерна карбида вольфрама замеряются по наибольшей грани при увеличении микроскопа не менее Х1000.
Фиг. 128. Зерна сплава при наблюдении в окуляр-микрометре (схема).
После измерения зерен на пяти или десяти полях шлифа подсчитывается общее число делений, пересекающих зёрна. Полученное значение делится на число измеренных зёрен.
6.9.1. АППАРАТУРА И МАТЕРИАЛЫ
1. Металлографический микроскоп ..... ........ ММУ3
2. Окуляр-микрометр ........ ................. ОМО
3. Специальный образец (травленый микрошлиф)
6.9.2. ПОРЯДОК ВЫПОЛНЕНИЯ РАБОТЫ.
Студент получает подготовленный микрошлиф, устанавливает его на столик микроскопа и, наблюдая картинку через окуляр-микрометр, производит определение параметров структуры наблюдаемого образца. Микроструктура зарисовывается и описывается. Определяется средний размер зерна.
Таблица наблюдений содержит результаты измерений и имеет вид, показанный на рисунке 129
№№
|
Количество зёрен в 1 мкм
|
Количество зёрен в 2 мкм
|
Количество зёрен в 3 мкм
|
Количество зёрен в 4 мкм
|
Количество зёрен в 5 мкм
|
Количество зёрен в 6 мкм
|
6.9.3. ТРЕБОВАНИЯ К ОТЧЕТУ
В отчете должны быть описаны виды структурных составляющих сплава и их значение при эксплуатации материала.
Отчет должен содержать зарисованную микроструктуру и таблицу наблюдений.
Отчет содержит 2-3 стр.
Отчет подписывается студентом.
6.9.4. ЛИТЕРАТУРА.
1. Сплавы твердые спеченные. Методы определения пористости и микроструктуры. ГОСТ 9391.
2. Методика структурного металлографического анализа твердых сплавов. М., Машгиз, 1962 г.
6.9.5. КОНТРОЛЬНЫЕ ВОПРОСЫ.
1. Что позволяет определить наблюдение микроструктуры ?
2. Опишите методику наблюдения микроструктуры.
3. Какие технологические параметры могут оказать влияние на микроструктуру изделия ?
Лабораторная работа № 38
6.10.
Определение гранулометрического состава спечённого изделия под микроскопом
В настоящее время существуют достаточно разработанные методы количественной оценки непосредственно элементов структуры.
Количественная размерная оценка структуры имеет ряд бесспорных преимуществ, из которых главное — возможность построения графиков зависимости служебных свойств изделий от их структуры, а также возможность эффективного использования лабораторных наблюдений для улучшения технологического процесса производства.
Наиболее точным из количественных методов оценки является планиметрический, по которому состав структуры сплава определяется путем измерения площадей, занимаемых структурными составляющими на общей площади шлифа. Однако этот метод слишком трудоемок и поэтому не может быть рекомендован для заводской практики исследования структуры.
В основу рассматриваемой здесь методики исследования структуры положен линейный метод количественного анализа, математически базирующийся на геометрическом принципе Кавальери, из которого следует, что отношение линейных отрезков двух геометрических фигур будет равно отношению их площадей и отношению их объемов в условиях параллельно секущих плоскостей:
= =
В применении к элементам структуры это означает, что можно ограничиться измерением относительной длины отрезков, приходящихся на долю отдельных структурных составляющих, и тем самым определить процентное содержание этих составляющих в объеме сплава.
Если пересечь видимую в микроскоп структуру (или ее фотографию) прямой линией, то контуры зерен отдельных фаз структуры рассекут ее на ряд отрезков. На каждую структурную фазу придется определенная (суммарная) длина линейных отрезков, пропорциональная содержанию фазы в объеме сплава. При работе с микроскопами в качестве секущей линии может быть использована линейка-окуляр микроскопа (подсчет производится вдоль обреза линейки).
Процентное содержание искомой фазы определяется отношением числа делений, отсекаемых этой фазой на линейке окуляр-микрометра, к числу делений всей линейки окуляра. Подсчет может проводиться также и в миллиметрах или микронах с учетом цены деления окуляр-микрометра.
