Титульный лист
ФЕДЕРАЛЬНОЕ АГЕНСТВО ПО ОБРАЗОВАНИЮ
Государственное образовательное учреждение
Высшего профессионального образования
«Российский Государственный Университет Туризма и Сервиса»
Волгоградский филиал
Кафедра «Общетехнические дисциплины»
РАСЧЕТНО-ПОЯСНИТЕЛЬНАЯ ЗАПИСКА
Тема _____________________________________________________________________________
______________________________________________________________________________________________________________________________________________________________________________________________________________________________________________________
Руководитель (фамилия, имя, отчество) ______________________________________________
Разработал студент (фамилия, имя, отчество) _________________________________________
_________курса________группы
Волгоград 2010
ФЕДЕРАЛЬНОЕ АГЕНСТВО ПО ОБРАЗОВАНИЮ
Государственное образовательное учреждение
Высшего профессионального образования
«Российский Государственный Университет Туризма и Сервиса»
Волгоградский филиал
Кафедра «Общетехнические дисциплины»
Утверждаю
Зав. Кафедрой
________В.А. Рыгин
«___»_________200__г.
ЗАДАНИЕ
ПО КУРСОВОМУ ПРОЕКТИРОВАНИЮ
Студенту _________________________________________________________________________
(фамилия, имя, отчество)
Группы ________
Тема проекта______________________________________________________________________
______________________________________________________________________________________________________________________________________________________________________________________________________________________________________________________
Срок предъявления законченного проекта ______________________________________________
Исходные данные к проекту _________________________________________________________
____________________________________________________________________________________________________________________________________________________________________
Содержание расчетно-пояснительной записки __________________________________________
________________________________________________________________________________________________________________________________________________________________________________________________________________________________________________________________________________________________________________________________________
Перечень графического материала ____________________________________________________
________________________________________________________________________________________________________________________________________________________________________________________________________________________________________________________________________________________________________________________________________
Дата выдачи задания «____» _____________________ 20__г.
Руководитель проекта _______________________________ ____________________________
(подпись, дата) (инициалы, фамилия)
Содержание расчетно-пояснительной записки
Титульный лист и лист с заданием на курсовой проект………………………………………1
Оглавление по содержанию расчетно-пояснительной записки.………………………………2
Введение с обоснованием выбранной кинематической схемы привода……………………..3
1. Выбор электродвигателя, кинематический и силовой расчет привода…………………...4
2. Расчет клиноременной передачи……………………………………………………………..6
3. Выбор материалов зубчатых колес…………………………………………………………...8
4. Определение допускаемых напряжений при расчете зубчатых передач на контактную выносливость и усталость при изгибе………………………………………………………..9
5. Определение геометрических размеров зубчатых колес передачи с последующей
проверкой прочности зубьев по контактным напряжениям и напряжениям изгиба…….10
6. Предварительный расчет валов редуктора и эскизная компоновка передачи……………14
7. Расчет валов редуктора на статическую прочность с учетом нагрузки
от ременной передачи…………………………………………………………………………15
8. Определение действительного коэффициента запаса прочности
тихоходного вала………………………………………………………………………………17
9. Подбор и расчет подшипников качения на долговечность…………………………………22
10. Определение конструктивных размеров корпуса редуктора………………………………23
11. Проверочные расчеты шпоночных соединений……………………………………………..25
12. Выбор системы смазки, определение типа масла и его количества………………………..26
ВВЕДЕНИЕ
Соединение вала машины с валом электродвигателя напрямую возможно лишь в относительно редких случаях, когда частоты вращения этих валов совпадают, например, в приводах центробежных насосов, компрессоров, вентиляторов и т.п. Для валов, имеющих различные скорости вращения, или когда они расположены под углом друг к другу, необходим привод, т.е. промежуточный механизм, служащий для согласования угловых скоростей двигателя (источника энергии) и рабочей машины.
Для выбора оптимальной конструкции привода надо учитывать множество факторов: энергетическую характеристику двигателя, условия эксплуатации, закон изменения нагрузки во времени, срок службы, расположение и габариты привода, требование техники безопасности, стоимость различных устройств привода и их монтаж, эксплуатационные расходы (в том числе и КПД) и удобство обслуживания.
В механический привод могут входить следующие устройства: цепные, ременные, фрикционные, зубчатые и зубчато-винтовые (червячные) передачи, различные соединительные муфты. Механизм, состоящий из зубчатых или червячных передач, выполненный в виде отдельного агрегата и служащий для понижения угловой скорости, называется редуктором.
Тип редуктора определяется составом передач, порядком их размещения в направлении потока мощности, т.е. от быстроходного (входного) вала к тихоходному (выходному), и положением геометрических осей соединяемых валов в пространстве. Самым простым и наиболее распространенным редуктором является одноступенчатый с цилиндрическими зубчатыми колесами. Наряду с редуктором в состав привода часто включают ременную передачу клиновыми ремнями, при этом отпадает необходимость использования соединительной муфты. Именно такой привод предусмотрен настоящим техническим заданием.
1. Выбор электродвигателя, кинематический и силовой расчет привода.
Исходные данные технического задания на курсовой проект: мощность на выходном валу привода (редуктора) Р2
= 2,0 кВт, частота вращения этого вала
n
2
= 110 об/мин, передаточное число редуктора
u
= 2,0, тип колес - прямозубые, расчетный срок службы привода
Lh
= 20000 час, характер нагрузки: близкая к постоянной, передача – реверсивная.
1.1. Определение потребляемой мощности
Потребляемую мощность электродвигателя определяют по формуле (1.1)
кВт ,
где Р2
= 2,0 кВт – мощность на выходном валу редуктора, h
общ
– общий коэффициент полезного действия (КПД) привода, значение которого применительно к заданной конструктивной компоновке привода (см. рис. П.1.1) определяем по формуле (1.2)
 .
Рис.1.1
. Кинематическая схема привода:
а – электродвигатель; б – клиноременная
передача; в – редуктор цилиндрический
одноступенчатый; 0 – вал электродвигателя;
1 и 2 – ведущий и ведомый (выходной) валы
редуктора; z
1
и z
2
– числа зубьев колес
Рис.1.1
|
Здесь (см. табл.1.1) = 0,96 – КПД клиноременной передачи, h
пк
= 0,99 – КПД одной пары подшипников качения, = 0,975 – КПД зубчатой цилиндрической передачи, h
Г
» 1 – коэффициент, учитывающий потери при перемешивании масла.
Затем необходимо определить диапазон частот вращения вала электродвигателя. Поскольку в состав привода входят клиноременная и зубчатая передачи, то его общее передаточное число определяется как
.
Здесь и u
= 2,0 – передаточное отношение и передаточное число ременной и зубчатой передач соответственно; n
эл
и n
2
= 110 об/мин – частоты вращения вала электродвигателя и выходного вала редуктора.
В механических приводах рекомендуется (см. табл.1.1) принимать = 2…4; поэтому частота вращения вала выбираемого электродвигателя должна находиться в диапазоне
= 110∙2,0∙(2…4) = (440…880) об/мин.
1.2. Выбор электродвигателя
По каталогу (cм. табл. П.1) в соответствии с найденными значениями Рэл.тр
и выбираем электродвигатель асинхронный марки 4А112МА8УЗ мощностью Рэл
= 2,2 кВт (соблюдая условие ) с синхронной частотой вращения вала nc
= 750 об/мин, которая находится в требуемом диапазоне изменений . Данный электродвигатель характеризуется скольжением ротораS
= 6,0 %, имеет кратность пускового момента КП
= 1,8 (т.е. отношение величин пускового момента Тпуск
к номинальному Тном
) и диаметр вала d
эл
= 32 мм (см. табл. П.2); действительная частота вращения n
эл
вала электродвигателя при номинальной нагрузке будет
n
эл
=
n
с
(1 – s/100) =
750(1 – 6,0/100) = 705 об/мин.
1.3. Кинематический и силовой расчет привода
Общее передаточное число привода определим по формуле
u
общ
=n
эл
/
n
2 =
705/110 =6,41 ,
поэтому передаточное отношение ip
проектируемой ременной передачи будет
ip
=
u
общ
/
u
= 6,41/2,0 ≈ 3,2 .
Далее определяем значения частот вращения (об/мин) и угловых скоростей (рад/с или с-1
) валов привода, мощностей (Вт) и вращающих моментов (Нм) на валах (i
– номер вала), используя зависимости:
и 
при этом согласно кинематической схеме привода:
и , n
1
=
un
2
, и .
Данные, полученные расчетом для каждого вала передачи, сводим в табл. П. 1.1.
Таблица П.1.1
Значения кинематических и силовых параметров привода
№ вала |
Наименование вала
|
n
,
об/мин
|
 ,
рад/с
|
Р,
Вт
|
Т,
Нм

