СОДЕРЖАНИЕ
СОДЕРЖАНИЕ. 4
Аннотация. 6
Введение. 7
1. Проектные решения цеха. 8
1.1 Классификация цеха по различным признакам. 8
1.2 Режим работы цеха. 8
1.3 Фонд времени. 9
1.4 Производственная программа. 10
1.5 Выбор и расчет оборудования. 16
1.5.1 Плавильное отделение. 16
1.5.Модельное,сборочное,подготовительное отделения. 23
1.5.3 Термическое отделение. 30
1.5.4 Очистное отделение. 30
1.6 Компоновка отделений цеха. 31
1.7 Характеристика и монтаж конструктивных элементов здания. 31
1.8 Бытовые помещения. 32
1.9 Вспомогательные отделения цеха. 33
1.10 Транспортная система цеха. 33
2. Разработка технологического процесса изготовления отливки «Кронштейн» в электрокорундовой форме. 35
2.1 Технология изготовления отливки. 35
2.1.1 Пресс-формы для изготовления моделей. 36
2.1.2. Приготовление огнеупорной суспензии. 37
2.1.3. Изготовление форм. 37
2.1.4. Вытопка модельного состава. 37
2.1.5.Прокаливание оболочковых форм. 38
2.1.6 Литье в керамические оболочки. 38
2.2 Краткое описание работы линии. 39
2.3 Комплектность линии. 41
3.Гидровлический расчет площади поперечного сечения питателя литниковой системы.. 45
4.Анализ вредных и опасных производственных факторов, 47
меры пожарной безопасности. 47
4.1.Санитарно-технологическая характеристика производства. 47
4.2.Комплексные мероприятия по обеспечению безопасных условий труда. 50
4.3.Меры по обеспечению пожарной безопасности. 53
4.4.Обеспечение проектируемого цеха санитарно – бытовыми, административными и вспомогательными помещениями и устройствами. 56
5. Определение технико-экономических показателей проектируемого цеха. 68
5.1 Ведомость технологического оборудования. 68
5.2 Расчет численности рабочих. 69
5.3 Основной капитал. 77
5.4 Расчет фондов заработной платы рабочих. 78
5.5 Расходы на содержание и эксплуатацию оборудования (РСЭО) 84
5.6 Калькуляция себестоимости продукции. 87
5.7 Финансовый план. 89
5.8 Экономические показатели цеха. 92
6. Технологический процесс изготовления художественной отливки. 93
6.1 Анализ технологичности отливки. 93
6.2 Технологический процесс изготовления отливки. 93
Список литературы.. 95
Аннотация
Разработанный проект предусматривает строительство цеха титанового литья по выплавляемым моделям мощностью 100 тонн отливок в год.
Номенклатура выпускаемых отливок разнообразна, возможен выпуск отливок с развесом до 5 кг.
В общей части дипломного проекта приведена номенклатура отливок цеха, составлена производственная программа, выполнены расчеты производственных отделений (плавильного, модельного, шихтового двора, отделения обсыпки).
В технологической части проекта разработан технологический процесс изготовления отливки "кронштейн" в электрокорундовых формах.
В специальной части проекта просчитан гидравлический расчет литниковой системы для нахождения площади поперечного сечения питателей в многоместной форме.
Графическая часть дипломного проекта включает:
- чертёж планировки проектируемого цеха;
- схему грузопотоков литейного цеха;
- продольный и поперечный разрезы цеха;
- чертёжи литейно-модельных указаний, литейной формы в сборе и сборочный чертёж пресс-формы.
В разделе "Техника безопасности и охрана труда" указаны мероприятия по улучшению условий труда в цехе, по противопожарной безопасности, и по обеспечению проектируемого цеха санитарно-бытовыми, административными и вспомогательными помещениями и устройствами.
В экономической части проекта сделан расчёт рабочей силы, фондов зарплаты, цеховых расходов, а так же расчёт средней себестоимости одной отливки.
Введение
Прогрессивные современные отрасли промышленности, такие как авиастроение, двигателестроение, производство химического и нефтехимического оборудования характеризуются все более интенсивным внедрением в сферу своего производства деталей из сплавов титана. В настоящее время работает немало цехов и участков фасонного литья, оснащенных совершенным оборудованием. Это привело к повышению качества отливок, возрастанию коэффициента использования металла до 0,3, расширению номенклатуры отливок. Важным резервом является внедрение экономичных заготовок, получаемых методами точного литья, коэффициент весовой точности при механической обработке в которых приближается к 0,7-0,9 вместо 0,1-0,3 при штамповке и ковке.
Существуют проблемы, которые требуют проведения дальнейших исследований с целью совершенствования производства титановых отливок, повышения их качества и снижения стоимости готовых деталей. Известно, что эффективность применения титановых деталей во многом определяется качеством их поверхности, характеристики которой зависят от интенсивности физико-химического, механического и теплового взаимодействия формирующейся отливки с литейной формой.
Технология получения фасонных титановых отливок в нашей стране развивалась в основном на базе авиа- и ракетостроения. Это привело к использованию при изготовлении форм таких материалов, как графит или электрокорунд. В настоящее время значительно возрастает спрос на литые фасонные изделия из титановых сплавов в различных отраслях промышленности (химическая, нефтеперерабатывающая и др.), однако их широкое внедрение тормозится дефицитностью и высокой стоимостью формовочных материалов и, вследствие этого, высокой себестоимостью титанового литья.
В настоящей работе была поставлена цель, разработать технологию изготовления комбинированных керамических форм из дешевых недефицитных материалов для получения качественных фасонных титановых отливок.
1. Проектные решения цеха
1.1 Классификация цеха по различным признакам
Первый признак:
по роду металла проектируемый цех относится к разряду жаропрочных сплавов на основе титана. Марки сплавов, выплавляемые в цехе, ограничиваются номенклатурой отливок: ВТ5Л, ВТ20Л.
Второй признак:
по мощности цех относится к производству малой мощности. Запроектированная производительность - 100 т. литья в год.
Третий признак:
по развесу – цех мелкого литья. В производственной программе цеха предусмотрен выпуск отливок с развесом до 5 килограмм. Это недостаточно весомый разброс по массе, поэтому при проектировании оборудования был выбран один технологический поток.
Четвёртый признак:
по серийности - проектируемый цех является цехом мелкосерийного производства. Номенклатура отливок включает в себя 21 наименование.
Пятый признак:
по степени механизации - проектируемый цех относится к механизированным цехам с частичной автоматизацией производства.
Согласно классификации литейных цехов по виду производства проектируемый цех относится к цехам мелкосерийного производства.
1.2 Режим работы цеха
Примем режим работы двухсменный, параллельный при пятидневной рабочей неделе, а для отделений термообработки и обсыпки - трехсменный режим работы.
Выбор такого режима работы обуславливается тем, что возможно создание наилучших условий организации труда и, кроме этого, существует возможность постоянного обслуживания технологического оборудования.
Третья смена планируется для обслуживания дуговых печей, а так же для поддержания режимов работы печей термообработки (ТО). Так же в течение третьей смены будут проводиться профилактические и ремонтные работы.
При выборе режима работы проектируемого цеха необходимо обратить внимание на требования охраны труда, которые допускают в общем, неизолированном помещении производить формовку, сборку, операции по заливке, выбивке литья, обрубке и приготовлению смесей.
Вредные операции с большим выделением газов, пыли, шума, других вредных и опасных факторов необходимо изолировать от помещений с менее вредными условиями труда.
1.3 Фонд времени
ФД
=(FК
-FНД
)∙S∙g∙КР
, где
FК
– календарный фонд рабочего времени;
FНД
– выходные и праздничные дни;
S – количество смен работы;
g – средняя продолжительность смены, час;
Кр - коэффициент потерь рабочего времени.
Полученные данные заносим в табл. 1.1
Таблица 1.1
Расчётные и действительные фонды времени для оборудования
Наименование отделения
|
Число смен работы
|
Календарный фонд рабочего времени, дн.
|
Кр
|
Потери времени, дн.
|
Действительный годовой фонд времени, час.
|
Плавильно-заливочное
|
2
|
365
|
0,95
|
115
|
3815
|
Модельное
|
2
|
365
|
0,95
|
115
|
3815
|
Формовочное
|
3
|
365
|
0,90
|
4
|
7800
|
ТО
|
3
|
365
|
0,90
|
4
|
7800
|
ЛЮМ-контроль
|
2
|
365
|
0,95
|
115
|
3815
|
Очистное
|
2
|
365
|
0,95
|
115
|
3815
|
Годовой бюджет рабочего времени представлен в табл. 1.2
Таблица 1.2
Структура годового бюджета времени одного рабочего
Состав бюджета рабочего времени
|
По плану на год
|
Дни
|
Часы
|
1. Календарный ФРВ
|
365
|
2920
|
2. Выходные и праздники
|
115
|
920
|
3. Номинальный ФРВ
|
250
|
2000
|
4. Целодневные невыходы
|
48
|
384
|
а) очередной отпуск
|
30
|
240
|
б) дополнительный отпуск
|
5
|
40
|
в) по болезни
|
8
|
64
|
г) выполнение гос. обязанностей
|
2,5
|
20
|
д) декретный отпуск
|
2,5
|
20
|
5. Явочный ФРВ
|
202
|
1616
|
6. Внутрисменные потери РВ
|
0,25
|
2
|
7. Эффективный ФРВ
|
202
|
1616
|
1.4 Производственная программа
Расчет проекта цеха производим по приведенной программе. Для этого подбираем технологические данные только для части номенклатуры отливок и выбираем наиболее характерные отливки – представители. Основой для проектирования является производственная программа участка титанового литья ООО НПФ «Барк». В проекте составлена точная производственная программа. Она состоит из 21 наименований отливок. Отливки обеспечены чертежами и техусловиями, поэтому расчет программы производим по каждой детали.
Для составления производственной программы отливки – представители заносим в таблицу 1.3. Составление производственной программы цеха начинаем с определения годового выпуска каждой отливки – представителя (в тоннах) в цехе – аналоге:
m ца
отл
= (g отл
∙n ца
отл
)/1000, где
g отл
- номинальный вес отливки, кг;
n ца
отл
- годовой выпуск отливок – представителей в цехе – аналоге, шт.
Доля выпуска отливок – представителей каждой весовой группы в общем объеме годового выпуска этих отливок в цехе – аналоге:
КП(ВГ)
= ∑m ца
отл
/ ∑∑m ца
отл
, где
∑m ца
отл
- годовой суммарный выпуск отливок – представителей соответствующей весовой группы в цехе – аналоге;
∑∑m ца
отл
- годовой суммарный выпуск отливок – представителей в цехе – аналоге.
Годовой выпуск отливок – представителей в каждой весовой группе в проектируемом цехе:
∑m вг
= КП(ВГ)
∙ РПР ,
где
РПР
- годовое производство отливок в проектируемом цехе согласно заданию, т.
Доля выпуска отливок – представителей в годовой программе цеха – аналога:
КП(
i)
= m ца
отл(
i)
/ ∑m ца
отл
, где
m ца
отл(
i)
- годовой выпуск отливки – представителя в годовой программе цеха – аналога, т;
∑m ца
отл
- суммарный годовой выпуск отливок – представителей в цехе – аналоге, т.
Условно – приведенное производство каждой отливки – представителя в проектируемом цехе, т:
МОТЛ
(i)
= КП
(i)
∙ ∑ МВГ
.
Условно – приведенный поштучный выпуск каждой отливки – производителя в проектируемом цехе, шт:
NОТЛ
(i)
= МОТЛ
(i)
/ g отл
.
Данные таблицы 1.3 являются базой для составления производственных программ всех других технологических отделений цеха.
1.5 Выбор и расчет оборудования
1.5.1 Плавильное отделение
Проектирование плавильного отделения начинаем с составления баланса металла, выбора плавильного агрегата, определения необходимого количества оборудования.
1. Расход жидкого металла на каждую отливку - представитель определяется отношением:
gотл
жм
= 100 ∙ gотл
/ (ТВГ), где
gотл
- номинальный вес отливки-представителя, кг;
(ТВГ) – технологический выход годного для отливки - представителя, %.
2. Средний технологический выход годного:
Средний (ТВГ) = , где
… - годовое производство отливок-представителей, шт.;
… - номинальный вес отливок-представителей, кг;
… - расход металла на отливки-представители, кг.
3. Средняя металлоемкость:
, где
… - годовое производство форм для отливок-представителей, шт.;
… - металлоемкость формы для каждой отливки – представителя соответственно, кг;
- годовое количество изготовляемых форм в весовой группе или в цехе в целом, шт.
4. Количество жидкого металла, потребное на годовое производство каждой из отливок-представителей, т:
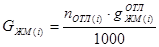
5. Общее количество металла на производство годных отливок:

6. Количество литников, прибылей и выпоров, возвращаемых на переплав:
, где
ТВГ- средний технологический выход годного;
- количество жидкого металла, покрывающего брак отливок, т.
, где
БР
- принятый брак отливок, % (5%).
7. Количество возвратных потерь:

8. Суммарное количество жидкого металла, необходимого для производства отливок согласно производственной программе цеха:

Результаты и необходимые данные об отливках-представителях оформляем в таблицу 1.4.
, где
- безвозвратные потери на угар, т;
U - угар, характерный для сплава и плавильного агрегата, в котором выплавляется сплав, % (5%).
9. Выход годного от металлозавалки (%):
, где
- общий номинальный вес выпускаемых в год отливок по цеху в целом, т;
-соответствующий вес шихтовых материалов согласно балансу металла, т.
В расчет необходимого количества жидкого металла необходимо учитывать ве литниково-питающих систем (ЛПС). Расчет приведен в табл. 1.5.
На основе полученных результатов составляем баланс металла (табл. 1.6),
Плавка титанового сплава и центробежная заливка его в форму производится в вакуумных дуговых гарнисажных печах с расходуемым электродом. Расходуемым электродом служит слиток заданного химического состава диаметром от 280 мм до 330 мм и длинной до 340 мм.
Преимущества вакуумных дуговых гарнисажных печей:
1. оптимальные режимы выплавки сложных сплавов;
2. высокая производительность, достигаемая благодаря большим значениям удельной мощности;
3. простота и удобство обслуживания печи, хорошие санитарно-гигиенические условия;
4. возможность быстрого перехода с выплавки сплава одной марки на другую.
Техническая характеристика печи ВДЛ-4М:
1. производительность печи – 0,1 т/час;
2. установленная мощность – 200 кВт;
3. расход электроэнергии – 900 кВт ∙ час/т;
Металлургические показатели:
1. Тmax
= 34000
С;
2. угар и безвозвратные потери 5%.
Определяем количество плавок на годовую программу для двух печей с разной емкостью тигля. Все данные сводим в таблицу 1.7.
Действительный годовой фонд времени =3815 ч
Определяем количество печей с ёмкостью тигля 0,2 т.
, где
- количество плавок, шт.;
- время плавки, ч;
- действительный фонд времени, ч.
Принимаем одну печь с емкостью тигля 0,2 т.
Определяем количество печей с ёмкостью тигля 0,25 т.
Таблица 1.7
Годовое количество плавок для каждой отливки
№ п/п
|
Марка сплава
|
Наименование отливки
|
Номинальный вес отливки,
кг
|
Годовой расход жидкого металла на отливку, т
|
Количество плавок на годовую программу, шт.
(емкость тигля 0,2 т.)
|
Количество плавок на годовую программу, шт.
(емкость тигля 0,25 т.)
|
1
|
2
|
3
|
4
|
5
|
6
|
7
|
1
|
ВТ20Л
|
Шарнир мужской
|
0,24
|
4,216
|
16,9
|
2
|
ВТ20Л
|
Шарнир женский
|
0,25
|
5,807
|
29,0
|
3
|
ВТ5Л
|
Основание
|
0,32
|
7,281
|
29,1
|
4
|
ВТ5Л
|
Стойка
|
0,5
|
6,968
|
27,9
|
5
|
ВТ20Л
|
Тройник
|
0,48
|
4,551
|
22,8
|
6
|
ВТ5Л
|
Патрубок
|
0,95
|
22,067
|
88,3
|
7
|
ВТ5Л
|
Тройник
|
0,86
|
28,13
|
140,7
|
8
|
ВТ20Л
|
Штуцер
|
0,5
|
14,147
|
70,7
|
9
|
ВТ20Л
|
Штуцер
|
0,8
|
9,102
|
45,5
|
10
|
ВТ20Л
|
Кронштейн
|
1
|
9,7
|
38,8
|
11
|
ВТ5Л
|
Заслонка
|
0,39
|
2,651
|
10,6
|
12
|
ВТ5Л
|
Стойка
|
0,64
|
13,492
|
54,0
|
13
|
ВТ20Л
|
Кронштейн
|
0,78
|
26,692
|
106,8
|
14
|
ВТ20Л
|
Шарнир
|
1,1
|
24,335
|
121,7
|
15
|
ВТ20Л
|
Рычаг
|
1,28
|
14,442
|
57,8
|
16
|
ВТ20Л
|
Угольник
|
1,3
|
18,391
|
92,0
|
17
|
ВТ20Л
|
Шток
|
1,67
|
14,812
|
74,1
|
18
|
ВТ5Л
|
Опора
|
1,75
|
59,488
|
238,0
|
19
|
ВТ20Л
|
Кронштейн
|
2,05
|
8,372
|
41,9
|
20
|
ВТ5Л
|
Кронштейн
|
1,8
|
12,649
|
50,6
|
21
|
ВТ20Л
|
Корпус
|
2,24
|
37,405
|
187,0
|
Итого
|
825,4
|
718,8
|

Принимаем одну печь емкостью 0,25 т.
Определяем коэффициент загрузки оборудования

1.5.Модельное,сборочное,подготовительное отделения
Особенности модельного отделения – полный локальный цикл изготовления конечного готового продукта – модельного блока. Цикл охватывает следующие основные операции:
1. расплав модельного состава;
2. сборка пресс-форм;
3. запрессовка пресс-форм модельной массой;
4. разборка пресс-форм, доводка моделей, контроль моделей;
5. изготовление ЛПС;
6. сборка модельных блоков;
7. контроль модельных блоков.
Для определения количества оборудования необходимо рассчитать годовой расход модельной массы. Расчет приведен в табл. 1.8.
Таблица 1.8
Ведомость расхода модельной массы
№ п/п
|
№ детали
|
Вес модели, кг.
|
Количество моделей на годовую программу, шт.
|
Количество моделей в пресс-форме, шт.
|
Количество моделей на годовую программу (с учётом брака 2%), шт.
|
Вес моделей .на годовую программу (с учётом брака 2%), т
|
Вес модели ЛПС, кг.
|
Количество моделей ЛПС на годовую программу, шт.
|
Вес моделей ЛПС на годовую программу, т
|
1
|
2
|
3
|
4
|
5
|
6
|
7
|
8
|
9
|
10
|
1
|
84-00-038
|
0,05
|
4977
|
1
|
5077
|
0,25
|
0,17
|
3532
|
0,59
|
2
|
84-00-089
|
0,05
|
5807
|
1
|
5923
|
0,30
|
0,18
|
4882
|
0,86
|
3
|
94-13-163
|
0,07
|
6636
|
1
|
6769
|
0,47
|
0,22
|
4486
|
1,00
|
4
|
94-10-636
|
0,11
|
4645
|
1
|
4738
|
0,52
|
0,35
|
2536
|
0,88
|
5
|
84-13-262
|
0,10
|
3318
|
1
|
3384
|
0,34
|
0,34
|
1661
|
0,56
|
6
|
СТв5-40-330
|
0,20
|
5807
|
1
|
5923
|
1,18
|
0,66
|
4931
|
3,26
|
7
|
94-10-606
|
0,18
|
7632
|
1
|
7785
|
1,40
|
0,60
|
7139
|
4,28
|
8
|
94-13-164
|
0,11
|
8959
|
1
|
9138
|
1,01
|
0,35
|
5320
|
1,85
|
9
|
94-10-610
|
0,17
|
3318
|
1
|
3384
|
0,58
|
0,56
|
2240
|
1,25
|
10
|
Э 94-03-2074
|
0,21
|
3152
|
1
|
3215
|
0,68
|
0,70
|
1796
|
1,25
|
11
|
83-04-023
|
0,08
|
2323
|
1
|
2369
|
0,19
|
0,27
|
1207
|
0,33
|
12
|
84-04-245
|
0,13
|
5973
|
1
|
6092
|
0,79
|
0,45
|
4221
|
1,88
|
13
|
94-10-583
|
0,16
|
9126
|
1
|
9308
|
1,49
|
0,54
|
7065
|
3,83
|
14
|
15Д-291
|
0,23
|
6636
|
1
|
6769
|
1,56
|
0,76
|
4297
|
3,29
|
15
|
31В-147
|
0,27
|
2821
|
1
|
2877
|
0,78
|
0,89
|
2397
|
2,13
|
16
|
701.3200
|
0,27
|
4479
|
1
|
4569
|
1,23
|
0,91
|
2656
|
2,41
|
17
|
93И-642
|
0,35
|
2439
|
1
|
2488
|
0,87
|
1,16
|
1801
|
2,09
|
18
|
26З-161
|
0,37
|
11614
|
1
|
11846
|
4,38
|
1,22
|
6076
|
7,41
|
19
|
58Д-243
|
0,43
|
1327
|
1
|
1354
|
0,58
|
1,43
|
755
|
1,08
|
20
|
3Д-66
|
0,38
|
1991
|
1
|
2031
|
0,77
|
1,25
|
1406
|
1,76
|
21
|
32Д-29
|
0,47
|
4314
|
1
|
4400
|
2,07
|
1,56
|
3490
|
5,45
|
Итого
|
109439
|
21,44
|
73895
|
47,43
|
Всего
|
68,87
|
Модельное отделение
Среднечасовая производительность барабана для варки модельной массы модели 651
Действительный годовой фонд времени
Потребное годовое количество модельной массы
Коэффициент неравномерности
|




|
Необходимое количество барабанов:

Принимаем один барабан.
Среднечасовая производительность модельной шприц-машины модели 6А54
Действительный годовой фонд времени
Количество съёмов на годовую программу
Коэффициент неравномерности
Коэффициент производительности
|
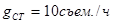




|
Необходимое количество модельных шприц-машин:

Принимаем 7 шприц-машин.
Среднечасовая производительность модельной шприц-машины для ЛПС 6А54
Действительный годовой фонд времени
Количество съёмов на годовую программу
Коэффициент неравномерности
Коэффициент производительности
|
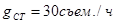

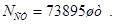


|
Необходимое количество модельных шприц-машин для ЛПС:
Принимаем две шприц-машины для ЛПС.
Среднечасовая производительность сборщицы моделей
Действительный годовой фонд времени
Количество блоков на годовую программу
Коэффициент выполнения норм
|


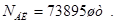

|
Необходимое количество сборочных столов:

Принимаем три сборочных стола.
Отделение подготовки форм
Станок для подрезки ЛПС - 1 шт.
Среднечасовая производительность автоклава
Действительный годовой фонд времени
Количество съёмов на годовую программу
Коэффициент неравномерности
Коэффициент производительности
|
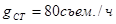

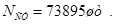


|
Необходимое количество автоклавов:

Принимаем один автоклав.
Ванна для подготовки форм – 1шт.
Сушило - 1 шт.
Оборудование для приготовления огнеупорного покрытия рассчитывается с использованием данных табл.1.9.
Среднечасовая производительность бака для 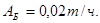
приготовления суспензии
Действительный годовой фонд времени 
Потребное годовое количество суспензии 
Коэффициент неравномерности 
Необходимое количество баков:
Принимаем один бак
Среднечасовая производительность для приготовления суспензии
Действительный годовой фонд времени
Потребное годовое количество суспензии
Коэффициент неравномерности
|
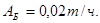



|
Необходимое количество барабанов:

Принимаем три бака.
Среднечасовая производительность прокалочной печи
Действительный годовой фонд времени
Количество съёмов на годовую программу
Коэффициент неравномерности
Коэффициент производительности
|


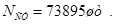


|
Необходимое количество прокалочных печей:

Принимаем три прокалочных печи.
Отделение обсыпки
Обсыпка форм производится на автоматической формовочной линии, работа которой описана ниже в пункте 2.2. Расчет годовой потребности линии в исходных формовочных материалах приведен в табл. 1.9
1.5.3 Термическое отделение
Для снятия внутренних напряжений после заварки титановые отливки подвергают неполному отжигу с нагревом в воздушной атмосфере. Для снятия напряжений в сложных корпусных отливках, их подвергают отжигу с нагревом в защитной атмосфере. В качестве защитной атмосферы применяется аргон по ГОСТ 10157-79.
Среднечасовая производительность термической печи
Действительный годовой фонд времени
Количество отливок на годовую программу
Коэффициент неравномерности
Коэффициент производительности
|
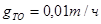




|
Необходимое количество термических печей:

Принимаем четыре термические печи.
1.5.4 Очистное отделение
В очистном отделении литейного цеха выполняются следующие операции: отделение литников и прибылей, зачистка и исправление дефектов литья, термообработка отливок.
Вибросито – 2 шт.
Ленточно-шлифовальный станок – 1 шт.
Шабровочный станок – 2 шт.
Отрезной станок – 1 шт.
1.6 Компоновка отделений цеха
Компоновка отделений цеха должна обеспечивать:
1. соблюдение последовательности технологического процесса при минимальных грузопотоках;
2. выполнение санитарно-технических требований предъявляемых к литейному цеху.
Основные положения при выборе здания:
1. выбираем одноэтажное здание с торцевым двухэтажным пристроем для размещения административных помещений;
2. высота здания и ширина пролетов согласована с применяемыми транспортными средствами.
Здание проектируемого цеха имеет прямоугольную форму, обеспечивающую возможность оптимального размещения технологического оборудования. Конструкция здания представляет собой 2 продольных пролета шириной 24 м.
Ширина 48 м.
Длина здания 108 м.
Высота пролетов от отметки нижней части несущей формы балки до нулевой отметки 14,400 м.
1.7 Характеристика и монтаж конструктивных элементов здания
Фундаменты колонн сборные железобетонные, стаканчатого типа с размерами в основании 2600 х 1900 мм, высотой 1200 мм, изготовляемые из армированного бетона. Фундаментный блок воспринимает нагрузки от здания, поэтому закладывается на глубину 2,25 м., т.к. промерзание грунта в районе г. Перми 1,8 м.
Несущим элементом здания является каркас, выполненный из железобетонных колонн, которые воспринимают нагрузку от перекрытий.
Размеры сечения колонн:
- крайнего ряда 800 х 400 мм;
- среднего ряда 800 х 600 мм.
Колонны среднего ряда – 2-х сторонние, колонны крайних рядов – 1-вет- венные.
Фермы стропильные: в соответствии с шириной пролетов принимаем фермы длиной 24 метров, высотой 3,3 метра.
В качестве покрытия применяем железобетонные ребристые плиты размерами 3 х 6 м. Плиты укладываются на фермы, на плиты наносится слой утеплителя. На утеплитель наносится обмазка горячим битумом БНК-5 в два слоя и 4 слоя рубероида. На здании установлены продольные свето-аэрационные фонари шириной 6 м и высотой 3 м. Каркас фонарей изготовлен из уголка, на который монтируется остекление.
В качестве ограждения конструкции здания выбираем панели, из которых складывается стена. Стеновая панель 6000х1200х400 мм из легкого бетона. Оконные проемы выбираем высотой 3 м и длиной 3м. Полы в цехе выложены металлической плиткой размерами 400х400 мм.
1.8 Бытовые помещения
Бытовые помещения находятся в административном здании. Здание 2-х этажное. Площадь гардеробной определяется исходя из количества рабочих и размеров шкафов для чистой и грязной одежды. В гардеробной не должно быть соединения чистого и грязного потока людей. Размеры шкафа 500х400 мм и высота 1,65 м. Ширина прохода между шкафами не менее 1,5 м. Душевые размещаются в помещениях смежных с гардеробными. Количество душевых определяется из расчета один душ на 7-9 человек. Количество умывальников определяется из расчета 1 умывальник на 15 человек.
1.9 Вспомогательные отделения цеха
Службы механика и энергетика выполняют профилактику и ремонт (кроме капитального) оборудования.
Служба механика – 216 м2
Служба энергетика – 216 м2
Склад готовых деталей.
Для хранения готового литья в цехе предусматривается площадь, которая определяется по планировке – 288 м
2
1.10 Транспортная система цеха
Транспортная система цеха состоит из транспортеров, электрокар, кран-балок и мостовых кранов.
На шихтовой склад металлическая шихта привозится на грузовых машинах и выгружается с помощью кран-балки. Песок для обсыпки поступает в готовом виде на самосвалах и разгружается в закрома. Загрузка плавильных печей осуществляется с помощью тележки. Отливки с литниками и прибылями перемещаются из заливочного отделения в отделение обрезки с помощью электропогрузчика. Отработанная формовочная смесь транспортируется ленточным транспортером в бункер и, далее, в отвал. Доставка отходов металла из отделения обрезки осуществляется с помощью электропогрузчика в бадьях. Отходы на шихтовом складе хранятся в специально выделенном месте. В отделении обрезки и зачистки отливки складируются в короба и передаются на термообработку, а затем на склад готовой продукции.
В рамках данного раздела в графической части проекта были выполнены следующие чертежи:
планировка цеха ДП.98.04.03.
поперечный и продольный разрезы цеха ДП.98.05.03.
схема грузопотоков ДП.98.06.03.
2. Разработка технологического процесса изготовления отливки «Кронштейн» в электрокорундовой форме
Данный раздел представляет собой разработку процесса изготовления отливки-представителя, взятой из производственной программы проектируемого цеха. Технология её изготовления должна соответствовать одному из принятых в проекте технологических процессов. Можно разрабатывать более совершенные технологии изготовления отливки для сокращения брака, снижения трудоемкости, внедрения нового технологического процесса и оборудования.
2.1 Технология изготовления отливки
Общие требования, которым должны удовлетворять отливки, изготавливаемые в керамическую форму:
1. отливки могут иметь сложную конфигурацию, при которой не требуется минимальное число разъемов;
2. отливки могут иметь различные выступающие части, поднутрения;
3. отливки могут иметь резкие переходы от тонких стенок к массивным.
Разработка чертежа отливки производится по чертежу детали, назначаются припуски на механическую обработку, технологические припуски, уклоны, допуски на размеры, литейную усадку.
Технологические операции, включенные в данный процесс, являются обязательными. Сначала изготавливаются модели отливок и литниково-питающих систем (ЛПС). Затем происходит сборка моделей отливок и ЛПС в блоки, путем наклеивания и припаивания. Контроль блоков осуществляется специальными инструментами. Каждый блок сопровождается контрольными листами и картами. Обсыпка готовых блоков на линии происходит автоматизировано, непрерывно в течение 3-х смен. Подготавливают форму к заливке в автоклаве, где используются высокие давление и температура. После этой операции готовая форма подвергается пропитке пироуглеродом с последующей выдержкой на воздухе. Перед заливкой все формы проходят контроль. Заливка форм осуществляется в вакуумных дуговых плавильно-заливочных установках ВДЛ-4М. Выбивка отливок из форм осуществляется на выбивных решетках, после чего идет механическая обработка отливок (обрубка, зачистка). Для данных титановых сплавов термическая обработка, рентгеноконтроль и ЛЮМ - контроль является обязательными технологическими операциями, т.к. сплавы используются для ответственных и особо ответственных деталей оборонной промышленности, авиации, ракетостроения.
Сам технологический процесс изготовления отливок литьем по выплавляемым моделям (ЛВМ) очень сложен и требует более глубокого и внимательного рассмотрения.
2.1.1 Пресс-формы для изготовления моделей
Выплавляемые модели изготавливают в специальных пресс-формах. От точности изготовления пресс-форм и чистоты их рабочей поверхности зависит чистота поверхности и точность отливок. Точность размеров и чистота поверхности рабочей полости пресс-формы должна быть на 1 и 2 класса выше требуемой точности и чистоты поверхности отливки. Пресс-формы изготавливают из стали Ст3 или 45, алюминиевого сплава АЛ2, свинцовосурьмянистых сплавов, высококачественного гипса, эпоксидных смол ЭД-5, ЭД-6, резины. Выбор материала для пресс-формы зависит от характера производства. В условиях массового производства пресс-формы изготовляют из стали, а мелкосерийного – из гипса, пластмасс, свинцовосурьмянистых сплавов.
Пресс-форму можно получать механической обработкой, отливкой по модели-эталону, способом гальванического нанесения металла на модель-эталон.
Извлечение модели из пресс-формы без повреждений и искажений обеспечивается правильным выбором разъема, уклонов и применением выталкивающих устройств. Величина уклонов должна быть не менее 0,5 град.
2.1.2. Приготовление огнеупорной суспензии
Приготовление суспензии производить в чистом смесителе.
Налить в смеситель необходимое количество связующего ГС-20Э.
Включить смеситель. Наполнитель вводить небольшими порциями и тщательно перемешивать до получения однородной суспензии, но не менее 30 мин.
Выключить смеситель и после трёхминутной выдержки проверить вязкость суспензии вискозиметром. Вязкость суспензии для первого слоя должна быть в пределах 28-35 с для второго и последующих слоёв 14-18 с. Требуемая вязкость суспензии доводится путём введения исходных составляющих по необходимости.
Замерить температуру суспензии. Температура должна быть в пределах 18-25о
С.
Срок годности суспензии не более одних суток.
2.1.3. Изготовление форм
Изготовление оболочковых форм производится на автоматической формовочной линии, работа которой описана далее в пункте 2.2.
2.1.4. Вытопка модельного состава
Технические характеристики автоклава:
- производительность автоклава - 80-100 блоков в час;
- максимальное давление - 8 атм.;
- максимальная температура - 170о
С;
- время набора до давления 4,5 атм. - 10 с;
- мощность - 121,75 кВт;
- вес - 9 т;
- размер загружаемых блоков в кассету - max. 550-750 мм.
Давление пара должно быть 5,5-8,3 атм. или выше. Применение более низкого давления пара может вызвать растрескивание керамической оболочки.
Впуск пара и выход на рабочее давление должен происходить как можно быстрее, желательно в течение 15 секунд и менее. Медленная передача тепла модельной массе вызовет растрескивание оболочки.
Выпуск пара после окончания цикла должен осуществляться медленно (в течение 30-60 секунд). Если пар будет выпущен быстро, то может произойти отслоение наружных слоев формы.
2.1.5.Прокаливание оболочковых форм
Прокаливание необходимо для полного удаления из форм остатков модельного состава, испарения остатков воды и продуктов не полного гидролиза связующего, а также спекания связующего и огнеупорного материала. Во время прокаливания в стенке оболочковой формы образуются поры и микротрещины, благодаря чему возрастает газопроницаемость оболочки. Чтобы стенки формы не возникли термические напряжения вследствие резкого одностороннего нагрева, начальную температуру в печи и скорость нагрева выбирают из условия равномерного нагрева оболочковой формы. Прокалку ведут при температуре 950 – 1050C, охлаждение форм производится вместе с печью.
2.1.6 Литье в керамические оболочки
Перед началом плавки необходимо проверить давление воды по манометру и убедиться в наличии воды на сливе.
Подать напряжение на печь включением ключа на пульте.
Опустить электрод вниз до образования дуги между гарнисажем и расходуемым электродом.
Произвести прогрев во время, которого при сплавлении металла уменьшить силу тока.
После прогрева быстро переключить силовой трансформатор на более высокую ступень и начать плавку, включить секундомер.
Остаточное давление во время плавки не должно превышать 10-2
мм р. ст. Допускается кратковременное падение вакуума в процессе ведения плавки до 10-1
мм р. ст.
Электрический режим плавки регулировать вручную короткими подачами электрода вверх-вниз, при изменении силы тока и напряжения добиваться «короткой дуги». Нулевое показание напряжения на приборе фиксирует короткое замыкание, при котором необходимо быстро поднять электрод вверх до возникновения дуги. При приварке расходуемого электрода к гарнисажу тигля плавку прекратить.
Начало плавки вести при минимальной силе тока, конец плавки - при максимальной.
При заливке тонкостенных отливок температуру металла увеличить за счёта вверх вниз, и начать плавку, включить секундомер.
ается для укладки в контейнер под заливку. увеличения времени плавки при максимальной силе тока.
Перед началом заливки включить центробежную машину и установить число оборотов. Если заливаются детали, у которых число оборотов при заливке разное, то устанавливают большее число оборотов.
Произвести слив металла.
Центробежную машину печи отключить согласно времени указанного в технологии.
2.2 Краткое описание работы линии
Подвески с модельными блоками навешиваются на цепной конвейер. Каждая подвеска будет перемещаться с определенным шагом по конвейеру с переключением вручную до тех пор, пока вся линия не будет полностью загружена (23-мя подвесками). Затем управление этого конвейера передается на панель управления PLC.
После этого начинается автоматизированный процесс окраски и сушки. Каждая подвеска с модельными блоками будет захватываться роботом, окрашиваться в соответствующем баке с суспензией, обсыпаться в соответствующем пескосыпе и подвешиваться в сушильном тоннеле.
При нанесении следующих слоев керамического покрытия робот уже будет брать подвеску из сушильного тоннеля. После нанесения всех слоев, робот переместит каждую из подвесок на второй уровень в тоннель окончательной сушки. После этого линия снова готова для нанесения керамической оболочки на следующую партию блоков.
Цикл нанесения всех слоев оболочки на одну партию блоков (минимум 92 блока) составляет примерно 10 часов, а время окончательной сушки блоков после нанесения всех слоев – 20 часов. Поэтому тоннели окончательной сушки в 2 раза больше (46 подвесок), чтобы вместить две партии блоков. В конце нанесения всех слоев на третью партию блоков из тоннеля окончательной сушки с помощью съемника удаляются формы первой партии, тем самым, освобождая место для третьей партии. Таким образом, через каждые 10 часов с линии сходит партия лишних блоков.
Техническая характеристика линии:
1. общая стоимость линии – 897 тыс. у.е.;
2. производительность – 40000 форм в год;
3. размеры форм, мм: max 220÷180÷450, min 160÷140÷250
4. максимальный вес формы – 30 кг;
5. минимальное число блоков на одной подвеске – 1 шт.;
6. среднее количество слоев – 7;
7. габариты линии, мм: 24 000÷125 000÷35 000
2.3 Комплектность линии
В комплект линии входит:
1. сушильный тоннель на 23 подвески. Сушильный тоннель расположен на первом уровне и оборудован тремя роторными диффузорами (объем воздуха 4 м3
/с, высота макс. 1845 мм, выход скорости потока 10 м/с, угол вращения 360 град.). Сушильный тоннель включает в себя системы кондиционирования;
2. сушильный тоннель для окончательной сушки 46 подвесок. Этот тоннель (с целью сокращения используемого пространства) расположен под сушильным тоннелем на 23 подвески и в два раза длиннее. Тоннель оборудован пятью роторными диффузорами. Сушильный тоннель включает в себя системы кондиционирования;
3. вращающийся бак для суспензии диаметром 1200 мм. Для первого слоя;
4. вращающийся бак для суспензии диаметром 1200 мм. Для второго слоя;
5. вращающийся бак для суспензии диаметром 1200 мм. Для последующих слоев;
6. пескосып для первых слоев диаметром 1200 мм;
7. пескосып для последующих слоев диаметром 1200 мм;
8. робот SК-120 (L= 700 мм., В=3000 макс. мм., Н=3020 макс. мм);
9. цепной конвейер для подачи модельных блоков (30 подвесок);
10. съемник (промышленный робот для выгрузки готовых форм);
11. система управления линией.
Описание линии
Линия состоит из следующего оборудования:
- пескосып дождевого типа;
- бак связующего;
- робот SK-120 грузоподъёмностью 120 кг;
- бак для приготовления связующего;
Робот оснащён цифровым управлением и надёжными механизмами, которые обеспечивают высокую точность и плавность хода. Жёсткая основа робота прикреплена к полу. Размах манипулятора достигает 3,5 метра по радиусу и до 2,5 метров в высоту (рис.2.9). У робота пять степеней свободы, что позволяет получить равномерное покрытие модели. Программное обеспечение простое и может быть отредактировано и загружено со стандартного персонального компьютера. Обладая небольшими размерами он несёт достаточно большую грузоподъёмность.
- контроллер робота;
- сушильный двухуровневый шкаф;
- конвейеры-накопители готовых форм и модельных блоков;
Предназначены для накопления готовых форм и модельных блоков. Оба конвейера закрыты защитным кожухом. Длина конвейера готовых форм 34.5 метра, что обеспечивает нахождения на нём 69 готовых форм. Длина конвейера модельных блоков 92 метра, что обеспечивает непрерывную работу. На нём может находиться до 184 подвесок с модельными блоками. Конвейеры снабжены также удобными, автоматическими устройствами погрузки и разгрузки.
- пять роторных диффузоров;
- бак для приготовления связующего;
- автоматическая система транспортировки связующего.
На рис 2.10 представлена блок-схема технологического процесса литья по выплавляемым моделям с использованием автоматической формовочной линии
В рамках данного раздела в графической части проекта были выполнены следующие чертежи:
чертеж отливки «Кронштейн» ДП.98.01.02.
сборочный чертеж пресс-формы на деталь «Кронштейн» ДП.98.02.02.
чертеж формы ДП.98.03.02.