Для того чтобы получить достоверные результаты, нельзя ограничиваться однократным измерением. Считают, что для практических целей достаточно надежные результаты дает измерение 200—250 частиц.
Это правило было проверено при определении процентного содержания крупных зерен карбида вольфрама в структуре сплава. Измерения проводились на различных количествах полей зрения (от 1 до 20) одного и того же шлифа.
Результаты последующего и предыдущего опытов сравнивались и на основании этого устанавливалась степень расхождения и ошибка в процентах:
Число замеренных полей
|
1
|
3
|
5
|
7
|
10
|
15
|
20
|
Погрешность (±)
|
-
|
3,1
|
2,3
|
2
|
1,5
|
1,48
|
1,46
|
Средний диаметр замеренных зерен составлял 5 мкм.
При измерении на пяти полях длина секущей была в 100, а при измерении на десяти полях в 200 раз больше среднего диаметра измеряемых зерен. Основные структурные характеристики следует замерять не менее, чем на десяти полях. Опытный металлограф может получить такие же результаты при измерении на пяти полях, производя замеры на участках структуры, наиболее типичных для данного шлифа.
Техника линейного метода анализа структуры иллюстрируется приводимым ниже примером.
Пример. Определим количество крупных зерен карбида вольфрама в структуре сплава группы ВК.
Линейка окуляр-микрометра накладывается на изображение структуры в поле зрения микроскопа. (Полученное изображение структуры схематически показано на рисунке фиг. 130. Зерна карбида вольфрама схематически изображены в виде многоугольников.) Секущая линия окулярмикрометра пересекает крупные и мелкие зерна структуры сплава. На всем протяжении неподвижной линейки замеряется величина каждого крупного зерна в делениях окуляра. В нашем примере на одно поле зрения приходятся зерна следующих размеров: 4, 10, 16, 5, 8, 10, 10 делений окуляра.
Затем поле зрения переносят на другие участки шлифа и вновь замеряют размеры зерен, каждый раз фиксируя результаты в протоколе записи первичных данных (табл. 3). Зерна карбида вольфрама замеряются по наибольшей грани при увеличении микроскопа не менее Х1000. Фиг. 130. Зерна сплава при наблюдении в окуляр-микрометре (схема).
После измерения зерен на пяти или десяти полях шлифа подсчитывается общее число делений, пересекающих зёрна выбранного класса. Шкала имеет 100 делений и, следовательно, общая длина секущей на пяти полях зрения равна 500 делениям. Из них на зерна определённых размеров приходится:
Ni
= Li
n
Принимая общую длину секущей за 100%, определяют процентное содержание зерен карбида вольфрама данного класса :
500 делений ....... 100%
Ni
делений ....... х%
Во взятом примере структурная характеристика выражена в виде процентного содержания мелких зерен, но, зная цену деления окуляра и размер каждого зерна в делениях, можно найти размер зерна в микронах и процентное содержание каждой группы зерен по фракциям.
С помощью линейного метода определяются и другие количественные характеристики структуры твердых сплавов: содержание фазы карбида вольфрама, количество зерен кольцевой формы в титановых твердых сплавах, степень пористости и карбидной неоднородности и содержание h-фазы.
6.10.1. АППАРАТУРА И МАТЕРИАЛЫ
1. Металлографический микроскоп .....……………………………………………....... ММУ3
2. Окуляр-микрометр ................……………………………………………………........ ОМО
3. Специальный образец (травленый микрошлиф)
6.10.2. ПОРЯДОК ВЫПОЛНЕНИЯ РАБОТЫ.
Студент получает подготовленный микрошлиф, устанавливает его на столик микроскопа и, наблюдая картинку через окуляр-микрометр, производит определение параметров структуры наблюдаемого образца. Микроструктура зарисовывается и описывается. Определяется средний размер зерна.
Таблица наблюдений содержит результаты измерений и имеет вид, показанный на рисунке 131
№№
|
Количество зёрен в 1 мкм
|
Количество зёрен в 2 мкм
|
Количество зёрен в 3 мкм
|
Количество зёрен в 4 мкм
|
Количество зёрен в 5 мкм
|
Количество зёрен в 6 мкм
|
Кривая распределения количества зёрен по фракциям.