|
0 |
Ведущий вал ременной передачи |
705 |
73,8 |
2170 |
29,4 |
1 |
Быстроходный вал редуктора |
220 |
23 |
2062 |
89,7 |
2 |
Тихоходный вал редуктора |
110 |
11,5 |
2000 |
173,9 |
2. Расчет клиноременной передачи
1.Вращающий момент на ведущем валу То
= 29,4 Нм.
2. Расчет выполняем для клиновых ремней нормального сечения. Для передачи этого вращающего момента рекомендуется использовать (см. рис. П.1 и табл. П.4) клиновые ремни сечения типа А
, имеющего размеры:bp
= 11 мм,
h
= 8 мм и А1
= 81 мм2
.
3. Расчетный диаметр меньшего шкива
мм.
Принимаем по ряду Ra
20 (cм. табл. П.3) ближайшее к верхнему пределу стандартное значение D1
= 112 мм, которое больше минимально допустимого D1,
min
= 90 мм для выбранного сечения (см. табл. П.4).
4. Расчетный диаметр большего шкива.
Примем в предварительных расчетах значение коэффициента упругого скольжения ремня ε
= 0,015 (см. п. 2.3), тогда
D2
=
D1
ip
(1 – ε) = 112·3,2(1 – 0,015) ≈ 353 мм
В соответствии со стандартным рядом (см. табл.П.3) назначаем D2
=355 мм.
5. Фактическое передаточное отношение передачи

6. Оптимальное межосевое расстояние
мм,
что больше минимального значения, равного
мм.
7. Длина ремня
мм.,
где
мм ;
мм2
.,
Принимаем стандартную длину ремня Lp
= 1400 мм (см. табл. П.4).
8. Уточняем межосевое расстояние
мм
9.Угол обхвата ремнем малого шкива

что больше минимально допустимого .
10. Частота пробегов ремня
П = υ/
Lp
= 1,3/(1400·10-3
) = 0,9, где скорость ремня υ
= 0,5 ω1
D1
= 0,5·23·112·10-3
= 1,3м/с.
с-1
< [П] = 10 с-1
,
11. Исходное полезное напряжение
МПа,
где Ki
= 1,14 – 0,14 e2,43(1 –
ip)
≈ 1,14 при ip
= 3,22.
12.Допускаемое полезное напряжение
МПа,
где ;
Cp
= 1 – 0,1Kp
= 1 – 0,1×1 = 0,9 ,
где по условию задачи при кратковременной перегрузке в 100% (КП
= 2) принято Kp
= 1.
13. Окружная сила
Ft
= 2
T
о
/D1
= 2 ∙ 29,4∙103
/112 = 525 Н.
14. Необходимое число ремней
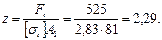
С учетом неравномерности распределения нагрузки между ремнями в многоручьевой передаче (см. форм. 2.31) принимаем Cz
= 0,95, тогда число ремней будет
z =
z΄
/
Cz
= 2,29/0,95 = 2,41.
Окончательно принимаем 3 ремня А-1400 Ш ГОСТ 1284.1 – 80.
15. Рабочий коэффициент тяги

где φТ,о
= 0,67 – исходное значение коэффициента тяги.
Силы, действующие в передаче:
натяжение от центробежных сил