Рис.2.9. Схема движения робота.

Рис. 2.10 Блок-схема технологического процесса ЛВМ.
3.Гидровлический расчет площади поперечного сечения питателя литниковой системы
Разница в продолжительности заполнения отдельных полостей формы чревата дефектами в отливках:
1. Чрезмерное быстрое заполнение нижних рядов формы может привести к образованию газовых раковин в отливках.
2. Недостаточная скорость заполнения верхних рядов, особенно если отливки тонкостенные, может привести к незаполнению формы вследствие того, что металл затвердевает прежде, чем заполнится форма.
Поэтому важно, чтобы отдельные полости формы заполнялись за определенное одинаковое время.
Применительно к дипломной работе, объектом расчета является задачи по нахождению площади поперечных сечении f1, f2, f3, f4 питателей.
Расчет ведется по формуле Озанна:
= ,см
Данные к задаче:
Многоместная форма, получаемая на автоматической формовочной машине, заливается чугуном.
Размеры каждой отливки а*в*с=100*200*100. Оси питателей размещены на расстоянии а/2 от днищ форм и расстояние между осями питателей h=140 мм. Размер h0=140 мм в процесс заливки формы остается неизменным. Коэффициент расхода всех питателей принять одинаковым и равным =0,7. Время заполнения всех отливок будет одинаковым и равны Т = 7 с.
Временем заполнения литниковой системы (чаши, стояка, питателей) пренебречь. Воздух и газы удаляются из формы за счёт её газопроницаемости. Давление на свободной поверхности расплава считать атмосферным.
Расчёт задачи:
Определяем HСР для каждой отливки по формуле Диттерта:
HСР = HО – P2
/2*C , где
НО – высота стояка;
Р – высота отливки над питателем;
С – полная высота отливки.
Определяем площадь поперечного сечения питателя подставляя найденное значение Нср в формулу Озанна:
= , где
F – площадь отливки;
T – время заливки с.;
– коэффициент расхода питателя;
g = 981 см/с2
.
1. Но = 560 мм. Р = а/2 = 50 мм. С = а = 100 мм.
Нср = 56 – 25/20 = 54,75 см.
f1
= =1,24см2
2. Н
0 = 420 мм.
Нср = 42 – 1,25 = 40,75 см.
f
2 = 2000/4,9*282,75 = 1,43 см2
3. Н
о = 280 мм.
Нср = 28 – 1,25 = 26,75 см
f
3 = 2000/4,9*229,1 = 1,81 см2
4. Н
0 = 140 мм.
Нср = 14 – 1,25 = 12,75 см
f
4 = 2000/4,9*158,17 = 2,57 см2
4.Анализ вредных и опасных производственных факторов,
меры пожарной безопасности
.
4.1.Санитарно-технологическая характеристика производства.
Литейное производство характеризуется наличием большого количества вредных и опасных производственных факторов, имеющихся на всех участках производственного процесса. Специфика литейного производства не позволяет полностью устранить влияние этих факторов на работающих, но с применением современных методов производства, можно значительно уменьшить их воздействие. Внедрение в производство автоматизации на наиболее вредных и опасных для здоровья людей участках позволяет отказаться от применения ручного труда. Строгое разграничение производственных участков исключает воздействие факторов технологического процесса одного участка на рабочих другого участка, т. к помещения участков изолированы друг от друга.
В проектируемом цехе имеются следующие вредные производственные факторы (по ГОСТ 12.0.003-74):
1. Повышенная загазованность воздуха рабочей зоны, присутствует на участках
- Плавки;
- Выделение легкоплавких и легко испаряемых элементов;
- Смесеприготовления - при приготовлении связующего.
- Опасность загазовоности в том, что при длительном воздействии на организм они могут привести к отравлениям, к хроническим изменениям в организме, проявляемым в повреждениях внутренних органов, кровеносной системы, нервной системы; могут иметь канцерогенное действие, оказывать удушающее, наркотическое и раздражающее воздействие.
2.Повышенная запыленность воздуха.
Проявляется на участках:
- Подготовки шихтовых и формовочных материалов;
- Смесеприготовления;
- Выбивки отливок;
- Очистки, отрезки.
Повышенная запыленность может привести к раздражению слизистой оболочки, кожи, десен; к повреждению дыхательных путей; к появлению профессионального заболевания - пневмокониоз.
3.Повышенная температура воздуха рабочей зоны.
Имеется на участках:
- Плавки, от трёх электродуговых плавильно-заливочных агрегатов;
- Термообработки, отливок от действия трёх печей;
- Прокалки форм от трёх прокалочных печей.
Влияние фактора повышенной температуры рабочей зоны заключается в снижении работоспособности, ослаблении сопротивляемости организма - к повышению заболеваемости, к тепловому истощению или удару.
4. Повышенный уровень шума.
Наиболее характерен для участков выбивки отливок, обрезки, зачистки отливок. Шум значительно уменьшает работоспособность, вызывает раздражения, ухудшает действие слуховых органов, влияет на нервную и сердечно - сосудистую систему.
5.Повышенный уровень вибрации.
Характерен для участков выбивки отливок, зачистки, обрезки литников и прибылей.
Вибрация ведет к: Повышению утомляемости, снижению работоспособности, появлению виброболезни - спазма сосудов, уменьшает чувствительность организма, влияет на нервную систему, костно-суставной аппарат.
6.Повышенная подвижность воздуха.
Имеется на всей территории цеха, обеспечивается естественной вентиляцией и работой искусственной вентиляции.
7.Повышенная яркость света.
Проявляется в процессе прокалки форм, ведет к повреждению глаз.
Литейный цех характеризуется наличием опасных производственных факторов (по ГОСТ 12.0.003-74):
1.Повышенная температура поверхности оборудования
Повышенную температуру поверхности имеют:
- Плавильные агрегаты;
- Печи термообработки.
2.Движущиеся машины и механизмы
Могут привести к ушибам и травмам. Особенно велика опасность травм на участке приготовления шихты, при транспортировке передаточных тележек, вблизи конвейерных линий.
3.Острые края, заусеницы, шероховатость поверхности заготовок и инструмента
Могут привести к ранениям рабочих на участках выбивки, обрезки, зачистки, термообработки, подготовки шихты.
4.Повышенное значение напряжения в электрической цепи, замыкание которой может произойти через тело человека.
Литейный цех характеризуется наличием большого числа электрооборудования. По опасности поражения электрическим током (по ГОСТ 12.1.013-78) его относят к особо опасным помещениям, так как в цехе имеются токопроводящие полы, пыль, агрессивные химические вещества, которые при длительном воздействии могут разрушить изоляцию проводов. Поражение человека электрическим током может привести к ожогам, электрическим ударам.
4.2.Комплексные мероприятия по обеспечению безопасных условий труда.
Для обеспечения наибольшей безопасности труда и улучшения условий труда, необходимо стремиться к ликвидации ручного труда в опасных и вредных условиях, заменяя его применением автоматизации и механизации.
Все мероприятия, проводимые в цехе для обеспечения безопасных условий труда, проектируются в соответствии с ГОСТ 12. 3. 027-92. На модельном участке предусмотрены следующие мероприятия:
1) Предотвращение воздействия на людей электрического тока производится в соответствии с ГОСТ 12.1.019-79. Для этого:
Предусмотрено защитное заземление в соответствии с ГОСТ 12.1.030-81.
- Проводится периодический контроль состояния электрооборудования и изоляции.
- Электроустановки имеют блокировки, которые исключают включение оборудования при открытых его частях, которые находятся под напряжением.
- Электрооборудование имеет сигнализацию, о его включении. Оборудование имеет предохранительные устройства, обесточивающие его при коротком замыкании.
2) Освещенность рабочих мест участков нормируется по СНиП 23-05-95.
3) Влажность, скорость движения воздуха и содержание вредных веществ в воздухе рабочей зоны нормируется по ГОСТ 12.1.005-88. Допустимые значения этих параметров поддерживаются путем создания естественной и искусственной вентиляции в соответствии с СНиП 2.04.05-91. Над ветвями охлаждения конвейерных и комплексно-механизированной линий имеются вытяжные зонты. На других участках предусмотрены дополнительные мероприятия: Все проектировочные решения выполнены в соответствии с ГОСТ 12.3.027-92 .
4) На участках с повышенной температурой воздуха и температурой поверхности оборудования производятся мероприятия:
- Для удаления избытков тепла применяется механическая вентиляция (СНиП 2.04.05-91)
Источники повышенного тепловыделения подвергают дополнительной теплоизоляции. При этом температура наружной поверхности не должна превышать +45 С.
- Рабочие плавильного участка имеют средства индивидуальной защиты (по ГОСТ 12.3.011-80) - сапоги, рукавицы, суконные брюки и куртка.
5) Содержание в воздухе цеха вредных веществ и пыли нормируется по ГОСТ 12.1.005-88 , а содержание вредных веществ в материалах и продуктах - по ГОСТ 12.1.007-94
- Создание приточно-вытяжной вентиляции по СНиП 2.04.05-91.
- Токсичные вещества хранят в отдельных помещениях в герметичной таре.
- На участке подготовки формовочных материалов, рабочие имеют СИЗОД - фильтрующую полумаску.
6) Допустимые уровни звукового давления нормируются по ГОСТ 12.1.003-83 . Мероприятия по борьбе с шумом проектируются по ГОСТ 12.1.029-80 ,а с вибрацией по ГОСТ 12.1.012-90.
- Проводятся регулярные осмотры оборудования, его смазка, настройка.
- Оборудование с большим уровнем вибрации, галтовочные очистные барабаны устанавливается на отдельный фундамент.
- Для защиты от шума применяются СИЗ – противошумные наушники, вкладыши. Для защиты от вибрации - рукавицы антивибрационные на операциях обрезки и зачистки.
7) Движущиеся части оборудования ограждаются, при этом предусмотрена блокировка для отключения оборудования при ее отводе.
На участках, где имеется пыль, при очистки отливок, отлетающие куски материала, рабочие используют защитные очки ГОСТ 12.4.013-85.
8) Мероприятия по обеспечению взрывобезопасности проводятся в соответствии с ГОСТ 12.1.010-94
- Взрывоопасные участки располагаются в отдельных помещениях, оборудованных аварийной вентиляцией
- Все электрооборудование на этих участках выполнено во взрывобезопасном исполнении
- Производятся регулярные осмотры оборудования
- На взрывоопасных участках используется инструмент из безыскрового материала (медь, бронза).
9) Организационно-профилактические мероприятия:
- Все работающие проходят инструктаж: вводный, первичный, внеочередной на рабочем месте и регулярно повторный.
- Регулярное прохождение медосмотров.
- Обязательное обучение персонала правилам безопасности.
4.3.Меры по обеспечению пожарной безопасности.
Категории помещений и зданий по взрывопожарной и пожарной опасности.
Пожаробезопасность зданий и сооружений СНиП 2.01.02-91.
В соответствии с НПБ-105-95 , участки цеха относятся к категориям по взрывопожарной и пожарной опасности:
1) плавильно-заливочный, категория Г
2) термообработка, категория Г
3) изготовление форм, категория Г
4) ЛЮМ контроль, категория Б
5) склады шихты и формовочных материалов, категория Д
6) бытовые помещения, категория В
7) регенерация категория Д
Степень огнестойкости зданий и пределы огнестойкости основных конструкций.
Пожарная опасность строительных материалов – НГ
Пожарная опасность строительных конструкций – КО
Степень огнестойкости здания
Таблица 4.1
Степень огнестойкости здания
|
Предел огнестойкости конструкций, не менее, мин.
|
Несущие элементы здания
|
Наружные стены
|
Перекрытия между этажами
|
Покрытия без чердачные
|
Лестничные клетки
|
Внутренние стены
|
Площадка лестниц
|
I
|
R 120
|
RE 30
|
REI 60
|
RE 30
|
REI 120
|
R 60
|
Первичные средства пожаротушения
В цехе имеются средства пожаротушения (ППБ-01-93):
1) Для тушения электрооборудования - углекислотные огнетушители, асбестовые и войлочные полотна.
2) На плавильном участке имеется песок для тушения металлов.
3) Для тушения возгорания газа применяют углекислый газ и порошковые огнетушители.
4) Меры пожарной безопасности проектируются в соответствии с ГОСТ 12.1.004-91.
5) В пожароопасных местах имеются таблички, запрещающие использование открытого огня.
6) В цехе имеется пожарная сигнализация и средства тушения пожара.
Таблица 4.2
Средства тушения пожара
Участок
|
Площадь,
|
Класс
Пожара
|
Категории по ВПБ
|
Применяемые огнетушители
|
Количество
|
1. Плавильно-заливочный
|
864
|
Д
|
Г
|
Порошковые вместимостью 10л
|
1
|
2. Термообработка
|
288
|
Е
|
Г
|
Порошковые вместимостью 5л
|
2
|
3. Изготовления форм
|
648
|
Е
|
Г
|
Порошковые вместимостью 5л
|
2
|
4. Склады шихты и формовочных материалов
|
720
|
Е
|
Д
|
Порошковые вместимостью 2л
|
2
|
5. Бытовые помещения
|
720
|
Е, А
|
В
|
Пенные и водные 10л
|
4
|
6. ЛЮМ контроль
|
144
|
В
|
Б
|
Порошковый 10л.
|
1
|
Эвакуационные выходы.
Выход называется эвакуационным, если он ведёт:
1. Из помещений первого этажа непосредственно наружу:
– непосредственно;
– через коридор;
– через лестничную клетку;
– через коридор и вестибюль;
– через коридор и лестничную клетку.
3. Из помещений любого этажа, кроме первого:
- в коридор ведущий непосредственно в лестничную клетку или на лестницу третьего типа.
- в холл (фойе), имеющий выход непосредственно в лестничную клетку или на лестницу третьего типа.
Все отделения цеха имеют не менее двух эвакуационных выходов, указанных выше. Этого достаточно для эвакуации максимально возможного числа рабочих от наиболее удалённого места работы до ближайшего эвакуационного выхода.
Пути эвакуации освещены в соответствии с требованиями СНиП 23-05.
Высота эвакуационных выходов не менее 2 м. и не менее ширина 0.8 м. Высота эвакуационных путей не менее 2 м. и ширина не менее 1.2 м.
В общих коридорах не допускается размещения оборудования, выступающие из плоскости стен на высоте менее 2 м, газоводы, а также встроенные шкафы, кроме шкафов для коммуникаций и пожарных кранов.
Двери эвакуационных выходов не должны иметь запоров, препятствующих их свободному открытию изнутри без ключа.
Все вышеперечисленные параметры в цехе соблюдены.
4.4.Обеспечение проектируемого цеха санитарно – бытовыми, административными и вспомогательными помещениями и устройствами
.
Настоящие нормы распространяются на проектирование административных и бытовых зданий высотой до 16 этажей включительно и помещений предприятий.
Настоящие нормы не распространяются на проектирование административных зданий и помещений общественного назначения.
При проектировании зданий, перестраиваемых в связи расширением, реконструкцией или техническим перевооружением предприятий, допускаются отступления от требований настоящих норм в части геометрических параметров.
1. Бытовые здания и помещения
1.1. Бытовые здания предприятий предназначены для размещения в них помещений обслуживания работающих: санитарно-бытовых, здравоохранения, общественного питания, торговли и службы быта, культуры.
1.2. В технологической части проекта должна быть установлена численность работающих - списочная, в наиболее многочисленной смене1
, а также в наиболее многочисленной части смены при разнице в начале и окончании смены 1ч и более, принимая для расчета бытовых помещений и устройств; при этом в численность работающих необходимо включать число практикантов, проходящих производственное обучение. 1
В дальнейшем — смене.
Для мобильных зданий допускается принимать численность смены, равную 70% списочной, в том числе 30% женщин.
Расчёт:
По предварительным расчётам списочная численность работающих, в наиболее многочисленной смене составляет 120 человека.
1.3. Геометрические параметры, минимальные расстояния между осями и ширину проходов между рядами оборудования бытовых помещений следует принимать по табл. 4.3.
Таблица 4.3
Параметры установки оборудования в бытовых помещениях.
Наименование
|
Показатель м
|
Размеры в плане
|
Кабины:
|
Душевых закрытые
|
1,8×0,9 (1,8×1,8)
|
Душевых открытые и со сквозным проходом, полудушей
|
0,9×0,9 (1,2×0,9)
|
Личной гигиены женщин
|
1,8×1,2 (1,8×2,6)
|
Уборных
|
1,2×0,8 (1,8×1,65)
|
Скамьи в гардеробных
|
0,3×0,8 (0,6×0,8)
|
Устройство питьевого водоснабжения
|
0,5×0,7
|
Шкафы в гардеробных для уличной и домашней одежды в зависимости от климатических районов и специальной одежды и обуви1
|
IIБ, IIВ, IIГ, IIIБ, IIIВ, IV
|
0,25×0,5
|
IВ, IД, IIА, IIIА
|
0,33×0,5
|
IА, IБ, IГ
|
0,4×0,5
|
Размеры по высоте
|
Разделительные перегородки:
|
до верха перегородки
|
1,8
|
от пола до низа перегородки
|
0,2
|
Шкафы для хранения одежды
|
1,65
|
Расстояние между осями санитарных приборов
|
Умывальники одиночные
|
0,65
|
Ручные и ножные ванны, писсуары
|
0,7
|
Ширина проходов между рядами
|
Кабины душевых закрытые, умывальники
|
1,2 (1,8)
|
Групповые
|
Кабины душевых открытые и уборных, писсуары
|
1,5 (1,8)
|
Умывальники одиночные
|
1,8
|
Ручные и ножные ванны, кабины личной гигиены женщин и фотариев
|
2
|
Шкафы гардеробных для хранения одежды при числе отделений в ряду:
|
до 18
|
1,4/1**
(2,4/1,8)
|
от 18 до 36
|
2/1,4**
(2,4/1,8)
|
1