Рис.132. Примерный вид кривой
распределения, полученной при
выполнении лабораторной ра-
боты.
6.10.3. ТРЕБОВАНИЯ К ОТЧЕТУ
В отчете должны быть описаны виды структурных составляющих сплава и их значение при эксплуатации материала.
Отчет должен содержать зарисованную микроструктуру и таблицу наблюдений.
Отчет содержит 2-3 стр.
Отчет подписывается студентом.
6.10.4. ЛИТЕРАТУРА.
1. Сплавы твердые спеченные. Методы определения пористости и микроструктуры. ГОСТ 9391.
2. Методика структурного металлографического анализа твердых сплавов. М., Машгиз, 1962 г.
6.10.5. КОНТРОЛЬНЫЕ ВОПРОСЫ.
1. Что позволяет определить наблюдение микроструктуры ?
2. Опишите методику наблюдения микроструктуры.
3. Какие технологические параметры могут оказать влияние на микроструктуру изделия ?
7. ОФОРМЛЕНИЕ ЛАБОРАТОРНЫХ РАБОТ
Лабораторные работы оформляются в соответствии с требованиями ГОСТ 2.104, ГОСТ 2.105, ГОСТ 2.106, ГОСТ 2.108 на оформление текстовых документов.
Для отчета по проведенным лабораторным работам используют листы писчей бумаги формата А4, сшитые (скрепленные) вместе в виде тетради (допускается применение скоросшивателей, скрепление спиралями и т.д.) с плотной обложкой из чертежной бумаги. На обложке выполняется титульная надпись по образцу. На второй странице помещают содержание отчета в виде перечня выполненных работ с указанием страниц.
Отчет по каждой лабораторной работе должен содержать краткое описание сути работы (теоретическая часть), порядок ее выполнения и таблицу наблюдений с необходимыми пояснениями, эскизами и графиками. В отчёте записываются ответы на контрольные вопросы по выполненной работе.
Департамент образования города Москва
ПОЛИТЕХНИЧЕСКИЙ КОЛЛЕДЖ №8
Отчет по лабораторной работе №__
учебного курса
ИНСТРУМЕНТАЛЬНЫЕ ТВЁРДЫЕ СПЛАВЫ
Студент ──────────────── ───────────────────
(Подпись) (Фамилия и инициалы)
Преподаватель──────────── ───────────────────
(Подпись) (Фамилия и инициалы)
МОСКВА 200 __ г.
|
Рис.133. Оформление титульного листа
Рис.134. Оформление текста и
размеры рамки.
Каждая лабораторная работа подписывается студентом отдельно.
Защита (сдача) лабораторных работ может производиться по мере их выполнения или всех вместе по выбору студента и по согласованию с преподавателем.
Оценка работы (зачет - незачет) проставляется в зависимости от качества оформления работы и от знания студентом сути выполненной работы, а также от качества изложения пройденного материала.
Автор, чл. Корр. РАМТН
канд.техн.наук Борисенко Н.И.
ПРИЛОЖЕНИЕ 1
Типовые формы частиц
Сферическая Округлая Угловатая
( lmax/lmin ( lmax/lmin lmax/lmin от 2,0 до 5,0
от 1,0 до 1,2) от 1,2 до 2,0) а) с наличием б) с наличием
криволинейных острых углов и
поверхностей плоских граней
Стержневая Игольчатая Пластинчатая или чешуйчатая
(lmax/lmin (lmax/lmin 7) сферической, 8) брызгооб-
от 5,0 до 25,0) свыше 25,0) разной или угловатой формы
Дендритная Частицы с внутренними пустотами
а) губчатая б) пористая с в) полая с нали-
со сквозными закры- чием единичных
тыми порами пустот с площадью
более 25% площади
проекции частицы
ПРИЛОЖЕНИЕ 2
Шкала оценки карбидной неоднородности (по Методике ВНИИИнструмента)
Структура сплава ВК8 (Х1000) Схема микроструктуры
ПРИЛОЖЕНИЕ 3
Шкала для оценки видимой пористости по ГОСТ 9391
ПРИЛОЖЕНИЕ 4
Шкала для оценки включений структурно-свободного углерода по ГОСТ 9391
|