где ρ
= 1,25 г/см3
– плотность материала ремня;
натяжение ветвей одного ремня


где согласно ф.(2.23) q
= ef
’
a1
= ;
предварительное натяжение одного ремня (с учетом центробежной силы)
F
о
= 0,5 (F1
+
F2
) + Fυ
= 0,5(379 + 116) + 0,2 = 248 H.
17. Сила, действующая на вал
Fp
≈ 2F
o
z
sin
(α1
/2) = 2 ∙ 248∙ 3 ∙ sin
(135 0
/2) ≈ 1400 H.
18. Далее, используя полученные данные и эмпирические зависимости рис. П.3, рассчитываем геометрические размеры шкивов, по которым делаем эскиз, а затем и рабочий чертеж одного из шкивов согласно технического задания (см. пример на рис.П.4).
3. Выбор материала зубчатых колес
Согласно положениям п.3.4.2 настоящего пособия применительно к редукторам, к которым не предъявляются специальные требования по ограничению массы, габаритных размеров, стоимости и пр., в качестве материала для прямозубых цилиндрических колес
, назначаем относительно недорогуе и широко распространенную сталь марки 45.
для колеса
– поковка из стали 45, улучшенная до твердости НВ2
= 200НВ
и имеющая при любых размерах заготовки σ
Т
= 340 МПа и σв
= 690 МПа;
для шестерни
– поковка из стали 45 диаметром до 90 мм, улучшенная до твердости НВ1
= 230НВ
и имеющая при этом σ
Т
= 440 МПа и σв
= 780 МПа.
При этом в соответствии с положениями п.3.4.1. необходимая для нормальной работы зубчатой пары разность в уровнях средней твердости материалов шестерни и колеса обеспечивается: НВ1
– НВ2
= 230НВ
– 200НВ
= 30НВ
> 20…50НВ
.
Если техническим заданием предусматривается расчет прямозубых цилиндрических колес
, то в качестве материала для них можно взять единую марку стали, например, сталь 45, при этом поковка для шестерни диаметром до 90 мм в состоянии улучшения будет иметь (см. табл. П.8) твердость НВ1
= 230НВ,
σ
Т
= 440 МПа и σв
= 780 МПа; прочностные свойства заготовки для колеса можно оставить прежними.
4. Определение допускаемых напряжений при расчете зубчатых передач на контактную выносливость и усталость при изгибе.
Допускаемые напряжения при расчете зубьев на контактную выносливость и усталость при изгибе определяются по формулам (3.1) и (3.3):
и ,
где и – базовые пределы контактной выносливости поверхностей зубьев и выносливости зубьев по излому от напряжений изгиба соответственно; и – коэффициенты долговечности и коэффициенты безопасности при расчете на контактную выносливость и усталость при изгибе соответственно; – коэффициент, учитывающий влияние двустороннего приложения нагрузки на зубья: для реверсивных передач = 0,7…0,8, а для нереверсивных – = 1.
Значения указанных параметров и коэффициентов находим отдельно для выбранных материалов шестерни (с индексом 1) и колеса (с индексом 2), для чего используем зависимости, приведенные в табл. П.9:

Поскольку проектируемая передача – реверсивная, с повышенным ресурсом эксплуатации (Lh
= 20000 час) и средняя твердость материала колес не превышает 350НВ,
принимаем:
, ,  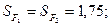 = 0,75.
Тогда:

Рассчитываемая зубчатая передача является прямозубой, поэтому в качестве расчетного допускаемого контактного напряжения принимаем

при этом условие соблюдается: 427 < 454 < 1,25∙427.
Результаты всех вычислений для прямозубых колес заносим табл.П.4.1.
Таблица П.4.1
Значения параметров, используемых при расчете допускаемых контактных напряжений и напряжений изгиба
Прямозубая цилиндрическая передача
№ п/п |
Наименование |
Материал и
термообработка
|
НВ
|
 |
 |

|

|
 |
 |
 |
МПа |
МПа |
1 |
Шестерня |
Ст.45, улучшен. |
230 |
530 |
414 |
1,1 |
1,75 |
482 |
177 |
427
|
2 |
Колесо |
Ст.45, улучшен. |
200 |
470 |
360 |
1,1 |
1,75 |
427 |
154 |
5.
Определение геометрических размеров зубчатых колес передачи с последующей проверкой прочности зубьев по контактным напряжениям и напряжениям изгиба.
Исходными данными для расчета зубчатой передачи являются: вращающий момент на тихоходном валу = 173,9 Нм, частота вращения этого вала = 110 об/мин, передаточное число u
= 2,0, тип колес – прямозубые
, расчетный срок службы привода = 20000 час, характер нагрузки (указывается режим нагружения, например: нагрузка близкая к постоянной); передача – реверсивная.
5.1. Определение межосевого расстояния и назначение модуля зацепления
Межосевое расстояние aw
(главный параметр) передачи определяем из условия обеспечения контактной прочности рабочих поверхностей зубьев, используя форм.(3.4)

в которой коэффициент принимают равным 49,5 при расчете прямозубых цилиндрических колес, если вращающий момент на выходном валу Т2
в Нмм; коэффициент ширины колеса относительно межосевого расстояния принимают по табл. П.6 согласно стандартного ряда линейных размеров; – коэффициент, учитывающий неравномерный характер распределения нагрузки по длине зубьев (см. п.3.4.3).
Для рассчитываемой прямозубой
передачи принимаем: Ка
= 49,5, Ψва
= 0,4, КН
b
= 1,05 и [σн
] = 427 МПа, следовательно,