В дальнейшем спецодежды. Для обычного состава спецодежды (халаты, фартуки, легкие комбинезоны) следует предусматривать шкафы размерами в плане 0,25×0,5м, для расширенного состава (обычный состав плюс нательное белье, средства индивидуальной защиты) - 0,33×0,5м, для громоздкой спецодежды (расширенный состав плюс полушубки, валенки, специальные комбинезоны) - 0,4×0,5м.
**В знаменателе приведена ширина проходов между рядами шкафов между рядами шкафов без скамей.
Расчёт:
Таблица 4.4
Принятые параметры оборудования
Наименование
|
Показатель м
|
Принимаю размеры в плане:
|
Кабины душевые со сквозным проходом
|
0,9×0,9 м
|
Скамьи в гардеробных
|
0,3×0,8 м
|
Устройство питьевого водоснабжения
|
0,5×0,7 м
|
Шкафы в гардеробных для уличной и домашней одежды
|
0,4×0,5 м
|
Размеры по высоте:
|
Разделительные перегородки: до верха перегородки
|
1,8 м
|
от пола до низа перегородки
|
0,2 м
|
Шкафы для хранения одежды
|
1,65 м
|
Расстояния между осями санитарных приборов:
|
Умывальники одиночные
|
0,65 м
|
Писсуары
|
0,7 м
|
Ширина проходов между рядами:
|
Кабины душевых открытые и уборные
|
1,5 м
|
Писсуары, умывальники одиночные
|
1,8 м
|
Шкафы гардеробных
|
2 м
|
Санитарно-бытовые помещения
1.4. В состав санитарно-бытовых помещений входят гардеробные, душевые, умывальные, уборные, курительные, места для размещения полудушей, устройств питьевого водоснабжения, помещения для обогрева или охлаждения, обработки, хранения и выдачи спецодежды1
.
1.5. Санитарно-бытовые помещения для работающих, занятых непосредственно на производстве, должны проектироваться в зависимости от групп производственных процессов.
1
В соответствии с ведомственными нормативными документами допускается предусматривать в дополнение к указанным другие санитарно-бытовые помещения и оборудование. Таблица 4.5
Норма численности работающих приходящееся на ед. оборудования.
Группа производственных процессов
|
Санитарная характеристика производственных процессов
|
Расчётное число человек
|
Тип гардеробных, число отделений шкаф на 1 чел.
|
Специальные бытовые помещения и устройства
|
На одну душевую сетку
|
На один кран
|
1
|
Процессы вызывающие загрязнение веществами 3- и 4-го классов опасности:
|
1а
|
Только рук
|
25
|
7
|
Общее одно отделение
|
-
|
1б
|
Тела и спецодежды
|
15
|
10
|
Общие два отделения
|
-
|
1в
|
Тела и спецодежды, удаляемое с применением специальных моющих средств
|
5
|
20
|
Раздельные по донному отделению
|
Химчистка или стирка спецодежды
|
2
|
Процессы протекающие при избытках явного тепла или неблагоприятных метеоусловиях:
|
2а
|
При избытках явного конвекционного тепла
|
7
|
20
|
Общие два отделения
|
Помещения для охлаждения
|
2б
|
При избытках явного лучистого тепла
|
3
|
20
|
То же
|
То же
|
2в
|
Связанные с воздействием влаги, вызывающей намокание спецодежды
|
5
|
20
|
Раздельные, по одному отделению
|
Сушка спецодежды
|
2г
|
При температуре воздуха до 10о
С
|
5
|
20
|
Раздельные, по одному отделению
|
Помещения для обогрева и сушки спецодежды
|
3
|
Процессы, вызывающие загрязнение веществами 1- 2-го классов опасности, а также веществами, обладающими стойким запахом:
|
3а
|
Только рук
|
7
|
10
|
Общие, одно отделение
|
Химчистка, искусственная вентиляция мест хранения спецодежды, дезодорация
|
3б
|
Тела и спецодежды
|
3
|
10
|
Раздельные, по одному отделению
|
4
|
Процессы, требующие особых условий к соблюдению чистоты или стерильности при изготовлении продукции
|
В соответствии с требованиями ведомственных нормативных документов
|
При гардеробных следует предусматривать кладовые спецодежды, уборные, помещения для дежурного персонала с местом для уборочного инвентаря, места для чистки обуви, бритья, сушки волос2
.Кроме отдельных гардеробных для уличной одежды.
1.6. Число душевых, умывальников и специальных бытовых устройств, предусмотренных табл. 4.6, следует принимать по численности работающих в смене или части этой смены, одновременно оканчивающих работу.
1.7. Уборные в многоэтажных бытовых, административных и производственных зданиях должны быть на каждом этаже.
При численности работающих на двух смежных этажах 30чел. или менее уборные следует размещать на одном из этажей с наибольшей численностью.
При численности работающих на трех этажах менее 10чел. допускается предусматривать одну уборную на три этажа.
При наличии в числе работающих инвалидов с нарушением работы опорно-двигательного аппарата уборные следует размещать на каждом этаже независимо от численности работающих на этажах.
1.8. Вход в уборную должен предусматриваться через тамбур с самозакрывающейся дверью.
В мужских уборных в соответствии с ведомственными нормами допускается применять взамен индивидуальных лотковые писсуары с настенным смывом.
При наличии в числе работающих инвалидов, пользующихся креслами-колясками, один из писсуаров в уборных должен размещаться на высоте не более 0,4 м от пола
1.9. Расстояние от рабочих мест в производственных зданиях до уборных, курительных, помещений для обогрева или охлаждения, полудушей, устройств питьевого водоснабжения должно приниматься не более 75м, для инвалидов с нарушением работы опорно-двигательного аппарата и слепых - не более 60 м, а от рабочих мест на площадке предприятия — не более 150м.
1.10. Нормы площади помещений на 1чел., единицу оборудования, расчетное число работающих, обслуживаемых на единицу оборудования в санитарно-бытовых помещениях, следует принимать по табл. 3.6.
Таблица 4.6.
Нормы площади помещений на одного человека и единицу оборудования
Наименование
|
Показатель
|
Площадь помещений на 1 чел. м2
|
Гардеробные уличной одежды, раздаточные
|
0,1
|
Спецодежды1
, помещения для обогрева или охлаждения
|
Кладовые для хранения спецодежды2
:
|
при обычном составе спецодежды
|
0,04
|
расширенном составе спецодежды
|
0,06
|
громоздкой спецодежде
|
0,08
|
Респираторные
|
0,07
|
Помещения централизованного склада спецодежды и средств индивидуальной защиты:
|
для хранения
|
0,06
|
выдачи, включая кабины примерки и подгонки
|
0,02
|
Помещения дежурного персонала с местом для уборочного инвентаря, курительные при уборных или помещениях для отдыха
|
0,02
|
Места для чистки обуви, бритья, сушки волос
|
0,01
|
Помещения для сушки, обеспыливания или обезвреживания спецодежды
|
0,15
|
Помещения для мытья спецодежды, включая каски и спец обувь
|
0,3
|
Площадь помещений на единицу оборудования, м2
|
Преддушевые при кабинах душевых открытых и со сквозным проходом
|
0,7
|
Тамбуры при уборных с кабинами
|
0,4
|
Число обслуживаемых в смену на единицу оборудования, чел. напольные чаши (унитазы) и писсуары уборных:
|
в производственных зданиях
|
18/12
|
"административных"
|
45/30
|
при залах собраний, совещаний, гардеробных, столовых
|
100/60
|
Умывальники и электрополотенца в тамбурах уборных:
|
в производственных зданиях
|
72/48
|
"административных"
|
40/27
|
Устройство питьевого водоснабжения в зависимости от групп производственных процессов:
|
2а, 2б
|
100
|
1а, 1б, 1в, 2в, 2г, 3а, 3б, 4
|
200
|
Полудуши
|
15
|
1
Предусматривать отдельные помещения для чистой и загрязненной спецодежды.
2
Для групп производственных процессов 1в, 2в, 2г,3б.
1) В I климатическом районе и подрайонах IIА и IIIА, а также при самообслуживании площадь гардеробных уличной одежды следует увеличивать на 25%.
2) При помещениях раздаточных, сушки, обеспыливания и обезвреживания спецодежды следует дополнительно предусматривать место для переодевания площадью 0,1м2
/чел., а в гардеробных уличной одежды и кладовых для хранения спецодежды — места для сдачи и получения спецодежды площадью 0,03м2
/чел. При респираторных более чем на 500чел. следует дополнительно предусматривать мастерские площадью 0,05м2
/чел. для проверки и перезарядки приборов индивидуальной защиты органов дыхания.
3) Площадь помещений, должна быть не менее 4м2
, преддушевых и тамбуров — не менее 2м2
.
4) В числителе даны показатели для мужчин, в знаменателе — для женщин.
5) При числе обслуживаемых менее расчетного следует принимать одну единицу оборудования.
Таблица 4.7.
Наименование
|
Показатель
|
Кол. оборудования
|
Число гардеробных шкафов + 30%, шт.
|
120 чел.
|
156
|
Число человек на одну душевую сетку
|
5
|
24
|
Число человек на один кран
|
15
|
8
|
Число писсуаров, шт. муж.
|
100
|
4
|
жен.
|
60
|
3
|
Площадь помещений, м2
|
Гардеробные уличной одежды раздаточные
|
0,2
|
31.2
|
Кладовые для хранения спецодежды
|
0,04
|
6,24
|
Площадь помещений на единицу оборудования, м2
|
Преддушевые
|
0,07
|
11,2
|
Тамбуры при уборных с кабинами
|
0,04
|
6,4
|
Число единиц оборудования, шт.
|
Уборных в производственных зданиях
|
18
|
7
|
Уборных в административных зданиях
|
45
|
3
|
Умывальники и электрополотенца
|
72
|
2
|
Устройства питьевого водоснабжения
|
100
|
2
|
Расчёт:
Количество мужчин 120х0,7=84
Количество женщин 120х0,3=36
число душевых кабинок Рм/Рп=84/5=17
Рж/Рп=36/5=7
число гардеробных шкафов Р+30%Р=120+36=156
число человек на 1 кран nm=84/15=8
nж=36/15=2
число писсуаров nm=84/18=4
nж=36/12=3
площадь помещения
Гардеробные уличной одежды S=156х0,2=31,2 м2
Кладовые для спецодежды S=156х0,04=6,24 м2
площадь на единицу оборудования
Преддушевые S=Pmax x Sпр=156х0,07=11,2 м2
Тамбуры при уборных S=156х0,04=6,4 м2
Число единиц оборудования
Умывальники и электрополотенца nm=84/72=1 nж=36/72=1
Устройства питьевого снабжения nm
=84/100=1 nж
=36/100=1
Помещения здравоохранения
1.12. При проектировании предприятий следует предусматривать здравпункты, медпункты, помещения личной гигиены женщин, парильные (сауны), а по ведомственным нормам — помещения для ингаляториев, фотариев, ручных и ножных ванн, а также помещения для отдыха в рабочее время и психологической разгрузки.
1.13. При списочной численности от 50до 300работающих должен быть предусмотрен медицинский пункт.
Площадь медицинского пункта следует принимать: 12м2
— при списочной численности от 50до 150работающих, 18м2
— от 151до 300.
На предприятиях, где предусматривается возможность использования труда инвалидов, площадь медицинского пункта допускается увеличивать на 3 м2
.
Медицинский пункт должен иметь оборудование по согласованию с местными органами здравоохранения.
1.14. Помещения и места отдыха в рабочее время и помещения психологической разгрузки следует размещать, как правило, при гардеробных домашней одежды и здравпунктах.
При допустимых параметрах воздуха рабочей зоны в производственных помещениях и отсутствии контакта с веществами 1‑ и 2‑го классов опасности допускается предусматривать места отдыха открытого типа в виде площадок, расположенных в цехах на площадях, не используемых в производственных целях.
1.15. В помещениях для отдыха и психологической разгрузки при обосновании могут быть предусмотрены устройства для приготовления и раздачи специальных тонизирующих напитков, а также места для занятий физической культурой.
1.16. Уровень звукового давления в помещениях и на местах для отдыха, а также в помещениях психологической разгрузки не должен превышать 65дБА.
Расчёт: по Р=120 принимаем
Площадь медицинского пункта 12м2
Помещения предприятий общественного питания
1.17. Предприятия общественного питания следует проектировать с учетом возможности использования их как общих объектов для групп предприятий, размещаемых в городской застройке или населенных пунктах с учетом организации обслуживания населения.
1.18. При проектировании производственных предприятий должны быть предусмотрены столовые, рассчитанные на обеспечение всех работающих предприятий общим, диетическим, а по специальным заданиям— лечебно-профилактическим питанием.
1.19. При численности работающих в смену более 200чел. Следует предусматривать столовую, работающую, как правило, на полуфабрикатах1
, до 200чел.— столовую - раздаточную.
При численности работающих в смену менее 30чел. вместо столовой - раздаточной допускается предусматривать комнату приема пищи.
1
При обосновании допускается предусматривать столовые, работающие на сырье.
1.20. Число мест в столовой следует принимать из расчета одно место на четырех работающих в смене или наиболее многочисленной части смены. В зависимости от требований технологических процессов и организации труда на предприятии число мест в столовых допускается изменять.
Расчёт: N=120/4=30 мест
Число мест в столовой - раздаточной 30 мест
2. Административные здания и помещения
2.1. В административных зданиях должны быть размещены помещения и оборудование управления, конструкторских бюро, охраны труда, общественных организаций, учебных занятий.
Состав общезаводских и цеховых административных помещений следует устанавливать в заданиях на проектирование в соответствии со структурой управления предприятием.
Помещения управления и конструкторских бюро
2.2. Площадь помещений следует принимать из расчета 4м2
на одного работника управления, 6м2
на одного работника конструкторского бюро, для работающих инвалидов, пользующихся креслами-колясками № 5,65 и 7,65 м2
соответственно.
При оснащении рабочих мест крупногабаритным оборудованием и размещении в рабочих помещениях оборудования коллективного пользования (терминалов ЭВМ, аппаратов для просмотра микрофильмов и др.) площади помещений допускается увеличивать в соответствии с техническими условиями на эксплуатацию оборудования.
Площадь кабинетов руководителей должна составлять не более 15% общей площади рабочих помещений.
2.3. При кабинетах руководителей предприятий и их заместителей должны быть предусмотрены приемные. Допускается устраивать одну приемную на два кабинета. Площадь приемных должна быть не менее 9м2
.
2.4. В цехах управления при числе инженерно-технических работников до 300чел., следует предусматривать залы совещаний, рассчитываемые на 30% работающих. Допускается увеличивать площадь одного из кабинетов руководителей цеха из расчёта 0,8 м2
на одно место.
При наличии в числе работающих инвалидов, пользующихся креслами-колясками, в залах совещаний должны быть предусмотрены места для них из расчета 1,65 м2
на одно место.
2.5. При залах совещаний на расстоянии до 30м следует предусматривать уборные.
Расчёт: Sпом упр=N x Sпр = 11 х 4 = 44 м2
Sприём,=11 м2
Sзалов= N x Sпр = 36 х 0,8 = 22,4 м2
Площадь помещений управления и конструкторских бюро 44м2
Площадь приёмной 11м2
Площадь зала совещаний и кулуаров 22,4м2
5. Определение технико-экономических показателей проектируемого цеха.
5.1 Ведомость технологического оборудования
В ведомости технологического оборудования указывается название оборудования, его марка, мощность, время работы, цена, а так же амортизационные отчисления и отчисления в ремонтный фонд. Расчет количества оборудования произведен в разделе 1.5, его результаты сведены в ведомость технологического оборудования (табл. 5.1).
5.2 Расчет численности рабочих
Фонд времени.
ФД
=(FК
-FНД
)∙S∙g∙КР
, где
FК
– календарный фонд рабочего времени;
FНД
– выходные и праздничные дни;
S – количество смен работы;
g – средняя продолжительность смены, час.
Таблица 5.2
Расчётные и действительные фонды времени для оборудования
Наименование отделения
|
Число смен работы
|
Календарный фонд рабочего времени, дн.
|
Кр
|
Потери рабочего времени, дн.
|
Действительный годовой фонд времени, час.
|
Плавильно-заливочное отделение
|
2
|
365
|
0,95
|
114
|
3815
|
Модельное отделение
|
2
|
365
|
0,95
|
114
|
3815
|
Отделение изготовления форм
|
3
|
365
|
0,90
|
4
|
7800
|
ТО
|
3
|
365
|
0,90
|
4
|
7800
|
ЛЮМ-контроль
|
2
|
365
|
0,95
|
114
|
3815
|
Очистное отделение
|
2
|
365
|
0,95
|
114
|
3815
|
Таблица 5.3
Структура годового бюджета времени одного рабочего
Состав бюджета рабочего времени
|
По плану на год
|
Дни
|
Часы
|
1. Календарный ФРВ
|
365
|
2920
|
2. Выходные и праздники
|
115
|
920
|
3. Номинальный ФРВ
|
250
|
2000
|
4. Целодневные невыходы
|
48
|
384
|
а) очередной отпуск
|
30
|
240
|
б) дополнительный отпуск
|
5
|
40
|
в) по болезни
|
8
|
64
|
г) выполнение гос. обязанностей
|
2,5
|
20
|
д) декретный отпуск
|
2,5
|
20
|
5. Явочный ФРВ
|
202
|
1632
|
6. Внутрисменные потери РВ
|
0,25
|
2
|
7. Эффективный ФРВ
|
202
|
1616
|
Расчет численности рабочих.
Списочная численность рабочих соответствующей профессии разряда:
, где
Nв
– приведенная программа выпуска;
ti
– трудоемкость выполнения i – й операции;
Фэ
– эффективный фонд времени работы одного рабочего в год;
Квн
– коэффициент выполнения норм;
m – количество наименований операций, выполняемых рабочими данной профессии и разряда.
1. Запрессовщики моделей (4 разряд):
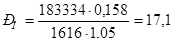
принимаем 18 человек.
2. Сборщики блоков (4 разряд):
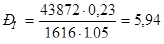
принимаем 6 человек.
3. Подрезка чаш ( рабочие 3 разряд):
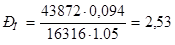
принимаем 2 человека
4. Вытопка (формовщики 3 разряд):
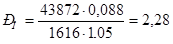
Принимаем 2 человека
5. Сварщики (4 разряд):
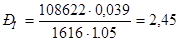
Принимаем 2 человека
6. Обдувка (рабочие 3 разряд):
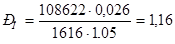
Принимаем 1 человека
7. Шлифовка (рабочий 3 разряд):
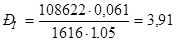
принимаем 4 человек
8. ТО (термист 5 разряд):