В соответствии со стандартным рядом по СТ СЭВ 229-75 (см. табл. П.10) назначаем aw
= 140 мм.
При выборе модуля прямозубого зацепления необходимо предусмотреть, чтобы отношение 2aw
/
m
было целым числом, поскольку оно равно сумме зубьев шестерни и колеса; поэтому принимаем m
= 2,5 мм, что так же удовлетворяет условию (3.5).
5.2. Определение чисел зубьев колес
В прямозубом
цилиндрическом зацеплении b
= 0о
, поэтому вначале найдем суммарное число зубьев в передаче
, а затем и .
Принимаем , тогда , и фактическое передаточное число передачи составит: u
=
Z
2
/
Z
1
= 75/37 = 2,03, что менее чем на 1% отличается от требуемого техническим заданием (при нормативном – 4%).
5.3. Определение основных геометрических параметров зубчатых колес
Основные геометрические параметры цилиндрической зубчатой передачи показаны на рис. П.5.1. Ширину венца зубчатых колес, диаметры окружностей: делительной (d
), впадин (df
) и вершин (da
) зубьев определяем по формулам табл.5.2 и результаты расчета отдельно для шестерни и колеса заносим в табл. П.5.1
Рис. П.5.1. Основные геометрические параметры
цилиндрической зубчатой передачи
Таблица П.5.1
Основные расчетные параметры проектируемых цилиндрических зубчатых передач (при 0,4)
№
п/п
|
Название параметра
|
Расчетная
формула
|
Значения параметров (в мм) в зацеплении |
прямозубом |
шестерня |
колесо |
1 |
Число зубьев |
– |
37 |
75 |
2 |
Модуль зацепления |
m
(mn
) |
2,5 |
3 |
Угол наклона зубьев |
β
|
0о
|
4 |
Межосевое расстояние |
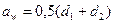 |
112
|
5 |
Ширина венца |
 |
50
|
45
|
6 |
Диаметр делительной окружности |
 |
92,5
|
187,5
|
7 |
Диаметр окружности впадин |
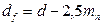 |
86,25 |
181,25 |
8 |
Диаметр окружности вершин |
 |
97,5 |
192,5 |
Примечание. Размеры ступицы колес рассчитаны ниже, и результаты расчета приведены в табл.П.7.1.
Силы в зацеплении колес
Составляющие нормальной силы Fn
, действующей в зацеплении зубчатых колес, определяем по формулам табл. 5.1 и результаты расчетов заносим в табл. П.5.2:
Таблица П.5.2
Значения сил в зацеплении колес (при a
w
=
a
= 20°)
№
п/п
|
Название
силы
|
Расчетная
формула
|
Значение силы (в Н) в зацеплении колес |
прямозубые |
1 |
Окружная |
 |
1855 |
2 |
Радиальная |
 |
675 |
3 |
Осевая |
 |
– |
5.4. Проверка зубьев колес на контактную выносливость
Расчет производится с целью исключения возможности выкрашивания рабочих поверхностей зубьев. При найденных выше значениях параметров зубчатой передачи определяем рабочее контактное напряжение и сравниваем его с расчетным допускаемым контактным напряжением ; при этом используем зависимость (3.8):
.
Для определения расчетных значений коэффициентов, входящих в эту формулу, вычисляем окружную скорость колес
υ =
0,5d
1
ω1
=
0,5∙92,5∙10-3
∙23 = 1,1 м/с,
по которой (см. табл. П.7) назначаем 9-ю степень точности их изготовления: = 9.
Коэффициент динамичности нагрузки : согласно табл. П.11 = 1,05 – для прямозубой передачи (при окружной скорости колес υ =
1,1 м/с);
коэффициент , учитывающий характер распределения нагрузки между зубьями в прямозубом зацеплении ,
Значение коэффициента было принято ранее: 1,05.
При фактическом значении передаточного числа передачи 2,03 расчетное контактное напряжение в прямозубой передаче
при её параметрах и найденных значениях расчетных коэффициентов:
< 427 МПа
.
Недогрузка этой передачи составляет 12% , что меньше нормативного показателя в 20% для прямозубых передач и поэтому допустима.
5.5. Проверка прочности зубьев колес на усталость при изгибе
Предотвращение усталостной поломки зубьев шестерни или колеса от напряжений изгиба гарантируется при соблюдении условия
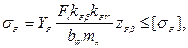
где – окружная сила; – ширина венца шестерни (или колеса); – коэффициент формы зуба, определяемый по табл. П.12 отдельно для шестерни и колеса в зависимости от числа зубьев (или эквивалентного числа зубьев ); коэффициент динамичности нагрузки, который находят по табл. П.11, а коэффициент определяют по формуле (3.11); – коэффициент повышения изгибной прочности зубьев косозубых передач по сравнению с прямозубыми: для прямозубых ,
для прямозубых колес – = 1,28.
При эквивалентных числах зубьев шестерни и колеса


коэффициенты формы зуба (см. табл. П.12): для прямозубых колёс (при и 75): 3,75 и 3,61. Тогда расчетные напряжения изгиба в основании зубьев колеса и шестерни составят соответственно:
–для прямозубой передачи
:
Условия прочности выполняются,
поэтому прочность зубьев на изгиб обеспечивается.
6. Предварительный расчет валов редуктора и эскизная компоновка передачи.
6.1. Предварительный расчет
Исходными данными для расчета валов на этом этапе являются вращающие моменты и , передаваемые валами.
Назначаем материалы валов из числа рекомендуемых: для тихоходного вала примем сталь 45 в состоянии нормализации (σ
Т
= 290 МПа и σв
= 570 МПа), при этом имеем в виду, что материал для вала-шестерни (быстроходный вал редуктора) был выбран ранее при расчете зубчатых передач. Хвостовики (концевые участки входных и выходных валов) выполняем цилиндрическими. Их диаметр d
х
определяем из расчета на кручение при пониженных допускаемых касательных напряжениях [t
] = 12…20 МПа по формуле, приведенной в табл. 7.1, с последующим округлением до стандартного значения. Эти и многие другие данные, полученные на этом этапе расчета применительно к выбранной ранее типовой схеме компоновки передачи в редукторе (см. рис. П.7.1), заносим в табл. П.7.1.
По найденным размерам (включая размеры зубчатых колес) делаем эскизную компоновку редуктора на миллиметровке (в масштабе 1:2), соблюдая порядок выполнения, описанный в п.6. За основу берем эскиз компоновки цилиндрической зубчатой передачи, приведенный на рис. 7.1: для облегчения дальнейшей работы над составлением рабочих чертежей отдельных деталей привода рядом с обозначением рассчитанных параметров проставляем в скобках их числовые значения. Затем строим расчетные схемы валов и приступаем ко 2-му этапу: расчету валов на статическую прочность.
6.2. Эскизная компоновка редуктора
Эскизная компоновка имеет своей целью конструктивно оформить зубчатые колеса, валы, корпус, подшипниковые узлы и крышки подшипников. Компоновочный чертеж выполняем на миллиметровой бумаге в масштабе 1:2 в одной проекции. За основу берем схему передачи, представленную на рис. П.7.1. Эскизную компоновку проектируемой передачи выполняем в следующей последовательности: проводим линию, соответствующую средней плоскости редуктора, и наносим осевые линии валов на расстоянии ; затем изображаем валы с соблюдением размеров, определенных в п. 7.1, при этом шестерню выполняем за одно целое с быстроходным валом (вал-шестерня); после чего вычерчиваем зубчатое колесо тихоходного вала по данным табл. П.3.2 и рис. П.3.1, показываем в разрезе подшипники качения (одну половину полностью, а для второй наносим лишь габариты).
Между торцами подшипников и внутренней полостью корпуса располагаем маслоудерживающие кольца (см. рис. П.5); их торцы должны выступать внутрь корпуса редуктора на 1÷2 мм, поэтому они будут играть одновременно и роль маслоотбрасывающих колец.
Вычерчиваем крышки подшипниковых узлов с уплотнительными прокладками толщиной ≈1 мм и болтами. В крышках прочерчиваем уплотнения манжетного типа для удержания жидкого масла.
Для фиксации зубчатого колеса в осевом направлении предусматриваем с одной стороны буртик, а с другой – устанавливаем распорную втулку.
7. Расчет валов редуктора на статическую прочность с учетом нагрузки от ременной передачи.
Данный этап расчета валов базируется на тех разделах курса сопротивления материалов, в которых рассматривается неоднородное напряженное состояние; при этом действительные условия работы вала заменяются условными, что приводит к созданию упрощенных расчетных схем. При переходе от реальной конструкции вала к расчетной схеме допускаем схематизацию нагрузок, опор и формы вала, вследствие чего этот расчет также будет приближенным. Расчетные нагрузки, в отличие от действительных, рассматриваем как сосредоточенные, при этом собственным весом валов и расположенных на них деталей пренебрегаем. Подшипниковые узлы заменяем шарнирно-неподвижной (А) и шарнирно-подвижной (В) опорами. Расчетные схемы быстроходного и тихоходного валов редуктора показаны на рис. П.7.2. Расчет валов приведен ниже.
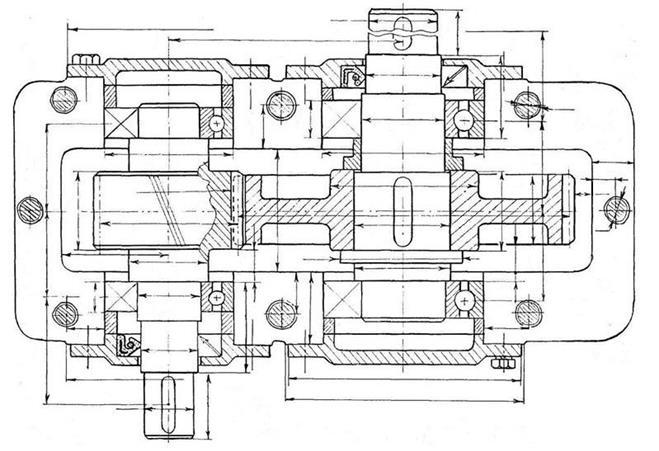
Рис. П.7.1. Типовая схема компоновки зубчатой цилиндрической передачи
в корпусе одноступенчатого редуктора
Таблица П.7.1
Линейные размеры деталей и узлов редуктора, определяемые на этапе
предварительного расчета и проектирования валов (к схеме на рис. П.7.1)
№
п/п
|
Наименование определяемых
параметров
|
Обозначение |
Расчетная зависимость
|
Значения пара-метров (в мм) |
Вал 1 |
Вал 2 |
1*
|
Диаметр хвостовика вала
(при [t
]1
= 17 МПа, [t
]2
= 20 МПа)
|
dX
|
 |
30
|
35
|
2*
|
Диаметр вала под подшипник |
 |
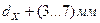 |
35 |
40 |
3
|
Типоразмер
выбранных подшипников
(№ серии, геометрические
размеры):
Динамическая грузоподъемность
Статическая грузоподъемность
|
D
п
B
п
r
|
По каталогу [2, с.459]
(см. также табл. П.3)
D
п
=
B
п
=
r
=
|
№ 207
72
17
2,0
|
№ 209
85
19
2,0
|
[Cr
] |
По каталогу (кН)
|
25,5 |
33,2 |
[C
о
] |
13,7 |
18,6 |
4*
|
Диаметр вала под уплотнение |
 |
 |
35 |
40 |
5 |
Диаметр свободного участка вала
(при df
,1
= 86,25 мм)
|
 |
 |
41 |
46 |
6
|
Длины участков вала:
– хвостовик
– опорная часть вала с уплотнением
|

|
» (1,2…1,5)dX
|
50
|
50
|
 |
» (1,4…1,6) |
49 |
56 |
7
|
Расчетные длины участков вала
(при 5 мм, 8 мм)
|
a
|
lo
+ 0,5( - B
п
) |
66 |
72 |
b= c
|
0,5(bw,1
+ B
п
) +D
+
d
|
» 47 |
» 47 |
8 |
Ширина внутренней части корпуса |
 |
»bw,1
+ 2D
|
61 |
9
|
Диаметр вала под зубчатым колесом |
 |
Назначается конструктивно при условии  |
–
|
46
|
10
|
Размеры ступицы зубчатогоколеса:
- диаметр
- длина
|
 |
 |
–
|
74 |
 |
 |
– |
50 |
11 |
Диаметр буртика |
 |
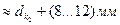 |
– |
56 |
Пункты требуют согласования расчетных значений со стандартным рядом нормальных линейных размеров.
8.
Определение действительного коэффициента запаса прочности тихоходного вала.
8.1. Быстроходный вал
Исходные данные
: ; нагрузка на вал от ременной передачи 
Силы в зацеплении: 
Длины участков вала (см. табл. 8.1): а
= 66 мм, в = с =
47 мм; диаметр делительной окружности шестерни 92,5 мм, поэтому 
1.Составляем расчетную схему (см. рис. П.8.1,а) и определяем реакции в опорах вала от сил, действующих в горизонтальной плоскости (условно):
а) : 

б) : 

Проверка: :  
2. Построение эпюры изгибающих моментов. Изгибающие моменты:
– под опорой А: 
– под шестерней (слева от плоскости действия момента )

– под шестерней (справа): 
По этим данным строим эпюру Ми
гор
(см. рис. П.8.1,г).
3.Определение реакций в опорах вала от сил, действующих в вертикальной плоскости.
Вследствие симметричного расположения шестерни относительно опор вала
,
а изгибающий момент под шестерней: .
Далее, строим эпюру изгибающих моментов Ми
вер
(см. рис. П.8.1,е).
4. Результирующие изгибающие моменты:
– под опорой А: 
– под шестерней: 
Поскольку диаметр вала под подшипником (см. табл. П.8.1) 35 мм меньше диаметра вала под шестерней
( 41 мм), проверим на статическую прочность оба сечения. Материал вала-шестерни – сталь 45 ( 440 МПа). Эквивалентные моменты в соответствующих сечениях вала (по четвертой теории прочности):
,
5. Расчет вала на статическую прочность. Условие прочности вала на изгиб
,
где , ,
2,0 (см. табл. П.1); поэтому
,
Условие статистической прочности выполняется. Теперь необходимо определить реакции в опорах вала, которые потребуются при расчете подшипников на долговечность:
, .
8.2. Тихоходный вал
Исходные данные
:

.
Длины участков валов (см. табл. П.4.1):
 
1. Составляем расчетную схему (см. рис. П.8.1,а) и определяем реакции в опорах вала от сил, действующих в горизонтальной плоскости:
а) : откуда находим

б) : откуда

Проверка : ; 0 – 337,5+ 337,5= 0.
2.Определение изгибающих моментов в различных сечениях вала.
Изгибающий момент под колесом:
слева от плоскости действия момента Ма2
:

а справа от неё – .
По этим данным строим эпюру Ми
гор
(см. рис. П.8.1,г).
3. Определяем реакции в опорах вала от сил, действующих в вертикальной плоскости.
Вследствие симметричного расположения шестерни относительно опор вала
,
а изгибающий момент в сечении под колесом:

Далее, строим эпюру изгибающих моментов Ми
вер
(см. рис. П.8.2,е).
4. Результирующий изгибающий момент в сечении вала под колесом:

Максимальный эквивалентный момент в этом сечении:
.
5. Расчет вала на статическую прочность.
Условие прочности вала на изгиб прежнее
,
однако здесь – осевой момент сопротивления сечения вала, ослабленного шпоночным пазом. Размеры призматической шпонкии шпоночного паза (см. табл. П.13) для мм: мм2
, мм. Материал вала – нор-мализованная сталь 45 с пределом текучести МПа (см. табл. П.8.1.). При КП
= 1,8 и
 
,
поэтому условие статической прочности вала выполняется.
6. Реакции в опорах вала: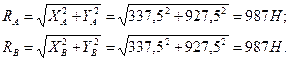
т.е. и для этого вала условие статистической прочности выполняется.
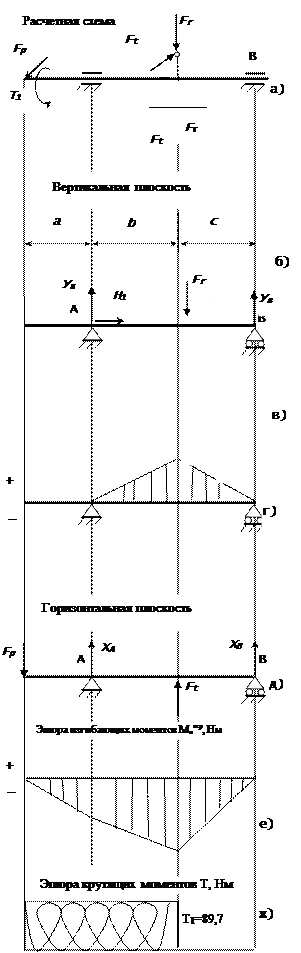 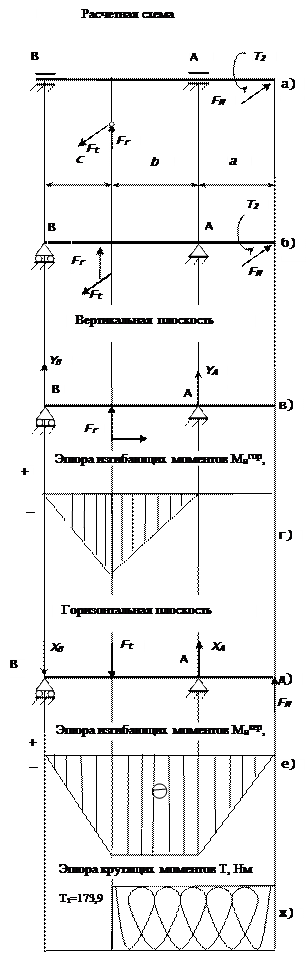
Рис.П.8.1. Схемы к расчету быстроходного (слева) и тихоходного (справа) валов
8.3. Расчет валов на выносливость
Расчет валов на выносливость выполняется как проверочный с целью определения действительного коэффициента запаса прочности этих валов. Расчет проводят по многим (условным) сечениям вала, однако опасным считается то, для которого коэффициент запаса прочности имеет наименьшее значение: оно может не совпадать с сечением вала, где действуют наибольшие крутящий или изгибающий моменты. Поэтому проверять необходимо несколько сечений и для каждого из них должно соблюдаться условие
,
где в качестве минимально допустимого значения принимают 1,7. Однако, с учетом повышенных требований к жесткости редукторных валов, рекомендуется принимать . Общий коэффициент запаса прочности определяется по формуле
,
где и – коэффициенты запаса прочности по нормальным и касательным напряжениям соответственно; их значения находят по зависимостям:
и ,
в которых и – пределы выносливости материала вала при симметричном цикле изменения напряжений изгиба и кручения: для валов из углеродистой стали 0,43 ,
а из легированной – , при этом ;
и – эффективные коэффициенты концентрации напряжений при изгибе и кручении: определяются по табл. П.14 и П.15 для валов с галтельными переходами и напрессованными деталями (например, подшипниками качения), а для концентраторов напряжений в виде шпоночного паза при σв
= 500…1000 МПа их значения принимают [3] равными: »1,5…2,0 и »1,4…2,1;
– масштабный фактор, зависящий от диаметра d
вала в опасном сечении; для валов из углеродистых и легированных сталей при кручении ( ) и легированных при изгибе ( ) его значение определяется по формуле (для d
³ 20 мм)
,
а при изгибе для углеродистых сталей его значение увеличивают на 0,11;
– коэффициент, учитывающий влияние шероховатости поверхности, который принимается равным: = 0,97…0,90 при параметре шероховатости Rа
= 0,32…2,5 мкм [3].
и - коэффициенты, корректирующие влияние постоянных составляющих циклов напряжений на сопротивление усталости:
и – для среднеуглеродистых сталей,
и – для легированных сталей;
и , и – амплитудные (индекс а
) и средние (индекс m
) значения циклов изменения нормальных и касательных напряжений в опасном сечении вала; они рассчитываются по следующим формулам (применительно к валам редукторов):
,
где и – осевой и полярный моменты сопротивления сечения вала соответственно:
для сплошного сечения вала диаметром : и , а для сечения вала, ослабленного шпоночным пазом шириной b
и глубиной t
1
(принимаются по табл. П.13):
 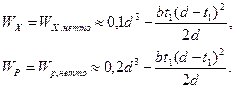
Значения изгибающего и крутящего Т
моментов в расчетном сечении вала определяют по эпюрам изгибающих и крутящих моментов (см. п. 8.1).
Согласно техническому заданию расчет на выносливость проводим для обоих валов. Результаты расчета по проведенным выше формулам для двух сечений и двух типов передач (по одному опасному сечению на вал) заносятся в табл. П.4.1. Там же указываем материал валов, диаметр вала в опасном сечении и тип концентратора напряжений: прессовая посадка колец подшипника (вал 1) и шпоночный паз (вал 2).
 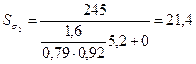
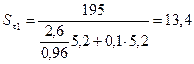 
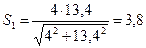 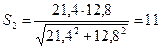
Таблица П.8.1
Результаты расчета валов прямозубой
передачи на выносливость
Вал
|
Тип концентратора напряжений |
Диаметр вала
, мм
|