принимаем 8 человек
Таблица 5.4
Численность основных рабочих по профессиям и разрядам
Профессия рабочих
|
Разряд
|
Списочная численность рабочих
|
Расчетная
|
Принятая
|
Запрессовщик моделей
|
4
|
17,1
|
17
|
Сборщик блоков
|
4
|
5,9
|
6
|
Подрезчик литниковых чаш
|
3
|
2,5
|
3
|
Вытопщик
|
3
|
2,2
|
2
|
Сварщик
|
4
|
2,25
|
2
|
Обдувщик отливок
|
3
|
1,2
|
1
|
Шлифовщик
|
3
|
3,9
|
4
|
Термист
|
5
|
7,6
|
8
|
ИТОГО по предприятию
|
43
|
Численность основных рабочих по рабочим местам и нормам обслуживания.
, где:
С – количество однотипного оборудования
S – число смен в сутках
Кпер
– коэффициент перевода явочного числа рабочих в списочное
1. Плавильщики модельной массы (формовщик 3 разряд)

Принимаем 2 человека
2. Изготовление форм
Изготовление форм производится на автоматическом конвейере. Конвейер обслуживается 5 рабочими в смену. При работе формовочного отделения в три смены принимаем 15 человек.
3. Плавильное отделение (плавильщик 5 разряд)

Принимаем 5 человек
Таблица 5.5
Численность основных рабочих по рабочим местам и нормам обслуживания
Профессия рабочих
|
Кол-во рабочих мест, оборудования
|
Число рабочих в смену
|
Число смен
|
Коэф-нт пересчета
|
Списочная численность рабочих
|
Формовщик
|
2
|
1
|
2
|
1,23
|
4
|
Линия изготовления форм
|
1
|
5
|
3
|
1,23
|
16
|
Плавильщик
|
2
|
1
|
2
|
1,23
|
5
|
Итого по предприятию
|
25
|
Расчет численности вспомогательных рабочих
Кпер
– коэф. перевода явочного числа рабочих в списочное:
 