|

|

|
 |

(кσ
/кd
)
|

(кτ
/кd
)
|

|

|

|
МПа |
- |
Быстроходный =92,4 Нм
Т =
89,7Нм
|
Сталь 45, улучшение; 780 МПа, 335 МПа, 195 МПа |
Прессовая
посадка
|
35 |
21,5 |
5,2 |
0,96 |
- |
(3,6) |
(2,6) |
4 |
13,4 |
3,8
|
Тихоходный
=43,6 Нм
Т=
173,9 Нм
|
Сталь 45, нормализация; 570 МПа, 245 МПа, 142 МПа |
Шпоночный паз |
46 |
5,2 |
4,8 |
0,92 |
0,79
0,72
|
1,6 |
1,5 |
21,4 |
12,8 |
11 |
Примечание. Осевые и полярные моменты сопротивлений сечений валов:
- для d
= 35 мм Wx
= 4288 мм3
и Wp
= 8575 мм3
;
- для d
= 46 мм Wx
= 8361 мм3
и Wp
= 18094 мм3
.
Усталостная прочность валов редуктора обеспечивается
9. Подбор и расчет подшипников качения на долговечность.
Предварительно выбранные в качестве опор валов шарикоподшипники (см. табл. 9.1) проверяем на долговечность по динамической грузоподъемности (Cr
) с учетом расчетного срока службы (Lh
) привода. Расчетная динамическая грузоподъемность Cr
связана с ресурсом работы шарикоподшипников (в млн. оборотов) зависимостью
,
где - эквивалентная нагрузка, рассчитываемая по формуле
.
В этом выражении (при вращении внутреннего кольца) ; - коэффициент безопасности для редукторов общего назначения; температурный коэффициент при температуре масла в редукторе 100о
С; и - осевая и радиальная (RA
или RB
) нагрузки на наиболее нагруженный подшипник, по соотношению которых и данным табл. П.9.1 определяют параметр осевого нагружения (е
), а затем и значения коэффициентов и .
Таблица П.9.1
Значения коэффициентов X
и Y
радиальных шарикоподшипников
 |
 |
 |
Параметр осевого нагружения е
|
X
|
Y
|
X
|
Y
|
0,014
0,028
0,056
0,084
0,11
0,17
0,28
0,42
0,56
|
1
|
0
|
0,56
|
2,30
1,99
1,71
1,55
1,45
1,31
1,15
1,04
1,00
|
0,19
0,22
0,26
0,28
0,30
0,34
0,38
0,42
0,44
|
Расчетная долговечность подшипников Lh
(
p
)
(в часах) связана с ресурсом их работы L
(в млн. оборотов) зависимостью
,
где - частота вращения вала с рассчитываемым подшипником. Работоспособность подшипниковых узлов будет обеспечена при условии:
Lh
(
p
)
Lh
.
Данные расчетов заносятся в табл..9.2. В прямозубой передаче .
Таблица П.9.2
Данные проверки подшипников для прямозубой
передачи (при Lh
=20∙103
ч.)
Параметры подшипника
|
Нагрузка |
 |
 |

|

|

|

|

|
 |
RA
|
RB
|
Н |
- |
Н |
час |
Подшипник № 207
25,5 кН
|
0
|
2246
|
1614
|
0
|
0
|
-
|
1
|
0
|
2098
|
1515152
|
Подшипник № 209
33,2 кН
|
0
|
987
|
987
|
0
|
0
|
-
|
1
|
0
|
1283
|
3030303
|
Примечание
: 220 об/мин, 110 об/мин, [C
о
]1
= 13,7 кН, [C
о
]2
= 18,6 кН.
10. Определение конструктивных размеров корпуса редуктора.
Корпус редуктора служит для размещения и координации взаиморасположения деталей передачи, защиты их от загрязнения, организации системы смазки, а также восприятия нагрузок, возникающих в зацеплении зубчатой пары. Для усиления жесткости предусматриваем ребра, располагая их у приливов под подшипниками.
Корпус выполняем разъемным, состоящим из основания (картера) и крышки. Материал корпуса – серый чугун СЧ15.
Общий вид одной из типовых конструкций корпуса с условными обозначениями размеров его основных элементов показан на рис. П.10.1. В табл. П.10.1 и П.10.2 приведены значения этих параметров, рассчитанные на основе практических рекомендаций.
Крышку и основание корпуса фиксируем относительно друг друга двумя коническими штифтами, которые устанавливаем без зазора до расточки гнезд под подшипники. Основание и крышку корпуса соединяют болтами М12 и М10. Из-за малого расстояния в корпусе между подшипниками валов вместо двух болтов М12 устанавливаем один. Для обеспечения герметичности расстояние между осями болтов М10 принимаем приблизительно 120…150 мм.
Для предотвращения протекания масла плоскости разъема смазывают спиртовым лаком или пастой «Герметик». Для захватывания редуктора при транспортировке и подъеме под фланцем основания располагаем приливы в виде крюков, а для снятия крышки предусматриваем крюки или петли на ней (аналогичные показанным на рис. П.9).
Для заливки масла и осмотра внутренней части редуктора в его крышке имеется смотровое окно, закрываемое другой крышкой с отдушиной (см. рис. П.10). Маслопропускное отверстие выполняется под пробку М16×1,5 (см. рис. П.7). Для контроля уровня масла применяем жезловый маслоуказатель, устанавливаемый в нижней части картера.
Для облегчения отделения крышки от основания корпуса при разборке на поясе крышки устанавливают два отжимных болта.
Рис. П.10.1
. Конструктивные размеры элементов корпуса редуктора
Расчет основных размеров элементов корпуса из чугуна Таблица П.10.1
Дополнительные размеры элементов корпуса Таблица П.10.2
11. Проверочные расчеты шпоночных соединений.
Для соединения валов с деталями, передающими вращение, применяем призматические шпонки (см. рис. П.8.1) из стали с временным сопротивлением , например, из стали 45. Размеры сечения призматической шпонки выбираем согласно ГОСТ 23360-78 по табл. П.13, исходя из диаметров валов в местах их установки; данные заносим в табл. 11.1. Длину шпонок назначаем из стандартного ряда так, чтобы она была несколько меньше длины ступицы присоединяемой детали ( на 5…10 мм).
Шпонки рассчитывают на срез по касательным напряжениям и смятие по нормальным напряжениям, однако проверку проводят только по напряжениям смятия, которые на гранях шпонки не должны превышать допускаемого, т.е. должно выполняться условие
,
, ,
где – вращающий момент (в Нмм) на валу диаметром d
(мм); = l
–
b
- рабочая длина шпонки, мм; = 100…120 МПа – допускаемые напряжения смятия.
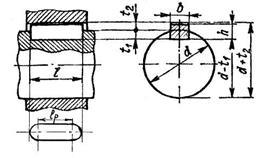
Рис.11.1.
Соединение призматической шпонкой
Таблица 11.1
Результаты проверки шпоночных соединений на прочность
Вал
|
Параметры
(место установки
шпонки)
|
d
|
b
|
h
|
t
1
|
t
2
|
l
|
lp
|
s
см
|
мм
|
МПа
|
Быстроходный |
Хвостовик
|
30 |
10 |
8 |
5,0 |
3,3 |
40 |
30 |
66 |
Тихоходный |
Хвостовик
|
35 |
10 |
8 |
5,0 |
3,3 |
40 |
30 |
110 |
Под колесом
|
46 |
14 |
9 |
5,5 |
3,8 |
40 |
26 |
83 |
В конструкции редуктора используются три шпоночных соединения, которые проверяем на прочность. Результаты расчета заносим в табл. П.11.1
Поскольку , то подбор шпонок успешно завершен. Если это условие не выполняется, то необходимо, либо увеличить длины шпонок, либо поставить две прежние.
12. Выбор системы смазки, определение типа масла и его количества.
Применим самый распространенный тип смазки зубчатых колес редукторов - картерное смазывание, которое осуществляется окунанием зубчатых колес в масло, заливаемое внутрь корпуса. Этот вид смазывания применяется при окружных скоростях зубчатых колес ≤ 12 м/с, т.к. при большей скорости масло сбрасывается с колес центробежной силой и увеличиваются потери на его перемешивание. Глубина погружения колеса в масло - не менее высоты зуба и не более трети радиуса колеса.
Основное назначение смазки – уменьшение потерь на трение, предотвращение чрезмерного износа и нагрева деталей. На практике сорт масла назначают в зависимости от контактного напряжения и окружной скорости колес. С увеличением контактного давления масло должно обладать повышенной кинематической вязкостью; с увеличением же скорости вязкость должна быть меньше. Поэтому вначале определяем кинематическую вязкость n50
требуемого масла при температуре 50°С, руководствуясь данными табл. 12.1 [3]: при s
Н
< 600 МПа и окружной скорости колес υ
< 1,1 м/с n50
= 35∙106
м2
/с.
Таблица.12.1 Таблица.12.2
Рекомендуемые значения Марки индустриального масла
вязкости n50
масла (при t
о
= 50°С)
Контактное
напряжение
s
Н
, МПа
|
Кинемат. вязкость n50
(10-6
×
м2
/с) при окружной скорости υ
, м/с |
£ 2 |
2…5 |
> 5 |
< 600 |
35 |
28 |
22 |
600…1000 |
60 |
50 |
40 |
1000…1200 |
70 |
60 |
50 |
Кинематическая вязкость n50
(10-6
×
м2
/с)
|
Марка
масла
|
17-23 |
И-20А |
24-27 |
И-25А |
28-33 |
И-30А |
35-45 |
И-40А |
47-55 |
И-50А |
57-63 |
И-60А |
65-75 |
И-70А |
По ее значению и данным другой табл.12.2 назначаем сорт индустриального масла:
И – 40А в объеме V
, определяемом по эмпирической зависимости [3, c. 251]:
V
≈ 0,5Р1
= 0,5∙2,06 ≈ 1,0 л,
где – потребляемая редуктором мощность, в кВт.
Формат |
Зона |
Поз. |
Обозначение
|
Наименование
|
Кол.
|
Примечание
|
Документация
|
А1 |
КП.ПМ.100100.012 СБ |
Сборочный чертеж |
1 |
Пояснительная записка |
1 |
Детали
|
А3 |
1 |
КП.ПМ.100101.012.001 |
Вал-шестерня |
1 |
Сталь 40Х |
2 |
КП.ПМ.100101.012.002 |
Кольцо уплотнительное |
1 |
Резина техн. |
3 |
КП.ПМ.100101.012.003 |
Крышка подшипника сквоз. |
1 |
Сч 15 |
4 |
КП.ПМ.100101.012.004 |
Подкладка регул.(комплект) |
2 |
Сталь 10 |
5 |
КП.ПМ.100101.012.006 |
Крышка подшипника глухая |
1 |
Сч 15 |
6 |
КП.ПМ.100101.012.007 |
Кольцо уплотнительное |
1 |
Резина техн. |
7 |
КП.ПМ.100101.012.010 |
Корпус редуктора |
1 |
Сч 15 |
8 |
КП.ПМ.100101.012.013 |
Крышка подшипника глухая |
1 |
Сч 15 |
9 |
КП.ПМ.100101.012.017 |
Крышка подшипника сквоз. |
1 |
Сч 15 |
А3 |
10 |
КП.ПМ.100101.012.023 |
Колесо зубчатое |
1 |
Сталь 45 |
А3 |
11 |
КП.ПМ.100101.012.024 |
Вал ведомый |
1 |
Сталь 45 |
12 |
КП.ПМ.100101.012.025 |
Прокладка регул. (комплект) |
2 |
Сталь 10 |
Курсовой проект по ПМ
|
Изм. |
Лист |
№ докум. |
Подпись |
Дата |
Разраб. |
Редуктор
Одноступенчатый
цилиндрический
|
Лит. |
Лист |
Листов |
Пров. |
Рыгин В.А. |
1 |
2 |
.
ВФ РГУТиС гр
|
Н.конт |
Утв. |
|
|
Формат |
Зона |
Поз. |
Обозначение
|
Наименование
|
Кол.
|
Примечание
|
Стандартные изделия
|
13 |
КП.ПМ.100101.012.101 |
Болт М10-20 ГОСТ 7808-70 |
8 |
14 |
КП.ПМ.100101.012.103 |
Болт М6-20 ГОСТ 7808-70 |
4 |
15 |
КП.ПМ.100101.012.016 |
Шпонка 10х8х40 |
ГОСТ 23360-78 |
1 |
Ст 45 |
16 |
КП.ПМ.100101.012.017 |
Шпонка 14х9х40 |
1 |
Ст 45 |
ГОСТ 23360-78 |
17 |
КП.ПМ.100101.012.018 |
Подшипник 209 |
2 |
ГОСТ8338-75 |
18 |
КП.ПМ.100101.012.019 |
Подшипник 207 |
2 |
ГОСТ8338-75 |
19 |
КП.ПМ.100101.012.020 |
Штифт 10х35 |
1 |
Ст 40 |
ГОСТ3129-70 |
Курсовой проект по ПМ
|
Лист |
Изм. |
Лист |
№ докум. |
Подпись |
Дата |
|