Таблица 5.6
Численность руководителей, специалистов и служащих по штатному расписанию
Профессия рабочих
|
Кол-во рабочих мест
|
Норма обслуживания
|
Число рабочих в смену
|
Кол-во смен
|
Списочная численность рабочих
|
1. Начальник цеха
|
1
|
1
|
1
|
1
|
1
|
2. Мастер
|
2
|
1
|
1
|
2
|
4
|
3. Зам. нач. цеха
|
2
|
1
|
1
|
1
|
2
|
4. Механик
|
2
|
1
|
2
|
2
|
2
|
5. Инженер-технолог
|
2
|
1
|
1
|
1
|
2
|
6. Бухгалтер
|
2
|
1
|
2
|
1
|
2
|
ИТОГО по предприятию
|
13
|
Численность рабочих по техническому обслуживанию оборудования определяется отдельно по профессиям:
, где
Rе
– кол. единиц ремонтной сложности оборудования в цехе, рем. ед.;
S - число смен в сутках;
N0
– норматив обслуживания одним рабочим в смену, рем. ед.
При двухсменной работе нормами рекомендуется принимать в первой смене
55% рабочих, во второй - 45%.
Таблица 5.7
Численность вспомогательных рабочих
Профессия
|
Разряд
|
Измерительные нормы обслуживания
|
Норма обслуживания на одного вспомогательного рабочего
|
Кол-во расчетных ед.
|
Коэф-нт пересчета
|
Списочная численность вспомогательных рабочих
|
Слесари по ППР и межремонтному обслуживанию
|
4
|
150
|
600
|
0,61
|
1,24
|
2
|
Станочники по ремонту
|
5
|
150
|
1650
|
0,22
|
1,24
|
1
|
Смазчики
|
3
|
150
|
1000
|
0,37
|
1,24
|
1
|
Электронщики
|
5
|
150
|
800
|
0,46
|
1,24
|
1
|
Наладчик автоматов
|
5
|
7
|
130
|
2,1
|
1,24
|
2
|
Транспортные рабочие
|
3
|
79
|
35
|
5,52
|
1,24
|
5
|
Контролеры ОТК
|
4
|
79
|
30
|
6,47
|
1,24
|
6
|
Уборщики производственных помещений
|
2
|
5184
|
1500
|
8,7
|
1,24
|
8
|
ИТОГО
|
24
|
Таблица 5.8
Сводная ведомость общего состава работающих на производстве
Категория работающих
|
Общее кол-во
|
Средний разряд
|
1-ая смена
|
2-ая смена
|
В % от общего кол-ва работающих
|
Основные рабочие
|
68
|
4-5
|
39
|
31
|
47
|
Вспомогательные рабочие
|
26
|
3-4
|
13
|
11
|
35,3
|
ИТОГО
|
94
|
52
|
42
|
Менеджеры
|
5
|
6
|
4
|
1
|
2,9
|
Специалисты
|
6
|
6
|
6
|
-
|
5,88
|
Служащие
|
2
|
6
|
2
|
-
|
8,82
|
МОП
|
-
|
-
|
-
|
-
|
-
|
ВСЕГО
|
107
|
64
|
43
|
100
|
5.3 Основной капитал
Таблица 5.9
Основной капитал
Наименование основных фондов
|
Первоначальная (балансовая) стоимость, т. руб.
|
Отчисления в ремонтный фонд
|
Амортизационные отчисления
|
% отчисления
|
Сумма в т. руб
|
Норма аморт., %
|
Сумма в т. руб.
|
Здания и сооружения
|
53280
|
2
|
1065,6
|
1,2
|
639,36
|
Силовые машины и оборудование
|
2511
|
2
|
50,22
|
15
|
376,65
|
Рабочие машины и оборудование:
|
технологическое
|
81773,97
|
2
|
1635,48
|
15
|
12266,08
|
Транспортные средства
|
669,6
|
2
|
13,39
|
12,5
|
83,7
|
Приспособления и оснастка
|
1896,43
|
2
|
37,92
|
20,0
|
379,28
|
Производственный и хозяйственный инвентарь
|
1635,48
|
2
|
32,71
|
9
|
147,19
|
Всего О.К.
|
141766,48
|
2835,32
|
13892,27
|
Производственные помещения и другая собственность.
Общая площадь цеха определяется как сумма площадей под участки производства продукции, вспомогательные отделения и склады, бытовые и конторские помещения.
Sп =
Sпу +
Sвс +
Sбк
= 5579м2
, где
Sп
- общая производственная площадь;
Sпу
- площадь под производственные участки;
Sвс
- площадь под вспомогательные отделения и склады;
Sбк
–площадь бытовых и конторских помещений.
Основной капитал.
ОК = Спл
+ Соб
+ Сдэ
+ Снма
, где
Спл
– стоимость площадей, тыс.руб.;
Соб
– стоимость оборудования и транспортных средств, тыс.руб.;
Сдэ
– стоимость других элементов основного капитала, тыс.руб.;
Снма
–стоимость нематериальных активов, тыс.руб.
ОК =55790 + 82443,57 + 3531,91 = 141766,48тыс. руб.
5.4 Расчет фондов заработной платы рабочих
Затраты по оплате труда основных рабочих относятся к переменным затратам, а вспомогательных рабочих, специалистов, менеджеров, СКП и МОП - к постоянным.
Тарифный фонд заработной платы рабочих-повременщиков:
, где
Счас
– часовая тарифная ставка рабочего-повременщика данной профессии и разряда, руб/час (табл. 5.14);
Фэф
– эффективный фонд времени одного рабочего, ч;
Рвсп
– списочная численность рабочих-повременщиков данной профессии и разряда.
Таблица 5.10
Ведомость транспортного оборудования
Наименование оборудования
|
Количество
|
Мощность двигателя, кВт
|
Первоначальная стоимость, $
|
ед.
|
всего
|
ед.
|
всего
|
Кран-балка
|
5
|
15
|
75
|
3300
|
16500
|
Транспортёр
|
1
|
5,2
|
5,2
|
950
|
950
|
Электрокар
|
3
|
-
|
-
|
1500
|
4500
|
Элеватор
|
1
|
4,8
|
4,8
|
1000
|
1000
|
Итого по оборудов.
|
85
|
22950
|
Таблица 5.11
Расчёт затрат на оснастку
|
Наименование оснастки
|
Количество
|
Цена за единицу, $
|
Общая стоимость, $
|
Тигли плавильно-заливочных печей
|
4
|
130
|
520
|
Футеровка ТО
|
4
|
155
|
620
|
Охладительные короба
|
18
|
15
|
270
|
Пресс-формы моделей
|
40
|
2500
|
100000
|
Пресс-формы стержней
|
10
|
3100
|
31000
|
Абразивный инструмент
|
250
|
5
|
1250
|
Итого
|
133660
|
Табл 5 12
Табл 5 13 Таблица 5.14
Тарифные ставки для рабочих промышленных и непромышленных групп
Разряд
|
Тарифный коэф.
|
Счас
, руб.
|
1
|
1,0
|
8,93
|
9,75
|
2
|
1,1
|
16,19
|
14,42
|
3
|
1,3
|
16,19
|
16,47
|
4
|
1,5
|
17,45
|
18,12
|
5
|
1,7
|
19,71
|
20,47
|
Фонд часовой зарплаты определяется суммированием тарифного фонда зарплаты и всех доплат, входящих в часовой фонд.
К числу доплат до часового фонда заработной платы относятся:
а) премии по сдельно-премиальной и повременно-премиальной системам оплаты труда;
б) доплата за условия труда;
в) доплата за многостаночное обслуживание и совмещение профессий;
г) доплата за работу в вечернюю и ночную смены;
д) доплаты не освобожденным бригадирам и др.
Зчас
= Зтар
+ dчас
Сдельно-премиальная и повременно-премиальная система применяется на предприятиях с выплатой премий за улучшение технико-экономических показателей. Сумма премий определяется в процентном отношении к прямой заработной плате рабочих сдельщиков.
Зд пр
= Зрс
× %Прем /100
Остальные доплаты учитываются в общей сумме через процент доплат. Процент премий и доплат принять равным 50% для основных рабочих и 40% - для вспомогательных.
Здоп
= Зрср
× % Допл /100
Дневной фонд зарплаты рассчитывается путем суммирования часового фонда и доплат до дневного фонда:
Здн
=Зчас
+ dдн
Фонд зарплаты соответствующих категорий рабочих по статьям калькуляции определяется исходя из среднегодовой зарплаты одного вспомогательного рабочего и численности данной категории рабочих.
Таблица 5.15
Расчет фонда заработной платы производственных рабочих
Элементы фонда з/п
|
Основные рабочие
|
Вспомогательные рабочие
|
Кол-во н.ч. на программу
|
Часовые тарифные ставки
|
Сумма в рублях
|
Часовые тарифные ставки
|
Эффек. фонд времени
|
Численность рабочих
|
Сумма в рублях
|
Фонд прямой з/п рабочих
|
2разряд
|
-
|
12,93
|
-
|
14,43
|
1616
|
8
|
186420
|
3разряд
|
32
|
16,19
|
837220
|
16,78
|
5
|
135500
|
4разряд
|
30
|
17,45
|
845980
|
18,13
|
8
|
234250
|
5разряд
|
8
|
19,7
|
254810
|
20,48
|
3
|
99240
|
Итого тарифный фонд з/п
|
1938010
|
655410
|
Доп. до основ. фонда
|
50%
|
969005
|
40%
|
262160
|
Итого основной фонд з/п
|
2907015
|
917570
|
Доп. до годового фонда
|
10%
|
290700
|
10%
|
91760
|
Итого годовой фонд з/п
|
3197715
|
1009330
|
Районный коэф.
|
15%
|
479660
|
15%
|
151400
|
ВСЕГО годовой фонд з/п
|
3677375,0
|
1160730
|
Среднегодовая з/п рабочего
|
52530
|
48360
|
Среднемесячная з/п рабочего
|
4380
|
4030
|
Таблица 5.16
Распределение фонда заработной платы и отчислений на социальные нужды по статьям калькуляции
Статья
калькуляции
|
Кол-во работающих
|
Категория работающих
|
Фонд з/п, т.руб.
|
Сумма отчислений на соц. Нужды (35,6%)
|
Сумма фонда з/п и суммы отчислений на соц. нужды
|
1
|
2
|
3
|
4
|
5
|
6
|
Зарплата основных рабочих
|
74
|
Основные рабочие
|
3677,4
|
1309,1
|
4986,5
|
Расходы на содержание и эксплуатацию оборудования:
|
-содержание оборудования
|
6
|
Дежурный персонал, наладчики, смазчики и др.
|
145,1
|
51,7
|
196,8
|
-ремонт оборудования и техоснастки
|
3
|
Слесари, станочники по ремонту
|
96,7
|
34,4
|
131,1
|
-прочие расходы
|
6
|
Контролеры ОТК
|
290,2
|
103,3
|
393,5
|
Цеховые расходы
|
-на внутрицеховое перемещение грузов
|
5
|
Транспорт. рабочие
|
241,8
|
86,1
|
327,9
|
-на содержание зданий, сооруж., инвентаря
|
8
|
Уборщики производственных помещений
|
386,9
|
137,7
|
524,6
|
ВСЕГО
|
94
|
6560,4
|
5.5 Расходы на содержание и эксплуатацию оборудования (РСЭО)
Смета РСЭО составляется табличным методом с учетом результатов ранее проведенных расчетов.
Расходы на вспомогательные эксплуатационные материалы определяются в размере 0,5% от стоимости технологического оборудования.
Затраты на силовую электроэнергию.
Суммарная мощность электродвигателей технологического и вспомогательного оборудования цеха: Nу
= 710 кВт;
Средний коэффициент загрузки эл. двигателей по мощности: Км
= 0,8;
Средний коэф. загрузки эл. двигателей по времени: КЗ
= 0,6;
Коэф. одновременной работы эл. двигателей: Код
=0,8;
Коэф. потерь эл. энергии в сети: КW
=1,06;
Эффективный фонд времени работы единицы оборудования: FЭ
=3815 ч;
Коэф. полезного действия эл. двигателей: h=0,8;
Стоимость 1 кВт/ч электроэнергии: Сэл
= 0,9 руб.
; WЭЛ
= 1240345 руб.
Затраты на сжатый воздух для обдувки деталей и узлов, на пневматические зажимные устройства, инструменты, подъемники:
Qчас – среднечасовой расход сжатого воздуха для всех воздухоприемников, м3 ;
Fэф
– эффективный фонд времени работы оборудования, ч;
КЗ
- средний коэффициент загрузки оборудования по времени;
Свозд
- стоимость 1000 м3
сжатого воздуха.

руб.
Прочие постоянные статьи затрат
1. Общепроизводственные расходы:
- содержание производственных помещений;
- заработная плата обслуживающих рабочих, специалистов, основная и дополнительная с отчислениями;
- расходы на сервисное обслуживание.
2. Общехозяйственные расходы:
- заработная плата управляющих, премии;
- командировочные расходы, оплата услуг связи, бухгалтерских и юридических услуг, арендные платежи, и др.
Таким образом общепроизводственные расходы связаны с обслуживанием и управлением производства. Их определяем в размере 500 % от основной ЗП основных производственных рабочих.
Сумма общехозяйственных расходов принимается в размере 300-400 % от основной ЗП основных производственных рабочих, а сумму внепроизводственных расходов – 2 % от себестоимости товарной продукции.
Таблица 5.17
Смета расходов на содержание и эксплуатацию оборудования цеха
Наименование статей
|
Состав статей
|
Сумма, т.руб.
|
1
|
2
|
3
|
1.Амортизация на полное восстановление оборудования и транспортных средств, оснастки
|
Амортизационное отчисление на полное восстановление по действующим нормам от первоначальной стоимости оборудования трансп. средств, дорогостоящего инструмента.
|
13892,27
|
ИТОГО по статье 1
|
¾
|
13892,27
|
2. Эксплуатация оборудования (кроме расходов на ремонт)
|
Затраты на вспомогательные эксплуатационные материалы.
|
408,86
|
Стоимость электроэнергии и сжатого воздуха
|
199,11
|
Зарплаты с отчислениями на соц. нужды вспомогательных рабочих, обслуживающих оборудование.
|
196,8
|
ИТОГО по статье 2
|
¾
|
804,77
|
3. Затраты на ремонт оборудования, транспортных средств, дорогостоящей оснастки.
|
Отчисления в ремонтный фонд
|
2835,32
|
Итого по статье 3
|
¾
|
2835,32
|
4. Внутрицеховое перемещение груза
|
Заработная плата с отчислениями на социальные нужды транспортных рабочих
|
327,9
|
Затраты по эксплуатации транспорта (стоимость смазочных, обтирочных материалов, горючего и т.д.)
|
69,3
|
ИТОГО по статье 4
|
397,2
|
5. Износ малоценных и быстроизнашивающихся инструментов и приспособлений.
|
Сумма износа малоценных и быстроизнашивающихся инструментов и приспособлений.
|
1896,43
|
Расходы по восстановлению и ремонту (з/п рабочих, занятых восстановлением, стоимость материалов)
|
37,59
|
ИТОГО по статье 5
|
¾
|
1934,02
|
6. Прочие расходы
|
Зарплата с отчислениями на соц. нужды контролеров ОТК, кладовщиков и др., исключая уборщиков производственных помещений.
|
393,5
|
ИТОГО по статье 6
|
¾
|
393,5
|
ВСЕГО расходов по эксплуатации и содержанию оборудования
|
¾
|
19229,41
|
Себестоимость всего объема определятся:
С = Зпер
×N + Зпост
= 1,75×108622 + 550078,78 = 245199,04 тыс. руб.
Себестоимость единицы продукции:
Сед
= Зпер
+ Зпост
/N = 1,75 + 55005,78/108622 = 2,2574 тыс. руб.
Где:
Зпер
– переменные затраты на единицу продукции, т.руб.;
Зпост
– постоянные затраты на весь объем, т.руб.;
N – годовая программа выпуска, шт.
5.6 Калькуляция себестоимости продукции
Таблица 5.18
Годовая приведенная программа предприятия, шт.
Наименование статей затрат
|
Затраты, тыс.руб.
|
На единицу
|
На весь выпуск
|
1. Основные материалы без возвратных отходов
|
1,231324
|
133745,6
|
2. Вспомогательные материалы технологического назначения
|
0,472881
|
51365,33
|
ИТОГО прямых материальных затрат
|
1,704205
|
185110,93
|
3. Затраты на технологическую энергию
|
0,000883
|
95,86
|
4. Затраты на технологическое топливо
|
-
|
-
|
5.Основная зарплата основных производственных рабочих
|
0,033858
|
3677,37
|
7. Отчисления на социальные нужды
|
0,012052
|
1309,1
|
ИТОГО переменных затрат
|
1,750998
|
190193,26
|
8. Расходы на содержание и эксплуатацию оборудования
|
0,177031
|
19229,41
|
9. Общепроизводственные расходы
|
0,169274
|
18386,85
|
10. Общехозяйственные расходы
|
0,118492
|
12870,8
|
Производственная себестоимость
|
2,215795
|
240680,32
|
11. Расходы на маркетинг
|
0,04160
|
4518
|
ИТОГО постоянные затраты
|
0,506397
|
55005,78
|
Полная себестоимость
|
2,257395
|
245199,1
|
Оборотные средства (оборотный капитал).
Величина оборотного капитала определяется по всем видам нормируемых оборотных средств.
;
руб.
затраты на материалы: Ос.м.
= 185110930 руб.;
величина планируемого периода в днях: Тп
=365;
норматив запаса на материал в днях: Нм
=7 ;
себестоимость годового объема продукции: С= 245199041 руб.;
норматив на незавершенное производство в днях: Ннзп
=5;
норматив запаса годовой продукции в днях: Нгп
=7.
Производственный капитал.
ПК
= О.К. + Об.К. ПК
=141766,48 + 11611,41 = 153377,89 руб.
5.7 Финансовый план
Расчет плановой суммы балансовой прибыли.
Прибыль определяется как разница между выручкой от реализации и себестоимостью продукции.
Цена: Цед
= Сед
× Крент
× НДС = 2,257×1,1×1,2 =3,251 т. руб.
Таблица 5.19
Расчет плановой суммы балансовой и чистой прибыли
Показатели
|
Величина, руб
|
1. Выручка от реализации: Цед
×Nпр
|
353092756
|
2. НДС (расчетная ставка=20%)
|
70618551
|
3. Полная себестоимость
|
245199040
|
4. Прибыль от реализации продукции
|
37275165
|
5. Доходы от иной деятельности
|
-
|
ИТОГО: балансовая прибыль
|
37275165
|
6. Платежи в бюджет (налоги)
|
11809344
|
7. Чистая прибыль
|
25465821
|
Расчет чистой прибыли.
Рассчитываются налоги с балансовой прибыли и налог на прибыль. Из балансовой прибыли вычитаются налоги:
Таблица 5.20
Налоги из балансовой прибыли
Вид налога
|
Величина налога, руб.
|
Налог на имущество, 2%
|
2793581
|
Налог на образование, 1,%
|
65604
|
Налог на содержание милиции, 3%
|
4120
|
Налог на прибыль, 24%
|
8946039
|
ИТОГО налоговых отчислений
|
11809344
|
Формирование баланса доходов и расходов.
Таблица 5.21
Баланс доходов и расходов
Доходы и поступление средств
|
Расходы и отчисления средств
|
1. Прибыль от реализации продукции
|
37275165
|
1. Налоги
|
11809344
|
2. Доходы от иной деятельности
|
-
|
2. Чистая прибыль в т.ч. на пополнение оборотных средств
|
25465821
|
3. Амортизационные отчисления
|
13892270
|
3. Амортизационные отчисления
|
13892270
|
4. Отчисления в ремонтный фонд
|
2835320
|
4. Отчисления в ремонтный фонд
|
2835320
|
ИТОГО
|
54002755
|
ИТОГО
|
54002755
|
Безубыточный объем производства продукции (график безубыточности).
шт.
Зпост
– постоянные затраты, определенные на объем производства;
Зпер
- переменные затраты не единицу продукции.
Экономические и финансовые показатели бизнеса.
Рентабельность производственного капитала.
;
Рентабельность продукции.
;
Маржа чистой прибыли.

Финансовый результат может быть оценен положительно, если маржа чистой прибыли не ниже 4,7 %.
5.8 Экономические показатели цеха
Таблица 5.22
Экономические показатели цеха
Наименование показателей
|
Единицы измерения
|
Значение показателей
|
Годовая приведенная программа
|
шт.
|
110012
|
Трудоемкость единицы продукции
|
н.ч./шт
|
0,033
|
Кол-во ед. технологического оборудования
|
шт.
|
43
|
Численность рабочих
|
чел.
|
107
|
Стоимость основного капитала
|
руб.
|
141766480
|
Себестоимость ед. продукции в т.ч.
|
руб /шт.
|
2,257395
|
-переменные затраты
|
руб /шт.
|
1,750988
|
-постоянные затраты
|
руб /шт.
|
0,506397
|
Цена единицы продукции
|
руб /шт.
|
3250,6
|
Прибыль балансовая
|
руб
|
37275170
|
Выручка от реализации
|
руб
|
353092760
|
Налоги в бюджет
|
руб
|
11809344
|
Чистая прибыль
|
руб
|
25465821
|
Средняя зарплата рабочего:
|
-основного
|
руб
|
4380
|
- вспомогательного
|
руб
|
4030
|
Эффективность:
|
-рентабельность производственного капитала
|
%
|
24,3
|
-рентабельность продукции
|
%
|
15,2
|
6. Технологический процесс изготовления художественной отливки
6.1 Анализ технологичности отливки
Изделие «Барельеф» изготавливается из алюминиевых сплавов промышленного назначения (АК-5, АК-5М2 и др.).
Композиция отливки выполняется методом литья в разовую песчано-глинистую форму. Для обеспечения полного заполнения формы и направленного затвердевания выбираю горизонтальное расположение отливки при заливке формы расплавом. Плоскость разъема формы горизонтальная. Заливка выполняется в стояк.
6.2 Технологический процесс изготовления отливки
Данный технологический процесс описывается для изготовления отливки Барельеф.
Процесс изготовления начинается с подготовки шихтовых материалов. Он заключается в распиливании чушки на куски, размеры которых удовлетворяют размеры тигля печи. После этого очищаем их от смазки используемой при распиловке и укладываем для прогрева перед закладкой в печь. Закладываем куски в вышедшую на режим плавления печь ≈ 720о
С.
Во время приготовления расплава приступаем к изготовлению формы, что в свою очередь начинается приготовления формовочной смеси. Для этого засыпаем в бегуны кварцевый песок, перемешиваем в течении 3-5 минут для перемалывания больших кусков. Добавляем 5-8 % формовочной глины. Перемешиваем 3-5 минут, и добавляем 3-5 % воды, после чего перемешиваем до получения однородной массы ≈ 5 минут. Облицовочная формовочная смесь готова. Наполнительная формовочная смесь приготавливается по аналогии, только с добавлением отработанной формовочной смеси.
Формовку ведём по горизонтальной плоскости разъема. Для чего укладываем нижнюю опоку на подопочную плиту. Выбираем место для модели и укладываем ее. Засыпаем сначала облицовочной смесью, уплотняем слой и слегка разрыхляем его верхний слой. Потом засыпаем наполнительную смесь, уплотняем и засыпаем ещё слой, чуть выше краёв опоки. Следим за неподвижностью модели и уплотнением смеси. Уплотняем до верхних краёв опоки. Излишки смеси срезаем ножом. Переворачиваем форму. Припудриваем графитом, обязательно заглаживаем. припудриваем и заглаживаем. Убираем излишки графита, и остатки формовочной смеси. Приступаем к изготовлению верхней полуформы.
Устанавливаем верхнюю опоку на нижнюю. Ставим стояк. Засыпаем облицовочную смесь, уплотняем и разрыхляем верхнюю часть слоя для лучшей связки слоёв между собой. Слоями засыпаем и уплотняем наполнительную смесь, также уплотняя и разрыхляя верхнюю часть слоя. Излишки формовочной смеси срезаются ножом.
Достаём модель стояка и подготавливаем отверстие по заливку, припудривая графитом и заглаживая.
Снимаем верхнюю полуформу. Аккуратно извлекаем модель. Вырезаем канал питателя. Выдуваем осыпавшуюся формовочную смесь. Собираем форму и даём ей выстоятся перед заливкой в течении 5-10 минут.
Расплав для заливки перегреваем до 760о
С, так как во время заполнения ковша и съёма окислительной плёнки с металла он успевает остыть. Заливку формы производим из ковша непрерывной струёй. Выдерживаем форму в течении 10 минут, чтобы металл успел остыть до температуры ≈ 300-350о
С.
Выбивку отливки из формы производим в ручную, таким образом, чтобы не повредить тело отливки.
Отрезку литниковой системы производим после полного охлаждения отливки пилой по металлу. Затем напильником удаляем облой и производим зачистку отливки от дефектов литья.
Список литературы
1. Немировский М.Б. Исследование поверхностного слоя титановых отливок и влияния его свойств на эксплуатационные характеристики литых деталей.- Автореферат.- Дисс. канд. техн. наук.- Пермь.- 1982.- 24 с.
2. Самарский А.А., Николаев Е.С. Методы решения сеточных уравнений. -М.: Наука, 1978.-592с.
3. Дульнев Г.Н., Парфенов В.Г., Сигалов А.В. Применение ЭВМ для решения задач теплообмена. -М.: Высшая школа, 1990.-207с.
4. Бибиков Е.Л., Неуструев А.А. Титановые сплавы. Производство фасонных отливок из титановых сплавов. М. «Металлургия», 1980.
5. Калиткин Н. Н. Численные методы. - М.: Наука, 1978. -512 с.
6. Ковалёв Ю. Г. Проект литейного цеха. – Пермь: ПГТУ, 1993. – 255 с.
7. Степанов Ю. А., Баландин Г. Ф., Рыбкин В. А. Технология литейного производства. – М.: Машиностроение, 1983. – 288 с.
8. Воздвиженский В. М., Грачёв В. А., Спасский В. В. Литейные сплавы и технология их плавки в машиностроении. – М.: Машиностроение, 1984. – 432 с.
9. Воздвиженский В. М., Жуков А. А. Контроль качества отливок. – М.: Машиностроение, 1990.
10. Логинов И. З. Проектирование литейных цехов. – Минск: Вышэйшая школа, 1975. – 320 с.
11. Аксёнов П. Н. Оборудование литейных цехов. – М.: Машиностроение, 1977. – 512 с.
12. Ковалёв Ю. Г. Тепловые процессы при формировании отливок. Часть 1. – Пермь: ПГТУ, 1976. – 50 с.
13. Сербинович П. П. Архитектурное проектирование промышленных зданий. – М.: Машиностроение, 1972.
14. Естественное и искусственное освещение. СНиП 23 – 05 - 95. – М.: Минстрой России, 1995. – 24 с.
15. Электробезопасность. Защитное заземление, зануление. ГОСТ 12.1.030 – 81. М., 1981. – 23 с.
16. Определение категорий помещений и зданий по взрывопожарной и пожарной опасности НП51.05 – 95. М.: МВД РФ, 1996.
17. Н.Н. Шубина, В.В. Ленина. Разработка бизнес-плана предприятия металлургического профиля. Метод. Указания к курсовой работе и дипломному проектированию для студентов. перм. гос. техн. Ун-т., 2001.
18. HTTP://WWW.VATECH.CO.UK
19. Баландин Г. Ф. Основы теории формирования отливки. Часть 1. -М.: Машиностроение, 1976.
20. Применение ЭВМ для решения задач теплообмена / Г. Н. Дульнев, В. Г. Парфенов, А. В. Сигалов. М.: Высш.шк, 1990. -207 с.
21. Ежов В.А. и др. Шамотные оболочковые формы для дитья по выплавляемым моделям // Литейное производство. 1977. №3. с.17-18.
22. Руденко А.А., Рыбкин В.А. Применение пористых огнеупорных материалов в оболочковых формах по выплавляемым моделям // Литейное производство. 1979. №2. с.18-2
23. Ковалев Ю.Г., Немировский М.Б. Шамотно-пироуглеродные формы для литья титана // Авиационная промышленность. 1980. №10. с.62-65.
|